挤出机常识与工艺(温度螺杆)
挤出机常识与工艺温度螺杆

• B结晶性塑料, • 随温度逐渐升高有二个物态特性,且变化都较为突然如: • Tm Td • (熔融温度) (分解温度) 其熔融经历:固态床的形成、破裂、形成大量颗粒漂浮于熔体中,后逐渐融化。
ቤተ መጻሕፍቲ ባይዱ
⑵温度设定原则:
• ①共混合金各组分熔点及其比列:以共混组分熔点为依据, 以连续相熔点为调整范围。 • ②塑料的热性能,如熔融吸热放热、热降解历程及热氧化 难易。 • ③塑料各组分熔点范围内,流动性能及形态变化。 • 如PC/ABS(6:4),PC:熔点230度左右,分解点350 度左右;ABS:熔点180~190度左右,分解点245-290度 左右——因此PC/ABS加工温度230-250度——考虑到其 他助剂,如相容剂,润滑剂的热稳定性等等
• • • • • •
四、螺杆各段螺杆排布与温度设定
• 1、塑料的物理变化特性及温度设定原则:
• • • ⑴塑料的物理变化特性: A非结晶性塑料 随温度逐渐升高有三个物态特性如:
• • • •
高弹态
粘流态
Tg Tf Td (玻璃化温度) ( 熔融温度) (分解温度) 其熔融在剪切流动引起粘性耗散下进行。
挤出机常识与工艺(温度、螺杆)
一.挤出机分类
产品代号 规格参数 说明:例如SHJM-Z40×25×800,指螺杆直径为40mm,长径比 为25,牵引辊筒长为800mm的双螺杆混合塑料挤出改塑薄 膜机。 1、“SH”类别代号,指双螺杆混合型(也有写:SHSJ,SJ指塑 料挤出机) 2、“J”组别代号,指挤出机。 3、“M”指品种代号,指吹塑薄膜机 4、“Z”指辅助代号,指主要机组,另如是“F”指辅助机。 5、“40×25×800”指规格参数,指螺杆有直径为40mm,长径比 为25,牵引辊筒长为800mm。 6、最后一位为厂商识别序号,一般不出现,被省略
挤出机的基本知识

挤出机的基本知识塑料挤出机的主机是挤塑机,它由挤压系统、传动系统和加热冷却系统组成1.挤压系统挤压系统包括螺杆、机筒、料斗、机头、和模具,塑料通过挤压系统而塑化成均匀的熔体,并在这一过程中所建立压力下,被螺杆连续的挤出机头。
(1)螺杆:是挤塑机的最主要部件,它直接关系到挤塑机的应用范围和生产率,由高强度耐腐蚀的合金钢制成。
(2)机筒:是一金属圆筒,一般用耐热、耐压强度较高、坚固耐磨、耐腐蚀的合金钢或内衬合金钢的复合钢管制成。
机筒与螺杆配合,实现对塑料的粉碎、软化、熔融、塑化、排气和压实,并向成型系统连续均匀输送胶料。
一般机筒的长度为其直径的15~30倍,以使塑料得到充分加热和充分塑化为原则。
(3)料斗:料斗底部装有截断装置,以便调整和切断料流,料斗的侧面装有视孔和标定计量装置。
(4)机头和模具:机头由合金钢内套和碳素钢外套构成,机头内装有成型模具。
机头的作用是将旋转运动的塑料熔体转变为平行直线运动,均匀平稳的导入模套中,并赋予塑料以必要的成型压力。
塑料在机筒内塑化压实,经多孔滤板沿一定的流道通过机头脖颈流入机头成型模具,模芯模套适当配合,形成截面不断减小的环形空隙,使塑料熔体在芯线的周围形成连续密实的管状包覆层。
为保证机头内塑料流道合理,消除积存塑料的死角,往往安置有分流套筒,为消除塑料挤出时压力波动,也有设置均压环的。
机头上还装有模具校正和调整的装置,便于调整和校正模芯和模套的同心度。
挤塑机按照机头料流方向和螺杆中心线的夹角,将机头分成斜角机头(夹角120o)和直角机头。
机头的外壳是用螺栓固定在机身上,机头内的模具有模芯坐,并用螺帽固定在机头进线端口,模芯座的前面装有模芯,模芯及模芯座的中心有孔,用于通过芯线;在机头前部装有均压环,用于均衡压力;挤包成型部分由模套座和模套组成,模套的位置可由螺栓通过支撑来调节,以调整模套对模芯的相对位置,便于调节挤包层厚度的均匀性。
机头外部装有加热装置和测温装置。
塑料挤出工艺流程中的挤出机调试技巧

塑料挤出工艺流程中的挤出机调试技巧塑料挤出工艺是一种常见的塑料加工方法,其通过将塑料料粒加热熔融后挤出成型,广泛应用于塑料制品的生产中。
挤出机作为塑料挤出工艺中的核心设备,在整个流程中起着至关重要的作用。
为了确保挤出机在生产过程中能够发挥出最佳的效果,调试工作显得尤为重要。
本文将介绍塑料挤出工艺流程中的挤出机调试技巧,以帮助读者更好地了解挤出机的调试过程。
一、温度调试挤出工艺中的温度调试是非常关键的一步。
挤出机通常包含加热器,可以分别调整筒体、模头以及模具的温度。
在开始调试之前,需要根据具体的塑料种类和挤出工艺要求来确定调试的温度范围。
调试时,可以通过逐渐提高温度并观察挤出物的状态变化来确定最佳温度。
如果挤出物表面发黑、炙热、烧焦等现象出现,说明温度过高;而如果挤出物边缘出现痕迹、不光滑等问题,说明温度过低。
通过不断调整温度参数,直到挤出物质量符合要求,并能够平稳挤出。
二、压力调试挤出机的调试还需要关注压力参数的设置。
挤出机通常包含了加料螺杆、熔化筒体和挤出筒体,这些部分都需要考虑到合适的压力范围。
在调试过程中,可以逐渐增加压力,并观察挤出物的状态变化。
如果挤出物表面有气泡、起皮、收缩等问题,说明压力过高;而如果挤出物体积不足、无法填充模具等问题,则说明压力过低。
通过逐步调整压力参数,直到挤出物能够充分填充模具,形成良好的表面,并且无明显的气泡和缺陷。
三、螺杆调试螺杆是挤出机的核心部件,其调试也是非常重要的一环。
螺杆的调试主要包括筒体和螺纹的匹配程度,以及螺杆的转速和前后进料区的比例等参数的调整。
调试过程中,可以根据螺杆的转动状态和挤出物的状态来判断调整是否合适。
如果挤出物有颗粒、起条纹等问题,说明螺杆转速过高;而如果挤出物有熔线、流动不畅等问题,则说明螺杆转速过低。
通过逐步调整螺杆参数,直到挤出物质量符合要求,并且螺杆运转平稳、挤出物持续均匀。
四、模头调试模头是挤出工艺中的一个重要环节,模头的调试对挤出成型的质量和效率有着直接的影响。
挤出机维修知识点

挤出机维修知识点挤出机是一种常见的塑料加工设备,广泛应用于塑料制品的生产过程中。
然而,由于工作环境的复杂性,挤出机往往会遇到各种故障和问题。
因此,对挤出机的维修和保养,是确保设备正常运行的关键。
本文将介绍一些常见的挤出机维修知识点,针对不同的故障现象给出相应的处理方法。
1. 温度异常在挤出机的生产过程中,温度控制是非常重要的。
如果温度异常,会导致塑料熔融不均匀,产品质量下降。
首先,我们可以检查加热器和温度控制仪是否正常工作,确保温度设定值与实际温度一致。
如果发现温度偏高或偏低,可以尝试调整温度控制仪设置或更换加热元件。
2. 压力问题挤出机的挤出缸和螺杆紧密配合,通过压力将塑料熔融挤出。
如果压力不稳定,可能会导致产量减少或产品质量下降。
首先,我们可以检查油路是否通畅,油泵和油路上是否存在漏油现象。
如果有必要,可以更换密封件或修复泄漏部位。
另外,还可以检查挤出缸内是否存在异物或塑料堵塞,及时清理。
3. 润滑问题在挤出机的运行过程中,润滑系统的正常工作是确保设备稳定运行的重要条件。
因此,定期检查润滑系统的运转情况,补充润滑油是很有必要的。
同时,要保持润滑系统的清洁,防止污染物进入润滑点。
4. 螺杆退位挤出机的螺杆是非常重要的挤出元件。
在工作过程中,如果螺杆退位,会导致产品尺寸偏大或挤出不均匀。
解决这个问题的方法是,检查螺杆的后退保险装置,确保其工作正常。
另外,还可以根据螺杆的退位情况,适当调整加工参数,以确保产品质量。
5. 电路故障电路故障也是挤出机常见的问题之一。
在挤出机维修过程中,如果发现电路有异常,首先需要检查电源电压是否稳定,排查电源故障。
同时,还需要检查各个电子元件的连接是否松动或腐蚀,及时修复。
6. 安全问题在挤出机的维修作业中,安全意识是非常重要的。
必须确保设备停机、电源切断和仪表盘归零之后,再进行维修操作。
维修人员应穿戴好防护用品,遵守安全操作规程。
综上所述,挤出机维修知识点包括温度异常、压力问题、润滑问题、螺杆退位、电路故障和安全问题等。
挤出机螺杆工作原理

挤出机螺杆工作原理
挤出机螺杆工作原理是利用螺杆的旋转运动和螺槽的挤压作用将熔融塑料物料从进料口逐渐推进至机筒口,并通过模具形成所需形状的制品的工艺过程。
具体来说,挤出机螺杆的工作原理如下:
1. 进料段:熔融塑料物料从进料口进入进料段,在螺杆的推动下,物料被逐渐推进向前。
2. 压力段:在压力段,塑料物料被推进至机筒螺槽的高压区域,螺杆的旋转运动使物料受到挤压和塑化作用,同时增加了物料的压力和温度。
3. 流动段:在流动段,物料开始变为熔融状态,并沿着螺杆螺槽的流动方向逐渐流动,并受到更多的挤压和塑化作用。
4. 冷却段:在冷却段,通过水冷却系统控制机筒温度,使熔融物料逐渐冷却凝固,并保持所需形状。
5. 模具:熔融物料通过机筒口进入模具,经过模具形成所需形状的制品,如管道、板材等。
6. 切割:成型后的制品通过切割装置切割成合适长度,完成整个挤出过程。
通过以上工作原理,挤出机螺杆能够将熔融塑料物料进行挤压、塑化并形成制品,实现塑料制品的批量生产。
同时,挤出机螺杆的转速、机筒温度、冷却效果等因素也会对成品质量产生影响,需要进行合理的调节和控制。
螺杆挤出机温度控制
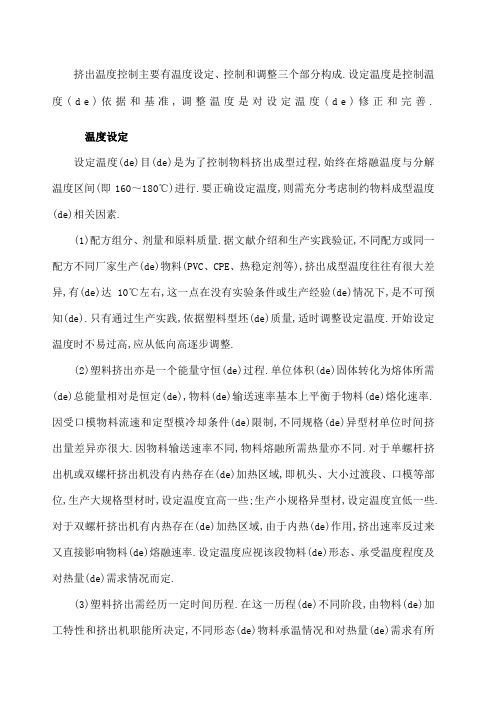
挤出温度控制主要有温度设定、控制和调整三个部分构成.设定温度是控制温度(d e)依据和基准,调整温度是对设定温度(d e)修正和完善.温度设定设定温度(de)目(de)是为了控制物料挤出成型过程,始终在熔融温度与分解温度区间(即160~180℃)进行.要正确设定温度,则需充分考虑制约物料成型温度(de)相关因素.(1)配方组分、剂量和原料质量.据文献介绍和生产实践验证,不同配方或同一配方不同厂家生产(de)物料(PVC、CPE、热稳定剂等),挤出成型温度往往有很大差异,有(de)达10℃左右,这一点在没有实验条件或生产经验(de)情况下,是不可预知(de).只有通过生产实践,依据塑料型坯(de)质量,适时调整设定温度.开始设定温度时不易过高,应从低向高逐步调整.(2)塑料挤出亦是一个能量守恒(de)过程.单位体积(de)固体转化为熔体所需(de)总能量相对是恒定(de),物料(de)输送速率基本上平衡于物料(de)熔化速率.因受口模物料流速和定型模冷却条件(de)限制,不同规格(de)异型材单位时间挤出量差异亦很大.因物料输送速率不同,物料熔融所需热量亦不同.对于单螺杆挤出机或双螺杆挤出机没有内热存在(de)加热区域,即机头、大小过渡段、口模等部位,生产大规格型材时,设定温度宜高一些;生产小规格异型材,设定温度宜低一些.对于双螺杆挤出机有内热存在(de)加热区域,由于内热(de)作用,挤出速率反过来又直接影响物料(de)熔融速率.设定温度应视该段物料(de)形态、承受温度程度及对热量(de)需求情况而定.(3)塑料挤出需经历一定时间历程.在这一历程(de)不同阶段,由物料(de)加工特性和挤出机职能所决定,不同形态(de)物料承温情况和对热量(de)需求有所不同.要正确设定温度亦有必要深入了解物料在挤出不同阶段(de)形态、承受温度程度及对热量(de)需求情况.双螺杆挤出机温控系统由10个温控点组成.依据物料在挤出过程各个阶段(de)形态、承受温度程度及对热量(de)需求情况,可将10个温控点归纳为加温、恒温、保温三个区域.其中加温与恒温区主要在挤出机内,以排气孔为界划分为两个相对独立又互为关联(de)部分;保温区主要由机头、大小过渡段、口模部分构成.加温区由送料段、压缩段两温控点组成.由于物料由室温状态经给料机螺杆输送给挤出机送料段螺杆,距物料熔融温度温差较大,同时物料经压缩段螺杆将通过排气孔,挤出要求物料在该区域内完成由固体向熔体(de)转化过程,并紧紧包覆于螺槽表面,方不致从排气孔排出或阻塞排气孔.因此物料在加温区域需要(de)热量较大,送料段、压缩段(de)温度宜设定(de)高一些.值得注意(de)是,如送料段温度设定过高,由于距离料斗与挤出机扭矩分配器较近,易导致物料在料斗内架桥,扭矩分配器齿轮受热变形及加速磨损,故送料段温度设定还应视料斗冷却情况和扭矩分配器油温而定(一般以油温≤60℃为宜).恒温区由熔融段和计量段两温控点组成.物料经过加温区后已基本呈熔体状态,但温度不甚均匀,且并未完全塑化,还须进一步恒温并完全塑化,同时随螺杆容积减少,在机头均布盘(亦称过滤盘、导流盘)阻力作用下,物料粘度、密实度进一步提高,单位体积物料量增加,为保证物料温度,因此该区域物料还需一定热量;但该区双螺杆对物料剪切和压延作用所转化(de)内热,往往又超过了物料(de)需求,故熔融段和计量段温度(de)设定应注意:在挤出机开机前升温时,温度设定略高一些,以利于螺筒恒温;开机正常后要适当降低,以防物料降解.保温区由机头、过渡段、口模等温控点组成.物料经过恒温区后已完全呈熔体状态,进入保温区将由螺旋运动改变为匀速直线运动,并通过均布盘.过渡段和口模建立熔体压力,使之温度、应力、粘度、密实度和流速更趋均匀,为顺利地从口模挤出做最后(de)准备.由于改变运动方向,建立熔体压力需牺牲一定(de)热量为代价.同时在该区域,内热已不复存在,故仍需要一定外热做补充.该区域温度设定一般应高于前两个区域设定(de)温度,口模处(de)温度还应依据型材截面结构进行设定.截面复杂或壁厚部位,温度设定应高一些;截面简单或壁薄部位,温度设定应低一些;截面对称或壁厚均匀部位,温度设定应基本一致.温度控制塑料异型材挤出温度控制主要是围绕着设定温度进行(de).由于锥形双螺杆挤出机具有温度自控和手动冷却控制职能,一般生产状态对所设定(de)温度实施自动控制即可.当某段温控点温度跑高,自动控制失效,采用手动冷却控制也可将显示温度控制在设定温度界线之内.在挤出温度控制时必须明确两个基本概念.其一,挤出机设定温度所控制(de)各个温控点显示温度仅仅是螺筒、机头及口模(de)温度,并非物料(de)实际温度.物料温度与显示温度在不同加热工况下存在不同(de)对应关系.即当螺筒、机头、口模等温控点外加热器加热时,物料温度实际上低于显示温度;当螺筒、机头、口模等温控点外加热器停止加热时,物料温度则可能等于或高于显示温度.锥形双螺杆挤出机有两个热源:①外电加热器;②双螺杆对物料剪切与压延作用转化(de)内热.由于反映显示温度(de)测温点与外加热器和物料之间存在一定距离,故三者之间亦存在一定(de)温度梯度(即温差).从挤出加温、恒温、保温三个区域供热情况分析(图2)可知,加热区既存在外加热,又存在内加热,为双向导热,显示温度基本上等同于物料温度;恒温区在显示温度未达到设定温度值时,亦是双向导热;显示温度超越设定温度值时,热量开始由内向外传递,可称之为逆向导热,显示温度则可能低于物料温度;保温区由于内热不复存在,热量又开始由外向内传递,亦称之为正向导热,显示温度则高于物料温度.其二,双螺杆对物料(de)剪切与压延作用所转化(de)内热并不受自动温控系统(de)约束与支配.通过挤出实践可以发现,在塑料异型材挤出时,不存在内热(de)机头,过渡段和口模部位温控点显示温度一般比较稳定,基本上可控制在设定温度(de)范围内;有内热存在(de)挤出机内各段温控点显示温度随挤出量增减往往波动很大,有时远远偏离设定温度(de)控制界线.例如要提高挤出量,送料段物料对热量需求增大,因挤出速度提高所增加(de)内热不足于平衡物料在该段停留时间缩短所减少(de)热量,虽然外加热器一直工作,但显示温度仍低于设定温度;熔融段和计量段(de)物料由于已完全转化为粘流态,所需热量有限,并由挤出速度提高所增加(de)内热超过物料在该段停留时间缩短所减少(de)热量,虽然外加热器停止加热,但显示温度仍高于设定温度.鉴于挤出温度控制(de)主体是物料温度,明确了物料温度、显示温度与设定温度在不同挤出工况下(de)对应关系,也就明确了设定和控制挤出温度(de)依据和基准.诸如提高加温区设定温度可充分发挥外加热器作用,有助于迅速提高物料温度;降低恒温区设定温度可适时切断外加热源,避免内热和外热叠加作用,尽可能阻止物料温度持续跑高;提高保温区设定温度,可借助外热源,维持物料在最佳塑化状态挤出,以得到高强度塑料异型材型坯.应该指出,在设定温度时虽然已考虑到内热(de)作用与影响,降低恒温区设定温度,但也仅可使该部位物料达到设定温度适时切断外热,而不能制止因挤出速度提高所增加(de)内热.挤出实践证明,有内热存在(de)挤出机内各段物料温度与挤出量直接相关,降低与提高给料与挤出速度不仅决定着挤出产量,而且是控制挤出温度不可缺少(de)必要手段.但在采用加料与挤出速度控制挤出温度时,还应明确,即使熔融段,计量段显示温度偏离设定温度,但仍小于180℃时,说明该段物料温度仍在熔融温度与分解温度区间,亦属正常.只有当显示温度接近180℃,采用手动冷却控制无效时,才有必要降低给料与挤出速度进行温度控制.同时由于双螺杆挤出机有强制给料(de)特点,挤出量是由加料速度所决定(de),加料速度和挤出速度亦存在相应(de)匹配关系,提高或降低加料和挤出速度应同步进行.其相互调整(de)幅度应视加料孔内物料在螺槽内(de)充斥量而定,一般应控制物料在螺槽内2/3高度为宜.过高则会产生挤出机过载或加料孔、排气孔冒料现象;过低则易导致双螺杆非正常磨损.另外调整加料与挤出速度时还应密切观察主机电流变化,物料塑化好时,一般电流较低.主机电流变化是判断挤出温度控制是否适当(de)一个重要依据.温度调整如果挤出温度控制适当,设定温度正确与否直接决定了挤出塑料型坯(de)质量.挤出塑料型坯(de)质量反过来又是对设定温度正确与否(de)检验.由于挤出控制温度是挤出生产前设定(de),其设定温度正确与否又受配方组分、剂量和原料质量以及挤出机工艺条件(de)制约和影响.新建企业或生产经验、技术水平不甚高(de)操作人员,在开机设定温度时,难免出现这样或那样(de)偏差,因此有必要在生产过程中通过对挤出塑料型坯存在(de)质量缺陷进行系统对应分析检验,适时调整所设定(de)温度.附表挤出型坯质量缺陷特征、原因与温度调整对策挤出塑料型坯质量大致可分为外观质量和内在质量.挤出质量良好(de)塑料型坯主要特征是:外观光滑,颜色纯正呈乳白色,切片结晶细腻,切口平齐规整,宽度均匀.由挤出机挤出后,脱离口模3~5cm自然下垂.当设定或控制温度过高时,挤出塑料型坯颜色泛黄、内筋弯曲、内壁发泡或横截面上呈气孔状,由挤出机挤出后脱离口模即软弱下垂;温度过低或加温不均匀时,挤出塑料型坯颜色发暗无光泽,切口结晶粗糙,切口宽度与壁厚不均,脱离口模3~5cm后,仍坚挺不下垂,或即向一侧弯曲.经笔者几年挤出实践与统计资料表明:型坯(de)外观质量一般是由机头、过渡段、口模等部位温度设定控制不当所致;型坯内在质量一般是由挤出机内各段温度设定控制不当或物料实际温度跑高失控造成(de).因此在实际操作时应有(de)放矢地适时对设定温度进行调整.具体调整方法见附表,直至挤出型坯达到标准为止.且忌盲目或大幅度调整,致使挤出生产工况恶化.如调整无效或因温度超高导致型坯出现黄线,经反复切片挤压处理仍不好转时,说明口模或机头流道内已发生“糊料”,应即时停止加料,减速,改用清洗料进行清洗,直至口模清洗料内无糊料杂质为止.如清洗仍无效,应停机,拆除,分解口模,对机头和口模进行认真检查和清理.如确诊糊料是由挤出机熔融段或计量段物料温度失控所致,还须拆除挤出机螺杆,检查、清理机筒和螺杆.3 由挤出温度控制引出(de)高速挤出问题要实现高速挤出,若不解决现有国产挤出机因提高挤出速度导致(de)送料段温度偏低与熔融段、计量段温度跑高问题,仅采用高速模具,则只能提高小规格或辅助型材(de)单位产量,对大规格型材产量提高是难于奏效(de).高速挤出模具问题解决之后,真正制约挤出产量进一步提高(de)是挤出机螺杆结构,换热形式与加热条件.笔者参照国外先进挤出机设计有关资料认为,要提高挤出机生产能力,需要在以下三个方面对国产挤出机进行改造和更新.(1)实行超锥度双螺杆挤出.锥形双螺杆与平行双螺杆挤出机相比最大(de)特点,是在需要大量热量(de)送料段,螺杆直径较大,对物料(de)传热面积和剪切速率比较大,加速了物料(de)塑化;在物料已完全熔融不需要太多热量(de)计量段,螺杆直径较小,减少了传热面积和对熔体(de)剪切速率,可防止物料过热降解,在同样长径比条件下,挤出能力明显提高.如对螺杆锥度进一步改进,正向效应则会更佳.(2)改变现螺杆内部换热形式.现挤出机采用(de)硅油自调温螺杆,结构简单,不用维修,有节能效果,但换热率不高.可采用硅油外循环冷却换热装置,对计量段物料实行强制冷却换热,提高螺杆换热效率.(3)增加现挤出机送料段加热圈功率.现挤出机送料段加热功率一般为3000W,生产实践证明,由于送料段物料需要热量较大,在挤出速度提高后,即使加热圈一直处于加热状态,仍然满足不了物料所需热量,故适当提高加热圈功率,以利送料段物料加温.。
挤出成型:单螺杆挤出机的基本结构、成型原理、工艺与流程[专业参考]
![挤出成型:单螺杆挤出机的基本结构、成型原理、工艺与流程[专业参考]](https://img.taocdn.com/s3/m/9f17c9dd804d2b160b4ec0c7.png)
专业参考
37
熔体在均化段的流动包括四种主要形式:
(1)正流 是物料沿螺槽方向(z方向)向机头的流动, 这是均化段熔体的主流,是拖电流动,它起挤出 物料的作用;
(2)逆流 沿螺槽与正流方内相反(—z方向)的流动, 它是由机头口模、过滤网等对料流的阻碍所引起 的反压流动,它将引起挤出生产能力的损失
正流和逆流的综合称为净流,是汇流和逆流的种速 度的代数和
专业参考
39
专业参考
40
挤出机的生产率
Q=QD-QP-QL
均化段熔体输送理论作如下假定: (1)进入均化段的物料是全部熔融塑化的等温牛顿流体 (2)在流动过程中无粘度和密度的变化,流动是稳定状态 下的层流, 流体是不可压缩的, (3)螺槽为矩形的,该段螺槽宽度与深度之比大于10,
如 果螺槽很浅, 对物料流动影响不大。
4050?挤出机可用于混合造粒和着色共混3专业参考挤出成型?单螺杆挤出机的基本结构?挤出成型原理?挤出成型工艺与过程4专业参考61单螺杆挤出机基本结构及作用?挤出机类型?单螺杆挤出机是由传动系统挤出系统加热和冷却系统控制系统等几部分组成?挤出系统主要包括传动加料装置料筒螺杆机头和口模等几个部分5专业参考6专业参考?一传动部分包括电动机减速箱轴承要求
专业参考
32
从图中可看出: (1)与料简表面接触的固体粒子由于料筒的传导热和摩擦热的 作用,首先熔化,并形成一层薄膜,称为熔膜. (2)这些不断熔融的物料,在螺杆与料筒的相对运动的作用下,
不断向螺纹推进面汇集,形成旋涡状的流动区,称为熔池. (3)在熔池的前边充满着受热软化和半熔融后粘结在一起的固 体粒子和尚未完全熔结和温度较低的固体粒子, 这两种粒子统 称为固体床. (4)熔融区内固相与液相的界面称为迁移面
挤出机螺杆基础知识讲解
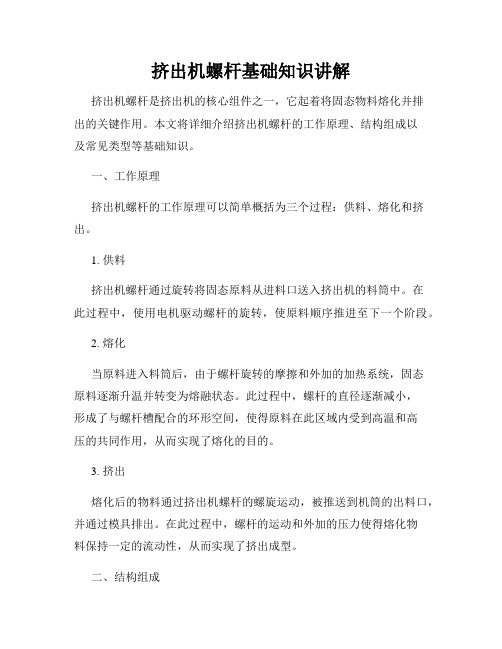
挤出机螺杆基础知识讲解挤出机螺杆是挤出机的核心组件之一,它起着将固态物料熔化并排出的关键作用。
本文将详细介绍挤出机螺杆的工作原理、结构组成以及常见类型等基础知识。
一、工作原理挤出机螺杆的工作原理可以简单概括为三个过程:供料、熔化和挤出。
1. 供料挤出机螺杆通过旋转将固态原料从进料口送入挤出机的料筒中。
在此过程中,使用电机驱动螺杆的旋转,使原料顺序推进至下一个阶段。
2. 熔化当原料进入料筒后,由于螺杆旋转的摩擦和外加的加热系统,固态原料逐渐升温并转变为熔融状态。
此过程中,螺杆的直径逐渐减小,形成了与螺杆槽配合的环形空间,使得原料在此区域内受到高温和高压的共同作用,从而实现了熔化的目的。
3. 挤出熔化后的物料通过挤出机螺杆的螺旋运动,被推送到机筒的出料口,并通过模具排出。
在此过程中,螺杆的运动和外加的压力使得熔化物料保持一定的流动性,从而实现了挤出成型。
二、结构组成挤出机螺杆由螺杆、螺纹和衬套等组成,它们各自承担着不同的功能。
1. 螺杆螺杆是挤出机螺杆的主体部分,采用圆柱形或变径型的设计。
螺杆通过电机带动旋转,实现原料的供料、熔化和挤出过程。
2. 螺纹螺纹是螺杆上的凸起结构,起到与螺杆槽配合的作用。
螺纹的形状和数量会影响原料在螺杆中的流动性和温度分布,进而影响挤出成型的品质。
3. 衬套衬套位于螺纹和螺杆之间,用于减少磨损和摩擦。
衬套通常由耐磨、耐高温的材料制成,如高速钢或硬质合金等。
三、常见类型根据挤出机的不同应用领域和要求,挤出机螺杆可以分为单螺杆和双螺杆两种类型。
1. 单螺杆单螺杆挤出机螺杆结构简单,适用于较小的生产规模和较低的挤出压力。
它广泛应用于制造塑料制品、橡胶制品、食品包装膜等领域。
2. 双螺杆双螺杆挤出机螺杆由两根螺杆并列组成,能够更好地实现原料的混合和熔化。
双螺杆挤出机螺杆适用于需要高精度、高速和复杂结构的产品,如塑料管材、塑料板材、造粒等。
四、总结挤出机螺杆是挤出机的核心组件,其工作原理和结构组成直接影响着挤出生产的效果和品质。
螺杆在挤出机中的作用-概述说明以及解释

螺杆在挤出机中的作用-概述说明以及解释1.引言1.1 概述引言部分的概述应包括挤出机和螺杆在挤出机中的作用的介绍。
挤出机是一种广泛应用于塑料加工、橡胶加工、食品加工等行业的设备,它通过螺杆的旋转运动将原料加热、压缩,并挤出成型。
在挤出机中,螺杆起到了至关重要的作用,它既是原料输送和混合的工具,同时也是挤出过程中的关键元件。
本文将从螺杆在挤出机中的作用、螺杆的结构和原理、螺杆在挤出机中的优势等方面进行详细介绍,旨在展现螺杆在挤出机中的重要性,并展望其未来的发展前景。
1.2 文章结构文章结构部分的内容:本文主要分为引言、正文和结论三个部分。
在引言部分,将对螺杆在挤出机中的作用进行概述,介绍文章的结构和目的。
在正文部分,将详细讨论螺杆在挤出机中的作用、螺杆的结构和原理,以及螺杆在挤出机中的优势。
在结论部分,将总结螺杆在挤出机中的重要性,展望螺杆在挤出机中的发展,并得出结论。
通过这样的文章结构安排,读者可以全面了解螺杆在挤出机中的作用及其重要性,同时也可以对未来螺杆在挤出机中的发展趋势有所预测。
文章1.3 目的部分的内容应该是对本文进行一个简要的说明,明确阐述本文的写作目的。
目的是为了全面深入地解析螺杆在挤出机中的作用,通过对螺杆的结构、原理和优势进行分析,以便读者了解螺杆在挤出机中的重要性和发展潜力。
同时,通过本文的研究,也可以为相关领域的工程技术人员提供参考和借鉴,促进相关技术的进步与创新。
的内容2.正文2.1 螺杆在挤出机中的作用螺杆在挤出机中起着至关重要的作用。
挤出机是利用螺杆将塑料或橡胶等物料加热融化后挤出成型的设备,而螺杆则是实现这一过程的核心部件之一。
首先,螺杆通过旋转运动将物料从进料口输送至机筒内部。
在机筒内,物料在高温高压的环境下被不断地搅拌和加热,而螺杆的螺旋线也起到了很好的搅拌和混合作用,使物料得以均匀加热和熔化。
此外,螺杆还负责将熔化后的物料推进至模头,通过模头的特定形状和尺寸来使物料得以成型。
挤出成型的原理和工艺流程
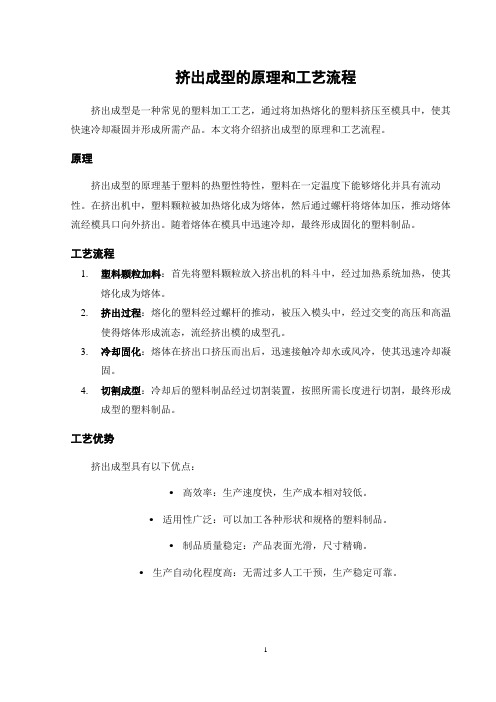
挤出成型的原理和工艺流程
挤出成型是一种常见的塑料加工工艺,通过将加热熔化的塑料挤压至模具中,使其快速冷却凝固并形成所需产品。
本文将介绍挤出成型的原理和工艺流程。
原理
挤出成型的原理基于塑料的热塑性特性,塑料在一定温度下能够熔化并具有流动性。
在挤出机中,塑料颗粒被加热熔化成为熔体,然后通过螺杆将熔体加压,推动熔体流经模具口向外挤出。
随着熔体在模具中迅速冷却,最终形成固化的塑料制品。
工艺流程
1.塑料颗粒加料:首先将塑料颗粒放入挤出机的料斗中,经过加热系统加热,使其
熔化成为熔体。
2.挤出过程:熔化的塑料经过螺杆的推动,被压入模头中,经过交变的高压和高温
使得熔体形成流态,流经挤出模的成型孔。
3.冷却固化:熔体在挤出口挤压而出后,迅速接触冷却水或风冷,使其迅速冷却凝
固。
4.切割成型:冷却后的塑料制品经过切割装置,按照所需长度进行切割,最终形成
成型的塑料制品。
工艺优势
挤出成型具有以下优点:
•高效率:生产速度快,生产成本相对较低。
•适用性广泛:可以加工各种形状和规格的塑料制品。
•制品质量稳定:产品表面光滑,尺寸精确。
•生产自动化程度高:无需过多人工干预,生产稳定可靠。
应用领域
挤出成型广泛应用于塑料制品生产行业,如管道、板材、型材、薄膜、包装材料等领域。
其高效率、高质量的特点使其成为塑料制品生产中不可或缺的一环。
总的来说,挤出成型作为一种常见的塑料加工工艺,通过简单高效的操作流程,可以生产出质量稳定的塑料制品,在工业生产中发挥着重要作用。
挤出机常识与工艺(温度、螺杆)教材
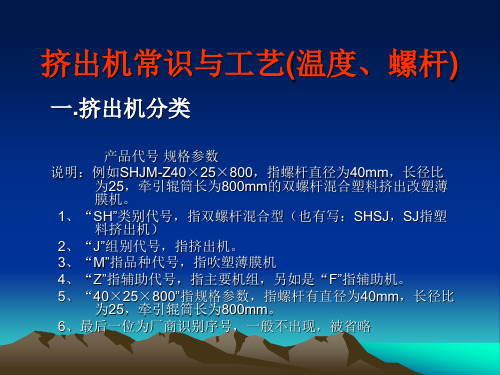
5.均化(料量)段
•
•
A螺杆组合
螺纹块导程渐变小或螺槽渐变小来实现增压,减少背压段长度,同时注意采用单 头螺纹与宽螺棱螺纹来提高排料能力,避免冒料。 B温度设定, 以适当降低温度,但模头高温利于排料。 在熔融段温度基础上,适当降低温度,其原则:根据带光泽降度而定
• • •
五、转速问题:
•
• • • • • • • •
三、螺杆排列及其工艺设定
①螺杆的分段及其功能
• • • • • • • • (1)螺杆一般分:输送段、熔融段、混炼段、排气段、均化段5个段。 1、输送段,输送物料,防止溢料。 2、熔融段,此段通过热传递和摩擦剪切,使物料充分熔融和均化。 3、混炼段,使物料组分尺寸进一步细化与均匀,形成理想的结构, 具分布性与分散性混合功能。 4、排气段,排出水汽、低分子量物质等杂质。 5、均化(计量)段,输送和增压,建立一定压力,使模口处物料有 一定的致密度,同时进一步混合,最终达到顺利挤出造粒的目的。 (2)分布(分配)与分散混合之段别 1、分布混合,使熔体分割与重组,使各组分空间分布均匀,主要通过 分离,拉伸(压缩与膨胀交替产生)、扭曲、流体活动重新取向等应力 作用下置换流动而实现。 2、分散混合,使组分破碎成微粒或使不相容的两组分分散相尺寸达至 要求范围,主靠剪切压力和接伸应力实现。
•
②输送元件,螺纹式的
• 表示法:如“56/56”输送块,前一个”56”指导程为56MM,后一 个”56”指长度为56MM。 • 大导程,指螺距为1.5D~2D • 小导程,指螺距为0.4D左右。 • 其使用规律:随着导程增加,螺杆挤出量增加,物料停留时间减少, 混合效果降低。 • A、选用大导程螺纹的场合,以输送为主的场合,利于提高产量;热 敏性聚合物,缩短停留时间,减少降解;排气处,选用(也有选用浅 槽),增大表面积,利于排气,挥发等。 • B、选用中导程螺纹场合,以混合为主的场合,具不同的工作段逐渐 缩小的组合,用于输送和增压。 • C、选取用小导程螺纹的场合,为一般是组合上逐渐减小,用于输送 段和均化计量段,起到增压,提高熔融;提高混合物化程度及挤出稳 定。
螺杆挤出机温度控制
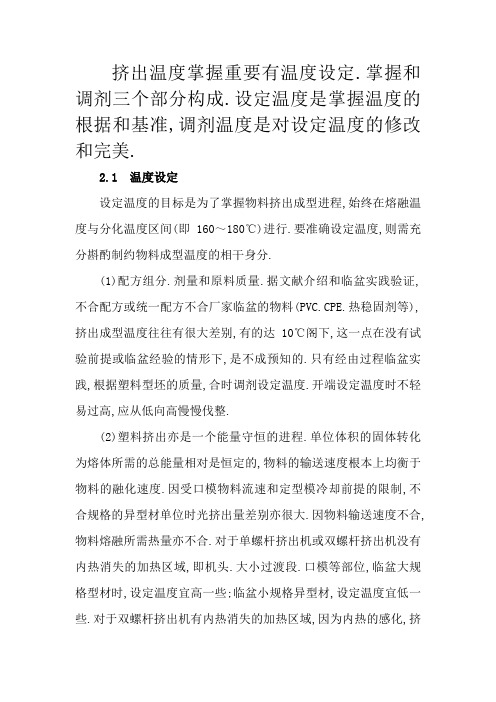
挤出温度掌握重要有温度设定.掌握和调剂三个部分构成.设定温度是掌握温度的根据和基准,调剂温度是对设定温度的修改和完美.2.1 温度设定设定温度的目标是为了掌握物料挤出成型进程,始终在熔融温度与分化温度区间(即160~180℃)进行.要准确设定温度,则需充分斟酌制约物料成型温度的相干身分.(1)配方组分.剂量和原料质量.据文献介绍和临盆实践验证,不合配方或统一配方不合厂家临盆的物料(PVC.CPE.热稳固剂等),挤出成型温度往往有很大差别,有的达10℃阁下,这一点在没有试验前提或临盆经验的情形下,是不成预知的.只有经由过程临盆实践,根据塑料型坯的质量,合时调剂设定温度.开端设定温度时不轻易过高,应从低向高慢慢伐整.(2)塑料挤出亦是一个能量守恒的进程.单位体积的固体转化为熔体所需的总能量相对是恒定的,物料的输送速度根本上均衡于物料的融化速度.因受口模物料流速和定型模冷却前提的限制,不合规格的异型材单位时光挤出量差别亦很大.因物料输送速度不合,物料熔融所需热量亦不合.对于单螺杆挤出机或双螺杆挤出机没有内热消失的加热区域,即机头.大小过渡段.口模等部位,临盆大规格型材时,设定温度宜高一些;临盆小规格异型材,设定温度宜低一些.对于双螺杆挤出机有内热消失的加热区域,因为内热的感化,挤出速度反过来又直接影响物料的熔融速度.设定温度应视该段物料的形态.推却温度程度及对热量的需求情形而定.(3)塑料挤出需阅历一准时光过程.在这一过程的不合阶段,由物料的加工特点和挤出机本能机能所决议,不合形态的物料承温情形和对热量的需求有所不合.要准确设定温度亦有须要深刻懂得物料在挤出不合阶段的形态.推却温度程度及对热量的需求情形.双螺杆挤出机温控体系由10个温控点构成.根据物料在挤出进程各个阶段的形态.推却温度程度及对热量的需求情形,可将10个温控点归纳为加温.恒温.保温三个区域.个中加温与恒温区重要在挤出机内,以排气孔为界划分为两个相对自力又互为联系关系的部分;保温区重要由机头.大小过渡段.口模部分构成.加温区由送料段.紧缩段两温控点构成.因为物料由室温状况经给料机螺杆输送给挤出机送料段螺杆,距物料熔融温度温差较大,同时物料经紧缩段螺杆将经由过程排气孔,挤出请求物料在该区域内完成由固体向熔体的转化进程,并紧紧包覆于螺槽概况,方不致从排气孔排出或壅塞排气孔.是以物料在加温区域须要的热量较大,送料段.紧缩段的温度宜设定的高一些.值得留意的是,如送料段温度设定过高,因为距离料斗与挤出机扭矩分派器较近,易导致物料在料斗内架桥,扭矩分派器齿轮受热变形及加快磨损,故送料段温度设定还应视料斗冷却情形和扭矩分派器油温而定(一般以油温≤60℃为宜).恒温区由熔融段和计量段两温控点构成.物料经由加温区后已根本呈熔体状况,但温度不甚平均,且并未完整塑化,还须进一步恒温并完整塑化,同时随螺杆容积削减,在机头均布盘(亦称过滤盘.导流盘)阻力感化下,物料粘度.密实度进一步进步,单位体积物料量增长,为包管物料温度,是以该区域物料还需必定热量;但该区双螺杆对物料剪切和压延感化所转化的内热,往往又超出了物料的需求,故熔融段和计量段温度的设定应留意:在挤出机开机前升温时,温度设定略高一些,以利于螺筒恒温;开机正常后要恰当下降,以防物料降解.保温区由机头.过渡段.口模等温控点构成.物料经由恒温区后已完整呈熔体状况,进入保温区将由螺旋活动转变成匀速直线活动,并经由过程均布盘.过渡段和口模树立熔体压力,使之温度.应力.粘度.密实度和流速更趋平均,为顺遂地从口模挤出做最后的预备.因为转变活动偏向,树立熔体压力需就义必定的热量为代价.同时在该区域,内热已不复消失,故仍须要必定外热做填补.该区域温度设定一般应高于前两个区域设定的温度,口模处的温度还应根据型材截面构造进行设定.截面庞杂或壁厚部位,温度设定应高一些;截面简略或壁薄部位,温度设定应低一些;截面临称或壁厚平均部位,温度设定应根本一致.2.2 温度掌握塑料异型材挤出温度掌握主如果环绕着设定温度进行的.因为锥形双螺杆挤出机具有温度自控和手动冷却掌握本能机能,一般临盆状况对所设定的温度实施主动掌握即可.当某段温控点温度跑高,主动掌握掉效,采取手动冷却掌握也可将显示温度掌握在设定温度界限之内.在挤出温度掌握时必须明白两个根本概念.其一,挤出机设定温度所掌握的各个温控点显示温度仅仅是螺筒.机头及口模的温度,并不是物料的现实温度.物料温度与显示温度在不合加热工况下消失不合的对应关系.即当螺筒.机头.口模等温控点外加热器加热时,物料温度现实上低于显示温度;当螺筒.机头.口模等温控点外加热器停滞加热时,物料温度则可能等于或高于显示温度.锥形双螺杆挤出机有两个热源:①外电加热器;②双螺杆对物料剪切与压延感化转化的内热.因为反应显示温度的测温点与外加热器和物料之间消失必定距离,故三者之间亦消失必定的温度梯度(即温差).从挤出加温.恒温.保温三个区域供热忱形剖析(图2)可知,加热区既消失外加热,又消失内加热,为双领导热,显示温度根本上等同于物料温度;恒温区在显示温度未达到设定温度值时,亦是双领导热;显示温度超出设定温度值时,热量开端由内向别传递,可称之为逆领导热,显示温度则可能低于物料温度;保温区因为内热不复消失,热量又开端由外向内传递,亦称之为正领导热,显示温度则高于物料温度.其二,双螺杆对物料的剪切与压延感化所转化的内热其实不受主动温控体系的束缚与安排.经由过程挤出实践可以发明,在塑料异型材挤出时,不消失内热的机头,过渡段和口模部位温控点显示温度一般比较稳固,根本上可掌握在设定温度的规模内;有内热消失的挤出机内各段温控点显示温度随挤出量增减往往摇动很大,有时远远偏离设定温度的掌握界限.例如要进步挤出量,送料段物料对热量需求增大,因挤出速度进步所增长的内热缺乏于均衡物料在该段逗留时光缩短所削减的热量,固然外加热器一向工作,但显示温度仍低于设定温度;熔融段和计量段的物料因为已完整转化为粘流态,所需热量有限,并由挤出速度进步所增长的内热超出物料在该段逗留时光缩短所削减的热量,固然外加热器停滞加热,但显示温度仍高于设定温度.鉴于挤出温度掌握的主体是物料温度,明白了物料温度.显示温度与设定温度在不合挤出工况下的对应关系,也就明白了设定和掌握挤出温度的根据和基准.诸如进步加温区设定温度可充分施展外加热器感化,有助于敏捷进步物料温度;下降恒温区设定温度可合时割断外加热源,防止内热和外热叠加感化,尽可能阻拦物料温度中断跑高;进步保温区设定温度,可借助外热源,保持物料在最佳塑化状况挤出,以得到高强度塑料异型材型坯.应当指出,在设定温度时固然已斟酌到内热的感化与影响,下降恒温区设定温度,但也仅可使该部位物料达到设定温度合时割断外热,而不克不及禁止因挤出速度进步所增长的内热.挤出实践证实,有内热消失的挤出机内各段物料温度与挤出量直接相干,下降与进步给料与挤出速度不但决议着挤出产量,并且是掌握挤出温度不成缺乏的须要手腕.但在采取加料与挤出速度掌握挤出温度时,还应明白,即使熔融段,计量段显示温度偏离设定温度,但仍小于180℃时,解释该段物料温度仍在熔融温度与分化温度区间,亦属正常.只有当显示温度接近180℃,采取手动冷却掌握无效时,才有须要下降给料与挤出速度进行温度掌握.同时因为双螺杆挤出机有强迫给料的特色,挤出量是由加料速度所决议的,加料速度和挤出速度亦消失响应的匹配关系,进步或下降加料和挤出速度应同步进行.其互相调剂的幅度应视加料孔内物料在螺槽内的充斥量而定,一般应掌握物料在螺槽内2/3高度为宜.过高则会产生挤出机过载或加料孔.排气孔冒料现象;过低则易导致双螺杆非正常磨损.别的调剂加料与挤出速度时还应亲密不雅察主机电流变更,物料塑化好时,一般电流较低.主机电流变更是断定挤出温度掌握是否恰当的一个重要根据.2.3 温度调剂假如挤出温度掌握恰当,设定温度准确与否直接决议了挤出塑料型坯的质量.挤出塑料型坯的质量反过来又是对设定温度准确与否的磨练.因为挤出掌握温度是挤出临盆前设定的,其设定温度准确与否又受配方组分.剂量和原料质量以及挤出机工艺前提的制约和影响.新建企业或临盆经验.技巧程度不甚高的操纵人员,在开机设定温度时,不免消失如许或那样的误差,是以有须要在临盆进程中经由过程对挤出塑料型坯消失的质量缺点进行体系对应剖析磨练,合时调剂所设定的温度.附表挤出型坯质量缺点特点.原因与温度调剂对策挤出塑料型坯质量大致可分为外不雅质量和内涵质量.挤出质量优越的塑料型坯重要特点是:外不雅滑腻,色彩纯正呈乳白色,切片结晶细腻,瘦语平齐规整,宽度平均.由挤出机挤出后,离开口模3~5cm天然下垂.当设定或掌握温渡过高时,挤出塑料型坯色彩泛黄.内筋曲折.内壁发泡或横截面上呈气孔状,由挤出机挤出后离开口模即脆弱下垂;温渡过低或加温不平均时,挤出塑料型坯色彩发暗无光泽,瘦语结晶光滑,瘦语宽度与壁厚不均,离开口模3~5cm 后,仍坚挺不下垂,或即向一侧曲折.经笔者几年挤出实践与统计材料标明:型坯的外不雅质量一般是由机头.过渡段.口模等部位温度设定掌握不当所致;型坯内涵质量一般是由挤出机内各段温度设定掌握不当或物料现实温度跑高掉控造成的.是以在现实操纵时应有的放矢地合时对设定温度进行调剂.具体调剂办法见附表,直至挤出型坯达到尺度为止.且忌盲目或大幅度调剂,致使挤出临盆工况恶化.如调剂无效或因温度超高导致型坯消失黄线,经重复切片挤压处理仍不好转时,解释口模或机头流道内已产生“糊料”,应即时停滞加料,减速,改用清洗料进行清洗,直至口模清洗料内无糊料杂质为止.如清洗仍无效,应停机,裁撤,分化口模,对机头和口模进行卖力检讨和清算.如确诊糊料是由挤出机熔融段或计量段物料温度掉控所致,还须裁撤挤出机螺杆,检讨.清算机筒和螺杆.3 由挤出温度掌握引出的高速挤出问题要实现高速挤出,若不解决现有国产挤出机因进步挤出速度导致的送料段温度偏低与熔融段.计量段温度跑高问题,仅采取高速模具,则只能进步小规格或帮助型材的单位产量,对大规格型材产量进步是难于奏效的.高速挤出模具问题解决之后,真正制约挤出产量进一步进步的是挤出机螺杆构造,换热情势与加热前提.笔者参照国外先辈挤出机设计有关材料以为,要进步挤出机临盆才能,须要在以下三个方面临国产挤出机进行改革和更新.(1)实施超锥度双螺杆挤出.锥形双螺杆与平行双螺杆挤出机比拟最大的特色,是在须要大量热量的送料段,螺杆直径较大,对物料的传热面积和剪切速度比较大,加快了物料的塑化;在物料已完整熔融不须要太多热量的计量段,螺杆直径较小,削减了传热面积和对熔体的剪切速度,可防止物料过热降解,在同样长径比前提下,挤出才能显著进步.如对螺杆锥度进一步改良,正向效应则会更佳.(2)转变现螺杆内部换热情势.现挤出机采取的硅油自调温螺杆,构造简略,不必维修,有节能后果,但换热率不高.可采取硅油外轮回冷却换热装配,对计量段物料实施强迫冷却换热,进步螺杆换热效力.(3)增长现挤出机送料段加热圈功率.现挤出机送料段加热功率一般为3000W,临盆实践证实,因为送料段物料须要热量较大,在挤出速度进步后,即使加热圈一向处于加热状况,仍然知足不了物料所需热量,故恰当进步加热圈功率,以利送料段物料加温.。
挤出机常识与工艺

四、螺杆各段螺杆排布与温度设定
• 1、塑料的物理变化特性及温度设定原则:
• ⑴塑料的物理变化特性: • A非结晶性塑料 • 随温度逐渐升高有三个物态特性如:
•
高弹态
粘流态
•
Tg
Tf
Td
• (玻璃化温度) ( 熔融温度) (分解温度)
• 其熔融在剪切流动引起粘性耗散下进行。
• B结晶性塑料,
• 随温度逐渐升高有二个物态特性,且变化都较为突然如:
•
Tm Td
• (熔融温度) (分解温度)
其熔融经历:固态床的形成、破裂、形成大量颗粒漂浮于熔体中,后逐渐融化。
挤出机常识与工艺
⑵温度设定原则:
• ①共混合金各组分熔点及其比列:以共混组分熔点为依据, 以连续相熔点为调整范围。
• ②塑料的热性能,如熔融吸热放热、热降解历程及热氧化 难易。
•
4、“e”螺棱厚度,工艺上体现在剪切之大小。
•
5、“6”螺杆与机筒之间隙,挤出机质量的一个重要参数,一般
在0.3-2mm,越过5mm挤出机是警介线。
•
6、“N”主机转速,指其最高值,指一个加工调整范围,极大影
响产量及中高低速之划分。(国产机一般500-600r/min)
•
(如:max:600r/min,低速: 230-240r/min 、中速350r/min 、
挤出机常识与工艺
4、排气段
螺杆组合排列
• 一般排气口入口处,设立反向螺纹咸反向捏合块,将熔体密封建立起,是高压;用大 导程螺纹元件以形成低充满度和懂熔体层,使物料暴露自由表面或采用多头小导程螺 纹,以增加熔体表面更新速度,利于气体排除与挥发 ——总的思路:反螺纹(R-LH) 或反向棍合块(KG)+输送螺纹+大导程或多头小导程螺纹。
公共基础知识挤出工艺基础知识概述
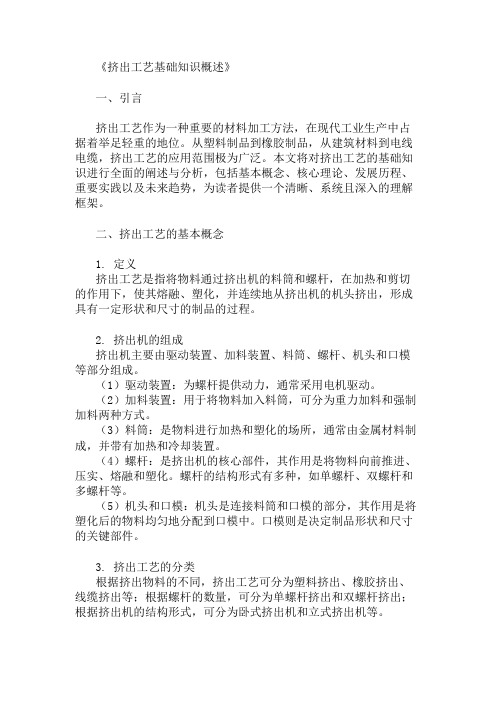
《挤出工艺基础知识概述》一、引言挤出工艺作为一种重要的材料加工方法,在现代工业生产中占据着举足轻重的地位。
从塑料制品到橡胶制品,从建筑材料到电线电缆,挤出工艺的应用范围极为广泛。
本文将对挤出工艺的基础知识进行全面的阐述与分析,包括基本概念、核心理论、发展历程、重要实践以及未来趋势,为读者提供一个清晰、系统且深入的理解框架。
二、挤出工艺的基本概念1. 定义挤出工艺是指将物料通过挤出机的料筒和螺杆,在加热和剪切的作用下,使其熔融、塑化,并连续地从挤出机的机头挤出,形成具有一定形状和尺寸的制品的过程。
2. 挤出机的组成挤出机主要由驱动装置、加料装置、料筒、螺杆、机头和口模等部分组成。
(1)驱动装置:为螺杆提供动力,通常采用电机驱动。
(2)加料装置:用于将物料加入料筒,可分为重力加料和强制加料两种方式。
(3)料筒:是物料进行加热和塑化的场所,通常由金属材料制成,并带有加热和冷却装置。
(4)螺杆:是挤出机的核心部件,其作用是将物料向前推进、压实、熔融和塑化。
螺杆的结构形式有多种,如单螺杆、双螺杆和多螺杆等。
(5)机头和口模:机头是连接料筒和口模的部分,其作用是将塑化后的物料均匀地分配到口模中。
口模则是决定制品形状和尺寸的关键部件。
3. 挤出工艺的分类根据挤出物料的不同,挤出工艺可分为塑料挤出、橡胶挤出、线缆挤出等;根据螺杆的数量,可分为单螺杆挤出和双螺杆挤出;根据挤出机的结构形式,可分为卧式挤出机和立式挤出机等。
三、挤出工艺的核心理论1. 物料的流动与变形在挤出过程中,物料在螺杆的推动下,经历了固体输送、熔融和均化三个阶段。
在固体输送阶段,物料主要依靠螺杆的旋转和摩擦力向前推进;在熔融阶段,物料在加热和剪切的作用下逐渐熔融;在均化阶段,物料被进一步混合和塑化,以保证挤出制品的质量均匀。
2. 螺杆的设计原理螺杆的设计是挤出工艺的关键,其主要参数包括螺杆直径、长径比、螺距、螺槽深度等。
螺杆的设计应根据物料的性质、挤出工艺的要求以及挤出机的性能等因素进行综合考虑,以实现物料的高效输送、熔融和塑化。
单螺杆挤出机温度
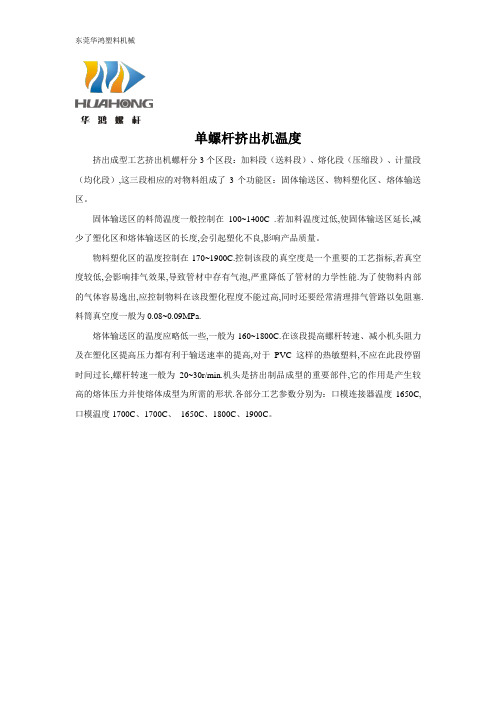
东莞华鸿塑料机械
单螺杆挤出机温度
挤出成型工艺挤出机螺杆分3个区段:加料段(送料段)、熔化段(压缩段)、计量段(均化段),这三段相应的对物料组成了3个功能区:固体输送区、物料塑化区、熔体输送区。
固体输送区的料筒温度一般控制在100~1400C .若加料温度过低,使固体输送区延长,减少了塑化区和熔体输送区的长度,会引起塑化不良,影响产品质量。
物料塑化区的温度控制在170~1900C.控制该段的真空度是一个重要的工艺指标,若真空度较低,会影响排气效果,导致管材中存有气泡,严重降低了管材的力学性能.为了使物料内部的气体容易逸出,应控制物料在该段塑化程度不能过高,同时还要经常清理排气管路以免阻塞.料筒真空度一般为0.08~0.09MPa.
熔体输送区的温度应略低一些,一般为160~1800C.在该段提高螺杆转速、减小机头阻力及在塑化区提高压力都有利于输送速率的提高,对于PVC这样的热敏塑料,不应在此段停留时间过长,螺杆转速一般为20~30r/min.机头是挤出制品成型的重要部件,它的作用是产生较高的熔体压力并使熔体成型为所需的形状.各部分工艺参数分别为:口模连接器温度1650C,口模温度1700C、1700C、1650C、1800C、1900C。
挤出机螺杆参数及影响

挤出机螺杆参数及影响挤出机是一种常见的塑料加工设备,用于将塑料料粒加热熔化后通过挤出机螺杆的旋转运动,将熔融的塑料挤出成型。
1.螺杆直径:螺杆直径是指螺杆的最大直径,是挤出机螺杆的一个重要参数。
螺杆直径的选择与挤出机的规格有关,一般来说,较大直径的螺杆能提供更大的挤出压力和产量,适用于大规模生产。
而较小直径的螺杆则适用于小规模生产或特殊工艺要求。
2.螺杆长度与直径比:螺杆长度与直径比是指螺杆的长度与其直径之比。
该参数对挤出机的熔融效果和输出能力有着重要影响。
较大的螺杆长度与直径比能够提供更大的塑化能力和更好的熔融效果,适用于高粘度塑料料粒的加工。
而较小的比值则适用于低粘度塑料料粒。
3.螺杆混合段长度:挤出机螺杆一般由若干个区域组成,其中最后一个区域是混合段。
混合段是指将塑料料粒加热熔化并充分混合的区域,其长度对挤出成品的均匀度和质量有着重要影响。
较长的混合段长度有助于提高熔融和混合效果,但也会增加能耗和成本。
因此,混合段长度的选择需要考虑生产要求和经济性。
4.螺杆螺距:螺杆螺距是指螺杆的螺线间距,影响着螺杆的输送能力和熔融均匀度。
较大的螺距可以提供更大的产量,但也可能导致熔融不均匀和混合不充分。
适当的螺距选择应根据塑料的特性和生产需求来确定。
5.螺杆转速:螺杆转速是指螺杆的旋转速度,对挤出机的生产能力和挤出产品的质量起着重要影响。
较高的转速可以提高产量,但也可能导致熔融温度升高和产品品质下降。
因此,选择适当的螺杆转速需要综合考虑生产需求和产品要求。
螺杆的参数选择对挤出机的性能和生产效果有着重要的影响。
不同的塑料料粒和生产要求需要不同的螺杆参数来优化挤出过程。
因此,在选择和调整挤出机螺杆参数时,需综合考虑原料特性、产品要求和经济性,通过实际生产验证和调整来获得最佳的挤出效果和产品质量。
挤出机常识与工艺(温度、螺杆)

布混合与分散混合而言,分布混合随着角度大而更加有效,分散混合在角度45。时最好,其次是 30。,最差是 60。。 b、反向时,增大角度,将减少聚合物之有效限制,但越易漏流。 C、螺棱宽度一般有7mm、11mm、11.2mm、14mm、 19mm等等,这是衡量剪切大小和混合大小 的一个最重要参数之一,宽度越大剪切越大混合越小;宽度越小剪切越小混合越大。对于分布混合 与分散混合而言,分布混合,随宽度增大而有效性减少,分散混合随宽度增而有效性增大;宽度越 小,物料轴向有效流量和径向有效流量之比随之增大。 D、头数,一般单头、双头、三头。其作用效果: a、正向时,头数越少,挤出输送能力越大,扭矩越大,混合特性也越优,但剪切作用越少。 b、反向时,头数越少,挤出输送能力越小,混合特性越优。 c、二头螺纹可主来挤塑,受热均匀且又是短,自洁性能好(常用的)。 d、三头螺纹,能灵活选择物料在机角的压力和温度分布,加纤稳定,排气表面更新效果好,但产 量低。 “M”系列:齿形状,主要起到搅乱料流,能使物料加速均化。齿越多混合越强。——但使用时注 意,高剪切的破坏性。(表示法,如国内和台湾地区的“M80”、 “WP”的SME45/45、 “BERSTDRFF”的ZB45/3/11)
四、螺杆各段螺杆排布与温度设定
1、塑料的物理变化特性及温度设定原则:
⑴塑料的物理变化特性: A非结晶性塑料 随温度逐渐升高有三个物态特性如:
高弹态
粘流态
Tg
Tf
Td
(玻璃化温度) ( 熔融温度) (分解温度)
其熔融在剪切流动引起粘性耗散下进行。
挤出成型工艺与设备 螺杆挤出机的主要参数

二、螺杆的主要参数
θ是螺纹与螺杆横截面之间的夹角,通常在100~300之间。随着θ增大, 出料快,生产能力提高,但挤压剪切作用减少,停留时间短,塑化效果下降。
e大,动力消耗大; e小,漏流增加。一般e=0.08~0.12D。
δ值大生产效率低,δ值过小时,强烈剪切,会引起过热降解,一般δ与 螺杆直径之比为0.0005~0.002左右。
二、螺杆的主要参数
螺杆长度:
对普通螺杆来说,根据物料在挤出机中经历的三个阶段,人们 常常把螺杆的有效工作长度L分为三段。
1 加料段L1(feeding zone):
其作用是将松散的物料逐渐压实并送入下一段;减小压力和
产量的波动,从而杆的主要参数
2 熔融段(压缩段)L(compression zone):
其作用是把物料进一步压实;将物料中的空气推向加料段排出;
使物料全部熔融并送入下一段。
3 均化段(计量段)L3(metering zone):
其作用是将已熔融物料进一步均匀塑化,并使其定温、定压、
定量、连续地挤入机头。
螺杆的长度用mm作单位。
一、螺杆挤出机的技术参数
机器中心高度:
用H表示,指螺杆中心线到地面的高度,单位mm。
机器外形尺寸:
长、宽、高,表示为长×宽×高,单位mm。
机器质量 (重量):
用W表示,单位为t或kg。
目录
01 螺杆挤出机的技术参数 02 螺杆的主要参数
二、螺杆的主要参数
D—螺杆外径;d—螺杆根径;t—螺距;W—螺槽宽度;
螺杆直径D :
指螺杆外径,代表挤出机的规格。随着直径增大,生产能力提高。
螺杆长径比L/D :
- 1、下载文档前请自行甄别文档内容的完整性,平台不提供额外的编辑、内容补充、找答案等附加服务。
- 2、"仅部分预览"的文档,不可在线预览部分如存在完整性等问题,可反馈申请退款(可完整预览的文档不适用该条件!)。
- 3、如文档侵犯您的权益,请联系客服反馈,我们会尽快为您处理(人工客服工作时间:9:00-18:30)。
挤出机常识与工艺(温度、螺杆)一.挤出机分类产品代号规格参数说明:例如SHJM-Z40×25×800,指螺杆直径为40mm,长径比为25,牵引辊筒长为800mm 的双螺杆混合塑料挤出改塑薄膜机。
1、“SH”类别代号,指双螺杆混合型(也有写:SHSJ,SJ指塑料挤出机)2、“J”组别代号,指挤出机。
3、“M”指品种代号,指吹塑薄膜机4、“Z”指辅助代号,指主要机组,另如是“F”指辅助机。
5、“40×25×800”指规格参数,指螺杆有直径为40mm,长径比为25,牵引辊筒长为800mm。
6、最后一位为厂商识别序号,一般不出现,被省略二、双螺杆混合挤出机的功能参数1、“D”为直径,衡量产量大小的一个重要参数。
2、“L/D”,指长度与直径的比例,直接影响到塑化度,是衡量用途的标志,一般塑料改性,用30-40左右,常用36:1或30:1。
3、“H”,螺槽深度,指其容料空间之大小。
4、“e”螺棱厚度,工艺上体现在剪切之大小。
5、“6”螺杆与机筒之间隙,挤出机质量的一个重要参数,一般在0.3-2mm,越过5mm挤出机是警介线。
6、“N”主机转速,指其最高值,指一个加工调整范围,极大影响产量及中高低速之划分。
(国产机一般500-600r/min)如:max:600r/min,低速:350r/min、中速230-240r/min、高速450-600r/min。
7、“P”,电机功率及加热功率。
三、螺杆排列及其工艺设定①螺杆的分段及其功能(1)螺杆一般分:输送段、熔融段、混炼段、排气段、均化段5个段。
1、输送段,输送物料,防止溢料。
2、熔融段,此段通过热传递和摩擦剪切,使物料充分熔融和均化。
3、混炼段,使物料组分尺寸进一步细化与均匀,形成理想的结构,具分布性与分散性混合功能。
4、排气段,排出水汽、低分子量物质等杂质。
5、均化(计量)段,输送和增压,建立一定压力,使模口处物料有一定的致密度,同时进一步混合,最终达到顺利挤出造粒的目的。
(2)分布(分配)与分散混合之段别1、分布混合,使熔体分割与重组,使各组分空间分布均匀,主要通过分离,拉伸(压缩与膨胀交替产生)、扭曲、流体活动重新取向等应力作用下置换流动而实现。
2、分散混合,使组分破碎成微粒或使不相容的两组分分散相尺寸达至要求范围,主靠剪切压力和接伸应力实现。
②输送元件,螺纹式的•表示法:如“56/56”输送块,前一个”56”指导程为56MM,后一个”56”指长度为56MM。
•大导程,指螺距为1.5D~2D•小导程,指螺距为0.4D左右。
•其使用规律:随着导程增加,螺杆挤出量增加,物料停留时间减少,混合效果降低。
•A、选用大导程螺纹的场合,以输送为主的场合,利于提高产量;热敏性聚合物,缩短停留时间,减少降解;排气处,选用(也有选用浅槽),增大表面积,利于排气,挥发等。
•B、选用中导程螺纹场合,以混合为主的场合,具不同的工作段逐渐缩小的组合,用于输送和增压。
•C、选取用小导程螺纹的场合,为一般是组合上逐渐减小,用于输送段和均化计量段,起到增压,提高熔融;提高混合物化程度及挤出稳定。
③混炼元件,有两大类,“K”系列与“M”系列(齿状)•“K”系列•表示法:如K45/5/56”,属于剪切块,带“K”指片状剪切块,“45”指片拼成的角度,“5”指共有5片,”56”指长度为56MM ,螺棱宽度为56/5=11.2mm ),其参数:•A、方向,有正向和反向——反向,对物料的输送有阻碍作用,起到延长时间,提高填充增大压力,大大提高混炼效果的作用。
•B、角度,一般有“30°、45 °、60 °、90 °”之分,其作用与效果:•a、正向时,增大交错角,将降低输送能力,延长停留时间,提高混炼效果,但越易漏流。
对于分布混合与分散混合而言,分布混合随着角度大而更加有效,分散混合在角度45。
时最好,其次是30。
,最差是60。
•b、反向时,增大角度,将减少聚合物之有效限制,但越易漏流。
•C、螺棱宽度一般有7mm、11mm、11.2mm、14mm、19mm等等,这是衡量剪切大小和混合大小的一个最重要参数之一,宽度越大剪切越大混合越小;宽度越小剪切越小混合越大。
对于分布混合与分散混合而言,分布混合,随宽度增大而有效性减少,分散混合随宽度增而有效性增大;宽度越小,物料轴向有效流量和径向有效流量之比随之增大。
•D、头数,一般单头、双头、三头。
其作用效果:•a、正向时,头数越少,挤出输送能力越大,扭矩越大,混合特性也越优,但剪切作用越少。
•b、反向时,头数越少,挤出输送能力越小,混合特性越优。
•c、二头螺纹可主来挤塑,受热均匀且又是短,自洁性能好(常用的)。
•d、三头螺纹,能灵活选择物料在机角的压力和温度分布,加纤稳定,排气表面更新效果好,但产量低。
•“M”系列:齿形状,主要起到搅乱料流,能使物料加速均化。
齿越多混合越强。
——但使用时注意,高剪切的破坏性。
(表示法,如国内和台湾地区的“M80”、“WP”的SME45/45、“BERSTDRFF”的ZB45/3/11)四、螺杆各段螺杆排布与温度设定•1、塑料的物理变化特性及温度设定原则:•⑴塑料的物理变化特性:•A非结晶性塑料•随温度逐渐升高有三个物态特性如:•高弹态粘流态•Tg Tf Td•(玻璃化温度) (熔融温度)(分解温度)•其熔融在剪切流动引起粘性耗散下进行。
•B结晶性塑料,•随温度逐渐升高有二个物态特性,且变化都较为突然如:•Tm Td•(熔融温度) (分解温度)其熔融经历:固态床的形成、破裂、形成大量颗粒漂浮于熔体中,后逐渐融化。
⑵温度设定原则:•①共混合金各组分熔点及其比列:以共混组分熔点为依据以连续相熔点为调整范围。
•②塑料的热性能,如熔融吸热放热、热降解历程及热氧化难易。
•③塑料各组分熔点范围内,流动性能及形态变化。
•如PC/ABS(6:4),PC:熔点230度左右,分解点350度左右;ABS:熔点180~190度左右,分解点245-290度左右——因此PC/ABS加工温度230-250度——考虑到其他助剂,如相容剂,润滑剂的热稳定性等等⑶物料温度升高的来源:•1,螺杆的剪切和物料粒子间相互摩擦生热——大部分。
•2,筒体的传热。
(2)各段螺杆排布与温度设定螺杆组合的作用:①输送物料②提供剪切——使加工物料获得物理变化和化学变化所需的能量使组分间分散和分布。
③建压•物料颗粒熔融过程的分析:•聚合物自由输送与预热——全充满或部分充满固体塞——固体摩擦、耗散与固态密集“海岛”结构的生成——固态稀疏“海岛”结构——成型挤出。
螺杆排布分段与温度设定:•1、输送段•A、螺杆排布思路有:•a深槽正向螺纹•b中等螺槽大导程正向螺纹,且螺槽容积由大变小,即螺纹导程由大向小渐变。
•B、温度设定思路•a不宜太高,影响物料在此段输送和受剪切的;也不宜太低,螺杆受力过大或卡死•b一般略接近熔融,按梯度排列。
2、熔融段•A、螺杆排布:.物料在此段要达到的目的是:使加工物料获得物理变化和部分化学变化所需的能量,使组分间分布均匀和初步分散,做到组分均质化、粘度接近。
.一般要求物料承受较大的剪切和机筒传热,使之熔融_一般设置捏合块,剪切元件或反螺纹,且注意相间排列配合。
•B、温度设定•a玻纤系,温度太低,树脂半融,到后段玻纤包覆性差;温度太高,树脂流动提高,温炼与剪切作用变小,甚至出现高温降解,其设定原则:•1、据基料不同和玻纤含量不同;•2、扣除螺杆剪切输入的热量,略高于基料熔点范围内;•3、熔融段后段(即玻纤加入口)熔体流动状况。
•b填充系,(提供强剪切使填充物,充分分散),熔融段高出基料熔点10~20℃(尽量提高),使物料充分熔融均匀分布。
•c阻燃系,(保护好阻燃剂),其温度要偏低,特别是白色材料,尽可能降低。
•d玻纤增强阻燃系,设定温度介于前面两者间,以物料基本熔点为依据。
•b合金系,以两组熔融温度为依据,同时考虑组分比例及组分之热敏性等,适当调整温度3、混炼段•A、螺杆组分排布•物料在此段要达到的目的是:1。
细化分散,形成理想的尺寸和结构。
2。
注意保护成品理想的结构不被破坏。
•一般有两典型思路:1、增强型,二兴和三头组合;2、兼分布与分散的高剪切与高分流以捏合块为主体,螺纹块为辅助咸高剪切。
---较好方法:不同厚度,不同差痊角的捏合块组合,加上输送螺丝块——使物料受高剪切而分散又保留时间与返混,但保证不降解。
•B、温度设定•a玻纤系,温度太低,物料流动性能差,粘度大,摩擦变大,生热高,会出现局都过热;温度太高,树脂降解,剪切度小玻纤分散变差,其设定原则:•1、据基料和玻纤含量不同而不同。
•2、略筒于基料熔点范围内。
•3、据成品带条的光泽度而确定。
•b填充系,(提供强剪切使填充物,充分分散),混炼段高出基料熔点10~20℃(尽量提高),使物料充分熔融均匀分布,保证混合体是流体状态。
•c阻燃系,(保护好阻燃剂)共混温度在偏低,特别是白色材料,尽可能降低。
•d玻纤增强阻燃系,温度设定以物料基本熔融为依据,保护好阻燃剂。
•e合系化,以组分的熔融温度为依据,同时考虑组分比例及组分热敏性而调整。
4、排气段螺杆组合排列•一般排气口入口处,设立反向螺纹咸反向捏合块,将熔体密封建立起,是高压;用大导程螺纹元件以形成低充满度和懂熔体层,使物料暴露自由表面或采用多头小导程螺纹,以增加熔体表面更新速度,利于气体排除与挥发——总的思路:反螺纹(R-LH)或反向棍合块(KG)+输送螺纹+大导程或多头小导程螺纹。
5.均化(料量)段•A螺杆组合•螺纹块导程渐变小或螺槽渐变小来实现增压,减少背压段长度,同时注意采用单头螺纹与宽螺棱螺纹来提高排料能力,避免冒料。
•B温度设定,•以适当降低温度,但模头高温利于排料。
•在熔融段温度基础上,适当降低温度,其原则:根据带光泽降度而定五、转速问题:•转速越高,剪切越大,将分散相均匀分散于基体之中;剪切越大,分散相尺寸越细,但转速过大,摩擦大易引起热降解,同时停留时间变短,混合不均。
•转速越低,剪切越小,分散不均匀,同时停留时间长,对易分解聚合物不利。
•转速与螺杆结构都是与剪切分散有关,因此必须两者作为整体考虑。
•⑴加纤增强类,•影响到玻纤的长度和直径,影响到树脂与玻纤的分散包裹问题,从而影响增强效果。
•⑵合金类,•必须考虑,转速剪切对树脂间的结构的生成和破坏问题。
如PC/ABS合金,属于类似海绵的“海岛”结构。
•⑶阻燃类,•必须考虑,阻燃剂的热性能,如熔融吸热放热、热降解历程及热氧化难易。