最新解决问题五原则表
问题解决5原则表的作成和运用指南

■不良现象的要因调查
・「什么时间、在哪个工序、发生了 什么?」
⇒锁定对象工程和对象批量 ・一般的记入内容
・工程的确认 ・每次确认的时候有无引起相关 不良的可能性 ・工程调查结果
工程履历、数据、作业记录 调查作业者的结果
5原则表的作成 (2)原因の究明
实施2种原因的究明!
別紙デ-タ10参照
○:マツダ様にて確認結果、 接点部導通しっぱなしなし
○:メカでの強制 O FF構造であ
接点溶着
り接点溶着なし
別紙デ-タ11参照
組み付け手順 間違い
○:マツダ様にて確認結果、 組付け手順に問題なし
スイッチ内部ズレ
バネ 不良
×:現象確認
別紙デ-タ3,4参照
下ケース
摺動体
接点
ランプ 接点組成
第2阶段 <对象扩大>
出荷
顾客
顾客索赔
必须! 第1阶段
5原则表的作成运用要点
①首先要优先于开始活动! 不要对策后才报告 ⇒中途经过也可以要向顾客迅速报告!
②不能只有QC担当者作成! 由主要因部门作成、QC协助、承认是基本的途径。 ⇒若是生产的要因那就是制造、设计的要因是技术… 当然要用CFT作成讨论
通过对问题进行4个合理的思考过程分析,从而得出正确的结论。
自然人的思考过程=从以下4个角度进行反复提问,对其结论进行持续考虑。 ①什么课题?(WHAT) ②为什么会那样?(WHY) ③怎样入手解决?(HOW) ④若什么的话会不会引起什么?(IF)
◎状况把握过程(略称SA=Situation Appraisal) 引起什么?→课题是什么?
要点:「目前的处置怎么办?」 首先要检讨不能扩大顾客困惑的处置方法。
5原则表
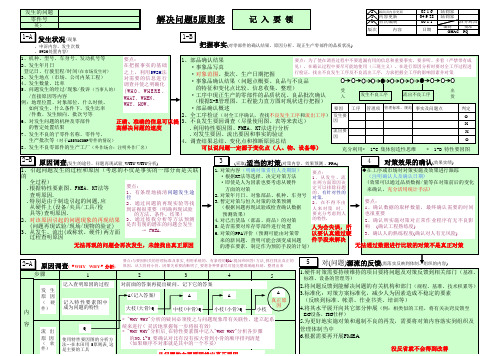
发生状况(现象、申诉内容、发生次数、5W2H处置内容)(使用反面)1、机种、型号、车身号、发动机号等2、发生年月日登记日、行驶里程/时间(在市场发生时)3、发生地点(市场、公司内某工程)4、发生数量、比率5、问题发生的经过/现象/投诉(当事人的)/直接原因等内容例:地理位置、对象部位、什么时候、如何发生、什么条件下、发生比率/件数、发生倾向、批次号等6、对发生问题的机种及零部件的暂定处置结果7、发生不良的子零件名称、零件号、生产批次等(对于ASSY&COMP 零件的情况)8、发生不良零部件的生产工厂(外作场合:注明外作厂名)内容记入要领要点:在把握事实的基础之上,利用5W2H 法对需要的信息进行调查并使之明确化(WHO 、WHERE 、WHAT 、WHEN 、WHY 、HOW 、1、部品确认结果·事象品写真·对象范围、批次、生产日期把握·事象品确认结果(问题点概要、良品与不良品的特征和变化点比较、信息收集、整理)·工序中现正生产的零部件的品质状况、良品批次确认(根据X-R 管理图、工程能力直方图对现状进行把握)·部品确认概述2、全工序检证(对全工序确认,查找不良发生工序和流出工序)3、不良发生要因调查(尽量使用图、表等来表达).利用特性要因图、FMEA 、KT 法进行分析.对发生要因、流出要因和事实的验证4、调查结果总结、变化点和推断原因总结使用特性要因图的分析方法…在本田用5原则表,这是主要的工具充分利用*1-C 集体创造性思维*1-D 特性要因图1-B12345记入查明原因的过程记入特性要素图中成为问题的特性发生原因(硬件)流出原因(软件)对前面的答案再提出疑问、记下它的答案A(记入答案)AA A 大枝(大骨)Q Q中枝(中骨)Q小枝小枝(小骨)Q真正原1、引起问题发生的过程和原因(考虑的不仅是事实的一部分而是关联的全过程).根据特性要素图、FMEA 、KT 法等查明原因..特别是由于制造引起的问题,应从硬件上(设备/夹具/工具/检具等)查明原因.2、对该原因引起的问题现象的再现结果(问题再现试验/现场/现物的验证)3、从发生、流出(或称软、硬件)两方面过程查明原因2-B 1-A 2-A原因,从大骨到小骨,因果关系要清晰明了,要将各种要素尽可能完整准确地归纳、整理出来34要点:为了使在调查过程中不要遗漏有用的信息和重要事实,要多听、多看(严禁带有成见),在确认过程中要尽可能地使用(三现主义)。
解决问题五原则表

作成部门
接收部门 日期 审批 确认
解决问题的5原则表
审批
确认
制作
1-A 问题定义--现象、投诉内容、发生件数、处置内容
1-B 问题定义(事实把握)--确认结果、分析原因、品质状况
2-A 找出根本原因(分析问题和回答)--根据特性要因图
问题① 为什麽② 显象(硬项目) 为什麽③ 为什麽④ 为什麽⑤
2-B 找出根本原因--问题和答案分析、问题产生过程、重复测试 根本原因的陈述
隐象(软项目)
3 纠正措施--内容、预期效果、潜在问题分析
4 确认措施--实际效果
5 反馈/下一步的行动
跟进日期:
解决问题的五原则
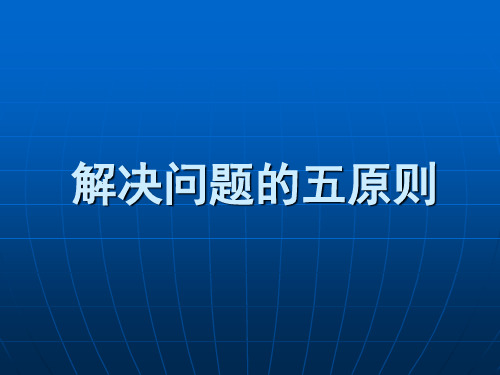
写好五原则表的关键:运用五原则手法分析、解决问题
五原则表的表达要求
要用简单、具体、准确的表述语言填写事实,不要 使用抽象性、否定性(确实、正确、避免、不要、 可能等)的语言。 要求插入示意图、照片、路线图、表格等,这样, 在传递过程时,就可以使你表达的意思和阅读的人 理解内容的一致。 ①.尽量使用短句写 ②.用小学六年的孩子能理解的话写
解决问题的五原则
五原则的定义
“五原则”是指从“三现主义”出发,分五个步骤解决问题
充分把握事实 查明的真正原因 实施切实的对策 确认对策的有效性 反馈到问题的源头
1
五 个 步 骤
2
3 4 5
三现主义
不但适用于制 造现场,也适 用于广泛的其 它工作。
亲自接触实物
亲自到现场
(现物)
总是以事 实为基础 而行动
异常对应难以预测的现象: 临时调休 突发的产品质量问题 突发的设备故障 到货材料、零件异常 停电、地震、洪灾、台风等
工厂是避免不了变化 点的,问题是对变化 点有没有制定正确的 对应方法
三、充分把握事实—2
<要因变化点的确定>
4M变化点
人 变化点的具体事例
(批次追踪及变化点调查)
对预测的变化点,没有进行 正确的管控时也会发生问题
③.用小学六年之前学过的汉字写
④.尽量不要使用专业性很强的文字和西洋文字 (英 、日文)写
五原则表填写要领
01.标题
发生状况 现状把握
02.发生状况
1-1 不良品确认 结果
合适 的 对 策
1-2 批次跟踪 变化点调查
1-3 原因分析
查 明的原 因
检查对 策 的效 果
2-1.查明的原因 发生机理 再现试验
5原则表填写说明

作业要领书的修改
□要 □否
条件表的修改 其他
□要 □否 □要 □否
18/23
19/23
通过对标准类(QC工程图、检查基准书、作业指示书)的 完善,明确再发防止策、对策实施效果的继续・维持方法。 ①判断需要对哪些文书进行修改。
作业标准类:PQC、检查基准书、作业指导书、包装 类指导书、作业要领书,条件表等
①取得正确的事实. ②针对发生及流出原因,用分析图明确表示 ③明确不具合发生基本原因. ④反复为什么为什么找到真正发生的原因. (更进一步使用春风分析图分析原因) ⑤进行适当对策并实施. ⑥反映到标准类、体系中. ⑦确认效果及数值.
1 3
6/23
2
5 4
6
1.发生状况(现实)
7/23
①.现象·投诉内容
□要 □否
担当
纳期
检查基准书的修改
□要 □否
作业指导书的修改 手顺书的修改
□要 □否 □要 □否
PIR记录项目变更
□要 □否
日常/定期点检项目变更
□要 □否
保养项目变更 异常处理方法变更
□要 □否 □要 □否
图面(治工具/金型/制品)的修改 □要 □否
FMEA的修改 包装类指导书的修改
□要 □否 □要 □否
发 生
内
容
流 出
探明原因[采用系统图法进行分析。] 从各个角度反复重复为什么为什么,抓住根本性真 正原因明确填写认为是最受影响的项目。
现象
为何发生
为什么
为什么
为何流出
为什么
为什么 为什么
为什么 为什么 为什么 为什么
为什么 为什么 为什么 为什么 为什么 为什么 为什么 为什么
对策五原则模板

对策五原则1. 背景和问题描述在处理问题时,我们经常需要找到解决方案。
对于复杂的问题,制定一套有效的对策是非常重要的。
对策五原则是一种帮助我们在制定对策时思考和分析的工具。
本文将介绍对策五原则的基本概念和使用模板,以帮助我们更好地解决问题。
2. 对策五原则概述对策五原则是以下五个关键问题,用于制定解决问题的对策:•目标是什么?:明确问题的解决目标,确保对策的制定与目标一致。
目标应该是具体、可衡量的。
•问题出在哪里?:识别问题的根本原因和关键因素。
了解问题的本质是解决问题的第一步。
•解决问题的方法是什么?:制定具体、可行的对策来解决问题。
对策应该能够解决问题的根本原因,并且可以在实践中操作。
•实施对策的方案是什么?:制定实施对策的具体方案和步骤。
考虑资源、时间和风险等因素,制定详细的实施计划。
•监控进展的指标是什么?:制定评估对策实施效果的指标和方法。
根据指标监控对策的实施进展,并根据实际情况进行调整和改进。
3. 对策五原则模板下面是一个用户友好且易于理解的对策五原则模板:3.1 目标明确问题的解决目标,确保对策的制定与目标一致。
目标应该是具体、可衡量的。
•问题描述:清楚地描述当前问题或挑战。
对问题进行分析,并确定需要解决的具体问题。
•目标定义:根据问题描述,明确解决问题的目标。
确保目标具体、可衡量,并与问题一致。
3.2 问题分析识别问题的根本原因和关键因素。
了解问题的本质是解决问题的第一步。
•问题原因:分析问题的根本原因。
这可能涉及到对问题进行深入调查和研究。
•关键因素:确定影响问题的关键因素。
这些因素可能包括内部和外部因素,需要理解它们是如何影响问题的。
3.3 对策制定制定具体、可行的对策来解决问题。
对策应该能够解决问题的根本原因,并且可以在实践中操作。
•对策方案:根据问题分析,制定解决问题的对策方案。
确保对策具体、可行,并与问题原因相关。
•对策操作:将对策方案转化为具体操作步骤。
确保对策可以在实践中操作,并达到预期效果。
最新三现五原则
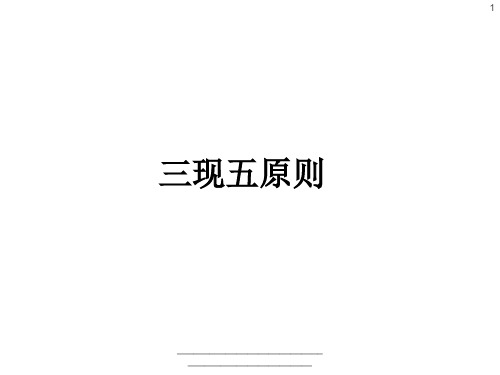
解决问题的五原则报告表
5
“解决问题五原则报告表”是运用五原则手法解决问题后作成的总结报告资料。
1、充分掌握事实情况
2、查明真正的原 因
3、实施切实 的对策
4、确认对策 效果
5、反馈到 源流
写好五原则报告表的关键_:___运__用___五__原___则___手__法___解__决___问题
1
三现五原则
___________________________ _______________________
五原则的定义
2
“五原则”是指从“三现主义”(现场、现物、现 实)出发,分五个步骤解决问题。
1 充分掌握事实情况 2 查明真正的原因
五个步骤是: 3 实施切实的对策
4 确认所采取的对策是否有效
见下页
___________________________ _______________________
五原则的填写说明-发 生 状 况(现象、投诉内容、发生件数、处置内容)
7
填入内容:
1、机种、型号、车架号、发动机号、批次号等 2、发生不良的子零件名称、零件号、 生产批次等 (对于总成或组件的情况)出货品的 确认结果 3、发生不良零部件的生产工厂(外作场合:注明外作 厂名) 4、发生年月日/ 登记日、行驶里程/时间(在市场发生时 ) 5、问题发生的经过/现象/投诉(当事人的)/直接原因 等内容 6、对发生问题的机种及零部件的暂定处置结果
(WHEN)何时:记入问题发生的日期 (WHERE)何地:记入问题发生的场所 (WHY)为什么:具体的内容
至少要问5个为什 么(WHY),具体参
解决问题的五原则分析

解决问题的五原则
五 原 则 的 定 义
“五原则”是指从“三现主义”(现场、现物、现 实)出发,分五个步骤解决问题。
2
1
充分掌握事实情况
2 查明真正的原因
五个步骤是:
4
3 实施切实的对策 确认所采取的对策是否有效
5 反馈到发生问题的源流
三现主义的定义
不但适用于制造现场,也适用 于广泛的其它工作 。
五原则的填写说明-Байду номын сангаас
8
事 实 的 把 握(部品的确认结果、原因分析、生产品的品质状况)
目标 1、为探明部品、部位的原因; 2、变化(工序与用户的使用方法)产生不良, 为了一针见血找到变化和限定批次。 见下页
五原则的填写说明-
填入内容:
9
事 实 的 把 握(部品的确认结果、原因分析、生产品的品质状况)
◆等待生产现场的联系或生产现场对于技术、品质、资材等部门服务、指导、指示、供应的等待。等待下级 的汇报,任务虽已布置,但是没有检查,没有监督。不主动去深入实际调查研究,掌握第一手资料,只是被动 地听下级的汇报,没有核实,然后作决定或向上级汇报,瞒天过海没有可信度,出了问题,责任往下级身上 一推。“三现主义”的缺乏是等待中的最致命原因之一,严重影响生产现场工作的及时解决。
三现主义在中国用得很早:远点,“捉贼捉脏, 捉奸捉双”;近点,毛主席的“没有调查研究 就没有发言权”;再近点,;新闻工作者不也是 天天在掌握第一手材料么?谁和谁有拍拖之 嫌呀,哪个和哪个出现在某酒店啊,这都是三 现主义的运用,可是中国的三现主义只用于 政治或只用于整人,很少用于品质管理。
三现主义的定义
①不良品 制造工序条件 ②不良品 制造年月日 ③不良品 发生个数、概率 …等,用工序系列、时间系列整理。
解决问题的5原则

试验温度
☆向其它部门提供信息 ①空军 46/02~ ②海军 46/02~ ③警察 48/03~
题目 零件号 零件名
分析记录[解决问题5原则表] 运用渠道1.要求对策时:编制部门 (报告单位) 2.其它、编制部门(编制-保管)
编 制 部 门
部室名或供货方名 年 月 日
—对策要求时→
要求报告不良对 策时,应付上不 良对策
解决问题的5原则
1. 把 2. 究 握 明 事 原 实 因
See Think Plan→Do Check Action
3. 合 适 的 对 策 4. 确 认 效 果
5.向 源 头 的 反 馈
六种教训
其一 不论什么报告也不一定 传达的完全准确、 其中可能隐蔽着 重要的事实。 其二 适切数据的收集和分析、 以此把因当事人的经验和观察力 所隐藏的重要的事实挑出
-25
o o o o o o o o o o
-30
o o o o o o o o o o
-35
x x o o o o o o o o
-40
向源头反馈(反映体制、计划内容) 1.硬件对策要继续保持 反映项目计划(基准、标准类) 2.成为原因的项目排除掉 反映机制计划(向横向波及 向横向水平展开 )(规程、基准、 )(规程、 技术积累等 基准、技术积累等 ) )
2
大的分支 流 采用特性要因图查出问题的特性 出
中分支
小分支
真正的原因
送弹部被破坏 勃朗宁机关枪的 破坏(中弹)
由于压力上升发生 爆炸 陆军的规格、只有 -20℃
颗粒呈切断固体状火 药的粘结剂在低温下 变脆、受到振动
陆军是根据冬季战场 经验设定为-20℃的
下降到-30℃后、 火药的粘结剂变脆 (根据再现测试)
QA07-解决问题的五原则

三、充分把握事实—1(不良品的确认结果)
1)现品的状态 <要点> 针对问题现物,不仅要记录不 良处,还要仔细观察,留 下更多记录
什么样形状的零件的什么部 分有问题?用简略图表达的 话较容易理解和判定
简略示意图或照片
2)明确与合格零件的不同之处 有必要的话在互换检查中判定零件状态
3)和图纸对照(或以公司内控基准、品质规定判断)
对其它变化点结合进行分析
3)要因分析包含如下内容
分析各种各样的原因,列出能想到的发生/流出原因 ■这里出现的原因仍属推测不是事实 ■这些项目是不是真因?需进行再现试验
■
○:排除在要因外 △:直接原因、关联原因 ×:二次、三次致命要因
×:致命要因 流出原因 检验标准漏掉螺 丝与橡胶粘接强 度扭力检查项目 末端原因 螺丝涂胶及涂胶 后摆放没有制定 工艺规定
1、确认数据的取样数量和时间段,这很重要 2、确认所实施对策对正常作业程序有无不良影响 3、确认人的熟练程度(评估人有无风险)
七、反馈到问题的源头(系统、机制、流程等)
1)分析为什么、为什么
<要点> 明确源头原因,从原因开始进一步深入 思考,没有反省的地方就没有改善
2 3 4 5
阶段 发生 内 容
异常对应难以预测的现象: 临时调休 突发的产品质量问题 突发的设备故障 到货材料、零件异常 停电、地震、洪灾、台风等
工厂是避免不了变化 点的,问题是对变化 点有没有制定正确的 对应方法
三、充分把握事实—2
<要因变化点的确定>
4M变化点
人 变化点的具体事例
(批次追踪及变化点调查)
对预测的变化点,没有进行 正确的管控时也会发生问题
△:直接原因 转向灯橡胶柄中 的螺丝与橡胶粘 结松脱
解决问题的五原则
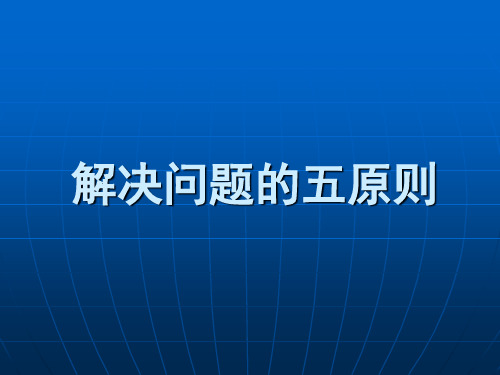
发
临时调休
点有没有制定正确的
的 变 化 点
突发的产品质量问题 突发的设备故障 到货材料、零件异常 停电、地震、洪灾、台风等
对应方法
三、充分把握事实—2 (批次追踪及变化点调查)
<要因变化点的确定>
对预测的变化点,没有进行 正确的管控时也会发生问题
4、发生数量:明确不良数量、不良率 车架/发动机号、购买日期、行驶里程(如果是市场发生时)
从反馈 部门得 到正确 的信息
5、发生现象:在什么情况下发生的? ●外观、装配问题可简单描述 ●动态问题要详尽描述:离合器手柄作动不顺畅!详尽:哪种角度还是全角度?
6、处理情况 发生问题的车(机)型及零件的处理内容 ●怎样处置:换装、挑选、调整、返修等
变化点 固定、反复的作业
通常这个能持续的话就 不会发生问题
可
非固定、非定期的作业
预
机种准备
测
夹具、刀具、设备、模具维修
由于有这样的事情出现导 致问题发生时就被定义 为要因变化点(见下页)
的
工艺变化、加工方法变更
变
零件更换
化
避免不了变化
突
异常对应难以预测的现象: 点的,问题是对变化
2日
3日
100
100
100
100
300
问题对象批次
4日
5日
100
/
100
100
变人
化 设备
☆设备变更了
点 方法 基于4M进行变化点的调查
材料
<批次追踪及变化点调查结果>
1)问题批次是×月×日~ ×月×日生产的××台
2)对象批次的变化点是什么?
<要点> 问题的发生总是 由变化点引起
解决问题的五原则

★可以说问题一定 源于变化点 ——变化点势必引 发事故——
9
“请三思而后行!不要轻易下结论”,一切皆有可能!
有一天美国通用汽车公司的庞帝雅克部门收到一封客户抱怨信:我们家每天在晚饭后都由全家人投票决定买何种口味的冰 淇淋, 每当我买的冰淇淋是香草口味时,我从店理出来车子就发不动,但如果我买的是其它的口味,车子发动就顺得很。 事实上庞帝雅克的总经理对这封信还真的心存怀疑,但他还是派了一位工程师去查看究竟。工程师去找这位仁兄时,工程 师安排与这位仁兄的见面时间刚好是在用完晚餐的时间,两人于是一个箭步跃上车,往冰淇淋店开去。那个晚上投票结果是香 草口味,当买好香草冰淇淋回到车上后,车子又不能发动了。这位工程师之后又依约来了三个晚上。第一晚,巧克力冰淇淋, 车子没事。第二晚,草莓冰淇淋,车子也没事。第三晚,香草冰淇淋,车子不能发动。 这位思考有逻辑的工程师,到目前还是死不相信这位仁兄的车子对香草过敏。因此,他仍然不放弃继续安排相同的行程, 希望能够将这个问题解决。工程师开始记下从头到现在所发生的种种详细资料,如时间、车子使用油的种类、车子开出及开回 的时间„,根据资料显示他有了一个结论,这位仁兄买香草冰淇淋所花的时间比其它口味的要少。 为什么呢?原因是出在这家冰淇淋店的内部设置的问题。因为,香草冰淇淋是所有冰淇淋口味中最畅销的口味,店家为了 让顾客每次都能很快的取拿,将香草口味特别分开陈列在单独的冰柜,并将冰柜放置在店的前端;至于其它口味则放置在距离 收银台较远的后端。 现在,工程师所要知道的疑问是,为什么这部车会因为从熄火到重新激活的时间较短时就会不能发动?原因很清楚,绝对 不是因为香草冰淇淋的关系,工程师很快地由心中浮现出,答案应该是“ 蒸气锁”。因为当这位仁兄买其它口味时,由于时 间较久,引擎有足够的时间散热,重新发动时就没有太大的问题。但是买香草口味时,由于花的时间较短,引擎太热以至于还 无法让“ 蒸气锁 ”有足够的散热时间。
解决问题五原则示例

²机种、型号:SDH-HA6(零件确认结果)²发生年月日:²用检具测定部品²发生件数:²发生场所: 广州本田AF 线上²投诉内容PIPE X 在发动机舱内和其他部品间隙过小P17²现象P18P19①间隙过小P20规格值:≥ 5mm 高H+实测值:1mmP21T+P22P23②难组装P24²处理:进行库存确认确认场所确认数量及处置Point23处曲率确认:广州本田90根中30根不良AF Line side —不良品作退货处理,并立即补充OK 品CC 物流公司无基准R=60±5广州 A A 有限公司60件不良(完成品)(设备确认)²设备管理记录显示²受理委托日期:²机种切换时,夹具、辅助滚轮、电²要求回复期限:(发生的途径)1、发生原因2、流出原因检具²机种切换时,夹具、辅助滚轮、电脑程序等都要作相应调整。
机种切换,实施设备的调整A²辅助滚轮调整不良再现试验23point 加工图示尺寸要求:74mm2003年11月23日2003年12月3日2003/11/2330零件名称PIPE X发生的问题PIPE X 形状不良(和其它部品间隙过小)零件号46xxx-Sxx-A0001、发生状況(现象²投诉内容²发生件数²处理内容)2、事实的把握(零3、原因调查(发生的途径、机理²问题的再现试验²为什么、为什么分析结果)把辅助滚轮调整致71mm 时,23point 的曲率² 端末部的检具槽为可动式设计,最大容许的活动量为 23 mm ,如下图所示:²通过检具进行零件的确认时A 部放大螺帽锁紧时位置容易发生偏移2~3mm容易忽略上述活动量,6结论:而导致错误的判断。
作业手法不熟练,辅助滚轮调整后锁紧时位置发生偏移,误将NG 品判定为合格锁紧后也没有再测量确认,从而导致加工的零件形状不良,装车后与其他部品配合间隙偏小。
- 1、下载文档前请自行甄别文档内容的完整性,平台不提供额外的编辑、内容补充、找答案等附加服务。
- 2、"仅部分预览"的文档,不可在线预览部分如存在完整性等问题,可反馈申请退款(可完整预览的文档不适用该条件!)。
- 3、如文档侵犯您的权益,请联系客服反馈,我们会尽快为您处理(人工客服工作时间:9:00-18:30)。
题 目运用方法:零部件编号 1.根据对策要求的场合:作成部门→对策要求部门(报告处)确认作成
责任人零部件名称
2.其他的场合:作成部门(作成→保管)Ⅱ机种:/J64K 后事项品处置:一、现品调查结果:2、平面度与焊接状态的关系验证
部番:/对在库的总成,单品,半成品1、不良品发生调查:
事项内容:焊接剥离.进行了全数返检。
不良类别:焊接不良返检方法:用橡胶榔头敲击3次发生地:福特敲击时距离100mm.
发生原因:
临时对策:
效果跟踪:1、对CNS在库造成全数进行返检;(用橡胶锤敲击防尘盖)
担当:杨茂盛;完成时间:08/07/10
整平模具已进行了修理,整平后骨架经焊接后试验合格(验证品6件)见附件报告。
2、对中鼎减震在库零件全数进行敲击返检,验证试验计划:08/06/30.生产数量:30件。
合格品作蓝色检查标识;
担当:涂家林;完成时间:08/05/26
3.对中鼎精工单件骨架全数进行敲击返检, 合格品作蓝色检查标识;
担当:周春芳;完成时间:08/05/26
永久对策:
1、增加滑块锁紧螺母的检查频度。
由1次/1天变更为1次/4小时担当:邹昌辉;完成时间:08/06/03
2.改进整平模具,保证上骨架焊接面的平整度在0.2mm之内;担当:杨正才;完成时间:08/06/03。
3.增加焊接性能抽检比例,对焊点外观100%进行普检,并用橡胶锤敲击;
担当:周春芳;完成时间:08/06/03。
修订QC工程管理表及相关作业文件。
1.将焊接面平整度纳入必须控制项目;经试验平整度在0.2mm之内的骨架焊接性能OK。
(见附件报告)
2.重新制定焊点外观和焊接性能检验作业文件。
担当:陈鸿萍、甘洁完成时间:2008/06/03
步骤解决问题五原则表
焊接剥离
作成部门
部门或分承包方
不良品接受日:080520发生时间:08/05/19维修时间:
见附件1
08 年 06月 27日
报
告处
宁江昭XB2E2-630-0B-CS 安徽中鼎负责人
对策要求场合→
骨架总成
程飞跃
Ⅵ、对源流的反馈(在体制组织上的反映内容)
Ⅴ.对策效果的确认(实际效果)Ⅲ.原因追究(发生的机械性、再现实验、层层原因分析) Ⅳ.适当的对策周春芳
Ⅰ发生状况(现象、报告内容、发生件数、处置内容)事实的把握(零部件的确认结果、原因分析、流动品的品质状况)内容
冲床滑块锁紧螺母
松动,工作时滑块
行程增加翻边整形时压力增加引起上骨架焊接面变形整平工序未对焊接面
起到应有的整平效果
车架号:行驶里程:1~2Km 组装日:080414
下骨架凸焊点与上骨架未熔合,产生虚焊。
性能检测为抽样检测,极少数不合格品不能
发现
焊接时,上骨架焊接面与下骨架
焊接凸点不能完全熔合
12345
①、由于骨架总成装车后,在福特路试异响,发现4点虚焊,上下骨架分离。
②、用塑料棰敲击该批次骨架,对发现失效件进行检测,发现上骨架焊接面明显不平,平面③、对上骨架加工生产流程进行排查,翻边整形工序中冲床的行程发生变化--行程增加。
引起上骨架焊接面不平
上骨架平整度0.5。
焊接后检查有1、2点母材撕裂。
焊接状态NG 。
上骨架平整度0.6.焊接后检查4点母材都没有撕裂。
与事项品破坏的焊接态相同。
2、滑块行程发生位移,行程逐渐增加。
3、下道整平工序对上骨架焊接面未起到应有的整平效果;且作业文件未要求对焊接面的平整度进
4、由于上骨架焊接面不平整,焊接时在0.5MPa 的压力下,上骨架与下骨架焊接凸点不能完全贴合。
5、下骨架凸焊点未完全熔合于上骨架中,导致上、下骨架产生虚焊、剥离。
由于性能检测为破坏性试验,我司在生产和出厂时焊接性能检测为抽样检测,故极少数不合格件不能发现,导致焊接NG
1、上骨架翻边整形工序,冲床的滑块的锁紧螺
⑷、冲床滑块的锁紧螺母松动。
不良事项:骨架总成
焊接剥离图片
3、行程增加到一定程度后,上骨架变形加剧。
导致焊接面严重变形。
平面度达0.5以上。
再现试验:
1、冲床滑块行程变化再现试验:对该冲床作业时滑块的变化进行进行了定期确认。
冲床工作一段时间后,锁紧螺母产生了松动。
滑块行程发生了变化,逐渐增加。
滑块松动前上骨架焊接面平面达0.3.滑块位移后平面度达0.5~0.6。
结论:证明了滑块增加后会导致平面度增加。
2、平面度与焊接状态的再现实验:见《附件焊接面平整度分析》。
结论:上骨架平面度不平达0.5以上是造成焊接状态NG 的原因。
市场多发性预测:
1、对象范围:07/9~08/5。
共生产件数:51076件。
2、在库品检查结果统计:共
返检24952件
不良件数7件。
不良率0.028%。
通过CNS 统计:长安福特装成整车台数为13062台,26124件。
4点母材没有撕裂。
宁江昭和
确认
没有撕
的焊接状.
整平模具已进行了修理,整平后骨架经焊接后试验合格(验证品6件)见附件报告。