机加工危险源辨识讲课教案
机械厂危险源识别教学提纲

岗序位号因素1、皮带轮1、安防护罩要牢固可靠碾11砂机未安防护罩,易造成绞伤致残2、可靠接地(零),定期检查。
3、联锁灵敏可靠,碾砂机运行时必须在取样门处取样。
4、人员进入碾内检修或清扫时,要在控制按纽处挂有“警示标牌”2、碾砂机未可靠接地(零),如果设备漏危险因素标制措施机、切面 机、电烤 炉接地不 良,接地 接零失 效,不按 规定检 查。
易发 生触电事 故。
1、 设临时线必须审批,专人监护,到时拆除。
2、 绝缘良好,线径与负荷匹配。
3、 用电设备要接地(接零)。
4、 临时线悬空或沿墙铺设。
3、盖机联 锁损坏不 及时维 修,联锁 失灵易发 生上肢体 绞入事 故。
2、临时线 绝缘不好,线径 与负荷不匹配,易临 时 15 4、作业人 员不按规 定佩带防 护用品。
女工发辫 易卷入。
1、安临时 线未经审批,无专 人监护, 易造成触电伤害。
灾。
3、临时用电设备无良好的接地(零),一旦设备漏电易造成触电事故。
4、临时线没有沿墙或悬空架设,在地面易拌伤行人或砸、绞碾、压等,破损裸露伤人。
1、按期对绝缘状况检测。
2、对所有接地(接零)做到安全可靠。
3、半年检测一次,做到安全可靠。
4、及时检查、检修,安装排风装置,经常检查。
16 2、变压器等设备接地、接零不良,易产生触电伤害。
1、设备绝缘不良,操作失灵,易发生触电。
期检测,造成触电伤亡。
" 病 从 肺 就置W装 訓 尘M︒ 吸跑故无 ︑ ︑7 00︑︑ O 栏7^ O ko端 器 蚀两尘油车 吸 埔跑安当量 由 ^7︱高过 温 由 ︑由量业作 无 好 完 持 保 槽因O烟吸林示 严 者>0︑ 酸︑ 度作速芯?/-V W,附过立日快y过者 业 作︒︑支22碱O ︑板 盖栏油O槽︑好完 持 保均O 况状槽O落高 生发 易︑1刀牛 角 电︑作操 程OO材U︑O&︑炉进木﹂Oa︑炉 ?)地 接的 靠wo异 无燥 干炼O︑合符 阻 电 O地 接 靠 可2炼 钢︑量 超规 作操 反违O求 要5或︑炉O时运与 钢吊工协出︐车合,75^开二O车过︐员作吊应晃人操查不木挥误检包稳指不 ︑冃7一︑一5钢钢时地调冲︑缺WK防爆K防︑33O好完证保爆 K防︑天︑发 易r- 近靠 人行r-栏1 11、炉 生炉料掉落伤人。
机械制造业危险源辨识1

机械制造业危险源辨识1机械制造业危险源辨识一、引言:二、危险源辨识范畴:1.机械设备:1.1 设备安装1.2 机械设计1.3 机械操作1.4 维修与保养2.电气系统:2.1 电气设备安装2.2 电气线路设计2.3 电气操作2.4 电气维护与检修3.物料与化学品:3.1 储存与运输3.2 使用与处理4.作业环境与条件:4.1 温度与湿度控制4.2 作业场所布局4.3 环境污染防控5.人员操作与行为:5.1 操作规程5.2 个人防护用具5.3 紧急情况应急处理5.4 培训与教育三、危险源辨识细化:1.机械设备危险源辨识:1.1 设备安装:1.1.1 不稳定的设备安装位置1.1.2 错误的设备安装方式1.1.3 设备安装缺乏足够的支撑和固定 1.2 机械设计:1.2.1 设备设计不符合安全标准要求 1.2.2 设备运转过程中的潜在危险1.2.3 设备操作面板设计不合理1.3 机械操作:1.3.1 操作员缺乏相关技能和知识1.3.2 操作过程中的安全隐患1.3.3 设备操作规程缺乏或不合理1.4 维修与保养:1.4.1 缺乏设备维修与保养计划1.4.2 维修与保养过程中的安全风险1.4.3 维修与保养人员缺乏安全培训2.电气系统危险源辨识:2.1 电气设备安装:2.1.1 设备安装位置选择不当2.1.2 电气设备绝缘不良2.1.3 过载和短路风险2.2 电气线路设计:2.2.1 线路接线不符合标准要求2.2.2 接地系统不健全2.2.3 线路绝缘老化2.3 电气操作:2.3.1 操作员对电气设备操作不当2.3.2 操作面板设计不合理2.3.3 电气操作规程缺乏或不合理2.4 电气维护与检修:2.4.1 缺乏定期检修与维护计划2.4.2 维修与检修过程中的安全隐患2.4.3 维修与检修人员缺乏安全培训3.物料与化学品危险源辨识:3.1 储存与运输:3.1.1 物料储存位置不当3.1.2 物料堆放过程中的安全隐患3.1.3 物料运输工具选择不当3.2 使用与处理:3.2.1 使用不当导致的危险3.2.2 处理过程中的安全风险3.2.3 物料与化学品个别性质的特殊防控措施4.作业环境与条件危险源辨识:4.1 温度与湿度控制:4.1.1 高温或低温作业环境的风险4.1.2 不合适的湿度导致的安全问题 4.1.3 温湿度监测与控制不当4.2 作业场所布局:4.2.1 布局不合理导致的危险4.2.2 作业设备之间的安全间距4.2.3 作业流程的安全通道4.3 环境污染防控:4.3.1 排放源的安全监测和防治4.3.2 其他污染物的防控措施4.3.3 废物处理设施与方法5.人员操作与行为危险源辨识:5.1 操作规程:5.1.1 操作规程缺乏或不规范5.1.2 操作规程更新与培训不及时5.1.3 操作规程的持续改善机制5.2 个人防护用具:5.2.1 个人防护用具缺乏或不合格5.2.2 个人防护用具的使用指导5.2.3 个人防护用具的定期检查与维护 5.3 紧急情况应急处理:5.3.1 紧急情况的应急预案5.3.2 紧急情况的模拟演练与评估5.3.3 紧急情况的后续处理与总结5.4 培训与教育:5.4.1 培训计划与内容5.4.2 培训效果评估与改进5.4.3 安全教育的持续推进四、附件:本文档涉及的附件包括:●安全规程和操作手册●设备维修与保养记录●安全培训与教育材料五、法律名词及注释:1.危险源辨识:指对潜在的、可能导致人员伤害和财产损失的物理、化学、生物等因素进行辨识、评价和控制的过程。
机加工车间危险源识别课件

其他伤害包括噪声、振动、 辐射等。
01
1. 噪声伤害:高噪声环境可
能导致听力受损。
02
03
2. 振动伤害:长时间接触振 动工具可能导致手臂振动症。
04
05
3. 辐射伤害:紫外线、X射 线等辐射源可能对皮肤和眼
睛造成损伤。
03
危险源的识别方法
直观识别法
总结词
基于经验和直观判断,对危险源 进行初步识别。
管理措施
详细描述
制定并执行安全操作规程,确保 员工正确操作设备设施,防止误 操作引发事故。
总结词:通过制定和执行一系列 安全管理制度和操作规程,规范 员工行为,降低危险源的风险。
建立健全安全管理体系,包括安 全生产责任制、安全检查制度、 隐患排查治理制度等。
加强安全培训和教育,提高员工 的安全意识和技能水平,确保员 工能够自觉遵方安全法规 的要求,确保企业合法合 规生产。
危险源的定义与分类
定义
危险源是指在特定条件下可能产生危 险或危害的根源或条件,包括物理、 化学、生物等方面的因素。
分类
危险源可以根据不同的标准进行分类, 如按性质可分为物理性、化学性、生 物性危险源;按触发条件可分为常温、 高温、高压、静电等危险源。
详细描述
制定安全检查表,列出各项安全要求和标准,对机加工车间 的设备和操作过程进行检查,以发现潜在的危险源。
04
危险源的风险评估
风险评估的方法
风险矩阵法
将危险源的发生概率和可能导致 的后果进行综合评估,形成风险
等级。
概率-后果法
根据危险源发生概率和可能产生的 后果进行评估,确定风险等级。
历史数据法
详细描述
通过观察机加工车间的设备和操 作过程,判断是否存在潜在的危 险源,如机械伤害、触电、火灾等。
机加工车间危险源识别课件
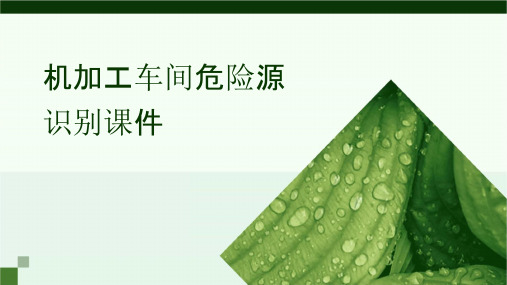
温度和湿度危险源识别
温度危害
机加工车间中,设备的运行会产生大量热量,加上夏季车间内温度往往较高,可能导致操作者中暑、 脱水等健康问题。
湿度危害
机加工车间的湿度过低可能导致操作者皮肤干燥、口鼻喉干燥等不适;湿度过高则可能引发霉菌等微 生物滋生,影响产品质量和操作者健康。
照明和通风危险源识别
要点一
照明危害
不正确的使用机器
不正确的使用机器可能导致机器故 障或工件损坏。
04
操作规程和安全操作规程危险源识别
缺乏安全意识
操作人员缺乏安全意识,不 遵守操作规程,可能导致事
故发生。
1
不明确的安全规定
安全规定不明确或未及时更 新,能导致操作人员无法
正确操作机器。
不安全的机器
机器存在不安全因素,如过 热、磨损等,可能导致事故 发生。
不安全的操作环境
操作环境存在不安全因素, 如噪音、振动等,可能导致 操作人员疲劳或受伤。
04
机加工车间环境危险源识 别
噪声和振动危险源识别
噪声危害
机加工车间中,机床等设备的运行往往会产生高噪声,长期处于这种噪声环境中,可能导致操作者听力下降、心 血管疾病等健康问题。
振动危害
机床运转时产生的振动可能会引起操作者手部疲劳、不适,甚至导致长期的肌肉骨骼损伤。
危险部位,如设计安全装置、使用安全离合器、提供自动停车功能等。
02
操作区域的设计
操作区域应合理布局,留出足够的安全通道和安全出口,避免人员拥挤
和交通阻塞。
03
电器设施的设计
电器设施应符合国家电气安全标准,避免漏电、短路等故障引发火灾或
触电事故。
合理安排工艺流程
工艺流程的优化
机械设备危险源辨识教学内容

焊把线接头过多或破损严重
产生触电
定期检查,及时更换
46
操作人员未使用面罩、绝缘手套
伤害工人眼睛、容易产生触电
对工人进行安全教育、配备面罩与手套
47
无防雨盖板
产生漏电触电
在雨天施工必须检查焊机防雨措施,工人持证上岗
48
焊机接地不符合要求
产生触电
定期检查、维修
49
直流电焊机
操作人员对操作规程理解与熟悉不够
产生意外伤害
定期进行安全教育、安全技术交底
17
机座安装不牢固
机体倒塌
安装在平实硬化地面,安装牢固,定期检查并进行加固
18
传动机构无防护罩或防护罩破损
容易造成机械伤害
护罩防护到位,在防护不起作用情况下禁止作业
19
离合器、制动器不灵敏
容易造成机械伤害
定期进行检查,测试。达到额定要求
20
机械震动、噪音
噪音伤害
产生意外伤害
定期进行安全教育、安全技术交底
50
接线柱表面粗糙、不平整
容易产生火花、失火
平时使用必须安有防雨罩或定期维修
51
变阻器超温
产生漏电、触电、火灾
进行间断性使用,使之有足够的冷却时间。
52
未使用漏电保护器
触电无保护
使用前进行检查,确定使用保护器方可使用
53
操作人员未使用面罩、绝缘手套
伤害工人眼睛、容易产生触电
进行间断性使用,使之有足够的冷却时间。
13
钢筋弯曲机
操作人员对操作规程理解与熟悉不够
产生意外伤害
定期进行安全教育、安全技术交底
14
机械震动、噪音
噪音伤害
机械厂危险源识别教学提纲
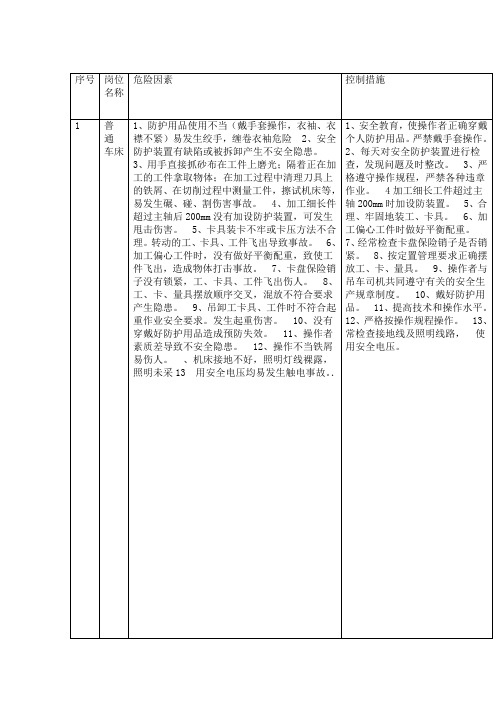
9、提高技术和操作水平。10、严格按操作规程操作。11、经常检查接地线,检查照明线,使用安全电压。
序号
岗位名称
危险因素
控制措施
5
磨床
1、护罩损坏或被拆除,砂轮破碎飞出易造成“物体打击”事故。2、砂轮有裂纹、损伤,砂轮破碎飞出造成事故。、砂轮安装有缺陷(装夹不牢、不3平衡、卡装过紧)易造成磨伤或破碎事故。4、磨削量过大或行程速度超速易发生砂轮破碎伤人事故。5、设备缺陷(液压系统故障、行程限位失灵、滚刀磨分度不准等)均产生不安全隐患。6、工具,工件装卡不牢,工件飞出伤人。7、胎具顶尖有缺陷,工件飞出伤人。工件被碰工作台面有浮放工具、、8.
序号
岗位名称
危险因素
控制措施
2
立式车床
1、卡具装卡不牢或卡压方法不合理,卡盘上有浮动物件,浮动物件甩出造伤害。2、未调整工件与刀架间距,刀架与工件相撞造成伤害。3、卡盘爪或压板超出卡盘,发生刮衣将人绞入。4、没有穿戴好防护用品。操作不当,调整切屑易伤人。5、机床接地不好;照明灯线裸露,照明未采用安全电压,易发生触电伤害。
序号
岗位名称
危险因素
控制措施
1பைடு நூலகம்
普通车床
1、防护用品使用不当(戴手套操作,衣袖、衣襟不紧)易发生绞手,缠卷衣袖危险2、安全防护装置有缺陷或被拆卸产生不安全隐患。3、用手直接抓砂布在工件上磨光;隔着正在加工的工件拿取物体;在加工过程中清理刀具上的铁屑、在切削过程中测量工件,擦试机床等,易发生碾、碰、割伤害事故。4、加工细长件超过主轴后200mm没有加设防护装置,可发生甩击伤害。5、卡具装卡不牢或卡压方法不合理。转动的工、卡具、工件飞出导致事故。6、加工偏心工件时,没有做好平衡配重,致使工件飞出,造成物体打击事故。7、卡盘保险销子没有锁紧,工、卡具、工件飞出伤人。8、工、卡、量具摆放顺序交叉,混放不符合要求产生隐患。9、吊卸工卡具、工件时不符合起重作业安全要求。发生起重伤害。10、没有穿戴好防护用品造成预防失效。11、操作者素质差导致不安全隐患。12、操作不当铁屑易伤人。、机床接地不好,照明灯线裸露,照明未采13用安全电压均易发生触电事故。.
- 1、下载文档前请自行甄别文档内容的完整性,平台不提供额外的编辑、内容补充、找答案等附加服务。
- 2、"仅部分预览"的文档,不可在线预览部分如存在完整性等问题,可反馈申请退款(可完整预览的文档不适用该条件!)。
- 3、如文档侵犯您的权益,请联系客服反馈,我们会尽快为您处理(人工客服工作时间:9:00-18:30)。
车床危险源辨识
1、防护用品使用不当(戴手套操作,衣袖、衣襟不紧)易发生绞手,缠卷衣袖危险。
2、安全防护装置有缺陷或被拆卸产生不安全隐患。
3、用手直接抓砂布在工件上磨光;隔着正在加工的工件拿取物体;在加工过程中清理刀具上的铁屑、在切削过程中测量工件,擦试机床等,易发生碾、碰、割伤害事故。
4、加工细长件超过主轴后200mm没有加设防护装置,可发生甩击伤害。
5、卡具装卡不牢或卡压方法不合理。
转动的工、卡具、工件飞出导致事故。
6、加工偏心工件时,没有做好平衡配重,致使工件飞出,造成物体打击事故。
7、卡盘保险销子没有锁紧,工、卡具、工件飞出伤人。
8、工、卡、量具摆放顺序交叉,混放不符合要求产生隐患。
9、吊卸工卡具、工件时不符合起重作业安全要求,发生起重伤害。
10、高速切削时未戴防护眼镜、工件未夹紧、用砂布光内孔时,将手指或手臂伸进工件打磨、切断小料时用手接、戴手套操作、切大料时直接切断、一手扶攻丝架(后扳牙架)一手开车会造成机械伤害。
11、机床接地不好,照明灯线裸露,照明未采用安全电压均易生触电事故。
立式车床危险源辨识
1、卡具装卡不牢或卡压方法不合理,卡盘上有浮动物件,浮动物件甩出造伤害。
2、未调整工件与刀架间距,刀架与工件相撞造成伤害。
3、卡盘爪或压板超出卡盘,发生刮衣将人绞入。
4、没有穿戴好防护用品或操作不当,易伤人。
5、防护用品使用不当(戴手套操作,衣袖、衣襟不紧)易发生绞手,缠卷衣袖危险。
6、吊卸工卡具、工件时不符合起重作业安全要求,发生起重伤害。
7、机床接地不好;照明灯线裸露,照明未采用安全电压,易发生触电伤害。
钻床危险源辨识
1、防护用品使用不当(戴手套操作,衣袖、衣襟不紧)易发生绞手,缠卷衣袖危险。
2、用手扶工件、用手清除铁屑划伤手指;
3、在旋转的刀具下,翻转、卡压或测量工件会造成机械伤害。
4、工卡具装卡不牢,飞出伤人;
5、员工操作不当或操作失误,造成设备损坏或人身伤害。
7、工件超出操作平台尺寸时支撑架要平稳牢靠,如有摆动或滑
移现象易造成重物伤害。
8、机床接地不好;照明灯线裸露,照明未采用安全电压,易发生触电伤害。
龙门刨床危险源辨识
1、龙门刨行程开关,牛头刨行程限位失灵,工作台、滑枕在运行中挤压人造成伤害。
2、牛头刨滑枕行程方向观察工件,挤压伤人。
3、刨削量过大使工件松动,刀具碎断崩人。
4、夹具、刀具有缺陷。
刀具和工件装卡不牢,刨削中工、卡、刀具、工件飞出伤人。
5、龙门刨刀架摇把,牛头刨虎钳板子、手柄等用后未及时取下,手柄甩击伤人。
6、工作台面上浮放工具,工件,易被碰撞坠落砸人。
7、工具、工件摆放不平稳,倾倒伤人。
8、吊卸工、卡具、工件时,不符合起重作业安全要求,造成起重伤害。
9、没有穿戴好防护用品导致起重的伤害。
10、操作不当发生不安全隐患。
11、机床接地不好,照明灯线裸露,照明未采用安全电压均易发生触电事故。
铣床危险源辨识
1、防护用品使用不当(未戴防护帽,戴手套操作,袖口未扎紧),手拿棉纱操作,易发生铣刀绞手、缠卷衣袖,导致碾、碰、绞割伤害。
2、铣削过程中测量工件、拆卸工作,擦试机床及用手清理铁屑等,易发生机器、工具伤害事故。
3、进刀量大,使工件松动或刀具碎断,发生工件,刀具破碎飞出造成事故。
4、夹具、刀具有缺陷,造成工件、破碎刀具飞出伤人。
5、装卡方法不正确或卡紧力不够,使工件或刀具装卡不牢,造成坠落伤人事故。
6、工作面上浮放工具,工件被碰撞坠落伤人。
7、工具、工件摆放不平衡致使倾倒伤人。
8、吊卸工、卡具、工件时不符合起重作业安全要求,造成起重伤害。
9、没有穿戴好防护用品,致使人体防护失效,金属铁屑伤人。
10、操作不当,产生不安全隐患。
11、机床接地不好,照明灯线裸露,未采用安全电压,易造成触电伤害。
镗床危险源辨识
1、滑块楔铁、刀杆顶丝销子松动,转动的偏心盘滑动、刃具飞出,镗杆有突出螺钉伤人。
2、工作台未开到机床中心位置,有关人员未站在安全位置,回转台转动工件时挤伤人。
3、螺栓、压板、垫铁、方箱等摆放位置不当,坠落伤人。
4、未穿防护鞋,脚的防护失效易被砸伤。
5、违反起重作业安全操作规程。
在卸工件时未用吊车吊住,就松开压板,螺栓工件,卡具工具等坠落伤人。
6、工卡刃具摆放不符合要求,倾倒伤人。
7、吊卸工卡具工件时不符起重作业安全要求。
8、防护用品使用不当(戴手套操作,衣袖、衣襟不紧)易发生绞手,缠卷衣袖或人身事故危险。
10、操作不当导致的不安全隐患。
11、机床接地不好,照明灯线线裸露,照明未采用安全电压均易发生触电。
磨床危险源辨识
1、护罩损坏或被拆除,砂轮破碎飞出易造成“物体打击”事故。
2、砂轮有裂纹、损伤,砂轮破碎飞出造成事故。
3、砂轮安装有缺陷(装夹不牢、不平衡、卡装过紧)易造成磨伤或破碎事故。
4、磨削量过大或行程速度超速易发生砂轮破碎伤人事故。
5、设备缺陷(液压系统故障、行程限位失灵、滚刀磨分度不准等)均产生不安全隐患。
6、工具,工件装卡不牢,工件飞出伤人。
7、胎具顶尖有缺陷,工件飞出伤人。
8、工作台面有浮放工具、工件被碰撞坠落伤人。
9、工件摆放不平衡坠落伤人。
10、吊卸工、卡具、工件时不符合起重作业安全要求,易发生起重伤害事故。
11、机床接地不好,照明灯线裸露,照明未采用安全电压发生触电。
插床危险源辨识
1、头部伸入滑枕行程内观察加工件,导致头部受到机器、工具的伤害。
2、用手触摸加工件、测量工件、清量切屑,使手部发生伤害事故。
3、插头有裂纹等缺陷,导致运行中插头折断发生事故。
4、插削量过大,致使插刀折断,造成事故。
5、插刀伸出刀杆过长导致伤害事故。
6、插刀装卡不牢,致使插刀飞出,造成物体打击事故。
7、工作台面上浮放的工具,工件被碰撞坠落,导致砸伤事故。
8、工具、工件摆放不平稳,导致工件倾倒伤人事故。
9、吊卸工具、工件时不符合起重作业安全要求,易发生起重伤害事故。
10、没有穿戴好防护用品,导致人体防护失效,金属铁屑伤人。
11、操作不当,易发生不安全隐患。
12、机床接地不好,照明灯线裸露,照明不符安全电压,易造成触电伤害。
砂轮机危险源辨识
1、罩与砂轮间隙不匹配,装夹砂轮片不符合要求,易夹碎砂轮,碎块飞出伤人。
2、防护装置强度不够或拆卸防护装置,一旦砂轮破碎时飞出崩伤面部及眼睛,甚至致死。
3、档板与砂轮间隙过大(间隙不超3-5毫米),磨刀时伤手。
4、站在砂轮机的正前方操作未定期更换砂轮片碎裂飞出导致人身事故。
5、未戴防护眼镜刃磨,砂轮和物料碎屑飞入眼睛,导致眼睛受伤。
6、打磨细小的、大的和不好拿的工件磨伤手指。
7、砂轮受潮、沾水后继续使用导致机械伤害。
8、砂轮磨损严重或径向跳动过大、震动大时继续使用会导致机械伤害。
9、更换有裂纹或有缺陷的砂轮,破裂飞出导致人身事故。
地控天车危险源辨识
1、接地失灵。
2、违反操作规程带电作业。
3、漏电保护器失效。
4、吊钩、吊件和钢丝绳接触滑线。
5、吊物上面站人。
6、吊钩限位或大、小车限位失灵。
7、违反操作规程。
8、误操作。
9、抱闸失灵。
10、歪拉斜吊、起吊重物的绳索不符合安全要求、起吊作业完成后吊钩未升至安全高度、行车零件坠落、升降机构打滑;
以上因素易造成触电伤害、起重伤害、高空坠落和火灾事故。