应变状态下ZL114A铝合金低周疲劳行为的研究
《2024年铝合金车轮双轴疲劳试验数值模拟研究》范文

《铝合金车轮双轴疲劳试验数值模拟研究》篇一一、引言随着汽车工业的快速发展,铝合金车轮因其轻量化、耐腐蚀性及高强度等优点得到了广泛的应用。
为了评估铝合金车轮在长期使用中的可靠性和耐久性,双轴疲劳试验成为了关键性的检测手段。
然而,传统试验方法存在成本高、周期长等问题。
因此,本文提出了一种铝合金车轮双轴疲劳试验的数值模拟研究方法,旨在为实际试验提供理论依据和优化方向。
二、研究背景及意义铝合金车轮因其优异的性能在汽车行业中得到了广泛应用。
然而,在长期使用过程中,车轮可能会受到各种复杂应力的作用,导致疲劳损伤。
双轴疲劳试验是评估车轮疲劳性能的重要手段,但传统试验方法存在诸多不足。
因此,开展铝合金车轮双轴疲劳试验的数值模拟研究具有重要的理论意义和实际应用价值。
三、数值模拟方法及模型建立1. 数值模拟方法本研究采用有限元法进行数值模拟。
有限元法通过将连续体离散成有限个单元,对每个单元进行分析,从而得到整个结构的近似解。
该方法在处理复杂问题时具有较高的精度和效率。
2. 模型建立在建立铝合金车轮双轴疲劳试验的数值模型时,需要考虑车轮的几何形状、材料属性、边界条件等因素。
首先,根据实际车轮的几何形状建立三维模型;其次,赋予模型正确的材料属性,包括弹性模量、泊松比、屈服强度等;最后,设置边界条件,包括加载方式、约束条件等。
四、双轴疲劳试验过程模拟1. 加载方式在双轴疲劳试验中,车轮受到复杂的应力作用。
因此,在数值模拟中需要设置合理的加载方式,以模拟实际试验中的应力状态。
本研究采用循环加载方式,通过设置不同的循环次数和应力水平来模拟不同工况下的车轮疲劳性能。
2. 疲劳损伤分析在双轴疲劳试验过程中,车轮会受到循环应力的作用,导致疲劳损伤。
为了评估车轮的疲劳性能,需要对损伤进行定量分析。
本研究采用基于应变-寿命曲线的疲劳损伤分析方法,通过计算各部位的应变能量密度来评估车轮的疲劳性能。
五、结果与讨论1. 结果展示通过数值模拟,我们得到了铝合金车轮在双轴疲劳试验过程中的应力分布、应变能量密度等关键数据。
ZL114A合金疲劳行为研究
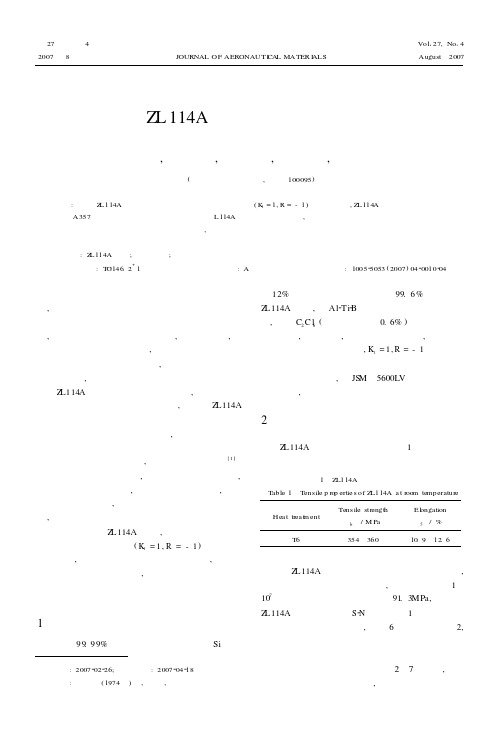
第27卷 第4期2007年8月 航 空 材 料 学 报JOURNAL OF AERONAUTI CA L MATER I ALSVol 127,No 14 August 2007ZL 114A 合金疲劳行为研究周永江, 熊艳才, 洪润洲, 姚惟斌, 张 喆(北京航空材料研究院,北京100095)摘要:研究Z L114A 合金的拉伸性能和轴向应力疲劳行为(K t =1,R =-1)。
结果表明,Z L114A 合金的疲劳性能与美国A357合金的疲劳性能相当。
系统研究了L114A 合金疲劳损伤特征,分析疏松、夹杂物等铸造缺陷在疲劳裂纹的形核、裂纹的扩展以及瞬断中所起的作用,表明铸造过程中形成的铸造缺陷数量、尺寸、位置对金属的疲劳性能都有不同程度的影响。
关键词:Z L114A 合金;疲劳性能;铸造缺陷中图分类号:T G146.2+1 文献标识码:A 文章编号:100525053(2007)0420010204收稿日期226;修订日期228作者简介周永江(—)男,硕士,从事铸造铝合金及铝合金精密铸造工艺的研究和开发工作。
飞行器部件要求重量轻、整体结构好、可靠性高,因此对飞行器结构件的结构和性能提出了越来越高的要求。
许多结构件工作时所承受的是交变应力,应力通常远低于材料屈服强度,但频率较高,时间较长。
在这种交变载荷下,构件会发生疲劳断裂。
因此研究金属材料的疲劳行为,对于结构件的设计、选材和生产,都有重大的科学意义和工程应用价值。
Z L114A 合金为高强度铸造铝合金,近年来广泛应用在航空航天等高性能结构件中,但针对Z L114A 合金的疲劳性能的研究在国内未见报道。
铸造铝合金的疲劳性能受诸多因素的影响,如结晶后枝晶间距、晶粒大小、疏松、夹杂物以及弥散质点等都会影响疲劳裂纹的形成和扩展,从而影响疲劳性能[1]。
铝合金铸件在铸造过程中,会形成不同程度的缺陷,如缩孔、疏松、夹杂物等,由于这些缺陷的存在,当铸件受到交变应力时,疲劳性能会受到不同程度的影响,影响程度主要取决于缺陷的形态、大小、和缺陷的位置等。
AZ91D应变状态下低周疲劳行为的研究
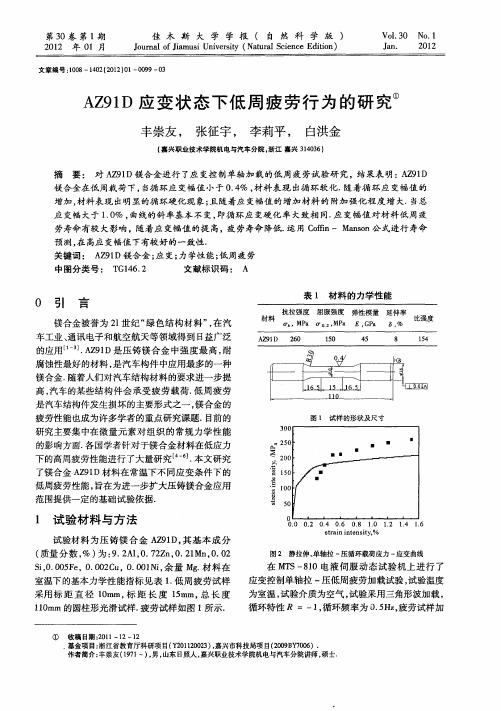
10 0
佳 木 斯 大 学 学 报 (自 然 科 学 版 )
21 0 2年
载的应变幅值分别为 06 ,.% ,.% ,.% . .% 0 8 10 12
疲 劳失 效 判据 为 各应 变 水 平下 的疲 劳 断裂 寿 命 ,按该应 变水平 下 的最 大 载 荷 衰减 到它 的 7% 5 时 的循 环数 . 个数 据点 测定 3~ 每 5个 合格试 样 , 然 后取平 均值 , 定其 应 变 载 荷 下 的疲 劳 寿命 . 验 确 试 加载控 制参数 及试验 结果 如表 2所示 .
第3 O卷 第 l期
21 年 0 月 02 1
佳 木 斯 大 学 学 报 ( 自 然 科 学 版 ) Ju a o i ui nvri N t a SineE io ) o r l f a s U i sy( a rl c c dt n n Jm e t u e i
Vo . O No 1 13 .
( 质量 分 数 , ) : . A , . 2 n 0 2 M , . 2 % 为 9 2 10 7 Z , . 1 n 0 0
图 2 静拉伸、 单轴拉 一 压循 环载荷应力 一 应变曲线
S,.0 F , .0 C , .0 N , i 05 e 0 02 u 0 0 1 i余量 M . 0 g材料在
命变化不 大 , 环应 变 幅值 大于 04 , 当循 .% 随着应 变 幅值增 大 , 料的低周疲 劳寿命 明显降低 . 材 许 多学 者 在研 究 其 它 不 同材 料 的疲 劳损 伤过
拉 伸状态 下 的应力 一应 变 曲线 , 析 可知 , 材料 分 该
在应变幅值为 04 .%时 , 材料由循环软化开始向循 环强化转变 , 并随应变幅值 的增加附加硬化程度明 显 增大 . 图 2 应 变 幅值 的大 小 对 材 料 疲 劳 寿命 如 ,
《2024年铝合金车轮双轴疲劳试验数值模拟研究》范文

《铝合金车轮双轴疲劳试验数值模拟研究》篇一一、引言随着汽车工业的快速发展,铝合金车轮因其轻量化、高强度、耐腐蚀等优点,正逐渐成为汽车制造行业的主流选择。
然而,在车辆使用过程中,车轮需承受来自双轴的复杂应力与疲劳载荷,因此对铝合金车轮的疲劳性能进行准确评估显得尤为重要。
本文将通过数值模拟的方法,对铝合金车轮双轴疲劳试验进行研究,以期为车轮的设计与制造提供理论支持。
二、铝合金车轮材料与结构特性铝合金车轮因其轻量化、高强度等优点,在汽车制造领域得到广泛应用。
其材料特性包括良好的塑形、较低的密度以及较高的抗腐蚀性。
此外,铝合金车轮的结构设计也需考虑其承受双轴应力与疲劳载荷的能力。
因此,在模拟研究过程中,应充分了解并考虑铝合金车轮的材料与结构特性。
三、双轴疲劳试验数值模拟方法为了研究铝合金车轮的双轴疲劳性能,本文采用数值模拟的方法。
首先,建立铝合金车轮的三维有限元模型,并利用材料力学性能参数对模型进行校准。
其次,根据实际双轴疲劳试验的工况,设定模拟试验的边界条件与载荷。
最后,通过有限元分析软件进行数值模拟,得出铝合金车轮在双轴疲劳试验过程中的应力分布、变形及疲劳寿命等情况。
四、模拟结果分析通过对铝合金车轮双轴疲劳试验的数值模拟,我们得到了以下结果:1. 应力分布:在双轴疲劳试验过程中,铝合金车轮的应力分布呈现出明显的非均匀性。
其中,轮辐与轮盘连接处、轮盘边缘等部位的应力较大。
这些部位在长期承受双轴应力与疲劳载荷的过程中,容易出现裂纹、断裂等损伤。
2. 变形情况:在双轴疲劳试验过程中,铝合金车轮的变形主要表现为弹性变形和塑性变形。
其中,弹性变形在加载过程中可恢复,而塑性变形则会导致车轮永久性的形状变化。
在设计中应考虑这些变形对车轮性能的影响。
3. 疲劳寿命:通过数值模拟,我们可以得出铝合金车轮在不同工况下的疲劳寿命。
结果表明,铝合金车轮的疲劳寿命受多种因素影响,如材料性能、结构设计、载荷大小及频率等。
在实际设计和制造过程中,应综合考虑这些因素以提高车轮的疲劳寿命。
ZL114A合金整体铸件力学性能稳定性研究论文
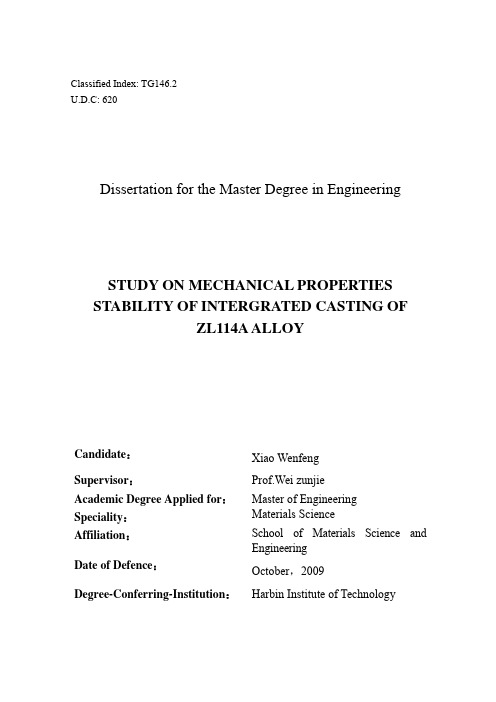
Classified Index: TG146.2U.D.C: 620Dissertation for the Master Degree in EngineeringSTUDY ON MECHANICAL PROPERTIESSTABILITY OF INTERGRATED CASTING OFZL114A ALLOYCandidate:Xiao WenfengSupervisor:Prof.Wei zunjieAcademic Degree Applied for:Master of EngineeringSpeciality:Materials ScienceAffiliation:School of Materials Science andEngineeringDate of Defence:October,2009Degree-Conferring-Institution:Harbin Institute of Technology摘要本文以提高航天用ZL114A合金铸件整体剖切力学性能为研究目标,研究了ZL114A合金主要元素和微量元素加入量对合金力学性能影响规律,Al-Ti-B细化剂和Sr变质剂加入量对Al-7Si合金组织和力学性能作用规律,以及细化和变质对阶梯试样、附铸试样作用效果对比。
以上述研究结果为基础,通过工艺调整,显著提高铸件整体剖切性能。
对ZL114A合金主要元素和微量元素加入量对合金力学性能影响规律研究结果表明,合金中Si含量增加较多的情况下铸件的抗拉强度和屈服强度均有较大提高,但伸长率显著降低。
少量增加合金中Mg元素的含量对抗拉强度影响显著性不大,但能够显著提高铸件的屈服强度,降低伸长率。
ZL114A合金中添加微量Cu元素对对抗拉强度和伸长率影响不大,但铸件的屈服强度获得提高。
对Al-Ti-B细化剂和Sr变质剂加入量对Al-7Si合金组织和力学性能作用规律进行了研究,结果表明合金变质效果最好的Sr加入量为0.04%左右,最佳Ti加入量为0.2%,此时合金的综合力学性能最好。
铝合金材料的疲劳行为研究进展
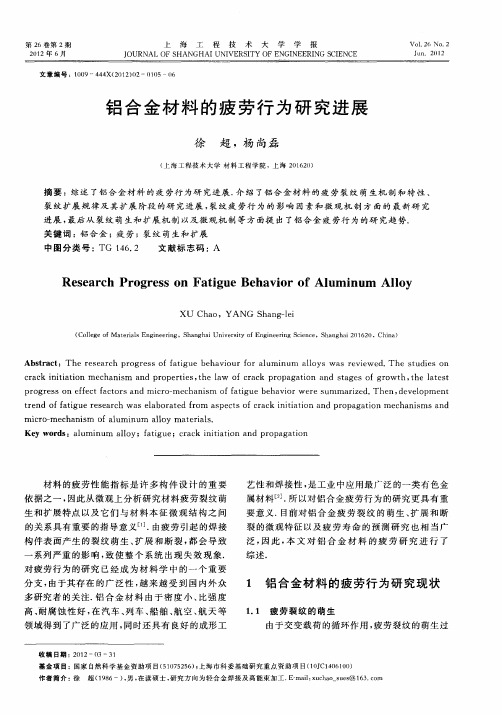
文 章 编 号 : 0 9 4 X(0 2 ( 一( ( 一( 1 0 —4 4 2 1 )2 ) ) 1 t 15 6
铝 合 金 材 料 的 疲 劳 行 为 研 究 进 展
徐 超 ,杨 尚 磊
( 海 工程 技 术 大 学 材 料 工 程学 院 ,上 海 2 1 2 ) 上 0 6 0
摘 要 :综 述 了铝 合 金 材 料 的 疲 劳行 为 研 究进 展 . 绍 了铝 合 金 材 料 的 疲 劳 裂 纹 萌 生 机 制 和 特 性 、 介
中 图 分 类 号 : 4 . TG 16 2 文献标 志码 : A
Re e r h Pr g e s o tg e Be v o fA l m i u Alo s a c o r s n Fa i u ha i r o u n m l y
X U Cha o, Y A N G a —e Sh ng l i
综述 .
系列严 重 的影 响 , 使 整个 系统 出现 失 效 现象 . 致
对疲 劳 行为 的研 究 已经 成 为 材 料学 中 的一 个 重 要
分支 , 由于其存 在 的广 泛性 , 越来 越 受 到 国 内外众 多研 究者 的关 注. 合 金材 料 由于 密 度 小 、 铝 比强度
依 据之 一 , 因此从 微观 上分 析研究 材料 疲劳 裂纹 萌 生 和扩 展特点 以及 它们 与 材 料 本 征微 观 结 构 之 间 的关 系具有 重要 的指导 意义 _ . 1 由疲劳 引起 的焊 接 ] 构 件表 面产 生 的裂 纹 萌生 、 扩展 和 断 裂 , 会 导 致 都
一
收 稿 日期 : 0 2—0 —3 21 3 1
基 金 项 目 :国 家 自然 科 学 基 金 资 助 项 目( 17 2 6 ; 50 55 ) 上海 市 科 委 基 础 研 究 重 点 资 助 项 目( OC 4 6 0 ) 1J 1 0 1 0
交变法向载荷作用下2024_铝合金的微动疲劳试验研究

Journal of Mechanical Strength2023,45(4):962-969DOI :10.16579/j.issn.1001.9669.2023.04.028∗20211118收到初稿,20220112收到修改稿㊂国家自然科学青年基金项目(51905028),北京市教育委员会科技计划一般项目(KM202110016002),北京建筑大学金字塔人才培养工程(JDYC20200323)资助㊂∗∗张育轩,男,1997年生,北京人,满族,北京建筑大学硕士研究生,主要研究方向为微动疲劳㊂∗∗∗李㊀欣(通信作者),男,1984年生,河北昌黎人,汉族,北京建筑大学副教授,博士,硕士研究生导师,主要研究方向为机械结构强度和疲劳耐久性㊂交变法向载荷作用下2024铝合金的微动疲劳试验研究∗EXPERIMENTAL STUDY ON FRETTING FATIGUE OF 2024ALUMINUM ALLOY UNDER ALTERNATING NORMAL LOAD张育轩∗∗1㊀李㊀欣∗∗∗1㊀杨建伟1,2㊀田㊀帅1㊀刘乐强1(1.北京建筑大学机电与车辆工程学院,北京100044)(2.城市轨道交通车辆服役性能保障北京市重点实验室,北京100044)ZHANG YuXuan 1㊀LI Xin 1㊀YANG JianWei 1,2㊀TIAN Shuai 1㊀LIU LeQiang 1(1.School of Mechanical-Electrical and Vehicle Engineering ,Beijing University of Civil Engineering and Architecture ,Beijing 100044,China )(2.Beijing Key Laboratory of Performance Guarantee on Urban Rail Transit Vehicles ,Beijing 100044,China )摘要㊀针对法向交变载荷作用下的2024铝合金微动疲劳失效问题开展了试验研究㊂设计了可施加交变法向载荷与远端载荷的双轴加载微动疲劳试验系统㊂通过Abaqus 有限元分析,对试验台法向加载装置进行分析计算,考察了法向加载时力传导误差与微动垫摆角对试验精度的影响,验证了试验机加载的精度㊂进而研究了在交变法向载荷作用下,0ʎ㊁45ʎ㊁90ʎ三种不同相位差对2024铝合金疲劳寿命的影响㊂试验结果表明,随着相位差的增加,2024铝合金试件的寿命逐渐增加㊂通过对磨损状态的分析发现,0ʎ与45ʎ相位差下,磨损的影响较小,寿命随着相位差的增大而增长;90ʎ相位差时磨损较为严重,在磨损与疲劳损伤的共同作用下,90ʎ相位差状态下试件的疲劳寿命进一步增加㊂试件微动疲劳寿命在交变法向载荷作用下的整体趋势为:随着相位差的增加寿命延长,随着相位差的增加,磨损增加㊂关键词㊀微动疲劳㊀交变法向载荷㊀2024铝合金㊀有限元分析中图分类号㊀TH114Abstract ㊀Fretting fatigue failure of 2024aluminum alloy under alternating normal load was investigated.A biaxial fretting fatigue test system is designed which can apply alternating phase load and distal load.Through Abaqus finite element analysis,the normal loading device of the test bench was analyzed and calculated,and the influence of the force conduction error and the swing angle of the fretting pad on the test accuracy was investigated,the accuracy of loading test machine is verified.The influence of phase difference of 0ʎ,45ʎand 90ʎon fatigue life of 2024aluminum alloy under alternating normal load was studied.The test results show that the life of 2024aluminum alloy specimens increases with the increase of phase difference.Through the analysis of wear state,it is found that the influence of wear is small when the phase difference is 0ʎand 45ʎ,and the life increases with the increase of phase difference.When the phase difference is 90ʎ,the wear is more serious.Under the joint actionof wear and fatigue damage,the fatigue life of specimens at 90ʎphase difference is further increased.The overall trend of fretting fatigue life of specimens under alternating normal load is that the life increases with the increase of phase difference,and the wear increases with the increase of phase difference.Key words㊀Fretting fatigue ;Alternating normal load ;2024aluminum alloy ;Finite element analysis Corresponding author :LI Xin ,E-mail :lixin 0301@ ,Fax :+86-10-61209518The project supported by the National Natural Science Foundation of China (No.51905028),the General Project of Science and Technology Plan of Beijing Education Commission (No.KM202110016002),and the Pyramid Talent Training Project of Beijing University of Civil Engineering and Architecture (No.JDYC20200323).Manuscript received 20211118,in revised form 20220112.㊀第45卷第4期张育轩等:交变法向载荷作用下2024铝合金的微动疲劳试验研究963㊀㊀0㊀引言㊀㊀微动疲劳作为一种物理-化学过程,其机制与演化行为非常复杂,涉及机械强度学㊁摩擦学㊁接触力学和材料学等多个学科㊂微动导致紧固连接结构的接触面发生局部磨损,进而使零部件更容易发生疲劳失效,导致结构疲劳寿命急剧下降㊂另外,微动疲劳现象发生在零部件的接触面内,隐蔽性强,难以及时发现,较常规疲劳问题更为危险㊂微动疲劳广泛存在于机械紧固连接结构中,是螺栓连接㊁榫连接㊁铆接㊁花键连接和过盈配合等结构的主要失效形式㊂因此,微动疲劳引起了航空航天㊁核能㊁交通运输㊁海洋船舶等对安全性和可靠性要求较高的工业部门的高度重视,甚至在生物医学㊁电工行业也出现了因微动疲劳导致的严重失效问题㊂可见,微动问题涉及的工业领城广泛,引起的失效问题突出,因此被称为 工业的癌症 ㊂铝合金不仅具有高的比强度㊁比模量㊁断裂韧度㊁疲劳强度和耐腐蚀稳定性,还具有良好的成形工艺性和焊接性㊂基于上述优点,铝合金在航天工业中应用广泛[1]㊂如表1所示,在一些商业飞机上用量已占整体材料的70%~80%㊂虽然铝合金在航天中应用广泛,但其对微动疲劳非常敏感,如图1所示,英国彗星号客机由于飞机增压舱内方形舷窗处的机身蒙皮产生疲劳断裂,最终引发空难㊂因此对铝合金的微动疲劳研究具有极其重要的工程应用价值和理论研究意义㊂表1㊀主要商业飞机上铝合金的用量Tab.1㊀Aluminum alloy used in major commercial aircraft 年代Eras 飞机型号Plane model 铝合金含量Aluminum alloy content ω/%1960~1970B74781A300761970~1980B76780B75778A32076.51980~1990A34075B777701990至今Since 1990A38060B78720针对上述问题,研究者开展了相关的研究工作㊂张俊等[2]对7075铝合金材料进行了扭转微动疲劳试验,讨论了相同法向载荷下不同扭转切应力对扭转微动疲劳寿命的影响㊂陈旭等[3]研究了恒定接触载荷和交变接触载荷对6061-T651铝合金微动疲劳寿命的影响㊂陈亚军等[4]研究了在航空载荷谱作用下2024铝合金的疲劳特性㊂研究表明,微动能使构件的疲劳寿命降低20%~图1㊀飞机机身蒙皮疲劳断裂图Fig.1㊀Fatigue fracture diagram of aircraft fuselage skin80%,甚至更低㊂自20世纪70年代以来,微动疲劳越来越受到国内外学者的重视㊂试验是研究微动疲劳的重要手段,早期的微动疲劳试验主要采用桥式微动垫结构,随着研究的深入,目前主要采用圆柱面微动垫与平板试件的结构形式进行试验研究[5]86-87㊂乐晓斌等[6]通过对2Cr13进行单轴拉-拉试验结合有限元分析,对微动疲劳寿命预测方法进行了讨论㊂吕宝桐等[7]对16Mn 钢进行试验,研究了接触压力与循环周次等因素对微动疲劳寿命的影响㊂杨洋等[8]对35CrMoA 钢进行单轴拉-拉加载下的微动疲劳试验,研究其微动疲劳特征及其微结构㊂CARLOS N 等[9]通过试验分析了微动疲劳条件下不同多轴疲劳准则对寿命评估的影响㊂刘兵等[10]通过柱面对柱面的接触方式,对35CrMoA 钢在拉扭复合载荷作用下的低周微动疲劳特性进行研究㊂ABBASI F 等[11]通过试验研究了轴向载荷和法向载荷相位差对结构微动行为的影响㊂虽然国内外学者对微动疲劳进行了许多试验研究,但研究都主要集中在拉压与扭转微动疲劳[5]86-87㊂这些试验都是固定法向载荷的㊂然而,在许多实际工程情况下,机械结构受到的法向载荷是不断变化的,对交变法向载荷如何影响微动疲劳行为研究得较少㊂鉴于法向载荷是影响微动行为的重要因素之一,本文开展了交变法向载荷下的微动疲劳试验,研究了双向加载因素对微动疲劳及磨损行为的影响㊂1㊀微动疲劳试验原理与试验机设计1.1㊀双轴加载微动疲劳试验原理㊀㊀接触区域产生微动必须满足:①存在法向载荷P使微动垫与试件接触;②切向力Q 使接触区域产生滑移㊂接触区域间的滑移受到施加的法向载荷P 与切向力Q 的影响,当Q /P 的值小于摩擦因数μ时,接触区域为局部滑移;当Q /P 的值达到μ时,接触区域为全局滑移㊂基于这一原理,微动疲劳试验逐渐形成了如图2所示的统一构型㊂通过夹具将试件在轴向固定,将两块圆柱面或球面的微动垫放置在试件两侧,两微动垫通过固定装置进行固定,该弹性支撑可等效为弹簧㊂施加法向载荷P 使微动垫与试件贴紧建立接㊀964㊀机㊀㊀械㊀㊀强㊀㊀度2023年㊀触,再向试件下端施加轴向的交变载荷σB ,由于有微动垫固定装置即等效 弹簧 的存在,微动垫运动会受到阻碍,在接触区域产生切向力Q ㊂在P ㊁Q ㊁σB 的共同作用下,试件与微动垫的接触区域发生微动㊂通过改变远端载荷大小与 弹簧 的刚度,来调节切向力Q 的大小,从而实现对微动运行状态和微动疲劳行为的控制㊂图2㊀微动疲劳试验模型Fig.2㊀Fretting fatigue test model但此模型存在一定的局限性,在许多实际工程问题上不能完全反应机械的微动情况,其中最典型的例子就是航空发动机燕尾槽处叶片与槽之间的接触问题[12-13]㊂如图3所示,受到轴向离心力F 与气动载荷q 的作用,接触区域的法向载荷是不断变化的㊂恒定法向载荷工况下的微动疲劳试验显然不能真实反应燕尾槽处的微动情况㊂进一步地,还需要考虑双轴加载状态下的比例与非比例加载,即相位差对于微动疲劳寿命的影响㊂因此本文在此模型基础上,设计了双轴加载微动疲劳试验系统㊂图3㊀航空发动机轮盘-叶片燕尾榫连接的微动工况Fig.3㊀Fretting condition of aero-engine wheel-blade dovetail joint1.2㊀双轴加载微动疲劳试验机设计1.2.1㊀试验机总体方案设计㊀㊀基于上述问题与模型,设计了一套新型疲劳试验机系统,通过对单轴拉压电液伺服疲劳试验的改造,通过增加一套法向加载设备,实现法向交变载荷的施加㊂试验机主要包括2个作动器和3个力传感器,通过作动器1施加轴向交变载荷σB ,作动器2施加法向交变载荷P ㊂力传感器1与力传感器3之间的差值即为切向力Q ,力传感器2测量和控制法向交变载荷㊂通过控制器与上位机进行闭环控制与试验数据采集,试验机系统结构如图4所示㊂如图5所示,其中试件通过夹具在轴向进行固定,法向一端与微动垫接触㊂为实现试件与微动垫接触一侧产生微动并保证试验机在法向受力平衡,试验机设计了法向支撑装置,该装置安装在原试验机立柱上,靠近试件一侧安装滚轮,与试件顶紧,用以平衡作动器2施加的法向交变载荷P ㊂在试验过程中,滚轮与试件形成滚动接触,在保证试件加载过程中不发生弯曲变形的同时,降低了该侧的摩擦力,保证试件与滚轮的接触不会产生微动㊂试验机系统实物图如图6所示㊂图4㊀试验机系统结构图Fig.4㊀Structure diagram of testing machinesystem图5㊀微动加载装置Fig.5㊀Fretting loadingdevice 图6㊀试验机系统实物图Fig.6㊀Physical picture of testing machine system1.2.2㊀结构设计和加载误差分析㊀㊀微动垫固定装置如图7所示,为防止微动垫受到切向力时在轴向产生过大摆动,通过4块板搭建的平台与试验机固定,再由上面的盖板与螺栓把微动垫紧固在平台上㊂固定装置中前后两块板可等效为试验模型中的 弹簧 ,通过改变两板的厚度δ,达到改变 弹簧 刚度的目的㊂微动垫所受法向交变载荷P 先通过加载装置施㊀第45卷第4期张育轩等:交变法向载荷作用下2024铝合金的微动疲劳试验研究965㊀㊀加到微动垫固定装置上,再传导到微动垫处,在这之间会存在误差,且不同板厚下有效力误差也会不同;微动垫在受到切向力Q作用时会产生轴向位移S,这些因素都会对试验的准确性产生影响㊂当微动垫受到切向力Q时,微动垫在轴向的位移会存在摆动角度α,且不同板厚下摆角α的大小不同㊂通过建立数学模型来计算微动垫的摆动角度㊂微动垫与试件接触模型如图8所示,把其简化为悬臂梁来计算摆动角度,简化后的悬臂梁如图9所示㊂模型计算过程如下:Q+F A+F B=0-Ql1+FB l2=0{(1)式中,Q为微动垫所受切向力;F A㊁F B为A㊁B两点由于切向力Q产生的形变力;l1为微动垫固定装置前支撑板到微动垫前端距离;l2为两支撑板间距离㊂图7㊀微动垫固定装置Fig.7㊀Fretting pad fixingdevice图8㊀微动垫与试件接触模型Fig.8㊀Contact model between fretting pad andspecimen图9㊀悬臂梁微动垫固定装置的简化分析模型Fig.9㊀Simplified analysis model of cantilever beam fretting pad fixing device㊀㊀解得F A与F B分别为F B=Ql1l2F A=-Q(l2+l1)l2ìîíïïïïï(2)㊀㊀弹簧弹性系数k为k=EA l3(3)式中,E为微动垫固定装置的弹性模量;A为前后支撑板横截面积;l3为上下两支撑板间距离㊂A㊁B两点位移变化分别为Δl A=|F A|k=Q(l2+l1)l2k=Q(l2+l1)l3EAl2(4)Δl B=|F B|k=Ql1l2k=Ql1l3EAl2(5)㊀㊀考虑到微动垫在摆动过程中,微动垫固定台存在扭转中心O,摆动角度即为两相似三角形的对顶角,如图10所示㊂通过相似三角形找到扭转中心O,确定OA与OB的长度:图10㊀微动垫固定装置简化模型的扭转分析Fig.10㊀Torsion analysis of the simplified model of fretting pad fixatorOAOB=Δl AΔlB=F AF B(6)OA=l2F AF A+F B=l2(l2+l1)2l1+l2(7)OB=l2F BF A+F B(8)㊀㊀摆动角α的大小为α=arctanΔl AOA=arctan Ql3(2l1+l2)EAl22(9)㊀㊀通过式(9)可以看出,摆动角α的大小与切向力Q以及板厚有关㊂切向力Q可等效成轴向的摩擦力,可以通过式(10)计算切向力:Q=μP(10)㊀966㊀机㊀㊀械㊀㊀强㊀㊀度2023年㊀式中,Q 为切向力;P 为法向交变载荷;μ为摩擦因数㊂按照文献[13]定义,滑动摩擦因数μ为0.65㊂切向力Q 与法向交变载荷P 的大小有关系,进一步地,通过Abaqus 对法向加载装置进行力学分析㊂对法向加载装置进行了建模,其中对接触区域网格划分进行局部加密,如图11所示㊂图11㊀微动加载装置模型网格划分Fig.11㊀Mesh division of fretting loading device model㊀㊀在1000~3000N 法向载荷下,通过实际施加的载荷F 1与模型计算出的接触区域所受力F 2进行误差计算:F C =(F 1-F 2)/F 1(11)式中,F C 为实际施加载荷与模型计算出接触区所受力之间的误差,得出表2所示的数据㊂表2㊀不同板厚与法向载荷下接触应力误差Tab.2㊀Contact stress error under different plate thickness and normal load板厚Plate thickness δ/mm1000N 法向载荷下误差Error at 1000N normal load F C /%2000N 法向载荷下误差Error at 2000N normal load F C /%3000N 法向载荷下误差Error at 3000N normal load F C /%20.090.080.07630.150.1450.1440.200.190.1851.131.11 1.096㊀㊀由表2可以看出,有效力误差整体很小,仅在5mm 板厚时有效力误差略大,但整体都不超过2%,因此有效力误差对试验的影响很小㊂在1000N㊁2000N㊁3000N 法向载荷下计算出切向力Q ,分别为650N㊁1300N㊁1950N㊂经模型计算后得出微动垫在轴向的位移,如表3所示㊂表3㊀不同板厚与切向力下微动垫位移Tab.3㊀Displacement of fretting pad under different plate thickness and tangential force板厚Plate thickness δ/mm650N 切向力下位移Displacement under tangential force 650N s /mm1300N 切向力下位移Displacement undertangential force 1300N s /mm1950N 切向力下位移Displacement undertangential force 1950N s /mm20.0070.0130.0230.0060.0110.01740.0050.010.01550.00480.00950.014㊀㊀由表3可知,在同一板厚情况下,切向力越大,微动垫上下摆动的角度越大;在同一切向力情况下,板厚越厚,微动垫上下摆动角度越小;但整体来看,微动垫在竖直方向的位移都是很小的,对于试验整体的影响不大,证明试验加载是准确的㊂结合上述提到的有效力误差,存在最优板厚,使摆动角度与有效力误差对试验影响最小㊂绘制了如图12所示的支撑板板厚与加载精度关系,两曲线交点即为最优板厚所在的点㊂由图12可以看出,最优板厚为3.6mm㊂因此试验时微动垫固定台板厚选取3.6mm㊂2㊀试验参数设计㊀㊀由于施加的均为交变载荷,所以在加载时存在两种情况:①同比例加载;②非比例加载,即存在相位差㊂本试验主要考虑非比例加载下对试件微动疲劳寿命的影响,相位差φ分别选取0ʎ㊁45ʎ㊁90ʎ,与P 的关系可表示为㊀第45卷第4期张育轩等:交变法向载荷作用下2024铝合金的微动疲劳试验研究967㊀㊀图12㊀支撑板板厚与加载精度的关系Fig.12㊀Relationship between plate thickness andloading accuracy of support plateP =P m +P a sin(ωt -φ)σB =σB,m +σB,a sin(ωt ){(12)式中,轴向载荷均值σB,m 设为0MPa;幅值σB,a 设为100MPa㊂根据试验系统的法向加载能力,设置法向接触力范围为140~200MPa㊂通过赫兹接触公式[14]:P 0=FE ∗πR ∗(13)式中,P 0为接触压力;F 为施加的法向力;E ∗为两弹性体的等效弹性模量,即1E ∗=1-μ21E 1+1-μ22E 2(14)式中,E 1㊁E 2分别为两弹性体的弹性模量;μ1㊁μ2分别为两弹性体的泊松比㊂1R ∗=1R 1+1R 2(15)式中,R ∗为等效曲率半径;R 1㊁R 2分别为两接触面的曲率半径㊂计算出法向力的加载范围为2960~6041N,法向施加的为压力,设置法向载荷均值P m 为-4.5kN,法向载荷幅值P a 为1.54kN㊂为保证试验的精准性,每相位差下进行2组试验,全部试验参数如表4所示㊂表4㊀试验参数Tab.4㊀Experimental parameters编号Number 法向载荷均值Mean value of normal load P m /kN法向载荷幅值Amplitude of normalload P a /kN轴向载荷均值Mean value of axial load σB,m /MPa轴向载荷幅值Axial load amplitudeσB,a /MPa板厚Plate thicknessδ/mm相位差Phase differenceφ/(ʎ)1-4.5 1.540100 3.602-4.5 1.540100 3.603-4.5 1.540100 3.6454-4.5 1.540100 3.6455-4.5 1.540100 3.6906-4.51.541003.690㊀㊀试验试件采用狗骨型结构,微动垫与试件的接触面为圆柱面㊂试件和微动垫的材料均为2024铝合金,弹性模量E =70300MPa,泊松比μ=0.345㊂试验前将试件和微动垫接触表面进行抛光处理,试验在标准实验室环境下进行(室温在21~24ħ之间,相对湿度在65%~75%之间)㊂试件与微动垫尺寸如图13所示㊂图13㊀试件与微动垫尺寸Fig.13㊀Dimensions of specimen and fretting pad3㊀试验分析3.1㊀试件形貌与寿命分析㊀㊀微动面是指微动疲劳试样与微动垫相互接触处的面,在微动疲劳过程中,由于微动面承受垂直方向的接触压力和切向的相对滑移,微动疲劳裂纹往往萌生于微动面,从而导致疲劳试样过早的断裂㊂图14所示为在同一轴向交变载荷与法向交变载荷,不同相位差作用下微动面的形貌㊂由图14可以看出,随着相位差的增加,微动面上滑移区面积增大,黏着区面积减小;相位差为90ʎ时,滑移区表面覆盖着较多的黑色氧化层,试件的磨损最为严重㊂不同相位差下的微动疲劳寿命如图15所示㊂由图15可见,随着相位差的增加,试件的微动疲劳寿命也随之增加㊂出现这个现象的原因是:随着相位差的增加,试件微动面滑移区范围增大,试件磨损增加,萌生的细小裂纹在磨损过程中被磨掉,延长了试件的微动疲劳寿命㊂3.2㊀微动疲劳断口分析㊀㊀本试验中相位差为0ʎ时,试件始终处于局部滑移㊀968㊀机㊀㊀械㊀㊀强㊀㊀度2023年㊀㊀㊀㊀㊀图14㊀微动面形貌Fig.14㊀Morphology of frettingsurface图15㊀不同相位差下的微动疲劳寿命Fig.15㊀Fretting fatigue life under different phase differences状态,相位差为90ʎ时,试件出现较大磨损,因此两相位差下的断口形貌具有明显区别㊂如图16所示,其中箭头标出的位置为裂纹源㊂图17为疲劳断口的典型形貌图㊂由图17可以看出,微动疲劳断口具有一般疲劳断口的显著特征,可分为3个区域,即裂纹源区㊁裂纹扩展区和瞬间断裂区㊂其中,可以清晰看到在扩展㊀㊀区存在解理状形貌,在瞬断区可清晰看到韧窝㊂通过观察0ʎ相位差与90ʎ相位差可以看出裂纹源均产生于接触边界,0ʎ相位差接触侧呈现多裂纹源状态,且断口表面凹凸不平㊂随着相位差的增加断疲劳断口呈现单一裂纹源状态㊂这个结果可以解释为:法向载荷与远端载荷的共同作用导致接触区边缘应力集中,在交变应力/应变的主导下,接触区边缘疲劳损伤最大,在接触区边缘宽度方向上产生多条疲劳裂纹并不断扩展融合最终导致疲劳断裂,但由于相位的增加使接触面处磨损增大,阻碍了多源裂纹的萌生和扩展,最终相位差为90ʎ时断口处呈现单一裂纹源萌生和扩展的状态㊂由此可知,随着相位差的增加,导致接触区微动状态的改变㊂微动状态从局部滑移逐步向全局滑移转变㊂2024铝合金微动疲劳行为逐渐由以应力-应变主导的机制转变为磨损影响逐渐增强的疲劳-磨损耦合机制㊂图16㊀不同相位差下疲劳断口形貌Fig.16㊀Fatigue fracture morphology under different phasedifferences图17㊀典型微动疲劳断口放大图Fig.17㊀Enlarged view of typical fretting fatigue fracture4 结论㊀㊀应用试验与数值分析相结合的方法对微动疲劳现象进行了系统的研究㊂应用有限元法建立了微动疲劳试验机法向加载装置模型,验证了试验机加载的精准性,建立了微动疲劳试验系统,对微动疲劳进行了试验㊀第45卷第4期张育轩等:交变法向载荷作用下2024铝合金的微动疲劳试验研究969㊀㊀研究,得出以下结论:1)本文设计了一套可施加法向交变载荷的微动疲劳试验系统,通过Abaqus对法向加载设备进行建模,验证了法向加载设备中力传导误差与微动垫在切向力下产生的位移对试验基本没有影响㊂利用该装置完成了对2024铝合金在法向交变载荷不同相位差下的微动疲劳试验,微动疲劳试验系统工作稳定㊂2)在同一法向交变载荷作用下,低相位差下断口处呈现 波浪状 花纹,随着相位差的增加,微动面处滑移区增大㊁黏着区减小,试件磨损变得严重,裂纹源减少, 波浪状 花纹消失,试件从多源裂纹萌生状态转变为单一裂纹源萌生状态㊂3)相位差的大小影响试件的微动运行机制和疲劳寿命㊂随着相位差的增加,微动状态从局部滑移逐步转变为全局滑移㊂2024铝合金微动疲劳行为逐渐由以应力-应变主导的机制转变为磨损影响逐渐增强的疲劳-磨损耦合机制㊂随着相位差的增加,微动疲劳寿命也随之增加㊂参考文献(References)[1]㊀张新明,刘胜胆.航空铝合金及其材料加工[J].中国材料进展,2013,32(1):39-55.ZHANG XinMing,LIU ShengDan.Aviation aluminum alloy andmaterial processing[J].Progress of Materials in China,2013,32(1):39-55(In Chinese).[2]㊀张㊀俊,彭金方,徐志彪,等.7075铝合金扭转微动疲劳行为研究[J].摩擦学学报,2017,37(6):854-862.ZHANG Jun,PENG JinFang,XU ZhiBiao,et al.Torsional frettingfatigue behavior of7075aluminum alloy[J].Tribology,2017,37(6):854-862(In Chinese).[3]㊀陈㊀旭,李建军,陈㊀刚,等.交变接触载荷下的铝合金微动疲劳[J].天津大学学报(自然科学与工程技术版),2017,50(5):459-465.CHEN Xun,LI JianJun,CHEN Gang,et al.Fretting fatigue ofaluminum alloy under alternating contact load[J].Journal of TianjinUniversity(Natural Science and Engineering Technology),2017,50(5):459-465(In Chinese).[4]㊀陈亚军,王艾伦,王付胜,等.在航空载荷谱作用下2024铝合金的疲劳行为[J].航空材料学报,2016,36(5):64-69.CHEN YaJun,WANG AiLun,WANG FuSheng,et al.Fatiguebehavior of2024aluminum alloy under aviation load spectrum[J].Journal of Aeronautical Materials,2016,36(5):64-69(In Chinese).[5]㊀沈明学,彭金方,郑健峰,等.微动疲劳研究进展[J].材料工程,2010(12):86-91.SHEN MingXue,PENG JinFang,ZHENG JianFeng,et al.Researchprogress of fretting fatigue[J].Materials Engineering,2010(12):86-91(In Chinese).[6]㊀乐晓斌,何明鉴.微动疲劳寿命预测方法的探讨[J].机械强度,1996,18(3):53-55.LE XiaoBin,HE MingJian.Discussion on fretting fatigue life predictionmethod[J].Journal of Mechanical Strength,1996,18(3):53-55(InChinese).[7]㊀吕宝桐,李东紫,郑修麟.16Mn钢的微动疲劳寿命[J].机械强度,1991,13(3):37-41.LÜBaoTong,LI DongZi,ZHENG XiuLin.Fretting fatigue life of16Mn steel[J].Journal of Mechanical Strength,1991,13(3):37-41(In Chinese).[8]㊀杨㊀洋,何国球,刘㊀兵,等.35CrMoA微动疲劳特性及其微结构研究[J].功能材料,2014,45(2):2077-2081.YANG Yang,HE GuoQiu,LIU Bing,et al.Fretting fatiguecharacteristics and microstructure of35CrMoA[J].Journal ofFunctional Materials,2014,45(2):2077-2081(In Chinese).[9]㊀CARLOS N,SERGIO M,JAIME D.On the use of multiaxial fatiguecriteria for fretting fatigue life assessment[J].International Journal ofFatigue,2007,30(1):32-44.[10]㊀刘㊀兵,何国球,蒋小松,等.多轴微动疲劳损伤行为[J].同济大学学报(自然科学版),2012,40(1):77-80.LIU Bing,HE GuoQiu,JIANG XiaoSong,et al.Multi-axis frettingfatigue damage behavior[J].Journal of Tongji University(NaturalScience),2012,40(1):77-80(In Chinese).[11]㊀ABBASI F,MAJZOOBI G H.Effect of out-of-phase loading onfretting fatigue response of Al7075-T6under cyclic normal loadingusing a new testing apparatus[J].Engineering Fracture Mechanics,2018(188):93-111.[12]㊀FOUVRY S,ARNAUD P,MIGNOT A,et al.Contact size,frequencyand cyclic normal force effects on Ti-6Al-4V fretting wear processes:Anapproach combining friction power and contact oxygenation[J].Tribology International,2017,113(9):460-473.[13]㊀FOUVRY S,DUO P,PERRUCHAUT P.A quantitative approachof Ti-6Al-4V fretting damage:friction,wear and crack nucleation[J].Wear,2004,257(9/10):916-929.[14]㊀杨咸启,钱㊀胜,褚㊀园,等.HERTZ型与非HERTZ型接触理论计算方法[J].黄山学院学报,2017,19(5):13-18.YANG XianQi,QIAN Sheng,CHU Yuan,et al.Theoretical calculationof HERTZ and non-Hertz contact[J].Journal of Huangshan University,2017,19(5):13-18(In Chinese).。
基于ProCAST_的ZL114A_尾段壳体凝固成形数值模拟与工艺优化

精 密 成 形 工 程第16卷 第3期 96JOURNAL OF NETSHAPE FORMING ENGINEERING 2024年3月收稿日期:2024-01-05 Received :2024-01-05引文格式:樊振中, 丛延, 吴凌华, 等. 基于ProCAST 的ZL114A 尾段壳体凝固成形数值模拟与工艺优化[J]. 精密成形工程, 2024, 16(3): 96-107.FAN Zhenzhong, CONG Yan, WU Linghua, et al. Numerical Simulation and Forming Optimization of ZL114A Tail Section Shell Solidification Process Based on ProCAST[J]. Journal of Netshape Forming Engineering, 2024, 16(3): 96-107. *通信作者(Corresponding author )基于ProCAST 的ZL114A 尾段壳体凝固成形数值模拟与工艺优化樊振中1,2*,丛延3,吴凌华4,李卫东5,罗磊4,张杨5,刘国5,张勇为5,王刚5,肖佑涛5(1.中国航发北京航空材料研究院,北京 100095;2.北京市先进铝合金材料及应用工程技术研究中心,北京 100095;3.北京宇航系统工程研究所,北京 100076;4.海装西安局驻成都地区第四军事代表室,成都 610100;5.四川航天长征装备制造有限公司,成都 610100) 摘要:目的 针对ZL114A 尾段壳体研制需求,利用低压充型液态成形工艺与数值仿真计算,预测疏松缺陷分布位置及严重程度,通过改进工艺来减少疏松缺陷,进而提高生产合格率。
方法 基于ProCAST 软件对ZL114A 尾段壳体低压充型凝固过程进行仿真计算,分析充型凝固过程中的流动场与温度场分布、充型时间、流动长度与凝固时间,预测疏松缺陷分布位置及严重程度,结合枝晶相干点双电偶热分析法测试结果,对低压充型工艺进行设计优化。
影响铝合金疲劳性能的内因及其机制
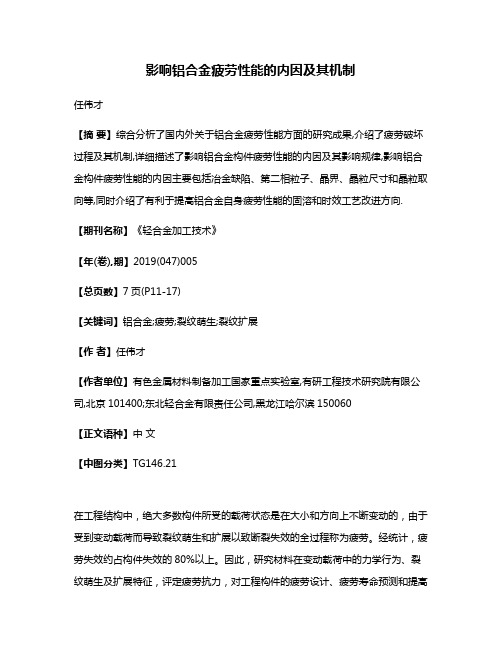
影响铝合金疲劳性能的内因及其机制任伟才【摘要】综合分析了国内外关于铝合金疲劳性能方面的研究成果,介绍了疲劳破坏过程及其机制,详细描述了影响铝合金构件疲劳性能的内因及其影响规律,影响铝合金构件疲劳性能的内因主要包括冶金缺陷、第二相粒子、晶界、晶粒尺寸和晶粒取向等,同时介绍了有利于提高铝合金自身疲劳性能的固溶和时效工艺改进方向.【期刊名称】《轻合金加工技术》【年(卷),期】2019(047)005【总页数】7页(P11-17)【关键词】铝合金;疲劳;裂纹萌生;裂纹扩展【作者】任伟才【作者单位】有色金属材料制备加工国家重点实验室,有研工程技术研究院有限公司,北京101400;东北轻合金有限责任公司,黑龙江哈尔滨150060【正文语种】中文【中图分类】TG146.21在工程结构中,绝大多数构件所受的载荷状态是在大小和方向上不断变动的,由于受到变动载荷而导致裂纹萌生和扩展以致断裂失效的全过程称为疲劳。
经统计,疲劳失效约占构件失效的80%以上。
因此,研究材料在变动载荷中的力学行为、裂纹萌生及扩展特征,评定疲劳抗力,对工程构件的疲劳设计、疲劳寿命预测和提高工程材料的疲劳抗力显得十分重要。
综合分析国内外关于铝合金疲劳方面的研究现状,主要介绍了影响铝合金疲劳性能的内因,旨在为铝合金加工工艺改进提供一些支持和参考。
1 疲劳破坏过程及其机制疲劳源即疲劳裂纹的萌生标志着铝合金设备疲劳损伤过程的开始。
疲劳源是材料微观组织永久损伤的核心,裂纹萌生后,逐渐长大并与其他裂纹合并,然后形成宏观主裂纹,萌生阶段结束;接下来进入了裂纹扩展阶段,经过一段稳定扩展后,裂纹达到了一个临界尺寸;随着下一次应力、应变的作用,构件无法承受,裂纹突然失稳扩展,构件瞬间断裂。
用三个阶段描述该过程:疲劳裂纹萌生阶段、疲劳裂纹扩展阶段和失稳断裂阶段。
裂纹萌生。
疲劳裂纹往往由于应力集中首先起源于物体内部微观组织结构的薄弱部位或高应力区,起始阶段,裂纹长度大致在0.05 mm~0.1 mm或更小,被定义为疲劳裂纹核。
ZL114A合金冷态焊接微观组织与力学性能
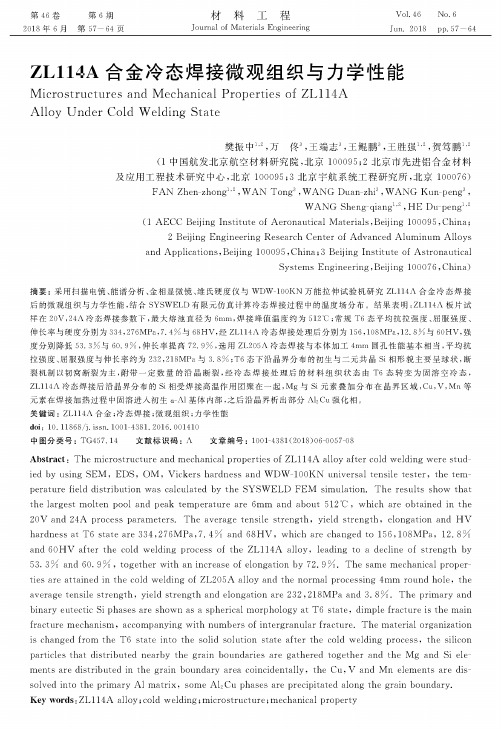
第46卷第6期2018年6月第57—64页材料工程Journal of M aterials EngineeringV ol.46 No.6Ju n.2018 pp.57 —64ZL114A合金冷态焊接微观组织与力学性能Microstructures and Mechanical Properties of ZL114AAlloy Under Cold Welding State樊振中12,万佟3,王端志3,王鲲鹏3,王胜强12,贺笃鹏12(1中国航发北京航空材料研究院,北京100095;北京市先进铝合金材料 及应用工程技术研究中心,北京100095 ;北京宇航系统工程研究所,北京100076)FAN Zhen-zhong1'2,W AN Tong3,WANG Duan-zhi3,WANG Kun-Peng3,WANG Sheng-qiang1,2,H E Du-peng1,2(1 AECC Beijing Institute of Aeronautical Materials,Beijing 100095, China;2 Beijing Engineering Research Center of Advanced Aluminum Alloysand Applications,Beijing 100095 ,China;3 Beijing Institute of AstronauticalSystems Engineering,Beijing 100076,China)摘要:采用扫描电镜、能谱分析、金相显微镜、维氏硬度仪与WDW-100K N万能拉伸试验机研究ZL114A合金冷态焊接后的微观组织与力学性能,结合SY SW E L D有限元仿真计算冷态焊接过程中的温度场分布。
结果表明:ZL114A板片试样在20V24A冷态焊接参数下,最大熔池直径为6m m,焊接峰值温度约为512^;常规T6态平均抗拉强度、屈服强度、伸长率与硬度分别为334,276M P a,7. 4%与68H V,经ZL114八冷态焊接处理后分别为156,108M P a,12. 8%与60H V,强度分别降低53. 3%与60. 9%,伸长率提高72. 9%,选用ZL205A冷态焊接与本体加工4m m圆孔性能基本相当,平均抗拉强度、屈服强度与伸长率约为232,218M P a与3.8%;T6态下沿晶界分布的初生与二元共晶S相形貌主要呈球状,断裂机制以韧窝断裂为主,附带一定数量的沿晶断裂,经冷态焊接处理后的材料组织状态由T6态转变为固溶空冷态,ZL114八冷态焊接后沿晶界分布的S相受焊接高温作用团聚在一起,M g与S元素叠加分布在晶界区域,C u,V,M n等元素在焊接加热过程中固溶进人初生a A l基体内部,之后沿晶界析出部分八l C u强化相。
铝合金材料的疲劳寿命预测模型研究

铝合金材料的疲劳寿命预测模型研究近年来,铝合金材料在工业领域中的应用越来越广泛。
然而,由于铝合金材料在长期使用过程中易产生疲劳现象,对其疲劳寿命进行准确预测成为一项重要的研究课题。
本文将探讨铝合金材料的疲劳寿命预测模型研究。
一、疲劳现象铝合金材料在承受循环载荷作用下会出现疲劳现象,即材料断裂在未达到其静态强度下的循环作用下发生。
这一现象在工业生产中常常出现,尤其是在航空航天、汽车制造、建筑工程等领域。
二、疲劳寿命的影响因素铝合金材料的疲劳寿命受到诸多因素的影响。
首先,材料的化学成分和内在微观结构对疲劳寿命具有决定性作用。
不同的合金成分和热处理工艺会导致材料的晶粒尺寸、相组成和纯度产生变化,从而影响材料的疲劳寿命。
其次,载荷形式和大小以及外界环境(如温度、湿度等)也会对疲劳寿命产生影响。
此外,材料的应力状态、缺陷和裂纹等因素也会进一步影响疲劳寿命。
三、现有预测模型目前,已提出了多种铝合金材料疲劳寿命预测模型。
其中一种常用的方法是基于经验公式。
这一方法通过对历史实验数据进行回归分析,得出疲劳寿命与载荷、材料等因素之间的关系,从而实现疲劳寿命的预测。
然而,这种方法具有一定的局限性,不能很好地适应不同的材料和载荷条件。
为了克服传统方法的局限性,一些研究者提出了基于数值模拟的预测方法。
该方法通过建立铝合金材料的微观模型,利用有限元分析等方法模拟材料的应变和应力分布,从而预测疲劳寿命。
这种方法不仅能够考虑材料的微观结构和力学响应,还能够对不同载荷条件进行灵活的模拟。
然而,由于模型的建立需要大量的实验数据和计算资源,目前该方法在实际应用中还存在一定的困难。
四、未来研究方向铝合金材料的疲劳寿命预测模型研究仍然具有较大的发展潜力。
未来研究可以从以下几个方面展开。
首先,可以将机器学习等新兴技术引入铝合金材料疲劳寿命预测的研究中。
通过大数据分析和深度学习算法,可以建立更准确、可靠的预测模型。
其次,可以进一步研究材料的微观结构与疲劳寿命之间的关系,探索新的材料设计方法。
《2024年铝合金车轮双轴疲劳试验数值模拟研究》范文
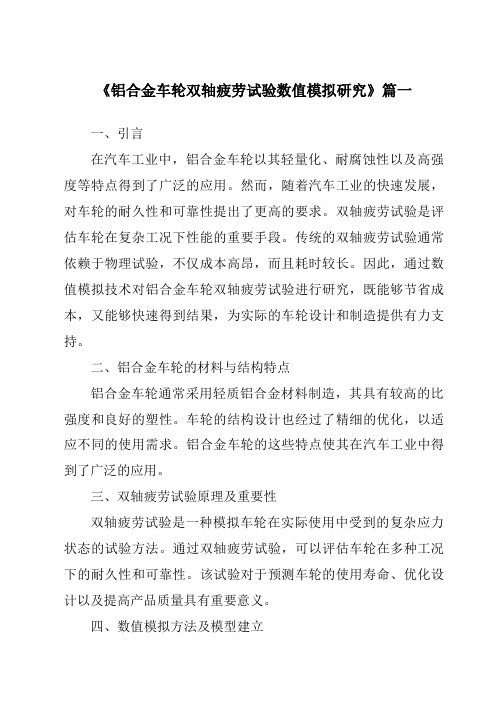
《铝合金车轮双轴疲劳试验数值模拟研究》篇一一、引言在汽车工业中,铝合金车轮以其轻量化、耐腐蚀性以及高强度等特点得到了广泛的应用。
然而,随着汽车工业的快速发展,对车轮的耐久性和可靠性提出了更高的要求。
双轴疲劳试验是评估车轮在复杂工况下性能的重要手段。
传统的双轴疲劳试验通常依赖于物理试验,不仅成本高昂,而且耗时较长。
因此,通过数值模拟技术对铝合金车轮双轴疲劳试验进行研究,既能够节省成本,又能够快速得到结果,为实际的车轮设计和制造提供有力支持。
二、铝合金车轮的材料与结构特点铝合金车轮通常采用轻质铝合金材料制造,其具有较高的比强度和良好的塑性。
车轮的结构设计也经过了精细的优化,以适应不同的使用需求。
铝合金车轮的这些特点使其在汽车工业中得到了广泛的应用。
三、双轴疲劳试验原理及重要性双轴疲劳试验是一种模拟车轮在实际使用中受到的复杂应力状态的试验方法。
通过双轴疲劳试验,可以评估车轮在多种工况下的耐久性和可靠性。
该试验对于预测车轮的使用寿命、优化设计以及提高产品质量具有重要意义。
四、数值模拟方法及模型建立1. 有限元分析方法:采用有限元分析软件对铝合金车轮进行建模和数值模拟。
通过建立精确的几何模型和材料模型,可以模拟车轮在双轴疲劳试验中的应力分布和变形情况。
2. 模型建立:根据铝合金车轮的实际尺寸和结构特点,建立精确的有限元模型。
在模型中考虑材料的非线性、塑性以及蠕变等特性,以更准确地反映实际工况下的车轮性能。
五、数值模拟结果与分析1. 应力分布:通过数值模拟,可以获得车轮在不同工况下的应力分布情况。
这包括车轮在不同角度下的弯曲、扭转以及剪切等应力状态。
2. 疲劳寿命预测:根据数值模拟结果,可以预测车轮的疲劳寿命。
通过分析不同区域的应力集中情况以及材料的疲劳性能,可以评估车轮在不同工况下的使用寿命。
3. 结果分析:将数值模拟结果与实际双轴疲劳试验结果进行对比,验证数值模拟方法的准确性和可靠性。
通过对模拟结果进行深入分析,可以优化车轮的设计和制造工艺,提高产品的性能和寿命。
铝合金材料疲劳性能测试与预测方法研究
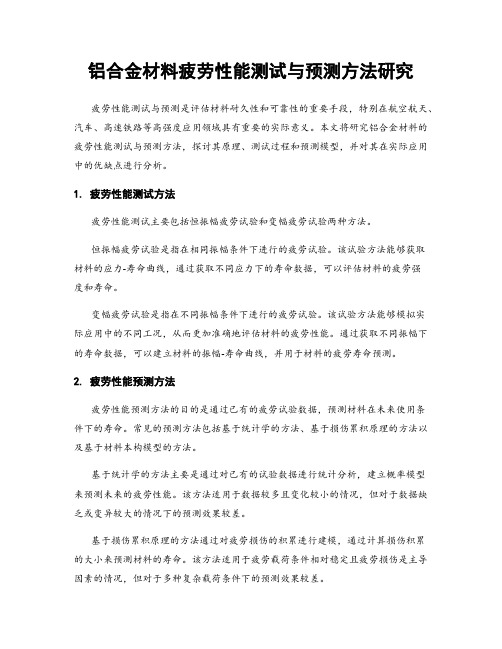
铝合金材料疲劳性能测试与预测方法研究疲劳性能测试与预测是评估材料耐久性和可靠性的重要手段,特别在航空航天、汽车、高速铁路等高强度应用领域具有重要的实际意义。
本文将研究铝合金材料的疲劳性能测试与预测方法,探讨其原理、测试过程和预测模型,并对其在实际应用中的优缺点进行分析。
1. 疲劳性能测试方法疲劳性能测试主要包括恒振幅疲劳试验和变幅疲劳试验两种方法。
恒振幅疲劳试验是指在相同振幅条件下进行的疲劳试验。
该试验方法能够获取材料的应力-寿命曲线,通过获取不同应力下的寿命数据,可以评估材料的疲劳强度和寿命。
变幅疲劳试验是指在不同振幅条件下进行的疲劳试验。
该试验方法能够模拟实际应用中的不同工况,从而更加准确地评估材料的疲劳性能。
通过获取不同振幅下的寿命数据,可以建立材料的振幅-寿命曲线,并用于材料的疲劳寿命预测。
2. 疲劳性能预测方法疲劳性能预测方法的目的是通过已有的疲劳试验数据,预测材料在未来使用条件下的寿命。
常见的预测方法包括基于统计学的方法、基于损伤累积原理的方法以及基于材料本构模型的方法。
基于统计学的方法主要是通过对已有的试验数据进行统计分析,建立概率模型来预测未来的疲劳性能。
该方法适用于数据较多且变化较小的情况,但对于数据缺乏或变异较大的情况下的预测效果较差。
基于损伤累积原理的方法通过对疲劳损伤的积累进行建模,通过计算损伤积累的大小来预测材料的寿命。
该方法适用于疲劳载荷条件相对稳定且疲劳损伤是主导因素的情况,但对于多种复杂载荷条件下的预测效果较差。
基于材料本构模型的方法主要是通过建立材料的疲劳损伤本构模型,通过对材料的应力应变响应进行模拟计算,来得到材料的寿命预测。
该方法适用于各种载荷条件下的预测,但需要建立复杂的本构模型,数据需求较高。
3. 方法的优缺点分析恒振幅疲劳试验的优点是测试过程简单,结果可重复性好,适用于评估材料的基本疲劳性能。
但其缺点是无法模拟实际应用中的变幅载荷条件,预测精度较低。
变幅疲劳试验的优点是能够模拟实际应用中的变幅载荷条件,预测精度较高。
《2024年铝合金车轮弯曲疲劳实验失效分析及工艺的研究》范文

《铝合金车轮弯曲疲劳实验失效分析及工艺的研究》篇一一、引言随着汽车工业的快速发展,铝合金车轮因其轻量化、高强度、耐腐蚀等优点,逐渐成为现代汽车制造领域的主要选择。
然而,铝合金车轮在长期使用过程中会受到弯曲疲劳的影响,导致其性能逐渐降低,甚至出现失效现象。
因此,对铝合金车轮的弯曲疲劳实验失效分析及工艺的研究显得尤为重要。
本文将针对铝合金车轮的弯曲疲劳实验进行详细分析,并探讨其失效原因及相应的工艺改进措施。
二、铝合金车轮弯曲疲劳实验方法及过程铝合金车轮的弯曲疲劳实验主要通过模拟车辆在实际使用过程中所承受的弯曲载荷,以评估车轮的耐久性能。
实验过程中,将铝合金车轮置于专用的测试设备上,通过施加循环的弯曲载荷,观察车轮的变形情况及疲劳性能。
此外,还需对实验过程中的温度、湿度、载荷等参数进行严格控制,以保证实验结果的准确性。
三、铝合金车轮弯曲疲劳实验失效分析铝合金车轮在弯曲疲劳实验中,常见的失效形式包括裂纹、变形及断裂等。
其中,裂纹是导致车轮失效的主要原因之一。
裂纹的产生往往与材料性能、制造工艺及使用环境等因素密切相关。
此外,变形和断裂也是铝合金车轮在实验过程中常见的失效现象,这些现象往往与材料的疲劳性能及应力分布有关。
四、铝合金车轮弯曲疲劳失效原因分析铝合金车轮弯曲疲劳失效的原因主要包括材料性能、制造工艺及使用环境等方面。
首先,材料性能是影响车轮疲劳性能的重要因素,如材料的强度、硬度、韧性等。
其次,制造工艺对车轮的质量及性能具有重要影响,如铸造、加工、表面处理等环节。
此外,使用环境也是导致车轮失效的重要因素,如道路状况、气候条件、载重等。
五、铝合金车轮工艺改进措施针对铝合金车轮的弯曲疲劳失效问题,可采取以下工艺改进措施:1. 优化材料性能:通过调整合金成分、提高材料硬度及韧性等手段,提高铝合金车轮的抗疲劳性能。
2. 改进制造工艺:优化铸造、加工及表面处理等环节,提高车轮的制造精度及表面质量。
3. 合理设计结构:根据使用需求及道路状况,合理设计车轮的结构及尺寸,以降低应力集中及提高疲劳性能。
铝合金材料的疲劳研究进展

铝合金材料的疲劳研究进展徐超,杨尚磊(上海工程技术大学材料工程学院上海 201620)摘要:综述了铝合金材料的疲劳研究进展,介绍了铝合金材料的疲劳裂纹萌生机制和特性、裂纹扩展规律及其扩展阶段的研究进展,同时概述了裂纹疲劳行为的影响因素和微观机理方面的最新研究进展,最后从裂纹萌生和扩展机制以及微观机理等方面概述了铝合金疲劳行为研究趋势。
关键词:铝合金疲劳裂纹萌生和扩展微观机理0 前言材料的疲劳性能指标是许多构件设计的重要依据之一,为此从微观上分析研究材料疲劳裂纹萌生和扩展特点以及他们与材料本证微观结构之间的关系具有重要指导意义[1]。
由疲劳引起的焊接构件表面产生的裂纹萌生、扩展和断裂,都会导致一系列严重的影响,致使整个系统出现失效现象。
疲劳行为的研究已经成为材料学中的一个重要分支,由于其存在的广泛性,越来越受到国内外众多学者的关注。
铝合金由于密度小、比强度高,耐蚀性好,在汽车、列车、船舶、航空、航天等领域得到了广泛的应用,同时还具有良好的成形工艺性和焊接性,因此铝合金成为在工业中应用最广泛的一类有色金属材料[2]。
铝合金材料的疲劳破坏是汽车、列车、船舶、航空、航天领域中经常遇到的现象,所以对铝合金的疲劳行为的研究更具有重要意义。
目前对铝合金疲劳裂纹的萌生、扩展和断裂的微观特征以及疲劳寿命的预测研究也相当广泛,因此,本文对铝合金材料的疲劳研究进行了综述。
2 铝合金材料的疲劳研究现状2.1 疲劳裂纹的萌生由于交变载荷的循环作用,疲劳裂纹的萌生过程往往发生在材料存在缺陷或薄弱区域以及高应力区,其通过不均匀的滑移或位移,从微细小裂纹形成而逐渐长大扩展至断裂。
主要可能存在以下形式:对一般的工业合金,在交变应力作用下第二相、夹杂物与基体界面开裂;对纯金属或单相合金,尤其是单晶体,材料表面的滑移带集中形成驻留滑移带就会形成开裂;当经受较高的应力或应变幅时,晶界结合力在低于晶内滑移应力下,晶界或亚晶界处易发生开裂;另外,对高强度合金,也会由于夹杂物、第二相本身属于脆性相从而发生开裂。
ZL114A铝合金本构关系与失效准则参数的确定

ZL114A铝合金本构关系与失效准则参数的确定谭毅;杨书仪;孙要兵;郭小军【期刊名称】《爆炸与冲击》【年(卷),期】2024(44)1【摘要】针对航空发动机机匣材料ZL114A铝合金,构建描述该材料在较大温度范围下大变形及失效行为的材料模型。
通过万能试验机及分离式霍普金森压杆试验装置测试ZL114A铝合金在常温准静态、高温和高应变率下的力学性能,分析温度和应变率对材料流动应力的影响。
采用有限元程序和优化算法反求25~375℃内材料的硬化参数,结合高应变率(1310~5964 s^(-1))下材料的动态行为关系,构建包含塑性应变、温度及应变率的经验型本构模型。
开展缺口拉伸、缺口压缩等试验并建立相对应的有限元模型,获取材料在不同应力三轴度下的失效应变,标定分段形式的Johnson-Cook(J-C)失效准则参数。
通过不同温度下的平板侵彻试验和数值模拟验证失效准则及其参数的有效性。
结果表明,ZL114A铝合金具有明显的应变硬化、温度软化及高应变率强化特性;具有应力饱和特征的Hockett-Sherby(HS)硬化模型较为准确地描述材料大变形下的力学行为;构建的材料本构关系可以描述ZL114A铝合金在大应变、宽温度、高应变率下的力学行为;分段形式的失效准则具有预测不同温度下材料失效行为的能力。
【总页数】20页(P86-105)【作者】谭毅;杨书仪;孙要兵;郭小军【作者单位】湖南科技大学机电工程学院;西北工业大学动力与能源学院;中国航发南方工业有限公司;中国航发湖南动力机械研究所【正文语种】中文【中图分类】O344.3;TG146.21【相关文献】1.多参数强度准则与非线性本构关系在砼坝有限元应力分析中的应用2.一种新形式的钢纤维混凝土冲击动态本构关系及材料参数的确定3.7A04铝合金的本构关系和失效模型4.2A12铝合金本构关系和失效模型5.6061-T6铝合金动态拉伸本构关系及失效行为因版权原因,仅展示原文概要,查看原文内容请购买。
新型高强韧铝合金疲劳行为研究的开题报告

新型高强韧铝合金疲劳行为研究的开题报告
一、研究背景
随着航空、汽车、轨道交通等行业的不断发展,对材料性能的要求越来越高,其中高强韧铝合金作为一种轻量化材料,也受到了广泛的关注。
但是,在高强韧铝合金的应用过程中,疲劳寿命问题一直是制约其应用的一个重要因素,因此对其疲劳行为进行深入研究具有重要意义。
二、研究内容
本研究将以某一新型高强韧铝合金为研究对象,从材料的微观结构、组织性质等方面入手,探究其疲劳行为规律及机理,并从疲劳裂纹扩展、疲劳寿命等指标着手,探究高强韧铝合金在疲劳载荷下的损伤演化及其对材料性能的影响。
三、研究方法
1. 实验法:通过疲劳试验,测试材料在不同载荷下的疲劳寿命及其破坏形态,分析材料在疲劳载荷下的损伤演化规律。
2. 显微结构分析:使用扫描电子显微镜(SEM)和透射电子显微镜(TEM)等分析工具,观察材料微观结构的演变过程,分析材料在长期使用过程中的性能变化。
3. 数值模拟方法:采用有限元分析方法,在考虑材料微观结构及力学性能的基础上,对材料疲劳寿命进行预测。
四、研究意义
本研究将探究新型高强韧铝合金在疲劳载荷下的行为规律及机理,为进一步优化材料设计及材料加工工艺提供科学依据。
同时,通过对高强韧铝合金的疲劳研究,拓宽铝合金材料在航空、汽车、轨道交通等领域的应用范围,具有重要的经济和社会意义。
一种ZL114A薄壁锥壳铸件的铸造工艺研究
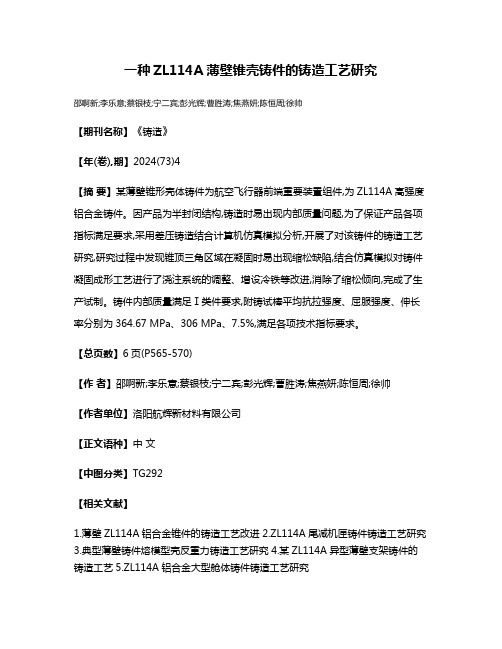
一种ZL114A薄壁锥壳铸件的铸造工艺研究
邵啊新;李乐意;蔡银枝;宁二宾;彭光辉;曹胜涛;焦燕妍;陈恒周;徐帅
【期刊名称】《铸造》
【年(卷),期】2024(73)4
【摘要】某薄壁锥形壳体铸件为航空飞行器前端重要装置组件,为ZL114A高强度铝合金铸件。
因产品为半封闭结构,铸造时易出现内部质量问题,为了保证产品各项指标满足要求,采用差压铸造结合计算机仿真模拟分析,开展了对该铸件的铸造工艺研究,研究过程中发现锥顶三角区域在凝固时易出现缩松缺陷,结合仿真模拟对铸件凝固成形工艺进行了浇注系统的调整、增设冷铁等改进,消除了缩松倾向,完成了生产试制。
铸件内部质量满足Ⅰ类件要求,附铸试棒平均抗拉强度、屈服强度、伸长率分别为364.67 MPa、306 MPa、7.5%,满足各项技术指标要求。
【总页数】6页(P565-570)
【作者】邵啊新;李乐意;蔡银枝;宁二宾;彭光辉;曹胜涛;焦燕妍;陈恒周;徐帅
【作者单位】洛阳航辉新材料有限公司
【正文语种】中文
【中图分类】TG292
【相关文献】
1.薄壁ZL114A铝合金锥件的铸造工艺改进
2.ZL114A尾减机匣铸件铸造工艺研究
3.典型薄壁铸件熔模型壳反重力铸造工艺研究
4.某ZL114A异型薄壁支架铸件的铸造工艺
5.ZL114A铝合金大型舱体铸件铸造工艺研究
因版权原因,仅展示原文概要,查看原文内容请购买。
- 1、下载文档前请自行甄别文档内容的完整性,平台不提供额外的编辑、内容补充、找答案等附加服务。
- 2、"仅部分预览"的文档,不可在线预览部分如存在完整性等问题,可反馈申请退款(可完整预览的文档不适用该条件!)。
- 3、如文档侵犯您的权益,请联系客服反馈,我们会尽快为您处理(人工客服工作时间:9:00-18:30)。
中图分类 号 : T G1 4 6 . 2 文献标 识码源丰富、 储量 巨大 , 也是有色金 属中用量最大和应用最 广泛 的金 属材料…. 铝及 其合金具有 良好 的的导热性、 导电性、 耐蚀性 , 还具 有密度小 、 比强 度 高 , 易 于铸 造、 易 于加 工 等 优 点 . 3 J , 广泛应 用 于航空 航 天 、 交通运输、 化 工 机 械
第3 1 卷 第 2期
2 0 1 3 年 O 3月
佳 木 斯 大 学 学 报 ( 自 然 科 学 版 ) J o u r n a l o f J i a mu s i U n i v e r s i t y( N a t u r a l S c i e n c e E d i t i o n )
①
收稿 E t 期: 2 0 1 3— 0 2—2 4 基金项 目: 黑龙江省教育厅科研项 目( 1 1 5 1 1 3 8 1 ) . 作者简介 : 刘 向东( 1 9 7 3 一) , 男, 黑龙江佳木斯人 , 佳木斯大学副教授 , 工学博士
第 2期
刘向东, 等: 应 变状 态下 Z L 1 1 4 A铝合金 低 周疲 劳行 为 的研 究
果表 明 : 材 料在低 周 载荷 下 , 当循 环应 变幅值 小于 0 . 6 %, 材 料 没 有表 现 出循 环 硬 化现 象. 随 着循
环应变幅值的增加 , 材料表现 出明显的循环硬化现象; 且随着应变幅值 的增加材料的附加强化程 度增大: 应 变幅值 的大小对 Z L 1 1 4 A铝合金低周疲劳寿命 有较 大影响 , 随着应 变幅值 的增 大, 疲 劳寿命 降低 明显; 疲 劳损伤断 口 表现 出大量的韧 窝和韧性断裂的特征.
图 1 试 样 的 形 状 及 尺 寸
1 试 验 材 料 与方 法
试 验材 料 Z L 1 1 4 A铝 合 金 的化 学 成分 ( 质 量分 数, %) 见表 1 . Z L 1 1 4 A 铝合 金 材 料 在 室 温 下 的基 本力 学性 能 指标 为 : 杨 氏模 量 , 抗拉强度 , 泊松比,
S i Mg Ti F e Mn A1
7 . 0
0 . 6
0 . 1 5
0 . 2
0 . 1
余量
低 周 疲 劳 试 验 在 MT S S 1 0疲 劳 试 验 机 上 进
行, 试验介质为空气 , 试验温度为室温, 试验采用应 变控制方式 , 用轴 向拉 一 压循环载荷加载方式 , 应 变 比为 R = 一1 , 应变波形为三角波 , 试 验 频率 为
0 . 5 H z . 失效准则为加载峰值下降 3 0 %时, 判定 低
周疲 劳试验 试 样失 效 .
化元素、 改进熔炼工艺等方法研究开发优 良力学性 能和铸造特性的新型合金 以满足使用要求 . 5 J .
Z L 1 1 4 A铝合 金 为 高 强 韧 A l —s i 系 的铸 造 铝 合金 , 近年来广泛应用于航空航天等高性能结构件 中, 本文 以 Z L 1 1 4 A铝合金为研究对象 , 探讨 了试 验材料在室温下不 同应变幅值 的低周疲劳性能和 显微 结构 , 旨在 为 Z L I 1 4 A铝 合 金 力 学性 能 的研究 提供 参考依 据 .
Ma r .
V0 1 . 31 No . 2 2 01 3
文章编号 : 1 0 0 8—1 4 0 2( 2 0 1 3 ) 0 2- 0 3 0 3-0 3
应 变 状态 下 Z L 1 1 4 A 铝 合 金 低 周 疲 劳 行 为 的研 究①
刘 向东 , 佟立丰? , 丰崇友。 , 韩 阳阳 , 张彩霞 , 陈 振 , 孙红旗 , 张成军
等领 域 . 但 是 随着 现代 化 工 业 的不 断 发 展 , 对 铝合 金材 料 的综 合性 能和 特种 性能 提 出 了更 高要 求 . 近 年来 , 许多 学者 通过 改 变 铝 合 金 的成 分 、 加 人 合金
试样 , 试样 尺 寸如 图 1所示 . 表 1 试验 材料 Z L 1 1 4 A的化 学成分 ( 质量 分数% )
3 0 5
性 能是 由其 显微 组织 的结 构决 定 的 , 凝 固过 程 中初
的主 要微观 特 征. 低 周 疲 劳 断 口分 析 结果 表 明 , 试
生相 1 2  ̄ 一 A 1 固溶体、 共 晶体( d+ S i ) 的形态 和分布 决定着材料的使用性能. 材料在循环塑性变形过程 中, 位错的滑移一般通过平面滑移机制和波状滑移 机制 两种方 式 进行 , 其 中应变 幅值 的大 小 以及层错 能 的高低共 同作 用影 响位 错 的滑 移机 制. 对 于层错
用O L Y MP U S G X 7 1 倒 置 式金相 显微 镜对 金相 组织
延伸率. 低周疲劳试样进行 固溶处理和完全人工时 效处理 ( , I ' 6 处理) , 低周疲劳试样采用 圆柱形实心
进行观察和分 析. 利用 J S M一 6 3 0 0 L V型扫描电镜
( S E M) 对断 口进行观测 , 研究分析断 口形貌、 断口
低周 疲劳 试 验后 , 保 存 试样 断 口, 显 微 组织 观 察试 样经 1 2 0 # 、 6 0 0 # 、 1 2 0 0 # 、 2 0 0 0 # 金 相 砂 纸 和水 磨砂 纸 打磨 后 , 用 金 刚石 研 磨 膏 进行 抛 光 处理 , 抛
光好 的试样用 0 . 5— 1 . O %氢 氟酸水 溶液腐蚀 , 采
( 1 . 佳木斯大学 。 黑龙江 佳木斯 1 5 4 0 0 7 ; 2 . 九江 职业技 术学院 。 江西 九江 3 3 2 0 0 7 ; 3 . 嘉兴职业技术学 院, 浙江 嘉兴 3 1 4 0 3 6 )
摘
要 : 在 室温应 变控 制 下 , 对Z L 1 1 4 A铝合金 进 行 了单 轴低 周 疲 劳试 验 研 究和 显微 分析 ,结