轧机工艺
酸轧轧机工艺讲解讲诉
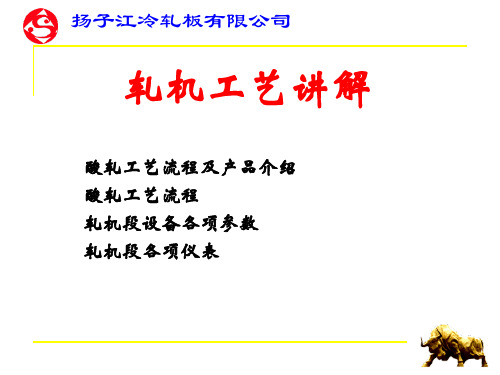
功能:卷取带钢,使带钢成卷。 参数:卷取张力:max.115 kN
卷筒:Φ508/Φ610×1450 mm
扬子江冷轧板有限公司
轧2、机轧段辊设数备据参数
轧机
单位
轧辊
辊身直径最大/最小 mm
辊身长度 辊颈直径 轧辊近似重量
两条机组设计年产量200万吨,单卷重量6-28 吨。机组主要 工艺参数:
入口段速度:最大500m/min 酸洗段速度:最大200m/min 圆盘剪速度:最大250m/min 轧机段速度:最大1700m/min 产品规格:厚度:0.18-2.0(mm); 宽度:750-1300(mm)
扬子江冷轧板有限公司
酸轧车间工艺流程
主要设备组成有:开卷机、激光焊机、入口活套、破鳞拉矫机、 酸洗槽、漂洗槽、出口活套、圆盘剪、联机活套、五机架连轧 机、飞剪、卷取机及焊缝检测仪、张力辊、纠偏辊、测厚仪、 板型仪等。
扬子江冷轧板有限公司
轧机段主要设备介绍
五机架连轧机
卷取机
功能:改变带钢规格和改善板型。 参数:工作辊:450/390×1420mm
扬子江冷轧板有限公司
轧机工艺讲解
酸轧工艺流程及产品介绍 酸轧工艺流程 轧机段设备各项参数 轧机段各项仪表
扬子江冷轧板有限公司
酸轧工艺流程及产品介绍
酸轧机组,采取酸洗-冷轧联合工艺,设备大量采取国内外 合作方式制造,技术先进、成熟,装备水平达世界一流。主要技 术有:激光焊接技术、喷射紊流式酸洗技术、五机架六辊轧制技 术以及全线自动带钢跟踪控制技术,能实现板厚、板形全自动控 制,可为后续工序提供尺寸精确板型好、表面光洁性能高的冷轧 原料。
20辊轧机工艺1
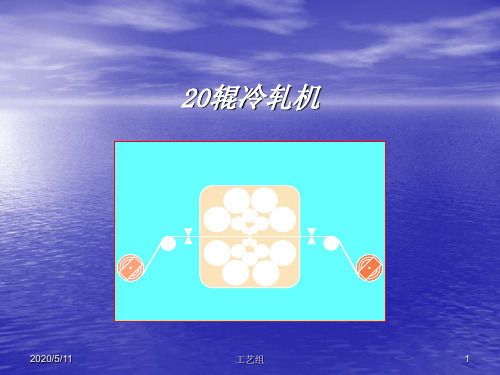
特性的变形能力,轧制成某一中间产品, 然后再送
往冷退火酸洗线 处理。作为成品或下一个轧程的原 料。
2014-8-6
工艺组
6
2.冷轧工艺
2.2 中轧 来料为退火酸洗的冷轧钢卷,根据材料的组织特 性的变形能力,轧制成某一厚度的中间产品,然后送 往冷退火酸洗线进行处理,作为成品或下一个轧程的
原料。
2014-8-6
b.运卷小车下降退出并返回到准备位置, c.外支撑门关闭,开卷机的压卷辊下降,剥卷导 板抬起 d.开卷机转动,带钢头部沿剥卷板进入直头机夹 送辊,
2014-8-6
工艺组
14
3.冷轧工艺过程描述
3.3 穿带 d.经直头后的带钢头部,沿伸缩式导板台进入轧
机入口夹送辊 e.轧机入口夹送辊夹持带钢进入导边对中装置, 然后通过刮油器,轧机入口压辊导板,轧机辊缝, 出口压辊导板,刮油器,横切剪,到达转向辊
4962
4962
4962
4962
2014-8-6
工艺组
30
5. Sundwig四立柱轧机
德国Sundwig 公司是奥地利 Andritz 集团下属的机械 制造公司,主要负责提供20轧机,平整机和一些辅助
设备,为酒钢提供的是四立柱分体式轧机,用于轧制
退火酸洗后的奥氏体300系列和铁素体400系列不锈钢, 产品厚度 0.2mm ~ 3.0mm ,宽度 750mm ~ 1350mm ,
2014-8-6
工艺组
28
4.5
20辊轧机传动功率参数
Sundwig I2 S VAI
表9 DMS
传动功率(kw) 传动功率(kw) 传动功率(kw) 传动功率(kw) 项目 500 690 410 开 卷 机 4250 4000 4400 4000 入口卷取机 4250 4000 4400 4000 出口卷取机 4250 4000 4500 4000 轧 机 12450 13990 12410 总传动功率 12750 8000kN 7500kN 8000kN 8000kN 轧制 力 过载能力 9000kN 一个轧程最 88% 88% 80% 85% 大压下率
冷轧机械设备和工艺介绍

最后一架工作辊进行预热,但也有所有机架上的轧辊都进行预热的。加热 有用蒸汽、煤气、电加热器和热风循环加热等方法,可以离线, 也可以在线进行。 (3)轧辊轴承座的更换
在轧制过程中,轴承烧伤的原因有润滑不良、润滑部分混进杂物、轴 承寿命、轧机的水平度不好及压下率太大等,但最多的是往轧辊装卸时碰 伤和由于轴承的内圈与辊轴外面的配
合较松,在滑动时产生伤痕。考虑为了节省劳动力,轧辊轴承更换装置应 充分定心,这对防止碰伤很有益处。在进行高速轧制及油雾润滑时,避免 碰伤显得更加重要。把改变轴承与轴承座的相对位置叫做轴承的位置更换。 提高轴承寿命必须定期检修。
(4)轧辊轴承座的清洗
换轴承座前,为了防止烧伤,检查一下轴承,对轴承座及轴承进行 清洗。从前清洗是在地面上用手工进行的,而现在把轴承座用台车或
(2)保证带钢表面质量所规定的技术要求。在轧制过程中, 轧辊表面与带钢表面直接接触,因此必须保证轧辊表面具有较高 的耐磨性,以保证带钢的表面质量。轧辊的耐磨性取决于轧辊的 表面硬度。
12
(3)保证安装和轧制精度所规定的轧辊配合尺寸与形位公差 要求。轧辊配合尺寸有辊颈直径、安装轴承的定位套筒和轴承 紧固螺丝用的尺寸、工作辊与联轴器的配合尺寸,工作辊传动 扁头的尺寸。 规定轧辊的形位公差包括辊颈的椭圆度和柱度公差、辊身 相对于辊颈的同轴度、各端面相对于轧辊轴心线的垂直度、工 作辊传动扁头的两平行平面相对于工作辊轴心线的对称度、轧 辊辊颈上各台阶相对于辊颈的径向跳动、各键槽表面相对于轧 辊轴心线的对称度等。
30
——稳定性:对于大张力薄带卷取,有产生塌卷的可能,这是不能允许 的。
——纠偏控制:一般采用光电元件——伺服阀,进行在线纠偏。
2.2 冷带卷取机的结构
一般以卷筒的结构进行分类。 (1)实心卷筒卷取机:其结构最简单,刚度大,可受大 张力;但无法胀缩故无法卸卷。 (2)四棱锥卷取机: 用于20辊1180轧机。它由四个扇形块、四棱锥(α=7045) 及胀缩液压缸组成。液压油由左端的旋转接头进入液压缸 使胀缩液压缸右移,同时使棱锥轴右移;锥轴上的四个斜 面将扇形板沿径向顶开。而棱锥轴左移则实现卷筒收缩。 在卷筒表面安有钳口,以固定带钢头部。 31
不锈钢热轧的生产设备及工艺流程

不锈钢热轧的生产设备及工艺流程
1.生产设备:
不锈钢热轧生产设备包括热轧机组、钢坯加热炉、轧机、冷却设备等。
热轧机组由机架、电机、润滑系统、冷却系统等组成,是不锈钢热轧的核
心设备。
钢坯加热炉用于将钢坯加热到适宜的轧制温度。
轧机用于将加热
后的钢坯进行轧制,将其加工成所需的工件。
冷却设备用于冷却轧制后的
工件。
2.工艺流程:
(1)原料准备:选择合适的不锈钢原材料(如304、316等)进行采购,并进行锅炉加热处理、理化检测等工序,以保证原材料的质量和性能。
(2)钢坯加热:将原料钢坯放入加热炉中,通过高温加热使钢坯达
到所需的轧制温度。
加热温度的选取需要根据具体材料和产品要求来确定。
(3)除鳞净化:将加热后的钢坯送入酸洗设备中进行除鳞净化处理,去除钢表面的氧化皮和污染物,以保证后续轧制质量。
(4)轧制:将除鳞后的钢坯送入轧机进行轧制,通过多道次轧制使
钢坯逐渐变形,形成所需的厚度和宽度。
(5)冷却:将轧制后的钢坯通过冷却设备进行快速冷却,使其达到
所需的力学性能和表面质量。
(6)切割定尺:根据客户需求,将冷却后的钢坯切割成所需的定尺
尺寸。
(7)质检包装:对切割后的工件进行质量检验,合格后进行包装和
入库。
以上只是不锈钢热轧的一般生产设备和工艺流程,具体的生产过程和设备配置还会根据不同产品的要求和工厂的实际情况有所不同。
轧机工作原理
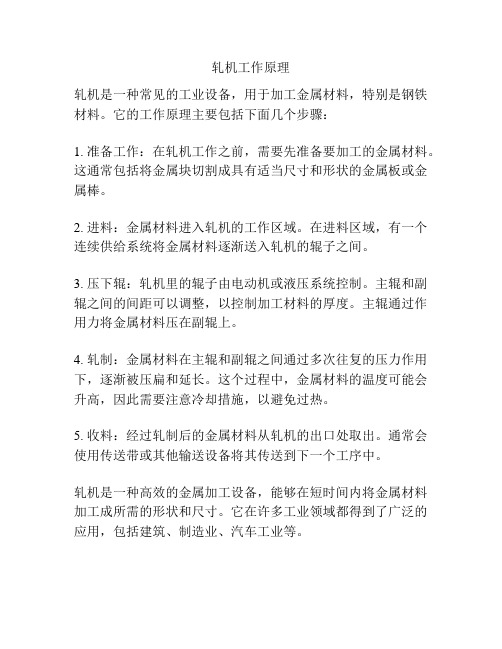
轧机工作原理
轧机是一种常见的工业设备,用于加工金属材料,特别是钢铁材料。
它的工作原理主要包括下面几个步骤:
1. 准备工作:在轧机工作之前,需要先准备要加工的金属材料。
这通常包括将金属块切割成具有适当尺寸和形状的金属板或金属棒。
2. 进料:金属材料进入轧机的工作区域。
在进料区域,有一个连续供给系统将金属材料逐渐送入轧机的辊子之间。
3. 压下辊:轧机里的辊子由电动机或液压系统控制。
主辊和副辊之间的间距可以调整,以控制加工材料的厚度。
主辊通过作用力将金属材料压在副辊上。
4. 轧制:金属材料在主辊和副辊之间通过多次往复的压力作用下,逐渐被压扁和延长。
这个过程中,金属材料的温度可能会升高,因此需要注意冷却措施,以避免过热。
5. 收料:经过轧制后的金属材料从轧机的出口处取出。
通常会使用传送带或其他输送设备将其传送到下一个工序中。
轧机是一种高效的金属加工设备,能够在短时间内将金属材料加工成所需的形状和尺寸。
它在许多工业领域都得到了广泛的应用,包括建筑、制造业、汽车工业等。
冷轧机轧制工艺

说到冷轧机相信对于很多朋友来讲都不会感到陌生,但说到该机器的轧制工艺很多人确是知之甚少,因此,下边为大家整理了以下具体的轧制工艺步骤,以供了解。
1、放线
根据不同需要,可采用架空式、卧式、回转式开卷机,卷重可达
500~2000Kg。
为保证安全,其后可设乱线按钮开关。
2、除锈
为了去除对冷轧不利的氧化铁皮,一般使用机械清理的反复弯曲法,有直线型和空间型,最大处理线径可达φ20mm。
3、减径
对母材进行初步的减径,方便后期的轧制。
4、轧机
作业线主体设备, 它有主动与被动两种。
5、测速
测试轧制速度的机械仪器。
6、中频
热处理设备,,对母材进行加热处理的设备。
7、切断
对母材进行定长切断,以便后期的储存运输。
8、料架
接收钢筋的机器,对切断后的钢筋进行翻转回收。
9、打捆
利用机器对翻转回收的钢筋进行打包,以便后期的搬运存储。
10、入库
将打好包的钢筋收入仓库,杜绝锈蚀。
河南金迪是专业生产成套冷轧设备的厂家,生产高、中、低速成套冷轧机,轧制CRB600H,CRB800H达到国家新标准,适用于楼层建筑、高铁、桥梁、隧道、高速公路,市场前景应用广阔。
远程全智能控制,大型线速达到600--1000米/分。
中板轧机工艺流程
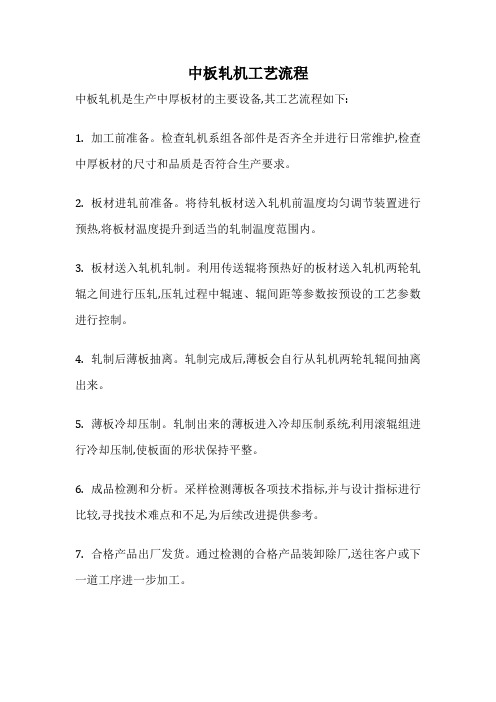
中板轧机工艺流程
中板轧机是生产中厚板材的主要设备,其工艺流程如下:
1. 加工前准备。
检查轧机系组各部件是否齐全并进行日常维护,检查中厚板材的尺寸和品质是否符合生产要求。
2. 板材进轧前准备。
将待轧板材送入轧机前温度均匀调节装置进行预热,将板材温度提升到适当的轧制温度范围内。
3. 板材送入轧机轧制。
利用传送辊将预热好的板材送入轧机两轮轧辊之间进行压轧,压轧过程中辊速、辊间距等参数按预设的工艺参数进行控制。
4. 轧制后薄板抽离。
轧制完成后,薄板会自行从轧机两轮轧辊间抽离出来。
5. 薄板冷却压制。
轧制出来的薄板进入冷却压制系统,利用滚辊组进行冷却压制,使板面的形状保持平整。
6. 成品检测和分析。
采样检测薄板各项技术指标,并与设计指标进行比较,寻找技术难点和不足,为后续改进提供参考。
7. 合格产品出厂发货。
通过检测的合格产品装卸除厂,送往客户或下一道工序进一步加工。
精轧机的轧制工艺

精轧机的轧制工艺精轧机是一种用于金属材料加工的设备,主要用于将粗轧后的金属材料进行精细轧制,以达到特定尺寸和表面质量要求。
精轧机的轧制工艺是指在整个轧制过程中,通过一系列的操作和参数调节来实现金属材料的精确加工。
精轧机的轧制工艺主要包括准备工作、轧制操作、轧制参数控制和轧后处理等一系列步骤。
首先是准备工作,包括对轧辊进行清洁和检查,对轧机的润滑和冷却系统进行检查和调整,保证轧机设备处于良好的工作状态。
接下来是轧制操作,首先将待轧材料送入精轧机的进料端,经过多道轧制工序,根据需要在不同的轧制工序中调整轧辊的间隙和轧辊的轧制力,以逐步将原始材料轧制成符合要求的尺寸和表面质量的金属板材。
轧制操作必须严格按照工艺要求进行,通过对轧制力、轧辊间隙、材料温度和轧辊表面状况等参数进行实时监测和调整,保证轧制质量和轧制稳定性。
轧制工艺中的轧制参数控制是非常重要的,包括轧辊间隙的控制、轧制力的控制、温度的控制等。
轧辊间隙的控制可以通过液压或机械的方式进行调整,以适应不同尺寸和材质的金属材料。
轧制力的控制可以通过调整轧制压力机的液压系统来实现,以保证轧制过程中的稳定压力。
而温度的控制可以通过冷却系统和加热系统来进行调节,以确保轧制过程中金属材料的温度符合要求。
最后是轧后处理,包括对轧制后的金属板材进行冷却、剪切、检测等一系列工序,以保证轧制后的金属板材的表面质量和尺寸精度符合要求。
在实际生产中,精轧机的轧制工艺需要工艺人员严格按照技术要求进行操作,并通过对轧制过程中各项参数的实时监测和控制,确保轧制质量和轧制稳定性。
同时,精轧机的轧制工艺还需要根据不同的金属材料和不同的轧制要求进行相应的调整和优化,以达到最佳的轧制效果。
总之,精轧机的轧制工艺是一个复杂的过程,需要严格的操作和参数控制,才能确保轧制后的金属材料具有良好的表面质量和尺寸精度。
通过不断的技术创新和工艺优化,精轧机的轧制工艺将会不断提升,为金属材料加工提供更好的技服和设备。
- 1、下载文档前请自行甄别文档内容的完整性,平台不提供额外的编辑、内容补充、找答案等附加服务。
- 2、"仅部分预览"的文档,不可在线预览部分如存在完整性等问题,可反馈申请退款(可完整预览的文档不适用该条件!)。
- 3、如文档侵犯您的权益,请联系客服反馈,我们会尽快为您处理(人工客服工作时间:9:00-18:30)。
1. 降低 角 h
R
2.
增加轧辊直径和减小压下量
3.
实际生产中可以采用:小头轧制和强迫咬入
4. 2. 提高 角
5.
改变轧辊或轧件的表面状态,提高摩擦角
6.
合理调整轧制速度,低速咬入
7.
轧制过程的纵变形
-前滑(forward slip)和后滑(backward slip)
由于压下的金属向轧辊入口和
最长纵条视为一正弦波,以翘曲波形表示板形,称为翘曲度。
翘曲度通常以百分比表示。
λ RV 100% LV
两种表示法之间的关系
I
ΔLV LV
105
πRV 2LV
2
105
5π 2 2
λ2
两种度量之间的关系
(πλ)2/4=ε
(πλ)2/4=10-5 I 单位
例如,λ=1%,对应7.85 I 单位
影响平坦度和板凸度的因素
其中: y- 稳定轧制阶段的咬入角
y - 稳定轧制阶段的摩擦角
Kx - 合力作用点系数
又由于一般稳定轧制阶段,Kx 2 故稳定轧制阶段的最大允许咬入角比开始咬入时的最大允许咬 入角大,同样稳定轧制阶段的最大允许压下量也比咬入时的最 大允许压下量大。
改善咬入条件的途径
凡是能够提高 角或降低 角的一切因素都有利于咬入:
实现咬入的条件
咬入力Tx和阻力Nx 之间的关系有以下三种:
Tx Nx
不能实现自然咬入
Tx Nx
平衡状态
Tx Nx
可以实现自然咬入
由于: Nx N sin
Tx Nf cos
f tan
其中: 咬入角; 摩擦角
故咬入条件: ---极限咬入条件
稳定轧制条件
稳定轧制阶段咬入条件
y
y
Kx
定义
靠旋转的轧辊与轧件之间形成的摩擦力将轧件拖进辊缝之间 轧件承受轧辊作用发生变形的部分
h
轧件与轧辊相接触的圆弧所对应的圆心角= R 轧件与轧辊相接触圆弧的水平投影长度= h R
轧制前、后轧件绝对尺寸之差 :h H h
轧制前、后轧件尺寸的相对变化 = H h 100% 轧制前、后轧件尺寸的比值 : HH
横截面轮廓--边部减薄
原因:
❖ 轧制压力引起轧辊压扁变形的分布 特征
❖ 边部金属和内部金属的流动规律显 著不同
影响因素:
❖ 影响轧制力的因素--压下量,轧 件材质等
❖ 辊径--工作辊辊径越小,边部减 薄越小
解决方法:
❖ 选用有锥度的工作辊 ❖ 工作辊横移
横截面轮廓--楔形
楔形 Wh是指带钢操作侧与传动侧边部标志点厚度之 差:
影响前滑的一些因素
➢ 压下率: 前滑随压下率的增加而增加 ➢ 轧件厚度:轧辊直径和中性角保持不变,轧件出口厚度越
小,前滑越大
德里斯顿公式: S 2 R
h ➢ 轧辊直径:前滑值随辊ቤተ መጻሕፍቲ ባይዱ的增加而增加 ➢ 摩擦系数: 摩擦系数越大,前滑越大 ➢ 张力: 前张力增加,前滑区增加,后张力增加,后滑
区增加
连续轧制中的连轧常数
Wh he0 hed
he0
hed hc
平坦度
➢ 带钢平坦度是指带钢中部纤维长度与边部纤维长度的相对延 伸差。带钢产生平坦度缺陷的内在原因是带钢沿宽度方向各 纤维的延伸存在差异,导致这种纤维延伸差异产生的根本原 因,是由于轧制过程中带钢通过轧机辊缝时,沿宽度方向各 点的压下率不均所致。当这种纤维的不均匀延伸积累到一定 程度,超过了某一值,就会产生表观可见的浪形。
h
咬入(nip)与稳定轧制
α
Nx A Tx
H
N Ny T
Ty
B
咬入与稳定轧制
概念
定义
咬入
依靠旋转的轧辊与轧件之间的摩擦力,轧辊将轧件拖入轧辊之 间的现象称为咬入。为使轧件进入轧辊之间实现塑性变形,轧 辊对轧件必须有与轧制方向相同的水平作用力。
稳定轧制 当轧件被轧辊咬入后开始逐渐充填辊缝,在轧件充填辊缝的过 程中,轧件前端与上下轧辊轴心连线间的夹角α不断减小。当轧 件完全充填辊缝时,α=0,开始稳定轧制阶段。
轧制工艺
rolling process
主要内容
➢ 轧制的基本概念(咬入,前后滑,板形) ➢ 轧机及轧制生产技术的发展 ➢ 板带材高精度轧制和板形控制 ➢ 板带材轧制制度的确定 ➢ 首钢冷轧具体工艺流程及主要工艺参数 ➢ 板形缺陷
轧制的基本概念
α
A
C
B
H
h
B1 A1
轧制的基本概念
概念
轧制 轧制变形区 咬入角 接触弧长度 绝对变形量 相对变形量 变形系数
如果残余内应力足够大,引起带钢的翘曲,称为“表观 的”板形不良
z
W(x,y)
b)
y Rw
o B
w Lw x
横截面轮廓--凸度
横截面轮廓的主要指标有凸度(Crown)、边部减薄(Edge Drop)和楔
形(Wedge)。
凸度
凸度Ch是反映带钢横截面外形最主要的指标,是指带钢中部标志点厚度 hc 与两侧标志点 he0和 hed 平均厚度之差:
RV
LV
L L
平坦度的表示方法-相对长度差表示法
平坦度的表示方法有很多,如波形法、相对长度差法、 残余应力法、矢量法等。
RV
LV
L L
相对长度差表示法: I L 105
L
平坦度的表示方法-波形表示法
Lv
Lv
Rv
Rv
带钢
LV LV
RV
平台
LV
翘曲的带钢切取一块置于平台上,如将最短纵条视为一直线,
F1V1
F2V2
F3V3
F4V4
F1V1 F2V2 ...... FnVn C C :连轧常数
轧制成品
概念
定义
板形(shape) 板带材的平坦度(flatness)和横截面轮廓(profile)。
理想板形
内应力沿带钢宽度方向上均匀分布。
潜在板形 表观板形
如果残余内应力虽然存在,但不足以引起带钢翘曲,称 为“潜在的”板形不良.
出口两个方向流动,导致:
1. 2. 2.
前滑前:滑vhS值h:vvh
后滑: vH v
v 100%
vcos
3.
后滑值:
SH
v cos vH v cos
100%
中性面
v cos
vH v v
v cos
v
vh
4. 3. 中性面:
vh v v v cos v cos vH
后滑区 前滑区
Ch hc (he0 hed ) / 2
he0
hed hc
标志点位置一般取为25mm或是40mm
横截面轮廓--凸度
➢ 比例凸度
比例凸度
C
是指带钢凸度与厚度之比
P
CP Ch / hc 100%
➢ 获得良好板形的条件:
h He0 e0
hed hc H ed H c
比例凸度恒定(凸度成比例) --板凸度一定原则 CP (轧前) C H H C CP (轧后) Ch hc