NEW COATINGS FOR THE CORROSION PROTECTION OF STEEL PIPELINES AND PILINGS
Akzo Nobel Coatings Inc. Resicoat R4-ES HJF42R 防腐蚀

Functional Powder CoatingsProduct Datasheet20, Culvert Street T+1 855-294-8934Nashville, TN 37210F+1 615-564-4181USAResicoat ®R4-ESfor Electrostatic Spray Application on Preheated Surfaces Code: HJF42RProduct DescriptionResicoat ® R4 is a high quality thermosetting epoxy powder coating for the corrosion protection of valves and fittings, manufactured from cast iron or steel. The powder coating is available to be applied in one layer on a preheated surface by electrostatic spray application. Typical film thickness achieved is in the range of 250 – 500 µm. The resultant thermoset epoxy has a high mechanical resistance with excellent electrical insulation properties. Drinking water approvals are available to confirm the coatings suitability, as a hygienic and environmental friendly coating. The outstanding adhesion of Resicoat ® R4epoxy powders to the metal substrate provides long term protection of the coated component. It ensures a reliable conservation to the function and value of the parts for the common water and gasdistribution network. The applicator of Resicoat ®R4 benefits from a modern and environmentallyfriendly process. It is possible to overcoat Resicoat ®R4 with polyester powder and liquid coatings to achieve UV protection.Typical valueMethod Powder PropertiesBinder System Epoxy resinDensity1.45 – 1.55 g/cm³ASTM D5965Gel time at 392° F (200° C )25 – 40 sec.ASTM D4217Particle size distribution D10 = 10 – 15 µm D90 = 135 – 160 µm Malvern ISO 8130-1Storage stability 6 months at ≤ 74 °F (23 °C)Safety precautionsSee Material Safety Datasheet (MSDS)Application DataPreheating temperature object 392 – 428 °F (200 – 220 °C) object temperaturePost cure conditions objectThe coating is self curing, if the wall thickness of the steel/cast iron is greater than 8 mm. If the wall thickness of the steel/cast iron is less than 8 mm, additional curing of 3 to 8 minutes at 392 °F (200 °C) object temperature is required.1. Pre-cleaning The surface must be free of oil, grease, salt, and other impurities.2. BlastingMolding sand, rust and sharp edges must be removed with angular steel grit. The graphite from the cast iron must beremoved from the blasting material according NACE No.2/ SSPC-10/Sa 2.5. Recommended anchor profile of ≥60 µm should be stored max. 4 hours before pre-heating (dust-free and dry).3. Pre-heating This form of heating produces a uniform, defined temperature in the component. Any oxidation should be avoided.4. Coating applicationImmediately after preheating, the coating process starts without loosing any object temperature. The coating is done in the shortest possible time in a single pass with no interruptionFunctional Powder Coatings20, Culvert Street T+1 855-294-8934Nashville, TN 37210F+1 615-564-4181USATypical valueMethodCoating Process5. Coating cureCuring is achieved by the heat contained in the object. If the heating capacity of the work piece is sufficient. To confirm fully curing, MIBK is dropped for 30 sec. on the film surface with no visible change.Material PropertiesColorblueRecommended film thickness 10 – 14 mils (250 – 350 µm)Flowsmooth Gloss at 90° angle 70 – 90 units DIN 67530Cross cut test Gt 0DIN EN ISO 2409Impact resistance> 5 Joule > 2.26 Joule > 18 JouleDIN 30677-2ASTM D279420 inchpoundASTM G14 modified1/8 in (3.2 mm) steel plate Abrasion resistance < 40 mg ASTM D4060CS-17, 1000 g, 1000 cycles Dielectric strength≥ 30 kV/mm IEC 60243-1Volume resistivity (DC voltage) 1.1 x 1015ASTM D257Elongation> 5 %DIN 30671Indentation resistance 48 h, 158 °F (70 °C)24 h, 140 °F (60 °C)< 30 %< 10 %DIN 30677-2/DIN EN 14901ASTM G17Compressive strength > 100 MPa ASTM D695Shear adhesion> 35 MPa ASTM D1002Heat aging in air (90 d), water fulfilled DIN EN 14901Thermal stability under heat aging pass AS/NZS 4158:2003Weathering (Xenon test), 100 d pass ASTM D2596-99HardnessF Pencil Strain polarization pass WIS 4-52-01Cathodic disbonding 30 d, 74 °F (23 °C)≤ 10 mm DIN 30677-2, GSK Hot water immersion 90 d, 158 °F (70 °C)pass AWWA C550-05Adhesion> 20 MPa ASTM D4541Adhesion after 7 d,194 °F (90°C)water≥ 16 MPaISO 4624, GSK Tensile strength approx. 500 kg/cm³ASTM D2370Penetration< 5 %ASTM G17Functional Powder Coatings20, Culvert Street T+1 855-294-8934Nashville, TN 37210F+1 615-564-4181USATypical valueMethodMaterial PropertiesDisinfectant resistanceaccording DVGW work sheet W 291(chlorine dioxide, sodium hypochlorite)no change of surface,no chalkingafter 10 test stages à 15 h The following migration test with demineralised water showed no defects of the film. The concentration of the examined parameters in the tested water were below the limits of the epoxy guideline for ancillaries for pipes DN > 300 mm (in main trunks).Water condensation test (Cleveland test), 21 d no changeASTM D4585Salt spray resistance, 2000 h no blistering, no loss of adhesionBS 3900:F4Salt spray test, 4000 hno under-rusting on the cut DIN EN ISO 9227(steel substrate)Water absorption, 100 d, 74 °F (23 °C)pass AS/NZS 3862Chemical resistance (pH 3–13, 23° C)fulfilledEN 598Conformities ·AWWA C116·AWWA C550-05·EN 14901·ISO 12944-2, table 1(standard does not include powder coating systems)It is assumed that Resicoat ® R4 is suitable to meet the high atmospheric corrosivity category C4 (typically in industrial areas and coastal areas with moderate salinity) and the very high atmospheric- corrosivity -categories C5-I (industrial) and C5-M (marine) if applied as a holiday-free coating at a film thickness> 400 µm. A sufficient film thickness is highly required to ensure good edge coverage. For gloss and color stability a UV-resistant polyester topcoat has to be applied.Drinking Water ApprovalsUS: ANSI/NSF 61 Drinking Water System Components – Health Effects, NSF DE: UBA-Coatings Guideline, Approval no.: C-138801-06, Hygiene InstitutDE: DVGW directive work sheet W 270, Approval no. W-211795-11, Hygiene Institut UK: BS 6920, Approval No. 1112500, WRASDate of issue:July 10, 2015Authorized by:GK Revision No.:3Disclaimer: This Product Data Sheet is based on the present state of our knowledge and on current laws. The data referring to Powder Properties, Application Data and Physical Tests is based on lab based samples. Factors such as quality or condition of the substrate may have an effect on the use and application of the product. It remains the responsibility of the user to test thoroughly if the product is applicable for the intended use. The use of the product beyond our recommendation releases us from our responsibility, unless we have recommended the specific use in writing. It is always the responsibility of the user to take all necessary steps to fulfil the demands set out in the local rules and legislation. We are not liable for any application-technological advice. The Product Data Sheet shall be updated from time to time. Please ensure you have the latest version before using the product. All products and Product Data Sheets are subject to our standard terms and conditions of sale (GCS). You can receive the latest copy of GCS via internet or our post address. Brand names mentioned in this Product Data Sheet are trademarks of or are licensed to the AkzoNobel group.Resistance against chemical substances of Resicoat ®R4 at room temperature20, Culvert Street T+1 855-294-8934Nashville, TN 37210F+1 615-564-4181USA Chemical resistanceAugust 01, 2014Page 1 of 3Acetic acid 10 % 2 years no change Ammonia 10 % 2 years no change Ammonia 36 % 1.5 years no change Antifrogen L 50 % 1 year no change Antifrogen N 50 %1 year no change Benzol 1 month no change Bore oil 1 year no change Butanol6 months no change Carbon tetra chloride 1 yearno change Caustic soda solution 10 % 2 years no change Caustic soda solution50 %2 years no change Chlorine cleanser and disinfectant 1.5 years no change Citric acid2 years no change Deicer Safeway KF HOT 1 year no change Deicer Safeway SF (solid) 1 year no change Deicer Safewing MP II 1951 1 yearno change Dichromatic potassium 10 % 1 year no change Diesel2 years no change Engine oil SAE 20 1 year no change Ethanol 1 year no change Ethyleneglycole 1 yearno change Formaldehyde 37 % 6 months no change Formic acid 5 % 2 years no change Formic acid 10 %1.5 years no change Glycerol 1 year no change Glysantin 1 yearno change Hydrochloric acid concentrated1 week no change Hydrochloric acid 10 %2 years no change Hydrochloric acid 25 % 1.5 yearsno change Hydrofluoric acid 1 % 1 day no change Hydrogen peroxide 3 % 1 year no change Hydrogen peroxide10 %1 yearfadedLactic acid10 % 1 week no changeMethanol 1 week no changeMethyl tert-butyl ether (MTBE)100% 6 months softeningNitric acid10 % 1.5 years no changeNitric acid25 % 1 year no changeOxalic acid 5 % 6 months no changePalm oil at 90° C7 days no changePetrol 2 years no changePetroleum 1 year no changePhosphoric acid10 % 2 years no changePhosphoric acid50 % 2 years no changePotassium hydroxide10 % 1 year no changePotassium hydroxide25 % 1 year no changePotassium hydroxide50 % 1 year no changePropanol 1 year no changeSea water 2 years no changeSodium acetate10 % 1 year no changeSodium carbonate20 % 1 year no changeSodium hypochlorite (15 % Cl2)10 weeks no changeSodium chloride 2 % 1 year no changeSodium chloride20 % 1 year no changeSodium formiate10 % 1 year no changeSuds 1 % 1 year no changeSulphuric acid 2 % 2 years no changeSulphuric acid20 % 2 years no changeSulphuric acid50 % 2 years no changeTartaric acid 5 % 1 year no changeToluol 1 year no changeTurpentine oil 1 year no changeUrea10 % 1 year no changeUrine 1 year no changeXylol 1 year no change 20, Culvert Street T+1 855-294-8934Nashville, TN 37210F+1 615-564-4181USA Chemical resistance August 01, 2014Page 2 of 3Our printed literature and technical information Sheets as well as our advisory services are offered to facilitate andsupport decision-making processes. All specifications provided reflect the state of our knowledge at the time of print. Anytechnical data and measured values supplied have been tested for compliance with current applicable standards, ifavailable. The information provided is not legally binding upon the party supplying such information.20, Culvert Street T+1 855-294-8934Nashville, TN 37210F+1 615-564-4181USA Chemical resistance August 01, 2014Page 3 of 3。
材料腐蚀与防护英文介绍范文

材料腐蚀与防护英文介绍范文Materials Corrosion and Protection.Materials corrosion is a natural process that occurs when metals or other materials are exposed to the environment. This process can lead to the degradation of the material, resulting in its failure. Corrosion can be caused by a variety of factors, including exposure to moisture, oxygen, acids, and bases.The rate of corrosion can be affected by a number of factors, including the type of material, the environment in which it is exposed, and the presence of protective coatings. Some materials are more resistant to corrosion than others. For example, stainless steel is more resistant to corrosion than carbon steel. The environment in which a material is exposed can also affect the rate of corrosion. For example, materials that are exposed to salt water are more likely to corrode than materials that are exposed to fresh water. The presence of protective coatings can alsoslow down the rate of corrosion. These coatings can act as a barrier between the material and the environment, preventing the material from coming into contact with the corrosive agents.Corrosion can have a significant impact on the performance and lifespan of materials. For example, corrosion can lead to the failure of metal components in bridges, buildings, and other structures. It can also lead to the failure of pipes, tanks, and other vessels that are used to store or transport fluids.There are a number of methods that can be used to protect materials from corrosion. These methods include:Using corrosion-resistant materials: Some materials are more resistant to corrosion than others. For example, stainless steel is more resistant to corrosion than carbon steel.Applying protective coatings: Protective coatings can act as a barrier between the material and the environment,preventing the material from coming into contact with the corrosive agents.Using cathodic protection: Cathodic protection is a process that uses an external electrical current to protect a metal from corrosion.Using sacrificial anodes: Sacrificial anodes are made of a metal that is more reactive than the metal that is being protected. The sacrificial anode corrodes instead of the protected metal.The best method of corrosion protection will depend on the specific application. It is important to consider the type of material, the environment in which it will be exposed, and the desired level of protection.Corrosion and the Environment.The environment can have a significant impact on the rate of corrosion. Some environments are more corrosive than others. For example, materials that are exposed tosalt water are more likely to corrode than materials that are exposed to fresh water. The presence of pollutants in the environment can also increase the rate of corrosion.The following are some of the factors that can affect the corrosiveness of the environment:Temperature: The rate of corrosion generally increases with increasing temperature.Humidity: The rate of corrosion generally increases with increasing humidity.Salinity: The rate of corrosion generally increases with increasing salinity.Acidity: The rate of corrosion generally increases with increasing acidity.Pollutants: The presence of pollutants in the environment can increase the rate of corrosion.Corrosion Protection.There are a number of methods that can be used to protect materials from corrosion. These methods include:Using corrosion-resistant materials: Some materials are more resistant to corrosion than others. For example, stainless steel is more resistant to corrosion than carbon steel.Applying protective coatings: Protective coatings can act as a barrier between the material and the environment, preventing the material from coming into contact with the corrosive agents.Using cathodic protection: Cathodic protection is a process that uses an external electrical current to protect a metal from corrosion.Using sacrificial anodes: Sacrificial anodes are made of a metal that is more reactive than the metal that is being protected. The sacrificial anode corrodes instead ofthe protected metal.The best method of corrosion protection will depend on the specific application. It is important to consider the type of material, the environment in which it will be exposed, and the desired level of protection.Conclusion.Corrosion is a natural process that can have a significant impact on the performance and lifespan of materials. However, there are a number of methods that can be used to protect materials from corrosion. By understanding the factors that affect corrosion, and by using the appropriate protective measures, it is possible to extend the life of materials and reduce the risk of failure.。
材料腐蚀与防护英文介绍范文

材料腐蚀与防护英文介绍范文英文回答:Materials Corrosion and Protection.Corrosion is the deterioration of materials due to chemical reactions with their environment. It is a common problem that affects a wide range of materials, including metals, ceramics, and polymers. Corrosion can lead to a variety of problems, including:Loss of strength.Reduced performance.Increased safety hazards.Environmental damage.There are a number of different ways to protectmaterials from corrosion, including:Using corrosion-resistant materials.Applying protective coatings.Using cathodic protection.Using sacrificial anodes.The best method of corrosion protection depends on the specific material and environment involved.Materials:The type of material used is a major factor in determining its susceptibility to corrosion. Some materials, such as stainless steel and aluminum, are naturallyresistant to corrosion. Other materials, such as iron and steel, are more susceptible to corrosion.Environment:The environment in which a material is used also playsa role in its susceptibility to corrosion. Factors such as temperature, humidity, and the presence of corrosive chemicals can all affect the rate of corrosion.Protective Coatings:Protective coatings can be applied to materials to protect them from corrosion. These coatings can be made ofa variety of materials, including paint, plastic, and metal. Protective coatings can provide a barrier between the material and the corrosive environment, and they can also help to slow down the rate of corrosion.Cathodic Protection:Cathodic protection is a technique that is used to protect metals from corrosion. This technique involves connecting the metal to a more reactive metal, which actsas a sacrificial anode. The sacrificial anode corrodes instead of the metal, thereby protecting it from damage.Sacrificial Anodes:Sacrificial anodes are used to protect metals from corrosion. These anodes are made of a more reactive metal than the metal that they are protecting. The sacrificial anode corrodes instead of the metal, thereby protecting it from damage.中文回答:材料腐蚀与防护。
TL245-2011中英互译
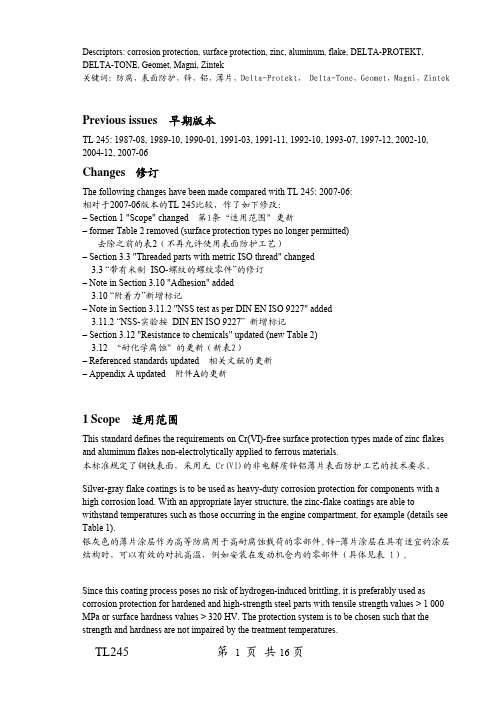
Descriptors: corrosion protection, surface protection, zinc, aluminum, flake, DELTA-PROTEKT, DELTA-TONE, Geomet, Magni, Zintek关键词:防腐,表面防护,锌,铝,薄片,Delta-Protekt, Delta-Tone,Geomet,Magni,ZintekPrevious issues 早期版本TL 245: 1987-08, 1989-10, 1990-01, 1991-03, 1991-11, 1992-10, 1993-07, 1997-12, 2002-10, 2004-12, 2007-06Changes 修订The following changes have been made compared with TL 245: 2007-06:相对于2007-06版本的TL 245比较,作了如下修改:– Section 1 "Scope" changed 第1条“适用范围”更新– former Table 2 removed (surface protection types no longer permitted)去除之前的表2(不再允许使用表面防护工艺)– Section 3.3 "Threaded parts with metric ISO thread" changed3.3 “带有米制 ISO-螺纹的螺纹零件”的修订– Note in Section 3.10 "Adhesion" added3.10 “附着力”新增标记– Note in Section 3.11.2 "NSS test as per DIN EN ISO 9227" added3.11.2 “NSS-实验按DIN EN ISO 9227” 新增标记– Section 3.12 "Resistance to chemicals" updated (new Table 2)3.12 “耐化学腐蚀”的更新(新表2)– Referenced standards updated 相关文献的更新– Appendix A updated 附件A的更新1 Scope 适用范围This standard defines the requirements on Cr(VI)-free surface protection types made of zinc flakes and aluminum flakes non-electrolytically applied to ferrous materials.本标准规定了钢铁表面,采用无 Cr(VI)的非电解质锌铝薄片表面防护工艺的技术要求。
中英文油漆规范

• Gloss finishing paints are of machine finish grade having high adhesion and high resistance to solvents, mineral oils, cutting oils, detergents, chipping and impact.
SECTION 09900
PAINTING 油漆
Part 1
GENERAL
概述
1.01 1.02
RELATED DOCUMENTS 相关文件
A. Provisions established within the Conditions of the Contract and Division 1 - General Requirements, all Sections of the Specifications, and the Contract Drawings are collectively applicable to this Section. 合同要求,第一篇普通要求和本规范的所有章节的合同图纸
当无特别要求,应按下列要求进行
• Protect all metal work, plant, equipment, pipelines, ducts, ancillaries, brackets and supports against corrosion and oxidisation.
防护所有金属、设备、管线、风管、支架,以防止腐蚀和氧化
地下防腐膜
• Cold applied, non woven synthetic fibre fabric, petroleum based anti corrosion tape 冷施工、非织合成纤维,石油基的防腐带
基于电化学对汽车用有机防腐蚀涂层的性能评价

范围为30~160弋。采用热重分析法对样品进行热重 分析,测试条件:在氮气的氛围下,升温速率10 P/rniii,升温范围为30〜600弋。采用透反偏光显微镜 对防腐蚀涂层的微晶结构进行分析。 1.3.2耐液体介质浸泡试验
将喷涂好的钢板置于腐蚀介质中,并观察有无起 泡、脱落及生锈等情况。根据GB/T 9274"色漆和清漆 耐液体介质的测定”,选用质量分数为10%的H2SO4和 10% NaOH溶液作为浸泡介质。 1.3.3 湿热试验
采用CHI660E电化学工作站测试极化曲线和交流 阻抗谱,以3.5%NaCl溶液为电解质,甘汞电极为参比 电极,钳电极为对电极,涂膜试片为工作电极。待开路 电位稳定后进行测试,测试条件为:扫描速率10 mV/s, 扫描范围为 1.0x(10-2~105) Hzo
2结果与讨论
2.1高低温稳定性分析 防腐蚀涂层在高温时容易被熔化,低温时容易产
Reddy等⑸以石蜡为原料,加入防流挂剂、增黏剂 及防锈剂等助剂,制备出一种附着力强的防腐蚀涂层; 连玉双⑹以石蜡与合成蜡复配作为基础成膜物质,将 改性剂、增黏剂、防锈剂添加到基础成膜物质中,制备
出汽车底盘防锈涂层。王晓蕾等⑺以氧化蜡为基础物 质,选用复合乳化剂进行乳化,在85-90 °C乳化40 min 后得到性能稳定的乳化蜡乳液,可制备防锈效果良好 的水性涂层;潘良等⑻以水性树脂和聚乙烯蜡为基础 原料,添加消泡剂、流平剂、润湿剂和抗盐雾剂等助剂, 得到快干型的水性防护涂层;张本雷⑼以聚乙烯 、石蜡 和丙烯酸树脂为原料制备了黏性小、性能稳定的纳米 颗粒水基涂料。
表2耐液体介质浸泡试验结果
10%H2S04 浸泡天数--------------------------
Vol.54 No.6 Jun. 2021
奈尔钢铁锈防腐防蚀喷漆系列-21种标准颜色说明书

"C o m p l e t e A i r C o n t r o l a n d D i s t r i b u t i o n S o l u t i o n s."w w w.n a i l o r.c omspecifications and performance requirements for color retention, chalk resistance, gloss retention, erosion,corrosion and chemical resistance as well as dry film thickness and hardness. Our state-of-the-art powder coat system provides an environment friendly finishing solution with more uniform coverage and coating thickness. The result is an exceptional finish that better resists scratching, fading and general wear. Additional liquid coat facilities for special requirements complete our ability to provide unmatched beauty and durability for any application.Custom color matching is also available upon request. Contact your local Nailor representative.Houston Las Vegas Toronto Calgary Thetford, U.K."C o m p l e t e A i r C o n t r o l a n d D i s t r i b u t i o n S o l u t i o n s."w w w.n a i l o r.c o m Fluoropolymer Powder CoatAAMA 2605-Superior Finish(AKA: Powdura ®5000,Coraflon ®Powder,Interpon ®D3000-Fluoromax)A vailable Finishes"Ultimate" − A next generation hyper durable powder coating, based on FEVE fluoropolymer resins and ceramic pigmentation that the industry has acknowledged as the foundation for superior performance coatings.They provide a hard surface that is resistant to scratching and scuffing,with superior color and gloss retention, when applied to a variety ofexterior architectural applications. This technology represents the “ultimate” in environmentally friendly finishes, with Zero-VOC emissions.A new alternative to traditional 70% Kynar 500®/ Hylar 500®PVDF fluoropolymer liquid coatings.10 years (Consult Nailor for availability of extended warranty)High Performance Powder Coat AAMA 2604 − High Performance Finish (AKA: Powdura ®4000,Envirocron ®Ultra DurablePowder, Dynadure ™400,Interpon ®D2000)"Better" − A high performance polyester powder coating, based on “super durable” resins that utilize infrared reflective pigments, which provides excellent resistance to outdoor weathering. A harder and more environmentally friendly coating than other liquid paint counterparts and with Zero-VOC emissions.A good alternative to 50% Kynar 500®/ Hylar 5000®liquid coatings. 5 yearsDurable Powder Coat AAMA 2603 −Pigmented Organic Coatings (AKA: Powdura ®3000,Envirocron ®Durable Powder,Dynadure ™300, Interpon ®D1000)"Good" − A durable powder coat based on thermosetting polyester resintechnology.Provides a good economical combination of physical and chemical resistance properties. Environmentally superior to liquid spray paints and Zero – VOC emissions. 1 year Clear Anodize 215-R1AA-M10C22A41(0.7 mil. min.)Architectural Class I. Clear, colorless and hard oxide aluminum coating that resists weathering and chemical attack. Recommended for severely corrosive and abrasive atmospheric exposure. 5 years Color AnodizeAA-M10C22A44(0.7 mil. min.)Architectural Class I. "Two-step" aluminum coating process. Following a standard anodizing procedure, a second electrolytic process deposits colored metallic pigments which penetrate the aluminum oxide pores,producing a corrosion resistant, colorfast finish. Available in light,medium, dark bronze and black.5 years Prime Coat Prime coat provides a stable base for painting of louvers in the field.Surface pretreatment includes degreasing and a chemical cleaning before an epoxy prime coat is applied. Finish coat should be field applied as soon as possible for best adhesion, after a thorough cleaning for dust etc.that can contaminate the final finish and cause premature flaking or peeling.N/AClear Anodize 204-R1AA-M10C22A31(0.4 − 0.7 mil.)Architectural Class II. Clear, colorless and hard oxide aluminum coating that resists weathering and chemical attack. Recommended for normal weather exposure. 1 year Paint finish warranties are not applicable to steel products.Powdura ®is a registered trademark of The Sherwin-Williams Company.Coraflon ®and Envirocron ®are registered trademarks of PPG Industries Ohio, Inc.Interpon ®is a registered trademark of Akzo Nobel Powder Coatings Ltd.Kynar 500®is a registered trademark of Arkema, Inc.Hylar 5000®is a registered trademark of Solvay Solexis, Inc.11/13/09。
热镀锌层钒酸盐转化膜的成膜机理

热镀锌层钒酸盐转化膜的成膜机理张子月;俞钢强;江社明;高志强;刘昕【摘要】采用扫描电镜观察不同成分的钒酸盐转化膜在形核、生长过程中的微观形貌;采用化学法对转化膜质量进行了测量;采用XPS对转化膜的化合物成分组成进行了分析.结果表明:钒酸盐转化膜主要是由低价钒化合物沉积、含锌和钒等盐类的晶体长大而组成的转化膜,转化膜质量在一定范围内随偏钒酸钠含量的增加而增加,钒酸盐钝化用于热镀锌层表面处理具备很大的潜力.【期刊名称】《腐蚀与防护》【年(卷),期】2019(040)005【总页数】5页(P370-373,378)【关键词】热镀锌;后处理;钒酸盐转化膜【作者】张子月;俞钢强;江社明;高志强;刘昕【作者单位】钢铁研究总院先进金属材料涂镀国家工程实验室,北京100081;钢铁研究总院先进金属材料涂镀国家工程实验室,北京100081;钢铁研究总院先进金属材料涂镀国家工程实验室,北京100081;钢铁研究总院先进金属材料涂镀国家工程实验室,北京100081;钢铁研究总院先进金属材料涂镀国家工程实验室,北京100081【正文语种】中文【中图分类】TG174.4“钒酸盐转化处理”是一种可替代传统转化处理的环境友好型处理方法,有关钒酸盐对铝和镁的抑制腐蚀作用已有大量研究报道[1-5]。
研究发现,钒酸盐转化膜呈层状结构,较薄(不超过100Å)的富集钒的化合物的底层(位于金属/膜层界面)具有较好的疏水性,可以起到关键的防腐蚀作用,且表层(位于金属表面)比较厚,能够弥补膜层的缺陷,从而可以得到无裂纹且致密的转化膜[6-18]。
钒酸盐转化膜优异的耐蚀性依赖五价钒的氧化能力,它可以在腐蚀环境中对氧的还原反应起到抑制效果[8,19-25]。
钒酸盐在许多方面具有与铬酸盐相似的特性。
在针对钒酸盐转化处理的研究中,人们大都采用五价钒作为研究对象,然而,在酸性条件下,钒酸根离子(V-Ⅴ)在获得质子的同时会因为脱水而缩合,得到缩合多钒酸盐[7,21]。
聚苯胺_新一代环境友好防腐材料

第 30 卷 第 8 期 2011 年 8 月
中国材料进展
MATERIALS CHINA
Vol. 30 No. 8 Aug. 2011
特约专栏
聚 苯 胺 ——— 新 一 代 环 境 友 好 防 腐 材 料
李应平1,2 ,王献红1 ,李 季1 ,王佛松1
( 1. 中国科学院长春应用化学研究所 先进生态环境材料国家重点实验室,吉林 长春 130022) ( 2. 中国科学院研究生院,北京 100039)
第8 期
李应平等: 聚苯胺———新一代环境友好防腐材料
19
要指出的是,聚苯胺的电化学沉积电位一般要高于金属 基底的钝化电位。因此在电化学沉积聚苯胺后,电极表 面往往会形成一层钝化层,这层钝化层是保护金属不受 腐蚀的关 键,而 聚 苯 胺 只 是 起 到 了 稳 定 钝 化 层 存 在 的 作用。
Wessling[12] 首 先 采 用 化 学 合 成 的 聚 苯 胺 来 涂 覆 金 属 电极,他将各种金属电极浸入聚苯胺分散液中,从而获 得聚苯胺涂覆的金属电极。与电化学沉积聚苯胺的方法 相比,这种方 法 在 引 入 聚 苯 胺 涂 层 的 同 时 不 会 在 聚 苯 胺 /金属界面形成钝化层,因此更能准确地评估聚苯胺 的防腐机理。在浸泡期间,聚苯胺涂层能使金属表面形 成钝化层,钝化层的形成可以被描述为: 纯聚苯胺涂层 或含聚苯胺的底漆在 Fe 表面涂覆后与 Fe 发生反应,使 Fe 表面生成由 Fe3 O4 和 γ-Fe2 O3 组成的钝化层,钝化层 的形成总是伴随着电位显著地移向高电位,并且使极化 电阻增高和腐蚀电流减小。Wessling 认为聚苯胺可逆的 氧化 - 还原 特 性 是 其 发 挥 钝 化 作 用 的 重 要 保 证[13],腐 蚀介质中的溶解 O 能将被 Fe 还原的聚苯胺重新氧化生 成氧化态聚苯胺,有利于形成致密的钝化层。
生活用水塑料管道德国标准号

DIN 16963-3-1980
DIN 16963-4-1988
DIN 16963-5-1999
DIN 16963-6-1989
DIN 16963-7-1989
高密度聚乙烯压力管道用管道 连接组件和管道配件.第 7 部 分:电阻焊接配件尺寸
DIN 16963-8-1980
Pipe Joints and Elements for High Density 1 型和 2 型高密度聚乙烯压力管 Polyethylene (HDPE) Pressure Pipelines, Types 道用管子接头与零件.承插焊接 1 and 2; Injection Moulded Elbows for 用注塑弯管.尺寸 Socket-welding, Dimensions Pipe Joints and Elements for High Density 1 型和 2 型高密度聚乙烯压力管 Polyethylene (HDPE) Pressure Pipelines, Types 道用管子接头与零件.承插焊接 1 and 2; Injection Moulded Tee Pieces for 用注塑三通管件.尺寸 Socket-welding, Dimensions 硬聚氯乙烯(PVC)制管子和管道 零件粘接用胶粘剂.一般质量要 求和检验 加热系统管道的标示颜色 持续工作温度不超过 50℃的地 下和水下管道外部有机防腐涂 层.带材和可收缩材料 Adhesives for Bonding Pipes and Pipe System Elements of Rigid PVC; General Quality Requirements and Testings Identification Colour Code for Heating System Pipelines External organic coatings for the corrosion protection of buried and immersed pipelines for continuous operating temperatures up to 50 °C
高速电弧喷涂FECRAL涂层和NICR涂层组织及性能研究

中文摘要中文摘要采用高速电弧喷涂技术(HVAs),在结构材料上喷涂FeCrAl涂层和NiCr涂层,使其具有优异的高温耐蚀性能和良好的耐磨性能,可以应用于火电厂锅炉水冷壁的高温防腐防磨领域,应用前景广阔。
本文采用扫描电子显微镜(SEM)、X.射线衍射仪(XRD)、能谱仪(EDS)、光学显微镜等现代分析手段研究了高速电弧喷涂FeCrAI层和NiCr层的微观结构,通过一系列实验研究了涂层的结合强度、抗高温腐蚀性能、耐磨损性能、抗热震性能、孔隙率,并研究了涂层的力学性能如涂层的弹性模量。
这些研究成果为这种高速电弧喷涂层的大规模工业应用奠定了理论基础。
本研究获得的主要成果如下:采用SEM和XRD分析了高速电弧喷涂FeCrAI涂层和NiCr涂层的微观结构。
涂层的显微组织呈典型的层状结构特征,涂层组织致密,无粗大孔隙,在扁平颗粒之间有很薄的氧化物膜和少量气孔。
FeCrAI涂层的主要相是铁基固溶体和少量Fe203;NiCr涂层的主要相是镍基固溶体、cr203和NiCr204。
研究了高速电弧喷涂FeCrAl层的结合强度,提出FeCrAl涂层与NiAl粘结底层之间的结合强度大于底层与基体间的结合强度,并且还提出在对基体表面进行了喷砂处理后,可以不用预制NiAl底层,这样对FeCrAl涂层结合强度影响很小。
对高速电弧喷涂FeCrAl层和NiCr层的抗高温腐蚀性能进行了研究,并采用XRD、SEM等手段对涂层的腐蚀机理进行了深入研究,并研究了FeCrAl层和NiCr层的孔隙率。
研究表明NiCr涂层的抗高温腐蚀性能最好,FeCrAl涂层次之,但比20#钢的耐腐蚀性能要好的多。
研究认为NiCr涂层中优先形成Cr203或尖晶石型氧化物是其具有优异的抗高温腐蚀性能的主要原因,FeCrAI涂层低温热腐蚀形成疏松的Fe203是其抗腐蚀性能稍差的主要原因。
另外,涂层的孔隙率也是不可忽视的一方面原因。
NiCr涂层和FeCrAl涂层孔隙率明显比普通电弧喷涂层降低,几乎可以和等离子喷涂层相媲美。
碱式硫酸锌微米片增强氟碳涂层的腐蚀防护性能

碱式硫酸锌微米片增强氟碳涂层的腐蚀防护性能WU Wen-dong;WANG Li-da;SUN Wen;WANG Sui-lin;LIU Gui-chang【摘要】以七水合硫酸锌(ZnSO4?7H2O)和六亚甲基四胺(HMT)为原料,采用化学浴沉积法合成了碱式硫酸锌(ZSH)微米片,并将其作为填料嵌入氟碳(FC)清漆中.采用傅里叶变换红外光谱仪、场发射扫描电镜、能谱仪和X射线衍射仪分析了ZSH微米片的健结构、形貌和组分.对比了不同ZSH的质量分数时在紫铜上所得FC–ZSH 复合涂层的剖面结构、ZSH分布情况及腐蚀防护性能.结果表明,所得ZSH呈典型的六方片状晶体结构,表面光滑、无缺陷.ZSH在FC–ZSH 复合涂层中均匀分布,令涂层的腐蚀防护性能增强,尤以ZSH质量分数为10%时为最佳.%Micron zinc sulfate hydroxide hydrate (ZSH) flakes were synthesized by chemical bath deposition with ZnSO4?7H2O and hexamethylenetetramine (HMT), and then embedded into fluorocarbon (FC) coating as fillers. The bond structure, morphology, and elemental composition of micron ZSH flakes were analyzed using Fourier-transform infrared spectrometer, field-emission scanning electron microscope, and X-ray diffractometer. The cross-sectional structure, distribution of ZSH and anticorrosion property of FC–ZSH composite coatings with different mass concentrations of ZSH on pure copper were compared. The results showed that the crystalline ZSH flake was typically hexagonal shape with a smooth and defect-free surface, and could be distributed uniformly in the FC coating, improving its anticorrosion property, especially when the mass fraction of ZSH was 10%.【期刊名称】《电镀与涂饰》【年(卷),期】2019(038)012【总页数】6页(P585-590)【关键词】碱式硫酸锌;微米片;化学浴沉积;氟碳涂层;紫铜;腐蚀防护【作者】WU Wen-dong;WANG Li-da;SUN Wen;WANG Sui-lin;LIU Gui-chang【作者单位】Department of Chemical Engineering, Dalian University of Technology, Dalian 116024, China;Department of Chemical Engineering, Dalian University of Technology, Dalian 116024, China;Department of Chemical Engineering, Dalian University of Technology, Dalian 116024, China;;Department of Chemical Engineering, Dalian University of Technology, Dalian 116024, China【正文语种】中文【中图分类】TQ630.7聚合物涂层在金属基材上的附着力强,并具有优异的耐化学品性、阻隔性和高低温耐久性,已被广泛应用于金属腐蚀防护领域[1]。
船舶涂装整套流程

船舶涂装整套流程Painting a ship involves a comprehensive process that begins with surface preparation. This involves cleaning the hull to remove any dirt, rust, or old paint. The next step is to apply a primer to protect the metal from corrosion and provide a smooth surface for the topcoat. The topcoat is then applied in multiple layers to achieve the desired color and finish. Finally, the ship is inspected to ensure that the paint job is of high quality and meets regulatory standards.船舶涂装涉及一个全面的过程,从表面处理开始。
这包括清洁船体,去除任何污垢,锈迹或旧漆。
接下来是涂抹底漆,以保护金属免受腐蚀,并为面漆提供光滑表面。
接着,面漆被涂抹在多层中,以达到所需的颜色和光泽。
最后,对船只进行检查,确保涂装质量高,符合监管标准。
The surface preparation stage is crucial as it determines the adhesion and longevity of the paint job. Any contaminants left on the hull can compromise the integrity of the coatings and result in premature failure. Therefore, thorough cleaning and preparation are essential to ensure a durable and flawless finish. In addition, proper surfacepreparation can also improve the overall efficiency and effectiveness of the painting process.表面处理阶段至关重要,因为它决定了涂装的附着力和寿命。
NACE SP 0108-2008 标准规范—使用防护漆对海上平台结构进行防腐蚀控制

Standard PracticeCorrosion Control of Offshore Structuresby Protective CoatingsThis NACE International standard represents a consensus of those individual members who have reviewed this document, its scope, and provisions. Its acceptance does not in any respect preclude anyone, whether he or she has adopted the standard or not, from manufacturing, marketing, purchasing, or using products, processes, or procedures not in conformance with this standard. Nothing contained in this NACE International standard is to be construed as granting any right, by implication or otherwise, to manufacture, sell, or use in connection with any method, apparatus, or product covered by Letters Patent, or as indemnifying or protecting anyone against liability for infringement of Letters Patent. This standard represents minimum requirements and should in no way be interpreted as a restriction on the use of better procedures or materials. Neither is this standard intended to apply in all cases relating to the subject. Unpredictable circumstances may negate the usefulness of this standard in specific instances. NACE International assumes no responsibility for the interpretation or use of this standard by other parties and accepts responsibility for only those official NACE International interpretations issued by NACE International in accordance with its governing procedures and policies which preclude the issuance of interpretations by individual volunteers.Users of this NACE International standard are responsible for reviewing appropriate health, safety, environmental, and regulatory documents and for determining their applicability in relation to this standard prior to its use. This NACE International standard may not necessarily address all potential health and safety problems or environmental hazards associated with the use of materials, equipment, and/or operations detailed or referred to within this standard. Users of this NACE International standard are also responsible for establishing appropriate health, safety, and environmental protection practices, in consultation with appropriate regulatory authorities if necessary, to achieve compliance with any existing applicable regulatory requirements prior to the use of this standard.CAUTIONARY NOTICE: NACE International standards are subject to periodic review, and may be revised or withdrawn at any time in accordance with NACE technical committee procedures. NACE International requires that action be taken to reaffirm, revise, or withdraw this standard no later than five years from the date of initial publication. The user is cautioned to obtain the latest edition. Purchasers of NACE International standards may receive current information on all standards and other NACE International publications by contacting the NACE International FirstService Department, 1440 South Creek Drive, Houston, Texas 77084-4906 (telephone +1 281- 228-6200).NACE Standard TM0108-2008 Item No. 21252 NACE SP0108-2008Item no. 21126Approved 2008-3-15NACE International1440 South Creek DriveHouston, Texas 77084-4906 +1 281-228-6200--`,,```,,,,````-`-`,,`,,`,`,,`---SP0108-2008________________________________________________________________________ForewordOffshore structures represent large capital investments and are being placed worldwide.Moreover, more and more offshore structures are being placed in deeper waters and, therefore,have become larger, more complex, and more expensive. Control of corrosion on offshorestructures is necessary to sustain oil and gas production, provide safe working and living areas,and avoid potential harm to the environment. For this standard, offshore structures includesmetallic offshore structures such as fixed-leg platforms, tension-leg platforms (TLPs),semisubmersibles, spar platforms, and floating production storage and offloading vessels(FPSOs).This NACE International standard is intended for use by facility owners’ corrosion controlpersonnel, coating applicators, and coating manufacturers. It covers coating materials, coatingtest protocol and acceptance criteria, surface preparation, coating application, quality assuranceand control, and repair methods. It also covers generic protective coating systems, flangecorrosion control, fastener coatings, pipe support corrosion control, and stainless steel (SS) tubingcorrosion control. The purpose is to facilitate more effective corrosion protection of offshorestructures by presenting reliable information and providing guidelines for coating manufacturers todevelop more durable products.This standard replaces a portion of NACE Standard RP0176.1 RP0176 was originally issued in1976 and revised in 1983 by Task Group (TG) T-1-2 on North Sea Corrosion Problems. It was --`,,```,,,,````-`-`,,`,,`,`,,`---revised in 1994 by TG T-1-5, and in 2003 by TG 170 on Offshore Steel Platforms—CorrosionControl: Review of NACE Standard RP0176, which is administered by Specific Technology Group(STG) 30 on Oil and Gas Production: Cathodic Protection. All editions of RP0176 prior to 2007addressed two aspects of corrosion control of steel fixed offshore structures associated withpetroleum production: cathodic protection (CP) and protective coatings. In 2007 it was decided toaddress these two aspects in separate NACE standards. Therefore, SP01762 was issued in 2007by TG 170 and STG 30 to address the CP aspects. TG 313—Offshore Platforms: Coatings forCorrosion Control of Steel was formed to address the protective coatings aspects from RP0176and provide expanded information. TG 313 is administered by STG 02—Coatings and Linings,Protective: Atmospheric. This standard is issued by NACE under the auspices of STG 02.In NACE standards, the terms shall, must, should, and may are used in accordance with thedefinitions of these terms in the NACE Publications Style Manual. The terms shall and must are usedto state a requirement, and are considered mandatory. The term should is used to state somethinggood and is recommended, but is not considered mandatory. The term may is used to statesomething considered optional.________________________________________________________________________SP0108-2008________________________________________________________________________NACE InternationalStandard PracticeCorrosion Control of Offshore Structuresby Protective CoatingsContents1. General (1)2. Definitions (1)3. Protective Coating Systems (2)4. Typical Generic Protective Coating Systems (5)5. Qualification Testing of Coating Systems (13)6. Surface Preparation (19)7. Coating Materials and Application (22)8. Quality Assurance and Control (23)9. Coating Repair (25)10. Flange Corrosion Control (26)11. Fastener Coatings (26)12. Pipe Support Corrosion Control (27)13. Corrosion Control of Small-Bore Stainless Steel Tubing (27)14. Health, Safety, and Environment (28)References (28)TABLESTable 1. Maximum Metal Content in the Dry Coating Film (4)Table 2. Routine Batch Testing Report (5)Table 3A. Typical Atmospheric Zone New Construction Coating Systems on Carbon Steels (6)Table 3B. Typical Atmospheric Zone Maintenance Coating Systems on Carbon Steels .. 8Table 4: Typical Atmospheric Zone Coating Systems on Stainless Steels (New Construction and Maintenance) (9)Table 5: Typical Atmospheric Zone Coating Systems for Nonferrous Metals (New Construction and Maintenance) (10)Table 6A: Typical Splash Zone New Construction Coating Systems on Carbon Steels (11)Table 6B: Typical Splash Zone Maintenance Coating Systems on Carbon Steels (12)Table 7A: Typical Exterior Submerged Zone New Construction Coating Systems on Carbon Steels (12)Table 7B: Typical Exterior Submerged Zone Maintenance Coating Systems on Carbon Steels (12)Table 8A: Typical Ballast Water Tank New Construction Coating Systems on Carbon Steels (13)Table 8B: Typical Ballast Water Tank Maintenance Coating Systems on Carbon Steels 13Table 9: Fingerprinting of Coating Materials (14)Table 10: Test Protocol for Atmospheric Zone and Splash Zone Coating Systems (15)Table 11: Test Protocol for Ballast Water, Void, and Seawater Holding Tank and Exterior Submerged Zone Coating Systems (16)Table 12: Acceptance Criteria for Offshore Structure Coating Testing (17)Table 13: Surface Finish Grades (19)Table 14: Abrasive Specifications (20)Table 15: Maximum Total Soluble Chloride Ion Content (24)________________________________________________________________________ --` , , ` ` ` , , , , ` ` ` ` -` -` , , ` , , ` , ` , , ` ---SP0108-2008 ________________________________________________________________________Section 1: General1.1 This standard provides guidelines for establishing minimum requirements for the corrosion protective coatings on steel offshore structures associated with oil and gas production, and on the associated handling equipment. It covers coating materials, coating prequalification test methods and the associated acceptance criteria, surface preparation, coating application, quality assurance and control, and repair methods. It also covers generic protective coating systems, flange corrosion control, fastener coatings, pipe support corrosion control, and SS tubing corrosion control. Offshore structures include metallic offshore and coastal structures such as fixed-leg platforms, TLPs, semisubmersibles, spar platforms, and FPSOs.1.2 For this standard, corrosion on offshore structures is divided into four zones: atmospheric zone, splash zone, exterior submerged zone, and ballast water tank (internally immersed). The exterior submerged zone also includes subsea facilities, such as valves and manifolds. Each zone may use different protective coating systems.1.3 This standard does not include corrosion protective coatings for subsea pipelines, pipeline risers, internal portions of production tubing, drill pipes, and chemical tanks that may be in use on the offshore structure, but does include external protection of the chemical tanks on the offshore structure in the atmospheric zone.1.4. Passive fire protection (PFP) coatings and nickel-copper alloy (e.g., UNS(1) N04400 [Alloy 400]) splash zone sheathings also are excluded from this standard.________________________________________________________________________Section 2: DefinitionsAmine Blush: Greasy film on the surface of a coating caused by its amine or polyamide curing agent reacting with carbon dioxide (CO2) and water (H2O). (It can greatly interfere with intercoat adhesion.)Atmospheric Zone: The portion of a marine structure that extends upward from the splash zone and is exposed to sun, wind, water spray, and rain.Cathodic Disbondment: The destruction of adhesion between a coating and the coated surface caused by products of a cathodic reaction.Coat: One layer of a coating applied to a surface in a single, continuous application to form a uniform film when dry.Coating System: The complete number and types of coats applied to a substrate in a predetermined order.(Coating) Test Protocol: A written checklist of coating properties that are evaluated by standard test methods to qualify the coating for the intended service conditions. (It is often refined as more is learned about the behavior of the coating system.)Crater: A small, rounded depression in a coating generally resulting from foreign matter in or deposited on a wet coating film. Crevice Corrosion: Localized corrosion of a metal surface at, or immediately adjacent to, an area that is shielded from full exposure to the environment because of close proximity of the metal to the surface of another material.Dry Film Thickness (DFT): The thickness of a dried film, coating, or membrane.Edge Retention: The ratio of DFT of the entire multicoat coating system at peak to average DFT on both flat surfaces of a sharp angle bar; used as a measure of a coating’s ability to retain its film coverage over sharp corners.Epoxy: Type of resin formed by the reaction of aliphatic or aromatic polyols (like bisphenol) with epichlorohydrin and characterized by the presence of reactive oxirane end groups.Fingerprinting: Method of identifying a coating material through laboratory analyses of coating density, solids content, pigment content, etc. (Infrared [IR] spectroscopy is often used in the analyses.)Fish Eye: A small dimple or crater resembling a fish eye that forms in a wet applied coating.Hot-Dip Galvanized Coating: A coating of virtually pure zinc applied to steel by immersing it in a bath of molten zinc.___________________________(1) Unified Numbering System for Metals and Alloys (UNS). UNS numbers are listed in Metals & Alloys in the Unified Numbering System, latest edition (Warrendale, PA: SAE International [SAE]) and West Conshohocken, PA: ASTM International [ASTM]).--`,,```,,,,````-`-`,,`,,`,`,,`---SP0108-2008Holiday: A discontinuity in a protective coating that exposes unprotected surface to the environment.Inorganic Zinc-Rich Coating: Coating containing a metallic zinc pigment (typically 75 wt% or more in the dry film) in an inorganic vehicle.Mill Scale: The oxide layer formed during hot fabrication or heat treatment of metals.Mud Line: The ocean floor at the location of interest. Orange Peel: The dimpled appearance of a dried coating resembling the surface of an orange.Organic Zinc-Rich Coating: Coating containing a metallic zinc pigment (typically 75 wt% zinc or more in the dry film) in an organic resin.Pipeline: A conduit for carrying produced oil, water, and gas between offshore structures or between offshore structures and onshore processing facilities.Platform: An offshore structure used to accommodate oil and/or gas wells, related production equipment, pipelines, and/or living quarters.Pot Life: The elapsed time within which a coating can be effectively applied after all components of the coating have been thoroughly mixed.Prefabrication Primer: A thin and fast-drying coating that is applied to blast-cleaned steel to provide temporary protection during fabrication while still allowing welding and cutting.Primer (Prime Coat): A coating material intended to be applied as the first coat on an uncoated surface. The coating is specifically formulated to adhere to and protect the surface as well as to produce a suitable surface for subsequent coats.Resin: A general term used to designate any polymer, natural or synthetic, used as a binder for coating materials. Recoat Window: The time period during the drying and curing of a coating in which a subsequent coat can be applied successfully.Rust Creepage: The penetration of a coating and the spread of delamination or corrosion from a scribe or holiday in the film.Shelf Life: The maximum length of time packaged materials (e.g., coating materials) can be stored at specified conditions and remain in usable condition.Splash Zone: The portion of a marine structure that is intermittently wetted by waves, wind-blown water spray, and tidal action. Surfaces that are wetted only during major storms are not included.Stripe Coat: A coat applied only to edges or to welds on steel structures before a full coat is applied to the entire surface. The stripe coat is intended to give those areas sufficient film build to resist corrosion.Submerged Zone: The surface area of a marine structure that is always covered with water and extends downward from the splash zone and includes that portion of the structure below the mud line.Surface Profile: The irregular peak and valley profile on the surface of bare metal that results from abrasive blast cleaning or power tool cleaning.Thermoplastic: A material capable of being repeatedly softened by heat and hardened by cooling.Thermoset: A material that undergoes a chemical reaction from the action of heat and pressure, catalysts, and ultraviolet (UV) light, leading to a relatively infusible state.Thinner: A volatile solvent used to lower the viscosity of a coating material.Topcoat (Finish Coat): The final coat of a coating system.Wet Film Thickness (WFT): The thickness of a coating measured immediately after application before any solvent has evaporated or drying has taken place.Zinc-Rich Primer: A general term used for inorganic zinc-rich coatings and organic zinc-rich coatings used as a primer.________________________________________________________________________ Section 3: Protective Coating Systems3.1 GeneralBecause the cost of field-applied maintenance coatings is much higher than that of shop-applied coatings, only the coating systems that have passed the qualification tests shall be specified for both new construction and maintenance. In addition to good coating performance, a successful coating system also requires proper surface preparation, coating application, and quality assurance and quality control procedures.SP0108-20083.2 Liquid CoatingsLiquid coatings used on offshore structures are normally multilayer coating systems composed of primer, intermediate coat(s), and topcoat to avoid holidays and thin spots.3.2.1 Primers. The primer is the most critical coat ofthe coating system. Normally, primers have at leastone of three different corrosion protection mechanisms:barrier, sacrificial, and inhibitive.3.2.1.1 Barrier primers. For immersion service,the primer is normally the barrier-type epoxycoating without zinc or corrosion inhibitors. Flake-shaped pigments, such as aluminum flake, glassflake, or micaceous iron oxide flake, may be usedto increase its barrier resistance to water andoxygen.3.2.1.2 Zinc-rich primers. These primers areeither organic or inorganic zinc-rich coatings with ahigh loading of zinc dust. The minimum zinc dustcontent of the nonvolatile portion of the primershall be 80% by mass. The zinc dust shall complywith the requirements specified in ASTM(2) D 5203(Type II or III) or ISO(3) 3549.4 Because zinc reactsreadily with both acids and strong alkalis, zinc-richprimers must be overcoated with chemicallyresistant coatings when used offshore because ofexposure to alkaline drilling mud and acidic well-completion fluids. However, care must be taken toensure that the zinc-primed surface is clean priorto overcoating. Because of the porous nature ofthe film, freshwater washing or power scrubbingmay be required to remove contaminants.Inorganic zinc-rich primers, when damaged, arenormally repaired with an organic zinc-rich coating.Because zinc-rich coatings sacrifice themselvesgalvanically when exposed in the splash zone orwhen immersed, causing rapid breakdown orfailure, other coatings should be used in theseareas.3.2.1.3 Organic inhibitive primers. These coatingsinclude inhibiting pigments that generate eitheralkaline or ionic conditions to retard the corrosionof the base metal when in contact with moisture.Because these primers generally contain reactivepigments and are only part of a protective coatingsystem, they must be protected with overcoats toperform as effective environmental barriers.Organic inhibitive primers must conform to allapplicable regulations regarding toxicity, safety,and environmental standards. Coating specifiersshould note that some inhibitive pigments canshorten coating system service life in immersion orsplash zone conditions.3.2.2 Intermediate Coats and Topcoats. Primers usedfor offshore structures should be overcoated with intermediate coat(s) and a topcoat. These coatingsfunction as barriers, retarding and restricting the permeation of water vapor, oxygen, and active chemical ions. A topcoat may also provide addedabrasion, impact, UV light, and solvent resistance, aswell as an aesthetically pleasing finish. Generic characteristics of intermediate coats and topcoats include the following:3.2.2.1 Chemically Cured Thermoset Coatings.These materials are usually epoxies, epoxyphenolics, polyesters, or vinyl esters.3.2.2.2 Polyurethanes or Polysiloxanes. Thesematerials are used exclusively as a topcoat in theatmospheric zone to provide UV resistance. Ingeneral, polysiloxane provides better UVresistance than polyurethane.3.3 Thermal-Sprayed Aluminum Coatings3.3.1 Thermal-sprayed aluminum (TSA) coatings(either flame or arc sprayed) sealed with an organicsealer have been used in the atmospheric zone andsplash zone, particularly for high-temperature servicesuch as flare booms. NACE No. 2/SSPC(4)-SP 105 orNACE No. 1/SSPC-SP 56 surface cleanliness shall beused for surface preparation. Ninety-nine percent orhigher-purity aluminum or Al-5Mg alloy should be usedwith two or more spray passes used in the application.The sealer enhances service life and appearance.3.3.2 The sealer shall be thinned adequately topenetrate into the body of the TSA and seal the interconnected surface porosity. The sealer shouldhave a contrasting color to the TSA to aid visualinspection. The overlay of sealer should be less than38 µm (1.5 mil) on the TSA coating after application.The sealer materials shall be two-component epoxy foroperating temperatures less than or equal to 120°C(248°F) or silicone for operating temperatures greaterthan 120°C (248°F).3.3.3 All TSA coatings shall be applied in accordancewith NACE No. 12/AWS(5) C2.23M/SSPC-CS 23.00.7__________________________________________(2) ASTM International (ASTM), 100 Barr Harbor Dr., West Conshohocken, PA 19428-2959.(3) International Organization for Standardization (ISO), 1 ch. de la Voie-Creuse, Case postale 56, CH-1211 Geneva 20, Switzerland.(4) The Society for Protective Coatings (SSPC), 40 24th Street, 6th Floor, Pittsburgh, PA 15222-4656.(5) American Welding Society (AWS), 550 N.W. LeJeune Road, Miami, FL 33126.SP0108-20083.4 Hot-Dip Galvanized Coatings3.4.1 Hot-dip galvanized coatings are an effective method for protecting complex steel shapes that would be costly and difficult to coat by conventional means. Such shapes as gratings, handrails, stairs, meter houses, and equipment skids may be protected by hot-dip galvanized coatings.3.4.2 Hot-dip galvanized coatings, like other zinc-rich coatings, are subject to attack by acid and alkaline conditions, and should not be exposed to cement, drilling mud, or well-completion fluids.3.4.3 Because hot-dip galvanized coatings sacrifice themselves galvanically when exposed in the splash zone or when immersed, causing rapid breakdown or failure, other coatings should be used in these areas.3.4.4 Hot-dip galvanized coatings should be overcoated by primers and topcoats in applications requiring chemical and saltwater resistance. New hot-dip galvanized coatings should be uniformly roughened with a light abrasive blast in accordance with NACENo. 4/SSPC-SP 78or chemically etched with a phosphoric acid-based conversion coating. A preliminary solvent cleaning in accordance with SSPC-SP 19should be used to remove any preservative oils applied to the hot-dip galvanized coating. Epoxycoatings can be applied to weathered hot-dip galvanized coatings (typically greater than one year of outdoor exposure) following surface preparation by low-pressure water cleaning (LPWC) in accordance withNACE No. 5/SSPC-SP 12.103.4.5 All hot-dip galvanized coatings shall be appliedin accordance with ASTM A 123/A 123M 11and ASTMA 153/A 153M.123.5 Health, Safety, and Environmental Requirements for Coating MaterialsThe health, safety, and environmental requirements for coating materials shall be in full compliance with any local and/or national governmental regulations. The following regulations may not be applicable outside the United States. The coating systems shall contain no carcinogens (e.g., asbestos, coal tar, polychlorinated bisphenyl). Tributyltin (TBT) shall not be used as the biocide in antifouling coatings. The metal content of a pulverized dry coating film shall be determined in accordance with 40 CFR (Code of Federal Regulations) Part 261, Appendix II,Method 1311,13 or U.S. EPA (6) Publication SW-846.14The coating manufacturers shall provide written certification that the metals in the dry coating film do not exceed the maximum values listed in Table 1. These maximum valuesare the same as in MIL-PRF-23236C.15Table 1. Maximum Metal Content in the Dry Coating FilmMetal Maximum wt% Metal Maximum wt%Antimony 0.015 Mercury 0.0002 Arsenic 0.001 Molybdenum 0.35 Barium (excluding barite) 0.10 Nickel 0.02 Beryllium 0.0002 Selenium 0.001 Cadmium 0.0005 Silver 0.001 Chromium VI compounds 0.0005 Tantalum 0.10 Chromium or Chromium III compounds0.56 Thallium 0.007 Copper 0.01 Tungsten 0.10Lead 0.005 (A)Vanadium 0.01(A)If the source of the lead is the zinc dust used in the zinc-rich primer, the maximum lead content in the zinc dust must be agreed to by the facility owner and the coating manufacturer. Four types of zinc dust are used in zinc-rich primers and each type has a different lead content.3.6 Coatings for Stainless Steels and High Nickel-Chromium AlloysSSs susceptible to crevice corrosion and stress corrosion cracking in chloride-containing environments shall be coated unless otherwise specified by the facility owners.Coatings for SSs or high nickel-chromium alloys shall not contain more than 200 mg/kg leachable chloride inaccordance with ASTM C 871.16In general, epoxy resin itself does not contain more than 10 mg/kg leachable chloride. Such coating formulations shall not contain metallic zinc, because of the possibility of inducing liquid metal cracking.3.7 Routine Batch TestingRoutine batch testing shall be carried out by the coating manufacturers for all batches of coating delivered. The test report shall include at least the parameters listed in Table 2.___________________________(6)U.S. Environmental Protection Agency (EPA), Ariel Rios Building, 1200 Pennsylvania Ave. NW, Washington, DC 20460.--`,,```,,,,````-`-`,,`,,`,`,,`---SP0108-2008Table 2. Routine Batch Testing ReportCoating Name Batch number Manufacturing Date Test DateProperty Component Test Result Specification with Tolerance Test StandardDensityPart A and B, each componentXX ±0.05 g/cm 3ASTM D 147517Solids content by weightMixed Parts A and BXX ±3 wt%ASTM D 2369183.8 Random Batch TestingThe facility owner may randomly choose an 8-L (2-gal) sample of liquid coating (part A & B) delivered to the field and carry out a random batch testing in a third-party laboratory to verify the fingerprint in accordance with the test methods listed in Paragraph 5.2. If a sample fails tomeet the required specification, the unused coating material shall be quarantined and the facility owner should contact the coating manufacturer to reach a resolution. The facility owner may reject the entire lot, if the coatings have not been applied. The contractor should remove this coating from areas already coated and recoat with a coating that meets the specification.________________________________________________________________________Section 4: Typical Generic Protective Coating Systems4.1 GeneralSteel offshore structures are exposed to several different service environments or conditions, which require different coating systems for corrosion protection. For the majority of the coated surface areas, test protocols have been developed to compare the laboratory performance of the coating systems for atmospheric zone and splash zone (see Paragraph 5.3) and exterior submerged zone and ballast water tanks (see Paragraph 5.4). The coating systems that pass the acceptance criteria (see Paragraph 5.5) shall be selected for the specific service. For each service category, typical generic coating systems are listed in this section. Coating systems that are not included in the generic coating tables may be used if they pass the acceptance criteria in Paragraph 5.5.4.2 Identification of Generic Coating SystemsFor the purpose of easy communication and identification, each generic coating system in the tables that follow is assigned a system code. The system code consists of two letters followed by a hyphen and a number. Definitions of the letters used are as follows:C: Carbon steel M: Maintenance N: New constructionO: Other surfaces (e.g., nonferrous metals) S: Stainless steel4.3 Typical Atmospheric Zone Coatings4.3.1 GeneralThe selection of atmospheric zone coating systems shall also consider local weather conditions (e.g., ambient temperature and relative humidity [RH]) to ensure the coating systems cure within the specified time. For maintenance coating application, the pot life and recoat window shall also be considered.4.3.2 Typical Atmospheric Zone Coating Systems on Carbon SteelsTypical atmospheric zone coating systems on carbon steels are listed in Table 3A for new construction and Table 3B for maintenance. Polyurethane, polysiloxane, or fluoropolymer should be used as the topcoat for UV resistance.--`,,```,,,,````-`-`,,`,,`,`,,`---。
2019石油化工设备和管道涂料防腐蚀设计标准

2019石油化工设备和管道涂料防腐蚀设计标准1.这个设备和管道涂料防腐蚀设计标准涵盖了石油化工行业的各种设备和管道。
This standard for corrosion protection design of equipment and pipelines coating covers various equipment and pipelines in the petrochemical industry.2.标准中包括了使用合适材料的建议和要求。
The standard includes recommendations and requirementsfor the use of suitable materials.3.防腐蚀设计要考虑设备和管道的使用环境和工艺条件。
Corrosion protection design needs to consider the operating environment and process conditions of the equipment and pipelines.4.设计标准要满足国家和行业相关法规和标准的要求。
The design standard must meet the requirements of national and industry-related regulations and standards.5.涂料的选择和施工要符合相关的技术规范。
The selection and application of coatings must comply with relevant technical specifications.6.标准中还包括了对防腐蚀涂料的性能要求。
The standard also includes performance requirements for corrosion-resistant coatings.7.对于不同介质的管道和设备,设计标准会有相应的适用要求。
AS-NZS 4534-2006 澳大利亚标准

AS/NZS 4534:2006Australian/New Zealand Standard ™Zinc and zinc/aluminium-alloy coatingson steel wireAS/NZS 4534:2006AS/NZS 4534:2006This Joint Australian/New Zealand Standard was prepared by Joint Tec hnic al Committee MT-009, Metal Finishing. It was approved on behalf of the Council of Standards Australia on 8 June 2006 and on behalf of the Council of Standards New Zealand on 16 June 2006.This Standard was published on 19 July 2006.The following are represented on Committee MT-009:Australian Institute of Metal FinishingAustralian Aluminium CouncilAustralian Industry GroupAustralian Paint Manufacturers’ FederationDepartment of DefenceGalvanizers Association of AustraliaInstitution of Materials Engineering AustraliaPowder Coaters AssociationThe Royal Australian Chemical InstituteSociety of Automotive Engineers—AustralasiaKeeping Standards up-to-dateStandards are living doc uments whic h reflec t progress in sc ienc e, tec hnology and systems. To maintain their c urrenc y, all Standards are periodic ally reviewed, and new editions are published. Between editions, amendments may be issued. Standards may also be withdrawn. It is important that readers assure themselves they are using a c urrent Standard, whic h should inc lude any amendments whic h may have been published since the Standard was purchased.Detailed information about joint Australian/New Zealand Standards can be found by visiting the Standards Web Shop at www.standards.c om.au or Standards New Zealand web site at www.standards.c and looking up the relevant Standard in the on-line catalogue.Alternatively, both organizations publish an annual printed Catalogue with full details of all c urrent Standards. For more frequent listings or notific ation of revisions, amendments and withdrawals, Standards Australia and Standards New Zealand offer a number of update options. For information about these servic es, users should contact their respective national Standards organization.We also welc ome suggestions for improvement in our Standards, and espec ially enc ourage readers to notify us immediately of any apparent inac urac ies or ambiguities. Please address your c omments to the Chief Exec utive of either Standards Australia or Standards New Zealand at the address shown on the bac k cover.This Standard was issued in draft form for comment as DR 06060.AS/NZS 4534:2006Australian/New Zealand Standard™Zinc and zinc/aluminium-alloy coatings on steel wireOriginated, in part, as part of AS K53.1—1934 and AS K53.2—1935.Previous edition AS/NZS 4534:1998.Second edition 2006.COPYRIGHT© Standards Australia/Standards New ZealandAll rights are reserved. No part of this work may be reproduced or copied in any form or by any means, electronic or mechanical, including photocopying, without the written permission of the publisher.Jointly published by Standards Australia, GPO Box 476, Sydney, NSW 2001 and Standards New Zealand, Private Bag 2439, Wellington 6020PREFACEThis Standard was prepared by the Joint Standards Australia/Standards New Zealand Committee MT-009, Metal Finishing, to supersede AS/NZS 4534:1998, Zinc and zinc/aluminium-alloy coatings on steel wire.The objective of this Standard is to specify requirements for zinc/aluminium-alloy coatings on steel wire and on fabricated wire products. The coatings are formed by the application of molten metal by hot dipping using a specialized continuous process, or by electroplating. However, in this revision of the Standard, a further range of coatings, specifically of high coating mass, has been added. The purpose of these new coatings, which first appeared in AS 2423―2002, Coated steel wire fencing products for terrestrial, aquatic and general use, is to provide superior protection to steel wire subjected to the more aggressive forms of corrosive environment, such as immersion in seawater.This edition contains improved guidelines, set out in an Appendix, for the selection of appropriate coatings for the corrosion protection of steel wire.During the preparation of this Standard cognisance was taken of ISO 7989:1988, Zinc coatings for steel wire. However, this international Standard could not be endorsed as an Australian Standard, as it is deficient in technical detail and is considered unsuitable by Australian industry.The terms ‘normative’ and ‘informative’ have been used in this Standard to define the application of the appendix to which they apply. A ‘normative’ appendix is an integral part of a Standard, where an ‘informative’ appendix is only for information and guidance.CONTENTSPage 1 SCOPE (4)DOCUMENTS (4)2 REFERENCED53 DEFINITIONS............................................................................................................4 DESIGNATION (6)5 WIRE MANUFACTURING PROCESS (7)6 APPEARANCE (8)7 SELECTION OF TEST SPECIMENS FOR COATING MASS AND COATINGADHERENCE TESTS (8)8 TEST METHOD AND REQUIREMENTS FOR COATING MASS (9)9 TEST METHOD AND REQUIREMENTS FOR COATING ADHERENCE (9)RESISTANCE (10)10 CORROSION11 ROUNDING OF TEST RESULT VALUES (10)12 MARKING (10)APPENDICESA PURCHASING GUIDELINES (13)B MEANS FOR DEMONSTRATING COMPLIANCE WITH THIS STANDARD (14)C CHANGES IN MECHANICAL PROPERTIES CAUSED BY AGEING ORHYDROGEN EMBRITTLEMENT (16)D TRANSPORT AND STORAGE OF ZINC-COATED ANDZINC/ALUMINIUM ALLOY-COATED WIRES (17)E DETERMINATION OF COATING MASS (18)F GUIDANCE ON CORROSION PROTECTION (25)STANDARDS AUSTRALIA/STANDARDS NEW ZEALANDAustralian/New Zealand StandardZinc and zinc/aluminium-alloy coatings on steel wire1 SCOPEThis Standard specifies requirements for the mass, quality and testing of zinc coatings and zinc/aluminium-alloy coatings on steel wire of circular or non-circular (shaped) cross-section. The coatings are applied in a continuous process and may be formed either by the application of molten metal or by electrodeposition.Six standard coating mass classes and a range of special coating mass classes are covered. The standard classes are intended, in general, for applications subjected to normal atmospheric corrosion conditions, whereas the special classes are specifically designed to provide acceptable durability under severe to extreme service conditions, such as for prolonged immersion in freshwater or seawater.This Standard applies to coatings on wire at its final size, whether or not the coating has been applied after final cold working, prior to cold working, or at an intermediate stage of cold working.Matters not relating to the coating itself are outside the scope of this Standard.This Standard does not apply to coatings on articles that have been fabricated from uncoated steel wire and which have subsequently been coated with zinc or zinc/aluminium alloy, except where the coating has been applied in a specialized continuous process (e.g. for wire netting) as opposed to batch treatment (e.g. for nails).NOTES:1 Advice and recommendations on information to be supplied by the purchaser at the time ofenquiry or order are contained in Appendix A.2 Coatings in accordance with this Standard may not be available in every combination of wiresize, coating mass class and coating type. Reference should be made to appropriate Australian Standards for the types of wire involved.3 Means for determining compliance with this Standard are given in Appendix B.4 Except as stated in this Clause, requirements for zinc coatings on manufactured wire articles,which have been electroplated following fabrication, are given in AS 1789.5 This Standard does not specify the Preece test for coating uniformity. If this test is required,arrangements should be made between the purchaser and the supplier.2 REFERENCED DOCUMENTSThe following documents are referred to in this Standard:AS1199 Sampling procedures for inspection by attributes1199.0 Part 0:Introduction to the ISO 2859 attribute sampling system1199.1 Part 1:Sampling schemes indexed by acceptance quality limit (AQL) forlot-by-lot inspectioningots1242 Zinc1329 Methods for the analysis of zinc and zinc alloys1329.1 Method 1: Determination of aluminium content—Titrimetric methodAS/NZS 4534:2006 5AS1789 Electroplated zinc (electrogalvanized) coatings on ferrous articles (batchprocess)2331 Methods of test for metallic and related coatings2331.1.4 Method 1.4: Local thickness tests—Magnetic induction and eddy currentmethods2331.2.3 Method 2.3: Tests for average cooling mass per unit area or for thickness—Hydrogen evolution method for zinc coatings2331.3.1 Method 3.1: Corrosion and related property tests—Neutral salt spray (NSS)testmaterials25 Metallic502505.6 Method 6: Wire—Wrapping test2706 Numerical values—Rounding and interpretation of limiting valuesAS/NZS2243 Safety in laboratories2243.1 Part 1:Planning and operational aspects2243.2 Part 2: Chemical aspects2312 Guide to the protection of structural steel against atmospheric corrosion bythe use of protective coatingsAS/NZS ISO9001 Qualitysystems—Requirementsmanagement9004 Quality management systems—Guidelines for performance improvementsHB18.28 Conformity assessment—Guidance on a third party certification system forproductsISO9223 Corrosion of metals and alloys—Corrosivity of atmospheres—ClasssificationSANZHB18.28 Guide 28—General rules for a model third-party certification system forproducts3 DEFINITIONSFor the purpose of this Standard, the definitions below apply:3.1 Coating classAn alphanumeric notation describing the coating mass in relation to the wire size forstandard coatings, but independent of wire size for special coatings (see Clauses 4.2 and 8).3.2 Coating massMass of zinc coating or zinc/aluminium-alloy coating per unit surface area of steel base,expressed in grams per square metre.3.3 Electrogalvanized coatingA zinc coating (see Clause 3.7) applied to the wire by electrodeposition.NOTE: In order to avoid confusion, it is essential that the term ‘electrogalvanized’ and any of itsderivatives not be shortened to ‘g alvanized’ or any of its abbreviations, such as ‘g alv’, since‘galvanized’ is conventionally employed for the hot-dip process.AS/NZS 4534:2006 63.4 Galvanized coatingA zinc coating (see Clause 3.7) alloyed to the steel substrate and applied to the wire by hot-dip immersion in molten zinc of at least 98% purity by mass.3.5 Hot-dip coatingA coating applied by immersion of separated single strands of wire, or of a continuouslength of fabricated wire product, in a bath of molten zinc or zinc/aluminium alloy.3.6 WireA steel filament of dimensionally uniform cross-section along its length, which is either thefeedstock for coating or is finish-coated with zinc or zinc/aluminium alloy.3.7 Zinc coatingA coating composed essentially of zinc, with or without zinc/iron alloy formation at thezinc/iron interface, and produced in a continuous manufacturing operation by dipping (immersing) prepared and separated single strands of steel wire, or a continuous length of fabricated wire product, in a bath of at least 98% purity by mass of molten zinc, or in an electroplating bath containing a solution of an appropriate zinc salt.3.8 Zinc/aluminium-alloy coatingA coating applied in a continuous manufacturing operation by dipping (immersing) eitheruncoated or zinc-coated separated single strands of steel wire, or a continuous length of fabricated wire product, in a bath of molten zinc/aluminium alloy containing between 4.5% and 50% aluminium. The designated nominal aluminium content is based on the resultant aluminium content of the coating, usually taken to be the nominal aluminium content of the bath.4 DESIGNATION4.1 GeneralThe coating class, type and material shall be designated in sequence as follows:(a) The number of this Standard, i.e. AS/NZS 4534.(b) The coating class (see Clause 4.2).(c) The coating type and material (see Clause 4.3).4.2 Designation of coating classFor standard coatings, the coating class shall be designated by the letter W followed by a two-digit number, as follows: W02, W05, W10, W15, W20 or W25 (see Table 1).For special coatings, the coating class shall be identified by the letters SW followed by a number representing the specified minimum coating mass in g/m2 (see Clause 8.2).4.3 Designation of coating type and materialThe coating type and material shall be designated in accordance with the following:(a) Hot-dip zinc or zinc/aluminium-alloy coating applied at final size:(i) Zinc.............................................................................................................Z.(ii) Zinc/aluminium alloy................................................................................ZA.(b) Electroplated zinc coating applied at final size.......................................................E.(c) Drawn (or rolled) after hot-dip coating ...........................DZ or DZA, as appropriate.(d) Drawn (or rolled) after electroplating..................................................................DE.7AS/NZS 4534:2006For zinc/aluminium-alloy coatings, the designation ZA shall include a number insertedbetween the letters to indicate the nominal percentage of aluminium by mass in the coating(see Clause 3.8), e.g. Z5A for 5% of aluminium.Examples of designation:(i) Example 1: AS/NZS 4534/W02Z—hot-dip zinc, Class W02.(ii) Example 2: AS/NZS 4534/W05Z10A—hot-dip zinc/10% aluminium, Class W05.(iii) Example 3: AS/NZS 4534/W25E—electroplated zinc (at final size), Class W25.(iv) Example 4: AS/NZS 4534/W10DZ—drawn (or rolled) hot-dip zinc, Class W10.(v) Example 5: AS/NZS 4534/SW600Z—special coating, hot-dip zinc, 600 g/m2 minimum.5 WIRE MANUFACTURING PROCESS5.1 Continuous coating process5.1.1 Raw materialsZinc for replenishing the molten bath, or for electrodes for electrolysis, shall comply withthe requirements of AS 1242 and shall be of 98.5% purity, or better, depending on thequality demands of the coating process.Zinc/aluminium-alloy bath replenishment shall be accomplished in such a way that thealuminium content of the zinc/aluminium alloy coating on the wire (see Clause 3.8) iswithin +0.5% and −0.5% of the designated nominal value. Raw material additions to thebath may contain minor levels of control elements.5.1.2 PrecautionsThe wire manufacturer shall take care in the coating process to avoid undue changes to themechanical properties of the steel base, particularly in respect of embrittlement, and toavoid damage, such as scoring, of the coating itself.NOTE: Appendix C g ives advice on unavoidable chang es, which may occur to the mechanicalproperties of softened wires, and on the effects of hydrog en embrittlement resulting fromelectrodeposition.The wire manufacturer shall take every precaution to ensure that the coating is free ofirregularities and defects (see Clause 6).5.2 Drawing or rolling processFor wires that are cold worked after the application of the coating, due care shall be takenby the manufacturer to avoid damage to the coating, such as abrasion, scoring or chattermarks, either prior to, or at any stage of, the cold working operation.5.3 Supplementary non-metallic coatingsZinc or zinc/aluminium-alloy coatings may be covered with a supplementary adherentcoating, such as chromate, paint, plastic, wax, or residual drawing lubricant.NOTES:1 Hot-dip zinc or zinc/aluminium-alloy coating s may carry a thin covering of wax, applied toreduce friction during subsequent mechanical forming treatments.2 Zinc or zinc/aluminium-alloy coated wires that have subsequently been drawn normally carrya thin covering of wire-drawing lubricant.AS/NZS 4534:2006 86 APPEARANCEThe zinc coating or zinc/aluminium-alloy coating shall be continuous, as smooth and evenly distributed as modern industrial technology permits, and be free of defects that are detrimental to the stated use of the wire.NOTES:1 Defects cannot be completely quantified. Where the presence, size or frequency of defectsin the coating is considered to be of concern, appropriate arrang ements should be madebetween the purchaser and the wire manufacturer or supplier. This may be achieved by theprovision of acceptable type samples or methods of test.2 The coating on hot-dip g alvanized or zinc/aluminium-alloy-coated wire is not perfectlysmooth or devoid of irreg ularities. It should be noted that diameter or dimensionaltolerances, required by appropriate wire or wire product specifications, apply torepresentative uniformly coated areas of the wire.3 With increasing coating mass, hot-dip coatings usually become less smooth.4 Hot-dip coating s applied in a specialized continuous process to fabricated wire articles areusually not as smooth as coatings applied to single wire strands.5 The finish of untreated zinc-coated wire, i.e. without a supplementary non-metallic coating(see Clause 5.3), is usually a lustrous silver colour when produced, but ages to a dull grey.Zinc/aluminium-alloy coating s ag e from silver, when initially produced, to a deep g rey.Provided that the coating complies with the requirements of this Standard, the colour andlustre of the finish should not be considered detrimental to the performance of the coating inservice.6 Advice on the transport and storage of coated wire is given in Appendix D.7 SELECTION OF TEST SPECIMENS FOR COATING MASS AND COATINGADHERENCE TESTS7.1 GeneralA suitable length of wire for performing the required tests shall be cut from one or bothends of each coil selected for sampling. If the ends of the coil are damaged or otherwise abnormal, an appropriate length of wire shall be discarded before taking the test lengths.Any supplementary non-metallic coating (see Clause 5.3), which may interfere with testing, shall be removed, taking care not to damage the surface of the zinc or zinc/aluminium-alloy coating.Lengths taken from products or articles fabricated from zinc-coated or zinc/aluminium alloy-coated wire shall be as representative as possible of the original coated wire.Lengths taken from products or articles that have been zinc or zinc/aluminium alloy-coated after fabrication, by means of a specialized continuous operation, shall be as representative as possible of the batch involved.Unless specified otherwise, test specimens taken from fabricated products or articles shall not be required to undergo adherence testing. However, the adhesion of the coating shall be fit for purpose.7.2 Coating massThe lengths of test specimens required for gravimetric, volumetric or non-destructive determination of coating mass are specified in Paragraphs E2.3, E3.4 or E4 respectively of Appendix E.7.3 Adherence of coatingThe test specimen shall be cut from the sample and shall be of sufficient length to ensure complete control of the wrapping or bending operation employed for adherence testing.8 TEST METHOD AND REQUIREMENTS FOR COATING MASS8.1 GeneralThe coating mass of zinc or zinc/aluminium-alloy coatings on steel wire of circular or non-circular cross-section, as produced, shall be determined in accordance with one of themethods specified in Paragraphs E2, E3 or E4 of Appendix E. In cases of dispute, thegravimetric method (see Paragraph E2, Appendix E) shall be used as the referee testmethod.The coating mass of zinc or zinc/aluminium-alloy coatings on round wire shall conform tothe limits specified in Table 1 for standard coatings and as given in Clause 8.2 for specialcoatings. For shaped wires, an equivalent nominal diameter appropriate to Table 1 is determined using the following equation:c cd 318.0==πwhered = the equivalent nominal diameter corresponding to the nominal size of thecoated shaped wire, in millimetresc = the circumference of the nominal size of the coated shaped wire, in millimetresNOTE: The ‘nominal diameter’ shown in Table 1 relates to the zinc or zinc/aluminium alloy-coated wire, excluding any supplementary non-metallic coating.If coating mass determinations are carried out on products that have been fabricated fromzinc-coated or zinc/aluminium alloy-coated wires, the specified minimum coating massesshown in Table 1 and in Clause 8.2 shall be reduced by 3%, and then rounded to the nearest5 g/m 2, unless specifically stated otherwise in the relevant product Standards.8.2 Specific requirements for special coatingsFor special zinc or zinc/aluminum-alloy coatings, the specified coating mass shall be atleast 300 g/m 2 minimum with incremental increases of 50 g/m 2; that is, 300, 350, 400,450 g/m 2 minimum and so on.NOTES:1 Special SW coating masses are independent of wire size; that is, the specified coating massdoes not vary with wire size.2 Not every specified minimum coating mass nor wire size may be commercially available.9 TEST METHOD AND REQUIREMENTS FOR COATING ADHERENCEThe adherence of the zinc coating or zinc/aluminium-alloy coating shall be tested by meansof a cylindrical mandrel. For wires of circular cross-section the relationship betweenmandrel diameter and wire diameter shall be in accordance with Table 2. For shaped wire,unless specified to the contrary, the nominal diameter given in Table 2 shall be taken to beits overall minor dimension.NOTES:1 This test applies only to wire where the coating is clearly visible throug h any thin,supplementary non-metallic coating (such as wax or wire-drawing lubricant), or where nosupplementary non-metallic coating exists, or where it has been carefully stripped from thewire.2 The ‘nominal diameter’ shown in Table 2 relates to the diameter of the zinc orzinc/aluminium-alloy coated wire, excluding any supplementary non-metallic coating.For wires of nominal diameter 7.50 mm and smaller, the adherence of the coating shall be tested by wrapping the wire at least six close turns snugly around the mandrel as specified in Table 2 (see Note 3), and in accordance with the procedure given in AS 2505.6. For wires over 7.50 mm nominal diameter, the adherence of the coating shall be tested by bending the wire through an angle of at least 90° around the appropriate mandrel specified in Table 2.The coating shall remain firmly adherent to the steel base and shall not crack or flake to a degree that any flakes of coating can be removed by rubbing with the bare fingers.NOTES:1 Loosening or detachment of small particles of coating during the adherence test, arising frommechanical polishing of the surface of the coated wire, should not be deemed cause for rejection. Small particles of coating, formed as small g lobules or frag ments on the surface during the coating process, may loosen or detach during the test, and this too should not be deemed to be cause for rejection.2 Due care should be exercised in selecting the appropriate mandrel for the wrap or bend testsince such mandrels are usually marked with radius rather than diameter.3 With shaped wires carrying less than Class W10 coating s, it may be found impracticable tosatisfactorily perform the wrap test as specified, when the ratio of the major dimension to the minor overall dimension is g reater than 1.5. In such instances, the adherence of the coating may be tested by bending the wire throug h an ang le of at least 90° around the mandrel appropriate to the minor dimension, which is taken as the nominal diameter.10 CORROSION RESISTANCEThe corrosion resistance of zinc-coated or zinc/aluminium-alloy coated wire is dependent on a number of factors including coating thickness and the atmospheric environment to which it is subjected.NOTE: Guidance on the selection of coating s for various corrosive environments is g iven in Appendix F.11 ROUNDING OF TEST RESULT VALUESThe determined value of coating mass shall be rounded to the nearest 5 g/m2. For advice on the method of rounding see AS 2706.12 MARKINGExcept where a wire or a wire product is covered by an Australian or Australian/New Zealand Standard, which refers the coating requirements to a specific class in this Standard, each coil of wire shall be legibly and durably tagged to enable the coating to be identified with this Standard. The information on the tag pertaining to the coating shall include the following:(a) The number of this Standard, i.e. AS/NZS 4534.NOTE: Where the space is limited on the tag, manufacturers may designate the number of this Standard as AS 4534 or NZS 4534, as appropriate.(b) Designation of coating class (see Clause 4.2).(c) Designation of coating type and material (see Clause 4.3).(d) Manufacturer’s trade identification.NOTE: Manufacturers making a statement of compliance with this Australian/New Zealand Standard on a product, packaging, or promotional material related to that product are advised to ensure that such compliance is capable of being verified.TABLE 1STANDARD COATING MASSES FOR ROUND WIRENominalMinimum coating mass, g/m2diameter ofcoated wire,Class W02 Class W05 Class W10 Class W15 Class W20 Class W25 mm>0.19 ≤0.23— 15 25 40 50 65— 25 45 70 90 115 >0.23 ≤0.33— 35 60 90 120 150 >0.33 ≤0.40>0.40 ≤0.46 — 40 75 115 150 190>0.46 ≤0.53 — 50 90 135 180 22520 60 105 160 210 265 >0.53 ≤0.6320 65 120 180 240 300 >0.63 ≤0.7525 70 130 195 260 325 >0.75 ≤0.8525 80 140 210 280 350 >0.85 ≤0.9525 85 150 225 300 375 >0.95 ≤1.0625 90 160 240 320 400 >1.06 ≤1.1830 95 170 255 340 425 >1.18 ≤1.3230 100 185 280 370 465 >1.32 ≤1.5535 110 200 300 400 500 >1.55 ≤1.8035 120 215 325 430 540 >1.80 ≤2.2440 125 230 345 460 575 >2.24 ≤2.7245 130 240 360 480 600 >2.72 ≤3.1550 135 250 375 500 625 >3.15 ≤3.5560 140 260 390 520 650 >3.55 ≤4.2570 150 275 415 550 690 >4.25 ≤5.0080 160 290 435 580 725 >5.00 ≤8.00>8.00 — 80 170 305 460 610 765NOTES:1 The class identification numbers reflect the minimum coating masses relative to Class W10. For example,the minimum coating masses f or Class W05 are approximately half those f or Class W10; those f or Class W25 are 2.5 times those for Class W10.2 Guidance for the selection of coating mass and material to suit particular external exposure conditions isgiven in Appendix F.3 For coating mass requirements for shaped wires, see Clause 8.1TABLE 2RELATIONSHIP BETWEEN MANDRELDIAMETER AND WIRE DIAMETERmillimetresMandrel diameterNominal diameter(d) of coated wireClassesW02 and W05Classes W10 and over≤3.80 1d4d >3.80 ≤10.00 1d5d >10.00 2d6d NOTE: For mandrel diameters for shaped wires, see Clause 9.APPENDIX APURCHASING GUIDELINES(Informative)A1 GENERALAustralian/New Zealand Standards are intended to include the technical provisions necessary for the supply of products referred to in the particular Standard, but do not purport to comprise all the necessary provisions of a contract. This Appendix contains advice and recommendations on the information to be supplied by the purchaser at the time of enquiry or order.A2 INFORMATION TO BE SUPPLIED BY THE PURCHASERThe purchaser should supply the following information at the time of enquiry or order:(a) The number of this Standard, i.e. AS/NZS 4534.(b) Designation of coating class, e.g. W10 and SW600 (see Clause 4.2).(c) Designation of coating material and process, or type, e.g. E for electroplated zinc, Zfor hot-dip galvanized (see Clause 4.3).(d) For zinc/aluminium alloys, the nominal percentage of aluminium by mass, e.g. Z5Afor 5% aluminium (see Clause 4.3).(e) Any special requirements for frequency of testing.(f) Whether an additional test for uniformity of the coating is required. Details of testrequirements should be included.(g) Whether a test report covering coating mass and adherence is required.(h) Whether it is the intention of the purchaser to inspect the coated product prior todelivery.(i) Any special or supplementary requirements, such as a passivation coating.NOTE: Soldering of material having a zinc/aluminium-alloy coating, or where passivation coatings have been applied, may present difficulties and may not be practicable.。
扫描振动电极(SVET)方法表征涂层的防腐蚀性能
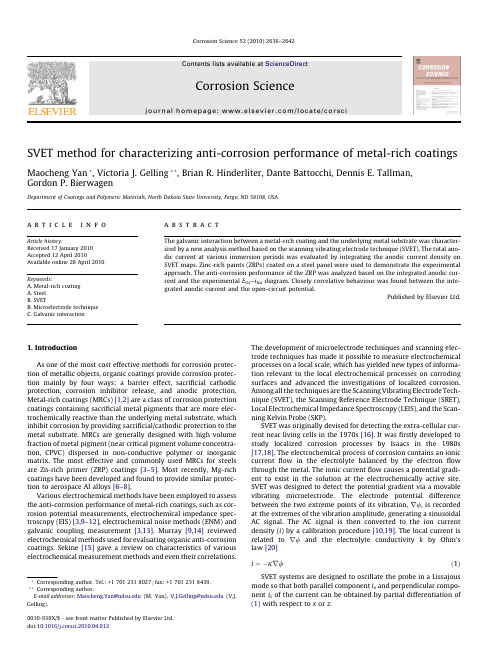
SVET method for characterizing anti-corrosion performance of metal-rich coatingsMaocheng Yan *,Victoria J.Gelling **,Brian R.Hinderliter,Dante Battocchi,Dennis E.Tallman,Gordon P.BierwagenDepartment of Coatings and Polymeric Materials,North Dakota State University,Fargo,ND 58108,USAa r t i c l e i n f o Article history:Received 17January 2010Accepted 12April 2010Available online 28April 2010Keywords:A.Metal-rich coating A.SteelB.SVETB.Microelectrode techniqueC.Galvanic interactiona b s t r a c tThe galvanic interaction between a metal-rich coating and the underlying metal substrate was character-ized by a new analysis method based on the scanning vibrating electrode technique (SVET).The total ano-dic current at various immersion periods was evaluated by integrating the anodic current density on SVET maps.Zinc-rich paints (ZRPs)coated on a steel panel were used to demonstrate the experimental approach.The anti-corrosion performance of the ZRP was analyzed based on the integrated anodic cur-rent and the experimental E OC –i Int diagram.Closely correlative behaviour was found between the inte-grated anodic current and the open-circuit potential.Published by Elsevier Ltd.1.IntroductionAs one of the most cost effective methods for corrosion protec-tion of metallic objects,organic coatings provide corrosion protec-tion mainly by four ways:a barrier effect,sacrificial cathodic protection,corrosion inhibitor release,and anodic protection.Metal-rich coatings (MRCs)[1,2]are a class of corrosion protection coatings containing sacrificial metal pigments that are more elec-trochemically reactive than the underlying metal substrate,which inhibit corrosion by providing sacrificial/cathodic protection to the metal substrate.MRCs are generally designed with high volume fraction of metal pigment (near critical pigment volume concentra-tion,CPVC)dispersed in non-conductive polymer or inorganic matrix.The most effective and commonly used MRCs for steels are Zn-rich primer (ZRP)coatings [3–5].Most recently,Mg-rich coatings have been developed and found to provide similar protec-tion to aerospace Al alloys [6–8].Various electrochemical methods have been employed to assess the anti-corrosion performance of metal-rich coatings,such as cor-rosion potential measurements,electrochemical impedance spec-troscopy (EIS)[3,9–12],electrochemical noise methods (ENM)and galvanic coupling measurement [3,13].Murray [9,14]reviewed electrochemical methods used for evaluating organic anti-corrosion coatings.Sekine [15]gave a review on characteristics of various electrochemical measurement methods and even their correlations.The development of microelectrode techniques and scanning elec-trode techniques has made it possible to measure electrochemical processes on a local scale,which has yielded new types of informa-tion relevant to the local electrochemical processes on corroding surfaces and advanced the investigations of localized corrosion.Among all the techniques are the Scanning Vibrating Electrode Tech-nique (SVET),the Scanning Reference Electrode Technique (SRET),Local Electrochemical Impedance Spectroscopy (LEIS),and the Scan-ning Kelvin Probe (SKP).SVET was originally devised for detecting the extra-cellular cur-rent near living cells in the 1970s [16].It was firstly developed to study localized corrosion processes by Isaacs in the 1980s [17,18].The electrochemical process of corrosion contains an ionic current flow in the electrolyte balanced by the electron flow through the metal.The ionic current flow causes a potential gradi-ent to exist in the solution at the electrochemically active site.SVET was designed to detect the potential gradient via a movable vibrating microelectrode.The electrode potential difference between the two extreme points of its vibration,r /,is recorded at the extremes of the vibration amplitude,generating a sinusoidal AC signal.The AC signal is then converted to the ion current density (i )by a calibration procedure [10,19].The local current is related to r /and the electrolyte conductivity k by Ohm’s law [20]i ¼Àj r /ð1ÞSVET systems are designed to oscillate the probe in a Lissajous mode so that both parallel component i x and perpendicular compo-nent i z of the current can be obtained by partial differentiation of (1)with respect to x or z .0010-938X/$-see front matter Published by Elsevier Ltd.doi:10.1016/j.corsci.2010.04.012*Corresponding author.Tel.:+17012318027;fax:+17012318439.**Corresponding author.E-mail addresses:Maocheng.Yan@ (M.Yan),V.J.Gelling@ (V.J.Gelling).Corrosion Science 52(2010)2636–2642Contents lists available at ScienceDirectCorrosion Sciencej o u r n a l h o m e p a g e :w w w.e l s e v i e r.c o m /l o c a t e /c o r s ci1.1.SVET for characterizing anti-corrosion performance of coatingsSVET has enjoyed wide acceptance as a powerful electrochemi-cal technique for evaluation of corrosion inhibitor,detection of cor-rosion activity and quantification of corrosion defects in coatings. SVET has been used in the research of various types of corrosion, such as pitting[21],cut-edge corrosion[22–24],galvanic corrosion [18],microbiologically influenced corrosion(MIC)[25],weld corro-sion,and stress corrosion cracking(SCC)[26].In the case of corro-sion of a coated metal,SVET is able to give detailed insights into the electrochemical interactions between a coating and its sub-strate at a defect,which has been provided valuable information on the anti-corrosion mechanism by a coating,including the gener-ation and development of defects,and the influence of pigments/ inhibitors on corrosion of substrate at a defect[27,28].In previous studies from this laboratory,series of coatings for Al alloy(AA)2024-T3has been characterized by SVET.To monitor both the corrosion activity of the substrate and the possible gal-vanic interaction between the coating and the substrate,the mea-surement was conducted in the vicinity of a scratch exposing the underlying substrate.The SVET results for polypyrrole deposited on AA2024-T3showed that a large anodic current occurred at the defect due to anodic dissolution of the alloy and that the catho-dic current was rather uniformly distributed over the polymer sur-face,which implies that a p-doped CP would promote active dissolution of the AA2024-T3substrate at the defect if the passiv-ation could not be obtained[29,30].Most recently,interesting interactions between neutral or n-doped poly(2,3-dihexylthieno-[3,4-b]pyrazine)and AA2024-T3has been demonstrated by SVET [31].The n-doped conjugated polymer exhibited the ability to sac-rificially protect the exposed Al alloy in a defect.For a redox inactive barrier coating,such as a plain epoxy coat-ing on steel or AA2024-T3,the SVET showed that both anodic cur-rent and cathodic current were located at the scribe[32].Due to the high impedance/low-conductivity of the intact barrier coating, a complete corrosion cell,if any,would be established within the defect,and no current was distributed on the coating.In the case of metal-rich coatings,such as Mg-rich primer coated on Al alloys, the SVET results exhibited a well-defined cathodic current peak above the scratch.The anodic current(related to the anodic disso-lution of the sacrificial pigment)distributed on the primer,which demonstrates that the sacrificial pigment functions by the cathodic protection mechanism[1,33,34].In this work,a SVET method is provided for further understand-ing the galvanic interaction between a metal-rich coating and the metal substrate,and evaluating the anti-corrosion performance of the metal-rich coating.A zinc-rich primer(ZRP)coated on steel was examined to demonstrate the efficacy of the method.Several characteristic indexes are obtained from the SVET current density map to characterize the galvanic interaction between the ZRP and its substrate.The total anodic current(and hence the corrosion rate)over the scan area is evaluated by integration of the overall anodic current density on the SVET maps.The variations of the to-tal anodic current and that of open-circuit potential(E OC)were analyzed as a function of the immersion time.Additionally,the SVET current indexes were compared with the galvanic current ob-tained by zero resistance amperometry(ZRA).2.Experimental2.1.Materials and electrode preparationAn epoxy resin(Epon828,from Hexion)and a modified poly-amide(Epikure3175,from Hexion)curing agent were mixed in a 1:1.1stoichiometric ratio.This ratio results in the optimal barrier properties and hardness of the primer by giving near to the max-imum amount of crosslinking.Methyl isobutyl ketone(MIBK) was used as solvent.Then,zinc powder was added to the solu-tion and was stirred to form a thick mortar-like mixture.A steel panel(R-35,from Q-Panel)was pretreated by grinding with400-and600-grit SiC sandpaper,followed by degreasing with hexane. The coatings were applied using a drawn down bar at a wet thickness of200l m.The coated panels were placed in a convec-tion oven at70°C for24h afterflashing off for approximately 30min.For the primers of pigment volume concentration(PVC) lower than25%,the zinc pigment wasfirstly dispersed in MIBK for full dispersion.The dryfilm thicknesses were in the range of140–190l m.2.2.SVET measurement and data analysisThe current distribution over the interface of solution/ZRP(67% PVC,subsequently referred to as ZRP67)was measured using a SVET system from Applicable Electronics(USA).The Pt–Ir microelectrode (Microprobe Inc.)with a10l m diameter tip which was platinized to a20l m diameter sphere.The microprobe was vibrated$200l m above the samples with the amplitude20l m along the X and Y directions.A pair of platinized platinum wires was used as both the reference and bath ground electrodes.The probe made20Â20 measurements in each scan($600s),generating a400-point mesh across the surface.Scans were initiated5min after immersion and repeated every60min.The ZRP67sample(1Â1cm2)was masked by a polyester tape,exposing an open area of3Â3mm2as the scan-ning area.An artificial scratch was introduced in the center of the scanning area.For comparison,the same SVET measurement was also conducted on an unscratched ZRP67.All SVET measurements were performed at the free-corrosion condition in a cell containing $5mL3.5wt.%NaCl aqueous solution.The SVET current density mapping and the statistical analysis of the data were performed with Origin software.The current densi-ties were displayed in three-dimensional(3D)maps,showing the spatial distribution of the current density as a function of the(x, y)position in the scan region on ZRP.The current values in the SVET map are positive for anodic currents and negative for catho-dic currents.The contour map of the current densities is at the bot-tom of the3D map.The SVET current density vector images superimposing the measured current vector onto an optical image of the sample showed images of the sample surface as well as the locations of anodic/cathodic area.Based on the SVET current density map,the anodic current den-sity peak(i A,max),the cathodic current density peak(i C,max),the average current density(i Ave)and the integrated anodic current (I Int)were used to characterize the anti-corrosion properties of the coating.I Int was evaluated by integration of the overall anodic current(I A)on a SVET current density map,which is theoretically equal to the total cathodic current(I C)over the ZRP surface.Split-ting the scan area(S,3Â3mm2)into20Â20small squares,we calculate the anodic or cathodic current on each square,and sum all the resulting currents to obtain I Int(l A)on the scan area,as shown byI Int¼SPi An¼ÀSPi Cnð2Þwhere i A is the anodic current density(i A P0),i C the cathodic cur-rent density(i C<0)and n the number of measurement points in each scan(n=400).2.3.Galvanic coupling measurementGalvanic coupling(both the mixed potential,E Mix,and the cou-pling current)between the coated metal and the bare substrateM.Yan et al./Corrosion Science52(2010)2636–26422637was measured using a Gamry PC4/300potentiostat in a zero resis-tance ammeter(ZRA)mode.The experiments were carried out in a two-compartment enclosed cell described in our previous work [29].The two-compartment cell permitted careful control of the atmospheric conditions in each compartment.The working elec-trode in one compartment was ZRP67-coated on the steel(subse-quently referred to as the ZRP-compartment)and the working electrode in the other compartment was the bare steel(subse-quently referred to as the steel-compartment).The exposed area of ZRP67was 1.0cm2and the bare steel was in a pinhole of 0.04cm2(simulating a coating defect),yielding an area ratio (ZRP67to steel)of ca.25.To simulate the condition for a top-coated sample,where a topcoat would protect the primer from di-rect oxygen access,the solution in the coating-compartment was purged with N2,while the solution in the alloy-compartment was purged with air.3.Results and discussion3.1.SVET current density mapsThe SVET current density maps for the bare steel in3.5%NaCl solution,as presented in Fig.1,showed several anodic current peaks that appear after several minutes,due to possible pitting nucleation.After30min,these anodic current peaks combined into one broad anodic peak,where dark corrosion products began to ap-pear on the steel surface.Fig.2displays SVET current density maps above the defect on the scratched ZRP67(67%PVC)after various immersion periods in3.5%NaCl solution.The cathodic current was mainly located at the scratch where a well-defined cathodic peak existed throughout the5-day immersion period.The anodic area appeared at different sites on ZRP67during the immersion.At the beginning of the immersion from0.1to4h,anodic areas were found to initiate only at the corners of the scratch,as shown in Fig.2a and b.After5h of the immersion,anodic areas were scattered around the scratch (Fig.2c).After10h of the immersion,significant changes occurred both in current distribution and in value,as presented in Fig.2d. The anodic activity moved from one area to another near the scratch;the cathodic area included to almost all the scratch and a well-defined cathodic peak was observed.After20h of the immersion(Fig.2e and f),the cathodic current decreased with time,and the anodic current was evenly distributed over the sur-face of the primer.The variations of the anodic current peak(i A,max),the cathodic current peak(i C,max)and the average current density(i Ave)in SVET maps are shown in Fig.3.The i A,max decreased over the immersion time on the whole,except for two peaks appearing at3and10h. The SVET experiment was conducted under free-corrosion condi-tion(without external polarization applied)where the anodic cur-rents and cathodic currents above the ZRP67are balanced and the net current should be zero.It should be note that,in a scanning plane above the free-corro-sion surface,the integrated anodic current I A should be theoreti-cally equal to the integrated cathodic current I C in the absolute value and hence the average current density(i Ave)should be zero. But deviations between I A and I C are usually obtained by SVET, which causes i Ave to deviate from zero.The deviations may be attributed to the fact that the current density on a SVET map was not taken at the same time.The corrosion behaviour and current distribution on the scan area are changing during scanning(one scan takes$10min).3.2.Integrated anodic current of the ZRP obtained by SVETThe ZRP paints under study here are heterogeneous systems with pores and zinc particles distributed randomly in the binder. The probable reactions on the primer in an electrolyte are as fol-lows:Zinc dissolution to the oxide(ZnO)/polymeric-binderfilm, electrochemical dissolution of the active zinc particles,and oxygen reduction on zinc particles or on the substrate through pores[35].A key aspect of the above mentioned mechanisms is the galvanic interaction between ZRP and the metal substrate.The galvanic interaction between ZRP and substrate may be influenced by any or all of the following factors:the electrochemical state of zinc par-ticles at ZRP/solution interface,reactive Zn/Fe area ratio(S Zn/Fe) interface,as well as the diffusion process through the coating and the deposit of Zn corrosion products[3,12].The electrochem-ical behaviour and cathodic protection performance of ZRPs have been well studied by corrosion potential monitoring[3],EIS [3,12,36],conductive atomic force microscopy(AFM)[2],as well as the scanning electron microscopy(SEM)[4,12].In this work, the electrochemical and corrosion performance of the ZRP was characterized by the SVET method.The integrated anodic current I Int above the ZRP67obtained by the SVET method is presented in Fig.4as a function of the immer-sion time,together with E OC measured under the same conditions. For the scratched ZRP67,closely correlative behaviour was found between E OC and the total anodic current.Most obviously,two sig-nificant anodic current peaks appeared during the immersion ex-actly before and after the E OC peak occurred.For comparison,I Int and E OC for the unscratched ZRP67are also presented in Fig.4. The trend of I Int of the unscratched ZRP67was similar to that of the scratched ZRP67but with much lower amplitude.The most2638M.Yan et al./Corrosion Science52(2010)2636–2642positive potential of ZRPs(unscratched)reached at$3h immersion and this potential was observed to depend significantly on the PVC, as shown in Fig.5.The most positive potentials for ZRPs with PVC5%,15%,45%and67.5%were0.166,0.00,À0.60andÀ0.91V,respec-tively.The following several stages were clearly recognized from both I Int and E OC shown in Fig.4for the scratched ZRP67.distributions over an artificial line scratch on ZRP(67%superimposed with current vectors(right of a and f)M.Yan et al./Corrosion Science52(2010)2636–264226393.2.1.The activating stageThe E OC(ca.À0.9V initially)shifted gradually towards negative direction during thefirst1h immersion as a result of the activation of Zn particles through dissolving ZnOfilm or soaking the binder film,approximatingÀ1.0V(E OC of the zinc particles)at$1h.In the following3h,the E OC shifted in the positive direction,implying that the steel substrate began to be wetted by the electrolyte through pores(decreasing the ratio of S Zn/Fe).The I Int($1.2Â10À2l A initially)slightly decreased in thefirst 1h immersion.Then,it gradually increased as a result of the disso-lution of ZnO/zinc particles at the ZRP surface.From3h immer-sion,I Int decreased sharply accompanying with the rapid increase of E OC due to the wetting process of the steel substrate until E OC reaching a peak(À0.71V)at5h,where the steel substrate was ex-pected to be totally wetted.A current valley(7.3l A)exactly corre-sponded to the E OC peak at5h.Once the substrate was wetted, galvanic interaction between zinc particles and steel substrate would be expected to occur.The period of the beginning$5h immersion can be referred to as the activating stage,where the main process was the dissolution of the ZnOfilm and then the zinc particles reaction with the electrolyte.In the activating stage,the electrochemical reaction process mainly occurred on the ZRP/solu-tion interface.3.2.2.The sacrificial protection stageEven after the steel surface became completely wetted at$5h in Fig.4,some zinc particles were still covered by thick oxides or by binderfilms.Zinc particles continued to be activated by the dis-solution of the ZnOfilm and/or galvanically coupling to the sub-strate.At the beginning of the galvanic stage,corrosion product was formed in pores in the primer,which tended to seal the pores, reducing the number and size of pores[3].This process shifted E OC toward negative directions and increased I Int sharply until attain-ing2.3Â10À2l A at$11h.Thefluctuation of E OC in the range ofÀ0.78toÀ0.87V in the vicinity of9h and the significant decrease in I Int at$10h might be attributed to the accumulation of Zn corrosion product which improved the barrier property of the coating.For the unscratched ZRP67,the E OCfluctuation at$8h immersion disappeared,which further implied that the E OCfluctuation might be related to the de-posit of the zinc corrosion product in the defect and its adhesion to the surface.3.2.3.The barrier stageThe E OC continued to decay,with somefluctuations,beginning from$11h(Fig.4).I Int decayed to a low value of1.2Â10À2l A, where it remained for the following duration of the experiment. The distinct decrease in I Int may be attributed to the zinc depleting and/or the improved barrier property of the primer.The barrier properties of the primer would improve by deposit of the corrosion product on the primer.The zinc corrosion product also trends to improve barrier effect by sealing pores in the primer,as has been proposed and observed by other authors[3,4,36].3.2.4.E OC–i Int diagramThe evolution of the E OC–i Int results for the scribed ZRP67is shown in Fig.6,with the numbers indicating the immersion time (in hour)and the dashed lines showing the shifting direction of the E OC–i Int points.Several stages(the wetting stage,the cathodic protection stage and the barrier stage)were demonstrated in the E OC–i Int evolution for the scratched ZRP67during the immersion period.Almost all the conventional electrochemical measurements re-quire an externally imposed polarization which would possibly have an unfavorable effect on the specimen.By contrast,SVET al-lows to measure integrated corrosion current at the free-corrosion condition(without external polarization applied)which is benefi-cial,especially for the highly active metal-rich coatings.2640M.Yan et al./Corrosion Science52(2010)2636–26423.3.Galvanic coupling between ZRP and the bare steelThe coupling current and mixed potential for ZRP67(1.0cm2,N2 purged)coupled with bare steel(0.04cm2,air purged)in3.5%NaCl solution are shown in Fig.7.The coupling current started at 4Â10À3l A and rapidly increased to12Â10À3l A at$25min.After immersion,the zinc particles were gradually activated through dis-solution of the oxide(ZnO)surface and water penetration through polymeric-binderfilm.The zinc particles were fully activated at the end of1h,where the mixed potential attained the lowest value and the coupling current was highest.Then the mixed potential in-creased and the coupling current declined steadily.At$26h,the E Mix attainedÀ0.85V,and the coupling current was6.9Â10À3l A.In the case of the galvanic coupling measurement in the two-compartment cell,the bare steel pinhole(simulating coating de-fect)is separated in another cell,where the bare steel was not af-fected by the deposit of the zinc corrosion product in the defect. The depletion of the zinc particles and the lack of the corrosion product deposit may lead to the steady decrease of the coupling current,which was a fundamental difference from the case of the SVET measurement,where the barrier stage was clearly observed as the result of a barrier effect of the Zn products deposit.4.ConclusionsBy integrating the overall anodic current density measured by scanning vibrating electrode technique(SVET),the total anodic current(and therefore the corrosion rate)over the coating surface was obtained and used to evaluate the galvanic interaction be-tween coatings and substrates.This SVET method allows the mea-surement of corrosion current at the free-corrosion condition (without external polarization applied),which is highly beneficial, especially for active metal-rich coatings.For the zinc-rich primer, several stages during immersion were distinctly recognized by the SVET method:the activating stage,the sacrificial protection stage and the barrier stage.Closely correlative behaviour was found between the total anodic current and the open-circuit poten-tial.This SVET analysis method may provide a new insight for the corrosion protection performance and even the service life of me-tal-rich coatings.AcknowledgmentThe authors would like to thank the US Army Research Labora-tory(Contract#W911NF-04-2-0029)for sponsoring this research. References[1]G.Bierwagen,D.Battocchi,A.Simoes,A.Stamness,D.Tallman,The use ofmultiple electrochemical techniques to characterize Mg-rich primers for A1 alloys,.Coat.59(2007)172–178.[2]G.Bierwagen,K.Allahar,B.Hinderliter,H.Jung,Zn-rich coatings revisited,in:Tri-Service Corrosion Conference,Denver,Co.,2007.[3]C.M.Abreu,M.Izquierdo,M.Keddam,X.R.Novoa,H.Takenouti,Electrochemical behaviour of zinc-rich epoxy paints in3%NaCl solution, Electrochim.Acta41(1996)2405–2415.[4]M.Morcillo,R.Barajas,S.Feliu,J.M.Bastidas,A SEM study on the galvanicprotection of zinc-rich paints,J.Mater.Sci.25(1990)2441–2446.[5]C.Hare,Corrosion control of steel by organic coatings,in:R.W.Revie(Ed.),Uhlig’s Corrosion Handbook,John Wiley&Sons,New York,2000,pp.1023–1038.[6]M.E.Nanna,G.P.Bierwagen,Mg-rich coatings:a new paradigm for Cr-freecorrosion protection of Al aerospace alloys,JCT Res.1(2004)69–80.[7]D.Battocchi, A.M.Simoes, D.E.Tallman,G.P.Bierwagen,Electrochemicalbehaviour of a Mg-rich primer in the protection of Al alloys,Corros.Sci.48 (2006)1292–1306.[8]G.Bierwagen,R.Brown,D.Battocchi,S.Hayes,Observations on the Testing ofMg-rich Primers for Totally Chromate-free Corrosion Protection of Aerospace Alloys,Department of Defense Corrosion Conference,Gaylord National, Washington DC,2009.[9]J.N.Murray,Electrochemical test methods for evaluating organic coatings onmetals:an update.Part III:multiple test parameter measurements,.Coat.31(1997)375–391.[10]G.Grundmeier,W.Schmidt,M.Stratmann,Corrosion protection by organiccoatings:electrochemical mechanism and novel methods of investigation, Electrochim.Acta45(2000)2515–2533.[11]F.Mansfeld,Use of electrochemical impedance spectroscopy for the study ofcorrosion protection by polymer-coatings,J.Appl.Electrochem.25(1995) 187–202.[12]J.R.Vilche,E.C.Bucharsky,C.A.Giudice,Application of EIS and SEM to evaluatethe influence of pigment shape and content in ZRP formulations on the corrosion prevention of naval steel,Corros.Sci.44(2002)1287–1309. [13]S.E.Faidi,J.D.Scantlebury,P.Bullivant,N.T.Whittle,R.Savin,Anelectrochemical study of zinc-containing epoxy coatings on mild steel, Corros.Sci.35(1993)1319–1328.[14]J.N.Murray,Electrochemical test methods for evaluating organic coatings onmetals:an update.Part II:single test parameter measurements,.Coat.31(1997)255–264.[15]I.Sekine,Recent evaluation of corrosion protective paintfilms byelectrochemical methods,.Coat.31(1997)73–80.[16]L.F.Jaffe,R.Nuccitelli,An ultrasensitive vibrating probe for measuring steadyextracellular currents,J.Cell Biol.63(1974)614–628.[17]H.S.Isaacs,Initiation of stress corrosion cracking of sensitized type304stainless steel in dilute thiosulfate solution,J.Electrochem.Soc.135(1988) 2180–2183.[18]H.S.Isaacs,The measurement of the galvanic corrosion of soldered copperusing the scanning vibrating electrode technique,Corros.Sci.28(1988)547–558.[19]J.Elvins,J.H.Sullivan,J.A.Spittle,D.A.Worsley,Short term predictive testingfor cut edge corrosion resistance in zinc–aluminium alloy galvanised steels, Corros.Eng.Sci.Tech.40(2005)43–50.[20]J.He,Applications of the Scanning Vibrating Electrode Technique to the Studyof Corrosion Protection by Conductive Polymers,Ph.D.Thesis,North Dakota State University,2002.[21]H.Krawiec,V.Vignal,R.Oltra,Use of the electrochemical microcell techniqueand the SVET for monitoring pitting corrosion at MnS inclusions,Electrochem.Commun.6(2004)655–660.M.Yan et al./Corrosion Science52(2010)2636–26422641。
表面处理简介_防腐

EC painting
Electroplated coating of Tin Y 108
Y 108
Electroplated coating of Zinc with chromating Y 105
Y 105
Electroplated coatings of zinc-iron with chromating Phosphating Y 104 Painting Y 520 Zinc-chromate metal and organic coating painting Y 500 painting Y 511 painting Y 550 painting Y 600 painting Y 650 K1,K2,K3,K4
表面处理简介
防腐工艺
目录
一.表面处理的分类 二.金属腐蚀的介绍 三.防腐表面处理方式分类 四.发黑 五.防锈剂 六.热浸锌 七.电镀 八.钝化 九.理方式 一三.防腐能力排序
表面处理的分类
按照表面处理的功用,大致可以分为以下三类:
防腐表面处理 表面处理方式的目的是为了减缓基层材料的腐蚀速度。主要的处理方式如下:
Fe/Zn-Fe C Y104
Y 520 Y 500 Y 511 Y 550 Y 600 Y 650 K1,2,3,4
STD 121-0009 STD 5771,7 STD 121-0006
STD 5752,53 STD 121-0003 STD 121-0004
STD 121-0012
STD 121-0013 STD 5732,11 STD 5732,12 STD 5732,109 STD 1281,21 STD 5732,108 STD 5732,105 STD 5732,104 STD 5742,104
Development of new materials for advanced coatings

Development of new materials foradvanced coatingsIntroductionAdvanced coatings play a pivotal role in enhancing the durability, sustainability, and performance of various industrial products. The development of new materials is crucial to the advancement of this field. In this article, we will discuss the importance of developing new materials for advanced coatings and the latest innovations in this area.Importance of Developing New Materials for Advanced CoatingsAdvanced coatings have a wide range of applications, from aerospace and automotive to electronics and medical devices. These coatings need to meet specific requirements in terms of performance, durability, and sustainability. Therefore, it is important to develop new materials that can meet these requirements and offer novel properties that can improve the performance of coatings.The development of new materials for coatings can lead to cost savings and increased efficiency in manufacturing processes. For instance, by using materials that are easier to handle and have lower toxicity levels, manufacturers can reduce the cost of production and make the manufacturing processes more environmentally friendly.Moreover, new materials can provide a competitive advantage to companies that use them. For instance, a company that can develop coatings that offer better scratch resistance or corrosion protection than those of their competitors will have an edge in the market.Innovations in New Materials for Advanced CoatingsNew materials for advanced coatings are being developed using various approaches, including nanotechnology, biomimetics, and advanced composites.Nanotechnology involves the manipulation of materials at the atomic and molecular level to produce coatings with unique properties. For example, nano-coatings made from materials such as carbon nanotubes or graphene offer exceptional strength, flexibility, and durability.Biomimetics involves the study of living organisms and their natural processes to develop materials with similar properties. For instance, coatings made from materials that mimic the properties of shark skin can reduce water turbulence and drag.Advanced composites are materials made from two or more different materials that offer enhanced properties. For example, coatings composed of metal and ceramic composites can offer exceptional wear resistance and temperature stability.ConclusionIn conclusion, the development of new materials for advanced coatings is crucial for the advancement of this field. New materials can lead to cost savings, increased efficiency, and a competitive advantage for companies. Innovations in nanotechnology, biomimetics, and advanced composites are offering novel solutions for the development of advanced coatings with unique properties. As the demand for advanced coatings continues to grow, the development of new materials will play a significant role in meeting the needs of various industries.。
corrosion reviews分区

corrosion reviews分区1. Auto Products: Customers may review corrosion protection products specifically designed for automobiles, such as rust inhibitors or undercoating sprays. These reviews may focus on how well the product prevents corrosion and if it effectively prolongs the life of the vehicle.2. Industrial Equipment: This category may include reviews for coatings, paints, and treatments that offer corrosion resistance for industrial equipment. Customers may comment on the durability of the product and its ability to withstand harsh environmental conditions.3. Marine & Boating: Reviews in this section may cover corrosion protection products for boats and other marine equipment. Customers may discuss the effectiveness of anti-corrosion coatings or treatments in saltwater and freshwater environments.4. Household: This section may feature reviews for corrosion-resistant products used in everyday household items, such as stainless steel appliances, faucets, or plumbing fixtures. Customers may comment on the product's ability to resist rust or tarnish over time.5. Infrastructure & Construction: Reviews in this category may focus on corrosion protection solutions for infrastructure and construction projects. Customers may discuss the effectiveness of coatings or treatments in preventing corrosion on bridges, pipelines, or building structures.6. Electronics: This section may include reviews for corrosion protection products for electronic devices and circuits. Customers may comment on the product's ability to prevent corrosion caused by moisture or other environmental factors.7. Outdoor & Recreation: Reviews in this section may cover corrosion protection products for outdoor equipment, such as camping gear, bicycles, or gardening tools. Customers may discuss the product's effectiveness in preventing rust and maintaining the equipment's functionality.8. Metalworking & DIY: This category may include reviews for corrosion inhibitors or treatments used in metalworking projects or DIY applications, such as rust preventatives for tools or metal surfaces. Customers may comment on the product's ease of use and its long-term effectiveness in preventing corrosion.These are just a few potential categories that could exist within the "corrosion reviews" section, as the specific products and industries can vary.。
- 1、下载文档前请自行甄别文档内容的完整性,平台不提供额外的编辑、内容补充、找答案等附加服务。
- 2、"仅部分预览"的文档,不可在线预览部分如存在完整性等问题,可反馈申请退款(可完整预览的文档不适用该条件!)。
- 3、如文档侵犯您的权益,请联系客服反馈,我们会尽快为您处理(人工客服工作时间:9:00-18:30)。
Printed in Great Britain.
0010-938X/93 $6.00 + 0.00 Pergamon Press Ltd
NEW COATINGS FOR THE CORROSION PROTECTION OF STEEL PIPELINES AND PILINGS IN SEVERELY AGGRESSIVE ENVIRONMENTS GEORGE M. HARRISand
ELEVATED TEMPERATURE TESTING
The elevated temperature pipeline coating which is the subject of this paper> has been tested at elevated temperatures in the laboratories of 14 international pipeline companies who operate high temperature pipelines. This high temperature coating is
ALAN LORENZ
பைடு நூலகம்
The Tapecoat Company, 1527 Lyons Street, P.O. Box 631, Evanston, IL 60204-0631, U.S.A.
Abstract--Two of the most aggressive corrosion environments for steel structures are elevated temperatures and exposure in the marine tidal and splash zone areas. There are now cold applied tape based products available which protect steel pipe or pilings exposed in these environments. These two distinct coatings are cold-applied systems and may be used as coatings on original projects or as rehabilitation coatings. The elevated temperature coating is a three layer system comprised of a high temperature liquid adhesive (primer) and a tape made from a heat resistant multiple alloy polymer with a high temperature resistant adhesive. This high temperature pipeline coating has been proven effective by high temperature testing in 14 pipeline industry laboratories and by field experiences by 30+ pipeline operators all over the world. The upper temperature limit for this high temperature tape system is 121°C (250°F). The coldapplied coating for steel circular pilings in marine environments is a six layer composite module which combines corrosion inhibitors and high mechanical strength. The modules are drawn around the piling by a mechanical closure mechanism either above or below the tide level during installation. The technical aspects of formulation, construction and installation of this protective system will be discussed.
1417
1418
G.M. HARRIS A. LORENZ and
a tape system. The coating is a three layer system consisting of one layer of a special high temperature primer and two layers of a high temperature tape: This high temperature tape has a specifically formulated multi-polymer alloy backing and a high temperature elastomeric adhesive. The tape is applied over a resin based high temperature adhesive primer. The tape is 0.625 mm (25 mils) thick. The backing is 0.25 mm (10 mils) thick and the adhesive is 0.375 mm (15 mils) thick. Two layers of the tape are always applied separately to produce a total system thickness of 1.25 mm (50 mils). The elevated temperature tests to which this high temperature tape system has been subjected to are resistance to: (i) cathodic disbonding, (ii) impact, (iii) penetration, (iv) abrasion and (v) chemical and electrical property changes. One other test is usually added to the usual high temperature series of tests, it is a "boiling water test". This test was introduced by pipeline companies when field experience showed fusion bonded epoxy coatings which had been expected to have good high temperature performance instead perform poorly on pipelines operating in the range of 60°C (140°F) to 82°C (180°F) in wet soil. 2 Resistance to cathodic disbonding at elevated temperatures is considered by most corrosion engineers, who test and evaluate pipeline coatings, as the most important property and the most indicative of a materials ability to work at high temperatures. Because of this strongly held belief, tests for measuring the resistance to cathodic disbonding at elevated temperatures are used as the first test and very often as the main, if not only, screening test for prospective high temperature coating materials. ELEVATED TEMPERATURE CATHODIC DISBONDING Cathodic disbonding tests used by pipeline industry laboratories include two variations from laboratory to laboratory: The test temperatures vary, as the testing temperatures are chosen to match the operating conditions of each company's pipelines. The methods of providing and controlling the temperature of the test specimen may be either by heating the external liquid test media or by internally heating the test specimens and cooling the liquid test media. When the coated test specimens are heated from within, the test conditions best correlate with actual pipeline operating conditions. In this case, the temperature of the pipe specimens, like the temperature of the pipeline, is maintained within a few degrees and the heat radiates from the test specimen, as it does from a pipeline, to the surrounding environment. In this configuration the temperatures decrease as the distances away from the hot pipe increase and there are temperature drops across the wall of the pipe, the thickness of the coating and then through the external environment. When the heat in an elevated temperature cathodic disbonding test is supplied to the test media in order to control the temperature the correlation to actual operating conditions is poor, because the heat is driven from the test solutions, i.e. from the environment through the coatings and then to the pipe specimens. In this case the coating and the external environment are at the same temperature, and no temperature gradients exists across the pipe specimen, the coating and the environment interfaces as they do on actual hot pipelines. It follows then, at any given test temperature, that the coating is exposed to higher temperatures when the test media is heated than when the pipe specimen is