焦化分馏塔模拟分析及改进_张龙
延迟焦化装置分馏塔腐蚀原因分析及改进措施_杨涛

石 油 炼 制 与 化 工2013年3月 收稿日期:2012-06-19;修改稿收到日期:2012-10-21。
作者简介:杨涛,技师,从事生产管理工作。
通讯联系人:孙艳朋,E-mail:sypai62@126.com。
延迟焦化装置分馏塔腐蚀原因分析及改进措施杨 涛,孙艳朋,翟志清,程前进(中国石化洛阳分公司,河南洛阳471012)摘 要:对中国石化洛阳分公司延迟焦化装置在检修期间发现的分馏塔顶部塔盘存在不同程度的腐蚀问题进行分析,认为造成分馏塔顶部塔盘腐蚀的主要原因为焦化原料和回炼重污油的盐含量高、分馏塔水洗操作不当。
结合装置的原料性质、操作参数及设备条件,采取加强原料盐含量监控、改善分馏塔上部热量分布、增设分馏塔顶部水洗专用线、优化分馏塔侧向回流等一系列改进措施,改善了分馏塔的结盐现象,为保证装置的长周期运行奠定了基础。
关键词:延迟焦化分馏塔 腐蚀 水洗中国石化洛阳分公司(以下简称洛阳分公司)1.40Mt?a延迟焦化装置在平稳运行38个月后于2011年9月1日进行首次停工检修。
检修期间发现分馏塔第3~11层塔盘出现明显的腐蚀减薄现象,而第4~7层塔盘的腐蚀减薄现象尤为严重。
为确保下一周期的安全平稳运行,在决定更换第3~11层塔盘的同时,认真分析腐蚀减薄现象产生的原因,提出一系列改进措施和建议,最大程度地减缓了生产期间塔盘的腐蚀速率,保证装置长周期运行。
本文主要介绍延迟焦化装置分馏塔腐蚀原因及改进措施。
1 装置腐蚀状况及原因分析1.1 塔盘腐蚀状况分馏塔第1、2层塔盘基体平整,有少量浮阀脱落;第3层塔盘约有1?3的浮阀脱落;第4层塔盘基体蚀坑连片,坑深约1~3mm;第5~7层塔盘和浮阀腐蚀减薄严重,局部腐蚀穿孔,且有大量浮阀脱落;第8~9层塔盘腐蚀减轻,但有大量黑色垢物堆积,浮阀基本已失去弹性。
利用扫描电子显微镜能谱仪(EDX)对第8层塔盘堆积的垢蚀物进行元素分析,结果见表1。
从表1可以看出,垢蚀物中以Fe,S,Cr,O等元素为主(约占94.7%),其中Fe和Cr为塔盘材质元素,S和O为腐蚀产物元素。
焦化车间分馏塔底改造项目顺利完成.docx

焦化车间分f留塔底改造项目顺利完成
延迟焦化装置杆浆掺炼比高达20% ,好浆中含有大量催化剂粉末,致使焦化装置一直以来存在着出装置产品焦粉携带量大的问题,同时产品焦粉携带量大也直接影响下游装置的安全平稳运行。
针对这一生产瓶颈,车间组织技术人员多方考察调硏, 决走对分馆塔底强化洗涤进行改造,并制走出具体改造方案, 于2019年大检修的对方案进行落实实施。
新的改造方案首
先在焦炭塔大好好管线入分f留塔加双列叶片式反应好分布器。
作用是增加大灯杆分布均匀度;二拆除分馆塔三层人字挡板,它的作用是增加喷淋空间,强化洗涤效果,从而减少焦粉携带量;三、拆除循环好下返塔直管分布管、分布槽,改分布管
为喷嘴,因为喷嘴分布好的颗粒细,洗涤效果好,对焦粉的捕捉能力强,能够达到强化洗涤的目的。
效果,为此焦化车间上下高度重视”由车间工艺设备管理人员组成的联合检查小组每天对分f留塔改造项目进行严密监
控、检查,现场三十几度的高温,塔内温度更是达到了40 多度,进塔里检查时需要穿一身塑料连体衣,不动弹都全身是汗,可他们没有一个人退缩,拿着照明设备在每层塔盘上爬上爬下”仔细认真检查着塔内每一个设备,确保每一处螺
栓禁锢到位,每一处焊接都达到标准……分憎塔内不知撒下他们多少辛苦的汗水,是他们忠实的守卫保证了分催塔洗涤改造项目顺利完工!。
(流程管理)焦化富气的流程模拟和改进

(流程管理)焦化富气的流程模拟和改进焦化富气的流程模拟和改进摘要在石油加工过程中产生的碳二组分(C2)、液化气组分(LPG)等组分,加以回收会对经济效益和社会效益产生很大的影响。
各炼油厂近年来逐渐对C2、LPG等有用组分的回收技术进行改造,通过采用新工艺和新型催化剂,使产气率大幅度提高,取得了显著的经济效益。
某厂采用吸收稳定系统回收焦化富气,由于扩产原因,该厂存在着严重的“干气不干”问题。
主要表现在两方面:1、该吸收稳定系统产出的干气中LPG组分严重超标,干气中LPG 浓度平均在10%左右,远超过设定浓度指标,导致液化气损失增大。
2、解析塔底富液中C2含量超标,导致稳定塔塔顶产生大量不凝气。
稳定塔顶不凝气流量约1700Nm3/h,含有大量的LPG组成,返回压缩机前入口,增加了整个系统的负荷,进一步导致干气不干的现象。
所以有必要对该系统进行改进以克服以上问题。
本文采用HYSYS模拟软件,对该富气吸收稳定流程进行流程模拟和流程改进,并通过流程调整,确定优化流程。
本论文在模拟原流程的基础上,采用了低温/冷凝-精馏过程改进原流程,使干气中碳三以上组分(C3+)含量降至5%;针对减少干气中LPG的损失率、增加C2的吸收率的目标,确定解吸塔的塔底温度控制在160℃为宜;针对C2作为产品从新增精馏塔产出的要求,为提高C2和LPG在新增塔的收率,优化新流程,吸塔塔底温度控制在155℃为宜,经济性显著增加。
关键词:焦化富气;干气回收;延迟焦化;HYSYS模拟目录摘要 (I)第1章引言 (1)1.1 焦化富气回收流程改进及模拟的重要意义 (1)1.2 国内外的发展状况 (2)1.3 国内外发展状况 (3)1.3.1 各公司发展现状 (3)1.3.2 中国石油加工工艺技术的发展 (5)1.3.3 延迟焦化 (5)1.4 焦化富气处理系统 (7)1.4.1 焦化富气 (7)1.4.2 吸收稳定系统 (7)1.4.3 吸收稳定过程同传统吸收过程比较 (9)1.4.4 选择适当的吸收条件 (9)1.4.5 解吸塔的进料方式 (10)1.4.6 控制合适的解析温度 (10)1.4.7 分析吸收和解析过程 (11)1.4.8 焦化产品的介绍 (12)1.5 HYSYS的介绍 (12)1.5.1 HYSYS模拟计算系统的特点和功能 (13)1.5.2 HYSYS模拟计算系统的主要物性计算方法 (15)1.5.3 HYSYS模拟计算系统中的不足 (16)1.6 设计的总体构想 (16)第2章流程模拟 (18)2.1 设计任务 (18)2.2 原流程图的介绍 (18)2.2.1 原流程的设计参数 (20)2.3 新流程的介绍 (28)2.3.1 经济评价 (31)2.3.2 环境影响 (31)第3章流程的优化 (32)3.1 优化干气组分 (32)3.1.1 参数调节对系统的影响 (32)3.1.2 结果分析 (43)3.2 优化C2、LPG的收率 (44)3.2.1 参数对系统的影响 (44)3.2.2 结果分析 (50)结论 (51)参考文献 (52)致谢 (53)第1章引言1.1 焦化富气回收流程改进及模拟的重要意义炼油工业中,延迟焦化是一个重要的原油二次加工过程。
运用流程模拟技术优化焦化装置分馏塔用能
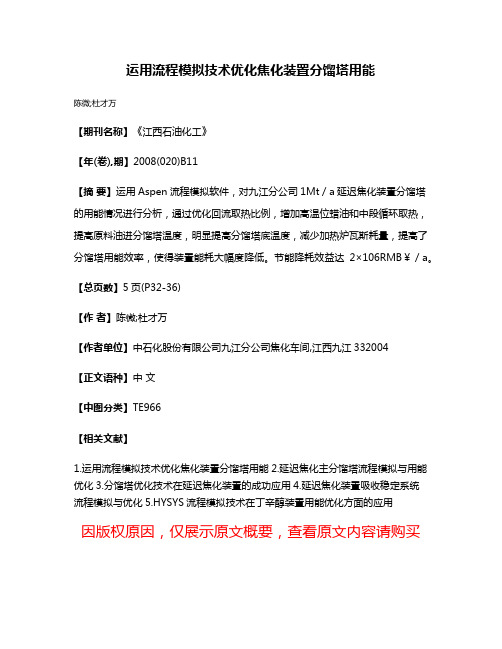
运用流程模拟技术优化焦化装置分馏塔用能
陈微;杜才万
【期刊名称】《江西石油化工》
【年(卷),期】2008(020)B11
【摘要】运用Aspen流程模拟软件,对九江分公司1Mt/a延迟焦化装置分馏塔的用能情况进行分析,通过优化回流取热比例,增加高温位蜡油和中段循环取热,提高原料油进分馏塔温度,明显提高分馏塔底温度,减少加热炉瓦斯耗量,提高了分馏塔用能效率,使得装置能耗大幅度降低。
节能降耗效益达2×106RMB¥/a。
【总页数】5页(P32-36)
【作者】陈微;杜才万
【作者单位】中石化股份有限公司九江分公司焦化车间,江西九江332004
【正文语种】中文
【中图分类】TE966
【相关文献】
1.运用流程模拟技术优化焦化装置分馏塔用能
2.延迟焦化主分馏塔流程模拟与用能优化
3.分馏塔优化技术在延迟焦化装置的成功应用
4.延迟焦化装置吸收稳定系统
流程模拟与优化5.HYSYS流程模拟技术在丁辛醇装置用能优化方面的应用
因版权原因,仅展示原文概要,查看原文内容请购买。
延迟焦化装置主分馏塔工艺模拟

延迟焦化装置主分馏塔工艺模拟党建军【摘要】利用PRO/Ⅱ软件模拟延迟焦化主分馏塔,得出准确的结果,为工艺的生产调优提供了理论依据.【期刊名称】《河南化工》【年(卷),期】2010(027)022【总页数】3页(P20-22)【关键词】延迟焦化装置;主分馏塔;模拟【作者】党建军【作者单位】中海油惠州炼油分公司,广东,惠州,516086【正文语种】中文【中图分类】TQ0181 概述中海油惠州炼油分公司延迟焦化装置设计处理量为 420万 t/a,于 2009年 4月开车一次成功。
装置由焦化、吸收稳定和公用工程三部分组成。
焦化分馏塔部分和吸收稳定部分热联合,分馏塔的过剩热量为吸收稳定部分的重沸器提供热源。
2 分馏塔模拟难点模拟难点是分馏塔进料,也就是焦炭塔油气性质的输入。
由于焦炭塔油气温度高,过热态,不可能取得实际的馏程数据,只能倒推组成。
实际的组成主要包括:循环油组分,循环油为分馏塔蜡油回流和焦炭塔油气逆向接触过程中,在脱过热段冷凝下来的重组分。
这部分组分也难以取得实际的馏程数据,通过循环油和原料的混合得到辐射进料油,通过分析辐射进料油的数据,间接得到循环油组分数据。
3 采用的物料平衡数据模拟时采用装置标定时的物料平衡数据,相对于平时的操作数据较准确,能很好的反映装置的整体水平。
物料平衡数据见表1。
表1 物料平衡数据物料流量/t·h-1 物料流量/t·h-1减压渣油 500 辐射量 645干气 27 重蜡油 16液化气 12 辐射量 645汽油 94 注水量 0.698(单路)柴油 152 蜡油 864 分馏塔模型建立分馏塔模型采用一个混合器模拟分馏塔油气进料,各组分以物料平衡数据为准。
分馏塔柴油回流按两个回流计算,一个为泵抽出柴油回流,另一个为富吸收柴油,分开计算主要因为这两个回流的组分和回流温度不同。
蒸发段 5层人字挡板主要起脱过热作用,基本无分离作用,所以采用一层理论塔板模拟。
炼油厂焦化分馏塔检修施工技术方案
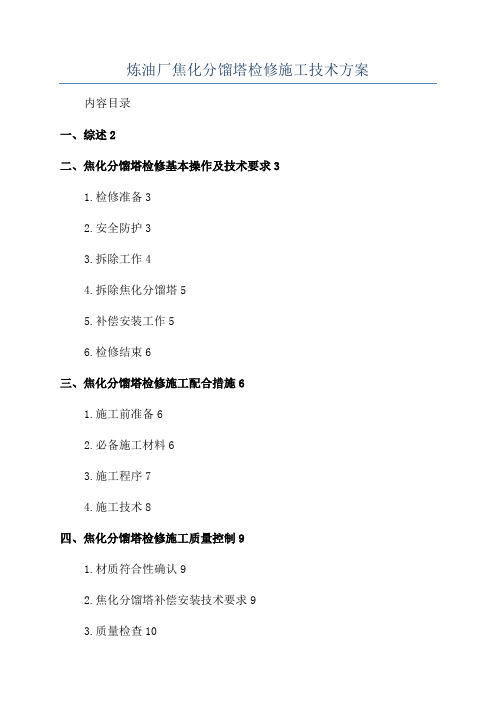
炼油厂焦化分馏塔检修施工技术方案内容目录
一、综述2
二、焦化分馏塔检修基本操作及技术要求3
1.检修准备3
2.安全防护3
3.拆除工作4
4.拆除焦化分馏塔5
5.补偿安装工作5
6.检修结束6
三、焦化分馏塔检修施工配合措施6
1.施工前准备6
2.必备施工材料6
3.施工程序7
4.施工技术8
四、焦化分馏塔检修施工质量控制9
1.材质符合性确认9
2.焦化分馏塔补偿安装技术要求9
3.质量检查10
五、焦化分馏塔检修施工组织及安排11
1.施工组织11
2.施工作业安排12
3.安全措施12
六、焦化分馏塔检修施工现场文明作业13
1.施工现场的卫生管理13
2.施工现场文明措施14
3.节能施工措施14
七、总结15
一、综述
石油炼油厂焦化分馏塔的检修是炼油厂运营的必要维护,对于炼油厂
的健康运营来说,它的正确操作和安全施工对设备的稳定运行至关重要。
为确保检修安全高效,有效提高炼油厂经济效益,需要认真编制一份完善
的焦化分馏塔检修施工技术方案。
本文旨在针对石油炼油厂焦化分馏塔检修施工这一行业进行详细分析。
焦化分馏塔顶循系统存在的问题和对策

过多 次操作 实践 观察 、 理论 分析 , 已对该 问题 有 现 了 比较 正确 的认识 , 定 了相应 的防 范措施 , 制 由此
指导 实际操 作 , 收到 了预期 的效果 。 I 顶循 系统 结盐 的原 因分 析
当温度 大于 3 7 8℃ 时 , 3. 固态 氯 化 铵 又 分解 为氯 化氢和 氨 。气 态 的 N 和 H 1 焦 炭 塔 塔 顶 油 H C随
T0 打 开 P0/ 入 口过滤 器 盖 板 上放 空 阀 , 12, 13 1 洗
涤后 的水 及少量 油 排入 含油 污水 系统 。控制塔 顶
对顶 循泵 入 口过滤 出来 的结垢 物进 行 了取样
抽 出温 度 保持 在2 5℃ 以上 , 3 柴油 返 回温度 保 持
收 稿 日期 :06—1 3 。 20 1— 0 作 者简 介 : 滨 , 级 工 程 师 ,9 2年 毕 业 于 中 国 石 油 大 学 瞿 高 19
( 东营 ) 现任该 公司炼 油二部副 主任 , , 从事装置 生产管理工
摘 要 : 对镇 海 炼 油 化 工 股 份 有 限 公 司 15 / 针 .0 Mta延 迟 焦 化 装 置 分 馏 塔 结 盐 的 现 象 及 危 害 , 析 了 结 盐 的 原 分
因, 提出结 盐处理 的方案 , 制定了相应的预防措施 : 保证原油脱盐效果 、 当分流部 分顶循环油 、 制顶循返塔温度 适 控 使之高于水蒸气凝结温度 , 由此指导实际操 作 , 得了较好的效果 。 取 关键词 : 延迟焦化装置 分馏塔 结盐 操作参数 措施
除, 这是焦 化 分馏塔 顶结 盐 的 内在 因素 , 而结 盐 的 外在 因素 是分 馏 塔顶 温较 低 , 馏 塔 顶部 塔 盘 温 分 度低 于与 水蒸 气 分 压对 应 的饱 和 温度 , 水蒸 气 凝
焦化分馏塔高负荷运行的瓶颈及对策
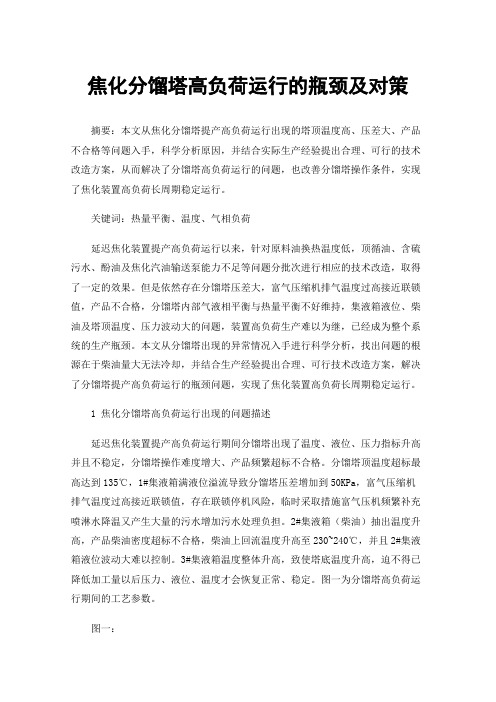
焦化分馏塔高负荷运行的瓶颈及对策摘要:本文从焦化分馏塔提产高负荷运行出现的塔顶温度高、压差大、产品不合格等问题入手,科学分析原因,并结合实际生产经验提出合理、可行的技术改造方案,从而解决了分馏塔高负荷运行的问题,也改善分馏塔操作条件,实现了焦化装置高负荷长周期稳定运行。
关键词:热量平衡、温度、气相负荷延迟焦化装置提产高负荷运行以来,针对原料油换热温度低,顶循油、含硫污水、酚油及焦化汽油输送泵能力不足等问题分批次进行相应的技术改造,取得了一定的效果。
但是依然存在分馏塔压差大,富气压缩机排气温度过高接近联锁值,产品不合格,分馏塔内部气液相平衡与热量平衡不好维持,集液箱液位、柴油及塔顶温度、压力波动大的问题,装置高负荷生产难以为继,已经成为整个系统的生产瓶颈。
本文从分馏塔出现的异常情况入手进行科学分析,找出问题的根源在于柴油量大无法冷却,并结合生产经验提出合理、可行技术改造方案,解决了分馏塔提产高负荷运行的瓶颈问题,实现了焦化装置高负荷长周期稳定运行。
1 焦化分馏塔高负荷运行出现的问题描述延迟焦化装置提产高负荷运行期间分馏塔出现了温度、液位、压力指标升高并且不稳定,分馏塔操作难度增大、产品频繁超标不合格。
分馏塔顶温度超标最高达到135℃,1#集液箱满液位溢流导致分馏塔压差增加到50KPa,富气压缩机排气温度过高接近联锁值,存在联锁停机风险,临时采取措施富气压机频繁补充喷淋水降温又产生大量的污水增加污水处理负担。
2#集液箱(柴油)抽出温度升高,产品柴油密度超标不合格,柴油上回流温度升高至230~240℃,并且2#集液箱液位波动大难以控制。
3#集液箱温度整体升高,致使塔底温度升高,迫不得已降低加工量以后压力、液位、温度才会恢复正常、稳定。
图一为分馏塔高负荷运行期间的工艺参数。
图一:2 原因分析1#集液箱液位、温度上涨,2#、3#集液箱温度上涨,表面反映出冷换设备、输送泵及出口管线能力不足,本质还是塔内气相负荷大幅增加所致。
- 1、下载文档前请自行甄别文档内容的完整性,平台不提供额外的编辑、内容补充、找答案等附加服务。
- 2、"仅部分预览"的文档,不可在线预览部分如存在完整性等问题,可反馈申请退款(可完整预览的文档不适用该条件!)。
- 3、如文档侵犯您的权益,请联系客服反馈,我们会尽快为您处理(人工客服工作时间:9:00-18:30)。
246
203
蜡油抽出温度/℃
363
369
蜡油返回温度/℃
270
277
表 2 焦化装置产品收率及设计收率
项目
设计收率/%
生产收率/%
干气
7.00
7.02
液化气
3.99
3.63
汽油
20.61
18.82
柴油
35.60
33.28
蜡油
1.80
6.33
焦炭
31.00
30.95
合计
100
100
表 3 分馏塔原产品性质对比
表 1 分馏塔操作参数及设计参数
项目
设计参数
操作参数
塔顶压力(表压)/MPa
0.100
0.092
塔顶温度/℃
131
132
反应油气进料温度/℃
415
410
顶循抽出温度/℃
149
130
顶循返回温度/℃ 柴油抽出温度/℃
109
98
239
235
柴油返回温度/℃
175
160
中段回流抽出温度/℃
306
309
中段回流返回温度/℃
在模型计算中,基于焦化分馏塔系统为非极性 物系,模型热力学方法采用 BK-10 物性选择集。汽、 液相的焓值计算采用 Johnson-Grayson,液相密度采 用 API 法计算[7]。模拟计算采用 Refinery 估算方 法[8]。模拟所得的分馏塔侧线产品性质和实际生产 数据对比见表 5 所示。
馏程/℃ IBP 5% 10% 30% 50% 266 335 378 475 591
注:残炭、芳烃、胶质和沥青质均为质量分数。
图 1 2#焦化装置模拟流程
1—焦化分馏塔;2—进料组合混合器;3—常压渣油分割器;4—塔底缓冲罐;5—蜡油分割器
成;并按照该分馏塔实际生产状况设塔顶循环回流、 柴油回流、中段取热循环回流、蜡油回流;回流取 热温差按生产现状分别设为 39℃、60℃、60℃、 80℃。
ZHANG Long1,ZHAO Yaxin2,FANG Xiangchen1,DU Weiqian3,GAO Jingshan1,BO Dechen1
(1Fushun Research Institute of Petroleum and Petrochemicals,SINOPEC,Fushun 113001,Liaoning,China;2SINOPEC Tahe Company,Kuche 842000,Xinjiang,China;3No. 2 Refinery of Fushun Petrochemical Company,PetroChina,
2 模拟计算
为了分析分馏塔的操作状况,本研究借助 SimSci/ProⅡ流程模拟软件对分馏塔进行了模拟计 算。模拟以常压渣油设计数据为基础数据,常压渣 油性质设计数据见表 4。针对分馏塔油气进料组成 无法确定的问题,模拟以分馏塔产品分布和产品性 质反推分馏塔进料组成。在模拟中将分馏塔脱过热 段与分馏段分开处理,非平衡级的塔底脱过热段采 用闪蒸设置。该焦化分馏塔分馏段设有 35 层塔盘, 底部蒸发段设有 6 层脱过热人字形洗涤板。根据该 分馏塔设计数据和经验,模拟设置时分馏塔精馏段 取 23 个平衡级来计算,脱过热段按平衡闪蒸来计 算[6]。按分馏塔生产工艺搭建模拟流程进行模拟计 算,模拟流程如图 1 所示。模型由分馏塔、闪蒸罐、 换热器、混合器、常压渣油分流器和蜡油分流器组
项目
焦化汽油
焦化柴油
焦化蜡油
设计值 生产值 设计值 生产值 设计值 生产值
密度/kg·m−3 740.0 731.6 860.0 859.8 945.0 946.9
馏程/℃
IBP
42
30
180 172 365 269
10%
78
51
214 246 382 341
50%
123 135 277 303 412 389
1 操作状况
某石化公司 2#常减压-延迟焦化装置的常压渣 油分两路进入延迟焦化单元。一路进入焦化分馏塔 塔底,另一路从分馏塔闪蒸段上部进入分馏塔。来 自焦炭塔的反应油气从分馏塔闪蒸段下部进入焦化 分馏塔,中间设置脱过热人字形洗涤挡板。反应油 气经过分馏塔洗涤板从蒸发段上升,与常压渣油换 热后,进入蜡油集油箱以上的分馏段,分馏出富气、 汽油、柴油和蜡油馏分。常压渣油升温后和循环油 在塔底混合由泵送往焦化加热炉。该分馏塔设置 4 个中段回流,依次为塔顶循环回流、柴油分馏段回 流、中部取热回流段、蜡油回流段。焦化汽柴油混 合进入加氢精制装置,不设柴油汽提塔。设计按循 环比 0.8 操作,出装置蜡油产量很小,不设蜡油汽 提塔。分馏塔操作条件及设计条件见表 1,装置产 品收率及设计收率见表 2,分馏塔原产品性质见 表 3。
模型,分析焦化分馏塔操作中的存在的问题;分析影响其分离精度的塔结构问题。针对焦化分馏塔恢复产能提
出了相应的改造建议,并进行了模拟计算和水力学计算验证。为分馏塔的优化操作和改造提供依据,同时为恢
复产能后的分馏塔稳定生产提供理论指导。
关键词:焦化装置;分馏塔;模拟;水力学核算
中图分类号:TE 624.3+2
and verified by simulation and hydraulic calculation to provide the basis for operation optimization and transformation of fractionation tower and the theoretical guidance for fractionation column stable production after capacity recovery. Key words:delayed coking unit;frationation column;analysis;hydraulic calculation
项目
焦化汽油
焦化柴油
焦化蜡油
模拟值 生产值 模拟值 生产值 模拟值 生产值
密度/kg·m-3 742.2 731.6 863.8 859.8 946.7 946.9
馏程/℃
IBP
31
30
124 172
—Байду номын сангаас
269
10%
77
51
217 246 366 341
50%
133 135 286 303 391 389
especially asphaltene content. For pre-estimating operating performance of fractionation column after capacity recovery,production data were collected. Its problems in operation were analyzed by building a process calculation model. Moreover,the influence of tower structure on separation accuracy was analyzed. Referring to capacity recovery of fractionation column,improvement suggestions were made
90%
162 209 345 347 450 441
95%
170 223 358 358 460 450
FBP
181 237 375 363 475 491
从焦化分馏塔的操作来看,柴油和蜡油馏分间 的重叠度较大,焦化蜡油中含有约 15%~20%的高 附加值柴油。蜡油的侧线抽出量偏大,蜡油收率远 高于设计收率。而汽柴油的收率偏低,小于设计收 率,装置整体液收较低。
·3118·
化工进展
CHEMICAL INDUSTRY AND ENGINEERING PROGRESS
2014 年第 33 卷第 11 期
应用技术
焦化分馏塔模拟分析及改进
张龙 1,赵亚新 2,方向晨 1,杜维谦 3,高景山 1,薄德臣 1
(1 中国石化抚顺石油化工研究院,辽宁 抚顺 113001;2 中国石化塔河分公司,新疆 库车 842000;3 中国石油 抚顺石化分公司石油二厂,辽宁 抚顺 113003)
90%
167 209 347 347 432 441
95%
175 223 354 358 438 450
FBP
184 237 363 368 450 491
蜡油与柴油恩氏蒸馏重叠度接近 80℃。蜡油初馏点 及 10%点温度较低,蜡油中含有大量的柴油馏分。 根据模拟计算结果作出分馏塔气液相负荷分布图, 见图 2 所示。
·3120·
化工进展
2014 年第 33 卷
密度(20℃) /kg·m−3 999.7
黏度(80℃) /mm2·s−1 1462
表 4 塔河原油常压渣油性质
凝点 残炭
酸值
闪点 芳烃 胶质
/℃ /%
/mgKOH·g−1
/℃ /% /%
24 20.2
<0.05
232 32.8 21.7
沥青质 /% 15.5
Fushun 113003,Liaoning,China)
Abstract It was planned to increase the capacity of 2# DCU (delayed coking unit) in Sinopec a Petrochemical from 1.4Mt/a to originally designed 2.2Mt/a. The blocked holes on trays of fractionation column would be opened. Meanwhile,the properties of crude oil changed greatly in recent years,