第六章生产与运作管理生产作业排序文档
生产作业计划与作业排序
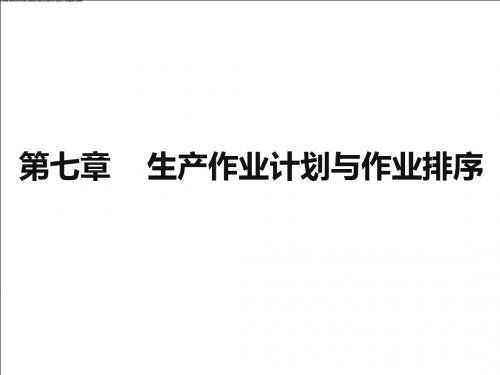
2/19/2019
THANK YOU
2/19/2019
2/19/2019
(三)生产提前期:产品(毛坯、零部件)在各个工艺阶
段出产或投入的日期比成品出产的日期应提前的时间。 1、投入提前期:各车间投入日期比成品出产日期应提前的 时间。公式=车间出产提前期+车间的生产周期。 2、出产提前期: 公式:当前后工序车间的生产间隔相等 车间出产提前期=车间投入提前期+车间保险期 当前后工序车间的生产间隔不相等 前车间出产提前期=后车间投入提前期+前车间的保 险期+ | 前车间生产间隔期-后车间生产间隔期 |
3、进行生产能力核算与平衡 4、检查生产作业准备 5、生产作业控制
2/19/2019
(二)生产作业计划的目标
1、保证生产计划任务能够按质、按量、按期、按品 种完成。
2、尽可能实现均衡生产,建立良好的生产秩序,提 高效率。
2/19/2019
二、大量大批生产作业计划
(一) 大量大批生产作业计划 1、节拍 节拍是流水线上相邻两件相同制品投产或出产的时 间间隔,它表明了流水线生产速度的快慢或生产效率的 高低。是大量流水生产期量标准中最基本的标准。 流水线节拍的计算公式:R=F/N 其中:R—流水线的节拍(分/件),F—计划期内有 效工作时间(分),N—计划期的产品产量(件)。
2/19/2019
平行顺序移动方式:保证各工序的加工时间不间断的条件 下,随时传送零件。 优点:劳动过程中断时间比顺序移动方式少,零件生产周 期较短。在一定程度上消除了工人与设备的空闲时间,使 工人和设备的空闲时间集中起来,便于用来做其他工作。 缺点:组织安排比较复杂 公式:
2/19/2019
1、单件小批生产类型及工艺专业化的生产单位宜 采用顺序移动方式; 2、大量大批生产类型及对象专业化的生产单位, 宜采用平行移动方式或平行顺序移动方式; 3、零件体积小、重量轻、工序劳动量小和单位加 工时间短的宜采用顺序移动方式; 4、零件体积大、重量重和单件加工时间长的宜采 用平行移动方式或平行顺序移动方式; 5、紧急件、关键件宜采用平行移动方式。
生产作业计划与作业排序共42页
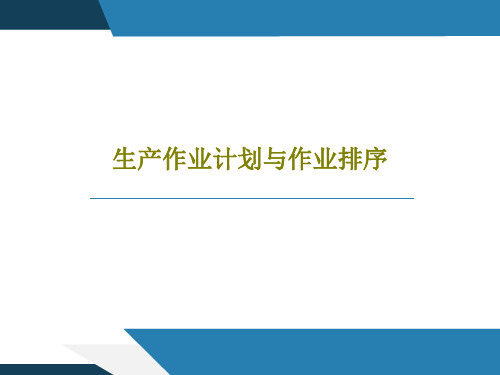
▪
26、要使整个人生都过得舒适、愉快,这是不可能的,因为人类必须具备一种能应付逆境的态度。——卢梭
▪
27、只有把抱怨环境的心情,化为上进的力量,才是成功的保证。——罗曼·罗兰
▪
28、知之者不如好之者,好之者不如乐之者。——孔子
▪
29、勇猛、大胆和坚定的决心能够抵得上武一个强壮的盲人,倚靠在明眼的跛子肩上。——叔本华
谢谢!
42
生产作业计划与作业排序
1、纪律是管理关系的形式。——阿法 纳西耶 夫 2、改革如果不讲纪律,就难以成功。
3、道德行为训练,不是通过语言影响 ,而是 让儿童 练习良 好道德 行为, 克服懒 惰、轻 率、不 守纪律 、颓废 等不良 行为。 4、学校没有纪律便如磨房里没有水。 ——夸 美纽斯
5、教导儿童服从真理、服从集体,养 成儿童 自觉的 纪律性 ,这是 儿童道 德教育 最重要 的部分 。—— 陈鹤琴
生产作业计划与排序概念
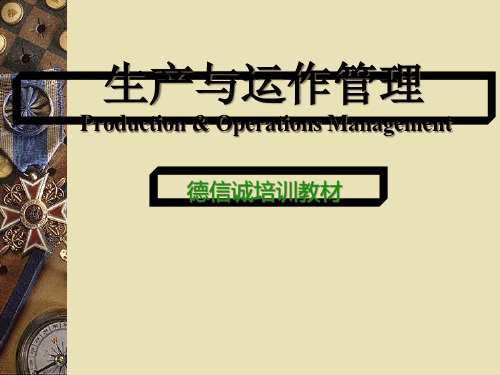
第六讲 生产作业计划与排序
一、基本概念 二、最长流程时间 三、n/2/F/Fmax问题的算法 四、n/m/P/ Fmax问题的启发式算法 五、单件车间排序问题
第七讲 工程项目计划与进度控制
一、工程项目管理的目标、内容 二、网络图 三、网络时间参数的计算 四、工程项目按期完成的概率分析 五、网络计划的优化
生产的概念
1)产品制造工艺(工艺流程) 改变加工对象的形状、尺寸、状态
及材料的化学性能,使之具有使用价 值的产品加工顺序过程。它是根据产 品结构设计,由粗到细,分层次制定 加工的工艺阶段和工序。
生产的概念
工艺流程划分成工艺阶段:
毛坯—零件—部件—产品
工艺阶段划分成工序:
毛坯——铸、锻、下料、焊接 机加工——车、钻、铣、铇、磨
2、Our destiny offers not only the cup of despair, but the chalice of opportunity. (Richard Nixon, American President )命运给予我们的不是失望之酒,而是机会之杯。二〇二一年五月二十六日2021年5月26 日星期三
生产与运作管理
Production & Operations Management
课程内容
•生产与运作管理的基本概念 •生产系统运行管理的基本理论与方法 (计划、组织与控制) •现代生产管理思想与方法(CIMS、 MRPII/ERP、JIT、OPT、LP、 AM 、 BPR)
第一讲 生产管理的基本概念
5、You have to believe in yourself. That's the secret of success. ----Charles Chaplin人必须相信自己,这是成功的秘诀。-Wednesday, May 26, 2021May 21Wednesday, May 26, 20215/26/2021
作业排序管理 ppt课件

作业排序管理
例12-1
生产任务编 J1
J2
J3
J4
J5
J6
号Ji
加工时间ti
4
8
2
5
9
3
(天)
预定交货期 24 23
8
di (天)
6 32 13
作业排序管理
• 加工顺序为: J3 —J6 —J1 —J4 —J2 —J5
生产任务编 J3
J6
J1
J4
作业排序管理
⑴ FCFS规则:优先选择最早到达的工件。 ⑵ SPT规则:优先选择加工时间最短的工件。 ⑶ EDD规则:优先选择交货期最短的工件。 ⑷ SCR:优先选择临界比最小的工件。临界比
为工件允许停留时间和工件余下加工时间之比。 ⑸ MWKR规则:优先选择余下加工时间最长的
工件。 ⑹ LWKR规则:优先选择余下加工时间最短的工
生产任务编 J4
J3
J6
J2
J1
J5
号Ji
完成时间Ci
5
(天)
7 10 18 22 31
交货延期量 0
0
0
0
0
0
Li (天)
最大延期量和平均延期量均为零,而平均流程时间为:
F 1 6i 6 1F i1 65 7 1 0 1 8 2 2 3 1 1.5 5
作业排序管理
(一)两台设备的流水型排序问题 1、排序方法: 约翰逊—贝尔曼规则
J2
J5
号Ji
完成时间Ci
2
5
9 14 22 31
(天)
交货延期量 0
0
0
8
0
生产作业计划与排序ppt课件教材讲义

二、最长流程时间
表 6-1 2 2 5 8 2 加工时间矩阵 3 4 3 1 6 7 7 5 4 3
i Pi1 Pi2 Pi3 Pi4
1 4 4 5 4
5 4 4 5 3
6 2 5 5 1
二、最长流程时间
i pi pi
1
6 22 5 5
7
12
1 4 4 5
6
5 4
10
2
4
12
3
13
2
5
1
3
16
11
17
pi
pi
4 3
2
4 5
15
22
Hale Waihona Puke 20307 27 5
35
6 33 7
42
8
1 13
4 21
3 25
2 32
3 38
4 46
三、n/2/F/Fmax问题的算法
Johnson算法: • 假定:ai为工件Ji在机器M1上的加工时 间,bi为工件Ji在机器M2上的加工时间, 每个工件按M1—M2的路线加工。
四、一般n/m/P/ Fmax问题的 启发式算法
1、Palmer法
• 计算工件斜度指标i : i [k (m 1) / 2]pik k 1 m : 机器数 pik :工件i在机器k上的加工时间。 M=3 i=-pi1 +pi3 M=4 i=-1.5pi1-0.5pi2 +0.5pi3+1.5pi4 排序方法: 按i从大到小的顺序排列。 • 按排序的顺序计算Fmax
一、基本概念
4)一般来说,排列排序问题的最优解不一定 是相应流水车间排序问题的最优解,但一般 是比较好的解。而对于仅有 2 台或 3 台机器的 情况,则排列排序问题的最优解一定是相应 流水车间排序问题的最优解。
3-2生产作业排序
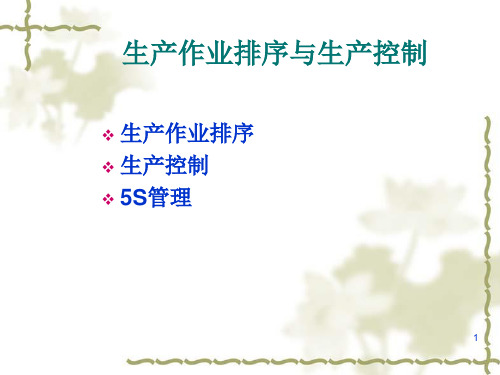
2
作业排序概念
❖ 作业排序(Job Sequencing)。确定工 件在机器上的加工顺序。
❖ 作业计划(Job Scheduling),不仅包 括确定工件的加工顺序,而且还包括确 定机器加工每个工件的开始时间和完成 时间。
❖ 最长流程时间(加工周期):从第一个
件
19
按SCR关键比例最小规则排序
零件加工顺序
1 23456
零件编号
C
关键比例
2.13
该零件所需加工时间(天) 8
B A DF E 2.14 2.2 3.33 3.6 6.25 7 10 6 5 4
完工日期
8 15 25 31 36 40
计划交货日期
17 15 22 20 18 25
延 误 日 期 (天)
38
“5S”管理的定义、目的、实施要领
1.“1S”—— 整理 (1)定义
① 将工作场所任何东西区分为有必要的与不必 要的; ② 把必要的东西与不必要的东西明确地、严格 地区分开来; ③ 不必要的东西要尽快处理掉; ④ 正确的价值意识——使用价值,而不是购买价 值。
39
(2)目的 ① 合理腾出空间,使之不影响生产过程,
“先到先服务”规则。它是指根据任务到达的先 后次序安排加工顺序,先到先加工。
❖ (2)SPT(shortest processing time)规则,即
“最短加工时间”规则。它是把加工时间由短到 长进行排序,优先选择加工时间最短的任务。
❖ (3)SCR(smallest critical ratio)规则,优 先选择关键比例最小的工件(关键比例=(交货 期-当前期)/余下的加工时间)。
第六章 作业排序(生产管理(华中科技大学 崔南方)

四、一般n/m/P/ Fmax问题的 启发式算法
i L=1 L=2 用 CDS 法求解 1 2 Pi1 1 2 Pi3 4 5 Pi1+pi2 9 6 Pi2+pi3 12 9 3 6 8 8 10 4 3 2 12 11
• L=1,按Johnson算法得到加工顺序(1,2,3,4),Fmax=28 • L=2,按Johnson算法得到加工顺序(2,3,1,4), Fmax=29 • 取顺序(1,2,3,4)为最优顺序。
五、单件车间排序问题(n/m/G/Fmax)
• 加工时间矩阵T:与D相对应。
1,1,1 1,2,3 1,3,2
D=
2,1,3 2,2,1 2,3,2
4 T=
6
3
5
7
4
华中科技大学管理学院
五、单件车间排序问题(n/m/G/Fmax)
• 加工顺序矩阵S:每一行与机器相对应,每一列与工 件相对应。
1,1,1 1,2,3 1,3,2
2 4 T=
1
D= 2,1,3 2,2,1 2,3,2 T’k 2 3 6 3 7 7 8 7 8 12 T* 2 3 7 7 8 M* M1 M3 M3 M1 M2
3 4 5 Oj 1,1,1 2,1,3 1,2,3 2,2,1 1,3,2 2,3,2
0 0 2 0 3 3 7 3
7 7
1,3,2 2,3,2 2,3,2
华中科技大学管理学院
二、最长流程时间
• 最长流程时间(加工周期):从第一个工件 在第一台机器上加工起到最后一个工件在最 后一台机器上加工完毕为止所经过的时间。 • 假定所有工件的到达时间都为0,则Fmax等 于排在末位加工的工件在车间的停留时间。
生产与运作管理 生产作业排序 资料

2020/7/12
一、作业排序的概念 作业排序就是确定工件在设备上的加工顺序,
使预定的目标得以实现的过程。 二、作业排序的目标
1、总流程时间最短 流程时间=加工时间+等待时间+运输时间
2、平均流程时间最短 3、平均在制品占用量最小 4、最大延迟时间最短 5、平均延迟时间最短 6、延迟工件最少
4、重复上述过程(步骤2和3),直到所有的人员需求得到 满足。
【例6-4】邮局一周内每天的员工需求如表6-1所示 。工会要求每名员工连续工作五天,然后连续休 息两天。试制定排班计划。
表6-1 一周内每天的员工需求量
日期 周一 周二 周三 周四 周五 周六 周日
员工 3
6
5
6
5
5
5
需求
量
解: 表6-2 每周员工安排表(循环排序法)
2020/7/12
仪器
工序1 工序2
Y1 Y2 Y3 Y4 Y5
12 4 5 15 10 22 5 3 16 8
仪器 工序1 工序2
•
2020/7/12
解: Y1 Y2 Y3 Y4 Y5
12 4 5 15 10 22 5 3 16 8
原则: 1.找min,前道工序--最前
后道工序--最后 2.若多个min,任选。
2020/7/12
以上这些规则各有其特点,不同的规则适用于不同的 目标。例如,FCFS规则比较公平;SPT规则可使平均流 程时间最短,从而减少在制品数量;EDD规则可使工件的 最大延迟时间最小、平均延误时间最小;Moore法则可使 延迟的工件数最少等。
2020/7/12
FCFS、SPT、EDD优先规则的应用
生产运作的战略决策与作业排序.pptx

▪ 战略(Strategy)
它是指运筹帷幄的谋划,统指重大的、 带全局性的决策。基于组织的使命。
▪ 目标(Aim)
• 它是指企业组织要达到的预期标准,目标是 使命的体现。
• 例:某公司的目标为:(1)占有市场份额 (2)实现一定的盈利水平
21
▪策略
策略是用来完成战略的方法和措施,策 略比战略更具体,策略的实质是“如何做?”。
1992
现代企业制度
承包制的形成
14
➢ 承包制的优缺点:
• 不顾后果使用固定资产,设备折旧速度快。 • 本应属于国家补贴的机构易加入“承包制的
洪流”。 • 理想的承包制应当根植于公开招标制,但是
复杂的社会人际关系确实最大的障碍。 • 承包制已成为企业和既是拥有者,又是经济环境的
管理者的国家之间矛盾关系的牺牲品。 • 违背了可持续发展的理论。
• 衰退期的特点:技术老化,新产品已替代总销售额 和利润都下降
44
▪ 产品寿命周期的理论对生产经营 管理的启发
• 缩短投入期 • 加长增长期 • 改进成熟期 • 更换衰退期
45
3 新产品研制开发方法
▪ 一般把科研工作为三大类:
❖ 基础研究:研究物质运动变化规律。纯理论.无 应用目的
❖ 应用研究:为了某种实用目的,运用基础研究成 果,开辟新的途径
量=δ 若 δ >1:选择供应原料的地方 若 δ <=1:选择靠近销售近的地方
• 有利于生态:环境能吸收 • 有利于战备:核电站 污染源不能投在城市
57
2 厂址选择的方案及程序
厂址选择的方案 决策者在选址规划时通常会考虑以下
三种选择方案: 1.扩展现有工厂(有足够空间,商
业销售中心); 2.新建地点(必须进行量-本-利
现代生产管理6生产现场管理和作业排序

6.2 现场管理的方法 6.2.3 看板管理 看板管理的作用
用看板作为“生产指令”“取货指令”和“运输指令”, 能起到严格控制生产进度的作用。
由于“看板”任何时候都与实物一起移动,因而生产管理 人员和全体职工只要通过看板,就可以直接了解生产情况, 及时发现生产中的问题。
生产中前后工序都严格按“看板”规定的时间和数量取货 和生产,可以对在制品实现最有效的实物管理,杜绝在制 品账实不符。
11
现代生产管 理概论
2
生产系统的 规划与组织
3
生产计划与生产 作业计划编制
4
工作研究与 工作设计
5
企业资源计 划(ERP)
6
生产现场管理 和作业排序
17
项目管理
8
企业物料管理
9
设备管理
10
质量管理与ISO 9000质量管理
体系认证
11
生产管理技 术发展与模
式改变
目录 / CONTENTS
6
生产现场管理和作业排序
6.2 现场管理的方法 6.2.2 6S管理 内容 6S管理是指对生产要素所处的状态不断地进行整理、整顿、清扫、清洁、安全 和提高素养的活动。由于整理(Seiri)、整顿(Seiton)、清扫(Seiketsu)、 清洁(Seiso)、安全(Safety)、素养(Shitsuke)这六个词的日文用拉丁 字母拼音时,头一个字母都是S,所以简称“6S”。
明确物品的名称及用途,用分类标示及用颜色区 分
目视管理的物品 管理
决定物品的放置场所,容易判断 物品的放置方法能保证顺利地进行,先入先出
决定合理的数量,尽量只保管必要的最小数量,且要 防止断货
6.2 现场管理的方法 6.2.1 目视管理法 目视管理的品质管理
生产作业计划与作业排序
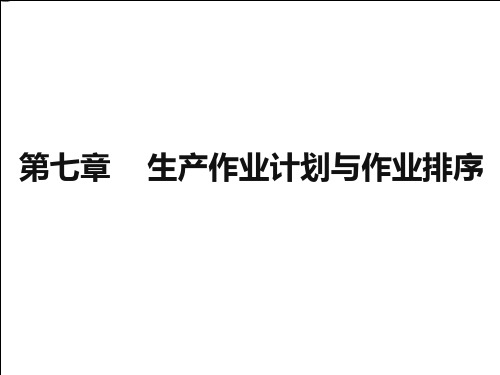
6/8/2014
(三)生产提前期:产品(毛坯、零部件)在各个工艺阶
段出产或投入的日期比成品出产的日期应提前的时间。 1、投入提前期:各车间投入日期比成品出产日期应提前的 时间。公式=车间出产提前期+车间的生产周期。 2、出产提前期: 公式:当前后工序车间的生产间隔相等 车间出产提前期=车间投入提前期+车间保险期 当前后工序车间的生产间隔不相等 前车间出产提前期=后车间投入提前期+前车间的保 险期+ | 前车间生产间隔期-后车间生产间隔期 |
3、进行生产能力核算与平衡 4、检查生产作业准备 5、生产作业控制
6/8/2014
(二)生产作业计划的目标
1、保证生产计划任务能够按质、按量、按期、按品 种完成。
2、尽可能实现均衡生产,建立良好的生产秩序,提 高效率。
6/8/2014
二、大量大批生产作业计划
(一) 大量大批生产作业计划 1、节拍 节拍是流水线上相邻两件相同制品投产或出产的时 间间隔,它表明了流水线生产速度的快慢或生产效率的 高低。是大量流水生产期量标准中最基本的标准。 流水线节拍的计算公式:R=F/N 其中:R—流水线的节拍(分/件),F—计划期内有 效工作时间(分),N—计划期的产品产量(件)。
6/8/2014
P128 【例7.1】以某冰箱厂为例,计算其计划期各车间X零 件的出产量和投入量,计划过程如下图
:
6/8/2014
订货点法(安全库存法):根据库存在制品下降 到订货点的时间来确定零件投产时间的一种方法。 应用场合:应用于短期的需求变化不定,但较长 时期内确有需求,定期重复生产的场合。用来安 排需求量大的标准件和通用件的生产 (三)车间生产作业计划编制
6/8/2014
生产与运作管理作业排序解析PPT课件
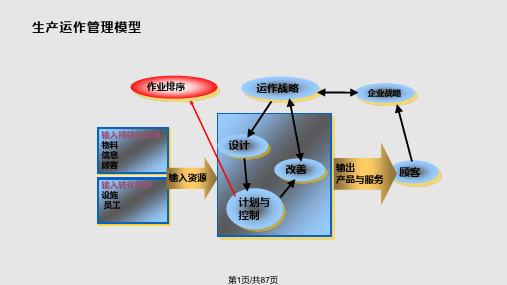
制造业生产作业排序分类
按机器数 量分类
单台机器的 排序问题
多台机器的 排序问题
单件作业排序问题 (Job-Shop)
流水作业排序问题
按工件到达车 间的情况不同
(Flow-Shop) 静态排序问题
排序时,所有工件都已到达,可一次性进行排序
动态排序问题
工件陆续到达,要随时安排它们的加工顺序
第32页/共87页
发动机机壳的加工与取货信息
一个加工车间负责加工发动机机壳,现在共有5个机壳等待加工。只 有一名技工在岗做此项工作。现各个机壳的标准加工时间已经被估算 出来,顾客也已经明确提出了他们所希望的完工时间。
发动机机壳
机壳1 机壳2 机壳3 机壳4 机壳5
所需标准加工时间(h) (包括机器调整)
第11页/共87页
• 对于某一工作 n个 地,在给定作的业一段的时间单内,台顺次机决定器下一排个被序加工问的工题件 (n/1)
• 可能要考虑交付日期、在制品数量、全部完工时间等因素
…
对象1 对象2 对象3
对象n
工作地
第12页/共87页
常用的优先顺序规则
规则
FCFS (First Come First Served)规则 EDD (Earliest Due Date)规则 SPT (Shortest Processing Time)规则 SCR (Smallest Critical Ratio)规则
第18页/共87页
最短余下时间 LWRK (Least work Remaining)
• 优先选择余下工作时间最短的工作
第19页/共87页
最多余下作业
MOPNR (Most Operations Remaining) • 优先选择余下处理工序最多的工作
作业排序与生产作业计划培训
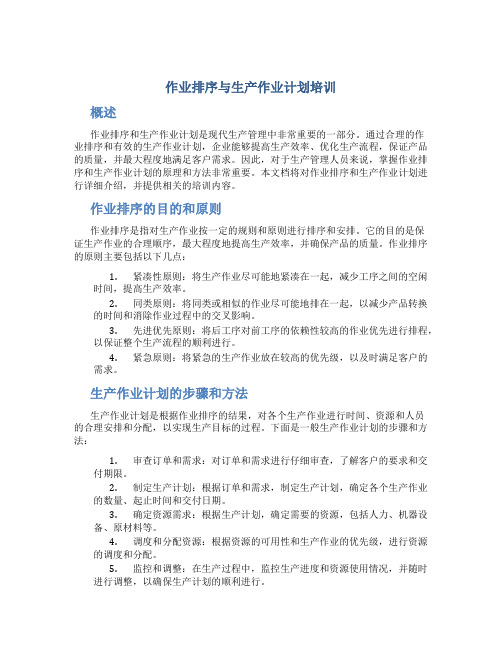
作业排序与生产作业计划培训概述作业排序和生产作业计划是现代生产管理中非常重要的一部分。
通过合理的作业排序和有效的生产作业计划,企业能够提高生产效率、优化生产流程,保证产品的质量,并最大程度地满足客户需求。
因此,对于生产管理人员来说,掌握作业排序和生产作业计划的原理和方法非常重要。
本文档将对作业排序和生产作业计划进行详细介绍,并提供相关的培训内容。
作业排序的目的和原则作业排序是指对生产作业按一定的规则和原则进行排序和安排。
它的目的是保证生产作业的合理顺序,最大程度地提高生产效率,并确保产品的质量。
作业排序的原则主要包括以下几点:1.紧凑性原则:将生产作业尽可能地紧凑在一起,减少工序之间的空闲时间,提高生产效率。
2.同类原则:将同类或相似的作业尽可能地排在一起,以减少产品转换的时间和消除作业过程中的交叉影响。
3.先进优先原则:将后工序对前工序的依赖性较高的作业优先进行排程,以保证整个生产流程的顺利进行。
4.紧急原则:将紧急的生产作业放在较高的优先级,以及时满足客户的需求。
生产作业计划的步骤和方法生产作业计划是根据作业排序的结果,对各个生产作业进行时间、资源和人员的合理安排和分配,以实现生产目标的过程。
下面是一般生产作业计划的步骤和方法:1.审查订单和需求:对订单和需求进行仔细审查,了解客户的要求和交付期限。
2.制定生产计划:根据订单和需求,制定生产计划,确定各个生产作业的数量、起止时间和交付日期。
3.确定资源需求:根据生产计划,确定需要的资源,包括人力、机器设备、原材料等。
4.调度和分配资源:根据资源的可用性和生产作业的优先级,进行资源的调度和分配。
5.监控和调整:在生产过程中,监控生产进度和资源使用情况,并随时进行调整,以确保生产计划的顺利进行。
作业排序与生产作业计划培训内容为了帮助生产管理人员掌握作业排序和生产作业计划的原理和方法,以下是一份可能的培训内容:第一天:作业排序•什么是作业排序及其重要性•作业排序的原则和方法•实例分析:如何进行作业排序•作业排序的实践技巧和注意事项第二天:生产作业计划•什么是生产作业计划及其作用•生产作业计划的步骤和方法•实例分析:如何制定生产计划•生产计划的实践技巧和调整方法第三天:作业排序与生产作业计划的整合应用•作业排序与生产作业计划的关系与衔接•整合应用的案例分析•实践操作:参与实际生产作业排序和生产作业计划的过程•培训总结和经验分享通过以上的培训内容,生产管理人员将能够全面了解作业排序和生产作业计划的原理和方法,掌握实际操作的技巧,并能够在实际工作中灵活运用,最大限度地提高生产效率和满足客户需求。
生产作业排
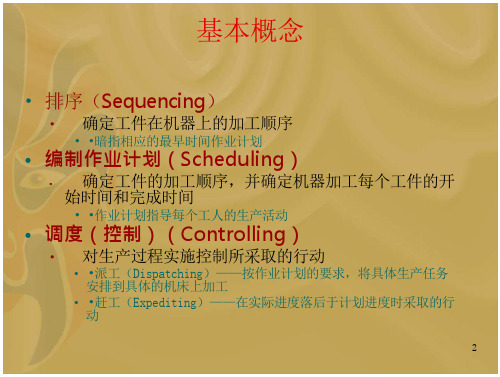
• MOPNR(Mostoperations remaining)法则
• 优先选择余下工序数最多的工件 • 与MWKR法则类似,只不过考虑工件在不同机器上的
转运排队时间是主要的
• SCR(Smallest c r i tica l ratio)法则
• •派工(Dispatching)——按作业计划的要求,将具体生产任务 安排到具体的机床上加工
• •赶工(Expediting)——在实际进度落后于计划进度时采取的行 动
2
假设条件
• 一个工件不能同时在几台不同的机器上加工 • 工件在加工过程中采取平行移动方式
• 当上一道工序完工后,立即送下道工序加工
基本概念
• 排序(Sequencing)
• 确定工件在机器上的加工顺序
• •暗指相应的最早时间作业计划
• 编制作业计划(Scheduling)
• 确定工件的加工顺序,并确定机器加工每个工件的开 始时间和完成时间
• •作业计划指导每个工人的生产活动
• 调度(控制)(Controlling)
• 对生产过程实施控制所采取的行动
• 按目标函数分类
• 平均流程时间最短,误期完工工件数最少,……
• 按参数的性质分类:确定型/随机型排序问题
8
排序问题表示法
9
流水作业排序问题
• 基本特征:各个工件的加工路线一致
• 工件的流向一致 • 并不要求每个工件必须经过加工路线上每台机器加工 • 如果某些工件不经某些机器加工,则相应加工时间为零
32
无延迟作业计划示例(续)
33
优先调度法则
• 能动作业计划与无延迟作业计划构成时,第(3) 步的两个条件一般都有多个工序可以满足
- 1、下载文档前请自行甄别文档内容的完整性,平台不提供额外的编辑、内容补充、找答案等附加服务。
- 2、"仅部分预览"的文档,不可在线预览部分如存在完整性等问题,可反馈申请退款(可完整预览的文档不适用该条件!)。
- 3、如文档侵犯您的权益,请联系客服反馈,我们会尽快为您处理(人工客服工作时间:9:00-18:30)。
为止,中途不插入其他工件。 (4)每道工序只在一台设备上加工。 (5)工件数、机器数与加工时间已知。 (6)每台设备同时只能加工一个工件。
2019/11/26
2、多项作业、两台机器的排序 -- Johnson 方法
? N项作业,2台机器,所有工件的加工路 线都相同。(S.M.Johnson,1954,)
已准备就绪,可以对全部工件进行一次性排序。 2、动态排序▁若工件陆续到达,要随时安排它们的
加工顺序。
2019/11/26
(三)按照目标函数的不同 1、平均流程时间最少 2、延期工件最少
2019/11/26
四、单台设备上的作业排序方法
排序规则: (1)最短加工时间优先规则SPT(Shortest processing time) (2)最短交货期优先规则EDD(Earliest due date) (3)先到先加工规则FCFS(First come first served) (4)最小松动时间优先规则STR(Slack time remaining)
2019/11/26
三、排序问题的分类
(一)按照机器数目的不同 1、单台机器的排序问题 2、多台机器的排序问题 按照工件加工路线的不同,又可以分为: ①流水型(flow shop)的排序问题 所有工件的工艺路线都相同 ②非流水型(job shop)的排序问题 每个工件的工艺路线各不相同
(二)按照工件的到达情况的不同 1、静态排序▁当排序时,所有的工件都已到达,并
2019/11/26
【例6-2】五台仪器修复作业排序
某公司在一次火灾中损坏了5台仪器,这些仪器的修复需 要经过如下2道工序:
(1)将损坏的仪器运至修理车间,拆卸开;
(2)清洗仪器部件,更换报废部分,装配,测试,并送 回原车间。
每台仪器在两个工序的各自所需时间如表所示。两道工 序分别由不同的人担当。由于原车间没有这 5台仪器就 无法恢复生产,所以希望找到一个较好的排序方案, 使全部修理时间尽可能短。
按FCFS规则排序
? 排序的结果是 A-B-C-D-E-F 。
顺序
A B C D E F 合计 平均
加工时间
2 8 4 10 5 12 41
流程时间
2 10 14 24 29 41 120 120/6=20
预定交货期
7 16 4 17 15 18
延期天数(如果为负 则赋值0)
0 0 10 7 14 23 54
2019/11/26
以上这些规则各有其特点,不同的规则适用于不同的 目标。例如,FCFS规则比较公平;SPT规则可使平均流 程时间最短,从而减少在制品数量;EDD规则可使工件的 最大延迟时间最小、平均延误时间最小;Moore法则可使 延迟的工件数最少等。
2019/11/26
FCFS、SPT、EDD优先规则的应用
(松动时间=交货期-加工时间) (5)临界比率最小优先规则SCR(Smallest critical ratio)
交货期-当前日期
CR=
作业时间 (6)综合规则(综合使用两种规则,如先按照交货期优先
排序,然后按照最短加工时间优先的原则排序) (7)后到先加工规则 (8)随机规则 (9)延迟工件最少的规则(Moore法则)
【例6-1】下表是在某工作中心等待加工的6项作业的加工时 间(包含换产时间)与预定日期,假设工作的到达顺序与 表中顺序相符 。根据以下规则来决定其作业顺序:①
FCFS②SPT③EDD并对它们分别进行评价。
作业
A B C D E F
加工时间(天)
2 8 4 10 5 12
预定日期(天)
7 16 4 17 15 18
第六章 生产作业排序
2019/11/26
一、作业排序的概念 作业排序就是确定工件在设备上的加工顺序,
使预定的目标得以实现的过程。 二、作业排序的目标
1、总流程时间最短 流程时间 =加工时间 +等待时间 +运输时间
2、平均流程时间最短 3、平均在制品占用量最小 4、最大延迟时间最短 5、平均延迟时间最短 6、延迟工件最少
A
B
?目标: 使全部完工时间最小。 ?条件: 每种工件在每台机器上的加工时间均为已知。
2019/11/26
Johnson方法
? 步骤:
1.选择最短的作业时间; 2.如果最短时间的作业在第 1个加工中心,则安
排在最前面,若在第 2个加工中心,则安排在 最后; 3.在等待的队列中,取消第 2步安排了的作业; 4.重复1,2,3步。
40/6=6.67
按EDD规则
? 作业顺序是 C-A-E-B-D-F
顺序
C A E B D F 合计 平均
加工时间
4 2 5 8 10 12 41
流程时间
4 6 11 19 29 41 110 110/6=18.33
预定交货期
4 7 15 16 17 18
延期天数(如果为负 则赋值0)
0 0 0 3 12 23 38
54/6=9
按SPT规则
? 作业顺序是 A-C-E-B-D-F
顺序
A C E B D F 合计 平均
加工时间
2 4 5 8 10 12 41
流程时间
2 6 11 19 29 41 108 108/6=18
预定交货期
7 4 15 16 17 18
延期天数(如果为负 则赋值0)
0 2 0 3 12 23 40
38/6=6.33
不同排序规则的结果分析
规则 FCFS
流动时间 (天)
120
平均流动 时间 (天)
20
总延期时 间(天)
54
平均延期 时间 (天)
9
SPT
108
18
40
6.67
EDD
110
18.33
38
6.33
排序规则的比较:
1、SPT规则,可以使作业流程时间最短,使滞留在加工过 程的平均在制品占用量最少,有利于节约流动资金,节约 厂房、仓库面积和保管费用。但是,由于未考虑交货期, 所以可能发生交货延期。
2、EDD规则,平均延迟天数最少,减少违约罚款损失,但 缺点是平均流程时间增加,不利于节约在制品占用资金。
3、FCFS规则,主要问题是加工时间过长。但其使用简单, 且体现公平,常用于服务业的排队系统。
2019/11/26
五、流水生产线作业排序方法
1、 Flow-shop 排序问题的描述
假设: (1)一个工件不能同时在不同机器上加工。 (2)工件在加工过程中采用平行移动方式(当上一道工序