潜在失效模式及后果分析表
潜在失效模式及后果分析FMEA新版表格2020.10.9

第2步 结构分析
第3步 功能分析
1.上一较高级别 2.关注要素
3.低一较低级别或 特性类型
1.上一较高 级别功能及
要求
2.关注要素功 能及要求
3.下一较低级别 功能及要求或特
性
AIAG - VDA DFMEA
项目: DFMEA开始时间: DFMEA修订日期: 多功能组:
FC的频度 (O)
针对FC或FM的 当前探测控制
DC
FC/FM 探测度
(D)
设计 FMEA措 标识(选 预防 施优先级 填) 措施
AP
探测 措施
责任人
计划完成 时间
第6步 改进措施
第6步 改进措施
状态:
采取基于证 据的措施
实际 完成 时间
S
O
D AP
第7步 结果文件化
第4步
失效分析
风
1.对于上一较高级 别要素和/或最终 用户的失效影响 (即:失效影响)
FE
FE的严重度 (S)
2.关注要ቤተ መጻሕፍቲ ባይዱ的失效模式 (即:失效模式) FM
3.下一较低级别要素 或特性的失效起因 (即:失效起因)
FC
对FC的当前 预防控制 PC
VDA DFMEA
第5步 风险分析
DFMEA ID 编号: 设计责任: 保密级别:
潜在失效模式及后果分析(PFMEA)

4 2 5 4 3
进料检验试产测试 要求供应商排版确认样品。 要求供应商排版确认样品。 要求供应商排版确认样品。 要求供应商提供确认样品。
2 2 3 2 3
32 28 75 40 54
保丽龙
重量 保丽龙 尺寸 外观不良 唛头
产品不安全,破损 外观不良,影响安全 客户投诉 唛头错误、客户投诉,
6 4 6 5
2
现行控制方法
l 来 料 检 验
外观不良
透明度不够,导致产品缺陷
供应商材料发生了变化
要求供应商固定客户原材料订购
树脂
浓度 重量 含铅 拉力不够
调配后产品收缩比列大,变形 数据预算错误,导致产品重量不足 不符合标准 翻次过低、影响使用次数
6 4 8 7
原材料过浓或者偏稀 供应商称重失误 供应商材料不达标 材料发生质变
3
按作业指导书操作。 现场巡检及日检查报表
4 3 2 3 3 2 2
60 0 12 48 27 12 20
2 4
现场巡检及日检查报表 现场巡检及日检查报表 现场管理巡检、操作员自检 现场巡检及日检查报表 核对产品所需物料全数清点
白坯检验功能不良
重量不符 尺寸
核对标准样件、按客户要求,每件称 3 重保重。 操4
供应商供应材料不符合欧美RoHS元素
3
要求供应商提供最新第三方检测报告,生产前送 第三方检测。
2
24
颜色易脱落,客服投诉 字体错误、印刷部清楚 导致条码无法读数,客户投诉 字体错误、印刷不清楚 产品不安全,破损
4 7 5 5 6
供应商品质部符合质量要求 供应商品质部符合质量要求 供应商品质部符合质量要求 供应商排版不挡 要求供应商按标准密度生产
FMEA潜在失效模式及后果分析含表单及评价标准最新制定
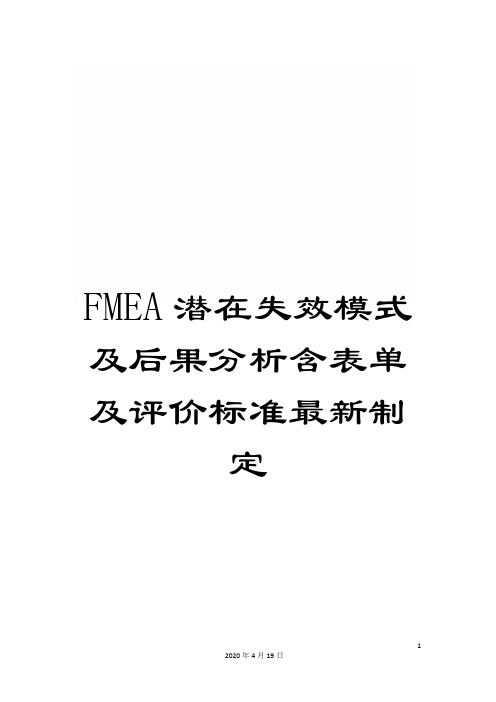
FMEA潜在失效模式及后果分析含表单及评价标准最新制
定
1
2020年4月19日
ZD-700-05
版本:10
QB
文件代码/版本:QI-02-09-A/0
潜在失效模式及后果分析
新制定
- 1 -
2020年4月19日
编制:审核:批准:
颁布日期:实施日期:
- 2 -
2020年4月19日
- 3 - 2020年4月19日
1. 目的:
1.1 认可并评价产品/过程中的潜在失效以及该失效的后果。
1.2 确定能否消除或减少潜在失效发生的机会并全部文件化。
2. 范围:
在进行FMEA时有三种基本的情形,每一种都有不同的范围或关注焦点:
2.1 对新设计、新技术或新过程,FMEA的范围是全部设计、技术或过程。
2.2 对现有设计或过程的修改(假设对现有设计或过程已有FMEA),FMEA的
范围是对设计或过程的修改、由于修改可能产生手工艺相互影响以及现
场的历史情况。
2.3 对现有的设计或过程用于新的环境、场所或应用(假设对现有设计或过
程已有FMEA),FMEA的范围是新环境或场所对现有设计或过程的影响。
3. 职责:
3.1 产品与技术中心:
3.1.1 负责本程序的制定与维护。
3.1.2 负责承担组织FMEA制定的发起者、对FMEA潜在模式及后果分析进行
管理。
3.1.3 负责对FMEA措施对策跟踪,以及组织小组人员对措施实施后风险顺
序数评估。
3.2 FMEA小组组长:负责调动和协调所有有关方面代表的积极参与,组织
- 4 -
2020年4月19日。
潜在的失效模式及效应分析表(过程)
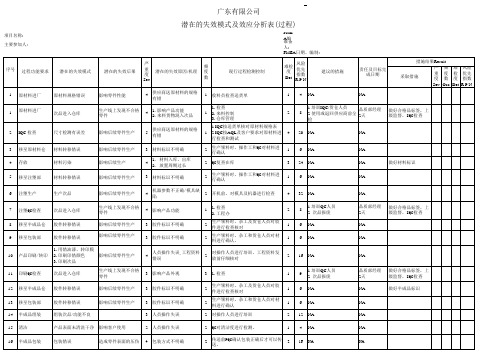
3 4 3
2 2 2
1 3 1
6 24 6
NA NA NA
NA NA NA 做好材料标识
6
注塑生产
生产次品
影响后续零件生产 生产线上发现不合格 零件 影响后续零件生产 影响后续零件生产
4
2
4
32
NA 1.培训QC人员 2. 次品报废 NA NA
NA 品质部经理 2天 NA NA 做好合格品标签,上 级监督,IQC检查
偏小 out of out 0.2 spec. of A spec. 偏小
影响客户使用
操作工对外观要求不明 确 操作工对包装要求不明 确 影响产品功能 人员失误 影响产品出货 材料标识不明确 货仓设施设备问题(是 否漏水等) 人员失误
2 2 2 1 2 2 1 1
QC对零件进行抽检
NA NA 品质部经理 2天 NA 品质部经理 2天 NA NA NA 做好合格品标签,上 级监督,IQC检查
7 8 9
注塑QC检查 移至半成品仓 移至包装部
次品进入仓库 胶件转移错误 胶件转移错误 1.用错油漆、转印膜 2.印刷印错颜色 3.印刷次品 次品进入仓库 胶件转移错误 胶件转移错误 组装次品/功能不良 产品表面未清洗干净 包装错误
4 3 3
1 2 2
2 1 1
8 6 6
10
产品印刷/转印
影响后续零件生产 生产线上发现不合格 零件 影响后续零件生产 影响后续零件生产
序号
过程功能要求
潜在的失效模式
潜在的失效后果
潜在的失效原因/机理
现行过程检测控制
1
原材料进厂 原材料进厂
原材料规格错误
影响零件性能 生产线上发现不合格 零件
潜在失效模式及后果分析-表

编制人:济南永安减振器责任有限公司FMEA日期:(编制)2005.05.20(修订)FMEA编号:JY/JC-JS-02项目名称:1005210A271皮带轮减振器总成车辆年/车辆类型: CA6DF1-26-51Q过程责任部门:FMEA 小组关键日期:2005.06.22主要参加人 项目小组全体人员: 杨从洛,张云忠,张宝,张超(过程FMEA)编制人:济南永安减振器责任有限公司FMEA日期:(编制)2005.05.20(修订)FMEA编号:JY/JC-JS-02项目名称:1005210A271皮带轮减振器总成车辆年/车辆类型: CA6DF1-26-51Q过程责任部门:FMEA 小组关键日期:2005.06.22主要参加人 项目小组全体人员: 杨从洛,张云忠,张宝,张超(过程FMEA)编制人:济南永安减振器责任有限公司FMEA日期:(编制)2005.05.20(修订)FMEA编号:JY/JC-JS-02项目名称:1005210A271皮带轮减振器总成车辆年/车辆类型: CA6DF1-26-51Q过程责任部门:FMEA 小组关键日期:2005.06.22主要参加人 项目小组全体人员: 杨从洛,张云忠,张宝,张超(过程FMEA)编制人:济南永安减振器责任有限公司FMEA日期:(编制)2005.05.20(修订)FMEA编号:JY/JC-JS-02项目名称:1005210A271皮带轮减振器总成车辆年/车辆类型: CA6DF1-26-51Q过程责任部门:FMEA 小组关键日期:2005.06.22主要参加人 项目小组全体人员: 杨从洛,张云忠,张宝,张超(过程FMEA)编制人:济南永安减振器责任有限公司FMEA日期:(编制)2005.05.20(修订)FMEA编号:JY/JC-JS-02项目名称:1005210A271皮带轮减振器总成车辆年/车辆类型: CA6DF1-26-51Q过程责任部门:FMEA 小组关键日期:2005.06.22主要参加人 项目小组全体人员: 杨从洛,张云忠,张宝,张超(过程FMEA)编制人:济南永安减振器责任有限公司FMEA日期:(编制)2005.05.20(修订)FMEA编号:JY/JC-JS-02项目名称:1005210A271皮带轮减振器总成车辆年/车辆类型: CA6DF1-26-51Q过程责任部门:FMEA 小组关键日期:2005.06.22主要参加人 项目小组全体人员: 杨从洛,张云忠,张宝,张超(过程FMEA)△----产品特性☆----过程特性。
潜在失效模式及其后果分析(FMECA)
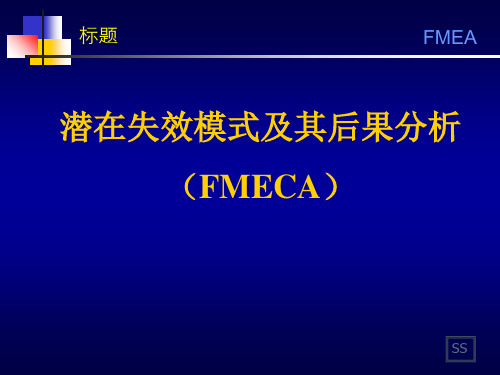
—— 有关术语
FMEA
2.2.3 失效率
已工作到 t 时刻的产品,在 t时刻后单位时间 t内发生故障的概率。
λ(t)= r(t)
NS t
N r(t)
0
0
NS r(t)
t
t+ t
t SS
2.2.4 寿命特征参数
可靠性
1) 平均故障时间 ( MTTF )
MTTF
=
—N10
N0
t
i=1
i
其中:No : 参加试验数→最终失效数 tI : 开始工作到失效的时间
系统的可靠性R系=R设·R软件·R人员·R接口
SS
——系统与系统结构图
一般系统的功能结构图
SE1.1
SE1 SE1.2
系统
System
SE2
SE3 (SE:系统单元)
SE2.1 SE2.2 SE2.3
...
SE3.5
SE2.2.1
SE2.2.2 交接点
SS
——系统与系统结构图
串联系统可靠性模型
使用过程形成:使用规范
使用可靠性
SS
—— 有关术语
FMEA
2.1.2 可靠度
产品在规定的条件下和规定的时间内完
成规定功能的概率。
可靠度是时间的递减函数。
R(t)= P( T > t )
SS
—— 有关术语
可靠性
可靠度的估计值:
R^ (t) = —N—o—-r(—t)— No
其中:No : t=0时刻,在规定条件下工作的产品数 r(t): 在0→t时刻的工作时间内,发生故障的 产品数
失效模式 错误模式 不能切换 提前运行 滞后运行 错误输入(过大) 输入过小 输出过大
潜在失效模式及后果分析表
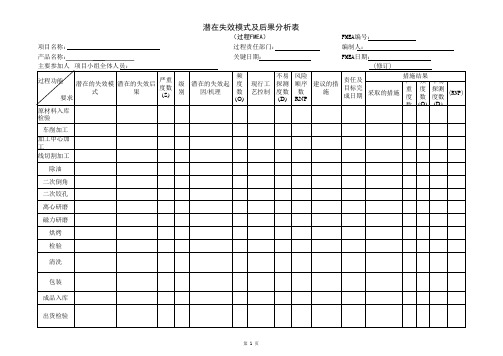
FMEA编号:
项目名称:
过程责任部门:
编制人:
产品名称:
关键日期:
FMEA日期:
主要参加人 项目小组全体人员:
(修订)
过程功能 要求
潜在的失效模 式
潜在的失效后 果
严重 度数 (S)
级 别
频 潜在的失效起 度
因/机理 数
(O)
现行工 艺控制
不易 探测 度数
(D)
风险 顺序
数
RNP
建议的措 施
责任及 目标完 成日期
风险 顺序
数
RNP
建议的措 施
责任及 目标完 成日期
措施结果 严 频 不易
采取的措施
重 度
度 数
探测 度数
(RNP)
数 (O) (D)
原材料入库
检验
车削加工 加工中心加 工 线切割加工
除油
二次倒角
二次铰孔
离心研磨
磁力研磨
烘烤
检验
清洗
包装 成品入库
出货检验
第1页
潜在失效模式及后果分析表
(过程FMEA)
潜在失效模式及后果分析表
(过程FMEA)
FMEA编号:
项目名称:
过程责任部门:
编制人:
产品名称:
关键日期:
FMEA日期:
主要参加人 项目小组全体人员:
(修订)
过程功能 要求
潜在的失效模 式
潜在的失效后 果严重Fra bibliotek度数 (S)级 别
频 潜在的失效起 度
因/机理 数
(O)
现行工 艺控制
不易 探测 度数
(D)
措施结果 严 频 不易
采取的措施
设计失效模式及后果分析表模板(DFMEA)
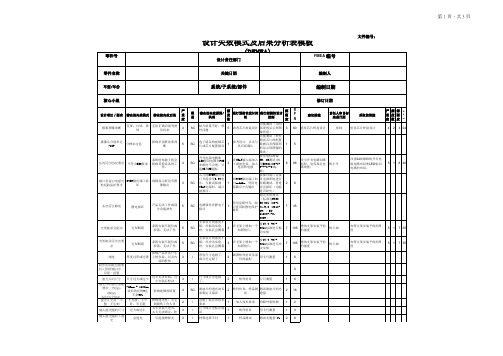
上支架的安装孔的 尺寸和厚度尺寸
尺寸不达标
无法与其他部件安 装;影响系统的厚
5
上支架的表面光滑 吗,无毛刺,无尖
不光滑,有毛 刺,有尖角
影响美观,以及安 装,使用的安全
6
角
下支架的安装孔的 尺寸和厚度尺寸
尺寸不达标
无法与其他部件安 装;影响系统的厚
5
下支架表面光滑, 不光滑,有毛 无毛刺,无尖角 刺,有尖角
61000-4-2:
2009)
SC
支架设计的强度不 够,在振动实验 时,安装孔会撕裂 。
3
在支架上增加一个 加固垫片。
按JT/T 7942011标准进行振 动实验
7
SC
支架设计的强度不 够,在冲击实验 时,安装孔会撕裂 。
3
在支架上增加一个 加固垫片。
按JT/T 7942011标准进行冲 击实验
7
60 优化芯片焊盘设计
制
控制
测 度
R P N
建议措施
责任人和目标 完成日期
采取的措施
严频探 R 重度测 P 度数度 N
SC
贴片质量不好,软 件问题
5
功能测试(用肉 改善芯片封装设计 眼观察显示屏图
像质量)
3
功能测试(软件
SC
选了错误的视频芯 片或芯片配置错误
1
参考设计,以及与 供应商确认
测试芯片的配置 数据以及肉眼判 断显示屏图像的
张钊
5
改小开关电路回路 96 面积。电容靠近电 胡小军
路放置。
6
35
105
增加支架安装平面 的强度
杨玉福
105
增加支架安装平面 的强度
潜在失效模式及后果分析
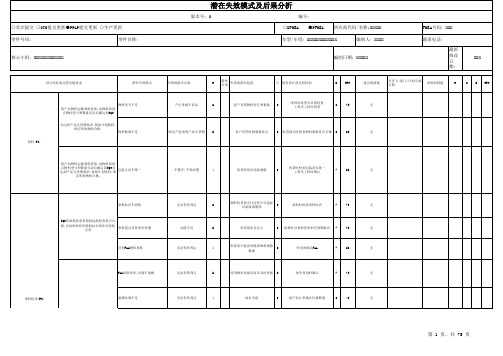
产品品质,提升
第 11 页,共 75 页
为达到焊接质量要求,所刮锡浆厚度.粘度.位置.平整度符合要求不良品,引起返工或退品,
客户不满意
第 12 页,共 75 页
为达到焊接质量要求,所刮锡浆厚度.粘度.位置.平整度符合要求第 13 页,共 75 页
多的PCB备用将影响产品交货期,客户不满意第 14 页,共 75 页
第 15 页,共 75 页
确定刮浆质量OK后投入贴片机贴片,由
IPQC确认机器贴装状况是否OK.
第 18 页,共 75 页
速,稳定后用炉温测试仪测试炉温确认
是否符合标准温度过底引起假焊或冷焊第 19 页,共 75 页
第 20 页,共 75 页
板生产,由IPQC确认贴装和焊接状况,合格后方可进行正式生产
产线贴片
足,使用寿命下降,使客户对产品不满意
生产将产生不良品引起返修或退品,客户不满意
确定刮浆质量OK后投入贴片机贴片,由IPQC确认机器贴装状况是否OK.
板生产,由IPQC确认贴装和焊接状况,合格后方可进行正式生产
品,客户不满意
料.短路.翻件.。
DFMEA设计潜在失效模式及后果分析表模板

8
Designer wrong input dimension data 设计人员标错尺寸
1. According design SOP (XJ-SJ-SOP-001)
3
2. Design leader re-check design 依照设计SOP参考,双人确认图档无误后,主管
Check Key dimension in CAD file
1. According design SOP (XJ-SJ-SOP-001)
0
2. Design leader re-check design
Remove shrinkage ratio to recheck
依照设计SOP参考,双人确认图档无误后,主管 3D dimension
1
确认
0
Team leader approve 设计开发部负责人审核确认
CNC加工
Electrode discharge allowance does Tooling dim. issue and product dim.
not match
failure
电机放电余量不符
影响模具尺寸,产品超尺寸公差
7
1. Gate desige/loacation issue 浇口方式不合理
Tooling Design 模具设计
Shrinkage issue 产品缩水率错误
Scrap mold core 模仁报废
Wrong dimension issue 尺寸标准错误
1.Fail to production 2.Fail to meet tooling schedule 3.Add tooling cost 模具不能量产/交期滞后/增加成本
过程潜在失效模式及后果分析表PFMEA--注塑焊接

3
1、每个风轮都 要动平衡的测量 目视检测平衡 。 机上参考的读 2、人离开机时 数确认 风轮不能停在机 台上。
3
1、每个风轮都 要经过动平衡 机的测量。 54 2、人离开机时 风轮不能停在 机台上。
1、每个风轮都要 经过动平衡机的测 1.IPQC检验记录 量。 6 3 3 54 表2、工艺卡 2、人离开机时风 轮不能停在机台上 。
1.工具校正后使用 不当出现错误 无法精准的 5 2.工具校正误差太 测量不良点 大,不适用 3.工具校正过期
3
1.建立工具保 养维护制度 2.培训正确使 用工具
1.核查设备校正 清单 2.考核设备使用 维护
5
1.定期设备校正 清单更新 2.设备使用维护 75 培训考核 3.设备编号特定 授权管理
1.工具设备清单 2.设备校正计划 表 3.设备校正报告 4.工具维修保养 记录
过程潜在失效模式及后果分析(PFMEA)
PFMEA编号:
项目阶段/过程:注塑件、焊接风轮 类别或产品型号: 核心小组 过程责任:塑料部 关键日期:2016-1-5 PFMEA日期(编制)2016-1-5 共1页,第 1 页 修订:2016-7-4
严 频 工序功能/ 潜在的失 潜在的失效 重 潜在的失效起因/机 现行过程控制 度 效模式 后果 度 预防 要求 理 (O) (S)
1. SV750-5A烘 干记录表2、过 程检验规范3、 《烘干作业指导 书》
1、投料前先试验 好烘干机发热情况 。2. 首检与客人签 6 3 3 54 样作对比目测确认 。
配料(依据 《配料作 色差 业指导书 》)
配料员配色母或色 影响外观要 7 种的比例不符合规 求 定,造成色差。
3
1.投料单注明 相关要求 2.首检确认
DFMEA设计潜在失效模式及后果分析

7
項目
潛在失 潛在失效
潛在原因/ 8 現行設計控制
建議行動 責任與目標
行動結果
效模式 之效應 功能
失效機制
嚴 重 性
等 級
發 預防性 生 頻 率
探測性
風 難險 檢優 度先
數
完成日期 已採取行動 風
嚴發難險 重生檢優 性度度先
數
9
10
11
12 13
14
15
16
17 18 19
20
21
22
8
FMEA表格
0.010 / 1000
發生度
10 9 8 7 6 5 4 3 2 132
FMEA表格
• 現行設計控制
➢ 現有的設計控制可以預防或驗證出該失效模式 及/或失效原因
➢ 一般可分為下 2 種設計控制
1.
的控制 2.
的控制
預防該失效模式/效 應/原因/機制出現 或減低出現頻次
用分析或測試方式, 可以失效模式/效應 /原因/機制出現前 偵查出來
➢ 是量度失效的風險指數 ➢ 數值愈高,代表風失效風險愈高 ➢ 應在設計發展過程前盡早完成控制
37
FMEA表格
• 建議行動
➢ RPN排序完成後,應該對排序最高的、 極為重要的項目首先採取行動
➢ 建議先處理高於 100分風險度的項目 ➢ 不論RPN指數為多少,應對一些高嚴重
性(S)的項目多加留意,例如S=9, 10
➢ 應根據公司過住的記錄,自行訂立指標 ➢ 設計小組對 評定準則和分級規則應意見
一致,即使因為個別產品分析作了修改也 應一致
31
發生度(O)的提議指標
失效發生的可能性
很高: 持續的ห้องสมุดไป่ตู้效 高: 反複發生的失效 中等: 偶然發生的失效
新版潜在失效模式及后果分析(FMEA)1

例举本次分析的产品失效模式:
31
➢ 步骤四:失效分析
失效链 FMEA中对失效的分析包括三个不同方面 ▲失效影响(FE) ▲失效模式(FM) ▲失效起因(FC)
30
➢ 步骤四:失效分析
失效 系统和子系统的失效模式描述是功能损失或退化。 功能的失效由功能推导而来。潜在失效模式包括但不限于以下 种: • 功能丧失(即无法操作、突然失效) • 功能退化(即性能随 间损失) • 功能间歇(即操作随机开始 停止 开始) • 部分功能丧失(即性能损失) • 非预期功能(即在错误的时间操作、意外的方向、不相等的性能) • 功能超范围(即超出可接受极限的操作) • 功能延迟(即非预期时间间隔后的操作) 例如:当向左打方向盘时,车辆向右转,这是非预期功能;
FMEA的定义和分类
FMEA的术语定义
• 失效(failure): 是指产品丧失规定功能的状态,又可译为故障。 失效与故障在含义上略有差别,失效是对不可修复产品而言;故障 是对可修复产品而言的。这里的失效含有这两方面的含义。
* 潜在失效模式(failure mode): 是指可以发生,但不一定非 得发生的失效模式,这时工程技术人员对设计、制造和装配过程中 认识到或感觉到的可能存在的隐患。
24
➢ 步骤二:结构分析
3.系统结构可视化:
灯泡
3
总成
4
D
极板
5
E
+ 零件
A.灯 罩
B.电 池
C.开 关
D.灯泡总成
E.电 极
潜在失效模式及后果分析表
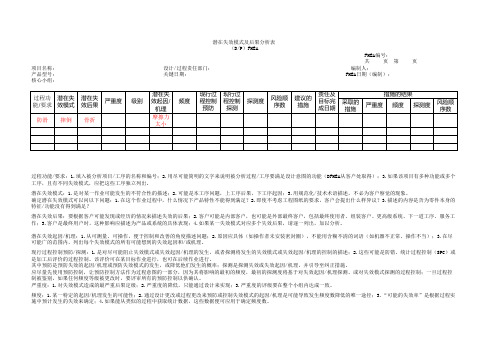
潜在失效模式及后果分析表(D/P)FMEAFMEA编号: 共 页 第 页项目名称: 设计/过程责任部门: 编制人:产品型号: 关键日期: FMEA日期(编制):核心小组:过程功能/要求:1.填入被分析项目/工序的名称和编号;2.用尽可能简明的文字来说明被分析过程/工序要满足设计意图的功能(DFMEA从客户处取得);3.如果该项目有多种功能或多个工序,且有不同失效模式,应把这些工序独立列出。
潜在失效模式:1.是对某一作业可能发生的不符合性的描述;2.可能是本工序问题,上工序后果,下工序起因;3.用规范化/技术术语描述,不必为客户察觉的现象。
确定潜在失效模式可以问以下问题:1.在这个作业过程中,什么情况下产品特性不能得到满足?2.即使不考虑工程图纸的要求,客户会提出什么样异议?3.描述的内容是否为零件本身的特征/功能没有得到满足?潜在失效后果:要根据客户可能发现或经历的情况来描述失效的后果;2.客户可能是内部客户,也可能是外部最终客户,包括最终使用者、组装客户、更高级系统、下一道工序、服务工作;3.客户是最终用户时,这种影响应描述为产品或系统的具体表现;4.如果某一失效模式对应多个失效后果,请逐一列出,加以分析。
潜在失效起因/机理:1.从可测量、可操作,便于控制和改善的角度描述问题;2.原因应具体(如操作者未安装密封圈),不能用含糊不清的词语(如机器不正常、操作不当);3.在尽可能广的范围内,列出每个失效模式的所有可能想到的失效起因和/或机理。
现行过程控制预防/探测:1.是对尽可能阻止失效模式或失效起因/机理的发生,或者探测将发生的失效模式或失效起因/机理的控制的描述;2.这些可能是防错、统计过程控制(SPC)或是加工后评价的过程控制。
该评价可在某目标作业进行,也可在后续作业进行。
其中预防是预防失效的起因/机理或预防失效模式的发生,或降低他们发生的概率;探测是探测失效或失效起因/机理,并引导至纠正措施。
设计潜在失效模式及后果分析表(DFMEA)
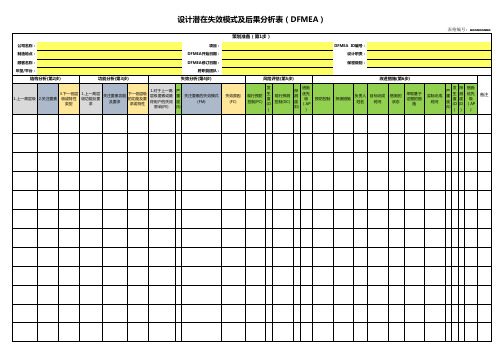
现行探测 控制(DC)
探 测 度 (D)
措施 优先
级 (AP
)
预防控制
探测措施
负责人 姓名
目标完成 时间
措施的 状态
采取基于 证据的措
施
实际完成 时间
严 重 度 (S)
发 生 度 (O )
探 测 度 (D )
措施 优先
级 (AP
)
备注
设计潜在失效模式及后果分析表(DFMEA)
策划准备(第1步)
表格编号:xxxxxxxxx
公司名称:
项目:
DFMEA ID编号:
制造地点:
DFMEA开始日期:
设计职责:
顾客名称:
DFMEA修订日期:
保密级别:
年型/平台: 结构分析(第2步)
功能分析(第3步)
跨职能团队: 失效分析(第4步)
风险评估(第5步)
改进措施(第6步)
1.上一高层级
3.下一低层 2.关注要素 级或特性
类型
1.上一高层 级功能及要
改进措施(第6步)
1.上一高层级
3.下一低层 2.关注要素 级或特性
类型
1.上一高层 级功能及要
求
关注要素功能 及要求
下一低层级 的功能及要
求或特性
1.对于上一高 层级要素或最 终用户的失效
影响(FE)
严 重 度 (S)
关注要素的失效模式 (FM)
失效原因 (FC)
现行预防 控制(PC)
发 生 度 (O )
目标完成 时间
措施的 状态
采取基于 证据的措
施
实际完成 时间
严 重 度 (S)
发 生 度 (O )
探 测 度 (D )
潜在失效模式及后果分析表(杭州2号线项目总装)

S评分标准特殊特性分类:影响产品的安全性和法规的符合性、影响产品的配合、功能、性能、影响后道工序的产品特性和过程特性。
分为:关键特性和重要特性。
关键特性(A):其失效会造成或影响到安全和法规的特性要求;用“A”标识;重要特性(B):虽然不会造成或影响到安全和法规,但会影响后续的装配、功能或性能的特性要求;用“B”标识;一般特性(不标注):不会影响到安全和法规和后续的装配、功能或性能的特性要求。
后果判定准则:后果的严重度这级别导致当一个潜在失效模式造成了在最终顾客和/或制造/装配厂的缺陷。
应该随时首先考虑到最终顾客。
如果在两者都发生缺陷,则采用两者中较高的严重度。
级别(顾客后果)(制造/装配后果)无警告的严重严重级别很高。
潜在失效模式影响车辆安全运行和/或包含不符合政府法规情形。
或,可能危及作业员(机器或组装)而无警告。
10有警告的严重严重级别很高。
潜在失效模式影响车辆安全运行和/或包含不符合政府法规情形。
或,可能危及作业员(机器或组装)但有警告。
9很高车辆/系统无法运行(丧失基本功能)。
或,产品可能必须要100%丢弃,或车辆/系统要在修理部门花上多于一小时来8高车辆/系统能运行,但性能下降。
顾客非常不满意。
或,产品可能必须要筛选,且一部分(少于100%)被丢弃,或车辆/系统要在修理部门花上半小时到一小时来加以修理。
7中等车辆/系统能运行,但舒适性/方便性项目失效。
顾客不满意。
或,可能有一部分(少于100%)的产品不经筛选地被丢弃,或车辆系统要在修理部门花上少于半小时来加以修理。
6低车辆/系统能运行,但舒适性/方便性项目运行性能下降。
或,100%的产品需要返工,或车辆/系统要下生产线修理,但不用到修理部门。
5很低装配和外观/尖响声和卡塔声等项目令人不舒服。
大多数(大于75%)顾客发现有或,产品可能必须要筛选,没有被丢弃,但一部分(少于100%)需要返工。
4轻微装配和外观/尖响声和卡塔声等项目令人不舒服。
失效模式及后果分析(FMEA)表
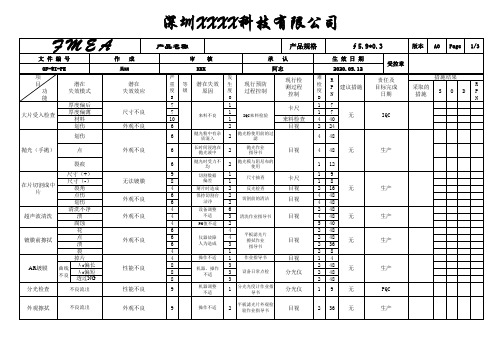
生产
曲线 不良
λ0偏长 λ0偏短 透过NG
分光检查
不良流出
无法镀膜 外观不良 外观不良 外观不良
性能不良 性能不良
外观擦拭
不良流出
外观不良
产品名称
产品规格
∮5.9*0.3
版本 A0 Page 1/3
审核
承认
XXX
阿志
严
发
重 等 潜在失效 生
度级
原因
度
S
O
现行预防 过程控制
7
1
7 10
来料不良
1 1
IQC来料检验
目视
4
PH值不适
2
6
4
6 6
仪器故障
4
人为造成
3
平板滤光片 擦拭作业 指导书
目视
4
1
4
操作不适
1
作业指导书
目视
8
3
8
机器、操作 不适
3
设备日常点检
分光仪
8
3
9
机器调整 不适
1
分光光度计作业指 导书
分光仪
生效日期
2020.05.12
难R
检 度 D
P 建议措施 N
17
17 4 40
无
2 24
4 48
4 48 无
6
2
6
抛光粉中有杂 质混入
2
抛光粉使用前的过 滤
6
长时间浸泡在 抛光液中
2
抛光作业 指导书
现行检 测过程
控制
卡尺 来料检查
目视
目视
6
抛光时受力不 均
2
抛光模与阻尼布的 使用
FMEA潜在失效模式及分析表格模版
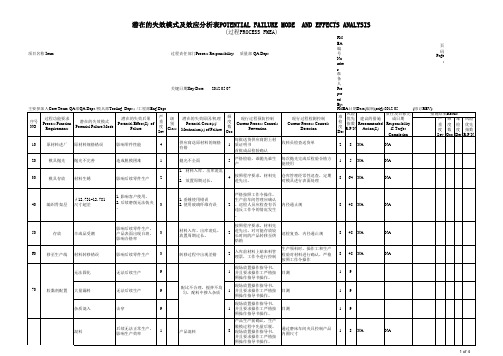
(过程PROCESS FMEA)
项目名称 Item: 主要参加人Core Team: QA部QA Dept./模具部Tooling. Dept.; /工程部Eng.Dept. 序号 NO. 过程功能要求 Process Function Requirements 潜在的失效模式 Potential Failure Mode 潜在的失效后果 Potential Effect(S) of Failure 严 级 重 别 度 Class Sev 4 潜在的失效原因/机理 Potential Cause(s)/ Mechanism(s) of Failure 供应商送原材料的规格 有错 抛光不全面 1. 材料入库、出库凌乱 。 2. 放置周期过长。 频 现行过程预防控制 度 Current Process Controls 数 Prevention Occ 1 每批送货供应商附上材 质证明书 首批成品检验确认 严格检验,谁抛光谁生 产 按照程序要求,材料先 进先出。 严格按照工作令操作。 生产前车间管理应确认 。巡检人员应检查有否 违反工作令的情况发生 。 按照程序要求,材料先 进先出。对可能存放较 长时间的产品转移至烘 焙箱 入库前材料上贴来料管 理票,工作令进行控制 现场放置操作指导书, 并且要求操作工严格按 照操作指导书操作。 现场放置操作指导书, 并且要求操作工严格按 照操作指导书操作。 现场放置操作指导书, 并且要求操作工严格按 照操作指导书操作。 产品生产前确认,生产 脱模过程中先量后脱。 现场放置操作指导书, 并且要求操作工严格按 照操作指导书操作。 控制真空度。现场放置 操作指导书,并且要求 操作工严格按照操作指 导书操作。 每日记录烘箱温度,升 温时间,固化时间,严 格按照工作令进行生产 活动。现场放置操作指 导书,并且要求操作工 严格按照操作指导书操 作。芯棒先行加热 严格按照工作令要求加 温 过程责任部门Process Responsibility: 关键日期Key Date: 2012.05.07 质量部 QA Dept.
- 1、下载文档前请自行甄别文档内容的完整性,平台不提供额外的编辑、内容补充、找答案等附加服务。
- 2、"仅部分预览"的文档,不可在线预览部分如存在完整性等问题,可反馈申请退款(可完整预览的文档不适用该条件!)。
- 3、如文档侵犯您的权益,请联系客服反馈,我们会尽快为您处理(人工客服工作时间:9:00-18:30)。
潜在失效模式及后果分析表
(D/P)FMEA
FMEA编号: 共 页 第 页
项目名称: 设计/过程责任部门: 编制人:
产品型号: 关键日期: FMEA日期(编制):
核心小组:
过程功能/要求:1.填入被分析项目/工序的名称和编号;2.用尽可能简明的文字来说明被分析过程/工序要满足设计意图的功能(DFMEA从客户处取得);3.如果该项目有多种功能或多个工序,且有不同失效模式,应把这些工序独立列出。
潜在失效模式:1.是对某一作业可能发生的不符合性的描述;2.可能是本工序问题,上工序后果,下工序起因;3.用规范化/技术术语描述,不必为客户察觉的现象。
确定潜在失效模式可以问以下问题:1.在这个作业过程中,什么情况下产品特性不能得到满足?2.即使不考虑工程图纸的要求,客户会提出什么样异议?3.描述的内容是否为零件本身的特征/功能没有得到满足?
潜在失效后果:要根据客户可能发现或经历的情况来描述失效的后果;2.客户可能是内部客户,也可能是外部最终客户,包括最终使用者、组装客户、更高级系统、下一道工序、服务工作;3.客户是最终用户时,这种影响应描述为产品或系统的具体表现;4.如果某一失效模式对应多个失效后果,请逐一列出,加以分析。
潜在失效起因/机理:1.从可测量、可操作,便于控制和改善的角度描述问题;2.原因应具体(如操作者未安装密封圈),不能用含糊不清的词语(如机器不正常、操作不当);3.在尽可能广的范围内,列出每个失效模式的所有可能想到的失效起因和/或机理。
现行过程控制预防/探测:1.是对尽可能阻止失效模式或失效起因/机理的发生,或者探测将发生的失效模式或失效起因/机理的控制的描述;2.这些可能是防错、统计过程控制(SPC)或是加工后评价的过程控制。
该评价可在某目标作业进行,也可在后续作业进行。
其中预防是预防失效的起因/机理或预防失效模式的发生,或降低他们发生的概率;探测是探测失效或失效起因/机理,并引导至纠正措施。
应尽量先使用预防控制,让预防控制方法作为过程意图的一部分,因为其将影响的最初的频度,最初的探测度将基于对失效起因/机理探测、或对失效模式探测的过程控制;一旦过程控制被鉴别,如果任何频度等级被更改时,要评审所有的预防控制以供确认。
严重度:1.对失效模式造成的最严重后果定级;2.严重度的降低,只能通过设计来实现;3.严重度的评级要在整个小组内达成一致。
频度:1.某一特定的起因/机理发生的可能性;2.通过设计更改或过程更改来预防或控制失效模式的起因/机理是可能导致发生频度数降低的唯一途径;3.“可能的失效率”是根据过程实施中预计发生的失效来确定;4.如果能从类似的过程中获取统计数据,这些数据便可应用于确定频度数。
探测度:最佳探测控制相关定级数,建议采用统计控制方法。
风险顺序数=严重度*频度*探测度
建议措施:1.首先针对高严重度、高风险顺序数或其他团队设计的项目采取预防或纠正措施;2.降低分数的排序是首先是严重度、其次是频度、最后是探测度;3.当严重度是9或10时,不管风险顺序数如何,都必须特别注意确认是否已利用现行的设计控制或预防/纠正措施。