轧机安装工艺方案
大型轧机机架安装技术探讨

大型轧机机架安装技术探讨摘要:机架的吊装及安装位置精度调整是轧机安装的核心。
本文对大型轧机机架安装技术进行探讨,重点探讨轧机机架吊装的方法比较及机架位置精度调整的方法和要求,对轧机机架的安装有广泛的参考意义。
关键词:轧机机架;吊装;调整0.前言轧机类型多,但基本结构类似,包括一个或几个工作机座及其传动装置。
其中由于机架重量及尺寸大、安装精度要求高,是轧机安装的核心。
轧机机架安装主要解决机架的吊装及机架安装时位置精度的检测和调整。
1.轧机机架的吊装目前轧机单片机架重量均在100吨以上,高度10米以上,轧制车间配置的行车最大起重量一般为100吨,起升高度为11米左右,车间行车的起重量及吊装高度通常不能满足机架吊装要求。
轧机机架的吊装方法需根据机架吊装时现场的场地布置及吊装机具的吊装能力、吊装高度空间综合考虑,本着安全、高效、低成本的原则确定。
机架吊装方法大致分为以下几种:在车间未安装吊装设备前利用大型履带或轮胎起重机吊装;利用车间内已安装的一台或两台桥吊吊装;利用液压提升系统吊装。
1.1利用移动式起重机吊装机架该方法利用大吨位的履带吊或者汽车吊在厂房封闭前先将机架就位。
这需要将机架提前进场,厂房施工和设备安装同步进行,设备安装周期延长,成本高,立体交叉施工安全隐患大,所以实际施工中较少采用。
1.2利用一台或者两台桥吊和专用吊具联合吊装1.2.1利用一台桥吊配合自制专用工具(旋转盘)吊装该方法适用于轧制车间只有一台桥吊,且吊装能力超过轧机单片机架一半以上但不足轧机单片重量时可采用。
自制两个旋转盘作为辅助工具,桥式起重机只负责吊机架的一端,在整个吊装过程中,机架始终有一端不离开地面的刚性支撑(用型钢制作、搭设的支架)。
转盘上、下表面采用30mm厚钢板制作,中间安装有直径50mm的钢球,钢珠内外两侧用钢板固定在转盘下底板上。
上面钢板上用20mm厚的钢板焊接成格状的加强肋。
转盘上表面通过钢珠相对于下表面可转动,该方法利用桥吊和旋转盘配合实现卸车和倒运到位,再利用桥吊配合倒链、千斤顶等辅助机具,将机架立起、就位。
冷轧轧机安装方案

冷轧轧机安装方案冷轧轧机是一种用于加工金属板材的设备,可以将金属板材进行压制和拉伸,以获得所需的尺寸和表面质量。
冷轧轧机的安装方案需要考虑多个因素,包括设备选择、土建工程、电气布置和安全措施等。
一、设备选择1.根据生产需求确定冷轧轧机的型号和规格,选择适合的设备供应商。
2.考虑设备的技术参数、生产能力和性能稳定性,以确保设备能够满足生产要求。
二、土建工程1.根据冷轧轧机的尺寸和重量,设计设备基础和基础承载能力,确保设备安全稳定地安装。
2.根据设备的布局和操作要求,设计厂房的布局和空间,确保运行和维修的便利性。
3.考虑设备的运输和搬运,规划合适的道路和起重设备,确保设备能够准确无误地安装到指定位置。
三、电气布置1.根据冷轧轧机的功率和工艺要求,设计电力系统和配电装置,确保设备供电可靠稳定。
2.设计合理的电缆布线和接线盒,确保设备的电气连接正确可靠。
3.安装适当的控制仪表和传感器,监测和控制设备的运行状态和工艺参数。
四、安全措施1.根据冷轧轧机的结构和工艺特点,设计并建立安全防护措施,确保操作人员的人身安全。
2.安装安全报警系统和紧急停机装置,以应对突发情况和危险事件。
3.培训操作人员,提供正确和安全的操作指导,确保设备的正常运行和生产安全。
五、调试和验收1.按照供应商提供的操作说明进行设备的调试和试运行,确保设备的性能和功能符合要求。
2.进行设备的负荷试验和安全评估,确保设备能够承担正常生产的工作。
3.参考国家相关标准和规范,对设备进行验收,确保设备的合格性和可靠性。
在冷轧轧机的安装过程中,需要充分考虑设备选择、土建工程、电气布置和安全措施等方面的因素,确保设备安全、稳定、高效地运行,提高生产效率和产品质量。
同时,在安装过程中要保证良好的沟通和协调,与供应商、工程师和操作人员等各方进行密切合作,确保安装工作的顺利进行。
轧机机架吊装工艺方案
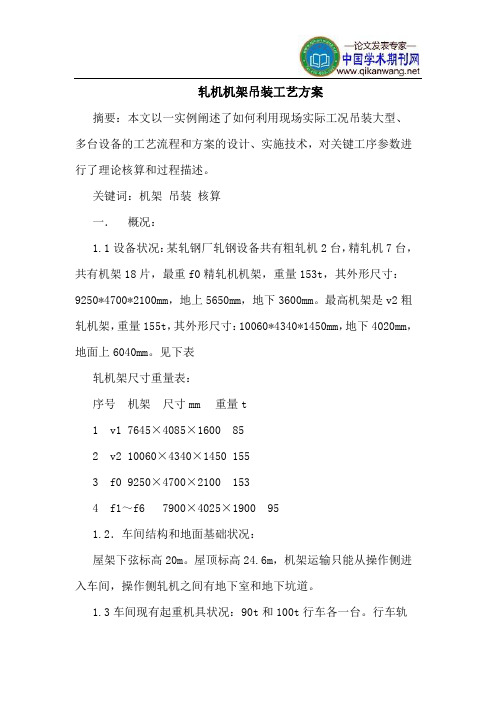
轧机机架吊装工艺方案摘要:本文以一实例阐述了如何利用现场实际工况吊装大型、多台设备的工艺流程和方案的设计、实施技术,对关键工序参数进行了理论核算和过程描述。
关键词:机架吊装核算一.概况:1.1设备状况:某轧钢厂轧钢设备共有粗轧机2台,精轧机7台,共有机架18片,最重f0精轧机机架,重量153t,其外形尺寸:9250*4700*2100mm,地上5650mm,地下3600mm。
最高机架是v2粗轧机架,重量155t,其外形尺寸:10060*4340*1450mm,地下4020mm,地面上6040mm。
见下表轧机架尺寸重量表:序号机架尺寸mm 重量t1 v1 7645×4085×1600 852 v2 10060×4340×1450 1553 f0 9250×4700×2100 1534 f1~f6 7900×4025×1900 951.2.车间结构和地面基础状况:屋架下弦标高20m。
屋顶标高24.6m,机架运输只能从操作侧进入车间,操作侧轧机之间有地下室和地下坑道。
1.3车间现有起重机具状况:90t和100t行车各一台。
行车轨道标高12m行车大梁下沿标高90t:11.5m,100t:11.24m;二.吊装方法分析选择:根据行车和设备状况,v1和f1~f6共14片机架在100t行车的起重量范围内,采用单台行车,制作专用吊具通过压下中心孔吊装;v2,f0的机架超过单台行车的起重量,不论从运输卸车和吊装,考虑本项目的工期和效率,应采用起重机械吊装,国外拆卸时使用400t汽车吊吊装,而国内这样大吨位的吊车比较少,使用时间很难自行掌握,另外考虑车间地面的结构原因,铺垫量大,吊车站位对影响车间其他设备安装的正常安装,而使用两台行车采用双机抬吊法吊装,需要采取以下措施:改造或制作一个吊梁,对吊装高度进行核算并设法降低机架的立直高度,即可进行。
轧机安装工艺流程
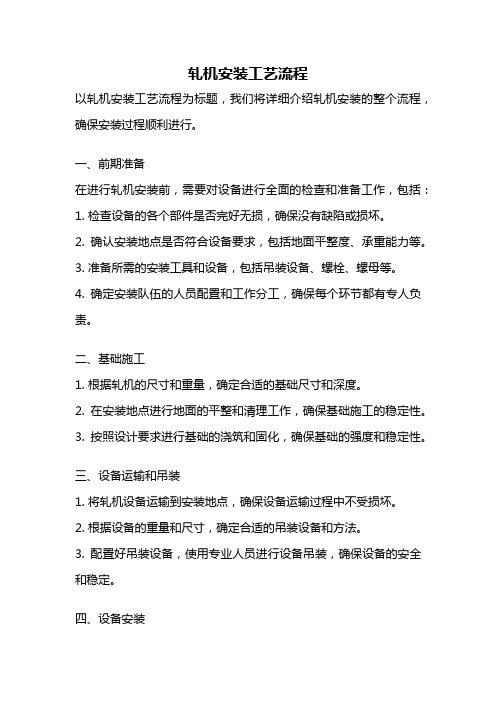
轧机安装工艺流程以轧机安装工艺流程为标题,我们将详细介绍轧机安装的整个流程,确保安装过程顺利进行。
一、前期准备在进行轧机安装前,需要对设备进行全面的检查和准备工作,包括:1. 检查设备的各个部件是否完好无损,确保没有缺陷或损坏。
2. 确认安装地点是否符合设备要求,包括地面平整度、承重能力等。
3. 准备所需的安装工具和设备,包括吊装设备、螺栓、螺母等。
4. 确定安装队伍的人员配置和工作分工,确保每个环节都有专人负责。
二、基础施工1. 根据轧机的尺寸和重量,确定合适的基础尺寸和深度。
2. 在安装地点进行地面的平整和清理工作,确保基础施工的稳定性。
3. 按照设计要求进行基础的浇筑和固化,确保基础的强度和稳定性。
三、设备运输和吊装1. 将轧机设备运输到安装地点,确保设备运输过程中不受损坏。
2. 根据设备的重量和尺寸,确定合适的吊装设备和方法。
3. 配置好吊装设备,使用专业人员进行设备吊装,确保设备的安全和稳定。
四、设备安装1. 根据设备的安装图纸和说明书,确定设备的安装位置和方向。
2. 使用螺栓和螺母等连接件,将设备固定在基础上,确保设备的稳定性。
3. 按照设备安装图纸进行设备的对中和调整,确保设备的运行平稳。
五、电气连接和调试1. 进行设备的电气连接,包括电源线、控制线等。
2. 根据设备的电气图纸进行接线,并进行接地处理,确保电气连接的安全可靠。
3. 对设备进行电气调试,确保各个电气元件的正常工作,包括电机、传感器等。
六、试运行和调整1. 在设备安装完成后,进行试运行,检查设备的运行状态和性能。
2. 根据设备的运行情况进行必要的调整,包括轧辊间隙、轧制压力等。
3. 进行设备的负荷试运行,确保设备在正常工作条件下的稳定运行。
七、安全检查和交接1. 对安装完成的设备进行全面的安全检查,包括紧固件的检查、电气系统的检查等。
2. 制定设备的操作规程和安全操作指南,确保操作人员的安全。
3. 进行设备的交接,将设备的使用和维护等相关事项告知使用单位。
轧机装配过程及验收

轧机装配过程及质量标准
1、认真检查所用轧辊的质量、轧槽的使用情况,测量轧辊的辊径值。
正确如实填写轧辊卡。
2、所有装配工作要小心,严禁使用蛮力拖出,轧辊吊运时不得碰撞。
3、轧辊拆开后检查轴承的使用情况。
检查压缩空气管路、油路。
要求做到油路、气路通畅。
4、检查轧辊的冷却水的管路是否通畅。
检查轧辊的冷却水管是否对齐所用轧槽。
要求做到水管通畅,冷却水管对准轧槽。
4、检查轧辊轴向调整机构,要求做到上辊轴向调整灵活。
5、对轧辊装配后的窜辊和辊缝值进行检测、调整,对轧辊进行转动,检查轧辊的转动情况。
要求按照工艺技术标准进行辊缝的调整。
7、连接好导卫的冷却水管、油管,并用压缩空气吹扫,检查是否畅通。
要求做到油路、气路通畅。
8、导卫的调整,进口导卫与轧辊间隙,粗轧约5㎜,中轧约4㎜,精轧约3㎜。
9、对安装好的轧机要进行记录,注明相关责任人。
10、将轧机吊至指定位置,摆放整齐,标识好。
轧机安装工艺简述
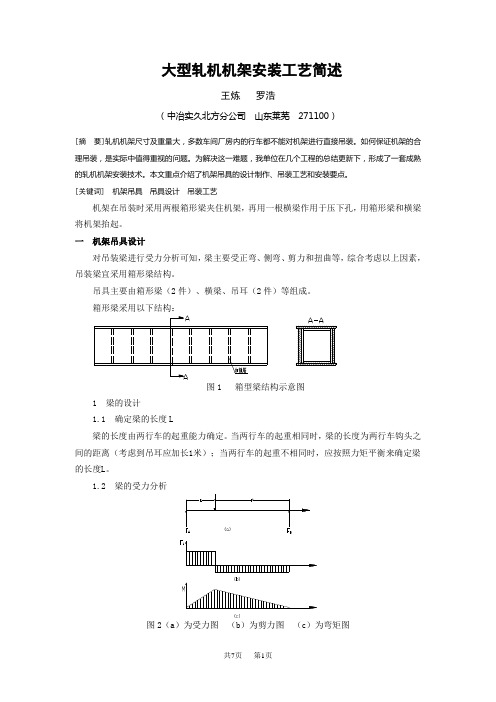
大型轧机机架安装工艺简述王炼罗浩(中冶实久北方分公司山东莱芜 271100)[摘要]轧机机架尺寸及重量大,多数车间厂房内的行车都不能对机架进行直接吊装。
如何保证机架的合理吊装,是实际中值得重视的问题。
为解决这一难题,我单位在几个工程的总结更新下,形成了一套成熟的轧机机架安装技术。
本文重点介绍了机架吊具的设计制作、吊装工艺和安装要点。
[关键词] 机架吊具吊具设计吊装工艺机架在吊装时采用两根箱形梁夹住机架,再用一根横梁作用于压下孔,用箱形梁和横梁将机架抬起。
一机架吊具设计对吊装梁进行受力分析可知,梁主要受正弯、侧弯、剪力和扭曲等,综合考虑以上因素,吊装梁宜采用箱形梁结构。
吊具主要由箱形梁(2件)、横梁、吊耳(2件)等组成。
箱形梁采用以下结构:图1 箱型梁结构示意图1 梁的设计1.1 确定梁的长度L梁的长度由两行车的起重能力确定。
当两行车的起重相同时,梁的长度为两行车钩头之间的距离(考虑到吊耳应加长1米);当两行车的起重不相同时,应按照力矩平衡来确定梁的长度L。
1.2 梁的受力分析图2(a)为受力图(b)为剪力图(c)为弯矩图12AF L F L= 12BF L F L = 其中: F —机架和梁的自重之和,即F=G+Q 中G 表示机架重量(已知)、Q 表示设计梁和吊耳的重量和(未知),Q 可以根据梁的截面尺寸计算式和吊耳的截面尺寸计算式的相关参数代替,在这里不作详细的代替过程的阐述。
从图(b )中可以确定:最大剪力tmax A =F F从图(c )中可以确定:最大弯矩max A 1=M F L 由公式可计算出截面模量:M max W 1.2f≥其中: f —抗弯强度 1.3 确定梁的截面尺寸1.3.1 腹板高度确定梁的高度由其经济性和刚度决定,经济性即梁最轻,刚度即为充分利用钢材强度,即满足梁的相对桡度W WL L ⎡⎤≤⎢⎥⎣⎦,桡度一般取1750。
按经济确定腹板高度:37300jw h=-按刚度确定腹板高度:[]min0.6fl E W L h= 其中: E —弹性模量f —材料屈服点按刚度确定的腹板高度应小于按经济确定的腹板高度,实际高度可以适当的大于计算结果。
轧机重点部位安装技术探析

轧机重点部位安装技术探析摘要:在科技水平不断提高的过程中,机器设备的安装要求也在逐渐提升,对于轧机设备而言,安装技术要求随着设备的不断更新发展也有明显的提升。
对于金属材料产品的生产加工,轧机的安装技术会对其产生一定的影响,从目前轧机设备的发展状况看,对设备安装的精度要求越来越高,因此安装技术非常关键。
本文主要针对轧机的重点部位安装技术进行了分析,以供参考。
关键词:轧机;安装技术;重点部位轧机主要是将金属锭、金属坯轧制成具体金属板材的成套设备,在金属轧制工艺流水线中属于核心设备,大多数金属板材都需要经过轧机进行轧制。
而在设备不断更新发展的过程中,对于安装技术要求也在逐渐提高,有关于轧机设备的重点部位安装技术,需要重视,使轧机的零部件之间安装精度进一步提高,对于设备的使用,能够有效的提高流水线生产的质量和效率。
1.调整垫板的安装安装轧机设备,最重要最基础的首先是对调整垫板的合理安装,这一部位的安装技术关系到荷载传递和应力的分散,同时对于轧机底座的调整也有很大的关联,对垫板安装最终的质量会影响轧机的使用期限以及轧机整体的运转精度。
通常在工程施工中使用的是灌浆法,同时对于垫板的规格以及材料等都需要做好设计,一组垫板的构成通常是一平两斜。
在安装垫板时,对于平垫板的处理需要进行固定灌浆,然后在安装时需要将基础表面进行凿毛。
利用锚固螺栓固定垫板和基础结构,接着调整螺帽以及螺杆,找平处理平垫板,然后用框式水平仪对其进行检查,横纵两个方向上的误差要保持在0.05‰的范围内,利用仪器检查合格后,再进行灌浆操作。
实施灌浆操作时,垫板以及基础固定位置不用接触,在灌浆的过程中需要注意的是,实施操作之前,混凝土表面需要保持湿润状态,同时在进行一侧灌浆操作时,垫板或者是模板都不能接触到。
另外在开始灌浆时,疏导拌合物可以通过推板进行,在对一块垫板进行灌浆时,需要保证在初凝之前完成所有的灌浆操作,并且灌浆完成后需要养护7天,在养护完工后,再一次检查垫板,确保垫板安装的质量,如果发现有任何不满足规范要求的,就需要重新安装,直到合格为止。
MPM轧机工艺及其施工技术
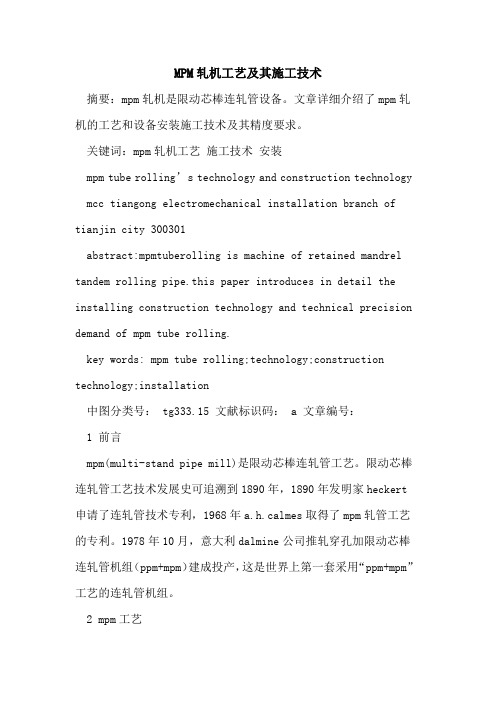
MPM轧机工艺及其施工技术摘要:mpm轧机是限动芯棒连轧管设备。
文章详细介绍了mpm轧机的工艺和设备安装施工技术及其精度要求。
关键词:mpm轧机工艺施工技术安装mpm tube rolling’s technology and construction technology mcc tiangong electromechanical installation branch of tianjin city 300301abstract:mpmtuberolling is machine of retained mandrel tandem rolling pipe.this paper introduces in detail the installing construction technology and technical precision demand of mpm tube rolling.key words: mpm tube rolling;technology;construction technology;installation中图分类号: tg333.15 文献标识码: a 文章编号:1 前言mpm(multi-stand pipe mill)是限动芯棒连轧管工艺。
限动芯棒连轧管工艺技术发展史可追溯到1890年,1890年发明家heckert 申请了连轧管技术专利,1968年a.h.calmes取得了mpm轧管工艺的专利。
1978年10月,意大利dalmine公司推轧穿孔加限动芯棒连轧管机组(ppm+mpm)建成投产,这是世界上第一套采用“ppm+mpm”工艺的连轧管机组。
2 mpm工艺2.1 mpm生产工艺流程采用mpm工艺轧管时,经穿孔延伸的毛管,抽出顶杆后被送至吹硼砂站,由一特制的喷嘴向毛管内部吹入硼砂,其作用是吹掉毛管内部的氧化铁皮,硼砂在高温状态下生成雾状气体,充满管内,防止在随后的运动中空气进入,使内表面产生二氧化碳。
- 1、下载文档前请自行甄别文档内容的完整性,平台不提供额外的编辑、内容补充、找答案等附加服务。
- 2、"仅部分预览"的文档,不可在线预览部分如存在完整性等问题,可反馈申请退款(可完整预览的文档不适用该条件!)。
- 3、如文档侵犯您的权益,请联系客服反馈,我们会尽快为您处理(人工客服工作时间:9:00-18:30)。
精轧机安装工艺方案1概述:精轧机列由F0-F6七架轧机以及相应的高压水除鳞、出/入口导卫、活套、测量房等组成。
精轧机属四辊轧机,每台精轧机主要部件由两片机架、底座、压下装置、主传动电机、变速箱、传动箱、传动轴、换辊装置、力辊装置、出入口导卫等所组成。
包括液压、润滑、冷却、除磷等系统的设备设备本体配管。
轧制线上的所有设备均是利用国外利旧拆迁的二手设备,各设备的安装精度参照执行YB9249-93《冶金机械设备安装工程施工及验收规轧钢设备》中的Ⅰ级精度作为本线设备的安装目标标准。
2施工人员计划3主要机工具计划主要工机具计划表4安装工艺4.1轧制设备安装工艺4.1.1轧制设备安装工艺流程4.1.2施工方法和注意事项4.1.2.1基础验收、放线、埋设标板设备安装前,依据设备安装图和土建单位的提出的检验记录对基础进行检查验收,其标准符合YBJ201-83《冶金机械设备安装工程施工及验收规通用规定》表1的规定。
对基础尺寸不合格的应及时出具检查报告交甲方进行处理直至提供设备安装所必须的合格基础。
轧机线对中心线的偏差要求很高,如何保证精轧机的水平轧制中心线就位准确十分重要。
在施工时,各工序必须使用同一纵向基准线、横向基准线和标高基准点,并确保各工序之间的正确衔接。
设备的放线工作应会同甲方、监理工程师等有关人员共同进行,根据甲方提供的基准线和基准点,放出各安装所需的基准线和基准点,并埋设标板,标板应有显著的标记,以便于识别。
对于安装来说,设备的纵横中心基准线有可能被设备就位后遮挡,应在设备边框外侧放一些辅助纵横中心线,并且应考虑在不同的高度位置,便于设备安装时的检测。
比如说:轧机机座的放线,考虑到操作检测的需要,轧制线的辅助线应设在机座上表面大约100mm,F0至F6的横向中心基准线应设在±0.00mm以上,安装轧机底座用辅助线,应放在轧机底座上表面下100mm,检测机架用辅助线,应放在轧机窗口的底部。
放线确定设备相关位置的尺寸,较大跨度的尺寸,拉尺测量,应考虑修正值。
测定相对标高应注意, 除轧机本体之外,还有驱动等附属设备,本体与辅机之间存在相对标高差。
需要比较精确的标高基准点,保证轧机本体与各辅机之间的相对标高,应在已确定的轧机底座上表面检测,确定各辅机标高,检测采用高精度水准仪(0.01mm)。
F0放线依据图号:120FHO67;199-301Y22F1~F6放线依据图号:120FH067;199-301Y22F0底座标高测定依据图号:160FG019F1~F6底座标高测定依据图号:220FG0244.1.2.2设备倒运、开箱、清洗将所需安装的设备按安装的先后顺序,倒运至厂房的暂时周转地点开箱、清点。
设备开箱清点时应会同厂方的有关人员一起进行,开箱是应细心仔细,不得野蛮拆箱,防止损坏设备及部件。
开箱时如发现包装箱损坏或设备及部件损坏应及时做好记录,在设备及部件清点时一要注意检查有无损坏,二要清点规格数量,如发现和设备装箱单不符时,应及时记录,三方人员应在设备开箱清点后,在设备开箱记录表上办理签字手续。
设备尤其是部件在开箱后如不马上进行安装,应及时封箱,避免丢失。
开箱时如有设备的备品备件应交厂方妥善保管,防止丢失和损坏。
设备及部件在开箱后,根据安装要求分批进行清洗。
清洗用清洗剂或柴油、煤油进行。
在设备及部件清洗时,如发现接触面有毛刺等缺陷时应及时修整,如发现设备及部件有损坏应及时向主管技术人员汇报,由项目工程师出具报告交厂方专家进行处理。
设备及部件在清洗后如不及时安装,应在机加工面和接触面涂抹机油或黄干油,防止部件生锈。
4.1.2.3设备放线、垫铁布置、座浆、基础铲麻面在设备基础上将设备的外轮廓线、各中心线和地脚螺栓孔的中心线,垫铁位置标出。
将设备基础二次灌浆接触面,用风镐或錾子凿成麻面以便二次灌浆。
设备垫铁的布置必须认真对待,要遵循尽可能靠近地脚螺栓,均匀分布,便于调整的原则。
垫铁座浆时,每组垫铁的水平度应控制在0.10/1000围,标高偏差在-3mm至-5mm之。
若座浆垫铁的水平超差,在座浆水泥凝固后,可用角向磨光机打磨至水平度合格。
详细座浆方法可见座浆工艺。
4.1.2.4轧机机座的安装按要求做完垫铁座浆后,可搁放机座,进行机座的找平找正工作,F0—F6轧机的18条机座是机架的基准,也是各辅机的基准,轧机底座安装这一工作对轧机来说是相当重要,,对于F1-F6轧机12条机座构成的约30m×4.5m平面,平面度要求较高。
如何测定、操作这一平面的要求分初平、找正、精平三步走。
初平:先用水准仪加框式水平仪进行初平,确定各条机座自身的水平以及相邻各条的标高值基本控制在一个水平上。
精平:各机座自身的纵横水平可用平尺、等高块加框式水平仪检查测定,最终检测用高精度水平仪,看是否同时满足平面度要求以及整个平面的标高要求。
找正:对于各成对机座找正控制位置尺寸精度按原设备安装说明书或参照冶金机械安装规。
但必须注意一点,F0—F6之间有中间机架连接,各台轧机之间的间距要保证要求。
机座找正、找平可采用框式水平仪、平尺、等高块、高精度水平仪、径千分尺、激光测距经纬仪、钢丝、线坠。
机座的调整应以F3机座为准向两头机座进行调整,并通过检查相邻机座的水平、标高来决定前后机座的标高。
调整每台机座时,其横向中心线以入口侧机座为准,并保持机座与主传动中心线的平行度。
调整结束,按地脚螺栓紧固工艺方法拧紧。
底座安装调整示意图底座安装精度表4.1.2.5.轧机机架的调整检测底座调整完毕后,进行机架的吊装。
机架分传动侧和操作侧两片机架,通过上、下横梁连接成一体。
机架吊装采用90吨行车或400吨汽车吊,专用吊具用德国拆卸时自制的。
就位时应在机架与底座的结合面上涂抹润滑剂(如二硫化钼),以利机架的移动。
吊入时要特别注意机架与机座的位置, 机座宽度与机架座的宽度之间,最大的间隙只有0.6mm,机架要吊平,否则,机架就位很容易把机座挤走。
精轧机的入口侧机座是基准机座,在吊入前可将出口侧机座地脚螺栓稍微松开,由机架将机座撑开,机座就位后再用液压千斤顶将出口机座顶回。
机架安装时,先装传动侧机架,再装操作侧机架,找正并检测铅垂度。
两机架间距粗调时要大于设计尺寸,已利于上、下连接梁的吊入。
同台轧机两片机架吊装完毕,进行该台轧机上、下横梁的吊装联接适当拧紧连接螺栓,插入机座与机架处的定位块。
机架吊装完毕,上下横梁安装后,进行机架的检测工作。
检查:机架窗口的垂直度,两窗口的平行度,两窗口底面的水平和标高,机架侧的垂直度,以及各机架相对纵横中心线的偏差,塞尺检查机架与底座的结合面,打紧定位块,塞尺检查上下横梁与机架结合面,按技术要求拧紧所有联结螺栓及地脚螺栓。
检查上述容如发现偏差(安装偏差),应对机座进行调整,不允许在底座与机架之间,机架与上下横梁之间垫任何东西进行调整。
机架调整检查完后,根据机架检测所确定的轧机纵横中心线,检查所有以前所放的线及基准标高,有必须调整的应调整。
若F0-F6所有精轧机机架的安装位置精度都符合要求,将机座和机架的地脚螺丝、联结螺丝用锤击板子锤击拧紧。
这时可以考虑精轧机架的在线机加工改造和辅机设备的安装全面铺开。
机架安装调整附图机架安装精度表4.1.2.6.机架窗口衬板的安装机架窗口衬板安装是一件比较繁琐的工作,衬板种类多,数量多,并且装配后的尺寸精度要求高,主要要保证支承辊、工作辊、轴承座与衬板之间的滑动间隙,窗口对称衬板装好后,要用千分尺检查尺寸是否符合要求,这部分参阅图纸。
安装时注意衬板与窗口结合面要刷一层厚度为0.2mm粘接剂,所有衬板联结螺栓都要用粘接剂。
4.1.2.7压下装置压下装置实际是一个轧制厚度调整装置,控制上支承辊水平位置。
以保证轧板厚度。
粗轧机的压下装置是由电动机、减速箱、蜗轮蜗杆副、丝杠螺母副、制动器组成的。
F0轧机的压下装置是由电动机、行星齿轮副、丝杠螺母副、组成的。
F1-F6精轧机的压下装置是液压控制压下装置(HAGC)。
安装时参照VAI的图。
粗轧机的压下装置的安装顺序:丝杠螺母―――蜗轮蜗杆――――减速箱――――电动机――――制动器。
F0轧机压下装置的安装顺序:螺母―――丝杠、行星齿轮副――――电动机―――风冷系统。
F1-F6精轧机压下装置的安装顺序:压下油缸―――――液压阀台――――配管。
4.1.2..8支承辊平衡装置支承辊平衡装置主要作用是用液压缸的推力来平衡上轧辊、轴承座和压下螺杆的,使压下螺杆和上轧辊轴承之间消除间隙,避免轧钢咬入时产生冲击。
安装时应把轧机顶部钢平台滑架先装上,然后装上横梁顶部的提升液压缸,再装前后侧的提升夹板装置,装配联结螺栓要用粘接剂。
安装F1-F6精轧机的支承辊平衡装置时参照VAI的图。
4.1.2.9换辊装置安装F1~F6精轧机原有工作辊液压换辊装置,F0精轧机有支撑辊和工作辊换辊装置,经过改造后,F1~F6精轧机增加支撑辊换辊装置。
精轧机支撑辊换辊装置由液压油缸、滑轨、盖板组成。
精轧机工作辊换辊装置由液压油缸、滑轨、横移平台组成。
精轧机换辊装置安装方法是:先安装支撑辊换辊装置,后安装工作辊换辊装置。
支撑辊换辊装置的安装方法:根据轧机横向中心线先装滑轨,调整滑轨上平面与轧机架窗口底面平齐,同时找准中心线、水平,用螺栓将滑轨与机架联结固定,检查滑轨的标高、水平、跨距。
再安装推拉液压油缸,在油缸座两侧找横向水平,在油缸活塞杆上找水平。
调整结束,在滑轨上涂油脂。
将支撑辊换辊装置装完,然后根据轧机的横向中心线安装横移平台的轨道及移动装置,然后再安装翻转推拉液压油缸装置。
调整横移平台上的导轨中心线与轧机架重合,调整导轨的水平、标高。
根据精轧机横向中心线安装工作辊推拉油缸装置,必须保证其轴线与精轧机横向中心线间距、标高和水平度。
调整完毕后,点焊垫铁,紧固螺栓,联结油管。
工作辊弯辊装置(CVC)精轧机经过改造,在F4~F6精轧机上安装弯辊装置。
工作辊弯辊装置是装在上下工作辊轴承座之间的传动、操作两侧机架窗口上。
它的作用:一是提供上下反向力使上下工作辊都依俯在上下支承辊上;二是在轧机工作状态,工作辊在轧制力的作用下,像一根承重梁挠曲变形,利用该装置在工作辊的两头施加一反向力,使工作辊强制变形,从而保证轧制带钢的厚度一致。
这部分参阅V AI的图,它主要有4个上下双向行程的液压缸以及其他部件所组成,安装时联结螺栓要用粘接剂。
4.1.2.10工作辊锁定轴向移动装置精轧机经过改造,在F4~F6精轧机上安装窜辊装置。
工作辊锁定轴向移动装置,装在操作侧的机架上,它主要有4个锁定缸和4个轴向移动缸所组成,工作时锁定缸锁住操作侧的工作辊轴承座,移动缸使工作辊轴向移动到位,并且在操作侧工作辊轴承座上始终加一径向力,使工作辊定位。
这部分参阅VAI图,安装时注意传感装置以及液压缸的装配标记,没有特别记号的联结螺栓要用粘接剂,定位板装配要用粘接剂。