大型热芯盒模具排气系统设计
轩业模具-模具的排气系统及分型面设计
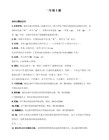
(1)、分型面的形式
注射模具具有的有一个分型面,也有多个分型面,分型面的形状应尽可能简单,以便于模具的制造和塑件的脱模。
(2)、分型面得选择原则
1、分型面应选择在塑件外形最大的轮廓处,只有这样才能使塑件从模具中顺利脱模,这是最基本的一条原则。
2、分型面得选择应考虑有利于塑件的脱模,一般模具的脱模机构通常设置在动模一侧,模具开模后塑件应该停留在动模一边,以便于塑件顺利脱模。
2、利用分型面排气
对于小型模具可以利用模具分型面的间隙来排出腔内的气体,但分型面必须位于熔体流动的末端;对于大型模具可以在分型面上开设排气槽,加强型腔内部气体排放。排气槽一般开设在分型面上凹模一边,位置位于塑料模具的末端排气槽尺寸以气体能顺利地排出而物料不溢出为原则;
3、利用粉末烧结合金块排气
3、型面的选择要保证塑件的精度要求,塑件光滑的表面不应设计成分型面,以避免影响到外观的质量;塑件中要求同轴度得部分要放到分型面的同一侧,以保证塑件同轴的要求。
4、分型面的选择还应考虑模具的侧向抽拔距,由于模具侧向分型是由机械分型机构来完成的,所以抽拔距都比较小,选择分型面时应将抽芯或分型距离长的方向置于开合模的方向,将小抽拔距作为侧向分型面或抽芯。
塑料模具的注射过程是熔融塑料将型腔中的空气置换出来的过程,当塑料将型腔填充时,必须顺利地排放出型腔及浇注系统中的空气及塑料受热而产生的热空气,如果气体不能被顺利排出,塑料会由于空气填充不足而产生接缝或表面轮廓不完整等缺陷。
一、模具排气的形式主要有以下三种形式:
1、利用配合间隙排气
模具的分型面、推杆与模板之间及活动型与模板之间都有一定的配合间隙,一般间隙值在0.03~0.05mm之间,利用模具零件之间的这种间隙,可以将型腔中的气体顺利排出。
电动机壳压铸成型模具设计中的模具排气系统优化方法分享

电动机壳压铸成型模具设计中的模具排气系统优化方法分享在电动机壳压铸成型模具设计中,模具排气系统的优化是非常重要的,它直接影响到最终产品的质量和生产效率。
本文将分享一些模具排气系统的优化方法,希望对相关行业从业人员有所帮助。
一、模具排气系统的作用模具排气系统是用来排除模腔内气体的系统,排气系统的质量直接影响到模具的成型效果。
不良的排气系统设计会导致产品内部气孔、气泡等缺陷,严重影响产品的质量。
二、模具排气系统的优化方法1. 合理设置排气口在模具的设计中,应该合理设置多个排气口,保证气体可以顺利排出模腔。
排气口的位置应该选择在模具设计中最易积聚气体的位置,比如拐角处、凹槽处等。
同时还要注意排气口的大小和数量,以确保足够的气体排出。
2. 增加排气道在部分复杂产品的模具设计中,可以考虑增加排气道,将多个排气口通过管道连接起来,增加排气的效率。
这种方式可以有效地减少气体滞留,避免气泡等缺陷的产生。
3. 优化排气结构在模具设计中,应该优化排气结构,比如采用倾斜排气口、螺旋排气道等结构,增加气体排出的效率。
同时还可以考虑在模具中设置一定的排气间隙,避免气体被密封在模具中。
4. 使用排气膜在一些对模具精度要求较高的产品中,可以考虑使用排气膜来替代传统的排气口。
排气膜可以有效地防止气泡的产生,提高产品的成型质量。
5. 定期清洁维护在使用过程中,应该定期对模具的排气系统进行清洁维护,确保排气系统畅通无阻。
同时还要及时更换损坏的排气部件,以确保排气系统的正常运行。
通过以上优化方法,可以有效地提高电动机壳压铸成型模具的生产效率和产品质量,减少产品的废品率。
希望相关从业人员能够根据实际情况选择合适的优化方法,提升生产效率和产品质量。
模具设计之模具排气设计标准
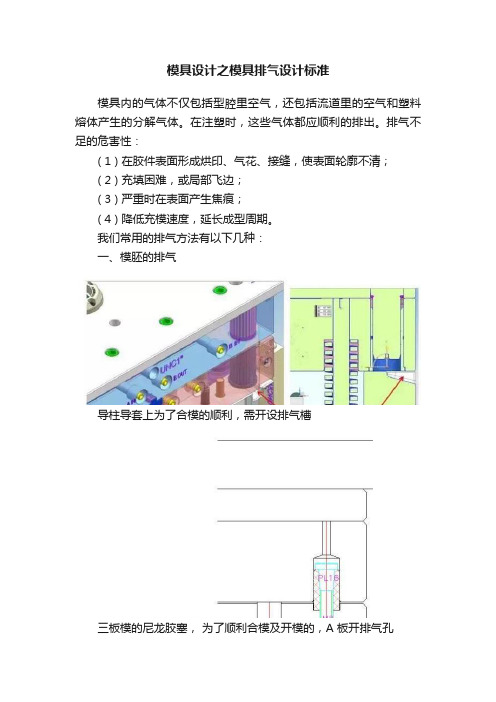
模具设计之模具排气设计标准
模具内的气体不仅包括型腔里空气,还包括流道里的空气和塑料熔体产生的分解气体。
在注塑时,这些气体都应顺利的排出。
排气不足的危害性:
( 1 ) 在胶件表面形成烘印、气花、接缝,使表面轮廓不清;
( 2 ) 充填困难,或局部飞边;
( 3 ) 严重时在表面产生焦痕;
( 4 ) 降低充模速度,延长成型周期。
我们常用的排气方法有以下几种:
一、模胚的排气
导柱导套上为了合模的顺利,需开设排气槽
三板模的尼龙胶塞,为了顺利合模及开模的,A 板开排气孔
二、流道末端的排气
三、成型零件的排气
1.分型面开排气槽排气:为了加工与清理的方便,一般的情况下是做在前模仁
如上图,宽度b=(4~8)mm 长度 L为3mm ~5mm左右,排气槽的深度h因树脂不同而异,主要是考虑树脂的粘度及其是否容易分解。
作为原则而言,粘度低的树脂,排气槽的深度要浅。
容易分解的树脂,排气槽的面积要大,各种树脂的排气槽深度可参考下表
2.镶件的排气
填充困难或最后填充的位置,在镶件上注意做排气,排气须引至模外
3.顶针排气
胶件中间位置的困气,可加设顶针,利用顶针和型芯之间的配合间隙,或有意增加顶针之间的间隙来排气
4.疏气钢
它的排气效果是与厚度成反比的,所以,他的一般厚度为30-50MM,精加工时不可以选择机加工,只能放电。
这点特别注意,由于成本等原因,实际上很少用到
另外还有排气栓排气(原理同疏气钢),其为标准件,可直接购买。
浇注系统和排气系统的设计
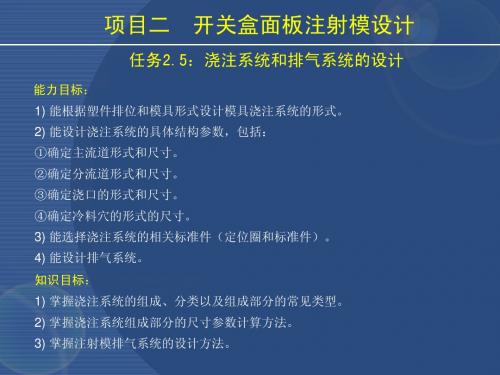
项目二 开关盒面板注射模设计
任务2.5:浇注系统和排气系统的设计
(1) 浇注系统的组成 普通流道浇注系统由主流道、分流 道(可分为一级分流道,二级分流道 等)、冷料井和浇口组成,如图 2-93 所 示。
图2-93 浇注系统的组成
(2) 浇注系统的总体设计原则
1) 在型腔排位方面,浇注系统设计时应注意以下三点:①尽可能采用平衡式布置, 以便熔融塑料能平衡地充填各型腔。②型腔的布置和浇口的开设部位尽可能使模具在注 塑过程中受力均匀。③型腔的排列尽可能紧凑,减小模具外形尺寸。
项目二 开关盒面板注射模设计
任务2.5:浇注系统和排气系统的设计
2) 热量损失和压力损失要小 3) 浇注系统应能捕集温度较低的冷料,防止其进入型腔,影响塑件质量。 4) 浇注系统应能顺利引导熔融塑料充满型腔各个角落,能使型腔内的气体顺利排出。 5) 防止制品塑件出现缺陷。。 6) 浇口的设置力求获得最好的制品塑件表面质量。
3) 同一系列规格的圆形、梯形、U形流道,塑料的流动及冷却性能相同,设计时以圆
形流道作为计算值。
项目二 开关盒面板注射模设计
任务2.5:浇注系统和排气系统的设计
(3) 圆形分流道尺寸的设计方法
1) 上一级分流道截面面积为下一级分流道截面面积的2倍。在设计时,各级分流道
示意图如图2-96所示,它们的尺寸关系可按表2-17所列圆整选取。
图2-95 两板模流道示意图
3.分流道的设计 多型腔或单型腔多浇口(塑件尺寸大)的模具应设置分流道。分流道即为连接主流道 和浇口的进料通道,起分流和转向作用。在设计分流道时,要求塑料熔体在流动时热量和 压力损失小,流道凝料少,各型腔能均衡进料。为便于分流道的加工和凝料脱模,分流道
大都设置在分型面上。
模具排气之设计

1.在分模度為 按鍵孔的靠破面設計排氣槽及排氣孔,排氣槽的寬度為2~3 ㎜。
排 氣 槽 深 度 為 : 0 .2 ~ 0 .5 m m . 排 氣 槽 深 度 如 附 表 所 示 .
排氣二
32~3㎜ m m ~4
排氣三
2~3㎜
說明結束 謝謝
3.抽真空排氣槽尺寸的基本要求
2~3㎜ DEEP 0.5~0.6㎜ ∮6㎜
3.5~4.0㎜ DEEP 如附表所示
(例如 注:當有其它原因無法製作O RING時,則不作O RING. (例如 SLIDE) 當有其它原因無法製作O RING時 則不作O
4.抽真空O型環結構之設計標準
V=
此種O型環的設計方式可以避免O 此種O型環的設計方式可以避免O型環掉落
=H
5.薄片Insert排氣方式
成品面 排氣槽只製作單面,深度 為塑膠原料對應排氣槽 的深度,離成品面應為 整面排氣
除客戶特別 指定, 指定,一般 不採用透氣 性鋼材
Depth:0.2 mm
在局部充填困難(成品肉厚較小處),可採用薄片 在局部充填困難(成品肉厚較小處),可採用薄片 ), Insert的方式,在薄片 的方式, 的方式 在薄片Insert上建立排氣槽 上建立排氣槽
在充填的末端及包風處 設計排氣, 設計排氣,排氣的基本 方式有: 方式有: 分割入子、設計頂針、 分割入子、設計頂針、 設計排氣槽等。 設計排氣槽等。
2.各種塑膠原料不發生毛邊的排氣孔深度明細
(排氣深度應先以最小值製作)
塑膠原料 PE PP PS SB ABS PC PBT 排氣孔深度(MM) 0.02 0.01~0.02 0.02 0.03 0.03 0.01~0.03 0.005~0.015 塑膠原料 SAN PPO POM PMMA PA PPS PC+ABS 排氣孔深度(MM) 0.03 0.03 0.01~0.03 0.03 0.005~0.015 0.01~0.03 0.015~0.02
模具排气系统设计

12
13
(2) 设排气槽
❖ 因为合模间隙很小,在强大的合模力作用下, 模板产生一定的变形,合模间隙更小。所以, 对于型腔容积较大的模具,仅仅利用合模间隙 排气,排气速率一般达不到要求。这时需要专 门开设排气槽。
❖ 当充模料流末端不在分 型面上,又没有配合间 隙可用时,一般难以开 设排气槽。
❖ 此时可在与料流末端接 触的成型零件上镶嵌可 透气的烧结金属块,并 用排气孔与外界或真空 系统连通,构成排气系 统。
19
小
结
排气系统设计主要考虑: ❖ 位置:一般设在料流的末端。 ❖ 尺寸:排气而不漏料。 ❖ 实施方式:
❖ 为有效排除模腔内的气体,排气系统的入口位置 (即排气系统在型腔内的开口)必须设在充模料 流的汇集处(料流末端)。
❖ 排气系统的出口位置可根据模具结构灵活安排, 但应注意采用排气槽等大截面排气系统时出口不 要正对操作者,以避免因工艺波动导致高温高压 熔体喷出时,可能造成的工伤事故。
8
2.排气系统尺寸
(1)利用分型面间隙排气。 (2)设排气槽。 (3)利用成型零件配合间隙排气。 (4)专设排气系统。
20
度w,根据缝隙深度h及在充模时间内排出模
腔内气体所需的排气通道截面积A确定
(w≥A/h)。
9
❖ 排气通道截面积A产下式计算 : A=0.05V/n
式中:A——排气通道截面积,mm2; V——型腔及浇注系统总容积,cm3; n——排气槽的数量
[说明:溢边值即物料能流入的最小缝隙,成型用 物料的溢边值取决于由物料特性和工艺条件决定 的物料流动性,流动性越好,溢边值越小。常用 塑料、常规成型条件下的溢边值如下表所示。]
电动机壳压铸成型模具设计中的模具排气系统优化

电动机壳压铸成型模具设计中的模具排气系统优化在电动机壳压铸成型模具设计中,模具排气系统的优化是至关重要的。
一个良好设计的模具排气系统能够有效地排除模具中的气体和气泡,保证铸件成品质量。
本文将重点探讨电动机壳压铸成型模具设计中的模具排气系统优化。
一、模具排气系统的作用模具排气系统是用来排除模具中气体和气泡的系统。
在电动机壳压铸成型过程中,熔化的金属液体会释放出大量的气体,如果这些气体不能及时排出模具,就会在铸件中形成气孔和气泡,严重影响铸件的质量。
因此,一个有效的模具排气系统对于确保铸件成品质量至关重要。
二、模具排气系统的设计原则1. 合理布局:模具排气系统的位置应当考虑到熔化金属液体流动的方向,尽可能置于熔池的高点,保证气体能够顺利排出模具。
2. 设计通道:模具排气通道应当尽可能短、宽,保证通畅。
同时,排气通道的截面积也要适当,不宜过小,以免造成排气不畅。
3. 避免死角:排气系统设计要避免死角,尽量减少气体困留的可能,确保气体能够顺利排出模具。
4. 多点排气:在模具设计中,应当考虑设置多个排气口,以增加排气效率,避免因为某个排气口被堵塞而导致排气不畅的问题。
三、模具排气系统的优化方案1. 采用液压顶出装置:在模具设计中,可以考虑在合适的位置装配液压顶出装置,通过液压力将气体推出模具,提高排气效率。
2. 添加排气针:在模具设计中,可以考虑在模具的关键位置设计排气针,利用针状结构的小孔将气体排出模具,从而加快排气速度。
3. 优化排气道设计:对于排气道的设计,可以通过优化通道的宽度、长度以及截面积等参数来提高排气效率,确保气体顺利排出。
四、总结在电动机壳压铸成型模具设计中,模具排气系统的优化是确保铸件质量的重要一环。
通过合理设计模具排气系统,能够有效避免气孔和气泡的生成,提高铸件的完整性和质量。
因此,在模具设计中,应当重视模具排气系统的设计,不断优化完善,以确保模具的稳定工作和生产出优质的铸件产品。
模具排气系统与形式

•模具排氣作用:1.減小塑膠在 型腔充填阻力.
•
2.提高產品成型質量與周期
•為何排氣之原因?
•排氣不良 •熔體射速降低 •熔膠溫度降低 •射壓提高 •應力集中 •翹曲變形
•料溫提高
•熱應力或材料裂 解
•
•模具排氣的形式
•流道排氣
•深度(depth) :
• 1. 0.075 mm易流塑料(easy-flow mat.)
模具排气系统与形式
2020年4月28日星期二
•側進膠
•
•搭接式進膠
•
•潛伏式進膠
•
•香蕉形進膠
•
•扇形進膠
•
•針點進膠
•
• 模具冷卻系統
•冷卻水路也叫溫度調節系統 。 •模具溫度調節的重要性﹕模具溫度對塑料制品的質 量和成型周期影響很大。 •(1)﹑模具溫度的波動對制品的收縮率﹑尺寸穩定性 ﹑變形﹑應力開裂﹑表面質量等都有很大的影響。 •(2)﹑模具溫度對成型周期的影響﹕冷卻時間約占成 型周期的80%。
•
•水路設計原則
•1)﹑在滿足冷卻所需的傳熱面積和模具結構允許的前 提下﹐冷卻回路數量應儘量多﹐冷卻水路孔徑要儘量 大。
•圖
•圖
•圖a的a冷卻速度比圖b要快
b
。 •水孔直徑一般取Φ6~Φ12MM。
•
•2)﹑冷卻水路的布置要合理。當制品肉厚基本均勻時﹐冷 卻水路離成品表面距離最好相等﹐分布與輪廓吻合﹐如圖 a﹔當成品肉厚不均一時﹐則在肉厚的地方加強冷卻﹐如圖b 。
•排氣通道通大氣(vent channel to atmosphere):
• 1mm深(deep)
•
•分模面排氣
•Parting Line Vents
模具抽真空排气设计方案

优点:结构简单,实施方便,效 果显著。
总结词:简单、高效、适用于小 型模具
优缺点
缺点:对于大型模具,需要更多 的时间和能量来抽真空,且可能 需要更高的维护成本。
方案二:间接抽真空法
01
02
背景
在塑料模具、压铸模具等高分子材料成型模具中,残留气体 和挥发物常常会引发许多问题,如气孔、翘曲、变形等,严 重影响产品的质量和生产效率。因此,模具抽真空排气设计 成为了解决这些问题的必要手段。
模具抽真空排气设计的意义
提高产品质量
通过排除模具内部的残留气体和 挥发物,可以减少气孔、翘曲、 变形等问题,从而提高产品的质
THANK YOU
问题三
管道和阀门连接不牢固,导致漏气或真空度不足 。
解决方案三
在连接管道和阀门时,应确保连接处紧固、密封性好, 检查管道和阀门的完好性。
控制:抽真空排气效果的监测和控制方法
01
02
03
方法一
使用压力表监测模具内的 压力变化,判断抽真空排 气效果。
方法二
观察模具表面情况,检查 是否有气孔、气泡等缺陷 ,判断排气效果。
不足
本次研究虽然取得了一定的成果,但在实验过程中发现,该方案对于一些特殊材料的排气效果还有待进一步提高 。
结论二:对未来研究方向的展望
深入研究不同材料对模具抽真空 排气效果的影响,找出更加普遍
适用的解决方案。
进一步优化模具抽真空排气的设 计方案,提高其使用效率和稳定
性。
结合其他先进的制造技术,研究 更加智能化的模具抽真空排气方 案,提高生产效率和产品质量。
注塑模具设计第11讲 实例1-2D-10 排气系统设计、其他标准件设计

2
十二、其他标准件的设计
1. 顶棍孔的设计
注塑模具设计实例教程
顶棍孔俗称 KO 孔,是注塑机顶棍穿过模具动模座板的通孔。顶棍孔通常处于 模具中心,如果模具浇口套偏心,则顶棍孔也要跟着一起偏移。 本例模架规格为 2530 ,故顶棍孔选用规格为 Φ 35 ,数量一个,开设在模具动 模座板的中心,如图1-1-70所示。 在动模视图中心处绘制一个 Φ 35 的虚线圆,并标上“KO”字样,用于表示顶 棍孔 >>注射机顶棍与顶棍孔动画:D032-注射机顶棍与顶棍孔.pdf 2. 推板导柱的设计 推板导柱俗称中托司。 注塑机顶杆推动顶出机构顶出产品时,安装推板导柱能使顶出机构 运动平稳且受力均匀,保证了产品的顺利顶出。 推板导柱的数量按模具的尺寸大小来定,通常为两支或四支。 3
?注塑成型时往往会作用有很大的侧向压力如果这种侧向压力传递到导柱则易使其弯曲变形甚至卡死损毁因此需要加边锁二次准确定位使其能够承受成型时的侧向压力配合导柱完成合模导向
实例一 电动工具盖注塑模具2D设计
复习:顶出系统的设计原则和要求
注塑模具设计实例教程
检查上次布置作业的完成情况
新课:
十一、排气系统的设计 模具内的气体不仅包括型腔里的空气,还包括流道里的空气和塑料熔 体产生的分解气体。在注塑时,这些气体都应顺利地排出。如果模具 内的气体不能顺利排出,将会造成充填困难,或局部飞边,严重时会 在产品表面产生焦痕。 常用的排气方法有以下几种: 利用分型面排气,利用推杆排气,利用镶拼间隙排气等。 当以上方法不能顺利地将模具内的气体排出时,则要开排气槽 排气。排气槽一般开设在型腔。
◎动手操作,用AutoCAD软件完成本例其他标准件的设计。 ◎参考视频:实例1-2D-10.其他标准件的设计.avi (该视频请从教材附带的光 盘中查找) 小结: 排气系统的设计、其他标准件的设计 作业: 完成练习一以下部分内容: 其他标准件的设计 11
模具排气设计

圖18.6及18.7是疏氣鋼鑲件設計的參考方法:
序號
修訂內容
批準/日期
審核/日期
制訂/修訂
2.6盡可能用銑床加工,然后省去刀紋.因為用磨床加工,往往平位太長,使空氣不能直接排出
2.7排氣坑兩旁可做45斜邊及拋光(用#320沙紙)。
3.
4.水口的排氣
4.1水口的排氣深度
5.頂針及司筒排氣設計
5.1 “X”闊度為膠料排氣坑深度的1/2陪,排氣坑深度可參考表12.1
5.2哥針亦可用同樣排氣設計。
8.7.檢查疏氣的方法,可塗_少量液體如脫模劑在疏氣鋼工件表面上,再由出氣位吹入高
壓風,檢查泡沫湧起的情況便可知道疏氣性能的情度。
8.8.清潔阻塞疏氣孔的方法:
(i)加熱工件至500F,維時最少一小時。
(ii)冷卻至室溫後,浸入丙酮(acetone),維時最少十五分鐘。
(iii)取出工件,用高壓風從工件底部吹出阻塞物。
模具排氣設計
1.
作為一通道給型腔內的空氣及塑料被注射時所產生的氣體,在注塑時可流出型腔。
2.
2.1尺寸依膠料,不同膠料排氣尺寸不同.
2.2所有流道及冷膠位要加排氣.
2.3所有成品要加排氣,位置在入水對面.死角位.最后走到的.
2.4 CORE針及司筒有需要加排氣.
2.5排氣針要銑坑駁通模胚பைடு நூலகம்排氣,或駁通頂針孔.
8.2.疏氣鋼須疏氣的部份在幼加工時(膠位及底部)除電蝕外,不可作任何機械加工(磨床或
鑼床);粗加工時可作任何機械加工。
8.3.鑲件底要做疏氣坑。
8.4.疏氣鋼可直接修螺絲。
8.5.疏氣鋼如要開運水,運水孔要作鍍Dichtol處理。
模具设计之排气、冷却系统设计

等溫線
B.串並聯水路的優缺點
串聯水路
並聯水路
優點
優點
– 統一的流動率
– 用在入子的周圍最好
– 統一的熱交換
– 高體積低壓力
缺點
缺點
4. 規格及其與成品肉--較厚高的的關壓系 降
– 沒有統一的流動率
– 冷卻水道的直徑優先採用大於 8mm,各個水孔的直徑應盡量易一於致堵,避塞免冷卻液的流速不均
合
传导率低不能使其过
金
热,否则易产生分解物
排 气
质而堵塞气孔。
3、各种不同树脂的排气槽深度。
―――主要依据是树脂的粘度及其是否容易分解。
原则:(1)粘度底的树脂排气槽的深度要浅。
(2)容易分解的树脂,排气槽的截面积要大。
树脂名称
排气槽深度 mm
树脂名称
排气槽深度 mm
PE
0.02
PA(含玻璃纤维) 0.01~0.03
模具设计之排气、冷却系统设计
一、排气系统设计
年 月 日发 布
排气系统设计
页数
1、 模具排气系统不顺畅,则可能出现以下几种成型缺陷。 (1) 充填不足 (2) 出现熔接痕 (3) 烧伤
2、 各种形式排气机构的设置。
排气机构基本类型
分 型 面 排 气
设计要点及使用场合
1、在型腔周围设置排气槽 2、使用中,在浇口对侧部
材料
Aluminum P20 CarbSt BeCu 420 ss H-13 C17200 (BeCu) C17510 (BeCu0) C18000 (NiSiCrCu)
熱傳導系數 W/m/deg K 221.9 29 41.9 130 24.9 28.2 105 245 207.6
模具抽真空排气设计方案

管路连接
采用可靠的连接方式,确保管路连接紧密,防止 气体泄漏。
排气效果评估方法
观察法
通过观察制品表面质量、气泡分布等情况,评估排气效果。
称重法
通过对比制品排气前后的重量差异,评估排气效果。
仪器检测法
使用真空度计、压力传感器等仪器,检测模具内真空度或气体压 力,评估排气效果。源自05安全防护与环保措施
以避免产生气泡、烧焦等问题。
排气效率
02 要求模具抽真空排气系统具有较高的排气效率,以缩
短生产周期,提高生产效率。
操作便捷性
03
模具抽真空排气系统应设计简洁、操作方便,以降低
操作难度和减轻工人负担。
设计方案目标与期望
实现自动化控制
01
通过引入自动化控制技术,实现模具抽真空排气过程的自动化
,提高生产效率和生产质量。
防止模具因内外气压差导致变形或损坏。
快速抽真空
缩短成型周期,提高生产效率。
关键部件选型及依据
真空泵
选择高效、稳定的真空泵,确保快速抽真空 及排气效果。
真空管道
选用耐腐蚀、低阻力的真空管道,确保气体 顺畅排出。
真空阀门
选择密封性好、操作灵活的真空阀门,实现 模腔内外气压的快速平衡。
传感器与控制系统
通过传感器实时监测模腔内真空度,配合控 制系统实现自动化控制。
导柱导套
确保模具合模时的精确定位, 提高模具寿命。
模具底座
承载模具各部件,确保整体稳 定性。
顶针
用于推出成型后的产品,保证 产品顺利脱模。
冷却系统
通过循环冷却液降低模腔温度 ,确保产品质量和成型效率。
抽真空排气功能需求
排除模腔内空气
在注射成型过程中,确保模腔内无气泡,提高产品质量。
电动机壳压铸成型模具设计中的模具排气系统优化方法

电动机壳压铸成型模具设计中的模具排气系
统优化方法
在电动机壳压铸成型模具设计中,模具排气系统的优化方法至关重要。
优化排气系统可以有效提高生产效率、降低成本、改善产品质量。
本文将介绍电动机壳压铸成型模具设计中的模具排气系统优化方法。
在电动机壳压铸成型过程中,排气系统的设计对产品质量具有直接
影响。
排气不畅导致气泡、气孔等缺陷的产生,影响了产品的外观和
性能。
因此,设计一个科学合理的排气系统至关重要。
首先,要合理设计模具的结构。
模具结构应简洁、易于加工和维护。
模具的各部件之间应该能够紧密配合,排气道应设计在模具的适当位置,以保证熔金的自由流动和气体的顺利排出。
其次,要合理设置排气道。
排气道应该设置在熔金的流动方向上,
以便气体顺利排出。
排气道的数量、形状、大小应该根据具体产品的
特点和生产工艺进行设计,以确保排气畅通。
另外,对于一些形状复杂、壁厚不均匀的产品,可以采用增加排气
道或设置排气阀来改善排气效果。
排气阀可以根据模具开合程度的变
化进行设计,以实现不同阶段的排气效果。
在模具的制造过程中,要注意对模具进行充分的清洁和维护,确保
排气系统的畅通性。
模具在使用中要定期检查排气道的状况,及时清
理堵塞的部分,以保证排气系统的正常运行。
综上所述,优化电动机壳压铸成型模具设计中的模具排气系统,是提高产品质量、降低生产成本的重要举措。
通过合理设计结构、设置排气道和定期维护保养,可以有效改善排气效果,避免产品缺陷的产生,提高生产效率,为企业的发展带来更大的价值。
模具设计—排气系统
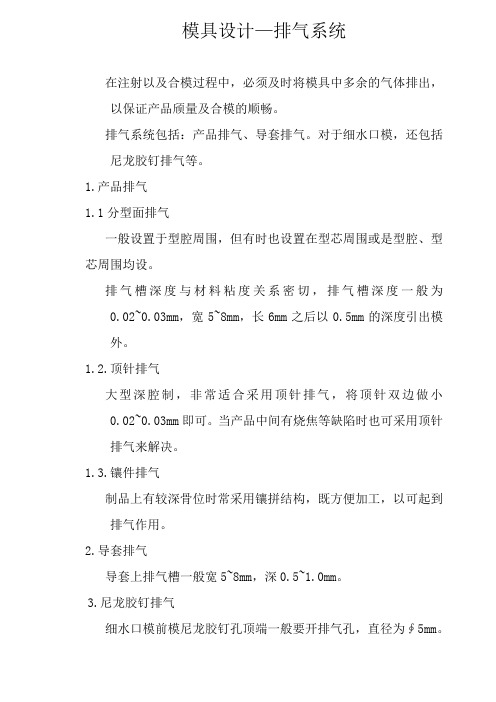
模具设计—排气系统
在注射以及合模过程中,必须及时将模具中多余的气体排出,以保证产品颀量及合模的顺畅。
排气系统包括:产品排气、导套排气。
对于细水口模,还包括尼龙胶钉排气等。
1.产品排气
1.1分型面排气
一般设置于型腔周围,但有时也设置在型芯周围或是型腔、型芯周围均设。
排气槽深度与材料粘度关系密切,排气槽深度一般为
0.02~0.03mm,宽5~8mm,长6mm之后以0.5mm的深度引出模
外。
1.2.顶针排气
大型深腔制,非常适合采用顶针排气,将顶针双边做小
0.02~0.03mm即可。
当产品中间有烧焦等缺陷时也可采用顶针
排气来解决。
1.3.镶件排气
制品上有较深骨位时常采用镶拼结构,既方便加工,以可起到排气作用。
2.导套排气
导套上排气槽一般宽5~8mm,深0.5~1.0mm。
3.尼龙胶钉排气
细水口模前模尼龙胶钉孔顶端一般要开排气孔,直径为∮5mm。
浅谈模具设计中的排气问题!

浅谈模具设计中的排气问题!有读者留言,问,排气该如何画?我怎么知道哪里要画排气啊?跟他了解了一下,小厂,画了一年多的模具从来没画过排气,突然,要求要做排气了,有点找不着北的感觉。
有些读者可能不知道为啥要排气?哪来的气体?分型面合得再死,不是都有间隙吗?有间隙不是都可以排气了吗?实话,我最开始做设计的时候,我就这么想了,除了太深的筋位,你说有气困在里面出不来,这个是可能,分型面,整面都是碰的,有气还不是可以从上面跑出来。
而且,塑胶一进去,气不就被赶出来了吗?这个问题我纠结了好久。
先来排除一个误区,我最开始做设计时,所以为的气,不过就是模具合起来后,中间原来就有的空气,得把它排出来,而实际上不完整。
气的产生,除了模具上本身存在的空气外,还有塑料在加热过程中,分解产生的各种气体,综合到一起,都需要排出去。
所以,排气,主要是指这两个方面,一是模具本身里面的空气;二是加热过程中分解的各种气体。
至于排气不良,会有啥后果,咱们这里不谈,还有导柱排气,胶塞排气等,这些,这里也不聊,只聊聊胶位相关的排气。
做排气,我们得先知道什么地方困气,才知道怎么去做排气。
一般来说,离胶位最远的那一端,或胶位流向有封闭的地方,都是需要排气的地方。
说到这里,又犯糊涂了,我怎么去判断呢?对于经验相对浅的人,可能对困气的位置评估不太足,哪怕经验非常丰富的人,也不见得百分分估得准,所以,前面的那段话,只是个理论。
因此,我们在设计的时候,往往也不能确切的知道哪里困气,所以,排气槽大多数情况下,你看到的模具图,一般都是围着产品四周做。
如下图这样做的目的是,能确切评估困气的地方,直接开好排气,不能评估的地方,模具试出来后,在仍有困气的地方,直接开槽就行了,也避免了二次上机的麻烦。
这种排气槽,直接在CNC光刀的时候,一起出来了,所以,在设计时,得考虑CNC加工的刀具。
如果分型面是平面,可以做平底槽,平底刀可以直接跑出来。
如果是曲面的,就只能做成R底槽,得用球刀。
塑胶模具排气系统设计Venting System Design

塑胶模具排气系统设计Venting System Design【塑胶模具排气系统设计Venting System Design】【1·简介】本文档旨在提供塑胶模具排气系统设计的详细指导。
通过合理设计和布局模具排气系统,能够提高模具的生产效率和产品质量。
【2·排气系统概述】2·1 排气系统的定义排气系统是指将注塑过程中产生的气体从模腔中迅速排出的系统,以避免产生气泡、热裂缝等缺陷。
2·2 排气系统的作用排气系统的主要作用有:●排除注射过程中产生的气体,避免气泡形成。
●提高产品表面质量。
●减少翘曲、热裂缝等模具缺陷的发生。
【3·排气系统设计】3·1 模具结构设计3·1·1 模腔设计●设计合理的模腔凸起或凹陷,以利于气体排出。
●避免过大的滞留截面,限制气体通过速度。
3·1·2 模具壁设计●壁厚均匀,避免过薄或过厚局部,以免产生热裂缝。
●考虑模具材料的热导率,避免热负荷过大。
3·2 排气通道设计3·2·1 通道数量和布局●确定合适的通道数量,避免过少或过多造成排气不畅。
●合理布局通道位置,覆盖整个模腔。
3·2·2 通道形状和尺寸●通道的形状可以选择圆形、方形等。
●尺寸要与产品和模具尺寸相匹配,确保气体排放顺畅。
【4·排气系统实施】4·1 制造排气通道●根据设计要求,在模具上开设排气通道。
●通过机械加工或电火花加工等方法,制作通道。
4·2 检查和调整排气系统●在注塑过程中,检查排气通道是否通畅。
●根据需要,调整通道尺寸或布局。
【5·附件】本文档涉及的附件包括模具设计图纸、排气通道制造工艺流程等。
【6·法律名词及注释】6·1 模具:用于成型产品的工具或装置。
6·2 注塑:将熔化塑料注入模具腔体中,通过冷却和固化得到成型产品的过程。
- 1、下载文档前请自行甄别文档内容的完整性,平台不提供额外的编辑、内容补充、找答案等附加服务。
- 2、"仅部分预览"的文档,不可在线预览部分如存在完整性等问题,可反馈申请退款(可完整预览的文档不适用该条件!)。
- 3、如文档侵犯您的权益,请联系客服反馈,我们会尽快为您处理(人工客服工作时间:9:00-18:30)。
大型热芯盒模具排气系统设计王明杰 范新凤 范有发(福建工程学院,福建福州350014)摘要:分析了热芯盒模具充型特点,指出在型砂的充型过程中如何快速排出型腔内的气体,以及充型过程中带入的空气是影响壳型质量的一个重要因素。
介绍了热芯盒模具分型面排气槽、排气塞以及推杆间隙排气等排气系统设计方法。
排气槽排气主要用于充型开始时的排气;排气塞用于型腔内部容易产生困气的部位和需要大量排气的部位;推杆间隙排气用于排气量不大或者开设排气塞会与推出机构产生干涉的部位。
这些排气方法互相配合,取长补短,根据壳型要求灵活布置,能起到良好的排气效果,并通过实例应用介绍了这些排气方法的设计原则和工艺参数。
关键词:热芯盒模具;排气系统;设计Design of Large Hot box Process Mold Vent SystemWang M ingjie,Fan Xinfeng,Fan Youfa(Fujian University of Technology,Fuzhou350014,China)Abstract:In the process of resin sand injection,the important factor influences the quality of shell mold is how to vent the air in mold rapidly.Desig n of vent system includes vent groove,vent plug and clearance of ejector pin.Vent groove is used in the process of beginning injection.Vent plug is used in the mold need to vent large quantity air.Clearance of ejector pin is used to vent little quantity air or the part may intervene with vent plug and ejector pin.With an example to introduce how to design vent system of hot process mold.Key words:hot box process mold;vent system;desig n传统使用湿型砂进行铸钢件的生产,需要设计复杂的砂处理系统完成形砂混制、型砂回收和型砂存储等功能,这样会占用大量的土地和厂房。
型砂的质量由于受到水分、灰分、粘结剂等因素影响,不容易稳定控制。
混好的型砂储存性不好,长时间不用需要进行二次处理。
湿砂型强度也很低,在搬运和浇注过程中容易产生塌箱、掉砂等缺陷。
在浇注和凝固过程中也会产生毛刺、夹砂结疤、型壁移动等表面缺陷,影响铸件质量[1]。
现在许多铸造厂改用壳型铸造进行铸钢件的生产,主要因为与普通湿型砂铸造相比,壳型铸造具有许多优点。
砂处理设备占地面积小可合理利用土地收稿日期:2005-05-19基金项目:福建工程学院科研发展基金项目(GY-Z0324)第一作者简介:王明杰,男,1972年生,讲师。
资源,这在目前土地资源越来越紧缺、土地征用成本越来越高的情况下,尤其具有很大的现实意义。
树脂砂(以下简称型砂)的混砂工艺成熟,质量稳定,还可进行长时间的存储。
壳型的强度高,便于生产和搬运。
型砂使用量小,对环保也有一定积极意义。
1 热芯盒模具排气系统设计方法热芯盒模具生产壳型的过程中,型砂在压缩空气的推动下充满型腔并紧实,然后在一定温度下硬化、成形。
热芯盒模具的排气系统不仅要排出型腔内的气体,防止出现 浇不满现象,还要排出型砂充型和紧实过程中带入的压缩空气,保证型砂颗粒之间紧密接触,使壳型成形后具有较高的强度。
型砂颗粒间空气排气不顺会使型砂颗粒间粘结强度低,产生壳型疏松、表面落砂等缺陷,导致壳型强度太低以及壳型表面质量太差。
壳型的强度不够,在浇注过程中易产生裂箱重大事故。
壳型表面质量太差也!53!设计∀研究 #电加工与模具∃2005年第5期会引起铸件表面质量很差。
因此热芯盒模具的排气量远大于普通的模具。
一般模具使用的分型面排气槽排气和排气!!!溢流系统排气都不能作为热芯盒模具的主要排气方式。
为保证顺利地快速排气,热芯盒模具排气系统采用排气塞排气为主、分型面排气槽排气和退出系统间隙排气为辅的排气方式。
1.1 排气塞排气由于热芯盒模具的排气量很大,分型面排气槽或推出系统间隙排气远远不能满足排气的需要,主要利用排气塞排气,其结构见图1。
排气塞上均匀开出排气缝隙,这些缝隙的宽度与使用型砂的颗粒度有关,一般要小于型砂颗粒的直径,防止型砂进入缝隙内部,堵死缝隙。
排气塞用45钢制作,并进行热处理,提高硬度,防止在安装排气塞和模具的使用过程中排气塞变形而堵住排气缝隙。
钢在高温下也易氧化,会缩短排气塞的寿命,热处理过的排气塞必须进行防锈处理。
树脂分解产物会在排气塞上沉积以及型砂碎裂后产生的粉尘会进入排气缝隙中,堵塞缝隙,影响排气效率。
排气塞后要开设排气道通向大气中。
排气塞在模具上的安装方式见图2。
图1排气塞结构图图2 排气塞安装图排气塞设置原则及注意事项:(1)排气塞尽量设置在模具的平面位置上,尽量避免设置在曲面位置上。
(2)在动模或定模上都要设置排气塞。
(3)设置排气塞时要开设排气道,要防止排气道与模具加热管、推杆及紧固件等产生干涉。
为了提高排气速度,尽量采用直的排气道,避免采用拐弯的排气道。
采用直排气道的另一个作用是当排气塞损坏时,容易进行更换。
(4)在砂流交汇处、砂流拐弯处及壳型内壁处都要设置排气塞。
(5)排气塞一般安装完毕后,应该比型腔面略高(至少要水平,一般不能低于型腔面)。
1.2 分型面排气槽排气分型面的排气槽加工方便,对于形状简单的壳型,也可作为一种主要的排气方式。
排气槽的位置要开设在模具射砂口的对面,排气槽的厚度要小于型砂直径。
即使超过一点也没有大问题,只是在生产过程中每次取件时要打扫排气槽,防止型砂粘死在排气槽中,影响排气。
排气槽的宽度一般比型腔宽度单边小20~40mm 左右即可。
一般做成直通的形式,不必像压铸模的排气槽那样做成 S 形。
一般不在模具的两端开排气槽,防止型砂飞出伤人。
模具使用一段时间后应当清理排气槽,模具生锈以及树脂分解后会在排气槽部位沉积,这些会减少排气槽的厚度,降低排气效率。
1.3 推出系统间隙排气对于一些由于设置推出系统而无法开设排气槽的部位,可利用推出系统间隙排气。
由于型砂颗粒直径较大,因此推杆和推杆孔的间隙可较大,做成间隙配合,这样利用推杆和推杆孔间隙就可顺利地排气。
与排气槽类似,使用一段时间后,树脂分解后会在推杆上沉积,减少间隙尺寸,降低排气效率,使用一段时间后最好进行清理。
2 在铸钢件壳型热芯盒模具中的应用集装箱角铸件采用16Mn 铸钢生产,要求一模四件。
模具动模模板部分见图3。
型砂充型顺序分析:型砂从射砂口进入型腔后,由于两侧型砂阻力较小,中间部分型砂受到镶块的阻碍,阻力较大。
模具两侧填充的型砂首先到达模具的底部,然后逐渐向中间堆积,与中间的型砂接触后,由模具底部向射砂口方向堆积。
总的填充形式是由两边往中间填充,由远离射砂口的地方向射砂口的方向填充,直到最后充满型腔[2]。
(下转第61页)!54!#电加工与模具∃2005年第5期设计∀研究统一的管理,对工艺数据进行存放、查询、增/删等操作,并充分利用Windows 系统的功能,通过系统提供的专门接口,可以实现在线式的修改、查询等功能,大大方便了系统对工艺数据的访问和管理。
相关网页见图9、图10。
图9 电火花加工工艺数据库管理系统相关界面1图10 电火花加工工艺数据库管理系统相关界面23 结束语将Web 、数据库、智能技术相结合用于电火花加工工艺规划中,可多快好省地完善工艺,使智能系统的 思维 机制更接近高水平操作者或专家,使加工过程更遂人愿,将智能软件进一步提高和完善已势在必行。
参考文献:[1] Dove R.Introducing pri nciples for agile sys tem.Automoti ve Production,1995(8):14~16[2] Goldman S L.Agile competitors and virtual organizations.M anufacturing Review,1995,8(1):59~67[3] 陈世欣,王勋.浅谈站点数据库访问技术.计算机应用研究.1999(5):3~6[4] Kaldos F,Erosicap.An expert system for the computer aidedpl anning of EDM sinking technology.EDM T echnology,1993(1):41~44[5] 康博创作室.Web 应用高级开发指南.北京:人民邮电出版社,1999[6] 希望图书创作室编译.PHP4.0程序员参考.北京:北京希望电子出版社,2000(上接第54页)1.分型面排气槽2.排气塞排气3.加热管%54.镶块5.推出系统间隙排气6.冒口7.直浇道8.射砂口位置图3 热芯盒模具动模模板部分排气系统分布分型面排气槽位于射砂口的对面位置,型砂在开始充型过程中,一部分气体就可以通过排气槽排出。
采用直通形式的排气槽加工方便,且排气槽的宽度很大,有助于排气。
当型砂到达底部堆积到一定程度时,就会将排气槽堵塞,使其丧失排气作用。
模具两侧的型砂填充速度比中间快,在镶块之间和冒口附近的气体被型砂和镶块阻挡不易排出,容易产生窝气,造成充不满,只能依靠排气槽和推出机构间隙排气的方式排气。
型砂堆积过冒口后,主要依靠靠近射砂口的几个排气槽和推出机构间隙进行排气,直到最后充满型腔。
镶块两侧排气要求不高的地方主要利用推出机构间隙进行排气。
3 结论与普通湿砂型铸造相比,壳型铸造具有占地面积少、壳型强度高等优点,正逐渐得到广泛应用。
型砂填充速度快,且有大量空气随型砂进入型腔,因此如何快速排气是大型热芯盒模具设计中的一个重要问题。
通过把排气塞排气、排气槽排气和推出机构间隙排气等排气方法有机结合起来,根据模具的具体要求,取长补短,互为补充,能满足模具快速排气的需要。
合理的排气系统能防止壳型出现充不满、表面疏松、强度低等缺陷,提高铸件的质量。
在生产过程中需及时清理排气系统,防止因堵塞而降低排气效率。
同时,也要控制合理的模具温度,防止型砂提前固化而失去流动能力,导致充不满的缺陷。
参考文献:[1] 曹文龙主编.铸造工艺学.北京:机械工业出版社,1993[2] 崔怡,李宏亮,吴浚郊.射砂过程数值模拟的应用.铸造,2003,52(6):415~419!61!工艺∀装备#电加工与模具∃2005年第5期。