极限配合及尺寸检测02
05第三章尺寸公差02
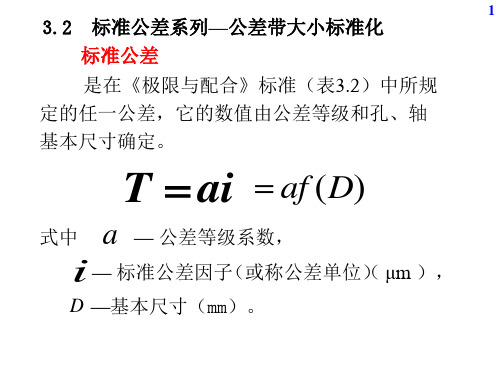
H 为 EI = 0,
h 为 es = 0。
14
IT (3) JS(js)-对称 JS( js) 2
15
若n为7~11级,Itn值为奇数时,
则
(4) J(j)-近似对称 对 J 仅保留 J6、J7、J8, 对 j 仅保留j5、j6、j7、j8。 J(j)将要由JS(js)代替。
(IT n) 1 JS(js ) 2
TD
(Td)
EI(ei)
例1 查表确定孔Φ30F8的极限偏差。 解:(1)查表确定F的基本偏差 由表 3.5得 EI= +20μm 由表 3.2 得 IT8 =33μm (2)ES=EI+IT8=+53μm
20
(3) 30F8 30
表3.5
0.053 0.020
例2 查表确定孔Φ25P7的极限偏差。 解:(1)由表 3.5 得 P—ZC,≤IT7的基本偏差为 在大于IT7的相应数值上增加一个Δ值。 ES≤7= ES>7+Δ = –22+8 = –14μm 由表 3.2 得 IT7 = 21μm 0.014 (2)EI=ES-IT7=-35μm (3) 25P7 25 0.035
2
i 0.45 D 0.001D
3
D>500~3150
I 0.004 D 2.1
i (I) 与零件尺寸的关 系见图2-10。 式中前者反映加工误差,
后者反映测量误差。
图3.10
3
二、公差等级及标准公差值的 计算公式( a ) 1.公差等级
公差等级用阿拉伯数字表示:
01,0,1,…,18 共 20 个等级。 精度越低。 常用的等级为1, 2,…,18共18个等级。
极限配合与测量技术第二章 2.4.1-3 几何公差的符号及代号

图2.24 零件的几何要素
零件的几何要素可分以下几类。
1.按存在的状态分类 (1)公称要素。
公称要素是指具有几何学意义的要素。
公称要素是没有任何误差的纯几何的点、线、面。
它是按设计要求,由图样上给定的点、线、面的理想状态。
线保持对称关系。
(2)基准要素。
基准要素是指用来确定被测要素的方向或(和)位置的要素。
理想基准要素称为基准。
在图2.25中,键槽中心平面对d1的轴线有对称度要求,因此d1的轴 线即为基准要素。
3.按几何特征分类 (1)组成要素。
组成要素是指构成零件轮廓的点、线或面。
图2.24所示的球面、圆锥面、圆柱面和棱锥面都是组成要素。 (2)导出要素。
如图2.27所示,
基准平面是处于实体之外与 基准组成要素相接触且符合最小 条件的理想平面。
这是因为几何误差对产品的功能要求,如零件的工作精度,固定 件的连接强度,密封性,活动件的运动平稳性、耐磨性以及寿命等都有 一定的影响。
所以为了满足零件的使用性能要求,保证工件的互换性和制造的
经济性,必须对工件的几何误差予以必要、合理的限制,即规定形
状和位置公差(简称几何公差)。
几何公差是用来控制几何误差的。
框格自左至右顺序标注以下内容,如图2.17~图2.21所示。
图2.17
图2.18
图2.19
图2.20
图2.21
3.基准符号 对有位置公差要求的零件,在图样上必须标明基准。
与被测要素相关的基准用一个大写字母表示。
字母标注在基准方格内,与一个涂黑的或空白的三角形相连以表 示基准,如图2.22和图2.23所示;
极限配合与技术测量
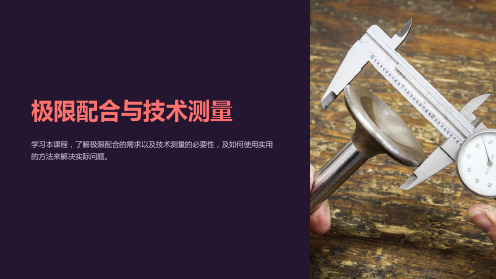
技术测量的重要性
高精度
数据处理
准确的测量可以保证产品符合制 定的标准,促进企业的健康发展。
数据化的处理可以将多个生产阶 段的数据及时记录,方便后续的 跟踪和纠正。
成本控制
技术测量的数据及时传递,可以 在生产过程中减少浪费,降低成 本。
常用极限配合技术测量方法
1
百分位法
通过判断零件的实际尺寸与理论尺寸之
极限配合与技术测量
学习本课程,了解极限配合的需求以及技术测量的必要性,及如何使用实用 的方法来解决实际问题。
什么是极限配合?
定义
极限配合指大量生产的零件之间尺寸的范围,以及它们之间最小的空隙量,以保证它们可以 组装在一起而无需调整或切削。
意义
实现极限配合可以保证生产出的商品符合标准,减少零部件之间摩擦和磨损,增加零部件的 耐用度和工作效率。
2 案例2
一家电子设备制造商使用测量仪器的方法检测了微处理器的每个焊点的尺寸,从而确保 其电气特性符合规格要求。
影响极限配合与技术测量的因素
材料
材料的特性,如热膨胀系数、 硬度等会影响到零件的尺寸精 度。
生产工艺
生产过程中的温度、压力、加 工精度等因素会影响到零件尺 寸和配合的实际结果。
人为操作因素
统计学检验法
2
间的差距 如何控制?而确定配合范围。
根据正态分布等统计规律,确定配合的
上下限。
3
测量仪器法
使用各种测量仪器,如卡尺、测微计等, 进行精确测量并以此确定配合范围。
极限配合与技术测量的案例
1 案例1
一家汽车配件厂商在生产刹车室的过程中使用百分位法确定了配件之间的空隙量,在几 次生产批次的测试中得到了一致的结果,大大减少了调整和切削的时间。
极限配合与技术测量第二章

3)过渡配合 (1)孔的实际尺寸可能大于或小于轴的实际尺寸, 只不过相差很小。 (2)孔、轴配合时可能存在间隙或过盈。 (3)孔的公差带与轴的公差带相互交叠。 5、配合公差带图 配合公差带图的画法与尺寸公差带图的画法相 似,也是按一定比例将极限间隙或极限过盈放大 后画在配合公差带图上。先画出零线代表基本尺 寸,零线的上方为正,代表极限间隙;下方为负, 代表极限过盈。用极限间隙和极限过盈两条直线 所限定的区域,就是配合公差带。
图2-1中方形孔和键槽两个非圆柱形内表 面都视为孔。因为方形孔是由两个单一尺寸 (长度和宽度)确定的;键槽是由两个平行平 面所构成的内表面,也是孔,它是由单一尺寸 12确定。
孔的特点: (1)装配后孔是包容面。 (2)加工过程中,零件实体材料变小,而 孔的尺寸由小变大。 2、轴 指工件的圆柱形外表面,也包括非圆柱形外 表面(由二平行平面或切面形成的被包容面)。
图2-4尺寸的偏差与公差 Th=Lmax-Lmin=ES-EI Ts=lmax-lmin=es-ei (P8例2)
公差和极限偏差是两个不同的概念。公差大小 是决定允许尺寸的变动范围,公差值是绝对值。 极限偏差决定极限尺寸相对其基本尺寸的位置 (在共差带图中),极限偏差值可以是正值、负 值或零。 2、尺寸公差带 表示零件的尺寸相对其基础尺寸所允许的变动 范围,称为公差带。用图表示的公差带,称为公 差带图。 在公差带图中,零线是确定基本偏差的一条基 准线,极限偏差位于零线上方,表示偏差为正; 位于下方,表示偏差为负;当与零线重合时,表 示偏差为零。
现将例3、5、8的计算结果按250:1的比例画 出配合公差带图,如图2-12所示。
6、配合性质的判断 在有基本偏差代号的尺寸标注中,可由基本偏 差代号和公差带图来判断其配合性质。但当尺寸 中只标注偏差的大小时,就要依据极限偏差的大 小来判断配合性质。在间隙配合中,孔的下偏差 (EI)大于或等于轴的上偏差(es);过盈配合 中,轴的下偏差(ei)大于或等于孔的上偏差 (ES)。即 EI≥es时为间隙配合 ei≥ES时为过盈配合 以上两条同时不成立,则为过渡配合。 (P16 例13)
第二章《极限配合与技术测量》试题
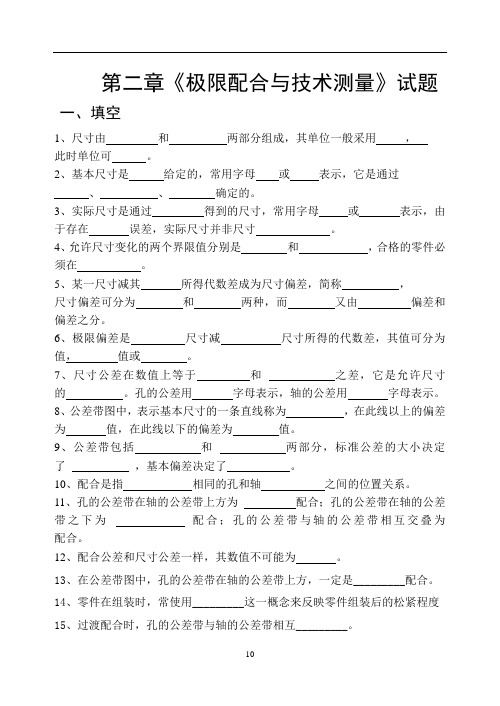
第二章《极限配合与技术测量》试题一、填空1、尺寸由和两部分组成,其单位一般采用,此时单位可。
2、基本尺寸是给定的,常用字母或表示,它是通过、、确定的。
3、实际尺寸是通过得到的尺寸,常用字母或表示,由于存在误差,实际尺寸并非尺寸。
4、允许尺寸变化的两个界限值分别是和,合格的零件必须在。
5、某一尺寸减其所得代数差成为尺寸偏差,简称,尺寸偏差可分为和两种,而又由偏差和偏差之分。
6、极限偏差是尺寸减尺寸所得的代数差,其值可分为值,值或。
7、尺寸公差在数值上等于和之差,它是允许尺寸的。
孔的公差用字母表示,轴的公差用字母表示。
8、公差带图中,表示基本尺寸的一条直线称为,在此线以上的偏差为值,在此线以下的偏差为值。
9、公差带包括和两部分,标准公差的大小决定了,基本偏差决定了。
10、配合是指相同的孔和轴之间的位置关系。
11、孔的公差带在轴的公差带上方为配合;孔的公差带在轴的公差带之下为配合;孔的公差带与轴的公差带相互交叠为配合。
12、配合公差和尺寸公差一样,其数值不可能为。
13、在公差带图中,孔的公差带在轴的公差带上方,一定是_________配合。
14、零件在组装时,常使用_________这一概念来反映零件组装后的松紧程度15、过渡配合时,孔的公差带与轴的公差带相互_________。
16、过盈配合中,除零过盈外,孔的实际尺寸永远_______轴的实际尺寸。
17、ES<ei时,一定是________配合.18、国家标准规定:标准公差等级有________个。
标准公差用_______表示。
19、在相同的尺寸段中,IT5比IT8公差数值____(大,小)。
20、国家标准规定:孔和轴各有_______种公差带位置。
21、基本偏差为H的孔,其下偏差是________。
22、Ф60H8/f8是_________(间隙、过盈、过渡)配合。
23、Ф20F7的含义是________________________________________。
极限配合与技术测量基础第2章技术测量基本知识及计量器具的使用
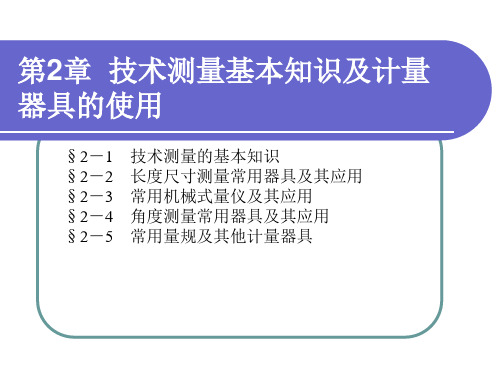
1.从尺身上读出游标零刻度线前指示的整度数。 2.判断游标上第n格的刻线与尺身上的刻线对齐,确定“分”的数值,即 n×2′。 3.把两者相加就是被测角度的数值。
3 .测量范围
(1)0°~50°角
(2)50°~140°角
水平仪——用来测量被测平面相对水平面的微小角度 的计量器具。
电子式水平仪 水准式水平仪:条式、框式和合像水平仪
条式水平仪
框式水平仪
水平仪的原理 相对倾角:α=4″×n
【例】用一分度值为0.02mm/1000m(4″)的水平仪测量 一长度为600mm的导轨工作面的倾斜程度,测量时水平仪 的气泡移动了3格,问该的导轨工作面相对水平面倾斜了多 少?
测量四要素:
测量对象(长度、角度、表面质量等) 计量单位 测量方法(指计量器具和测量条件的综合) 测量精度(指测量结果与真值的符合程度)
一、计量单位 二、测量方法 三、测量精度与测量误差
一、计量单位
二、测量方法
1.计量器具的分类 2.测量方法的分类
1.计量器具的分类 (1)量具
(2)量规
百分表的分度值为0.01mm。
二、百分表的分度原理与读数方法
百分表的测量杆移动1 mm,通过齿轮传动系统使大 指针回转一周。刻度盘沿圆周刻有100个刻度,当指针转 过1格时,表示所测量的尺寸变化为1/100=0.01 mm,所 以百分表的分度值为0.01 mm。
如上页图所示的百分表,示值范围为0~10 mm,分度 值为0.01 mm。当大指针沿大刻度盘转动一周时,小指针 转动1格,测量头移动1 mm。因此,小刻度盘的1格分度值 为1 mm。读数时,先读小刻度盘的格数n,再读大刻度盘 的格数m,则测量值为(n×1+m×0.01)mm。
模块一 极限配合与尺寸检测
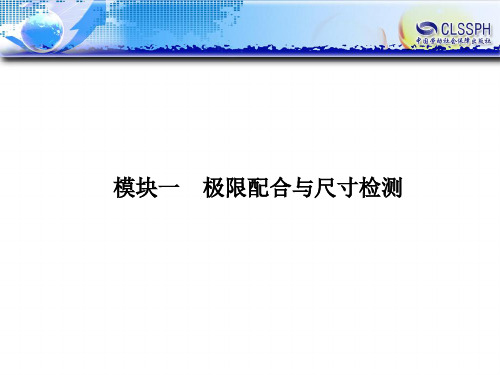
分度值0.02㎜
分度值0.05㎜
分度值0.10㎜
课题一 尺寸公差与检测
2.读取游标卡尺的示值 (1)读主尺 (2)读游标 (3)计算尺寸数值
3.选择游标卡尺的规格 分度值 0.02㎜,测量范围 0~150㎜。
课题一 尺寸公差与检测 二、用游标卡尺测量轴套的尺寸
EI=Dlow-D; ei=dlow-d 尺寸φ40㎜的上极限尺寸为:
dup =d + es=40+( + 0.052)=40.052㎜ 尺寸φ40㎜的下极限尺寸为: dlow =d+ei=40+(-0.010)=39.990㎜
课题一 尺寸公差与检测 4.尺寸公差
尺寸公差(简称公差)是允许 尺寸的变动量,等于上极限尺寸减 其下极限尺寸之差,或上极限偏差 减下极限偏差之差。
+ 0 -
0.052 0.010㎜
0.052
0.010
φ40
课题一 尺寸公差与检测
2.φ25
0.052
0
㎜
+ 0 -
0.052
3.φ45
0.087 0.025
㎜
+ 0 -
φ25
0.087
0.025
φ45
课题一 尺寸公差与检测
一、孔的定义
孔通常指工件的圆柱形内表 面,也包括非圆柱形内表面。
二、轴的定义
轴通常指工件的圆柱形外表 面,也包括非圆柱形外表面 。
孔为包容面,轴为被包容面
课题一 尺寸公差与检测
子课题2 用游标卡尺检测工件
1.了解游标卡尺的结构,掌握其读数方法。 2.掌握游标卡尺的使用方法。 3.掌握使用游标卡尺的注意事项。 4.了解游标卡尺的示值误差。 5.了解其他类型的游标卡尺。
公差与配合极限配合及尺寸检测

合适的公差和配合类型可以避免零件在 使用中出现过紧或过松的问题
极限配合的定义和特点
上下公差限
极限配合通过定义上下公差限来确定允许的尺寸范围
易于检验和选择
极限配合的标准化使得检验和选择变得简单方便
满足特定的装配要求
极限配合可以根据装配要求来选择合适的配合类型
尺寸检测的目的和方法
公差与配合极限配合及尺 寸检测
公差是机械工程中非常重要的概念,可以确保零件的互换性和装配性。它有 不同的种类和表示方法,与配合的关系密切。尺寸检测通过使用不同的工具 和方法来确保零件尺寸的准确性。
公差的种类和表示方法
线性公差
例如长度、直径等
形状公差
例如平面度、圆度等
角度公差
例如倾斜度、角度等
位置公差
1 确保质量和精度
尺寸检测是为了确保零件 的质量和精度达到要求
2 验证设计规范
通过与设计规范比对,确 认尺寸是否符合要求
3 检查制造工艺
可通过尺寸检测检查是否 存在制造工艺上的问题
常用的尺寸检测工具
千分尺
用于测量直径、厚度等尺寸
卡尺
用于测量长度、外径等尺寸
量块
用于校准和检验其它测量工具
例如同轴度、平行度等
配合的基本概念和分类
紧配合
零件间的配合紧密,需要施加力 来组装和拆卸
过渡配合
零件间的配合有一定的间隙,便 于组装和拆卸
松配合
零件间的配合有明显的间隙,便 于组装和拆卸
公差与配合的关系
1பைடு நூலகம்
配合关系决定装配方式
2
根据配合类型,可以决定是使用冷装配
还是热装配等方式
3
公差限制配合尺寸
极限配合与技术测量第二章课后习题答案

第二章孔、轴尺寸的极限与配合2-1什么叫基本尺寸、实际尺寸和极限尺寸?答:基本尺寸:设计时给定的尺寸。
实际尺寸:通过测量得到的尺寸。
极限尺寸:允许尺寸变化的两个极端尺寸。
2-2什么叫尺寸偏差、极限偏差?答:尺寸偏差:某一尺寸(实际尺寸、极限尺寸)减去其基本尺寸所得的代数差。
极限偏差:上、下偏差统称为极限偏差。
2-3什么叫尺寸公差?为什么尺寸公差必须大于零?答:尺寸公差就是允许尺寸的变动范围,大小上等于最大极限尺寸与最小极限尺寸之差;因为最大极限尺寸大于且不等于最小极限尺寸,所以,公差必须大于零。
2-4用500 :1的放大比例画出孔φ60+0.0300和轴φ60-0.010-0.035的公差带图。
答:按比例画公差带图时,只用对极限偏差进行放大就可以了,所以,ES=+0.030 0.030×500=15 EI=0es=-0.010 -0.010×500=5 ei=-0.035 -0.035×500=-17.5画图步骤:1)画零线,画基本尺寸线;2)画极限偏差线,标注极限偏差;2-5有一孔φ80+0.032,试计算L MAX 、L MIN和T h答:L MAX =L+ES=80+0.032=80.032;L MIN=L+EI=80+0=80;Th=ES-EI=0.0322-6 有一轴φ45+0.012-0.007,试计算lmax、lmin和Ts答:lmax=l+es=45+0.012=45.012Lmin=l+ei=45+(-0.007)=44.093Ts=es-ei=0.012-(-0.007)=0.0192-7什么是配合?配合有哪三种?答:配合:指基本尺寸相同、相互结合的孔和轴公差带之间的位置关系。
配合分为间隙配合、过渡配合和过盈配合三种。
2-8什么叫间隙配合、过盈配合和过渡配合,其形成条件是什么,配合特点是什么?答:间隙配合:孔的尺寸减去相配合轴的尺寸之差为正值,称为间隙配合。
极限配合及技术测量习题答案
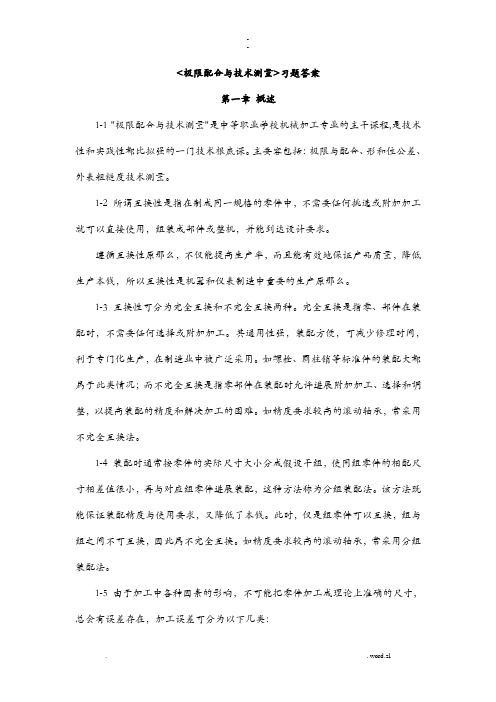
<极限配合与技术测量>习题答案第一章概述1-1 "极限配合与技术测量"是中等职业学校机械加工专业的主干课程,是技术性和实践性都比拟强的一门技术根底课。
主要容包括:极限与配合、形和位公差、外表粗糙度技术测量。
1-2 所谓互换性是指在制成同一规格的零件中,不需要任何挑选或附加加工就可以直接使用,组装成部件或整机,并能到达设计要求。
遵循互换性原那么,不仅能提高生产率,而且能有效地保证产品质量,降低生产本钱,所以互换性是机器和仪表制造中重要的生产原那么。
1-3 互换性可分为完全互换和不完全互换两种。
完全互换是指零、部件在装配时,不需要任何选择或附加加工。
其通用性强,装配方便,可减少修理时间,利于专门化生产,在制造业中被广泛采用。
如螺栓、圆柱销等标准件的装配大都属于此类情况;而不完全互换是指零部件在装配时允许进展附加加工、选择和调整,以提高装配的精度和解决加工的困难。
如精度要求较高的滚动轴承,常采用不完全互换法。
1-4 装配时通常按零件的实际尺寸大小分成假设干组,使同组零件的相配尺寸相差值很小,再与对应组零件进展装配,这种方法称为分组装配法。
该方法既能保证装配精度与使用要求,又降低了本钱。
此时,仅是组零件可以互换,组与组之间不可互换,因此属不完全互换。
如精度要求较高的滚动轴承,常采用分组装配法。
1-5 由于加工中各种因素的影响,不可能把零件加工成理论上准确的尺寸,总会有误差存在,加工误差可分为以下几类:〔1〕尺寸误差:指加工后零件某处的实际尺寸对理想尺寸之差的偏差值。
如图纸上标注的尺寸为30mm,加工后的尺寸为29.98mm,那么尺寸误差为0.02mm。
〔2〕形状误差:指加工后零件上实际的线或面对理想形状的偏差值。
如轴的横截面为圆形,加工后实际形状为椭圆形,这就是形状误差。
〔3〕位置误差:指实际零件形体上的点、线、面对各自要求的理想方向和理想位置的偏差量。
理想方向和理想位置指几何意义上的绝对平行、垂直、同轴及绝对准确的角度和位置关系。
第2章尺寸的公差、配合与检测

例2-1 查表确定φ35j6、φ72K8、φ90R7的基本偏差与另 一极限偏差。
解: φ 35j6:查表3-1 IT6时,Td = 16μ m 查表3-4 ei = - 5μ m,则es = ei + T d = +11μ m 即φ 35j6 φ 35 mm φ 72K8:查表3-1 IT8时,TD = 46μ m 查表3-5 ES= - 2μ m +Δ = (-2+16)μ m=+14μ m EI = ES - T D = (14 - 46)μ m = - 32μ m 即φ 72K8 φ 72 mm φ 90R7:查表2-3 IT7时,TD =35μ m 查表2-5 ES = - 51μm +Δ=(-15+13)μm=- 38μm EI =ES -TD =(-38-35)μm= -73μm 即φ90R7 φ90 mm
尺寸、基本尺寸、实际尺寸
Φ 25.1
Φ 24.9
φ 25
φ 25
孔
孔
Φ 24.9
孔
Φ 25.1
轴
轴
轴
ቤተ መጻሕፍቲ ባይዱ
实际尺寸 基本尺寸 实际尺寸
实际尺寸 基本尺寸
实际尺寸
Dmin
D 孔 Dmax 孔 dmin 轴 d dmax 轴
孔
极限尺寸
轴
尺寸偏差(简称偏差)
尺寸偏差是指某一尺寸减去基本尺寸所得的 代数差。
一般、常用和优先的公差与配合
1.尺寸公差带 国家标准: 20个公差等级、28种基本偏差
孔公差带: 20×27+3 = 543 (J6、J7、J8)
轴公差带: 20×27+4 = 544 (j5、j6、j7、j8)
项目二极限配合与尺寸检测

如φ50H8/f7或φ5寸为
φ50mm,孔的公差带代号为H8,轴的公差带代号为f7,为
【例2-3-1】 解读标注φ25H8/f7mm,并画出公差带图解。 解:公称尺寸为φ25mm; 基孔制,间隙配合; 孔公差等级为8级,轴公差等级为7级; 查标准公差表得 IT8=33μm IT7=21μm 基准孔 EI=0 ES= EI+ IT=+0.033mm 配合轴 查极限偏差表得:es=-20μm=-0.020mm ei= es-IT0.041mm 公差Th=0.033mm Ts =0.021mm Tf=Th+ Ts=0.054mm 极限盈隙 Xmax= ES - ei =+0.074mm Xmin= EI- es=+0.020mm
4.配合的类型
过盈配合
配合类型
间隙配合
过渡配合
(1)间隙配合
具有间隙的配合(包括间隙为零)称为间隙配合。当配合为 间隙配合时,孔的公差带在轴的公差带上方
最大间隙 Xmax=Dmax-dmin=ES-ei 最小间隙 Xmin=Dmin-dmax=EI-es 配合公差 Tf=︱Xmax- Xmin︱=Th+Ts
3.极限偏差表
查表:
由公称尺寸查行,由基本偏差代号和公差等级查列,
行与列相交处的框格有上下两个偏差数值,上方的为上极 限偏差,下方的为下极限偏差。
五、测量方法和工具
1.外径千分尺
2.千分尺的读数方法:
(1)先从微分筒的边缘向左看固定套管上距微分筒边缘最近的刻线, 从固定套管中线上侧的刻度读出整数,从中线下侧的刻度读出 0.5mm的小数; (2)再从微分筒上找到与固定套管中线对齐的刻线,将此刻线数乘以 0.01mm就是小于0.5mm的小数部分的读数,最后把以上几部分相加 即为测量值。
极限配合与技术测量项目二任务三
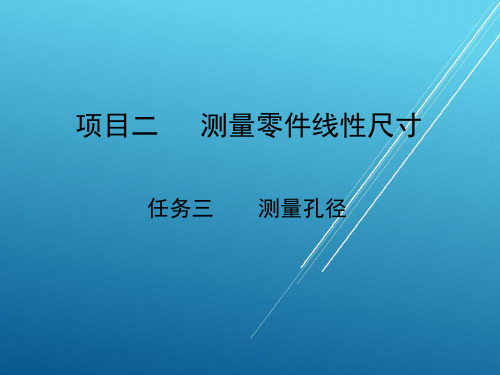
一、常用孔径测量量具
3.内径百分表 内径百分表根据测量架的不同,测量范围有6~10mm、10~
18mm、18~35mm、35~50mm、50~100mm、100~160mm、160~ 250mm、250~450mm等。
10-18mm
18-35mm
35-50mm
50-160mm
一、常用孔径测量量具
一、常用孔径测量量具
①内测千分尺的读数方法与外径千分尺相同,但它的测量方 向和读数方向都与外径千分尺相反。所以,在固定套管上读毫米 整数和半毫米数、在微分筒上读小数时,留心不要读错。
②千分尺是精密量具,使用时要轻拿轻放,用完之后在裸露 部位涂上防护油, 并放入专用盒内,放在干燥通风的地方。
③测量时不能用力转动微分筒,以免影响测量精度。 ④微分筒移动不要超出量程后0.5mm,以免损坏千分尺和它的 精度。 ⑤不要试图拆下千分尺的零部件以免造成损坏而不能使用。 ⑥两测量砧上有硬质合金,测量时不能过多地调整千分尺的 位置,以免损坏被测表面和引起测量不正确。
一、常用孔径测量量具
内测千分尺的使用
1)测量前:清洁测量面,用检定合格 的标准环规校对零位。 2)测量时:先将两个测量爪测量面之 间的距离调整得比被测内尺寸稍小, 然后用左手扶住左边固定测量爪,并 抵在被测表面上不动。 3)读数:右手按顺时针方向慢慢转动 测力装置,并轻微游动内测千分尺, 找出最大尺寸(测内孔时寻找最大尺 寸,测槽宽时寻找最小尺寸)。然后 拧紧锁紧装置(取出千分尺)并读数。
一、常用孔径测量量具
(2) 三爪内径千分尺
使用注意事项
1)选择与被测要素尺寸相适应的三爪内径千分尺, 在使用前用校对环规校对零位。
2)被测表面必须擦拭干净。 3)将内径千分尺尺寸调整至比被测要素尺寸 小0.5~1mm,然后将三爪伸入被测要素内。
极限配合第二章

第二章技术测量的基本知识及常用计量器具练习题一、选择题1. 检验与测量相比,其最主要的特点是()A. 检验适合大批量生产B. 检验所使用的计量器具比较简单C. 检验只判定零件的合格性,而无须得出具体量值D. 检验的精度比较低答案:C2. 关于量具下列说法错误的是()A. 量具的结构一般比较简单B. 量具可分为标准量具和通用量具两种C. 量具没有传动放大系统D. 量具只能与其他计量器具同时使用答案:D3. 下列计量器具中不属于通用量具的是()A. 钢直尺B. 量块C. 游标卡尺D. 千分尺答案:B4. 关于间接测量法,下列说法中错误的是()A. 测量的是与被测尺寸有一定函数关系的其他尺寸B. 计量器具的测量装置不直接和被测工件表面接触C. 必须通过计算获得被测尺寸的量值D. 用于不便直接测量的场合答案:B5. 关于相对测量法下列说法中正确的是()A. 相对测量的精度一般比较低B. 相对测量时只需用量仪即可C. 计量器具的测量装置不直接和被测工件表面接触D. 计量器具所读取的是被测几何量与标准量的偏差答案:B6. 用游标卡尺测量工件的轴径尺寸属于()A. 直接测量、绝对测量B. 直接测量、相对测量C. 间接测量、绝对测量D. 间接测量、相对测量答案:A7. 计量器具能准确读出的最小单位数值就是计量器具的()A. 校正值B. 示值误差C. 分度值D. 刻度间距答案:C8. 刻度间距和分度值之间的关系是()A. 分度值越大,则刻度间距越大B. 分度值越小,则刻度间距越大C. 分度值的大小和刻度间距的大小没有直接的关系D. 分度值越大与刻度间距成反比关系答案:C9. 下列各项中,不属于方法误差的是()A. 计算公式不准确B. 操作者看错读数C. 测量方法选择不当D. 工件安装定位不准确答案:B10. 读数值为0.02mm的游标卡尺,当游标卡尺的读数为42.18mm时,游标上第9 格刻线应对齐尺身上的第()mm刻线。
- 1、下载文档前请自行甄别文档内容的完整性,平台不提供额外的编辑、内容补充、找答案等附加服务。
- 2、"仅部分预览"的文档,不可在线预览部分如存在完整性等问题,可反馈申请退款(可完整预览的文档不适用该条件!)。
- 3、如文档侵犯您的权益,请联系客服反馈,我们会尽快为您处理(人工客服工作时间:9:00-18:30)。
3.画公差带图的注意点: ①.作图比例基本一致; ②.单位 µm 、mm均可,单位为mm时 省略不标注; ③.基本尺寸相同的孔、轴公差带才能画 在一张图上; ④.同一公差带图中,孔、轴公差带沿零 线方向的长度任意(可对齐,可错 开),但长度相等; ⑤.孔、轴公差带的剖面线方向相反,且 疏密程度不同,一般是孔疏、轴密。
4.比较公差与偏差
公差与偏差是两个不同的概念; 公差表示制造精度的要求,反映加工的 难易程度; 偏差表示与基本尺寸远离程度,它表示 公差带的位置,影响配合的松紧程度。
三.标准公差系列 1.标准公差:用以确定公差带大小的公差。 对于一定的基本尺寸,公差等级高,标 准公差值愈小,尺寸的精确程度愈高。
由于形状误差,同一表面不同部位的实际尺寸往 往不相等,因此要用二点法进行测量。 见下页图
尺寸合格条件:
Dmin≤Da≤Dmax dmin≤da≤dmax
最大极限尺寸 最小极限尺寸 公差 下偏差 上偏差 基本尺寸
孔
图2-1
最小极限尺寸
最大极限尺寸 基本尺寸 零线
轴
公差 下偏差 上偏差
4.极限尺寸:一个孔或轴允许的尺寸的两个 极端。是以基本尺寸为基数来确定的。实际 尺寸应位于其中,也可达到极限尺寸。 ①孔或轴允许的最大尺寸称为最大极限尺寸; ②孔或轴允许的最小尺寸称为最小极限尺寸。 ③孔和轴的最大极限尺寸分别用Dmax和 dmax表示,最小极限尺寸分别用Dmin和 dmin表示。 ④极限尺寸可以大于、等于、小于基本尺寸。 所以基本尺寸可以在极限尺寸所确定的范围 内,也可以在极限尺寸所确定的范围外(见 下页)。
插图P17表中0.02精度图 P21图2-9b
三.游标卡尺的使用方法 测量小工件:左手拿工件,右手拿卡尺; 测量大工件:工件固定,左手握住主尺量 爪,右手握住主尺并推动活动量爪靠近被 测零件表面 1.测量外形尺寸时,应先把量爪张开得比被 测尺寸稍大,再把固定测量爪(左边一爪) 与被测表面靠上,然后慢慢推动尺框(带 游标的框),使活动测量爪轻轻地接触被 测表面,并稍微游动一下活动测量爪,以 便找出最小尺寸部位,可获得正确的测量
插图P13图2-3
3.孔和轴的区别 ①装配关系:孔是包容面,轴是被包容面; ②加工过程:孔的尺寸由小变大,轴的尺寸 由大变小。 二.相关尺寸的概念和符合 1.尺寸:用特定单位(工程为mm)表示线 性几何量(或长度)的大小的数值。如直 径、宽度、高度、中心距等。 注:为了简化技术图样,便于直观看图,规 定技术图样上的尺寸数值的特定单位为 mm时省略标注。
模块二 极限配合及尺寸检测
在现代化的大量或成批生产中, 要求互相装配的零件或部件都要符合 互换性原则。例如,从一批规格为 φ10的油杯(下页图)中任取一个装 入尾架端盖的油杯孔中,都能使油杯 顺利装入,并能使它们紧密结合,就 两者的顺利结合而言,油杯和端盖都 具有互换性。
任务1 认识孔、轴的尺寸 一.孔、轴的概念 1.孔:通常指工件的圆柱形内表面,也 包括非圆柱形内表面(由两平行平面 或切面形成的包容面)。 2.轴:通常指工件的圆柱形外表面,也 包括非圆柱形外表面(由两平行平面 或切面形成的被包容面)。
②计算: 上偏差=最大极限尺寸-基本尺寸 下偏差=最小极限尺寸-基本尺寸 孔的上偏差:ES=Dmax-D 孔的下偏差:EI =Dmin-D 轴的上偏差:es =dmax-d 轴的下偏差:ei =dmin- d ③极限偏差的标注形式:基本尺寸右上 角为上偏差,基本尺寸右下角为下偏
④极限偏差的有以下六种形式:P23
5.最大实体尺寸:孔或轴具有允许材料 量为最多时状态(最大实体状态,简称 MMC)下的极限尺寸。孔和轴的最大实 体尺寸分别用DM和dM表示。 6.最小实体尺寸 孔或轴具有允许材料量 为最少时状态(最小实体状态,简称LMC) 下的极限尺寸。孔和轴的最小实体尺寸分 别用DL和dL表示。极限尺寸与实体尺寸 有如下:
四.使用千分尺的注意事项 1.使用前根据被测工件的尺寸,选择相 应测量范围的千分尺。 2.测量前应校正零位 。 3.测量时,千分尺测量轴的中心线应与 被测尺寸长度方向一致,不要倾斜。 4.不能在工件转动或加工时测量。 5.不准用千分尺测量粗糙表面。 6.读数值时应注意半毫米数值刻线是否 露出,小心错读一圈。
五.用千分尺对零件的实际尺寸进行测量
2.73mm 教材P28图2-13读数
六.其他千分尺介绍
教材P26、P27
任务5 认识尺寸公差 一.尺寸公差的概念、符号和相关计算 1.尺寸公差(TD、Td): 定义:允许尺寸的变动量。 在零件的加工过程中,不可能把零 件的尺寸做得绝对准确。为了保证互 换性,必须将零件尺寸的加工误差限 制在一定的范围内,规定出尺寸允许 的变动量,这个变动量就是尺寸公差, 简称公差。
五.用游标卡尺对零件的实际尺寸进行测量
插图教材P20图2-8
六.其他游标卡尺介绍
教材P19、P20表2-2
任务3 识读偏差 一.偏差的概念、符号 1.尺寸偏差:某一尺寸减去其基本尺寸所得 的代数差,是指偏离基本尺寸大小的数值, 包括极限偏差和实际偏差。 注:偏差有正、负和零。 2.极限偏差(ES、EI、es、ei): ①定义:极限尺寸减去其基本尺寸所得的代 数差。 极限偏差是上、下偏差的统称。
2.尺寸公差带图的作图步骤: ①.画一条水平直线(零线),用来表示 基本尺寸,以它为基准确定极限偏差 和公差。在其左端标上“+”,“0”和 “-”号;在其左端下方画有一带箭头的 尺寸线,并标上基本尺寸值。 ②.将公差和极限偏差部分一般按500: 1的放大比例画出,正偏差位于零线上 方,负偏差位于零线下方,零偏差与 零线重合。并标出孔、轴上、下偏差 值及其他要求标注的数值和单位。
3. 测量沟槽宽度时,卡尺的操作方法与 测量孔径相似,测量爪的位置也应摆 正,要垂直于槽壁。 4.测量深度时,应使游标卡尺的尺身下 端面与被测件的顶面贴合,向下推动 深度尺,使之轻轻接触被测底面。 5.测量孔中心与侧平面之间的距离与 测 量外形尺寸相似。 6.测量两孔的中心距与测量内孔相似。
四.使用游标卡尺的注意事项 1.测量前应先用软布或软纸檫干净两量 爪的测量面,合拢量爪,检查光标零 线是否与主尺零线对正(调零); 2.测量前应檫干净零件被测量表面; 3.不准用卡尺测量毛坯表面; 4.读数时视线垂直于刻线处的尺寸表面, 不得歪斜。
二.千分尺的读数方法: ①先读出固定套筒上露在外面的刻线数 值,中线之上为整毫米数值,中线之 下为半毫米数值。 ②再读出在微分筒上从零开始第x条刻线 与固定套筒上基准线对齐的数值,x乘 以其测量精度值0.01mm即为读数不 足0.5mm的小数部分。
③得出被测尺寸—把上面两次读数的整 数部分和小数部分相加,就是被测实 际尺寸。 三.千分尺的使用方法 1.选规格:根据被测工件尺寸大小,选 用合适规格的千分尺。 2.擦干净:用软布或软纸檫干净测砧、 活动测量杆端面和工件的被测表面。
3.分类:游标卡尺按测量精度分为: 0.01mm、0.05mm、0.02mm三种, 其中0.02mm精度的最为常用。 4.游标卡尺的刻线原理(以0.02mm精 度为例)(见下页图):尺身每小格 为1mm,游标刻线共50小格,这50 小格的长度为49mm,即游标每小格 为49/50=0.98mm,尺身与游标每 小格相差1-0.98=0.02mm。
插图P16表中0.02MM精度
二.游标卡尺的读数方法 1.先读整数(尺身上的数,每小格1mm)— 看游标零线的左边,尺身上最靠近的一条 刻线的数值,读出被测尺寸的整数部分; 2.再读小数(游标上的数)—看游标零线的 右边,读出游标第几条刻线与尺身刻线对 齐,读出被测尺寸的小数部分(即游标读 数值乘其对齐刻线的顺序数); 3.得出被测尺寸—把上面两次读数的整数部 分和小数部分相加,就是卡尺的所测尺寸 。
二.极限偏差的相关计算 例:(孔)计算其极限尺寸及其偏差。 基本尺寸D=φ50 最大极限尺寸 Dmax=50+0.042=50.042mm 最小极限尺寸 Dmin=50+0.015=50.015mm 上偏差ES=+0.042mm 下偏差EI=+0.015mm
任务4 使用千分尺(以外径千分尺为例) 一.千分尺的刻线原理 1.定义:是利用螺旋副的运动原理进行测量 和读数的测微量具。 2.优点:使用普遍,是一种重要的精密测量 器具。它具有体积小、坚固耐用、测量准 确度较高、使用方便、容易调整以及测力 恒定。 3.测量范围:可以测量工件的各种外形尺寸, 如长度、厚度、外径以及凸肩板厚或壁厚 等。
2.基本尺寸(D,d):设计时给定的尺寸,通过它 并应用上下偏差可算出极限尺寸的尺寸(如图21)。它可以是一个整数或一个小数值(见上图)。
3.实际尺寸(Da,da):通过测量获得的某 一孔、轴的尺寸。它零件上实际存在的尺寸。 孔和轴的实际尺寸分别用Da和da表示。 由于测量误差,实际尺寸不一定是尺寸的真值。
4.精度:0.01mm。 5.规格:0~25mm、 25~50mm、 50~75mm、 75~100mm等。 6.结构型式:
7.千分尺的刻线原理 测微螺杆右端螺纹螺距为0.5mm, 当微分筒转一周时,就带动测微螺杆 轴向移动一个螺距0.5mm。由于固定 套筒上的刻线间距每小格为0.5mm, 微分筒圆锥面上刻有50小格的圆周等 分刻线,因此当微分筒转过1小格时, 就代表测微螺杆轴线移动0.01mm。
3.校正零位:在千分尺两测量面之间放 入校对棒,检查接触情况,不得有明 显的漏光现象。同时检查微分筒与固 定套筒的零刻线是否对齐。 4.测量:测量时,先转动微分筒,使测 微螺杆端面逐渐接近工件被测表面, 再转动棘轮,直到棘轮打滑并发出 “咔卡”声,表明两测量端面与工件 刚好贴合或相切,然后读出测量尺寸 值。
注:从上图的 六种形式可以看出 a.上、下偏差的“小数点”应对齐; b.偏差的“0”不能省略; c.小数位数相同(不够的添0); d.上偏差﹥下偏差; e.偏差的“+”、“-”号不能省略。