工艺验证方案中风险评估报告
工艺风险评估范文
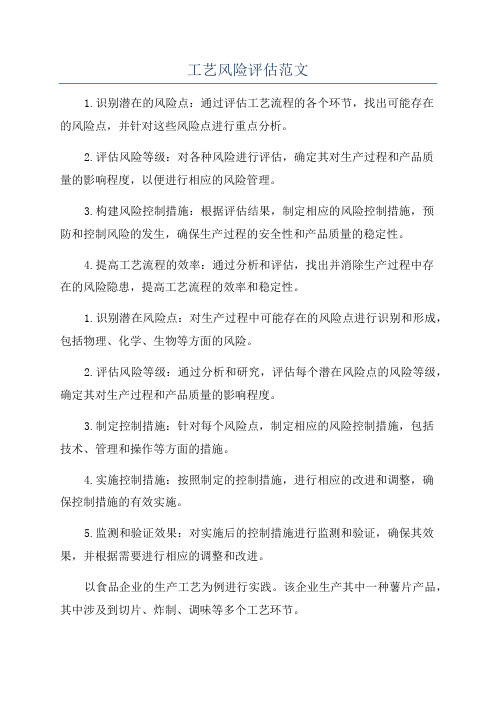
工艺风险评估范文1.识别潜在的风险点:通过评估工艺流程的各个环节,找出可能存在的风险点,并针对这些风险点进行重点分析。
2.评估风险等级:对各种风险进行评估,确定其对生产过程和产品质量的影响程度,以便进行相应的风险管理。
3.构建风险控制措施:根据评估结果,制定相应的风险控制措施,预防和控制风险的发生,确保生产过程的安全性和产品质量的稳定性。
4.提高工艺流程的效率:通过分析和评估,找出并消除生产过程中存在的风险隐患,提高工艺流程的效率和稳定性。
1.识别潜在风险点:对生产过程中可能存在的风险点进行识别和形成,包括物理、化学、生物等方面的风险。
2.评估风险等级:通过分析和研究,评估每个潜在风险点的风险等级,确定其对生产过程和产品质量的影响程度。
3.制定控制措施:针对每个风险点,制定相应的风险控制措施,包括技术、管理和操作等方面的措施。
4.实施控制措施:按照制定的控制措施,进行相应的改进和调整,确保控制措施的有效实施。
5.监测和验证效果:对实施后的控制措施进行监测和验证,确保其效果,并根据需要进行相应的调整和改进。
以食品企业的生产工艺为例进行实践。
该企业生产其中一种薯片产品,其中涉及到切片、炸制、调味等多个工艺环节。
1.识别潜在风险点:通过对每个工艺环节进行分析,确定可能存在的风险点。
比如在切片过程中,可能存在刀具伤害的风险;在炸制过程中,可能存在油温不稳定的风险等。
2.评估风险等级:对每个潜在风险点进行评估,确定其对产品质量和生产过程的影响程度。
比如对于刀具伤害的风险,在评估中确定其属于重要性较高的风险。
3.制定控制措施:针对每个风险点,制定相应的风险控制措施。
对于刀具伤害的风险,可以采取设置防护装置、加强培训等措施。
4.实施控制措施:根据制定的控制措施,对生产工艺进行相应改进和调整。
例如,设置防护装置并进行工人培训,确保切片过程中的刀具安全使用。
5.监测和验证效果:对实施后的控制措施进行监测和验证,并根据需要进行相应的调整和改进。
工艺风险评估验证及状态维护资料

工艺风险评估验证及状态维护资料在工业生产中,为了确保产品的质量和安全,需要进行工艺风险评估、验证及状态维护。
本文将从三个方面对工艺风险评估、验证及状态维护资料进行详细介绍。
首先,工艺风险评估是通过对每个生产工艺步骤进行系统、全面的分析和评估,确定其中存在的潜在风险,并采取相应措施进行控制和防范。
工艺风险评估资料主要包括以下几个方面:首先,需要明确每个工艺步骤的活动描述、目标、原理、参数和操作方法,以及可能产生的问题和风险。
其次,需要评估每个工艺步骤的潜在风险,包括人员安全、设备安全、环境安全、产品质量和客户满意度等方面的风险。
最后,需要针对每个潜在风险制定相应的控制措施和防范措施,并进行风险评估报告的编制和归档。
其次,工艺验证是通过实际操作和验证实验,验证工艺过程的可行性和有效性。
工艺验证资料主要包括以下几个方面:首先,需要明确验证的目标和标准,即要验证的工艺参数和指标,并制定验证方案和实施计划。
其次,需要详细记录和归档每次验证的操作过程、操作方法、参数设置和操作数据等,包括原始数据、衍生数据和验证结果。
最后,需要根据验证结果进行总结和评估,确定工艺参数和指标的可行性和有效性,并进行验证报告的编制和归档。
同时,还需要定期进行工艺验证的复核和更新,确保验证结果的准确性和可靠性。
最后,工艺状态维护是为了确保工艺过程的持续稳定和可靠性,避免由于人为原因或其它外部因素导致工艺变化和失控。
工艺状态维护资料主要包括以下几个方面:首先,需要确定适当的工艺参数和指标,以及监测和测量工具和方法,并编制相应的监测计划和维护计划。
其次,需要定期进行工艺状态的监测和测量,并记录和归档监测数据和测量结果,包括原始数据、衍生数据和状态评估结果。
最后,需要根据监测和测量结果进行状态评估和调整,及时采取相应的控制措施和防范措施,确保工艺的持续稳定和可靠性,并编制状态维护报告和状态调整方案。
综上所述,工艺风险评估、验证及状态维护资料的建立和管理对于确保产品质量和安全至关重要。
原料药工艺风险评估

原料药工艺风险评估标准化管理处编码[BBX968T-XBB8968-NNJ668-MM9N]XXXXX原料药工艺风险评估(样本)一、风险等级评估风险等级严重性可能性可检测性对关键质量属性有影响操作范围接近设计空间或注风险发生及有高必须严格控制才能保证册范围或参数范围较窄,参发生趋势时可以质量参数偏离范围为关数本身较难控制,正常情况立即被发现。
键性偏差。
下可能会偏离范围。
对关键质量属性可能有操作范围接近设计空间或注发现发生后稍中影响,不严格控制会出册范围或参数范围较宽,参后才能被发现现质量大的偏差数本身容易控制,异常情况下才会偏离范围。
对关键质量属性影响很操作范围远比设计空间或注发现发生后很低小,参数偏离范围为小册范围窄或参数范围比较宽,久后才能被发现偏差或微偏差紧急情况下才会偏离设计空间二、风险评估矩阵1、风险等级矩阵2、内在关键性矩阵高高高高严高潜在关键关键严中低中高重中非关键潜在关键重低低低中性低非关键非关键潜在性低低中高低中高可能性可能性3、可检测性和内在关键性矩阵 4、评估相关性报告文件最终关键性序名称描述可高非关键非关键关键号1 产品属性评估表影响工艺步骤评估检中非关键关键关键2 产品质量属性评估表影响工艺参数评估3 产品质量属性评估表工艺参数关键性评估测低非关键关键关键4 产品质量属性评估表工艺参数关键性评估性非关键潜在关键(采取控制措施后)内在关键性三:产品工艺风险评估1、风险评估小组确定评估小组负责人,成员有研发专家、技术转移人员、生产操作人员、工程人员、项目人员、验证人员、QA、QC、供应商(如必要);2、寻找产品质量属性(CQA)和关键工艺参数(CPP)的必要前提条件:1)文件资源:A 保证评估前已具备所有必要的文件;B 详细的文件资料能有效支持CQA和CPP风险评估的执行,有资料需求单。
2)良好培训A GMP知识培训;B 质量风险管理(ICHQ9);C 公司质量风险管理规程;D 产品工艺知识;E 产品质量属性和关键工艺参数评估程序;F 产品质量属性和关键工艺参数风险评估模板。
XX片剂工艺验证风险评估模板

质量风险评估工艺参数关键性评估报告编号:STP-SJ-品名:XXX片生产阶段:研发阶段口中试阶段口批量生产阶段口评估日期:20XX年X月X日1、质量风险评估的目的运用风险管理的工具,全面评估现执行的XXX片生产工艺,通过质量风险管理方法评估后确定生产工艺的关键步骤和关键工艺参数;通过加强员工培训教育、完善工艺规程及标准操作规程等管理和控制措施,提高质量风险控制的能力,以确保持续稳定的生产出符合预定用途和注册要求的药品。
2、评估流程五步法评估关键工艺参数1)筛选产品与工艺相关的关键质量属性2)筛选影响产品关键质量属性的工艺步骤3)筛选影响关键质量属性的工艺参数4)结合工艺参数进行风险评估确定工艺参数的关键性5)采取管理和控制措施进行风险控制,重新评估工艺参数的关键性3、风险等级与风险矩阵3.1风险等级3.2严重性和可能性矩阵(风险等级、内在关键性)风险等级内在关键性低中高 可能性3.3可检测性和内在关键性矩阵(最终关键性) 最终关键性内在关键性4、评估报告相关文件可 检 测 性重 性高 中 低非关键潜在关键关键产品质量属性评估表1—影响工艺步骤评估产品质量属性评估表2—影响工艺参数评估产品风险评估表3—工艺参数关键性评估产品风险评估表4—工艺参数关键性评估(采取管理或控制措施后)说明:1、产品质量属性:根据产品质量指标填写,如:外观、溶解度、鉴别、含量、杂质、水分等。
2、工艺步骤:该栏填写工艺步骤编号和相应的工艺步骤名称。
3、对质量属性有无影响填写“有”或“无” ;人机物法环任何一项或以上对质量属性有影响,结论栏中填写“有” ;均无影响,结论栏中填写“无” 。
4、质量指标(关键质量属性):该栏填写对应的工艺参数发生偏差时可能产生的影响,分高、中、低、无四个等级。
高:影响啊很大,主要决定因素;中:异常时有影响,影响一般;低:有影响但很小;无:无影响。
5、影响:按照该参数对各个关键质量属性各项中最严重程度来确定该参数的最终影响产品质量的程度。
风险评估预防措施报告

【最新资料,WORD文档,可编辑修改】1.目的对生产工艺中风险的可能性进行评估,以保证药品质量,保护公众用药安全。
2.范围此风险评估、预防措施报告仅适用于我公司生产和质量管理中存在风险评估、预防。
3.责任人质量风险管理小组4.内容4.1 风险评估工具:4.1.1风险等级计算 (RPN):RPN = O x S x DO = 失败发生的概率(Probability of occurrence)S =失败的严重性(Severity)D = 发现失败的概率(Probability of detection)原则:三个数值各自独立发生。
4.1.2 RPN 值的评估(RPN ):风险等级值是O ,S 和D 相乘的结果。
PRN 值在1-125之间,根据我公司的抗风险能力及公司实际情况采用下图中的限度2 。
4.1.3 依据风险等级值将风险划分为低风险、中等风险、高风险,具体如下: 1-16(低风险:应有一定的控制措施防止风险进一步升高);17-36(中等风险:须立即采取有效措施控制解决);37-65(较高等风险:应立即采取有效措施控制解决,增加监控频次及力度)。
66-95(高等风险:应立即采取有效措施控制解决,在得不到有效解决之前,不得继续生产)。
95-125(最高风险:应停止生产整顿)。
4.2.4 生产过程风险评估及预防措施4.2.5 生产设备风险评估及预防措施4.2.6 人员风险评估及预防措施人员的风险评价4.2.7 运输风险评估及预防措施4.2.9 检验风险评估及预防措施5.风险审核及批准结论审核人结论:。
生产工艺质量风险评估规范(含表格)

德信诚培训网生产工艺质量风险评估规范(ISO9001:2015)1.1风险分析标准从风险的严重性、频率数和检测性三方面对工艺存在的风险进行分析评估,判定标准如下:1.1.1严重性分级标准失败使中间产品或成品质量指标出现不合格或产生质量隐患,或对批产品质量均一性高(H)产生不良影响,导致该批产品全部做报废处理。
失败使中间产品某项质量指标不合格,但可经偏差处理,且不会对批产品质量均一性中(M)产生不良影响,不会导致成品有什么质量缺陷或隐患。
低(L)失败只会造成个别产品质量指标不合格,但可以百分之百将不合格品剔除。
1.1.2频率分级标准高(H)发生可能性每季高于1次。
中(M)发生可能性每年高于1次,低于4次。
低(L)发生可能性每年低于1次。
1.1.3可检测性分级标准具有反映质量均一性的质量指标,如含量均匀度、有关物质等能被仪器、设备100%控高(H)制和检测。
中间产品质量与成品质量指标均对同一质量项目进行控制和检测。
涉及水分、装量等能被仪器、人员进行离线检测,但如不对过程进行有效控制,产品中(M)质量均一性无法确认,检测结果应被怀疑的质量指标。
无法对影响产品质量的控制指标的真实性进行有效监控,因此可能会影响到产品质量低(L)均一性,也可能会造成整批产品报废,可通过产品质量间接反映出问题。
1.2 风险分析列表项目可能的失败模式可能的失败影响风险评价控制措施风险再评价验证活动严重性S可能性O可检测性D风险级别严重性S可能性O可检测性D风险级别领料领料发料错误产品整批报废H M H M 按生产指令、批生产记录进行复核。
H L H L 确认复核方式、复核内容粉碎过筛使用了错误的筛网物料细度与工艺要求不一致,影响后续工艺和产品溶出度H M M H筛网应有目数标识;每次使用前操作人员必需核对筛网目数;用标准筛对物料粉末进行过筛检查;H L H L确认筛网标识、筛网目数;检查粉末细度;筛网破裂异物进入产品中H M M H每次使用前、后对筛网的完好性进行检查H M H L 确认筛网的完好性;软材制备软材干湿度不均匀影响湿颗粒的制备M M M M控制设备转速、粘合剂浓度与加量、湿混时间;依据经验判定软材的干湿程度;M L M L确认设备转速、粘合剂、软材外观;软材含量不均匀影响干颗粒、成品含量的均一性H M M H 控制干混时间、湿混时间;M L M M 确认干混、湿混时间粘合剂配制错整批产品报废H L M M 双人单独复核粘合剂名称、浓度H L L L 确认复核方式项目可能的失败模式可能的失败影响风险评价控制措施风险再评价验证活动严重性S可能性O可检测性D风险级别严重性S可能性O可检测性D风险级别误湿法制粒湿法整粒刀转速过低或过高颗粒粒度不符合要求,影响后续生产M M M M每次使用前操作人员必需确认整粒刀转速;M M H L 确认整粒刀转速;筛网破裂异物进入产品中H M M H每次使用前、后对筛网的完好性进行检查H M H L 确认筛网的完好性;沸腾干燥使用的干燥空气不洁净颗粒被微生物污染H H M H使用高效过滤器对空气进行过滤,并定期维护保养、更换H L M M 无使用的干燥空气风量不足延长干燥时间,影响药品水分含量M M M M控制风机频率,确保风量;控制抖袋频次,防止堵塞;M L M L 确认风机频率、抖袋频次;加热温度不足延长干燥时间,影响药品水分含量M M M M控制进风温度、物料温度及干燥时间;M L M L确认进风温度、物料温度及干燥时间;干燥颗粒损耗大物料平衡、收率不合格,成品收率降低M M H M过滤袋安装前检查;根据干燥前中后段对风机频率调M L H L 确认风机频率项目可能的失败模式可能的失败影响风险评价控制措施风险再评价验证活动严重性S可能性O可检测性D风险级别严重性S可能性O可检测性D风险级别节。
生产工艺验证风险评估报告
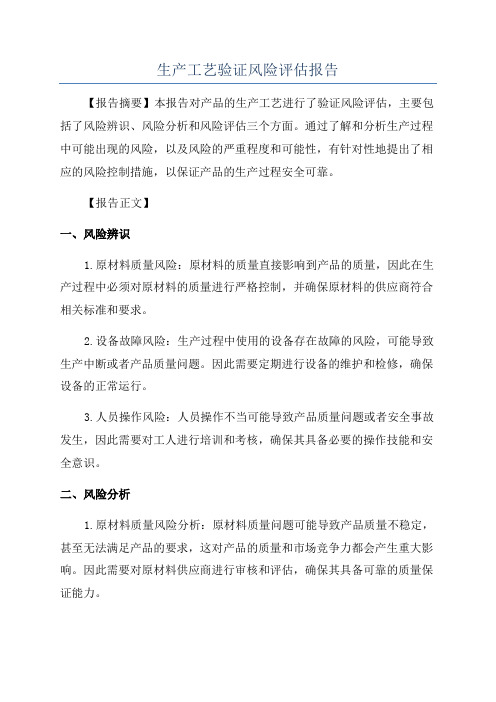
生产工艺验证风险评估报告【报告摘要】本报告对产品的生产工艺进行了验证风险评估,主要包括了风险辨识、风险分析和风险评估三个方面。
通过了解和分析生产过程中可能出现的风险,以及风险的严重程度和可能性,有针对性地提出了相应的风险控制措施,以保证产品的生产过程安全可靠。
【报告正文】一、风险辨识1.原材料质量风险:原材料的质量直接影响到产品的质量,因此在生产过程中必须对原材料的质量进行严格控制,并确保原材料的供应商符合相关标准和要求。
2.设备故障风险:生产过程中使用的设备存在故障的风险,可能导致生产中断或者产品质量问题。
因此需要定期进行设备的维护和检修,确保设备的正常运行。
3.人员操作风险:人员操作不当可能导致产品质量问题或者安全事故发生,因此需要对工人进行培训和考核,确保其具备必要的操作技能和安全意识。
二、风险分析1.原材料质量风险分析:原材料质量问题可能导致产品质量不稳定,甚至无法满足产品的要求,这对产品的质量和市场竞争力都会产生重大影响。
因此需要对原材料供应商进行审核和评估,确保其具备可靠的质量保证能力。
2.设备故障风险分析:设备故障可能导致生产中断,引起产品质量问题和生产计划延误。
因此需要对设备进行定期的检修和维护,并建立相应的备用设备,以应对可能的故障情况。
3.人员操作风险分析:人员操作不当可能导致产品质量问题或者安全事故发生,对生产和企业形象都会产生负面影响。
因此需要对工人进行培训,提高其操作技能和安全意识。
三、风险评估1.原材料质量风险评估:原材料质量风险的严重程度取决于原材料对产品质量的影响程度,以及原材料质量的稳定性。
通过对原材料的质量进行评估,确定其对产品质量的影响,以及原材料供应商的质量管理能力。
2.设备故障风险评估:设备故障可能导致生产中断,严重影响生产进度和产品质量。
通过对设备的故障概率、维修时间和备用设备的可用性进行评估,确定设备故障风险的可能性和严重程度。
3.人员操作风险评估:人员操作不当可能导致产品质量问题和安全事故发生。
工艺验证工艺风险评估
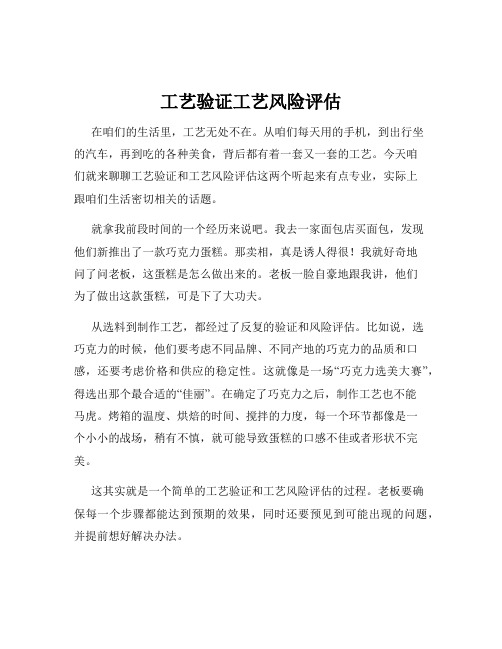
工艺验证工艺风险评估在咱们的生活里,工艺无处不在。
从咱们每天用的手机,到出行坐的汽车,再到吃的各种美食,背后都有着一套又一套的工艺。
今天咱们就来聊聊工艺验证和工艺风险评估这两个听起来有点专业,实际上跟咱们生活密切相关的话题。
就拿我前段时间的一个经历来说吧。
我去一家面包店买面包,发现他们新推出了一款巧克力蛋糕。
那卖相,真是诱人得很!我就好奇地问了问老板,这蛋糕是怎么做出来的。
老板一脸自豪地跟我讲,他们为了做出这款蛋糕,可是下了大功夫。
从选料到制作工艺,都经过了反复的验证和风险评估。
比如说,选巧克力的时候,他们要考虑不同品牌、不同产地的巧克力的品质和口感,还要考虑价格和供应的稳定性。
这就像是一场“巧克力选美大赛”,得选出那个最合适的“佳丽”。
在确定了巧克力之后,制作工艺也不能马虎。
烤箱的温度、烘焙的时间、搅拌的力度,每一个环节都像是一个小小的战场,稍有不慎,就可能导致蛋糕的口感不佳或者形状不完美。
这其实就是一个简单的工艺验证和工艺风险评估的过程。
老板要确保每一个步骤都能达到预期的效果,同时还要预见到可能出现的问题,并提前想好解决办法。
再比如说,咱们穿的衣服。
一件衣服从布料变成咱们身上漂亮的时装,这中间也经历了无数的工艺环节。
服装厂要验证裁剪的方式是否合理,缝纫的线是否结实,染色是否均匀,而且还要评估在生产过程中会不会出现布料浪费、工人操作失误等风险。
工艺验证,简单来说,就是检查咱们的工艺是不是真的能做出咱们想要的东西,而且每次做出来的质量都差不多。
就像做数学题,咱们得保证用同样的方法,每次都能算出正确的答案。
这可不是一件容易的事儿!得有严格的标准,得有精确的测量,还得有认真负责的态度。
比如说,一家生产玩具的工厂,他们要生产一款会说话的娃娃。
那在生产之前,就得先验证一下,设计的电路能不能让娃娃清晰地说话,外壳的材质够不够结实,颜色够不够鲜艳。
这每一个环节都得仔仔细细地检查,不能有一点儿马虎。
工艺风险评估呢,则是在工艺验证之前,先想想可能会出现哪些问题。
- 1、下载文档前请自行甄别文档内容的完整性,平台不提供额外的编辑、内容补充、找答案等附加服务。
- 2、"仅部分预览"的文档,不可在线预览部分如存在完整性等问题,可反馈申请退款(可完整预览的文档不适用该条件!)。
- 3、如文档侵犯您的权益,请联系客服反馈,我们会尽快为您处理(人工客服工作时间:9:00-18:30)。
1.概述:根据《药品生产质量管理规范》2010年修订第二章第十四条规定:应当根据科学知识及经验对质量风险进行评估,以保证产品质量。
本报告是对公司工艺验证方案中质量风险评估。
2.目的:通过对生产部门质量风险评估,确认目前采取的各项生产管理控制措施可以将产品在生产过程中产生的质量风险控制在可以接受的范围内。
3.范围工艺验证方案中质量风险评估
4.风险识别评估--工艺验证中涉及到导致验证失败的风险因素( 表1)
5、采取避免风险的措施后再评估
针对以上可能产生的情况,我们采取以下措施:(表2)
6.评估结论:根据以上分析评估,对存在风险经采取相应措施后,我公司生产工艺验证方案中质量风险基本可控,确保工艺验证的有效性。
工艺验证工作中还应加强以下几点:6.1.认真做好操作人员和验证人员培训工作。
将工艺验证过程中可能发生的质量风险贯彻到每个操作人员思想意识中、落实到每个验证环节中去。
6.2. 操作人员和验证人员严格执行各项管理规程和生产操作规程,所有验证应该复核的工作必须坚持做到。
表1工艺验证风险要素和级别列表
风险序号可能的风险风险级别
1 文件不完整或内容有错误,或者包含有让人
误解的信息。
高
2 操作人员没有经过相关培训,导致未按规定
的要求进行操作
中
3 生产设备不匹配、操作不当或没有校验中
4 车间洁净区尘埃粒子、沉降菌超标,房间之
间压差不符合要求
中
5 纯化水不符合要求高
6
设备及场地清洁不彻底,导致成品微生物限
度超标
高
评估意见根据以上分析评估,对工艺验证存在风险点采取相应的消减措施
评估人员:
年月日
表2 采取避免风险的措施后评估表。