layout(工厂布局)
工业工程 工厂layout布局设计

yout 计划的基础情报
部门 市场/销售
生产数量 产品的销售价 SVC 部品 产品的季节性/ 周期性
设计/工程
BOM 装配工程图 产品图纸 新产品开发日程
经营管理/企划
库存政策 投资政策 新产品开发计划 自制/外协决策 部门间相互关系 Feasibility History
必须情报
yout计划顺序体系
柔韧性研究, 用布局变更改善 现象问题的可能 水平是?
前题条件 其它方法的 改善方案
决定布局改善的 阶层/范围/水平 -P-Q -范围 -level
设定改善目标
布局变更/改善的 效果推导 第二层问题明确化 推出负反映效果
布局改善 项目选择
环境条件
-上流阶层 -管理方针 -管理体系
限制条件 Project 推进计划
Check Mark
6 5,1 4 11 1 10
5
14 1,3 4,2,1,9 12,13 2,3,14 2,6
6
9 3,10 7
10
2,9 4 1
11
9,14
2
6 2,4 5,9,12 13,10 1 9,11, 13,14 3,7
1
4,5,12 6,8 14 4,8
8
9,12,13
3
6 12 9,12,13 13,14 5,9,12 13,14 9
4
1,5 13
7
14
Space Requirement Planning
9
1,4
2,3,5 6,8,10 9,13
12
4
1,2,3 5,8 9,12,14
14
1,4,5 6,8 7,11 1,4
13
layout(工厂布局)(课堂PPT)
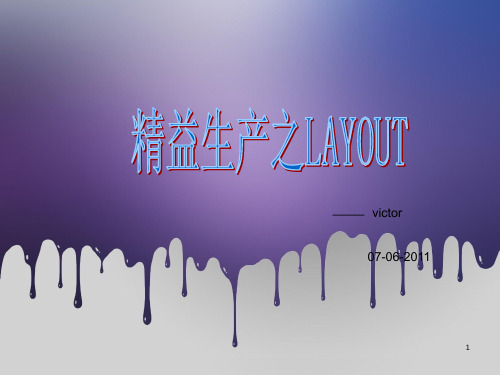
2020/4/7
4
种类
目的
特征程分析
的工艺流程
作业流程分 主要分析作业
析
者的作业流程
2020/4/7
多人通过多 台设备制造 同一产品
一人通过不 同设备或不 同工序,制造 多个产品的 过程
(1).改变包装作业流 程
打保证书
贴标签
品 质 部 出 库
2020/4/7
数外 搬
输
量观 运
入
检检 至
机
查查 电
身
脑
号
处
包
传
封
装
送
箱
加
工
改善后包装作业流程图
搬储 运存 至 成 品 仓
17
2.改变车间布局
品质部开关盒储存区
辅料存放区
包装车间开关盒 临时存放区
电脑输入出
保
证 书
包装LINE A
打
印
包装LINE B
(1).Leadtime
A.Leadtime的定义
从客户下订单到工厂交货,这个过程所花费的时间就是leadtime, 即完成某项目标所花费的流程时间
B科特尔法则
Leadtime=存货数量×生产节拍或存货数量×生产能力
C. 生产节拍
生产节拍是指每生产一个产品所需要的间隔时间
例如:一台设备的生产能力是每小时生产120个产
P4
P6
P9
P5
P7
P8
P10
工序8
产品分族矩阵
2020/4/7
33
生产线排单: Line A:生产P1产品 Line B生产P2产品 Line C生产P3产品 Line D生产P4 P6 P9产品 Line E生产P5 P7产品 Line F生产P8 P10产品
layout是什么意思.

layout是什么意思
layout是什么意思
layout
[‘lei.aut]
n.
1、规划, 设计, (书刊等)编排, 版面, 配线, 企划, 设计图案, (工厂等的)布局图
2、版面设计
Layout是属于动画专用名词,也是比较少见的工作,在工作性质上接近中文的“构图”,只有在一些剧场版作品可能采用,例如设计多层次背景,令每层背景移动速度不同,就能表现出逼真写实的远近距离感。
而画Layout的人必须在脑海里意识到摄影机的存在,从摄影机的观点去看场景里的一草一木,然后将这些画面详细地画下来。
这个工作,主要是弥补不大会画图的导演所画的分镜表,将杂乱简略的画面仔细的呈现出来,作为日后原画、动画、背景、色指定等等的依据。
在押井守的作品,例如机动警察剧场版、机动警察剧场版2、攻壳机动队等等,都是运用大量Layout的实例,而特色就是“用2D的作画也能精确表现3D的视觉效果”。
PCB layout
这是。
Layout规划经验谈
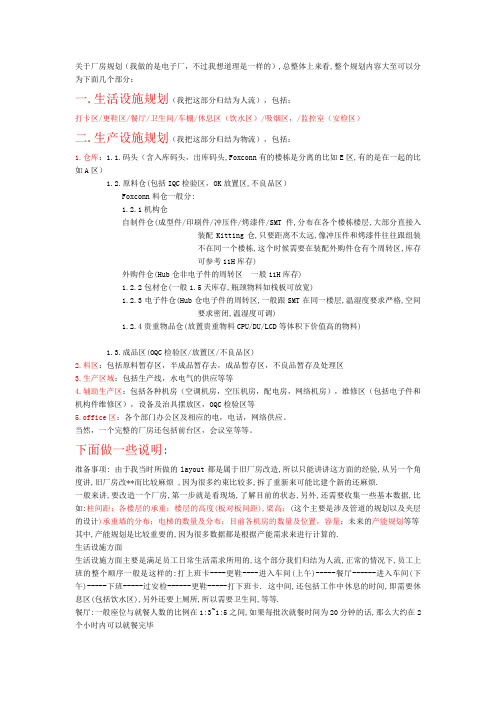
关于厂房规划(我做的是电子厂,不过我想道理是一样的),总整体上来看,整个规划内容大至可以分为下面几个部分:一.生活设施规划(我把这部分归结为人流),包括:打卡区/更鞋区/餐厅/卫生间/车棚/休息区(饮水区)/吸烟区,/监控室(安检区)二.生产设施规划(我把这部分归结为物流),包括:1.仓库:1.1.码头(含入库码头,出库码头,Foxconn有的楼栋是分离的比如E区,有的是在一起的比如A区)1.2.原料仓(包括IQC检验区,OK放置区,不良品区)Foxconn料仓一般分:1.2.1机构仓自制件仓(成型件/印刷件/冲压件/烤漆件/SMT件,分布在各个楼栋楼层,大部分直接入装配Kitting仓,只要距离不太远,像冲压件和烤漆件往往跟组装不在同一个楼栋,这个时候需要在装配外购件仓有个周转区,库存可参考11H库存)外购件仓(Hub仓非电子件的周转区一般11H库存)1.2.2包材仓(一般1.5天库存,瓶颈物料如栈板可放宽)1.2.3电子件仓(Hub仓电子件的周转区,一般跟SMT在同一楼层,温湿度要求严格,空间要求密闭,温湿度可调)1.2.4贵重物品仓(放置贵重物料CPU/DU/LCD等体积下价值高的物料)1.3.成品区(OQC检验区/放置区/不良品区)2.料区:包括原料暂存区,半成品暂存去,成品暂存区,不良品暂存及处理区3.生产区域:包括生产线,水电气的供应等等4.辅助生产区:包括各种机房(空调机房,空压机房,配电房,网络机房),维修区(包括电子件和机构件维修区),设备及治具摆放区,OQC检验区等5.office区:各个部门办公区及相应的电,电话,网络供应。
当然,一个完整的厂房还包括前台区,会议室等等。
下面做一些说明:准备事项: 由于我当时所做的layout都是属于旧厂房改造,所以只能讲讲这方面的经验,从另一个角度讲,旧厂房改**而比较麻烦 ,因为很多约束比较多,拆了重新来可能比建个新的还麻烦.一般来讲,要改造一个厂房,第一步就是看现场,了解目前的状态,另外,还需要收集一些基本数据,比如:柱间距;各楼层的承重;楼层的高度(板对板间距),梁高;(这个主要是涉及管道的规划以及夹层的设计)承重墙的分布;电梯的数量及分布;目前各机房的数量及位置,容量;未来的产能规划等等其中,产能规划是比较重要的,因为很多数据都是根据产能需求来进行计算的.生活设施方面生活设施方面主要是满足员工日常生活需求所用的,这个部分我们归结为人流,正常的情况下,员工上班的整个顺序一般是这样的:打上班卡----更鞋----进入车间(上午)-----餐厅------进入车间(下午)-----下班-----过安检------更鞋-----打下班卡. 这中间,还包括工作中休息的时间,即需要休息区(包括饮水区),另外还要上厕所,所以需要卫生间,等等.餐厅:一般座位与就餐人数的比例在1:3~1:5之间,如果每批次就餐时间为20分钟的话,那么大约在2个小时内可以就餐完毕卫生间:对于不同功能,其数量是不一样的,如果是集中用,比如生产线休息的时候,这时候上厕所的人就特别多,所以生产区域的数量就要多,我记得我看过一个法规建议值:15人/个(中小学生),对于office区域,由于都是不定时使用,所以比例可以高一些,我记的我们当时基准是40人/个车棚:这个需要实际统计,包括自行车,小轿车,电动车的数量各自为多少.休息区:这个要根据实际需要测算,一般根据每批次休息人数来规划安检区:安检门的数量根据高峰下班时段的人数来进行计算,这个部分如果从理论上讲,是排队论的一些运用,当然在实际中,不用考虑那么负责,我们当时设计的方案是估算高峰时段的人力Q,然后测量一下一个人过安检门需要多少时间T(s),在给一个目标时间,比如20分钟可以让所有人过完,这样,就可以根据公式(Q*T)/(20*60)来得到所需数量,此外还需要考虑回流的路线设计.打卡区:这个的规划和安检门的规划所用的原理差不多.生产设施方面: 一般来讲,一个电子厂的比较正常的流程是:供应商送货至码头-----仓管收货,盘点------到暂存区-----IQC检验------入库-----生产部门领料(or仓库发料)------暂存区(Kitting 仓)------发料至生产线-----成品暂存区-------成品仓在规划整体的布局的时候,基本上可以按照物流的流向来进行考虑.当然,这只是正常的顺序,实际上,还存在回流的情况,比如IQC验货NG的时候,需要退料,成品抽检NG,需要重工,等等.一些杂七杂八的点:1.仓库:一般来说,电子厂的料主要分为三大类:电子件,机构件(包括塑胶件和五金件),包材,这三类的存储要求还是有很多区别的,尤其是电子料,一般都有温湿度的管控要求,所以一般都是单独建仓库来放置,而机构件和包材对环境要求不大.还有一些比较贵重的料,可能会存在一些比较安全的区域,考虑另外码头的分布,对于整个物流路线的规划起着很重要的作用.2.对于物流,现在一般厂房都有好几层,所以都有电梯,个人觉得电梯的分布对整个物流的顺畅起着很重要的作用,所以对于电梯的分布一定需要注意从整体上去考虑,很多时候可以通过合理设置电梯的分布避免物流的交叉,另外,电梯的宽度大小及其高度及承重是按照其所运送货物的栈板的最大宽度和高度来确定的,当然,需要有15%左右的宽放.3夹层,建夹层是为了增加空间的利用率,但是这有个约束,就是楼层的高度,如果需要车间需要安装空调,风管等管道,从经验上讲,这些管道要占到80cm左右的高度,那么楼层的高度如果低于6m就很难建夹层.4.吊顶:一般来讲,吊顶的高度距离地面不要低于 2.8m,否则人就会感觉很压抑,这也是为什么如果板对板的间距低于6m,就很难建夹层.(如果梁高50cm,风管+桥架+灯具要占到80cm,这样就去掉1.3m,吊顶2.8m,那么夹层的高度最多只有2.7m了)5.各种通道的设计:通道的实际一般都是参考车间里所用的运输工具来设计的,比如,在车间内部一般都是用叉车拉栈板,所以通道的宽度至少要比最宽栈板的宽度大15%左右.物流通道:包括主物流通道油压车,双行 2.76 3m次物流通道油压车,单行 1.38 1.5m线体间通道平板车,双行 1.38 1.4m电动叉车通道叉车转弯半径/栈板大小 3.75 4m备注:栈板按1.2m*1.2mTV:这里讲的CCTV不是指中央电视台,而是监控系统.监控系统主要就是摄像头的分布,摄像头的分布一般参考所在区域是否有贵重物品,一般来说,库房里摄像头是比较多的,此外,各个门口基本上都要安装摄像头,还有就是重工区,料区,等等.7.各种机房:如上面所讲,工厂的机房一般都包括水塔(水),配电房(电),空压机房(气),空调机房(冰水主机室),网络机房等等,需要注意的是压降问题,对于一些比较精密的设备,可能对于电压要求比较高,所以如果配电房到设备所在地过远,可能会有压降导致设备不能正常运转,这个问题,可以请教专门电气施工人员,当然,网络也有这样的问题,从交换机出来的网线如果超过100m,信号就会发生衰减.8.线槽:这个设计到布线,工厂所用的线包括强电和弱电,大部分情况下强弱电是可以并在一起走的,但是有些情况下最好不要合并.这个可以请教专业人士.9.消防系统:消防系统要按照法规来进行,这个一般建厂的都比我们有经验,只是在设计layout的时候一定要把这个因素考虑进去,有时候规划可能很合理,但是却不符合消防法规,在消防规划中,包括逃生动线,各种********(包括烟感器,防烟垂壁,喷淋头,消火栓,灭火器)的摆放等等.10.施工:施工从一般性来讲分为土建和机电两个部分.从我的经验讲,了解一些施工的知识对于画layout是很有帮助的.在整个厂房的规划中,layout基本上随施工一直在调整,因为有时候你规划是这样,但是随着施工的进行,发觉有些规划并不是那么合理,所以需要进行调整.可以说,施工没有结束,layout就会一直调整.11.各楼层的电力负荷.。
布局分析
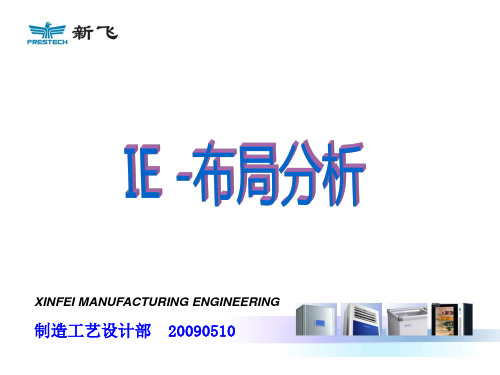
制造工艺设计部
20090510
1、布局分析 2、搬运布置
布局分析
工厂布局的含义:
简称PL(Plant Layout),就是综合考虑生产规模、工
艺安排、功能衔接等条件,对区域功能划分(出口、入口、
加工区、暂存区、通道等)、机械摆放等进行规划安排的
搬动的情况。
例如:飞机、火箭、楼房、船舶、电梯。 各部件流程性布局+固定布局上总装
布局分析
4.混合布局:
集约式布局+流程式布局+固定布局。 精益生产推崇流程性布局。
布局分析
柔性的生产布局:
象橡皮筋一样有弹性、灵活的制造流程,即柔性生产。
诞生背景: 多品种、小批量生产的需要; 缩短交货期的需要; 降低固定成本和库存的需要。
布局的经济型原则:
相邻原则;
充分利用立体空间原则ห้องสมุดไป่ตู้ 统一原则;
最短距离原则;
物料顺畅原则; 减少存货原则; 便于沟通原则; 安全原则; 灵活机动原则; 环境和美观。
布局分析
布局分析常用的四种工具:
布局成本函数
单位时间内人或物品的流动量、与距离相关的成本。
来往(From-To)矩阵分析法
活动。
布局分析
布局分析的时机 1.生产规模发生变化时; 2.新产品导入、新设备投入时;
3.生产方式变更时;
4.减少内部的物流浪费时。
布局分析
常见的四种布局:
1.集约式布局:将同种工艺的设备、工序集中在一起的 布局。是以机械设备为中心的布局,又称功能式布局。 例如冲压车间。
优点: 设备单一,易于现场指导,员工可迅速掌握技能; 机械故障易于排除; 可同时生产许多产品,设备故障对后续影响不大。
SMT工厂的布局思路
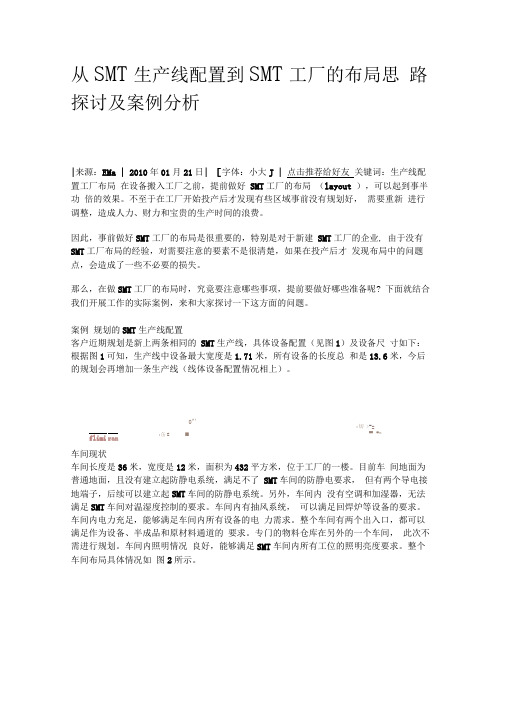
从SMT 生产线配置到SMT 工厂的布局思 路探讨及案例分析|来源:EMa | 2010年01月21日| [字体:小大J | 点击推荐给好友 关键词:生产线配置工厂布局 在设备搬入工厂之前,提前做好 SMT 工厂的布局 (layout ),可以起到事半功 倍的效果。
不至于在工厂开始投产后才发现有些区域事前没有规划好, 需要重新 进行调整,造成人力、财力和宝贵的生产时间的浪费。
因此,事前做好SMT 工厂的布局是很重要的,特别是对于新建 SMT 工厂的企业, 由于没有SMT 工厂布局的经验,对需要注意的要素不是很清楚,如果在投产后才 发现布局中的问题点,会造成了一些不必要的损失。
那么,在做SMT 工厂的布局时,究竟要注意哪些事项,提前要做好哪些准备呢? 下面就结合我们开展工作的实际案例,来和大家探讨一下这方面的问题。
案例 规划的SMT 生产线配置客户近期规划是新上两条相同的 SMT 生产线,具体设备配置(见图1)及设备尺 寸如下:根据图1可知,生产线中设备最大宽度是1.71米,所有设备的长度总 和是13.6米,今后的规划会再增加一条生产线(线体设备配置情况相上)。
车间现状车间长度是36米,宽度是12米,面积为432平方米,位于工厂的一楼。
目前车 间地面为普通地面,且没有建立起防静电系统,满足不了 SMT 车间的防静电要求, 但有两个导电接地端子,后续可以建立起SMT 车间的防静电系统。
另外,车间内 没有空调和加湿器,无法满足SMT 车间对温湿度控制的要求。
车间内有抽风系统, 可以满足回焊炉等设备的要求。
车间内电力充足,能够满足车间内所有设备的电 力需求。
整个车间有两个出入口,都可以满足作为设备、半成品和原材料通道的 要求。
专门的物料仓库在另外的一个车间, 此次不需进行规划。
车间内照明情况 良好,能够满足SMT 车间内所有工位的照明亮度要求。
整个车间布局具体情况如 图2所示。
flimi ran 0^':缶E ■:切 >-= ■ Ir客户的要求1、对目前新搬入的生产线以及相关辅助工具、区域进行定位;2、整个车间能够满足未来三条生产线的架设和生产要求,不需对规划区进行重新调整;3、将每条生产线的起始位置尽量保持一致,使整个车间整齐有序地排列三条生产线。
系统的布置图SLP
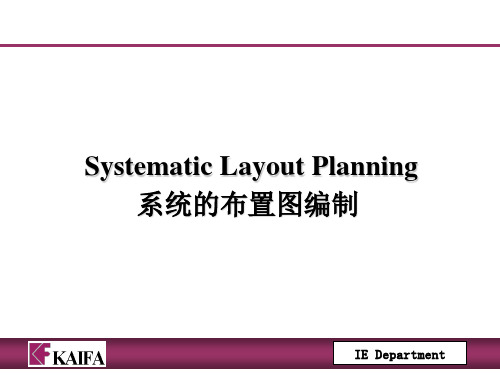
IE Department
Layout Planning的目的 的目的
改善操作(Improve Operation) 改善操作 降低成本(Reduce the Cost) 降低成本 增加产出(Increase Output) 增加产出 改善质量(Improve Quality) 改善质量 优化流程(Optimize Process) 优化流程 使员工方便和满意(Convenience and Satisfaction 使员工方便和满意 for Company Personnel)
IE Department
Layout Planning的步骤 的步骤
Each Area Space Calculation& Estimation — 各区域面积 的概算 Equipment—设备 设备 Station —工位 工位 Line —生产线 生产线 Workbench —工作台 工作台 Conveyor —传送带 传送带 Material Rack—货架 货架 Aisle—通道等 通道等
IE Department
Layout的内容 的内容
Workshop/Clean Room Layout—车间 净化间布置图 车间/净化间布置图 车间 Material movement (Transfer box, aisle) —物料运转 转件窗 主通道 辅通道 物料运转(转件窗 主通道,辅通道 物料运转 转件窗,主通道 辅通道) Material storage (Material rack) —物料储存场地 货架 物料储存场地(货架 物料储存场地 货架) Production line space (Prime, rework, sampling, testing, package, QA) — 生产线的面积 正常 返修 抽检 测试 包装 生产线的面积(正常 返修,抽检 测试,包装 正常,返修 抽检,测试 包装,QA) Output capacity—生产能力 生产能力 Equipment (Worktable, netware, power) —设备 工作台 网络 动力供应 设备(工作台 网络,动力供应 设备 工作台,网络 动力供应) Operator in/out route—工人进 出路线 工人进/出路线 工人进 Assistant operation (Unpack, barcode print, phone, safety requirement) —辅助作业 拆包 条码打印 电话 安全门 辅助作业(拆包 条码打印,电话 安全门) 辅助作业 拆包,条码打印 电话,安全门
精益生产之LAYOUT38张课件
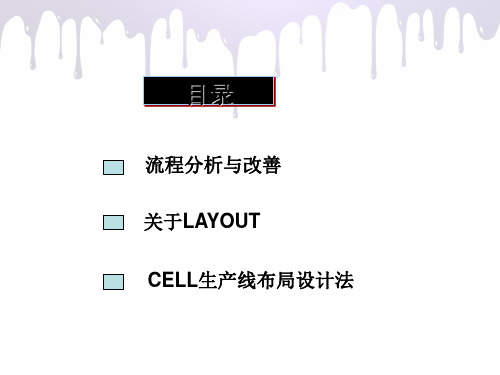
搬动距离 (米)
30
10
关于layout
一.Layout的定义
Layout的中文名称是“布局”,简单的说布局 就是对设备,作业台,物料,工装,半成品, 水,电,气等的综合配置。主要研究工序之间, 车间之间,部门之间及工厂整体的设备,作业 台,材料,仓库等配置与放置的合理性,已达 到整个生产系统人流与物料畅通化,流程最优 化,效率最大化的目标
1.作业顺序 2. 作业条件 3.主 要工装夹具
移动
1.移动状态 2.搬运设 备 3.搬运手段
移动距离 路线 移动时间 次数
1.搬运数量 2.使用工具
检查 1.检查内容 2,检查工具
地点
检查时间
1.检查方法 2.不良率
等待 等待原因
等待地点
等待时间
五.流程分析与改善的主要工具
1.流程分析的图示符号
•
4、心中没有过分的贪求,自然苦就少。口里不说多余的话,自然祸就少。腹内的食物能减少,自然病就少。思绪中没有过分欲,自然忧就少。大悲是无泪的,同样大悟
无言。缘来尽量要惜,缘尽就放。人生本来就空,对人家笑笑,对自己笑笑,笑着看天下,看日出日落,花谢花开,岂不自在,哪里来的尘埃!
有无产生浪费的工序,哪些工序的工时多 工序间平衡率有多高,有没有停滞或多于工序 有没有重复或多于的动作 搬运线路是否合理
三.流程分析的种类
种类
目的
特征
优点
缺点
产品工艺流 主要分析产品
程分析
的工艺流程
作业流程分 主要分析作业
析
者的作业流程
多人通过多 台设备制造 同一产品
一人通过不 同设备或不 同工序,制造 多个产品的 过程
A.Leadtime的定义
layout基本知识培训V1
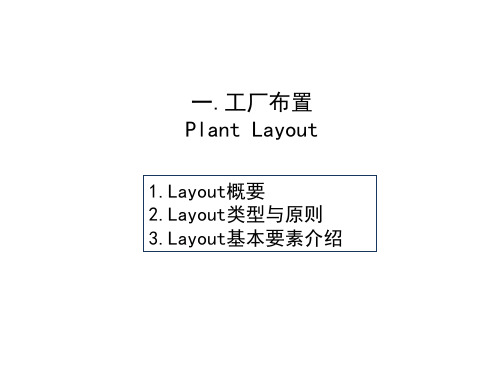
□详细LAYOUT设计
- 生产线: 通道宽度、线(line)布置和间隔、工作地区、线(line)长度、适当的 工作台等
- 仓库: 适当的库存、堆放方法、布置、通道设计等 - 配套设施: 设定办公室、休息室、洗手间的人均单位面积 - Dock场 : 设计Dock数量、布置间隔、进路、Leveler等 - 公司内道路和出入门 : 道路宽度、道路数量、与公司外道路连接等
搬运距离短。 工序间的中途中断、停工待料少 生产效率高 难以适应产品的变化 受流水线中断的影响大。
三、LAYOUT基本形式
4)混合式布局
将不同功能与种类的设备,放在同一块区域,形成一个生 产制造的群体,让相类似的产品或制程可以同在此制造群体 中生产。
基本型式
标准件
原 材
1料仓 U字型配置
缩短物流动线
□ 使物品迅速顺利地流动 - 布置时考虑交叉和逆行。 - 最大限度地减少M/H (Material Handling)数 。
空间效率
□ 平面性布置 → 立体性布置 - 广泛利用地面∼天花板,提高空间利用效率。 -提高Conveyor、通道、工作区域等地区的空间效率。
2.生产线设计
2.1.2基本方向
安全规定 布局是否符合安全特性
步骤八:实施评价
步骤七:方案实施
10
3.系统布置设计SLP
二.SLP (systematic layout planning)的顺序系统图
时间(T) 路径(R)
工程图
销售计划
PQ 分析
生产计划
物流 分析
活动 相互 关系 分析
作业物 流相关 表 作业单 位相关 表
辅助服务(S)
重近轻远: 比较重的物品放在近处,轻的放在远处 重厚长大:把重的,厚的,长的,大的放在近处 轻薄短小:把轻的,薄的,短的,小的放在远处
如何实现生产布局最优化
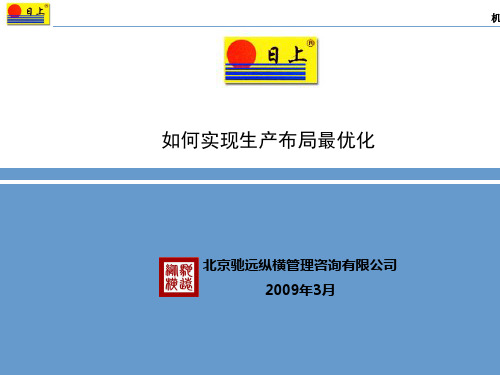
4、“口”字型布局
具有移动距离最短、搬运效率最高等优点:但外形不美观、面积利用率不高是其致 命缺点。
如何实现生产布局最优化
机
布局分析的工具
1、布局成本函数
首先要合理安排工序或工作中心的位置,以减少物料移动的处理成本。主要考虑:
(1)两个工序之间某一时间内物料和人员的流动量
(2)工序距离相关的成本
为了达到降低成本的目的,那些物料和人员流动较多的工序或设备就应该以相邻为
原则。
in
c X C ij ij i 1
n=工作中心或工序的总数量
i、j=各个工序
Xij =工序i到工序j的物料流动数量 Cij =一件物料在工序i和工序j之间的流动成本
如何实现生产布局最优化
机
布局分析的工具
2、接近相互关联分析法
例:某工厂有材料仓库、零部件仓库、机械加工、最后加工、喷漆、组装、检验、产品 仓库、工具室9个场所。
如何实现生产布局最优化
机
布局设计和改善和的“十大原则”
7、相邻原则 8、减少库存原则 9、便于沟通原则 10、环境和美观
如何实现生产布局最优化
机
布局设计和改善的四种形态
1、串联式布局
进料口
2、“U”型布局
•方便设备维修 进料口 •物流路线清晰
•设备按物流路线直线配置 •扩产是只需增加列数即可 •回收材料与垃圾可用传送带
布局设计和改善的“十大原则”
1、统一原则
在布局设计和改善时,必须将各工序的人机料法
料
4要素有机结合起来并保持充分的平衡。
2、最短距离原则
机
人 设备 法
3、人流物流通畅原则
必须使工序没有堵塞、物流顺畅无阻。应注意:尽量避免倒流和交叉现象,否则会 导致一系列意想不到的后果,如质量问题、管理难度问题、生产效率问题、安全问题。 如合扇
工厂layout布局分析与设计
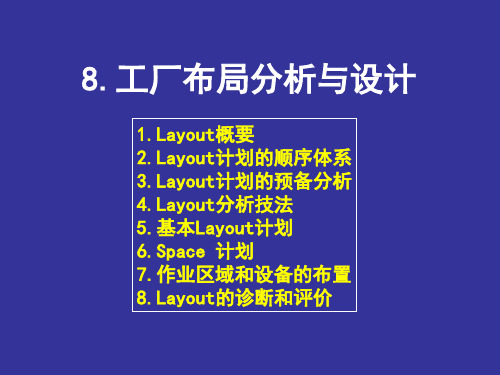
运行level
限制条件
yout计划预备分析
1)改善Layout的预备分析内容
Layout 变更可以 改善的问题领域
问题实际现象
-生产日程延迟 -过多的在制品 -高价设备运转率低 -用于搬运的工时 -人的移动距离 -空间的浪费 -活动之间的妨碍/干涉 -危险或不安全作业环境
ห้องสมุดไป่ตู้
原因/活动 效果分析
-所有A关系排列在模板的4边 -E关系至少排列在模板的四角 -X关系绝对隔离 -A关系连4角都没排到,X关系排到4边时 -A关系排到角落,X关系排到4角或E关系 边角都没排上
与基准模板有I,O,U,X 关系的模板,以相同的方法排列后 在 check mark 数评价layout
yout分析及方法
生产系统的构思
-制造工程/装配顺序 -设备所需台数及规格 -人力资源所需计划 -作业方式的构思 -现场及部门的区分 -管理及服务的要求功能 -搬运及库存系统运营 方式的构思
基本计划
-决定阶层构成要素 -物流及工程流程分析 -决定工厂生产率 -space 计划 -各要素间的搬运强度 /接近性评价 -各构成要素的规划分配 -评审物流设备
8.工厂布局分析与设计
yout概要 yout计划的顺序体系 yout计划的预备分析 yout分析技法 5.基本Layout计划 6.Space 计划 7.作业区域和设备的布置 yout的诊断和评价
yout概要
1)Layout 概要
Plant Layout 是指为增加设备,设施,资材,人力资源和能源使用的效率,对公司或工 厂内所有设施重新布置的一系列系统的活动 为使生产容易安全方便的进行,把4M画在图纸上
时间(T) 路径(R)
工厂合理化布局Layout

空间关系表
综合 & 调整
要求地方
可用地方
工程图
计划 A
计划 B
计划 C
修正条件
限制条件
Layout 决策
战略level
战术level
运行level
Handing system 存储设备 位置 人力要求 建筑的特性 Utility & service
1 改善Layout的预备分析内容
yout计划预备分析
8 7 6 5
3 Dimensionless Block Diagram制作
yout分析及方法
准备相当活动的个数,四角模板 Templet
作为工厂block layout 计划的一阶段用于工厂布局主计划的制定
四角模板的中央记录相当于活动 名称
除了U的关系,在模板的四角记录有A,E,I,O的activity 的数据,X的关系记入中央下半部
四角模板中选一个放在桌子中间,与此有A关系的模板放在 第一个模板的四边,有A关系的模板在两个以上时考虑它们 的相互关系再排列
之后排列与基准模板有E关系的活动,E的关系至少与基准模 板遵循对上角的原则.考虑与已排列的A关系模板和X,U关系 排列模板
与基准模板有I,O,U,X 关系的模板,以相同的方法排列后 在 check mark 数评价layout
Layout 变更可以 改善的问题领域
设定改善目标
问题实际现象 -生产日程延迟 -过多的在制品 -高价设备运转率低 -用于搬运的工时 -人的移动距离 -空间的浪费 -活动之间的妨碍/干涉 -危险或不安全作业环境
原因/活动 效果分析
其它方法的 改善方案
柔韧性研究, 用布局变更改善 现象问题的可能 水平是
LAY-OUT管理
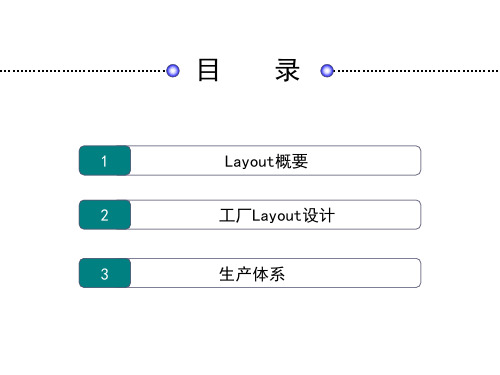
Location 选定
Block - Layout
Detail - Layout Installation
第3 阶段 详细Layout的 理论修整 4 实际性安排计划以及按照 计划实际布置 布置完后,进行生产,布 置计划的使命也随之结束 第4阶段 实际布置 计划的修整
修改
Layout 配置
1.结构物/现场配置
有效率的 Layout的必要性抬头
在80年代中期以后,为了避免成本的亏损,展开了经营合理化运动, 并为了在危机中生存 → 创造优质低价 → 加速企业之间的竞争和生产合理化运动
时代的 需 要
现 象
过去扩大竞争时代 → 不断增设生产设备 → 追求量的生产而带来的非效率性 Layout的养成 Layout的问题点的抬头 - 面积效率低 - 物品的搬运和人的步行多 - 不必要的中间停滞多 - 比起加工时间,制造时间长 - 现场无秩序、动作缓慢等
Layout 评价
1. 评价方向
1. 实施需要的投资额: 土地、建筑物的价格、布置变更所需的休止损失 以及配管道、配线的移动金额等 2. 实施经费 : 搬运费、工资、在工/库存费用 3. 管理的容易度 4. 便利度 : 有关所有功能的综合等 5. 作业环境: 安全、舒适(温度、采光、通风等)、防灾 6. 对将来变化的适应性 8. 外观、宣传效果 10.基地和建筑物的利用度 7. 对组织以及制度的适应性 9. 与外部环境的调和
○ 横向(按机种、技能别)布置,不如纵向(按部品别、制品别、
类似部品别、类似工程别)配置
○ 搬运距离要短,搬运尽可能动力化、机械化、自动化 ○ 要考虑到现场之间的能力Balance的调整及将来计划 ○ 通道的宽度要适中,用白色(或黄色)带标示 ○ 环境条件(暖气、通风、采光、照明等)要好 ○ 对象物品的拿取次数尽可能要少 ○ 空间的有效利用
介绍工厂布局英文版作文
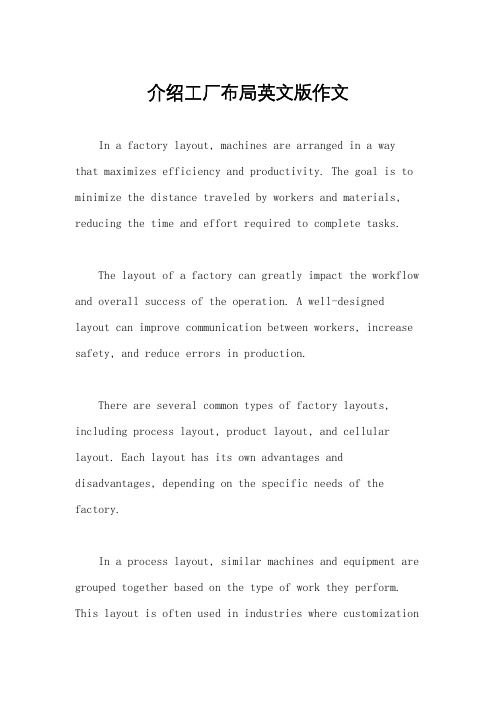
介绍工厂布局英文版作文In a factory layout, machines are arranged in a waythat maximizes efficiency and productivity. The goal is to minimize the distance traveled by workers and materials, reducing the time and effort required to complete tasks.The layout of a factory can greatly impact the workflow and overall success of the operation. A well-designed layout can improve communication between workers, increase safety, and reduce errors in production.There are several common types of factory layouts, including process layout, product layout, and cellular layout. Each layout has its own advantages and disadvantages, depending on the specific needs of the factory.In a process layout, similar machines and equipment are grouped together based on the type of work they perform. This layout is often used in industries where customizationand flexibility are important.A product layout, on the other hand, arranges machines and equipment in a linear fashion, following the sequence of production. This layout is ideal for industries with high-volume production and standardized products.A cellular layout divides the factory into self-contained units, or cells, each responsible for a specific task or product. This layout encourages teamwork and collaboration among workers, leading to increased efficiency and quality.Regardless of the type of layout used, the key is to create a workspace that is organized, efficient, and safe for workers. By carefully planning and designing the factory layout, businesses can optimize their operations and achieve greater success in the long run.。
- 1、下载文档前请自行甄别文档内容的完整性,平台不提供额外的编辑、内容补充、找答案等附加服务。
- 2、"仅部分预览"的文档,不可在线预览部分如存在完整性等问题,可反馈申请退款(可完整预览的文档不适用该条件!)。
- 3、如文档侵犯您的权益,请联系客服反馈,我们会尽快为您处理(人工客服工作时间:9:00-18:30)。
6.对改善后的数据进行分析,总结
产品 加工时间 搬动时间 检查时间 等待时间 小计 搬动距离 (米)
A
5.4
2.1
8.65
3.5
19.65
10
7.改善成果总结,对比
状态 加工时间 搬动时间 检查时间 等待时间 小计 搬动距离 (米)
改善前 改善后
差数
5.57 5.4
-0.17
4.9 2.1
-2.8
3.Cell布局五步法
1).通过产品分类确定生产类型
在进行产品分类时,可以通过P-Q分析法,P-Q分析法是 指对企业目前的所有产品按按加工工艺分类,同时对 各类产品的生产量进行统计分析的一种方法
1200 1000 数 量 800 600 400 200 0
100 90 80 70
60 50
40 30
生产线排单: Line A:生产P1产品 Line B生产P2产品 Line C生产P3产品 Line D生产P4 P6 P9产品 Line E生产P5 P7产品 Line F生产P8 P10产品
2).掌握工艺流程图和标准工时 3).确定每个工序的标准在制品(WIP)数量
WIP数量=工序周期时间/生产节拍
3.现状分析
单位:分 产品 加工时间 搬动时间 检查时间 等待时间 小计 搬动距离 (米) 30
A
5.57
4.9
20.6
73.2
104.3
主要问题: 1.等待时间太长,占整体时间的70.2%,这是导致生产 作业周期长的主导因素,也是效率低的最主要原因 2.由于包装车间的整体布局不好,导致搬运距离长,等 待时间长 3.包装的流程没有充分利用平行生产的原则进行,,导 致无用工序多
移动
检查
等待
作业者在作业中间等待及工序间的等待
2.工艺流程图
218-40b品质文 件.xls
3.工程分析表
工程分析表.xls
某电子厂,由于成品包装车间的工作效率低,中 间在制品多,占用空间多,人员的积极性不高, 包装作业生产周期长,导致交货期延长的频率越 来越高。为了能快速解决问题,分析如下:
二. 精益Layout设计原则
统一的原则 最短距离的原则 人流,物流畅通的原则 充分利用立体空间的原则 安全满意的原则 灵活机动的原则
三. Cell(单元)生产线布局
Cell生产式layout主要是对企业各类产品进行分类,以 相同的加工工艺流程作为一条生产线进行的layout设计
(1).Leadtime
20
10 0
P1
P2
P3
P4
P5
P6
P7
P8
P9
P10
某公司产品P-Q分析法
如上图式,按照2/8原则,可以将P1,P2,P3设计为专用生产 线,因为其量大,这样可以稳定生产,减少切换,提高品质效 率.P4~P10根据其工艺流程利用"产品分族矩阵"进行分析
产品 按工艺顺序(关键设备或工艺) 工序1 工序2 工序3 工序4 工序5 工序6 工序7 工序8
5 15
螺丝
底板
# C
10
B
焊接10
导线 C单元生产人数 =10/5=2人
B单元生产人数 焊接10 =40/5=8人 #代表组
搬运
检查
停止储存
B.作业流程分析图示
工序种类 符号 说 明
作业
零部件,产品的形状,尺寸,性质发生变化,与其他理 念进行装配,分解的行为。包括加工,检查,移动而进 行的整理,准备前期工作,即包括操作性在内的全部行 为 作业者将加工物搬运到其他场地或空手移动的行为,0.5 米以内取物放作不属于移动动作 对材料,零部件或产品的品质和数量进行测定,并判定 工序能力
P4 P5 P6
P7 P8 P9 P10 分析后产品分族矩阵图
从上图可知: P4,P6,P9产品的工艺几乎相同 P5,P7产品的 工艺几乎相同 P8,P10产品的工艺几乎相同
产品 按工艺顺序(关键设备或工艺) 工序1 工序2 工序3 工序4 工序5 工序6 工序7 工序8
P4 P6 P9
P5 P7 P8 P10 产品分族矩阵
1.不同作业者 作业流程不 1.容易发现作 一样 业者的无效 2.必须紧随作 动作 业者行动才 2.易于对作业 能观察,这样 员进行改善 必能增加分 析工作量和 难度
1. 5W1H提问分析法
项目 WHY WHERE WHEN WHO WHAT HOW HOW MUCH 问题 目的是什么 在什么地方执行 什么时候做 谁来做 做什么 如何做 需要多少费用 为什么 为什么 为什么 为什么 为什么 为什么 为什么 为什么 改善方向
可以和其他工序 重新组合的工序
简化工序
各工序标准化
B.作业流程分析检查表
项目 作业 调查主题 场所 作业场所 时间 方法 1.作业顺序 2. 作业条件 3.主 要工装夹具 1.搬运数量 2.使用工具 1.检查方法 2.不良率
1.作业内容 2.机械设备
1.移动状态 2.搬运设 备 3.搬运手段 1.检查内容 2,检查工具 等待原因
4.提出并实施改善对策
(1).改变包装作业流 程
打保证书 贴标签
品 质 部 出 库
数 量 检 查
外 观 检 查
搬 运 至 电 脑 处
输 入 机 身 号
包 装 加 工
传 送
封 箱
搬 运 至 成 品 仓
储 存
改善后包装作业流程图
2.改变车间布局
品质部开关盒储存区 品质部开关盒储存区
电脑输入出 辅料存放区 包装车间开关盒 临时存放区 辅料存放区 保证书打印
Q1
某工厂收到一产品订单数量为20个,该产 品中间周转库存分别为500,600,和300个在 制品,该工厂有A,B,C三个工序,三个工序 生产能力相同,都是1秒/个,请问 1),生产该20个产品的生产周期要多少时间? 2),A,B,C三道工序的加工时间要多少时间?
2).Cell生产布局的类型
A. U型生产线
20.6 8.65
-11.95
73.2 3.5
-69.7
104.3 19.65
-84.65
30 10
等待时间由原来89.1%减少为17.9%
一.Layout的定义
Layout的中文名称是“布局”,简单的说布局
就是对设备,作业台,物料,工装,半成品, 水,电,气等的综合配置。主要研究工序之间, 车间之间,部门之间及工厂整体的设备,作业 台,材料,仓库等配置与放置的合理性,已达 到整个生产系统人流与物料畅通化,流程最优 化,效率最大化的目标
以“U'字的形式进行布局,使第一道工序与最 后一道在同一方向,这样可以清楚的看到产品 进出状况,有利于产品的数量管理,生产线的 平衡,多人工的运用,空间的节省,产品质量 的控制
a.完结式
一人完结式U型生产线
b.分割式
多人分割式U型生产线
C.逐兔式
逐兔式式U型生产线
B. I 字型布局
B. Y字型布局
某产品工艺流程及标准工时
1)Layout分割
A.根据标准工时找出加工工艺主线,一般情况下加工 时间最长的工艺路线为加工工艺主线。本例中的主线 为
B.根据工艺分支进行分割尽可能让分支在其他单元 内完成,如图示
2)确定作业人数和设备台数
S本体 #
S铁芯 10 A
A单元生产人数 =10/5=2人
螺丝
# 框架 #
1.作业时间 2.单位时间产量
移动
移动距离 路线 移动时间 次数
检查
地点
检查时间
等待
等待地点
等待时间
1.流程分析的图示符号
A.产品工艺流ቤተ መጻሕፍቲ ባይዱ分析符号
工序种类 加工 符号 说 明 材料,零部件或新产品在加工过程中发生了外形规格性质 等的变化或为下一工序进行准备的状态 材料,零部件或产品在一定状态下不变, 同时转移位置状 态 对材料,零部件或产品的品质和数量进行测定,并判定工 序能力 对材料,零部件或产品在进行加工或检查或前或后的一种 停止状态
4).进行作业分割,确定作业人数和设备数量
生产人数=标准工时/生产节拍 设备所需台数=设备加工标准工时/生产节拍
5).按精益流程原则进行模拟布局
案例分析
某公司某产品的工艺流程及每道工序的标准时间如下下图示,已知该产 品生产节拍为5秒/个,请确定该部件的作业人数,并进行Layout设计
S本体 # 螺丝 # 框架 # 焊接10 导线 #代表组 焊接10 15 # 10 5 螺丝 S铁芯 10 底板
victor
07-06-2011
流程分析与改善 关于LAYOUT CELL生产线布局设计法
一.流程分析与改善
流程分析的定义
流程分析是指把工艺流程中的物流过程及人 的工作流程以符号的形式进行记录、分析、 并设计出改善的方法。通过反应工序整体的 状态,有效的把握现有流程的问题点,并研 究制定改善的对策,以提高现有的流程效率 和生产效率。
搬运线路是否合理
种类
目的
特征
优点 1.产品在流动 情况下被加 工 2.可以清晰对 照工艺管制 图,更容易寻 找和分析问 题
缺点
产品工艺流 程分析
主要分析产品 的工艺流程
多人通过多 台设备制造 同一产品
不易分析作 业员的各动 作,即有一定 的模糊性
作业流程分 析
主要分析作业 者的作业流程
一人通过不 同设备或不 同工序,制造 多个产品的 过程
1.绘制流程图
品 质 部 出 库
搬 运 至 包 装 车 间
数 量 检 查
外 观 检 查
搬 运 至 电 脑 处
打 保 证 书
输 入 机 身 号