模具设计概论精编WORD版
模具概论第5章
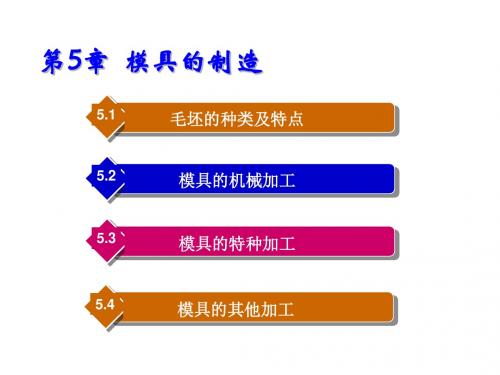
平面的加工方法有车、刨、铣、磨、研磨、 刮研,可根据模座与模板的不同精度和表面粗糙 度要求选用,并组成合理的加工工艺方案。 加工模座、模板上的导柱和导套孔除应保证 孔本身的尺寸精度外,还要保证各孔之间的位置 精度。可采用坐标镗床、数控镗床或数控铣床进 行加工。若无上述设备或设备精度不够时,也可 在卧式镗床或铣床上将模座或模板一次装夹,同 时镗出相应的导柱孔和导套,以保证其同轴度, 如图5-7所示。
图5-6 导套研磨工具 1—锥度心轴 2—研磨套 3、4—调整(锁紧)螺母
研磨时将导柱安装在车床上,由主轴 带动旋转,导柱表面涂上一层研磨剂,然
后套上研磨工具并用手握住,作轴向往复 运动。研磨导套与研磨导柱类似,由主轴 带动研磨工具旋转,手握套在研具上的导 套,作轴向往复直线运动。调节研具上的 调整螺钉和螺母,可以调整研磨套的直径, 以控制研磨量的大小。
图5-1 模具加工与生产中,坯料(毛坯)的加工 与制造是由原材料转变为成品的生产过程 的第一步。模具寿命的长短,质量的好坏, 在很大程度上都取决于所选择的毛坯。因 此,毛坯的种类和制造方法的选择,需根 据生产类型和具体生产条件,并注意充分 利用新技术、新工艺、新材料以便降低成 本,提高质量。
(2)坐标磨削。坐标磨削加工和坐标镗削 加工的有关工艺步骤基本相同,是按准确的 坐标位置来保证加工尺寸的精度,只是将镗 刀改为砂轮。它是一种高精度的加工工艺方 法,主要用于淬火工件、高硬度工件的加工。 对消除工件热处理变形、提高加工精度尤为 重要。坐标磨削范围较大,可以加工直径小 于1 mm至直径达200 mm的高精度孔。加工精 度可达0.005 mm,加工表面粗糙度Ra可达 0.32~0.08 m。
4.工厂生产条件 选择毛坯应考虑毛坯制造车间的工艺 水平和设备情况,同时应考虑采用先进工 艺制造毛坯的可行性和经济性。如中小工 厂其锻压设备能力较差,或根本没有锻压 设备,在不影响零件质量及性能的情况下, 尽量选用型材毛坯加工,但应该注意提高 毛坯的制造水平。
模具概论第3章

3.级进模
级进模又称连续模,是指在压力机的 一次行程中,依次在同一模具的不同工位 上同时完成多道工序的冲裁模。在级进模 上,根据冲件的实际需要将各工序沿送料 方向按一定顺序安排在模具的各工位上, 通过级进冲压便可获得所需冲件。
图3-13 级进模结构原理 1—冲孔凸模 2—落料凸模 3—导正销 4—卸料板 5—导料板 6—固定挡料销 7—凹模 8—始用挡料销
2.复合模 复合模是指在压力机的一次行程中, 在模具的同一个工位上同时完成两道或 两道以上不同冲压工序的冲模。复合模 是一种多工序冲模,它在结构上的主要 特征是有一个或几个具有双重作用的工 作零件——凸凹模
落料冲孔复合模工作部分的结构原理 图,如图3-10所示,凸凹模5兼起落料凸模 和冲孔凹模的作用,它与落料凹模3配合完 成落料工序,与冲孔凸模2配合完成冲孔工 序。在压力机的一次行程内,在冲模的同 一工位上,凸凹模既完成了落料又完成了 冲孔的双重任务。
(1)冲裁级进模。冲裁级进模根据条料的 送进定位方式进行分类,常见的结构形式有 用固定挡料销与导正销定位的级进模和用侧 刃定距的级进模两种。
用固定挡料销和导正销定位的冲孔落 料级进模,如图3-14所示。工作零件为冲 孔凸模3、落料凸模4和凹模7,定位零件为 固定挡料销8、始用挡料销10、导正销6和 导料板(与卸料板做成了一个整体),导 板5既是上、下模的导向装置又是卸料装置, 还起到条料导向作用。
第3章 模具的基本结构及功能
3.1
冷冲模结构
3.2
塑料成形模具结构
3.3
压铸模及锻模结构 粉末冶金模具结构
3.4
3.1 冷冲模结构
1.冷冲模的结构类型 冷冲模的结构类型很多,一般可按 下列不同特征分类。 (1)按工序性质分类,可分为落料 模、冲孔模、切断模、切口模、切边模等。 (2)按工序组合程度分类,可分为 单工序模、级进模、复合模等。 (3)按模具导向方式分类,可分为 开式模、导板模、导柱模等。
模具概论II第110页-第219页

I================================================================================= 110 模具概論Ⅱ表3-2 塑膠材料的線膨脹係數與收縮率在射出成形加工中,模具需承受很高的射出壓力與鎖模壓力;因此,模具的各構成部分要有足=================================================================================I ================================================================================================================================================================== 夠的強度,才不致於產生破裂或變形.欲瞭解模具需要的強度時,首先應知道塑膠射入型腔中的壓力,型腔中的壓力會因塑膠種類.成形品厚度.模具型態以及成形條件而有所差異,一般強度計算時約取500~700kg/cm 2.實際計算模具強度時,是以模具允許的變形量為依據的;即在壓力下,模具變形在一限定範圍內時之強度.模具允許之變形量,依成形品需求及塑膠流動而異,一般精密度要求不高的成形品可取0.1~0.2mm,如此成形品上可能會有毛邊產生;如精密度要求高且不允許有毛邊時,流動性較差的塑膠約採用0.01mm,流動性良好的塑膠則頇在0.02mm 以下. 1. 矩形凹模側壁計算矩形凹模側壁厚度的計算,依其構造可分為:(1) 凹模與底部不成一體時:模板加工穿透孔,再嵌入模塊做為凹模底部,如圖3-42,計算側壁厚度h 之公式如下h=3ä384124Eb a plh:側壁厚度(mm) p:成形壓力(kg/cm 2) l:凹模寬度(mm) a:凹模深度(mm)e:彈性係數,銅料取2.1×106kg/cm 2 b:模板厚度(mm) δ:允許變形量(mm)(2) 凹模與底部成一體時:直接在模板上加工凹模,強度較高,如圖3-43,計算側壁厚度h 之公式如下I ================================================================================================================================================================== h=34äE cpah:側壁厚度(mm) p:成形壓力(kg/cm 2)a:凹模深度(mm)e:彈性係數,銅料取2.1×106kg/cm 2δ:允許變形量(mm)c:計算常數,取決於l/a 之值,如表3-3 l:凹模寬度(mm)利用此公式也可計算模板變形量,計算時公式改變為:δ=34Ehcpa 表3-3 取決於l/a 的常數c 值2. 圓形凹模側壁計算圓形凹模無底的情況,如圖3-44,其側壁變形量之計算公式如下:δ=⎪⎪⎭⎫ ⎝⎛+-+m r R r R E rp 222δ:凹模半徑的變形量(mm)P:成形壓力(kg/cm 2) E:楊氐係數(kg/cm 2)R:凹模外圓半徑(mm) R:凹模內圓半徑(mm) M:蒲松氏比,鋼料為0.253. 可動模模板的計算可動側模板加工穿透孔,再嵌入模塊成為击模時,頇在模板背面加裝承板,如圖3-45,此時击模I ================================================================================================================================================================== 之力量是由承板承受的, 承板頇有足夠的強度以免變形. 承板變形量的計算公式如下(設定L=l 時):δ=3434432512138453845EBhpbL Bh E pbL EIpbL =⋅= 將此公式改變計算承板厚度,則成為:h=34325∂EB pbLh:承板厚度(mm)p:成形壓力(kg/cm 2) L:間隔塊間的距離(mm) L:承受壓力部分的長度(mm) B:承受壓力部分的寬度(mm) B:模板寬度(mm) δ:允許變形量(mm)E:彈性係數,銅料取2.1×106kg/cm 2I:承板的斷面二次矩=123Bh當成形品投影面積大時,L 值較大,承板厚度也要加厚;若在間隔塊中間加設支柱,如圖3-46,可使用厚度較小的承板,承板厚度可用下式算出,約為原度的40%.I ================================================================================================================================================================== h=()34322/5∂EB L pb若在間隔塊中間加設二支支柱,如圖3-47,則承板度應用下式算出,約為原厚度的23%.H=()∂EB L pb323/5343.3-5模具設計程式1. 分析成形品:瞭解成形品的形狀.材質.數量.特性.選定分模線位置.2. 決定模具大小及材質:依據成形品情況.生產需要進行成形品佈置,計算模具強度,決定模板尺度.材質.3. 決定模具型態:安排流道.選擇澆口,決定脫模方式.模具組成.冷卻系統.熱處理.電鍍.4. 決定模具結構:計算其他各模板尺度.強度,決定各零件尺度.規格.材質.5. 相關資料:瞭解成形機資料.冷卻系統資料.塑膠收縮率等.6. 繪製組合圖:注意模具組合.加工方法.功能.7. 繪製零件圖:計算收縮率,注意配合許可差.加工方法. 8. 檢查設計結構及尺度.本章重點整理1. 以模具成形為塑膠最主要的成形方法.壓縮成形.轉移成形.射出成形之模具,都是利用填型腔來製I================================================================================= 作成形品的.2.壓縮成形之模具可分為溢出型.防溢型及半防溢弄三種類型.轉移成形模具要分為罐式及柱塞式二種類型.射出成形模具可分為二板式.三板式及特殊機構三種類型.3.二板式模具可由分模面分開為固定側及可動側二部分,包含的零件有:模板.導銷.導銷襯套.定位環.豎澆道襯套.頂出銷.復歸銷. 豎澆道拉料銷.頂出板.間隔塊.安裝板等.4.三板式模具的主體,除了固定側模板與可動側模板外,另加上一塊澆道脫料板.5.成形品設計對模具設計影響大,成形品設計應注意分模線.脫模斜度.厚度.補強及防止變形.击轂.孔.螺紋等.6.模具設計必頇計算成菜收縮率.模具強度.7.模具設計之套裝程式含:分析成形品.決定模具大小及材質.決定模具型態.決定模具結構.相關資料.繪製組合圖.繪製零件圖.檢查設計結構及尺度.118模具概論Ⅱ學後評量=================================================================================I=================================================================================一.填充題1.壓縮成形模具主要的構成為____________及___________.2.壓縮成形模具由柱塞與型腔閉合方式的不同,可分為_________._______及____________三種.3.轉移成形模具依其構造上有二種基本類型,分別為___________轉移模具及__________轉移模具.4.射出成形模具依其構造區分為_______模具_______模具._______模具等三類.5.二板式模具是由__________側及__________側兩大部分所構成.6.三板式模具開模時,由固定側模板與可動側模板間取出的是__________,由固定側模板與澆道脫料板間取出的是______________.7.無流道模具一塑膠保溫與加熱方式可分為____________.____________,及___________四種.8.二板式模具的固定側模板,一般稱為_________模板,用以塑製成形品的_________表面;可動側模板一般稱為________模板,用以塑製成形的__________表面.9.模具的二塊模板合模之接觸面稱為________面,合模後內部所形成的空間為____________.10.模板開閉時,做引導定位工作的是__________與______________.11.一般模具安裝引導定位裝置時,是將_________裝於可動側,而將_______裝於固定側.12.在模具中,為取出成形品而分開之模板接觸面稱為____________面.13.分模面在成形品上去留下之細線痕跡稱為_________線,一般用________來表示.14.為使成形品在開模時附著在可動側,通常模具側之脫模角應較_________側略小.15.塑膠成形品上應避免使用螺距_______mm以下的螺紋.16.塑膠成形收縮率為a,成形品尺度為M時,常溫模具尺度應為_________.17.欲瞭解模具需要的強度時,應先知道塑膠射入型腔中的___________.實際計算強度時,是以模具允許的___________量為依據的.二.問答題1.說明壓縮成形的加工方式.2.說明溢出型壓縮成形模具的優缺點.3.說明防溢型壓縮成形模具的優缺點.4.說明轉移成形的加工方式.5.說明射出成形的加工方式6.定位環與豎澆道襯套有何功用?7.說明復歸銷之作用原理.8.豎澆道有何功用?=================================================================================I=================================================================================9.說明三板式模具開模之動作.10.良好之模具應具備那些條件?11.分模線位置決定時,應考慮那些事項?12.說明決定成形品厚度時,應考慮的因素.13.塑膠成形品上的肋有何功能?14.說明模具設計之程式.流道系統44.1 流道的形狀=================================================================================I================================================================================= 4.2 澆口的類型4.3 流道與澆口尺度計算122 模具概論Ⅱ流道系統是在模具中,引導熔融塑膠進入型腔中的通道.轉移成形模具.射出成形模具中均有流道系統,其中又以射出成形模具化較多,較具有代表性.各種射出成形模具中,二板式模具.三板式模具滑動模具之流道系統較具有共同性,在本章會有完整說明,而無流道模具其流道較特殊,將在第七章中再介紹〃塑膠模具的統道系統包含豎澆道(sprue).橫澆道(runner).澆口(gate)等.此系統的設計,會影響成形=================================================================================I================================================================================= 品的品質.精密度.外觀及成形週期,在模具設計時,必頇詳加考量.4.1 流道的形狀典型的塑膠模具流道系統如圖4-1,塑膠自成形的噴嘴進入模具,流經豎澆道充填冷料井,再流經橫澆道,通過澆口而進入型腔中,同時將模具內之氧體經由排氧孔排出模具.即完整的流道系統依序為:豎澆道→冷料井→橫澆道→澆口→型腔→排氧孔.4.1-1 豎澆道(sprue)豎澆道又稱注道,是塑膠進入模具的入口.通常自塑膠進入處向模具內伸進的方向,其直徑應逐漸擴大,目的是為了豎澆道的脫模;擴大的錐度一般約2°~4°.豎澆道必頇加工光滑,減不塑膠流動阻力也使脫模容易,一般可直接在模板上鑽孔.鉸孔,也可安裝現成的豎澆道襯套.其入口直徑,頇視成形品.材質與成形機而異,一般小型成形品約為3mm,中型成形品約為4mm,大型成形品則用5mm或以上,而塑膠流動性較差時,尺度頇加大.實際應用時,豎澆道入口直徑(D)應略大於成形機噴嘴口直徑(d),=================================================================================I=================================================================================如圖4-3,因若d>D時,噴嘴前端冷凝之塑膠會堵塞隹豎澆道入口,塑膠無法進入模具,或在成形後無法拉出;同時,豎澆道入口之圓弧(R )也應略大於嘴端之圓弧(r ),如圖4-4,若r>R時,會有塑膠流入圓弧間之空隙,成形後無法脫模.4.1-2 橫澆道(runner)橫澆道設於分模面上,是連接澆道到澆口間的通道.在模具中,若一次成形兩件以上成形品,或只成形一件成形品但需設兩個以上澆口時,都需要以橫澆[道引導塑膠到成形品的各澆口.在安排橫澆道時,應注意儘可能使橫澆道等長,也儘可能短,圖4-5為在模具內橫澆道等長之安排方式,等長的橫澆道=================================================================================I ================================================================================= =================================================================================能使塑膠同時充填各型腔.為使塑膠在橫澆道內流動順利,橫澆道表面頇加工光滑;對於流動性較差之塑膠,橫澆道應儘可能避免轉折,或在轉折處做成圓弧,如圖4-6.不同的橫澆道安排,使成形品有不同的佈置方式,會影響模具之尺度,故在模具設計時,成形品佈置.橫澆道安排必頇先決定.橫澆道的斷面形狀有圓形.梯形及U 字形等三種,如圖4-7所示.圓形斷面可容納最大的塑膠量,而與塑膠接觸的表面積最小,流動摩擦與熱損失最少,是最理想的斷面形狀;但在製作時,必頇在分模面兩側加工半圓要槽才能脫模,較為困難.梯形橫澆道通常只在澆口同側加工,因製作容易,節省時間,常被採用4.1-3 澆口(gate)澆口是塑膠進入型腔的入口,如圖4-8,可分為非限制澆口與限制澆口兩類.澆口的主要功能,在控制塑膠進入型腔,當澆口較大時,塑膠容易充填型腔,但也易使成型品受流道壓力的影響,在澆品附近殘留較大應力.如澆口過小,塑膠進入型腔速度過慢,可能造成充填不足.收縮下陷.收縮率大.燒焦.熔接線等間題.適當的澆口尺度,應由形品的大小.形狀.澆口的配置.形狀,塑膠的特性及模具的情況等因素來決定.I=================================================================================澆口位置的安排對成形品影響很大,同時也會影響模具的結構及成形作業.安排澆口時應注意,儘可能在成形品厚度較大的部位,因塑膠自厚處流向薄處較容易;且在厚處硬化時間長,收縮量較大,在保壓期較易由澆口補充塑膠.澆口是成形品連接橫澆道之處,會在成形品上留下痕跡,設置時應考慮是否容易去除,及如何避免造成外觀及功能上之影響.此外,澆口會有殘留應力集中,應避免設於成形品受力之處.4.1-4 冷料井(slag well)冷料井用以容納流動時前端冷凝的塑膠,避免橫澆道或澆口被阻塞,通常設於豎澆道末端及橫澆道分叉部位,如圖4-9.當塑膠在流道系統中流動時,前端的冷凝塑膠會先流進冷料井,待冷料井充填滿後,高溫的塑膠才繼續流向型腔.一般模具冷料井的直徑約深度則約為直徑之1-1.5倍.豎澆道末端的冷料井,除了收集冷凝塑膠外,還與豎澆道拉料銷共同作用,利用圖4-10之倒鉤,在模具開啟時將豎澆道拉離固定模,再由豎澆道拉料銷將豎澆道及冷料井一起頂出活動模,如圖4-11.=================================================================================I=================================================================================4.1-5排氧孔(vent)模具排氧的目的,是使型腔是的空氣.塑膠帶入或產生的氧體,能在成形時迅速的排出於模具外,以防止充填不完全,或在工件上造成燒焦.氧泡等,影響成形品品質及外觀.一般模具排氧的方法,是利=================================================================================I ================================================================================= =================================================================================用塑膠流動的壓力,將氧體經由模具排氧孔排出模具外.模具排氧孔位置的選擇,是在型腔中塑膠最後到達或可能補塑膠密封的地方,通常是在遠離澆中的分模面上或型腔凹入部位,可利用頂出銷.嵌入模塊的配合間隙以及在分模面上加工淺凹槽.排氧孔必頇使氧體能通過,而塑膠不能進入形成毛邊,故尺度必頇加以注意.加工凹槽做為排氧孔時,一般採用的深度約0.02-0.03mm,寬度依成形品形狀而定,約5-10mm,圖4-12.4.2 澆口的類型塑膠成形品形狀千變萬化,成形時塑膠的流動亦受各種因素影響,在模具中澆口之安排,必頇依成形品的形狀.塑膠的特性而變化,一般應用的澆口種類包含:4.2-1 非限制澆口由豎澆道直接將塑膠注入型腔的澆品稱為直接澆口(direct gate),為非限制澆口的代表.直接澆口如圖4-13,一次隻成形一件成形品,塑膠直接由豎澆道進入型腔,壓力損失小,充填良好,有利於大成形品及較深成形品之成形;俚因截面形狀變化大,凝固時冷卻速度不同,且有應力集中之尖角,故澆口附近澆口附近會有殘留應力集中,容易造成平面的翹曲,扭曲.採用直接澆口通常未設冷料井,僅在正對豎澆道部位使成形品略微击出,以掩飾豎澆道之收縮痕跡,如圖4-14,困未設冷料井,成形時冷凝塑膠會直接進入型腔,影響成形品品質,應加注意.直接澆口因型態特殊,澆口的位置較為固定,能做的選擇少,且成形品上會留下大的澆口痕跡,選擇採用時,應多加考慮.表4-1為一般使用的直接澆口尺度參考。
模具设计概论第3-2章
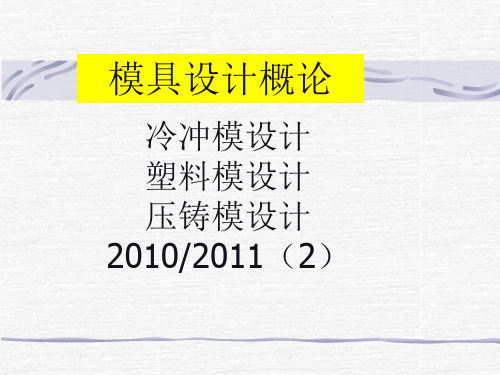
§3-7 模具压力中心的确定
3.复杂形状零件模具压力中心的确定
复杂形状零件模具压力中
心的计算原理与多凸模冲裁压 力中心的计算原理相同。 除上述的 解析法 外,还可 以用作图法和悬挂法。
§3-8 冲裁工件的排样
一、排样原则
冲裁件在条料上的布置方法称为排样。
图3-23 用阶梯凸模冲裁
§3-6 冲裁力
三、卸料力、推件力和顶件力
卸料力F卸:从凸模上卸下板料所需的力 推件力F推:下打料时,从凹模内向下推 出工件或废料所需的力 顶件力F顶:上打料时,从凹模内向上推 出工件或废料所需的力
§3-6 冲裁力
三、卸料力、推件力和顶件力
在实际生产中按照经验公式计算三种力:
§3-5 凸模与凹模工作部分尺寸的计算
二、模具制造方法5
1.分别加工法 分别规定凸模和凹模的尺寸和公差,分别进行制造。 用凸模与凹模的尺寸及制造公差来保证间隙要求。 模具制造难度大;形状简单、间隙较大的模具或精 密设备加工的凸模和凹模;具有互换性,便于成批 制造 2.单配加工法 用凸模、凹模相互单配的方法来保证合理间隙。加 工后的凸模与凹模不能互换,必须对号入座。 落料件选择凹模为基准模,冲孔件选择凸模为基准 模。多用于冲裁件形状复杂、间隙较小的模具
一、尺寸计算的原则
3.保证合理间隙 (见表3-3、3-4 ) 由于间隙在模具磨损后会增大,所以在设计凸、凹模 时均取最小合理间隙Zmin 。 注意:合理的冲裁间隙值有一个变动范围,取较小的间 隙有利于提高冲裁件的质量,取较大的间隙有利于提 高模具的寿命,所以在确定冲裁间隙时要综合考虑, 一般取最小合理间隙。 4.凸、凹模的制造公差应与冲裁件的尺寸精度相适应。 可查表3-1 5.尺寸计算要与模具制造方法相适应(详细内容见“模 具制造方法”部分)
模具概论第9页-第18页
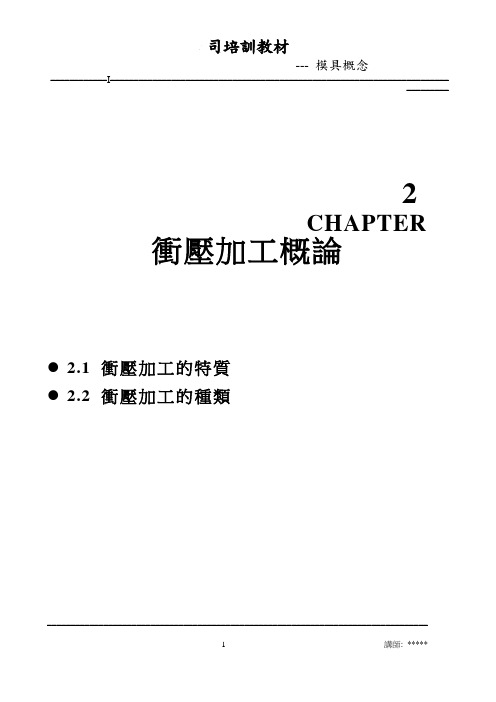
============I ==================================================================================================================================================================2 CHAPTER衝壓加工概論● 2.1 衝壓加工的特質● 2.2 衝壓加工的種類============I ==================================================================================================================================================================衝壓加工在近代工業大量生產及材料加工技術中扮演著非常重要的角色,在工業界不斷的研究與改進中,零件制造的精度與生產效率均已大大的提高,取代了很多傳統切削加工;如鍛造及壓鑄、鑄件等,成為現代工業生產中降低成本的最佳方法之一. 所謂的沖壓加工,係指利用沖壓機械及其專用工具-[模具]在常溫狀態下對欲加工材料施行各種成形加工.現今沖壓加工之應用已非常普遍,沖壓加工的零件隨處可見.如手上的戒指、手錶裹大部分的零件、衣服上的拉鏈、銅釦、皮帶釦環、眼鏡架及鞋帶或金屬接頭等,可能都是沖壓件.照明用具的罩子、燈泡銅頭、門的把手、煙灰缸、刀叉、湯匙、廚具電力零件……等等,許多之家庭用具均是衝壓模具所生產的零件,這些用品以簡單的一套模具一次加工即可完成,複雜的則需幾個工程,甚至數套模具來完成,但其加工的速度仍是其他加工法所不及的,就如螺釘、墊圈等零件,用模具生產每日產量可達數十万件之多,大如汽車輪轂、翼子板、車門、車頂、飛機機身等零件,每日產量亦可達上百件之多,可見模具之應用範圍已與日俱增,而模具之未來前途發展正如旭日東升,不可限量.============I ==================================================================================================================================================================2.1 衝壓加工的特質衝壓加工,正式應用在材料加工生產,始於十九世紀末期,此種生產機械零件之加工方式,有諸多其他加工方式無法同時兼顧之優點,故近百年來深受工業界人士所重視,不斷的研究發展力求改進並擴大應用,致有今日蓬勃成長的景象,其特點如下:一、 衝壓加工的優點1 .合乎經濟效益(1) 生產量大,相對零件制造成本低.(2) 縮短工作時間,節省勞力.(3) 操作簡單,非熟練工人亦能操作2 .材料使用率高在衝壓加工中,不但廢料較其他加工少,而廢料幾乎可100%回收. 3 .加工簡單在材料耗費不大的情況下,簡單的衝擊即可得複雜的零件. 4 .生產率高在生產的過程中,應用了自動化的機械設備及多工程的進給裝置,已大大的提高了零件的生產效率.============I ==================================================================================================================================================================5 .精密度高同一模具制造出來的產品,具有相同的尺寸與形狀,可得良好的互換性零件.有上述諸優點,但並非任何零件均可加工,亦有其限制,分別列述如下:二 、衝壓加工的缺點1 .零件的形狀需合乎衝壓加工生產的形狀,才能加工.2 .模具屬專用化,一副模具只能生產同一形狀的零件.3 .對於生產量少的零件,較不適合模具加工,因為要分攤較高的模具費用,相對提高了零件的制造成本.4 .模具制造需相當的時間,不能即時生產以致交貨期受到限制.5 .零件的形狀大小不同,則衝壓機械的選用亦不同. 2.2 衝壓加工的種類依各種加工性質不同來區分,有些需將材料剪斷分離,有些則是加工於材料使其產生塑性變形,所以一般依成品加工性質的不同而將衝壓加工分為衝剪加工(shearing)、彎曲加工(bending)、引伸加工(drawing)及壓縮加工(compression)等四大類.============I ==================================================================================================================================================================一 、衝剪加工的種類將材料置於衝頭及下模塊之間,利用衝壓機械在材料上施以剪斷強度以上的外力,使衝頭刀刃與下模刀刃相互作用,讓材料一部份與另一部份分離的加工謂之衝剪加工,此種加工主要可完成切斷、下料、衝孔、衝口、修邊與整緣等工作,如表2.1所示.表 2.1 衝剪加工種類============I ==================================================================================================================================================================二、彎曲加工及其種類加工於金屬板料,使其在塑性變形範圍內,彎曲成所需要的形狀與角度,當外力除去時仍能維持其彎曲之永久變形謂之彎曲加工。
模具设计概述word资料35页

目录1 概述2 设计步骤3 五金模具设计流程4 塑料模具设计步骤5 模具CAD/CAE1 概述2 设计步骤3 五金模具设计流程4 塑料模具设计步骤5 模具CAD/CAE6 模具设计师模具设计- 概述模具设计模具,是以特定的结构形式通过一定方式使材料成型的一种工业产品,同时也是能成批生产出具有一定形状和尺寸要求的工业产品零部件的一种生产工具。
大到飞机、汽车,小到茶杯、钉子,几乎所有的工业产品都必须依靠模具成型。
用模具生产制件所具备的高精度、高一致性、高生产率是任何其它加工方法所不能比拟的。
模具在很大程度上决定着产品的质量、效益和新产品开发能力。
所以模具又有“工业之母”的荣誉称号。
什么是模具设计呢?按国家职业定义,模具设计是:从事企业模具的数字化设计,包括型腔模与冷冲模,在传统模具设计的基础上,充分应用数字化设计工具,提高模具设计质量,缩短模具设计周期的人员。
模具设计- 设计步骤模具CAD1、对所设计模具之产品进行可行性分析,以电脑机箱为例,首先将各组件产品图纸利用设计软件进行组立分析,即我们工作中所说的套图,确保在模具设计之前各产品图纸的正确性,另一方面可以熟悉各组件在整个机箱中的重要性,以确定重点尺寸,这样在模具设计中很有好处的,具体的套图方法这里就不做详细的介绍了。
2、在产品分析之后所要进行的工作,对产品进行分析采用什么样的模具结构,并对产品进行排工序,确定各工序冲工内容,并利用设计软件进行产品展开,在产品展开时一般从后续工程向前展开,例如一产品需要量五个工序,冲压完成则在产品展开时从产品图纸开始到四工程、三工程、二工程、一工程,并展开一个图形后复制一份再进行前一工程的展开工作,即完成了五工程的产品展开工作,然后进行细致的工作,注意,这一步很重要,同时需特别细心,这一步完成的好的话,在绘制模具图中将节省很多时间,对每一工程所冲压的内容确定好后,包括在成型模中,产品材料厚度的内外线保留,以确定凸凹模尺寸时使用,对于产品展开的方法在这里不再说明,将在产品展开方法中具体介绍。
模具设计与制造设计说明word版
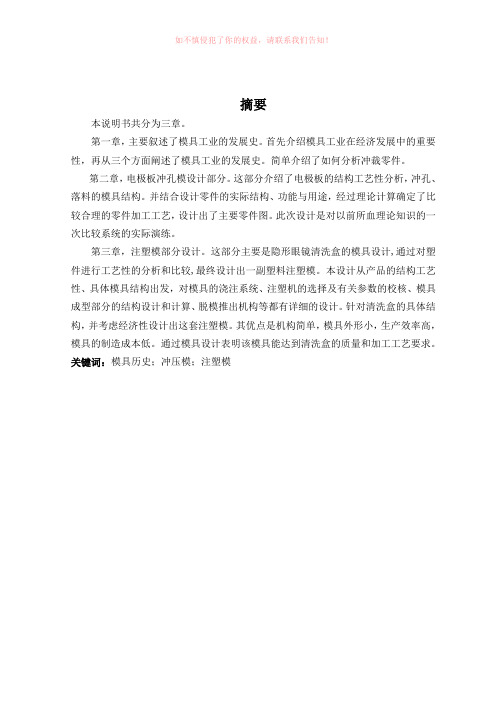
摘要本说明书共分为三章。
第一章,主要叙述了模具工业的发展史。
首先介绍模具工业在经济发展中的重要性,再从三个方面阐述了模具工业的发展史。
简单介绍了如何分析冲裁零件。
第二章,电极板冲孔模设计部分。
这部分介绍了电极板的结构工艺性分析,冲孔、落料的模具结构。
并结合设计零件的实际结构、功能与用途,经过理论计算确定了比较合理的零件加工工艺,设计出了主要零件图。
此次设计是对以前所血理论知识的一次比较系统的实际演练。
第三章,注塑模部分设计。
这部分主要是隐形眼镜清洗盒的模具设计,通过对塑件进行工艺性的分析和比较,最终设计出一副塑料注塑模。
本设计从产品的结构工艺性、具体模具结构出发,对模具的浇注系统、注塑机的选择及有关参数的校核、模具成型部分的结构设计和计算、脱模推出机构等都有详细的设计。
针对清洗盒的具体结构,并考虑经济性设计出这套注塑模。
其优点是机构简单,模具外形小,生产效率高,模具的制造成本低。
通过模具设计表明该模具能达到清洗盒的质量和加工工艺要求。
关键词:模具历史;冲压模;注塑模Abstractspecifications is three chapters together mark.The first chapters , the phylogeny having narrated mould industry's mainly. Introduce mould industry phylogeny having set forth mould industry again from three aspect in significance in economic growth first. How analyse according to cutting a part that the simplicity has been introduced.Second chapters , electrode board punched hole models design a part. This part has introduced unnatural electrode structure manufacturability analysis, punched hole , the blank mould structure. And link structure , function designing the part reality with use, by that theory calculates picture having ascertained the comparatively rational part processing handicraft , having designed out the main part. Design a comparatively systematic reality being institute blood theory knowledge to the previously this time drilling.Third chapters, produce plastic articles by injection moulding the model part designs that. This part is that the haptic lens washes the box design for die and mould mainly , pass to analysis and comparison moulding the manufacturability being in progress piece, model designing that a set of plastic produces plastic articles by injection moulding out ultimately. Design that structure sets off from product structure manufacturability , concrete mould originally, both the physical design to mould choice pouring system , the injection machine and school core , mould about parameter molding part and secretly scheming against , demould debuting organization and so on have detailed design. Specifically for the structure cleaning the box concre, and think that economy designs that this produces plastic articles by injection moulding set out model. Whose merit is that organization is simple , mould external form is small , the efficacy is high, the mould cost of manufacture is low. Can reach the mass cleaning a box's and process technological requirements by the fact that design for die and mould indicatesthat mould.Keywords: Mold history , the stamping model, produce plastic articles by injection moulding mold目录第一章综述························································1 概述·························································2 如何分析冲裁零件···············································第二章电极板冲孔模的设计···········································1 产品简介·······················································2 电极板冲孔模设计的前期准备·····································2.1研究设计任务···············································2.1.1阅读冲裁件产品零件图····································2.1.2分析冲裁件零件·········································2.1.3冲裁加工的经济性分析···································3 电极板冲孔模总体方案的确定·····································3.1电极板冲孔模类型的确定·····································3.1.1三种方案················································3.1.2分析论证················································3.2结构形式的确定·············································3.2.1操作方式选择············································3.2.2等位方式的选择··········································3.2.3卸料方式················································4 电极板冲孔工艺计算············································4.1凸凹模刃口尺寸计算········································4.1.1凸凹模刃口尺寸计算原则··································4.1.2简单形状凸凹模刃口尺寸的计算····························4.2冲压里的计算··············································4.2.1计算冲裁力··············································4.2.2计算卸料力、推件力······································4.2.3计算冲压力总和··········································4.3初选压力机················································4.3.1压力机类型的选择········································4.3.2压力机规格的选择········································4.4压力中心的计算·············································4.4.1简单形状压力中心········································4.4.2多凸模的压力中心········································5电极板冲孔模主要零部件设计计算·································5.1凹模的设计计算·············································5.1.1凹模孔口的设计··········································5.1.2凹模外型结构的设计······································5.1.3凹模凹模外型尺寸的计算··································5.1.4凹模的固定方法··········································5.2固定板的实际计算···········································5.2.1凹模固定板的设计·······································5.2.2凸模固定板的设计········································5.3卸料板的设计计算···········································5.3.1卸料板的类型选择········································5.3.2卸料板的尺寸············································5.4定位零件的设计计算·········································5.4.1定位板的结构············································5.4.2定位板尺寸的计算········································5.5弹性元件设计计算···········································5.5.1橡胶垫的自有高度········································5.5.2橡胶垫的直径············································5.6凸模的设计计算·············································5.6.1凸模的结构设计··········································5.6.2凸模尺寸的计算··········································5.7电极板冲孔模其他零件的设计和选择···························5.7.1模座的设计··············································5.7.2模柄的设计··············································5.8电极板冲孔模闭合高度的计算·································5.9压力机的选择···············································第三章隐形眼睛清洗盒注塑模的设计··································1 拟定模具的结构形式·············································1.1塑件成型工艺分析···········································1.2分型面位置的确定···········································1.3确定型腔数量和排列方式·····································1.3.1型腔数量的确定··········································1.3.2型腔排列形式的确定······································1.4模具结构形式的确定·········································1.5注射机型号的选定···········································1.5.1注射量的计算············································1.5.2投影面积及所需锁模力的计算······························1.5.3选择注射机··············································1.5.4注射机有关参数的校核····································2浇注系统的设计·················································2.1主流道设计·················································2.1.1主流道尺寸··············································2.1.2主流道衬套形式··········································2.1.3主流道凝料体积··········································2.1.4主流道剪切速率校核······································2.2分流道设计·················································2.2.1分流道布置形式··········································2.2.2分流道尺寸长度··········································2.2.3分流道的形状、截面尺寸及凝料体积························2.2.4分流道剪切速率校核······································2.2.5分流道表面粗糙度········································2.3浇口的设计·················································2.3.1潜伏式浇口尺寸的确定····································2.3.2浇口剪切速率的校核······································2.4冷料穴的设计···············································2.4.1主流道冷料穴············································2.4.2分流道冷料穴············································3成型零件的设计·················································3.1成型零件的结构设计·········································3.1.1凹模设计················································3.1.2型芯设计················································3.2成型零件钢材的选用·········································3.3成型零件工作尺寸的计算·····································3.3.1型腔径向尺寸············································3.3.2型芯径向尺寸············································3.4成型零件强度及支承板厚度计算·······························3.4.1型腔侧壁的厚度·········································3.4.2支承板的厚度···········································4 模架的确定。
模具概论II第254页-286页
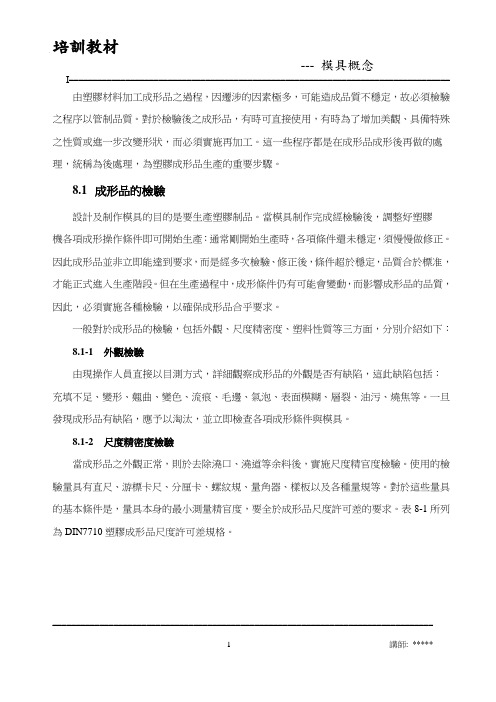
I================================================================================= 由塑膠材料加工成形品之過程,因遷涉的因素極多,可能造成品質不穩定,故必頇檢驗之程序以管制品質。
對於檢驗後之成形品,有時可直接使用,有時為了增加美觀、具備特殊之性質或進一步改變形狀,而必頇實施再加工。
這一些程序都是在成形品成形後再做的處理,統稱為後處理,為塑膠成形品生產的重要步驟。
8.1成形品的檢驗設計及制作模具的目的是要生產塑膠制品。
當模具制作完成經檢驗後,調整好塑膠機各項成形操作條件即可開始生產:通常剛開始生產時,各項條件還未穩定,頇慢慢做修正。
因此成形品並非立即能達到要求,而是經多次檢驗、修正後,條件超於穩定,品質合於標准,才能正式進入生產階段。
但在生產過程中,成形條件仍有可能會變動,而影響成形品的品質,因此,必頇實施各種檢驗,以確保成形品合乎要求。
一般對於成形品的檢驗,包括外觀、尺度精密度、塑料性質等三方面,分別介紹如下:8.1-1外觀檢驗由現操作人員直接以目測方式,詳細觀察成形品的外觀是否有缺陷,這此缺陷包括:充填不足、變形、翹曲、變色、流痕、毛邊、氣泡、表面模糊、層裂、油污、燒焦等。
一旦發現成形品有缺陷,應予以淘汰,並立即檢查各項成形條件與模具。
8.1-2尺度精密度檢驗當成形品之外觀正常,則於去除澆口、澆道等余料後,實施尺度精官度檢驗。
使用的檢驗量具有直尺、游標卡尺、分厘卡、螺紋規、量角器、樣板以及各種量規等。
對於這些量具的基本條件是,量具本身的最小測量精官度,要全於成形品尺度許可差的要求。
表8-1所列為DIN7710塑膠成形品尺度許可差規格。
=================================================================================I=================================================================================表8-1塑膠成形品尺度許可差(a)直接取決於模具的尺度許可差單位:mm=================================================================================I================================================================================= (b)非直接取決於模具的尺度許可差單位:mm=================================================================================I=================================================================================影響成形品尺度精密度的因有:(1)與模具有關的因素:包括模具設計、模具制作精密度、模具材料選用及模具是否磨損等。
模具设计讲义概论第1章

液压压力机
二.曲柄压力机简介
曲柄压力机的结构如图1-1所示。 1.曲柄压力机的基本组成:
床身 工作机构 操作系统 传动系统 能源系统
曲柄 连杆 滑块
工作原理
2.曲柄压力机的分类
(1)按床身结构分
开式压力机:床身在三个方向是敞开的 床身呈C形,如图1-2所示
闭式压力机:床身两侧封闭,如图1-3所示
单点压力机:只有一个连杆,如图1-1所示 (2)按连杆数分 双点压力机:有两个连杆,如图1-4所示
四点压力机:有四个连杆
(3)按滑块行程是否可调
曲轴压力机:行程大,但不可调, 如图1-1所示
偏心压力机:行程小,但可调, 如图1-5所示
单动压力机:只有一个滑块,如图1-1所示 (4)按滑块数目分 双动压力机:有两个滑块,如图1-8所示
汽车制造业中
有60%~70% 的零件是冲压 工艺制成的
在机电及仪器、仪表生产中有60%~70%的零 件采用冷冲压工艺,在电子产品中,冲压件的 数量约占零件总数的85%以上。
§1-2 冷冲压设备—压力机
一、压力机的分类
冷冲压设备中使用最多的是压力机。
压力机
机械压力机
曲柄压力机-最常用 摩擦压力机
三动压力机:用于较复杂件的拉深
(5)按传动方式分 上传动:传动系统置于工作台之上 下传动:传动系统置于工作台之下
可倾式 (6)按工作台结构分 固定式 如图1-9所示
升降式
3. 压力机的主要技术参数 1)标称压力(公称压力):压力机曲柄旋转到离下止点
前某一特定角度(约等于20-30度)时,滑块上所允许 的最大工作压力Fmax,如图1-12所示。 选用压力机时应保证:标称压力>所需的冲压力
塑料模具设计概论

3.中空成型 (吹塑成型) 特点:先注射或挤出管筒形 状的熔融坯料,再放入吹塑模具内吹入空气成型制件。可 成型中空制件和管筒型薄膜,如瓶、桶、球、户壶、箱等。 4.压缩成型(压制成型) 用于成型热固性塑料。 5.压注成型(传递成型) 用于成型形状复杂或带有较 多嵌件的热固性塑料。 6.固相成型 特点:在熔融温度以下成型,主要用于 塑料板材的二次成型加工,如真空成型、压缩空气成型和 压力成型等。
第二节 塑料的加工适应性
塑料的物理状态:玻璃态、高弹态、粘流态 θg-玻璃化温度 θf -粘流温度 θd-热分解温度 1.当 θ< θg时,塑料为坚硬的固体,弹性模量大, 形变值小,变形不可逆,可进行车、铣、刨、削 等机械加工。(脆化温度θx-使用的下限温度) 2.当θg 2. θg <θ< θf 时,塑料为高弹态,弹性模量减小, 形变能力增大,变形可逆,可进行真空成型、压 力成型、压延和弯曲成型。(熔点温度θm) 3.当θf <θf< θd时,塑料为粘流态,弹性模量减到 最小,形变能力更大,变形不可逆,冷却后能永 久保持形变,常进行注射、挤出、吹塑和熔融纺 丝的成型。 4.当θ>θd时,塑料发生热分解。
压延成型(薄膜、硬片、人造革)、浇铸成型(齿轮、叶轮、轴 套)、滚塑成型、泡沫成型。
成型加工的方法的种类很多,但它们不一定都能够适用于各 种塑料。表1列出部分塑料对成型加工方法的适应性。
第二章 塑料成型理论基础 第一节 聚合物的流变学性质
概念: 概念: 研究物质变形与流动的科学称为流变学。 研究内容: 研究内容 聚合物材料在外力作用下产生的应力、应变和应 变速率等力学现象与自身粘度之间的关系。 研究目的:应用流变学理论,正确地选择和确定比较合理的 研究目的 工艺条件,设计合理的注射成型系统和模具结构。 1.牛顿流动规律 牛顿流动规律 回顾流体力学中,液体在圆管中的流动分为层流和紊流两种形 式。用液体的雷诺数Re区分。当Re<2100时,为层流; Re>2100 时,为紊流。 注射成型时,聚合物熔体的雷诺数远小于2100,故将它们的流 动形式视为层流。 牛顿流动:流体处于层流状态时,粘度与切应力(切变速率)无 牛顿流动 关的流体的流动。 非牛顿流动:流体处于层流状态时,粘度与切应力(切变速率) 非牛顿流动 有关的流体的流动。
模具设计概述.doc

一塑胶模具定义人们为满足生产及生活的需要,按一定的要求而制造的生产工具。
模具即生产工具,一般均可重复使用。
工业中常见的有塑胶模、五金冲压模、压铸模、吹塑模、挤塑模等;广义来讲,一些日常生活中的刀模、纸模、石膏模、甚至拍月饼的木板模等都可称为模具。
塑胶模具就是注塑成型生产中使用的模具。
塑胶模具主要是装在塑胶注塑机上啤塑胶产品时使用的,如无特别注明,以下文章中提到的模具均指塑胶模二、必备1、基础知识:三角函数、平面&立体几何、解析几何、工程制图、画法几何、机械基础、五金&化学基础等;2、基础实践经验;3、软件知识:AutoCAD、PRO-E、UG、SilodWorks、CATIA、MasterCAM、CIMATRON IT、MOLDFL OW等;三、塑胶模具结构及分类1)模具的基本结构及相关概念1、模胚即模架:MoldBase。
模胚是整套模具的骨架,所有模具的零部件的制作均需考虑模胚的结构。
模胚的成本一般占整套模具的30%左右,模胚由专门的大型模胚厂制造,已标准化,各模具制造厂只需根据自身的需要向模胚厂定制即可。
模胚分为面板、A板(前模板)、B板(后模板)、C 板(方铁)、底板、顶针面板、顶针底板、司筒、导柱、回针、顶针、撑头、限位钉等。
目前珠三角区域规模较大的模胚厂商有龙记模胚(LKM)、鸿丰模胚、中华模胚等,其中又以LKM名气最大,其模胚广大模具制造厂普遍采用,品质、精度均有保障。
2、模仁又称型腔,即嵌入模胚模板内的成型模芯。
分为前模仁,后模仁,俗称前模(Cavity),后模(C ore)。
为何要在模板内嵌入模仁呢?主要是为节约成本。
因为塑胶对模具的钢材特性有很高的要求,如硬度、耐腐蚀性、耐高温(热变形)等;而模胚的模板则无需太高的要求。
模仁硬度一般为45~65HRC,模胚的模板硬度30~45HRC;用作模仁的钢料每公斤可达RMB 200,而模胚的钢料一般只需RMB20~30元。
模具设计与制造方案概述(doc 8页)

模具设计与制造方案概述(doc 8页)模具设计与制造方案材料:Q235钢材料厚度:1mm零件图一、冲压件工艺性分析工件有冲孔、内孔翻边、落料三个工序。
材料为Q235钢,具有良好的冲压性能,适合冲裁。
工件的尺寸全部为自由公差,可看作IT14级,尺寸精度较低,普通总裁即可满足要求。
二、冲压工序方案的确定工件包括三个基本工序,这里采用级进模生产。
级进模生产只需一副模具,生产效率高,操作方便,工件精度也能满足要求。
三、主要设计计算1.排样方式的确定及其计算.冲孔的大小。
2.工作零件刃口尺寸计算零件采用自由公差因而可取公差值为IT14根据材料及板厚查得冲裁间隙Z min=0.100mm,Zmax=0.140mm.各工作零件的刃口尺寸计算如下:冲孔凸模与凹模尺寸的计算1)计算56mm⨯16mm孔的凸模与凹模刃口尺寸:冲孔时:d T=(d min+ X∆)0-δT d A=(d T+Z min)0+δA查得56mm的∆=0.74 δT=δA=0.185 X∆=0.370尺寸转换为560+0.74得:d T=(56+0.37)0-δT=56.370-0.185mmd A=(56.37+0.100)0+δA=56.470+0.185mm查得12mm的∆=0.43 δT=δA=0.110 X∆=0.220尺寸转换为160+0.43得:d T=(12+0.220)0-δT=12.220-0.110mmd A=(12.22+0.100) 0+δA=12.320+0.110 mm2)计算7mm⨯2mm孔的凸模与凹模尺寸:查得7mm 的∆=0.360 δT=δA=0.090 X∆=0.180 尺寸转换70+0.360得:d T=(7+0.180)0-δT=7.180-0.090mmd A=(7.18+0.100)0+δA=7.28 0+0.090mm查得2mm的∆=0.25 δT=δA=0.060 X∆=0.130尺寸转换为20+0.060得:d T=(2+0.130)0-δT=2.130-0.060mmd A=(2.13+0.100)0+δA=2.230+0.060mm3)计算φ2.5孔的凸模与凹模尺寸:查得φ2.5孔的∆=0.25 δT=+0.008 δA=-0.006 X=0.75尺寸转换为φ2.500.25得:d T=(2.5+0.25⨯0.75)0-δT=2.6880-0.080mmd A=(2.688+0.100)0+δA=2.7880+0.060mm落料凸模与凹模尺寸的计算落时:D A=(D max-X∆)0+δA D T=(D A-Z min)-δT首先判断凸模与凹模的加工方法,根据对零件的分析,易采用配作法加。
- 1、下载文档前请自行甄别文档内容的完整性,平台不提供额外的编辑、内容补充、找答案等附加服务。
- 2、"仅部分预览"的文档,不可在线预览部分如存在完整性等问题,可反馈申请退款(可完整预览的文档不适用该条件!)。
- 3、如文档侵犯您的权益,请联系客服反馈,我们会尽快为您处理(人工客服工作时间:9:00-18:30)。
模具设计概论精编W O R D版IBM system office room 【A0816H-A0912AAAHH-GX8Q8-GNTHHJ8】模具设计概论第一章、冲压加工概述与冲压设备一、什么是冷冲压?冷冲压分为哪两类?答:⑴冷冲压是在常温下利用冲模在压力机上对材料施加压力,使其产生分离或变形,从而获得一定形状、尺寸和性能的零件的加工方法。
⑵冷冲压概括起来可以分为分离工序和变形工序两大类二、什么是分离工序和变形工序?答:分离工序是将冲压件或毛坯沿一定的轮廓相互分离;变形工序是在材料不产生破坏的前提下使毛坯发生塑性变形,形成所需的形状及尺寸的制件。
三、常用的冷冲压设备有哪些?曲柄压力机的工作原理是什么?答:⑴在冷冲压生产中,为了适应不同的冲压工作需要,所采用的设备为各种不同类型的压力机。
压力机的类型很多,按传动方式的不同可以分为机械压力机和液压压力机两大类。
⑵工作原理、详细见课本4—5页。
四、什么是双点压力机?什么是双动压力机?答:⑴按连杆的数目分,可以分为单点、双点和四点压力机。
双点压力机是指有两个连杆的压力机。
⑵按滑块的数目分,可以分为单动压力机、双动压力机三动压力机等,其中有两个滑块的压力为双动压力机。
五、设计模具需要考虑压力机的哪些技术参数?答:(压力机的主要技术参数是反映一台压力机的工艺性能、所能加工的零件的尺寸范围以及生产率等的指标,也是模具设计中选择冲压设备、确定模具结构的重要依据)主要包括:①标称压力(公称压力)②滑块行程③滑块每分钟行程次数④压力机的装模高度⑤压力机工作台面尺寸⑥漏料孔尺寸⑦模柄孔尺寸⑧压力机的电动机功率。
第二章、冲裁工艺一、冲裁的概念?答:使板料分离的冲压工艺称为冲裁。
二、冲裁过程可分为哪几个变形过程?答:①弹性变形过程②塑性变形过程③剪裂阶段。
三、冲裁件的断面有哪几个特征?答:冲裁件的断面有四个特征区:①圆角带:又称榻角,产生在板料不与凸模或凹模相接触的一面,是由于板料受弯曲、拉伸作用而形成的。
材料塑性越好,凸、凹模之间的间隙越大,形成的榻角也就越大。
②光亮带:紧挨着榻角,是由于凸模切入板料,板料被挤入凹模而产生塑性剪切变形所形成的。
材料的塑性越好,凸、凹模之间的间隙越小,光亮带的高度就越高。
③断裂带:紧挨着光亮带,是由冲裁时所产生的裂纹扩张而形成的。
断裂带表面粗糙,并带有4°~6°的斜度。
凸、凹模之间的间隙越大则断裂带高度越大,且斜度也增大。
④毛刺:紧挨着断裂带的边缘,是由于裂纹的产生不是正对着凸模和凹模的刃口而是靠在刃口的侧面。
四、冲裁件的质量包括哪几方面?答:应该保证一定的尺寸精度、良好的断面质量和无明显的毛刺。
五、什么是冲裁间隙?冲裁间隙有什么重要性?答:冲裁间隙是指冲裁凸模和凹模之间的工作部分的尺寸之差。
冲裁间隙是保证合理冲裁过程的最主要的工艺参数,对冲裁件的质量有着决定性的作用。
第三章、冲裁模的结构与设计一、冲裁模的凹、凸尺寸计算的原则有哪些?答:计算原则主要有①落料时,落料件的尺寸是由凹模决定的,因此应以落料凹模为设计准则;冲孔件的尺寸是由凸模决定的,因此应以冲孔凸模为设计基准。
②凸模和凹模应考虑磨损规律。
③凸模和凹模之间应保证有合理间隙。
④凸模和凹模的制造公差应与冲裁件的尺寸相适应。
⑤尺寸计算要考虑模具的设计特点。
二、模具的制造方法有哪几种?答:三、降低冲裁力的措施有哪些?答:降低冲裁力的措施主要有①加热冲裁②斜刃冲裁③阶梯冲裁四、什么是模具的压力中心?答:冲压力合力的作用点称为模具的压力中心。
五、什么是冲裁排样?什么是结构废料?什么是工艺废料?答:冲裁件在条料上的布置方法称为排样。
冲孔所产生的废料即为结构废料,结构废料是由工件的形状所决定的。
条料上的料头、料尾及边缘部分均为工艺废料,工艺废料是由冲压方式与排样方式所决定的。
六、搭边有什么作用?答:搭边的作用有:⑴起补偿条料的剪裁误差、送料步距误差以及补偿由于条料与导板之间有间隙所造成的送料歪斜误差的作用;⑵使凹、凸模刃口双边受力;⑶对于利用搭边拉条料的自动送料模具,搭边使条料有一定的刚度,以保证条料的连续送进。
七、什么是工艺零件?有哪些?答:工艺零件是直接参与完成冲压工艺过程并和坯料直接发生作用。
包括工作零件(直接对毛坯进行加工的成形零件),定位零件(用以确定加工中毛坯正确位置的零件),压料、卸料及出件零件。
八、什么是结构零件?有哪些?答:结构零件是不直接参与完成工艺过程,也不和坯料直接发生作用,只对模具完成工艺过程起保证作用或对模具的功能起完善作用。
包括导向零件(保证上、下模之间的正确相对位置),固定零件(用以承装模具零件或将模具安装固定到压力机上),紧固及其它零件。
九、凹模洞口答:凹模洞口的形式基本上有直壁式、斜壁式以及凸台式三种。
十、冲裁模有几种卸料形式?答:冲裁模的卸料形式主要有刚性卸料、弹性卸料以及废料切刀卸料。
十一、根据导柱的布置将模架分为哪几种?答:根据导柱的布置可以将模架分为后侧导柱模架、中间导柱模架、对角导柱模架以及四导柱模架。
第四章、塑料基础知识一、塑料与树脂的关系?答:塑料的概念是:以树脂为主要成分,以增塑剂、填充剂、润滑剂、着色剂等添加剂为辅助成分,在加工过程中一定温度和压力的作用下能流动成形的高分子有机材料。
树脂的概念是:指受热时通常有转化或熔融范围,转化时受外力作用具有流动性,常温下呈固态或半固态或液态的有机聚合物,它是塑料最基本的,也是最重要的成分。
二、塑料的成分有哪些?各自作用如何呢?答:塑料的成分主要有树脂和添加剂树脂的作用是:决定塑料的类型和基本性能,可以胶粘其它成分材料,赋予塑料可塑性和流动性;添加剂中的⑴填充剂:是塑料的重要的但非必不可少的成分,可以减少树脂用量,降低塑料成本;改善塑料的某些性能,扩大塑料的应用范围。
⑵增塑剂:提高塑性、流动性和柔软性;降低刚性和脆性;改善塑料的工艺性能和使用性能。
⑶主要作用是阻缓材料的变质。
其中包含:①热稳定剂:抑制或防止树脂在加工或使用过程中受热而降解②光稳定剂:阻止树脂在光的作用下降解(塑料变色、力学性能下降等等)③抗氧化剂:延缓或抑制塑料抗氧化速度。
⑷润滑剂:可以防止塑料在成形过程中粘模,减少塑料对模具的摩擦,改善塑料的流动性,提高塑件表面的光泽度。
⑸着色剂:起装饰美观的作用,某些着色剂还能够提高塑料的光稳定性、热稳定性和耐候性。
三、塑料按物理化学性质可以分为几种?答:塑料按物理化学性能可以分为热塑性塑料和热固性塑料两种。
四、热塑性塑料和热固性塑料的主要区别是什么?答:热塑性塑料是指在特定温度范围内能反复加热软化和冷却硬化的塑料,其分子结构是线型或支链型结构;热固性塑料是指在受热和其它条件下能固化成不熔不溶性物质的材料,其分子结构最终为体型结构。
五、合成树脂与天然树脂的区别是什么?答:天然树脂是指由自然界中动植物分泌物所得的无定形有机物,如松香、琥珀、虫胶等;合成树脂是指由简单有机物经化学合成或某些天然产物经化学反应而得到的树脂产物。
六、塑料按性能和用途可以分为几种?答:塑料按性能和用途可以分为通用塑料、工程塑料和特种塑料三类。
七、热塑性塑料的工艺性能有哪些?热固性塑料的工艺性能有哪些?答:热塑性塑料的工艺性能主要有收缩性、流动性、结晶性以及其它工艺性如热敏性、水敏性、吸湿性、应力敏感性和各种热能性。
热固性塑料的工艺性能主要有收缩率和流动性。
第五章、塑料的成型工艺一、塑料的成型工艺主要有哪些?答:塑料的成型工艺主要包括:塑料的成型原理、注射成型工艺以及塑料制品的设计。
二、注射成型工艺过程包括哪几个阶段?答:主要包括加料、塑化、注射、保压、冷却和脱模等步骤。
实质上主要是塑化、流动与冷却定型两大过程。
三、注射成型的工艺参数主要有哪些?答:注射成型的工艺参数主要有:温度、压力和时间。
四、从满足注射成型工艺的角度出发,在设计塑料制品的形状和壁厚等方面时应注意哪些问题?答:设计形状时,应该注意尽量避免侧壁凹槽或制品脱模方向垂直的孔,可避免瓣合分型或侧抽芯等复杂模具结构和使分型面上留下飞边。
设计壁厚时,主要决定于制品的使用条件,但壁厚大小对成型影响很大,过小会导致流动阻力大,冲模难,不能保证强度和刚度;过大会导致浪费原料,增加成本,且增加成型时间,降低生产率,还易出现气泡、缩孔等,壁厚应求均匀,否则会产生内应力。
第六章、塑料注射模具设计一、何为模具的分型面?选择分型面的基本原则主要有哪些?答:模具上用以取出制品及浇注系统凝料的可分离的接触表面称为分型面。
分型面的选择原则是:①分型面应尽量选在制品断面轮廓最大的部位;②因推出机构一般设置在动模一侧,分型面应尽量选在应使制品留在动模内的地方;③保证制件的精度要求;④满足塑件的外观质量要求;⑤便于模具加工制造;⑥减少塑件在合模分型面上的投影面积;⑦排气效果好;⑧对侧向抽芯的影响。
二、按分型面的特征注射模具应分为哪几类?不同模具的动作原理是什么?答:按分型面的特征,注射模具可以分为单分型面注射模具、双分型面注射模具以及活动镶块式注射模具。
热固性模具的动作原理主要是压缩、传递和注射;热塑性模具的动作原理主要是吹塑、气动成型以及注射。
三、塑料注射模具由哪几部分组成?、答:塑料注射模具主要由合成零件、合模导向机构、浇注系统以及定向分型与四、注射模具设计时需要校核哪些注射机的工艺参数?答:需要校核的注射机的工艺参数主要有:①最大注射量的校核;②注射压力的校核;③锁模力的校核及型腔数的校核;④模具闭合高度H和平面尺寸的校核;⑤模具的平面尺寸应小于注射机模板尺寸。
五、普通流道浇注系统的组成是什么?各部分的作用是什么?答:普通流道浇注系统的组成主要包括主流道、分流道、浇口、冷料穴以及排气槽。
*主流道的作用是:连接注射机料筒喷嘴和注射模具的桥梁;熔融塑料进入模具最先经过的地方;主流道的大小影响塑料进入型腔的速度和充型时间。
*分流道的作用是:在压力损失最小的情况下,通过截面积的变化和流向变换,平稳地将来自主流道的熔融塑料以较快的速度送到浇口处冲模,同时分流道内残留的塑料最少,以减少冷料的回收。
*浇口的作用:浇口可以分为限制性浇口和非限制性浇口两种。
非限制性浇口起着引料、进料的作用;限制性浇口一方面通过截面积的突然变化,使塑料熔体产生加速度,提高剪切速率,迅速而均衡地充满型腔;另一方面改善熔体进入型腔的流动特性,调节浇口尺寸,可使多型腔同时充满。
同时起着封闭型腔,防止塑料熔体倒流,并便于浇口凝料与制品分离的作用。
*冷料穴的作用是:具有容纳冷料的作用,还具有在开模时将主流道和分流道的冷凝料钩住,将其保留在动模一侧,便于脱模的功能。
*排溢系统的作用:解决形成气泡、接缝、便面轮廓不清及充填缺料等缺陷;解决气体受压、体积缩小而产生高温会导致塑件局部碳化或烧焦的问题;解决存积的气体由于产生反向压力而降低冲模速度的问题。