白塔机场钢结构加工制作方案
呼和浩特白塔机场航站楼结构设计

呼 和 浩 特 白塔 机 场 航 站 楼 结 构 设 计
・ ・ ・ ・ 冯 香 玲
( 中国 民航 机 场建设 集 团公 司规 划设计 总 院 )
一
、
工 程概 况
航 站楼 作 为 内蒙 古 自治 区 的重 要工 程 之一 ,建 筑 设计 独特 ,结 构体 系新 颖 ,为 了体现 航站 楼 建 筑 美 观 、大厅 无柱 的要 求 ,大厅 屋盖 采用 大跨 度 钢结 构 体 系 。两 榀拔 地 而起 的刚性 主拱 相互 倾 斜 ,并适 当拉开 ,主拱 落 地 长度 2 54 1. 0 m、两 榀 拱 脚 距 离 1 5 .7 m,拱 顶 距 离 1 m,主 拱 最 高 点 高 度 4 m, 32 8 2 0 拱 与地 面成 6 。 4 。屋 面 中间 最 高 点 高度 3 m,主 拱 0
制值为 07 f 张拉变形值 由专Байду номын сангаас 施工单位按 现 .5p 行施 工 规 范计算 。 ( 期 ) 0 1 第 2 1
梁 、斜腹杆构成 了两个连体空间三角形桁架 ,形成 了稳定的空间结构。屋面的纵 向荷载由屋面梁传递 到 拱架 上 ,由钢 结构 单独 承载 。由于拱 结构 具 有抗 水 平力 的优 越性 ,因此屋 面 和侧墙 的风荷 载和 地 震 荷 载均 由上 部钢 结构 承担 ,大 厅 四周 的外墙 不 需 要 设 结构 抗侧 支撑 系统 。 大跨 度拱 形 结 构 在 航 站 楼 的设 计 中首 次 采 用 , 航 站楼主拱落 地跨 度 为 2 54 1.0 m,水 平 推力计 算 值 1 为 67.k 215 N,为 了保证 主拱 的稳定 ,设 计 中拱脚 基 础采 用 4个尺 寸为 1 ( ) ×1 ( ) × . ( ) 6 长 3 宽 75 高 r n的大型混凝 土基础 ,在 承受 主拱水 平推 力 的一 侧 , 为 了保证拱 脚基 础 与土 体 之 间 的紧密 结 合 ,在基 础 施工 完成后 ,基 础和土体 之 间的空 隙用混 凝土 回填 , 主拱 拱脚基础 之间采用 4束 1d 5预应力 钢绞线 拉 2O1 结 ,两榀拱脚 基础 之 间采 用 2束 8 1 应力 钢 绞 5预 线拉结 ,保证 了拱脚基础 的整体稳定 性 。 主拱 平面 内半 径约 111 4.m,拱 断 面采用 下大 上 小 的变高度 箱 型断 面 ,由钢 板 焊 接而 成 ,翼缘 宽 度 14 不变 ,截 面 高 度 由 18 至 14 渐 变 ,壁 厚 .m .m .m 2m 5 m,在拱的自身斜平面内呈 圆弧形 ,便于制作安 装 ,与地 面倾斜 后 ,拱 的立 面成 为 椭 圆形 。屋 面 梁 断面 为焊接 H 型钢 H o 4O×1 2 ,两 端 悬 挑 70× O 2× 0 梁 为变断面 ,梁 高 由 30 m变 为 70 m,两 边纵 向 0m 0m 联 系梁 采 用 50×30×1m 的箱 型 断 面 ,主 拱 斜 0 0 6m 拉 杆 采 用 圆钢 管 ,钢 管 直 径 中间 为 58 m,壁 厚 0m
机场钢结构加工制作
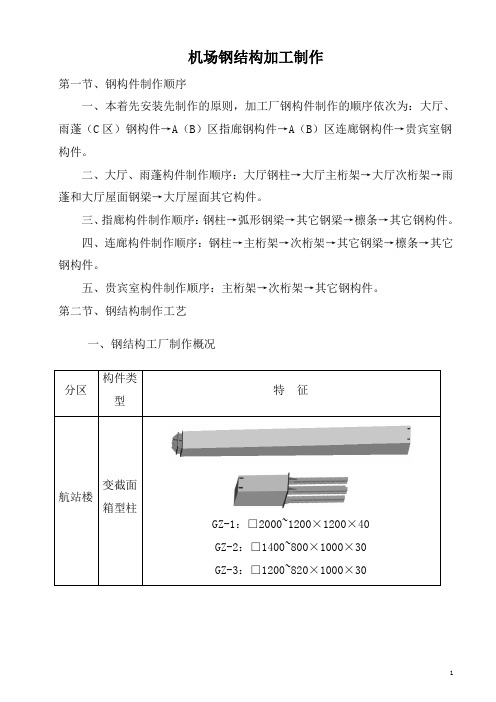
机场钢结构加工制作第一节、钢构件制作顺序一、本着先安装先制作的原则,加工厂钢构件制作的顺序依次为:大厅、雨蓬(C区)钢构件→A(B)区指廊钢构件→A(B)区连廊钢构件→贵宾室钢构件。
二、大厅、雨蓬构件制作顺序:大厅钢柱→大厅主桁架→大厅次桁架→雨蓬和大厅屋面钢梁→大厅屋面其它构件。
三、指廊构件制作顺序:钢柱→弧形钢梁→其它钢梁→檩条→其它钢构件。
四、连廊构件制作顺序:钢柱→主桁架→次桁架→其它钢梁→檩条→其它钢构件。
五、贵宾室构件制作顺序:主桁架→次桁架→其它钢构件。
第二节、钢结构制作工艺一、钢结构工厂制作概况分区构件类型特征航站楼变截面箱型柱GZ-1:□2000~1200×1200×40GZ-2:□1400~800×1000×30GZ-3:□1200~820×1000×30三角管桁架桁架高:3.0m 桁架宽:3.0m上弦杆:φ273×14 下弦杆:φ351×16 腹杆:φ159×8 注:局部杆件加强平面管桁架弦杆:φ159×8 腹杆:φ89×5桁架高:3.0~3.2m雨篷梁主梁:最大截面H450~1800×450×16×25 最小截面H450~700×450×16×25 次梁:H600x350x12x20、HM450x300x11x18 封檐梁:HM450x300x11x18其它连廊箱形钢柱□600×600×30方通平面桁架弦杆:□250×250×8腹杆:□125×125×6桁架高:4.0m连系梁截面:H600×300×12×20指廊H型钢柱截面:H600×500×20×25H500×400×12×18异型钢梁截面:T1500×500×25×25+屈曲半径:40.3mH型钢梁HM450×300×11×18HM400×300×10×16H600×400×12×10其它平面支撑:φ245×10柱间支撑:φ180×8+φ140×6主檩:[]350×200×5H350×200×6×8挑梁:T200~780×100×10×10二、钢结构工厂制作的具体思路分区构件类型制作思路航站楼变截面箱型柱平行板多头同步切割,扇形板双头同步切割;隔板组立机组焊环形隔板,钢胎具组组立箱型柱;环形隔板三面手工焊接,一面电渣焊;钢柱分段端头端铣,工厂预拼。
机场钢结构施工组织设计方案

机场钢结构施工组织设计方案一、设计背景随着中国经济的发展,民用航空业的迅速发展,机场建设工程也逐渐提高了其技术的要求,特别是在施工技术中,钢结构施工技术已经成为现代工程建筑的一种重要手段,并得到了广泛的应用。
机场建设工程中,机场航站楼是一个核心工程,而钢结构的使用对于提高机场航站楼的稳定性、效率和质量具有非常重要的作用。
因此,在机场钢结构施工组织设计方案中,要考虑到钢结构在施工过程中的操作、安全、效率等方面的因素,以确保机场建设工程的顺利完成。
二、施工工艺流程1.预制构件制作:传统的机场钢结构施工采用的是现场动态组装的方法,但是由于现场工作难以控制,且需要花费大量的人力、物力和时间,因此现在一般采用的是先预制构件再进行组装的方法。
通过这种方法可以提高施工的效率和减小工程的难度。
2.构造组装:在进行预制构件后,需要将这些构件进行组装,以形成整体的机场钢结构。
组装过程中需要注意结构的稳定性和安全性,遵守安全规定,严格执行组装和焊接工艺。
3.装配外部构件:将预制好的外部构件装配至钢结构上,如玻璃幕墙、地面、悬挂天花等。
4.基础施工:在机场钢结构施工之前,需要进行基础施工。
基础施工是整个工程的基础,需要非常注重细节和专业性,以确保机场建设工程运行的平稳性和稳定性。
三、方案优势1.施工时间短:预制构件制作的过程可以在工厂中全自动化的进行,从而大大的减少了施工时间,降低机构使用的成本。
2.施工质量高:在使用钢结构进行施工时,整个建筑的质量、强度和稳定性都可以得到保证。
3.节约人力物力:预制构件在工厂中完成制作,减少了施工过程中的大量人力和物力投入,降低了工程的成本。
4.施工环保:预制构件生产的优点在于能够减轻现场施工带来的噪音、粉尘以及其他的对于环境造成的负面影响,减少环境污染。
5.结构稳定:钢结构比传统的建筑工程结构更为坚固和稳定,因此能够更好的应对各种自然灾害,降低了安全隐患。
四、安全保障为了保障机场钢结构施工在安全方面的需要,需要遵守以下三点:1.严格执行施工规定:在机场钢结构施工过程中,必须严格执行施工规定和规范要求,确保安全。
机场钢结构加工制作方案

钢结构加工制作方案1 钢结构加工程序说明和工艺流程图1.1 钢结构加工程序说明本工程钢结构件加工主要由普通钢结构件等组成。
普通钢结构件为本工程主楼和指廊两部分的屋面部分,、包括有大厅的主拱、纵向中心拱、纵向联联系梁、横向屋面梁、斜腹杆、等结构件。
本工程钢结构工厂加工的原则是:1.1.1由于结构的特殊性,主拱以及其他构件的部件都通过工厂制作成单件,开好坡口,根据运输条件,确定单件长度,运输到现场.1.1.2本工程上的节点板构件、支座都是以半成品运输到现场。
1.1.3主拱在工厂制作成前后都要进行预处理,第一道的防锈油漆和中间油漆的工作。
工厂制作完成后,构件在现场胎架上根据现场吊装的要求进行拼装。
在现场胎架上验收合格后吊离构件,详细内容见现场拼装工艺简述。
1.2 钢结构制作工艺流程图2. 材料采购及管理2.1 材料采购本工程材料主拱及主拱斜拉杆采用Q235C结构钢;其它材料采用Q235B碳素结构钢。
对于本工程所采用的材料,需严格把好质量关,以保证整个工程质量。
2.1.1 材料入库后由总承包物资管理处组织质量管理部门对入库材料进行检验和试验。
2.1.2所有进厂材料均应有生产厂家的材质证明书。
2.1.3按供货方提供的供货清单清点各种规格钢管、型钢和钢板以及焊接材料、涂料数量,并计算到货重量。
2.1.4按供货方提供的钢管、型钢和钢板尺寸及公差要求以及焊接材料、涂料,对于各种规格钢管,抽查其口径、壁厚及椭圆度;对于各种规格型钢,检查其断面尺寸、壁厚、长度及直线度;对于各种规格钢板,检查其长宽尺寸、厚度及平整度,并检查钢管、型钢及钢板焊接材料的外表面质量。
2.1.5汇总各项检查记录,交现场监理确认。
2.2 材料管理2.2.1选取合适的场地或仓库储存本工程材料,按品种、按规格集中堆放,加以标识和防护,以防未经批准的使用或不适当的处置,并定期检查质量状况以防损坏。
2.2.2 材料的使用严格按排版图和放样资料进行领料和落料,实行专料专用,严禁私自代用。
机场钢结构施工组织设计方案

机场钢结构施工组织设计方案工程特点第1页共63页一、工程特点1、设计多样、结构形式独有:本工程航站楼钢结构屋盖呈“伞形”,它由xx_榀跨度分别为xx_m和xx_m的空间曲线桁架组成,重量分别为xxt和xx_t,桁架截面为倒置三角形,采用管一管相贯线连接,桁架高差达13m,主桁架(t-1,t-2)、(a)、(g)轴通过法兰连接底座、(d)轴通过多根发射状的摆式杆支承在3排52根四肢(双肢)格构式钢柱上,屋面通过轻型檀条、系杆连成整体后安装压型钢板及采光天窗。
2、所有车轴柱为格构式钢柱,最小长度超过xxm,“伞形”主桁架中部(d轴)通过摆式杆与钢柱使用铰接式相连接,摆式杆最在长细比达xx,对钢屋砌的整体强度及稳定性建议很高。
3、屋盖钢结构设计在xx层(+xxm)予应力楼板上,楼面设计荷载为xxkg/m2,航站楼四周施工场地与道路开阔,可满足钢结构现场分段拼装及跨外吊装的需要。
4、工期紧:必须确保xx_具有声母条件,航站楼必须全封闭,这样地下室工程施工须要xx_月份进场,xx_月份顺利完成并具有钢柱吊装条件;而钢结构的制作工作尚未已经开始,必须确保xx_月份初钢柱进场特别是主桁架的制作能满足现场拼装及吊装的需要,难度很大。
施工难点第2页共63页二、施工难点:1、钢架柱为格构式钢柱,长细比较小(最低超过xxm_),与xx_m楼板使用悬浮式相连接,当主桁架在施工过程中产生形变、快速反应及xx_m楼板出现加速度时易产生歪曲与变形。
2、摆式杆长细比达xx_,与主桁架及车轴柱使用铰接式,其自身刚度和稳定性掌控难度很大,极易产生失速。
3、整个钢屋砌结构为轻型结构,其整体刚度与整体稳定性均极差,形变、快速反应难以掌控。
4、总体工期紧,各工序交叉配合尤其是xx_楼板、予应力张拉与屋盖结构的交叉施工配合难度较大。
方案挑选第2页共63页三、方案选择:针对上述特点和难点,我们对可能将适用于于位该工程屋盖钢结构的三种施工方案在安全可靠性、质量掌控、工期掌控及成本资金投入四个方面展开了深入细致地分析与比较:方案一:“高空拼装、单无滑移、分片累积滑移就位”基本思路是:在航站楼(14)轴线侧布置台k50/50行走式塔吊,利用φ48×3.5脚手架钢管在航站楼一端架设22m×110m位移组装胎架,并沿(a)、(d)、(g)轴架设位移轨道(43kg/m)((a)轴位移轨道加装在托架梁上),(d)、(g)轴线的位移轨道加装在布置于+7.00m楼面的位移钢架架上,t-1、t-2各分段桁架通过奔跑式塔吊吊装至组装胎架上展开组在、校正、冲压及屋面檀条、系杆的加装(根据须要可以将屋面板、通风拎等加装不好),将组装不好的分片桁架(4-6榀)落下放到(a)、(d)、(g)轴三条轨道上,通过设置在+7.00m楼面上的三台8t装配卷扬机展开分片积累位移准备就绪。
机场钢结构工程施工方案

机场钢结构工程施工方案一、工程概述机场钢结构工程是指在机场建设中使用钢材作为主要结构材料进行构建的工程。
钢结构具有强度高、重量轻、可塑性好等优点,因此在机场建设中具有重要的地位和作用。
本文将详细介绍机场钢结构工程的施工方案。
二、施工准备1. 施工人员准备为了保证施工的顺利进行,需要组建具备相关经验和专业技能的施工团队,并进行相关培训,确保施工人员具备必要的技术素质和安全意识。
2. 施工准备材料除了常规的施工工具和设备,还需要准备以下材料: - 钢材:根据设计要求和工程规模准备合适的钢材,包括各种型号的钢梁、钢柱等。
- 焊接材料:保证施工过程中的焊接质量,准备合适的焊接材料和焊接设备。
3. 施工机械准备根据工程规模和具体需求,准备必要的施工机械设备,例如吊车、塔吊、钻机等,以提高施工效率和安全性。
4. 施工方案制定基于工程设计要求和具体情况,制定详细的施工方案,包括施工工序、施工顺序、安全措施等,确保施工过程的顺利进行。
三、施工工艺1. 地基处理钢结构施工前需要对地基进行处理,以确保地基质量满足钢结构施工要求。
包括地面平整、紧实、无杂物等。
2. 钢结构制作钢结构制作包括以下步骤: - 制作工艺准备:准备施工材料和设备,并控制好施工环境。
- 制作构配件:根据设计要求进行钢构配件的制作,包括切割、锻造、折弯、钻孔等。
- 拼装组合:将各个构配件按照设计图纸要求进行拼装组合,并进行严密的连接和固定。
3. 焊接钢结构施工过程中,需要进行焊接工作,包括以下注意事项: - 焊接材料和设备准备:选择适合的焊接材料和焊接设备。
- 焊接工艺选择:根据焊接材料和结构要求选择合适的焊接方法和工艺参数。
- 焊接质量控制:严格按照焊接工艺要求进行焊接操作,保证焊缝质量符合设计要求。
4. 安装钢结构制作完成后,需要进行安装工作,包括以下步骤: - 临时支撑:采用适当的支撑和固定措施,确保安装过程中结构的稳定和安全。
- 吊装安装:利用吊车等设备进行结构吊装和安装,确保结构的正确位置和稳定性。
钢结构加工制作施工方案与技术措施

钢结构加工制作施工方案与技术措施本工程钢构件的制作加工,由与我公司长期合作的具有一级制作加工资质的工厂承担,全部在工厂按设计图纸的要求加工完成后,运至施工现场安装。
1.加工制造工艺流程2.制作加工2.1 制作施工准备钢结构制作施工准备阶段应对以下五个方面进行质量控制,以保证构件制作施工全过程在受控制之下进行。
(1)施工人员准备A对技术复杂、难度大、精度高的特殊工序,应由技术熟练、经验丰富的人员来完成。
B从事结构制作的各类焊工,必须经过考试合格,并取得国家机构认可部门颁发的合格证,证件注明施焊内容、有效期限。
C检查焊缝质量的无损检测人员持有相应等级范围检测资格证。
D各岗位人员均应持证上岗。
(2)材料准备A根据设计图纸要求采购材料。
钢材、压型钢板、焊材、高强螺栓、保温材料等材料均要符合设计要求的规格、品种、性能,并有材质证明书。
焊接用焊条、焊丝、焊剂等应与母材匹配。
所进材料按规定做好复检记录,并做好主材使用跟踪记录。
B钢材存放于干燥的专用场地,不允许露天存放。
C钢材表面损伤,经打磨修整后,局部厚度削减量不应大于轧制厚度的公差。
D焊接用焊条、焊丝、焊剂应符合现行国标的有关技术要求并与主体金属强度相适应。
E普通螺栓采用Q235—A钢制作,双母。
螺栓、螺母、垫圈的尺寸及技术条件等须符合规范规定。
(3)施工设备准备A按生产上适用、性能上可靠、使用上安全、操作上方便等原则,合理选用各种设备。
B检验、测量设备应保证量值传递的统一、准确和可靠。
施工中所用的钢卷尺、板尺、角尺、水平尺、弹簧测力器等各种计量工具,入库前检定,保证进入施工现场的计量器具都是合格的,在施工中要定期检查所用工具。
保证每一个工具在同一工程中始终满足计量精度要求。
(4)施工技术准备A对设计图进行加工图转换。
B根据设计文件和施工详图的要求及制作车间的条件,编制制作工艺书。
制作工艺书包括施工所依据的标准,制作质量保证体系,成品的质量保证和为保证成品达到规定的要求而制订的措施,生产场地的布置,采用的加工、焊接设备和工艺装备,焊工和检查人员的资质证明,各类检查项目和生产进度计划表。
航站楼钢结构屋盖施工方案
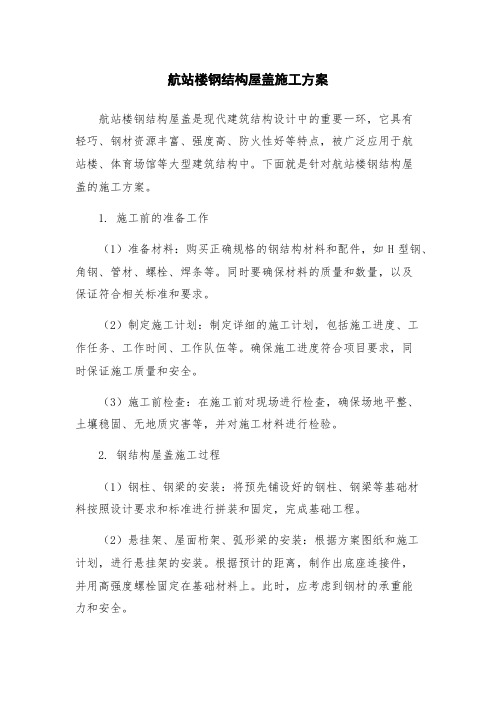
航站楼钢结构屋盖施工方案航站楼钢结构屋盖是现代建筑结构设计中的重要一环,它具有轻巧、钢材资源丰富、强度高、防火性好等特点,被广泛应用于航站楼、体育场馆等大型建筑结构中。
下面就是针对航站楼钢结构屋盖的施工方案。
1. 施工前的准备工作(1)准备材料:购买正确规格的钢结构材料和配件,如H型钢、角钢、管材、螺栓、焊条等。
同时要确保材料的质量和数量,以及保证符合相关标准和要求。
(2)制定施工计划:制定详细的施工计划,包括施工进度、工作任务、工作时间、工作队伍等。
确保施工进度符合项目要求,同时保证施工质量和安全。
(3)施工前检查:在施工前对现场进行检查,确保场地平整、土壤稳固、无地质灾害等,并对施工材料进行检验。
2. 钢结构屋盖施工过程(1)钢柱、钢梁的安装:将预先铺设好的钢柱、钢梁等基础材料按照设计要求和标准进行拼装和固定,完成基础工程。
(2)悬挂架、屋面桁架、弧形梁的安装:根据方案图纸和施工计划,进行悬挂架的安装。
根据预计的距离,制作出底座连接件,并用高强度螺栓固定在基础材料上。
此时,应考虑到钢材的承重能力和安全。
(3)屋面桁架的安装:在完成地面固定的基础材料上安装屋面桁架,在安装的过程中应注意在中央建造完整的桁架并通过支架将其托起,接下来将挂钩带到建筑物上,并将其固定,以保证其安全。
(4)屋面覆盖材料的安装:安装钢结构屋面覆盖材料的时候,应注意s新颖,抗风、耐火等性能,同时要考虑美观和舒适性,用焊接和螺栓固定到钢结构上。
(5)底部的百叶窗安装:在安装好钢结构屋面之后,需要在底部安装百叶窗。
采用自动开关控制,可以随时自动打开或关闭。
同时,要注意按照标准和规范进行选择。
3. 施工后的验收和检查施工完成后需进行验收,通常验收工作由现场总监和管理人员完成。
验收范围包括施工质量、安全、环保等,保证工程达到设计要求和标准。
总之,钢结构屋盖施工具有复杂性和专业性,需要专业的技术和经验。
同时,施工过程中要严格按照相关标准和规范进行验收和检查。
机场钢结构工程施工方案

机场钢结构工程施工方案一、项目概况机场钢结构工程是指在机场建设过程中所涉及的各种钢结构工程,主要包括航站楼、跑道、停机坪、地面设施等。
机场钢结构工程具有施工周期短、规模大、技术复杂等特点,对施工方案的制定和实施提出了较高的要求。
本次机场钢结构工程为某某国际机场扩建工程,总投资金额50亿元人民币,总占地面积2000亩,项目包括新建T1航站楼、扩建跑道、新建停机坪等。
工程旨在提升该机场的通航能力和服务水平,满足日益增长的航空客流需求。
本施工方案旨在合理安排施工进度、保障施工质量、确保施工安全、提高工程施工效率,最终实现项目的顺利交付和竣工。
二、施工组织1. 施工组织机构为了确保机场钢结构工程的施工顺利进行,保证工程质量、安全和有效进度,我们将建立以下施工组织机构:(1)总包单位:由某某建筑工程有限公司担任,负责工程的总体组织和协调,并对各专业施工单位进行管理和监督。
(2)设计单位:由某某设计院负责设计工作,并协助总包单位对施工过程中的设计变更进行审核和调整。
(3)监理单位:由某某监理工程有限公司担任,负责对施工过程进行监督和检查,确保施工质量和进度。
(4)安全质量监督员:由总包单位提供,专职进行施工现场安全和质量工作的监督。
2. 人员分工(1)总包单位:设立项目经理、工程师、材料员、质量监督员等工作人员。
项目经理负责工程的整体管理和协调;工程师负责现场技术支持和协调;材料员负责材料采购和使用;质量监督员负责施工质量检查。
(2)设计单位:设立总工程师、结构工程师等工作人员,负责施工图纸的审核和设计变更的协调。
(3)监理单位:设立总监理工程师、项目监理工程师等工作人员,负责对施工过程进行监督和检查。
(4)安全质量监督员:设立安全监督员、质量监督员等工作人员,负责施工现场的安全和质量检查。
三、施工准备工作1. 施工前准备:(1)安排项目经理、工程师、监理工程师和安全质量监督员对施工计划进行细化,明确各专业施工单位的具体任务和施工进度。
钢结构加工制作方案

钢结构加工制作方案随着现代建筑技术的不断发展,钢结构建筑已经成为建筑行业中的重要构件。
钢结构广泛应用于工业厂房、体育馆、展览馆、桥梁、高层建筑等,成为现代建筑中的重要组成部分。
本文将介绍钢结构加工制作方案,以帮助钢结构制造企业更好地开展钢结构加工业务。
钢结构制作工序钢结构制作过程复杂,需要进行多道工序。
一般包括材料的采购、切割、焊接、钻孔、喷漆等环节。
材料采购钢结构制作的第一步是材料采购。
选用质量优异的原材料是保证钢结构质量的前提。
在采购时建议选购质量好、供货量稳定的钢材制造企业的产品。
在采购时应注意确定环境温度和场地情况,从而确保材料的适应性能。
切割采购回来的钢材需要进行切割。
钢材长度、宽度、高度等尺寸需要精确计算,进行相应的切割。
切割设备通常包括火焰切割机、等离子切割机、数控切割机等,通过合理组合进行切割。
焊接钢结构制作过程中,焊接是必不可少的工序。
主要分为手工焊、气体保护焊、电弧焊、埋弧焊等多种形式。
选择不同的焊接方式,需要考虑焊接的材料、厚度等因素。
钻孔是钢结构制作的必要工序之一。
钻孔作用是为了将钢杆、钢板连接起来,在钢结构加工中扮演着相当重要的角色。
钻孔设备有手持钻机、钻床等。
喷漆在钢结构制作中,最后一个工序是喷漆。
喷漆可以起到美化产品的作用,同时还可以起到保护钢结构表面的作用。
主要有电泳涂漆、粉末涂漆等喷涂方式。
选用不同的喷涂方式,需要考虑产品的用途及所处环境等因素。
钢结构制作要点•控制加工误差:建议在加工过程中采取各种措施,控制加工误差。
只有做好加工精度控制,才能保证钢结构产品的质量。
•保持良好的通风环境:焊接工序会产生大量的废气和烟雾,需要保持良好的通风环境。
同时,在钻孔和切割等工序中也需要保持良好的通风。
•加强安全管理:在加工过程中,要严格遵守安全管理规定,切勿随意操作各类设备,确保作业过程中的安全。
•依据规范加工:在加工过程中,需要遵循相应的标准和规范要求,避免一些不必要的损伤和浪费。
机场航站区钢结构工程施工组织设计方案
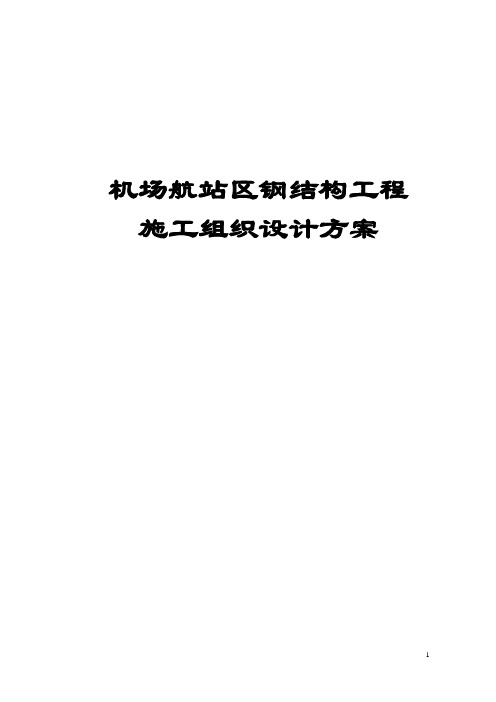
机场航站区钢结构工程施工组织设计方案一、总则1、本施工方案为**机场钢结构工程投标方案,具体施工时可进一步完善细化。
2、本方案根据中国航天建筑设计研究院完成的“**机场钢结构工程”进行编制。
3、本工程详图设计,钢结构工厂制作,现场拼、安装的质量检验严格按照现行国家规范标准的要求执行。
二、工程概况该项目位于**市**,为原航站楼的改造及扩建部分。
扩建部分分为三部分:Ⅰ区为原航站楼后部贴建的二层钢框架结构,梁柱均采用Q345B钢,柱网6.9m×6.9m,柱高9.3m,总长142.84m,投影面积2294㎡,钢结构重379 吨;Ⅱ区为原航站楼前部贴建的锥形钢架结构,梁柱及斜撑杆均采用Q235C钢,柱距13.8m,跨度12.3m,悬挑6m,柱高9.3m,投影面积2612㎡,钢结构重212 吨;Ⅲ区为原航站楼东侧贴建的单层钢框架(局部夹层)结构,梁柱均采用Q235B钢,柱网6.9m×6.4m,柱高7.5 m,总长27.6m,投影面积185㎡,钢结构重31吨。
另外,钢制作登机桥3座,重量26吨。
投影面积共5091㎡钢结构共648吨。
框架柱采用热扎H型钢及钢管,规格为HW400×400×13×21至HW300×300×10×15及ø550×18、ø219×12。
框架梁采用焊接H型钢,规格为HW500×250×12×16至HW180×100×6×10,局部为便截面HW(350-1100)×250×12×14。
檩条采用高频焊接H型钢H200×100×4.5×6。
其他构件采用普通型材。
三、钢结构施工工艺1、施工工艺流程施工工艺流程如下:钢结构施工工艺流程图 现场准备、机具及周转材料进场 焊机、焊接设施就绪 竣工验收 绘制细部施工详图放样、下料原材料进厂检验 组拼、焊接 平直、矫正 除锈、涂装 构件制作台模设置图纸会审(交底) 包装、运输 整体测量 清理现场竣工资料移交 压型钢板安装 钢结构安装工程检测控制 搭设脚手架拼装平台 柱网复核 测量放线 标识、预拼装 钢柱、钢梁安装 檩条、支撑安装2、施工准备2.1、熟悉图纸,组织技术人员进行图纸自审,提出问题,以便在设计交底或图纸会审中了解清楚。
机场项目钢筋工程方案范本

机场项目钢筋工程方案范本一、项目背景随着民航业的快速发展和旅客运输量的增加,各地机场的建设和扩建工程也在不断进行。
机场工程是一个复杂的大型工程项目,其建设要求高、投资大、周期长,且与安全相关度高,因此在机场项目的设计与施工中,钢筋工程显得尤为重要。
二、项目概况本项目是一座新建机场工程,总建筑面积达10万平方米,包括航站楼、塔台、跑道、停机坪等整体建筑。
由于工程规模庞大,机场使用寿命长,因此在钢筋工程的设计与施工中需要高度重视。
三、工程技术要求1. 钢筋工程设计要符合国家相关标准,考虑到机场建筑的特殊性,需要考虑地质条件、风荷载、地震动、冻融、设备的震动等因素。
2. 钢筋混凝土的配筋要经过严格的计算与优化,以保证机场建筑的强度和稳定性。
3. 钢筋工程施工需要严格按照设计图纸执行,确保每一根钢筋的数量和位置符合设计要求。
4. 钢筋工程施工材料和设备的选择要符合国家标准,且要求质量合格。
四、工程实施方案1. 钢筋混凝土设计1.1 确定框架结构根据机场建筑的功能和结构特点,确定适用的结构形式,如框架结构、框架-墙结构、框架-剪力墙结构等。
1.2 钢筋混凝土配筋计算经过结构力学计算,确定混凝土结构的受力情况,设计合理的钢筋配筋方案。
1.3 防护层和保护层设计针对机场建筑下部混凝土结构,设计防护层和保护层,以提高结构的耐久性和安全性。
2. 钢筋工程施工2.1 严格遵循设计图纸施工过程中,施工方要严格按照设计图纸中的钢筋布置要求进行,确保每一根钢筋的数量和位置符合设计规定。
2.2 施工材料和设备选择选择符合国家标准的钢筋、混凝土、钢筋焊接设备等材料和设备,确保工程质量。
2.3 现场监测在施工过程中,对钢筋混凝土结构的施工质量进行实时监测,及时发现和解决问题。
五、工程质量控制1. 施工单位要制定严格的施工方案和质量控制措施,确保施工质量符合设计要求。
2. 设计单位要派专业人员对钢筋混凝土结构的施工进行监督和验收,确保施工质量符合设计要求。
机场钢结构工程施工方案

机场钢结构工程施工方案主要包括以下几个方面:工程概述、施工准备、施工流程、质量控制、安全防护和环境保护。
以下是详细的机场钢结构工程施工方案。
一、工程概述机场钢结构工程主要包括航站楼、机库、飞机维修车间、控制塔等建筑的钢结构施工。
本方案以航站楼为例,介绍机场钢结构工程施工。
航站楼钢结构工程主要包括主钢架、屋面梁、支撑系统、檩条、吊车梁等部分的安装。
二、施工准备1. 技术准备:根据设计图纸和相关规范,编制施工组织设计、施工方案、安全技术措施等文件。
对施工人员进行技术培训和安全教育。
2. 施工现场准备:清理现场,平整土地,设置临时设施,如办公室、仓库、临时道路等。
3. 施工设备准备:根据工程量和工作量,配置足够的施工设备,如吊车、行车、焊机、切割机、测量仪器等。
4. 材料准备:根据工程需要,提前采购合格的钢材、焊接材料、紧固件等材料。
三、施工流程1. 施工顺序:先安装主钢架,然后安装屋面梁、支撑系统、檩条、吊车梁等部分。
2. 主钢架安装:先将主钢架分段,然后在基础上设置预埋件,采用吊车将主钢架吊装到预埋件上,调整到位后进行焊接。
3. 屋面梁安装:屋面梁分为若干段,采用吊车将梁段吊装到主钢架上,按照设计要求进行焊接。
4. 支撑系统安装:支撑系统包括柱支撑和屋面支撑,采用吊车将支撑杆件吊装到相应位置,焊接固定。
5. 檩条安装:檩条分为若干段,采用吊车将檩条段吊装到屋面梁上,按照设计要求进行焊接。
6. 吊车梁安装:吊车梁分为若干段,采用吊车将梁段吊装到主钢架上,按照设计要求进行焊接。
四、质量控制1. 严格按照设计图纸和规范施工,确保结构尺寸和连接质量。
2. 焊接质量控制:采用合格的焊接材料,严格按照焊接工艺进行施工,焊后进行焊缝检查,不合格的焊缝及时整改。
3. 紧固件质量控制:选用合格的紧固件,确保连接牢固。
4. 防腐和防火措施:根据设计要求,对钢结构进行防腐和防火处理,确保结构的使用寿命。
五、安全防护1. 施工现场设置安全警示标志,提醒施工人员注意安全。
钢结构加工制作方案

钢结构加工制作方案
钢结构是一种重要的建筑结构形式,具有高强度、轻质、抗震性能好等优点,因此在现代建筑中得到了广泛的应用。
钢结构的加工制作是保证建筑质量和安全的重要环节,下面将介绍钢结构加工制作的方案。
首先,钢结构加工制作的第一步是设计方案的确定。
在设计方案中需要考虑到建筑的结构形式、荷载情况、使用功能等因素,确定合理的结构形式和材料规格,以及合理的连接方式和工艺要求。
其次,钢结构加工制作的第二步是材料的准备和加工。
在材料的准备中需要选择优质的钢材,根据设计要求进行切割、成型、打孔等加工工艺,确保材料的尺寸精准、表面光洁,并进行防锈处理。
第三,钢结构加工制作的第三步是焊接和组装。
在焊接和组装过程中需要严格按照设计要求进行,采用合适的焊接工艺和设备,确保焊接接头的质量和牢固度,同时进行组装时需要注意结构的平整度和垂直度。
最后,钢结构加工制作的最后一步是质量检验和涂装。
在质量检验中需要对钢结构的尺寸、焊接接头、表面质量等进行检测,确保符合设计要求和相关标准,然后进行涂装处理,提高钢结构的耐腐蚀性能和美观度。
总之,钢结构加工制作是一个复杂而又重要的过程,需要设计、加工、焊接、组装、质量检验等多个环节的严格把控,只有这样才能保证钢结构的质量和安全。
希望以上方案能够对钢结构加工制作有所帮助。
呼和浩特白塔机场扩建工程航站楼钢结构工程质量评估报告

以我给的标题写文档,最低1200字,要求以Markdown文本格式输出,标题为:呼和浩特白塔机场扩建工程航站楼钢结构工程质量评估报告# 呼和浩特白塔机场扩建工程航站楼钢结构工程质量评估报告## 概述呼和浩特白塔机场扩建工程航站楼钢结构工程作为整个机场建设的重要部分,对机场的使用效率、安全性以及整个建筑群的造型影响巨大。
为此,我们对该工程的钢结构工程进行了全方面的质量评估和分析。
## 工程概况呼和浩特白塔机场扩建工程航站楼钢结构工程位于呼和浩特白塔机场扩建工程中,距离原机场航站楼约1.5公里。
该航站楼建筑面积约4.8万平方米,总建筑高度约31米,钢结构总重量约7500吨。
## 工程评估### 项目设计方案评估我们首先对该航站楼工程的设计方案进行了评估。
评估结果表明,项目设计方案满足了相关国家标准和建筑安全规范,符合工程建设要求。
设计方案中的钢结构结构形式合理、节点连接方式可靠,满足工程使用要求。
### 现场施工质量评估针对该航站楼钢结构工程的现场施工,我们进行了详细的质量评估。
评估结果表明,施工方案合理,施工过程中的各项环节得到了严格的控制和检查,每道工序都符合相关标准要求,工程运行稳定,施工期间未出现任何质量问题。
### 钢结构质量评估作为该工程的重要组成部分,钢结构质量也得到了评估。
评估工作主要围绕钢结构件的制作、运输、安装、验收等方面展开。
评估结果表明,在生产过程中,制作车间严格管理,生产工艺合理,使用的原材料质量合格。
在运输和安装过程中,施工方严格把关,安全可靠,钢结构件完好无损。
验收过程中,各项指标均符合要求,不合格情况得到了及时修正处理。
## 结论通过对呼和浩特白塔机场扩建工程航站楼钢结构工程的全方位评估和分析,我们得出以下结论:- 该工程设计方案符合相关要求,结构形式合理、节点连接方式可靠;- 该工程现场施工各项环节得到了严格的控制和检查,工程运行稳定,未出现任何质量问题;- 该工程钢结构件制作和安装过程中得到了严格控制,各项指标均符合要求;综上所述,呼和浩特白塔机场扩建工程航站楼钢结构工程质量达到了设计要求和建设标准。
机场钢结构工程施工方案

机场钢结构工程施工方案一、前言机场是一个国家的门户,是国际间物流和人员交流的重要枢纽。
机场的建设将直接影响一个国家的国际形象和经济发展。
在机场建设中,钢结构工程是至关重要的一部分,其质量和安全直接关系到机场的使用和运营。
本文将以某机场钢结构工程施工方案为例,详细介绍钢结构工程的施工流程、施工技术和质量控制方法,从而保障机场钢结构工程的顺利进行。
二、工程概况某机场钢结构工程包括航站楼、停车场、货运区和塔楼等建筑,总建筑面积约为10万平方米。
其中,航站楼为主体建筑,采用钢框架结构,总建筑面积为6万平方米。
停车场和货运区为附属建筑,采用钢筋混凝土结构,分别建设在航站楼的两侧。
塔楼位于航站楼正中心,高度约为50米,为机场的标志性建筑。
三、施工准备1.施工组织设计:在项目启动前,施工单位应根据项目需求制定施工组织设计方案,明确施工内容、施工组织结构、任务分工和施工进度等。
同时,应合理配置施工人员和设备,确保施工进度和质量。
2.施工人员培训:在施工前,施工单位应进行相关人员的培训,包括对工程监理、施工管理人员和施工工人的技术培训,确保施工人员能够熟练掌握施工流程和工艺要求。
3.材料采购:施工单位应提前准备好所需的钢结构材料、施工设备和施工工具,确保施工进度和质量。
同时,应对采购的材料进行质量检测,确保符合相关标准和规定。
4.技术方案确认:在施工前,施工单位应确认好钢结构工程的施工技术方案,包括施工流程、工艺要求和安全措施等。
同时,应制定相应的施工方案,确保施工进度和质量。
四、施工流程1.基础施工:钢结构建筑的基础施工是整个工程的基础,直接关系到建筑物的承重能力和稳定性。
在基础施工阶段,应根据设计要求进行地质勘察和基坑开挖,然后进行地基处理和钢筋混凝土浇筑,最后进行基础验收,确保基础符合设计要求。
2.钢结构搭设:在基础验收合格后,应进行钢结构的搭设工作。
首先,应根据设计图纸确定吊装方案和起吊点,然后进行钢梁和柱的吊装和连接,最后进行梁柱的焊接和验收,确保钢结构的稳定性和安全性。
钢结构加工制作方案

钢结构加工制作方案一、钢结构加工制作1、钢结构件制作工艺流程见下图。
钢结构件制作工艺流程图二、放样核对图纸的安装尺寸和孔距;以1:1的大样放出节点,核对各部分的尺寸;制作样板和样杆作为下料、弯制、铣、刨、制孔等加工的依据。
放样时,铣、刨的工件要考虑加工余量,焊接构件要按工艺要求预留焊接收缩余量。
放样和样板(样杆)的允许偏差三、号料检查核对材料;在材料上划出切割、铣、刨、弯曲、钻孔等加工位置;打冲孔及标出零件编号。
号料时应尽可能做到合理用材。
号料的允许偏差(mm)四、切割钢材下料的方法采用气割,气割前应将钢材表面切割区域内的铁锈、油污等清除干净;切割后断口上不得有裂纹和大于1.0mm的缺口,并应清除干净边缘上的熔物和飞溅物等。
切割截面与表面垂直度偏差不大于钢材厚度的10%且不大于2mm。
气割的允许偏差(mm)注:t为切割面厚度。
五、制孔A、B级螺栓孔(Ⅰ类孔),应具有H12的精度,孔壁表面粗糙度R a不应大于12.5um。
注:①A、B级螺栓孔、H12精度,是根据现行国家标准《紧固件公差螺栓、螺钉和螺母》和《公差与配合》的分级规定确定的;②R a是根据现行国家标准《表面粗糙度参数及其数值》确定的。
C级螺栓孔(Ⅱ类孔),孔壁表面粗糙度R a不应大于25m,允许偏差应符合下表规定。
螺栓孔孔距的允许偏差应符合下表的规定。
螺栓孔的允许偏差超过上述规定时,不得采用钢块填塞,可采用与母材材质相匹配的焊条补焊后重新制孔。
6、钢板厚度大于6mm时应开坡口。
7、钢结构件组装经检验合格后方可焊接。
8、平直焊缝应采用自动焊机焊接。
焊缝高度应符合图纸要求。
焊接时应采取有效措施防止钢结构件变形。
9、预拼装和检验合格的构件方可进行打砂、除锈。
打砂、除锈质量应符合现行国家标准《涂装前钢材料表面锈蚀等级和除锈等级》和设计要求。
打砂除锈质量经质检部检验合格的,方允许按设计要求进行涂装。
质检部要做好打砂除锈检验、验收记录。
- 1、下载文档前请自行甄别文档内容的完整性,平台不提供额外的编辑、内容补充、找答案等附加服务。
- 2、"仅部分预览"的文档,不可在线预览部分如存在完整性等问题,可反馈申请退款(可完整预览的文档不适用该条件!)。
- 3、如文档侵犯您的权益,请联系客服反馈,我们会尽快为您处理(人工客服工作时间:9:00-18:30)。
钢结构加工制作方案1 钢结构加工程序说明和工艺流程图1.1 钢结构加工程序说明本工程钢结构件加工主要由普通钢结构件等组成。
普通钢结构件为本工程主楼和指廊两部分的屋面部分,、包括有大厅的主拱、纵向中心拱、纵向联联系梁、横向屋面梁、斜腹杆、等结构件。
本工程钢结构工厂加工的原则是:1.1.1由于结构的特殊性,主拱以及其他构件的部件都通过工厂制作成单件,开好坡口,根据运输条件,确定单件长度,运输到现场.1.1.2本工程上的节点板构件、支座都是以半成品运输到现场。
1.1.3主拱在工厂制作成前后都要进行预处理,第一道的防锈油漆和中间油漆的工作。
工厂制作完成后,构件在现场胎架上根据现场吊装的要求进行拼装。
在现场胎架上验收合格后吊离构件,详细内容见现场拼装工艺简述。
1.2 钢结构制作工艺流程图预组2. 材料采购及管理2.1 材料采购本工程材料主拱及主拱斜拉杆采用Q235C结构钢;其它材料采用Q235B碳素结构钢。
对于本工程所采用的材料,需严格把好质量关,以保证整个工程质量。
2.1.1 材料入库后由总承包物资管理处组织质量管理部门对入库材料进行检验和试验。
2.1.2所有进厂材料均应有生产厂家的材质证明书。
2.1.3按供货方提供的供货清单清点各种规格钢管、型钢和钢板以及焊接材料、涂料数量,并计算到货重量。
2.1.4按供货方提供的钢管、型钢和钢板尺寸及公差要求以及焊接材料、涂料,对于各种规格钢管,抽查其口径、壁厚及椭圆度;对于各种规格型钢,检查其断面尺寸、壁厚、长度及直线度;对于各种规格钢板,检查其长宽尺寸、厚度及平整度,并检查钢管、型钢及钢板焊接材料的外表面质量。
2.1.5汇总各项检查记录,交现场监理确认。
2.2 材料管理2.2.1选取合适的场地或仓库储存本工程材料,按品种、按规格集中堆放,加以标识和防护,以防未经批准的使用或不适当的处置,并定期检查质量状况以防损坏。
2.2.2 材料的使用严格按排版图和放样资料进行领料和落料,实行专料专用,严禁私自代用。
2.2.3 焊接材料应按牌号和批号分别存放在具有适温或干燥的贮藏室内。
焊条和焊剂在使用之前应按出厂证明书上的规定进行烘焙和烘干,焊工应清除铁锈、油物以及其它污物。
2.2.4 车间剩余材料应加以回收管理,钢材、焊材、螺栓应按不同品种规格、材质回收入库。
2.2.5 加工时的材料识别材料排版及下料加工后的重要材料应按总承包项目部质量管理的要求作钢印移植。
2.2.6 原材料的对接1)型钢的对接需焊透,有探伤要求。
接长段≥500mm,且错开节点板及孔群100mm。
焊缝视安装情况而定是否磨平。
2)梁原则上由整块板下料。
若允许拼接则梁的上下翼板在跨中1/3的跨长范围内应尽量避免拼接,上下翼板与腹板三者的对接焊缝不应设置在同一截面上,应互相错开规定距离,与加劲板和孔群亦应错开100mm以上,且应分别对接后才能组焊成型。
原材料拼板焊接后按要求进行探伤。
3)分段弦杆应以钢管最大利用长度对接,但应使接头至腹杆与弦杆的节点≥500mm。
腹杆原则上不对接。
4)所有构件的原材料若长度、宽度不够,应先对接,符合要求后再制作构件。
情况特殊之构件可报技术部门以寻求解决的方法。
2.2.7 原材料检验程序流程3 各制作工序工艺3.1 放样3.1.1 放样前,放样人员必须熟悉施工图和工艺要求,核对构件及构件相互累计的几何尺寸的连接有否不当之处。
如发现施工图有遗漏或错误,以及其他原因需要更改施工图时,必须取得技术部签证的设计变更文件,不得擅自修改、3.1.2 放样使用的钢尺,必须经计量单位检验合格。
丈量尺寸,应分段叠加,不得分段测量后相加累计全长。
1.3 放样应在平整的放样台上进行。
凡放大样的构件,应以 1 :1的比例放出实样;当构件零件较大,难以制作样杆、样板时,可绘制下料图。
3.1.4 样杆、样板的测量必须平直;如有弯曲,必须在使用前予以矫正。
3.1.5 样杆、样板制作时,应按施工图和构件加工要求,作出各种加工符号、基准线、眼孔中心等印记,并按工艺要求预放各种加工预量,然后号上冲印等印记,用磁漆(或其它材料)在样杆、样板上写出工程、构件及零件编号、零件规格孔径、数量及标注有关符号。
3.1.6放样工作完成,对所放大样和样杆、样板(或下料图)进行自检、无误后报专职检验人员检验。
3.1.7 样杆、样板应按零件号及规格分类存放,妥为保存。
3.1.8 放样和样板(样杆的允许偏差,应符合下表的规定)。
3.2 号料3.2.1 号料前,号料人员应熟悉样杆、样板(或下料图)所注的各种符号及标记等要求,核对材料牌号及规格、炉批号。
当供料或有关部门未作出材料配割(排料)计划时,号料人员应作出材料切割计划,合理排料,节约钢材。
3.2.2 号料时,复核材料的规格,检查材质外观,凡发现材料规格不符要求或材质外观不符要求者,需及时报质管、技术部门处理;遇有材料弯曲或不平值超差影响号料质量者,须经矫正后号料。
3.2.3 凡型材端部存有倾斜或板材边缘弯曲等缺陷,号料时应去除缺陷部分或先行矫正。
3.2.4 根据锯、割等不同切割要求和对刨、铣加工的零件,预放不同的切割及加工余量和焊接收缩量。
3.2.5 因原材料长度或宽度不足需焊接拼接时,必须在拼接件上注出相互拼接编号和焊接坡口形状。
如拼接件有眼孔,应待拼接件焊接、矫正后加工眼孔。
3.2.6 相同规格较多、形状规则的零件可用定位靠模下料。
使用定位靠模下料时,必须随时检查定位靠模和下料件的准确性。
3.2.7 按照样杆、样板的要求,对下料件应号出加工基准线和其他有关标记,并号上冲印等印记。
号孔应按照工艺要求进行,对钻孔的眼孔,应在孔径上号上五梅花冲印。
在每一号料件上用漆笔写出号料件及号料件所在工程、构件的编号,注明孔径规格及各种加工符号。
3.2.8 下料完成,检查所下零件规格、数量等是否有误,并作出下料记录。
3.2.9 号料与样板(样杆)允许偏差应符合下表的规定。
号料与样杆(样板)的允许偏差3.2.10 当精度要求较高构件的钢材号料时宜用针划线,划线宽度约0.3mm,较长的直线段为0.8mm,可用弹簧钢丝配合直尺、角尺联合划线。
3.3 矫正成型3.3.1 钢材的初步矫正,只对影响号料质量的钢材进行矫正,其余在各工序加工完毕后再矫正或成型。
3.3.2 钢材的机械矫正,一般应在常温下用机械设备进行,矫正后的钢材,在表面上不应有凹陷,凹痕及其他损伤。
3.3.3 碳素结构钢和低合金高强度结构钢,允许加热矫正,其加热温度严禁超过正火温度(900℃)。
用火焰矫正时,对钢材的牌号为Q345的焊件,不准浇水冷却,一定要在自然状态下冷却。
3.3.4 弯曲成型加工1)弯曲加工分常温和高温,热弯时所有需要加热的型钢,宜加热到880℃~1050℃,并采取必要措施使构件不致“过热”,当温度降低到普通碳素结构钢700℃,低合金高强度结构钢800℃,构件不能再进行热弯,不得在兰脆区段(200℃~400℃)进行弯曲。
2)热弯的构件应采用电加热,成型后有特殊要求者,再退火处理,冷弯的半径应为材料厚度的2倍以上。
3.3.5 加工弯曲成型的零件,其弦长大于1500mm,应用弦长不小于1500mm的弧形样板检查;弯曲零件弦长小于1500mm时,样板的弦长不应小于零件的弦长的2/3,其间隙不得大于2.0mm。
3.3.6 组装成型时,应采用定位点焊,作好标记,点焊时,点焊高度不得超过设计焊缝高度的2/3,长度应大于30~75mm,间距应均匀,最大不得超过300~500mm。
3.3.7 弯曲或弯折及类似成型构件,不允许表面产生损伤或裂纹。
3.4 制孔3.4.1采用数控钻床钻模板后套钻节点板螺栓孔群(针对相同类型数量多),一般螺栓孔(针对相同类型数量较少)和地脚螺栓孔的钻孔,可采用划线钻孔的方法。
采用划线钻孔时,孔中心和周边应打出五梅花冲印,以利钻孔和检验。
钻孔公差如下:3.4.2孔位的允许偏差3.5 工厂组装3.5.1 在组装前,组装人员必须熟悉施工图、组装工艺及有关技术文件的要求,并检查组装零部件的外观、材质、规格、数量,当合格无误后方可施工。
3.5.2 组装焊接处的连接接触面及沿边缘30~50mm范围内的铁锈、毛刺、污垢、冰雪等必须在组装前清除干净。
3.5.3 板材、型材需要焊接拼接时,应在部件或构件整体组装前进行;构件整体组装应在部件组装、焊接、矫正后进行。
3.5.4 构件的隐蔽部位应先行涂装、焊接,经检查合格后方可组装;完全封闭的内表面可不涂装。
3.5.5 构件组装应在适当的工作平台及装配胎模上进行。
3.5.6 组装焊接构件时,对构件的几何尺寸应依据焊缝等收缩变形情况,预放收缩余量;对有起拱要求的构件,必须在组装前按规定的起拱梁做好起拱。
不要求起拱的构件,不允许出现下挠。
3.5.7 胎模或组装大样定型后须经自检,合格后质检人员复检,经认可后方可组装。
3.5.8 构件相邻节间的纵向焊缝,以及其他构件同一截面的多条对接焊缝“十字型”或“T字型”拼缝均应错开200mm以上,或按工艺要求。
3.5.9 构件组装时的连接及紧固,宜使用活络夹具紧固器具。
3.5.10 拆取组装卡夹具时,不得损伤母材,可用气割方法割除,切割后并磨光残留焊疤。
3.5.11构件组装完毕后应进行自检和互检,准确无误后再提交专检人员验收,若在检验中发现问题,应及时向上反映,待处理方法确定后进行修理和矫正。
3.5.12构件组装精度,见下表。
3.6 焊接3.6.1 焊接设备下列焊接设备适用于该工程的的焊接工作3.6.2 焊工资格从事本工程焊接工作的焊工(包括定位焊工)采用经业主监理认可的标准考试合格的焊工进行焊接;焊工从事的焊接工作必须具有对应的资格等级。
3.6.3 焊接材料1) 焊接材料的选择2) 材料的烘焙和储存焊接材料在使用前应按材料说明书规定的温度和时间要求进行烘焙和储存;如材料说明要求不详,则按下表要求执行:3.6.4 焊接工艺参数1) 工厂制作焊接参数2) 预热和层间温度焊前,母材的最小预热温度和层间温度应按下表要求执行:a. .接头的预热温度应不小于上表规定的温度,层间温度不得大于230℃。
b. 接头预热温度的选择以较厚板为基准,应注重保证厚板侧的预热温度,严格控制薄板侧的层间温度。
c. 预热时,焊接部位的表面用火焰或电加热均匀加热,加热区域为被焊接头中较厚板的两倍板厚范围,但不得小于100mm区域。
d. 预热和层间温度的测量应采用测温表或测温笔进行测量。
e. 当环境温度(或母材表面温度)低于0℃(当板厚大于30mm时为5℃)而大于-18℃时,不需预热的焊接接头应将接头的区域的母材预热至大于21℃,焊接期间应保持上表规定的最低预热温度以上。
3) 焊接环境当焊接处于下述情况时,不应进行焊接:a. 被焊表面处于潮湿状态,或暴露在雨、雪和高风速条件下。