液化石油气脱硫
液化气脱硫工艺现状分析

液化气脱硫工艺现状分析液化气脱硫工艺是指对液化石油气中的硫化氢进行脱除的工艺。
随着环保意识的增强和对环境污染的重视,液化气脱硫工艺在化工领域中变得越来越重要。
本文将对液化气脱硫工艺的现状进行分析,并对其发展趋势进行展望。
一、液化气脱硫工艺的主要方法液化气中的硫化氢是一种有害的气体,不但对人体健康造成危害,而且还会对大气环境造成污染。
对液化气脱硫的要求越来越高。
目前,液化气脱硫主要采用以下几种工艺方法:1. 化学吸收法:化学吸收法是通过将液化气通入含有分散在其中的化学吸收剂的吸收器中,利用吸收剂与气体中的硫化氢发生化学反应,从而将硫化氢从气体中脱除。
常用的吸收剂有醇胺、乙二胺等。
化学吸收法能够将硫化氢脱除率达到较高水平,但是需要消耗大量的吸收剂,并且在后续的再生过程中也需要投入大量的能源,造成了一定的能源浪费。
2. 生物脱硫法:生物脱硫法是指利用一些特定微生物对液化气中的硫化氢进行生物氧化反应,从而将硫化氢转化为硫酸盐或者硫,达到脱硫的目的。
生物脱硫法具有脱硫效率高、耗能低、对环境友好等优点,但是存在微生物生长慢、对气体成分要求高、操作复杂等缺点。
3. 传质脱硫法:传质脱硫法是指利用气液两相之间的传质作用,将液化气中的硫化氢传送到液相中去。
传质脱硫法的工艺简单、操作方便、成本较低,但是脱硫效率和适用范围相对较窄。
上述方法各有优缺点,并且适用于不同的工艺条件和需要。
在实际工程中,常常会根据具体情况选择合适的液化气脱硫工艺方法,或者进行工艺的组合应用。
随着对环境保护的要求日益提高,液化气脱硫工艺在制气、天然气液化、LPG储罐、地下储罐以及分装装置等领域中得到了广泛应用。
在我国,液化气脱硫工艺的现状包括以下几个方面:1. 技术水平不断提高:近年来,我国在液化气脱硫工艺方面的技术水平不断提高,大量技术装备和工艺设备逐步更新升级。
在传质脱硫、化学吸收脱硫、生物脱硫等方面都取得了一定的突破和进展。
2. 成本不断降低:随着液化气脱硫工艺技术的进步和成熟,其成本不断降低。
液化石油气的硫含量标气
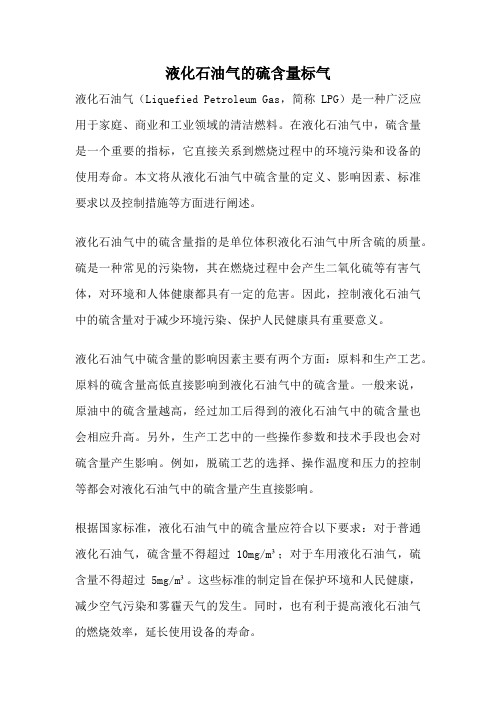
液化石油气的硫含量标气液化石油气(Liquefied Petroleum Gas,简称LPG)是一种广泛应用于家庭、商业和工业领域的清洁燃料。
在液化石油气中,硫含量是一个重要的指标,它直接关系到燃烧过程中的环境污染和设备的使用寿命。
本文将从液化石油气中硫含量的定义、影响因素、标准要求以及控制措施等方面进行阐述。
液化石油气中的硫含量指的是单位体积液化石油气中所含硫的质量。
硫是一种常见的污染物,其在燃烧过程中会产生二氧化硫等有害气体,对环境和人体健康都具有一定的危害。
因此,控制液化石油气中的硫含量对于减少环境污染、保护人民健康具有重要意义。
液化石油气中硫含量的影响因素主要有两个方面:原料和生产工艺。
原料的硫含量高低直接影响到液化石油气中的硫含量。
一般来说,原油中的硫含量越高,经过加工后得到的液化石油气中的硫含量也会相应升高。
另外,生产工艺中的一些操作参数和技术手段也会对硫含量产生影响。
例如,脱硫工艺的选择、操作温度和压力的控制等都会对液化石油气中的硫含量产生直接影响。
根据国家标准,液化石油气中的硫含量应符合以下要求:对于普通液化石油气,硫含量不得超过10mg/m³;对于车用液化石油气,硫含量不得超过5mg/m³。
这些标准的制定旨在保护环境和人民健康,减少空气污染和雾霾天气的发生。
同时,也有利于提高液化石油气的燃烧效率,延长使用设备的寿命。
为了控制液化石油气中的硫含量,生产和使用过程中需要采取一系列的措施。
首先,在生产过程中,可以采用脱硫工艺对原料进行处理,降低硫含量。
常用的脱硫方法包括催化剂脱硫、吸收剂脱硫和氧化脱硫等。
其次,在使用过程中,可以选择低硫液化石油气产品,避免使用高硫液化石油气。
此外,也可以通过改进燃烧设备和控制燃烧工艺,减少硫的排放。
液化石油气中的硫含量是一个重要的指标,它直接关系到环境污染和设备使用寿命。
通过控制原料和生产工艺,制定合理的标准要求,以及采取适当的控制措施,可以有效降低液化石油气中的硫含量,减少环境污染,保护人民健康。
TS-1型液化石油气常温精脱硫剂的性能研究

随着我国进口高硫含量原油量的增加,从原油中分离出的液化石油气中硫化物含量、结构和分布都有较大变化,传统的液化气脱硫工艺,往往达不到精脱硫要求,脱后液化石油气硫化物含量仍偏高,铜片腐蚀严重超标,影响产品质量和生产系统安全以及造成很大的环境污染。
液化石油气的脱硫方法和技术有很多种,包括:干法脱硫,湿法脱硫,膜分离脱硫,生物脱硫,电子束照射法及微波法脱硫等。
各种脱硫方法都有各自的特点、优点和缺陷,但在液化石油气的脱硫中,需要找到脱硫效果最好,工艺简单,脱硫成本较低的方法。
目前有很多研究报道了液化石油气的脱硫方法及技术或者脱硫剂的研究。
杨云平[1]介绍了HB5-l、HB5-3(DS-1)精脱硫剂在液化气中的工业应用情况。
结果表明,该脱硫剂脱硫效果很好,使液化气的铜片腐蚀从3级降至l级,总硫明显下降。
开发和合成新型的脱硫剂是目前对液化石油气脱硫的工作重点。
本文应用湖北省化学研究所开发出的TS-1型转化吸收精脱硫剂进行实验研究。
该脱硫剂以大孔结构为主,兼顾大量发达的微孔,并添加有助催化剂和活性促进剂。
TS-1型精脱硫剂在常温液相条件下对COS、硫醇有极强的转化吸收能力,同时对H2S、元素硫又具有优良的脱除性能,成本却有大幅降低,T S-1型精脱硫剂物化性能见表1。
表1TS-1型精脱硫剂物化性能1.实验部分1.1试验流程液化石油气原料以试验需求量的H2S、C OS、元素硫和甲硫醇等硫化物与液化石油气(经WK-2D总硫分析仪检验总硫小于0.01mg/m3)按一定比例混合均匀后配制而得。
原料经减压阀进入反应器,反应后尾液经过汽化器后,再经流量计、燃烧器、碱液吸收装置后放空。
在脱硫反应器前后均有取样点,以检测硫化物含量、种类和铜片腐蚀情况。
1.2试验条件试验原料所用液化石油气中丙烷、丁烷体积含量≥96%,戊烷及戊烷以上组分体积含量≤2%,O2<5mg/m3,H2O≤1000mg/m3,H2S、元素硫、COS、甲硫醇按实验要求配入。
液化石油气脱硫工艺概述
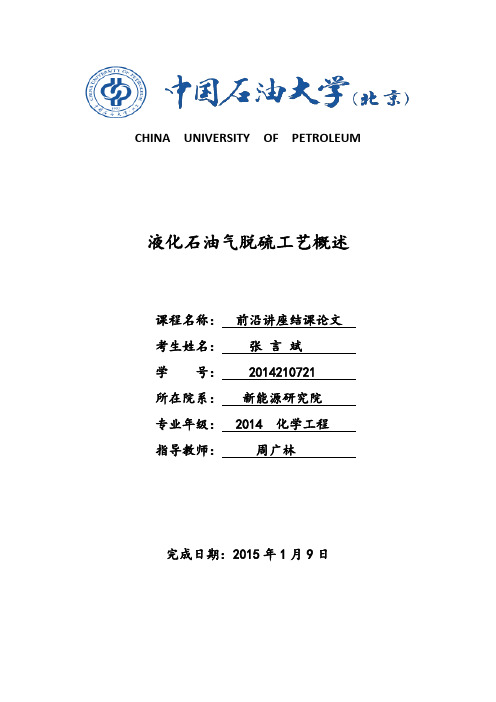
CHINA UNIVERSITY OF PETROLEUM 液化石油气脱硫工艺概述课程名称:前沿讲座结课论文考生姓名:张言斌学号: 2014210721 所在院系:新能源研究院专业年级: 2014 化学工程指导教师:周广林完成日期:2015年1月9日前沿讲座结课论文摘要液化石油气的杂质中除含有H2S和CO2等酸性组成外,还含有硫醇、硫醚、二甲基二硫醚、CS2等有机硫,这些硫的存在会对下游产品加工、环境保护和设备防腐蚀等方面造成非常不利的影响。
因此,液化石油气的脱硫及其硫化物的检测是液化石油气生产与检测中的重要环节。
脱除硫化物的方法和技术日渐发展和成熟,液化石油气脱硫的方法很多,在工业上应用的主要有湿法和干法两大类[1],近年来又发展了液膜脱硫技术,分子筛吸附脱硫,ThiolexSM技术,催化氧化-吸附结合法,等离子体法,生物脱硫法[2],电子束照射法和微波法等[3]。
关键词:液化石油气;含硫物;脱硫工艺;液化石油气主要来源于炼油厂催化裂化、延迟焦化、常减压、加氢裂化、连续重整等装置,其主要组分是C3和C4烃及少量C2和C5烃类,还含有硫化氢(质量浓度约0.01%~4%)、硫醇(质量浓度约1~9000mgS/Nm3)、硫醚(质量浓度0~100mgS/Nm3),COS 等硫化物。
常减压、加氢裂化、连续重整装置的液化气因烯烃含量少,大部分是丙烷、丁烷等饱和烃。
如果作为民用液化气,则精制后的总硫质量浓度满足不大于343 mgS/Nm3产品质量标准即可;如果作为下游装置的化工原料,如生产丙烷、正丁烷、异丁烷等,则总硫质量浓度通常控制在100 mgS/Nm3以下,越低越好;催化裂化、焦化装置产的液化气因含有高附加值的丙烯、异丁烯,为满足气体分离装置分离丙烯、丙烷和C4,必须将精制液化气总硫质量浓度脱除至小于100 mgS/Nm3以下[4]。
由以上产品的质量标准可以看出,液化石油气的脱硫是液化石油气净化精制工艺中极为重要的步骤,液化石油气的脱硫工艺也成了研究、探索、优化的重点。
液化石油气脱硫工艺探讨及应用
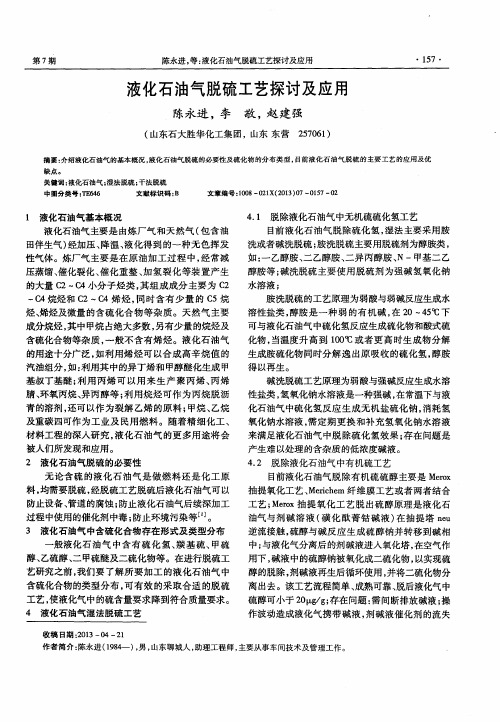
青的溶剂 , 还可以作为裂解 乙烯 的原料 ; 甲烷、 乙烷 及重碳四可作 为工业及 民用燃料 。随着精细化工、 材料工程的深入研究 , 液化石油气 的更 多用途将会 被人们所发现和应用 。
2 液化 石 油气脱 硫 的必 要性
无论含硫 的液化石油气 是做燃 料还是化工原 料, 均需要脱硫 , 经脱硫工艺脱硫后液化石油气可以 防止设备、 管道的腐蚀 ; 防止液化石油气后续深加工 过程中使用的催化剂 中毒 ; 防止环境污染等… 。
山 东 化 工 S H A N D O N G C H E M I C A L I N D U S nt Y
Zn O +H2 S— —— + Zn S+H2 O
2 0 1 3年第 4 2卷
等。
Me r i c h e m 纤维 膜 工 艺 脱 出硫 醇 原 理 为 纤 维 膜
溶性盐类 , 醇胺是一种弱 的有机碱 , 在2 O一 4 5 o 【 = 下 可与液化石油气中硫化氢反应生成硫化物和酸式硫
含硫化合物等杂质 , 一般不含有烯烃 。液化石油气 的用途十分广泛 , 如利用烯烃可 以合成高辛烷值的 汽油组分, 如: 利用其 中的异丁烯和 甲醇醚化生成 甲 基叔丁基醚 ; 利用丙烯 可 以用 来生产 聚丙烯、 丙烯
4 . 1 脱除液化石油气 中无机硫硫化氢工艺 目前 液 化 石 油 气 脱 除 硫 化 氢 , 湿法 主要 采用 胺
洗 或者 碱洗 脱硫 ; 胺 洗 脱硫 主要 用脱 硫剂 为醇胺类 , 如: 一 乙醇胺 、 二 乙醇胺 、 二异 丙 醇 胺 、 N一甲基 二 乙
田伴生气) 经加压、 降温、 液化得到的一种无 色挥 发 性气体 。炼厂气 主要是在原油加工过程 中, 经常减 压蒸馏 、 催化裂化、 催化重整 、 加氢裂化等装 置产生 的大 量 C 2一C 4小 分 子 烃 类 , 其组成成分主要为 C 2
液化石油气深度脱硫工业应用总结

液化石油气深度脱硫工业应用总结于宏【摘要】为满足下游甲基叔丁基醚(MTBE)装置的生产要求,2011年7月,锦西石化分公司对重油催化裂化装置吸收稳定及脱硫系统进行隐患整改,采用深度脱硫技术对液化石油气脱硫醇部分进行了改造.介绍深度脱硫技术在重油催化裂化装置液化石油气脱硫醇系统的应用情况.对过去两年装置运行数据的统计和系统分析结果表明,液化石油气深度脱硫技术在装置运行中操作简便、稳定可靠;液化石油气脱后总硫质量浓度低于10 mg/m3,液化石油气除臭精制液单耗为0.05 kg/t,新鲜碱液单耗为0.05 kg/t,软化水单耗为30 kg/t.单位液化气处理成本累计降低2.95 RMB ¥/t,上述指标均大大低于传统的液化石油气脱硫醇工艺,产生了良好的经济和社会效益.【期刊名称】《炼油技术与工程》【年(卷),期】2014(044)003【总页数】4页(P6-9)【关键词】重油催化;液化石油气;脱硫;脱硫醇;减排【作者】于宏【作者单位】中国石油天然气股份有限公司锦西石化分公司,辽宁省葫芦岛市125000【正文语种】中文产自催化裂化装置和延迟焦化装置的液化石油气(简称液化气)是聚丙烯和甲基叔丁基醚(MTBE)生产的重要原料,要求其总硫质量浓度小于50 mg/m3,铜片腐蚀不超过1级[1]。
近年来,汽油质量升级要求降低MTBE的硫含量,进而要求液化气的硫质量浓度降低到10 mg/m3以下。
传统的液化气脱硫醇工艺因脱硫率低,能耗、物耗高,环境污染大,无法满足新的生产要求。
在这种情况下,各种新型脱硫醇催化剂、设备和工艺应运而生。
锦西石化分公司液化气脱硫醇装置于1998年8月投产,设计规模168 kt/a,采用MEROX液-液抽提工艺。
投用后装置存在着铜片腐蚀经常不合格、脱后总硫质量浓度偏高(120 mg/m3左右)的问题,影响了液化气产品出厂及下游MTBE、聚丙烯装置的生产。
2005年该公司对重油催化裂化(简称重催)装置进行MIP扩能改造,液化气脱硫醇装置维持原工艺,对部分设备进行了改造,但脱后液化气铜片腐蚀经常不合格和脱后总硫质量浓度偏高(100 mg/m3左右)的问题仍然没有解决。
液化石油气基本知识(2)
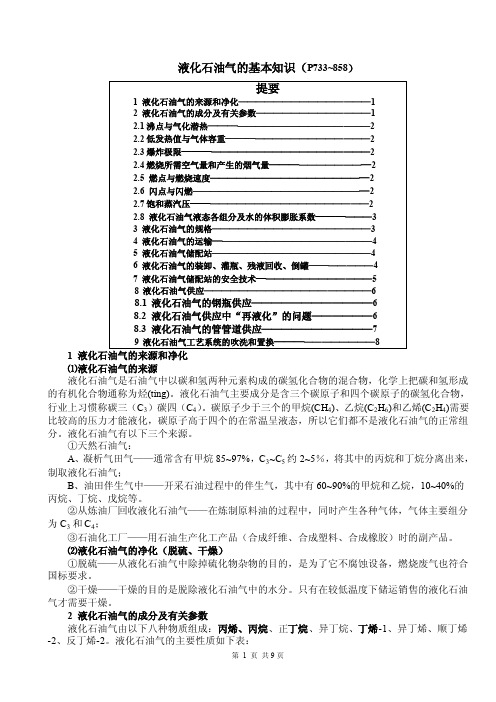
液化石油气的基本知识(P733~858)1⑴液化石油气的来源液化石油气是石油气中以碳和氢两种元素构成的碳氢化合物的混合物,化学上把碳和氢形成的有机化合物通称为烃(ting)。
液化石油气主要成分是含三个碳原子和四个碳原子的碳氢化合物,行业上习惯称碳三(C3)碳四(C4)。
碳原子少于三个的甲烷(CH4)、乙烷(C2H6)和乙烯(C2H4)需要比较高的压力才能液化,碳原子高于四个的在常温呈液态,所以它们都不是液化石油气的正常组分。
液化石油气有以下三个来源。
①天然石油气:A、凝析气田气——通常含有甲烷85~97%,C3~C5约2~5%,将其中的丙烷和丁烷分离出来,制取液化石油气;B、油田伴生气中——开采石油过程中的伴生气,其中有60~90%的甲烷和乙烷,10~40%的丙烷、丁烷、戊烷等。
②从炼油厂回收液化石油气——在炼制原料油的过程中,同时产生各种气体,气体主要组分为C3和C4;③石油化工厂——用石油生产化工产品(合成纤维、合成塑料、合成橡胶)时的副产品。
⑵液化石油气的净化(脱硫、干燥)①脱硫——从液化石油气中除掉硫化物杂物的目的,是为了它不腐蚀设备,燃烧废气也符合国标要求。
②干燥——干燥的目的是脱除液化石油气中的水分。
只有在较低温度下储运销售的液化石油气才需要干燥。
2 液化石油气的成分及有关参数液化石油气由以下八种物质组成:丙烯、丙烷、正丁烷、异丁烷、丁烯-1、异丁烯、顺丁烯-2、反丁烯-2。
液化石油气的主要性质如下表:512614易变成气体而成为残液;②上表中的斜体数字未经核实;③正丁烷与异丁烷的分子式、分子量相同,但它们的结构不同,即碳与碳的连接方式不同,故性质也不同。
2.1沸点与气化潜热——液化石油气主要成分的沸点都很低,所以常温下是在沸腾的情况下气化,并吸收大量潜热(1kg液化石油气气化所吸收的潜热相当于1kg水升高101℃所吸收的热量)。
当大量液化石油气从狭口喷出时,会形成白茫茫的一片,就是因为喷出的液化石油气吸收了周围空气的热量,本身也因压力突降而降温,把空气里的水分凝结成霜的缘故。
双氧水给液化石油气脱硫反应-概述说明以及解释
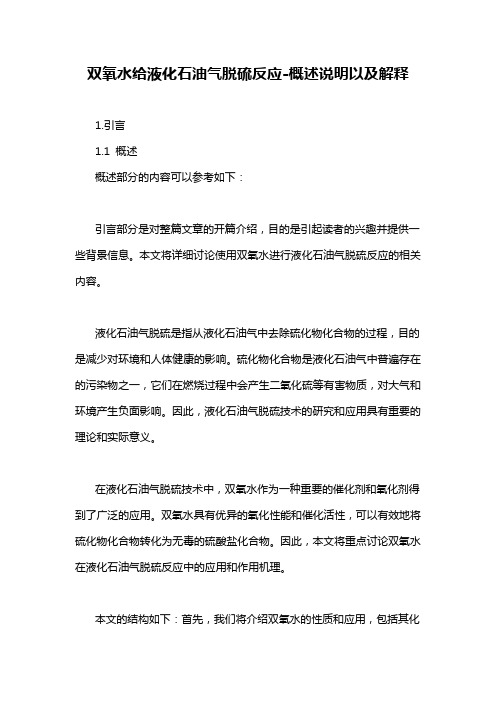
双氧水给液化石油气脱硫反应-概述说明以及解释1.引言1.1 概述概述部分的内容可以参考如下:引言部分是对整篇文章的开篇介绍,目的是引起读者的兴趣并提供一些背景信息。
本文将详细讨论使用双氧水进行液化石油气脱硫反应的相关内容。
液化石油气脱硫是指从液化石油气中去除硫化物化合物的过程,目的是减少对环境和人体健康的影响。
硫化物化合物是液化石油气中普遍存在的污染物之一,它们在燃烧过程中会产生二氧化硫等有害物质,对大气和环境产生负面影响。
因此,液化石油气脱硫技术的研究和应用具有重要的理论和实际意义。
在液化石油气脱硫技术中,双氧水作为一种重要的催化剂和氧化剂得到了广泛的应用。
双氧水具有优异的氧化性能和催化活性,可以有效地将硫化物化合物转化为无毒的硫酸盐化合物。
因此,本文将重点讨论双氧水在液化石油气脱硫反应中的应用和作用机理。
本文的结构如下:首先,我们将介绍双氧水的性质和应用,包括其化学性质、反应特点以及在其他领域的应用情况。
接着,我们将探讨液化石油气脱硫的背景和需求,包括液化石油气中硫化物化合物的来源和对环境的影响。
最后,我们将总结双氧水在液化石油气脱硫中的作用,评估其优势和局限性,并展望未来可能的研究方向。
通过对双氧水在液化石油气脱硫反应中的研究和应用进行系统的总结和分析,有助于更好地理解和推动该领域的发展。
双氧水在液化石油气脱硫中具有潜在的应用前景,但也面临一些挑战和限制。
通过深入研究这一领域,我们可以进一步优化反应条件、提高脱硫效率,并为环境保护和可持续发展做出贡献。
1.2文章结构文章结构部分包括对整篇文章的组织和分章节的介绍。
在这篇文章中,我们将按照以下结构进行叙述:1. 引言1.1 概述:介绍液化石油气脱硫的背景和意义,同时提及双氧水在脱硫反应中的重要作用。
1.2 文章结构:简要说明本文的章节组织和内容安排,引导读者对整篇文章的概况有所了解。
1.3 目的:阐明本文的研究目的和意义,概括研究效果和观点的目标。
炼油厂液化石油气胺法脱硫工艺设计优化
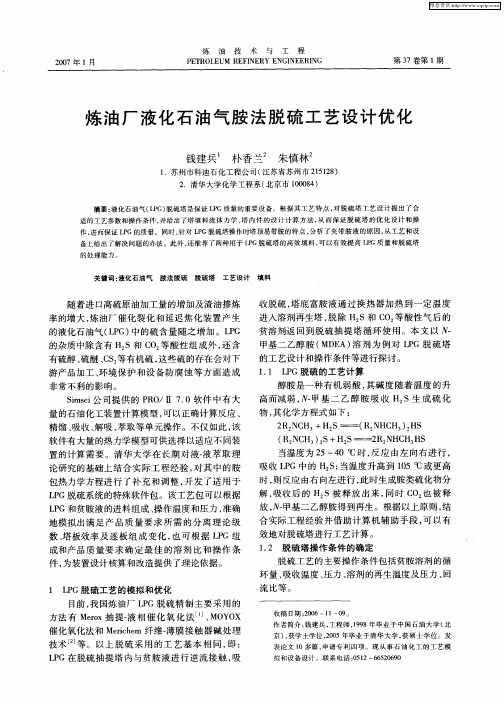
进入溶剂再生塔 , 脱除 H s和 C O 等酸性气后 的 贫溶 剂返 回到 脱 硫 抽 提 塔 循 环 使 用 。本 文 以 Ⅳ 一 甲基二 乙醇胺 ( D A) M E 溶剂为例对 L G脱硫塔 P 的工 艺设 计 和操 作条件 等进行 探 讨 。
1 1 L G脱 硫 的工艺 计算 . P 醇胺是 一种 有 机 弱 酸 , 碱 度 随 着 温度 的升 其 高 而减 弱 , 甲 基 二 乙 醇 胺 吸 收 H S生 成 硫 化 Ⅳ一 物 , 化学方 程式 如下 : 其
流 比等 。
收稿 1期 :0 6—1 —0 。 3 20 1 9
目前 , 国炼 油厂 L G脱 硫精 制 主 要 采用 的 我 P 方 法 有 Meo 提一 相 催 化 氧 化 法¨ MO O rx抽 液 、 Y X 催化 氧化 法 和 Mei e 纤维一 膜接 触 器 碱处 理 rhm c 薄 技术 等 。 以上 脱 硫 采 用 的工 艺 基 本 相 同 , : 即 L G在 脱硫 抽 提 塔 内与贫 胺 液进 行 逆 流接 触 , P 吸
2 2C 3 2 R N H +H S一 ( 2 H H )H R N C 32 S 2 2 H H S RN C 3 H ( 2 C 3 2 H2 一 R N H ) S+ S
的杂 质 中除含 有 H s和 C 酸性 组 成 外 , 含 在 会对 下 硫 c, 这 游产 品加工 、 境 保护 和设 备 防腐 蚀 等方 面 造 成 环 非 常不 利的影 响 。 Sm c公 司提供 的 P O 17 0软 件 中有 大 isi R /1 .
作者 简介 : 钱建兵 , 工程师 ,9 8年毕业于 中国石油大学 ( 19 北 京 ) 获学士学位 ,0 5年毕 业于清华大学 , , 20 获硕士学位 。发 表论 文 l O多篇 , 申请专 利 四项 。现从 事石 油化工 的工艺模 拟和设备 设计 。联 系电话 :52— 6 26 0 O 1 6 50 9
油气田液化石油气脱硫
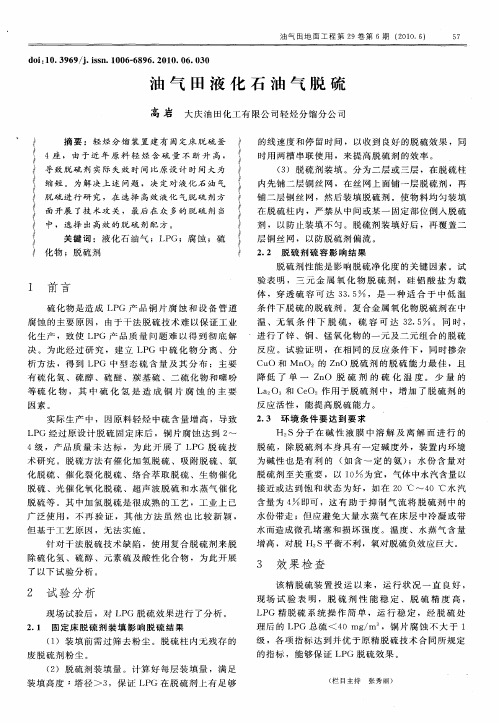
除硫化 氢 、硫 醇 、元 素硫及 酸 性化 合 物 ,为此 开展
了 以下 试验 分 析 。
3 效 果 检 查
该 精脱 硫 装 置 投 运 以来 ,运 行 状 况 一 直 良好 ,
2 试 验 分 析
现 场试 验后 ,对 L G脱 硫 效果 进行 了分析 。 P
2 1 固 定 床 脱 硫 剂 装 填 影 响 脱 硫 结 果 .
但 基 于 工 艺 原 因 ,无 法 实 施 。
H。 S分子 在 碱 性 液 膜 中溶 解 及 离 解 而 进 行 的 脱 硫 ,除脱硫 剂本 身 具有 一定 碱度 外 ,装置 内环境
为碱 性也 是有 利 的 ( 含 一 定 的 氨 ) 如 ;水 份 含 量 对
脱 硫 剂至 关重 要 ,以 1 为 宜 ,气体 中水汽含量 以 O 接 近或达 到 饱 和状 态 为好 ,如 在 2 O℃ ~4 C水 汽 0。
化 物 ;脱 硫剂
脱硫 剂 性能 是影 响脱 硫 净化 度 的关键 因素 。试
l 前 言
硫化 物 是造 成 L G 产 品 铜 片腐 蚀 和 设 备 管 道 P
验 表 明 , 三 元 金 属 氧 化 物 脱 硫 剂 ,硅 铝 酸 盐 为 载
体 ,穿 透硫 容 可 达 3 . ,是 一 种 适 合 于 中低 温 35
油 气 田地 面 工 程 第 2 9卷 第 6期 (0 0 6 21. )
5 7
d i1 . 9 9 j is . 0 6 6 9 . 0 0 0 . 3 o :0 3 6 / .sn 1 0 — 8 6 2 1 . 6 0 0
油 气 田 液 化 石 油 气 脱 硫
高 岩 大庆油田 化工有限公司轻烃分馏分公司
液化石油气工艺流程
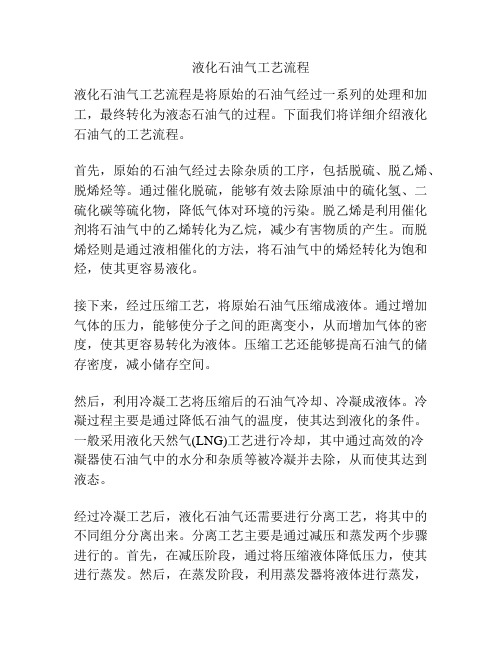
液化石油气工艺流程液化石油气工艺流程是将原始的石油气经过一系列的处理和加工,最终转化为液态石油气的过程。
下面我们将详细介绍液化石油气的工艺流程。
首先,原始的石油气经过去除杂质的工序,包括脱硫、脱乙烯、脱烯烃等。
通过催化脱硫,能够有效去除原油中的硫化氢、二硫化碳等硫化物,降低气体对环境的污染。
脱乙烯是利用催化剂将石油气中的乙烯转化为乙烷,减少有害物质的产生。
而脱烯烃则是通过液相催化的方法,将石油气中的烯烃转化为饱和烃,使其更容易液化。
接下来,经过压缩工艺,将原始石油气压缩成液体。
通过增加气体的压力,能够使分子之间的距离变小,从而增加气体的密度,使其更容易转化为液体。
压缩工艺还能够提高石油气的储存密度,减小储存空间。
然后,利用冷凝工艺将压缩后的石油气冷却、冷凝成液体。
冷凝过程主要是通过降低石油气的温度,使其达到液化的条件。
一般采用液化天然气(LNG)工艺进行冷却,其中通过高效的冷凝器使石油气中的水分和杂质等被冷凝并去除,从而使其达到液态。
经过冷凝工艺后,液化石油气还需要进行分离工艺,将其中的不同组分分离出来。
分离工艺主要是通过减压和蒸发两个步骤进行的。
首先,在减压阶段,通过将压缩液体降低压力,使其进行蒸发。
然后,在蒸发阶段,利用蒸发器将液体进行蒸发,使其中的不同组分按照沸点的不同而蒸发或凝结,从而实现分离。
最后,通过调节和控制系统,将液化石油气进行储存和运输。
液化石油气通常储存于特殊设计的大型储罐中,以保证其在运输和储存过程中的安全性。
在运输过程中,液化石油气通常采用钢制罐车或集装箱进行运输,以确保其在运输过程中的稳定性和安全性。
总的来说,液化石油气工艺流程主要包括去除杂质、压缩、冷凝、分离、储存和运输等步骤。
这些步骤的串联和协调,使得原始的石油气能够经过一系列的加工和处理,最终转化为液态石油气,使其更加方便储存、运输和使用。
这种工艺流程的建立和优化,对于液化石油气的生产和应用具有重要的意义。
催化氧化脱硫醇工艺应注意什么?

催化氧化脱硫醇工艺应注意什么?催化氧化脱硫醇〔脱臭〕是将液化石油气、催化汽油或航空煤油用磺化酞菁钴〔或聚酞菁钴〕碱液为催化剂, 用抽提和氧化方法将其中的硫醇转化为无臭味、腐蚀性小的二硫化物的工艺过程。
能提升石油产品的抗氧化性, 改善使用性能和减少燃烧尾气对大气环境的污染。
催化氧化脱硫醇是一种精制石油产品的工艺, 依据精制对象和产品质量要求不同, 分一步法和二步法两种工艺流程。
液态烃脱硫醇采纳抽提一步流程, 经催化剂碱液抽提水洗后就送出装置。
溶于碱液中的硫醇以硫醇钠状态存在, 并进一步与空气氧化生成二硫化物, 在分开器中与碱液分开。
汽油脱硫醇采纳抽提和氧化二步流程。
经催化剂碱液抽提后的汽油进入氧化塔, 把残余硫醇氧化成二硫化物, 去除其恶臭味。
氢氧化钠是腐蚀性很强的碱, 在配制催化剂碱液时最容易发生碱灼伤事故。
碱液管线, 盛碱容器也容易腐蚀泄漏。
配制时假设碱罐盛装液面太高, 搅拌碱液压缩风开得过快过猛, 会把碱液溢出、沾上身体, 造成人体灼伤事故。
含硫醇钠碱液经与空气氧化后生成二硫化物, 至分开器进行分开。
分开器制定有分开柱, 筛网破沫结构。
分开柱液面控制不好, 碱液和二硫化物会窜入尾气系统, 放空管线窜碱, 造成操作压力波动。
分开器碱液界面过高, 可能使碱液窜入二硫化物管线, 不仅影响二硫化物焚烧处理, 还造成催化剂碱液损失。
催化汽油经抽提脱硫醇后和催化剂碱液、压缩空气一起进入氧化塔进行氧化脱臭。
进塔的各物料量比例控制不当, 特别是压缩空气压力波动会使汽油和碱液窜入压缩空气管道, 造成操作波动, 甚至引起爆炸事故。
在配制催化剂碱液时要穿戴好防碱护品, 慎重操作, 严防碱液沾上人体。
注意碱液罐及工艺管线泄漏。
配制罐的碱液面不能太高, 要缓慢通入压缩空气搅拌。
罐的四周要设置冲洗水龙头。
假设沾上碱液时应迅速冲洗。
避免分开器的分开柱、破沫网、格栅等内部结构件腐蚀损坏, 以坚持其优良的破乳分开效果。
罐体上的液面计, 液面控制系统要灵活好用, 分开器的界〔液〕面操作要控制在一定范围, 以防止碱、二硫化物窜入尾气放空系统, 以及把碱液窜入二硫化物管道。
液化石油气脱硫方法及技术的研究进展
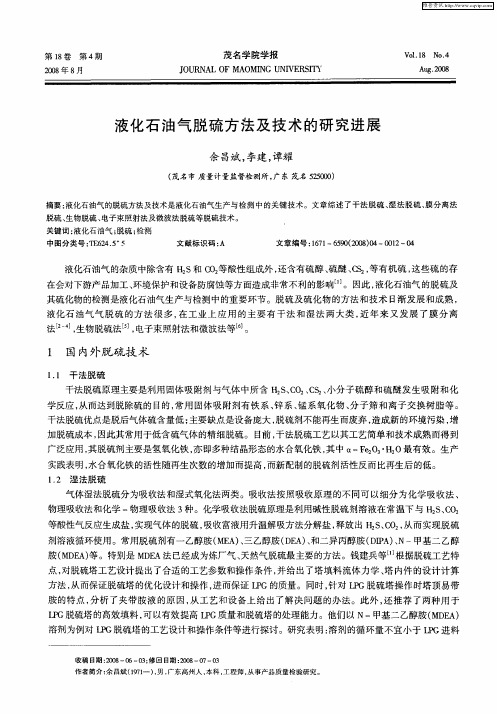
胺的特点 , 分析 了夹带胺 液的原 因, 从工艺和设备上 给出了解决问题 的办法。此外 , 还推荐 了两种用 于 LG脱硫塔的高效填料 , P 可以有效提高 LG质量和脱硫塔的处理能力。他们以 N一甲基二乙醇胺( D A P M E) 溶剂为例对 L G脱硫塔的工艺设计和操作条件等进行探讨。研究表明: P 溶剂的循环量不宜小于 LG进料 P
余 昌斌 , 李建 , 谭耀
( 茂名市 质量计量监督检测所 , 东 茂名 550 ) 广 200
摘要 : 液化石油气的脱硫方法及技术是液化石油气生产与检测 中 的关键 技术 。文 章综述 了干法脱 硫 、 湿法脱 硫 、 分离法 膜
脱硫 、 生物脱硫 、 电子柬照射法及 微波法脱硫等脱硫 技术 。
关键词 : 液化石油气 ; 脱硫 ; 检测 中图分类号 :E 2 . T 645 5 文献标识码 : A 文章编号 :6 1 50 20 )4 02 4 17 —69 (08 0 —0 1 —0
液化 石油气 的杂质 中除含 有 H S和 C 酸性 组成外 , 2 0等 还含 有硫 醇 、 醚 、S , 硫 C 2等有 机 硫 , 这些 硫 的存
1 3 膜 分离 法脱硫 .
膜分离法是利用半渗透膜的选择性和膜两侧的能量差将气体中的 Hs c 2 2、 o 与其他组分分离。但是
复杂的制膜工艺使得膜系统造价昂贵 , 限制了它在工业上的广泛使用。 目 前美 国和加拿 大几家公司利用
这 一技术 分离 天然 气 中的 HS和 C 2 O 。缪 希 平 研究 了纤 维 液 膜 接触 器在 液 化 石 油 气 脱 硫 工 艺 中 的应
胺( D A 等。特别是 M E M E) D A法 已经成为炼厂气、 天然气脱硫最主要 的方法。钱建兵等…根据脱硫工艺特 点, 对脱硫塔工艺设计提出了合适的工艺参数和操作条件 , 并给出了塔填料流体力学 、 塔内件的设计计算
液化气脱硫工艺现状探讨

液化气脱硫工艺现状探讨摘要:从现状结合目前我国对于液化气脱硫的客观要求,讨论了几种常见的硫化物的形态和对其相应的脱硫工艺。
关键词:液化气;脱硫;工艺1 前言近些年来,随着国内市场需求的增长以及我国高硫原油加工量的增加,石油产品的含硫量也随之增大。
众所周知,石油产品硫含量过高对其石化工业的下游加工、环境保护和有关石化设备的腐蚀等方面会造成非常不利的影响。
其中的主产物之一液化气作为重要的化工原料和民用燃料,其脱硫的相关研究是十分重要的。
随着环保意识的增强,我国逐渐提高了汽油和柴油的相关质量标准,新标准中对汽油的含硫量作出了严格的规定。
为此,必须想办法降低汽油中的含硫量,而对于汽油来说,降低其硫含量主要也就是降低汽油中添加剂组分的含硫量,以符合新的汽油标准。
甲基叔丁基醚(mtbe)作为无铅汽油中重要的添加剂组分,其含硫量也应得到严格的控制。
由于mtbe具有分子结构的不稳定性和自身溶于水的特性,以及硫化物在mtbe中的溶解性比烃类要好,再加上合成mtbe时硫醇和甲醇一样也可以和异丁烯发生醚化反应甚至硫醇自己发生自醚化反应,所以从产品mtbe中脱硫是很困难的。
所以要从生产mtbe的原料——液化气来入手降低其硫含量,因此,液化气脱硫的相关研究也是十分必要的。
就目前各炼厂的液化气脱硫技术来说,炼厂中采用的方法也很多,如酸碱精制法、醇胺精制法、merox脱臭精制法等[1],针对脱除硫化物的不同也有相应的脱硫方法。
为实现资源的高效利用,就要求根据液化气中硫化物种类与含量的不同来选择相应的脱除方法和工艺流程。
2 液化气中硫化物的大致种类液化气中硫化物种类较多,不易分析,总结来说大致有以下几种:硫化氢、元素硫、羰基硫、二硫化碳、硫醇、硫醚[1]。
其中硫化氢的含量最高,是液化气中含硫的主要因素,但其脱除方法也较多。
羰基硫(cos)含量较少,主要存在于c3馏分中,可以水解为h2s和co2。
二硫化碳含量少。
硫醇在其中的含量仅次于硫化氢,一般为甲硫醇、乙硫醇,偶尔也含少量丙硫醇、丁硫醇。
一种石油液化气深度脱硫精制组合工艺[发明专利]
![一种石油液化气深度脱硫精制组合工艺[发明专利]](https://img.taocdn.com/s3/m/822e39f66c175f0e7dd1378f.png)
专利名称:一种石油液化气深度脱硫精制组合工艺专利类型:发明专利
发明人:申志兵,张君涛,梁生荣
申请号:CN201410782329.8
申请日:20141216
公开号:CN104403688A
公开日:
20150311
专利内容由知识产权出版社提供
摘要:本发明涉及一种用于液化石油气的深度脱硫工艺。
针对液化气中所含的硫化物的不同性质特点,分别采用羰基硫水洗塔脱除液化气中的硫化氢和羰基硫,通过氧化塔将液化气中的小分子硫醇转化为沸点较高的二硫化物,再通过精馏的方式将硫化物与液化气产品分离,塔底为富硫的C5或重C4组分,在塔顶为超低硫的液化气产品。
该过程液化石油气中的硫含量降至5μg/g以下,脱硫率高,无碱渣排放。
申请人:西安石油大学
地址:710065 陕西省西安市电子二路东段18号
国籍:CN
代理机构:北京科亿知识产权代理事务所(普通合伙)
代理人:汤东凤
更多信息请下载全文后查看。
- 1、下载文档前请自行甄别文档内容的完整性,平台不提供额外的编辑、内容补充、找答案等附加服务。
- 2、"仅部分预览"的文档,不可在线预览部分如存在完整性等问题,可反馈申请退款(可完整预览的文档不适用该条件!)。
- 3、如文档侵犯您的权益,请联系客服反馈,我们会尽快为您处理(人工客服工作时间:9:00-18:30)。
液化石油气脱硫研究进展摘要:综述了国内外液化石油气脱硫技术,特别是Merox抽提-氧化工艺、纤维膜接触器碱处理技术、无碱固定床催化氧化-吸附结合法等脱硫技术发展现状,并对液化气脱硫技术发展前景作出展望。
关键词:液化气;脱硫;有机硫中图分类号:TQ203.2文献标识码:A石油炼制过程中,焦化、常减压、催化裂化等装臵产生的液化石油气(liquefied petroleum gas,LPG),含有大量的硫化物[1~3],除H2S 外,还有各种形态的有机硫,如COS,CH3SH,C2H5SH,CH3SCH3等,其中主要是CH3SH。
硫化物会造成后续加工过程中催化剂的中毒和失活,而元素硫和硫化氢对管路及储存容器腐蚀大,作为民用燃料时会生成SOx,污染环境,形成酸雨等。
目前,国内外对LPG作为燃料时,其总硫含量和铜片腐蚀级别有所要求;如果作为化工原料,则要求更严。
我国的液化气标准(GB 1174-1997)规定,LPG中总硫质量分数小于343 mg/m3,铜片腐蚀的级别小于1级。
因此,深度脱除LPG中的硫化物,具有重要的经济和环保意义。
1 LPG脱硫工艺研究传统的LPG脱硫精制有干法和湿法两种方法[3~6],一般根据其硫含量及净化要求而定,对于硫含量低或处理量小的LPG采用干法,如用氧化锌、氧化铝、活性炭吸附或者用简单的碱法吸收。
对于硫含量高、处理量大的LPG的处理包括两部分:第一步利用醇胺溶液脱除LPG中的硫化氢,或将COS水解后一并脱除,常用的醇胺[7,8]有MEA,DI-PA,MDEA,DEA及相应的复配溶液,该工艺已非常成熟;第二步则是用碱洗或精脱硫催化剂进行精制。
另外,欧美少数公司采用分子筛法,具有同时脱H2S,COS,水和有机硫的能力;也有学者研究[9]利用等离子体破坏硫醇结构来脱硫。
液化气脱硫醇的方法最早是由美国环球油品公司(UOP)1958年提出的,发展至今形成了成熟的液液抽提、氧化再生工艺,即Merox 抽提氧化法。
目前国内外应用最广泛的是美国UOP公司的梅洛克斯(Merox)脱硫醇技术和美利肯(Merichem Co.)公司的纤维薄膜(Fiber-Film)接触器碱处理技术,即硫醇提净(ThiolexSM)技术[3,10]。
LPG 脱COS、硫醇等有机硫是脱硫的难点,是国内外研究的重点。
1.1 湿法脱硫醇传统湿法工艺中,液化气首先通过MDEA吸收塔脱H2S,CO2等,再用10% NaOH溶液洗脱残余的H2S,然后用溶解了磺化酞菁钴的碱液脱除LPG中的硫醇,脱后LPG去气分装臵;脱硫塔底碱液进再生塔,经通风在磺化酞菁钴催化剂作用下,将硫醇钠氧化成二硫化物,使碱液得到再生后循环使用。
其反应原理如下:碱液加助剂可显著提高高分子硫醇在碱液中的溶解度,提高硫醇脱除率。
研究表明[6,11],液化气用磺化酞菁钴脱硫醇时,MEA、氯化铵、吗啉、尿素、烷基氢氧化钠等助催化剂,可显著提高脱硫醇效率。
该法缺点如下:(1)酞菁钴类催化剂处于碱相,易聚集失活[12],导致频繁更换催化剂,催化剂成本相当高,同时使生产力受到一定程度影响,而且生产过程退碱时,易造成液化气跑损事故,造成生产的不安全性;(2)液化气用含有催化剂的碱液进行硫醇抽提,在催化剂存在条件下硫醇钠易生成二硫化物带到精制的液化气产品中,造成液化气总硫含量超标[13];(3)由于使用了液体苛性碱而加重了环保压力。
为减少废碱液的排放,采用氨水代替液体苛性碱进行液化气预碱洗,使用污水气体装臵处理氨水,使氨再生和循环利用。
该技术必须增加气体装臵,且氨水碱性较弱,有机硫难以洗脱。
也有用固体碱代替液碱洗,再与活性剂混合进入脱臭塔后脱臭,但需加入专门的脱臭剂。
1.2 固定床(干法)脱硫醇Merox固定床吸附脱硫醇工艺是国际上近期发展最快的方法之一,固定床吸附工艺具有流程简单、投资少、操作简便等特点,其载体一般是活性炭,催化剂是磺化酞菁钴或聚酞菁钴。
固定床工艺流程将含有硫醇的LPG与分散在多孔载体上的金属酞菁钴催化剂接触,在碱性条件下,用空气将硫醇氧化成二硫化物。
其原理[14,15]如下:在脱硫醇过程中,需向催化剂中注入碱液,使其处于被碱液浸润状态,以维持催化剂的活性和稳定性。
载体应具有以下特点:(1)不溶于苛性碱液,不与LPG反应;(2)有足够的活性位吸附金属酞菁钴催化剂;(3)有一定的孔容来保证硫醇分子与金属酞菁钴作用;(4)有足够的抗磨损强度。
目前,工业应用最广泛的是活性炭载体[16,17]。
美国UOP公司推出了最小碱量固定床脱硫醇工艺,即在LPG中注入少量碱液并与空气混合后一起通过催化剂床层,该工艺不需要定期向床层注碱,与液-液体系相比,碱使用量减少了约90%。
1.3 分子筛吸附法分子筛是一种合成沸石,具有选择吸附特性,可同时将H2S和有机硫脱除至很低水平,其特点是物理吸附,无化学反应。
13X分子筛是脱硫醇最好的吸附剂[18,19],分子筛法具有无须预碱洗、无污染、能在常温吸附等优点,但须在300℃左右高温再生,因而增大了操作成本,且资金投入较大。
因此,分子筛用于LPG脱硫醇受到限制,一般欧美国家应用较多,国内也有初步应用。
申永谦等研究了分子筛脱硫的影响[19],研究表明,因分子筛对水等极性小分子具有极强的吸附能力,因此,LPG脱硫醇工序一定要严格控制水的含量。
三聚环保公司用一种经高价态金属阳离子,如镧、铈或混合轻稀土元素交换后的改性X型或Y型分子筛物理吸附,脱除液化石油气中的有机硫化物[20],该工艺操作简单、效率高,催化剂可反复使用,但再生至少要在200℃以上进行。
Peter等用0.3 nm,0.4 nm,0.5 nm分子筛分别脱除水分和硫化氢,13X分子筛用Zn2+等过渡金属离子改性后脱硫醇[21]。
Yoshitsugi也利用分子筛来脱除气流中的硫化氢[22]。
1.4 ThiolexSM技术硫醇提净(THiolexSM)技术是美利肯公司开发的一种利用纤维-薄膜接触器来提取H2S、CO2和硫醇的专利技术。
它可用于丙烷/丙烯、丁烷/丁烯等脱硫处理过程。
其接触面积大、碱用量低、废碱产生少,操作费用与投资都相应较低,特别对于碱液处理LPG的场合,不会发生碱液的携带现象,也不需在下游设臵碱液聚合器。
国内金陵石化于1999年最早引进该技术,目前已基本国产化[23]。
茂名石化应用该技术处理从焦化装臵产出的液化气,经纤维液膜脱硫系统后,脱硫率达到95%以上,出厂液化气的总硫质量分数由原来的5000 mg/m3降至目前的200 mg/m3以下,这一数据远远低于国家新标准规定的要求。
1.5 催化氧化-吸附结合法液化气无碱脱臭工艺以复合金属氧化物为催化剂,利用液化气中所溶解的微量氧将硫醇氧化成二硫化物,在总硫超标的情况下可通过精馏除去二硫化物,同时预碱洗过程使用固定床脱硫剂脱硫化氢,使整个工艺过程不存在碱渣排放问题,具有很好的应用前景。
其原理是通过催化氧化与吸附结合的方法来脱硫。
常用的有铁系催化剂、MnO-CuO催化剂、稀土金属催化剂、贵金属催化剂系列等[24~29],其脱硫机理类似。
该类催化剂可在常温常压下将LPG中的甲硫醇、乙硫醇等转化成二硫化物和三硫化物,然后再用活性炭或用冷凝方法除去;且铁能与LPG中的H2S反应生成稳定的硫化物,除去硫化氢。
齐鲁石化研究院和石油大学合作研制了以分子筛为载体、非贵金属为活性组分的脱硫剂,能有效地脱除液化石油气中较难脱除的二硫化物[27]。
与载体未处理的脱硫剂相比,经预处理的分子筛载体脱硫剂其脱硫性能较好。
开发的QTM-01硫醇氧化催化剂是在复合金属氧化物中加入适量的活性助剂和特种添加剂,经混碾、成型、干燥和焙烧后制成。
QTM-01催化剂具有硫醇氧化活性高、稳定性好且能吸附H2S等特点。
工业侧流试验结果表明,该催化剂在液相及常温条件下可有效地将液化气中的硫醇氧化成二硫化物,无碱液排放。
南京大学梅华等研究用固体碱替代污染大的液体苛性碱[28],结果表明,较高的Mg与Al物质的量比制备的MgO/Al2O3-CoPeS催化剂具有较高的表面碱量,在硫醇催化氧化反应中表现出相对高的催化活性。
石油大学夏道宏等在哈尔滨石化分公司液化气脱硫醇预碱洗系统中进行了固体碱技术的工业应用试验[29,30],试验结果表明,固体碱洗能够达到或超过液体碱洗的效果;固体碱洗不仅脱硫化氢效果好,而且具有脱硫醇和总硫的功能;使用固体碱无废碱液排放,对环保有利。
三聚环保公司研制了一系列无碱固定床催化氧化吸附脱硫催化剂[31~33],其中JX-2A硫醇转化催化剂在中石化大庆炼化公司成功应用,其活性组分结构属于结晶化学中ABO型化合物,是高价态过渡金属,活性组分中的晶格氧能将硫醇氧化成二硫化物,当液化石油气中有微量氧存在时,立即补充到晶格氧中,使活性组分结构不破坏,如此循环反复。
根据此机理,催化剂需在氧的浓度大于硫醇浓度的前提下使用。
进行反应时,不需加入活化剂,也不需加入有机碱和无机碱,真正实现了无碱脱臭和不产生二次污染的碱渣。
实际生产的液化石油气中微量氧的浓度比硫醇的浓度高2~5倍。
该工艺采用2或3个固定床,将醇胺法脱H2S后的液化石油气,先脱去液化石油气中夹带的醇胺残液,后进入COS水解罐,将COS水解生成的H2S和醇胺法未脱尽的H2S脱除,最后进入催化氧化硫醇转化催化剂床,硫醇被氧化成二硫化物,简化了原工艺流程,消除了碱渣。
1.6 等离子体法南京工业大学张帆等学者研究了低温等离子体脱除液化石油气中的硫醇[9,34],考察了硫醇初始质量分数、停留时间、放电功率等参数对等离子体脱硫的影响,并分析了等离子体对液化气烃类组成的影响。
实验结果表明,低温等离子体能很好地脱除液化石油气中的硫醇,随着初始硫醇质量分数的降低、停留时间的增加和放电功率的增加都能提高硫醇的转化率。
等离子体法脱除液化石油气中硫醇的机理可分为两部分:一是由等离子体产生的电子直接与硫醇分子碰撞,从而使其电离、解离和激发;二是在电场作用下获得加速动能的带电粒子(特别是电子)与气体分子碰撞使气体电离,加之阴极二次电子发射等其他机制的作用,产生各种自由基和活性基团,包括OH和O原子等,它们和硫醇分子发生一系列的化学反应,从而形成其他对环境无害的物质,实验推断最终产物是单质硫、二硫化物及三硫化物。
在上述各方法中,Merox法及其改进方法和ThiolexSM技术是目前LPG脱硫醇的主要方法。
而催化氧化法与吸附法相结合效果较好,污染小,是未来研究的重点方向。
2 结语随着经济发展,世界各国对LPG的需求量正在逐渐上升,特别是作为化工原料的需求增加较快,LPG脱硫醇是保证LPG进行深加工利用的关键。
Merox抽提-氧化法脱硫醇技术是目前炼油厂LPG脱臭的主要方法,随着环保意识的增强,对其研究特别是机理研究会更加深入。