FMEA在空压机使用中的应用
设备FMEA管理办法

4.工作描述 4.1 由动力设备部负责,车间协助将设备按照 A 类(关键设备)、B 类(重要设 备)、C 类(一般设备)的分类法进行分类,规则如下: 将所有的进口设备均化为 A 类; 4.1.2 按加工工序对产品质量的影响程度、设备价值和设备产能来分:影响程度 高、价值高和瓶颈工序的设备直接划为 A 类设备; 4.1.3 其次为重要设备,再其次为一般设备; 4.2 由设备部组织车间的设备管理、技术及维修人员,负责对 A 类设备进行 FMEA 分析,对风险特性评价,评价的结果至少要经上述人员共同评审过,方可被正式 采用。具体评价规则如下: 4.2.1 严重度:评价每一失效模式对应的后果,其依据是设备的可维修性、生产 产品的质量以及安全性。
4.2.2 频度:导致事故发生的原因出现的频率、失效模式发生的频率。
严重度 数 1 2 3
4
5
影响
选定条件
较小 较小的失效,对设备的使用无主要影响,修复时间TI=≤60 min
一般 主要
一般的失效,需要短期的修理,60 min ﹤ TI ≤120 min 主要的失效,需长期的行动,120 min ﹤ TI ≤240 min 或影响到设备的加工精度,被设备的使用者注意到并纠正。
1.目的:
设备 FMEA 管理办法 编号:QCH/GL/012
预防由于设备失效而使生产中断,缩短维修时间,持续改善设备维护工作。
2.范围: A 类设备,即关键设备.
3.术语: 关键设备(A 类设备):生产线上无法用其它设备取代的设备、单台价格昂
贵的、功能复杂的、维修难度较大的、精大稀设备及引进设备。对于关键设备要 建立“设备 FMEA 表”,提出预见性维护的要求。
灾难性 严重失效,TI ﹥240 min 或加工工件不合格,加工出的工件产生工
DFMEA-汽车空调 - 压缩机总成

启动空 没有空调 调,压缩 功能或制 机不运 冷能力 转,或制 弱,客户 冷效果差 抱怨
8 8
8
压缩机内部故障 2 I 压缩机制冷能力差 1
压缩机泄漏
1
整车匹配计算
8
润滑效果差
4
6
压缩机安装不牢固 2
6
运行平稳, 噪声小
运行稳定 不能正常 性差,噪 使用,客
声大 户抱怨
6
6
6
压缩机支架存在设 计缺陷
风 险R 顺P 序N 数
编制人: FMEA日期(编制):
建议措施
责任及目标完 成日期
FMEA编号: 页码: 第 页 共 页
(修订)
措施执行结果
采取的措施
S O D RPN
线束通电检查,插 接件插接牢固
1
16
零部件性能试验 5
80
零部件性能试验 2
16
零Байду номын сангаас件性能试验 5
40
零部件性能试验 5
发动机低速运转,
空调 压缩机总成
系统 子系统
潜在失效模式及后果分析 (设计FMEA)
年度车型/车辆 部件 类型:
设计责任: 关键日期:
核心小组: 过程功能
要求
严
频
潜在失效模式
潜在失效后 果
重 度
分 潜在失效起因/机理 度
(S) 类
(O)
现行设计控制 预防
8
电源断路,插接件 不牢
2
吸入制冷剂 进行压缩, 并将压缩后 的制冷剂输 送到空调系
3
改进设计,增加强 度和刚度
N 皮带过松导致打滑 5
压缩机安装偏差较 大
5
基于FMEA的螺杆空气压缩机控制器可靠性分析

分袁 梳理出每个功能模块所包含的元器件遥 明确 每个元器件的故障模式和功能电路模块的故障表 现形式 [2]袁 根据元器件的故障模式对功能模块电 路的影响袁 得到元器件的故障模式与功能电路故 障模式之间的关系遥 然后袁 再根据功能模块电路 的故障模式对整体电路所产生的影响袁 得到功能 模块电路的故障模式与整体电路的故障模式之间 的对应关系遥 最后袁 得到元器件的故障模式与功 能模块电路故障模式袁 以及整体电路故障模式之 间的对应关系遥
FMEA 是一种归纳分析方法袁 它可 以分析系统中每一种产品所有可能产生 的故障模式及其对系统造成的所有可能 影响袁 并按每一个故障模式的严重程度尧 检测难易程度和发生频度予以分类遥 其 目的在于找出系统或产品潜在的失效及 其影响袁 为设计尧 制造和质量控制提供 可行的消除或减少潜在失效发生的措施 与对策袁 及早地进行设计与制造过程的 改进袁 提高产品质量 [1]遥 FMEA 的结构 框图如图 1 所示遥
对各功能电路 明确功能电路
进行划分
的故障模式
梳理整体电路 描述整体电路 的功能清单 功能故障模式
元器件的故障 模式对功能电路
产生的影响
功能电路的故障 对整体电路产生
的影响
梳理元器件 清单
描述元器件 故障模式
建立元 器件的 故障模 式和整 体电路 的功能 故障模 式之间 的联系
损模块采用故障模式及影响分析 渊FMEA冤 的方法袁 对控制器在使用 过程中的各种潜在的故障模式尧 故障原因进行定
1 KS 系列某型控制器 FMEA 的目的
原理概述
本文所研究的对象是单级喷油螺杆空压机 KS 系列某型控制器数模混合板级电路袁 该电路的功 能框图如图 2 所示袁 包含 8 个单元电路模块袁 分 别是院 主控模块尧 电源模块尧 存储模块尧 数据采 样模块尧 电平测试模块尧 液晶屏和触摸屏驱动模 块袁 以及接口电路模块遥
空调系统风险评估(FMEA五分制法)

空调系统质量风险识别及控制规程一、目的1、为降低和控制车间洁净区空调系统相关的风险,建立有效的洁净区空调系统质量控制体系,提高产品质量提供风险分析参考。
2、为设计单位提供风险分析参考,以便设计单位采取适当设计措施以规避或将风险控制在可以接受的范围内,更好地设计出符合生产工艺和GMP要求的空调系统,减少可能的设计缺陷。
3、为车间洁净区空调系统的验证确认活动提供风险分析参考。
4、为车间洁净区空调系统日常运行和产品的质量控制提供风险分析参考。
二、适用范围,空调系统的设计,安装,使用,验证过程。
三、定义:风险:是危害发生的可能性及其危害程度的综合体。
风险管理:即系统性的应用管理方针、程序实现对目标任务的风险分析、评价和控制。
风险分析:即运用有用的信息和工具,对危险进行识别、评价。
风险控制:即制定减小风险的计划和对风险减少计划的执行,及执行后结果的评价。
四、风险识别内容• 4.1、风险评估风险由两方面因素构成,风险评估是基于对危害发生的频次和危害程度这两方面考虑而得出的综合结论。
4.1.1风险产生的后果即危害的严重程度(S)严重程度第1级:可忽略第2级:微小第3级:中等第4级:严重第5级:毁灭性4.1.2风险发生的概率(O)第1级:稀少(发生频次小于每十年一次)第2级:不太可能发生(发生频次为每十年一次) 第3级:可能发生(发生频次为每五年一次)第4级:很可能发生(发生频次为每一年一次)第5级:经常发生(几乎每次都可能发生)4.1.2风险发生时的可预知性(D)第1级:不可能预知第2级:不太可能预知第3级:可能预知第4级:很可能预知第5级:完全可预知4.2风险识别项目风险源风险详述风险可能导致的结果风险严重程度风险发生概率风险可预知性1 风源、新风新风空气质量低,顾在大量灰尘初效过滤器使用期限缩短1 3 2新风温度、湿度极高或初效过滤器使用期限缩短洁净区内温、湿度4 2 5极低超出可处理范围不合格2 初效过滤泄露、破损中效使用期限缩短1 1 23 中效过滤泄露、破损高效使用期限缩短2 2 34 高效过滤泄露、破损洁净区洁净度受到破坏,使药品以污染5 5 25 空调机组泄露臭氧消毒后,气体泄露到外部影响人身安全 5 5 2送风量不足影响洁净区洁净度,使药品生产受到污染4 5 26 风管泄露臭氧消毒后,气体泄露到外部影响人身安全 1 5 5洁净区送风量不足影响洁净区洁净度,使药品生产受到污染1 1 17 回风阀失灵空调关闭后,空气倒流洁净区洁净度受污染5 1 38 加湿段蒸气压力不稳洁净区湿度超标,影响高效使用寿命4 5 59 加热段蒸气压力不稳洁净区温度超标 4 5 510 表冷器冬季防冻,表冷器内部冻结表冷器冻裂,露水,空调停用1 2 511 除湿段无除湿设施夏季湿度超标 4 5 512 风机轴承磨损空调停用 4 1 1 风叶变形噪音过大,加速轴承磨损4 1 113 人员人员未经培训或培训不到位导致错误操作影响洁净区洁净度,使药品生产受到污染或损坏空调系统4 2 5人员疲劳导致误操作影响洁净区洁净度,使药品生产受到污染或损坏空调系统4 2 5五、风险控制规程:5.1降低风险的计划5.11.在验证的准备阶段,对所有相关的文件均进行了一次核查,以确保文件的准确性5.12.对相关的操作人员进行了岗位操作规程的培训,以确保全部验证过程能按文件规定执行。
FMEA在设备管理方面的应用

FMEA在设备管理方面的应用摘要:本文主要思考了FMEA在设备管理方面的应用,明确了应用的方法,以及应用过程中需要注意的问题,希望可以为今后的应用工作带来参考。
关键词:FMEA;设备管理;应用前言FMEA在生产管理中广泛应用,FMEA能够分析问题及影响,并进行风险评估,能够预防性改进,提高生产的可靠性。
FMEA应用在设备管理上,可以进行设备故障风险预防,保障设备运行的可靠性.1 FMEA的实施FMEA实施采用8D流程,即D1建立解决问题小组;D2描述问题;D3执行暂时对策;D4找出问题真正原因;D5选择永久对策;D6执行及验证永久对策;D7防止再发;D8团队激励,FMEA的主要表现形式为潜在失效模式和后果分析表格,即FMEA表。
FMEA表中包含了FMEA活动过程中的所有信息,可以将表格的填写项目分为以下三部分:第一部分,后果影响是什么?(1)潜在失效模式,问题可能发生的部分;(2)潜在失效后果,推测问题可能引起的不良结果;(3)严重度(S),结果影响后果的程度;(4)级别,主要是分辨失效后果是属于关键还是重要。
第二部分,怎样取得预防或探测对策?(1)潜在失效起因,即分析故障产品的可能原因是什么,这里可以运用多种工具,最常用的是鱼骨图;(2)频度(0),针对失效起因而言,出现的几率;(3)探测度(D),表示现行方法对潜在问题查出的难易程度(4)RPN,表示优先次序的指数,数值越大代表潜在问题越严重,应尽早采取措施;(5)建议措施,对潜在问题制定相应的预防措施,针对这些潜在的问题点,应提前预防。
第三部分,措施的实施效果如何?采取的措施,即前面建议措施的结果,对预防措施计划实施状况的确认。
评判出措施实施后新的严重度、频度和探测度,并计算出新的RPN。
FMEA表在实际应用中需关注以下几点:(1)严重度(S):即评价失效后果后赋予的分值,取1~10分,不良影响愈严重则分值愈高。
需要强调一点,我们所给出的严重度是给定失效模式最严重的影响后果的级别,其降低只能通过改变设计的手段才能实现。
FMEA(失效模式与影响分析)简介

没有影响;事件发生的频率要记录特定的失效原因和机理多长时间发生一次以及发生的几率。
如果为10,则表示几乎肯定要发生,工艺能力为0.33或者ppm大于10000。
5.2检测等级是评估所提出的工艺控制检测失效模式的几率,列为10表示不能检测,1表示已经通过目前工艺控制的缺陷检测。
5.3计算风险优先数RPN(riskprioritynumber)。
RPN是事件发生的频率、严重程度和检测等级三者乘积,用来衡量可能的工艺缺陷,以便采取可能的预防措施减少关键的工艺变化,使工艺更加可靠。
对于工艺的矫正首先应集中在那些最受关注和风险程度最高的环节。
RPN最坏的情况是1000,最好的情况是1,确定从何处着手的最好方式是利用RPN的pareto图,筛选那些累积等级远低于80%的项目。
推荐出负责的方案以及完成日期,这些推荐方案的最终目的是降低一个或多个等级。
对一些严重问题要时常考虑拯救方案,如:一个产品的失效模式影响具有风险等级9或10;一个产品失效模式/原因事件发生以及严重程度很高;一个产品具有很高的RPN值等等。
在所有的拯救措施确和实施后,允许有一个稳定时期,然后还应该对修订的事件发生的频率、严重程度和检测等级进行重新考虑和排序。
在设计和制造产品时,通常有三道控制缺陷的防线:避免或消除故障起因、预先确定或检测故障、减少故障的影响和后果。
FMEA正是帮助我们从第一道防线就将缺陷消灭在摇篮之中的有效工具。
FMEA是一种可靠性设计的重要方法。
它实际上是FMA(故障模式分析)和FEA(故障影响分析)的组合。
它对各种可能的风险进行评价、分析,以便在现有技术的基础上消除这些风险或将这些风险减小到可接受的水平。
及时性是成功实施FMEA的最重要因素之一,它是一个"事前的行为',而不是"事后的行为'。
为达到最佳效益,FMEA必须在故障模式被纳入产品之前进行。
FMEA实际是一组系列化的活动,其过程包括:找出产品/过程中潜在的故障模式;根据相应的评价体系对找出的潜在故障模式进行风险量化评估;列出故障起因/机理,寻找预防或改进措施。
车用空压机应用工程规范

汽车用空气压缩机应用工程规范(1)亚新科美联(廊坊)制动系统有限公司产品部付滨涛2009年1月多年来的《APQP》和《FMEA》提醒我们:为了获得所期望的空压机的耐用性/可靠性,加强、补充和完善《APQP》是非常必要的!目的!•做为《空压机产品设计输出》的一部分,汽车/工程机械应按照《空压机应用工程规范》正确地安装和使用空压机。
本文所引用的参考资料1.AEB20.11报告《发布汽车-工业安装要求—Cummins牌(Wabco)15.2,18.7,30.4and37.4CFM型空压机的空气压缩机系统》2.WABCO—2008-0003检测报告3.QC/T29077-92中华人民共和国汽车行业标准《汽车用空气压缩机质量分等》4.QC/T29078-92中华人民共和国汽车行业标准《汽车用空气压缩机技术条件》5.亚新科美联(廊坊)制动系统有限公司产品部相关试验报告压缩空气系统压缩空气系统•压缩空气系统包括空压机,空滤器,空压机进气管,排气管,调压阀,接收罐,空气干燥器,净化罐,储气罐,第一储气罐和第二储气罐以及空气损耗装置。
作用:为汽车/机械上的空气消耗装置提供具有合适压力的清洁、干燥、凉爽的空气。
空气压缩机•通过运动件的位移,使一定容积的气体顺序地吸入和排出封闭空间,以提高静压力的机器.空压机的几个特性1.空压机的工作原理2.工作特性3.排气量4.容积效率5.排气温度6.进气阻力7.随气排油8.负载循环9.轴功率空气机的工作原理•以发动机为动力源;•由齿轮/皮带轮传递扭矩。
•在空压机曲柄连杆机构的带动下,空压机的活塞做直线往复运动。
•在活塞的往复运动间,空压机的进、排气阀片反复地交替开启和关闭。
空压机就是通过这样动作,将压缩空气顺序地送入气体存储装置。
空压机《工作特性》湿气空气润滑油•当活塞下行时,经过滤清的空气被吸入气缸体。
•空气中所含的水分也随着空气被吸入到气缸体内。
•少量的润滑油从缸壁的间隙中不可避免地也被虹吸到活塞顶部。
机械设备故障模式与效果分析FMEA

机械设备故障模式与效果分析FMEA 机械设备在操作过程中难免会出现故障,一些故障对设备造成的影响比较小,而另外一些故障则会引发设备的停机甚至是严重的损坏。
为了更好地防范机械设备故障,提高设备的稳定性与可靠性,近年来,机械设备故障模式与效果分析(FMEA)得到了广泛的关注与应用。
FMEA方法可以有效地帮助企业识别并消除故障,并且它可以简化维修和修理时需要的时间和成本。
本文将详细介绍机械设备故障模式与效果分析FMEA,并分析其应用情况。
一、机械设备故障模式的定义机械设备故障模式是指在机械设备的使用过程中,出现的各种故障类型。
这些故障类型可能为机械磨损、部件的故障、电器失效、以及在运转过程中的各种故障等。
这些故障都会对设备的使用带来一定的限制和威胁,因此我们需要针对不同的故障类型进行研究和分析,以便更好地维修和管理机械设备。
二、机械设备故障模式的分类根据机械设备的故障类型不同,可以将其分为以下几个方面进行分类,便于更好地进行分析和研究:1. 机械磨损故障:由于机械设备长期使用和磨损,是其中最常见的一种故障类型,这种故障会导致机械部件的磨损程度加剧,从而导致所使用的设备效率降低。
2. 电气失效故障:由于电气部件的故障原因,可能是由于电气维护不当造成的电气故障,也可能是由于同步器故障或是线圈故障等引起的电气失效情况。
3. 运转安装故障:由于设备安装的不合理,导致设备在运行中不稳定的状况,从而产生一系列故障,如设备振动、响声和阻碍等等。
4. 流体压力、温度故障:设备在运行时,可能产生流体压力和温度故障,导致液压泵的失效,导致机械设备无法正常运转。
三、机械设备故障模式及其效果分析FMEA作为一种管理方法,主要用于识别并消除潜在故障,以及简化维修和修理时需要的时间和成本。
在机械设备故障模式和效果分析中,常常采用故障树分析法,来进行机械设备故障模式和效果的分析。
1. 故障树分析法故障树分析法是通过对设备故障的情况进行系统分析,进而对系统产生影响的子系统和部件进行分析,以便更好地维护和管理机械设备。
空气压缩机自动控制技术的应用

空气压缩机自动控制技术的应用摘要:企业选择将空气压缩机自动控制技术应用于实际作业中,可以显著提高空气压缩仪器组的实际使用效率,最终保证空气压缩机器组实际运行的安全、可靠。
因此,企业内的工作人员在使用空气压缩机器自动化控制技术的时候,需要注意以空气压缩机器的基本原理作为前提,并充分掌握空气压缩机自动控制技术的系统构造,争取掌控多个环节内容,从而使空气压缩机器可以创造较高的经济收益以及社会效益,为空气压缩机器的长久、可持续发展提供支持,促使我国空气压缩机器的实际收益显著提高。
关键词:空气压缩机;自动控制技术;分析一、空气压缩机器的相关概述随着我国工业生产的不断发展,其研发出多个不同的科技衍生物,而空气压缩机器作为一种新型的动力机器设备,其广泛应用于机械制造领域、矿山等大部分行业中,且逐渐成为各个行业主要应用的机械设备。
一旦空气压缩机器在实际作业的过程中,发生机械不稳定或者故障的情况,会对企业的实际作业产生不良影响,甚至导致企业丧失部分经济效益。
现阶段,各个行业中经常使用的空气压缩机器多是常规的继电器电气控制系统、智能单片机操作系统或者小型可以编制程度的控制机器系统。
空气压缩机器在无人参与作业的状况下,可以根据空气压缩系统设定的控制系统展开作业,而自动控制系统作为实现空气压缩自动化的主要途径,相关人员需要根据实际操作原理的不同,将其分成开环控制系统以及闭环控制系统。
目前,空气压缩自动化控制系统中,主要包含的内容包括继电器电气控制系统、智能单片机控制系统以及PLC控制系统。
而PLC控制系统作为一种模拟继电器控制系统发展的全新系统,其最先被适用于汽车制造行业中。
二、空气压缩机自动控制系统构成2.1空气压缩机器的工作原理现阶段,大部分企业使用的空气压缩机常为离心式的压缩机,根据压缩机的实际压缩能力,可以将其分成三个不同的等级:一级压缩主要是指空气压缩机自动控制系统接通电源之后,叶轮可以进行长时间、持续的转动措施,并将空气经过过滤网过滤到一级对应的压缩腔中;二级压缩是指空气在离心机设备中,被机器甩进下一级别的腔壁中,并经过腔壁孔进入到对应的二级压缩腔内;三级压缩主要是指空气经过压缩腔壁的压力后,可以进入到对应的三级压腔中。
压力传感器在空压机安全管理系统上的应用

压力传感器在空压机安全管理系统上的应用随着科技的不断发展,空压机在各个领域得到了广泛的应用。
空压机作为重要的机械设备之一,其安全管理至关重要。
在安全管理的过程中,压力传感器是不可或缺的一部分。
压力传感器是一种测量压力的设备,主要用于测量和控制液体、气体等在流体系统中的压力。
在空压机的安全管理中,压力传感器可以起到一定的作用。
下面将重点介绍压力传感器在空压机安全管理系统上的应用。
一、监测压缩机运行状态压缩机是空压机的关键设备之一,其运行状态的良好与否会直接影响空压机的性能和安全。
通过安装压力传感器来监测压缩机的运行状态,可以实时地检测到压缩机的压力变化情况,从而及时发现并解决压力变化过大的问题,确保压缩机的正常运行。
二、自动调节压力空压机在运行时,需要保持一定的工作压力,以保证空气系统正常工作。
通过在空压机的出口部位安装压力传感器,可以自动地检测压缩机的出口压力,并通过控制压缩机的出口压力来实现自动调节压力的目的。
这样,即使系统中的工作压力发生变化,也可以及时对压缩机输出压力进行调整,从而保证系统的正常工作状态。
三、预警系统空压机在运行时,可能会出现各种安全隐患。
例如,系统压力过高、过热、油压不足等问题,这些问题可能会影响整个系统的稳定性和安全性。
通过安装压力传感器,可以预警系统管理员,及时采取措施避免安全隐患的发生,有效地减少了安全事故的发生率。
四、数据监测和分析压力传感器可以将实时监测的压力数据传输到控制系统中进行处理和分析,从而提供对空压机运行状态的全面了解。
通过对数据的分析和研究,可以识别系统存在的问题,并查找问题的根源,为控制系统的优化提供依据。
压力传感器在空压机安全管理系统上的应用非常广泛。
通过安装压力传感器,可以及时监测压缩机的运行状态并自动调节压力;同时,还可以提供预警系统,及时避免安全隐患的发生。
通过数据的监测和分析,可以识别问题并寻找问题的根源,从而为后续的控制系统优化提供依据。
飞机供气系统故障模式与效果分析FMEA

飞机供气系统故障模式与效果分析FMEA飞机供气系统作为飞机的关键部件之一,在保证飞机正常运行和乘客舒适度的同时,也面临着各种潜在的故障模式和可能的影响。
本文将对飞机供气系统的故障模式进行分析,并评估可能产生的效果,以便为相关维修保养提供参考。
1. 引言飞机供气系统是指负责为飞机提供正常工作所需的气源,并维持飞机在飞行过程中的气压平衡。
该系统通常由压力变送器、气源总管、驱动机构、控制元件等多个组件组成。
然而,在长时间使用或者特殊情况下,该系统可能面临各种故障模式。
2. 故障模式分析2.1 压力变送器失效在飞机供气系统中,压力变送器负责测量气源总管中的气压,并将其转换为电信号用于飞机系统的控制。
当压力变送器失效时,可能会导致气源总管中的气压无法正常测量,从而影响飞机供气系统的正常工作。
2.2 气源总管泄漏气源总管作为飞机供气系统的主要部分,负责将气源引导至各个飞机系统。
如果气源总管发生泄漏,无论是由于管道破裂、接头松动还是其他原因,都会导致气源无法正常供给,进而影响飞机的正常运行。
2.3 驱动机构故障驱动机构是飞机供气系统的核心组件之一,负责将气源从气源总管传递至各个系统并维持稳定的气压。
然而,驱动机构可能面临各种故障,例如电源故障、机械驱动部件磨损等,这些故障可能导致气源无法正常传递,进而影响飞机的正常运行。
3. 故障效果分析3.1 供气不足当飞机供气系统遭遇压力变送器失效、气源总管泄漏或驱动机构故障等情况时,供气可能会出现不足的情况。
这将导致飞机系统无法正常工作,例如发动机性能下降、空调系统无法提供舒适的气流等。
3.2 燃油效率下降飞机供气系统的故障可能导致发动机性能下降,进而导致燃油效率下降。
当供气不足时,发动机无法正常燃烧燃油,从而造成额外的燃油消耗,增加运营成本。
3.3 客舱压力异常飞机供气系统的故障还可能导致客舱压力异常。
当供气不足或气源泄漏时,客舱内的气压无法保持正常,可能会对乘客产生不适,甚至危及乘客的安全。
FMEA的作用及分析方法

可以做什么? —设计变更 —过程变更 —特别的控制 —标准、程序或
指南的更改
采取措施后的 效果验证
3.5 PFMEA分析要素——过程步骤/功能
➢ 过程步骤:指工序
✓ 在编号过程和术语的基础上,填入识别的所需分析过程步骤或操作 (可填入编号或名称。名称方面如车削、钻孔、功丝、焊接、装配 等)。
✓ 使用的过程编号体制、先后排序和术语应与那些用于过程流程图的 文件(控制计划、作业指导书)保持一致,以确保可追溯性和联系。
•DFMEA---设计FMEA,在产品设计前对产品的每一个模块和软件 系统进行各自的DFEMA分析,如结构安装、安全设计、机芯配合、 外部接口等,也可细化到各个元器件。分析对象:以系统、子系 统或零部件为分析对象
•PFMEA---过程FMEA(制造/装配FMEA),针对产品的生产制造过程 进行的分析。分析这些生产过程中可能会产生什么样的失效模式 以及带来怎么样的影响后果,最终导致产品的失效的。分析对象 :以生产工艺过程的每道工序为分析对象;
➢ 产品生产之前,设计阶段,由设计缺陷产生 的故障模式
➢ 在生产之前,针对生产和组装过程缺陷的故 障模式
➢ 在产品使用之前,对系统或过程产生的缺陷 引起的故障模式的分析
➢ 对设备系统(一般机械)、分系统(电子、机 械、控制)、组件(工装夹具、物料输送、驱 动)、部件的潜在失效模式的分析
1.4 FMEA的分类
措施结果
建议 措施
责任和目标
完成日期
采取措施及 生效日期
S
O
D
R P
N
3.3 PFMEA表头信息
➢ 项目名称:
填入所需分析过程的系统、子系统或零部件的名称
➢ 过程责任:
压缩空气系统质量风险评估(FMEA四分制法)

压缩空气系统质量风险评估压缩空气系统风险评估1.概念:1.1质量风险:指质量危害出现的可能性和严重性的结合。
2.质量风险管理的程序:3、风险矩阵图危害发生的可能性(F)启动风险管理过程质量风险管理程序的输出/结果4 HACCP分析流程5风险评估方法5.1 风险确认:可能影响产品质量、产量、工艺操作或数据完整性的风险;5.2 风险判定:包括评估先前确认风险的后果,其建立在严重程度、可能性及可检测性上;5.3 严重程度(S):主要针对可能危害产品质量数据完整性的影响。
严重程度分为四个等级:5.4 可能性程度(P):测定风险产生的可能性。
工艺/操作复杂性知识或小组提供的其他目标数据,可获得可能性的数值。
为建立统一基线,建立以下等级:5.5 可检测性(D):在潜在风险造成危害前,检测发现的可能性,定义如下:RPN(风险优先系数)计算:将各不同因素相乘;严重程度、可能性及可检测性,可获得风险系数( RPN = SPD )RPN > 16 或严重程度= 4高风险水平:此为不可接受风险。
必须尽快采用控制措施,通过提高可检测性及降低风险产生的可能性来降低最终风险水平。
验证应先集中于确认已采用控制措施且持续执行。
严重程度为4时,导致的高风险水平,必须将其降低至RPN最大等于816 ≥RPN ≥8中等风险水平:此风险要求采用控制措施,通过提高可检测性及(或)降低风险产生的可能性来降低最终风险水平。
所采用的措施可以是规程或技术措施,但均应经过验证。
RPN ≤7低风险水平:此风险水平为可接受,无需采用额外的控制措施。
质量风险评估表质量风险评估表(续前页)质量风险评估表质量风险评估表质量风险管理记录18。
设备FMEA

设备和工装潜在失效模式及后果分析Potential Failure Mode and Effects Analysis for Tooling & EquipmentMachineryFMEA简介失效模式及后果分析思想可用于机器以降低与有关机器有关的潜在失效模式发生的可能性。
(贯穿全文中的术语“机器”包括设备和工装),机器FMEA(MFMEA)支持从设计开发到设计批准的机器设计过程。
MFMEA是对机器的整个运行过程中每一步骤或每项功能的完全评审。
本手册陈述了用于开发有效MFMEA的思路。
对于机器的过程FMEA的建立开发,应遵循克莱斯勒、福特和通用公司FMEA手册中的过程FMEA思路。
应在用于生产的任何机器制造之前,启动建立过程FMEA。
MFMEA是用于评估、改进机器的可靠性、可维修性、耐用性的设计的输出。
MFMEA是动态文件,在机器开发与运行的各个阶段,发生更改或获得更多信息时持续予以更新。
用户的定义MFMEA中“用户”的定义安装用于生产的机器的制造机构。
制造机构包括工厂工程师、维护、生产以及其它工厂方支撑人员。
小组的努力在进行MFMEA的过程中,希望负责机器的工程师能够主动地联系所有相关部门的代表。
这些领域区包括(但不限于)生产、制造工程,安全、质量、供方、产品工程和用户。
FMEA过程应成为促进各相关部门之间相互交换意见的一种催化剂,从而推进小组协作的工作方式。
另外,对于任何商业“类别”的组分,如果需要的话,也应查询来自这些供方代表的意见。
机器FMEA 除非负责的工程师有FMEA和团队工作推进经验,否则有一位有经验的MFMEA推进员来协助小组的工作是非常有益。
机器FMEA基本上是由负责机器工程师/小组使用的一种分析技术,用于尽可能地确保机器在运行过程中的潜在失效模式及其相关的失效起因/机理都考虑到了。
因为MFMEA是预防性维护方案的输入,并用于辅助将使用的机器控制的实现,因此协作小组中如无用户维护及供方现场服务部门的代表,不同能形成有效的MFMEA。
工艺FMEA在机械零件加工过程中的应用
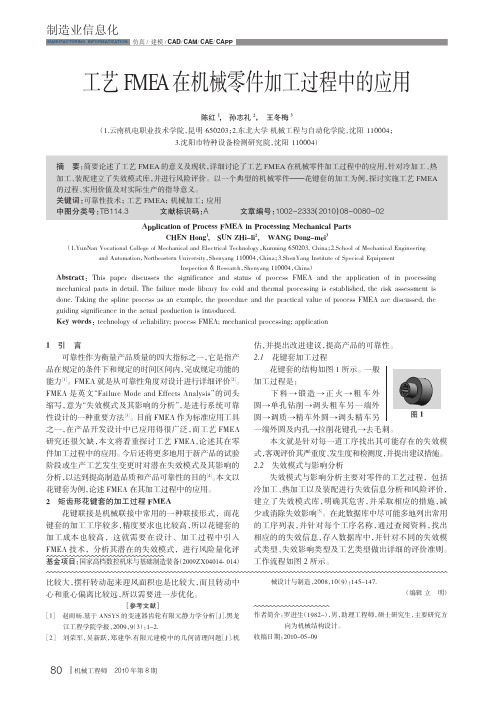
中图分类号: TB114.3
文献标识码: A
文章编号: 1002-2333 (2010 ) 08-0080-02
WANG Dong-mei3
Application of Process FMEA in Processing Mechanical Parts
CHEN Hong1, SUN ZHi-li2,
!!!!!!!!!! ) , 女, 副教授, 研究方向为机械可靠性。 作者简介: 陈红 (1966收稿日期: 2010- 04- 28
机械工程师
2010 年第 8 期
81
(1.YunNan Vocational College of Mechanical and Electrical Technology , Kunming 650203, China; 2.School of Mechanical Engineering and Automation, Northeastern University , Shenyang 110004, China; 3.ShenYang Institute of Specical Equipment Inspection & Research, Shenyang 110004, China )
风险评价
风险评价 准则库
采取的措施
根据采取的措施重 新进行风险评价
效果对比
风险评价参数的梯形图
保存
工艺 FMEA 汇总表
图2
工艺 FMEA 系统功能结构图
下面以花键套加工过程中第六道工序 “ 粗车 ” 为例, 分析其失效模式及影响可能出现的失效模式如下。 (1 ) 外圆出现混乱波纹 。 产生的影响是表面粗糙度 大, 加剧磨损, 而产生的原因是车床主轴轴向窜动大或主 轴轴承磨损严重,建议措施为更换轴承。按风险评价准 发生度为 3, 检测度为 4。 当我们根据 则, 此项严重度为 5, 建议采取措施后, 其发生度降为 2, 检测度为 3, 危险优先 数 RPN 从 60 降为 30。 (2 ) 圆柱度超差。产生的影响是装配精度降低, 产生 ) 车床主轴轴线与床身导轨 的原因及建议措施如下: (a
冲压车间设备FMEA分析法

录
运停异常有碰 伤人员风险
电气控制系统 4 故障、行车轮
卡阻
PM 检查大 PM 检查大小
1
小车电控 车电控柜, 柜,检查车 检查车轮磨
5
轮磨损状态 损状态
供应商 PM
定期测试
20
检查电控 柜;行车车
轮轮缘磨
损每周记
刘春阳
行车外包供应商 PM 定期测试检查 电控柜;行车车轮 4 轮缘磨损每周记 录
1
5
20
1
加入风险因 素辨识,每 日 TPM、定 期 PM 相关 检查
加入风险因 素辨识,每 日 TPM、定 期 PM 相关 检查
7
每年由叉 车维保服 7 务商进行 控制系统 测试维保
ห้องสมุดไป่ตู้
责任人及 目标日期
采取措施
闫峻/于 大江
每年由叉车维保 服务商进行控制 系统测试维保
严 重 度 S
频 度 数 O
可 探 测 度 D
吊运过 程中起 升机构 无动作
冲压 车间
吊运模具、空工 位及设备维修 使用
大小车 不运行 或轨迹 异常
严
潜在的失效后 重
果
度
S
潜在的失效 原因
频 度 数 O
现行过程控 制预防
现有过程控 制监测
可 探 测 度 D
风 险 系 数 RPN
建议措施
1、损坏安全装 置;2、碰伤、 撞伤人员
1
电气控制系统 故障、液压力 不足或液压系 统故障
风 险 系 数 RPN
113 3
1、损坏安全装 置;2、碰伤、 撞伤人员;3、 驾驶人员受伤
1
轮胎磨损超标
1
设置轮胎报 废警示线, 每日 TPM 检 查,按需更 换
- 1、下载文档前请自行甄别文档内容的完整性,平台不提供额外的编辑、内容补充、找答案等附加服务。
- 2、"仅部分预览"的文档,不可在线预览部分如存在完整性等问题,可反馈申请退款(可完整预览的文档不适用该条件!)。
- 3、如文档侵犯您的权益,请联系客服反馈,我们会尽快为您处理(人工客服工作时间:9:00-18:30)。
空气和油混合气体经过粗 、 精两道分离 , 将压缩空气 中的油分离出来 , 最后得到洁净 的压缩 空气 。冷却
器用 于冷 却压 缩空 气 和油 。
22 故 障模 式及 影响 分析 . 分 析人 员 通 过 调查 走 访 相关 的企 业 , 取 空压 选 机 常 见 故 障及 事 故 案 例 , 析可 能 发生 的不 期望 发 分
等级
1 0 8
6
故障可检测度
需专业的测试方法 ,否则无 法检 测到故障
风 险优先 度 R N按 以下 公式 进行 计算 : P
RPN=O ×S ×D 口 1
通过拆解 ,并经仪器可测量 ,需要 时间较长
通过拆解可检测
其 中 : 一潜在 故 障模 式 发 生 时影 响后 果 的严 重程
.
过 喷 油对 主 机 内 的压 缩 空气 进 行 冷却 , 主机 排 出的
安 全 事故 的发 生 , 保证 生产 的顺 利进 行 。
12 F A的评 价 步骤 . ME
对 系统进 行 F A分 析一 般分 为 4个 步骤 ] ME 。 ( ) 查 所分析 系统 的情况 , 集 整理 资料。 1调 收
措施 ,从源头上消 除故 障隐患。 关键词 : ME 空 压机 ; F A; 潜在 失效模式 中图分类号 : P3 . T 1 5 1 文献标识码 : B 文章编号 : 6 19 0 (0 20 —0 30 17 .9 5 1)90 6 —3 2
故 障类 型 和影 响分 析 ( ME 是 一种 用来 确定 F A)
( 分析 故 障类 型 和影 响 。列 出造 成 每一 个 不 4) 期 望 发 生 事 件 出现 的故 障类 型 。这 是 F A评 价 ME 的核 心单 元 , 要 对 整个 系 统 和 系统 可 能产 生 的故 需 障 非 常熟 悉 , 则 会严 重 影 响 分析 质 量 。最 好 由安 否 全管 理人 员 、 技术 负 责人 员和工 人 三者共 同进行 。 结果 汇 总 , 对 系统影 响 大的 故障 汇总 , 将 详细 分 析并 制定 削减 风 险 的措 施 。
程 度 , 出可 以或 可 能采取 的预 防改进 措施 , 提 以减少
2 空压机使 用 中 F E M A分析应用
21 空压 机 系统概 述 .
空 气压 缩 机 是 气 源装 置 中 的主体 , 它是 将 原 动 机 ( 常 是 电动 机 ) 机 械 能 转换 成 气 体 压 力 能 的 通 的 装置 , 杆式 空气 压缩 机是 喷油 单级 双螺 杆压 缩机 , 螺 采 用 高效 带轮 传 动 , 动 主机转 动进 行空 气压 缩 , 带 通
生 事 件类 型 , 致 不 期 望 发生 事 件 的故 障类 型 和故 导
障发生的原 因, 如常见的储气罐 、 安全阀 、 压缩机和
冷 却 系统 的故 障 。 23 确 定 故 障等级 .
作者 简 介 : 陆春 荣 ,男 ,安 全 工程 硕 士 ,南京 化 工 职业 技术 学 院讲 师 ,安 全专 业 学科 带 头人 ,主要 负责 化工 安 全技 术 、安 全 管理 方 面 的教 学和 研究 工作
等 方 面 的数 据 和资 料 。 ( 确 定 分 析 的基 本要 求 , 个 分 析 易 发 生 故 2) 逐 障 的零 部件 。特别关 注 一些 关键 设 备 。 ( 绘 制 系统 图和 可靠性 框 图 。为 了便 于分析 , 3) 对 复 杂 系统 可 以 绘 制 各 功 能 子 系 统 相 结 合 的 系 统 图, 以表 示各 系统 问 的关 系 。从 系 统 图可 以继 续 画 出可 靠 性框 图 , 用来 表示 各单 元 式 串联 或 并联 , 以及
第 4 卷 第 9 1 期
21 0 2年 9月
化
工
技
术
与
开
发
Vo . 1 41
No9 .
Te h oo y & De e o c n lg v lpme to e c lI d sr n fCh mi a n u ty
S p2 2 e .01
F A在空压机使用 中的应用 ME
陆春 荣
( 南京 化工职业 技术学院 ,江苏 南京 2 04 10 8)
摘 要: 介绍 了故障类型和影 响风 险 ( ME F A)的评价理论和分析方法 。通过对空压机使用过程 中的各种潜在 的故障类型 、故障原 因 、后 果严重度 、发生概率及 风险等级进行逐个分析 ,并根据评价结果采取有针对性 的对 策
输入 和输 出情况 。
潜在失效模式及其原 因的分析方法 , 通过分析系统
中 每一 个 潜 在 的 故 障模 式 , 定 其 对 系统 所 产 生 的 确 影 响 , 而识 别 系统 中 的薄弱 环节 和关 键项 目, 从 为制 定 预 防措 施提 供 依据 , 源头 上消 除故 障 隐患 。 从
收稿 日期 : 0 20 .5 2 1—6 1
化
工
技
术
与
开
发
表 3 障检测 难度 ( D)
第 4 1卷
半 定量 的评 价 故 障的危 险等 级 , 采用 失效 引
起 危 害 程 度 的 全 局 值 可 以 由风 险 优 先 数 R N P
( i pi i n mbr 表述 。 r k r ry u e ) s ot
1 FE M A概 述
11 F A 的 内涵 . ME
F A实 际 上是 F ME MA ( 障类 型 分 析 ) F A 故 和 E ( 障 影 响分 析 ) 故 的组 合 … 。其 中 , 障 类 型分 析 是 故 指通 过 分 析 潜 在 的错 误 和 缺 陷 现象 , 找 安 全 生产 查 管 理 中任 何可 能 出现 的安 全 隐 患 ; 障影 响分 析是 故 指 通 过分 析该 失效 模 式对 系统 的安 全 和功 能 的影 响