(整理)D-对羟基苯甘氨酸的生产工艺.
d-对羟基本甘氨酸甲酯盐酸盐生产工艺规程
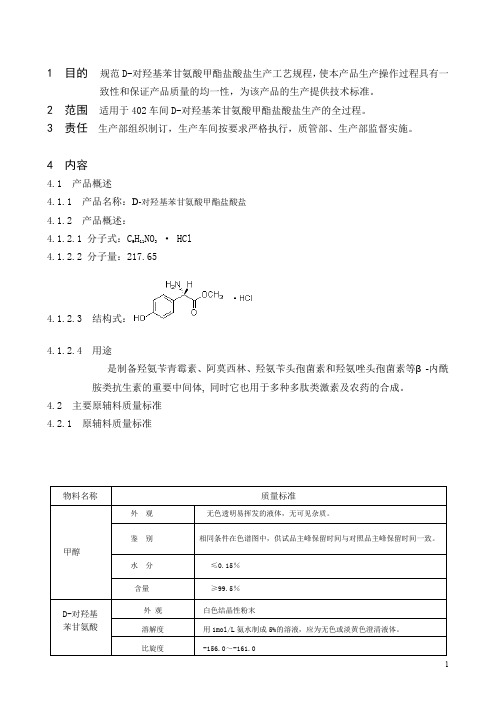
1 目的规范D-对羟基苯甘氨酸甲酯盐酸盐生产工艺规程,使本产品生产操作过程具有一致性和保证产品质量的均一性,为该产品的生产提供技术标准。
2 范围适用于402车间D-对羟基苯甘氨酸甲酯盐酸盐生产的全过程。
3 责任生产部组织制订,生产车间按要求严格执行,质管部、生产部监督实施。
4 内容4.1 产品概述4.1.1 产品名称:D-对羟基苯甘氨酸甲酯盐酸盐4.1.2 产品概述:4.1.2.1 分子式:C9H11NO3· HCl4.1.2.2 分子量:217.654.1.2.3 结构式:4.1.2.4 用途是制备羟氨苄青霉素、阿莫西林、羟氨苄头孢菌素和羟氨唑头孢菌素等β-内酰胺类抗生素的重要中间体, 同时它也用于多种多肽类激素及农药的合成。
4.2 主要原辅料质量标准4.2.1 原辅料质量标准物料名称质量标准甲醇外观无色透明易挥发的液体,无可见杂质。
鉴别相同条件在色谱图中,供试品主峰保留时间与对照品主峰保留时间一致。
水分≤0.15%含量≥99.5%D-对羟基苯甘氨酸外观白色结晶性粉末溶解度用1mol/L氨水制成5%的溶液,应为无色或淡黄色澄清液体。
比旋度-156.0~-161.0吸光值用1mol/L HCl 制成浓度5%的溶液吸光值应:≤0.040用1mol/L NaOH 制成浓度为5%的溶液吸光值应:≤0.100含 量≥99.0% 水 分 ≤0.30%氯化亚砜外 观无色至淡黄色透明有刺激性臭味的液体。
密度(20℃) 1.630~1.650 色度,(K 2CrO 4)≤1#沸程,75-80℃%(V/V ) ≥99.0 %水质符合饮用水标准。
4.3 化学反应过程及生产工艺流程图 4.3.1 化学反应式:+ CH 3OH4.3.2 工艺流程图(见附表)温度D-对羟基苯甘氨酸甲醇氯化亚砜合成罐D-对羟基苯甘氨酸甲酯盐酸盐4.4 生产工艺过程往合成反应罐中加入D-对羟基苯甘氨酸450kg、750Kg、825Kg、900Kg、1000Kg、1500Kg, 甲醇1600L、2800L、3000L、3300L、3700L、5600L。
D-对羟基苯甘氨酸生产新工艺研究
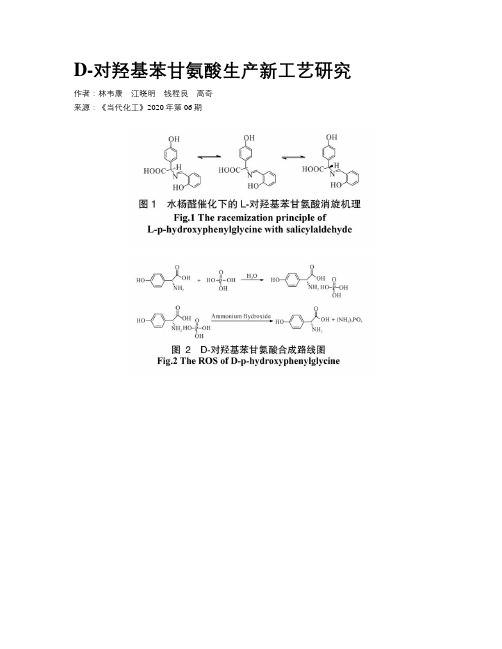
D-对羟基苯甘氨酸生产新工艺研究作者:林韦康江晓明钱程良高奇来源:《当代化工》2020年第06期Study on a Novel Production Process of D-p-HydroxyphenylglycineLIN Wei-kang1, JIANG Xiao-ming1, QIAN Cheng-liang1, GAO Qi2(1. Zhejiang Yuntao Biotechnology Co., Ltd., Shaoxing Zhejiang 312369, China;2. Aiyinuo Technology Co., Ltd., Zhuji Zhejiang 311800, China)对羟基苯甘氨酸(D-p-Hydroxyphenylglycine),分子式C8H9NO3,分子量167.16,是以苯酚为起始原料,先经合成反应制得DL-对羟基苯海因或DL-对羟基苯甘氨酸,再经酶法(原料为DL-对羟基苯海因)或化学拆分(原料为DL-对羟基苯甘氨酸)制得。
D-对羟基苯甘氨酸是合成β-内酰胺类半合成广谱抗生素(如青霉素类、头孢菌素类等)侧链的重要原料,也是合成抗菌和抗病毒药物、人工甜味剂的重要中间体[1-2]。
2017年6月6日,世卫组织在《2017年基本药物标准清单》中将阿莫西林这种广泛用于治疗肺炎等感染的抗生素划归为“可用类”[3]。
另外,随着国家安全、环保整治力度的加大,国内很多安全或环保不达标的D-对羟基苯甘氨酸生产企业永久退出市场,在这样的背景下,开发一种更安全、更环保、成本更低的D-对羟基苯甘氨酸生产工艺是非常有意义的。
目前,国内DL-对羟基苯海因和DL-对羟基苯甘氨酸的生产工艺已经相对成熟,生产成本已基本没有下浮空间,但国内外D-对羟基苯甘氨酸生产企业的工艺水平参差不齐,这里对典型的几種D-对羟基苯甘氨酸生产工艺进行比较分析。
第一种,以D-3-溴樟脑-8-磺酸或1-苯基乙磺酸或萘酚磺酸或邻甲基苯磺酸为拆分剂,在催化剂水杨醛的存在下,边拆分DL-对羟基苯甘氨酸边消旋L-对羟基苯甘氨酸,得到D-对羟基苯甘氨酸拆分剂复盐,再经水解制得D-对羟基苯甘氨酸,水解母液用酸再生得到可以循环套用的拆分剂[4-9]。
D-对羟基苯甘氨酸的制备
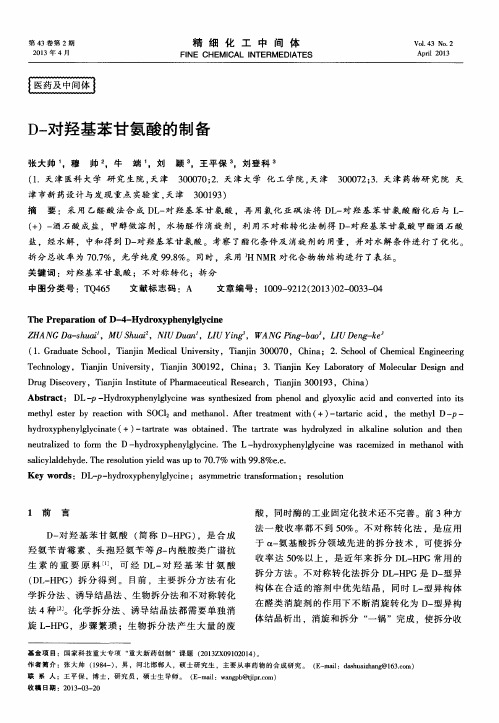
第4 3卷 第 2期
2 0 1 3年 4月
精 细 化 工 中 间 体
F I NE CHE MI CAL I NTERM EDl ATES
Vo 1 . 4 3 No . 2 Ap r i l 2 01 3
D 一 对 羟 基苯 甘 氨 酸 的制 备
张 大帅 ’ ,穆 帅 z 。牛 端 ’ ,刘 颖 0 ,王 平保 0 ,刘登科 s
( 1 . G r a d u a t e S c h o o l ,T i a n j i n Me d i c a l U n i v e r s i t y ,T i a n j i n 3 0 0 0 7 0 ,C h i n a ;2 . S c h o o l o f C h e m i c a l E n g i n e e r i n g
关 键词 :对 羟基 苯甘 氨 酸 ;不 对称 转化 :拆 分
中图分 类号 :T Q 4 6 5
文献标 志 码 :A
文章 编号 :1 0 0 9 — 9 2 1 2 ( 2 0 1 3 ) 0 2 — 0 0 3 3 — 0 4
DL-对羧基苯甘氨酸技术

DL-对羟基苯甘氨酸技术(DL-HPG )1、名称:DL-对羟基苯基甘氨酸 DL-P-Hydroxyphenylglycine 2、化学结构:C 8H 9NO 3=167.163、 mp225~227℃,比旋度[α]D =0°,[D-mp240℃(分解), [°(C=1,1N HCl )]4、用途:DL-对羟基苯基甘氨酸是合成阿莫西林、头孢羟氨苄等的重要中间体。
5、 合成反应6、 工艺过程 6.2 操作6.2.1 在3000L 搪玻璃反应锅中,投入950㎏水,开动搅拌和夹套冷却水缓缓加入63㎏硫酸,分别再向釜内投630㎏氨基磺酸,540㎏苯酚和900㎏乙醛酸。
(苯酚事先应放置在烘房中熔化,m.p.43℃)。
6.2.2 反应时会发出热量,使其缓缓升温,控制反应温度70±2℃,反应8小时,反应完毕将反应料液压出二分之一到中和锅。
6.2.3 开中和锅搅拌,用30%浓度的液碱中和料液调节PH 值到4-5(3.5),继续搅拌5分钟复测PH 值正确无误,降温冷却至35℃以下,出料离心甩干,滤饼为产物,滤液经处理后排放。
反应锅中余下的一半料液压入中和锅,重复上述操作,得DL-HPG 粗品。
6.2.4 在3000L 洗涤锅中投入70%甲醇1600L ,开动搅拌投入约1200㎏DL-HPG 粗品,在常温下搅拌均匀即可离心分离,用少量甲醇冲洗滤饼,可得DL-HPG 约920㎏,含量≥98.0%,母液和洗液经蒸馏后套用,蒸馏浓缩物离心回收。
7、参考文献① 周华等,中国医药工业杂志,1998,29(11):519② Ger 1980:283118(CA 1980;92:921577s )③ 周华等,化学世界,1995;37(2):84 O H CH COOH2OHOHCHCOOH 2+CHOCOOH +NH 2SO 3HH O.H SO。
一种生产D-对羟基苯甘氨酸的方法[发明专利]
![一种生产D-对羟基苯甘氨酸的方法[发明专利]](https://img.taocdn.com/s3/m/cf5968df67ec102de2bd89ea.png)
专利名称:一种生产D-对羟基苯甘氨酸的方法专利类型:发明专利
发明人:谢建中,张芦苇,刘万民
申请号:CN201010267779.5
申请日:20100831
公开号:CN102382000A
公开日:
20120321
专利内容由知识产权出版社提供
摘要:本发明涉及化工、制药生产领域,具体地说是涉及一种生产D-对羟基苯甘氨酸的方法。
D-对羟基苯甘氨酸的制造方法。
包括以下步骤:(1)按重量比水∶D-对羟基苯海因∶氯化钠=100∶20-30∶1-3配置溶液作为反应液备用;(2)在上述反应液中加入10-15%碳酸铵溶液,边加入边搅拌,加入的碳酸铵重量是D-对羟基苯海因重量的10%,在25~30℃的情况下,至溶液中D-对羟基苯海因的含量为0.12%以下为止,结晶即得D-对羟基苯甘氨酸。
这样生产的D-对羟基苯甘氨酸的制造方法操作方便、不需要加热室温条件下即可、反应时间短为5-7个小时、产率高达75%的效果。
申请人:河南新天地药业股份有限公司
地址:461500 河南省长葛市市区轻工路东段南侧新天地药业有限公司
国籍:CN
更多信息请下载全文后查看。
d-对羟基苯甘氨酸甲酯盐酸盐(cep)生产工艺规程
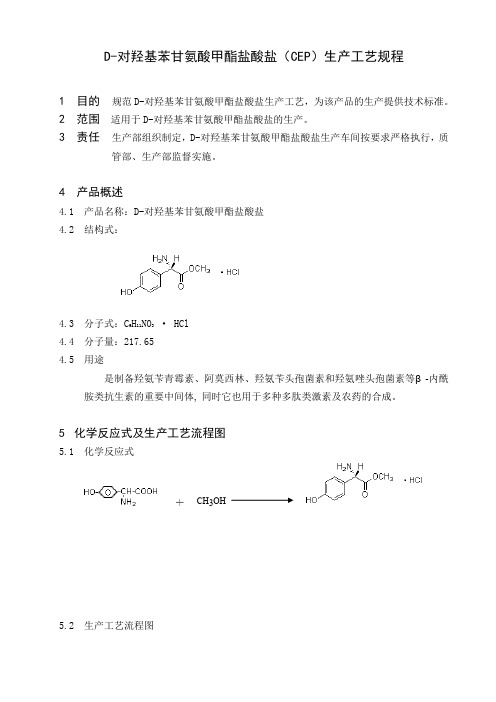
D-对羟基苯甘氨酸甲酯盐酸盐(CEP)生产工艺规程1 目的规范D-对羟基苯甘氨酸甲酯盐酸盐生产工艺,为该产品的生产提供技术标准。
2 范围适用于D-对羟基苯甘氨酸甲酯盐酸盐的生产。
3 责任生产部组织制定,D-对羟基苯甘氨酸甲酯盐酸盐生产车间按要求严格执行,质管部、生产部监督实施。
4 产品概述4.1 产品名称:D-对羟基苯甘氨酸甲酯盐酸盐4.2 结构式:4.3 分子式:C9H11NO3· HCl4.4 分子量:217.654.5 用途是制备羟氨苄青霉素、阿莫西林、羟氨苄头孢菌素和羟氨唑头孢菌素等β-内酰胺类抗生素的重要中间体, 同时它也用于多种多肽类激素及农药的合成。
5化学反应式及生产工艺流程图5.1化学反应式+CH3OH5.2生产工艺流程图甲醇、氯化亚砜工艺用饮用水物料 工序检验项目 控制参数注:带*的为中间体质量标准,其他的为中间控制质量标准。
6 生产过程、工艺条件、注意事项及常见偏差6.1 生产前准备岗位操作人员进入生产现场按岗位操作程序进行生产前检查。
如不符合要求,按相关SOP 重新处理并经车间质管员或授权人员确认后才可进行下一步操作。
6.2 原辅料领取、发放、验收6.2.1 车间领料员依据生产需求从仓库领取原辅料。
原辅料经检查品名、批号、规格、外包装无异常后才可领用。
6.2.2 注意事项6.2.2.1 物料应经检验合格并由质量管理部门批准放行后,方可使用,原辅料生产商变更后应通过小样试验,必要时需通过验证。
6.2.2.2 物料应做到帐、卡、物一致。
6.2.3 常见偏差及处理办法在检查原辅料的过程中如发现原辅料的外观形状、数量异常,应立即将异常的原辅料单独定置存放,并挂上“待处理”标示牌,明确物料状态。
并及时报告车间质管员,由车间质管员按偏差处理程序进行处理。
6.3 酯化反应工序 6.3.1 备料D-对羟基苯甘氨酸 酯化反应 D-对羟基苯甘氨酸甲酯盐酸盐温度、时间纯度溶解D-对羟基苯甘氨酸甲酯盐酸盐溶液 外观、含量*名称投料量D-对羟基苯甘氨酸 750kg甲醇 2800L氯化亚砜 400L工艺用饮用水 1800L6.3.2 操作过程6.3.2.1 将准备好的D-对羟基苯甘氨酸750kg投入酯化罐内。
制备D-对羟基苯甘氨酸新工艺

本文 介绍 的对 羟基 苯 甘 氨 酸拆 分 工 艺 以 D . 3 溴 代樟 脑 一 磺酸铵( 简称 D — A B C S ) 为拆 分 剂 , 冰
醋 酸为 溶剂 , 加少量 浓盐 酸或浓硫 酸 , 以水杨 醛 为催 化剂 , 使 目标 对 映体 的 拆分 及 非 目标 对 映体 的外 消
作者简介 : 李祖文 , 男, 1 9 6 3年 出生 , 1 9 8 6年毕业于沈阳药科大学 , 学 士学位 , 工程师 , 主要从事药物合成及生产管理工作 。
在此 过程 中起 着关键 的作用 … 。
2 0 1 3年 4月
李祖文等 。 制备 D 一 对羟基苯甘氨酸新工艺
・2 3・
对 羟 基 苯 甘氨 酸 在 自然 界是 不 存在 的 , 其 制 备
此, 所 得产 物存在 收率低 、 质量 差 的问题 。 理论上讲 , 一 次 结 晶过程 收率 可 达 5 0 %, 但 实
际上 只能 达 到 4 0 %左 右, 产 品 的光 学 纯 度 9 5 % 左
右 。在实 际工业 生 产 中 , 非 目标 对 映体 只有 重 复不
制备 D 一 对 羟 基 苯 甘 氨 酸 新 工 艺
李祖 文 , 郭剑虹
( 山 西博 康 药 业有 限公 司 , 山西 太原 0 3 0 0 2 1 )
摘要: 以D - 3 一 溴代樟脑 一 8 - 磺酸铵( 简称 D . A B C S ) 为拆分 剂 , 冰醋酸 为溶剂 , 加少 量浓硫酸 , 以水杨 醛为催化剂 , 使 目标对映体 的拆 分及非 目标 对映 体的外 消旋 化 同时进 行 , 获得高 收率 、 高纯 度的 D 一 对羟基苯甘氨酸 。
断地 进行 消旋 化 , 才 能 提高 目标对 映 体 的 收率 。 因
酶法生产D-对羟基苯甘氨酸提取方法综述
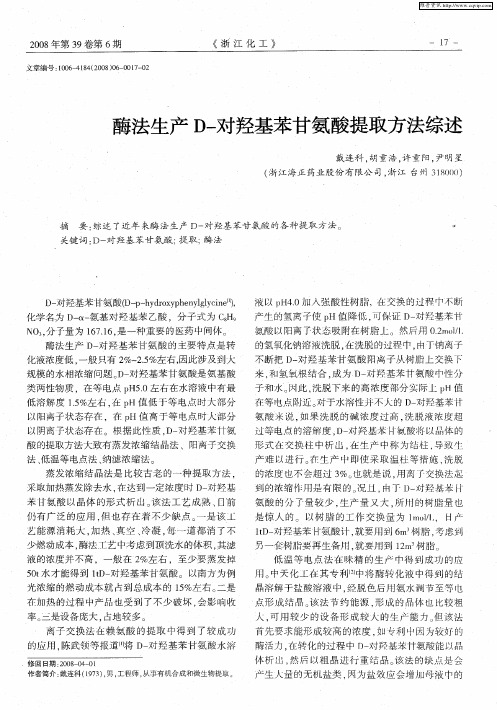
化学 名为 D 仪 氨 基 对 羟 基苯 乙酸 ,分 子 式 为 CH 一一 。
液 以 p 40加 入强 酸 性树 脂 ,住 交 换 的过 程 巾不 断 H.
产 生 的氢离 子使 p H值 降 低 , 保证 D 对 羟基 苯甘 可 一
氨 酸 以 阳离 了状 态吸 附在 树 脂 上 。然后 用 02 o I . l o t /
N 分 子量 为 171 , 一种 重要 的医药 中间休 。 O, 6、 是 6
酶 法 生 产 D 对 羟 基 苯 氨 酸 的 主要 特 点 是 转 一
的氢 氧化 钠溶 液洗 脱 , 洗脱 的 过程 巾 , 住 南丁钠 离 子
不 断把 D 对 羟 基 苯甘 氨 酸 阳离 子从 树脂 上 交 换 下 一
苯 氨 酸 以 晶 体 的 形 式 析 出 。 法 工 艺 成 熟 、 该 口前
仍 有 广 泛 的应 用 , 也 存 在着 不 少 缺 点 。 是 该 上 但 一 艺能 源 消耗 火 , 热 、 空 、 凝 , 一 道 都 消 了不 加 真 冷 每
是 惊 人 的 。 以 树 脂 的工 作 交 换 量 为 1 o/, 日产 m l I
( 浙江 海正 药业股 份 有 限公 司 , 江 台州 3 ( ) 浙 1 3 0
D—对羟基苯甘氨酸的合成方法及各自的优点

-,对羟基苯甘氨酸的合成1.1.对甲氧基苯甲醛法以上方法,合成收率为64.3%,拆分收率为73%,总收率约为47%。
该方法是早期用于工业生产D,L-HPG的合成方法,对甲氧基苯甲醛于氰化钠在水溶液或者醇溶液里面,经过环合,加压碱水解和脱甲基,得到D,L-HPG。
该工艺的优点是技术成熟,缺点是使用剧毒危险品氰化钠,生产和管理不便;在碱性条件下缩合时酚羟基容易氧化着色,杂质分离困难,生成的对羟基苯海因质量不好。
过去国内采用先醚化保护羟基,随后再水解的方式,虽然减轻了酚羟基氧化,但生产工艺复杂,生产成本高,已经被放弃了。
1.2.乙醛酸法1.2.1.对羟基扁桃酸氨解法乙醛酸与苯酚反应生成对羟基α-羟基苯乙酸,再在酸性或碱性情况下于50~70摄氏度反应,接缩合成D,L-对羟基苯海因,再经水解成DL-对羟基苯甘氨酸,收率为68%,反应条件易于控制。
但是反应时间长,收率偏低。
如果在第二步反应中加入相转移催化剂十八烷基二甲基苄基氯化铵,用苯二甲酰亚胺和氨水代替铵盐与对羟基扁桃酸反应,反应时间为8h,温度60℃,收率83.5%以上,产物纯度99%以上。
1.2.2乙醛酸水溶液、苯酚和醋酸铵“-步法”勒通收等人在前人研究的基础上,以乙醛酸水溶液、苯酚和醋酸铵为原料,采用-步法合成路线,合成了DL-对羟基苯甘氨酸。
原料摩尔配比:乙醛酸:苯酚:醋酸铵为1:1:4,体系的pH值为6.0~6.5、反应温度为30~35℃和反应进行24 小时的条件下,产率可达53.9%,纯度为98.5%。
与国外报道的相比,原料苯酚少用了-半,反应时间由48h缩短到24h,产率却超过了文献值。
殷树梅等又在乙醛酸、苯酚与铵盐作用,-步法合成目标产物的基础上进行改进,成功地以氨基磺酸代替醋酸铵,选用适当地催化剂,反应时间缩短为12h,产品收率达61%。
并确定最佳工艺条件为:原料摩尔比(乙醛酸:苯酚:氨基磺酸=1.0:1.3:1.3),反应时间为12h。
正交试验优化DL-对羟基苯甘氨酸合成工艺
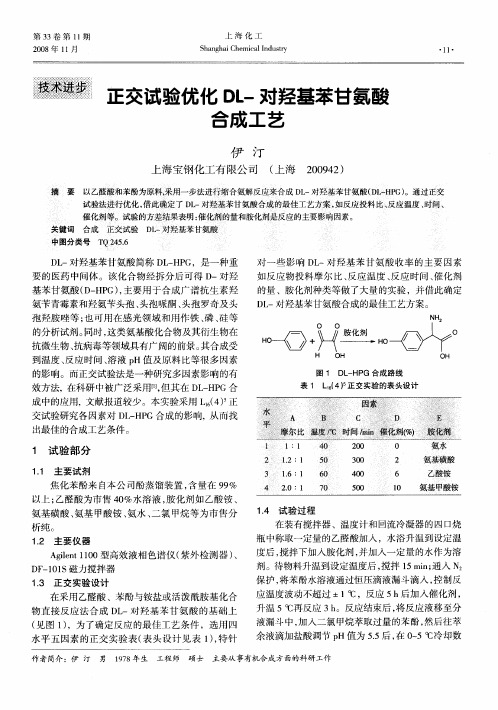
称重 , 经液相色谱分析纯度后计算得率 。
15 产 品分 析 .
采用 A in l0 get 0型高效液相色谱仪 ( l 1 紫外检
测器) 测定 D — G纯度 。 L HP
2 结 果 与讨 论
21 相关 因素正 交试验表 .
与由试验误差所引起的试验结果的波动区分开来 , 也没有 提供判 断 因素对试 验结果 影 响程度 的识别 标
主要 从事有机合成方面的科研 工作
矾髓
小 时后 过滤 , 用水洗 涤至滤 液无 色 。 到 的乳 白色 固 得 体 即为 D — P L H G,将 固体放入 真空 干燥 器 中干燥后
瞒 耵鼹 聃 mⅢ 眦 啪
第3 3卷
A B C D E 。从 各列极 差效应 来看 , 3 2 4 3 1 可得 主次五个 应温度 、 反应 时间 、 料 比。极差 分析法 是一 种 比较 投
12 主要 仪器 .
1 0
氨基 甲酸铵
14 试验 过程 .
在装 有搅 拌器 、温度计 和 回流冷凝 器 的四 口烧 瓶 中称取 一定 量 的乙醛 酸加入 ,水 浴 升温 到设 定 温 度后 , 搅拌 下加 入胺 化 剂 , 并加 入一 定 量 的水作 为溶
Aget 0型 高效 液相 色谱 仪 ( in 1 l 10 紫外 检 测器 ) 、 D 一 0 S磁力搅 拌 器 F 1I
准。 因此 在极差 分析 的基础 上又进 行 了方 差分析 ( 见 表 3, )由于极 差分 析 中得 出苯 酚 与乙醛 酸 的投料 比
按照正交表安排 D — P L H G合成试验 , 其结果见
表 2 :
表 2 五 因素 四 水 平正 交 设 计 及 实验 结 果
d-对羟基苯甘氨酸甲酯盐酸盐生产工艺流程

d-对羟基苯甘氨酸甲酯盐酸盐生产工艺流程下载提示:该文档是本店铺精心编制而成的,希望大家下载后,能够帮助大家解决实际问题。
文档下载后可定制修改,请根据实际需要进行调整和使用,谢谢!本店铺为大家提供各种类型的实用资料,如教育随笔、日记赏析、句子摘抄、古诗大全、经典美文、话题作文、工作总结、词语解析、文案摘录、其他资料等等,想了解不同资料格式和写法,敬请关注!Download tips: This document is carefully compiled by this editor. I hope that after you download it, it can help you solve practical problems. The document can be customized and modified after downloading, please adjust and use it according to actual needs, thank you! In addition, this shop provides you with various types of practical materials, such as educational essays, diary appreciation, sentence excerpts, ancient poems, classic articles, topic composition, work summary, word parsing, copy excerpts, other materials and so on, want to know different data formats and writing methods, please pay attention!d对羟基苯甘氨酸甲酯盐酸盐生产工艺流程1. 引言在医药和化工领域,d对羟基苯甘氨酸甲酯盐酸盐是一种重要的中间体,广泛用于合成药物和化学制品。
高密度转化D
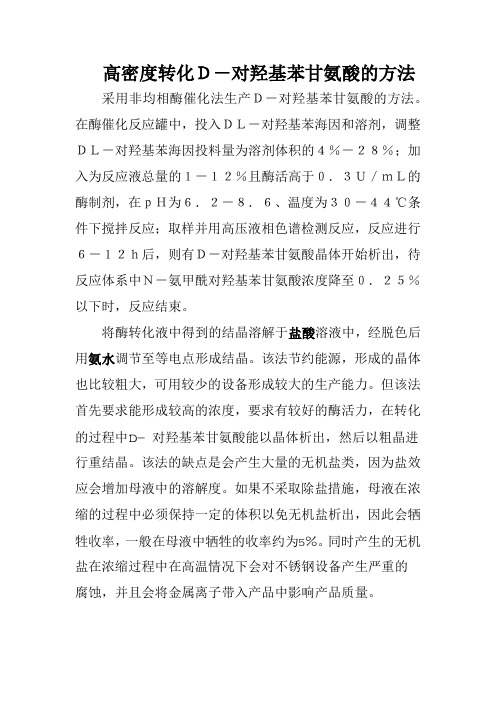
高密度转化D-对羟基苯甘氨酸的方法
采用非均相酶催化法生产D-对羟基苯甘氨酸的方法。
在酶催化反应罐中,投入DL-对羟基苯海因和溶剂,调整DL-对羟基苯海因投料量为溶剂体积的4%-28%;加入为反应液总量的1-12%且酶活高于0.3U/mL的酶制剂,在pH为6.2-8.6、温度为30-44℃条件下搅拌反应;取样并用高压液相色谱检测反应,反应进行6-12h后,则有D-对羟基苯甘氨酸晶体开始析出,待反应体系中N-氨甲酰对羟基苯甘氨酸浓度降至0.25%以下时,反应结束。
将酶转化液中得到的结晶溶解于盐酸溶液中,经脱色后用氨水调节至等电点形成结晶。
该法节约能源,形成的晶体也比较粗大,可用较少的设备形成较大的生产能力。
但该法首先要求能形成较高的浓度,要求有较好的酶活力,在转化的过程中D- 对羟基苯甘氨酸能以晶体析出,然后以粗晶进行重结晶。
该法的缺点是会产生大量的无机盐类,因为盐效应会增加母液中的溶解度。
如果不采取除盐措施,母液在浓缩的过程中必须保持一定的体积以免无机盐析出,因此会牺牲收率,一般在母液中牺牲的收率约为5%。
同时产生的无机盐在浓缩过程中在高温情况下会对不锈钢设备产生严重的
腐蚀,并且会将金属离子带入产品中影响产品质量。
D-对羟基苯甘氨酸的生产工艺
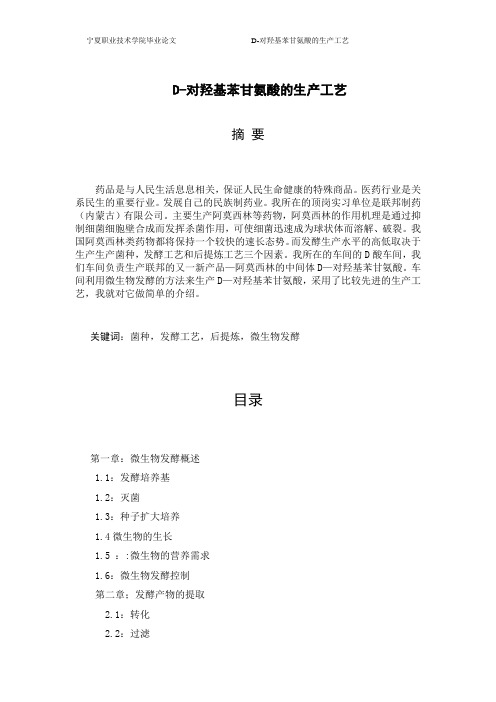
D-对羟基苯甘氨酸的生产工艺摘要药品是与人民生活息息相关,保证人民生命健康的特殊商品。
医药行业是关系民生的重要行业。
发展自己的民族制药业。
我所在的顶岗实习单位是联邦制药(内蒙古)有限公司。
主要生产阿莫西林等药物,阿莫西林的作用机理是通过抑制细菌细胞壁合成而发挥杀菌作用,可使细菌迅速成为球状体而溶解、破裂。
我国阿莫西林类药物都将保持一个较快的速长态势。
而发酵生产水平的高低取决于生产生产菌种,发酵工艺和后提炼工艺三个因素。
我所在的车间的D酸车间,我们车间负责生产联邦的又一新产品—阿莫西林的中间体D—对羟基苯甘氨酸。
车间利用微生物发酵的方法来生产D—对羟基苯甘氨酸,采用了比较先进的生产工艺,我就对它做简单的介绍。
关键词:菌种,发酵工艺,后提炼,微生物发酵目录第一章:微生物发酵概述1.1:发酵培养基1.2:灭菌1.3:种子扩大培养1.4微生物的生长1.5 ::微生物的营养需求1.6:微生物发酵控制第二章;发酵产物的提取2.1:转化2.2:过滤2.2.1:膜过滤2.2.2:活性炭过滤2.3:结晶2.4:离心2.5干燥第一章微生物发酵概述D-对羟基苯甘氨酸酸的发酵是典型的代谢控制发酵,也是好气性纯种发酵,在培养基配制及灭菌,种子扩大培养,空气除菌,发酵过程的检测及控制等环节十分关键,D—对羟基苯甘氨酸外观为白色结晶粉末,是合成半合成青霉素和头孢菌素的中间体,用于制造羟氨苄青霉素(阿莫西林amoxicillin)和头孢羟氨苄。
我所在的车间采用微生物发酵来生产D—对羟基苯甘氨酸,为比较先进的生产工艺,产品是否合格与每个工段及环节有着至关重要的联系。
在管理上采用新老思想的结合,对车间的发展起到关键性的因素。
1、发酵培养基在发酵工程中,拥有良好生产菌种是前提。
在正常生理条件下,微生物依靠自身代谢调节系统,趋向于快速生长和繁殖,而发酵则需要微生物积累大量的代谢产物。
微生物生长所需要的营养物质应该包括所有组成细胞的各种化学元素,这些营养物质可分为水,碳源,氮源,无机盐,生长因子等五大类。
D_对羟基苯甘氨酸的生物合成

Shijiazhuang 050041, C hina)
!! A bstract:This paper introduces chem ical precipitation m ethod and ion exchange resin m ethod to deal w ith zinc ion in the w aste w ater ofcephalosporin C and confirm som e optim um conditions and feasibility study on directdischarge after ion exchange resin.
(下转第 66 页)
66
河北化ຫໍສະໝຸດ 工2005 年第 6 期
表 1 等摩尔数不同沉淀剂对锌沉淀转化反应的影响
沉淀剂 锌沉淀转化率/% 过滤时间/m in
氢氧化钠
90
65
碳酸钠
86.7
10
碳酸氢钠
73.3
10
母 液 锌 残 留 含 量/%
备注
0.06
沉淀发粘,土褐色
0.06
疏 松 、白 色
0.16
疏 松 、白 色
[收稿日期]2005-07-07 [作者简介]许 喆(1977-),男,从事医药中间体的生产技术工作。
2 生产工艺路线
!! 将乙醛酸和苯酚、尿素分别加入到盛有浓盐酸 的 罐 中 , 搅 拌 加 热 进 行 反 应 , 反 应 液 经 冷 却 、结 晶 得 到D L-对羟基苯海因悬浮液, 然后经过滤洗涤得到 对羟基苯海因。 !! 将培养液经过一级种子罐、二级种子罐,培养后 送至发酵罐,将培养基配置罐内配好的诱导剂、玉米 浆、液糖送至发酵罐进行发酵。发酵液经过滤系统 循环过滤浓缩,透析液排放,浓缩的菌丝体加入无盐 水顶洗,压入转化罐。向转化罐内加入苯海因,实现 D L-对羟基苯海因的转化水解。得到的转化液经过 滤系统循环过滤浓缩, 除去菌丝和大部分可溶性蛋 白,送至板框压滤机过滤得到转化液,即得到D 酸溶 液 。 再 将 转 化 液 进 行 树 脂 处 理 、真 空 浓 缩 、结 晶 、离 心、干燥得到白色结晶产品D -对羟基苯甘氨酸。 3 该生产工艺存在的问题 3.1 发酵液进行絮凝、板框压滤等处理,操作时间过 长导致酶活下降(约5 h/批,酶活损失40% )。 3.2 在转化过程中大部分菌体已经自溶, 释放出大 量蛋白,导致过滤困难,需添加助滤剂才能得以过滤 且滤饼中的产品不能洗涤干净。 3.3 释放的蛋白质需用树脂吸附、加热调节等电点 来去除,且D -对羟基苯甘氨酸在碱性条件下容易氧 化,色泽加深,导致脱色时活性炭量增加,收率降低。 3.4 外循环蒸发的能耗较大,单位处理能力小且由
D-对羟基苯甘氨酸的制备

D-对羟基苯甘氨酸的制备制药081(10084349)刘朝阳1前言1.1目的D-对羟基苯甘氨酸是重要的医药中间体,通过查阅国内外有关文献,本文总结了对羟基苯甘氨酸的性质、用途、主要生产路线和生产开发情况。
1.2产品介绍D-对羟基苯甘氨酸(简称:D-p-HPG)是一种重要的医药精细化学品,主要用于合成β-2-内酰胺类半合成抗菌素,如羟氨苄青霉素(阿莫西林)、头孢克罗、头孢立新、头孢拉定等抗菌药物。
这些药物用途广泛,对革兰氏阳性菌、革兰氏阴性菌、弓形体、螺旋体等均有杀灭作用;同时它也用于多种多肽类激素及农药的合成、人工甜味剂的重要中间体。
【结构式】D-对羟基苯甘氨酸 (D-p-hydroxylphenylglycine,D-p-HPG),化学名D-α-氨基对羟基苯乙酸,分子式(OH)C6H4NH2CH2COOH,分子量167.2。
【性状】白色片状结晶,熔点204℃(分解),微溶于乙醇和水,易溶于酸或碱溶液生成盐。
1.3研究意义D-对羟基苯甘氨酸是一种重要是合成广谱抗生素羟氨卞青霉素和羟基头孢菌素的重要原料,用途广泛。
中国是抗生素类药物的生产和需求大国,而且中国制药行业已把半合成青霉素和半合成头孢菌素作为发展重点,因此对D-HPG新工艺的研究具有重要的现实意义。
2合成方法综述合成方法大致分两类:一类是生物酶催化选择性合成D-HPG,该法选择性高,污染小,但因生物菌培养问题,大规模工业化生产还有一定技术难度;另一类是采用化学方法合成得到外消旋体D,L-对羟基苯甘氨酸(D,L-HPG),再经拆分得到具有光学活性的D-HPG。
2.1D,L-HPG的合成化学合成是工业上生产D-HPG普遍采用的,但近年来,随着环保要求的不断提高和生物酶技术在手性氨基酸药物中的研究的不断进展,利用生物催化合成D-HPG逐渐成为研究的热点。
2.1.1生物催化合成法与化学合成方法相比, 生物催化法具有环境污染小、反应条件温和、选择性和转化率高等优点,但生物菌种的筛选较为困难,投资大,生物酶容易失活,无法大规模连续化生产。
一种双酶法生产D-对羟基苯甘氨酸的方法[发明专利]
![一种双酶法生产D-对羟基苯甘氨酸的方法[发明专利]](https://img.taocdn.com/s3/m/2777abfe227916888586d793.png)
专利名称:一种双酶法生产D-对羟基苯甘氨酸的方法 专利类型:发明专利 发明人:周志辉,徐海,刘涛,攸德伟,钱引 申请号:CN202011031917.X 申请日:20200927 公开号:CN112080532A 公开日:20201215
摘要:本发明公开了一种双酶法生产D‑对羟基苯甘氨酸的方法,包括:以DL‑对羟基苯海因为底 物,在溶剂中,在海因酶的作用下,在无氧环境中于pH 为9.5~11、温度为4 0~50℃的条件下反应 至结束,得到中间反应液;将中间反应液进行超滤除杂,去除中间反应液中的蛋白和色素,收集超滤 透过液;将N‑氨甲酰水解酶加入超滤透过液中,在无氧环境中于pH为7.0~8.5、温度为50~55℃的 条件下反应至结束,得到D‑对羟基苯甘氨酸。本发明能够提高底物的酶转化效率,降低生产中使用的 酶用量,从而降低成本,提高酶法生产D‑对羟基苯甘氨酸的争优势。
申请人:铜陵利夫生物科技有限公司 地址:244000 安徽省铜陵市经济开发区翠湖五路西段129号综合服务楼 国籍:CN 代理机构:合肥市长远专利代理事务所(普通合伙) 代理人:余婧 更多信息请下载全文后查看
对羟基苯甘氨酸工艺说明
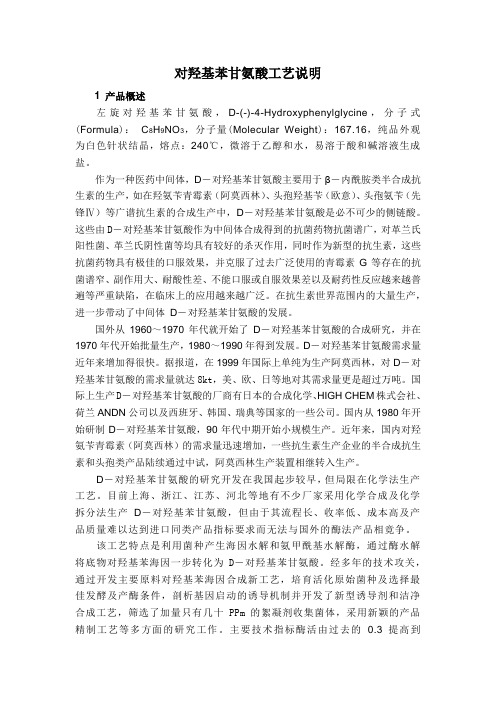
对羟基苯甘氨酸工艺说明1 产品概述左旋对羟基苯甘氨酸,D-(-)-4-Hydroxyphenylglycine,分子式(Formula):C8H9NO3,分子量(Molecular Weight):167.16,纯品外观为白色针状结晶,熔点:240℃,微溶于乙醇和水,易溶于酸和碱溶液生成盐。
作为一种医药中间体,D-对羟基苯甘氨酸主要用于β-内酰胺类半合成抗生素的生产,如在羟氨苄青霉素(阿莫西林)、头孢羟基苄(欧意)、头孢氨苄(先锋Ⅳ)等广谱抗生素的合成生产中,D-对羟基苯甘氨酸是必不可少的侧链酸。
这些由D-对羟基苯甘氨酸作为中间体合成得到的抗菌药物抗菌谱广,对革兰氏阳性菌、革兰氏阴性菌等均具有较好的杀灭作用,同时作为新型的抗生素,这些抗菌药物具有极佳的口服效果,并克服了过去广泛使用的青霉素G等存在的抗菌谱窄、副作用大、耐酸性差、不能口服或自服效果差以及耐药性反应越来越普遍等严重缺陷,在临床上的应用越来越广泛。
在抗生素世界范围内的大量生产,进一步带动了中间体D-对羟基苯甘氨酸的发展。
国外从1960~1970年代就开始了D-对羟基苯甘氨酸的合成研究,并在1970年代开始批量生产,1980~1990年得到发展。
D-对羟基苯甘氨酸需求量近年来增加得很快。
据报道,在1999年国际上单纯为生产阿莫西林,对D-对羟基苯甘氨酸的需求量就达8kt,美、欧、日等地对其需求量更是超过万吨。
国际上生产D-对羟基苯甘氨酸的厂商有日本的合成化学、HIGH CHEM株式会社、荷兰ANDN公司以及西班牙、韩国、瑞典等国家的一些公司。
国内从1980年开始研制D-对羟基苯甘氨酸,90年代中期开始小规模生产。
近年来,国内对羟氨苄青霉素(阿莫西林)的需求量迅速增加,一些抗生素生产企业的半合成抗生素和头孢类产品陆续通过中试,阿莫西林生产装置相继转入生产。
D-对羟基苯甘氨酸的研究开发在我国起步较早,但局限在化学法生产工艺。
目前上海、浙江、江苏、河北等地有不少厂家采用化学合成及化学拆分法生产D-对羟基苯甘氨酸,但由于其流程长、收率低、成本高及产品质量难以达到进口同类产品指标要求而无法与国外的酶法产品相竟争。
- 1、下载文档前请自行甄别文档内容的完整性,平台不提供额外的编辑、内容补充、找答案等附加服务。
- 2、"仅部分预览"的文档,不可在线预览部分如存在完整性等问题,可反馈申请退款(可完整预览的文档不适用该条件!)。
- 3、如文档侵犯您的权益,请联系客服反馈,我们会尽快为您处理(人工客服工作时间:9:00-18:30)。
D-对羟基苯甘氨酸的生产工艺摘要药品是与人民生活息息相关,保证人民生命健康的特殊商品。
医药行业是关系民生的重要行业。
发展自己的民族制药业。
我所在的顶岗实习单位是联邦制药(内蒙古)有限公司。
主要生产阿莫西林等药物,阿莫西林的作用机理是通过抑制细菌细胞壁合成而发挥杀菌作用,可使细菌迅速成为球状体而溶解、破裂。
我国阿莫西林类药物都将保持一个较快的速长态势。
而发酵生产水平的高低取决于生产生产菌种,发酵工艺和后提炼工艺三个因素。
我所在的车间的D酸车间,我们车间负责生产联邦的又一新产品—阿莫西林的中间体D—对羟基苯甘氨酸。
车间利用微生物发酵的方法来生产D—对羟基苯甘氨酸,采用了比较先进的生产工艺,我就对它做简单的介绍。
关键词:菌种,发酵工艺,后提炼,微生物发酵目录第一章:微生物发酵概述1.1:发酵培养基1.2:灭菌1.3:种子扩大培养1.4微生物的生长1.5 ::微生物的营养需求1.6:微生物发酵控制第二章;发酵产物的提取2.1:转化2.2:过滤2.2.1:膜过滤2.2.2:活性炭过滤2.3:结晶2.4:离心2.5干燥第一章微生物发酵概述D-对羟基苯甘氨酸酸的发酵是典型的代谢控制发酵,也是好气性纯种发酵,在培养基配制及灭菌,种子扩大培养,空气除菌,发酵过程的检测及控制等环节十分关键,D—对羟基苯甘氨酸外观为白色结晶粉末,是合成半合成青霉素和头孢菌素的中间体,用于制造羟氨苄青霉素(阿莫西林amoxicillin)和头孢羟氨苄。
我所在的车间采用微生物发酵来生产D—对羟基苯甘氨酸,为比较先进的生产工艺,产品是否合格与每个工段及环节有着至关重要的联系。
在管理上采用新老思想的结合,对车间的发展起到关键性的因素。
1、发酵培养基在发酵工程中,拥有良好生产菌种是前提。
在正常生理条件下,微生物依靠自身代谢调节系统,趋向于快速生长和繁殖,而发酵则需要微生物积累大量的代谢产物。
微生物生长所需要的营养物质应该包括所有组成细胞的各种化学元素,这些营养物质可分为水,碳源,氮源,无机盐,生长因子等五大类。
选取培养基的原则是:能满足生产菌生长,代谢的需要。
目的代谢产物要高。
产物的率最高。
产生菌生长及代谢迅速。
减少代谢副产物的生成。
价廉并且具有稳定的质量。
来源广泛且供应充足。
有利于发酵过程的溶氧与搅拌。
有利于产物的提取和纯化。
废物的综合利用性强且处理容易。
发酵培养基的配制原则:1.根据生产菌株的营养特性配制培养基。
2.营养成分的配比恰当。
3.渗透压。
4.PH。
还有注意各营养成分的加入次序以及操作步骤尤其是一些微量营养物质,如生物素,维生素等,更要注意避免沉淀生成或破坏而造成损失。
2灭菌在发酵过程中,如果污染了杂菌,杂菌将与生产菌争夺营养物质,溶氧等,甚至会消耗氨基酸产物,造成损失;由于杂菌的繁殖,且导致产物的提取,精制变得困难;若杂菌污染严重或发生噬菌体污染,生产过程将会失败。
灭菌是防止染菌的关键,为了防止染菌,车间对灭菌十分重视,凡是与产生菌接触的培养基,发酵罐,管路,通入的空气,其它相关器具以及无菌室的空间都要经过严格灭菌。
常用的灭菌的方法有:1.化学药剂灭菌法,如75%的酒精,5%的苯酚,0.25%新洁尔灭等。
2.辐射灭菌法:紫外线,高能电磁波,放射性物质3.干热灭菌法:在160℃下维持1h。
4.火焰灭菌法:利用火焰灭菌。
5.湿热灭菌法:利用饱和蒸汽进行灭菌。
6.过滤除菌法:用过滤方法。
在发酵企业,由于蒸汽容易获得,且价格比较低廉,故培养基和发酵设备一般使用湿热法进行灭菌。
它灭菌的好坏取决于灭菌温度和灭菌时间。
培养基灭菌:在各种微生物都有一定的最适温度范围。
当温度超过微生物最适温度的上限时,微生物细胞的蛋白质会发生不可逆的变性,病迅速死亡。
在实践中,通常采用致死时间,致死温度,对数残留规律作为灭菌操作的依据。
影响培养基灭菌是否彻底,主要和培养基的pH;培养基成分;无机盐溶液;泡沫;培养基中的颗粒。
培养基的灭菌方式:1.分批灭菌(实消)记在发酵罐内,整批培养基与设备同时经过加热升温,保温,降温等操作而达到灭菌的过程。
2.连续灭菌(连消)即在一套专门灭菌设备中,培养基连续进料,瞬时升温,短时保温,尽快降温,完成灭菌操作后才进入发酵罐的过程。
连消是发酵罐采用高温短时灭菌的连续操作过程,培养基营养成分的破坏较少,有利于提高发酵产率,整个过程占用发酵设备的操作周期较少,发酵罐的利用率高,整个过程使用蒸汽均衡,可采用自动控制,减轻劳动强度。
工业生产中,大批量的培养基普遍采用连消工艺。
空气除菌:氨基酸发酵是好氧性发酵,产生菌的生长和产物合成都需要消耗大量的氧气。
在工业生产上,通常以空气作为微生物所需氧气的来源。
但是,大量各种微生物悬浮于空气中,若随空气进入发酵培养基,在合适的条件下就会大量繁殖,消耗培养基的营养物质,产生各种副产物,从而破坏了纯种培养的发酵进程,严重时易导致倒灌。
因此,发酵必须使用洁净无菌的空气,空气除菌是正常发酵的一个关键。
空气除菌就是除去或杀死空气中的微生物。
其方法有:加热灭菌;辐射灭菌;经典灭菌;过滤除菌。
常用的过滤介质要求具有吸附性强,耐高温;阻力小等。
深层过滤常用的介质有棉花,玻璃纤维,烧结材料,活性炭,过滤器等。
介质深层过滤机理:1惯性撞击滞留作用。
2拦截滞留作用3布朗扩散作用。
4重力沉降作用5静电吸附作用。
绝对过滤除菌:是介质之间的孔隙小于被滤除的微生物,当空气流过介质层后,在空气中的微生物被滤除。
主要的介质有:聚偏氟乙烯,聚四氟乙烯等。
空气过滤除菌流程:1.两级冷却,分离,加热的空气除菌流程:空气✂粗过滤器✂经过空气压缩机✂储罐✂经过冷却器✂旋风分离器✂冷却器✂丝网分离器✂加热器✂过滤器✂无菌空气。
在流程中,压缩空气经过一级冷却至温度30~35℃,大量油,水凝结成较大雾滴,由旋风分离器去除;再经过二级冷却至温度20~25℃,使空气进一步析出较小雾滴,采用丝网分离器分离;最后利用加热器加热,把空气的相对湿度降低至50%℃左右,保证过滤介质在干燥条件下过滤。
这个是适应于空气湿含量较大的地区。
2.冷却空气直接混合式除菌流程:空气✂粗过滤器✂空气压缩机✂储罐✂冷却器✂丝网分离器✂总过滤器。
适用于气候寒冷,干燥的地区。
空气的温度低,相对湿度低,经压缩,冷却后析出的油和水很少,混合后的空气湿度保持在60%以下,还可以满足过滤介质除菌的干燥条件。
·3种子扩大培养:种子扩大培养的一般流程:保藏菌种✂斜面活化✂摇瓶培养✂种子罐培养✂发酵罐。
一般氨基酸发酵生产上,在生产车间以种子罐进行种子培养。
种子罐的大小需根据发酵工艺要求和发酵罐容量大小来确定,目前氨基酸生产工艺一般要求接种量为10%左右,故种子罐容积为发酵罐的10%左右。
如果发酵罐容积极大,而菌种生长又比较缓慢,可考虑采用多级种子罐完成种子的扩大培养。
在种子扩大培养中,越接近发酵罐的培养级数,其培养基组成越接近发酵培养基,以有利于种子接入发酵罐后尽快适应发酵培养基。
根据种子罐培养基的量而决定培养基灭菌操作方式,采用实消或连消,灭菌后降温至培养温度,等待接种。
在接种时,在火焰范围内将一级种子瓶的软管套在种子罐的接种管上,一级种子与种子罐连通后,通过急剧排除种子罐内的空气,是一级种子瓶与种子罐之间产生气压差,而将一级种子液压进种子罐。
培养过程中,主要控制温度,PH,通气量等条件,并定时取样进行化验和镜检,如检验残糖和显微细胞观察等。
培养成熟的种子液经取样检验正常后,方可移接下一级。
影响种子质量的主要因素:培养基,接种龄,接种量,温度,PH,通气与搅拌,泡沫4微生物生长微生物的生长可以用微生物生长曲线来描述其生长阶段,微生物生长曲线是以微生物数量即活细菌个数或细菌重量为纵坐标,培养时间为横坐标画得的曲线。
一般说,微生物重量的变化比个数的变化更能在本质上反应出生长的过程。
曲线可分为三个阶段即生长率上升阶段、生长率下降阶段及内源呼吸阶段。
单细胞微生物典型生长曲线分为延滞期即适应期、指数期、稳定期和衰亡期四个时期。
各个时期的特点是:停滞期:(1)细胞物质开始增加;(2)有的细胞开始不适应环境而死亡;(3)细菌总数下降;(4)停滞期末期,细胞代谢活动能力强,细胞中RNA含量高,嗜碱性强。
对不良环境条件较敏感,呼吸速度、核酸及蛋白质的合成速度接近对数细胞,并开始细胞分裂。
对数期:(1)菌体以几何数增加,增长速度快;(2)细胞代谢能力最强;(3)细菌很少死亡或不死亡。
稳定期:(1)生长速率下降,死亡率上升;(2)细胞数达到最大值,新生的细菌数和死亡的细菌数相当。
衰亡期:(1)死亡率增加,细菌少繁殖或不繁殖;(2)细菌常出现多形态、畸形或衰退型,有的会产生芽孢。
5微生物营养要求微生物生长繁殖所需的营养物质主要有水、碳源、氮源、无机盐和生长因子等。
(1)水:水是各种生物细胞必需的。
水是良好的溶剂,微生物的新陈代谢过程中的一切生化反应都离不开水的作用。
(2)碳源:碳源是合成菌体成分的原料,也是微生物获取能量的主要来源。
整体上看来,微生物可以利用的碳源范围极广,从大类上说,可以分为有机碳源和无机碳源两大类,凡必须利用有机碳源的微生物就是异养微生物,凡能利用无机碳源的微生物就是自养微生物。
糖类是最广泛利用的碳源。
(3)氮源:氮源主要是供给合成菌体结构的原料,很少作为能源利用。
与碳源相似,微生物作为一个整体来说,能利用的碳源种类十分广泛。
某些微生物(如固氮菌)能利用空气中分子态的氮或利用无机氮化物如铵盐、硝酸盐合成有机氮化物。
多数致病菌则必须供给蛋白胨、氨基酸等有机氮化物才能生长。
(4)无机盐类:无机盐主要可为微生物提供除碳、氮以外的各种重要元素。
微生物需要的无机盐类很多,主要有P、S、K、Na、Ca、Mg、Fe等,其主要功能为构成菌体成分;调节渗透压;作为某些酶的成分,并能激活酶的活性等。
(5)生长因子:有些微生物虽然供给它适合的碳源氮源和无机盐类,仍不能生长,还要供给一定量的所谓“生长因子”。
其种类很多,主要是B族维生素的化合物等。
生长因子可以从酵母浸出液、血液或血清中获得。
6、微生物发酵控制微生物发酵是利用微生物,在适宜的条件下,将原料经过特定的代谢途径转化为人类所需要的产物的过程。
微生物发酵所需的培养基必须包括微生物所需的五大营养物质,且有固定比例及严格的数量与质量要求,发酵为我车间的第一道工序,培养基的正确配制则是发酵的前提,其需要玉米浆为氮源,液态葡萄糖为碳源,因为我们发酵所需的最终产品为一种诱导酶,培养基中必须加入诱导剂。
此外还有硫酸铵、硫酸镁等。
配好培养基后需要经过高温高压蒸汽灭菌来消除培养基及罐体内的杂菌,我们采取二级发酵来培养菌体。
制备好种子后在无菌条件下将种子接种至一级种子罐中,在适宜的温度及PH条件下培养种子,实现种子的一级扩大培养。