生产效率改善技巧-设备综合效率(OEE)改善
设备综合效率管理(OEE)
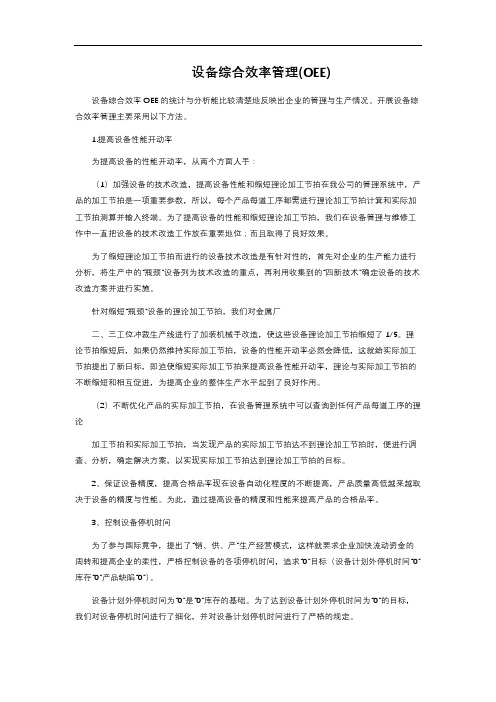
设备综合效率管理(OEE)设备综合效率OEE的统计与分析能比较清楚地反映出企业的管理与生产情况。
开展设备综合效率管理主要采用以下方法。
1.提高设备性能开动率为提高设备的性能开动率,从两个方面人手:(1)加强设备的技术改造,提高设备性能和缩短理论加工节拍在我公司的管理系统中,产品的加工节拍是一项重要参数,所以,每个产品每道工序都需进行理论加工节拍计箕和实际加工节拍测算并输入终端。
为了提高设备的性能和缩短理论加工节拍,我们在设备管理与维修工作中一直把设备的技术改造工作放在重要地位;而且取得了良好效果。
为了缩短理论加工节拍而进行的设备技术改造是有针对性的,首先对企业的生产能力进行分析,将生产中的“瓶颈”设备列为技术改造的重点,再利用收集到的“四新技术”确定设备的技术改造方案并进行实施。
针对缩短“瓶颈”设备的理论加工节拍,我们对金属厂二、三工位冲裁生产线进行了加装机械手改造,使这些设备理论加工节拍缩短了1/5。
理论节拍缩短后,如果仍然维持实际加工节拍,设备的性能开动率必然会降低,这就给实际加工节拍提出了新日标,即迫使缩短实际加工节拍来提高设备性能开动率,理论与实际加工节拍的不断缩短和相互促进,为提高企业的整体生产水平起到了良好作用。
(2)不断优化产品的实际加工节拍,在设备管理系统中可以查询到任何产品每道工序的理论加工节拍和实际加工节拍,当发现产品的实际加工节拍达不到理论加工节拍时,便进行调查、分析,确定解决方案,以实现实际加工节拍达到理论加工节拍的目标。
2、保证设备精度,提高合格品率现在设备自动化程度的不断提高,产品质量高低越来越取决于设备的精度与性能。
为此,通过提高设备的精度和性能来提高产品的合格品率。
3、控制设备停机时间为了参与国际竟争,提出了“销、供、产”生产经营模式,这样就要求企业加快流动资金的周转和提高企业的柔性,严格控制设备的各项停机时间,追求“0”目标(设备计划外停机时间“0”库存“0”产品缺陷“0”)。
设备综合效率OEE实战01——管理篇_2

转时间 损失
外加工件或其它零部件迟延交货所引起之待料,质量问题解决; 动力设施故障停止等引起生产设备停止时间
突发故障引起之停止时间
模具、夹具之交换、调整、试加工之时间。 运转时间-(加工数×C.T) 基准加工速度与实际加工速度之差。加工数×(实际C.T-基准C.T)
正常生产时作出不良品之时间。选别、修理不良品而致设备停止 有效稼动之时间
2、设备综合效率OEE的原理
设备
6大LOSS
计算设备综合效率
负荷时间
停
运转时间
止 损
失
实际
速 度
运转时间 损
失
不
创造价值 良 运转时间 损
失
(1)故障 (2)作业准备、调整
时间运转率
=
负荷时间-停止时间 负荷时间
×100%
(3)空转、瞬间停止 (4)速度低下
理论周期X加工数量
性能运转率=
运转时间
×100%
时间开动率 Availability
性能开动率 Performance Rate
合格品率 Quality Rate
计划停机 Plan
外部因素 Exterior Reason
故障停机 Breakdown
设置和重新定位 Set-up and
Repositioning
速度降低 Reduced 速度
空转和小停机 Idling and Minor
3、 设备产能利用率TEEP
关于生产时间的区分
实际运转时间:设备加工产品必需要的时间;
实际运转时间 = 理论加工周期 X 生产数量
实际运转时间 = 设备运转时间 - 性能损失时间
设备空闲和暂停:
性
如何用OEE来指导生产改善(干货)
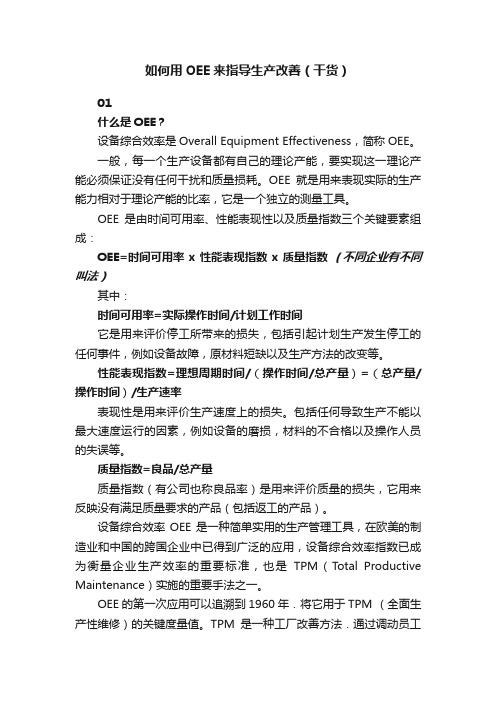
如何用OEE来指导生产改善(干货)01什么是OEE?设备综合效率是Overall Equipment Effectiveness,简称OEE。
一般,每一个生产设备都有自己的理论产能,要实现这一理论产能必须保证没有任何干扰和质量损耗。
OEE就是用来表现实际的生产能力相对于理论产能的比率,它是一个独立的测量工具。
OEE是由时间可用率、性能表现性以及质量指数三个关键要素组成:OEE=时间可用率 x 性能表现指数 x 质量指数(不同企业有不同叫法)其中:时间可用率=实际操作时间/计划工作时间它是用来评价停工所带来的损失,包括引起计划生产发生停工的任何事件,例如设备故障,原材料短缺以及生产方法的改变等。
性能表现指数=理想周期时间/(操作时间/总产量)=(总产量/操作时间)/生产速率表现性是用来评价生产速度上的损失。
包括任何导致生产不能以最大速度运行的因素,例如设备的磨损,材料的不合格以及操作人员的失误等。
质量指数=良品/总产量质量指数(有公司也称良品率)是用来评价质量的损失,它用来反映没有满足质量要求的产品(包括返工的产品)。
设备综合效率OEE是一种简单实用的生产管理工具,在欧美的制造业和中国的跨国企业中已得到广泛的应用,设备综合效率指数已成为衡量企业生产效率的重要标准,也是TPM(T otal Productive Maintenance)实施的重要手法之一。
OEE的第一次应用可以追溯到1960年.将它用于TPM (全面生产性维修)的关键度量值。
TPM是一种工厂改善方法.通过调动员工的主人翁精神来调动员工的自主性。
从而持续、快速地改善制造工艺水平。
02OEE的计算实例设某设备某天工作时间为8H,班前计划停机10Min,故障停机30Min,设备调整35Min,产品的理论加工周期为1min/件,一天共加工产品400件,有20件废品,求这台设备的OEE。
计算得知:计划运行时间=8*60-10=470(min)实际运行时间=470-30-35=405(min)时间有效率=405/470=0.86(86%)性能表现性=400/405=0.98(98%)质量指数=(400-20)/400=0.95(95%)OEE=有效率*表现性*质量指数=80%在上表中,我们只列举了一些事件原因,在实际应用中它可能包括与生产有关的任何原因。
设备综合效率OEE计算公式和方法实例1

设备综合效率OEE计算公式和方法实例影响设备综合效率的主要原因是停机损失、速度损失和废品损失。
它们分别由时间开动率、性开动率和合格品率反映出来,故得到下面设备综合效率公式:设备综合效率=时间开动率×性能开动率×合格品率这里,负荷时间为规定的作业时间除去每天的停机时间,即负荷时间=总工作时间-计划停机时间按滁州30000无菌线为例,每班按8小时计,理论效率按80%。
工作时间则是负荷时间除去那些非计划停机时间,如故障停机、设备调整和更换模具停机等非计划情况。
【例1】若总工作时间为8h,班前计划停机时间是20min,而故障停机为实际20min,安装准备工器具时间为25min,调整设备时间为25min。
负荷时间=480-20=460min开动时间=460--20-25-25=390min时间开动率=速度开动率×净开动率(A)每天工作时间=60×8=480min。
(B)每天计划停机时间(生产、维修计划、早晨会议等)=20min。
(C)每天负荷时间=A-B=460min。
(D)每天停机损失=60min(其中故障停机=20min,安装准备=25min,调整=25min)。
(E)每天开动时间=C-D=390min。
(F)每天生产数量=12800件。
每小时产能按30000bph,按80%的生产效率折算。
8小时产能为12800箱(G)合格品率=99.8%。
(H)理论加工周期=0.037min/件。
(I)实际加工周期= 0. 043min/件。
(J)实际加工时间=I×F=0.043×12800=414.4min。
(K)时间开动率=(E/C) ×100%=(390/460)×100%=84.8%。
(L)速度开动率=(H/I)×100%= (0.037/0.043)×100%=86%。
(M)净开动率=(J/E)× 100%=(414.4/390)×100%=106%。
设备综合效率OEE的分析与改善!太实用了!
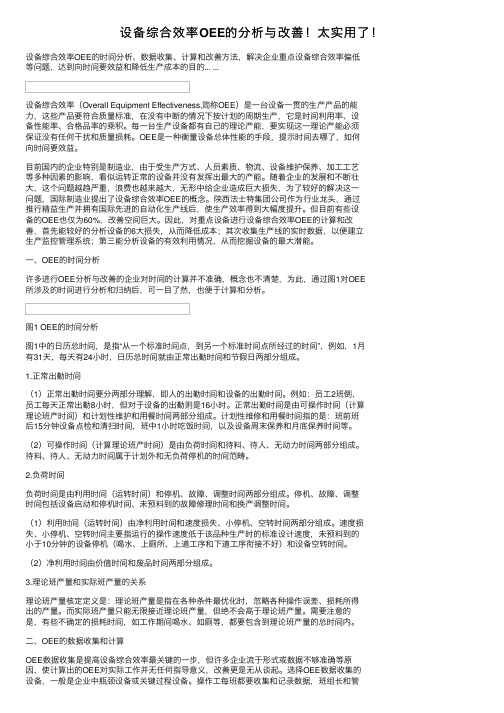
设备综合效率OEE的分析与改善!太实⽤了!设备综合效率OEE的时间分析、数据收集、计算和改善⽅法,解决企业重点设备综合效率偏低等问题,达到向时间要效益和降低⽣产成本的⽬的... ...设备综合效率(Overall Equipment Effectiveness,简称OEE)是⼀台设备⼀贯的⽣产产品的能⼒,这些产品要符合质量标准,在没有中断的情况下按计划的周期⽣产,它是时间利⽤率、设备性能率、合格品率的乘积。
每⼀台⽣产设备都有⾃⼰的理论产能,要实现这⼀理论产能必须保证没有任何⼲扰和质量损耗。
OEE是⼀种衡量设备总体性能的⼿段,提⽰时间去哪了,如何向时间要效益。
⽬前国内的企业特别是制造业,由于受⽣产⽅式、⼈员素质、物流、设备维护保养、加⼯⼯艺等多种因素的影响,看似运转正常的设备并没有发挥出最⼤的产能。
随着企业的发展和不断壮⼤,这个问题越趋严重,浪费也越来越⼤,⽆形中给企业造成巨⼤损失,为了较好的解决这⼀问题,国际制造业提出了设备综合效率OEE的概念。
陕西法⼠特集团公司作为⾏业龙头,通过推⾏精益⽣产并拥有国际先进的⾃动化⽣产线后,使⽣产效率得到⼤幅度提升。
但⽬前有些设备的OEE也仅为60%,改善空间巨⼤。
因此,对重点设备进⾏设备综合效率OEE的计算和改善,⾸先能较好的分析设备的6⼤损失,从⽽降低成本;其次收集⽣产线的实时数据,以便建⽴⽣产监控管理系统;第三能分析设备的有效利⽤情况,从⽽挖掘设备的最⼤潜能。
⼀、OEE的时间分析许多进⾏OEE分析与改善的企业对时间的计算并不准确,概念也不清楚,为此,通过图1对OEE所涉及的时间进⾏分析和归纳后,可⼀⽬了然,也便于计算和分析。
图1 OEE的时间分析图1中的⽇历总时间,是指“从⼀个标准时间点,到另⼀个标准时间点所经过的时间”,例如,1⽉有31天,每天有24⼩时,⽇历总时间就由正常出勤时间和节假⽇两部分组成。
1.正常出勤时间(1)正常出勤时间要分两部分理解,即⼈的出勤时间和设备的出勤时间。
设备综合效率(OEE)
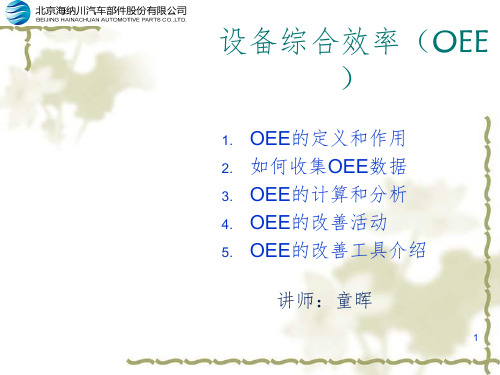
设备损失结构分析9 图
从6大损失到16大损失
生产活动中的16大损失
1
2
3
8大 设 备 损 失
4
5
6
7
8
9
10
5大 人 力 损 失
11
12
13
14
3大 原 材 料 与 能 源 损 失
15
16
设备故障 切换
切刀/工夹具的更换 开关机 小停机
速度损失 缺陷/返工 工厂计划停产 管理损失 运作损失 生产线管理损失 后勤和运输 测量和调节损失 能源损失 备品备件损失 原材料损失
8
设备损失结构 休息时间
参考定义 •影响设备运转的时间==〉人的休息时间。 •生产计划规定的休息时间。
停 止 管理对外时间
时 间 计划停止之时间
•朝会(每日10分)、发表会、参加讲习会、教育训练、消防演习、健 康检查、预防注射、盘点、试作、原动力设施之停止等引起设备之停止 时间。 •计划的保全、改良保养时间。 •TPM活动日,每日下班之清扫10分钟。
19
答案:综 合 设 备 效 率(OEE)
设备负荷时间= (8*60 – 60-30)=390
时间开动率= (390-20-15*2-10) / 390=330/390= 0.85 性能开动率= (0.4 分钟/台 * 750 台) / 330 = 300/330=0.91 合格品率= (750 台 – 50不良品) / 750 =700/750= 0.93
❖ 质量:提高产品质量.降低返修率。
4
中岛清一全员生产维护的五大要素
1、TPM致力于设备综合效率最大化的目标
2、TPM在整个设备一生建立彻底的预防维修体制
如何进行OEE指标设定与改善
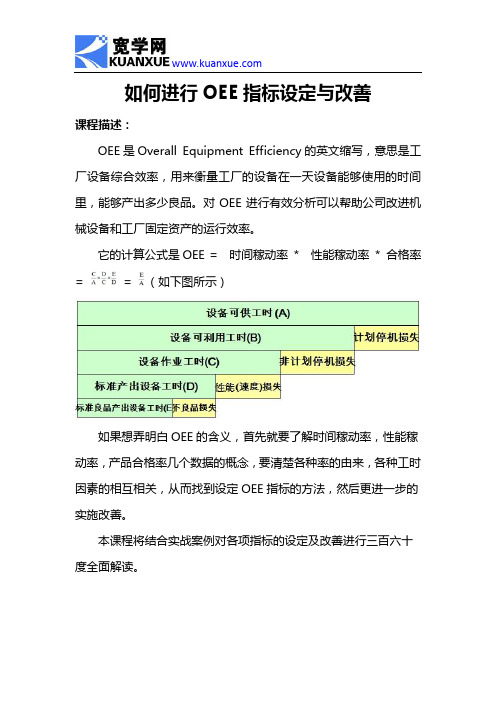
如何进行OEE指标设定与改善课程描述:OEE是Overall Equipment Efficiency的英文缩写,意思是工厂设备综合效率,用来衡量工厂的设备在一天设备能够使用的时间里,能够产出多少良品。
对OEE进行有效分析可以帮助公司改进机械设备和工厂固定资产的运行效率。
它的计算公式是OEE = 时间稼动率* 性能稼动率* 合格率= = (如下图所示)如果想弄明白OEE的含义,首先就要了解时间稼动率,性能稼动率,产品合格率几个数据的概念,要清楚各种率的由来,各种工时因素的相互相关,从而找到设定OEE指标的方法,然后更进一步的实施改善。
本课程将结合实战案例对各项指标的设定及改善进行三百六十度全面解读。
解决方案:他山之石,可以攻玉!虽然各类生产行业在进行OEE指标设定与改善时,都有不同的策略,但万变不离其宗!下面我们从实战经验中给大家总结一些方法流程,以便大家参考!上文中,我们对OEE进行了拆解并分出设备时间稼动率、设备性能稼动率和产品合格率这三个指标,但又有哪些因素影响这三个指标而导致OEE值降低呢?我们再重新梳理一下这三个指标中五个工时因素及其控制改善方向。
时间稼动率是设备可供工时与设备作业工时的比值。
1.设备可供工时的具体值可通过向设备供应商的询问以得到此设备日最大开机时间为多少,也可用行业内运转良好的设备作为参考大致预估,另外,为使OEE最大化,应尽量让关键设备24小时开机生产。
2.说完设备可供工时后,顺便向大家介绍一下设备可利用工时,因为设备可利用工时是设备可供工时减去计划停机损失得来的值,而设备可利用工时减去非计划停机损失,就能得出设备作业工时,因此,为提高设备作业工时,一方面是增加设备可利用工时,另一方面是降低非计划停机损失。
增加设备可利用工时可从三方面进行思考:一是查看出货计划是否能将设备可供工时填满;二是明确计划内新产品试产占用设备的工时是多少,是否可以采用实验设计进行压缩;三是查看设备定期维护保养的时间是否可以优化。
生产设备综合效率 OEE
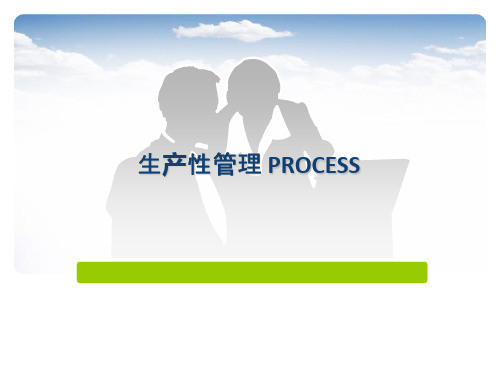
Ⅰ阶段
Image
对生产现场发生的 Loss 分析不了,改 善零散。
Ⅱ阶段
掌握Loss,部分改 善持续,构成改善 组织。
Ⅲ阶段
经过全部门掌握生产 Loss,S.T改善 连接,明确设定 改善目标
Ⅳ阶段
计划性的促进 S.T节俭活动 , RTY技法部分 构成
Ⅴ阶段
根据全部分体现的 经营效果扩大RTY 的适用范围
part长 部门长
问题认识
改善计划树立
生产/不良Loss
•次数率 •工程执行率
当日內 是否可能 根本改善
? YES
No 每日结算会议
•活动目标
•改善方法
•(6σ,3次元
F/P, 5W1H,单顺)
•完成日期
•担当
关联部门
改善
•无,再作业Loss •工程执行率 Worst 10
树立改善计划
是否可 能自体改善
备注
12.整理用语
1. 工数
: 表示作业量的方法有很多种,最常用的是时间,机械时间和 (MACHINE HOUR) 人作业时间 (MAN HOUR). 两者都表现为工数,但一般指M.Hr(人作业时间).
2. 总出勤工数 : 日程期间内测定单位总人员(直接人员 + 间接人员)的实绩总出勤(总人员× 出勤时间), (管理者,办公室技术职, Q.C 现状社员除外) 总出勤工数区分为直接工数和间接工数。 (定员*8HR)+加班工数+早出工数+特勤工数+其他-(休假+早退+其他)
树立计划
•选定对象 -主力型号 /Tool (3~4 Model)
工程分析
•工程/型号别 S.T策定
掌握现水准/ 设定目标
设备综合效率(OEE)知识讲解
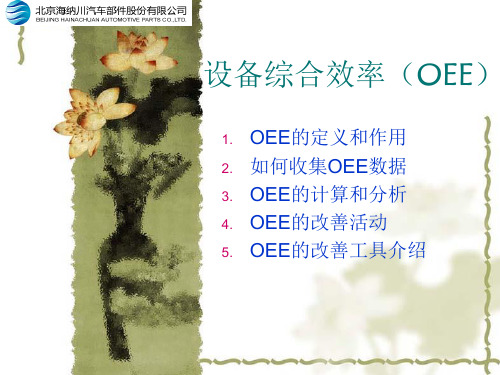
设备损失结构 休息时间
参考定义 •影响设备运转的时间==〉人的休息时间。 •生产计划规定的休息时间。
停 止 管理对外时间
时 间 计划停止之时间
•朝会(每日10分)、发表会、参加讲习会、教育训练、消防演习、健 康检查、预防注射、盘点、试作、原动力设施之停止等引起设备之停止 时间。 •计划的保全、改良保养时间。 •TPM活动日,每日下班之清扫10分钟。
•实际产生附加价值的时间。 •生产良品所花的时间。
设备损失结构分析图
从6大损失到16大损失
生产活动中的16大损失
1
2
3
8大 设 备 损 失
4
5
6
7
8
9
10
5大 人 力 损 失
11
12
13
14
3大 原 材 料 与 能 源 损 失
15
16
设备故障
切换
切刀/工夹具的更换
开关机
小停机
速度损失
时
缺陷/返工
工厂计划停产
通过6大损失计算OEE
设备
六大损失
全效率计算
负荷时间
停
开动时间
机 损
失
净开动
速
时间
度
损
失
设备故障 安装调整
空转短暂 停机 速度降低
时间 开动率
=
开动时间 负荷时间
性能 开动率
=
实际生产量 理论生产量
有价 废 值开 品 动时 损 间失
加工废品
初期未 达产
合格 品率
=
合格品数量 加工量
设备综合效率OEE=时间开动率×性能开动率×合格品率
3. 空转与短暂停机:设备空转和未预料到的(未计划的)小 于10分钟的设备停机
OEE设备综合效率改善(2+1模式)2

5、确定设备问题的要因:确定各项原因的判别标准,现场分析确认各项原因是否达到标准,以此判定是否是主要原因
6、制定改善对策方案:针对要因制定改善对策方案和改善计划
7、对策实施方案:能马上落实的改善对策现场实施,其它方案根据改善计划实施并及时跟进实施状况
9、设备故障树分析法(FTA)
10、检修管理作业标准
11、建立完善的检修管理标准化流程
案例:滚动轴承功能故障前的不同潜在故障点分析
案例:汽机检修作业标准案例分析
案例:双螺杆常见故障分析
五、提高设备利用率改善OEE
1、人机配合效率改善
2、设备切换效率改善
3、作业切换时间的形态
4、快速切换改善着眼点
5、快速切换的实施法则
1、掌握设备综合效率的计算方法
2、通过建立设备点检标准改善OEE
3、通过建立设备保养标准改善OEE
4、通过建立设备检修标准改善OEE
5、提高设备利用率改善OEE
6、设备故障问题分析解决改善OEE
7、减少设备准备时间,实现快速换型
8、降低加工不良,学习防错技术
9、提升维修技术,减少故障时间
培训对象
维修部门的工程师、经理、主管,中高层管理者和生产(制造)部门经理、主管、现场班组长。
(1)设备点检表项目---点检部位
(2)设备点检表项目---点检内容
(3)设备点检表项目---点检方法
(4)设备点检表项目---点检标准
(5)设备点检表项目---点检周期
10、精密点检与设备劣化倾向管理
(1)精密点检内容
(2)精密点检的主要检测方法
(3)设备劣化管理
综合设备效率OEE

备事故及故障停机率等。
这些指标反映的是以时间为单位的设备的可利用程
度,管理指标较多,既不直观,也不全面,作为对设备的 运行管理,以上指标不能真实反映生产的速度损失(导致
设备性能开动率下降)情况,也无法反映生产废次品而造
成的设备效率的损失(导致设备生产的合格品率下降),以及拼设备超 产对设备的伤害而产生的设备效率损失等。
×100%
如何计算OEE
6、合格品率:
相对于总产出的数量中合格品数量所占的比率。合格
品是总产出的数量中去掉初期开始的不合格品、生产中的 不合格品、降级和返工品(再作业)后剩余的。
不合格品=初期开始的不合格品+生产中的不合格品+降级+返工品
总数量-不合格数量
合格品率=
总数量
×100%=
合格品数量 总数量
速度开动率=
理论加工周期 实际加工周期
×100%
如何计算OEE
4、净开动率:
体现设备的开动时间中有多少时间是进行产品生产的。
生产数量×实际加工周期
净开动率=
开动时间
×100%
如何计算OEE
5、性能开动率:
速度开动率和净开动率相乘得出的设备的性能发挥情况。
性能开动率=速度开动率×净开动率=
理论加工周期×生产数量 开动时间
资产的利用率。每一个企业的目标都是把固定资产的收益
最大化,换而言之就是使设备尽可能地高效利用起来,特 别是关键设备。所以提高关键设备的综合效率(OEE)是
降低制造成本的有效手段,从而帮助企业在生产运营方面
更加具有市场竞争力。
为什么引进OEE
钢铁企业为什么要提高OEE
设备综合效率OEE实战01——管理篇_2

一、认识设备综合效率OEE
2、设备的效率损失在哪里?
1)故障停止损失
故障可分为功能停止型故障和功能下 降型故障两大类。
故障损失是阻碍效率的最大原因。
2)作业准备、调整损失
设备加工部品前的准备、调整阶段停 机就是准备、调整损失。
其中“ 调整时间”有时很长。
停止 LOSS 停机
准备和调整
一、认识设备综合效率OEE
Stoppage
降级和返工 Downgrade and Reprocessing
初期不合格品 Yield 损失
目标 最小化 0 0 最小化 0 0
0 最小化
一、认识设备综合效率OEE
2、设备的效率损失在哪里?
设备运行效率的科学管理
问题回答 ✓完好率能否体现设备的工作效率?
✓故障率能否表示设备的工作效率?
1、使设备的运转状态与企业的经济效率结合起来,
2、有利于“设备服务于生产”,“生产业绩靠设备“观念树立及团队合作。
3、OEE的统计和分析可暴露出企业管理各个方面的问题。有利于改善设备的 使用、维护保养、 资材保证、质量检查及后勤服务的工作,消除方方面面的 浪费,提高生产效率。
4、OEE管理即能提高设备工作效率,也能避免“拼设备”的短期行为。
例如:工作8小时(480分钟);工作24小时(1440分钟) 注意:员工的延时工作及节假日加班时间也是此类时间!
设备负荷时间:公司计划安排设备生产的时间;
设备负荷时间 = 日历出勤时间 - 生产停止时间
3、 设备产能利用率TEEP
关于生产停止时间
设备损失时间
生产活动内容
计划停产时间
生产计划规定的休息时间和吃饭及工间休息时间;
生 产
OEE分析与改善

提高OEE的措施
03
设备维护保养计划
定期检查设备 运行状况,及 时发现并解决
潜在问题
制定合理的维 护保养计划, 确保设备得到 及时有效的保
养
提高操作人员 的技能水平, 使其能够正确 使用和维护设
备
建立设备维修 档案,记录设 备的维修保养 情况,方便跟
踪管理
操作人员培训和考核
培训:提高操作人员的技能和知识水平,使其能够更好地操作设备。 考核:对操作人员进行定期考核,确保其技能水平符合要求。 激励:对表现优秀的操作人员进行奖励,提高其工作积极性和责任心。 反馈:及时向操作人员提供反馈,帮助其改进工作方法和提高效率。
生产计划优化
优化生产流程,减少生产过 程中的瓶颈和浪费
制定合理的生产计划,确保 设备利用率最大化
引入先进的生产管理软件, 实时监控生产数据,及时调
整生产计划
加强生产人员培训,提高生 产技能和效率意识
工艺流程改进
引入自动化设备,提高生产 效率
识别瓶颈工序,优化工艺流 程
定期维护和保养设备,确保 设备正常运行
目的:识别设备效率损失,确定 改善方向
作用:为企业决策提供数据支持
添加标题
添加标题
添加标题
添加标题
意义:提高设备利用率,降低生 产成本
价值:提升生产效率和产品质量
OEE分析的方法和步骤
收集数据:收 集设备运行过 程中的各种数 据,如开机时 间、停机时间、 产品数量等。
分析数据:对 收集到的数据 进行整理和分 析,找出设备 运行过程中的 瓶颈和问题。
OEE改善案例分析
04
案例一:某下、生产 成本高的问题
OEE指标分析:通 过分析OEE指标, 发现设备运行效率 低下、故障率高、 生产时间损失严重
设备综合效率OEE

进一步,我们还可以利用PM分析,向更深层搜寻,找出影响OEE的深层次原因,如图1-3所示。图1-3所示计算中,如果时间开动 率不高(用方框框出部分),意味着可能的因素是设备故障。工模具更换或调整停机时间过长,经检验发现是故障停机时间过长。 再向下分析,发现既不是轴承,又不是推进器的原因,而是密封泄漏。为什么会发生密封泄漏呢?检查结果发现是旋流器损坏影响 所致。 如此一层层向下分析,直到找出可以解决的答案。减少六大损失应注意以下几个问题: (1)故障与短暂停机是一个障碍,应该加强对设备的检查,从小处做起。例如前面曾提到的日本西尾泵厂就提出:无人(化) 管理起始于无尘。 (2)防止设备劣化。蝼蚁虽小,能决万里之堤,设备劣化往往从尘土开始。尘土粘附在设备上,产生划痕,容易腐蚀,逐渐松 动,继而又造成振动,这就是劣化的开始。除了日常的紧固螺钉之外,还要注意预防维修。图1-4展示了预防维修与预防医疗之间 的关系。 图1-5上半部分是设备故障率浴盆曲线,下半部分则展示了不同时期的主要故障原因和处理对策。 (3)零故障的处理对策。故障是冰山的顶峰,消除故障应从小做起。如:①严格保持设备原始基本状态(靠清洁、润滑和紧固 螺钉);②遵守操作规程;③及时根除劣化;④改进设备设计缺陷;⑤改进操作与维修技能。
设备综合效率OEE 设备综合效率
什么是设备综合效率OEE 什么是设备综合效率 设备综合效率是Overall Equipment Effectiveness,简称OEE。一般,每一个生产设备都有自己的理论产能,要实现 这一理论产能必须保证没有任何干扰和质量损耗。OEE就是用来表现实际的生产能力相对于理论产能的比率,它是一个 独立的测量工具。 OEE是由可用率,表现性以及质量指数三个关键要素组成: OEE=可用率*表现指数*质量指数 其中: 可用率=操作时间/计划工作时间 它是用来评价停工所带来的损失,包括引起计划生产发生停工的任何事件,例如设备故障,原材料短缺以及生产方 法的改变等。 表现指数=理想周期时间/(操作时间/总产量)=(总产量/操作时间)/生产速率 表现性是用来评价生产速度上的损失。包括任何导致生产不能以最大速度运行的因素,例如设备的磨损,材料的不 合格以及操作人员的失误等。 质量指数=良品/总产量 质量指数是用来评价质量的损失,它用来反映没有满足质量要求的产品(包括返工的产品)。 全局设备效率OEE是一种简单实用的生产管理工具,在欧美的制造业和中国的跨国企业中已得到广泛的应用,全局 设备效率指数已成为衡量企业生产效率的重要标准,也是TPM(Total Productive Maintenance)实施的重要手法之一。 OEE的第一次应用可以追溯到1960年.将它用于TPM (全员生产维修)的关键度量值。TPM是一种工厂改善方法.通 过调动员工的主人翁精神来调动员工的自主性.从而持续、快速地改善制造工艺水平。 实行OEE的效益 的效益 实行 OEE的解决方案能够使得制造商在世界占有一席之地。另外.可以获得以下几方面效益。 设备:降低设备的故障以及维修成本,加强设备管理以延长设备的使用寿命。 员工:通过明确操作程序.提高劳动者的效力.增加生产力。 工艺:通过解决工艺上的瓶颈问题.提高生产力。 质量:提高产品质量.降低返修率。
关于生产线的OEE(设备综合利用效能)

关于生产线的OEE(设备综合利用效能)第一概述一般,每一个生产设备都有自己的最大理论产能,要实现这一产能必须保证没有任何干扰和质量损耗。
当然,实际生产中是不可能达到这一要求,由于许许多多的因素,车间设备存在着大量的失效: 例如,除去设备的故障、调整,以及设备的完全更换之外,当设备的表现非常低时,可能会影响生产率,产生次品,返工等。
OEE是一个独立的测量工具,它用来表现实际的生产能力相对于理论产能的比率。
国际上对OEE的定义为:OEE是Overall Equipment Effectiveness(全局设备效率)的缩写。
它由可用率,表现性以及质量指数三个关键要素组成,即:OEE=可用率X 表现性 X质量指数其中:可用率=操作时间/计划工作时间。
它是用来考虑停工所带来的损失,包括引起计划生产发生停工的任何事件,例如设备故障,原料短缺以及生产方法的改变等。
表现性=理想周期时间 / (操作时间 / 总产量)=总产量 / (操作时间X理论生产速率)表现性考虑生产速度上的损失。
包括任何导致生产不能以最大速度运行的因素,例如设备的磨损,材料的不合格以及操作人员的失误等。
质量指数=良品/总产量质量指数考虑质量的损失,它用来反映没有满足质量要求的产品(包括返工的产品)。
利用OEE的一个最重要目的就是减少一般制造业所存在的六大损失:停机损失、换装调试损失、暂停机损失、减速损失、启动过程次品损失和生产正常运行时产生的次品损失。
注意事项·OEE要应用在一台机器上(可视为一台机器的生产线)而不能应用在整个生产线或全厂上,这样才有意义。
·OEE要作为一系列一体化的综合关键业绩指标中的一部分来运用而不能孤立使用,否则将造成生产批次规模加大或有质量缺陷的产品。
·OEE必须与精益原则相符,要确保对OEE的计算不会导致浪费合理化、制度化,例如,绝不要允许给换线留出时间。
关设备的生产信息,为OEE提供最有价值的数据,同时,该系统也可以生成实时的生产信息报告,包括故障停工,在制品信息和OEE等。
设备综合效率OEE

设备综合效率OEE目录什么是设备综合效率OEE设备综合效率是Overall Equipment Effectiveness,简称OEE。
一般,每一个生产设备都有自己的理论产能,要实现这一理论产能必须保证没有任何干扰和质量损耗。
OEE就是用来表现实际的生产能力相对于理论产能的比率,它是一个独立的测量工具。
OEE是由可用率,表现性以及质量指数三个关键要素组成:OEE=可用率*表现指数*质量指数其中:可用率=操作时间/计划工作时间它是用来评价停工所带来的损失,包括引起计划生产发生停工的任何事件,例如设备故障,原材料短缺以及生产方法的改变等。
表现指数=理想周期时间/(操作时间/总产量)=(总产量/操作时间)/生产速率表现性是用来评价生产速度上的损失。
包括任何导致生产不能以最大速度运行的因素,例如设备的磨损,材料的不合格以及操作人员的失误等。
质量指数=良品/总产量质量指数是用来评价质量的损失,它用来反映没有满足质量要求的产品(包括返工的产品)。
全局设备效率OEE是一种简单实用的生产管理工具,在欧美的制造业和中国的跨国企业中已得到广泛的应用,全局设备效率指数已成为衡量企业生产效率的重要标准,也是TPM(Total Productive Maintenance)实施的重要手法之一。
OEE的第一次应用可以追溯到1960年.将它用于TPM (全员生产维修)的关键度量值。
TPM是一种工厂改善方法.通过调动员工的主人翁精神来调动员工的自主性.从而持续、快速地改善制造工艺水平。
实行OEE的效益OEE的解决方案能够使得制造商在世界占有一席之地。
另外.可以获得以下几方面效益。
设备:降低设备的故障以及维修成本,加强设备管理以延长设备的使用寿命。
员工:通过明确操作程序.提高劳动者的效力.增加生产力。
工艺:通过解决工艺上的瓶颈问题.提高生产力。
质量:提高产品质量.降低返修率。
OEE的使用同一设备的OEE公式可以采用多种形式,它可以作为基准设计和分析工具用于可靠性分析、设备使用效率分析或两方面都用。
全面生产维护中OEE全局设备效率或设备综合效率介绍
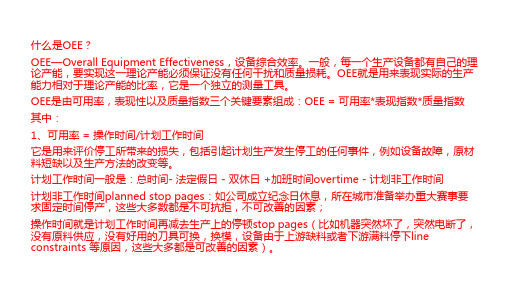
理想周期时间 是根据设备的铭牌上的参数得来的,理想中的加工能力。它乘以生产数量,就是理 想状态下,加工这么多产品需要的时间;
但是实际的生产中会产生,比如设备空转,设备磨损导致的加工速度变慢,一些不需要维修人员 介入的,能够自我调整的故障。这些都导致了实际的operating time要高于ideal operating time(ideal cycle time * total pieces);
其中:
1、可用率 = 操作时间/计划工作时间
它是用来评价停工所带来的损失,包括引起计划生产发生停工的任何事件,例如设备故障,原材 料短缺以及生产方法的改变等。
计划工作时间一般是:总时间- 法定假日 - 双休日 +加班时间overtime - 计划非工作时间
计划非工作时间planned stop pages:如公司成立纪念日休息,所在城市准备举办重大赛事要 求固定时间停产,这些大多数都是不可抗拒,不可改善的因素;
操作时间就是计划工作时间再减去生产上的停顿stop pages(比如机器突然坏了,突然电断了, 没有原料供应,没有好用的刀具可换,换模,设备由于上游缺料或者下游满料停下line constraints 等原因,这些大多都是可改善的因素)。
8 运行
什么是OEE?
2、表现指数 = 理想周期时间/(操作时间/总产量)=(总产量/操作时间)/生产速率
在上式中,我们只列举了一些事件原因,在实际应用中它可能包括与生产有关的任何原因。OEE能 准确地告诉你设备效率如何,在生产的哪个环节有多少损失,以及你可以进行哪些改善工作。长 期的使用OEE工具,企业可以轻松的找到影响生产效率的瓶颈,并进行改进和跟踪,以达到提高 生产效率的目的。
OEE设备综合效率分析与管理

OEE设备综合效率分析与管理一、引言在现代工业生产中,设备的高效运行对于企业的生产效率和利润的提升至关重要。
OEE(Overall Equipment Efficiency)即设备综合效率,是评估设备性能的重要指标。
本文将从OEE的概念与计算方法入手,探讨OEE设备综合效率的分析与管理。
二、OEE概述OEE是用来衡量设备综合效率的一个指标。
它综合考虑了设备的可用时间利用率、性能效率和质量合格率,通过计算得出设备的OEE值。
OEE的计算公式为:OEE = 可用时间利用率 ×性能效率 ×质量合格率可用时间利用率 = 设备运行时间 / (设备运行时间 + 设备停机时间)性能效率 = 实际产量 / 理论产量质量合格率 = 合格产品数量 / 总产量三、OEE设备综合效率分析1. 可用时间利用率分析通过分析设备运行时间和设备停机时间,可以得出设备的可用时间利用率。
可用时间利用率的提升可以通过减少停机时间、缩短换模时间、加快设备故障修复等手段实现。
2. 性能效率分析性能效率衡量了设备在运行过程中的产量和理论产量之间的比例。
通过分析实际产量和理论产量的差异,可以找出影响设备性能的因素,并采取相应的措施进行改进,如提高生产速度、优化工艺流程等。
3. 质量合格率分析质量合格率是指设备生产的合格产品数量与总产量之间的比例。
通过对质量合格率的分析,可以发现设备存在的质量问题,并采取相应的措施进行改进,如加强质量管控、提高操作技能等。
四、OEE设备综合效率管理1. 设备维护管理定期进行设备维护和保养,及时处理设备故障,确保设备处于良好的工作状态。
同时,建立设备维护记录和维修历史,为后续的故障分析和改进提供数据支持。
2. 运营管理加强对设备运行过程的监控与管理,及时发现问题并采取措施进行处理。
建立运营数据指标体系,对设备的关键性能指标进行监测与分析,及时发现设备运行异常,并进行预警与预防。
3. 人员培训和技能提升加强对操作人员的培训和技能提升,提高其操作技能和质量意识。
生产效率改善方法-设备综合效率(OEE)改善

24小时
计划休息时间11:30pm-7:30am
计划行政活动时间-晨会
计划停机时间-保养、用餐
无生产需求时间(计划原因)
停止时间
负荷时间 TL
设备时间损失说明
24小时
停机时间
计划休息时间
计划行政活动时间
计划停机时间
无生产需求时间
停止时间
负荷时间 TL
突发故障时间 (紧急修理)
计划停止之时间
计划的预防保全、改良保养时间 1700活动、TPM活动日,每日下班之清扫10分钟
无负荷时间
外注品或其他工程部品延迟纳入引起之待料
负 荷 时 间
停机时间
故障
突发故障引起之停机时间
换工程,调整自工程疏失停工
模具、治工具之交换、调整、试加工之时间;自己项目中(其它)所包含之时间
运 转 时 间
设备表现的指标是什么?
设备负荷% 设备稼动%(故障%) 修理频率 调整时间(设定) 产品不良比率 ..
需要时可用 使用时不会突然停止(非计划内停机) 精度维持(不会时好时坏) 修理频率不高 维修保养费用 设备寿命长 操作意外事故
生产方面关心的话题
可运行时间24 hrs
AL 计划运行时间21 hrs
泄漏造成了浪费
新油的浪费 + 加油时劳动力浪费 清洁的浪费 除油污的废料浪费: 设备停机 安全问题 – 地面油滑? 环境 – 地面污染?
例:轴承为什么失效.....
其它 (18.6%)
过载 (6.9%)
脏物污染 (19.6%)
不恰当的润滑 (34.4%)
轴承制造商 SKF 的研究表明, 超过50%的轴承失效是由于“润滑不当”造成的。
- 1、下载文档前请自行甄别文档内容的完整性,平台不提供额外的编辑、内容补充、找答案等附加服务。
- 2、"仅部分预览"的文档,不可在线预览部分如存在完整性等问题,可反馈申请退款(可完整预览的文档不适用该条件!)。
- 3、如文档侵犯您的权益,请联系客服反馈,我们会尽快为您处理(人工客服工作时间:9:00-18:30)。
我们在企业内开展TPM是为了: - 在企业内建立起团队合作和主人翁精神的企业文化 - 使企业中的所有部门都参与到TPM的管理系统中 - 企业中的所有人(从最高层领导到一线的员工)都参与到TPM
增进操作人员与 维修人员的团队工作
帮助减少浪费
改善人因 工学
故障后的维护 成本昂贵 (10X)
阐明一个完整的 维护计划
TPM活动概要
1970 日本爱知县“日本电装株式会社”为了彻底实施“丰田生产方
式”首度采用“TPM” TPM效果 生产力 + 400% 故障率 1% 生产不良率 0.3% 1971年获 JIPM协会 “第一类PM优秀奖” 其他日本企业跟进
TPM定义
通过设备为导向的管理,将现有设备的表现 最优化;就是使设备在其寿命周期内保持生 产能力最大化的系统方法和过程
提升设备的有效稼动率及生产能力的过程 维持设备的稳定性,以消除设备变动对产品
质量、产量的干扰的过程 培养对设备关心、爱惜的作业人员与环境
定义说明
TPM的目的在于设备保养、消除计划外停机 TPM是改进生产与维护人员协作关系的常规方法 包括检查、日常保养、维修、预防/预测性维护
什么是OEE?
中文翻译:设备综合效率
英文名称:
Overall Equipment
Effectiveness
作用:生产过程中设备使用效率的一种评 价方法
0. 关于TPM
Total Productive Maintenance
TPM是“全员共同参与的生产力维护和管理”的简称,是一套综 合性的企业管理体系,以帮助我们建立并维护适合本企业经营和 发展的各类管理系统
的活 动中,并与企业得到共同的发展 - 通过各项有效工具的开展,挑战零事故,零损失,零缺陷和零
浪费,追求生产和经营效率的极限
TPM Objective TPM目标
* Zero accident 零事故
* Zero breakdown and loss 零故障损失
* Zero defect and complaint 零过失及抱怨
间和方法; 超前思维 实现设备导向型管理模式。
1. 问题引入
当前公司的主要关注点
客户
生产力
为中心 WTO 全球性竞争
员工参与
与设备有关的8大损失 - 计划性的停机和试车/故障/更换品种/设
定和调节/启动和停机/小停机和空转/速度损 失/质量缺陷返工(安装调整、空转短暂停机、 试生产)
管理浪费(Management) 资料的浪费 会议的浪费 管理的浪费 通讯的浪费 收据的浪费
遵守安全( Safety ) 防止灾害,事故 灾害事故是浪费以前的浪费 所有解除浪费是安全第一
设备浪费(Machine) 大型机械的浪费 法定机械的浪费 传送带的浪费 空气加工的浪费 故障的浪费 机械等待的浪费
生产效率改善的方法
设备综合效率(OEE)介绍与计算
课程目的
1. 了解TPM对企业的重要与TPM的组成部分 2. OEE的定义 3. OEE的目的及作用 4. OEE的理论及计算和如何改善OEE 5. 理解5S与改善OEE 的关系
6. 如何建立和维护设备的历史记录,评价目前 的OEE水平
7. 定 义 支 持 O E E 的 组 织 和 角 色 (项目负责人、主管、维护人员、操作员)
如果我们不关注TPM, 那些情况很可能发生, 或是常看到
1-4
一般情况
故障常常发生 临时性的维修频繁 生产中断常常发生 生产过程速度降低 产生成本的浪费 设备状态不稳定(使用时不良、保养时
OK) 有人抱怨、没人改善 没有人量化过这种损失
质量浪费(Quality) 做出不良品的浪费 维修不良品的浪费 犯错误的浪费 检查的浪费 质量管理的浪费
目前的生产环境 (设备与生产的紧密关系)
设备性能决定 产品质量水平 设备能力决定 产品产出能力 设备的费用 是生产成本的第二大项,决定了是
盈利水平
我们力神的设备会有哪些情况?
时间
停机
7大浪费
物资浪费(Material) 没有的浪费 库存的浪费 搬运的浪费 拿、放的浪费 等待的浪费 困难工序的浪费
作业方法浪费(Method) Lot的浪费 库存的浪费 搬运的浪费 拿、放的浪费 困难工序的浪费
人力浪费(Man) 步行浪费 寻找浪费 工序动作浪费 看不见的浪费
TPM活动的目的
改变对设备的看法、与管理
TPM
设备
生产
TPM活动的目的
改变对设备的看法、与管理
设备
TPM
生产
问题:
如何评价TPM的效果? 如何利用TPM活动提升高生产效率?
引申(回顾)
被动思维 反映了生产管理(含技术、质量)和设备
管理的效果; 主动思维 通过分析指标构成来寻找生产过程改善空
8. 掌握实施OEE改善的方法 9. OEE系统
课程对我的帮助
加深理解TPM的内容与对企业的重要 认识OEE与OEE计算方法 理解OEE改善项目中的角色 能够计划和实施OEE改善活动 认识OEE系统
解决疑惑
OEE就是一项普通的考核指标; OEE是设备人员的事; OEE考核管理给操作人员带来麻烦; 。。。。。。
等各种手段 TPM准时化生产的必要条件 TPM过程旨在培养一种环境,以鼓励员工致力于
安全、质量和效率方面的团队努力和创造力
TPM 就是使PM 旨在培养一种环境
鼓励全员参与的 致力于安全、质量、成本、贡献和 创造力方面的努力
1-3
TPM如何帮助我们?
与人有关的5大损失 - 生产线布局损失/后勤和运输/管理损失/
测量和调节损 失/操作运动损失
其它方面的3大损失 - 工夹具损失/能源损失/原材料损失
设备故障 安装与调整 空转短暂停机 速度降低 加工废品 试生产
100
%
速度损失
生产能力
启动
小停车 和空转
质量 缺陷
故障
设置和 调整