TPM全面生产维护实战训练149页
TPM全员生产性维护培训

路漫漫其悠远
寓言故事中的TPM
事情并不如想象中那么顺利,先是鸟俊滨那组总是嫌其他两组太慢 ;后来当过花农的蛇秀辉发现,大家找来的石头大部分都不是玫瑰红的 ;最后由于地形不熟,大家经常日复一日地在同一个房间里找灵石。大 家的信心又开始慢慢丧失。
第二天,醉敏把这个梦告诉六个伙伴,有四个人相信,只有草鱼文 利和鸟俊滨愿意和他一起去努力。
开始的几天里,草鱼文利想先找些木柴生火,这样既能取暖又让房 间里有些光线;鸟俊滨想先找那个有食物的房间;而醉敏想快点把240块 灵石找齐,好快点让咒语解除。三个人无法统一意见,决定各找各的, 但几天下来,三个人都没有成果,倒是累得筋疲力尽,其他四个人取笑 不已。
经过交流,大家发现,有些人找准房间很快,但在房间里找到的石 头都是错的;而那些石头找得非常准的人,往往又速度太慢,其中的道 理是具有专业素质的人才很关键。于是在草鱼文利的提议下,大家决定 每天开一次会,交流经验和窍门,然后,把有用的那些都抄有亮光的墙 上,使大家少走弯路。
路漫漫其悠远
寓言故事中的TPM
路漫漫其悠远
TPM常用的缩写
•DT •FA •FTA •MCBF •MCTR •MTBA
路漫漫其悠远
■ TEM活动中常用术语
• DT-Scheduled Downtime 计划停机时间 • FA-Failure Analysis 失败(效)分析 • FTA-Fault Tree Analysis 故障树分析 • MCBF-Mean Cycle Between Failure 平均故障间隔周期 • MCTR-Mean Cycle-To-Repair 平均修理周期 • MTBA-Mean Time Between Assists 设备平均所需辅助间隔时间 • MTBF-Mean Time Between Failures 平均故障间隔 • MTTA-Mean Time To Assist 平均辅助时间 • MTTC-Mean Time To Convert 平均转换时间 • MTTR-Mean Time-To-Repair 平均维修时间 • OEE-Overall Equipment Effectiveness 设备综合效率
《TPM全面生产维护实战训练》

TPM全面生产维护实战训练课程背景:设备是企业的基本生产工具,它的好坏直接关系到产品的质量优劣和生产周期的长短。
目前国内的企业跟本谈不上设备管理,叫着“小车不倒直管推”。
设备管理的内容基本上就是设备事后维修,这种状况给企业的生产成本带来极大的负担。
课程收益:1.了解TPM设备管理的精髓:谁使用谁保养、从事后维修转变为预防维修;2.了解设备管理的范围及要求;3.学会制定设备的:1、操作规程;2、使用规程;3、维护规程;4.了解TPM的两大基石和八大支柱的具体内容;5.掌握TPM活动开展的三个阶段和八个步骤;6.掌握以现场为中心的自主管理活动推进流程;7.学会以现场为中心的自主管理活动的七大方法;8.学会如何开展以效益为中心的焦点改善活动;9.掌握焦点改善九步方法;10.学会如何开展以员工为中心的提案活动;11.学会如何计算设备时间稼动率;12.学会如何计算设备性能稼动率;13.学会如何计算设备综合效率;14.学会如何制定设备点检表;15.学会如何开展设备点检活动实战型管理教练-黄俭老师简介:滨江双创联盟荣誉理事长;上海蓝草企业管理咨询有限公司首席讲师;多家知名企业特聘高级管理顾问。
黄老师多年在企业管理、公司战略规划、市场营销、品牌建设、员工管理、绩效考核、上市公司等等方面有着丰富的实践经验;深刻理解了东西方管理精髓。
进入培训教育行业,作为资深培训讲师,在企业内训课、公开课、CEO总裁班等百余家企业和大学课堂讲授战略管理、营销管理、品牌管理等领域专业课程,结合自身的企业实践和理论研究,开发的具有知识产权的一系列新营销课程收到企业和广大学员的欢迎和热烈反馈。
听黄老师上课,可以聆听他的职场经历,分享他的成绩,干货多多!课程突出实用性、故事性、新鲜性和幽默性。
宽广的知识体系、丰富的管理实践、积极向上、幽默风趣构成了独特的教学培训风格,深受听众欢迎。
通过一系列案例剖析点评,使管理人员掌握一些管理先进理念,分析技巧、提高解决问题的能力。
TPM全面生产维护实战训练

编制设备操作规程时,应该以制造厂提供的设备说明
书的内容要求为主要依据。
设备使用规程
B
是对操作工人使用设备的有关要求和规定。例如: 操作工人必须经过设备操作基本功的培训,并经过
考试合格,发给操作证,凭证操作;不准超负荷使
用设备;遵守设备交接班制度等。
设备维护规程
C
是指保证设备正常运转而必须采取的
措施和注意事项。例如:操作工人上班时
方法1:红牌作战(问题票)
序号 1 2 3
4
项
目
红牌作战的目的
红牌作战的对象
内
容
通过醒目的红色标志标明现场存在的问题,使所有人都能一目 了然地知道管理上的缺点在哪里,对培养员工的问题意识,督促 员工快速改善具有重要意义
自主管理的五大内容
会处理小故障
了解设备的 构造和性能
1
LOREM
会正确 操作设备
会诊断故障
会保养设备
以上各条对应的措施是什么
17
自主管理三要素
纳入绩效考核
01
员工要有自主 管理的意识
03
自主管理要 求员工付诸
行动
02
员工要有自主
管理的能力
如何才能做到这三条呢
培训
3、 自主管理的意义
打破传统 分工的局限
成功推进TPM的技巧与条件
30%
25%
02
高层
意志坚定
45% 中层的积极推动 中层管理者始终扮演 着主要推动人的角色
01
企业高层的意识虽然是推动管理的诱导性
因素,但却不是成功推行TPM活动的最重
要条件
03
基层的全面参与
没有基层员工的参与,那么TPM
全面生产维护TPM管理实战
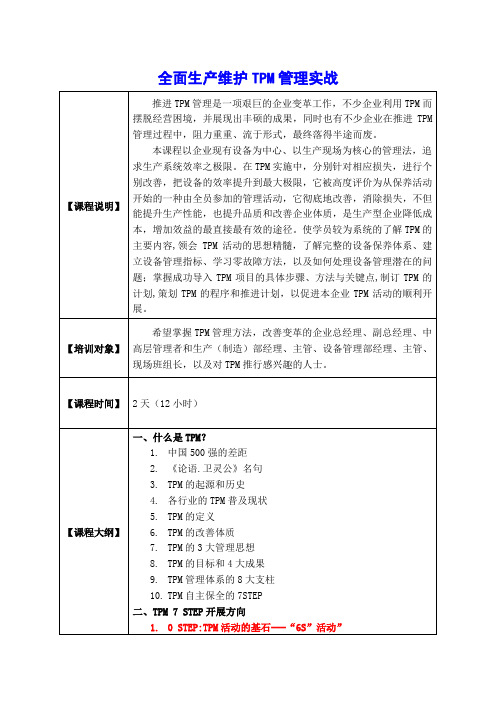
6.研究清扫工具
7.问题点的清单
8.2 STEP:发生源和困难源的对策
9.发生源和困难源的分类
10.挑出“二源”的方法,填写“二源”清单
11.绘制困难点简图,KNOW-WHY分析
12.KNOW-WHY分析表
13.“二源”对策表
14.OPL的概念,制作方法和使用要领
15.OPL的格式和目的
5.何谓焦点?
6.业务部门的焦点改善如何选题课题?
7.课题的评价项目
8.事务改善的7个步骤
9.课题改善查找问题点的方法
10.8大浪费
11.课题事例:瞬间停止的改善课题事例
12.课题事例:减少初期损失的改善课题事例
13.课题改善的步骤
14.诊断活动
15.诊断提交表
16.诊断过程,评委构建
17.诊断结果评价
35.多能工培训的5个步骤
36.教育学分制
37.技能水准
38.点检效率化的目的和目标
39.可视化改善的着眼点
40.可视化Biblioteka 善的案例41.点检的预知化
42.他机点检和部件展开案例学习
三、TPM的开展机制
1.员工提案活动
2.提案活动的意义和范围
3.提案的评价机制,提交流程,激励方法
4.焦点课题改善活动(事务改善)
四、设备管理
1.设备管理的目的和目标
2.专业保全的必要性和目的
3.保全方式的分类
4.设备管理的意义和范围
5.何谓设备的“一生”
6.设备的要求条件:DREAM
7.设备管理的2大指标:MTBF MTTR
8.MTBF和MTTR的计算方法
9.现场练习:计算MTBF和MTTR
《TPM一线班组长生产维护实战训练》
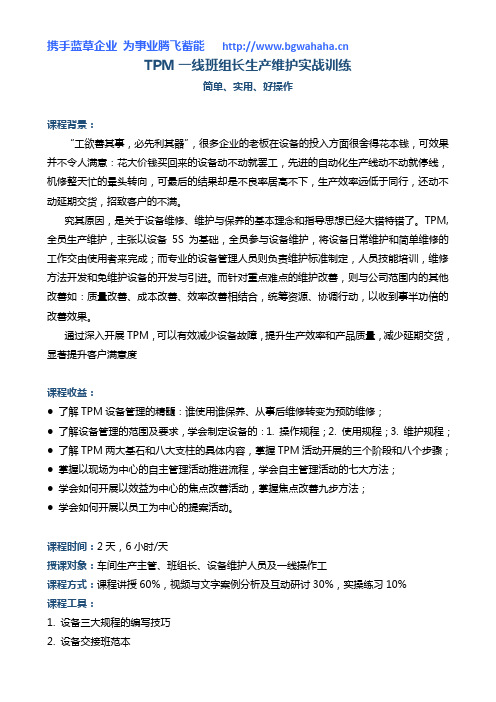
TPM一线班组长生产维护实战训练简单、实用、好操作课程背景:“工欲善其事,必先利其器”,很多企业的老板在设备的投入方面很舍得花本钱,可效果并不令人满意:花大价钱买回来的设备动不动就罢工,先进的自动化生产线动不动就停线,机修整天忙的晕头转向,可最后的结果却是不良率居高不下,生产效率远低于同行,还动不动延期交货,招致客户的不满。
究其原因,是关于设备维修、维护与保养的基本理念和指导思想已经大错特错了。
TPM,全员生产维护,主张以设备5S为基础,全员参与设备维护,将设备日常维护和简单维修的工作交由使用者来完成;而专业的设备管理人员则负责维护标准制定,人员技能培训,维修方法开发和免维护设备的开发与引进。
而针对重点难点的维护改善,则与公司范围内的其他改善如:质量改善、成本改善、效率改善相结合,统筹资源、协调行动,以收到事半功倍的改善效果。
通过深入开展TPM,可以有效减少设备故障,提升生产效率和产品质量,减少延期交货,显著提升客户满意度课程收益:●了解TPM设备管理的精髓:谁使用谁保养、从事后维修转变为预防维修;● 了解设备管理的范围及要求,学会制定设备的:1. 操作规程;2. 使用规程;3. 维护规程;● 了解TPM两大基石和八大支柱的具体内容,掌握TPM活动开展的三个阶段和八个步骤;● 掌握以现场为中心的自主管理活动推进流程,学会自主管理活动的七大方法;● 学会如何开展以效益为中心的焦点改善活动,掌握焦点改善九步方法;● 学会如何开展以员工为中心的提案活动。
课程时间:2天,6小时/天授课对象:车间生产主管、班组长、设备维护人员及一线操作工课程方式:课程讲授60%,视频与文字案例分析及互动研讨30%,实操练习10%课程工具:1. 设备三大规程的编写技巧2. 设备交接班范本3. TPM全面生产维护的两大基础和八个支柱4. 设备难以清扫的三大困难源及对策5. 设备自主管理的五大内容6. 设备自主维修七步法7. 设备自主保养的五个范围8. 设备自主保养的3个阶段9. 设备自主保养的3大法宝10. 推行设备自主保养的7大方法课程大纲第一讲:TPM发展过程与核心理念一、TPM关键指标介绍1. OEE——综合设备效率2. MTBF——平均故障间隔时间3. MTTR——平均维护时间二、TPM发展过程1. 设备维修体制发展过程2. TPM的改善发展过程三、TPM核心理念1. 以设备5S为基础的全员参与2. 以强调预防为主保全体系实施3. 以“零事故、零不良、零故障“为追求目标管理四、关于设备维护的认识误区1. 操作人员只管使用,不管保养2. 保养维护只与机修且只有机修才会做3. 故障停机很正常,没必要大惊小怪4. 修都修好了,还做什么记录?5. 开机、调整谁不会,还要什么标准视频案例&互动思考:某苏北化工企业大爆炸与设备管理的关系第二讲:TPM维护方法一、TPM维护八大支柱1. 自主维护2. 计划维修3. 个别改善4. 人员培训5. 环境改善6. 专业改善7. 设备早期管理8. 质量改善二、TPM自主维护的目标、方法与步骤1. 自主维护的目标2. 自主维护的方法与步骤1)初期清扫2)发生源困难部位对策3)制定自主保全的临时基准4)总点检5)自主点检6)标准化7)自主管理三、TPM计划维修的目标、方法与步骤1. 计划维修的目标2. 计划维修的方法与步骤1)选择维修工作次序2)改进现行维修方式3)确定维修标准4)开展维修相关工作5)提高设备维修效率6)设备的全面诊断7)建立设备维护体系互动思考:自主维护与计划维护的重点有何不同?。
2020年(TPM生产维护)新TPM工厂全面改善实战训练

(TPM生产维护)新TPM —工厂全面改善实战训练独创国内现场情景摸拟训练,全体学员现学现用——《新TPM—工厂全面改善实战训练》课程背景:中国已经成为世界制造大国(而不是强国)!正在人们为之雀跃的时侯,巨大的运营压力来临啦。
全球性的金融危机、原材料涨价、劳动力成本上升、出口退税政策调整、人民币升值、世界性的贸易保护主义愈演愈烈。
所有这些都在压迫着中国制造业本就脆弱的脊梁。
壹些心存侥幸和毫无准备的企业终于为此付出了代价且不得不退出竞争,更多的制造型企业仍在坚持着,期望能够顺利渡过难关。
在许多工厂里,生产过程控制不好,产品质量不高;生产计划及物料管理不善,造成产品积压或库存过高,占用资金多;现场管理水平不高,有脏乱不堪现象,影响生产效率及工厂形象;员工积极性不高,企业活力不够;劳动生产率和设备效率低下,事故、工伤、故障、浪费多;人力资源管理缺少办法,劳资关系紧张等。
所有这些都是广大企业普遍存在的问题。
为解决困惑广大制造型企业的之上问题,我们开发了《新TPM—工厂全面改善实战管理课程》,从中可寻求到问题的解决答案和方法。
课程目的:为制造型企业广大管理技术人员提供工厂全面改善的思路、方法、手段和工具.课程效果:如持续地坚持不懈的运用,体当下1、有形成果:生产(人和设备)效率明显提升;不良品率明显降低;生产和管理周期明显缩短;库存量、资金积压明显减少;各类损耗、浪费、生产成本明显降低;顾客投诉明显减少,顾客满意度明显上升;员工提案和发明创造能力明显提升;其他有形成果2、无形成果企业全面改善文化形成员工的改善意识、参和意识提高;员工精神面貌改观,企业凝聚力增强;员工自信心增强,能力水平提高;企业形象改善;其他无形效果受训对象:制造型企业班组长(含)之上管理技术人员课程时间:单纯讲课重点讲2天/12小时祥细讲7天/42小时如需现场辅导除外课程大纲:第壹章TPM全面改善实战第一节、TPM的发展及其作用1、TPM的起源和发展2、TPM活动的定义3、TPM和TQM的比较4、TPM的活动体系5、TPM的俩大基石6、TPM八大支柱的内容第二节、TPM全面改善在中国的成功实践1、企业推动TPM活动的困难2、TPM全面改善的定义3、TPM全面改善的的三大活动机制4、工厂改善的三大管理思想5、全面改善追求的目标和期待的成果第三节、TPM全面改善的成功导入1、X公司高层宣布推进2、改善活动导入培训和宣传3、全面改善活动的组织的建立4、全面改善活动方针目标设定5、改善活动大计划制作6、改善活动正式启动7、5S活动(0STEP)推进8、自主管理(1-5STEP)活动开展9、员工提案活动的开展10、焦点改善活动推进11、活动成果总结12、持续运营的三大活动机制第四节、TPM全面改善导入前的准备1、推进工作的特点2、推进工作的人才准备3、成功推进的技巧4、成功推进全面改善活动的条件第二章、自主管理成就卓越现场第一节、自主管理的意义1、保全活动的分类和自主管理2、自主管理活动的三大要素3、正确认识和规划自主管理活动4、微缺陷成长和倍增法则5、自主管理活动的积极意义6、自主管理活动的步骤7、自主管理活动期待的效果8、如何评价自主管理活动成效第二节、自主管理活动内容简介1、初期清扫(微缺陷挖掘和复原改善)2、“俩源”改善对策3、点检标准制订4、点检工作效率化改善5、自主管理体制建立6、活动导入五个步骤之间的关系7、自主管理活动导入完成后怎么办第三节、导入自主管理活动的准备1、推进组织的建立2、自主管理基础知识教育3、活动方针的制订4、活动导入过程中应注意的问题第四节、初期清扫的推进1、识别初期清扫实施的对象、制订活动计划2、集中消除微缺陷3、有效的推进办法:问题票活动4、阶段活动成果总结和诊断实施第五节、“俩源”改善对策活动1、登记发生源和困难源,制订改善计划2、对问题进行对策改善3、问题对策改善的常用工具4、阶段活动成果总结和诊断验收实施第六节、点检标准制订的推进1、对操作者的教育2、点检项目的确定3、点检表格的制订和点检的实施4、阶段活动成果总结和诊断实施第七节、点检效率化推进1、点检内容的简化和优化2、目视管理活动的开展3、点检通道的设置4、创意目视管理改善5、阶段活动成果总结和诊断实施第八节、构建自主管理机制第九节、现场诊断的准备和营运1、诊断前的准备和营运2、现场诊断的实施第三章、提案活动发掘员工智慧第一节、提案活动和全员参和1、提案活动和提案的自主实施2、改善提案不同于提建议3、提案活动的积极意义第二节、走出提案活动的误区第三节、提案活动的运营管理第四节、激活提案活动的办法第五节、认识管理中的问题点第六节、提案标准和事例1、提案活动标准范例2、改善事例解说第四章、焦点改善提升管理绩效第一节、焦点改善活动概要第二节、焦点课题定义和成果评价第三节、焦点改善的PDCA法1、PDCA和SDCA管理循环2、解决问题的八步法第四节、焦点改善的项目管理第五章、焦点改善案例学习第一节、如何提高生产效率1、生产效率化改善的基本思路2、影响生产效率的16大损耗3、管理活动中的损耗构造图4、设备方面的损耗及效率计算5、人员方面的损耗和劳动生产率6、材料投入等3大损耗的计算第二节、效率化改善小案例学习案例1:安排和调整损耗减低案例2:生产组织损耗减低案例3:材料投入损耗减低第三节、焦点改善管理制度第四节、焦点改善课题案例学习第五章课程总结和交流探讨授课专家:国内资深工厂管理实战派专家王小伟老师。
TPM全面生产维护培训图文PPT课件

*
以构筑企业组织结构,追求最大限度提高经营系统效率为目标。 以生产体系的全体为对象,确立预防 “灾害、故障、不良”等所有浪费的体制。 包括生产、开发、销售、管理等所有部门。 从总裁到第一线工作人员的全体员工参加。 依靠重复小组的活动达到浪费为 0。
TPM 历程
*
TPM活动内容
建立健全 追求生产系统效率极限化的体质
2000
提高率
201%
单位:百万美圆
综合效率
83.8
87.5
79.9
70
80
90
1998
1999
2000
提高
38
%
人均生产量
307
392
210
100
300
500
1998
1999
2000
提高
87
%
单位:台/套
不良率
12584
9435
15675
0
10000
20000
1998
1999
2000
单位:PPM
可使用性 x 运行率 x 合格率
Overall Equipment Effectiveness 综合设备利用率
=
六大类损失
1. 设备故障停机
6. 启动阶段和产量减少
5. 生产中有次品
3. 怠工和小故障
4. 速度减慢
2. 调试和调节
可使用性损失
运行损失
质量损失
净生产时间
怠工& 速度损失
生产作业时间
TPM使企业效率达到最佳
TPM
Input 投入
Output 产出
产出 投入
=
TPM全面生产维护(TPM)实践讲义

TPM全面生产经营系统(Total Productive Management system;TPS)
18
1. 全面生产维护(TPM)概述
事后维护(Break-down Maintenance)
指当设备发生故障后停止或性能显著劣化才修理的维护方式,就 好象人生了病才去看病一样。
实施方式分为突发修理和事后修理。突发修理是指突发的故障, 故障后马上修理;事后修理是指故障修理时,若有备用设备,可 以事后修理并处置。
34
全面生产维护(TPM)实践
2.
设备日常管理
35
2. 设备日常管理
维护设备
发展一个可持续的环境
改善设备
最高要求水平的业绩
设备管理
采购设备
低成本的生命周期
36
2. 设备日常管理
识别问题
确定现有 的条件
改善设备
解决问题
37
TPM 设备状况分析
设备编号 # 日期可靠性/意见: 设备描述 评估人 -
使命、承诺
客户
• 更高质量 • 可靠交付 • 降低成本
公司 是由股东投资, 致力于通过提供 良好的安全、质量和 产品使客户更具有竞争力。 投资者
• 改进的收益率 • 改进的资金流 资源
雇员
• • • • 提高安全 减少浪费 易于维护 提高士气
7
1. 全面生产维护(TPM)概述
世界级模式 企业价值
优先发展
13
1. 全面生产维护(TPM)概述
TPM的活动对象
在已建立的生产系统中,以设备整个生命周期为对象,追求 零故障,防止损失发生。这是达成以往TPM目标的手段和方 法。 目前,这不仅指已建立成形的生产系统而已,还包含建立新 生产系统前的维护预防设计(关注整个设备生命周期),这 些都是TPM活动的对象; 其次,要使设备损失为零,并且须建立防范损失于未然的管 理,并表现于生产系统中的“现场、现物”中,这是TPM的 一大特色。`
2020(TPM生产维护)TPM实战

(TPM生产维护)TPM实战(TPM生产维护)TPM实战第1讲我们离世界工厂有多远【本讲重点】引言他们为什么成功世界工厂的四大特点制造业保持竞争优势的方法前言有个著名的企业家曾经说过:“企业要点点滴滴地追求合理化,使管理最简单化。
”可是在实际管理中,一个简单的问题往往会变得很复杂,很多管理者都在困惑:究竟该如何强化管理呢?通过如下的案例,我们希望能总结出一些经验教训。
【案例】管理者的困惑:如何强化管理?某企业有个开放式的大办公室,里面有300多人办公。
但这个办公室经常出现这样的问题:早上上班的时候发现灯和空调在昨晚没有关掉。
公司高层知道这件事后,要求行政部出台措施、强化管理,尽快解决这个问题。
为此,行政部采取了一些措施。
例如,在门上贴上一个告示“人走灯灭”;有人提出制定标准,要求保安加强巡视,每天下班时检查是否关灯;仍有人提出采用点检表,要求员工轮流值班,发现问题、解决问题;最后,仍有人提出对最后离开办公室而未关灯的人给予罚款等。
最后的结果如何呢?一段时间过去后,结果且不理想。
这时候,公司高层开始抱怨行政部门管理不力、员工素养低下。
事实上,这种抱怨既不客观,更不能解决问题。
此时,管理者应该自问:是不是真的有这样严重的问题?在实际管理过程中,有一些企业表现得很优秀,它们通常有俩类比较好的方法:第一类是宾馆的做法。
宾馆如何解决这类问题呢?在宾馆住宿过的人都会发现,宾馆将钥匙和开关变成联动的形式:打开房门,将钥匙卡插进开关后就会接通房间电源;而离开房间时,必须取出钥匙卡,此时电源自动关闭。
这样,很好地解决了人员离开时电器有效关闭的问题。
为什么酒店能做到而工厂反而做不到?原因在于酒店遵循一个前提,即考虑到客人不会重视能源的消耗,但他重视房间的安全,重视钥匙卡。
因此,酒店设置了联动的开关,客人在离开房间时必定会带走钥匙,带走钥匙的同时灯就被关掉了。
这样做是基于一个考虑,酒店的客人且不愿意听酒店关于节约能源的呼吁,因而需要创造一种机制让他们不知不觉地遵守。