球壳板设计及制造
球形顶盖注塑模设计
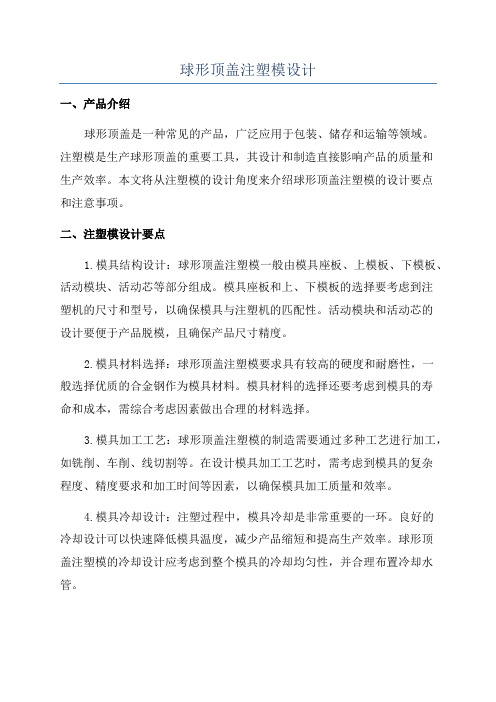
球形顶盖注塑模设计一、产品介绍球形顶盖是一种常见的产品,广泛应用于包装、储存和运输等领域。
注塑模是生产球形顶盖的重要工具,其设计和制造直接影响产品的质量和生产效率。
本文将从注塑模的设计角度来介绍球形顶盖注塑模的设计要点和注意事项。
二、注塑模设计要点1.模具结构设计:球形顶盖注塑模一般由模具座板、上模板、下模板、活动模块、活动芯等部分组成。
模具座板和上、下模板的选择要考虑到注塑机的尺寸和型号,以确保模具与注塑机的匹配性。
活动模块和活动芯的设计要便于产品脱模,且确保产品尺寸精度。
2.模具材料选择:球形顶盖注塑模要求具有较高的硬度和耐磨性,一般选择优质的合金钢作为模具材料。
模具材料的选择还要考虑到模具的寿命和成本,需综合考虑因素做出合理的材料选择。
3.模具加工工艺:球形顶盖注塑模的制造需要通过多种工艺进行加工,如铣削、车削、线切割等。
在设计模具加工工艺时,需考虑到模具的复杂程度、精度要求和加工时间等因素,以确保模具加工质量和效率。
4.模具冷却设计:注塑过程中,模具冷却是非常重要的一环。
良好的冷却设计可以快速降低模具温度,减少产品缩短和提高生产效率。
球形顶盖注塑模的冷却设计应考虑到整个模具的冷却均匀性,并合理布置冷却水管。
5.模具排气设计:注塑过程中,模具要充分排除注塑材料中的气体,以避免产生气泡和缺陷。
球形顶盖注塑模的排气设计要充分考虑到产品的形状和尺寸,确保气体能顺利排出。
三、注塑模设计注意事项1.尺寸精度:球形顶盖是一个外观要求较高的产品,因此注塑模的设计要求尺寸精度较高,以确保产品的一致性和美观度。
在模具设计中,要考虑到模具的收缩率和产品的加工余量,以达到设计尺寸。
2.模具寿命:球形顶盖注塑模一般有较长的使用寿命,因此在设计模具时要选择高质量的模具材料,合理设计模具结构,以增加模具的寿命。
3.材料流动性:球形顶盖注塑模的设计要考虑到注塑材料的流动性,以确保注塑过程中塑料能充分填充模具腔体,避免短充、缩短等缺陷。
球壳板设计及制造

球壳板设计及制造(上、下中心板,上、下极边板)主要参数:1000M3,材质16MnDR,厚度30mm一.设计部分1.球壳板结构形式选择目前,世界各国球形容器主要结构形式有桔瓣式、足球瓣式、混合式三种,以桔瓣式结构应用最广。
八十年代末以来,一些先进国家在大型球形容器中广泛采用混合式结构,它具有结构新颖,材料利用率明显提高,焊缝总长减少等诸多优点;我国近年来也采用了这种新结构。
球形容器的结构设计,参照GB/T17261 – 1998《钢制球形储罐形式与基本参数》,将两种结构形式的分带散,球壳板数量、焊缝总长、材料利用率、支柱数量的参数的对比,然后择优选取。
2.球壳板材料的选择该球罐的设计压力为常压,设计温度为常温,上作介质为天然气。
按GH12337-1998标准,可供选择的材料有16MnDR.它的板厚可选30mm。
3.球壳板制造设计球壳板的制作我厂采用二次下料法,即首先通过计算展开,再将放样尺寸周边适当放大,切割的毛坯冷压成型后,再进行精确切割。
样板的设计制作尤为关键,样板的精确直接影响球片的成形质量。
赤道带、温带板的下料计算与桔瓣式完全相同。
二.制造部分1.上、下级中心板主要参数:SR6150、δ=30、弦长L=2007.0/2399.6*6833.5/6741.9、弧长L=2016.0/2415.1*7245.3/7135.5工序包括:材料复验、一次下料、压制、二次好料、修磨、整形、修磨、坡口探伤、测厚、接管与法兰组焊、无损检测、级带划线,开孔、接管与壳板组焊、焊接、无损检测、热处理、整形、检验、标识包装。
材料的进厂入库检验结构材料和焊接材料验收合格后,应按企业标准,分别存放在金属材料库和焊接材料库。
金属材料主要存放各种钢材、有色金属和外购铸、锻件等,不允许露天堆放。
不锈钢板、钢管和有色金属材料,应分别单独存放并妥善保管。
放样、划线与号料放样、划线与号料是决定焊接坯料形状与尺寸公差的重要工艺,亦是焊接结构过程主要质量控制点之一。
大型全足球瓣式球罐球壳板制作工法

大型全足球瓣式球罐球壳板制作工法大型全足球瓣式球罐球壳板制作工法概述:大型全足球瓣式球罐球壳板制作工法是一种用于制作大型球形容器外壳的先进工艺。
这种工法可以应用于石油、化工、食品等行业中,用于制作贮罐、反应器、储罐等容器的外壳。
该工法的独特设计和生产流程,能够保证球罐球壳板的高质量、高强度和耐久性,为工业生产提供重要的基础设施。
工法步骤:1. 设计和制造球罐模具。
首先,通过计算和设计确定球壳的直径、高度和几何特征等参数,然后制造合适的模具。
模具是根据球壳的尺寸和形状来设计的,通常由金属材料制成,以保证足够的强度和稳定性。
2. 制作球壳板。
在完成模具制造之后,需要选择合适的材料来制作球壳板。
通常情况下,球壳板由高强度和耐腐蚀的材料制成,如不锈钢、铝合金或碳钢等。
在制作球壳板之前,需要对材料进行预处理,如切割、修整和准备焊接接头。
然后,将球壳板放入模具中,并根据需要进行角焊接,以确保球壳板能够完全封闭和保持结构强度。
3. 进行球壳板焊接。
将球壳板放入焊接工作台上,使用合适的焊接设备进行焊接。
焊接工艺需要根据球壳板的材质和设计要求来确定。
通常情况下,采用氩弧焊、封孔焊和角焊等方式进行焊接,以保证焊缝的质量和均匀度。
焊接完毕后,需要对焊缝进行检查和测试,以确保焊接质量达到标准要求。
4. 进行球壳板的后续处理。
在完成焊接之后,需要对球壳板进行抛光、除锈、喷涂和表面处理等工序。
这些工序的目的是提高球壳板的表面光洁度、耐腐蚀性和机械性能。
根据具体需求,可以额外进行防水、防火和隔热等处理,以增强球罐球壳板的性能和功能。
5. 进行球罐球壳板的组装和安装。
完成球壳板的制作和处理后,需要将其进行组装和安装。
这需要根据设计要求进行精确的测量和定位,以确保球壳板的安装位置和连接口与球壳的其他组件完全配合。
在组装过程中,还需要进行必要的密封和减震处理,以确保球罐球壳板在使用过程中能够安全、稳定地运行。
总结:大型全足球瓣式球罐球壳板制作工法是一项复杂的工程,在制作过程中需要高度的技术和专业知识。
浅谈球形储罐的设计
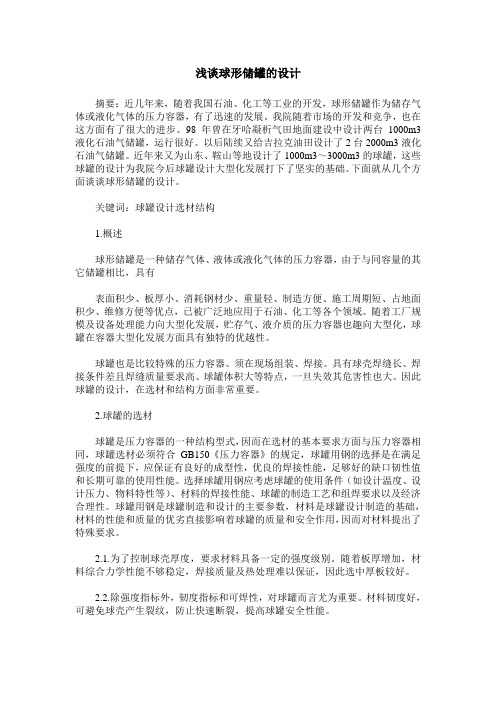
浅谈球形储罐的设计摘要:近几年来,随着我国石油、化工等工业的开发,球形储罐作为储存气体或液化气体的压力容器,有了迅速的发展。
我院随着市场的开发和竞争,也在这方面有了很大的进步。
98年曾在牙哈凝析气田地面建设中设计两台1000m3液化石油气储罐,运行很好。
以后陆续又给吉拉克油田设计了2台2000m3液化石油气储罐。
近年来又为山东、鞍山等地设计了1000m3~3000m3的球罐,这些球罐的设计为我院今后球罐设计大型化发展打下了坚实的基础。
下面就从几个方面谈谈球形储罐的设计。
关键词:球罐设计选材结构1.概述球形储罐是一种储存气体、液体或液化气体的压力容器,由于与同容量的其它储罐相比,具有表面积少、板厚小、消耗钢材少、重量轻、制造方便、施工周期短、占地面积少、维修方便等优点,已被广泛地应用于石油、化工等各个领域。
随着工厂规模及设备处理能力向大型化发展,贮存气、液介质的压力容器也趣向大型化,球罐在容器大型化发展方面具有独特的优越性。
球罐也是比较特殊的压力容器。
须在现场组装、焊接。
具有球壳焊缝长、焊接条件差且焊缝质量要求高、球罐体积大等特点,一旦失效其危害性也大。
因此球罐的设计,在选材和结构方面非常重要。
2.球罐的选材球罐是压力容器的一种结构型式,因而在选材的基本要求方面与压力容器相同,球罐选材必须符合GB150《压力容器》的规定,球罐用钢的选择是在满足强度的前提下,应保证有良好的成型性,优良的焊接性能,足够好的缺口韧性值和长期可靠的使用性能。
选择球罐用钢应考虑球罐的使用条件(如设计温度、设计压力、物料特性等)、材料的焊接性能、球罐的制造工艺和组焊要求以及经济合理性。
球罐用钢是球罐制造和设计的主要参数,材料是球罐设计制造的基础,材料的性能和质量的优劣直接影响着球罐的质量和安全作用,因而对材料提出了特殊要求。
2.1.为了控制球壳厚度,要求材料具备一定的强度级别。
随着板厚增加,材料综合力学性能不够稳定,焊接质量及热处理难以保证,因此选中厚板较好。
球罐生产工作及流程

• 用刨边机刨边, 应用样板检验 破口尺寸。 • 进刀量应较小, 避免产生撕裂 装表面,并用 砂轮机修磨整 个表面。
• 所用焊接坡口进 行渗透或磁粉检 测,Ⅰ 测,Ⅰ级合格。 • 板材周边100mm 板材周边100mm 范围内超声, JB4730, JB4730,Ⅲ级合 格。
由前线施工单位制作
球壳板的焊接
• 考虑到球形储罐具有体积大、运 输困难的特点,球罐大多进行室 外焊接,在现场完成球壳板的组 对和焊接。
球壳的焊接
谢谢观赏
、整形
• 切割后进行曲率测量,若有超差现象, 上整形胎进行整形。
8、无损检测
• 坡口进行渗透或磁粉 检测,Ⅰ 检测,Ⅰ级合格。 • 周边100mm范围内超 周边100mm范围内超 声,JB4730 UT声,JB4730,UT-Ⅲ JB4730, 级合格。
9、测厚
• 用超声波或测厚 仪对成型后的壳 体测厚,布点应 有代表性,大致 均匀排列,每张 板一般5点以上。
球壳板防腐工艺
• 表面预处理合格后至涂敷第一道底漆的时间不 应超过8h。如果表面在8h间隔内出现锈蚀现象, 应超过8h。如果表面在8h间隔内出现锈蚀现象, 涂敷前应对锈蚀部位重新进行表面预处理。 • 清除球壳板坡口表面和两侧至少50mm范围内 清除球壳板坡口表面和两侧至少50mm 50mm范围内 的油污、水分及其他熔渣级氧化皮有害杂质清 除干净,涂刷可焊性涂料。 • 其他要求详见《容器防腐工艺守则》。
4、二次号料
• 用精确软样板进行号料,该样板 需在成性良好的球壳板上制作。 检查线和检查点应清楚。
5、坡口加工
• 用专用切割胎具进 行切割,在切割前 要进行调胎使切割 轨迹对准切割线, 将胎具定位后进行 半自动切割割炬的 顺序为下坡口、钝 边、上坡口。
百事通:第三册第三章第八节球形储罐设计

第八节球形储罐设计一、总则1.适用范围本节是对GB12337《钢制球形储罐》的补充,适用于碳钢、低合金钢制且设计压力不大于4MPa的以支柱支撑的球形储罐的设计、制造、组装、检验与验收。
2.本节引用的标准、规范,如为新的标准、规范代替时,则应采用新的标准,规范。
二、型式与参数1)型式桔瓣式或混合式球壳;2)参数球形储罐参数见表3-8-1。
表3-8-1 球形储罐参数三、设计参数(一)设计温度常温下盛装混合液化石油气的球形储罐,应以50℃为设计温度,盛装天然气的球形储罐应以地区最冷月最低平均温度和最热月最高平均温度作为设计温度。
(二)设计压力常温下盛装混合液化石油气的球形储罐,其设计压力应按《压力容器安全技术监察规程》第27条规定确定;盛装天然气的球形储罐以最高操作压力为设计压力。
(三)地震烈度按《中国地震烈度区划图(1990)》和《中国地震烈度区划图(1990)使用规定》确定。
(四)风压值10m高度处的基本风压按建罐地区30年一遇10分钟平均风速计算确定,可查有关规范选取基本风压值。
但在有台风经过的沿海地区或海岛建罐,应将基本风压值适当加大或取当312地台风风速计算基本风压值。
四、材料选择(一)原则选择用于制造球形储罐球壳的钢材应考虑以下原则:(1)强度高,以减小球壳厚度;(2)韧性好,以保证材料避免产生裂纹;(3)塑性好,以满足球壳制造中变形的需要;(4)可焊性好,以保证球壳组装焊接的要求;(5)经济合理。
(二)钢板下列钢板可用于制造球壳板,见表3-8-2。
(三)钢管常用于支柱或接管的钢管见表3-8-3。
表3-8-2 钢板种类表3-8-3 常用钢管五、结构设计(一)带数和支柱数应按表3-8-1确定。
(二)各带球心角与各带分块数应根据钢板宽度、球壳板成形的压机开档尺寸,减少纵焊缝长度,钢板利用率高确定最优的球心角和各带分块数。
(三)支柱(1)支柱由圆管、底板、端板组成,圆管应采用无缝钢管制作。
(2)支柱分成单段式和双段式两种型式。
球壳加工过程

球壳加工过程
球壳加工是一种重要的制造工艺,通常用于生产各种球体零件,如球阀、球型铰链、摆线传动器等。
球壳加工的过程包括以下几个步骤:
1. 选材:选择适合加工的材料,通常为金属材料,如钢、铝合金等。
2. 初步加工:将原材料切割成一定大小的块状,以便进行后续的加工。
3. 粗加工:将块状原料进行初步加工,如车削、铣削等,使其逐步接近球形。
4. 精加工:对初步加工后的零件进行精密加工,如车床球面加工、磨床球面加工等,以达到高精度的要求。
5. 表面处理:对精加工后的零件进行表面处理,如镀铬、喷漆等,以提高零件的耐腐蚀性和美观度。
6. 检验:对加工后的球壳进行检验,包括外观检验、尺寸检验、质量检验等,以确保产品达到设计要求。
球壳加工过程需要先进的设备和技术,通常由专业的加工厂家或机械加工工程师完成。
随着科技的发展,越来越多的自动化设备应用于球壳加工中,提高了生产效率和产品质量。
- 1 -。
大型钢制球罐球壳板制造工艺

大型钢制球罐的球壳板制造工艺摘要;本文综合阐述了目前国内球罐球壳板的制造工艺,并针对球壳板制造中的几个主要环节提出了一些提高球壳板制造质量的注意事项,为以后大型球罐球壳板的制造积累有益的经验。
关键词;球罐;球壳板;制造工艺0 前言球罐由于具有技术先进、经济合理、使用安全等特点,已被广泛应用于国内外的石油、化工、煤气和天然气、冶金等工业领域。
另外,随着材料、焊接、制造、施工安装技术的不断提高,球罐的大型化和高参数的势头锐不可挡。
但是,同一般的圆柱形压力容器相比,球罐在制造上也存在着许多困难之处,如下料工序较复杂、尺寸精度要求严格、焊缝冷却收缩而造成的球体几何尺寸变形无法采用滚圆法纠正等。
我厂球容车间在2008年先后完成了3台2000 m3液化气球罐,3台1000 m3天然气球罐和3台1500 m3轻烃球罐的球壳板预制工作。
在实际生产过程中,我们也遇到了许多难题,阻碍了生产的顺利进行。
为了解决以上问题,进一步提高大型球罐的制造质量,特总结出球壳板的制造工艺及制造中所需特别注意的环节。
1 球壳板的制造工艺1.1 球壳板制造所需的工装机具近年来, 由于大型化球罐的制造以及高强度调质低合金钢被广泛采用, 球壳板制造一般采用冷压成形。
冷压成形就是钢板在常温状态下,经冲压变形成为球面球壳板的过程,其特点是小模具、多压点,钢板不必加热、成形美观、精度高、无氧化皮[1]。
冲压设备多采用800~2500t压力机,我厂所使用的是2400t液压机。
球壳板在冷压过程中所需工装机具主要用于两个环节,一是所需的上下胎具、曲率样板;二是用于切割的专用切割轨道和二次精下料样板。
文中着重论述上下胎具半径的计算。
加工完成的胎具如图1所示。
上、下胎具的曲率半径可按公式(1)、(2)计算:Rt1=R(1-E) (1)式中Rt1——上胎球体曲率半径,mm;R ——球壳板名义半径,mm;E——回弹量(% )。
对于不同厚度的低合金钢板,取15% ~30%。
大型全足球瓣式球罐球壳板制作施工工法(2)

大型全足球瓣式球罐球壳板制作施工工法大型全足球瓣式球罐球壳板制作施工工法一、前言大型全足球瓣式球罐球壳板制作施工工法是一种在建设大型球罐球壳板时采用的施工工艺。
该工法通过瓣式球罐球壳板的制作和组装,能够满足球罐球壳板的需求,并确保施工过程的稳定和成功。
二、工法特点该工法具有以下特点:1. 瓣式球罐球壳板制作简单,模块化程度高,可预制和快速安装。
2. 经过优化设计,球壳板具有良好的刚度和承载力,能够满足球罐的使用要求。
3. 采用专用机具设备进行施工,操作方便,效率高。
4. 施工过程中采取严格的质量控制和安全措施,确保施工质量和工人的安全。
三、适应范围该工法适用于建设大型球罐的项目,如油罐、天然气罐等。
可以在各种地质条件下进行施工,适应范围广泛。
四、工艺原理该工法的工艺原理是通过计算和预制,将球壳板分成若干个瓣片,然后根据实际需要进行组装。
球壳板的制作需要考虑材料的刚度和承载能力,以及瓣片的连接方式等。
通过分析和解释工法的理论依据和实际应用,可以让读者了解该工法的原理和应用方法。
五、施工工艺该工法的施工工艺包括以下几个阶段:1. 准备工作:包括地基处理、材料准备、机具设备的调配等。
2. 瓣式球壳板制作:将球罐球壳板分成若干个瓣片,按照设计要求进行制作。
3. 瓣片组装:将制作好的瓣片进行组装,使用专用工具进行连接和固定。
4. 球壳板调整和修整:对组装好的球壳板进行调整和修整,确保其符合设计要求。
5. 球壳板安装和固定:将调整好的球壳板安装到球罐上,并进行固定,确保其稳定和牢固。
6. 后续工作:包括检验、清理和验收等。
六、劳动组织在施工过程中,需要组织专业的施工队伍,包括工程师、技术人员和工人。
根据施工进度和工程要求,科学安排和调配劳动力,确保施工进度和质量。
七、机具设备该工法需要使用一些机具设备,如球壳板制作设备、组装工具等。
这些机具设备具有一定的特点和性能,操作简便,能够提高施工效率。
八、质量控制为确保施工过程中的质量,需要采取一些质量控制的方法和措施。
混合式结构球罐壳板尺寸计算表
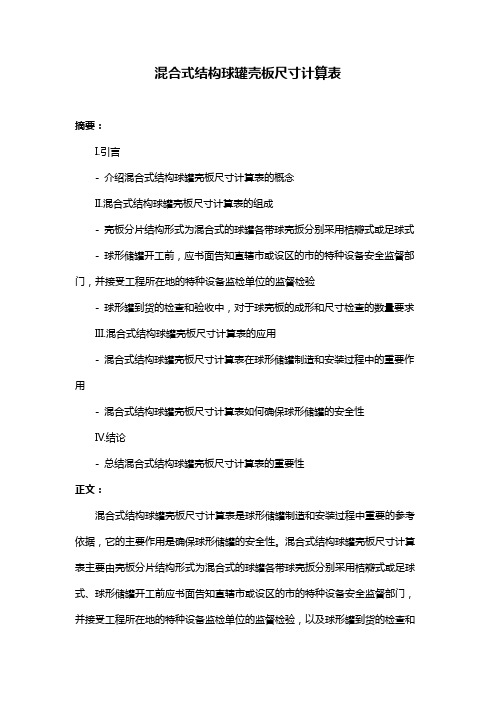
混合式结构球罐壳板尺寸计算表
摘要:
I.引言
- 介绍混合式结构球罐壳板尺寸计算表的概念
II.混合式结构球罐壳板尺寸计算表的组成
- 壳板分片结构形式为混合式的球罐各带球壳扳分别采用桔瓣式或足球式- 球形储罐开工前,应书面告知直辖市或设区的市的特种设备安全监督部门,并接受工程所在地的特种设备监检单位的监督检验
- 球形罐到货的检查和验收中,对于球壳板的成形和尺寸检查的数量要求III.混合式结构球罐壳板尺寸计算表的应用
- 混合式结构球罐壳板尺寸计算表在球形储罐制造和安装过程中的重要作用
- 混合式结构球罐壳板尺寸计算表如何确保球形储罐的安全性
IV.结论
- 总结混合式结构球罐壳板尺寸计算表的重要性
正文:
混合式结构球罐壳板尺寸计算表是球形储罐制造和安装过程中重要的参考依据,它的主要作用是确保球形储罐的安全性。
混合式结构球罐壳板尺寸计算表主要由壳板分片结构形式为混合式的球罐各带球壳扳分别采用桔瓣式或足球式、球形储罐开工前应书面告知直辖市或设区的市的特种设备安全监督部门,并接受工程所在地的特种设备监检单位的监督检验,以及球形罐到货的检查和
验收中,对于球壳板的成形和尺寸检查的数量要求等内容组成。
混合式结构球罐壳板尺寸计算表在球形储罐制造和安装过程中的重要作用体现在,它能够准确地计算出球罐壳板的尺寸,从而保证球形储罐的结构完整性。
同时,它也能够确保球形储罐在开工前,到货后的安全性和合格性,避免因设备问题导致的安全事故。
球形壳冷缩径工艺及模具

球形壳冷缩径工艺及模具球形壳冷缩径工艺及模具是一种常用于金属加工的技术,它能够将金属板材冷缩成球形壳体,并且具备高精度和表面质量好的特点。
本文将介绍球形壳冷缩径工艺的基本过程以及相关的模具设计要点。
球形壳冷缩径工艺主要由下面几个步骤组成:准备金属板材、制作模具、冷缩成型。
首先,我们需要准备一块适合尺寸的金属板材,通常选用的是钢材或铝材。
然后,根据球形壳的设计尺寸,制作相应的模具。
模具的设计应考虑到冷缩成型时的材料流动和变形,以确保成品的精度和质量。
最后,将金属板材放入模具中,并施加适当的力量进行冷缩成型。
冷缩过程中,金属板材会受到模具的约束,逐渐变形成球形壳体。
冷缩径过程可以通过模具的形状和设计来控制,以达到所需的尺寸和形状。
在球形壳冷缩径工艺中,模具的设计至关重要。
以下是一些模具设计要点:1. 防止金属板材产生褶皱:在模具设计中,应增加适当的滚辊和凸轮,以使金属板材在变形过程中能够顺利流动,避免出现褶皱。
此外,还可以使用压边和辅助材料来加固金属板材,防止褶皱的发生。
2. 控制金属板材的厚度:为了使球形壳的表面平滑,模具设计中应考虑控制金属板材的厚度分布。
一般来说,应该使金属板材的厚度在整个冷缩过程中均匀变化,以避免厚度不均造成的问题。
3. 确保模具的耐磨性和刚度:由于球形壳冷缩成型需要施加较大的力量,模具的材料必须具备良好的耐磨性和刚度。
通常情况下,我们会选用硬度高、抗磨性好的材料,如工具钢或硬质合金。
4. 优化模具的结构和形状:为了提高球形壳的成形精度和表面质量,模具的结构和形状也需要进行优化设计。
例如,可以采用分段模具来减小金属板材的变形量,从而提高成形精度。
此外,还可以通过凸台和凹槽的设计来控制金属板材的流动路径,以获得更好的表面质量。
通过运用球形壳冷缩径工艺及合理的模具设计,我们可以获得高精度和表面质量好的球形壳体,广泛应用于机械制造、航天航空等领域。
在实际应用中,我们应根据具体要求和材料特性进行工艺参数和模具设计的选择,以达到最佳的成形效果。
球壳结构控制要点
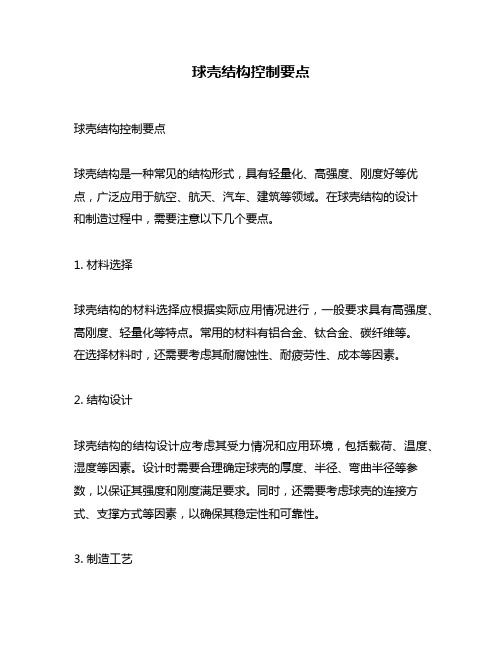
球壳结构控制要点球壳结构控制要点球壳结构是一种常见的结构形式,具有轻量化、高强度、刚度好等优点,广泛应用于航空、航天、汽车、建筑等领域。
在球壳结构的设计和制造过程中,需要注意以下几个要点。
1. 材料选择球壳结构的材料选择应根据实际应用情况进行,一般要求具有高强度、高刚度、轻量化等特点。
常用的材料有铝合金、钛合金、碳纤维等。
在选择材料时,还需要考虑其耐腐蚀性、耐疲劳性、成本等因素。
2. 结构设计球壳结构的结构设计应考虑其受力情况和应用环境,包括载荷、温度、湿度等因素。
设计时需要合理确定球壳的厚度、半径、弯曲半径等参数,以保证其强度和刚度满足要求。
同时,还需要考虑球壳的连接方式、支撑方式等因素,以确保其稳定性和可靠性。
3. 制造工艺球壳结构的制造工艺包括成型、加工、连接等环节。
成型方式有拉伸成型、压力成型、旋转成型等,需要根据材料和结构特点选择合适的成型方式。
加工方式包括切割、钻孔、铆接等,需要保证加工精度和表面质量。
连接方式包括焊接、铆接、螺栓连接等,需要根据实际情况选择合适的连接方式。
4. 检测和质量控制球壳结构的检测和质量控制是制造过程中的重要环节。
检测方法包括超声波检测、X射线检测、磁粉检测等,需要保证检测精度和可靠性。
质量控制包括材料质量控制、加工质量控制、连接质量控制等,需要建立完善的质量管理体系,确保产品质量符合要求。
总之,球壳结构的设计和制造需要综合考虑材料、结构、制造工艺、检测和质量控制等因素,以确保产品的强度、刚度、稳定性和可靠性。
在实际应用中,还需要根据具体情况进行优化和改进,以满足不同领域的需求。
球壳板制造几何尺寸公差要求

±3mm
d.两对角线间的距离
≥5mm
单片对角线平面度
≤4mm
坡口
角度偏差
±2.5“
光洁度25um,
平面度小于1ห้องสมุดไป่ตู้m
钝角偏差
±1mm
钝边中心位移偏差
±1mm
3
支柱
立柱直径及长度偏差
±2mm
支柱直线度
≤12mm
柱体中心线对底板垂直偏差
≤2mm
4
球罐总尺寸
焊缝对口间隙
2±2mm
对口错边量
≤3mm
对口角变形
≤7mm
内径及椭圆度
≤80mm
5
附件
人孔、接管开口位置偏差
≤5mm
人孔、接管外伸长度偏差
±5mm
接管法兰平面与接管中心线允差
≤3mm
球壳板制造几何尺寸公差要求
序号
分项内容
标准要求公差
备注
1
曲率
曲率
赤道带、极带
球壳板周边150mm内与样板间隙不大于2mm;其它部位允许间隙不大于3mm
样板弦长≥2000mm
2
球壳板
厚度
冲压后最小值
27.75/29.75/33.75mm
几
何
尺
寸
a.长度方向弦长.
±2.5mm
b.任间宽度方向弦长
±2mm
- 1、下载文档前请自行甄别文档内容的完整性,平台不提供额外的编辑、内容补充、找答案等附加服务。
- 2、"仅部分预览"的文档,不可在线预览部分如存在完整性等问题,可反馈申请退款(可完整预览的文档不适用该条件!)。
- 3、如文档侵犯您的权益,请联系客服反馈,我们会尽快为您处理(人工客服工作时间:9:00-18:30)。
球壳板设计及制造(上、下中心板,上、下极边板)
主要参数:1000M3,材质16MnDR,厚度30mm
一.设计部分
1.球壳板结构形式选择
目前,世界各国球形容器主要结构形式有桔瓣式、足球瓣式、混合式三种,以桔瓣式结构应用最广。
八十年代末以来,一些先进国家在大型球形容器中广泛采用混合式结构,它具有结构新颖,材料利用率明显提高,焊缝总长减少等诸多优点;我国近年来也采用了这种新结构。
球形容器的结构设计,参照GB/T17261 – 1998《钢制球形储罐形式与基本参数》,将两种结构形式的分带散,球壳板数量、焊缝总长、材料利用率、支柱数量的参数的对比,然后择优选取。
2.球壳板材料的选择
该球罐的设计压力为常压,设计温度为常温,上作介质为天然气。
按GH12337-1998标
准,可供选择的材料有16MnDR.它的板厚可选30mm。
3.球壳板制造设计
球壳板的制作我厂采用二次下料法,即首先通过计算展开,再将放样尺寸周边适当放
大,切割的毛坯冷压成型后,再进行精确切割。
样板的设计制作尤为关键,样板的精
确直接影响球片的成形质量。
赤道带、温带板的下料计算与桔瓣式完全相同。
二.制造部分
1.上、下级中心板
主要参数:SR6150、δ=30、弦长L=2007.0/2399.6*6833.5/6741.9、
弧长L=2016.0/2415.1*7245.3/7135.5
工序包括:材料复验、一次下料、压制、二次好料、修磨、整形、修磨、坡口探伤、测厚、接管与法兰组焊、无损检测、级带划线,开孔、接管与壳板组焊、焊接、无损检测、热处理、整形、检验、标识包装。
材料的进厂入库检验
结构材料和焊接材料验收合格后,应按企业标准,分别存放在金属材料库和焊接材料库。
金属材料主要存放各种钢材、有色金属和外购铸、锻件等,不允许露天堆放。
不锈钢板、钢管和有色金属材料,应分别单独存放并妥善保管。
放样、划线与号料
放样、划线与号料是决定焊接坯料形状与尺寸公差的重要工艺,亦是焊接结构过程主要质量控制点之一。
放样是在制造金属结构之前,按照设计图样,在放样平台上用1:1的比例尺寸,划出结构或者零件的图形和平面展开尺寸。
号料和划线采用划针或者磨尖的石笔、粉线作线。
毛坯尺寸下料
根据展开尺寸,考虑各种影响变形的因素,按下料时各边留出18~20 mm的加工余量,做出毛坯下料样板进行画线下料。
二次精确下料
毛坯经成型加工,曲率合乎要求后,进行二次准确下料。
二次下料的切割线采用球面样板画出,以得到尺寸准确的球壳板。
球壳板的切割在弧形格板胎具上进行。
胎具由弧形格板与支架构成,弧形壳板组成的球形弧面与被加工的球壳板曲率完全符合。
因此,同一胎具可以切割同一球罐上的所有球壳板,割炬自行小车可在相同弧形轨道上运动。
球瓣的压制
球瓣的成型方法主要是通过压机的压力冲压加工而达到要求的形状。
该过程称为成型操作。
球罐的成型操作分冷压,热压及温压。
考虑球壳的厚度,曲率半径,强度等因素,选用热压
成型方法。
热压成型是指将钢板加热到临界点以上的某一温度,并在这个温度下成型。
其优点是:可将钢板加热到塑性变形温度,然后用模具一次冲压成型,降低材料的屈服极限,
减少动力消耗,避免应变硬化和增加材料的延展性。
一次成型可避免冷压的多点多次冲压过程。
采用厚截面热轧材料如16MnR等,为了提高材料的安全性,用正火温度来进行热压成型,不但达到了热压的效应,而且通过热压使材料的性能提高了。
由于冲压过程毛坯塑性变形较大,对于壁厚较大或冲压深度较大的板材,为了提高材料变形能力,保证球壳成型质量,一般都采用热冲压成型。
由于本次所选用的球壳壁厚为55mm壁厚较大,因此球壳的冲压成形选用热冲压一次冲压成形。
坡口加工
坡口加工采用火焰热切割并清除表面的氧化层,坡口表面应平滑;
焊接接头坡口形状和几何尺寸的设计,应遵循以下原则:
(1)保证焊接质量(2)坡口加工简易(3)便于焊接加工(4)节省焊接材料
2上、下极边板
主要参数:SR6150、δ=30、弦长L=1378.7*6644.5*7231.6、
弧长L=1381.6*7019.3*8032.3
工序包括:材料复验、一次下料、压制、二次号料、坡口加工、修磨、整形、无损检测、测厚、检验、标识包装。
3 上、级中心板
主要参数:SR6150、δ=30、弦长L=2100.4*5973.5*6741.9
弧长L=2110.7*6237.5*7135.5
工序包括:材料复验、一次下料、压制、二次号料、坡口加工、修磨、整形、无损检测、检验、标识包装。