安全库存经济批量eoq再订货点
库存控制的基本模型和库存控制的方法
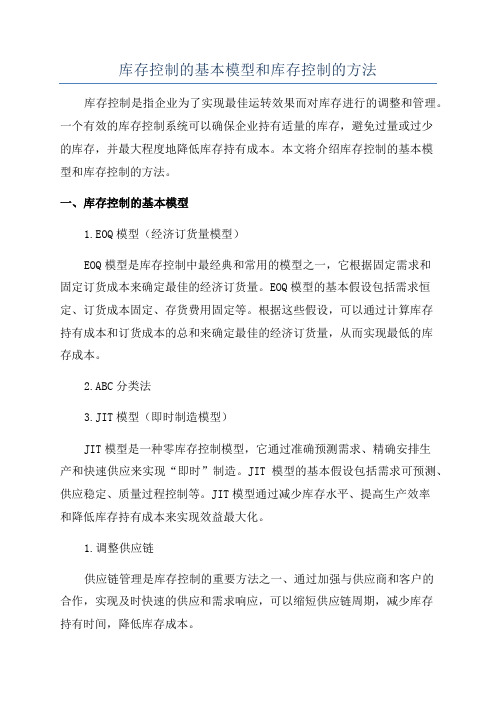
库存控制的基本模型和库存控制的方法库存控制是指企业为了实现最佳运转效果而对库存进行的调整和管理。
一个有效的库存控制系统可以确保企业持有适量的库存,避免过量或过少的库存,并最大程度地降低库存持有成本。
本文将介绍库存控制的基本模型和库存控制的方法。
一、库存控制的基本模型1.EOQ模型(经济订货量模型)EOQ模型是库存控制中最经典和常用的模型之一,它根据固定需求和固定订货成本来确定最佳的经济订货量。
EOQ模型的基本假设包括需求恒定、订货成本固定、存货费用固定等。
根据这些假设,可以通过计算库存持有成本和订货成本的总和来确定最佳的经济订货量,从而实现最低的库存成本。
2.ABC分类法3.JIT模型(即时制造模型)JIT模型是一种零库存控制模型,它通过准确预测需求、精确安排生产和快速供应来实现“即时”制造。
JIT模型的基本假设包括需求可预测、供应稳定、质量过程控制等。
JIT模型通过减少库存水平、提高生产效率和降低库存持有成本来实现效益最大化。
1.调整供应链供应链管理是库存控制的重要方法之一、通过加强与供应商和客户的合作,实现及时快速的供应和需求响应,可以缩短供应链周期,减少库存持有时间,降低库存成本。
2.优化订货策略根据不同的物料特性和需求变化,采取合适的订货策略可以有效控制库存。
例如,对于季节性需求的物料,可以采用季节性订货策略来控制库存水平;对于快速周转的物料,可以采用定期订货策略来实现库存的定期补充。
3.制定安全库存安全库存是为了应对不可预见的需求波动或供应延迟而保留的库存量。
制定合理的安全库存水平可以确保库存可靠供应,避免售罄和延迟交货等问题。
4.制定库存监控机制建立有效的库存监控机制可以及时发现和解决库存异常问题。
通过定期盘点、库存周转率和平均库存周期等指标的监控,可以及时调整库存控制策略,避免库存积压或库存缺货的问题。
5.采用信息技术支持采用信息化系统可以更加高效地管理和控制库存。
例如,采用ERP系统可以实现库存的自动跟踪和监控,及时生成库存报表和预警信息,提高库存控制的效率和准确性。
库存控制的定量分析方法--EOQ

平均库存(Q/2)* 单位存货存储成本 (P*H)
未考虑
当不考虑价格波动 时,P*D为常量 库存总成本TC:
单调递减
单调递增
TC = P * D + C *
D Q + P*H * Q 2
存货量 Q Q/2 R O a b c d e f
时间
......
Tn
T1
T2
T3
(1)图中,Q为订货批量,Q/2为平均库存量。 (2)R为订货点,ab=cd=ef为前置时间,ac=ce为订货间隔期。 Q (3)对于时间段任意 Tk 内,其存储成本为 * P * H Tk 2 那么对于整个1年内, H = H T + H T + ... + H T
(三)EOQ基本思想
参数设置: (1)年需求量 D (2)订货批量 Q (3)每次订货的成本 C (4)商品的订购单价 P (5)年存储费率 H (6)年订货次数 n=D/Q (7)年平均库存量 Q/2
库存总成本
采购成本
+
订货成本
+
储存成本
+
缺货成本
商品单价(P)* 全年订货总量(D)
全年订货总次数 (n=D/Q)* 订货单价C
2 DC 2*1000*5 EOQ1 = = = 47.67 ≈ 48 ( 件 ) PH 22*0.2
TC在Q < 48时单调递减,则 min ( TC ) 在Q = 40处取得
40 1000 TC1 =1000* 22 + 22* * 20% + 5* = 22213 ( 元 ) 2 40
1 2 n
存储总成本为
Q Q * P * H T1 + H T2 + ... + H Tn = * P * H 2 2
会设安全库存,再订货点的计算就很容易

会设安全库存,再订货点的计算就很容易在库存计划领域,除了安全库存,经常打交道的还有再订货点(或者就叫订货点)。
其逻辑是一旦库存降到预设的水位(再订货点,ROP),就启动订货机制,驱动供应链补充一定数量的货(订货量,ROQ);在货来到之前,库存继续下降,直到订的货到达,拉高库存的水位,然后开始下一个循环,如图1[1]。
再订货点法在企业里使用很广,它的几个参数,在此稍作解释。
图1:再订货法示意图先说再订货点。
再订货点由两部分构成:(1)补货周期内的平均需求——这是平均需求预测*补货周期(如果需求相对稳定的话,一般会用过去一段时间的平均需求来代替);(2)安全库存——这是为了应对需求和供应的不确定性,以及提高有货率,我们在前面已经详细探讨过。
这概念其实你在做单身汉的时候就烂熟于胸:你每周买一次菜(这意味着补货周期是7天),每天平均吃半斤小白菜,那你要把小白菜“库存”至少建到3.5斤,那是“补货周期内的平均需求”;有时候斜对门的另一个单身汉来蹭饭,那是“需求的不确定性”,你就得多备点,得了,再加1斤,就是你的“安全库存”。
这样,你的“再订货点”就是4.5斤。
再说订货量。
这是说每当补货时,需要补多少。
你知道,最少也要达到或超过再订货点(取决于不同的计算机系统:在有些系统,库存水位达到再订货点,就触动补货;而在另一些系统,需要低于再订货点)。
但同时,还要考虑补货相关的成本。
在订货量方面,你天生就是专家:(1)订货成本越高,订货量就越大——为了几根葱,就让你跑趟菜市场,你会很愤怒,因为你跑一趟的“订货成本”很高,你当然希望多买些东西,把单位订货成本降下来;(2)需求量越大,订货量就越大——这能解释为什么你一次买50斤米,但不会买50斤盐;(3)库存成本越高,订货量就越小——这就是为什么你不会买半年喝的水,因为占地方没处放;你也不会买一个月吃的小青菜,因为小青菜会坏掉,两种情况下的库存成本都很高。
在经济学上,有个经济订货量(EOQ)的概念,已经研究了一百年了,就是平衡上述订货成本、需求量和库存成本,生产的最小批量,采购的最小订货量也是来源于此[2]。
安全库存及重订货点

一、安全库存设置供给:现有库存+接收(采购订单,确认订货建议,生产订单等等)需求:计划独立需求,客户需求,相关需求,物料预留以及预测需求等等以三达现在的设法为例,MRP类型PD,批量为EX,按正常情况下,运行MRP对供给和需求进行平衡后,供给等于需求,如果设置了安全库存,则供给=需求+安全库存。
也就是说安全库存是在需求计划外多备的一部分库存,这部分库存可以在紧急情况下使用,如采购来不及、紧急需要等。
最小安全库存是指系统中一定要备有的数量,这部分数量不能用于发料,建议不要设置。
使用安全库存的优点就是可以满足紧急情况下使用,缺点是因为这部分库存在需求之外,增加了库存成本。
如果某个物料具有采购周期较长、经常采购来不及、使用较频繁、成本较低的特征可以考虑设置安全库存二、人工重订货点设置人工重订货点的MRP类型为VB,在MRP1视图重订货点输入需要重订货的基准数量。
PD与VB的差别在于PD是供给跟需求进行平衡,当供给小于需求时,系统会产生计划订单或采购申请对需求进行平衡,而VB是供给跟重订货点进行平衡,即VB不考虑实际的需求情况。
当供给低于重订货点时,系统根据设置的批量策略来进行补给,如批量设置成HB,最大库存水平为500,则当供给小于100时,运行完MRP系统产生供给(计划订单或采购申请)补充到500。
例:假设当前没有接收(采购订单、生产订单、采购申请等),需求数量为100,当前库存50,运行MRP后,系统产生450的计划订单,即系统不会考虑需求数量为100,而是考虑供给小于100应该触发重新订货,然后重新订货根据批量设置了HB,最大库存水平设置了500,从而将供给补充到500。
人工重订货点主要是根据历史消耗的情况来设置,这种方式不基于当前系统的实际需求数量来计划。
采用重订货点方式需考虑重订货点数量设置多少,以及补给策略,如最大库存水平大小。
仓库库存管理的优化策略与模型建立

仓库库存管理的优化策略与模型建立在现代企业管理中,仓库库存管理是非常重要且复杂的任务之一。
合理优化仓库库存管理可以帮助企业降低成本、提高效率,并确保产品供应的稳定性和客户满意度。
本文将探讨仓库库存管理的优化策略以及如何建立相应的模型来实现最佳管理结果。
一、仓库库存管理的重要性仓库库存管理对企业运营至关重要。
首先,合理的库存管理可以降低企业的资金占用成本。
过高的库存会导致企业的资金长期固定在库存中,影响企业的流动性和盈利能力。
其次,精确的库存管理可以避免库存积压和过期等问题。
合理的库存数量可以确保物流顺畅,减少仓储空间的浪费,同时避免商品过期浪费。
最后,优化的库存管理有助于提高企业的服务水平和客户满意度。
及时准确的库存管理可以保证产品供应的稳定性,提高企业的竞争力。
二、仓库库存管理的优化策略1.需求预测与订单管理准确的需求预测是优化仓库库存管理的基础。
通过分析历史销售数据、市场趋势、客户反馈等信息,可以预测未来的需求量,并根据预测结果制定合理的订单管理策略。
订单管理包括定货量、定货周期等要素的确定,可以避免库存过多或过少的问题,提高运营效率。
2.安全库存与经济批量安全库存是为了应对需求不确定性而设置的库存储备量,可以帮助企业应对突发的需求增加或供应链中的延迟等问题。
根据需求预测的准确性和供应链的稳定性,合理确定安全库存水平。
经济批量是指在订货成本和库存成本之间寻找最佳平衡点。
企业可以通过经济批量的分析,确定最优的订货数量,降低采购成本和库存成本。
3.供应链协同与信息共享仓库库存管理涉及到供应链各个环节的协同配合。
与供应商、生产部门等建立良好的合作关系,并通过信息共享实现供需的快速反应与协调。
通过优化供应链上下游的协同配合,可以减少库存积压和缺货的情况,提高企业运营效率。
三、建立仓库库存管理模型建立适合企业的仓库库存管理模型是优化库存管理的关键步骤。
常用的模型包括EOQ模型、ROP模型、ABC分类法等。
仓库管理中常用的五种库存管理方法

仓库管理中常用的五种库存管理方法2018年1月17日◎文丨来源:网络物流过程中商品数量的管理简称库存管理。
以前普遍认为仓库里的商品越多,表明企业越发达、越兴隆,而现代管理学则认为零库存是最好的库存管理。
传统库存管理方法有很多种,目前WMS仓储管理系统也能很好地解决这一问题,但了解传统管理方法会更有助于我们在仓库管理中提升效率和业务水平。
现在简单介绍五种常用的传统库存管理方法。
一、准时生产制库存管理方法(JIT)JIT作为一种先进的生产方式,通过看板等工具的应用,保证了生产的同步化和均衡化,实行“适时、适量、适物”的生产,效果明显。
JIT的基本原理是以需定供、以需定产,即供方(上一环节)根据需方(下一环节)的要求,按照需求方的品种、规格、质量、数量、时间、地点等要求,将生产物资或采购物资,不多、不少、不早、不晚且质量有保证地送到指定地点。
看板管理是JIT生产方式中最独特的部分,是JIT生产现场控制技术的核心,将传统生产过程中前道工序向后道工序送货,改为后道工序根据“看板”向前道工序取货。
二、ABC重点控制法ABC重点控制法的基本点是:将企业的全部存货分为A、B、C三类,管理时对金额高的A类物资,作为重点加强管理与控制;B类物质按照通常的方法进行管理和控制;C类物资品种数量繁多,但价值不大,可以采用最简便的方法加以管理和控制。
(1)对A类存货的控制,要计算每个项目的经济订货量和订货点,尽可能适当增加订购次数,以减少存货积压,也就是减少其昂贵的存储费用和大量的资金占用。
(2)对B类存货的控制,也要事先为每个项目计算经济订货量和订货点,同时也可以分享设置永续盘存卡片来反映库存动态,以节省存储和管理成本。
(3)对于C类存货的控制,由于它们为数众多,而且单价又很低,存货成本也较低,因此,可以适当增加每次订货数量,减少全年的订货次数。
三、经济批量法(EOQ)经济批量法是确定批量和生产间隔期时常用的一种以量定期方法,是指根据单位产品支付费用最小原则确定批量的方法,也是确定批量和生产间隔期时常用的一种以量定期方法。
最佳订货量计算公式_概述说明以及解释

最佳订货量计算公式概述说明以及解释1. 引言:1.1 概述:在现代供应链管理中,订货量计算是一个关键的决策环节。
准确计算订货量可以帮助企业实现经济效益最大化、减少库存成本并提高客户满意度。
因此,寻找一种最佳的订货量计算公式对于企业来说具有重要意义。
1.2 文章结构:本文将首先阐述订货量计算公式的重要性,包括它对经济效益、库存成本和客户满意度的影响。
其次,我们将介绍几种常见的订货量计算方法,例如EOQ模型、安全库存法和最大库存法。
然后,我们将探讨这些公式在不同行业中的应用场景,包括零售业务、制造业务和服务行业。
最后,我们将总结文章内容和观点,并展望未来发展趋势和研究方向。
1.3 目的:本文旨在提供读者一个全面了解订货量计算公式及其应用的概述说明和解释。
通过深入分析订货量计算公式的重要性以及不同方法在不同行业中的应用情况,读者可以更好地理解如何选择适合自己企业需求的订货量计算公式,并以此优化供应链管理,实现更高的经济效益和客户满意度。
2. 订货量计算公式的重要性:订货量计算公式是供应链管理中的关键概念之一,它对企业的经济效益、库存成本以及客户满意度都有着重要影响。
以下将详细说明订货量计算公式的重要性。
2.1 经济效益:正确计算订货量可以帮助企业实现更高的经济效益。
通过使用适当的订货量计算公式,企业能够平衡生产成本与销售收入之间的关系,从而最大程度地提高利润。
如果订货量过低,企业将面临供应不足和销售机会损失;而过高的订货量则可能导致库存积压和资金闲置等问题。
因此,合理地计算订货量对于企业获得良好的经济效益至关重要。
2.2 减少库存成本:订货量计算公式还可以帮助企业减少库存成本。
库存是企业运营中占用大量资金并需要额外维护费用的重要方面。
通过根据需求预测和采用适当的订货量计算方法,企业能够更好地控制库存水平,避免过高的库存积压和运营风险。
合理的库存管理可以降低库存持有成本、仓储费用以及过期损失等,从而提高企业的整体运营效率。
安全库存量的确定

从属需求的需求数量和需求时间与其他 的变量存在一定的相互关系,可以通过一定 的数学关系推算得出。
2、独立需求与从属需求的区别:
掌握需求的数量和时间的方式不同: 独立需求是随机的,只能靠预测掌握; 而从属需求根据生产计划来确定。
=365/N
书上例题
4)订货点,一般情况下,公司的存货不能做到随时 补充,因此不能等存货用完再去订货,而需要在没有用完 前提前订货。提前订货情况下,公司再次发出订货单时,
尚有存货的库存量称为再订货点,用R表示。 它是交货时间(L)与每日平均需用量(d)的乘积:
R Ld
若考虑到按订货点发出订单后,需求量增大或送货延迟, 则需多储备一些存货,以备应急之需。此时,考虑保险储
注意送货延误大批量需求安全库存工作库存再订货水平送货延误大批量需求安全库存工作库存再订货水平通过安全存货来提高安全系数2安全库存的变量1需求量的变动2订货提前期的变动3服务水平发出订货成批到货发出订货成批到货时间时间订货点保险有货量前置发出订货成批到货发出订货成批到货时间时间订货点保险有货量前置理想库存模型前置时间时间前置时间前置时间缺货前置时间时间前置时间前置时间缺货前置时间时间前置时间前置时间缺货实际库存模型050100050100保险存货量与服务水准服务水准不缺货概率3
四、库存管理的功能
库存管理的功能主要表现在: 1、在保证企业生产、经营需求的前提
下,使库存量经常保持在合理的水平上。 2、掌握库存量动态,适时,适量提出订
货,避免超储或缺货。 3、减少库存空间占用,降低库存总费用。 4、控制库存资金占用,加速资金周转。
五、库存管理的思想
1、独立需求与从属需求 所谓独立需求是指需求变化独立于人们
安全库存 经济批量EOQ 再订货点

安全存储量报告(以深圳制水器为例)摘要:仓库贮存货物数量所涉及的主要几点问题:1.应该存储多少数量产品(安全存储量以及经济批量EOQ)2.什么时间应该补充存货(再订货点R)3.应该补充多少数量存货(经济批量EOQ)一、应该存储多少数量产品产品存储数量通常为安全仓储量安全存储量=预计每天销售*提前期L+安全库存SS(供大于求则”-”,供小于求”+”)安全库存:安全库存是除去预计销量外,保留在仓库中的应急保障数量提前期固定的安全库存SS=Z**STD销售量固定的安全库存SS=Z*STD2*D(提前期内的日需求量)提前期销售量均未定的安全库存SS=Z*Z年订货次数顾客服务水平及安全系数表顾客服务水平(%) 安全系数z 顾客服务水平(%) 安全系数z100.00 3.09 96.00 1.7599.99 3.08 95.00 1.6599.87 3.00 90.00 1.8099.20 2.40 85.00 1.0499.00 2.33 84.00 1.0098.00 2.05 80.00 0.8497.70 2.00 75.00 0.6897.00 1.88二、什么时间应该补充存货再订货点R=平均需求量D*提前期L+安全库存SS三、应该补充多少数量存货在不考虑经济订货批量的情况下再订货量=平均需要量*设定的安全库存期(如一周七天)+安全库存-现库存-在途物资但是上述在订货量不是经济订货量,全年下来成本偏高,本厂不生产的经济订货批量为:EOQ=在此基础上的产品年总成本T=年购置成本+年库存成本即T=年产品成本+年采购成本+年库存成本T=DC+S*D/EOQ+H*EOQ/2T:年总成本D:年需求量C:单位产品成本S:采购成本EOQ:经济订货批量R:再订购点L:提前期H:采购单位产品的年平均存储成本上述经济订货批量即最优库存量对于本厂生产的产品最优库存量(即经济生产批量EPL)为P为生产率;d为需求率(d<P);T为生产时间;Imax为最大库存量;Q为生产批量;RL为订货点;LT为生产提前期,D—年总需求量,TC—年总成本,S—每次生产的生产准备费, H—单位货物每年的存储成本;求出过程:而Q=pt,tp =Q / p,故Imax =t p(P−d) = (Q / p)(P−d) = Q(1 −d / P)根据EOQ的总费用公式,可得对上式求导,可得:2则,为经济生产批量。
库存EOQ与安全库存公式
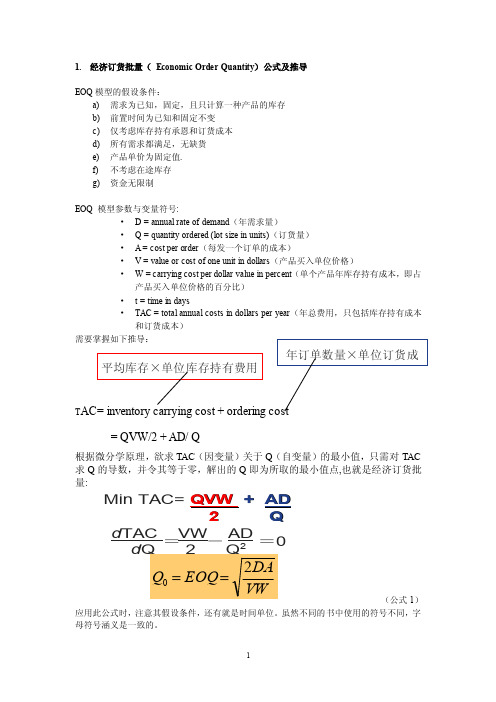
1. 经济订货批量( Economic Order Quantity )公式及推导EOQ 模型的假设条件:a) 需求为已知,固定,且只计算一种产品的库存b) 前置时间为已知和固定不变c) 仅考虑库存持有承恩和订货成本d) 所有需求都满足,无缺货e) 产品单价为固定值.f) 不考虑在途库存g) 资金无限制EOQ 模型参数与变量符号:• D = annual rate of demand (年需求量)• Q = quantity ordered (lot size in units)(订货量)• A = cost per order (每发一个订单的成本)• V = value or cost of one unit in dollars (产品买入单位价格)• W = carrying cost per dollar value in percent (单个产品年库存持有成本,即占产品买入单位价格的百分比)• t = time in days• TAC = total annual costs in dollars per year (年总费用,只包括库存持有成本和订货成本)需要掌握如下推导:T AC= inventory carrying cost + ordering cost= QVW/2 + AD/ Q根据微分学原理,欲求TAC (因变量)关于Q (自变量)的最小值,只需对TAC 求Q 的导数,并令其等于零,解出的Q 即为所取的最小值点,也就是经济订货批量:(公式1) 应用此公式时,注意其假设条件,还有就是时间单位。
虽然不同的书中使用的符号不同,字母符号涵义是一致的。
平均库存×单位库存持有费用 年订单数量×单位订货成Min TAC= QVW + AD 2 Q d TAC VW AD d 2-==02.安全库存(只需掌握概念和各公式应用的条件,推导过程可在学完概率论与数理统计课程再理解)Safety Stock(安全库存) refers to t he inventory a company holds above normal needs as a buffer (缓冲) against delays in receipt of supply or changes in customer demand.(安全库存,又称为缓冲库存,是指一个企业所持有的超过正常需要的库存,其作为缓冲以应对需求不确定性或供应的延迟。
库存管理的基本原理和方法

库存管理的基本原理和方法库存管理是指企业对物资、产品和半成品等库存进行有效的控制和管理,以实现企业库存的最优化。
其基本原理是根据市场需求、供应链状况等因素,合理确定库存水平和库存周期,确保库存的准确性和合理性。
第一,经济订货批量(EOQ)模型。
EOQ模型是基于库存成本、发货成本和订货成本等因素来确定最优订货批量的数学模型。
该模型的基本假设是需求是稳定的、发货时间和订货成本是固定的,通过计算最小化总供应链成本来确定最优的订货批量。
第二,安全库存法则。
安全库存是指为了应对需求不确定性、供应链延迟等风险因素而额外储存的库存量。
安全库存的确定可以采用统计方法如安全系数法、防冻库存法等,也可以根据经验和专家判断进行确定。
第三,ABC分类法。
ABC分类法是根据物资的重要性和价值来对库存进行分类的方法。
按照价值和重要性高低将物资分为A、B、C三类,然后针对不同分类制定不同的库存管理策略。
比如对A类物资要进行频繁盘点和控制,而C类物资则可以进行周期性盘点。
第四,合理预测需求。
准确预测需求对库存管理至关重要。
可以采用统计方法如时间序列分析、回归分析等,也可以借助市场调研和销售预测等手段来进行需求预测,以便合理安排订货计划和库存水平。
第五,供应链配送管理。
供应链配送管理是通过合理安排供应链内物资的流动和配送过程,以提高库存周转率和减少库存积压量。
可以采用物流管理技术和系统,优化仓库布局和运输路线,提高配送效率和降低成本。
除了以上几种方法,库存管理还需要根据实际情况选择合适的库存控制方法和策略。
如定期盘点、库存报表和库存系统管理等,以确保库存数量的准确性和合理性,并且及时调整库存水平和订货策略,以适应市场需求和供应链状况的变化。
再订货点与安全库存
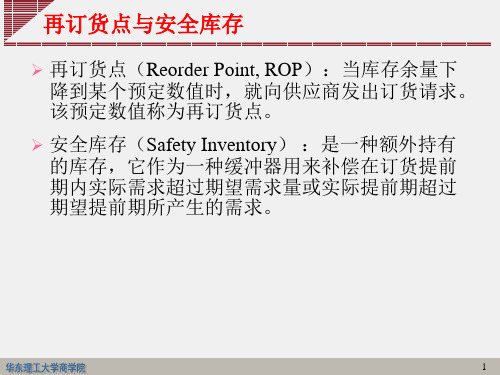
再订货点(Reorder Point, ROP):当库存余量下
降到某个预定数值时,就向供应商发出订货请求。 该预定数值称为再订货点。
安全库存(Safety Inventory) :是一种额外持有
的库存,它作为一种缓冲器用来补偿在订货提前 期内实际需求超过期望需求量或实际提前期超过 期望提前期所产生的需求。
标准正态分 布中的安全 系数
需求服从正 态分布时的 再订货点
平均需求
再订货点
安全 系数
0
Z
6
给定采购补货策略下的服务水平衡量
服务水平(CSL)衡量公式:
CSL=Prob(周期需求≤ROP)
在需求服从正态分布的条件下,上式变为:
CSL=F( ROP,DLT ,σLT )
ROP D LT , 0, 1) =Φ(
缩短供应提前期需要供应商付出努力,而减少的是采购 商的库存,因而需要设计相应的收益分享激励机制。
降低需求的不确定性,即标准差σ 安全库存与标准差保持同比例下降。 方法:采用更好的市场情报系统和更先进的需求预测方法。
对供应链管理来说,要降低需求的不确定性,就必须使各环 节的预测与最终顾客需求的数据相一致,协同预测(CPFR)。
用标准方差
• 库存在不确定性需求下如何处理?
1 2
用批量定货量与平均需求匹配
用一个安全库存来保证变化下的服务水平
安全库存与需求分布的方差有关 安全库存与服务水平有关
5
服务水平与安全库存的关系
服务水平 (无缺货概率) 无缺货概率
安全 库存
在提前期内需求 近似服从正态分 布的情况下,如 果没有安全库存, 缺货的概率可达 50% 。增加安全 库存后,降低了 缺货风险,提高 了服务水平。
库存商品订货批量计算公式

库存商品订货批量计算公式在零售和批发业务中,库存管理是非常重要的。
其中一个关键的方面就是订货批量的计算。
订货批量是指一次性订购的商品数量,它直接影响着企业的库存成本和运营效率。
因此,正确地计算订货批量是非常重要的。
本文将介绍库存商品订货批量的计算公式以及其应用。
订货批量计算的公式通常基于经济批量模型,该模型旨在最小化库存成本和订货成本的总和。
经济批量模型的基本假设是,需求是稳定的,没有折扣或促销活动,以及订货成本和库存成本是已知的。
在这个模型中,订货批量的计算公式如下:EOQ = √(2DS/H)。
其中,EOQ代表经济订货量,D代表年需求量,S代表订货成本,H代表库存持有成本。
首先,让我们来解释一下这个公式中的各个变量。
年需求量(D)是指企业一年内需要订购的商品数量。
订货成本(S)是指每次订货所需要支付的成本,包括运输成本、订购成本等。
库存持有成本(H)是指企业一年内持有库存所需要支付的成本,包括仓储成本、资金占用成本等。
通过这个公式,我们可以计算出一个最优的订货批量,以最小化总的订货成本和库存成本。
在实际应用中,订货批量的计算还需考虑一些额外的因素。
首先,企业可能会面临订货数量的限制,例如供应商最小订购量、货架空间限制等。
其次,订货批量还需要考虑到商品的季节性需求、市场变化等因素。
因此,在实际应用中,我们可能需要对经济订货量进行调整,以适应实际的经营环境。
除了经济订货量,企业还需要考虑订货周期。
订货周期是指两次订货之间的时间间隔。
它直接影响着库存水平和库存周转率。
通常情况下,订货周期的计算公式如下:ROP = dL + SS。
其中,ROP代表再订货点,d代表日需求量,L代表订货周期,SS代表安全库存。
再订货点是指当库存水平降至一定程度时需要再次订货的点。
安全库存是指为了应对意外情况而额外储备的库存。
通过再订货点的计算,企业可以及时地进行补货,以避免库存不足的情况发生。
在实际应用中,订货周期的计算还需要考虑到供应商的交货周期、季节性需求等因素。
库存管理的五种方法
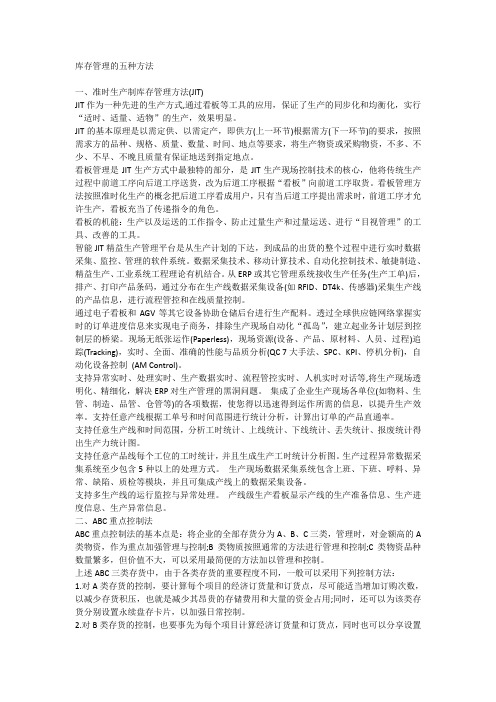
库存管理的五种方法一、准时生产制库存管理方法(JIT)JIT作为一种先进的生产方式,通过看板等工具的应用,保证了生产的同步化和均衡化,实行“适时、适量、适物”的生产,效果明显。
JIT的基本原理是以需定供、以需定产,即供方(上一环节)根据需方(下一环节)的要求,按照需求方的品种、规格、质量、数量、时间、地点等要求,将生产物资或采购物资,不多、不少、不早、不晚且质量有保证地送到指定地点。
看板管理是JIT生产方式中最独特的部分,是JIT生产现场控制技术的核心,他将传统生产过程中前道工序向后道工序送货,改为后道工序根据“看板”向前道工序取货。
看板管理方法按照准时化生产的概念把后道工序看成用户,只有当后道工序提出需求时,前道工序才允许生产,看板充当了传递指令的角色。
看板的机能:生产以及运送的工作指令、防止过量生产和过量运送、进行“目视管理”的工具、改善的工具。
智能JIT精益生产管理平台是从生产计划的下达,到成品的出货的整个过程中进行实时数据采集、监控、管理的软件系统。
数据采集技术、移动计算技术、自动化控制技术、敏捷制造、精益生产、工业系统工程理论有机结合。
从ERP或其它管理系统接收生产任务(生产工单)后,排产、打印产品条码,通过分布在生产线数据采集设备(如RFID、DT4k、传感器)采集生产线的产品信息,进行流程管控和在线质量控制。
通过电子看板和AGV等其它设备协助仓储后台进行生产配料。
透过全球供应链网络掌握实时的订单进度信息来实现电子商务,排除生产现场自动化“孤岛”,建立起业务计划层到控制层的桥梁。
现场无纸张运作(Paperless),现场资源(设备、产品、原材料、人员、过程)追踪(Tracking),实时、全面、准确的性能与品质分析(QC 7大手法、SPC、KPI、停机分析),自动化设备控制(AM Control)。
支持异常实时、处理实时、生产数据实时、流程管控实时、人机实时对话等,将生产现场透明化、精细化,解决ERP对生产管理的黑洞问题。
供应链管理中的库存优化算法

供应链管理中的库存优化算法在供应链管理中,库存优化算法扮演着至关重要的角色。
库存管理不仅涉及到如何减少库存成本,还需要确保及时供应和满足客户需求。
因此,寻找一种高效的库存优化算法对于提升供应链效能至关重要。
本文将探讨几种常见的库存优化算法,并分析其优缺点。
一、经济订货数量模型(EOQ)经济订货数量模型(EOQ)是库存管理中最基础也是最常用的算法之一。
该算法通过平衡订货成本和持有成本来确定最经济的订货数量。
EOQ模型假设需求是稳定且可预测的,且每次订单的成本是固定不变的。
它的计算公式如下:EOQ = √((2DS)/H)其中,D表示需求量,S表示订货成本,H表示持有成本。
优点:EOQ模型简单易懂,计算公式明确,可迅速得到最优订货数量。
缺点:该算法假设需求是稳定不变的,忽略了季节性需求和市场波动性,因此在需求不稳定的情况下容易导致库存不足或过剩。
二、安全库存算法安全库存算法是一种常见的库存优化算法,旨在确保供应链中不会因为突发事件或需求的不确定性而导致缺货。
安全库存量是基于过去的需求波动考虑的,一般通过计算标准差来确定。
优点:安全库存算法考虑到需求的波动性,可以提供一定的缓冲,在某种程度上减少了缺货风险。
缺点:安全库存算法无法解决库存过高的问题,容易导致库存堆积。
三、定期审查和重新订货算法定期审查和重新订货算法是一种基于定期检查的库存管理方法。
在每个固定时间间隔结束时,对库存进行检查,如果库存低于设定的阈值,则重新订货。
该算法关注的是防止缺货而不是最小化成本。
优点:定期审查和重新订货算法容易实施和管理,可以防止缺货。
缺点:该算法没有考虑到需求的不确定性和波动性,容易导致库存过高。
四、基于需求预测的算法基于需求预测的算法尝试通过分析历史数据和市场趋势来预测未来的需求,并根据预测结果进行库存管理决策。
常见的需求预测方法包括移动平均法、指数平滑法和回归分析等。
根据需求的预测结果,可以灵活地调整订货量和安全库存量。
正确运用定量订货法,如何确定合适的订货点与订货批量

正确运用定量订货法,如何确定合适的订货点与订货批量定量订货方式是在库存下降到预定的最低库存量(订货点)时,按规定数量(一般以经济批量EOQ为标准)进行订货补充的一种库存控制方法。
它主要靠控制订货点和订货批量两个参数来控制订货,达到既最好地满足库存需求,又能使总费用最低的目的。
运用定量订货法中的订货点和订货批量的计算方法如下:1.确定订货点根据影响订货点的三个因素:订货提前期、平均需求量、安全库存来确定订货点,具体方法如下:(1)在需求和订货提前期确定的情况下,不需要设立安全库存时,计算公式如下:订货点=订货提前期(天)×全年需求量/360(2)在需求和订货提前期都不确定的情况下,需要安全库存,计算公式如下:订货点=(平均需求量×最大订货提前期)+安全库存提醒您:订货点公式中安全库存采用前一技能点中介绍的安全库存计算方法计算得到。
2.确定订货批量在定量订货方式中,对于每一品种的商品每次订货批量都是相同的,所以每个品种都要制定一个订货批量,通常取经济批量为订货批量。
计算公式为:C—单位订货成本(元/次),D—某库存物品的年需求量(件/年),FK,P—单位库存平均年库存保管费用(元/件年),P—单位采购成本(元/件),F—单件库存保管费用与单件库存采购成本之比。
3.适用范围因为定量订货法订货数量固定,所以在具有管理方便、便于采用经济订货批量进行订货等优点的同时也具有不便于严格管理、事前计划比较复杂等一些缺点,所以有一定的适用范围,通常在以下几种情况下采用定量订货法比较适合:(1)单价比较便宜,不便于少量订货的产品,如螺栓、螺母等;(2)需求预测比较困难的维修材料;(3)品种数量繁多、库房管理事务量大的物品;(4)消费量计算复杂的产品;(5)通用性强、需求总量比较稳定的产品等。
牢记要点定量订货方式的两个参数:确定订货点确定订货批量实践练习请您做下面的计算题。
某单位去年全年对商品M的需求量如第153页表所示,已知最大订货提前期为4个月,缺货概率为5%,每箱产品的保管费用为3元,每次订货的成本为30元,试求商品M的订货点和订货批量。
再订货点与安全库存myOM
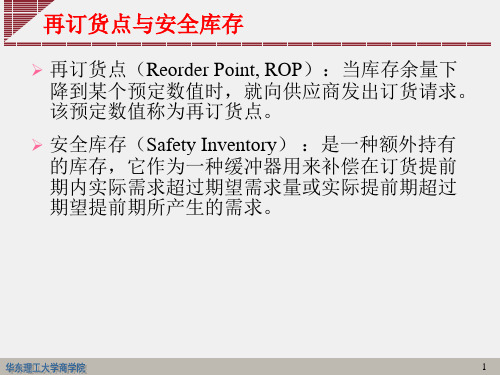
需求和提前期都不确定条件下的再订货点
DLT=d×ALT
σDLT=
LT2d2
2 LT
ROP = DLT+ SI = DLT+ z× σDLT
12
例4中,假设提前期均值为3天,标准差为0.5天。
σDLT= L T2d2L 2T= 332020 20 0.52
=112 .7 SI=1.64×112.69≈185件 ROP=200×3+185=785件
ROPDL
LT
T=Φ-1(
CSL
,
0,
1)
ROP = DLT+Φ-1( CSL , 0, 1)× σLT
SI =Φ-1( CSL , 0, 1)× σLT
安全系数z
转化为标准正 态分布求解
9
例4:某大型服装零售商销售一款服装,每天平 均需求量为200件,标准差为30件,订货提前期 为3天。若该零售希望达到95%的周期服务水平, 则应如何确定安全库存和再订货点?
1
需求与提前期都是常数时的再订货点
在库存持有量能够满足等待订货期间(即提 前期)的需求时下订单。 ➢ 若需求与提前期都是常数,再订货点为:
ROP = d LT 其中: d —— 需求率; LT —— 提前期
Q*=93
ROP=?
2
需求与提前期变化时的再订货点
➢ 一旦需求或提前期发生变化,实际需求就 有可能超过期望需求。因此,为了减少缺 货风险,应持有额外库存即安全库存。这 时,再订货点为: ROP = 提前期内的期望需求 + 安全库存(SI)
再订货点与安全库存
➢ 再订货点(Reorder Point, ROP):当库存余量下 降到某个预定数值时,就向供应商发出订货请求。 该预定数值称为再订货点。
安全库存及再订货量
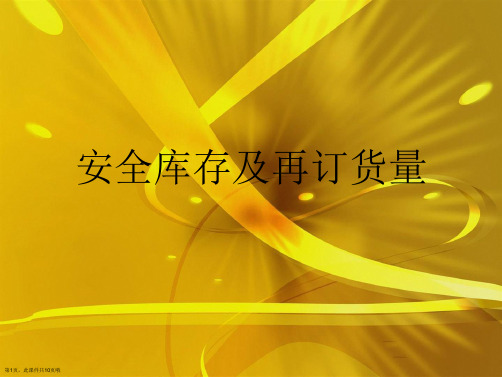
3、批量对批量
周 1 2 3 4 5 6 7 8 9 10 合计 需求 77 42 38 21 26 112 45 14 76 38 489 补足量 77 42 38 21 26 112 45 14 76 38 489
4、固定期间需求(FPD)
e.g.period=2
周1 2 3
需求 77 42 38
7 8 合计 98 156 2294
参数 数值
平均周需求 周需求量的 提前期的需
量
标准差
求量
44.46
32.09
88.91
安全库存 库存(订货点) 供应周数
85.31
174
3.92
2、数据分享:外仓整合的理论库存
第2页,此课件共10页哦
二、再订货量的计算
1、两种传统的库存计划模型
1)再订货点(s,Q)模型(定量订货法)
所谓定量订货法,就是预先确定一个订货点和订货批量,随时检查库存,当库存下降到订 货点时就发出订货。在整个系统运作过程中订货点和订货批量都是固定的。
----订货批量Q:一般为经济订货批量
----订货点:ROP(s)=LT*D+SS
应用前提: 订货不受限制的情况,即随时随地都能订到货,这样市场必需具备物资资源供应充足和自 由流通的条件。 直接运用只适用于单一品种的情况。如果要实行几个品种联合订购,就要对公式进行 灵活处理才能运用。
安全库存及再订货量
第1页,此课件共10页哦
例题讲解
1、假设某品牌奶粉的历史销售数据如下,提前期约为两个星期,如果希望保证服务水平
大约为97%,其安全库存和库存水平应为多少?
月份
9 10 11 12 1 2 3 4 5 6
- 1、下载文档前请自行甄别文档内容的完整性,平台不提供额外的编辑、内容补充、找答案等附加服务。
- 2、"仅部分预览"的文档,不可在线预览部分如存在完整性等问题,可反馈申请退款(可完整预览的文档不适用该条件!)。
- 3、如文档侵犯您的权益,请联系客服反馈,我们会尽快为您处理(人工客服工作时间:9:00-18:30)。
安全库存经济批量E O Q再
订货点
-标准化文件发布号:(9456-EUATWK-MWUB-WUNN-INNUL-DDQTY-KII
安全存储量报告(以深圳制水器为例)
摘要:仓库贮存货物数量所涉及的主要几点问题:
1.应该存储多少数量产品(安全存储量以及经济批量EOQ)
2.什么时间应该补充存货(再订货点R)
3.应该补充多少数量存货(经济批量EOQ)
一、应该存储多少数量产品
产品存储数量通常为安全仓储量
安全存储量=预计每天销售*提前期L+安全库存SS(供大于求则”-”,供小于求”+”)安全库存:安全库存是除去预计销量外,保留在仓库中的应急保障数量
提前期固定的安全库存SS=Z**STD
销售量固定的安全库存SS=Z*STD2*D(提前期内的日需求量)
提前期销售量均未定的安全库存SS=Z*
Z/年订货次数
顾客服务水平及安全系数表
顾客服务水平(%)安全系数z顾客服务水平(%)安全系数z
二、什么时间应该补充存货
再订货点R=平均需求量D*提前期L+安全库存SS
三、应该补充多少数量存货
在不考虑经济订货批量的情况下
再订货量=平均需要量*设定的安全库存期(如一周七天)+安全库存-现库存-在途物资
但是上述在订货量不是经济订货量,全年下来成本偏高,本厂不生产的经济订货批量为:
EOQ=
在此基础上的产品年总成本
T=年购置成本+年库存成本
即T=年产品成本+年采购成本+年库存成本
T=DC+S*D/EOQ+H*EOQ/2
T:年总成本D:年需求量C:单位产品成本S:采购成本
EOQ:经济订货批量 R:再订购点L:提前期
H:采购单位产品的年平均存储成本
上述经济订货批量即最优库存量
对于本厂生产的产品最优库存量(即经济生产批量EPL)为
P为生产率;d为需求率(d<P);T为生产时间;Imax为最大库存量;Q
为生产批量;RL为订货点;LT为生产提前期,D—年总需求量,TC—年总成本,S—每次生产的生产准备费, H—单位货物每年的存储成本;
求出过程:
而Q=pt,t p = Q / p,
故I max = t p(P−d) = (Q / p)(P−d) = Q(1 −d / P)
根据EOQ的总费用公式,可得
2
对上式求导,可得:
则,为经济生产批量。
综述,需提供如下信息:提前期、单次采购成本、库存产品的应计利息(机会成本)需财务提供)以及存储成本
由以上内容可以得出:
1.安全库存量及最优库存量
2.具体的补充库存时间
3.补充库存时的经济批量
4.最优年存货总成本
5.采购部最优采购次数以及每次采购量
6.生产车间最优生产次数以及每次生产量
注:
1存储成本包括:
1.1固定成本:仓库的折旧费、保险费、修理费、冷暖气费、通风照明费等
仓储费用,以及仓库内部的装卸搬运费、仓库管理费等;
1.2变动成本:存储的货物本身占用资金的费用,为储存物资占用资金而支
付的利息或占用费、物资陈旧变质、损坏、拆耗所发生的损失等。
2采购成本(订货成本):
1.1固定成本:采购人员的工资等,称为订货的固定成本
1.2变动成本:与订货次数有关,发出采购订单去向外部供应商购买物料而
发生的成本,主要有办公费、差旅费、邮资、电话电报费、运输费、检
验费、入库搬运费等支出等成为订货的变动成本;向内部工厂发出订单
而发生的成本,如向工厂订制一批物料时,所发生的文书工作的成本、
机器调整费、新调整后首次生产带来的开工废品以及其他取决于订货或
生产的批数的一次性费用。
于修俊
2016年5月8日。