潜在的失效模式及效应分析表(过程)
失效模式分析表

潜在失效模 式(Pontential 功能要求 Failure (Functiona Model) l Requireme nt)
潜在原因/失效 严 发 机制(Pontent 重 生 Cause(s)/Mecha 度 度 预防 nism(s) of (S) (P) (Preventio Failure n)
侦 测 度 (D)
0 0
0 0Leabharlann 000 0 0 0
0 0 0 0
FMEA编号: 第 版 页码: 第 / 页 填表人: 初稿(Orig)日期: 修订(Rev)日期:
行动结果(Action Result) 风 责任与目 险 标/完成日 优 建议措施 期 严 发 侦 风险 先 Recommended Responsibi 实行措施 重 生 测 优先 数 Action(s) lity /target (Action Taken) 度 度 度 数值 值 Completio (S) (P) (D) RPN RPN n Date
潜在失效模式与效应分析表( FMEA)
项目(Item): 产品生产年份: 核心小组(core team):
设计/制 程项目 ( item) 潜在失效潜 在效应 (Potential Effect(s) of Failure
设计责任: 生效日期:
现行的设计//制程管制 (Current Process Design Controls) 侦测 (Detection)
FMEA失效模式效应分析表-
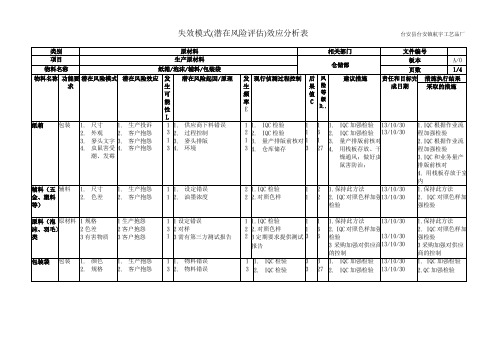
失效模式(潜在风险评估)效应分析表
台安县台安镇航宇工艺品厂
类别
成品
相关部门
文件编号
项目 物料名称
包装好的成品 成品
仓储部
板本
A/0
页数
3/4
功能要求 潜在风险模式 潜在风险效应 发 生 可 能 性 L
潜在风险起因/原理
发 现行侦测过程控制 生 频 率 E
后风
果险 值等 C级
D..
建议措施
责任和目标
行组装和包装
1 2、质检不到位
2 2.加强检验
3 18 7 14
1.严格按客人 13/10/30 和包装流程进 行组装和包装 2.员工自检和 13/10/30 品检全检相结 合的检验方式 彻底执行,保 证质量
1.严格按客人和包装 流程进行组装和包装 2.员工自检和品检全 检相结合的检验方式 彻底执行,保证质量
燥通风;做好虫
鼠害防治;
2 1.IQC 检验 2 2.对照色样
1 2 1.保持此方法
13/10/30
1 2 2. IQC 对照色样加强13/10/30
检验
1.IQC 根据作业流 程加强检验 2.IQC 根据作业流 程加强检验 3.IQC 和业务量产 排版前核对 4. 用栈板存放于室 内 1.保持此方法 2. IQC 对照色样加 强检验
台安县台安镇航宇工艺品厂
半成品
相关部门
文件编号
制程半成品 工序
生产部
板本
A/0
页数
2/4
发 潜在风险起因/原理 生 可 能 性 L
3 1. 操作不良 3 2. 破损 3 3. 伤害身体,影响健康
发 现行侦测过程控 后 风
生
制
玩具产品过程风险评估PFMEA(带内容)
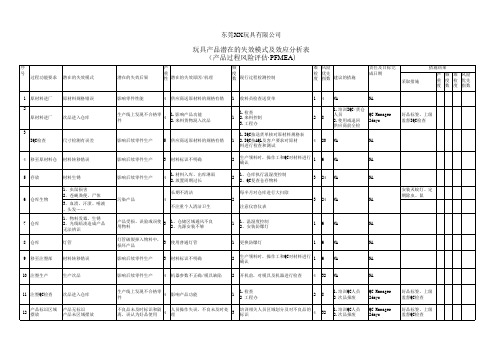
9 移至注塑部 材料转移错误
10 注塑生产
生产次品
东莞XX玩具有限公司
潜在的失效后果
玩具产品潜在的失效模式及效应分析表 (产品过程风险评估·PFMEA)
严
重 性 潜在的失效原因/机理
频
度 数 现行过程检测控制
难 风险
检 优先 度 指数 建议的措施
责任及目标完 成日期
采取措施
措施结果
严 频 难 风险 重 度 检 优先 度 数 度 指数
4 32
15 注塑部生物 16 注塑部环境
1、虫鼠损害 2、苍蝇粪便、尸体
3、血渍、汗渍、唾液 、头发……
1、物料发霉、生锈 2、光线暗淡造成产品 无法辨识
17
移至喷油部/移 印部
胶件转移错误
1.用错油漆 18 胶件喷油/移印 2.喷错颜色
3.喷油次品
19
喷油/移印QC检 查
次品进入仓库
污染产品
长期不清洁 4
、头发……
22
喷油/移印部环 境
1、物料发霉、生锈 2、光线暗淡造成产品 无法辨识
23 移至装配部 胶件转移错误
污染产品
长期不清洁 4
不注重个人清洁卫生
产品受损、误验或误使 用物料
3
1、车间通风不良 2、光源安装不够
影响后续零件生产 3 胶件标识不明确
每半月对车间进行大扫除 2
注意仪容仪表
3 24
1
组装次品/功能不良
污染产品
长期不清洁 4
不注重个人清洁卫生
产品受损、误验或误使 用物料
3
1、车间通风不良 2、光源安装不够
影响后续零件生产 3 人员操作失误
每半月对生产拉及工厂进行清洁 2
闻泰S98519-DFMEA潜在失效模式及分析(同兴达LCM)-20140702
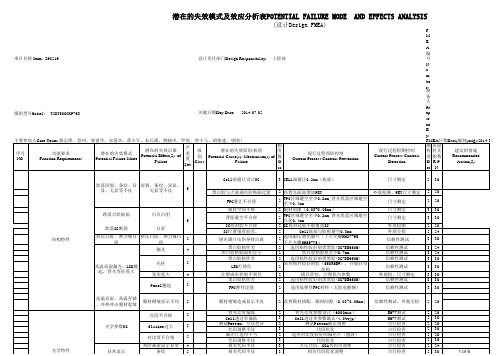
4 of 4
工
电特性
严 潜在的失效原因/机理 潜在的失效后果 级 潜在的失效模式 重 Potential Effect(S) of Potential Cause(s)/ Mechanism(s) of 别 Potential Failure Mode 度 Failure Class Failure Sev 6 信号输出、匹配不良 异常显示 LCD_ID信号异常 GOA代码不佳 绑定不良(错位、欠压、过压) FPC焊盘腐蚀 FPC断裂 5 环境测试失效 异常显示 FPC金手指切割铜皮残留、卷曲 元器件排布过于紧凑 FPC原材不良(微断短路) FPC原理NG FPC原理NG 接地设计不佳 ESD防护设计不佳 接地设计不佳 FPC Layout 不佳 稳压电容振动发出噪声
5 5
版本 Rev. A0
变更内容Comment 新制/New
日期 Date 2014-7-2
准备人Prepared by 唐刚
审核Checked by
批准Appro
2 of 4
L FAILURE MODE
AND EFFECTS ANALYSIS
页码Page: (修订REV): 措施结果Result 严 频 难 重 度 检 度 数 度 Sev Occ Det
2 FPC菲林管控、制程管控,选择无胶电解铜 1 1 2 2 2 2 2 FPC原理审核 FPC原理审核 改善接地设计、增强可靠性 改善ESD防护设计 改善接地设计、增强可靠性 Layout审核确认 程序代码改善
ESD测试失效
ESD测试失效
5
EMI测试失效 其他 噪声
EMI测试失效 LCM点亮时产生噪声
3 CELL端避让0.2mm(底部) 2 在背光底部增加PET FPC区域避空至少0.2mm,背光焊盘区域避空 2 至少0.4mm 2 膜材间隙(0.03~0.05mm) 2 FPC区域避空至少0.2mm,背光焊盘区域避空 只是0.4mm 2 IC处封硅胶不能覆盖IC 2 Cell底部与胶框避空0.3mm 选用耐压增光膜片(上片光耀KH27-95 2 下片光耀KH69-75) 2 选用粘性较好的黑黑胶(3G-BB650M) 2 黑白胶粘胶框至少0.7mm 2 选用粘性较好的黑黑胶(3G-BB650M) 2 采用粘性较好的胶(550R6BW),并做回型 结构 2 模具管控,注塑机台参数 2 选用粘性较好的黑黑胶(3G-BB650M) 2 2 2 3 2 3 2 3 3 3 3 3 2 2 3 2 2 2 2 2 2 2 1 2 2 选用低弹性FPC材料(无胶电解铜) 改善膜材搭配、膜材间隙 (0.03~0.05mm) 背光亮度参数设计(6000min) Cell透过率参数确认(4.8%typ) 测试Pattem确认调整 代码优化 选用对比度较好的偏光片(盛波) 代码优化 升压代码、GOA代码等调整 相关代码优化调整 相关代码优化调整 选用低温ACF、优化绑定条件 调整增光膜角度避免干涉条纹 选用雾面下偏光片 背光胶框掏料处理,确认TP泡绵尺寸 调整增光膜角度避免干涉条纹 和IC供应商一起check FPC原理 选用功耗表现较佳IC(HX8379C) 代码优化 和IC供应商一起check FPC原理 选用功耗表现较佳IC(HX8379C) 代码优化 LED原材管控(铃涛
标签及铭板 FMEA潜在失效模式及分析
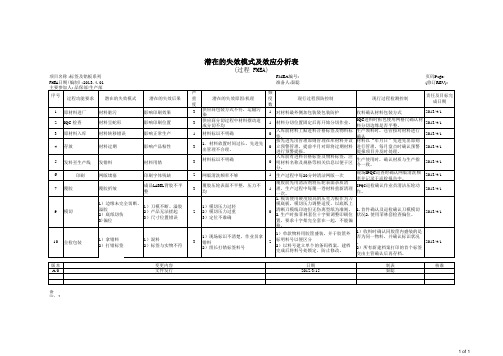
9
模切
1)边缘未完全切断、 1)刀模不断、溢胶 溢胶 2)产品无法搓起 2)底纸切伤 3)尺寸位置错误 3)偏位
2
0
10
全检包装
1)拿错料 2)打错标签
偏小
1)混料 2)标签与实物不符
3
1)现场标识不清楚,作业员拿 错料 2)组长打错标签料号
2
IQC进料时拆包使用网格尺确认材 2013-4-1 料分切边缘是否平整。 入库前材料上贴进料合格标签及物料标 生产领料时,仓管按对材料进行 2013-4-1 签。 确认 按先进先出管理原则管理在库材料并设 材料以“年月日”先进先出原则 立预警管理,提前半月对即将过期材料 进行管理,每月盘点时确认预警 2013-4-1 进行预警提报。 提报项目并及时处理。 入库前有进料合格标签及物料标签,注 生产使用时,确认材质与生产指 2013-4-1 明材料名称及规格等相关信息以便于区 令一致。 分。 现场IPQC巡查时确认网版清洗频 2013-4-1 生产过程中每20分钟清洁网版一次 率并记录于巡检报告中。 覆胶前先用清洁剂将压轮表面杂质清 IPQC巡检确认作业员清洁压轮动 2013-4-1 理,生产过程中每覆一卷材料重新清理 作。 一次。 1.模切使用硬度较高的压克力板作为刀 模底板,模切压力调整适度,以底纸上 清晰刀模线印迹但无伤离型纸为准则。 1.首件确认及巡检确认刀模模切 2013-4-1 2.生产时按菲林套位十字架调整印刷位 状况2.使用菲林套检查偏位。 置,要求十字架完全套在一起,不能偏 移。 1)收料时确认同胶筐内盛装的是 1)单款物料用胶筐盛装,并于胶筐外标 否为同一物料,并确认标识状况 明料号以便区分 2013-4-1 。 2)以料号建立单个的条码档案,建档完 2)所有新建档案打印的首个标签 成后将料号处锁定,防止修改。 交由主管确认后再存档。 日期 2012-3-15 制表 秦聪 核准
FMEA潜在失效模式及分析表格模版
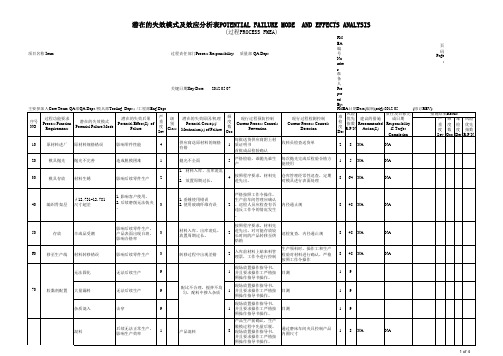
2
入库前材料上贴来料管 理票
生产领料时,操作工和生产 检验对材料进行确认
4
24
NA
NA
∮15.840-15.870 尺寸超差 140 外圆磨削
影响客户装配
4
1.砂轮磨损 2.零件装夹不到位
2
1. 定期维护保养磨床 2. 现场放置操作指导 书,并且要求操作工严 格按照操作指导书操作 。 3.确保砂轮无振动
工 AND EFFECTS ANALYSIS
现行过程检测控制 Current Process Controls Detection
FMEA编号Number: 页码Page: 准备人Prepared By: FMEA日期Data(编制(orig):2012.05 (修订REV): 责任及目标完 措施结果Result 难 风险 建议的措施 严 频 难 成日期 检 优先 Recommended Responsibility 重 度 检 度 指数 Action(S) 度 数 度 & Target Det R.P.N Sev Occ Det . Completion
2
生产领料时,操作工和生产 检验对材料进行确认,严格 按照工作令操作 目测
8
48
NA
NA
无法固化
无法后续生产
9
1
1
9
70
胶黏剂配置
大量漏料
无法后续生产
9
配比不合理,搅拌不均 匀,配料中掺入杂质
1
目测
1
9
杂质混入
击穿
9
1
目测
1
9
混料
后续无法正常生产, 影响生产效率
1
产品混料
8
通过磨床车间夹具控制产品 内圆尺寸
pfmea分析表
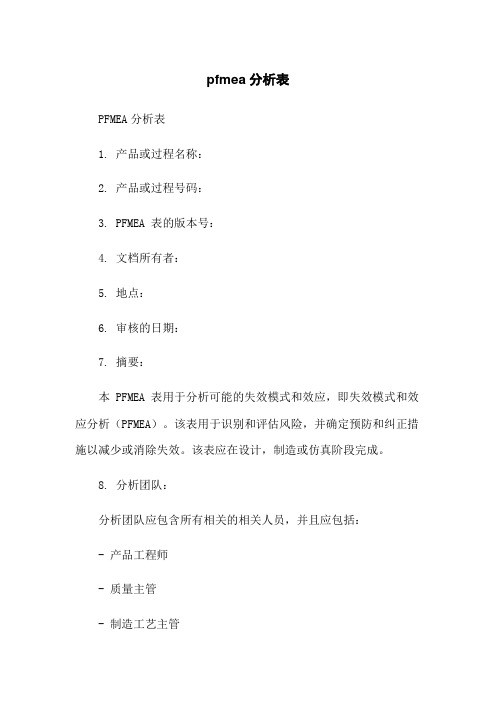
pfmea分析表PFMEA分析表1. 产品或过程名称:2. 产品或过程号码:3. PFMEA 表的版本号:4. 文档所有者:5. 地点:6. 审核的日期:7. 摘要:本 PFMEA 表用于分析可能的失效模式和效应,即失效模式和效应分析(PFMEA)。
该表用于识别和评估风险,并确定预防和纠正措施以减少或消除失效。
该表应在设计,制造或仿真阶段完成。
8. 分析团队:分析团队应包含所有相关的相关人员,并且应包括:- 产品工程师- 质量主管- 制造工艺主管- 安全主管- 故障分析师- 设计负责人- 制造工程师- 客户服务代表9. 步骤:步骤1:识别过程、组件或子组件- 识别过程、组件或子组件,该过程对产品性能,质量和可靠性的影响最大- 如果有多个过程,组件或子组件,请在单独的表中进行分析步骤2:确定失效模式- 对于每个识别的过程、组件或子组件,列出可能的失效模式步骤3:确定失效效应- 确定每种失效模式的影响,包括可能导致的产品或过程故障、风险和/或安全问题步骤4:确定失效严重性(S)- 确定失效对于产品功能和可靠性的影响严重性级别为S步骤5:确定失效发生概率(O)- 确定失效的发生概率级别为O步骤6:确定失效检出度(D)- 确定失效的检出度级别为D步骤7:计算风险优先级数(RPN)- 计算风险优先级数(RPN),即 RPN = S × O × D步骤8:制定预防和纠正措施- 针对高优先级数(RPN)的失效模式制定预防和纠正措施步骤9:跟踪措施有效性- 跟踪预防和纠正措施的实施,以确保其有效性。
10. 列举本文档所涉及简要注释如下:- 失效模式和效应分析(PFMEA):用于确定可能的失效模式和效应并采取纠正措施的过程。
- 风险优先级数(RPN): PFMEA 表中计算风险的指标。
RPN = S × O × D。
11. 列举如下本文档所涉及的法律名词及注释:无总结本文介绍了 PFMEA 分析表,该表用于识别和评估风险,并确定预防和纠正措施以减少或消除失效。
FMEM过程潜在失效模式及效应分析

3 63
3 63
2 28 3 42 3 36 3 36 2 36 2 48
2 36
2 24 2 48 2 36 3 72
降低射速 加强模温机点检
提高射速 提高射压 生技擦拭 提高射嘴温度 修模处理 延长保压时间 提高射压 降低保压压力、时间 调整顶针后退速度 修模处理 加设排气槽 降低射速 降低射压
第 1页 共4页
措施结果
采行措施
严发难 重 生 检 RPN 度度度
色差不良 影响产品外观 7 ★
原料本身不良
2
色板不符合
2
材质不符 影响正常生产 7 ■
外包商疏忽
2
进料/满足 异点、杂质 影响正常生产 6 ■
原料本身不良
2
生产要求
数量不符 实物与账面不符 7 ●
外包商疏忽
2
IQC检验 IQC检验 IQC检验 IQC检验
成型 成型
烘料员加强点检 烘料员加强点检
7 2 3 42 7 2 3 42
模具温度过低
2
产品表面流痕
影响产品外观, 客户不满意
6
★
料管温度过低 进胶与注胶道过小
3 3
进胶与注胶道有粘料现象 3
射出速度过快
3
产品变形(弯 曲、平整度、
凹塘)
影响产品实配, 功能性受损
7
★
射出压力过高 模具温度过低 公母模温度配合不当
成型生技
成型生技
成型生技
成型生技 成型生技 成型生技 成型生技 成型生技 成型生技
模具部
IQC 成型 成型 成型
第 1页 共4页
措施结果
采行措施 降低射速
严发难 重 生 检 RPN 度度度
液晶显示器PFMEA制程潜在失效模式及效应分析表
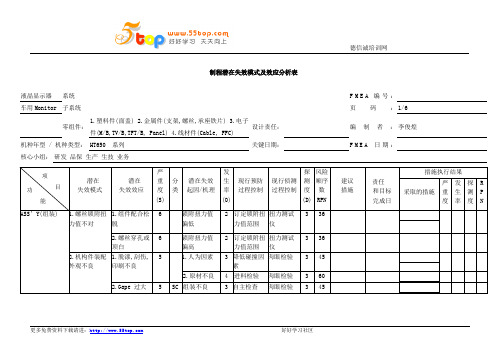
德信诚培训网制程潜在失效模式及效应分析表液晶显示器系统F M E A编号:车用Monitor 子系统页码:1/6零组件:1.塑料件(面盖) 2.金属件(支架,螺丝,承座铁片) 3.电子件(M/B,TV/B,TFT/B, Panel) 4.线材件(Cable, FFC)设计责任:编制者:李俊煌机种年型 / 机种类型: HT650 系列关键日期:F M E A日期:核心小组:研发品保生产生技业务德信诚培训网制程潜在失效模式及效应分析表液晶显示器系统F M E A编号:车用Monitor 子系统页码:2/6 零组件:半成品机台设计责任:编制者:机种年型 / 机种类型: HT650 系列关键日期:F M E A日期:核心小组:研发品保生产生技业务德信诚培训网制程潜在失效模式及效应分析表(量试 PFMEA)液晶显示器系统F M E A编号:车用Monitor 子系统页码:3/6 零组件:设计责任:编制者:半成品机台机种年型 / 机种类型: HT650 系列关键日期:F M E A日期:核心小组:研发品保生产生技业务德信诚培训网制程潜在失效模式及效应分析表(量试 PFMEA)液晶显示器系统F M E A编号:车用Monitor 子系统页码:4/6 零组件:半成品机台设计责任:编制者:机种年型 / 机种类型: HT650 系列关键日期:F M E A日期:核心小组:研发品保生产生技业务德信诚培训网制程潜在失效模式及效应分析表(量试 PFMEA)液晶显示器系统F M E A编号:车用Monitor 子系统页码:5/6 零组件:设计责任:编制者:半成品机台,纸箱,配件,标签机种年型 / 机种类型: HT650 系列关键日期:F M E A日期:核心小组:研发品保生产生技业务德信诚培训网制程潜在失效模式及效应分析表(量试 PFMEA)液晶显示器系统F M E A编号:LB00070100X-20030430 车用Monitor 子系统页码:6/6零组件:成品机台设计责任:编制者:机种年型 / 机种类型: HT650 系列关键日期:F M E A日期:核心小组:研发品保生产生技业务。
FMEA管理-范本
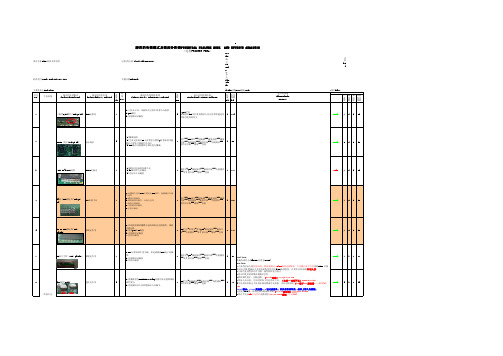
FMEA编号Number:页码Page:准备人Prepared By:严重度频度数难检度风险优先指数1三极管Q453移位(JT37A2MB)HDMI无联动71.上料未卡好,导致贴片过程中吸著中心偏移2.AOI漏检3.功能测试站漏检61.AOI拦检2.測試站SOP中有要求測試人員注意菜單處是否有綠色底紋的英文3126CLOSE733632IC150 反向(JT37A2 MB)无法烧录6(1)機器拋料(2)生產交接班時OP人員將當天散料A材重新使用脆盤后正常貼片導致打件反向(3)DIP後段功能測試也無法進行攔截。
5裂片---DIP插件---過錫爐---爐後接板---爐後目檢---錫面檢修---錫面目檢---功能測試---零件面目檢---總檢---包裝390CLOSE632363 U51 29-30pin连锡HDMI1无输出7(1)维修时造成的短路不良(2)FT测试站人员漏检(3)总检站人员漏检5维修室-AOI-錫面檢修---錫面目檢---功能測試---零件面目檢---總檢---包裝5175OPEN733635RF端子PIN脚连焊(JT37A2MB)DTV画面不良71.此機種生產時H101位置是由DIP插件,過鍋爐后有幾率連焊2.爐後目檢漏检3.錫面檢修站漏失,未進行拉焊4.錫面目檢漏检5.功能测试站漏检6.总检站漏检5裂片---DIP插件---過錫爐---爐後接板---爐後目檢---錫面檢修---錫面目檢---功能測試---零件面目檢---總檢---包裝3105CLOSE722286IC U1 PIN脚连锡(JT24keypad)按键无作用71.印刷設備擦拭機構出現故障無法自動擦拭,導致印刷短路2.重流AOI站OP漏检3.功能测试站漏检4.总检站漏检4AOI拦检-维修室-重流AOI-錫面檢修---錫面目檢---功能測試---零件面目檢---總檢---包裝4112CLOSE722287CN接口空焊(JT24keypad)按键无作用71元件維修不當少錫,易造成插拔CN1端子時錫裂。
潜在失效模式与效应分析(PFMEA)
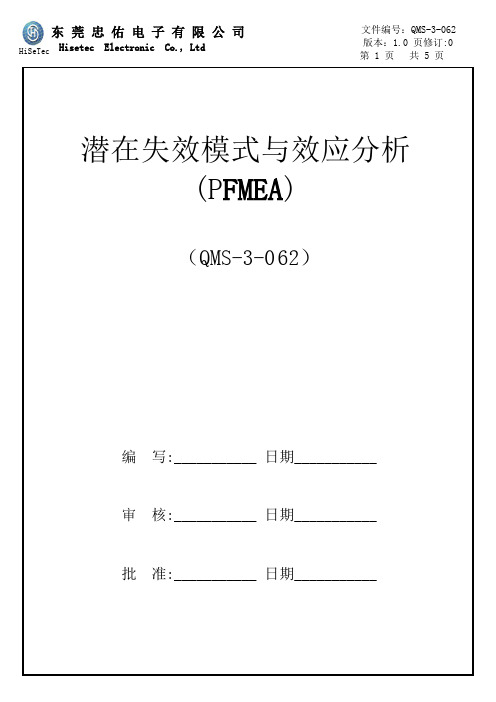
潜在失效模式与效应分析(P FMEA)(QMS-3-0 62)编写:___________ 日期___________审核:___________ 日期___________批准:___________ 日期___________修订记录序号修订时间修订页码修订内容修订前版/页次修订后版/页次修订者1 2014/2/28 全文新增第1.0版第1.0版朱冠一.目的:利用可靠性分析技术对产品.制程.设备进行分析,以求在设计阶段早期发现问题,及早谋求解决措施。
二.适用范围:(1)产品开发及改善。
(2)制程开发及改善。
(3)设备开发及改善。
三.定义:(1) PFMEA : (Potential Failure Mode & Effect Analysis) 潜在失效模式与效应分析。
(2)严重度(Severity) :恒量失效的影响程度。
(3)发生率(Occurrence) :失效发生的几率。
(4)难检度(Detection) :在现行的控制措施下,侦测失效发生的能力。
(5)风险优先数(RPN)= 严重度(S) *发生率(O) *难检度(D)。
四 . PFMEA分析流程:四 . PFMEA分析流程(接上表):序号作业流程权责作业内容参考文件相关表单序号作业流程权责作业内容参考文件相关表单1 客户总经理室工程部品管部1-1.由客户/工程部/总经理室相关部门人员审查方案可靠性;1-2.工程部经理或以上人员核准;1-3.品管部分别与工程部.生产部组成PFMEA团队。
《品质手册》《管理责任控制程序》《合约控制程序》《文件控制程序》《可靠度工程评估报告》2工程部生产部2-1. 工程部.生产部执行人分别填写开发段.改善段PFMEA2-2 对产品.制程.设备可能出现的失效逐条列出《文件控制程序》《预防措施控制程序》《工程变更控制程序》《潜在失效模式与效应分析》可靠性评估潜在失效模式OK3SOD分析计算风险优先数优先改善决定建议改善措施改善实施效果确认工程部生产部3-1 工程部,生产部执行人分别对失效模式的发生率,难检度,严重度进行评估《文件控制程序》《预防措施控制程序》《潜在失效模式与效应分析》4 工程部生产部4-1 工程部,生产部执行人依据SOD分析计算风险优先数(RPN=S*O*D)《文件控制程序》《预防措施控制程序》《潜在失效模式与效应分析》5 工程部生产部5-1工程部,生产部执行人依据风险优先数决定优先改善的失效模式(RPN ≥ 90)《文件控制程序》《预防措施控制程序》《潜在失效模式与效应分析》6 工程部生产部品管部6-1工程部,生产部执行人对决定优先改善的失效模式提出建议改善措施6-2 工程部,生产部. 品管部主管签核《文件控制程序》《预防措施控制程序》《品质手册》《管理责任控制程序》《潜在失效模式与效应分析》7 工程部生产部7-1 工程部,生产部执行人在设计,改善方案中纳入建议改善措施《文件控制程序》《预防措施控制程序》《潜在失效模式与效应分析》8 品管部工程部生产部8-1 设计,改善项目实施后,对予改善方案品管部.工程部.生产部确认处理结果《文件控制程序》《预防措施控制程序》《品质手册》《管理责任控制程序》《潜在失效模式与效应分析》9 工程部生产部9-1 工程部,生产部执行人将PFMEA入文件控制中心《文件控制程序》《预防措施控制程序》《潜在失效模式与效应分析》标准化五、附录:(1)严重度(S)划分标准等级/评分划分标准1 几乎不会对产品有任何影响,即使有影响,客户亦不会注意。
FMEA潜在失效模式及後果分析(第三版)sim
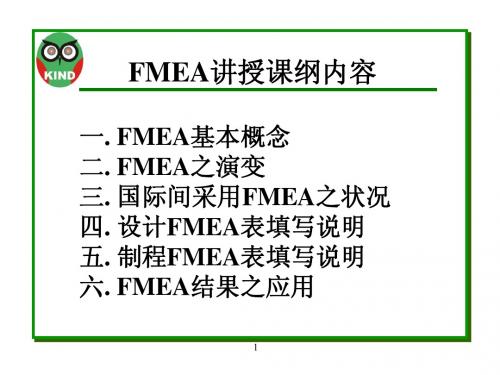
作疲勞度評 估
品管 品管 工程
8 3 6 144 8 3 4 96 8 2 4 64
12
設計FMEA表(範例4)
系統 子系統 零組件: PAPER 設計責任: 車型/年份: 1350電氣膠帶 生效日期:85.10.25 核心小組: 如附表
項目 功能 潛在失 效模式 潛在失 效效應
FMEA編號: 1350 頁次: 1 of 1 準備者: FMEA日期 (製訂) 85.10.10(修訂)
严重度
10 9
很高
高 中等 低 很低 轻微 很轻微 无
车辆/项目不能运行(丧失基本功能)
车辆/项目可运行,但性能下降,顾客非常不满意 车辆/项目可运行,但舒适性/方便性项目不能运行,顾客不满意 车辆/项目可运行,但舒适性/方便性项目的性能下降,顾客有些不满意 配合和外观/尖响和卡嗒响等项目不舒服。大多数顾客(75%以上)能感觉 到有缺陷。 配合和外观/尖响和卡嗒响等项目不舒服。50%的顾客能感觉到有缺陷。 配合和外观/尖响和卡嗒响等项目不舒服。有辨识能力的顾客(25%以下) 能感觉到有缺陷。 无可辨别的后果 18
負責人 與 日 期
執行結果 採行措施 S O D RPN
冷媒 造 成 冷 氣 洩漏 不 冷 或 將高壓高溫 A/C 不 作 氣態冷煤, 動 變為高壓中 溫液態冷媒
一般可靠 度 8 項目實驗 同上 7
7
4
196
7
‧振動接點 破損
6
同上
5
210
依測試報告編 加嚴耐腐蝕 實驗課 號 :1212 變更 測試 材質 依測試報告編 加嚴高溫測 號 :3212 容許 試 彎曲 2-13mm 實驗結果可接 受 5%變異 加嚴振動測 試 以上需作實車 作動耐久
PFMEA分析标准表格模版

(过程PROCESS FMEA)
项目名称 Item: 主要参加人Core Team: 序号 NO. 过程功能要求 潜在的失效后果 潜在的失效模式 Process Function Potential Effect(S) of Potential Failure Mode Requirements Failure 严 级 重 别 度 Class Sev 潜在的失效原因/机理 Potential Cause(s)/ Mechanism(s) of Failure 频 现行过程预防控制 度 Current Process Controls 数 Prevention Occ 过程责任部门Process Responsibility: 关键日期Key Date:
准备人PrepareBiblioteka by审核Checked by
批准Approval by
1 of 1
工
现行过程检测控制 Current Process Controls Detection
措施结果Result 严 频 难 重 度 检 度 数 度 Sev Occ Det
风险 优先 指数 R.P.N.
out of 0.2 A spec.
偏小
版本 Rev. A0
变更内容Comment 新制/New
日期 Date
AND EFFECTS ANALYSIS
FMEA编号Number: 准备人Prepared By: FMEA日期Data(编制(orig): 责任及目标完 难 风险 建议的措施 成日期 检 优先 指数 Recommended Responsibility 度 Action(S) & Target Det R.P.N . Completion 页码Page:
PFMEA过程潜在失效模式效应分析(玲珑电子范本)

1.0 目的PFMEA是认可或评价产品/过程中潜在的失效及失效后果,找出能够避免或减少这些潜在失效发生机会的措施,减少开发风险和过程损失,将生产可以满足客户品质需求的产品的过程形成规范的文件。
2.0 范围适用于公司所有产品过程设计的过程FMEA。
3.0术语和定义潜在失效模式:所谓潜在失效模式是指部件、子系统或系统有可能会未达到或不能实现项目/功能栏中所描述的预期功能的情况(如预期功能失效)。
潜在失效的后果:潜在失效的后果定义为顾客感受到的失效模式对功能的影响。
严重度(S):严重度是一给定失效模式最严重的影响后果的级别。
严重度是单一的FMEA范围内的相对定级结果(附表一)。
发生度(O):发生度是指某一特定的起因/机理在设计寿命内出现的可能性(附表二)。
探测度(D):探测度是与设计控制中所列的最佳探测控制相关联的定级数(附表三)。
风险顺序数:风险顺序数是严重度(S)、频度(O)和探测度(D)的乘积RPN=(S)× (O)× (D)。
4.0权责4.1 项目质量:负责组织研发项目部、生产部、工程部、质量部中熟悉工序、经验丰富的成员组成PFMEA核心小组,FMEA小组可以通过产品的使用者操作过程和生产工艺流程,对过程进行潜在失效模式的评审。
FMEA小组可以使用头脑风暴等方法进行评审,需要关注过去已经发生的问题:包括客户投诉,不合格品,质量问题等,并整理成对应类型产品的《过程失效模式分析》。
4.2 质量部:负责编制本规定,负责公司教育培训,综合、协调各部门计划,组织和主导PFEMA各环节实施。
4.3 研发部和生产部:配合执行PFEMA各环节实施。
4.4 工程部和质量部PQE:负责根据产品分类收集和积累过程失效模式清单。
5.0作业内容5.1. FMEA编号:填入FMEA 文件编号,以便查询。
5.1.1 编制者:填入负责编制FMEA的工程师的姓名,以便查询称。
5.1.2 产品类型:填入所分析的设计将要应用和/或影响的产品类型。
潜在的失效模式与效应分析

潜在的失效模式与效应分析潜在的失效模式与效应分析(FMEA)(Failure Mode and Effects Analysis)是一种用于识别和评估潜在失效模式及其对系统或过程性能的影响的方法。
它被广泛应用于各个行业,包括制造业、汽车工业、医疗保健等,用于提前预防潜在的问题和缺陷,减少风险和成本。
FMEA方法通过系统地识别可能的失效模式、评估其严重性、确定其潜在的原因和效应,并制定相应的预防措施和应对措施来提升产品和过程的质量。
具体而言,FMEA步骤包括:1.确定分析对象:确定要进行FMEA分析的系统、产品、流程或部件。
2.建立团队:组建由跨职能团队成员组成的FMEA分析团队,以确保全面的视角和专业知识。
3.描述分析对象:对分析对象进行详细描述,包括功能、特性、运行条件等。
4.列举失效模式:通过头脑风暴或专家判断,列举所有可能的失效模式。
5.评估严重性:评估每个失效模式对系统或过程性能的影响,包括安全性、可靠性、维修性、性能等方面。
6.确定原因:分析每个失效模式的潜在根本原因,通过鱼骨图、5W1H分析等方法找出原因。
7.评估概率:评估每个失效模式发生的可能性,可以借助历史数据、统计分析等方法。
8.制定预防措施:针对每个失效模式,制定预防措施来减少失效概率或降低严重性。
9.制定应对措施:针对每个失效模式,制定应对措施,包括监测、检测、报警、维修等,以减少影响。
10.重新评估:根据预防和应对措施的实施情况,重新评估每个失效模式的概率和严重性,并对措施进行迭代改进。
FMEA方法的优势在于可以提前预防潜在的问题和缺陷,减少风险和成本。
通过系统地分析潜在失效模式和其效应,可以及早采取措施进行风险管理和改进,提高产品和过程的质量。
此外,FMEA还能够改善跨职能团队的沟通和协作,增强问题解决能力和质量意识。
然而,FMEA方法也存在一些潜在的局限性。
首先,FMEA方法无法准确预测未来的潜在失效模式和效应,而只能基于现有的经验和知识进行分析。
失效模式及后果分析(FMEA)表
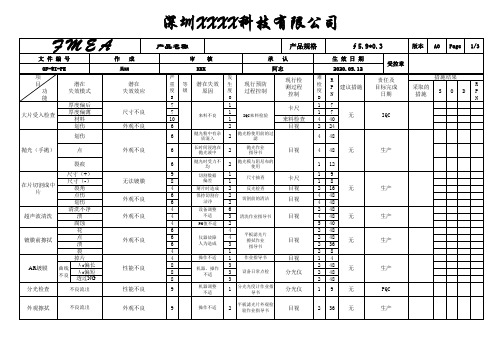
生产
曲线 不良
λ0偏长 λ0偏短 透过NG
分光检查
不良流出
无法镀膜 外观不良 外观不良 外观不良
性能不良 性能不良
外观擦拭
不良流出
外观不良
产品名称
产品规格
∮5.9*0.3
版本 A0 Page 1/3
审核
承认
XXX
阿志
严
发
重 等 潜在失效 生
度级
原因
度
S
O
现行预防 过程控制
7
1
7 10
来料不良
1 1
IQC来料检验
目视
4
PH值不适
2
6
4
6 6
仪器故障
4
人为造成
3
平板滤光片 擦拭作业 指导书
目视
4
1
4
操作不适
1
作业指导书
目视
8
3
8
机器、操作 不适
3
设备日常点检
分光仪
8
3
9
机器调整 不适
1
分光光度计作业指 导书
分光仪
生效日期
2020.05.12
难R
检 度 D
P 建议措施 N
17
17 4 40
无
2 24
4 48
4 48 无
6
2
6
抛光粉中有杂 质混入
2
抛光粉使用前的过 滤
6
长时间浸泡在 抛光液中
2
抛光作业 指导书
现行检 测过程
控制
卡尺 来料检查
目视
目视
6
抛光时受力不 均
2
抛光模与阻尼布的 使用
注塑玩具产品潜在的失效模式及效应分析表(注塑玩具产品风险评估表)
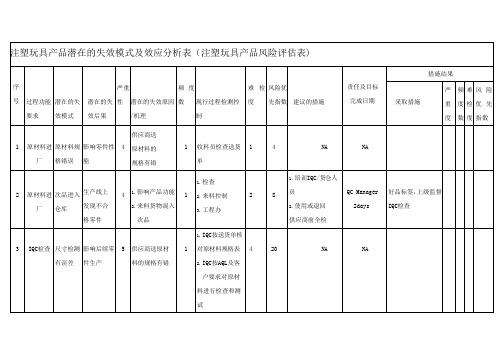
喷油/移印部利器
易碎品
断针、剪刀、碎玻璃掉入产品
导致产品污染
4
监管不到位,造成利器、易碎品混入产品
3
制订利器、玻琉、首饰管控程序
4
32
1、培训利器操作人员
2、管理员定期巡查
每天
1、工厂使用利器发入记录
2、工厂使用易碎品检查记录
21
喷油/移印部生物
1、虫鼠损害
2、苍蝇粪便、尸体
污染产品
4
长期不清洁
传送前PQC确认包装正确后才可能传送
2
16
NA
NA
30
包装全检
零件外观项目检查有误
影响客户使用
2
操作工对外观要求不明确
2
QC对零件进行抽检
1
4
NA
NA
31
包装全检
包装有误
造成零件外观不良
2
操作工对包装要求不明确
2
QC对零件进行抽检
1
4
NA
NA
32
装配QC检查
次品进入仓库
生产线上发现不合格零件和包装成品
5
供应商送原材料的规格有错
1
1.IQC按送货单核对原材料规格表
2.IQC按AQL及客户要求对原材
料进行检查和测试
4
20
NA
NA
4
移至原材料仓
材料转移错误
影响后续零件生产
3
材料标识不明确
2
生产领料时,操作工和QC对材料进行确认
1
6
NA
NA
5
存放
材料生锈
影响后续零件生产
4
1.材料入库、出库淋雨
2.放置周期过长
FMEA潜在失效模式及分析表格模版
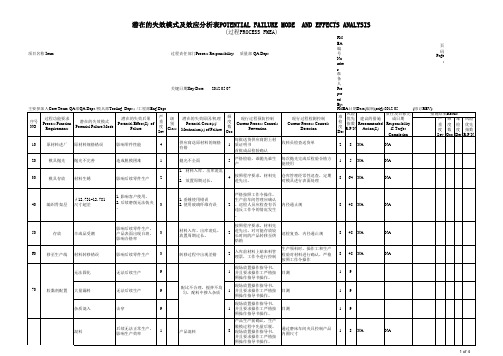
(过程PROCESS FMEA)
项目名称 Item: 主要参加人Core Team: QA部QA Dept./模具部Tooling. Dept.; /工程部Eng.Dept. 序号 NO. 过程功能要求 Process Function Requirements 潜在的失效模式 Potential Failure Mode 潜在的失效后果 Potential Effect(S) of Failure 严 级 重 别 度 Class Sev 4 潜在的失效原因/机理 Potential Cause(s)/ Mechanism(s) of Failure 供应商送原材料的规格 有错 抛光不全面 1. 材料入库、出库凌乱 。 2. 放置周期过长。 频 现行过程预防控制 度 Current Process Controls 数 Prevention Occ 1 每批送货供应商附上材 质证明书 首批成品检验确认 严格检验,谁抛光谁生 产 按照程序要求,材料先 进先出。 严格按照工作令操作。 生产前车间管理应确认 。巡检人员应检查有否 违反工作令的情况发生 。 按照程序要求,材料先 进先出。对可能存放较 长时间的产品转移至烘 焙箱 入库前材料上贴来料管 理票,工作令进行控制 现场放置操作指导书, 并且要求操作工严格按 照操作指导书操作。 现场放置操作指导书, 并且要求操作工严格按 照操作指导书操作。 现场放置操作指导书, 并且要求操作工严格按 照操作指导书操作。 产品生产前确认,生产 脱模过程中先量后脱。 现场放置操作指导书, 并且要求操作工严格按 照操作指导书操作。 控制真空度。现场放置 操作指导书,并且要求 操作工严格按照操作指 导书操作。 每日记录烘箱温度,升 温时间,固化时间,严 格按照工作令进行生产 活动。现场放置操作指 导书,并且要求操作工 严格按照操作指导书操 作。芯棒先行加热 严格按照工作令要求加 温 过程责任部门Process Responsibility: 关键日期Key Date: 2012.05.07 质量部 QA Dept.
- 1、下载文档前请自行甄别文档内容的完整性,平台不提供额外的编辑、内容补充、找答案等附加服务。
- 2、"仅部分预览"的文档,不可在线预览部分如存在完整性等问题,可反馈申请退款(可完整预览的文档不适用该条件!)。
- 3、如文档侵犯您的权益,请联系客服反馈,我们会尽快为您处理(人工客服工作时间:9:00-18:30)。
3 4 3
2 2 2
1 3 1
6 24 6
NA NA NA
NA NA NA 做好材料标识
6
注塑生产
生产次品
影响后续零件生产 生产线上发现不合格 零件 影响后续零件生产 影响后续零件生产
4
2
4
32
NA 1.培训QC人员 2. 次品报废 NA NA
NA 品质部经理 2天 NA NA 做好合格品标签,上 级监督,IQC检查
偏小 out of out 0.2 spec. of A spec. 偏小
影响客户使用
操作工对外观要求不明 确 操作工对包装要求不明 确 影响产品功能 人员失误 影响产品出货 材料标识不明确 货仓设施设备问题(是 否漏水等) 人员失误
2 2 2 1 2 2 1 1
QC对零件进行抽检
NA NA 品质部经理 2天 NA 品质部经理 2天 NA NA NA 做好合格品标签,上 级监督,IQC检查
7 8 9
注塑QC检查 移至半成品仓 移至包装部
次品进入仓库 胶件转移错误 胶件转移错误 1.用错油漆、转印膜 2.印刷印错颜色 3.印刷次品 次品进入仓库 胶件转移错误 胶件转移错误 组装次品/功能不良 产品表面未清洗干净 包装错误
4 3 3
1 2 2
2 1 1
8 6 6
10
产品印刷/转印
影响后续零件生产 生产线上发现不合格 零件 影响后续零件生产 影响后续零件生产
序号
过程功能要求
潜在的失效模式
潜在的失效后果
潜在的失效原因/机理
现行过程检测控制
1
原材料进厂 原材料进厂
原材料规格错误
影响零件性能 生产线上发现不合格 零件
供应商送原材料的规格 有错 1.影响产品功能 2.来料货物混入次品 供应商送原材料的规格 有错 材料标识不明确 1. 材料入库、出库 2. 放置周期过长 材料标识不明确 机器参数不正确/模具缺 陷 影响产品功能 胶件标识不明确 胶件标识不明确 人员操作失误,工程资料 错误 影响产品外观 胶件标识不明确 胶件标识不明确 人员操作失误 人员操作失误 包装方式不明确
4
2
16
NA 1.培训QC人员 2. 次品报废 NA NA NA NA
NA
NA 品质部经理 2天 NA NA NA NA
NA
11 12 13 14 15 16
印刷QC检查 移至半成品仓 移至包装部 半成品组装 清洁 半成品包装
3 3 3 3
3 2 2 2 2
2
1 1 1 2 1
2
9 6 6 12 4
措施结果Result 建议的措施 责任及目标完 成日期 采取措施 严 重 度 Sev 频 度 数 Occ 难 检 度 Det 风险 优先 指数 R.P.N.
17 18 19 20 21 22 23 24
包装全检
零件外观项目检查有 误 包装有误 次品进入仓库 装错货/装货比例错 次品进入仓库 成品转移错误 成品损坏 成品转移错误
广东有限公司 潜在的失效模式及效应分析表(过程)
项目名称: 主要参加人: FMEA编号: 准备人: FMEA日期、编制: 严 重 度 Sev 4 频 度 数 风险 难检 优先 度 指数 Det R.P.N 1 4 NA 措施结果Result 建议的措施 责任及目标完 成日期 采取措施 严 重 度 Sev 频 度 数 Occ 难 检 度 Det 风险 优先 指数 R.P.N.
1
收料员检查送货单 1.检查 2.来料控制 3.仓库管理 1.IQC按送货单核对原材料规格表 2.IQC按AQL及客户要求对原材料进 行检查和测试 生产领料时,操作工和QC对材料进 行确认 QC复查在库 生产领料时,操作工和QC对材料进 行确认 开机前,对模具及机器进行检查 1.检查 2.工程办 生产领料时,杂工及货仓人员对胶 件进行检查核对 生产领料时,杂工和货仓人员对材 料进行确认。 对操作人员进行培训,工程资料发 放前仔细核对 1.检查 生产领料时,杂工及货仓人员对胶 件进行检查核对 生产领料时,杂工和货仓人员对材 料进行确认 对操作人员进行培训 QC对清洁度进行检测。 传送前PQC确认包装正确后才可以传 送。
16
做好合格品标签,上 级监督,IQC检查 做好半成品标识
影响客户使用 造成零件表面的压伤
2
4
序号
过程功能要求
潜在的失效模式
潜在的失效后果
严 重 度 Sev 2 2 3 5 3 3 5 5
潜在的失效原因/机理
频 度 数
现行过程检测控制
风险 难检 优先 度 指数 Det R.P.N 1 1 1 1 1 1 2 2 4 4 6 5 6 6 10 10 NA NA
包装全检 装配QC检查 装箱 包装QC检查 移至成品仓 存放 送至客户
造成零件外观不良 生产线上发现不合格 零件和包装成品 影响客户使用 生产线上发现不合格 包装成品 影响客户使用 影响客户使用 影响客户使用
偏小
QC对零件进行抽检 1.检查 2.工程办 对操作人员进行培训 1.核对箱唛及装箱比例资料 货仓人员对材料进行确认 QC复查在库 对人员进行培训/ 出货时OQC对产品 进行确认
NA 做好合格品标签,上 级监督,IQC检查
1
次品进入仓库
4
1
2
8
1.培训IQC/货仓人员 品质部经理 2.使用或退回供应商前全 2天 检 NA NA
2
IQC 检查
尺寸检测有误差
影响后续零件生产
5
1
4
20
3 4 5
移至原材料仓 存放 移至注塑部
材料转移错误 材料污染 材料转移错误
偏小
影响后续零件生产 影响后续生产 影响后续零件生产
1.培训QC人员 2. 次品报废 NA 培训QC人员 NA NA NA
产品图片:
编制:
审批:
日期: