日产全球诊断标准
各小组SWOT分析&后续课题
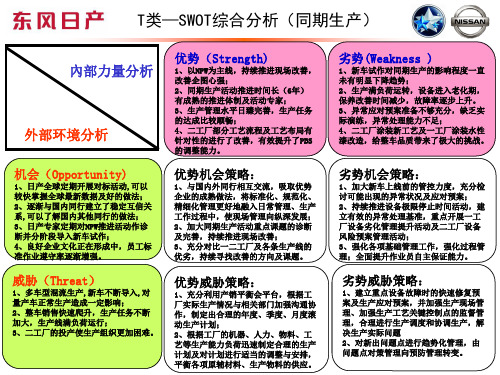
劣势(Weakness )
1、新车试作对同期生产的影响程度一直 未有明显下降趋势; 2、生产满负荷运转,设备进入老化期, 保养改善时间减少,故障率逐步上升。 3、异常应对预案准备不够充分,缺乏实 际演练,异常处理能力不足; 4、二工厂涂装新工艺及一工厂涂装水性 漆改造,给整车品质带来了极大的挑战。
外部环境分析
同期生产 事务局
推进《强化制程管理》活动,重点 同期生产 加强现场作业观察及问题点反馈、 分析,提升员工作业自主保障能力; 事务局 T 类 加强各工程不良流出管理,减少总 同期生产 装下线后弹出车比例及返修工作量; 事务局 加强发动机、变速箱等返修困难的 重点零部件的品质管理,递减滞留 车数量 推进设备极限停止时间活动的日常 化管理,降低设备停线影响度; 坚持制造及销售部门周例会制度, 将生产计划调整置于可控范围(目 标是不调整已生成的顺序计划); 与SCM部共同提升物料保障能力, 保证物料供应及品质。
同期生产 事务局 同期生产 事务局 同期生产 事务局 同期生产 事务局
-2-
S&E类—后续展开课题一元表
类别 项目 二工厂EHS体系建立 担当 安技科 安技科 二厂各车间 各车间 安技科 安技科 涂装、树脂 安技科 安技科 6.30 6.30 12.30 11.30 完成日期 6.30 1月 2月 3月 4月 5月月 6月 7月 8月 9月 10月 11月 12月
进一步研讨生产能力提升的可行性, 同期生产 提升HD工厂生产的应变能力,保证 事务局 2012年生产任务的顺利达成; 努力挖掘D-STAR持续课题并持续改 善,为下一步D-STAR持续挑战标杆 打好基础; 树脂L/T继续保持日产年度全球标 杆;
同期生产 事务局
同期生产 事务局
日产GK现场管理改善概要

开发 … 商品的企画・设计・实验
生产技术 … 制品设计、工程设计、技术开发
製造
・强大的现场 ・强大的现场管理人员
现场管理
3
LOGO
一、经营与现场管理
2、满足客户的要求,确保公司的利益,只能是递减成本!
销售价 (客户要求价)
成本 (制造成本)
﹖ 盈利
(剩余为公司利益)
销售价 (客户要求价)
盈利
(确保公司利益)
*帐票类就这样使用。没有必要作成新的。 现在使用的帐票类能进行修改。
21
LOGO
改善的十条基本精神
1:丢弃老观念
丢弃老做法的因定观念・・作业历史越长的工场的意识越老旧,改善首先要从丢弃老观念开始
2:与其找理由不做改善,不如找改善的方法
与其找理由还不如想解决的方法・・找借口不做改善的人更多。「哎呀ー这个呀、那个呀」
三
不良品
不
不流出
不良品
原
则
不接受
不良品
全数品质 納品 保证
(QCT)
销售店
顾客满意
东风日产责任
顾客
13
LOGO
二、什么现场管理
6-2、现场管理的推进:
不製造
三
不良品
不
不流出
不良品
原
则
不接受 不良品
全数品质 保证
(QCT)
納品 东风日产
顾客满意
供应商责任
顾客
14
LOGO
二、什么现场管理
6-3、现场管理的推进:
*水平 5:理想姿态。(现场的不断进步)
(以现场的理想姿态进行管理、具备有对应变化实力的现场。)
19
LOGO
肝功能化验单解读
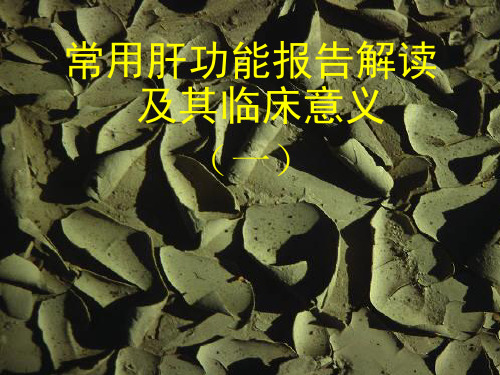
3、γ 球蛋白 系免疫球蛋白,由浆细胞生成,γ球蛋 白的增高机理: (1)肝内炎症反应 (2)自身免疫反应 (3)从肠道内吸收过多抗原 (4)白蛋白下降,γ球蛋白代偿性增加
γ球蛋白增高常见于慢性肝炎,失代 偿肝炎肝硬化,结缔组织疾病。急性肝 炎后γ球蛋白持续增高者,提示向慢性发 展。
疾 病 急性病毒 性 肝 炎 慢性肝炎
γ-GTP增高的意义
(1)急性病毒性肝炎时轻中度升高,恢复期 趋于正常,如持续增高常提示慢性化。 (2)慢性肝炎和肝硬化非活动期,γ-GTP大 多正常,而活动期大多增加,可作为慢性肝病活 动性指标之一。 (3) 原发性肝癌 γ-GTP明显增高,敏感度比 AFP高但特异性不如AFP。
(4)肝外阻塞性黄疸,肝内胆汁淤积 时明显增高。 (5)酒精肝显著升高,戒酒后逐步 下降,复饮者会迅速上升,因此Y-GTP 是诊治酒精肝的敏感指标。 (6)非酒精性脂肪性肝炎呈轻度升 高。
(三)标本明显溶血AST平均增加 8~11倍, ALT平均增加5倍。
三、碱性磷酸酶(ALP;AKP)
正常人AKP主要来自肝脏和骨胳, 还有少部分来自小肠。 正常人15~112U/L,儿童高2~3倍。
AKP增高主要疾病有
肝外胆管阻塞; 肝内胆汁淤积; 肝内占位性病变; 肝内肉芽肿或浸润性病变; 如肝结核、结节病、肝内恶性淋巴瘤等。
组织 肝脏 肾脏 心脏 脾脏 脑组织 骨骼肌 血 清
酶u/g湿组织 AST ALT 50000 42000 48000 2900 128000 3400 10000 1300 33000 1000 31000 28000 106 47<血清
临床上解读转氨酶增高时需注 意以下几个问题
(一)、转氨酶升高除病毒性肝炎外
常见疾病有:
日产阳光轿车发动机怠速抖动的故障诊断与排除

日产阳光轿车发动机怠速抖动的故障诊断与排除作者:涂允忠来源:《时代汽车》2021年第24期摘要:我国整体经济发展水平显著提升,汽车数量和使用率逐步提升,其中日产阳光轿车深受人们喜爱。
在日产阳光轿车正常行驶期间,会受到多项因素的影响,无形中就会埋下诸多安全隐患,如果没能及时发现和解决,将会产生更加非常严重的安全事故。
发动机怠速抖动这类故障现象比较常见,为了能够保证人们驾驶安全,就要做好该类故障诊断与排除工作,从而防止人们驾驶日产阳光轿车发生安全事故。
关键词:日产阳光轿车发动机怠速抖动安全性Trouble Diagnosis and Elimination of Engine Idle Jitter on Nissan Sunshine CarTu YunzhongAbstract:China's overall economic development level has been significantly improved, and the number and utilization rate of automobiles have gradually increased. Among them, the Nissan Sunshine sedan is deeply loved by people. During the normal driving period of the Nissan Sunshine sedan, it will be affected by many factors, and many hidden safety hazards will be buried invisibly. If it is not discovered and resolved in time, more serious safety accidents will occur. Engine idling jitter is more common. To ensure people's driving safety, it is necessary to do a good job in diagnosis and troubleshooting of this type of fault, to prevent safety accidents while driving Nissan Sunshine cars.Key words:Nissan sunshine car, engine, idling jitter, safety1 引言从汽车行业的角度进行细致分析,就会发现汽车发动机怠速抖动问题发生率较高,具体表现为发动机噪音增大、横向摆动明显、怠速不稳定等,一旦转速有所提高,其就会出现减轻或是消失的现象。
某汽车工厂GK推进分享(PPT 38页)

一、GK活动说明
2、异常的管理。为了实现基准定义的状态,将已发生 问题的原因分类成4M,再分析其真正的原因,从源头 加以改善,使相同的问题不再发生。处理问题的方法中, 可分类成:为了减少损失的“紧急对策”,为了立即防 止问题的发生或不合格品流向下一道工序的“暂定对策” 及针对问题根源的“恒久对策”。
J43-GK-001-001
√
○
账
002 组的充实度管理台账
J43-GK-001-002
√
○
个系统来推进,那么GK将是难于被实施的。 003 系长活动计划书 004 班长活动计划书
J43-GK-001-003
√
J43-GK-001-004
√
○ 日常时挂在班组管理看板,诊断时收 入文件夹
○
日常时挂在班组管理看板,诊断时收 入文件夹
系长C&J
班组C&J
C&J
班组管理的充实
按时更新
管理表单更新
数据一致性
看板表单
和部下沟通
月度反省回顾学习
未达项目标识 未达项目解析对策
月度反省 课题跟踪
建
立
班活动计划学习
学
习
签
到
上级交办重要事项
跟
踪
4M手法进行解析
重点品质事项
8
一、GK活动说明
而根据我对GK的理解、结合涂装管理实际拟使用的表 单也有上百项。需要使用的表单及各表单间的逻辑关系 请见下表:
活动推进的支援工具
现场管理· 方针管理·劳务管理 安全管理 安全管理 N-TWI · ISO基准 现场管理(作业观察手册) N-TWI N-TWI N-TWI 作业管理 作业管理· 品质管理·安全管理 ·成 本管理 品质管理(QRQC手册) 设备管理 · 品质管理
国际主流车厂汽车电子EMC测试比较研究经典干货

ISO 11452-3
BCI
ISO 11452-4
带状线
ISO 11452-5
直接注入 ISO 11452-7
低频磁场 ISO 11452-8
静电放电 ISO 10605
电瞬态传导 ISO 7637-2
150kHz-108MHz 150kHz-1GHz 80MHz-18GHz 10kHz-200MHz 1MHz-400MHz 10kHz-400MHz 250kHz-400MHz 15Hz-30kHz
调制深度80%
DC-10614 (Daimler Chrysler)
➢ 频率范围:1MHz-400MHz ➢ 最大电流:500mA
GMW 3097
➢GMW 3097:2004,覆盖了下列标准:
–GMW12559,GMW12002V,GMW12002R和 GMW3100
直接注入法
250kHz-400MHz
800mm带状线
10kHz-400MHz
连续波EMS系统
➢ 频率范围最大为10kHz-3.2GHz ➢ 低频自由场(10kHz-200MHz)的造价非常昂贵(50V/m
需要3500瓦功放) ➢ 建设:
–低频部分,200MHz(400MHz)以下,选择BCI/带状 线
– 就是说,EUT的壳体和导线长度小于18cm(7.5cm)时,EUT不会接收 空间的10kHz-80MHz(200MHz)的信号。
低频自由场系统
➢ EUT对自由场的80MHz以下频率敏感的原因,可以分 为三种可能性:
–壳体和/或电源线长度大于18cm,EUT外壳接地,就可以 由BCI对电源线/地线注入射频信号完成测试。
– 壳体或者导线总长为1/2波长时成为最佳天线; – 导线总长为1/4波长且在导线一端辐射,成为单极天线; – 导线总长<1/20波长,确保不会成为天线。 – 波长λ=300/f(MHz),因此
日标充电标准

日标充电标准全文共四篇示例,供读者参考第一篇示例:日本电动车充电标准:雷打不动的稳定性日本一直以其严格的标准和高品质的产品而闻名于世。
在电动车充电领域,日本也不例外,制定了严谨细致的充电标准,以确保充电过程安全可靠,并为用户提供便捷的充电体验。
这些日本的电动车充电标准受到了国际认可,被认为是业界的典范之一。
本文将介绍日本电动车充电标准的主要内容和特点。
一、充电接口标准日本电动车充电接口标准主要参照了国际上通用的CCS (Combined Charging System)标准,即组合式充电系统。
这种标准集成了直流快充和交流慢充两种充电方式,用户可根据实际需求选择适合的充电模式。
日本还对充电接口的插头进行了细致的设计和规范,确保不同品牌的电动车充电器可以兼容使用,提高了充电的便捷性和互操作性。
二、充电功率规范日本电动车充电标准规定了不同充电桩的输出功率范围,以满足用户不同充电需求。
一般来说,日本的直流快充桩功率可达到50千瓦以上,可在30分钟内将电池充满80%以上;而交流慢充桩功率一般在3-22千瓦之间,适合在家、办公室等日常场所进行充电。
这些功率规范不仅可以保证充电效率,还可以减少能源浪费,促进能源的可持续利用。
日本电动车充电标准对充电设备的安全性能有着严格的要求。
充电桩必须通过ISO 15118、IEC 61851等国际认可的安全标准测试,保证其在充电过程中不会发生短路、漏电等危险情况。
充电桩的防水、防尘等性能也需要符合相关标准,以保证其在各种恶劣环境下均能正常工作。
日本还规定了充电桩的定期维护和监测制度,确保其长期稳定运行。
四、用户体验标准日本电动车充电标准注重用户体验,致力于提供便捷、快捷、安全的充电服务。
日本的充电桩广泛布局在各大城市、高速公路、停车场等公共场所,用户可随时随地找到充电设备进行充电。
日本还推广了充电会员卡、手机App等便捷支付方式,简化了充电流程,提高了用户的充电体验。
日本电动车充电标准还规定了充电设备的信息显示、故障报警等功能,方便用户随时监控充电状态,及时处理故障。
日产标准nes-mo301

日产标准nes-mo301什么是日产标准nesmo301?日产标准nesmo301是一个综合性能标准,由日产汽车公司推出。
它涵盖了多个方面的要求,包括发动机性能、底盘悬挂、操控稳定性、车身轻量化、安全性能等等。
这个标准的目的是为了提供给日产的工程师们一个统一的参考,让他们在开发和设计车辆时有一个明确的目标。
一、发动机性能在日产标准nesmo301中,发动机性能是至关重要的一部分。
发动机是车辆的核心部件之一,它的性能直接影响着车辆的加速、燃油经济性和环保性。
日产要求其发动机达到一定的功率输出和扭矩输出,以确保车辆有足够的动力。
二、底盘悬挂底盘悬挂对于车辆的操控稳定性和乘坐舒适性来说非常重要。
日产标准nesmo301要求底盘悬挂系统具备良好的减震效果和稳定性,以确保车辆行驶时能够保持良好的悬挂平衡。
三、操控稳定性操控稳定性是衡量一辆车性能的重要指标之一。
日产标准nesmo301要求车辆在高速行驶、急转弯和变线等情况下能够保持稳定,以确保驾驶者的安全和舒适。
四、车身轻量化车身轻量化是如今汽车行业的一个趋势,它可以提高汽车的燃油经济性和操控性能。
在日产标准nesmo301中,要求车身结构和材料具备一定的轻量化设计,以减轻车辆的整体重量。
五、安全性能安全性能一直是汽车制造商们关注的重点,也是消费者购车时考虑的重要因素之一。
在日产标准nesmo301中,车辆必须符合严格的安全标准,包括高强度车身结构、预防碰撞技术、主动安全系统等等。
总结一下,日产标准nesmo301是一个综合性能标准,涵盖了发动机性能、底盘悬挂、操控稳定性、车身轻量化和安全性能等多个方面。
它的目的是为了提供给日产的工程师们一个统一的参考,让他们在开发和设计车辆时有一个明确的目标。
通过遵循这个标准,日产汽车能够不断推出性能优越、安全可靠的车辆,满足消费者对汽车的要求。
NCAP:中、欧、日、美五大测试标准比较

NCAP:中、欧、日、美五大测试标准比较NCAP是最早在美国开展并已经在欧洲、日本等发达国家运行多年的新车评价规程,一般由政府或具有权威性的组织机构,按照比国家法规更严格的方法对在市场上销售的车型进行碰撞安全性能测试、评分和划分星级,向社会公开评价结果。
由于这样的测试公开、严格、客观,为消费者所关心,也成为汽车企业产品开发的重要规范,对提高汽车安全性能作用显著。
近年,更多国家(如澳大利亚、韩国、印度等)开始重视和建立本国的NCAP。
严格的试验条件是保证评价结果客观准确的重要前提,因此,国外NCAP试验室普遍都具备高水平的测试设备和专业能力。
但是,各国NCAP在组织实施方式、试验规程和评分方法上都有明显不同,这与各国在法规体系、道路交通事故统计和车辆状况等方面存在的差异密切相关。
显然,盲目照搬国外做法来建立中国的NCAP是缺乏科学分析基础和不切实际的。
以下是几种最常见到的NCAP测试与中国的C-NCAP测试标准的比较。
『从图表上看,日本、中国、美国以及欧洲的撞击测试标准有同有异』● 我国的C-NCAP据了解,中国汽车技术研究中心在深入研究和分析国外NCAP的基础上,结合我国的汽车标准法规、道路交通实际情况和车型特征,并进行广泛的国内外技术交流和实际试验确定了C-NCAP的试验和评分规则。
与我国现有汽车正面和侧面碰撞的强制性国家标准相比,不仅增加了偏置正面碰撞试验,还在两种正面碰撞试验中在第二排座椅增加假人放置,以及更为细致严格的测试项目,技术要求也非常全面。
C-NCAP对试验假人及传感器的标定、测试设备、试验环境条件、试验车辆状态调整和试验过程控制的规定都要比国家标准更为严谨和苛刻,与国际水平一致。
● 标准正面、侧面测试C-NCAP正面100%和40%的撞击测试速度上较欧洲NCAP(下称“E-NCAP”)以及美国高速公路保险协会IIHS的测试速度还有所不及。
C-NCAP的侧面撞击速度与日本NCAP(下称“J-NCAP”)和美国公路交通安全管理局NHTSA的侧面速度标准也相差达10%。
日产现场管理说明

本公司的问题
对本公司之影响
本公司将来方向定位
本公司的经营实况
应反映中期计划 之课题
年度活活动计划
中期经营计划
20
日产现场管理说明
方针管理来自公司的经营计划
六、GK说明
日产现场管理说明
说明: 1.GK(现场管理、日本语缩写) 2.日产采用全球通用的标准进行对班长培训,并进行现场管理水平的诊断。 3.每月系长和科长对班长进行诊断,每半年总经理对班长进行诊断。 4.班组管理水平高不高可以从GK诊断来说明。
八、TPM说明
日产现场管理说明
TPM的含义 把创造追求无限生产系统效率化(综合性效率化)的企业体制作为目标 以生产系统的整个生命周期为对象,在现场现物构筑 “零故障、零损失、零不良、零灾害”,预先防止所有损失的结构。 以生产部门为主﹑跨越现场、技术、管理等所有部门。 从公司最高领导层到一线员工全员参与。 通过重复小集团活动来达到零损失的目标。
作业管理
安全卫生管理
生产
活动
人
物
设备
(D)
交期
(C)
成本
(Q)
品质
最少的资源
最大的效益
现场管理的体制
十一、结束语
日产现场管理说明
1.日产作为世界级的公司,现场管理的经验。我们很多地方值得我们去学习。 2.现场做得好不好,关键是现场管理者的水平。 3.公司的体制及制度决定管理者水平的高低。
Nissan Production Way
日产现场管理说明
二、工作展开要点
制造 生产/物流管理 5S(安技环保)
GK(现场管理)
T P M
J I T
S Q C
nissan m0007标准
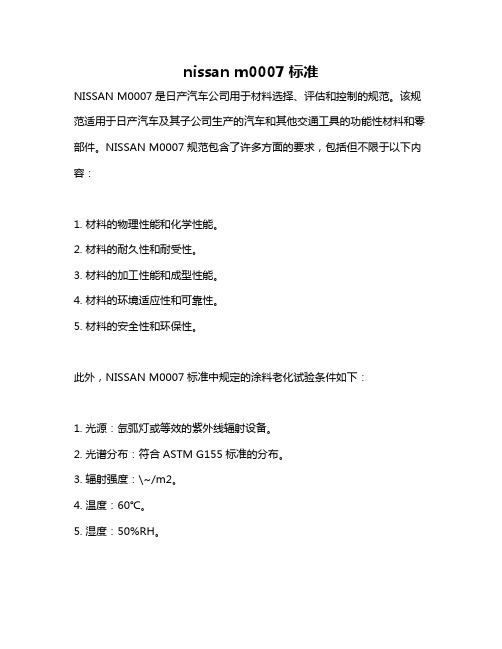
nissan m0007标准
NISSAN M0007是日产汽车公司用于材料选择、评估和控制的规范。
该规范适用于日产汽车及其子公司生产的汽车和其他交通工具的功能性材料和零部件。
NISSAN M0007规范包含了许多方面的要求,包括但不限于以下内容:
1. 材料的物理性能和化学性能。
2. 材料的耐久性和耐受性。
3. 材料的加工性能和成型性能。
4. 材料的环境适应性和可靠性。
5. 材料的安全性和环保性。
此外,NISSAN M0007标准中规定的涂料老化试验条件如下:
1. 光源:氙弧灯或等效的紫外线辐射设备。
2. 光谱分布:符合ASTM G155标准的分布。
3. 辐射强度:\~/m2。
4. 温度:60℃。
5. 湿度:50%RH。
6. 试验时间的长短应根据所选涂料和应用环境而定。
通常情况下,试验时间应为500\~2000小时。
如需了解更多关于NISSAN M0007标准的信息,建议咨询日产汽车公司或查阅相关文献资料。
汽车配件检测项目及标准-日产汽车零部件专项检测

汽车配件检测标准,日产汽车零部件专项检测如果准备向客户证明您产品的安全性、高质量和耐用性,同时降低产品返回或召回的风险,那么很有必要全面了解您产品的物理、化学和环境特性。
在面向消费品、零售、汽车等各种行业,针对产品的安全性、稳定性和可靠性开展物理和机械测试方面,GRGTEST是行业先行者。
在全国实验室和办事处组成的全球网络以及技术精湛的业内专家的支持之下,我们的物理、化学和环境测试服务既具有国际触角又贴近当地监管要求,因此您可相信,我们一方面在制定满足您具体期望的测试方案,另一方面也在关注您客户和监管机构的期望。
作为整车生产的基础,汽车材料及零部件的质量是整车生产成功与否的先决条件。
随着各种新车型日益完善的功能和人们对乘车感受及安全的不断追求,要求汽车生产企业必须在源头上对材料质量和安全性作出监控。
汽车供应链对质量越来越关注,伴随着众多零部件和原材料在很多不同的地区和供应商采购,期望着每一个质量环节都能达到高的质量标准,同时也期望在开始就知道这些质量信息,并期望着众多的供应商能在现在和未来都能持续满足他们的需要,这是一个挑战,同时也是一个机遇以证明产品质量并且与汽车供应链建立持续的互动联系。
广电计量检测股份有限公司向各大汽车零部件供应商提供贯穿整个汽车及其零部件从生产到价值链的服务,帮客户降低风险,抵抗质量危机。
汽车零部件检测项目包括:1)汽车用材料测试:高分子材料测试(机械力学性能、热学性能、绝缘电性能、耐化学药品测试、人工加速老化、燃烧测试等)反光测试测试(尺寸、颜色、反光性能、耐着力、冲击性能、冲击强度、抗磨性能、色牢度、盐雾试验、压缩性能、绕曲强度、裂纹等)泡沫泡棉材料测试(表观密度、压缩形变、硬度、拉伸性能、吸水率、导热系数、反抗弹力、燃烧性能等)橡胶材料测试(密度、硬度、拉伸性能、冲击性能、挠曲性能、门尼粘度、热学性能、燃烧试验、人工加速老化试验、耐化学试剂、耐油试验等)2)汽车外饰件测试3)适用产品:汽车前后塑料(金属)保险杠、金属&非金属翼子板、后视镜壳、发动机罩、外装饰件、防撞条等测试项目:机械力学性能、刚强度、变形量测试、表层厚度测试、附着力测试、抗腐蚀测试、抗磨耗测试、高低温环境测试/紫外线老化测试、紫外/氙弧光老化、高低温环境力学试验、环境机械性能测试、沙尘/淋雨/飞石测试、金相测试、无损探伤、综合性能测试/疲劳耐久测试等。
SES手册(一)

4.日产的SES历程与效果:
——自1998年以来,日产先后开发了SES1、SES2,由日产每年对工厂 进行两次评价( SES2一年一次),工厂每月对车间进行一次评价。日 产的SES1评价值由1998年的7.5降至2003年的2.4,事故频率同期由 0.76降至0.32。SES1过去工厂最高100多分,04年最高分为13分。
(PPT/报告)
工厂领导 部门领导 车间领导 班组长
共同 对策
共86页,第19页
4.搭建起一种能够形成互动的工作机制。
⑴结果的 充分告知
评价者
⑶指导/监督
受评单位
⑵改善及 情况反馈
共86页,第20页
四.三项支柱 ——推行SES的基础和支撑条件。
零事故
SES1/SES2
目
专
行
标
业
为
体
化
规
系
范
共86页,第21页
——发现安全问题并改进的工具
制造规划总部安技环保部 二OO九年一月 编制
共86页,第1页
前言
SES评价是日产特有的一种针对现状的安全评价工具。 具有注重过程、立足于深入的问题发现、量化评价的特点, 适用于现场安全生产状况的诊断和改善。
DFL于2007年将日产SES标准进行了转换,并结合公司 实际制定并不断完善了自己的标准,先后在十堰、襄樊、 花都、郑州等基地的14个单位进行试点,取得了明显的效 果并广受基层单位的欢迎。在此基础上,正式建立了东风 有限的SES标准。
共86页,第4页
一. 何谓SES
1.SES的含义: ——SES是Safety evaluation system的缩写,意指“安 全评价系统”。SES由日产开发而成,由SES1和SES2两部 分组成。
日系车质量标准
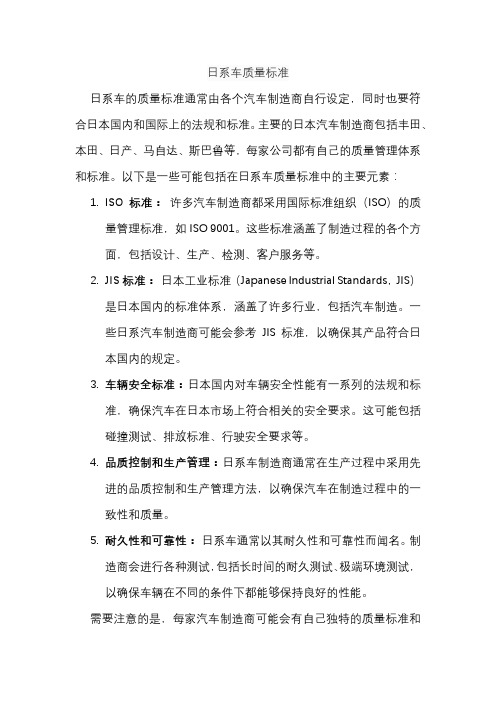
日系车质量标准
日系车的质量标准通常由各个汽车制造商自行设定,同时也要符合日本国内和国际上的法规和标准。
主要的日本汽车制造商包括丰田、本田、日产、马自达、斯巴鲁等,每家公司都有自己的质量管理体系和标准。
以下是一些可能包括在日系车质量标准中的主要元素:
1.ISO标准:许多汽车制造商都采用国际标准组织(ISO)的质
量管理标准,如ISO 9001。
这些标准涵盖了制造过程的各个方
面,包括设计、生产、检测、客户服务等。
2.JIS标准:日本工业标准(Japanese Industrial Standards,JIS)
是日本国内的标准体系,涵盖了许多行业,包括汽车制造。
一
些日系汽车制造商可能会参考JIS标准,以确保其产品符合日
本国内的规定。
3.车辆安全标准:日本国内对车辆安全性能有一系列的法规和标
准,确保汽车在日本市场上符合相关的安全要求。
这可能包括
碰撞测试、排放标准、行驶安全要求等。
4.品质控制和生产管理:日系车制造商通常在生产过程中采用先
进的品质控制和生产管理方法,以确保汽车在制造过程中的一
致性和质量。
5.耐久性和可靠性:日系车通常以其耐久性和可靠性而闻名。
制
造商会进行各种测试,包括长时间的耐久测试、极端环境测试,
以确保车辆在不同的条件下都能够保持良好的性能。
需要注意的是,每家汽车制造商可能会有自己独特的质量标准和
测试流程,因此具体的标准可能会有所不同。
要获取特定日系车型的详细质量标准,建议查阅制造商的官方资料或直接联系制造商。
汽车行业DSTR介绍

DSTR相关知识介绍DONGFENG NISSAN PASSENGER VEHICLE COMPANYDSTR是什么?Design Standard Time Ratio设计基准时间倍率间接时作业间物流作业实工数…DSTR B DST 直接作业 A DST 实工数实工数:平均每台车的作业时间(H/台);统计得DST:基准时间(H/台);设定得DSTR就是检验制造效率高低的标尺第2页DSTR的意义最大的目的就是把劳动生产力的两大要素进行定量评价。
『产品设计的好坏』- DST越小,设计水平越高『制造效率的好坏』- DSTR越小,制造效率越高DST 实工数DSTR 6H A车(a工厂)3H 6H 2倍实工数实工数B车(b工厂)2H 6H 3倍3H D 2H S △× DST T DST R ○ △小A车(a工厂)B车(b工厂)小DST DSTR为同行业开展BM活动相互比较提供了合理的平台DSTR的内涵是消除低无附加价值作业,提升设计及工艺水平DSTR从公司的总体战略意义理解是一种降成本的手段第3页DSTR的计算说明⊙『DSTR』的准确性取决于DST设定及实工数统计的正确性⊙①DST 系数自然台折算台实工数DSTR A车型1.0H /台 1.0 200 200 DST B车型 1.1H /台 1.1 100 110 实工数人力×出勤天数×出勤时间÷约当台数C车型 1.2H /台 1.2 150 180 DST: 计算值,设定条件变化要重新计算D车型0.9H /台0.9 50 45 ①多车型整体对比情况时采用方式合计500 535 管控好实工数人力范围管控好出勤时间及无标时间管控好折算台系数②DST 实工数DSTR 判断A车型 1.0H /台 2.2H /台 2.20 3 ②相同车型或车型间对比情况时采用方式B车型1.1H /台 2.4H /台 2.18 2 实工数计算准确较难,编程要做的好才行管控好各车型参与人力及作业标准时间C车型1.2H /台2.6H /台2.17 1 D车型0.9H /台2.0H /台2.22 4 第4页DSTR活动开展介绍⊙如何通过DSTR开展活动?⊙DSTR DSTR活用不同车型DSTR在各工程的情况对通过对于DST恶化的要因进行分析、比较,明确改善的重点和方向。
东风有限供应商QCD评价标准

东风有限供应商QCD评价标准文献内容提醒:QCD总部文献-1包含:标准作业书、QCD总部文献-2包含:标准作业书-1、标准作业书-2、标准作业书-3、标准作业书-4标准作业书-5标准作业书-6工场诊断(PIP)标准目录前言①工场诊断②工场诊断的对象③工场诊断的方法④工场诊断的概要⑤工场诊断的注意事项⑥诊断的印象附表1工场诊断项目附表2工场诊断明细表2、活动环节①事前准备②实际调查③调查汇总3、工场诊断日程表①基本时间日程4、工场诊断基准①诊断基准(M、Q、C、D、S)①工场诊断结果报告②公司概要调查表③工场诊断结果汇总表④工场诊断表(结果)⑤工场诊断表(因素)前言90年7月份编制工场评价系统(P1P=PointOfkIea1P1ant),作为提高收益改善的标准而进行工场评价,这个评价适应国内外的工场。
同时也可作为海外研修生的导入教育的指导。
基于这个方面,而重新编制使用。
一方面针对国内往来的厂家的评价的需求较少,使用这个标准评价的人也较少,以及对这个评价不了解的状况也存在,尚有,以前评价诊断表的评价内容和评价的定义不明确的地方也存在,因评价人的不同,评价的内容也不同。
这次针对以前的局限性之处的修订和此后对海外供应商的诊断,针对具有一个流的生产活动以及各种改善活动等经验、知识的诊断者,对方案推动方法、基准、诊断表进行重新修订。
但是,内容尚有局限性之处,通过以后国内外诊断活动的意见和希望,对《工场诊断标准》进行修订。
基准不是一成不变的,最后是通过诊断者,假如不能掌握诊断的技巧和工场的现状,也不能作出合适的诊断。
(注)1、方案D工场诊断*通过现场观测和征询来掌握工场的管理系统的实际状况。
*诊断内容是从工场及生产线的管理状况、管理职能、管理实际情况(管理水平、实际值、改善的灵活性)中明确改善的课题。
*通过现场诊断(参照生产诊断标准),明确工场的课题是全面提高工场的管理水平和生产能力。
*生产诊断:通过工作调查削减低效作业以及改善主体作业的充实度,以提高生产能力。
日产GK基本概念及要点
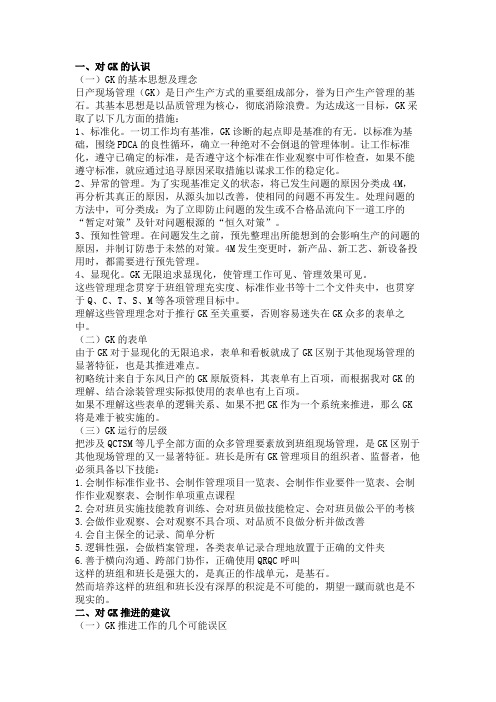
一、对GK的认识(一)GK的基本思想及理念日产现场管理(GK)是日产生产方式的重要组成部分,誉为日产生产管理的基石。
其基本思想是以品质管理为核心,彻底消除浪费。
为达成这一目标,GK采取了以下几方面的措施:1、标准化。
一切工作均有基准,GK诊断的起点即是基准的有无。
以标准为基础,围绕PDCA的良性循环,确立一种绝对不会倒退的管理体制。
让工作标准化,遵守已确定的标准,是否遵守这个标准在作业观察中可作检查,如果不能遵守标准,就应通过追寻原因采取措施以谋求工作的稳定化。
2、异常的管理。
为了实现基准定义的状态,将已发生问题的原因分类成4M,再分析其真正的原因,从源头加以改善,使相同的问题不再发生。
处理问题的方法中,可分类成:为了立即防止问题的发生或不合格品流向下一道工序的“暂定对策”及针对问题根源的“恒久对策”。
3、预知性管理。
在问题发生之前,预先整理出所能想到的会影响生产的问题的原因,并制订防患于未然的对策。
4M发生变更时,新产品、新工艺、新设备投用时,都需要进行预先管理。
4、显现化。
GK无限追求显现化,使管理工作可见、管理效果可见。
这些管理理念贯穿于班组管理充实度、标准作业书等十二个文件夹中,也贯穿于Q、C、T、S、M等各项管理目标中。
理解这些管理理念对于推行GK至关重要,否则容易迷失在GK众多的表单之中。
(二)GK的表单由于GK对于显现化的无限追求,表单和看板就成了GK区别于其他现场管理的显著特征,也是其推进难点。
初略统计来自于东风日产的GK原版资料,其表单有上百项,而根据我对GK的理解、结合涂装管理实际拟使用的表单也有上百项。
如果不理解这些表单的逻辑关系、如果不把GK作为一个系统来推进,那么GK 将是难于被实施的。
(三)GK运行的层级把涉及QCTSM等几乎全部方面的众多管理要素放到班组现场管理,是GK区别于其他现场管理的又一显著特征。
班长是所有GK管理项目的组织者、监督者,他必须具备以下技能:1.会制作标准作业书、会制作管理项目一览表、会制作作业要件一览表、会制作作业观察表、会制作单项重点课程2.会对班员实施技能教育训练、会对班员做技能检定、会对班员做公平的考核3.会做作业观察、会对观察不具合项、对品质不良做分析并做改善4.会自主保全的记录、简单分析5.逻辑性强,会做档案管理,各类表单记录合理地放置于正确的文件夹6.善于横向沟通、跨部门协作,正确使用QRQC呼叫这样的班组和班长是强大的,是真正的作战单元,是基石。
损工事件管理

一、损工事件管理:相关术语
2、相关术语: 受伤人次数=(轻微伤人次数)+(轻伤人次数+重 伤人次数+死亡人次数) 制度工作工时:指按照国家(或企业)规定工人应该 工作的工时。其计算公式为:报告期内制度工作总工时 数=报告期内平均职工人数×(报告期内的日历天数-报
告期内制度公休天数)×制度规定每天工作小时数。
三、损工事件管理:导入推进过程
2010年损工事件管理标准实施计划
2010年 目标 责任区分:主责◎辅责○ 管控△ 8 9 10 11 12 安技环 保部 事业部 工厂
达成方 策
管理项目
目标值 2 3 4 5 6 7
损工 事件 管理 标准 导入
实施 方法 的制 定
编制实施方法 文本化 研讨 标准宣贯 编制公司、工 厂实施办法 班组长培训 上报流程建立 报表上报 完成 完成
7、事故举例
某公司09年1月发生轻微受伤事件9起(假设每起事件损失半天,则0.5天×9=4.5 天),发生工伤事故1起,该员工胸骨骨折,左手无名指近节指骨截肢、左手食指、中 指远节指骨骨折。计算1月事故率及事故严重度。 多处伤害应以较严重伤害为主进行定性。定量时,首先进行累积伤害(同一、 同名肢体、或器官、或组织系统的多处伤害)计算。将每处伤害数值逐项相加,但 最后得出的损失工作日数不能大于该器官(肢体、功能系统)完全丧失的损失工作 日数,其次,进行共存伤害(功能无关的肢体、器官、组织系统的伤害)计算,其 伤害按重轻顺序,最重者取100%,次之取70%,再次之取10%,然后相加,但总值 不能大于6000损失工作日。 (引自《事故伤害损失工作日标准》(GB/T15499-95) ) 分析: 此起事故为多处伤害,事故以胸骨骨折为主,对照表中损失工作日换算所得:胸 骨骨折:300天,左手无名指近节指骨截肢:240天(如果左手为利手损失工作日为 280天),食指远节骨折:50天,中指远节骨折:40天。 损失工作日=(300×100%)+(240+50+40)×70%=531天 该公司09年1月总工时=员工总数×工作日×8=2342400小时(假设值) 事故率(FR)=10/2342400×106 =4.2
- 1、下载文档前请自行甄别文档内容的完整性,平台不提供额外的编辑、内容补充、找答案等附加服务。
- 2、"仅部分预览"的文档,不可在线预览部分如存在完整性等问题,可反馈申请退款(可完整预览的文档不适用该条件!)。
- 3、如文档侵犯您的权益,请联系客服反馈,我们会尽快为您处理(人工客服工作时间:9:00-18:30)。
QRQC <车间日会>
故障损失的大小是否及时把握,处 置以及跟踪是否迅速应对?
1.重点线的确认要有 重点线・ 设备以及信赖性向上活动是 班组的主攻方向. 2. 重点线・ 设备明确,并在 与厂、车间的战略保持一致,并且每 可否考虑5线也为重 据此实施对策。 年都在修订。 点线. 综合效率(时间开动 1 故障强度率目标厂 率) 故障 故障低减目标値与综合效率(时间开 下达指标应该为下降 结果系和要因系的目标値 强度率 动率)、故障强度率具有一致性(整 趋势 2 故障强度率 已经确定,也有实绩记入。 JPH(SPH)等 班组没有设定目标值 合性)。 <标杆> 3 有的表格目标值和 <生产模拟> 厂目标值有矛盾 故障件数・ 故障强度率 1 5线,6线故障管理报 MTTR・ MTBF 告书都要有, 2 所有 保全对应故障等,只保存 全部的故障信息都是与制造共享的, 短仃工没有记录和对 保全费 了一部分故障记录,不能 保全信息是将确定的内容按确定的方 策, <开动(制造)日报> 把握整体情况。 式在实施。 <点检检查表> <重大停报告书> <保全原单位>等 1 共性问题:表格上的 带回对策完成率 对导致生产未完成的设备 对导致生产未完成的设备故障进行了 所有要求填写的位置 <生产实绩(产量)表> 故障进行了把握,并得到 把握,并有及时的处置(下一班次 不能空无内容.包括签 <前日问题点一览表> 处置(即使是应急也行) 前)和长久对策的计划方案。 字 <带回对策报告书>等 。 <QCC活动报告书> <回顾书Ⅱ> <月度活动报告书> 等 <保全方式逻辑树> <回顾书Ⅱ> <一齐点检检查表> <集中点检检查表> <问题点登记一览表> 1 QRQC会内容记录全 月度目标未达时对故障现 根据设备故障停止的月度数据,将故 否,年、月、周要有 象进行分类,设备・部位明 障现象进行分类,设备・部位明确,找 回顾,问题解决要有 确,并与对策关联。 出了着眼点。 对策,要有数据,要 没有保全方式设定的思路/ 保全方式是依据数据、根据而设定的 逻辑/顺序,但设定了保全 。 方式。 虽然在实施总点检、但只 是有上级等的指示时才开 大致设定了总点检的瞄准点和点检的 展的活动。没有专门的点 基准,并以此在实施。 检基准,凭感觉和经验在 劣化复原还包含了制造现 场发现的内容。 将劣化的复元项目登录在保全日历 里,并按优先顺序实施,对实施状况在 进行管理。 故障分析在认真实施,使用为什么为 什么分析和QC程式,透过现象找出 原因。
在组内的相关设备上实施再发防止 (水平展开)。 ④设备 改善对策(在前项①~③的基础上) 每次重大停发生后,对发生要因和长 时间要因进行究明,从再发防止和短 时间复旧两方面来实施对策,并进行 效果确认。
通过数据分析结果掌握了本组的弱点 把握了重大停故障的MT 故障和设备,并反映到技能教育训练 TR,对数据在进行分析。 计划和备件管理里。 有实施点检作业的基准, 但不全。 基准来自于故障分析等的回顾,并在 及时修订,在运行PDCA循环。
故障件数 故障强度率 MTTR MTBF 每班目标强度率> 确认是否有对实施对策效果进行 水 平 效果确认 确认的体系、是否已经固化。 (确认是否再发) 展 开 和 用重大停报告书和QCC活动报告书把 反 杜绝再发 握再发防止对策实施到了何种水平 馈
确定了对策效果的确认流 程(无再发的判断),并 在实施。 对发生了故障的设备在进 行防止再发的活动。 ①再发防止对策 ②标准化 ③技能教育训练 等 每次重大停发生后,对发 生要因和长时间要因进行 了究明,也在实施再发防 止对策,但实施率低。 (60%以下) 对策效果的确认流程(无再发的判断) 已在组内普及(指导员层在进行确认) 。
的实施 掘出的问题点是否按照优先顺序在 进行处理。
<保全日历> <问题点処理清单> 问题点发掘率 <保全日历>
对点检维护作业和发掘的问题点有优 先顺序排位,特A设备的点检维护1 00%完成,问题点A的処理在发掘 後1个月以内完成。 正在针对慢性故障、重大停等重要度 高的问题,导入要因系管理(诊断、 状态监视等)。
以库存品清单为依据,借鉴 过去的经验(突发故障 重点线的采购备件清单是依据MTB 等),来确定应采购的备件 F等数据来确定的。 。 所有备件清单化,保管场所 有无备件看清单就清楚,在指定的保 明确(指定),并记录在清 管场所有对应的实物。 单里。同时保管场所的3 S也做好了。 虽然处于混在状态,但新 品、再生品、维修完成品 等有明确标识。 分成新品、维修完成品、未完品在进 行保管,经年劣化品、维修品等明确 标示有入库日和维修日。对电路板类 的有防尘措施。
复 问题项目复原率 (总点检后 是否定量地把握了劣化复原的项目, 原 的) 劣化复 究明造成劣化的要因,确立对策项目 解析项目对策率
原和解析 并跟踪其进展状况? 是否从硬件、软件两方面来展开追 求,究明真正原因的刨根问底是否 已经形成习惯? 是否有重大停和慢性难故障报告书 的运用基准,并按基准在运用。同 时,在报告书的管理上下功夫,与 再发确认等的管理结合在一起?
车间 提高设备信赖性活动诊断表
管 理 对 诊 断 项
活动项目
☆车间(生产 线)诊断活动 对象的决定
评价要点 为了有效活用资产、谋求信赖性的 改善提高,是否对生产线进行重点 指向管理,活动有没有分重要度? 是否以生产线能力和生产计划为前 提,使用综合效率和故障强度率, 理性设定改善目标値,有无过程和 技术含量?
故障解析
再 发 防 止 和 弱 点 对 策
故障报告书 的运用
<问题点登记一览表> <保全日历> <重大停报告书> <QC活动报告书> <慢性故障报告书> <难故障对策书> <回顾Ⅱ> 等 <重大停报告书> <慢性(难)故障对策书> <QC活动报告书>等
故障解析使用了一部分Q C手法。
重大停报告书虽按照运用 重大停报告书在按照运用基准书活 基准书活用了,但对策的实 用,大部分对策得到完成。 施率较低。 一个一个地积累对策案直到消除现状 与目标的差异为止。 在按实施一览表等进行对策的进度管 理,对落后部分有挽回计划等处置。
对于「应该掌握的保全作业和知识 」、按照掌握的结果是按个人在进 行管理吗、掌握的水平也能通过I LU等判明吗? 根据个人及班组平均掌握水平、明 确技能上的弱点,并反馈到训练计 划中了吗? 定期保全的整体框架明确,专业保全 自 和制造自主保全有明确职责分工。 主 与专业保全的职 确定的事情都能持续实行,始终围 保 责分担 绕减少故障这一主题来做自主保全 全 支援活动。
<记事>
根据技能水平和经验、应该掌握的 保全作业和知识是否得到整理?技 能弱点(个人&组)是否把握、同 时针对如何克服这些弱点将必要的 知识和技能定期地反馈到技能教育 项目里? <作业要件一览表> <8设备80作业> <固有技能作业> <重大停MTTR分析 (弱点把握)> 教育训练实施率 模擬故障训练实施率 <个人技能训练计划表> <班组技能训练计划表> <中・ 长期训练计划表> <出勤计划表> <基础技能手册> <基本技能手册> <固有技能手册> <标准作业书> <OPL> <厂家操作说明>等 应该掌握的保全作业、知 识得到整理。 根据技能水平和经验 、应该掌握的 保全作业和知识得到整理。
管理指标 <管理表单>
<回顾书Ⅰ、Ⅱ> <设备计划申请文件> <生产计划> <保全费> <生产模拟>
评价点 2 <平均以下>
评价点 3 <平均水平>
日产专家诊断问题点
☆车间(生产 线)诊断目标 的决定
设 备 和 工 作 的 现 状 把 握
保全信息管理 (故障履历管 理)
故障信息、设备管理指标信息等的 记录管理状况是否良好
教育项目
班、个人的训练目标和训练计划的 技能训练计划表 进展情况、及其习熟结果是否做到 了看得见?训练实施后、对其习熟 保 和实施 水平是否具备完善的评价体系? 全
按个人都有训练计划表。
有已落实进出勤计划的班组、个人月 度训练计划、具备可以切实实施的环 境。
技 能 提 向 教育工具&环境 高 上 设 备 信 赖 性 评价与个人管理
累积项目实施率 没有考虑目标达成,只将现 对策案是否有利于达成目标、是否 <对策项目一览表(累积 对策制定 状故障的『最差3』作为 改 按照最有效的优先顺序在制定计划? 量)> 对策立案。 良 <其他对策计划书> 等 保 是否在使用实施一览表等对对策进 故障对策实施率 虽实施了对策的进度管理, 全 对策实践 行进度管理,对于落后部分是否采取 <对策项目一览表> 但落后于计划的项目比较 <其他对策计划书> 了挽回计划等处置? 多。
提 高 设 备 信 赖 性
水平展开实施率 标准化反馈率 等 <标准作业书> 和范围,用右记表单进行确认。 <一个重点教程> 再 <MP情报> 等 重大停永久对策实施率 发 是否充分认识到了重大停给生产造 减 时间遵守 重大停故障件数 防 重 <面积时 成的影响,是否从减少重大停的次数 重大停防止胜率 止 大 间低减> 和时间这两方面来实施推进活动 重大停故障(总)时间 和 的? 停 <月度重大停故障一览> 降 弱 的 是否通过重大停MTTR分析明确 低 点 活 MTTR 要因、排除这些要因的相应对策是 重大停防止胜率 重大停MTTR 故 对 动 缩短 否按计划展开、MTTR是否在缩 <重大停一览表> 等 障 策 短? 在推进予知保全・ 予防保全的时候, 的 制定和重 要严格按照定期保全业务的基准在 <设备別管理基准书 > 过 新修订基 推进。确认定期点检・ 维护项目设 <点检维护基准书 程 定 准 定的流程是否明确,是否在实施修订 兼记录表> 等 期 改善 有月・ 年・ 中长期的保全日历,运 保 制作和修 营时与生产计划紧密关联,并有挽 <保全PM工时> 全 订保全日 回计划,同时,根据故障状況和点检 <点检确认一览表> 予 体 历 结果对点检周期进行修改后,是否 <保全日历> 防 制 反映在日历里。