5S现场改善图片案例
5S现场管理培训系列之现场改善篇(PPT 71张)

整顿(Seiton):“零时间”能找到需 要
方法九
看板管理 让所有人一看就知道怎样做
公示类:岗位职责、人员配置、安全规程 作业类:工艺流程、交货期限、工作进程 设备类:平面布置、点检要求、维修计划 品质类:质量统计、不良处理、成品等级 事务类:去向显示、通知通告、文体娱乐
整顿(Seiton):“零时间”能找到需 要
整顿(Seiton):“零时间”能找到需 要
方法七
色彩管理
主 通 道:暗 红 色 运输设施:桔黄色 自来水管:黑色色环 蒸气管道:大红色环
直观透明
废 品 区:大 红 色 起重设施:黄黑相间 煤气管道:中黄色环 暖气管道:银灰色环
整顿(Seiton):“零时间”能找到需 要
方法八
愚巧化:改善工具,使“愚人”能象“巧匠”一样 工作。 手工配钥匙需要很高的技巧,用一台仿形机任何人 都能把它做得又快又好。 用手数小螺钉又慢又差,做一个定数器就能数得又 快又好。
卫生间的清扫
无蛛网、灰尘 无积垢、污迹 无明显气味 无乱涂乱划 墙面、地面、便沟内瓷砖整洁无破损 Seiso):规格化的清除工作
办公室的清扫
桌、椅、文件柜、电脑、花草等排列整齐 除茶杯外,不应有其他生活用品出现 门窗玻璃整洁明亮、桌椅沙发保持本色 桌面上面不应有太多的摆放,话机保持本色 茶杯、烟缸等客用品做到人走场清 报架、纱窗、遮阳蓬整齐无破旧 除装饰外,墙壁上不应有与工作无关的张贴
注 意
整理(Seiri) 区分“要”与“不要”
正常流转的原料、在制品 工位器具、周转箱 加工工具和检验用具 种类看板、工艺文件 办公桌椅、办公用品 安全消防用品 清洁清扫用品
要
5S实战改善案例(PPT129页).pptx

项目 区分
红
问题现Leabharlann 牌象描述原
因
理由
发行人
改善期限
改善责任人
处理方案
处理结果
效果确认
□物料 □地面 □看板
□产品 □电气 □作业台 □机器 □墙壁 □门窗 □文件 □档案 □办公设备 □运输设备 □更衣室 □厕所
□可(关闭) □不可(重对策) 确认者:
第六步:红牌作战
红牌作战要点: 不要让现场的人自己贴; 不要贴在人身上; 理直气壮地贴,不要顾及面子; 红牌要挂在引人注目处; 有犹豫的时候,请贴上红牌; 挂红牌要集中,时间跨度不可太长; 可将改善前后的对比摄下来,作为经验和成果向大家展示 挂红牌的对象可以是:设备、搬运车、踏板、工夹具、刀 具、桌椅、资料、模具、备品、材料、产品、空间等。
整顿推进的原则和方法 清扫推进的原则和方法 清洁推进的原则和方法
素养推进的原则和方法
定义:所谓“整理”是将活动主体作一番清理, 主要在于区分需要与不需要,然后将不需要的 东西予以处置。
目的:
分清要与 不要
●分清要与不要物,使条理分明;
●处置不要物,空间活用;
●找出发生根源,防止再发。
对象: ●工作场所中的所有物品,如材料及半成 品、工位器具、加工设备、工具等。
预备….开始!
1 2 3 4 5 6 7 8 9 10 1 2 3 张三 5 6 7 8 9 10
11 12 13 14 15 16 17 18 19 20 11 12 13 14 李四 16 17 18 19 20
21 22 23 24 25 26 27 28 29 30 21 22 23 24 25 王五 27 28 29 30
预备….开始!
5S与现场目视化管理(1)
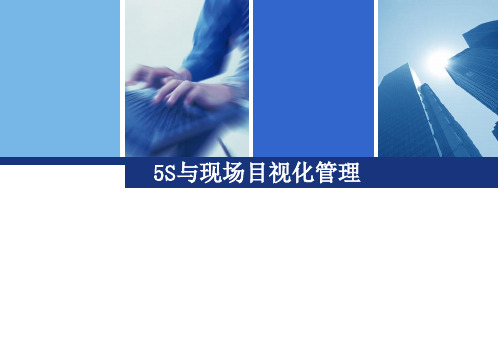
生产现场“查找污染源”活动操作流程
对现场划分区域,分组进行清扫、清洁活动。
组员对长期给现场带来污染的问题进行记录——填 写《现场“污染源”问题清单》。
活动负责人将查找到的污染进行汇总,填写《现场 5S问题改进跟踪评价表》。
清扫
活动负责人组织组员对污染进行源头分析。
讨论解决方案,明确实施负责人和改进期限。 实施改进。
缓冲工作台表面无污垢、杂物、蜘蛛网
流水线段 工位区域内流水线面板表面无污垢、杂物
地面 当班保持工位区域地面清洁干净、无杂物
班组 版本
A线A1、A2班
频次 使用工具
1次/班
抹布
方法 擦试
1次/班 1次/班 1次/周
51次/班
抹布 油枪 抹布
擦试 注油 擦试
1次/班 1次/班 1次/班
抹布 抹布 扫把/垃圾斗
44
修养
修养==对自身的高要求
➢ 人人养成好习惯,依规定行事,做遵守公
司制度,严于自律的员工
有人丢垃圾,无人捡垃圾是三流的工厂; 有人丢垃圾,有人捡垃圾是二流的工厂; 无人丢垃圾,有人捡垃圾是一流的工厂。
45
修养 坚持不懈地教育,才能养成良好的习惯
制度化 行动化 习惯化
一切活动都靠人,假如“人” 缺乏遵守规则的习惯,或者缺 乏自动自发的精神,推行5S易 于流于形式,不易持续
32
定点摄影法
现场一点改善对比图( CIP )
车间: XX车间
姓 名:
徐XX
成员:
生产线:
A线
班组:
活动名称
车间现场问题改善
活动时间: 2006.1.9
XX、XX、XXX A1、A2
Before 改善 前
仓库5S管理(附完整版仓库改善案例) PPT

又有怎样的感想?
管理不到位 保管员业务不熟 找个东西不容易吧
后果:效率低下,仓储成本高
现状:现实
高 枕 无 忧 的 年 代
原材料
已
人力
经
其它
过 去
现状:压力
资料来源:物资配送中心运营转型工作组
现状:选择
改善思路:“精益”理念触动管理者
备件库建库27年来,考察过不少 单位,进行过不少次的整理,但终究无 果。如何才能有效改变?成为一直是压 在领导层和每个职工心头的一块大石头。
资料来源:物资配送中心运营转型工作组
诊断分析
运用鱼刺图进行现场改善影响因素分析并制定措施
法
人
不同品种、3
工作不到位 1
不同规格混放
混放
备
件
5 制度不全
业务技能不够 2
4
无效、长期无动 态、常用物资混放
库 现 场
改
库内卫生差
无动态物资多 6
善 影
9 8
响 因
库内区域
无效物资多 7
素
规划不当
环
料
机
措施
5S:
(1)整理 (2)整顿
(3)清扫
(4)清洁
2019年11月15日星期五
(5)素养
3
为什么要做5S?
现场5S不彻底
仓库物品 摆放杂乱/‘
地面不洁
家人担心/照顾
容易对人身 造成伤害
5S = 安 全
大家要牢记 哦!
影响家庭生活
公司生产无法 正常进行
本人遭受痛苦 耽误工作
2019年11月15日星期五
办公桌、文件柜、放物架之物品 过期的表单、文件、资料 私人物品 生产现场堆积之物品
5S现场改善实战

区域清楚明了
16
二、生产现场改善前后对比图片
钣金车间改善成果展
改善前
改善后
这材料都是有用的吗, 怎么区分呢
分类标识摆放
2020/5/2
17
二、生产现场改善前后对比图片
钣金车间改善成果展
改善前
改善后
机台和工具摆放未规 划
2020/5/2
规划后,空间多了
18
二、生产现场改善前后对比图片
8
二、生产现场改善前后对比图片
钣金车间改善成果展
改善前
改善后
物品堆放杂乱的生产 车间一角
整齐分类并标识,一 目了然
2020/5/2
9
二、生产现场改善前后对比图片
钣金车间改善成果展
改善前
改善后
生产车间一角
2020/5/2
规划后生产车间一角
10
二、生产现场改善前后对比图片
钣金车间改善成果展
改善前
改善后
有用的分类摆放了
21
二、生产现场改善前后对比图片
钣金车间改善成果展
改善前
改善后
机台漏水了
2020/5/2
注意机台细节,分区 了,干净了
22
二、生产现场改善前后对比图片
钣金车间改善成果展
改善前
改善后
这是通道哦,都是摆 放的都是杂物
2020/5/2
通道有了,物品摆放 整齐了
23
二、生产现场改善前后对比图片
35
二、生产现场改善前后对比图片
喷涂车间改善成果展
改善前
改善后
报废的?
2020/5/2
清理了,通道明了
36
二、生产现场改善前后对比图片
5S现场管理-实例(前后对比)

• 处置方式: – 就近放在工作区域 – 丢弃 – 放在仓库
– 多余部分或是丢弃 或是放在仓库
20
不要物—桌子或柜子内
• 破旧的书籍、报纸或过期的刊物 • 老旧无用的报表、帐本 • 损耗的工具、余料、样品 • 已经损坏的文具 • 磨损的钻头、丝攻、磨刀石、锯条 • 精度已经恶化的游标卡尺、塞尺、量规等计测
视觉、 万用表 用抹布擦
抹布
修理依 赖清扫
2◇
点检 管道状态、冷却温度40-55℃ 清扫 无灰尘、水
视觉 用抹布擦 抹布
修理依 赖清扫
3◇
点检 清扫
油路正常、压力≤140kgf/cm2 无油污、灰尘
视觉、 操作 用刷子、 抹布清扫
抹布
修理依 赖清扫
10 ◇ ◇
◇
点检 油压2-3kgf/cm2 清扫 无油污
5
实施5S的好处...
• 对于个人而言:
– 提供您创造性地改善您工作岗位的机会; – 使您的工作环境更舒适; – 使您的工作更方便; – 使您的工作更安全; – 使您更容易和周围的同事交流; – ...
6
实施5S的好处...
• 对于企业而言:
– 零次品 -- 提高产品质量; – 零浪费 -- 降低成本; – 零“耽误” -- 提高交付可靠性; – 零事故--提高安全性 – 零停机--提高设备利用率 – 零抱怨-提高信心和信任
目的: ·培养全员讲卫生的习惯 ·创造一个干净、清爽的工作环境 ·使人心情舒畅
这里有脏污
3个注意点:
责任化、标准化 污染发生源改善
注意点1:责任化
区域、清扫部位、 清扫周期、要点·要求·目标
车间5S清扫点检表:
区域 清扫部位
5S改善案例(PPT 41页)
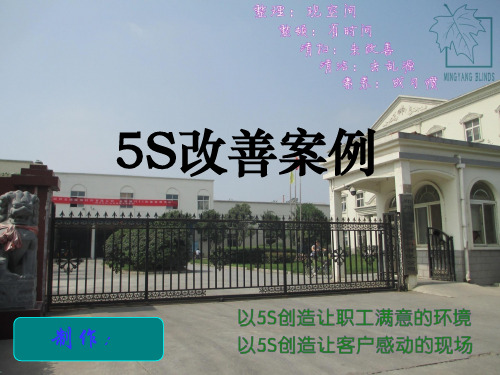
制作:
前言
5S是一场领导重视、全员 参与的持久战。能否成功 取决于我们的用心、恒心 与信心!
物检室砝码摆放整齐美观
改善前
改善后
外观水杯整齐有序、有标识
改善前
改善后
捻线员工休息室窗台
改善前
改善后
化验室剪刀有家了
呵,怎么剪刀兄弟也爬出来了?!
还是呆在“家里” 安全点!!
改善前
改善后
t-2020.10.2
• 14、我只是自己不放过自己而已,现在我不会再逼自 己眷恋了。20.10.204:51:442 October 202004:51
改善前
改善后
部品堆放易出现损坏现象
用废弃包装板制作部品摆放盒,这 样既方便又整齐,同时也避免了部 品积压。
工场改善成果展
改善前
改善后
焊膏机前的防静电板角有翘起 现象,操作很容易把脚踢伤, 造成安全事故。
在防静电板的四个角都安装螺 钉紧固,避免安全隐患。
5S
整理不可无, 整顿不可少。
成
清扫时时记,
•
6、意志坚强的人能把世界放在手中像 泥块一 样任意 揉捏。 2020年 10月2 日星期 五上午4 时51分 44秒04 :51:442 0.10.2
•
7、最具挑战性的挑战莫过于提升自我 。。20 20年10 月上午 4时51 分20.10. 204:51 October 2, 2020
•
8、业余生活要有意义,不要越轨。20 20年10 月2日 星期五4 时51分 44秒04 :51:442 October 2020
谢 谢 大 家 020 4:51 AM10/2/2020 4:51 AM20.10.220.10.2
5s现场管理精益改善案例

5s现场管理精益改善案例摘要:1.5S 现场管理的概念和作用2.5S 现场管理的内容和方法3.5S 现场管理的案例分析4.5S 现场管理在精益改善中的作用正文:5S 现场管理是一种有效提升现场管理水平和效率的方法,它通过对现场进行整理、整顿、清扫、清洁和素养等五个方面的改善,使现场达到安全、整洁、规范、有序的状态。
5S 现场管理不仅能够提高生产效率,还能提升产品质量,降低成本,提高员工的工作满意度和归属感。
5S 现场管理的内容包括:整理(SEIRI)、整顿(SEITON)、清扫(SEISO)、清洁(SEIKETSU)、素养(SHITSUKE)。
整理是指对现场的环境和物品进行清理,区分需要和不需要的物品,减少不需要的物品,使现场更加宽敞明亮。
整顿是指对现场的物品进行分类,将需要的物品摆放整齐,明确物品的存放位置,使现场更加有序。
清扫是指对现场进行彻底的清洁,清除垃圾和污垢,保持现场干净整洁。
清洁是指对现场进行定期清洁,保持现场的环境卫生,使现场更加美观。
素养是指对员工进行培训和教育,提高员工的素质和意识,使员工养成良好的工作习惯。
5S 现场管理的方法包括:标准化、可视化管理、看板管理、颜色管理等。
标准化是指对现场的工作进行标准化,制定标准操作程序和标准作业指导书,使工作更加规范化和标准化。
可视化管理是指将现场的工作内容和工作进度进行可视化,使员工能够清晰地了解现场的工作状态和工作要求。
看板管理是指通过看板将现场的工作内容、工作进度、质量状况等信息进行公示,使员工能够及时了解现场的工作情况。
颜色管理是指将现场的工作区域和物品进行颜色标记,使员工能够快速地识别物品的属性和位置。
5S 现场管理的案例分析:在某制造企业中,通过实施5S 现场管理,现场的环境和物品得到了有效的整理和整顿,现场的清洁和清洁工作得到了加强,员工的素养也得到了提高。
实施5S 现场管理后,该企业的生产效率提高了10%,产品质量合格率提高了20%,员工的工作满意度提高了30%。
5S现场管理改善建议
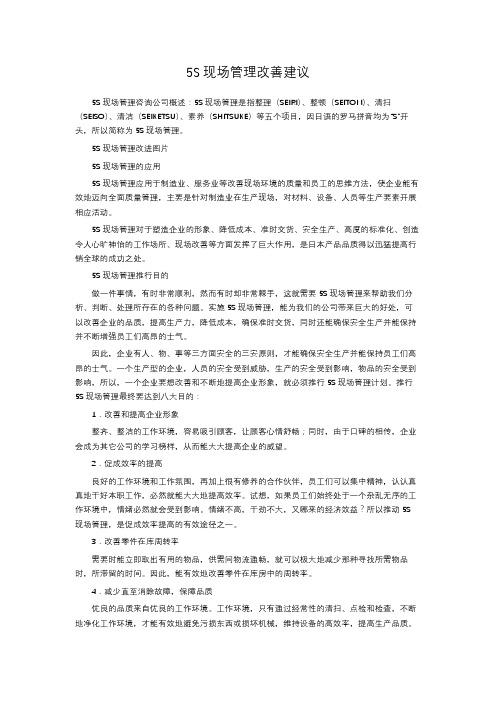
5S现场管理改善建议5S现场管理咨询公司概述:5S现场管理是指整理(SEIRI)、整顿(SEITON)、清扫(SEISO)、清洁(SEIKETSU)、素养(SHITSUKE)等五个项目,因日语的罗马拼音均为“S”开头,所以简称为5S现场管理。
5S现场管理改进图片5S现场管理的应用5S现场管理应用于制造业、服务业等改善现场环境的质量和员工的思维方法,使企业能有效地迈向全面质量管理,主要是针对制造业在生产现场,对材料、设备、人员等生产要素开展相应活动。
5S现场管理对于塑造企业的形象、降低成本、准时交货、安全生产、高度的标准化、创造令人心旷神怡的工作场所、现场改善等方面发挥了巨大作用,是日本产品品质得以迅猛提高行销全球的成功之处。
5S现场管理推行目的做一件事情,有时非常顺利,然而有时却非常棘手,这就需要5S现场管理来帮助我们分析、判断、处理所存在的各种问题。
实施5S现场管理,能为我们的公司带来巨大的好处,可以改善企业的品质,提高生产力,降低成本,确保准时交货,同时还能确保安全生产并能保持并不断增强员工们高昂的士气。
因此,企业有人、物、事等三方面安全的三安原则,才能确保安全生产并能保持员工们高昂的士气。
一个生产型的企业,人员的安全受到威胁,生产的安全受到影响,物品的安全受到影响,所以,一个企业要想改善和不断地提高企业形象,就必须推行5S现场管理计划。
推行5S现场管理最终要达到八大目的:1.改善和提高企业形象整齐、整洁的工作环境,容易吸引顾客,让顾客心情舒畅;同时,由于口碑的相传,企业会成为其它公司的学习榜样,从而能大大提高企业的威望。
2.促成效率的提高良好的工作环境和工作氛围,再加上很有修养的合作伙伴,员工们可以集中精神,认认真真地干好本职工作,必然就能大大地提高效率。
试想,如果员工们始终处于一个杂乱无序的工作环境中,情绪必然就会受到影响。
情绪不高,干劲不大,又哪来的经济效益?所以推动5S 现场管理,是促成效率提高的有效途径之一。
现场改善案例

垃圾线马达节约用电改善
垃圾线输送 带8小时连续 运转
设定运行时间, 每小时运行15 分钟
垃圾箱太小, 容易造成堆 积,需每5— 10分钟整理 一次
现员工15—45 分钟整理清扫 一次,劳动强 度减小了
改善前每年电费:12672度*0.71元/度=8997.12元 改善前每年电费:3168度*0.71元/度=2249.28元 每年为公司节约6747.84元(人民幣)
改善前将 把手套在 心轴杆上 后,再拿起 胶锤用力 打紧.每装 配一个把 手需要时 间是60秒. 劳动强度 大,产能 低。
改善后用 汽缸压把 手套,操作 时间是10秒, 操作轻松, 比改善前 工时减少 83%.
节约人工工时费用=(改善前瓶颈工时-改善后瓶颈工时)*作业人数*年产量*人工小 时费用=(60-24.7)秒*19人/3600秒*8520pcs*7.2元=11428.73元/年
自动吹铜 屑装置.
改善后,试水之 后马上在试水 台边吹铜屑, 且由自动装置 自动完成.搬 运0m
脚牙加工改善
改善前,牙板套为固定式, 造成平牙不良率为3%,返 修后会造成0.7%的废 品.(其中002029不良稍 低,为1.5%)
改善后,牙板套不固 定,可根据本体中 心自动修正,不良 率为0.
成 效
2.减少因碰伤不良品过多而影响出货交期的次数
3.减少不良品管理时间
拷贝纸回收再利用
员工成本意识不 强回收频率很少, 有时回收自用
会议倡导成本 意识,并要求 回收
回收后没有分类包 装有大、有小,没 部门领用,放了一 段时间影响“5S” 扔掉
派人员附助管 理、整理
自已部门用、 多余的扔掉
整理打包后现 有部门领用一 部分
精选5S改善图片1PPT42页

整顿事例—清扫工具2
清扫工具摆放凌乱,拿取不方便,不能判断状态的正常·异常。
规范清扫工具的摆放,明确管理担当,能一眼判断清扫工具摆放及返还状态的正常·异常。
P2
清扫工具摆放凌乱,拿取不方便,不能判断状态的正常·异常。
规范清扫工具的摆放,明确管理担当,能一眼判断清扫工具摆放及返还状态的正常·异常。
设计、作成新的作业台(只允许放置需要使用数量的东西),并标识、定位。能一眼判断正常·异常。
整顿事例—作业台
P13
油壶摆放凌乱,存在混用隐患,不能一目了然地看到油壶的在库状态及返还状态,不能判断油壶的正常·异常
对油柜实施整理、整顿。不同油类用颜色识别,并管理油壶数量,能一眼判断油壶数量、放置状态的正常·异常
作业台简化改善
改善前
改善后
作业台垃圾桶放置改善
作业区域包材限高改善及定位改善
手套回收基准明确改善
各种改善事例
5改善事例
扳手形状定位改善
工具柜物品放置标示改善
垃圾分类改善
安全帽3定管理
安全管理规定明确
成品放置标示改善
安全—防撞铁角
P24
『异常』配线杂乱缠绕,且直接落在地面上,既影响环境美观,又不方便清扫,且存在安全隐患。
『正常』实施配线整理后,既美观、干净,又方便清扫,安全隐患消除。
配线整理事例1
P25
配线整理事例2
『异常』配线杂乱缠绕,且直接落在地面上,既影响环境美观,又不方便清扫,且存在安全隐患。
『正常』实施配线整理后,既美观、干净,又方便清扫,安全隐患消除。
第二次改善
第三次改善
事例⑩:油柜的改善
5改善事例
问题概述:油类标识不清晰,油瓶没盖,摆放混乱,无法区分适用的油瓶
精益5S改善图例(大全三)
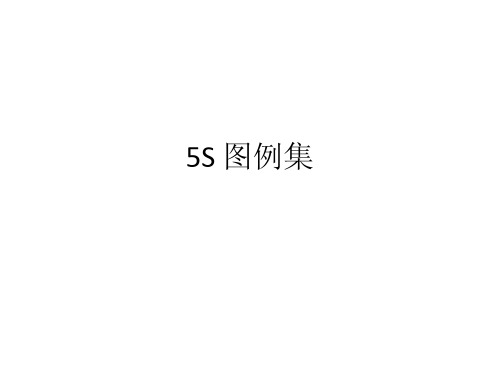
各类工装备件分类标识,说明具体用 途,附图片以避免备件防错位置
温度计
压力表
现物上如有标志,即不必每次对照标准书,任谁都可以 知道正常与否。
18. 人员素养
每班班前会重申5S、设备TPM、劳保用品穿戴、工艺纪律等要求
通过简单易懂的图片,将5S要求、员工自ຫໍສະໝຸດ 提出的5S改进内容张 贴在工厂门口
目视墙上将所有正在改进的5S项目公布于众,跟踪进度
员工5S宣言书,张贴在人人都能看到的通道旁,宣言书中有此员 工负责的5S具体项目和完成时间,小组成员等
管理人员定期对5S的推行效果进行评估
5S 图例集
红色使用区域
• 灭火机箱 • 50mm 红色胶带 实心线
红色使用区域
• 消火拴 • 50mm红色胶带 实心线 • 开门处1M内无障碍物,25cm为 一格分成四格
红色使用区域
• 禁止通行 • 50mm红色胶带 实心线
红色使用区域
• 工位操作区域:起始和结束位置
工位开始和结束位置
工位70%位置
2. 工位器具
工位器具5S要求
• 工位器具上无灰尘、油污、垃圾等
工位器具5S要求
• 工位器具上存放的 零件与工位器具需 吻合 • 现场有工位器具损 坏需及时报修(或 负责修理部门需及 时给予修理) • 工位器具上存放的 零件数与工位器具 设计存放零件数符 合
工位器具5S要求
• 工位器具上存 放的零件按存 放要求存放 • 工位器具摆放 整齐
入口编号
仓库位置 人行通道标识 警示
开启方向
人员通行许可
定置定位
地面和墙 上均标明 存放物料 相关信息
S改善案例(经典作品)
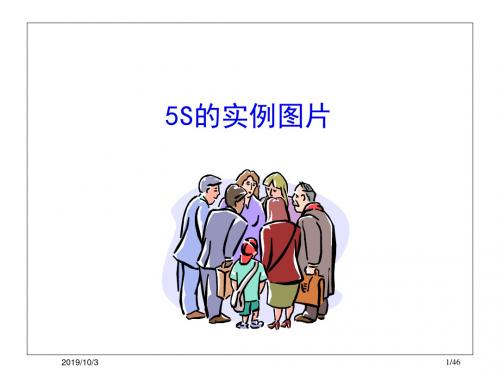
好
37/46
◎形迹定位管理 自己制作
2019/10/3
38/46
2019/10/3
39/46
2019/10/3
40/46
2019/10/3
41/46
2019/10/3
42/46
2019/10/3
43/46
2019/10/3
44/46
安冈正笃 名言-----日本汉学大师
心态变则态度变; 态度变则习惯跟着变; 习惯变则人格随之变; 人格一变则人生也就变。
态度 行为 习惯 人格 命运
想改变自己命运的时候,就从态度开始。
2019/10/3
45/46
谢谢大家!
2019/10/3
46/46
27/46
2019/10/3
28/46
2019/10/3
29/46
2019/10/3
30/46
2019/10/3
31/46
2019/10/3
32/46
2019/10/3
33/46
2019/10/3
34/46
2019/10/3
35/46
2019/10/3
不好 36/46
2019/10/3
检验区和作业区分开,慎防混料
文件未加以分类定置,易丢失
有了位置线,放错也不容易
车间规划清晰,一尘不染
物料置于车间通道,阻碍物流,影响效率
在制物料未标示清楚,易使产线弄错
整洁车间现场一览
车间整洁,员工战斗力高
流动红旗简单有效,你也可试
2019/10/3
26/46
2019/10/3
5S的实例图片
2019/10/3