柴油加氢工艺流程课件
柴油加氢工艺流程精

柴
油
延迟焦化柴油
加 氢
催化裂化柴油
改
质
装
置
燃料气 石脑油 加氢柴油
总厂燃料气管网 催化重整预分馏 油品调合罐区
加工原理:在柴油加氢精制改质装置,除了发生了加氢脱除杂质的反应, 还发生了改质反应,即使柴油中低十六烷值的组分在高压氢气和催化剂存在 的条件下转化成较高十六烷值的组分,进而提高整体柴油的十六烷值。
职业教育应用化工技术专业教学资源库《汽柴油生产操作》课程
柴油加氢装置工艺流程
郑哲奎
承德石油高等专科学校
职业教育应用化工技术专业教学资源库《汽柴油生 冷却器
排放氢
1
2
原料泵
加热炉
高
低分气
分
罐
低
污水
分 罐
精制油去分馏塔 污水
冷氢
柴油加氢精制装置反应系统工艺流程图 (1 精制反应器 2 改质反应器)
职业教育应用化工技术专业教学资源库《汽柴油生产操作》课程
氢气
高
低分气
分
罐
低
污水
分 罐
精制油去分馏塔 污水
高分罐内分离 三相是氢气、油相和 污水
低分罐内分离 三相是低分气、精制 油和污水
职业教育应用化工技术专业教学资源库《汽柴油生产操作》课程
分馏单元的任务是做好柴油 轻组分含量的控制,即50%蒸发 温度的控制。
馏
反应油从低分罐来
塔
原料泵
回流罐
瓦斯气 石脑油
柴油出装置
柴油加氢精制装置分馏系统工艺流程图
分馏塔底泵
职业教育应用化工技术专业教学资源库《汽柴油生产操作》课程
分离塔顶的气体产出量不应 有变化,如果其产量增高,说明 在反应器内发生的加氢裂化量增 加,需要调整反应温度、压力、 剂油比、空速等因素。
加氢工艺原理与操作课件
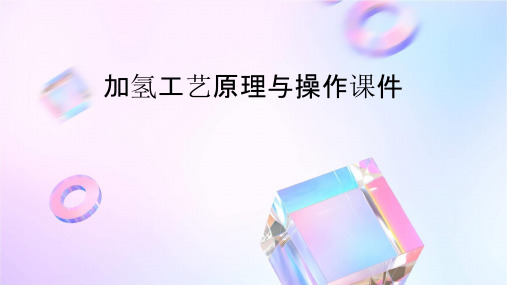
该石油公司针对现有加氢工艺流程进行优化,改进反应条件和操作参数,降低能耗和物耗,提高油品质量和产量。 同时,采用新型催化剂和反应器技术,提升加氢工艺的效率和稳定性。
某化学公司的加氢催化剂研究
总结词
研发高效加氢催化剂,降低生产成本。
详细描述
该化学公司开展加氢催化剂研究,通过实验和模拟手段探究催化剂活性组分、载体和制备方法对加氢 反应性能的影响。同时,优化催化剂的制备工艺,降低生产成本,为加氢工艺的广泛应用提供技术支 持。
高分子合成
在材料科学领域,加氢工艺可用于高分子合成的特定步骤,如聚合物链的加氢饱 和。通过加氢反应,可以提高聚合物的稳定性和性能。
04
加氢工艺的未来发展
加氢工艺的技术进步
01
02
03
高效催化剂
研发更高效、稳定的催化 剂,提高加氢反应的转化 率和选择性。
反应器优化
改进和优化反应器设计, 提高设备的传热和传质效 率,降低能耗。
催化剂的选择
根据不同的加氢反应类型和原料性 质,需要选择适宜的加氢催化剂以 保证反应的顺利进行和产物质量的 合格。
加氢工艺流程与设备
工艺流程
加氢工艺通常包括原料预处理、 反应、产物分离和精制等步骤, 各步骤之间通过管道和设备连接
形成完整的工艺流程。
主要设备
加氢工艺的主要设备包括反应器、 加热炉、压缩机、分馏塔等,这 些设备的性能和操作直接影响到 整个工艺过程的效率和产品的质 量。
氢气纯度与流量控制
加氢反应需要使用纯度较高的氢气,同时需要控制氢气的流量,以 保证反应的稳定和产物的质量。
加氢原料与产物的处理
原料预处理
加氢原料通常需要进行预处理, 如脱水和脱硫等,以去除杂质和 提高原料的质量。
柴油加氢培训课件
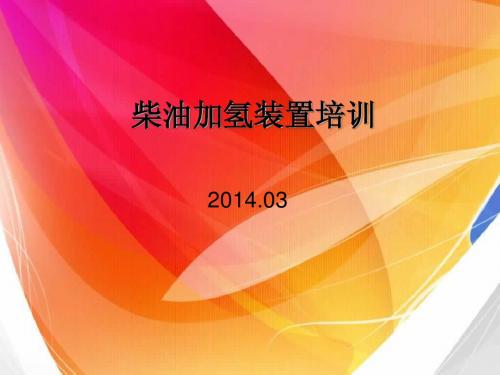
三、我厂柴油升级现状及升级方案
• 2、为满足柴油全部加氢和调整柴油产品结 构的要求,因此新建160万吨/年柴油加氢装 置。该装置主要加工催化柴油、焦化柴油 和I、Ⅱ套常减压的直馏柴油等,经过对原 料的加氢精制以满足平衡全厂柴油硫含量、 十六烷值和多环芳烃的需要。为了保障产 品的质量,因此全厂柴油加工路线设冬、 夏季工况,在冬季工况下通过侧线抽出部 分低凝柴油,以达到生产低凝柴油的目的。
120 160 160 2 100 180 4
改造 改造 新建 新建 新建 新建 新建
三、我厂柴油升级现状及升级方案
• 4、升级后的总加工流程及产品质量。
四、新建柴油加氢装置流程复述
• 1、新建一套160×104t/a柴油加氢精制装置。 采用中国石油石油化工研究院开发的PHF101P系列保护剂、PHF-101柴油加氢精制 催化剂,夏季加工直馏重柴油、催化柴油 和焦化柴油;冬季加工直馏重柴油、直馏 轻柴油、催化柴油和焦化柴油。主要生产 满足国V柴油质量要求的调和组分(冬季需 兼顾-35#低凝柴油调和组分生产),同时副 产部分石脑油和脱硫干气。
四、新建柴油加氢装置流程复述
• 3、具体工艺流程。
谢谢!
一、柴油质量升级
具体指标对比。
1、国三柴油标准 2、国四柴油标准 3、国五柴油标准 主要指标硫含量
国二 硫含量ppm 2000
国三 350
国四 50
国五 10
年份
2013.07
2015.01
2018.01
一、柴油质量升级
3、柴油质量升级难点(即柴油超深度脱硫的难点)是脱 除4,6-二甲基二苯并噻吩类有空间位阻效应影响的大分 子硫化物。 途径一:直接脱硫 途经二:先加氢再脱硫
催化加氢汇总PPT精品课件

2021/3/1
1
第一节 概 述
催化加氢过程是指石油馏分(包括渣油)在氢 气存在下催化加工过程的通称。 一 、加氢的重要性 ❖ 渣油:加氢是最理想的方式; ❖ S/N/O加氢脱除; ❖ 高质量的燃料生产:清洁燃料,清洁柴油只有 加氢,生物柴油。
提高加工深度,改善产品质量,提高轻质油 收率,减少大气污染。
2021/3/1
13
2、环烷烃的加氢裂化,单环环烷烃在加 氢裂化过程中发生异构化、断环、脱烷 基侧链反应。
环烷烃加氢裂化反应方向因催化剂的 加氢和酸性活性的强弱不同而有区别。
2021/3/1
14
长链单环六员环烷烃在高酸性催化剂上进行 加氢裂化时,主要发生断侧链反应,六员环较 稳定,很少发生断环。短侧链单环六员环烷烃 在高酸性催化剂上加氢裂化时,异构化生成环 戊烷衍生物,然后再发生后续反应。反应过程 明显现出正碳离子的机理特征。
2021/3/1
4
❖ 加氢裂化:高压下,烃分子与氢气在催化剂表 面进行裂解和加氢反应生成较小分子的转化过 程。
馏分油加氢裂化:减压蜡油、焦化蜡油、裂化 循环油、脱沥青油。生产高质量的轻质油品, 优质低冰点航空煤油以及低凝点柴油。轻质油 品收率高,灵活性大,用各种原料,不同的操 作条件,根据生产需要和市场行情调节生产方 案,生产柴油、航空煤油,汽油甚至液化气。
本身活性并不高,只有与活性组分合 理搭配才能发挥良好的作用。
2021/3/1
19
担体:提供较大的比表面积,使活性组分很好 的分散在其表面,减少活性组分的用量。
中性担体:中性氧化铝;酸性担体:硅酸铝、 分子筛等。
其他性能:形状:三叶形等异型;根据催化剂 特点,确定孔径、比表面积、孔径小,比表面 大,活性高。
汽柴油加制氢介绍.ppt
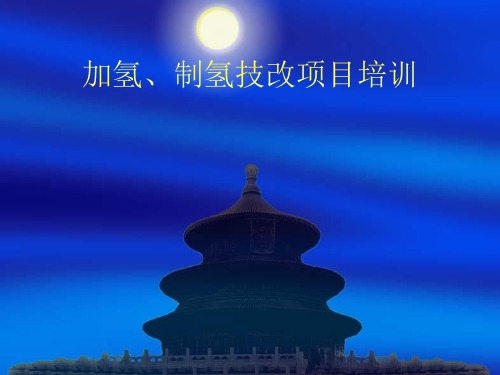
2) 产品氢气压力
≥2.4 MPa.G
3) 产品氢温度
≤40 ℃
4) PSA部分解吸气排气压力
≥0.03 MPa
5) PSA部分氢气回收率(设计值) ≥83 %
3、30万吨/年催化汽油加氢装置 该装置设计点为28.80万吨/年催化汽油,最大加工量为36万吨/年,最小加工量为20
万吨/年。装置主要原料为催化汽油,其主要性质为 :
产品设计目标为: 1) 加氢后汽油产品硫含量<150PPm(主要由专利商保证)。 2) 加氢处理RON损失≯1.5个单位(主要由专利商保证)。 3) 重汽油加氢单元C5+以上液体收率>99.6 m %。 三套装置与一期项目装置共用一套公用工程,并在此基础上新增2台1000m3原料调合罐, 以保证装置进料的平稳性;新上10000m3气柜一台,以缓解火炬系统的压力,并能达到合 理利用装置废气的目的。
该装置设计点为38.56万吨/年,其中直馏柴油、催化柴油、直馏汽油的比例分别为 57.05%、35.17%、7.78%,最大加工量为46万吨/年,最小加工量为26万吨/年。装置原 料主要性质为:
装置产品设计目标为:
1) 精制柴油硫含量: 2) 精制汽油(石脑油)干点: 3) 精制柴油闪点:
≤350ppm ≤200℃ ≥55℃
2 、生产流程简述 1) 生产流程简述 ①反应部分
自罐区来的原料油,按预期的原料比例,首先进入原料调合罐进行调和,然
后在原料油缓冲罐(V3001)液面和流量控制下混合,经原料油脱水器 (SW3001)脱水(保证原料水含量低于350ppm),再通过原料油过滤器(FI3001) 滤去原料中大于25微米的颗粒,然后进入原料油缓冲罐(V3001)。原料油缓冲 罐采用燃料气进行保护。来自原料油缓冲罐(V3001)的原料油经加氢进料泵 (P3001A,B)增压至9.2MPa(G),在流量控制下,经反应流出物/原料油换热器 (E3003A,B)换热后,与混合氢混合进入反应流出物/反应进料换热器(E3001A、B、 C),然后经反应进料加热炉(F3001)加热至反应所需温度,进入加氢精制反应 器(R3001)。该反应器设置三个催化剂床层,床层间设有注急冷氢设施。来自 加氢精制反应器(R3001)的反应流出物,经反应流出物/反应进料换热器 (E3001A、B)、反应流出物/低分油换热器(E3002)、反应流出物/反应进料 换热器(E3001C)、反应流出物/原料油换热器(E3003A、B)依次与反应进料、 低分油、原料油换热,然后经反应流出物空冷器(A3001)冷却至50℃,最后经 反应流出物水冷器(E3011)冷却至45℃进入高压分离器(V3002)。为了防止 反应流出物中的铵盐在低温部位析出,通过注水泵(P3002A、B)将除盐水注至 反应流出物空冷器(A3001)上游侧的管道中。
柴油加氢工艺流程(精)ppt课件
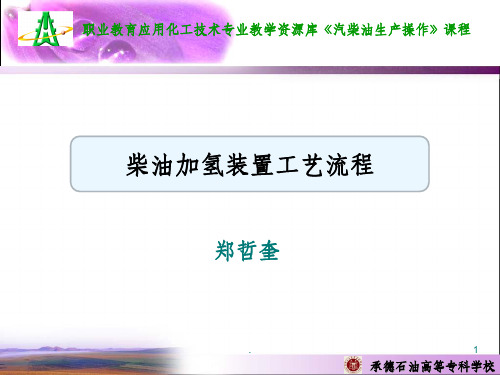
应。或者作为化工洁净原料。
分
馏
塔
反应油从低分罐来
原料泵
回流罐
瓦斯气 石脑油
柴油出装置
柴油加氢精制装置分馏系统工艺流程图
分馏塔底泵
.
6
职业教育应用化工技术专业教学资源库《汽柴油生产操作》课程
分离塔顶的气体产出量不应有
变化,如果其产量增高,说明在
反应器内发生的加氢裂化量增加,
需要调整反应温度、压力、剂油
.
2
职业教育应用化工技术专业教学资源库《汽柴油生产操作》课程
柴油加氢装置加氢精制反应器内发生的反应:
一、加氢脱硫反应: 三、加氢脱氧反应: 五、烯烃饱和反应:
二、加氢脱氮反应: 四、加氢脱金属反应:
但是与催化重整预加氢反应器不同的是,柴油加氢精制反应器内的 反应压力更高,约在8.6MPa左右。
这是因为精制反应器与后面的改质反应器是串联,改质反应是芳烃 开环的反应,需要较高的反应压力。
延迟焦化柴油 催化裂化柴油
装柴 置油
加 氢 改 质
燃料气 石脑油 加氢柴油
总厂燃料气管网 催化重整预分馏 油品调合罐区
加工原理:在柴油加氢精制改质装置,除了发生了加氢脱除杂质的反应,
还发生了改质反应,即使柴油中低十六烷值的组分在高压氢气和催化剂存在
的条件下转化成较高十六烷值的组分,进而提高整体柴油的十六烷值。
炉温的控制有何要求?
为什么是全回流?
组成有哪些?
.
17
职业教育应用化工技术专业教学资源库《汽柴油生产操作》课程
工艺操作参数与常减 压装置常压塔顶回流罐 相同么?
.
18
职业教育应用化工技术专业教学资源库《汽柴油生产操作》课程
《加氢裂化工艺》课件
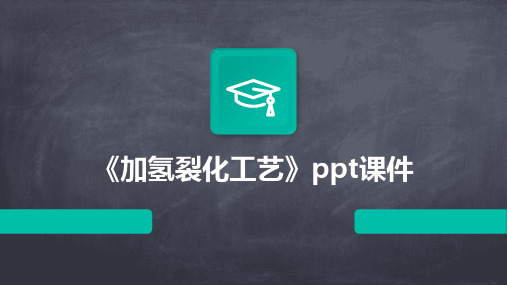
反应器的设计应考虑压力降、温度分布、催化剂装填量等因素,以确 保原料油在最佳条件下进行反应。
04
反应器的操作应控制适当的反应温度和压力,以获得所需的加氢裂化 产物。
加热炉
加热炉是加氢裂化工艺中用于 加热原料油的关键设备。
加热炉通常采用管式加热炉, 炉管内通过原料油,炉管外燃 烧燃料油或天然气,通过热传 导和热辐射将热量传递给原料
技术发展趋势与展望
高效催化剂
研发高效、稳定的催化剂是加氢裂化工艺的重要 发展方向。新型催化剂可提高反应活性和选择性 ,降低能耗和原料消耗,提高产品收率和质量。
智能化控制
智能化控制技术可以提高加氢裂化工艺的安全性 和稳定性。通过实时监测、自动控制和优化操作 ,可降低人工操作成本和事故风险,提高生产效 率。
压缩机的设计应考虑压缩比、 输送能力、机械效率等因素, 以确保气体和液体能够被顺利 压缩和输送。
压缩机的操作应控制适当的入 口和出口压力,以防止气体和 液体在压缩过程中发生泄漏和 堵塞。
分离器
分离器是加氢裂化工艺中用 于分离液体和气体的关键设
备。
1
分离器通常采用立式或卧式 分离器,通过重力或离心力 的作用将液体和气体进行分
绿色低碳发展
随着环保意识的提高,低碳、环保的加氢裂化工 艺成为未来的发展趋势。通过优化反应条件、降 低能耗和减少废物排放,实现加氢裂化工艺的绿 色低碳发展。
拓展应用领域
随着市场需求的变化,加氢裂化工艺的应用领域 也在不断拓展。例如,在生产高品质润滑油、石 蜡、高纯度溶剂等化学品方面,加氢裂化工艺具 有广阔的应用前景。
环保要求与处理措施
01
02
03
04
加氢裂化工艺应符合国家和地 方环保法规要求,确保排放的 废气、废水等污染物达到标准
柴油加氢—典型柴油加氢生产工艺(石油加工课件)
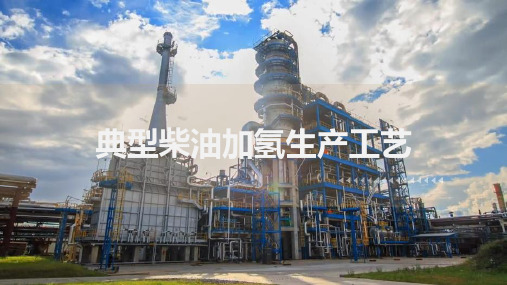
典型柴油加氢生产工艺
二段加氢裂化工艺
在这种工艺流程中有两个反应器,分别装有不同性能的催化剂。第一个反应 器中主要进行原料油的精制;第二个反应器中主要进行加氢裂化反应,形成独立 的两段流程体系。
典型柴油加氢生产工艺
二段加氢裂化工艺
在这种工艺流程中有两个反应器,分别装有不同性能的催化剂。
第一个反应器中主要进行原料油的精制;第二个反 应器中主要进行加氢裂化反应,形成独立的两段流程体 系。二段加氢裂化工艺适合处理高硫、高氮减压渣油, 催化裂化循环油,焦化蜡油或这些油的混合油。
典型柴油加氢生产工艺
单段一次通过流程的加氢裂化装置主要是以直馏减压馏分油为原料生产喷 气燃料、低凝柴油,裂化尾油作高黏度指数、低凝点润滑油料。
工艺流程简单,体积空速相对较高。
所采用的催化剂应具有较强的耐S、N、O等化合物的性能。 原料油的氮含量不宜过高,馏分不能太重,以加工常压瓦斯 油(AGO)/轻减压瓦斯油(LVGO)为宜。 反应温度相对较高,运转周期相对较短。
典型柴油加氢生产工艺
二段加氢裂化工艺特点
二段加氢裂化工艺适合处 理高硫、高氮减压渣油,催化 裂化循环油,焦化蜡油或这些 油的混合油。
第一、二段的反应器、高压分离器和 循环氢(含循环压缩机)自成体系。
补充氢增压机、产品分馏塔两段公用。
工艺流程复杂、投资及能耗相对较高。
对原料油的适应性强,生产灵活性大, 操作运转周期长。 与一段工艺相比,气体产率低、干气少、 目的产品收率高、液体总收率高;产品 质量好,特别是产品中芳烃含量非常低; 氢耗较低。
思政小课堂
随着我国工业化进程的加 快和人们环保意识的不断增长, 对柴油产品的质量提出了更高 的要求,柴油加氢技术不断进 步,不断丰富生产工艺。
加氢裂化工艺及过程 ppt课件

中国石油化工股份有限公司
CHINA PETROLEUM & CHEMICAL CORPORATION
金陵石化分公司炼油运行一部
PPT课件
1
催化加氢技术
1.0 概述 1.1 加氢裂化的沿革 1.2 国内加氢裂化技术发展历程 1.3 加氢裂化的基本原理及特点 1.4 加氢裂化原料油及产品 2.0 加氢裂化工艺流程 2.1 两段法加氢裂化 2.2 单段加氢裂化 2.3 一段串联(单程通过,未转化油全循环、部分循环)
PPT课件
12
催化加氢技术
1.2 国内加氢裂化技术的发展
◎ 50年代, 恢复了页岩粗柴油高压加氢, 发展了页岩油全馏分固定
床加氢裂化, 以及低温干馏煤焦油的高压三段加氢裂化技术。
◎ 60年代中期, 开发了107、219无定型加氢裂化催化剂和H-06沸石
催化剂;
◎ 1966年在大庆炼厂建成了40万吨/年加氢裂化装置, 加工大庆常三
为现代渣油悬浮床加氢以及馏分油固定加氢的基本模式奠定了基 础。
PPT课件
8
催化加氢技术
◎ 二战以后, 可多方获得中东油, 催化裂化技术的发展, 为重瓦斯 油(HVGO)转化生产汽油提供了更经济的手段, 加氢裂化的重要 性曾一度有所降低。
◎ 40年代末50年代初的“相关事件”, 铁路运输由蒸汽机车向柴油 机车驱动的转变,廉价天然气的供应使燃料油用量减少, FCC 发展导致富含芳烃难转化的循环油过剩, 汽车压缩比的提高和 高辛烷值汽油标准的实施等, 都迫切需要将难转化的原料加工 成汽油、柴油,导致对新的烃类转化技术需求的增产。
PPT课件
9
催化加氢技术
◎ 1959年Chevron研究公司宣布“加氢异构裂化工艺”在里蒙炼 厂
柴油加氢工艺流程课件(共 55张PPT)

加氢反应系统
反应系统操作原则
加氢反应原料为催化、焦化柴油和焦化汽油
a 原料要求: 装置加工的焦化柴油和焦化汽油杂质和烯烃含量较高,原料先经过滤 质颗粒,为保证脱除效果降低过滤器的过滤负荷,要求罐区控制较高的柴 时间,汽油罐维持较低的汽油罐存,缩短停留时间,减加氢后的汽柴油,反应生成硫化氢以及加氢干气。 的硫、氮等杂质含量升高,则加氢反应条件应适当的提高,以确保精制产
原料油过滤装置内设置原料自动反冲洗过滤器,脱除大于25微米的固体颗粒。 原料油惰性气体保护原料油缓冲罐采用燃料气覆盖措施,以防止原料被氧化生成胶质。 高压空冷前注水在反应流出物进入空冷前注水,来溶解铵盐,避免铵盐结晶析出堵塞管路。 采用双壳程、螺纹锁紧环换热器,提高换热效率,减少换热面积,节省投资。 采用炉前混氢方案 ,提高换热效率和减缓结焦程度。 采用板焊结构热壁反应器,内设两个催化剂床层,中间设置了冷氢箱。 采用冷高分流程 分馏部分采用双塔蒸汽汽提流程。
1
仪表第四维护班
装置简介
设计能力
装置公称规模为120×104t/a,实际处理量为113.43×104t/a,投产于2003年7月,原设计能力 品有粗汽油、精制柴油,副产品为加氢干气。2004年6月进行掺炼焦化汽油改造,装置实际加工能 主要由反应和分馏两部分组成。
装置特点
a b c d e f g h
10
仪表第四维护班
加氢反应系统
加氢反应温度TRCA-8133A
控制范围:反应器入口温度TRCA-8133A:210-280℃ 控制目标:指令反应温度±2℃ 相关参数:加热炉出口温度点TRCA-8133B高高联锁温度为328℃。
控制方式:PIC-8102与TRCA-8133A串级控制,TRCA-8133A为主调,PIC-8102 压力来控制反应器入口温度TRCA-8133A。提高反应温度可促进加氢反应,有利于 高,会促进裂化反应,而使液收降低,而且催化剂积碳速度加快,缩短催化剂的 须足够高,使得进入反应器的物料100%的汽化,以保证物料在催化剂床层的均匀 效果的情况下,为得到最长的催化剂寿命,反应器入口温度应尽量的低。反应器 断下降而逐渐提高。
柴油加氢精制工艺
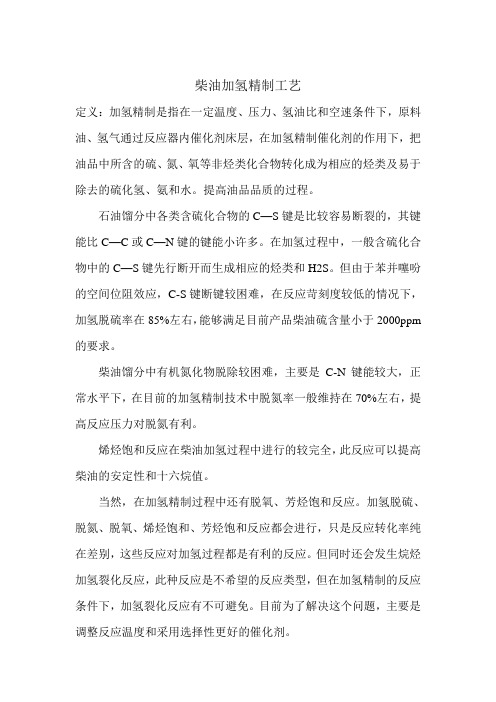
柴油加氢精制工艺定义:加氢精制是指在一定温度、压力、氢油比和空速条件下,原料油、氢气通过反应器内催化剂床层,在加氢精制催化剂的作用下,把油品中所含的硫、氮、氧等非烃类化合物转化成为相应的烃类及易于除去的硫化氢、氨和水。
提高油品品质的过程。
石油馏分中各类含硫化合物的C—S键是比较容易断裂的,其键能比C—C或C—N键的键能小许多。
在加氢过程中,一般含硫化合物中的C—S键先行断开而生成相应的烃类和H2S。
但由于苯并噻吩的空间位阻效应,C-S键断键较困难,在反应苛刻度较低的情况下,加氢脱硫率在85%左右,能够满足目前产品柴油硫含量小于2000ppm 的要求。
柴油馏分中有机氮化物脱除较困难,主要是C-N键能较大,正常水平下,在目前的加氢精制技术中脱氮率一般维持在70%左右,提高反应压力对脱氮有利。
烯烃饱和反应在柴油加氢过程中进行的较完全,此反应可以提高柴油的安定性和十六烷值。
当然,在加氢精制过程中还有脱氧、芳烃饱和反应。
加氢脱硫、脱氮、脱氧、烯烃饱和、芳烃饱和反应都会进行,只是反应转化率纯在差别,这些反应对加氢过程都是有利的反应。
但同时还会发生烷烃加氢裂化反应,此种反应是不希望的反应类型,但在加氢精制的反应条件下,加氢裂化反应有不可避免。
目前为了解决这个问题,主要是调整反应温度和采用选择性更好的催化剂。
下面以我厂100万吨/年汽柴油加氢精制装置为例,简单介绍一下工艺流程:60万吨柴油加氢精制催化汽油选择性加氢脱硫醇技术(RSDS技术)催化汽油加氢脱硫醇装置的主要目的是拖出催化汽油中的硫含量,目前我国大部分地区汽油执行国三标准,硫含量要求小于150ppm,烯烃含量不大于30%,苯含量小于1%。
在汽油加氢脱硫的过程中,烯烃极易饱和,辛烷值损失较大,针对这一问题,石科院开发了RSDS技术。
本技术的关键是将催化汽油轻重组分进行分离,重组分进行加氢脱硫,轻组分碱洗脱硫。
采取轻重组分分离的理论基础是,轻组分中烯烃含量高,可达到50%以上,通过直接碱洗,辛烷值几乎不损失。
《柴油加氢培训包》课件——3柴油加氢催化剂

催化加氢催化剂
不同的非贵金属组分搭配产生的反应活性
反应活性
在H2S存在下
加氢脱氮活性 Ni- Mo-Co>Co-Mo>Co-W
无H2S存在下
加氢脱硫活性 Co-Mo>Ni- Mo>Ni-W>Co-W
加氢脱氧活性 Ni-Mo>Co-Mo>Ni-W>Co-W 芳烃饱和活性 Ni-W- Ni-Mo>Co-Mo>Co-W Ni-W- Ni-Mo>Co-Mo>Co-W
催化加氢催化剂
3.载体 载体具有高的表面积,可高度分散活性的金 属;具有理想的孔结构(孔体积和孔分布),有利 于反应分子的扩散;为容纳积炭提供空间,载体能 改善催化剂的导热性、防止活性组分因局部过热而 烧结失活;作为催化剂的骨架,提高催化剂的稳定 性和机械强度,并使催化剂具有一定的形状和大 小,以适应工业过程中流体力学的需求。
催化加氢催化剂
2.裂化组分 加氢裂化催化剂中的裂化组分就是载体,它为 催化剂提供酸性中心,提供合适的孔结构和增加有 效表面积,并且与活性金属组分形成新的化合物, 改善催化剂性质。 这些载体主要有:活性氧化铝(即γ-AI2O3)、 无定型硅酸铝 、沸石。
催化加氢催化剂
3.助剂 (1)结构性助催化剂
异构化活性 Ni-W>Ni-Mo>Co-Mo>Co-W Ni-W>Ni-Mo>Co-Mo>Co-W 加氢裂化活性 Ni-Mo>Ni-W>Co-Mo>Co-W Ni-Mo>Ni-W>Co-Mo>Co-W
催化加氢催化剂
贵金属组分反应活性与非贵金属组分反应活性的对比
反应活性 芳烃饱和性
无H2S存在下 Pt>Pd>Ni-W- Ni-Mo>Co-Mo>Co-W
催化加氢催化剂
(三)润滑油加氢催化剂 用以代替润滑油的溶剂精制和白土精制。 催化剂是催化加氢的技术核心。加氢装置的投
柴油加氢工艺流程(精)
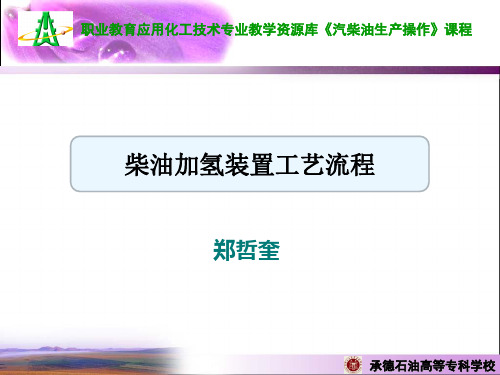
瓦斯气
分馏单元的任务是做好柴油 轻组分含量的控制,即50%蒸发 温度的控制。
具体轻组分控制量为多少? 要看油库待调和的直馏柴油的情 况而定。
反应油从低分罐来
回流罐
石脑油
分 馏 塔
原料泵 柴油出装置
柴油加氢精制装置分馏系统工艺流程图
分馏塔底泵
职业教育应用化工技术专业教学资源库《汽柴油生产操作》课程
瓦斯气 回流罐
燃料气 石脑油 加氢柴油
延迟焦化柴油 催化裂化柴油
加工原理:在柴油加氢精制改质装置,除了发生了加氢脱除杂质的反应, 还发生了改质反应,即使柴油中低十六烷值的组分在高压氢气和催化剂存在 的条件下转化成较高十六烷值的组分,进而提高整体柴油的十六烷值。
职业教育应用化工技术专业教学资源库《汽柴油生产操作》课程
工艺操作参数与常减 压装置常压塔顶回流罐 相同么?
职业教育应用化工技术专业教学资源库《汽柴油生产操作》课程
航煤汽提塔
组成特点?
职业教育应用化工技术专业教学资源库《汽柴油生产操作》课程
如果没有航煤生产任料 中, 正十六烷的体积百分数。
正十六烷 α-甲基萘
十六烷值为100
十六烷值为0
碳链越直,结构越简单的烃类,其十六烷值越高。
职业教育应用化工技术专业教学资源库《汽柴油生产操作》课程
循环氢压缩机 排放氢 新氢 冷却器 高分罐 低分气 1
2
稳
低分罐
定 塔
原料泵 加热炉 精制油去分馏塔
这里的石脑油,杂质含量很 少,可以作为精制油直接进入催 化重整装置重整反应系统发生重 整反应。或者作为化工洁净原料。
石脑油
分 馏
反应油从低分罐来
塔
原料泵 柴油出装置
柴油加氢裂化培训课件(1)

2.4
0.3
0.4
2.9
5.7
返回 19
未转化油
组分 质量流量
比重 馏程 IBP 5% 10% 30% 50% 70% 90% 95% FBP
硫 十六烷值 十六烷值
指数 稠环芳烃
闪点
单位 Tons/h
℃
wt ppm D613 D976 wt.% °C
方法 D86
运行初期 1.786 0.8002
运行末期 1.786 0.8052
• 该装置的主要目的是将自常减压装置来的直馏柴油和HOil装置来的柴油转化成重石脑油和轻石脑油,并最大化生产 重石脑油。装置设计操作负荷为50% ~ 100%负荷。
返回 3
装置总体概况
返回 4
装置总体概况
返回 5
装置物料平衡(恒力)
进料[1]
加工量 (t/h )
直馏柴油 217.3
产品 酸性气
0.05
3.26
3.26
1.39
1.39
1.76
1.76
0.45
0.45
0.24
0.24
9.62
9.62
8.69
1.47 13.59
8.69
1.47 13.59
14.58
14.58
0.5 0.54 1.26 0.79 14.47
10.84
0.1 0.25
1.45
2.09 0.08 8.76 0.14
IBP
10%
30%
50%
70%
90%
FBP
开工初期
0.813 10 1 0.1 79 19 2
166 188 213 244 282 352 488
汽柴油加氢精制生产工艺
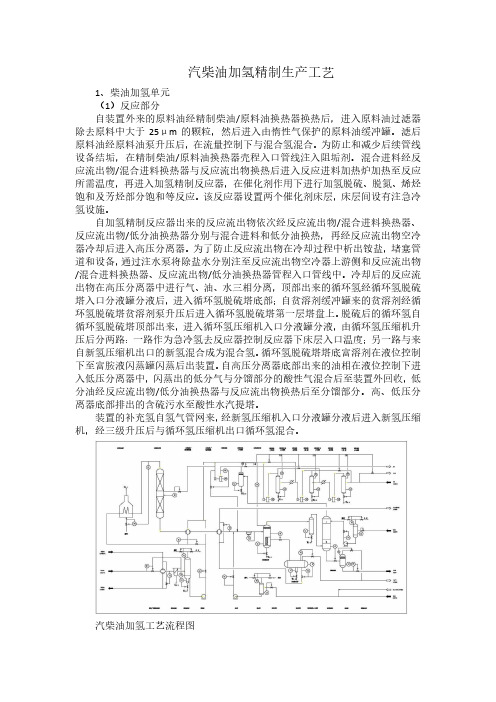
汽柴油加氢精制生产工艺1、柴油加氢单元(1)反应部分自装置外来的原料油经精制柴油/原料油换热器换热后,进入原料油过滤器除去原料中大于25μm的颗粒,然后进入由惰性气保护的原料油缓冲罐。
滤后原料油经原料油泵升压后,在流量控制下与混合氢混合。
为防止和减少后续管线设备结垢,在精制柴油/原料油换热器壳程入口管线注入阻垢剂。
混合进料经反应流出物/混合进料换热器与反应流出物换热后进入反应进料加热炉加热至反应所需温度,再进入加氢精制反应器,在催化剂作用下进行加氢脱硫、脱氮、烯烃饱和及芳烃部分饱和等反应。
该反应器设置两个催化剂床层,床层间设有注急冷氢设施。
自加氢精制反应器出来的反应流出物依次经反应流出物/混合进料换热器、反应流出物/低分油换热器分别与混合进料和低分油换热,再经反应流出物空冷器冷却后进入高压分离器。
为了防止反应流出物在冷却过程中析出铵盐,堵塞管道和设备,通过注水泵将除盐水分别注至反应流出物空冷器上游侧和反应流出物/混合进料换热器、反应流出物/低分油换热器管程入口管线中。
冷却后的反应流出物在高压分离器中进行气、油、水三相分离,顶部出来的循环氢经循环氢脱硫塔入口分液罐分液后,进入循环氢脱硫塔底部;自贫溶剂缓冲罐来的贫溶剂经循环氢脱硫塔贫溶剂泵升压后进入循环氢脱硫塔第一层塔盘上。
脱硫后的循环氢自循环氢脱硫塔顶部出来,进入循环氢压缩机入口分液罐分液,由循环氢压缩机升压后分两路:一路作为急冷氢去反应器控制反应器下床层入口温度;另一路与来自新氢压缩机出口的新氢混合成为混合氢。
循环氢脱硫塔塔底富溶剂在液位控制下至富胺液闪蒸罐闪蒸后出装置。
自高压分离器底部出来的油相在液位控制下进入低压分离器中,闪蒸出的低分气与分馏部分的酸性气混合后至装置外回收,低分油经反应流出物/低分油换热器与反应流出物换热后至分馏部分。
高、低压分离器底部排出的含硫污水至酸性水汽提塔。
装置的补充氢自氢气管网来,经新氢压缩机入口分液罐分液后进入新氢压缩机,经三级升压后与循环氢压缩机出口循环氢混合。
- 1、下载文档前请自行甄别文档内容的完整性,平台不提供额外的编辑、内容补充、找答案等附加服务。
- 2、"仅部分预览"的文档,不可在线预览部分如存在完整性等问题,可反馈申请退款(可完整预览的文档不适用该条件!)。
- 3、如文档侵犯您的权益,请联系客服反馈,我们会尽快为您处理(人工客服工作时间:9:00-18:30)。
工艺流程
▪ 分馏部分
从反应部分来的低分油与T1102底油换热后进入脱硫化氢汽提塔(T1101),塔底通入220℃汽提蒸 汽,塔顶油气经汽提塔顶空冷器(A1102)、汽提塔顶后冷器(E1107)冷凝冷却至40℃,进入汽提塔顶 回流罐(V1104)进行气、油、水三相分离。闪蒸出的气体与低分气合并送至装置外;V1104含硫含氨污 水与高分、低分酸性水一起送出装置;油相经汽提塔顶回流泵(P1103A,B)升压后全部作为塔顶回流 。为了抑制硫化氢对塔顶管道和冷换设备的腐蚀,在塔顶管道注入缓蚀剂。脱硫化氢汽提塔底油经 E1102与反应流出物换热后进入产品分馏塔(T1102),T1102设有29层浮阀塔盘,塔底设蒸汽汽提,塔 顶油气经产品分馏塔顶空冷器(A1103)、产品分馏塔顶后冷器(E1105)冷凝冷却40℃后进入产品分馏 塔回流罐(V1105),回流罐压力通过燃料气控制。回流罐液相经产品分馏塔塔顶回流泵(P1104A、B) 升压后,一部分作为分馏塔的回流,另一部分作为粗汽油产品出装置。V1105分水包排出的含油污水自 流出装置由工厂统一处理。产品分馏塔底油经柴油泵(P1105A、B)升压后先经E1106A~D换热,后经柴 油空冷器(A1104)冷却至50℃,再经过柴油聚集器(V1108)脱水后,精制柴油送出装置
在加氢精制条件下,氮化物在氢作用下,转化为NH3和烃,几种含氮化合物反应如下: 胺类:R-NH2+H2→RH+NH3
加氢原料油中氮化物大部分是环状化合物,加氢时首先是杂环结构被氢饱和生成氢化衍生物,然后氢化环在不 同位置上断裂生成胺,胺进一步加氢分解,转化为氨和相应的饱和烃和烷基芳烃。例如喹啉的反应:
▪ 装置特点
a 原料油过滤装置内设置原料自动反冲洗过滤器,脱除大于25微米的固体颗粒。 b 原料油惰性气体保护原料油缓冲罐采用燃料气覆盖措施,以防止原料被氧化生成胶质。 c 高压空冷前注水在反应流出物进入空冷前注水,来溶解铵盐,避免铵盐结晶析出堵塞管路。 d 采用双壳程、螺纹锁紧环换热器,提高换热效率,减少换热面积,节省投资。 e 采用炉前混氢方案 ,提高换热效率和减缓结焦程度。 f 采用板焊结构热壁反应器,内设两个催化剂床层,中间设置了冷氢箱。 g 采用冷高分流程 h 分馏部分采用双塔蒸汽汽提流程。
柴油加氢工艺流程课件
2020年4月27日星期一
装置简介
▪ 设计能力
装置公称规模为120×104t/a,实际处理量为113.43×104t/a,投产于2003年7月,原设计能力为120万吨/年,主要产品 有粗汽油、精制柴油,副产品为加氢干气。2004年6月进行掺炼焦化汽油改造,装置实际加工能力为104×104t/a。装置主要 由反应和分馏两部分组成。
工艺原理
▪ c 烯烃饱合
烯烃饱合生成烷烃,其加氢反应速度比脱硫反应略慢,原料由于烯烃的存在,会增加催化剂上的积碳,缩短生 产周期。化学反应方程式:
CnH2n + H2→CnH2n+2 烯烃饱合也为耗氢和放热反应,原料油溴价每降低一个单位,放热8.11×103焦/公斤进料,耗氢量约为1.07- 1.42NM3/M3原料。
▪ d 脱氧反应:
加氢原料油中含有酚、过氧化物、酮等化合物,它们在加氢精制条件下发生下列反应。
Байду номын сангаас
工艺流程
▪ 反应部分
原料油自装置外来,在原料油缓冲罐(V1101)液面控制下,通过原料油过滤器(FI1101)进行过 滤,除去原料中大于25μm的颗粒。过滤后的原料油进入原料油缓冲罐,然后经加氢进料泵(P1101A、B )升压后,在流量控制下,与混合氢混合作为反应进料,依次与反应流出物经两个台位的反应流出物/ 反应进料换热器(E1103A、B和E110l)换热后,进入反应进料加热炉(F1101)加热至反应所需温度, 再进入加氢精制反应器(R1101),在催化剂作用下进行脱硫、脱氮、烯烃饱和、芳烃饱和等反应。该 反应器设置两个催化剂床层,床层间设有注急冷氢设施。来自R1101的反应流出物,经反应流出物/反 应进料换热器(E1101、E1103A,B)、反应流出物/分馏塔进料换热器(E1102)依次与反应进料、分 馏塔进料、反应进料换热,然后经反应流出物空冷器(A1101)冷却至49℃进入高压分离器(V1102)。 为了防止反应流出物中的铵盐在低温部位析出,通过注水泵(P1102A、B)将脱盐水注至A1101上游侧的 管道中。冷却后的反应流出物在高压分离器(V1102)中进行油、气、水三相分离。高分气进入循环氢 压缩机(C1101)升压后分两路:一路作为急冷氢进入反应器;一路与来自新氢压缩机(C1102A、B)的 新氢混合,混合氢与原料油混合作为反应进料。含硫、含氨污水自V1102底部排出,至装置外酸性水汽 提装置处理。高分油相在液位控制下经调节阀减压后进入低压分离器(V1103)。V1103闪蒸出的低分气 至分馏部分与脱硫化氢汽提塔顶气合并送出装置进行脱硫处理。低分油经柴油/低分油换热器(E1106A ~D)与柴油产品换热后,进入脱硫化氢汽提塔(T1101)。新氢经新氢压缩机入口分液罐(V1106)分 液后进入C1102A、B,经两级升压后与C1101出口的循环氢混合。
工艺流程
▪ 含氢尾气膜分离提氢部分
由芳烃装置、加氢裂化装置和柴油加氢装置提供异构化富氢、100#酸性气、加氢裂化、柴油加氢干气等四股富 含氢原料气汇集混合后输送到氢气压缩机入口缓冲罐(V102)。混合原料气通过氢气压缩机升压至6.8MPa(G),经氢气 压缩机冷却器(E102)冷却后进入氢气压缩机出口分液罐(V103),先脱除所含液态烃,然后进入膜分离系统。膜分离 氢提纯工艺流程主要由两部分组成,即预处理和膜分离。预处理的目的是除去原料气中的固体微粒和重烃,并将气 体加热到比露点温度高10~20℃,从而得到既干净又温热的气体。该气体可直接进行膜分离。膜分离的目的是提纯 氢气。含氢尾气经稳流后, 以6.8MPa 、40 ℃进入膜分离装置界区, 此气体先经一除雾器(X-101),除去较大水滴和 油滴。再由高效联合过滤器(X-102 )除去大于0.01μm 的粒子, 可冷凝的液沫及雾滴被捕集形成液体后, 通过过 滤器底部的阀门排出界区。联合过滤器分两组,一组在线,一组备用。分别为两级串联。然后原料气经过一套管式 加热器(E-101 )加热至83 ℃, 使原料气远离露点, 不至于因为氢气渗透后滞留气烃类含量升高,冷凝形成液膜而 影响分离性能。 用一蒸汽流量调节阀TV-101 和温度变送器TT-101 实现原料气温度控制,指示报警和联锁。原料气 经过加热器(E-101 )加热至83 ℃后,经一管道过滤器(SP-101 ), 再进入PRISM®膜分离器(M101A/B/C )进行 分离。膜分离器M-101A 与M-101B 并联,然后与M-101C 串联运行。 每个PRISM®膜分离器外型类似一管壳式热交换 器,膜分离器壳内由成千上万根中空纤维束填充,类似于管束。原料气从下端侧面进入PRISM®膜分离器。由于各种 气体组分在透过中空纤维膜时的溶解度和扩散系数不同,导致不同气体在膜中的相对渗透速率不同,在加氢尾气的 各组分中氢气的相对渗透速率最快,从而可将氢气分离提纯。在原料气沿PRISM®膜分离器长度方向流动时,更多的 氢气扩散进入中空纤维。在中空纤维芯侧得到92%的富氢产品,称为渗透气,压力为2.3MPa; 在壳程得到富含惰性气 体的物流,称为非渗透气。 其压力由HV-101 控制, 并减压至1.0 Mpa ,进入燃料气管网。PRISM®膜分离器可以根
▪ 原料及产品
原料为焦化汽油、焦化柴油和催化柴油的混合油,产品为精制柴油和精制汽油,副产品为干气,至装置外脱硫后作燃 料使用
工艺原理
▪ 加氢精制
加氢精制是指在催化剂和氢气存在下,石油馏份中含硫、氮、氧的非烃类组份和有机金属化合物分 子发生脱除硫、氮、氧和金属的氢解反应,烯烃和芳烃分子发生加氢反应,被处理的原料平均分子量及
烃类分子的骨架结构发生极小的变化。
▪ a 脱硫反应:
在加氢条件下,石油馏份中的各种含硫化合物转化为相当的烃和H2S,从而脱除了硫。 硫醇加氢:R-SH+H2→RH+H2S 硫醚加氢:R-S-R`+2H2→RH+R`H+H2S 二硫化物加氢:R-S-S-R`+3H2→RH+R`H+2H2S
工艺原理
▪ b 脱氮反应