日产GK现场管理改善概要
日产GK现场管理改善概要

JIT・SQC・TPM →排除浪费的工具
JIT:将物品流程切开口后进行综合改善 SQC:统计品质改善,问题的分析・解析 TPM:在设备信赖上切开口后进行综合改善
GK(现场管理) →日产生产方式的基石
是汇总「工作的标准化和改善」,「人材的培养」所 形成的 是制造品质在现场QCT水准的维持、及提高的内 容
三
不良品
不
不流出
不良品
原
则
不接受
不良品
全数品质 納品 保证
(QCT)
销售店
顾客满意
东风日产责任
顾客
13
LOGO
二、什么现场管理
6-2、现场管理的推进:
不製造
三
不良品
不
不流出
不良品
原
则
不接受 不良品
全数品质 保证
(QCT)
納品 东风日产
顾客满意
供应商责任
顾客
14
LOGO
二、什么现场管理
6-3、现场管理的推进:
LOGO
GK现场管理改善 概要
1
LOGO
1 2 3 4 5
目录
经营与现场管理 什么现场管理 GK过往活动成果 GK提升思路 GK诊断说明
2
LOGO
一、经营与现场管理
1、 现场管理在企业经营中的位置???
公司利益(盈利)向上
*成本下降 (只有成本下降,销售与公司利
益才能均有效向上)
*优良的品质(Q) *低成本,低价格 (C) *必要的时候生产必要的产品(D)
实现制造产品的理想姿态重点在于设定标准、持续提高标准,尽快运行PDCA循环。
生产活动
入/ Input 生产三要素
日产GK现场管理要义及其推进策略

日产GK现场管理要义及其推进策略一、对GK的认识(一)GK的基本思想及理念日产现场管理(GK)是日产生产方式的重要组成部分,誉为日产生产管理的基石。
其基本思想是以品质管理为核心,彻底消除浪费。
为达成这一目标,GK采取了以下几方面的措施:1、标准化。
一切工作均有基准,GK诊断的起点即是基准的有无。
以标准为基础,围绕PDCA的良性循环,确立一种绝对不会倒退的管理体制。
让工作标准化,遵守已确定的标准,是否遵守这个标准在作业观察中可作检查,如果不能遵守标准,就应通过追寻原因采取措施以谋求工作的稳定化。
2、异常的管理。
为了实现基准定义的状态,将已发生问题的原因分类成4M,再分析其真正的原因,从源头加以改善,使相同的问题不再发生。
处理问题的方法中,可分类成:为了立即防止问题的发生或不合格品流向下一道工序的“暂定对策”及针对问题根源的“恒久对策”。
3、预知性管理。
在问题发生之前,预先整理出所能想到的会影响生产的问题的原因,并制订防患于未然的对策。
4M发生变更时,新产品、新工艺、新设备投用时,都需要进行预先管理。
4、显现化。
GK无限追求显现化,使管理工作可见、管理效果可见。
这些管理理念贯穿于班组管理充实度、标准作业书等十二个文件夹中,也贯穿于Q、C、T、S、M等各项管理目标中。
理解这些管理理念对于推行GK至关重要,否则容易迷失在GK众多的表单之中。
(二)GK的表单由于GK对于显现化的无限追求,表单和看板就成了GK区别于其他现场管理的显著特征,也是其推进难点。
初略统计来自于东风日产的GK原版资料,其表单有上百项,请见下表:而根据我对GK的理解、结合涂装管理实际拟使用的表单也有上百项。
需要使用的表单及各表单间的逻辑关系请见下表:如果不理解这些表单的逻辑关系、如果不把GK作为一个系统来推进,那么GK将是难于被实施的。
(三)GK运行的层级把涉及QCTSM等几乎全部方面的众多管理要素放到班组现场管理,是GK区别于其他现场管理的又一显著特征。
现场改善活动标准书(文件稿)110718

(会签页。
此页无正文)一、现场改善活动目的为有效实现公司生产经营总目标,提高经营效益,有效提升现场管理水平,贯彻NPW(日产生产方式)对生产现场的要求,开展现场改善活动。
二、组织机构三、相关支持单位职责保证改善活动有效开展,鼓励员工积极投入改善活动,提高工场管理运营水平。
根据改善类别,结合部门职能,对相关部门在改善活动中的职责分工界定如下:经营计划部:较大改善项目的资源协调;财务会计部:改善费用管理、收益管理;财务层面的降低成本、提高收益的提案会签及效果确认;人力资源部:三等及以上改善奖励费用管理;工务部:涉及设备、工装硬件的改善方案会签及效果确认;制造部:现场作业编程、调整等有关生产提升的改善方案会签及效果确认;品质保证·TCS部、质量检查部:有关品质提升的改善方案会签及效果确认;SCM部:有关物流工作的改善方案会签及效果确认;生产技术部:涉及工艺变更的改善方案会签及改善后工艺符合性的确认;其他部门:结合本部门职能,各司其职,协同做好改善活动。
四、改善提案相关规定(一)提案内容1、能节能降耗的有关提案;2、能加强资材管理、节约资材,开发与利用废物的各种提案;3、能稳定和提高产品品质的提案;4、能提高生产效率的各种操作方式、工艺规程;5、能防止废品产生的各种方法与手段;6、能改进及维护设备、工具的各种提案;7、能提高生产技术的各种提案;8、能减轻劳动强度,提高事务处理能力及省时、省力的各种提案;9、输送、搬运及保管方面的各种能提高效益的提案10、有关安全生产、卫生健康、福利、劳保方面的各种提案;11、能促进规章制度执行及提高生产积极性的各种提案;12、改善生产组织及管理方法的各种提案;13、部品、构件交货形式方法的改进、改善方面的提案;14、改善经营管理与提高生产能力的提案;15、其他有利于提高公司效益的提案。
(二)不能作为提案的内容1、调整工资、改变工作条件及内容的意见;2、仅提出不满和苦恼以及要求,而无改进方法的提案;3、违反相关法律、法规的提案;4、其他无效率的提案。
日产作业环境改善活动

针对派遣员工 的推荐工位
针对高龄者・女性 的推荐工位
降低工位难易度,以便 实达现成Q任C何T人。均可以稳定 (增加推荐工位)
新车人机工程学评价
(部分)
数字试制的人机工程学评价
NIMS (以人为本的生产线)
新设备融入人机工程学要 件
优点导入活动
人机工程学指导生产线
共通指标管理
人机工程学诊断
人机工程学评价
改善/教育
’03年度
’04年度~
(全球)
速度提升
日产 Value-up期间的 作业环境目标
中期目标和达成时期
目 ES
部门技能一般
Information 250 1650
Optimal View 300
170
6 情报和作业
Optimal 700
Control
700 500
Poor
1800 1700 1400
-作业料架尺寸
Fair
700
Recommended
400
Poor
250
7 一般环境要因
- 噪音 - 振动 - 照明 - 温度 - 化学物质
通过作业环境的改善,不断扩大「以人为本,任何人 均可以稳定工作的工位」。
(参考)作业者和工位的要件
小 ↑ 精作 神业 负难 担度
↓ 大
C 等级
B 等级
A 等级
小 ← 肉体负担 → 大
c等级 b等级 a等级
Cc 工位 Bc 工位 Ac 工位
Cb 工位 Bb 工位 Ab 工位
Ca 工位 Ba 工位 Aa 工位
4.生产运营和教育 作业编成和轮调 限制作业者用的工程的确保 短期人员用的工程的确保 人机工程学教育
GK train
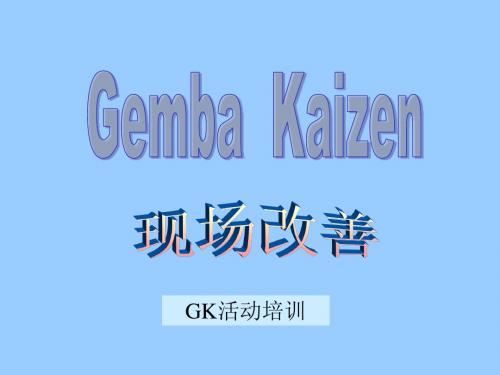
應該工作的地方,以 無謂的動作蒙混過去 偷工
馮改善把無謂的勞動 改成工作 合理化
動作的流費
三. 现场改善的黄金法则
当生产线发生异常. 追求3现 (Gemba Gembutsu Gemjisn ) 临时应急措施
用5Why找出根本原因和解决方法
防止再发生 标准化. 自律
四. 現場督導人員的角色
1. MTP:Management Training Program 管理訓練課程 TWI: Training Within Industries 督導人員訓練課程
通過消除浪費達至成本降低 注:全球生產系統示意圖
7
3
目的:A. 人際關系及員工參與的重要性 B. 持續改善流程.產品的方法及其价值. C. 以科學及合理的“計劃--執行--觀察”循環步驟, 用以管理人員和生產的實用性. 2. 早會 由督導人員及作業人員擔任主導的角色,每天早晨所做的第一件事, 將所做的不合格品陳列在桌上, 按現場現物的 原則當場提出改善對策.
东风日产 GK1 现场管理
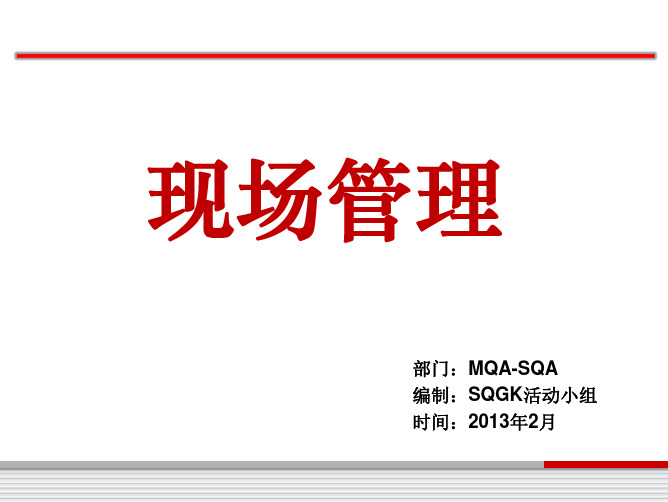
・做为团队的一员,每个人的职责都要明确, 团队成长的同时也是个人的成长。
【留意点】 ・将自己想规划的现场的样子传达给下属。 ・选拔培养核心指挥员。 ・明确目标、付与职责,发挥个性。 ・制定现场的规章制度并遵守。 ・通过与下属对话,交流想法。
第二章:现场的职责
3、管理者(科长)的职责
JIT;Just In Time 在必要的时间,把必要的
东西按照必要的量进行生产的生产方式
SQC;Statistical Quality Control 统
计的品质管理
TPM;Total Preventative Maintenance 综合的生产保全
第一章:日本生产方式中的现场管理
1、日本生产方式中现场管理的定位
■ 第二章:现场的职责
■ 第三章:现场管理推进和方法
第一章:日本生产方式中的现场管理
1、日本生产方式中现场管理的定位
●在日本生产方式中GK的定位:基石!
日产生产方式 制造产品的理想姿态
同期生产
没有现场管理就 没有日本生产 方式。
TQM
JIT
SQC
TPM
GK(现场管理)
TQM;Total Quality Management 全公司的品質管理活動
●在日本生产方式中GK教材的定位:
第一章:日本生产方式中的现场管理
1、日本生产方式中现场管理的定位
●在日本生产活动中现场管理的定位:
投入
人、物料、设备
生产系统
移动体系
加工体系
(生产管理) (工程学)
作业顺序体系 (现场管理)
(管理体系)
●劳务管理
●现场管理 ●品质管理
(●库存管理 ) ●作业管理 ●成本管理
NISSAN(日产公司) 的现场管理

NISSAN(日产公司) 的现场管理实施工作这是指通过部下的工作谋求目标的完成,也同时可以反映出职场的业绩。
这里所说的工作范围并非单纯意味着操作及操作指示,它还包含着给部下一定的活动范围以及推动上司的工作、与有关部门的协调等广泛的内容。
最重要的是监督者首先要行动。
③ 核查:C仅仅靠命令、指示、教育,管理现状的改变是不会实现的。
定期按照目标、标准活动进行核查才是最重要的。
在核查的方法中,有检查确认工作是否按照标准进行(要素系列的核查)以及检查Q、D、C的产品能否顺利地生产出来(结果系列的核查)两种方法。
以上这些内容在后面的"提高现场管理水平'的项目中有详细的解说,但现场的监督者前问题发生前就应事先察觉其异常点,并制定对策才是最重要的要点。
检查时的注意要点如下:根据管理项目,把握实际状况。
不能仅仅漠视与观察,而要灵活应用检查,测试。
采用任何人一看就明白是正常还是异常的方法进行管理。
注意所得出的结果不能散乱。
(要素系列的检查)核查的第一步是能否正确分析要素(人、物、设备、方法)的状态。
为此,经常参照标准巡视现场是很重要的。
(结果系列的检查)有必要在分析Q、D、C的结果后牢牢抓住要素的问题点。
即重要的不是检查结果,而是用结果进行检查。
另外,为了用结果进行检查,了解数据的记录以及背景也是很重要。
④ 处理:A当检查的结果显示已达到了预定的目标时,就应该回顾所采用的策略并深入各项标准的内容,设定并挑战更高要求的标准。
当脱离了预先设定的目标及标准时,会发现引起异常的要素,在了解了这些要素之后应予以处理,修正过去所订的计划和策略之后,再进入PDCA的循环中。
在这些处理方法中必须要注意的是:仅仅消除了异常的现象,而异常的情况仍有发生。
因此,关于为什么会形成这种状况,要首先反复地问五个"为什么'切实地追寻到问题的根源,防止问题的再度发生才是最重要的。
(2)把握事实情况应注意的要点:在前一项中说明了PDCA良性循环方法,这里要说明为了监督者能把握好事实情况,应该怎样做。
日产汽车现场管理概述
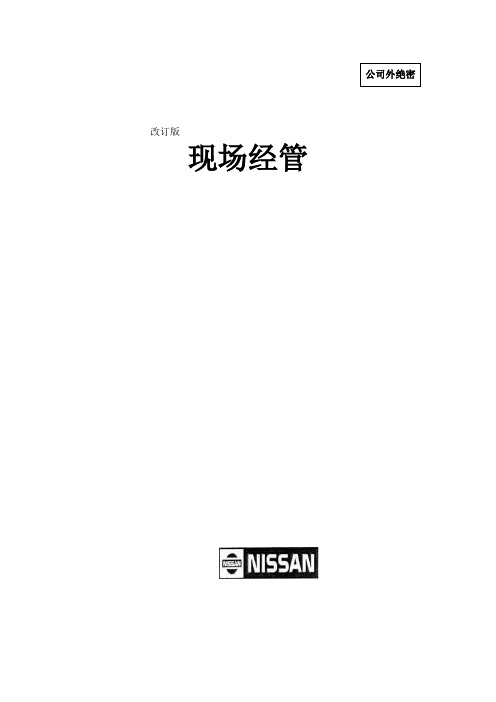
公司外绝密改订版现场经管前言1(附表)日产生产方式中的现场经管原文的位置及结构图 (4)第1章日产生产方式中的现场经管◆日产生产方式中的基本思想51. 以质量为基准 (6)2. 杜绝浪费 (7)(1) 杜绝丧失机会浪费 (7)(2) 杜绝资源的浪费 (7)(3) 杜绝工作进度的浪费 (8)❖产品制造所应有的模式91. 全数保证后工序所必需的质量 (9)2. 仅在必要的时候制造后工序必需的零件 (10)3. 用最少的资源(人、物品、设备)制造 (11)4. 重视人材 (11)第2章现场应完成的任务◆现场的任务131. 生产的完成 (13)2. 改善收益 (15)3. 人材的培养 (16)❖监督者及经管者的任务181. 监督者的任务 (18)(1)达到预定目标 (18)(2)工作的规范化及规范化的提高 (20)(3)培育部下 (23)2. 经管者(科长)的任务 (27)(1)方针的设定及达到 (27)(2)培育人材 (28)(3)环境的制造 (29)(附表)现场经管中组长、工段长、科长的任务 (30)3.经管干部与现场协作 (32)第3章现场经管的实施方法◆经管的基础331. 工作的规范化 (34)(1)何为规范化 (34)(2)规范化为何有必要? (34)(3)规范化的操作方法 (35)2. PDCA 周期的运转方式 (37)(1)经管周期的四个步骤 (37)(2)掌握事实的要点 (42)❖为了提高现场经管的水平451. 强化持续经管 (46)2.贯彻源流经管 (47)3. 预期经管的构筑 (49)(1)所谓维持类型 (50)(2)所谓变革类型 (51)♦监督者(组长)担负的日常现场经管工作52第4章日产生产方式中应有姿态的实现54(附表)日产生产方式系统图 (55)原则Ⅱ散乱的排除 (56)配置故障报警 (57)贯彻操作规范化 (58)完全的质量保证 (59)配置工序内检查 (60)实行由责任部门纠正错误 (61)杜绝不良品 (62)计划变动时的应对措施 (63)设备异常停止情况的排除 (64)遵守生产节拍 (65)遵守工序的排列 (66)促进小批量化 (67)工序内库存的最小化 (68)工序之间库存的最小化 (69)实施倍率的最小化 (70)试制人员的最少化 (71)成品率的最大化 (72)便宜、长期地使用 (73)确保安全 (74)排除费劲的操作方式 (75)教育、训练、活用 (76)通过小集团的活动构成车间 (77)(资料)(附表)组长的日常活动一天的活动 (78)一个月的活动 (80)一年的活动 (81)前言为了在我们的生产部门中,谋求无论在什么样的经营环境下都可以让其产生经济效益的体制的实现,创造一种在任何时代背景下都可以稳定的制造产品的通用价值观念,我们编写了《日产生产方式——本编——》。
某汽车工厂GK推进分享

系长C&J
班组C&J
C&J
班组管理的充实
按时更新
管理表单更新
数据一致性
看板表单
和部下沟通
月度反省回顾学习
未达项目标识 未达项目解析对策
月度反省 课题跟踪
建
立
班活动计划学习
学
习
签
到
上级交办重要事项
跟
踪
4M手法进行解析
重点品质事项
8
一、GK活动说明
而根据我对GK的理解、结合涂装管理实际拟使用的表 单也有上百项。需要使用的表单及各表单间的逻辑关系 请见下表:
3
一、GK活动说明
2、异常的管理。为了实现基准定义的状态,将已发生 问题的原因分类成4M,再分析其真正的原因,从源头 加以改善,使相同的问题不再发生。处理问题的方法中, 可分类成:为了减少损失的“紧急对策”,为了立即防 止问题的发生或不合格品流向下一道工序的“暂定对策” 及针对问题根源的“恒久对策”。
1.根据实绩数据,对目标 半年进行反省一次. 2.同时对系长及班长的活 动计划书进行修订
1.数据真实,与目标实绩 一至 2.反省内容要有说服力, 反省课题要有针对性 3.课题来源可以从品质 保证月度分析中选取.
1.月度不达标项目需在下 月度展开小集团活动. 2.针对展开活动 应当进行 相对标准化
方策活动计划 J43-GK-001-005 目标与实绩统计 J43-GK-001-006
东风日产郑州工厂GK推进分享
东风日产乘用车公司 2015/10/8
1
一 GK活动说明
二 GK推进
目
录
三 GK体制建立四 自源自诊断2一、GK活动说明
1、对GK的认识
日产GK基本概念及要点
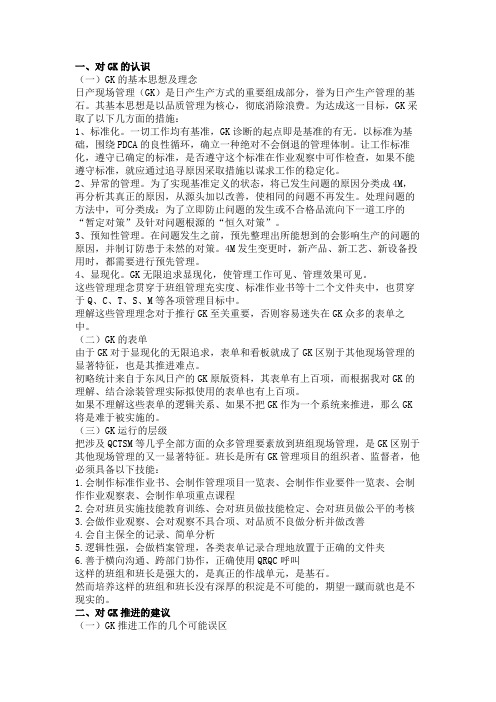
一、对GK的认识(一)GK的基本思想及理念日产现场管理(GK)是日产生产方式的重要组成部分,誉为日产生产管理的基石。
其基本思想是以品质管理为核心,彻底消除浪费。
为达成这一目标,GK采取了以下几方面的措施:1、标准化。
一切工作均有基准,GK诊断的起点即是基准的有无。
以标准为基础,围绕PDCA的良性循环,确立一种绝对不会倒退的管理体制。
让工作标准化,遵守已确定的标准,是否遵守这个标准在作业观察中可作检查,如果不能遵守标准,就应通过追寻原因采取措施以谋求工作的稳定化。
2、异常的管理。
为了实现基准定义的状态,将已发生问题的原因分类成4M,再分析其真正的原因,从源头加以改善,使相同的问题不再发生。
处理问题的方法中,可分类成:为了立即防止问题的发生或不合格品流向下一道工序的“暂定对策”及针对问题根源的“恒久对策”。
3、预知性管理。
在问题发生之前,预先整理出所能想到的会影响生产的问题的原因,并制订防患于未然的对策。
4M发生变更时,新产品、新工艺、新设备投用时,都需要进行预先管理。
4、显现化。
GK无限追求显现化,使管理工作可见、管理效果可见。
这些管理理念贯穿于班组管理充实度、标准作业书等十二个文件夹中,也贯穿于Q、C、T、S、M等各项管理目标中。
理解这些管理理念对于推行GK至关重要,否则容易迷失在GK众多的表单之中。
(二)GK的表单由于GK对于显现化的无限追求,表单和看板就成了GK区别于其他现场管理的显著特征,也是其推进难点。
初略统计来自于东风日产的GK原版资料,其表单有上百项,而根据我对GK的理解、结合涂装管理实际拟使用的表单也有上百项。
如果不理解这些表单的逻辑关系、如果不把GK作为一个系统来推进,那么GK 将是难于被实施的。
(三)GK运行的层级把涉及QCTSM等几乎全部方面的众多管理要素放到班组现场管理,是GK区别于其他现场管理的又一显著特征。
班长是所有GK管理项目的组织者、监督者,他必须具备以下技能:1.会制作标准作业书、会制作管理项目一览表、会制作作业要件一览表、会制作作业观察表、会制作单项重点课程2.会对班员实施技能教育训练、会对班员做技能检定、会对班员做公平的考核3.会做作业观察、会对观察不具合项、对品质不良做分析并做改善4.会自主保全的记录、简单分析5.逻辑性强,会做档案管理,各类表单记录合理地放置于正确的文件夹6.善于横向沟通、跨部门协作,正确使用QRQC呼叫这样的班组和班长是强大的,是真正的作战单元,是基石。
GK现场管理

营造女性・高龄者 能工作的环境。
2)培养人才,创造能最大限度发挥人的 能力的工作环境。
逐个培养。
9
培养小组 。
第二章
现场发挥的职责
现场的职责和监督者・管理者的职责
①现场的职责
1.达成生产。 2.赢利的改善。 3.人才培养。
工 作 的 標 準 化
設備管理的標準化 作業的標準化 品質管理的標準化 其他的標準化
顺序2:彻底遵守已設定的標準,并开展持续遵守管理活動 作業観察及其記録 定期巡视车间并做記録 顺序3:問題的明显化及反馈活动 QC手法 IE手法 PM分析手法
整理出能说明问题的数据。 顺序4:为提高生产效率所作的改善活動
1.需保证后工程所需的 每个产品的品质
保证每个产品的品质是指、全部部件已规 定需保证的项目以适当方法确保不超过所 规定的品质规格。
品 质 保 证
1.制程品质 1.不制作出不良品 1.不流出不良品 1.维持管理
6
需实行标准 作业。 追溯起源消 除异常原因。
第一章:日产生产方式之现场管理
2.后工程所需品仅限在
21
第三章:現場管理的推进方法
2.PDCA环的循环方法
(1)管理サイクルの4 (1)管理环的四个步骤
ACTION 采取措施 决定目標 PLAN
决定实现目标 的方法 教育訓練 工作
检查実施状況 的結果 CHECK
DO
(2)把握事実的注意点 ①.贯彻5現主義 (原理・原則・在現場・看現物・现实性処 ②.以数据说明问题 对所发生現象进行量化的数据で把握する ③.以5W2H整理する (何时:When 何处:Where 誰:Who 什么:What 为何:Why 怎样:How 多少:How Much
GK现场改善作战十条

现场改善------作战十条
一、不要找借口
Don’t make excuses for anything
二、不要说不行、要想方法去做
Never Say”It’s impossible,We can’t make it!” Just think and do it.
三、先不要担心
Don’t be worried about before taking action.
四、根据事实做议论,不要凭空想像推论
Conclusions are made based on facts instead of imagination
五、有困难才会有智慧
Difficuly makes wit.
六、不要追求完美,有60分也要勇敢去做。
Don’t expect everything to be perfect Sixty points is enough for trying.
七、立即去做,做后再提意见
A ction first,question second.
八、不要用钱,要用智智慧、没有智慧,多流汗,智慧就出来了
Use your wit instead of money .You’ll have wits by sweating more.
九、要把无价值的动作,移到有价值的劳动中去
Remore operation adding no Value to products,ong valuable operation left 十、改善是无限的
Raizen(improvement)is foreverand endless。
日产现场管理说明

•新车一元化管理
•改善提案(合理化、QC)
•SOS作成指导
•标准作业诊断
•班组管理标准化
B E S T Q
日产现场管理说明
三、NPW基本5行动
Bench Marking
标杆活动
Education & Training
人才培养
Stopping Line
有异常就停线
Time & Sequence
时间和顺序的遵守
日产现场管理说明
目录 一、NPW(日产生产方式)介绍 二、日产生产方方针管理说明
日产现场管理说明
一、NPW活动体系
Nissan Production Way
检查诊断 追求的姿态
TOP诊断 同期生产(NPW)
全球No.1 方针
TQM Q,C,T,S,M
TQM Q,C,T,S,M
•基本5行动展开 •内部诊断 •NPW推进部支援诊断
方针管理 /BM
T 加工 P 铸造 M 保全
J 装配 I 物流 T
S 品质 TPM事务局推动
Q
保证
JIT活动由IE推动 SQC纳入IE/GK管理
C
GK(现场管理)
标准设定、贯彻、改善
生产/物流管理
制造
5S(安技环保)
环境/安全卫生职业健康管理
• TPM的定义
• Total Productive Maintenance • 全员参与的生产保全 • 广义的TPM:TPM活动就是全员参与的工
厂全面改善活动 • 狭义定义是:全体人员,包括企业领导、生
产现场工人以及办公室人员参加的生产维修、 保养体制。
日产现场管理说明
八、TPM说明
• TPM的含义
日产作业环境改善活动PPT优选版
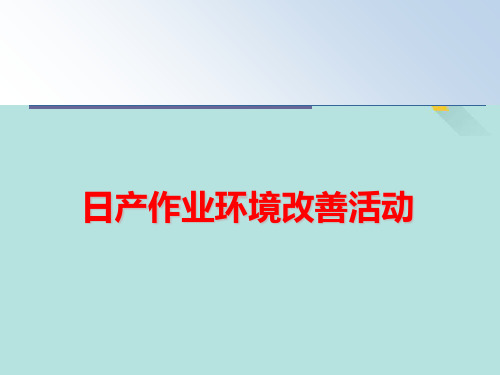
共通指标管理
人机工程学诊断
人机工程学评价
改善/教育
’03年度
’04年度~
(全球)
速度提升
日产 Value-up期间的 作业环境目标
P ro d u c tio n M a n a g e m e n t and T raining
NIMS和人机工程学改善事例
“Nissan Integrated Manufacturing System” 的导入
柔性的一条生产线 ➢ 按照多车型随机顺序生产・个月追加车型
Integrate&Fishbone ➢ 和供应商的統合(模块、供应商停车场)
5 治工具
Infrequent
Information 250 1650
Optimal View 300
170
6 情报和作业
OptimalΒιβλιοθήκη 700Control700 500
Poor
1800 1700 1400
-作业料架尺寸
Fair
700
Recommended
400
Poor
250
7 一般环境要因
- 噪音 - 振动 - 照明 - 温度 - 化学物质
4.生产运营和教育 作业编成和轮调 限制作业者用的工程的确保 短期人员用的工程的确保 人机工程学教育
5.一般环境 以下的项目的目标达成情况: -噪音 –温度 –照明 –化学物质
6.作业相关的健康管理 肉体的苦痛・不舒适的管理・报告 康复中心和身体治疗 伸展体操 作业判断所需的身体能力基准 医疗费管理
(新车的部品单位)
人机工程学评价
※新车的评价・判断
人机工程学 指导生产线
人机工程学诊断
短期对策 设备对策 产品设计对策 工程设计对策 管理改善
- 1、下载文档前请自行甄别文档内容的完整性,平台不提供额外的编辑、内容补充、找答案等附加服务。
- 2、"仅部分预览"的文档,不可在线预览部分如存在完整性等问题,可反馈申请退款(可完整预览的文档不适用该条件!)。
- 3、如文档侵犯您的权益,请联系客服反馈,我们会尽快为您处理(人工客服工作时间:9:00-18:30)。
目标(=Q・C・T); 设定目标和方策后; 年・月・日进行管理; 运转PDCA循环
・建立工作的标准,
并贯彻执行。 ・确定了PDCA循环, 制定提高标准内容。
协助下属提高每个 人的能力,及建立 人际关系;提升自身 技能,培训新人、接 班人。
12
二、什么现场管理
6-1、现场管理的推进:
不製造 不良品
三 不 原 则
7
二、什么现场管理
2、 GK发展史
GK的起源
GK起源于二 战后美国军火工 业广泛采用的“工 业内部培训” TWI (Training Within Industry) 和由美国空军发 明的MT(Management Training)
☆TWI (Training Within Industries) JIT(Job Instructional Training)让 领导认识到使员工得到足够职业培训 的重要性及怎样进行培训; JMT(Job Methods Training)关于如 何获得改进和完善工作方法的思路并 实践; JRT(Job Relations Training)关于
6
二、什么现场管理
1、 什么是GK Gemba Kaizen-Kanri。
GK 现场改善
管理
用常识性、低成本的方法来管 理工作场所——产生附加价值
的地方
大英词典的释义: Gemba Kaizen-Kanri A Commonsense Low-cost approach to Management
︵ 改提 善升 ︶
试作开始
SOP 活动期间
时间
改善活动通过 P→D→C→A 的循环持续进行,以提升部门管理水平和绩效。 落实标准化,以维持现状水平(管理)。 活用改善手法与工具,进行现场改善活动,以提升管理水平。
16
二、什么现场管理
8、PDCA循环的运转方法(12个项目诊断并提升):
管理循环的4个阶段 Action(处理)
Gemba Kaizen -Kanri 体系
9
二、什么现场管理
3、 关于日产生产方式和现场管理
在日产生产方式推进中,所运用的共通管理、改善工具
来自TQM管理循环 →活动的支柱
日产生产方式 (NPW) 制造产品的理想姿态
同期生产 TQM JIT SQC TPM
明确全部部门的目的、职责及活动方向,明确运 行管理周期的同时力求提高步骤。
GK现场管理改善
概要
1
目
录
1 2 3 4 5
经营与现场管理 什么现场管理
GK过往活动成果
GK提升思路 GK诊断说明
2
一、经营与现场管理
1、 现场管理在企业经营中的位置???
公司利益(盈利)向上 *成本下降 (只有成本下降,销售与公司利 益才能均有效向上)
*优良的品质(Q) *低成本,低价格 (C) *必要的时候生产必要的产品(D)
4:不追求完美,50分既可,迅速去做
不追求100%的完美,50分就可以迅速去做・・为了追求100分要花费很多时间去议论、商讨。浪费时间。一 个小小的改善就将很多金钱都浪费到说话上了。
5:马上纠正错误
有错误马上纠正・・发现现在的方法不好马上改正,另外改善后的东西如果无法得到认同时也要马上改正
6:不使用金钱成本的改善
开发 … 商品的企画・设计・实验
生产技术 … 制品设计、工程设计、技术开发 製 造
・强大的现场 ・强大的现场管理人员
现场管理
3
一、经营与现场管理
2、满足客户的要求,确保公司的利益,只能是递减成本!
销售价 (客户要求价)
成本 (制造成本)
盈利
(剩余为公司利益)
﹖ ﹖
4
销售价 (客户要求价)
盈利
(确保公司利益)
0.5
20
GK诊断说明
GK诊断内容
*现场・班长・帐票・询问作业者、确认实践内容, 了解实践内容进行评价。 GK、多样化了解现场的实力。 *用抽查方式决定诊断工程、以工程的休息场所为现场诊断中心、含作业者的理解 度業及实践内容的偏差及作业实力。 *实施诊断日程为各供应商2天(含指导)。 *评价项目进行详细化、12项评价项目关于职种别品质保证的内容进行评价。 (要因系管理) *帐票类就这样使用。没有必要作成新的。 现在使用的帐票类能进行修改。
生产活动
入/ Input
出/ Output
生产三要素
有价值的商品
人 物 设备
安全管理 作业管理 现场管理 (GENBA KANRI) 资材管理 工程管理
收益力 竞争力・ QCD+T
15
二、什么现场管理
7、GK 现场管理水准提高:
P
生 産 準 備 ・ 現 場 管 理 ( 水 平 )
A
标准化 D
C
标准化 (维持)
上下级关系和领导方法的培训。
☆MT(Management Training) ●认识员工个人相互关系的重要性 ●持续对工艺和产品完善改进的方法及价值 ●把人和工作方法相结合,科学使用PDCA
8
二、什么现场管理
2、 GK发展史
TWI和MT 引进 消化 吸收
形成与发展 结合日 本实际 创造发 展 TQC/TQ M、TPM、 JIT…… 来自日本企业的做法
5S
10
二、什么现场管理
4、现场的职责:
「最大限度的灵活运用人、物、设备、将品质 完全纳入工程,追求効率化」。
达成生产
有效益的改善
人材培养
生产达成,不单单只 是完成计划台数,而 是要一面确保安全, 一面按照交期交出比 其他公司品质更好更 便宜的商品
效益改善,是在提 升品质,确保交期 的同时,还要进行 人力递减及降低库 存等改善,进行降 成本等活动
成本 (制造成本)
一、经营与现场管理
3、提升现场管理水平,递减制造成本,确保并提升公司利益。
Text 成本 (递减制造成本)
正确经营现场 的人、机、料 、法环,减少 浪费!
就是提 升现场 管理水 平!
现 场 管 理 水 平 提 升
盈利
(确保公司利益)
5
二、什么现场管理
1、 什么是GK Genba Kaizen-Kanri。 Gemba 现场
企业的支柱是 人; 实现制造品质应有 姿态的是 人;培养 人 和 团队精神 是 必不可少的
11
二、什么现场管理
5、现场管理人员的职责:
监督者管理的对象内容是、安全・品质・交期 ・成本・设备・人・部品・材料等等、为了使全部要素 靠近理想姿态,期待着一歩一歩提高水平。
达成目标
工作的标准化 及其提高
下属的培养
(能用要因管理、解析手法・改善手法进行现场实施、効果有提高。)
*水平 5:理想姿态。(现场的不断进步)
(以现场的理想姿态进行管理、具备有对应变化实力的现场。)
19
GK诊断说明
全球GK评价的方法
评价点
水平1 水平2 水平3
・全球 GK诊断
NG 当到这儿NG(不良项目)时, 不管水平2・3做得如何,评价 就停止在水平1。
21
改善的十条基本精神
1:丢弃老观念
丢弃老做法的因定观念・・作业历史越长的工场的意识越老旧,改善首先要从丢弃老观念开始
2:与其找理由不做改善,不如找改善的方法
与其找理由还不如想解决的方法・・找借口不做改善的人更多。「哎呀ー这个呀、那个呀」
3:不找借口,否定现状
不找借口,首先否定现状・・借口多的工场多数没有力量,总认为现状的做法是最好的。这样是不会有进步的。 如果认为现在的做法是最差的话就不会有借口了。
9:团体力量战胜个人力量
10个人的智慧胜过一个人的知识一・・・通过大家在现场所学到的智慧胜过头脑中的知识
10:改善是无止境的
改善是无止境的,成本可以无止境下降,改善能做到无止境,这是JIT的信念
22
23
广义上: “事件真正发生的地方” 狭义上: “工作领域”或“工作位置” ☆制造产品或提供服务的地方 ☆直接创造利润的场所 ☆常被管理部门忽略
Kanri --- Kaizen 管理 改善
– ☆一种企业经营理念,用以持续不断 地改进工作方法和人员的效率; – ☆一种常识性和低成本的改进方式; – ☆与创新相比风险较低; – ☆强调以员工的努力、士气、沟通、 训练、团队、参与及自律来达成目标 – ☆改善步伐一小步一小步、阶梯式, 但随时间推移,会带来戏剧性重大成 果。 – 达 标 - 被 动 式 的 管 理 思 想 改 善 - 主 动 式 的 管 理 思 想
不流出 不良品
全数品质 保证
(QCT)
納品
销售店
不接受 不良品
顾客满意
东风日产责任
顾客
13
二、什么现场管理
6-2、现场管理的推进:
不製造 不良品
三 不 原 则
不流出 不良品
全数品质 保证
(QCT)
納品
东风日产
不接受 不良品
顾客满意
供应商责任
顾客
14
二、什么现场管理
6-3、现场管理的推进:
实现制造产品的理想姿态重点在于设定标准、持续提高标准,尽快运行PDCA循环。
进行处理
决定目标
பைடு நூலகம்
Plan(计划)
决定方策 实施教 育培训 开展工作
Check(确认)
确认实施的状 况与结果
Do(实施)
17
二、什么现场管理
9、12个项目诊断并提升( PDCA循环的运转方法)
Level-1#---5# 12个项目
18
GK诊断说明
全球GK诊断的评价水平 *水平 1:有设定基准(标准)。 (进行工作后将工作的基准(标准)进行设定・让班长以上人员理解。) *水平 2:标准内容的导入及活用