PFMEA_著名手机工厂完全案例
PFMEA分析案例

型號 :審核者﹕批准者﹕表格編號﹕項目 :23/APR/2001日期﹕日期﹕版本﹕主要參加人員:采取的措施嚴重度發生度難檢度RPN2.來料檢查2.1 線路板(PCB)不良:線路短路;線路斷路;尺寸不符合要求;爛板(損傷);扭曲變形;混板;上錫PAD有綠油或污漬或氧化;絲印脫落;綠油脫落;無功能測試記號;線路欠損;線路刮花;線路間有銅箔渣;無V-CUT;V-CUT深或V-CUT淺;插件孔孔塞或嚴重披峰;補線路浮起或松動;報廢板未分開包裝;文字印刷嚴重移位;外標識與BOM要求不符.產生外觀不良或性能不良8供應商的4M1E管理不完善:a.人員培訓考核不完善或沒作人員變更管理;b.原材料不良或沒作物料變更管理;c.機器設備(包括儀器)保養維護不完善或沒作機器設備(包括儀器)變更管理;d.不按操作程序作業或操作程序不完善或沒作方法變更管理;e.溫濕度及5S管理不完善.3根據檢查指引抽查,發現有問題時通知供應商改善.5120通知供應商改善或要求供應商提供PFMEA分析.王剛山/2001/08/20通知供應商改善或要求供應商提供PFMEA分析.543602.2 貼片電容(CCAP)不良:電極氧化或發黑;損傷;混料;外標識與BOM要求不符;尺寸不符合要求;容值超差;電容漏電.產生外觀不良或性能不良8供應商的4M1E管理不完善:a.人員培訓考核不完善或沒作人員變更管理;b.原材料不良或沒作物料變更管理;c.機器設備(包括儀器)保養維護不完善或沒作機器設備(包括儀器)變更管理;d.不按操作程序作業或操作程序不完善或沒作方法變更管理;e.溫濕度及5S管理不完善.3根據檢查指引抽查,發現有問題時通知供應商改善.5120通知供應商改善或要求供應商提供PFMEA分析.王剛山/2001/08/20通知供應商改善或要求供應商提供PFMEA分析.543602.3 貼片電阻(CRES)不良:電極氧化或發黑;損傷;混料;外標識與BOM要求不符;尺寸不符合要求;阻值超差.產生外觀不良或性能不良8供應商的4M管理不完善:a.人員培訓考核不完善或沒作人員變更管理;b.原材料不良或沒作物料變更管理;c.機器設備(包括儀器)保養維護不完善或沒作機器設備(包括儀器)變更管理;d.不按操作程序作業或操作程序不完善或沒作方法變更管理;3根據檢查指引抽查,發現有問題時通知供應商改善.5120通知供應商改善或要求供應商提供PFMEA分析.王剛山/2001/08/20通知供應商改善或要求供應商提供PFMEA分析.543602.4 色碼電阻(LRES)不良:引腳氧化或變形或發黑;損傷;混料;絲印模糊;外標識與BOM要求不符;色環與阻值不符;阻值超差;功率與要求不符.產生外觀不良或性能不良8供應商的4M管理不完善:a.人員培訓考核不完善或沒作人員變更管理;b.原材料不良或沒作物料變更管理;c.機器設備(包括儀器)保養維護不完善或沒作機器設備(包括儀器)變更管理;d.不按操作程序作業或操作程序不完善或沒作方法變更管理;3根據檢查指引抽查,發現有問題時通知供應商改善.5120通知供應商改善或要求供應商提供PFMEA分析.王剛山/2001/08/20通知供應商改善或要求供應商提供PFMEA分析.54360發生度(O)現行的控制方法難檢度(D)RPN建議的措施責任人及完成時間第一頁共四頁措施結果工序名稱潛在的失效模式潛在的失效后果嚴重度(S)級別潛在的失效原因過程潛在的失效模式及后果分析(PFMEA)准備者﹕SMD-FM-B003PWB組裝日期﹕02.5插腳二極管(DIODE)不良:引腳氧化或變形或發黑;損傷;混料;絲印模糊;極性標識錯誤;實物絲印內容與BOM要求不符.外標識與BOM要求不符;尺寸不符合要求;電氣性能不良.產生外觀不良或性能不良8供應商的4M管理不完善:a.人員培訓考核不完善或沒作人員變更管理;b.或原材料不良或沒作物料變更管理;c.或機器設備(包括儀器)保養維護不完善或沒作機器設備(包括儀器)變更管理;d.或不按操作程序作業或操作程序不完善或沒作方法變更管理;3根據檢查指引抽查,發現有問題時通知供應商改善.5120通知供應商改善或要求供應商提供PFMEA分析.王剛山/2001/08/20通知供應商改善或要求供應商提供PFMEA分析.543602.6插腳三極管(TRAN)不良:引腳氧化或變形或發黑;損傷;混料;絲印模糊.實物絲印內容與BOM要求不符;外標識與BOM要求不符;尺寸不符合要求;極性錯誤;電氣性能不良.產生外觀不良或性能不良8供應商的4M管理不完善:a.人員培訓考核不完善或沒作人員變更管理;b.原材料不良或沒作物料變更管理;c.機器設備(包括儀器)保養維護不完善或沒作機器設備(包括儀器)變更管理;d.不按操作程序作業或操作程序不完善或沒作方法變更管理;3根據檢查指引抽查,發現有問題時通知供應商改善.5120通知供應商改善或要求供應商提供PFMEA分析.王剛山/2001/08/20通知供應商改善或要求供應商提供PFMEA分析.543602.7貼片三極管(TRAN)不良:電極氧化或變形或發黑;混料;損傷;絲印模糊;實物絲印內容與BOM要求不符;外標識與BOM要求不符;電氣性能不良.產生外觀不良或性能不良8供應商的4M管理不完善:a.人員培訓考核不完善或沒作人員變更管理;b.或原材料不良或沒作物料變更管理;c.或機器設備(包括儀器)保養維護不完善或沒作機器設備(包括儀器)變更管理;d.或不按操作程序作業或操作程序不完善或沒作方法變更管理;3根據檢查指引抽查,發現有問題時通知供應商改善.5120通知供應商改善或要求供應商提供PFMEA分析.王剛山/2001/08/20通知供應商改善或要求供應商提供PFMEA分析.543602.8直插式IC不良:引腳氧化或變形或發黑;封裝形式不符要求;損傷;混料;絲印模糊;絲印內容與BOM要求不符;外標識與BOM要求不符;尺寸不符合要求;電氣性能不良.產生外觀不良或性能不良8供應商的4M管理不完善:a.人員培訓考核不完善或沒作人員變更管理;b.或原材料不良或沒作物料變更管理;c.或機器設備(包括儀器)保養維護不完善或沒作機器設備(包括儀器)變更管理;d.或不按操作程序作業或操作程序不完善或沒作方法變更管理;3根據檢查指引抽查,發現有問題時通知供應商改善.5120通知供應商改善或要求供應商提供PFMEA分析.王剛山/2001/08/20通知供應商改善或要求供應商提供PFMEA分析.543602.9貼片式IC不良:引腳氧化或變形或發黑;封裝形式不符要求;損傷;混料;絲印模糊;實物絲印內容與BOM要求不符;外標識與BOM要求不符;尺寸不符合要求;電氣性能不良.產生外觀不良或性能不良8供應商的4M管理不完善:a.人員培訓考核不完善或沒作人員變更管理;b.或原材料不良或沒作物料變更管理;c.或機器設備(包括儀器)保養維護不完善或沒作機器設備(包括儀器)變更管理;d.或不按操作程序作業或操作程序不完善或沒作方法變更管理;3根據檢查指引抽查,發現有問題時通知供應商改善.5120通知供應商改善或要求供應商提供PFMEA分析.王剛山/2001/08/20通知供應商改善或要求供應商提供PFMEA分析.543602.10瓷片電容(LCAP)不良:引腳氧化或變形或發黑;損傷;混料;絲印模糊;絲印內容與容值不符;外標識與BOM要求不符;尺寸不符合要求;容值超差;耐壓值不符要求;電容漏電.產生外觀不良或性能不良8供應商的4M1E管理不完善:a.人員培訓考核不完善或沒作人員變更管理;b.原材料不良或沒作物料變更管理;c.機器設備(包括儀器)保養維護不完善或沒作機器設備(包括儀器)變更管理;d.不按操作程序作業或操作程序不完善或沒作方法變更管理;e.溫濕度及5S管理不完善.3根據檢查指引抽查,發現有問題時通知供應商改善.5120通知供應商改善或要求供應商提供PFMEA分析.王剛山/2001/08/20通知供應商改善或要求供應商提供PFMEA分析.543602.11排阻(NRES)不良:引腳氧化或發黑;損傷;混料;封裝形式不符要求;外標識與BOM要求不符;尺寸不符合要求;排阻的網絡阻值超差.產生外觀不良或性能不良8供應商的4M1E管理不完善:a.人員培訓考核不完善或沒作人員變更管理;b.原材料不良或沒作物料變更管理;c.機器設備(包括儀器)保養維護不完善或沒作機器設備(包括儀器)變更管理;d.不按操作程序作業或操作程序不完善或沒作方法變更管理;e.溫濕度及5S管理不完善.3根據檢查指引抽查,發現有問題時通知供應商改善.5120通知供應商改善或要求供應商提供PFMEA分析.王剛山/2001/08/20通知供應商改善或要求供應商提供PFMEA分析.543602.12晶振(RESONATOR)不良:引腳氧化或變形或發黑;損傷;混料;絲印模糊;外標識與BOM要求不符;實物絲印內容與BOM要求不符;尺寸不符合要求;電氣性能不良.產生外觀不良或性能不良8供應商的4M1E管理不完善:a.人員培訓考核不完善或沒作人員變更管理;b.原材料不良或沒作物料變更管理;c.機器設備(包括儀器)保養維護不完善或沒作機器設備(包括儀器)變更管理;d.不按操作程序作業或操作程序不完善或沒作方法變更管理;e.溫濕度及5S管理不完善.3根據檢查指引抽查,發現有問題時通知供應商改善.5120通知供應商改善或要求供應商提供PFMEA分析.王剛山/2001/08/20通知供應商改善或要求供應商提供PFMEA分析.543602.13貼片二極管(DIODE)不良:焊腳氧化或發黑;損傷;混料;實物絲印內容與BOM要求不符;外標識與BOM要求不符;尺寸不符合要求;極性標識錯誤;電氣性能不良.產生外觀不良或性能不良8供應商的4M1E管理不完善:a.人員培訓考核不完善或沒作人員變更管理;b.原材料不良或沒作物料變更管理;c.機器設備(包括儀器)保養維護不完善或沒作機器設備(包括儀器)變更管理;d.不按操作程序作業或操作程序不完善或沒作方法變更管理;e.溫濕度及5S管理不完善.3根據檢查指引抽查,發現有問題時通知供應商改善.5120通知供應商改善或要求供應商提供PFMEA分析.王剛山/2001/08/20通知供應商改善或要求供應商提供PFMEA分析.543602.14插座/排插(SOCKET)不良:引腳氧化或發黑;損傷;混料;實物絲印內容與BOM要求不符;外標識與BOM要求不符;尺寸不符合要求;針腳氧化或變形或針腳高或針腳低或少針或多針;電氣性能不良.產生外觀不良或性能不良8供應商的4M1E管理不完善:a.人員培訓考核不完善或沒作人員變更管理;b.原材料不良或沒作物料變更管理;c.機器設備(包括儀器)保養維護不完善或沒作機器設備(包括儀器)變更管理;d.不按操作程序作業或操作程序不完善或沒作方法變更管理;e.溫濕度及5S管理不完善.3根據檢查指引抽查,發現有問題時通知供應商改善.5120通知供應商改善或要求供應商提供PFMEA分析.王剛山/2001/08/20通知供應商改善或要求供應商提供PFMEA分析.543602.15貼片電解電容(SMD ECAP)不良:電極氧化或發黑;損傷(壓痕);混料;編帶反向.絲印模糊;實物絲印內容與BOM要求不符;外標識與BOM要求不符;尺寸不符合要求;容值超差;電容漏電.產生外觀不良或性能不良8供應商的4M1E管理不完善:a.人員培訓考核不完善或沒作人員變更管理;b.原材料不良或沒作物料變更管理;c.機器設備(包括儀器)保養維護不完善或沒作機器設備(包括儀器)變更管理;d.不按操作程序作業或操作程序不完善或沒作方法變更管理;e.溫濕度及5S管理不完善.3根據檢查指引抽查,發現有問題時通知供應商改善.5120通知供應商改善或要求供應商提供PFMEA分析.王剛山/2001/08/20通知供應商改善或要求供應商提供PFMEA分析.543602.16直插式電解電容(ECAP)不良:引腳氧化或發黑;損傷(包括PVC套管破損、移位);極性電容正負極標識錯誤;防爆帽凸出;編帶反向.混料;絲印模糊;實物絲印內容與BOM 要求不符;外標識與BOM要求不符;尺寸不符合要求;電氣性能不符要求.產生外觀不良或性能不良8供應商的4M1E管理不完善:a.人員培訓考核不完善或沒作人員變更管理;b.原材料不良或沒作物料變更管理;c.機器設備(包括儀器)保養維護不完善或沒作機器設備(包括儀器)變更管理;d.不按操作程序作業或操作程序不完善或沒作方法變更管理;e.溫濕度及5S管理不完善.3根據檢查指引抽查,發現有問題時通知供應商改善.5120通知供應商改善或要求供應商提供PFMEA分析.王剛山/2001/08/20通知供應商改善或要求供應商提供PFMEA分析.543602.17線圈(COIL)不良:引腳氧化或變形或發黑;損傷;混料;外標識與BOM要求不符;尺寸不符合要求;電氣性能不良.產生外觀不良或性能不良8供應商的4M1E管理不完善:a.人員培訓考核不完善或沒作人員變更管理;b.原材料不良或沒作物料變更管理;c.機器設備(包括儀器)保養維護不完善或沒作機器設備(包括儀器)變更管理;d.不按操作程序作業或操作程序不完善或沒作方法變更管理;e.溫濕度及5S管理不完善.3根據檢查指引抽查,發現有問題時通知供應商改善.5120通知供應商改善或要求供應商提供PFMEA分析.王剛山/2001/08/20通知供應商改善或要求供應商提供PFMEA分析.543602.18開關(SWITCH)不良:焊腳氧化或變形或發黑;損傷;混料;外標識與BOM要求不符;尺寸不符合要求;機械性能不良;電氣性能不良.產生外觀不良或性能不良8供應商的4M1E管理不完善:a.人員培訓考核不完善或沒作人員變更管理;b.原材料不良或沒作物料變更管理;c.機器設備(包括儀器)保養維護不完善或沒作機器設備(包括儀器)變更管理;d.不按操作程序作業或操作程序不完善或沒作方法變更管理;e.溫濕度及5S管理不完善.3根據檢查指引抽查,發現有問題時通知供應商改善.5120通知供應商改善或要求供應商提供PFMEA分析.王剛山/2001/08/20通知供應商改善或要求供應商提供PFMEA分析.543602.19插腳火牛不良:插腳氧化或變形或發黑;損傷;混料;外標識與BOM要求不符;尺寸不符合要求;電氣性能不良.產生外觀不良或性能不良8供應商的4M1E管理不完善:a.人員培訓考核不完善或沒作人員變更管理;b.原材料不良或沒作物料變更管理;c.機器設備(包括儀器)保養維護不完善或沒作機器設備(包括儀器)變更管理;d.不按操作程序作業或操作程序不完善或沒作方法變更管理;e.溫濕度及5S管理不完善.3根據檢查指引抽查,發現有問題時通知供應商改善.5120通知供應商改善或要求供應商提供PFMEA分析.王剛山/2001/08/20通知供應商改善或要求供應商提供PFMEA分析.54360??序號號IPQC抽檢不適用,因為研究RPN值達不到24,屬低風險.??序號QA抽檢不適用,因為研究RPN值達不到24,屬低風險.2.20跳線(JUMPER WIRE)不良:焊腳氧化或變形或發黑;損傷;混料;外標識與BOM要求不符;尺寸不符合要求;性能不良.(特別注意:這項僅適用于BJH-3122)產生外觀不良或性能不良8供應商的4M1E管理不完善:a.人員培訓考核不完善或沒作人員變更管理;b.原材料不良或沒作物料變更管理;c.機器設備(包括儀器)保養維護不完善或沒作機器設備(包括儀器)變更管理;d.不按操作程序作業或操作程序不完善或沒作方法變更管理;e.溫濕度及5S管理不完善.3IQC根據檢查指引抽查,發現有問題時通知供應商改善.5120通知供應商改善或要求供應商提供PFMEA分析.王剛山/2001/08/20通知供應商改善或要求供應商提供PFMEA分析.54360備注:這份來料檢查的PFMEA僅供參考,如制作PFMEA時必須根據BOM的要求刪除或增加(目前應不需要增加)某些項目,如有問題,請聯絡品質一部---陳偉業(內線208).。
pfmea案例

pfmea案例PFMEA案例。
在制造业中,PFMEA(过程失效模式和影响分析)是一种非常重要的工具,用于识别和消除潜在的过程问题,以确保产品质量和生产效率。
下面我们将通过一个实际案例来说明PFMEA的应用和重要性。
某汽车零部件制造公司在生产过程中出现了一个严重的质量问题,在焊接过程中,焊接接头出现了裂纹,导致产品质量下降,甚至出现安全隐患。
为了解决这个问题,该公司决定进行PFMEA分析。
首先,团队收集了与焊接过程相关的所有信息,包括设备、材料、人员、环境等方面的数据。
然后,团队对焊接过程进行了全面的分析,识别了潜在的失效模式,如焊接接头裂纹、焊接温度过高、焊接压力不均等。
接着,团队对每种失效模式进行了评估,确定了其可能的影响,包括产品质量、生产效率、安全性等方面。
在分析的基础上,团队制定了针对每种失效模式的改进措施。
例如,针对焊接接头裂纹,团队提出了优化焊接参数、加强焊接工艺控制、提高焊接操作人员的技能水平等措施。
针对焊接温度过高,团队提出了优化冷却系统、加强温度监控、定期检查设备状态等措施。
在实施改进措施后,团队对焊接过程进行了再次评估,发现裂纹现象得到了显著改善,产品质量得到了提升,生产效率也得到了提高。
通过PFMEA分析,该公司成功解决了焊接过程中的质量问题,为产品质量和生产效率提供了保障。
通过这个案例,我们可以看到PFMEA在制造业中的重要作用。
它不仅可以帮助企业识别和消除潜在的过程问题,还可以指导企业制定有效的改进措施,提高产品质量和生产效率。
因此,我们在生产过程中应该重视PFMEA的应用,不断完善和优化自己的生产过程,确保产品质量和客户满意度。
总而言之,PFMEA是一个非常有价值的工具,它可以帮助企业提前发现潜在的问题,并通过科学的方法进行改进,从而确保产品质量和生产效率。
希望更多的企业能够重视PFMEA的应用,不断提升自身的竞争力。
FMEA-PFMEA案例3 精品

42
技质部
20XX.07.25
技质部郑宝生组织阶段评审
7
2
1
14
磁极线圈
ST110H-130
ST110H-140
ST110H-150
ST110H-160
产生定子的励磁磁场
磁场强度不足
起动机输出力矩小
7
扁铜线的材料选用不正确造成线圈内阻过大。
2
根据同类产品进行一次比较确定选材
2
28
20XX
7.10
采供部考察市场提出方案郑宝生负责确定小组评审
7
间隙选用不正确,对机壳内径、磁极厚度和电枢外径组成的尺寸链计算和选用公差不当
2
根据同类产品正确选用合理的间隙并对合理安排各部件的公差和重新计算尺寸链进行校核。
2
28
20XX
07,25
项目小组进行设计评审
7
2
1
14
转子旋转不畅
起动时噪声增大甚至造成转子卡壳
7
由于轴和三个支承点产的不同心造成
3
增加外壳两端企口的同心度形位公差
7
2
1
14
7
绕制圈数不正确
2
理论计算值需经过试验验证
2
28
产品试验时测试
项目小组做设计确认
7
2
1
14
绝缘纸
ST110H.132
磁极线圈的匝绝缘
磁极线圈匝间击穿短路
起动机损坏
8
匝间衬垫的绝缘材料选用不正确造成线圈局部匝间短路最后烧毁。
2
根据同类产品确定绝缘材料并进行耐压试验验证
1
16
磁极
ST110H-104
和换向片和换向器夹片组成换向器传递电力并起换向作用
PFMEA案例
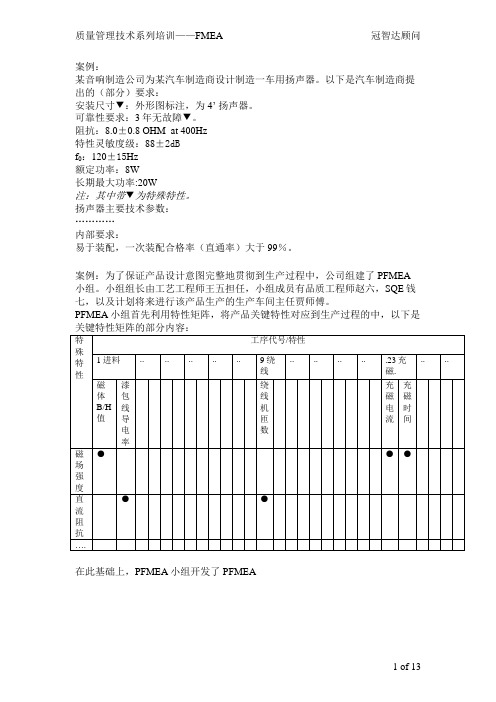
50个 每1000件
9
高:经常性失效
20个 每1000件
8
10个 每1000件
7
中等:偶然性失效
5个 每1000件
6
2个 每1000件
5
1个 每1000件
4
低:相对很少发生失效
0.5个 每1000件
3
0.1个 每1000件
2
级低:失效不太可能发生
≤0.01个 每1000件
1
推荐的PFMEA探测度评价准则
附录1:美国三大汽车评价严重度,频度数,探测度的准则
推荐的PFMEA严重度评价准则
后果
评定准则:后果的严重度
当潜在失效模式导致最终顾客和/或一个制造/装配厂产生缺陷时便得出相应的定级结果。最终顾客永远是要首先考虑的。如果两种可能都存在的,采用两个严重度值中的较高者。(顾客的后果)
评定准则:后果的严重度
扬声器主要技术参数:
…………
内部要求:
易于装配,一次装配合格率(直通率)大于99%。
案例:为了保证产品设计意图完整地贯彻到生产过程中,公司组建了PFMEA小组。小组组长由工艺工程师王五担任,小组成员有品质工程师赵六,SQE钱七,以及计划将来进行该产品生产的生产车间主任贾师傅。
PFMEA小组首先利用特性矩阵,将产品关键特性对应到生产过程的中,以下是关键特性矩阵的部分内容:
一个潜在的关键特性(启动PFMEA)
严重度=9,10
PFMEA小组关注
设计
YS
一个潜在的重要特性(启动PFMEA)
严重度=5~8,且频度数=4~10
PFMEA小组关注
设计
不是特殊特性
严重度=1~4
无
过程
pfmea标准案例
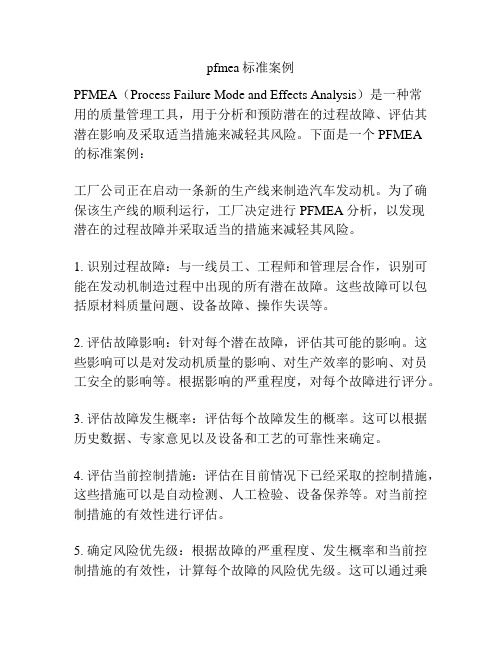
pfmea标准案例PFMEA(Process Failure Mode and Effects Analysis)是一种常用的质量管理工具,用于分析和预防潜在的过程故障、评估其潜在影响及采取适当措施来减轻其风险。
下面是一个PFMEA的标准案例:工厂公司正在启动一条新的生产线来制造汽车发动机。
为了确保该生产线的顺利运行,工厂决定进行PFMEA分析,以发现潜在的过程故障并采取适当的措施来减轻其风险。
1. 识别过程故障:与一线员工、工程师和管理层合作,识别可能在发动机制造过程中出现的所有潜在故障。
这些故障可以包括原材料质量问题、设备故障、操作失误等。
2. 评估故障影响:针对每个潜在故障,评估其可能的影响。
这些影响可以是对发动机质量的影响、对生产效率的影响、对员工安全的影响等。
根据影响的严重程度,对每个故障进行评分。
3. 评估故障发生概率:评估每个故障发生的概率。
这可以根据历史数据、专家意见以及设备和工艺的可靠性来确定。
4. 评估当前控制措施:评估在目前情况下已经采取的控制措施,这些措施可以是自动检测、人工检验、设备保养等。
对当前控制措施的有效性进行评估。
5. 确定风险优先级:根据故障的严重程度、发生概率和当前控制措施的有效性,计算每个故障的风险优先级。
这可以通过乘以这三个因素得到一个风险优先级数值。
6. 制定预防和纠正措施:根据风险优先级数值的高低,确定改进措施的紧急性。
高风险的故障可能需要立即采取纠正措施,而较低风险的故障可以在以后的时间里解决。
7. 实施措施:对确定的措施进行实施,并跟踪它们的有效性。
确保改进措施的有效性并记录结果。
通过这个PFMEA案例,工厂公司可以识别并降低生产线制造发动机过程中的潜在风险,提高发动机质量和生产效率,从而满足客户需求并实现更好的质量管理。
PFMEA失效模式分析案例

PFMEA失效模式分析案例标题:PFMEA失效模式分析案例研究PFMEA(Process Flure Modes and Effects Analysis)是一种用于识别、评估和防止潜在生产过程中可能出现的失效模式的工具。
本文将通过一个具体的案例来展示PFMEA的应用。
假设我们正在生产一款高端智能手机。
在生产过程中,我们发现产品的屏幕质量不稳定,经常出现亮点、坏点和其它显示问题。
为了解决这个问题,我们决定采用PFMEA进行失效模式分析。
首先,我们成立了一个由生产、质量、工程和技术人员组成的团队,对生产过程进行详细的分析。
我们发现,问题主要出现在液晶屏的贴合过程中,而这个过程又涉及到多个子过程,如屏幕切割、屏幕清洗、光学贴合等。
接下来,我们对每个子过程进行详细的失效模式分析。
我们发现,屏幕切割过程中可能会由于切割刀的磨损导致屏幕出现坏点;屏幕清洗过程中可能会由于清洗液的污染导致亮点;光学贴合过程中可能会由于压力不均导致坏点。
针对这些潜在的失效模式,我们提出了相应的风险评估和预防措施。
例如,对于屏幕切割过程中的切割刀磨损,我们可以采用更耐磨的切割刀,并定期进行检查和更换;对于屏幕清洗过程中的清洗液污染,我们可以定期更换清洗液,并定期检查清洗液的浓度;对于光学贴合过程中的压力不均,我们可以采用更先进的贴合设备,并定期进行维护和校准。
通过这些措施的实施,我们可以大大降低智能手机屏幕出现质量问题的风险。
我们还可以对生产过程中的其他潜在失效模式进行分析和预防,从而全面提升产品的质量和生产效率。
总结,PFMEA是一种有效的质量工具,可以帮助我们识别和预防生产过程中的潜在失效模式。
通过案例分析,我们可以看到,PFMEA不仅可以解决具体的问题,还可以帮助我们发现并解决更深层次的问题,从而实现持续改进和提升。
新版(七步法案例)PFMEA

头下R角偏小 一冲设计不合理 模具制作有偏差 冷墩时光钉直径偏大
5
增加抽风机或空调
2 检查/核对 2
6
要求供应商对模具尺寸进行 中限管理并提供出货检验报
告
3
目视/ 核对/检测
2
6
每隔两个小时对锁紧螺丝紧 固一次
3
检查
2
8
修理模具R角位置
3 检测 2
8
修改一冲相关尺寸
3 检测 2
6
要求供应商对模具尺寸进行 中限管理并提供出货检验报
05 热处理
硬度检测 (维式硬度计)
产品外观及硬度性能符合图纸 目视检测产品外观及仪器检测产品硬度性
要求
能符合图纸要求
电镀后表面发黑
产品从清洗区清除杂质后进入淬火炉进行
渗碳淬火(预热区860℃-60/+20℃,保温
产品表面硬度与芯部硬度需符 区900℃ ±10℃,淬火区 860℃ ±10
合图纸工艺要求:
完成状态
结合经验重新设计一冲模具
2020/3/10 8 2 1 ※ L
完成状态
严格要求模具厂商按我司图纸尺寸制作 2020/3/10 6 2 1
L
我司模具按图纸中限尺寸设计,并要求模具厂 完成状态 商对每批模具进行尺寸检验并提供检验报告到 2020/3/10 7 2 1 ※ L
我司核对
完成状态
要求牙板供应商严格按标准要求设计牙板并提 供检测数据报告
提供检测报告
对
高成
2020/3/10
要求牙板供应商严格按标准要求设计牙板
目视/核 对
董茂文
2020/3/10
将主模模腔尺寸定义在中限并要求供应商 目视/核
pfmea的案例

pfmea的案例哎哟喂,各位看官,今天咱们来摆一摆PFMEA(过程失效模式与影响分析)的案例。
咱们四川人说话直来直去,陕西朋友说话豪爽,再加上北京大哥的实在,咱们一起来把这个案例给讲明白了。
先说咱四川这边的例子。
咱们四川有个做电子产品的厂家,那厂里的生产线可是热火朝天。
有天,他们发现产品中的某个小零件老是出问题,导致整批产品都得返工。
这一下,工人们忙得团团转,老板也急得像热锅上的蚂蚁。
后来,他们用了PFMEA,把每个生产环节都仔细分析了一遍,最后发现是那个零件的供应商出了问题。
换了供应商之后,问题就迎刃而解了。
你看,这就是PFMEA的妙处,能帮我们找到问题的根源。
再说说陕西的例子。
咱们陕西的兄弟做事可是讲究个实在。
有个做机械加工的厂家,他们发现机器在加工过程中经常出现误差,导致产品质量不稳定。
他们用了PFMEA,从人、机、料、法、环、测六个方面进行分析,最后发现是操作工人的技能不够熟练。
于是,他们加强了对工人的培训,问题也就迎刃而解了。
你看,PFMEA不仅能找到问题,还能帮我们找到解决问题的方法。
最后说说北京的例子。
咱们北京的大哥做事可是有条不紊。
有个做食品的厂家,他们发现产品在储存过程中容易变质。
于是,他们用了PFMEA,对每个可能导致变质的因素都进行了详细的分析。
最后,他们发现是储存环境的温度控制不够精确。
于是,他们改进了温度控制系统,问题也就解决了。
你看,PFMEA就像是个指南针,能帮我们找到前进的方向。
这三个例子,虽然地方不同,但都用到了PFMEA这个方法。
它就像是个万金油,哪里有问题就往哪里抹一抹,问题就迎刃而解了。
所以呀,咱们在工作中,也得学会用这种方法,才能事半功倍,把工作做得更好。
TC002-PFMEA案例02

27
培训2.拉长 加强监督力
度
冯立猛 2014.3.1
6
1.加强作业员 的自检意识 2.加强监管力 度
3
2
2 12
焊接USB线到电 路板
USB线极性焊 接正确,无 假焊、破皮
方向焊接 错,假焊/ 线材破皮
产品功能不 良
4
1.未按SOP作 业。2.粗心
大意
3
1.巡检/抽检 2.依SOP作业
3
1.加强岗位
3
2
2 12
超声
缝隙均匀无 溢胶断差
产品外观不 良,内部线 材短路,五 金轴卡死
产品外观不 良/影响功能
不良
4
1.未按SOP作 业。2.粗心
大意
3
1.巡检/抽检 2.依SOP作业
3
1.加强岗位
36
培训2.拉长 加强监督力
度
冯立猛 2014.3.1
6
1.加强作业员 的自检意识 2.加强监管力 度
3
3
1.某些功能 没法测试
2.良品与不 良品混淆
导致流到客 户端的成品
无法使用
1.测试员的 专业知识不 6够 2.参数制订 有异议
1.测试工位
3
必须持上岗 证2.依SOP作
3
业
1.加强岗位
54
培训3.制订 标准化、规
范化文件
冯立猛 2014.3.1
6
1.进行上岗培 训 2.必须依照SOP 作业
6
2
2 24
失效模式及效应分析表
段次/工位
FMEA编号:
DFMEA□ PFMEA■
产品类别型号:TC002
责任部门:工程部
PFMEA案例(全套表格)
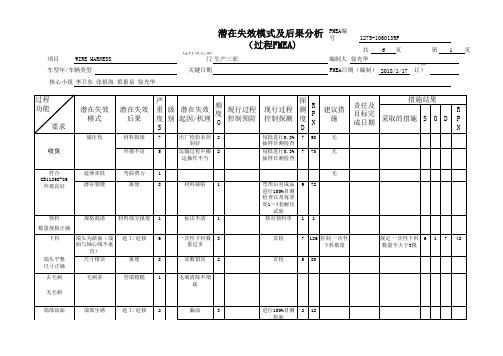
责任及 目标共完 成日期
措施结果 采6 取页的措施 S 第O
R D3 P 页
N
产品应在试验要 求的条件下工作
正常
包装
端部生锈
外观不良 3
管材缺陷 1 包装袋破损 2
抽检
10 80
目测
8 48
为保护产品及数 量清点防止失效 对成品进行封头
及捆绑
0
0
00
0
0
00
评分
等级
Cp或者Cpk值
等
级
(
顾
客
评分
是 用
级 别
潜在失效 起因/机理
频 度 O
现行过程 控制预防
现行过程 控制探测
探 测 度 D
R P N
建议措 施
责任及 目标共完 成日期
措施结果 采6 取页的措施 S 第O
R D6 P 页
N
1 似乎不会发生 1.67≤Cpk
非
常
低
(
被
识
别
力
1
强 的
顾
客
指
摘
的
程
度
)
1-2
自工序可以 检出
③ 发生频率>3&检出难易度>5
项目
WIRE HARNESS
车型年/车辆类型
核心小组 李卫东 张祖海 黄惠泉 徐光华
潜在失效模式及后果分析 FMEA编 号 (过程FMEA) 过程责任部
1275-1060139F 共 6页
第1页
门 生产三部
编制人 徐光华
(修
关键日期
FMEA日期(编制) 2018/1/17 订)
过程 功能
要求
收货
潜在失效 模式
最新过程PFMEA完整实例严格按工具书

3
材料标识不明确 Un-clear label
2
生产领料时,操作工和QC对 材料进行确认 Operators and QC verify the material in production line.
8
48
无 N.A
60
P200T 冲压 P200T Stamping
4
QC复查在库 re-check the parts in period.
8
64
N.A
50
移至生产线 Move Material to Production Line
材料转移错误 mistake the rawmaterial
影响后续零件生产 affect parts production next process
48
无 N.A
30
移至原材料仓 材料转移错误 Move Material mistake the to Store rawmaterial
影响后续零件生产 affect parts production next process
3
材料标识不明确 Un-clear label
入库前材料上贴来料管 理票 set the label on the Raw-material before store.
10
原材料进厂 原材料规格错误 影响零件性能 In-coming Raw Material spec is wrong affect parts' capability Material
供应商每批货附上出货 清单 The supplier attached the shipping list to each shipment
工程部 AND EFFECTS ANALYSIS
aiag vda pfmea例子
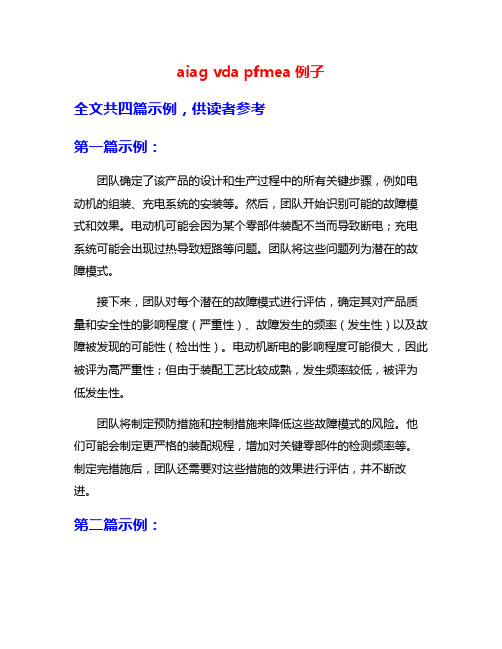
aiag vda pfmea例子全文共四篇示例,供读者参考第一篇示例:团队确定了该产品的设计和生产过程中的所有关键步骤,例如电动机的组装、充电系统的安装等。
然后,团队开始识别可能的故障模式和效果。
电动机可能会因为某个零部件装配不当而导致断电;充电系统可能会出现过热导致短路等问题。
团队将这些问题列为潜在的故障模式。
接下来,团队对每个潜在的故障模式进行评估,确定其对产品质量和安全性的影响程度(严重性)、故障发生的频率(发生性)以及故障被发现的可能性(检出性)。
电动机断电的影响程度可能很大,因此被评为高严重性;但由于装配工艺比较成熟,发生频率较低,被评为低发生性。
团队将制定预防措施和控制措施来降低这些故障模式的风险。
他们可能会制定更严格的装配规程,增加对关键零部件的检测频率等。
制定完措施后,团队还需要对这些措施的效果进行评估,并不断改进。
第二篇示例:AIAG VDA PFMEA是指根据国际汽车行业标准组织(AIAG)和德国汽车工程师协会(VDA)共同制定的一种过程失效模式及影响分析方法。
这种方法是为了帮助汽车行业的供应链伙伴在产品设计和生产过程中识别和解决潜在的故障模式,从而提高产品质量和可靠性。
在本文中,我们将以实际案例为例,介绍AIAG VDA PFMEA的具体应用及其重要性。
故障模式及影响分析(FMEA)是一种常见的质量管理工具,其目的是通过系统性地识别和排除产品和过程中的潜在故障模式,以确保产品的质量和可靠性。
在汽车行业,产品设计和生产过程中存在着各种各样的潜在故障模式,如设计错误、工艺不当、零部件失效等,这些故障模式可能会导致产品的功能失效、安全性降低,甚至对用户造成伤害。
AIAG VDA PFMEA是结合了AIAG和VDA两个国际汽车行业标准组织的最佳实践而制定的一种FMEA方法。
它强调了全面性和系统性,要求参与方从产品设计、制造、测试、维修等全过程来考虑潜在故障模式,并评估其可能的影响程度和频率。
PFMEA案例
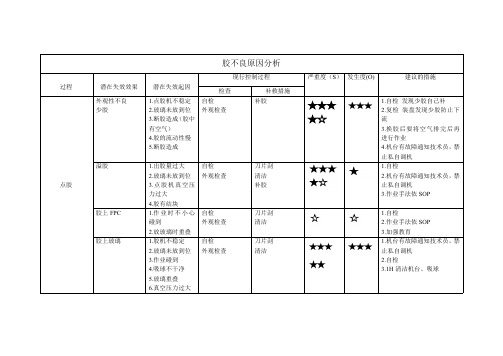
作业手法不对碰 自检
到胶
外观检查
刀片刮 清洁
棉签挑
刀片刮 清洁
1.自检 2.吸球吸玻璃的中间位置 3.1H 清洁吸球
1.现场 5S、成品盘装玻璃前 抖一抖 2.作业自检 1.自检 2.胶未干,禁止贴易撕贴 3.作业手法严格按照 SOP
1.自检 2.作业手法依 SOP 3.加强教育 1.机台有故障通知技术员,禁 止私自调机 2.自检 3.1H 清洁机台、吸球
胶上玻璃
装盘
胶异物
贴 易 撕 贴 / 电 测 / 胶上玻璃 外观
1.作业碰到 2.玻璃重叠 3.吸球不干净 4.胶未干,玻璃倾 斜 成品盘上异物掉 落
自检 外观检查
自检 外观检查
胶不良原因分析
过程 点胶
潜在失效效果
外观性不良 少胶
潜在失效起因
1.点胶机不稳定 2.玻璃未放到位 3.断胶造成(胶中 有空气) 4.胶的流动性慢 5.断胶造成
现行控制过程
检查 自检 外观检查
补救措施 补胶
溢胶
胶上 FPC 胶上玻璃
1.出胶量过大 2.玻璃未放到位 3. 点 胶 机 真 空 压 力过大 4.胶有结块 1.作 业 时 不 小 心 碰到 2.放玻璃时重叠 1.胶机不稳定 2.玻璃未放到位 3.作业碰到 4.吸球不干净 5.玻璃重叠 6.真空压力过大
自检 外观检查
自检 外观检查 自检 外观检查
刀片刮 清洁 补胶
刀Байду номын сангаас刮 清洁
刀片刮 清洁
严重度(S) 发生度(O)
建议的措施
1.自检 发现少胶自己补 2.复检 装盘发现少胶防止下 流 3.换 胶 后 要 将 空 气 排 完 后 再 进行作业 4.机台有故障通知技术员,禁 止私自调机 1.自检 2.机台有故障通知技术员,禁 止私自调机 3.作业手法依 SOP
第五版过程PFMEA标准实例
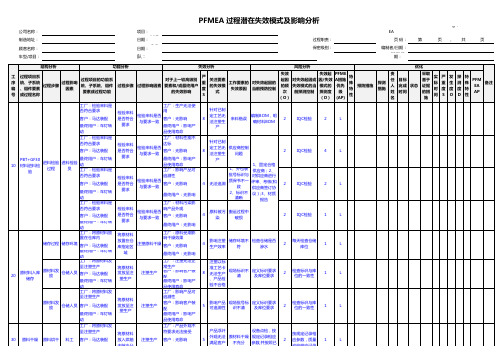
项PF目M:EA开始 日PF期M:EA修订 日跨期职:能团 队:
PFMEA 过程潜在失效模式及影响分析
过程职责: 保密级别:
PM EA
页 码:
第
编制者批/准日/期日: 期:
版本 号:
页, 共
页
结构分析
功能分析
失效分析
风险分析
优化
工 过程项目系
失效
失效起 PFME
最终用户:无影响
4
原料被污 搬运过程中
染
破损
2
IQC检验
1
L
工厂:将原材料放 将原材料
工厂:原料受潮影
置在仓库内 储存过程 储存环境 客户:马达装配
放置在仓 库指定区
响干燥效果 注塑原料干燥 客户:无影响
4
影响注塑 储存环境不 检查仓储是否
生产效率
符
渗水
2
每天检查仓储 库位
1
L
最终用户:车灯转
域
动
最终用户:无影响
检验来料 是否符合
要求
达标 检验来料是否 客户:无影响
与要求一致 最终用户:影响产
品使用寿命
工厂:影响产品可
针对已制
8
定工艺无 供应商控制 法注塑生 问题
产
1、固定合格 1、外包装 供应商;2、
2
IQC检验
4
L
否符合要求
客户:马达装配
最终用户:车灯转 动 工厂:检验来料是
检验来料 是否符合
要求
追溯性 检验来料是否
2
注塑机台
注塑生产
、模具、 注塑成型
客户:马达装配
工艺
FMEA经典案例91472
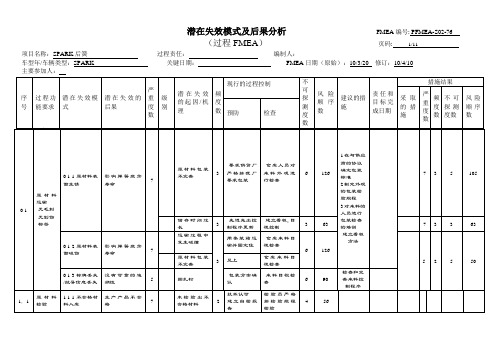
-质保部抽样检查
2
56
7
4
2
56
2-1 表面不能达到平滑要求
影响弹簧的疲劳寿命
6
HIC
卷簧机滚轮调整不正确
3
1.首件认可
1.操作工定期抽检一班1次/2h
2.质期抽检1次/4h
3
36
2-2. 总圈数不能达到要求
影响弹簧装配
6
HIC
-外径偏差
-送料长度偏差
4
1.设备卷绕方向保证
2.首件认可
30
分供方检验器具确定
5
2
3
30
1.2-1 不合格的丸粒
影响弹簧的疲劳寿命
5
供应商提供不合格的丸粒
2
供应商技术认可
对丸粒的来料检查
3
30
1.2-2磷化液不符合规
影响涂层质量
5
供应商提供不合格的磷化液
2
供应商技术认可
对磷化液进行来料检查
3
30
1.2-3涂装的粉末不符合规
影响涂层质量
5
供应商提供的粉末不符合规
-建立看板,目视控制
3
63
7
3
3
63
0.1-2原材料表面碰伤
影响弹簧疲劳寿命
7
运输过程中发生碰撞
3
用集装箱运输并固定住
-仓库来料目视检查
6
126
5
2
5
50
原材料包装不完善
见上
仓库来料目视检查
0.1-3标牌丢失/批号信息丢失
没有可靠的追溯性
5
捆扎松
-包装方案确认
-来料目视检查
6
pfmea案例

pfmea案例PFMEA案例。
PFMEA(Process Failure Mode and Effects Analysis)是一种用于识别和评估制造过程中潜在故障模式及其影响的方法。
它可以帮助企业在生产过程中提前识别潜在的问题,并采取相应的措施进行预防,从而提高产品质量和生产效率。
下面我们将通过一个实际的案例来介绍PFMEA的应用。
在某汽车零部件生产企业,他们使用PFMEA来分析生产线上的焊接工艺。
首先,团队收集了关于焊接工艺的所有相关信息,包括焊接设备、焊接材料、操作流程等。
然后,团队针对每个潜在的故障模式进行分析,包括焊接接头断裂、焊接温度过高、焊接时间过长等。
接着,团队对每种故障模式的可能影响进行评估,比如焊接接头断裂可能导致产品失效,焊接温度过高可能导致材料变形等。
最后,团队制定了针对每种故障模式的预防措施,比如加强对焊接工艺的监控,优化焊接参数,加强员工培训等。
通过PFMEA的分析,该企业发现了一些潜在的问题,并及时采取了相应的措施进行预防,从而避免了可能导致产品质量问题的故障发生。
这不仅提高了产品质量,也降低了生产成本,提高了生产效率。
通过以上案例可以看出,PFMEA作为一种有效的质量管理工具,在生产过程中发挥着重要作用。
它可以帮助企业在生产过程中及时发现潜在的问题,并采取预防措施,从而提高产品质量,降低生产成本,提高生产效率。
因此,建议更多的企业在生产过程中引入PFMEA方法,以提升竞争力,满足市场需求。
综上所述,PFMEA在制造业中具有重要意义,通过对潜在故障模式和影响进行分析和评估,有助于企业提前预防问题的发生,提高产品质量和生产效率。
希望更多的企业能够重视PFMEA的应用,从而在激烈的市场竞争中脱颖而出。
pfmea案例

pfmea案例PFMEA案例。
PFMEA(Process Failure Mode and Effects Analysis)是一种系统性的分析方法,用于识别和评估制程中的潜在故障模式及其影响。
通过对潜在故障模式的分析,可以帮助企业预防和减少制程中可能出现的质量问题,提高产品的质量和可靠性。
下面我们将通过一个实际案例来说明PFMEA的应用。
某汽车零部件制造企业在生产过程中,发现了一个常见的故障现象,在焊接过程中,焊接接头出现了焊缝不均匀的情况。
这种情况可能导致焊接接头的强度不足,从而影响产品的质量和安全性。
为了解决这一问题,企业决定对焊接制程进行PFMEA分析。
首先,我们对焊接制程进行了详细的分解,确定了焊接接头的关键特征及其制程参数。
然后,我们列出了可能的故障模式,包括焊接接头焊缝不均匀、焊接接头未完全熔化、焊接接头气孔等。
接着,我们对每种故障模式进行了评估,确定了其可能的影响,包括产品质量不合格、产品性能下降、客户投诉等。
在确定了故障模式及其影响后,我们对每种故障模式进行了风险评估,确定了其严重性、频率和检出能力。
在分析的过程中,我们发现焊接接头焊缝不均匀是导致焊接质量问题的主要原因。
为了解决这一问题,我们采取了一系列的改进措施,包括优化焊接工艺参数、加强操作人员的培训、改进焊接设备等。
经过改进措施的实施,焊接接头的焊缝均匀性得到了显著改善,焊接质量得到了有效保障。
通过对焊接制程的PFMEA分析,我们不仅解决了焊接接头焊缝不均匀的质量问题,还提高了焊接制程的稳定性和可靠性,为企业的持续发展提供了有力支持。
这个案例充分展示了PFMEA分析方法的重要性和实用性,为企业的质量管理工作提供了有力的指导和支持。
总之,PFMEA是一个非常重要的质量管理工具,可以帮助企业识别和预防制程中的潜在故障模式,提高产品的质量和可靠性。
希望企业能够充分认识PFMEA 的重要性,加强对制程的分析和改进,不断提升产品的质量和竞争力。
pfmea案例

pfmea案例PFMEA案例。
在生产制造过程中,为了确保产品质量和生产效率,我们需要对潜在的故障模式和影响进行全面的分析和评估。
而这正是PFMEA(过程失效模式和影响分析)的作用所在。
下面,我们将通过一个实际案例来详细介绍PFMEA的应用。
案例背景:某汽车零部件制造企业在生产过程中出现了一些质量问题,导致产品的合格率下降,客户投诉增加,给企业带来了一定的经济损失和声誉影响。
为了解决这一问题,企业决定对生产过程进行全面的分析和改进,以提高产品质量和生产效率。
案例分析:1. 识别潜在故障模式:首先,我们对生产过程中可能出现的故障模式进行了全面的识别和分析。
通过与生产人员和工程师的讨论,我们确定了可能导致产品质量问题的故障模式,如材料变质、设备故障、操作失误等。
2. 评估故障影响:针对识别出的故障模式,我们对其可能造成的影响进行了评估。
比如,材料变质可能导致产品外观不良,设备故障可能导致生产线停机,操作失误可能导致产品参数偏差等。
我们对每种故障模式的影响进行了量化和分级,以便后续的优先处理。
3. 制定改进措施:在识别和评估了潜在的故障模式和影响之后,我们制定了一系列的改进措施。
比如,对可能导致材料变质的环境因素进行控制,对设备进行定期维护和保养,加强操作人员的培训和管理等。
这些改进措施旨在消除潜在的故障源,提高产品质量和生产效率。
4. 实施改进措施:在制定改进措施之后,我们对其进行了逐一实施,并对改进效果进行了监控和评估。
通过实施改进措施,企业逐渐解决了之前出现的质量问题,产品合格率得到了提高,客户投诉也明显减少,企业的经济效益和声誉得到了提升。
结论:通过对上述案例的分析,我们可以看到PFMEA作为一种全面的故障分析和预防工具,在生产制造过程中发挥了重要作用。
通过对潜在故障模式和影响的分析和评估,企业可以及时发现和解决潜在的质量问题,提高产品质量和生产效率,降低生产成本,提升企业竞争力。
因此,PFMEA的应用具有重要的意义,值得在生产制造过程中广泛推广和应用。
PFMEA案例

30
检查与评估现有的操纵方法
生产部
7﹑
装扣钩
漏装扣钩/扣钩装的位置不正确
线束装入车辆时困难或者安装失败
6
操作员未依规定操作
3
培训操作人员并重点标注图面要求
依照图面规定操作/100%外观检验
2
54
检查与评估现有的操纵方法
生产部
6
扣钩插入的深度不充分
2
培训操作人员并重点标注图面要求
依照图面规定操作/100%外观检验
装线盆入线不正确
3
用正确的装线盆/架
操作员检验
3
36
绝缘破皮,导线断线
端子铆线困难/导通测试不良
4
*裁线机故障/刀片设置太低/刀片用旧;*短路或者开路
5
保护保养/点检
100%检查
2
40
2﹑
压端子
端子变形
铆线端子插入壳仔困难
6
送料爪的变化导致端子经导流板时不正确
2
加大清洁/润滑端子机活动部门的频次
PQC每小时巡检/操作员自检
3
பைடு நூலகம்36
检查与评估现有的操纵方法
工程部
铆线端子插入壳仔后不合格
6
端子在导流板卡住而被硬拉出铆线
2
加大清洁/润滑端子机活动部位的频次
PQC每小时巡检/操作员自检
3
36
检查与评估现有的操纵方法
工程部/品管部/生产部
拉力不够
端子铆线不正确
8
▲
模座/刀座松动
2
保护保养/操纵正确的C/H
每小时拉力测试;巡检
3
48
灯炮装配线束时困难
5
检查图面脏污或者褪色未及时更换
PFMEA范例
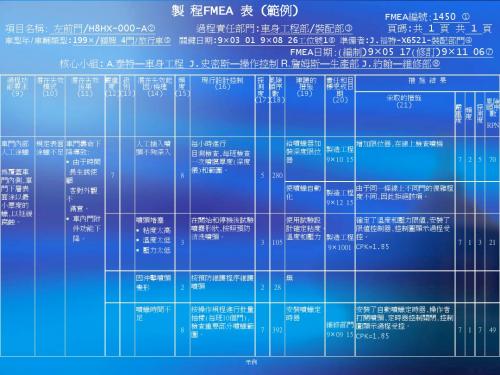
適中的
適度高的 高的 非常高的 幾乎確定
5
4 3 2 1
製程管制方法幾乎可以確定查出失效模式。
製 程 FMEA 填 寫 說 明
19.風險優先數 風險優先數是嚴重度(S)、發生度(O)、和難 檢度(D)的乘積。 RPN=(S)(O)(D) 是一項設計風險的指標。當RPN較高時,設計
小組應提出矯正措施來降低RPN數。一般實務上,
1 in 400
1 in 2,000 1 in 15,000 1 in 150,000 <=1 in 1,500,000
≧1.00
≧1.17 ≧1.33 ≧1.50 ≧1.67
5
4 3 2 1
“可能失效的比率”是根據製程執行中預計發生的失效來確定的。 “失效的機率”用文字描述適合任何類似製程的歷史數據進行主觀評價。
9
8 7 6 5
非常低的
次要的 非常次要的 沒有
4
3 2 1
製 程 FMEA 填 寫 說 明
13.等級 這個欄位用來區分任何 對零件、子系統、或系統將 要求附加於製程管制的特殊 產品特性(如:關鍵的、主要 的、重要的)。如果在製程 FMEA被認定等級,通知設計 負責工程師,這將影響工程 文件相關管制項目的認定。 14.潛在失效原因/機理 在盡可能的範圍里列出所有 可能想像得到的失效原因: ○不當的扭力。 ○不適當的焊接,電流、時間、 壓力。 ○不精確的量具。 ○熱處理不正確-時間、溫度澆 口/通風不正確。 ○不適當或沒有潤滑。 ○缺少零件或放錯。 需要考慮諸如試驗設計之類的方法,來明確那些根本原因起主要作用, 哪些原因容易得到控制。
製 程 FMEA 填 寫 說 明 追蹤確認
製程責任工程師應負責確認所有的建議措施均已
- 1、下载文档前请自行甄别文档内容的完整性,平台不提供额外的编辑、内容补充、找答案等附加服务。
- 2、"仅部分预览"的文档,不可在线预览部分如存在完整性等问题,可反馈申请退款(可完整预览的文档不适用该条件!)。
- 3、如文档侵犯您的权益,请联系客服反馈,我们会尽快为您处理(人工客服工作时间:9:00-18:30)。
2
32 NA
NA
NA
NA
NA
3 8
Supplier failure/Operator error improper handling
SAP check - procedure for RTV if vendor/date is not on the packing Training about the handling and storage of components. Incoming Inspector check the Inspection Lot Number, and open the Inspection Instruction with this number acc. To 35-IC30-GEN-018 (INCOMING QUALITY ASSURANCE WORK INSTRUCTION) SAP system alarm if the good receipt slip is taken to another parts Incoming Inspector must follow the SAP instruction and procedure . Green Acceptance stamp must put on outside of container in case of released components. SAP tracking and blocking the outgoing of the non-conforming materials from stock. Incoming Inspector check the Inspection Lot Number, and open the relevant Inspection Instruction. If the material was not inspected by Incoming Inspection, the SAP do not let the components into the shopfloor.
Document Number: Revision: Release date: Prepared By: Approved by:
Customer sign off (if applicable):
35-QE25-NTM9GENPFMEA-001 B 4/30/2013 xxx xxxx
Action Results Responsibility NA Target Date NA Actions Taken NA Effective date NA S E V O C C D E T R P N
Requirements Precess step/Function Receiving ID 1 Product Correct& good materials Process Follow WI
xxx
xxx
(PFMEA)
A Wuxi/Bay9-1/SMT+FATP xxx
Potential Failure Mode Endanger incoming packaging safety Potential Effects of Failure Functional failure S E V . 8
Current Process Control(Prevention) Receiving Inspector to maintain packaging safety per 35-IC30-GEN-010 (RECEIVING WORK INSTRUCTION) 35-QE30-GEN-043 (Moisture Sensitive Device Control Guide) Incoming Inspection plan 35-IC30-GEN-018 (INCOMING QUALITY ASSURANCE WORK INSTRUCTION) 35-IC30-GEN-006 (MATERIAL ACCEPTANCE INTO STOCKROOM WORK INSTRUCTION Incoming Inspection plan 35-MT30-GEN-019 (SAMPLING PLAN(抽 样计划))
Process Responsibility: xxx Project phase: PVT
Special Char. PotentialCause(s) Symbol /Mechanism(s)OF Failure / ID Supplier system and Jabil system not followed Moisture sensitive component procedure not followed O C C . 2 D E T . 3 R P Recommented Action(s) N . 48 NA
2
Visual - in process inspection. Testing process:FCT AOI (text recognition - comp shape), OBA, FINAL QC Visual Inspection according to moisture indicator card Visual Inspection according to moisture indicator card Visual Inspection according to moisture indicator card Visual inspection, and First article check Testing process:FCT AOI (text recognition - comp shape), OBA, FINAL QC Visual - in process inspection.
2
Visual - in process inspection. Testing process:FCT AOI (text recognition - comp shape), OBA, FINAL QC
2
32 NA
NA
NA
NA
NA
Inspection plan not in line with component inspection requirements damaged packing wrt risk for moisture absorption (coming from supplier) damaged packing wrt risk for moisture absorption (in Jabil)
Current Process Control(Detection) Receving WI
Component doesn't meet component specification
Damaged Functional failure
8
Wrong supplier test
2
Receving WI
Functional failure or field failure Line downtime Repair
8
Sap system not followed, Receiving doesn't identify the parts for inspection No inspection plan existing Right measuring tool not available
4 2
Receving WI Visual - in process inspection. FCT, OBA, FINAL QC Visual - in process inspection. Testing process: , FCT AOI (text recognition - comp shape), OBA, FINAL QC
3
48 NA
NA
NA
NA
NA
Incoming Inspection
2
Accept material
All measure tools
Raw material arrived Damaged in damaged Functional failure conditions Cannot assemble product, loose productivity Raw material Damaged damaged in Functional failure or field transport to failure incoming Cannot assemble product, loose productivity Missing Vendor lost traceability date/lot code Damaged Functional failure or components/ cosmetic failure packing Mixed components Functional failure or field failure Line downtime Repair
PROCESS FAILURE MODE AND EFFECT ANALYSIS
Customer mandated RPN threshold (if applicable):
Customer: Product(s): Product revision: Production line / Cell / Area: FMEA Team:
2 2
24 NA 32 NA
NA NA
NA NA
NA NA
NA NA
8
Incoming Inspector error, system not followed Supplier labeling problem Wrong Jabil labeling at receiving