潜在失效模式与后果分析报告
整车设计失效模式分析-DFMEA

有毒有害物质 检测
3
座椅VOC超标
2
按 2005/673/EC 有毒有害物质
设计
检测
3
动力系统匹配不 当
5
整车总布置报告
NVH测试
2
噪声大:
传动系统匹配不 当
4
整车总布置报告
NVH测试
4
驾驶员耳旁
噪声不合 格; 车内噪声不
顾客抱怨,引 起驾驶疲劳
6
S
合格;
行驶系统设计不 当
4
车身各总成刚度 设计值不足
1999测定;
S
制动系统设计不 合理
3
设计评审 与参考车型对比
3
制动异响
顾客抱怨制动 有异响
7
S
制动系统设计不 合理
4
设计评审 与参考车型对比
样车动态评价
4
灯光照度不 够
影响行车安 全,违反法规
9
R
灯光照明系统设 计不合理
3
计算校核设计评 审
按 GB 459994附录D测 定;
2
灯光指示和信号 报警系统设计不 3 设计评审
2
设计计算
按GB
2
T6323.6-1994
悬架匹配计算
测定;
3
FMEA日期
造型
车身造型不美观 5
不美观
造型不美观顾 客不满意
6
R
外装饰系统造型 美观
5
造型评审 造型评审
样车评价 2 样车评价 2
跑偏
制动时方向
侧滑
稳定性差 失去转向能力
9
影响乘员安全
S
制动系统泄露
3
设计评审 与参考车型对比 按 GB 12676-
pfmea过程失效模式与后果分析报告

通过深入分析,我们确定了导致这些失效的潜在原因,包 括设备老化、操作规程不完善、员工培训不足、原材料质 量控制不严格以及工艺参数设置不合理等。
对未来工作的建议和展望
改进措施建议
持续改进计划
未来研究方向
基于PFMEA的结果,我们提出了一系 列改进措施,包括更新设备、优化操 作规程、加强员工培训、严格控制原 材料质量以及调整工艺参数等。这些 措施旨在减少失效发生的风险,提高 生产过程的可靠性和稳定性。
为了确保改进措施的有效实施,我们 制定了持续改进计划。该计划包括定 期评估改进效果、监测潜在问题的出 现以及调整改进措施等。通过持续改 进,我们期望能够不断优化生产过程 ,提高产品质量和客户满意度。
在报告的最后,我们提出了一些未来 可能的研究方向。这些方向包括进一 步探索失效模式与潜在原因之间的关 系、研究新的失效分析方法以及开发 更加智能化的失效预测模型等。通过 深入研究,我们期望能够为企业的持 续改进提供更有力的支持。
失效模式
汽车发动机性能下降
后果
影响汽车动力性能,可能导致油耗增加、排放超标
潜在原因
制造过程中材料、工艺、设备等方面的问题
风险评估
高风险,需采取措施进行改进
案例二:电子产品制造过程的PFMEA分析
失效模式
电子元件短路
潜在原因
制造过程中元件组装、焊 接等环节出现问题
后果
产品功能失效,可能引发 安全事故
提前发现和预防问
题
PFMEA是一种预防性的质量工具 ,它通过提前发现和预防潜在的 问题,减少后期修改和返工的成 本。
优化设计和过程
PFMEA分析结果可以为设计和过 程的改进提供指导,帮助企业优 化产品和过程的性能、可靠性和 安全性。
潜在失效模式后果分析FMEA控制程序
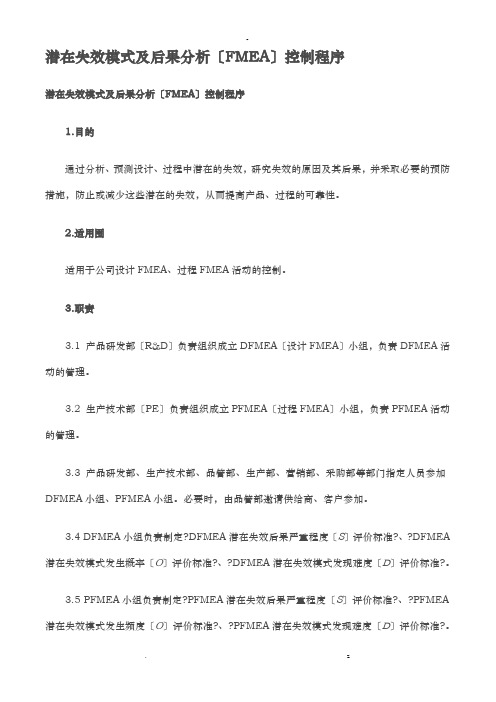
潜在失效模式及后果分析〔FMEA〕控制程序潜在失效模式及后果分析〔FMEA〕控制程序1.目的通过分析、预测设计、过程中潜在的失效,研究失效的原因及其后果,并采取必要的预防措施,防止或减少这些潜在的失效,从而提高产品、过程的可靠性。
2.适用围适用于公司设计FMEA、过程FMEA活动的控制。
3.职责3.1 产品研发部〔R&D〕负责组织成立DFMEA〔设计FMEA〕小组,负责DFMEA活动的管理。
3.2 生产技术部〔PE〕负责组织成立PFMEA〔过程FMEA〕小组,负责PFMEA活动的管理。
3.3 产品研发部、生产技术部、品管部、生产部、营销部、采购部等部门指定人员参加DFMEA小组、PFMEA小组。
必要时,由品管部邀请供给商、客户参加。
3.4 DFMEA小组负责制定?DFMEA潜在失效后果严重程度〔S〕评价标准?、?DFMEA 潜在失效模式发生概率〔O〕评价标准?、?DFMEA潜在失效模式发现难度〔D〕评价标准?。
3.5 PFMEA小组负责制定?PFMEA潜在失效后果严重程度〔S〕评价标准?、?PFMEA 潜在失效模式发生频度〔O〕评价标准?、?PFMEA潜在失效模式发现难度〔D〕评价标准?。
4.工作程序4.1 设计FMEA的开发实施DFMEA实施的时机.1 按APQP的方案进展DFMEA。
.2 在出现以下情况时,DFMEA小组应在产品零件图纸设计之前进展DFMEA活动:① 开发新产品/产品更改;② 产品应用的环境发生变化;③ 材料或零部件发生变化。
DFMEA实施前的准备工作① 产品研发部〔R&D〕牵头成立DFMEA〔设计FMEA〕小组,生产技术部、品管部、生产部、营销部、采购部等部门指定人员参加DFMEA小组,必要时,由品管部邀请供给商、客户参加。
② 在DFMEA活动实施前,DFMEA小组应制定出?DFMEA潜在失效后果严重程度〔S〕评价标准?、?DFMEA潜在失效模式发生概率〔O〕评价标准?、?DFMEA潜在失效模式发现难度〔D〕评价标准?。
DFMEA报告

职责及目
严发
标 完成日期
采取措施和 重 生 生效日期 度 率
D
PRN
SO
LECU固定螺钉选型有
误,振动时松动脱
对LECU固定螺钉进
8 落,导致在LECU壳体 4
行材质及尺寸的测 2 64
中滚动,引起板子短
试验证
路BMU固定螺钉选型有
电池系统内
误,振动时松动脱
对BMU固定螺钉进行
电池管理 的高压器件 8 落,导致在BMU壳体 4
2
报警,输入输出
BMU软硬件
控制
版本号读取 8
数据存储错误 2
失败
故障检测错 误
8
故障触发条件判断错 误
2
BMS故障
预警与处 高压互锁功
理
能失效
8
高压互锁采样或控制 电路故障
2
碰撞开关功 能失效
8
碰撞开关检测电路故 障
2
BMS诊断 诊断功能失
功能
效
8
诊断代码错误 2
备注: 在下列三种失效条件下,须制定相应的改善措施: (1)最优原则:S≥9时,必须分析设计控制或建议措施 (2) 严重度S≤8,风险顺序数RPN≥80时(或依顾客需求) (3)关键特性发生失效时。
2 32
拉力试验
2 64
CAN通讯功 8 通讯接插件端子松脱 4
能失效 8
通讯程序bug
2
8 继电器控制电路故障 2 放电回路继
电器失效 管理功能
下降
8
放电启动或停止条件 错误
2
检测电池状态, 计量SOC,整车 通信,电滥用保 护,故障识别及
8 继电器控制电路故障 2 慢充回路继
PFMEA过程失效模式及后果分析报告

科技股份有限公司作业文件文件编号:XXXX-XXXX.XX 版号:A/0(PFMEA)过程失效模式及后果分析作业指导书批准:审核:编制:受控状态:分发号:2016年01月15日发布2016年01月15日实施过程潜在失效模式及后果分析作业指导书(PFMEA)XXXX-XXXX.XX1目的过程潜在失效模式及后果分析,简称PFMEA。
是一种信赖度分析的工具,可以描述为一组系统化的活动,是对确定产品/过程必须做哪些事情才能使顾客满意这一过程的补充。
其目的是:(a)并评价产品/过程中的潜在失效以及该失效的后果;(b)确定能够消除或减少潜在失效发生机会的措施;(c)将全部过程形成文件。
2 范围:适用于公司用于零组件的所有新产品/过程的样品试制和批量生产。
适用于过程设计的风险性及后果的分析;适用于过程重复,周期性永不间断的改进分析。
3 术语和定义:1)PFMEA:指Process Failure Mode and Effects Analysis(过程失效模式及后果分析)的英文简称。
由负责制造/装配的工程师/小组主要采用的一种分析技术,用以最大限度地保证各种潜在的失效模式及其相关的起因/机理已得到充分的考虑和论述。
2)失效:在规定条件下(环境、操作、时间),不能完成既定功能或产品参数值和不能维持在规定的上下限之间,以及在工作范围内导致零组件的破裂卡死等损坏现象。
3)严重度(S):指一给定失效模式最严重的影响后果的级别,是单一的PFMEA范围内的相对定级结果。
严重度数值的降低只有通过设计更改或重新设计才能够实现。
4)频度(O):指某一特定的起因/机理发生的可能发生,描述出现的可能性的级别数具有相对意义,但不是绝对的。
5)探测度(D):指在零部件离开制造工序或装配之前,利用第二种现行过程控制方法找出失效起因/机理过程缺陷或后序发生的失效模式的可能性的评价指标;或者用第三种过程控制方法找出后序发生的失效模式的可能性的评价指标。
DFMEA失效模式分析报告

度
O
现行控制
探
测
度
D
RPN
建议
方法
责任
及目
的完
毕日
期
方法成果
防止
探测
采用的方法
S
O
D
RP
N
PCBA
EPON各项
指标合客
户规定
陶瓷电容(C1 C23C24C60源自C46..)影响产品性能、寿命
1
1
1.元器件一致性局限性 2 器件破损
2
1.元件降额使用,最小确保元件使用降额 90%2.规定全部器件严格测试
2
6
无
光模块
(U17)
影响产品性能
3
3
2
零件承认产品试作产品验证
3
54
无
LED灯(LED1-LDE5)
影响产品性能
2
3
1
零件承认产品试作产品验证
3
18
无
PCBA
EPON 各项指标合客户规定
FLASH(U30)
影响产品性能
2
1
1.元器件
一致性局
限性 2.器
件破损
2
1.元件降额使用,最小确保元件使用降额 90%2.规定全部器件严格测试
设计失效模式分析
DESIGNFMEA
产品名称:
NAME:
日期:
DATE:
客户产品型号:
CUSTOMERTYPENO:
批准
Approvedby
审核
Checkedby
拟 制
Madeby
产品EP401M潜在失效模式及后果分析
(设计FMEA)
子系统
功效规定
【精编范文】fmea案例-范文模板 (6页)

本文部分内容来自网络整理,本司不为其真实性负责,如有异议或侵权请及时联系,本司将立即删除!== 本文为word格式,下载后可方便编辑和修改! ==fmea案例篇一:FMEA经典案例潜在失效模式及后果分析 FMEA编号: PFMEA-S02-76(过程FMEA)页码: 1/11项目名称:SPARK后簧过程责任:汽弹分厂编制人:蔡永芳车型年/车辆类型:SPARK 关键日期: FMEA日期(原始):10/3/20 修订:10/4/10 主要参加人:篇二:FMEA案例潜在失效模式及后果分析 FMEA编号: PFMEA-S02-76(过程FMEA)页码: 1/11项目名称:SPARK后簧过程责任:汽弹分厂编制人:蔡永芳车型年/车辆类型:SPARK 关键日期: FMEA日期(原始):04/3/20 修订:04/4/10 主要参加人:篇三:手持产品FMEA分析案例手持产品FMEA分析案例FMEA实际上意味着是事件发生之前的行为,并非事后补救。
因此要想取得最佳的效果,应该在工艺失效模式在产品中出现之前完成。
产品开发的5个阶段包括:计划和界定、设计和开发、工艺设计、预生产、大批量生产。
作为一家主要的EMS提供商,Flextronics International已经在生产工艺计划和控制中使用了FMEA管理,在产品的早期引入FMEA管理对于生产高质量的产品,记录并不断改善工艺非常关键。
对于该公司多数客户,在完全确定设计和生产工艺后,产品即被转移到生产中心,这其中所使用的即是FMEA管理模式。
在该新产品介绍(NPI)发布会举行之后,即可成立一个FMEA团队,包括生产总监、工艺工程师、产品工程师、测试工程师、质量工程师、材料采购员以及项目经理,质量工程师领导该团队。
FMEA首次会议的目标是加强初始生产工艺MPI (Manufacturing Process Instruction)和测试工艺TPI(Test Process Instruction)中的质量控制点同时团队也对产品有更深入的了解,一般首次会议期间和之后的主要任务包括:1.工艺和生产工程师一步一步地介绍工艺流程图,每一步的工艺功能和要求都需要界定。
注塑件 PFMEA过程潜在失效模式及后果分析

过程潜在失效模式及后果分析(PFMEA)产品型号: WX文件编号:版本编号:发布日期:客户名称: 项目名称: 产品料号: PFMEA 编号: 模具编号: 过程责任:关键日期:PFMEA 版本: 小组成员: 修订日期:工序号功能 步骤要求潜在失效 模式潜在失效后果严重度S特性符号失效的潜在 要因发生率O现有设计控制预期现有设计控制探测探测率DRPN建议措施目标完成日期措施结果采取 措施 S O D RPN05 来料检验符合ROHS 要求材料不符合ROHS 违反法律法规9▽供应商未做相应管控2 要求供应商对材质进行禁用合规检查供应商提供报告5 90要求供应商每年一次安排第三方测试并提交测试报告并建立《原材料合规报告管理台账》 2018/12/11供应商SGS 检测报告每年1次并登记《原材料合规报告管理台账》 9 2 4 72未向供应商要求提供禁用物质报告2 要求供应商对材质进行禁用合规检查供应商提供报告5 90UL 阻燃性能合规 原料不符合UL 阻燃要求 客户投诉索赔9▽ 未向供应商要求提供UL合规检测报告2 要求供应商提供UL合规检测报告供应商提供UL合规检测报告5 90建立《原材料合规报告管理台账》并进行2018/12/11 建立《原材料合规报告管理台账》并进行登记9 2 4 72来料规格符合图纸要求 来料规格不符合图纸要求 原材料不能使用 7 供应商送错货 2采购订单明确要求来料检验 4 56材料外观 合格 料粒色泽不均匀,有杂质 原材料不能使用7.供应商来料不良2 进料检验规范中明确定义来料标准 来料检验 4 56来料嵌件尺寸合格尺寸超差嵌件不能装入模具7 嵌件来料不良 2识别嵌件重要尺寸来料检验 4 56顾客投诉7 嵌件来料不良 2识别嵌件重要尺寸来料检验 4 56客户名称: 项目名称: 产品料号: PFMEA 编号: 模具编号: 过程责任:关键日期:PFMEA 版本: 小组成员: 修订日期:工序号功能 步骤要求潜在失效 模式潜在失效后果严重度S 特性符号失效的潜在 要因发生率O现有设计控制预期现有设计控制探测探测率D RPN建议措施目标完成日期措施结果采取 措施S O D RPN10 原料入库有检验合格标签,保证合格品入库 无检验合格 标签,无法辨别是否合格 使用不合格原料生产,使产品报废8原料未检验2 无合格标签,库管员不予办理入库 入库时库管员目视核查348 7 检验后 未贴标签3 无合格标签,库管员不予办理入库入库时库管员目视核查3 63批次清晰无批次标记或标记模糊难辨 无法执行先进先出,原料保质期存在风险6来料批次标记磨损脱落3来料批次登记备查 入库时库管员目视核查35415 生产领料 领用正确材质、牌号物料领料材质或牌号错误无法生产,影响功能和交期 7◇仓库发料错误2 仓库按单发料 受领双方核对456领料单填写错误 2领料单严格按BOM填写生产核料20拌料拌料时间 色纹 客户投诉 7 拌料时间不足2作业指导书中明确时间要求拌料员填写《拌料记录》巡检确认 4 56色粉配比正确色差外观不良 顾客投诉 7 色粉配比错误 3 作业指导书中明确配比要求 拌料员填写《拌料记录》 484 巡检核对《拌料记录》2018/11/12 巡检核对《拌料记录》并签字 7 3 363色粉添加正确且拌料机内清洁无异物颜色不良产品报废8 色粉颜色错误 2作业指导书中明确色粉规格 拌料员填写《拌料记录》348顾客抱怨 投诉7拌料机内有不符合要求物料或色粉残留3拌料前检查料桶拌料员检查并填写《拌料记录》3 63客户名称: 项目名称: 产品料号: PFMEA编号: 模具编号: 过程责任: 关键日期: PFMEA版本: 小组成员: 修订日期:工序号 功能步骤要求潜在失效模式潜在失效后果严重度S特性符号失效的潜在要因发生率O现有设计控制预期现有设计控制探测探测率DRPN 建议措施目标完成日期措施结果采取措施S O D RPN25 烘料 烘料时间、温度等设定正确原料结块无法成型影响效率5烘料时间过长31.作业指导书明确烘料时长及烘料温度2.烘料员自检并填写《烘料记录表》1.烘料员自检;2.巡检员巡检。
产品潜在失效模式及后果分析

产品潜在失效模式及后果分析目录1. 产品潜在失效模式及后果分析概述 (2)1.1 研究目的 (3)1.2 研究方法 (4)1.3 研究范围 (5)2. 失效模式分类及描述 (7)2.1 设计失效模式 (8)2.1.1 设计缺陷 (9)2.1.2 设计不合理 (10)2.1.3 设计错误 (11)2.2 制造失效模式 (12)2.2.1 材料失效 (13)2.2.2 工艺失效 (14)2.2.3 装配失效 (16)2.3 使用失效模式 (18)2.3.1 操作不当 (19)2.3.2 维护不当 (20)2.3.3 环境因素影响 (21)3. 潜在失效模式分析方法 (22)3.1 FMEA(失效模式及后果分析)方法 (23)3.1.1 定义和目的 (25)3.1.2 步骤和流程 (26)3.1.3 结果和改进措施 (27)3.2 CBET(控制基于工程的方法)方法 (28)3.2.1 定义和目的 (29)3.2.2 步骤和流程 (30)3.2.3 结果和改进措施 (31)4. 具体案例分析 (32)4.1 案例一 (32)4.2 案例二 (33)4.3 案例三 (34)5. 结果与讨论 (35)5.1 FMEA结果报告示例 (36)5.2 CBET结果报告示例 (38)5.3 结果讨论与改进建议 (38)1. 产品潜在失效模式及后果分析概述产品潜在失效模式及后果分析(PFMEA)是一种分析工具,用于识别产品在设计、制造和生命周期各个阶段的潜在失效模式。
它旨在预测和预防潜在的产品失效,以及评估和减少产品对用户造成的不利后果。
本文档概述了如何实施产品潜在失效模式及后果分析的过程和方法,旨在提高产品质量和安全性。
产品潜在失效模式及后果分析是质量管理和风险管理的一种技术,用于评估产品或过程可能发生的失败以及这种失败可能导致的后果。
PFMEA可以帮助识别产品设计中的潜在问题,以及制造过程中的潜在缺陷,从而提高产品的可靠性、安全性和性能。
FMEA
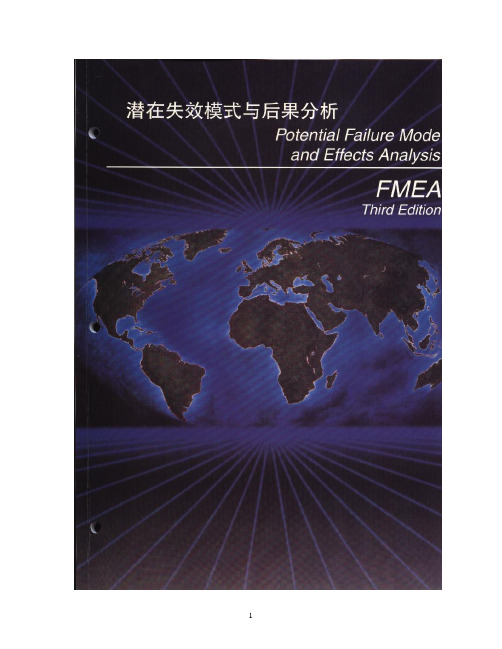
潜在失效模式和后果分析(FMEA)参考手册本文件等效于SAE J—1739技术内容。
实施QS-9000的供方公司应该采用潜在失效模式及后果分析(FMEA)第一版1993年2月出版第二版1995年2月出版第三版2001年7月出版前言第一版及第二版本参考手册及报告格式是由戴姆勒克莱斯勒、福特和通用汽车公司的失效模式及后果分析(FMEA) 工作组编写的。
这项工作是在美国质量控制协会(ASQC) 汽车部门和汽车工业行动集团(AIAG) 主持下进行的。
ASQC/AIAG授权将戴姆勒克莱斯勒、福特和通用汽车公司在其各自的供方质量系统中应用的参考手册、程序、报告格式和技术术语进行标准化处理。
因此,供应商在其设计/生产过程中应用FMEA技术时,应该采用经戴姆勒克莱斯勒、福特和通用汽车公司批准和认可的本手册及报告格式。
过去,戴姆勒克莱斯勒、福特和通用汽车公司各有指南和格式来确保供供方FMEA的符合性。
这些指南和格式的差异导致了对供供方资源的额外要求。
为了改善这种状况,戴姆勒克莱斯勒、福特和通用汽车公司同意编写这本手册,并通过AIAG发行。
负责手册编写的工作组由福特汽车公司的George Baumgartner领导。
本手册提供了准备FMEA的总体指南,并没有给出如何完成每一FMEA项目的具体说明,这些具体工作应由每一FMEA小组来完成。
本手册也并非是综合性的FMEA的参考资料或培训教材。
虽然这些指南意在涵盖所有在设计阶段或过程分析中通常发生的情况,但还是不能避免一些问题的出现。
这些问题应直接向顾客的供方质量保证部门(SQA)反映。
如果不知如何与有关SQA 部门联系,则顾客的采购部的采购人员可提供帮助。
特别工作组衷心感谢戴姆勒克莱斯勒汽车公司副总裁Thomas T.Stallkamp、福特汽车公司副总裁Norman F.Ehlers和通用汽车公司副总裁J.Ignasio Lopez de Arriortua的领导和参与;感谢AIAG在本手册的开发、出版和发行中所提供的帮助。
冲压件 PFMEA潜在失效模式及后果分析
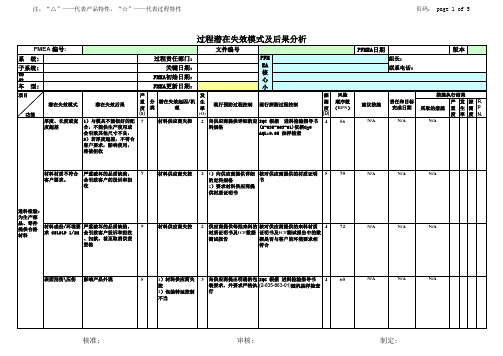
96
N/A
N/A
6
2)模具冲头磨损 3)模具设计制作 、错误 4)模具冲头崩断
4
2)模具保养、维修及 记录 3)按制程作业指导书
不良 2.IPQC根据制程作业指导书 (2-635-863-01)首检、制程 每小时巡检一次
指导生产
3.统计技术(SPC)Xˉ-R管制
4
96
N/A
N/A
4)模具验收及判定标 图( CPK≥1.33 )
准作业指导书
影响产品外观
5
1.产品碰撞刮伤 4
1.员工自检是否压伤不良
4
80
N/A
N/A
2.模具边角锋 利,货品取放时
4
按制程作业指导书指导 2.IPQC根据制程作业指导书
生产
(2-635-863-01)首检、制程每
4
80
N/A
N/A
影响产品外观及组装功 6 能
划 1.花模具跳废料
2. 模具凹凸不平 或生锈
72
材质证明书及ICP数据 证明书及ICP测试报告中的数
测试报告
据是否与客户的环境要求相
N/A
N/A
N/A
资格
符合
表面刮伤\应商失 3 向供应商提出明确的包 IQC 根据 进料检验指导书 4
60
N/A
N/A
N/A
控
装要求,并要求严格执 (2-635-863-01)随机抽样检查
小
组长: 联系电话:
潜在失效后果
严
发
重 分 潜在失效起因/机 生
度类
理
率
(s)
(O)
现行预防过程控制 现行探测过程控制
探 风险 测 顺序数 度 (RPN) (D)
冲压件 PFMEA潜在失效模式及后果分析
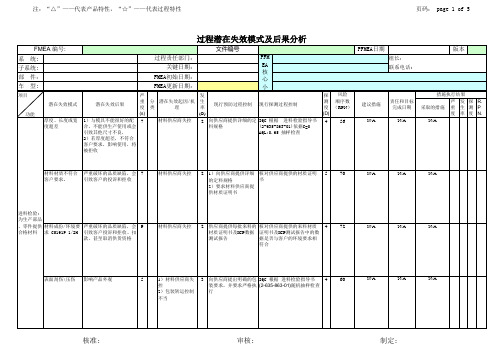
页码: page 5 of 5
FMEA 编号: 系 统: 子系统: 部 件: 车 型:
项目
潜在失效模式
潜在失效后果
功能
表面划花
外观不良,客户投诉
过程潜在失效模式及后果分析
文件编号
过程责任部门:
关键日期:
FMEA初始日期:
FMEA更新日期:
严
发
重 分 潜在失效起因/机 生
度类
理
率
现行预防过程控制
(s)
84
96
影响产品外观及使用性能 6 和使用寿命
6
1.天气潮湿,产 品受潮
2.制程工序间没 喷防锈油或防锈 油不足
3 按制程作业指导书生产
4 按制程作业指导书生产
4 72 4 96
PFMEA日期 组长: 联系电话:
建议措施
责任和目标 完成日期
N/A
N/A
N/A
N/A
N/A
N/A
N/A
N/A
N/A
N/A
外形,从坯
料中分离出
零件或毛坯
并折成不同
几何形状的
五金零件 刮伤
压伤
潜在失效后果 1)可能对使用者造成伤 害 2)导致装配不良
装配不良
文件编号
过程责任部门:
关键日期:
FMEA初始日期:
FMEA更新日期:
严
发
重 分 潜在失效起因/机 生
度类
理
率
现行预防过程控制
(s)
(O)
6
1.模具磨损、冲 4 1)模具保养、维修及
2)包装转运控制
行
不当
核准:
审核:
制定:
注:“△”——代表产品特性,“☆”——代表过程特性
产品潜在失效模式及后果分析(PFEMA)--报告模板

5
90
第 5 页,共 228 页
潜在失效模式及后果分析
GLP1007 ◎首次提交 ○OTS提交更新 ○PPAP提交更新 ○生产更新
版本号:5
○DFMEA ◎PFMEA
供应商代码/名称 100036
编号:
零件号码:01727609
零件名称:GPS主机-MP5
核心小组:PE-毛积钧、唐庆姚、廖正江 、黄业旺 SQE - 吴冲 ,ME - 郭业亮 ,新进-梁 小华,叶振超 PM -温闻,田梦棠
潜在失效模式及后果分析
GLP1007 ◎首次提交 ○OTS提交更新 ○PPAP提交更新 ○生产更新
版本号:5
○DFMEA ◎PFMEA
供应商代码/名称 100036
编号:
零件号码:01727609
零件名称:GPS主机-MP5
核心小组:PE-毛积钧、唐庆姚、廖正江 、黄业旺 SQE - 吴冲 ,ME - 郭业亮 ,新进-梁 小华,叶振超 PM -温闻,田梦棠
编制人:毛积钧
编制日期:2014-04-15
设计项目或过程功 能要求
潜在失效模式
失效的潜在后果
S
特性分 类
失效的潜在起因
○
现有设计或过程控制
D RPN
二维条形码贴装
条形码纸翘起或是中间 凸起
外观不良
3
条形码纸贴装完后没 有用手抹平贴纸
3
条形码纸贴装完用手指将胶 纸抹平贴紧.
8
72
Z刮浆
拉尖、锡孔、短路、少 丝印不良,回流焊接后产生
设计项目或过程功 能要求
潜在失效模式
失效的潜在后果
S
特性分 类
失效的潜在起因
○
现有设计或过程控制
潜在失效模式及后果分析PFMEA

Part name:Proces TechnicalPrepared By:Approval By:零件名称:过程责技术部编制:批准:Part number:KeyDateFMEA Date(Orig):FMEA Date(Rev.):Rev.A/0零件号:关键日FMEA 日期(编制):FMEA 日期(修订):版本:A/0Core Team:general manager :主要参加人:总经理:, 技术部: , 销preservation溶解,保温Part name:Proces TechnicalPrepared By:Approval By:零件名称:过程责技术部编制:批准:Part number:KeyDateFMEA Date(Orig):FMEA Date(Rev.):Rev.A/0零件号:关键日FMEA 日期(编制):FMEA 日期(修订):版本:A/0Core Team:general manager :主要参加人:总经理:, 技术部: , 销Part name:Proces TechnicalPrepared By:Approval By:零件名称:过程责技术部编制:批准:Part number:KeyDateFMEA Date(Orig):FMEA Date(Rev.):Rev.A/0零件号:关键日FMEA 日期(编制):FMEA 日期(修订):版本:A/0Core Team:general manager :主要参加人:总经理:, 技术部: , 销Part name:Proces TechnicalPrepared By:Approval By:零件名称:过程责技术部编制:批准:Part number:KeyDateFMEA Date(Orig):FMEA Date(Rev.):Rev.A/0零件号:关键日FMEA 日期(编制):FMEA 日期(修订):版本:A/0Core Team:general manager :主要参加人:总经理:, 技术部: , 销Part name:Proces TechnicalPrepared By:Approval By:零件名称:过程责技术部编制:批准:Part number:KeyDateFMEA Date(Orig):FMEA Date(Rev.):Rev.A/0零件号:关键日FMEA 日期(编制):FMEA 日期(修订):版本:A/0Core Team:general manager :主要参加人:总经理:, 技术部: , 销Part name:Proces TechnicalPrepared By:Approval By:零件名称:过程责技术部编制:批准:Part number:KeyDateFMEA Date(Orig):FMEA Date(Rev.):Rev.A/0零件号:关键日FMEA 日期(编制):FMEA 日期(修订):版本:A/0Core Team:general manager :主要参加人:总经理:, 技术部: , 销。
FEMA过程失效模式及后过分析报告
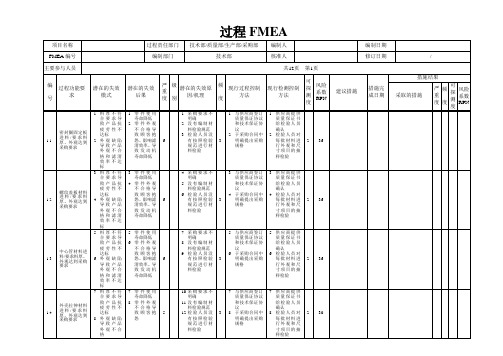
密封固定板整形/要求尺寸准确、外观无毛刺、破裂等现象
模具损坏导致尺寸变差超标
外观毛刺过大
、破裂
7.零件寿命降低
8.滤清效率降低,影响发动机寿命
9.顾客不满意\退货
6
模具损坏
首件检验没有执行
设备故障
模具定期保养,每批产品末件随模具入库以确保模具在闲置期间没有发生变化
实施设备二级保养制度,定期由员工和设备管理人员对设备进行点检和保养
15.检验人员对每批材料进行外观和尺寸项目的抽样检验
2
24
2
材料搬运储存/要求材料储存防护得当,不生锈变质、破裂受潮
1.材料变质导致疲劳性能不符合要求
2.生锈、破裂等导致产品滤清效率降低
1.零件寿命降低
2.滤清效率降低,影响发动机寿命
3.顾客不满意\退货
6
1.材料存放没有防护措施
2.仓库湿度过大
3.材料堆放高度过高
7
!
攻丝刀具选择错误
定位不准
夹紧松动
攻丝刀磨损过度
设备故障
3
攻丝刀标识清楚
上道加工工序保证定位和夹紧
定期更换攻丝刀实施设备二级保养制度,定期由员工和设备管理人员对设备进行点检和保养
编制产品加工工艺卡,指导员工操作和检验
首件和末件由员工和检验人员确认
员工每小时对产品外观进行检验
检验人员对重要尺寸进行每小时一次的巡检
4.于采购合同中明确提出采购规格
10.检验人员对每批材料进行外观和尺寸项目的抽样检验
2
36
1.7
弹簧进料/要求材料尺寸、外观符合采购要求
5.弹簧尺寸不合格导致产品可装配性降低
6.外观污脏导致产品滤清效率不达标
潜在失效模式分析PFMEA

对模具作模流分析,选择合适位置、 3 形状、大小的浇口,使结合线位置满 5
足要求
3
由低到高逐步调整注射压力,得到合 适值
5
C 顶出受力不平衡
3
增加顶杆数目或加大顶出面积,并确 保其均匀分布、受力平衡
5
C 注塑压力过大
3
由小到大调整,使得到一适合的注塑 压力值
5
C 保压压力过大
3
由低到高逐步调整保压,得到合适的 保压值
(ABS电镀级)
原材料性能不能满足 要求
产品性能不能满足
7
禁用/限用物质超标 客户投诉,产品报废 7
燃烧性能﹥80mm/min 车易燃烧
8
10.3
验收方头螺栓 、纸箱、气泡
尺寸超差
影响装配
6
袋
C
不符合原材料采购技术 要求
2
每批1次1袋目视检查原料实物 (比对样料)
6 72
无
C
不符合原材料采购技术 要求
5
C
注塑时间过长
4
由低到高的调整注塑时间,以得到稳 定合适的注射时间后锁定工艺
4
第 3 页,共 10 页
操作人员 100%检 108 查,巡检2 小时一次 进行抽查
操作人员 100%检 108 查,巡检2 小时一次 进行抽查
90
无
锁定生产样 108 件成型工艺
参数
操作人员 72 100%检
查,巡检2 操作人员 108 100%检 查操,作巡人检员2 108 100%检 查操,作巡人检员2 108 100%检 查操,作巡人检员2 108 100%检 查,巡检2 小时一次
4
4
7 外观不合格,客户不满 意
潜在失效模式与后果分析报告程序
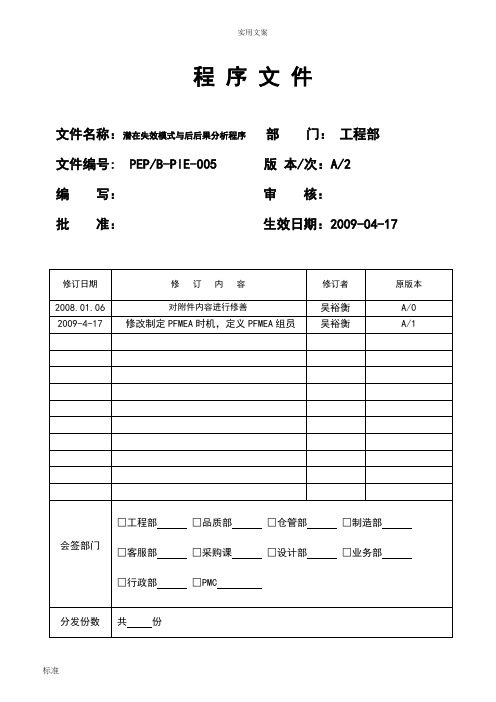
修订者
吴裕衡 吴裕衡
原版本
A/0 A/1
□工程部 会签部门 □客服部
□行政部
□品质部 □采购课 □PMC
分发份数 共 份
□仓管部 □设计部
□制造部 □业务部
标准
XX 光电科技有限公司
文件别 文件名称
程序文件
制订日期 2007-08-15 版本/次 A/1
潜在失效模式与后果分析程序 文件编号 PEP/B-PIE-005 页数
潜在失效模式与后果分析程序 文件编号 PEP/B-PIE-005 页数
8-8
中等 2. 产品的某些舒适/方便项目无法使用。
6
3. 客户不满意。
1. 产品(或系统)可以运行。
低
2. 产品的某些舒适/方便性项目性能下降。
5
3. 客户有些不满意。
1. 外观与组装完工/运转与振动异音项目无法配合一致。
极低
4
2. 多数(75%以上)客户能发觉缺陷
1. 外观与组装完工/运转与振动异音项目无法配合一致。
4. 客户有些不满意。
1. 生产线极轻微中断。
低
2. 全部产品必须经筛选且部分必须重修。
3. 客户感觉不舒适。
1. 生产线极轻微中断。
极低
2. 全部产品须经过筛选且部分必须重修。 3. 外观与组装完工/运转与振动异音项目无法配合一致。
4. 多数(75%以上)客户户能发觉缺陷。
1. 生产线极轻微中断。
控制有很少的机 会能探测出
X 只通过双重目测来实现控制
7
小
控制可能能探测 出
X
X
用制图的方法,如 实现控制。
SPC(统计过程控制)来
6
中等
DFMEA 座椅泡绵 潜在失效与后果分析

xxx-xx-xx 汽车 座椅面料 系统 座椅 泡绵 核心小组: 项目 子系统 零组件:坐垫、靠背 xxx车 设计责任: 关键日期: xx部 -xx-xx 编制: FMEA日期(编制): 探 风险 建议 测 顺序 数 措施 度 R.P.N D 每批次首 3 90 改善工艺 件检查 现行探测 设计控制 自测 5 180 甲醛含 量要求≤ 300mm/k g 供应商改 善工艺 供应商改 善工艺 供应商改 善工艺 生产管控 责任和 目标完 采取的 成日期 措施 质保部 措施执行结果 严 发 探 R.P.N 重 生 测 度 率 度 同建议 2 5 2 20 措施 依照检 测报告 变更标 准 同建议 措施 同建议 措施 同建议 措施 同建议 措施 依照检 测报告 变更材 质 9 2 3 54 FMEA编号: 001 污染 燃烧性 (mm/min)
大多数顾客感 觉有缺陷 50%顾客感觉 有缺陷 50%顾客感觉 有缺陷 大多数顾客感 觉有缺陷 不符合政府的 法规
4 3 3 4 9
○ 影响外观,乘坐体 验不舒服 ○ 影响外观,乘坐体 验不舒服 ○ 影响外观,乘坐体 验不舒服 ○ 影响外观,乘坐体 验不舒服 ● 泡沫阻燃未能达标
车型年度/车辆类型:
严 重 潜在失效模 潜在失 效后果 式 度 S 功能
色泽/色差
顾客不满意
6
气味 1.增加乘 坐舒适 感; 2.保护车 内零部 件; 3.保护乘 客免受划 伤等。
不符合政府的 9 法规
发 生 潜在失效起因/机理 现行预防设计控制 率 O ☆ 制作工艺管控,材 5 首次供货提供第三方 料色牢度要求低(染 检验 料的热稳定性差) ● 甲醛标准偏低 4 首次供货提供第三方 检验
6 6 5 5 4
DFMEA失效模式分析报告-范例

电感(L21
L3 L151)
影响产品性能
4
1
2
零件认可
产品试作
产品验证
2
16
无
电源按键
(S3)
影响产品性能
3
1
1
零件认可
产品试作
产品验证
2
6
无
光模块
(U17)
影响产品性能
3
3
2
零件认可
产品试作
产品验证
3
54
无
LED灯
(LED1-LDE
5)
影响产品性能
2
3
1
零件认可
产品试作
产品验证
3
18
无
PCBA
EPON各项
产品试作
产品验证
3
12
无
电源接口
(J5)
影响产品组装
2
1
1
零件认可
产品试作
产品验证
3
6
无
变压器
(T2)
影响产品性能
3
1
2
零件认可
产品试结构器件
满足外观
及结构要
求
下壳
影响外观及安装
2
1
安装及搬
运过程中
划伤
1
注意操作规
范
零件认可
产品试作
产品验证
3
6
无
上盖
影响外观及安装
2
1
1
零件认可
产品试作
产品验证
3
6
无
产品EP401M潜在失效模式及后果分析
(设计
子系统
功能要求
潜在失效 模式
- 1、下载文档前请自行甄别文档内容的完整性,平台不提供额外的编辑、内容补充、找答案等附加服务。
- 2、"仅部分预览"的文档,不可在线预览部分如存在完整性等问题,可反馈申请退款(可完整预览的文档不适用该条件!)。
- 3、如文档侵犯您的权益,请联系客服反馈,我们会尽快为您处理(人工客服工作时间:9:00-18:30)。
FMEAPotential Failure Mode and Effects Analysis潜在失效模式及后果分析何谓FMEA⏹FMEA是一组系统化的活动,其目的是:⏹发现、评价产品/过程中潜在的失效及其后果。
⏹找到能够避免或减少这些潜在失效发生的措施。
⏹书面总结上述过程。
⏹为确保客户满意,这是对设计过程的完善。
FMEA发展历史⏹虽然许多工程技术人员早已在他们的设计或制造过程中应用了FMEA这一分析方法。
但首次正式应用FMEA技术则是在六十年代中期航天工业的一项革新。
FMEA的实施❖由于不断追求产品质量是一个企业不可推卸的责任,所以应用FMEA技术来识别并消除潜在隐患有着举足轻重的作用。
对车辆回收的研究结果表明,全面实施FMEA能够避免许多事件的发生。
❖虽然FMEA的准备工作中,每项职责都必须明确到个人,但是要完成FMEA还得依靠集体协作,必须综合每个人的智能。
例如,需要有设计、制造、装配、售后服务、质量及可靠性等各方面的专业人才。
❖及时性是成功实施FMEA的最重要因素之一,它是一个“事前的行为”,而不是“事后的行为”,为达到最佳效益,FMEA必须在设计或过程失效模式被无意纳入设计产品之前进行。
❖事前花时间很好地进行综合的FMEA分析,能够容易、低成本地对产品或过程进行修改,从而减轻事后修改的危机。
❖FMEA能够减少或消除因修改而带来更大损失的机会。
❖适当的应用FMEA是一个相互作用的过程,永无止境。
DFMEA(设计FMEA)简介⏹设计潜在FMEA是由“设计主管工程师/小组”早期采用的一种分析技术,用来在最大范围内保证已充份的考虑到并指明各种潜在失效模式及与其相关的起因/机理。
⏹应评估最后的产品以及每个与之相关的系统、子系统和零部件。
⏹FMEA以其最严密的形式总结了设计一个零部件、子系统或系统时,一个工程师和设计组的设计思想(其中包括,根据以往的经验和教训对一些环节的分析)。
⏹这种系统化的方法与一个工程师在任何设计过程中正常经历的思维过程是一致的,并使之规范化、文件化。
⏹在设计阶段使用FMEA时,能够用以下方法降低产品的失效风险⏹有助于对设计要求的评估及对设计方案的相互权衡。
⏹有助于对制造和装配要求的最初设计。
⏹提高在设计/开发过程中已考虑潜在失效模式及其对系统和车辆运行影响的(概率)可能性。
⏹对制定全面、有效的设计试验计划和开发项目,提供更多的信息。
⏹根据潜在失效模式对“顾客”的影响,对其进行排序列表,进而建立一套改进设计和开发试验的优先控制系统。
⏹为推荐和跟踪降低风险的措施提供一个公开的讨论形式。
⏹为将来分析研究现场情况,评价设计的更改及开发更先进的设计,提供参考。
集体的努力❖在最初的设计潜在FMEA过程中,希望负责设计的工程师们能够直接地、主动地联系所有有关部门的代表。
这些部门应包括(但不限于):装配、制造、材料、质量、服务和供方,以及负责下一总成的设计部门。
❖FMEA可成为促进有关部门间充分交换意见的催化剂,从而提高整个集体的工作水平。
❖此外,任何(内部或外部的)供方设计项目应向有关负责设计的工程师进行咨询。
❖设计FMEA是一份动态文件,应在一个设计概念最终形成之时或之前开始,而且,在产品开发各阶段中,当设计有变化或得到其它信息时,应及时,不断地修改,并最终在产品加工图样完成之前全部结束。
❖考虑制造/装配的要求是相互联系的,设计FMEA在体现设计意图的同时,还应保证制造或装配能够实现设计意图。
制造或装配过程中可能发生的潜在失效模式和/或其原因/机理不需包含在设计FMEA当中,此时,它们的识别,影响及控制是由过程FMEA来解决。
⏹设计FMEA不是靠过程控制来克服设计中潜在的缺陷,但的确要考虑制造/装配过程中技术的/体力的限制,例如⏹必要的拔模(斜度)⏹要求的表面处理⏹装配空间/工具可接近⏹要求的钢材硬度⏹过程能力/性能设计FMEA的开发⏹主管设计工程师拥有许多用于设计FMEA准备工作的文件。
⏹设计FMEA应从列出设计希望做什幺及不希望做什幺开始,如设计意图。
顾客需求(正如由QFD之类活动所确定的一样)、车辆要求文件、已知产品的要求和制造/装配要求都应结合起来。
⏹期待特性的定义越明确,就越容易识别潜在的失效模式,采取纠正措施。
⏹设计FMEA应从所要分析的系统、子系统或零部件的框图开始。
附录A给出了一个框图的示例,这个框图也可指示出信息、能量、力、流体等的流程。
其目的在于明确对于框图的(输入),框图中完成的过程(功能),以及来自框图的(输出)。
⏹框图说明了分析中包括的各项目之间的主要关系,并建立了分析的逻辑顺序。
⏹用于FMEA的准备工作中这种框图的复制件应伴随FMEA 过程。
目的⏹生产品设计开发初期, 分析产品潜在失效模式与相关产生原因提出未来分析阶段注意事项, 建立有效的质量控制计划定义⏹失效:⏹在规定条件下(环境、操作、时间)不能完成既定功能。
⏹在规定条件下, 产品参数值不能维持在规定的上下限之间。
⏹产品在工作范围内, 导致零组件的破裂、断裂、卡死等损坏现象。
⏹为了便于将潜在的失效模式及其影响后果分析成文,已设计出专用表格。
⏹下面介绍这种表格的具体应用,所述各项的序号都相应标在表上对应的栏目内,完成的设计FMEA表格的示例见附录B:•FMEA编号⏹填入FMEA文件编号, 以便查询。
系统、子系统或零部件的名称及编号•设计责任⏹填入整车厂(OEM)部门和小组, 如果知道,还应包括供方的名称。
4)编制者⏹填入负责FMEA准备工作的工程师的姓名、电话和所在公司的名称。
•年型/车型⏹填入将使用和/或正被分析的设计所影响的预期的年型及车型(如果已知的话)。
•关键日期⏹填入FMEA初次预定完成的日期,该日期不应超过计划的生产设计发布的日期。
•FMEA日期⏹填入编制FMEA原始稿的日期及最新修订的日期。
•核心小组⏹列出有权确定和/或执行任务的责任部门和个人姓名(建议所有参加人员的姓名、部门、电话、住址等都应记录在一张分发表上)。
•项目/功能⏹填入被分析项目的名称和编号, 尽可能简洁地填入被分析项目的功能符号, 设计意图。
包括这个系统作业相关的信息(如: 说明温度、压力、湿度范围)如果项目包含一个以上有不同潜在失效模式功能时, 则列出所有个别功能。
•潜在失效模式❖为零件、子系统或系统于符号设计意图过程中可能失效的种类, 也可能是较高阶子系统或系统之失效原因, 或较低阶零组件的失效效应。
❖列出特别项目和功能的每一潜在失效模式。
假设失效是将发生的但不是必须发生的, 潜在失效模式或尽可能发生于某些作业条件下(如: 热、冷、干燥、灰尘等)和某些使用条件下。
❖一般的失效模式包含下列各项, 但不限于此: 裂纹、变形、松弛、泄漏、粘结、短路、生锈氧化、断裂。
•潜在失效后果❖为被客户察觉在功能特性上失效模式的后果, 也就是: 失效模式一旦发生时, 对系统或装备以及操作使用人员所造成的影响。
❖一般在讨论失效后果时, 先检讨失效发生时对干部所产生的影响,然后循产品的组合架构层次, 逐层分析一直到最高层级人员, 装备所可能造成的影响。
❖常见的失效后果包括: 噪音、漏气、操作费力、电动窗不作用、煞车不灵、跳动、乱档、冷却不够、车辆性能退化, 产生臭气, 外观不良等。
•严重度(S)⏹严重度是潜在失效模式发生时对下序零件、子系统、系统或顾客影响后果的严重程度(列于前一栏中)的评价指标。
⏹严重度仅适用于后果⏹要减少失效的严重度级别数值,光能通过修改设计来实现,严重度的评估分为1到10级。
•分级⏹这个字段用来区分任何对零件、子系统或系统、将要求附加于制程管制的特殊产品特性(如关键的、主要的、次要的)。
⏹任何项目被认为是要求的特殊过程控制, 将被以适当的特征或符号列入设计FMEA的分级字段内, 并将于建议措施字段被提出。
⏹每一个于设计FMEA列出的项目, 将在过程FMEA的特殊过程管制中被列出。
•潜在失效的起因/机理•潜在失效起因是指一个设计薄弱部分的迹象,其作用结果就是失效模式。
•一般失效原因包括下列, 但不局限于此:•错误的原物料规格。
•不适当的设计寿命假设。
•超过压力。
•润滑或加油能力不足。
•不适当的维护作业。
•缺乏环境保护。
•错误的算法。
⏹一般装备失效包括下列, 但不局限于此⏹生产效益率低。
⏹金属疲劳。
⏹原物料材质不稳定。
⏹欠流畅。
⏹磨损。
⏹腐蚀。
•频度(0)❖频度是指某一特定失效起因或机理(已列于前栏目中)出现的可能性❖发生机会:❖为原因或装备可能发生的事。
可能发生的等级是一个值。
透过设计变更是唯一能删除或管制, 因各种原因或装备所产生的失效模式。
❖潜在失效起因/机理出现频度的评估分为1到10级,在确定这个估计值时,需要考虑下列问题:❖相似零件或子系统的过去服务取得资料和相关经验?❖零件、或前一等级类似零件或子系统是否渍销?❖从前一等级的零件或子系统, 改变的程度大小?❖零件与前一等级零件, 基本上是否有差异?❖零件是否为全新的产品?零件使用条件是否改变?❖作业环境是否改变?❖是否运用工程分析去评估, 实施执行与期望发生比率可组相提并论?推荐的评估准则•现行设计控制⏹列出利用预防, 设计验证/确认或其它作业未确认对失效模式设计适当, 和/或原因/机器设备均被考虑。
常用的控制(如: 道路试验、设计评审、运算研究、可行性审查、样件试验等)为一些已被或正在使用的相同或类似的设计。
有三种设计管制或特征:⏹预防起因/机理, 或失效模式/后果的出现或降低发生比率。
⏹查出起因/机理, 并提出纠正措施。
⏹查出失效模式。
⏹可能的话, 最好利用第1种控制方法; 再使用第2种控制方法; 最后才使用第3种控制方法。
•不易探测度(D)•风险顺序数(RPN)❖风险顺序数是严重度数(S), 频率数(0), 不易探测数(D)等级的乘积。
RPN = (S) ×(0) ×(D)是一项设计风险指针, RPN取值在1至1000之间。
当RPN 较高时, 设计小组应提出纠正措施来降低RPN值。
一般实务上, 较不注意RPN质的结果, 通常严重度数(S)较高时, 就会特别注意。
•建议措施❖当失效模式依RPN值排列其风险顺序时, 针对最高等级的影响和关键项目提出纠正措施, 任何建议措施的目的要清除任何的频次, 严重度和/或不易探测度的等级。
增加设计验证或确认作业的结果, 只可降低查出缺失的等级。
透过设计变更去除或控制某一或多个影响失效模式的起因/机理, 只能降低频次数的等级。
只有设计变更能降低严重度等级。
可以考虑下列的措施, 但不限于此:❖试验设计。
❖修改试验计划。
❖修改设计。
❖修改材料性能要求。
•责任(对建议措施)❖填入建议措施的负责单位或个人, 和预定完成的日期。
•采取的措施❖完成纠正措施后, 填入简短的执行作业或生效日期•纠正后的RPN❖将纠正措施实施后, 经鉴定, 评估和记录严重程度、出现频次和不易探测度数值的等级结果填入。