钢渣脱硫
LF炉快速脱硫

关于LF炉如何快速脱硫的讨论罗小武1.引言在实际的生产中,LF炉冶炼脱硫能力对后续能否生产出合格的产品至关重要。
特别是随着新产品开发的需要,对钢中S含量要求越来越高,对LF炉快速脱硫工艺要求更为严格。
因此在LF炉生产过程中快速有效的脱硫越来越受到我们的重视。
2.脱硫原理分析2.1脱硫过程LF脱硫机理按照冶金学理论脱硫应该按如下步骤进行:(1)在钢-渣界面上,钢水中[FeS]按分配定律进入炉渣。
[FeS]=(FeS) (1-1)(2)渣中(FeS)与渣中自由(CaO)结合为稳定的(CaS)。
(FeS)+(CaO)=(FeO)+(CaS) (1-2) 脱硫基本过程大体分为:硫由钢液内向钢-渣界面迁移;界面的化学反应,硫化物向渣层迁移。
2.2钢水氧化性对脱硫的影响涟钢所采用的LF炉脱硫剂为石灰,其脱硫反应按离子理论可写作:(O2-)+[S]=(S2-)+[O] (1-3) 由上式可知,降低炉渣氧化性促进反应向有利于脱硫的方向进行。
因为钢渣之间存在氧的传质,如果钢水的含氧量较高,必然将影响脱硫反应向右进行。
即钢水的脱氧与脱硫是相互联系的,脱氧良好的钢水可提高渣的脱硫能力,这也是脱硫的前提条件。
2.3炉渣碱度对脱硫的影响炉渣碱度和流动性对脱硫的影响由式(1-3)可知:炉渣中Ca2 +活度越高,越促进脱硫反应的进行。
因此提高炉渣碱度,可促进脱硫反应向右进行。
但是在碱度达到一定程度后,继续提高碱度不利于脱硫,这是因为当( CaO)含量过高后,渣中会有固相质点析出,使炉渣粘度提高,流动性变差,影响了脱硫的动力学条件,使脱硫效果变差。
生产实践中,当炉渣碱度偏高时,采用加精炼渣的办法加以调整。
2.4渣量对脱硫的影响理论分析,渣量越大,对脱硫越有利,但渣量过大,会导致原材料、电能等生产成本的增加,因此实际生产时,需要合理考虑渣量大小,在适当范围内尽量增大渣量。
2.5搅拌强度对于脱硫的影响由于脱硫反应是钢渣界面反应,而钢中[S]向渣中扩散是这个反应的限制环节。
钢铁脱硫反应

钢铁脱硫反应desulfurization in iron and steel making在钢铁冶炼过程中脱除硫的化学反应。
硫是钢中主要的有害杂质之一,它在铁液中无限溶解,而在固体铁中溶解度很小(在γ-Fe中最多溶解0.05%,在Fe和FeS共晶温度988时,硫的溶解度仅为0.013%)。
含硫较高的钢液凝固时,硫以化合物[k g2]FeS[kg2]等形态富集在晶粒间界上,形成Fe和[kg2]FeS[kg2]的低熔共晶体,从而在热加工时造成钢锭及钢材的“热脆”现象。
钢铁生产过程中,硫来源于矿石(包括球团等)、金属料(包括铁合金)、熔剂及燃料,而主要是由燃料带入的。
在钢铁冶炼的每一阶段都应对原料和燃料的硫含量有所限制,并且努力创造条件从钢铁产品中将硫脱除到合乎要求。
生铁允许的最高含硫量为0.074%,大多数钢种中允许的含硫量为0.015~0.045%,优质钢的含硫量小于0.02%或更低(易切削钢除外)。
高炉炼铁过程中生铁的脱硫反应高炉内的脱硫反应是整个钢铁生产中最重要的脱硫环节。
高炉炉料中硫的载荷一般为每吨生铁4~6公斤,其中焦炭带入的硫约占总硫量的60~80%,矿石带入硫量不超过总硫量的1/3。
在冶炼过程中,约有5~20%的硫以CS及COS气体随高炉煤气排出炉外,其余的硫分配于炉渣与生铁两者之间。
通过炉渣除去生铁中的硫的反应是最主要的脱硫反应:(CaO)+[S]+[C]─→(CaS)+CO[145-1]或可写作(O)+[S]+[C]─→(S)+CO[145-1]式中圆括号表示炉渣中的组分,方括号表示铁液中的组分。
发生在生铁液滴穿过炉渣层落入炉缸的过程中和在熔渣-生铁二液相界面上的脱硫反应,使90%以上的硫进入炉渣。
即使炉渣中含硫量达到0.7~1.5%,也可得到含硫量合格的生铁。
熔渣的碱度[kg2][174-01][kg2]高,有利于生铁脱硫。
中国高炉渣碱度一般在1.0~1.2之间。
炉缸操作温度高也有利于脱除硫。
钢厂脱硫工程施工方案

钢厂脱硫工程施工方案一、概述钢厂是排放大量二氧化硫气体的工业企业,为了减少对环境的污染,必须进行脱硫工程。
脱硫工程是指将燃煤或其他含硫燃料燃烧产生的二氧化硫气体通过适当的工艺方法净化处理,使排放的气体中的二氧化硫含量降低到一定的标准以下。
本文将对钢厂脱硫工程的施工方案进行详细介绍。
二、脱硫工程施工准备工作1.组织机构为了确保脱硫工程施工的顺利进行,需要建立一个脱硫工程施工组织机构。
包括总负责人、项目经理、施工员、安全员等相关职责人员,明确各自的职责和权限。
2.材料采购根据工程设计要求和实际情况,进行脱硫设备所需要的材料采购,包括管道、阀门、设备配件等。
确保供货及时、质量合格。
3.人员培训对施工人员进行脱硫工程相关知识的培训,包括设备操作、安全生产规定等,使其具备相关技术和安全意识。
4.施工计划制定脱硫工程的施工计划,包括工程进度、工期安排、人员配置等,确保施工按时按质完成。
三、脱硫设备安装1.设备搬运根据设计要求和图纸标明的位置,进行脱硫设备的搬运和安装。
需确保设备的平稳、安全搬运,避免设备损坏和人身伤害。
2.管道布置根据设计要求进行脱硫设备的管道布置,确保管道连接紧密,无泄漏,符合相关安全标准。
3.设备安装对脱硫设备进行逐一安装调试,保证设备安装正确、运转正常。
4.系统调试对脱硫系统进行调试,保证系统运行稳定、效果达标,确保脱硫工程的质量。
四、质量控制1.工艺参数检测对脱硫设备的工艺参数进行定期检测,确保设备运行正常。
2.检测报告每次检测完成后,制作检测报告,并及时向项目负责人汇报检测结果,确保质量控制的及时性和准确性。
3.材料验收对所采购的材料进行严格的验收,保证材料质量合格,与设计要求一致。
4.安全培训针对脱硫工程施工的人员,进行安全培训,确保安全生产,避免施工事故的发生。
五、环境保护1.废气排放对脱硫系统排放的废气进行监测,确保排放符合国家相关标准和规定。
2.废水处理对脱硫工程产生的废水进行处理,确保废水排放符合相关标准和规定,不对环境造成二次污染。
钢厂脱硫渣用途
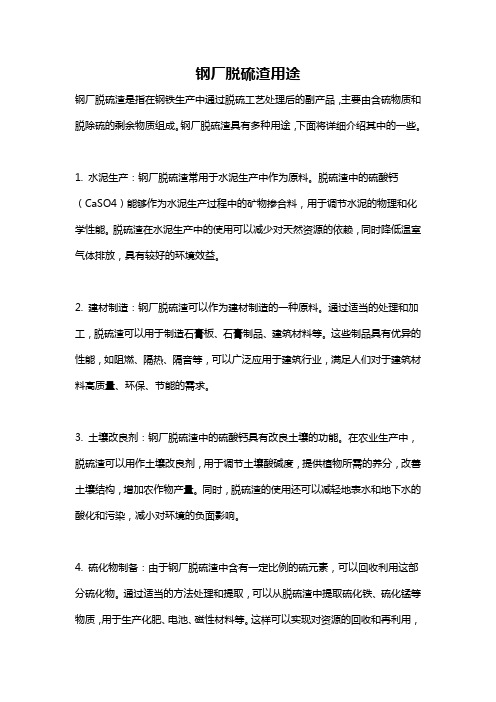
钢厂脱硫渣用途钢厂脱硫渣是指在钢铁生产中通过脱硫工艺处理后的副产品,主要由含硫物质和脱除硫的剩余物质组成。
钢厂脱硫渣具有多种用途,下面将详细介绍其中的一些。
1. 水泥生产:钢厂脱硫渣常用于水泥生产中作为原料。
脱硫渣中的硫酸钙(CaSO4)能够作为水泥生产过程中的矿物掺合料,用于调节水泥的物理和化学性能。
脱硫渣在水泥生产中的使用可以减少对天然资源的依赖,同时降低温室气体排放,具有较好的环境效益。
2. 建材制造:钢厂脱硫渣可以作为建材制造的一种原料。
通过适当的处理和加工,脱硫渣可以用于制造石膏板、石膏制品、建筑材料等。
这些制品具有优异的性能,如阻燃、隔热、隔音等,可以广泛应用于建筑行业,满足人们对于建筑材料高质量、环保、节能的需求。
3. 土壤改良剂:钢厂脱硫渣中的硫酸钙具有改良土壤的功能。
在农业生产中,脱硫渣可以用作土壤改良剂,用于调节土壤酸碱度,提供植物所需的养分,改善土壤结构,增加农作物产量。
同时,脱硫渣的使用还可以减轻地表水和地下水的酸化和污染,减小对环境的负面影响。
4. 硫化物制备:由于钢厂脱硫渣中含有一定比例的硫元素,可以回收利用这部分硫化物。
通过适当的方法处理和提取,可以从脱硫渣中提取硫化铁、硫化锰等物质,用于生产化肥、电池、磁性材料等。
这样可以实现对资源的回收和再利用,减少对原始矿物资源的开采和消耗。
5. 道路建设:钢厂脱硫渣可以用于道路建设中的路基填充材料。
脱硫渣具有一定的韧性和承载力,可以增加道路的稳定性和强度,同时能够减少对自然资源的开采和消耗。
将脱硫渣应用于道路建设中,不仅降低了成本,还减少了对石料等原材料的需求,具有一定的经济和环境效益。
总结起来,钢厂脱硫渣具有广泛的用途,可以应用于水泥生产、建材制造、土壤改良剂、硫化物制备以及道路建设等领域。
这些应用不仅能够实现对脱硫渣资源的合理利用和回收,还能够减少对自然资源的开采和环境的污染,具有较好的经济和环境效益。
随着钢铁行业的不断发展和技术的进步,对于钢厂脱硫渣的利用也将不断提升和完善,促进钢铁产业的可持续发展。
现代转炉炼钢脱硫工艺

现代转炉炼钢脱硫工艺摘要对转炉出钢渣洗脱硫进行了理论分析和工业试验。
结果表明:除温度外,转炉出钢渣洗脱硫的热力学和动力学条件均优于炉内脱硫。
在顶渣流动性良好的前提下,提高碱度和降低渣中w(FeO+MnO)有利于脱硫。
预熔型脱硫剂的脱硫效果优于机械混合型脱硫剂,其平均脱硫率达到51%。
关键词:炼钢转炉脱硫工艺发展现状AbstractTheoretical analysis and commercial experiment on BOF tapping desulphurization are described in this paper.The results show that the dynamic and thermodynamic factors of tapping desulphurization are better than those in the converter desulphurization,except for temperature conditions.When the slag has better fluidity,increasing slag basicity and decreasing w(Fe +MnO)in slag are beneficial to desulphurization.The desulphurization effect of pre-melted desulphurizer is higher than that of simply mixed one.Its desulphurization efficiency was reached by 51% 。
Key words steelmaking converter desulphurization craft1 钢液脱硫的基本原理1.1.1 钢液的脱硫主要是通过两种途径来实现,即炉渣脱硫和气化脱硫,根据熔渣的分子理论,碱性氧化渣与金属间的脱硫反应为:[S] + (CaO) == (CaS) + [O] ;[S] + (MnO) == (MnS) + [O];[S] + (MgO) == (MgS) + [O];根据熔渣的离子理论,脱硫反应可表示为:[S] + (O2-) == (S2-) + [O]的方式被除去,反应式可表示为:气化脱硫是指金属液中[S]以气态SO2}[S] +2[O] == { SO21.1.2 影响钢渣间脱硫反应的因素(1)碱度:提高碱度有利于脱硫,降低钢中含硫量。
吹炼过程中的脱磷和脱硫
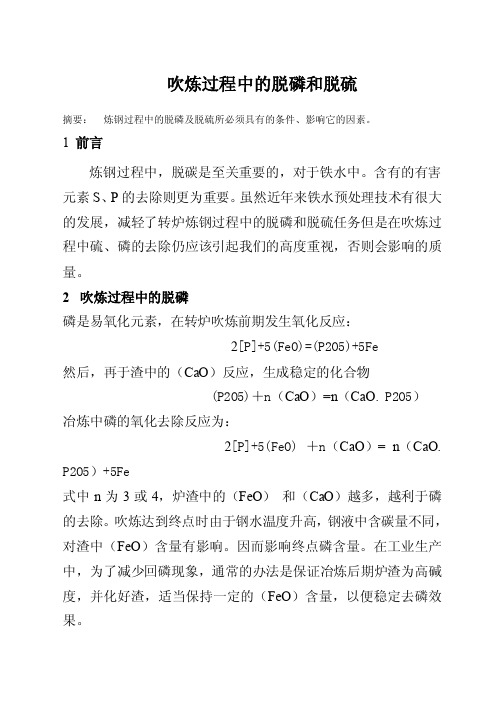
吹炼过程中的脱磷和脱硫摘要:炼钢过程中的脱磷及脱硫所必须具有的条件、影响它的因素。
1前言炼钢过程中,脱碳是至关重要的,对于铁水中。
含有的有害元素S、P的去除则更为重要。
虽然近年来铁水预处理技术有很大的发展,减轻了转炉炼钢过程中的脱磷和脱硫任务但是在吹炼过程中硫、磷的去除仍应该引起我们的高度重视,否则会影响的质量。
2吹炼过程中的脱磷磷是易氧化元素,在转炉吹炼前期发生氧化反应:2[P]+5(FeO)=(P2O5)+5Fe然后,再于渣中的(CaO)反应,生成稳定的化合物(P2O5)+n(CaO)=n(CaO. P2O5)冶炼中磷的氧化去除反应为:2[P]+5(FeO) +n(CaO)= n(CaO. P2O5)+5Fe式中n为3或4,炉渣中的(FeO)和(CaO)越多,越利于磷的去除。
吹炼达到终点时由于钢水温度升高,钢液中含碳量不同,对渣中(FeO)含量有影响。
因而影响终点磷含量。
在工业生产中,为了减少回磷现象,通常的办法是保证冶炼后期炉渣为高碱度,并化好渣,适当保持一定的(FeO)含量,以便稳定去磷效果。
为了去磷,吹炼过程中,应根据去磷的热力学条件,首先要搞好前期渣,尽快形成高氧化性的炉渣,以利于前期低温去磷。
而在吹炼后期要控制好炉渣碱度和渣中的(FeO),以利于后期高温、高碱度、高(FeO)脱磷。
当脱磷反应达到平衡时,用浓度来表示的平衡常数为:Kp= (P2O5)/[p]2(FeO)5(CaO)4常用磷在炉渣和金属中的分配比来表示脱磷能力,其表示方法很多。
常用L p=(P2O5)或Lp= (P2O5)/ [p].Lp越大,炼钢过程中脱磷能力也越大。
平衡常数和温度的关系:Lg=51875/T-33.16从脱磷反应的反应式、平衡常数及温度关系,可知影响脱磷的因素有:2.1炉渣碱度的影响。
由分配比公式可知:渣中的CaO越高,分配比越高,脱磷能力就越强。
CaO的脱磷作用在于:它能使P2O5生成稳定的磷酸钙。
炼钢的脱硫方法

炼钢的脱硫方法
炼钢的脱硫方法是炼钢工艺中的一个重要环节。
在炼钢过程中,铁水中的硫含量会对钢的性能产生不良影响,因此需要进行脱硫处理。
目前常用的炼钢脱硫方法有物理法、化学法和生物法。
物理法主要包括气体脱硫法和渣液脱硫法。
气体脱硫法是将含硫的铁水通过喷吹氧气的方式,使其与氧化剂反应,生成气体二氧化硫,达到脱硫的目的。
渣液脱硫法是将含硫铁水注入含有氧化剂的炉渣中,使其与氧化剂反应,生成气体二氧化硫和固体硫酸钙,达到脱硫的目的。
化学法主要包括碱性脱硫法和氧化剂脱硫法。
碱性脱硫法是将含硫铁水加入碱性溶液中,使其与氢氧化钙反应,生成气体二氧化硫和固体硫酸钙。
氧化剂脱硫法是将含硫铁水加入含有氧化剂的溶液中,使其与氧化剂反应,生成气体二氧化硫和固体硫酸钙。
生物法主要是利用微生物进行脱硫。
这种方法不仅能够有效脱除铁水中的硫,而且还能够将脱除的硫转化为硫酸盐,具有环保、经济的优点。
但是生物法的脱硫速度较慢,需要较长时间的处理。
综上所述,不同的脱硫方法各有优缺点,炼钢厂可以根据自身的生产需要和环保要求选择合适的脱硫方法。
- 1 -。
矿渣–钢渣–脱硫石膏基胶凝材料
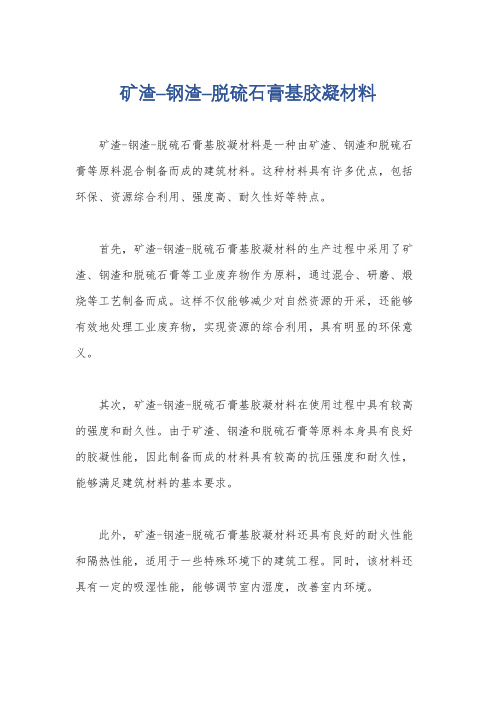
矿渣–钢渣–脱硫石膏基胶凝材料
矿渣-钢渣-脱硫石膏基胶凝材料是一种由矿渣、钢渣和脱硫石膏等原料混合制备而成的建筑材料。
这种材料具有许多优点,包括环保、资源综合利用、强度高、耐久性好等特点。
首先,矿渣-钢渣-脱硫石膏基胶凝材料的生产过程中采用了矿渣、钢渣和脱硫石膏等工业废弃物作为原料,通过混合、研磨、煅烧等工艺制备而成。
这样不仅能够减少对自然资源的开采,还能够有效地处理工业废弃物,实现资源的综合利用,具有明显的环保意义。
其次,矿渣-钢渣-脱硫石膏基胶凝材料在使用过程中具有较高的强度和耐久性。
由于矿渣、钢渣和脱硫石膏等原料本身具有良好的胶凝性能,因此制备而成的材料具有较高的抗压强度和耐久性,能够满足建筑材料的基本要求。
此外,矿渣-钢渣-脱硫石膏基胶凝材料还具有良好的耐火性能和隔热性能,适用于一些特殊环境下的建筑工程。
同时,该材料还具有一定的吸湿性能,能够调节室内湿度,改善室内环境。
总的来说,矿渣-钢渣-脱硫石膏基胶凝材料是一种具有广阔应用前景的新型建筑材料,其环保、资源综合利用、强度高、耐久性好等特点使其在建筑行业中备受关注。
希望未来能够进一步推广和应用,为建筑行业的可持续发展贡献力量。
科技成果——工业烟气钢渣法联合脱硫脱硝技术

科技成果——工业烟气钢渣法联合脱硫脱硝技术
技术开发单位
郑州中科新兴产业技术研究院、中国科学院过程工程研究所
适用范围
主要适用于钢铁、焦炭、水泥、玻璃等非电行业。
成果简介
该技术在钢渣法脱硫的基础上,开发了烟气臭氧氧化钢渣联合脱硫脱硝与尾渣资源化技术。
突破了强化吸收助剂开发、联合脱硫脱硝高效吸收塔设计、脱硫脱硝废水中硝酸盐分离提取与尾渣建材化/生态化利用等关键技术。
技术效果
该技术已开展千方级中试技术验证,结果表明,SO2脱除率>95%,NOx脱除率>70%,烟气污染物出口浓度满足国标特殊区域排放要求。
该技术实现了烟气中SO2和NOx在一塔中的同步脱除和钢渣的规模化协同处置,具有臭氧用量小、投资与运行成本低、无废水废渣排放、副产品效益高等优势,形成了以废治废、高效利用的循环经济型废气治理新模式。
应用情况
在小试试验基础上,中国科学院过程工程研究所与宁波太极环保设备有限公司(以下简称太极环保)合作,于太极环保厂区内建立了3000m3/h烟气钢渣法联合脱硫脱硝中试装置。
经过一个月的稳定运行,试验结果表明,整套装置运行良好,SO2脱除率达99%左右,NOx
脱除率达70%左右,出口烟气污染物浓度满足国标要求。
地址:宁波市慈溪市北三环西路。
市场前景
该技术进一步可以推广至玻璃、水泥、工业锅炉、垃圾焚烧炉、陶瓷窑炉、石化催化裂化烟气、化工烟气等行业,支撑这些行业对脱硫脱硝技术的迫切需求,整个市场容量保守估计超过2000亿元。
钢渣、高炉渣烟气脱硫技术介绍

邯钢 42~54
3~8 12~20
2~6 4~18 2.5~13 1~2 0.2~1.3 2~10
钢渣由这些金属和非金属氧化物(CaO、 FeO、SiO2、MgO)等构成矿物,构成的矿 物主要有:
硅酸二钙(2CaO·SiO2) 硅酸三钙(3CaO·SiO2) 钙镁橄榄石(CaO·MgO·SiO2) 镁蔷薇辉石(3CaO·MgO·2SiO2) 钙铝黄长石(2CaO·Al2O3·SiO2) 铁酸钙(CaO·FeO) 及RO相等。 这些矿物组成取决于钢渣的的化学成 分。不同碱度转炉钢渣的矿物组成如表2 所列。
第一阶段,反应的前6个小时。新鲜的 钢渣浆液的pH值由13降到6.5,在前3个小 吋内,pH值迅速由13降到7,然后缓慢降 至6.5。
第二阶段,随后24个小时。SO2继续 溶于水中,钢渣浆液pH值下降至6~6.5。
第三阶段,最后5个小时。 SO2继续溶 于水中,钢渣浆液pH值下降至4以下。
2、主要技术指标
(3CaO SiO2 +3SO32- 3CaSO3+SiO2
(6
CaSO3+ -12O2 CaSO4
=
(7
MgSO3+ -12O2 MgSO4
=
(8
..
.
=(
(3CaO MgO 4SiO2 +4SO42- 3CaSO4+MgSO4+4SiO2
(9
=(
(3CaO SiO2 +3SO42- 3CaSO4+SiO2
除雾
吸收后浆液
中和 中和剂
中和后浆液
过滤
滤液
滤饼
图1“炉渣”吸收烟气中SO2 工艺流程示意图
钢渣脱硫案例分析报告
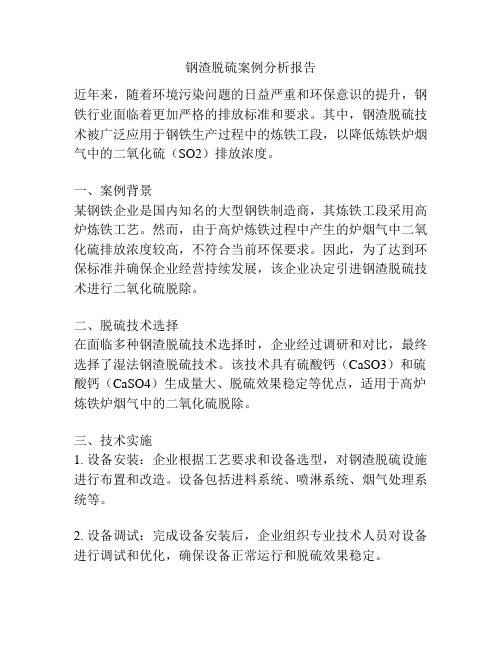
钢渣脱硫案例分析报告近年来,随着环境污染问题的日益严重和环保意识的提升,钢铁行业面临着更加严格的排放标准和要求。
其中,钢渣脱硫技术被广泛应用于钢铁生产过程中的炼铁工段,以降低炼铁炉烟气中的二氧化硫(SO2)排放浓度。
一、案例背景某钢铁企业是国内知名的大型钢铁制造商,其炼铁工段采用高炉炼铁工艺。
然而,由于高炉炼铁过程中产生的炉烟气中二氧化硫排放浓度较高,不符合当前环保要求。
因此,为了达到环保标准并确保企业经营持续发展,该企业决定引进钢渣脱硫技术进行二氧化硫脱除。
二、脱硫技术选择在面临多种钢渣脱硫技术选择时,企业经过调研和对比,最终选择了湿法钢渣脱硫技术。
该技术具有硫酸钙(CaSO3)和硫酸钙(CaSO4)生成量大、脱硫效果稳定等优点,适用于高炉炼铁炉烟气中的二氧化硫脱除。
三、技术实施1. 设备安装:企业根据工艺要求和设备选型,对钢渣脱硫设施进行布置和改造。
设备包括进料系统、喷淋系统、烟气处理系统等。
2. 设备调试:完成设备安装后,企业组织专业技术人员对设备进行调试和优化,确保设备正常运行和脱硫效果稳定。
3. 操作培训:为了确保设备正常运维和操作过程中的安全性,企业对操作人员进行培训,包括设备操作、维护和故障处理等内容。
四、效果评价1. 二氧化硫排放浓度:企业在钢渣脱硫设备投入运行后,通过在线监测系统对炉烟气中的二氧化硫浓度进行实时监测。
结果显示,二氧化硫排放浓度从原先的超过国家排放标准的数十毫克/立方米降至几毫克/立方米以下,大幅度减少了二氧化硫对环境的污染。
2. 设备运行稳定性:经过一段时间的运行,企业的钢渣脱硫设备运行稳定,连续运行时间逐渐增加,设备故障和停机时间明显减少,有效提高了钢铁生产的连续性和生产效率。
3. 脱硫剂消耗情况:脱硫剂消耗量作为评价钢渣脱硫技术效果的重要指标之一。
通过进行脱硫剂消耗的核算和分析,企业发现采用湿法钢渣脱硫技术后,不仅可以有效降低炉烟气中的二氧化硫浓度,还能显著减少脱硫剂的消耗量,实现了成本的降低。
炼钢脱硫工艺流程

炼钢脱硫工艺流程
《炼钢脱硫工艺流程》
炼钢脱硫是钢铁生产过程中非常重要的环节,其主要任务是将炼钢过程中产生的硫等有害元素去除,以提高钢的质量和性能。
炼钢脱硫工艺流程包括氧气顶吹法、转炉脱硫法、加料喷吹法等多种方法。
氧气顶吹法是炼钢脱硫的最常用方法之一。
在这种工艺中,先将熔炼的炉料表面到氧气,通过氧气的吹入,炉内的硫等有害元素就能与氧气反应生成气体,进而从炉料中移除。
这种方法操作简单,效果好,因此被广泛应用。
另一种常见的炼钢脱硫方法是转炉脱硫法。
这种方法主要是通过废气逆掺熔剂、脱硫剂等物料,来达到脱硫的目的。
在操作上需要注意熔炼温度、熔化度等因素,以确保脱硫效果。
加料喷吹法是近年来发展起来的一种新型脱硫工艺。
在这种方法中,通过将加料与气体一起喷入炉内,使得炉内的炼钢过程受到加料的影响,从而实现脱硫的目的。
这种方法具有脱硫效果好、设备投资低等特点,因此备受青睐。
总的来说,炼钢脱硫工艺流程涉及多种方法,通过不同的操作手段和技术设备,可以达到去除炼钢过程中产生的有害元素的目的。
随着科技的不断发展,相信炼钢脱硫工艺流程会越来越完善,为钢铁行业的发展做出更大的贡献。
基于湿法脱硫技术的钢渣脱硫剂性能研究的开题报告
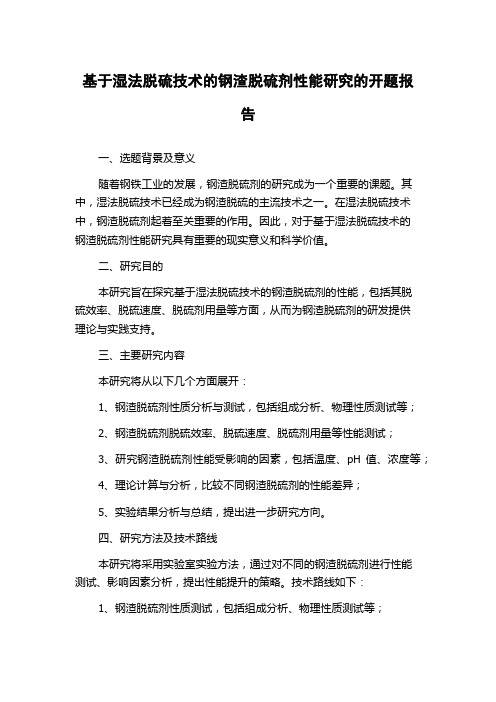
基于湿法脱硫技术的钢渣脱硫剂性能研究的开题报告一、选题背景及意义随着钢铁工业的发展,钢渣脱硫剂的研究成为一个重要的课题。
其中,湿法脱硫技术已经成为钢渣脱硫的主流技术之一。
在湿法脱硫技术中,钢渣脱硫剂起着至关重要的作用。
因此,对于基于湿法脱硫技术的钢渣脱硫剂性能研究具有重要的现实意义和科学价值。
二、研究目的本研究旨在探究基于湿法脱硫技术的钢渣脱硫剂的性能,包括其脱硫效率、脱硫速度、脱硫剂用量等方面,从而为钢渣脱硫剂的研发提供理论与实践支持。
三、主要研究内容本研究将从以下几个方面展开:1、钢渣脱硫剂性质分析与测试,包括组成分析、物理性质测试等;2、钢渣脱硫剂脱硫效率、脱硫速度、脱硫剂用量等性能测试;3、研究钢渣脱硫剂性能受影响的因素,包括温度、pH值、浓度等;4、理论计算与分析,比较不同钢渣脱硫剂的性能差异;5、实验结果分析与总结,提出进一步研究方向。
四、研究方法及技术路线本研究将采用实验室实验方法,通过对不同的钢渣脱硫剂进行性能测试、影响因素分析,提出性能提升的策略。
技术路线如下:1、钢渣脱硫剂性质测试,包括组成分析、物理性质测试等;2、制备脱硫实验样品;3、对实验样品进行脱硫实验,测定脱硫效率、脱硫速度和脱硫剂用量等性能;4、研究不同因素对脱硫剂性能的影响;5、理论模拟与分析,比较不同钢渣脱硫剂的性能差异;6、实验结果分析与总结,提出进一步研究方向。
五、预期成果本研究预期成果包括:1、多种钢渣脱硫剂的性能测试数据,包括脱硫效率、脱硫速度、脱硫剂用量等方面;2、不同因素对钢渣脱硫剂性能的影响分析;3、钢渣脱硫剂性能的理论模拟与分析结果;4、对钢渣脱硫剂研发的启示和指导性建议。
六、研究进度安排本研究预计周期为一年,具体进度安排如下:1、前期调研与文献综述:1个月;2、钢渣脱硫剂性质分析与测试:2个月;3、脱硫性能测试:4个月;4、影响因素分析与理论计算:2个月;5、结果分析与论文撰写:3个月。
七、参考文献1. 钢渣脱硫剂的性能与应用研究[D]. 湖南科技大学, 2018.2. 王某某, 罗某某. 钢渣脱硫剂研究进展[J]. 钢铁, 2016, 51(9): 1-7.3. 侯某某, 李某某, 魏某某. 钢渣脱硫剂的研究进展[J]. 钢铁科学技术, 2014, 26(4): 56-61.4. 朱某某, 张某某. 新型钢渣脱硫剂的研发与应用[J]. 工业黄页, 2019(10): 156-159.。
基于湿法脱硫的钢渣脱硫研究初探
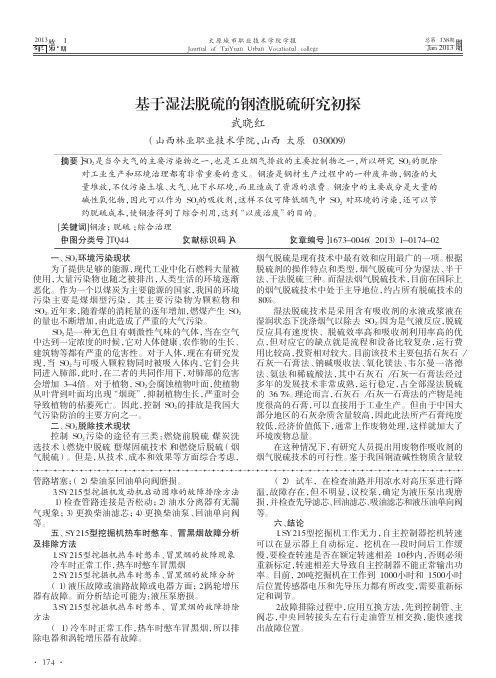
管路堵塞;(2)柴油泵回油单向阀磨损。
3.SY215型挖掘机发动机启动困难的故障排除方法1)检查管路连接是否松动;2)油水分离器有无漏气现象;3)更换柴油滤芯;4)更换柴油泵、回油单向阀等。
五、SY215型挖掘机热车时憋车、冒黑烟故障分析及排除方法1.SY215型挖掘机热车时憋车、冒黑烟的故障现象冷车时正常工作,热车时憋车冒黑烟2.SY215型挖掘机热车时憋车、冒黑烟的故障分析(1)液压故障或油路故障或电器方面;2)涡轮增压器有故障。
而分析结论可能为:液压泵磨损。
3.SY215型挖掘机热车时憋车、冒黑烟的故障排除方法(1)冷车时正常工作,热车时憋车冒黑烟,所以排除电器和涡轮增压器有故障。
(2)试车,在检查油路并用凉水对高压泵进行降温,故障存在,但不明显,议校泵,确定为液压泵出现磨损,并检查先导滤芯、回油滤芯、吸油滤芯和液压油单向阀等。
六、结论1.SY215型挖掘机工作无力,自主控制器挖机转速可以在显示器上自动标定,挖机在一段时间后工作缓慢,要检查转速是否在额定转速相差10秒内,否则必须重新标定,转速相差大导致自主控制器不能正常输出功率。
目前,20吨挖掘机在工作到1000小时和1500小时后位置传感器电压和先导压力都有所改变,需要重新标定和调节。
2.故障排除过程中,应用互换方法,先到控制管、主阀芯,中央回转接头左右行走油管互相交换,能快速找出故障位置。
·················································2013年第·1期太原城市职业技术学院学报Journal of TaiYuan Urban Vocational college期总第138期Jan2013[摘要]SO2是当今大气的主要污染物之一,也是工业烟气排放的主要控制物之一,所以研究SO2的脱除对工业生产和环境治理都有非常重要的意义。
炼钢脱硫反应

炼钢脱硫反应一、介绍钢铁是重要的工业材料,广泛应用于建筑、汽车制造等行业。
然而,在钢铁制造过程中,炼钢焦炭和铁矿石的还原反应会产生大量的硫化物,如二硫化碳、硫化氢等,这些硫化物会对环境和人体健康造成严重危害。
因此,进行炼钢脱硫反应是非常重要的环保措施。
二、脱硫反应原理炼钢脱硫反应的原理主要是通过化学反应将钢中的硫化物转化为易挥发的硫酸气体或其他化合物,从而实现硫的去除。
常用的炼钢脱硫方法有以下几种:2.1 碱性脱硫法碱性脱硫法主要是通过将碱性物质加入到炼钢过程中,与钢中的硫化物反应生成易溶于钢水中的硫化物,然后再通过钢水的翻搅或其他方式将钢水中的硫化物带出。
常用的碱性脱硫剂有生石灰、氨水等。
2.2 氧化性脱硫法氧化性脱硫法是通过将氧化剂加入到炼钢过程中,将钢中的硫化物氧化成易挥发的二氧化硫气体,从而实现硫的去除。
常用的氧化剂有石灰石、氧气等。
2.3 脱磷脱硫一体化技术脱磷脱硫一体化技术是将脱磷反应和脱硫反应同时进行,通过添加适量的添加剂,使钢中的磷和硫同时被去除。
这种技术可以减少工艺步骤,提高效率。
2.4 脱硫渣处理脱硫渣处理是将脱硫剂加入到钢水中,与钢中的硫反应生成硫化物,然后通过渣化反应,将硫化物转化为易分离的硫化渣。
这种方法可以有效地去除钢中的硫。
三、炼钢脱硫反应的应用与发展炼钢脱硫反应在钢铁制造中得到了广泛的应用,并且随着环境保护要求的提高,脱硫技术也在不断地发展。
3.1 应用领域炼钢脱硫反应主要应用于钢铁冶炼过程中,可以有效去除钢中的硫,提高钢的品质。
同时,炼钢脱硫反应也可以减少对环境的污染,改善工作环境。
3.2 技术发展随着科学技术的不断发展,炼钢脱硫反应的技术也在不断地改进和完善。
新型的脱硫剂和脱硫装置不断涌现,使得炼钢脱硫反应更加高效、安全、环保。
四、炼钢脱硫反应的挑战与展望尽管炼钢脱硫反应取得了显著的进展,但仍面临一些挑战。
4.1 高硫矿石的处理随着矿石资源的日益减少,高硫矿石的使用比例也在增加。
钢铁制造流程脱硫工艺

钢铁制造流程脱硫工艺引言随着工业的发展,钢铁制造产生了大量的废气和废水,其中含有大量的二氧化硫(SO2)。
二氧化硫是一种有害气体,对环境和人类健康造成了巨大的危害。
为了减少二氧化硫的排放,钢铁制造过程中引入了脱硫工艺。
本文将介绍钢铁制造流程中主要的脱硫工艺及其原理。
1. 石灰石脱硫工艺石灰石脱硫是一种常见的钢铁制造过程脱硫工艺,它主要通过反应碱性氧化物与二氧化硫进行化学反应,使硫化物转化为较稳定的硫酸盐。
具体工艺步骤如下:1.加入石灰石石粉:将石灰石石粉加入脱硫设备的喷射器中。
2.喷射器喷射:利用喷射器将石灰石石粉喷入反应器,与废气中的二氧化硫发生反应。
3.反应:石灰石石粉中的碱性氧化物与二氧化硫发生反应,生成硫化物。
4.氧化:通过加入适量的氧气或空气,将硫化物氧化为硫酸盐。
5.除尘:将除尘器中产生的硫酸盐进行集中处理。
6.脱水:对硫酸盐进行脱水处理,形成固体硫酸盐产品。
7.再生:通过加热脱水后的硫酸盐,使其分解为二氧化硫和石灰石。
石灰石脱硫工艺具有工艺简单、成本低廉的特点,是钢铁制造中常用的脱硫工艺。
2. 氨法脱硫工艺氨法脱硫是另一种常见的钢铁制造过程脱硫工艺,它主要通过二氧化硫与氨气的反应,生成较稳定的硫酸铵。
具体工艺步骤如下:1.加入氨气:将氨气加入脱硫设备的喷射器中。
2.喷射器喷射:利用喷射器将氨气喷入反应器,与废气中的二氧化硫发生反应。
3.反应:二氧化硫与氨气在反应器中进行反应,生成硫酸铵。
4.除尘:将除尘器中产生的硫酸铵进行集中处理。
5.干燥:对硫酸铵进行干燥处理,形成固体硫酸铵产品。
6.再生:通过加热干燥后的硫酸铵,使其分解为二氧化硫和氨气。
氨法脱硫工艺具有高效、脱硫效果好的特点,但成本较高,需要处理产生的废液。
3. 湿法脱硫工艺湿法脱硫是采用吸收剂将二氧化硫吸收至溶液中,通过化学反应转化为硫酸盐或硫酸铵。
湿法脱硫工艺主要包括氧化吸收和还原吸收两个过程:3.1 氧化吸收1.加入吸收剂:将吸收剂加入脱硫设备中的吸收塔。
炼钢脱硫条件

炼钢过程中脱硫主要在转炉、电炉以及LF(钢包精炼炉)等设备中进行,其条件主要包括:
1. 温度:脱硫反应通常在较高的温度下进行,因为高温有利于硫化物的溶解和扩散。
在转炉冶炼阶段,一般要求温度保持在约1600℃以上;在LF精炼时,温度范围可能在1450℃至1700℃之间。
2. 碱度:炉渣的碱度是影响脱硫效果的重要因素。
高碱度渣能够提供更多的氧离子,与硫形成稳定的硫酸盐从而从钢液中去除硫。
常用的脱硫剂如石灰石(CaCO3)、白云石(CaMg(CO3)2)、镁砂(MgO)等可以提高炉渣的碱度。
3. 炉渣流动性及粘度:良好的炉渣流动性有助于增强硫化物与炉渣之间的接触和化学反应速率,降低粘度可增加传质效率,因此选择适当的助熔剂以维持适宜的炉渣性能是重要的脱硫条件之一。
4. 脱硫剂添加:通过向炉内添加专门的脱硫剂,如镁基合金(如FeMnSiAl)、钙基合金(如CaSi)或直接加入含钙、镁元素的材料,来增加脱硫能力。
5. 搅拌作用:通过吹氩等方式加强钢水与炉渣的混合,提高硫化物与炉渣反应界面处的浓度梯度,促进脱硫反应的进行。
6. 时间控制:脱硫是一个动态过程,需要适当的时间保证硫充分转化为炉渣中的硫酸盐并排出。
综上所述,炼钢脱硫的条件需综合考虑温度、碱度、炉渣性质、脱硫剂使用以及工艺操作等多个方面,确保高效、经济地完成脱硫工序,达到钢材所需的低硫含量目标。
- 1、下载文档前请自行甄别文档内容的完整性,平台不提供额外的编辑、内容补充、找答案等附加服务。
- 2、"仅部分预览"的文档,不可在线预览部分如存在完整性等问题,可反馈申请退款(可完整预览的文档不适用该条件!)。
- 3、如文档侵犯您的权益,请联系客服反馈,我们会尽快为您处理(人工客服工作时间:9:00-18:30)。
脱硫副产物处理系统流程图
(4) 控制系统
脱硫控制系统在设计上采用分散控制、集中管理, 整个系统结构紧凑、技术先进、适应性强、经济合理、
可靠性高、可操作和可维护性好。
控制系统流程图
四、钢渣脱硫实验研究及可行 性分析
钢渣法脱硫实验研究结果
钢渣和CaCO3作为脱硫剂的比较
(1)脱硫效率随PH值的变化
我国部分钢厂转炉钢渣的化学成分(%)
厂名 首钢 本钢 唐钢 太钢 SiO2 Fe2O3 Al2O3 CaO 14.9 16.0 15.4 14.2 10.4 12.3 12.7 8.8 3.9 3.0 2.5 2.9 44.0 40.5 40.3 47.8 MgO 10.0 9.2 9.1 9.3 FeO 13.3 7.3 14.1 13.3 MnO P2O5 f-CaO 碱度 1.1 1.3 1.9 1.1 1.3 0.6 1.1 0.6 1.8 2.8 1.8 1.6 2.7 2.5 2.5 3.1
典型烧结烟气脱硫技术优缺点
(3) 循环流化床法
优势:该法占地面积小、耗水量小、无腐蚀,不需要废 水处理、脱硫剂容易获得、投资费用较低。 劣势:脱硫效率较低,运行不稳定,副产物不易利用。
(4) 活性炭法
优势:占地面积小、副产物可利用、不产生二次污染。
缺势:不适合低浓度含硫烟气,投资及运行费用高。
烧结烟气脱硫的主要技术难题
100% 95%
90% 85% 80% 75% 70%
65% 60% 55% 4 5 6 7 8 9 10 11 12 13 钢渣 CaCO3
钢渣法脱硫实验研究结果
钢渣和CaCO3作为脱硫剂的比较
(2)排放浓度随时间变化
600 550 500 450 400 350 300 250 钢渣 CaCO3
国内外烧结烟气脱硫技术发展现状及趋势
国外烧结烟气脱硫技术起步较早,经过几十年的发
展,脱硫技术已日趋成熟。从脱硫工艺来看,湿法、半 干法、干法都有成功的业绩,其中应用最成熟的是石灰 石—石膏法。近年来,日本已率先开始应用钢渣作为脱 硫剂的研究,并已取得一定成果。 我国钢铁企业烧结烟气脱硫的研究和应用起步较晚 ,2005年才开始进行烧结烟气脱硫工作。据不完全统计
量都很低,此时接近于清水吸收。其主要反应
如下: SO2+H2O → H2SO3 H2SO3 ↔ H++HSO3−↔2H++SO32-
(3) 中间稳定阶段
pH值越来越低,Fe2+、Fe3+不断生成,此阶段反应的 活性组分以FeO、Fe2O3为主,其主要可能的反应如下:
FeO+2H+ ↔ Fe2++H2O Fe2O3+6H+ ↔ 2Fe3+ +3H2O Fe2+、Fe3+与溶于水中的SO32-、O2等发生一系列反应。 Fe2+ + SO32- ↔ FeSO3 2 Fe3+ + 3SO32- ↔ Fe2(SO3)3 FeSO3+1/2O2 ↔ FeSO4 Fe2(SO3)3+3/2O2 ↔ Fe2(SO4)3 2FeSO4+SO2 +O2↔ Fe2(SO4)3 Fe2(SO4)3+SO2 +2H2O↔ 2FeSO4+2H2SO4 此过程中,Fe2+、Fe3+的溶出是控制关键。
马钢
鞍钢 南钢 韶钢
11.5
15.4 17.2 18.4
6.5
10.7 7.4 7.5
2.1
2.4 1.5 3.0
41.3
39.3 40.1 40.8
7.3
11.0 8.8 3.1
15.8
16.5 16.9 15.5
1.8
1.3 2.0 5.4
1.1
0.7 1.5 1.3
12.8
2.0 4.3 8.6
,目前已建和在建的烧结烟气脱硫装置约150余台套。
典型烧结烟气脱硫技术优缺点
(1) 石灰-石膏法
优势:脱硫效率高(90-95%),系统稳定可靠,脱硫 剂价格便宜。 不足:占地面积大,投资及运行费用高,副产物脱硫 石膏应用途径有待进一步拓宽。
(2) 氨-硫酸铵法
优势:反应速度快,吸收剂利用效率高,系统助力小, 占地面积相对较小。 不足:氨易挥发,易溢出,形成二次污染并存在安全 隐患;脱硫生成物硫铵质量差,难以资源化利用。
含有重金属、二噁英等。
这些特点都在一定程度上增加了烧结烟气二氧化硫 治理的难度。
烧结烟气脱硫的主要技术难题
(3)投资和运行费用高
投资方面:烧结烟气脱硫设施投资占烧结机总投资 的20%~30%,每个烧结脱硫项目的投资金额从2000
万~2亿元不等,主要影响因素有烧结机面积大小、现场
条件和脱硫技术的选择等。从国内已实施建设的太钢、 石钢、柳钢、济钢和郉钢等几个项目的情况看,项目造 价在4000万~8000万元之间。烧结烟气脱硫的运行费用 也很高,国家又未出台相应的补助政策,巨大的费用支 出是多年来烧结烟气脱硫不能有效开展的重要因素之一。钢渣法烧结烟气脱硫技术 Nhomakorabea张
凡
内
容
一、钢铁行业二氧化硫污染与控制现状
二、钢渣特性及脱硫机理
三、钢渣法烧结烟气脱硫装置工艺流程 四、钢渣脱硫实验研究及可行性分析 五、成果
一、钢铁行业二氧化硫污染
与控制现状
我国钢铁行业二氧化硫污染状况
我国重点钢铁企业二氧化硫排放量约175万吨, 约占全国工业二氧化硫工业排放量的8.8%,位居 全国工业二氧化硫排放总量笫三位。烧结工序排放 的二氧化硫约占钢铁生产总排放量的70%以上,是 钢铁行业实现二氧化硫污染减排的关键也是政府和 企业关注的减排热点和难点。
统、(4)烟气系统及控制系统。系统工艺流程图如
下:
钢渣法烧结烟气脱硫装置工艺流程图
(1)钢渣吸收剂制备系统
钢渣经“破碎—筛分—磁选、破碎—湿磨—磁选、
钢铁渣超细磨”等工艺条件,其粒度要达到较大的比 表面积的同时,其吸收二氧化硫的残渣与水泥添加剂
的粒度相匹配。流程图如下图:
钢渣制备工艺流程图
(2) 吸收塔系统
独有的滤泡发生器会在塔内产生大量的细密气泡, 使气液两相得以充分接触,烟气同时被浆液冷却并达到 饱和,烟气中的SO2等成分被吸收;再流经两层锯齿形 除雾器后除去所含雾滴;经洗涤和净化的烟气流出吸收 塔,通过净烟道进入烟囱排放。
吸收塔系统流程图
(3) 脱硫副产物处理系统
本系统改善了烟气中的微粒与液体的接触条件, 可以达到很高去除效率。脱硫后产生的残渣,很容易 进行脱水。脱硫残渣可直接制成高品质的水泥,也可 作为盐碱地的土壤改良剂,实现以废治废、变废为宝, 有力降低了烧结烟气的脱硫成本。
钢渣法脱硫主要优势:
1)具有较强的碱性可,作为脱硫剂用于处理烧结机 含SO2烟气;
2)钢渣中含有一定量的氧化性金属化合物,对于脱
硫副产物的氧化十分有利:
3)钢渣目前尚无其他用途,属于极其廉价的脱硫
剂,可大幅度降低烧结机烟气脱硫的运行费用; 4)钢渣磨制后为脱硫后副产物的资源化利用奠定了 基础; 5)废渣的综合利用符合国家的产业政策。
(2)烧结烟气的特殊性
◎ 风量变化大,幅度高达40%以上。
◎ SO2浓度变化大,400mg/Nm3~5000mg/Nm3 。
◎ 温度变化大,一般为80℃~180℃。 ◎ 水分含量大且不稳定,一般为10%~13%。 ◎ 含氧量高,一般为15%~18%。 ◎ 含有多种污染成分,除含有二氧化硫、粉尘外,还
(1) 初始阶段
由于pH值较高(一般为9左右),钢渣中的 活性组分以CaO为主,可能还有一些如MgO 之类的活性金属氧化物,但是Fe的氧化物基 本不会溶解。此阶段的反应机理与石灰石—石
膏法类似,其化学反应机理具体可参阅石灰
石—石膏法脱硫的相关文献。
(2) 过渡阶段
钢渣中的CaO已接近反应完全,pH值降 低到Fe2+、Fe3+开始溶出,但这些活性组分含
3.3
2.4 2.2 2.1
钢渣脱硫机理
钢渣中含有40%~50%的氧化钙,利用钢渣 浆液为脱硫吸收剂与直接利用CaO或者CaCO3, 非常相似,但钢渣法也有与之不同的地方,钢渣中
含有的大量金属氧化物对其湿法脱硫的整个过程起
到重要作用,不容忽视。
利用钢渣为吸收剂湿法脱硫可分为四个过程:
初始阶段、过渡阶段、中间稳定阶段和结束阶段。
(4) 结束阶段
此时活性组分基本耗尽,以水的物理吸
收为主,其机理可参考第二阶段。
三、钢渣法烧结烟气脱硫装置 工艺流程
钢渣法烧结烟气脱硫装置工艺流程
钢渣法是一种类似于石灰石-石膏法的湿法脱硫
工艺,二者在流程设置上也比较相似。钢渣湿法脱
硫装置主要包括(1)钢渣吸收剂(钢渣浆液)制备
系统、( 2 )吸收塔系统、( 3 )脱硫副产物处理系
钢渣的特性
钢渣是钢铁生产过程中排出的固体废弃物。由
于各个企业采用的工艺、原料、炉型等各有区别,
其产生的钢渣成分也各不相同。一般而言,钢渣的
主要成分是硅、钙、铁等的氧化物,其矿物相主要
为硅酸三钙(C3S)、硅酸二钙(C2S)等,总量在
50%以上。
钢渣的特性
钢渣经过处理,消除因 f-CaO 引起的膨胀崩坏等
二、钢渣特性及脱硫机理
钢渣利用现状
目前我国钢渣堆积量达4亿吨,据保守估算每
年钢渣产生量约7500万吨,目前我国钢渣利用率不
足10%,已成为制约我国钢铁行业可持续发展的瓶
颈之一。
目前,钢渣的综合利用方向主要有回收废钢、
水泥、筑路材料及农业生产等几个方面,但钢渣的
成分波动大和硬度较大难磨的特点使其利用率不高。