制程不良重工流程
MRB处理流程--属于三级文件。

1. Purpose 目的本程序是对不合格的物料、半成品、成品评审处理的程序。
当来料、制程、出货时发现不良品时,如不良品属于生产急用或急于出货,物料部与品质部、工程部、生产部、客服部、供应链组成的评审委员会对不良品进行评估,并做出处理意见的程序。
2. Scope 范围本程序适用于安保科技有限公司的不合格产品及物料的MRB 评审处理流程。
3. Responsibility 职责 3.13.1 采购部采购部采购部::3.1.1 澄清异常物料异常原因及相关处理意见(批退/挑选加工),若需申请让步放行需说明其原因,开出特采单。
3.1.2 负责联络厂商处理来料不良和生产退料评审的不良品。
3.2.2 PMC PMC :3.2.1负责对异常物料所涉及生产订单机型及计划上线时间予以说明,另外,对超出24h未处理之异常物料进行协助跟进。
3.2.2 负责紧急物料不良MRB会议主导。
3.3 .3 工程部工程部::负责物料来料无检验依据(规格书/图纸/样品)、或实物与检验依据要求不符等异常,给出判定动作及判定意见,其中包括物料模拟试装、签样等,制定出作业指导书。
3.43.4. . . 仓库仓库仓库::负责执行“让步接受”物料所涉及后续存储、隔离、指定生产订单发料等具体操作动作。
3.5 制造部造部::负责执行“让步接受”物料,按评审的作业方式及作业方法作业方式及作业方法作业方式及作业方法要求上线生产。
3.6 3.6 质量部质量部::3.6.1 IQC负责《IQC 来料检验报告》的开出及相关部门的提报,状态标示。
3.6.2 SQE参与来料MRB评审; 最终核准结果划分责任;追踪供应商的分析改善报告。
3.6.3 IPQC 负责跟进“让步接受”物料在制程使用品质状况。
3.6.4 QE参与制程不良及客户投诉MRB评审;最终核准结果划分责任,追踪责任部门的分析改善报告。
4. Definition 定义Material Review Board (MRB):全称物料评审委员会,由PMC 、品质部、工程部、生产部、采购部、市场部相关部门组成,针对不合格产品及物料做出最终处理的会议。
产品质量异常处理流程
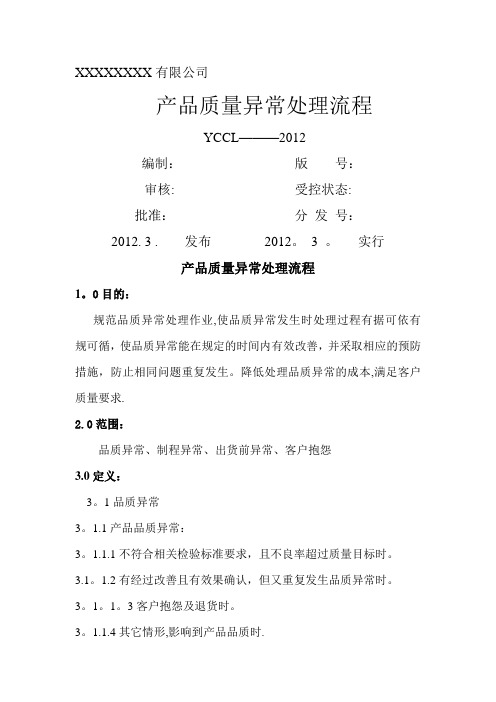
XXXXXXXX有限公司产品质量异常处理流程YCCL———2012编制:版号:审核: 受控状态:批准:分发号:2012. 3 . 发布2012。
3 。
实行产品质量异常处理流程1。
0目的:规范品质异常处理作业,使品质异常发生时处理过程有据可依有规可循,使品质异常能在规定的时间内有效改善,并采取相应的预防措施,防止相同问题重复发生。
降低处理品质异常的成本,满足客户质量要求.2.0范围:品质异常、制程异常、出货前异常、客户抱怨3.0定义:3。
1品质异常3。
1.1产品品质异常:3。
1.1.1不符合相关检验标准要求,且不良率超过质量目标时。
3.1。
1.2有经过改善且有效果确认,但又重复发生品质异常时。
3。
1。
1。
3客户抱怨及退货时。
3。
1.1.4其它情形,影响到产品品质时.3。
1。
2 制程异常3。
1.2。
1不遵守操作标准操作。
3.1.2.2虽然照操作标准操作,但因各种标准不完善,以致无法控制变异原因。
3。
1。
2.3使用不合格的原料或材料。
3.1.2。
4机械发生故障或磨损。
3.1.2.5其它情形,可能存在品质隐患时。
4。
0职责4.1质控部:4.1.1负责各生产部门质量异常不良的提出4。
1.2负责不良现象及不良比例的确认和判定,临时对策效果的确认及不良物料的处理。
4。
1。
3负责质量外观不良类的最终判定与裁决。
4.2技术部:负责结构类和功能类质量异常的分析与临时对策的提出。
4。
3生产部门:负责按质控部/技术部临时对策的执行,并配合处理相关不良品处理。
4.4业务部:负责接收客户投诉并反馈信息至技术、质控,投诉分析完成后把处理结果反馈至客户。
4。
5其它部门:在问题涉及时负责问题的分析、措施的提出及执行。
5。
0工作程序:5。
1进料品质异常:5。
1。
1 IQC依相关检验标准判定不合格,针对不合格物料标示“不合格”,并通知仓库立即移至不良品区域。
5。
1.2异常成立1小时内开立《品质异常处理单》通知采购/生产管理部门.5.1.3采购接《品质异常处理单》后1小时内转责任供应商。
重工作业程序(含表格)
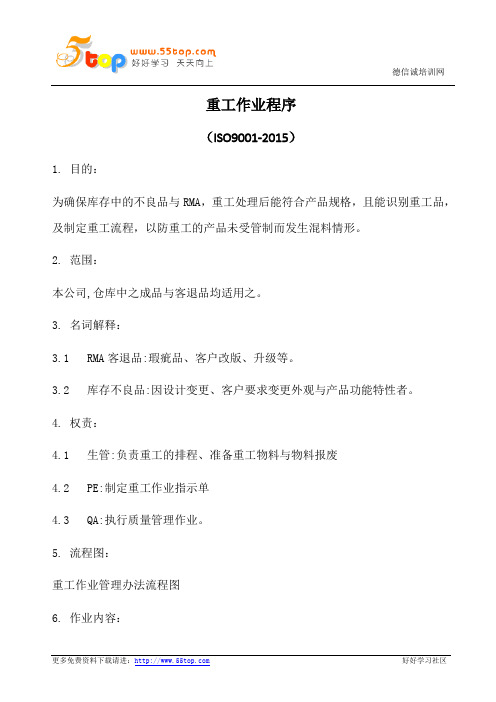
重工作业程序(ISO9001-2015)1. 目的:为确保库存中的不良品与RMA,重工处理后能符合产品规格,且能识别重工品,及制定重工流程,以防重工的产品未受管制而发生混料情形。
2. 范围:本公司,仓库中之成品与客退品均适用之。
3. 名词解释:3.1 RMA客退品:瑕疵品、客户改版、升级等。
3.2 库存不良品:因设计变更、客户要求变更外观与产品功能特性者。
4. 权责:4.1 生管:负责重工的排程、准备重工物料与物料报废4.2 PE:制定重工作业指示单4.3 QA:执行质量管理作业。
5. 流程图:重工作业管理办法流程图6. 作业内容:6.1需重工之制品:由相关部门判定重工后,于重工品上标示重工原因以及重工方式。
6.2订定重工作业与流程:6.2.1由PE订定重工作业内容与流程,包含需更换或保留之零件。
针对重工制程订定自主检验标准,以及在重工制程所产出特定检验项目。
6.2.2「重工处理作业指示单」应述明重工作业所需之更换物料,以利备齐相关物料。
6.2.3由业务部提出客户对重工品之需求,含客户所需要之标示(例:最新版标签、客户指定标示)、包装。
6.3开重工订单:资材部依据需求单位所发出的联系单或重工指示单,开出重工订单交给制造部/外包作为开工依据,并依「重工处理作业指示单」准备重工所需更换之物料。
6.4领料:由仓库依据资材部发出「重工订单」及「重工处理作业指示单」,发料。
6.5重工作业:6.5.1由仓管将重工所需之物料备齐,制造部/外包依据PE所订定的「重工处理作业指示单」与原属SOP教导作业人员重工作业方式,包含重工标示及位置等。
6.5.2重工作业外观检视,依该机种SOP外观检检站,或依该机种的样品相互比对。
6.5.3品保部依照「重工处理作业指示单」执行巡检作业。
6.5.5重工标示:除客户特定需求之外一律在产品卷标日期最后位置做黑色圆点记号。
如有特殊标示,应于「重工处理作业指示单」另行注明。
最大外包箱重工标示依照客户需求。
工厂生产及质量培训--SWR(重工)作业讲义

正常作業
重工及特殊需求系統講義(六)
申請單位 申請日期 一. 目的:
特殊工作需求作業單(SWR)
申請者
表單編號:_____________ 有效期限:_____________
單位主管
年 月 日 品保主管
事業處主管
二. 作業流程:
三. QC 計划:
四. 允收/拒收標准:
五. 其它:
申請單 位
重工及特殊需求系統講義(三)
五、重工作業最低要求:
1.重工必需在VDCS或制程異常連絡單或特裁單完成或RMA 確定后,且材料被判定必需重工才可為之,并且依附件一之流 程運作.
2.若材料重工為必需,則工程人員必需判斷重工是否會改 變問題材料之外觀尺寸及功能.
3.若重工造成外觀尺寸及功能之改變,則工程人員必需制 定重工作業方法,同時將重工方法寫在特殊工作要求單(SWR) 上,見附件(二).
未考慮到此處彈片的避位性,使得 1.16± 0.25 受力擠壓后發生變形偏低,嫌疑不良數
量:10000PCS)
二. 作業流程:
1. 取不良品→重工→檢查→包裝
2. 重工時注意掌握力度,避免多次重工
3. 包裝時注意工件的擺放,避免再次變形
三. QC 計划:
劉小平 4/28/00
1. IPQC 依上述流程查核作業
彈片間隙(目視檢查)
何鑫 4/28/00
特殊工作需求作業單(SWR)
申請單 位
制一工程
申請者
張浩
單位主管
: SWR2000427
效期限:
4/27~4/29
石為民 4/28
申請日期 2K 年 4 月 27 日 品保主管 王延國代 事業處主管 王相舜 4/28/00 一. 目的:
OQC作业流程图
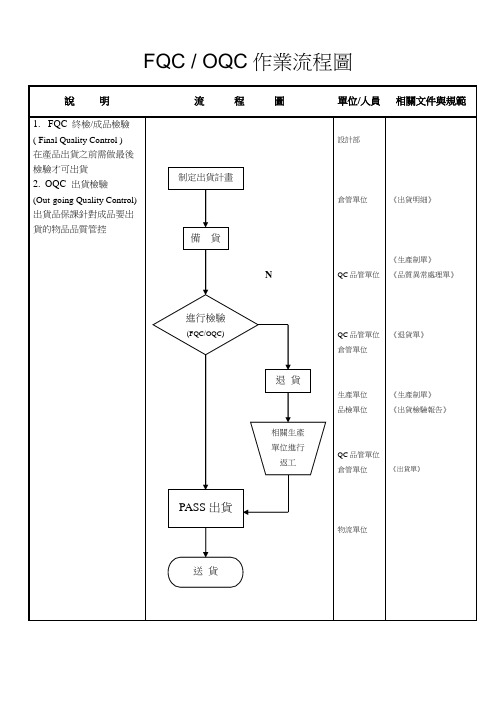
FQC / OQC作業流程圖製程巡檢作業辦法目的:落實品質意識在現場作業人員于制程過程中,實施檢驗或試驗以查證制程之合格性。
三〃範圍:凡本公司產品之各制程。
四、職責:生產部門:負責自製品自檢、送檢、重工、維修及入庫。
品保部門:負責自製品檢驗及記錄、標示。
五、內容:1、首件(產前樣/批版)、自主、巡迴檢驗:(1)品保部門IPQC人員在以下時段需做首件檢驗。
(1)每台機開始生產前開機需做首件檢驗。
(2)設計規格變更時需做首件檢驗。
(3)人員或材料更換時需做首件檢驗。
(2)生產部門作業人員應隨時注意生產產品品質狀況,並按照規定做好自主檢驗。
(3)品保部門IPQC人員應到現場做巡迴檢驗並做好記錄。
(4)品保部門檢驗管制程式,應按照規範和作業指導書之要求訂制(QC工程圖)。
(5)生產部門相關人員在制程中,發現不合格又無法矯正時,應及時停機報告主管,並通知品保部門,而品保部門應按照相關程式處理。
(6)品保部門IPQC人員按照實際檢驗情況記錄不合格品,並對制程式不良品作統計分析把結果回饋於相關部門,作糾正預防對策之依據。
(7)不合格品處理與標示(紅豆標&件投標):(1)、經判定為不合格品時,應在該批半成品貼上紅色圓點貼紙(故障貼紙)又稱紅豆,並加以區分,隨後將不合格批移至返工區或報廢區進行處理。
(2)、發生不合格品時,品保部門IPQC人員應填寫《IPQC服裝(巡廠)驗貨報告》加以記錄,並按照相關程序處理,並通知相關部門處理。
六〃使用表單:1、首件(制前樣/批版)吊卡2、特采申請單3、IPQC服裝(巡廠)驗貨報告4、返工\返修單5、報廢單6、制程異常備忘錄不合格品處理作業辦法一、目的:按照品質計畫及管制措施找出不合格品,採取各項管理及處理措施,並對不合格品進行分析,以防誤用。
二、範圍:供方之原材料、主輔料;廠內制程中之半成品、成品和庫存品;顧客之退貨品。
三、職責:生產、資材部門:負責不合格品標示、隔離及處理,必要時參與評審。
FA(不合格品管制流程)范本
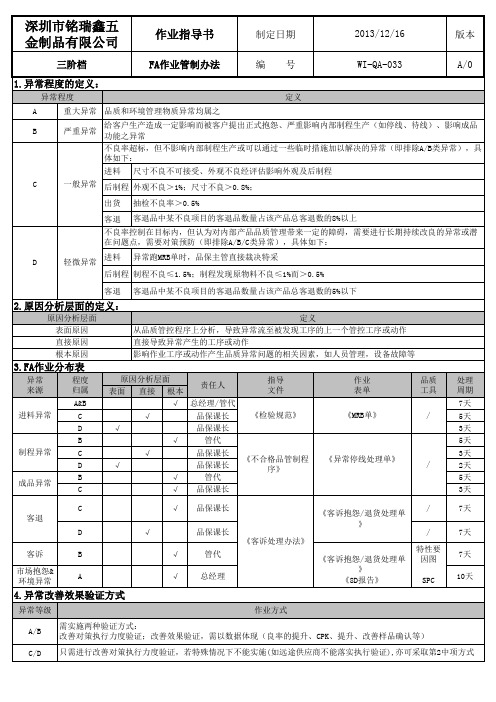
检验规
首件检验NG,需重新制作或重新考量重工方式 范》
的重要性;
首件检验 报告
针对重工过程中出现的不可返修品,需进行NG 标示后,直接做报废申请,申请过程同【不合 格管制程序】;
《标示 与追溯 管理办 法》
IPQC检验 日报表 报废单
品保 生产 品保 品保
巡检 OK
标示
NG
针对重工返修品,需依据【标示与追溯管理办 法】,进行标示作业,IPQC抽检频率提升一 级; OQC依据标示,将AQL提升一级作业; 品保课长追溯产品至客户端的品质状况; 视异常等级区别,实施不同的改善效果验证方 式;
确定处理 方式
针对制程不合格重工,需悬挂重工SOP,并制作
重工首件,由IPQC确认OK,方可实施重工返修 《品保
动作;
检验规
若首件检验NG,需重新制作或重新考量重工方 范》
式的重要性;
首件检验 报告
品保 品保 品保
品保/生产
制做重工首件
NG
首件检查
OK NG
巡检
OK
标示/入库
针对重工过程中出现的不可返修品,进行NG标 示后,直接做报废申请,申请过程同【不合格 品管制程序】;
深圳市铭瑞鑫五 金制品有限公司
作业指导书
制定日期
2013/12/16
版本
三阶档
FA作业管制办法
编号
WI-QA-033
A/0
1.异常程度的定义:
异常程度
定义
A
重大异常 品质和环境管理物质异常均属之
B
严重异常
给客户生产造成一定影响而被客户提出正式抱怨、严重影响内部制程生产(如停线、待线)、影响成品 功能之异常
C/D 只需进行改善对策执行力度验证,若特殊情况下不能实施(如远途供应商不能落实执行验证),亦可采取第2中项方式
制程不良品管理办法

铜陵集思意特种编织线有限公司制程不良品管理办法制作:审核:1. 目的:1.1对制程中产生之不良品进行规范化管制,防止不良品误用及可重工品的合理化使用. 1.2确保制程中产生之无氧与低氧、镀锡、漆包线等不良品的合理管控,防止混用或造成无氧产品的污染.2. 范围:制程中各工序产生的不合格品均属之.3. 定义:略.4. 职责:4.1 制造部:4.1.1负责对100%全检的不合格品进行重工确认,减少因人员检验漏失造成的误判.并将最终确认结果记录于《成品检验记录表》.4.1.2负责客户退回品的全检及不合格品的判定,标示及隔离.4.1.3负责按规定对不合格品的标示及隔离;以及对不合格品的包装、整理、退庫.处理.4.1.4制造之合格品流至下一工序进行包装入库,不可重工品,转下一工序依《报废品作业管理办法》执行.4.1.5 对于无氧裸铜与低氧裸铜不合格品须进行分开放置并相应之标示。
无氧裸铜不合格品须进行无氧裸铜字样的标签标示.4.2 品保部:4.2.1 负责对不合格品的判定、标示、隔离以及《品质异常单》的开立,以确保不合格品不被误用及流入客户端.4.2.2负责对制程中无氧裸铜与低氧裸铜不合格品的鉴别与标示.5. 作业内容:5.1制程中不良品处理流程图:5.2各工序完成品由作业人员进行100%自主检查,良品填入《生产流程卡》并流至下一工序.5.3 各工序产生之不良品放置于不合格品区域,《生产流程卡》流至品检单位进行不良品的最终确认.5.3.1质量技术部在制程中如发现以下不良项目需开立品质异常单,并转相关单位做分析改善,同时需进行不良追溯。
5.3.1.1制程中如发现5KG以下异常;5.3.1.2发现5KG以上品质异常则开立《品质异常单》转制造单位进行分析改善,并对该批原材所生产之机种做立即停线处理,同时对该批材料进行追溯。
5.3.2倒轴工位制程中如发现以下不良项目需开立《品质异常单》,并转相关单位做分析改善,同时需进行追溯。
重工作业指导书(含表格)
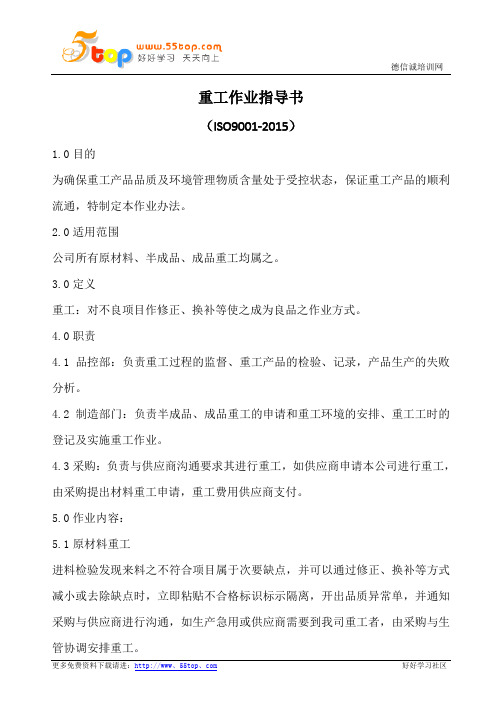
重工作业指导书(ISO9001-2015)1.0目的为确保重工产品品质及环境管理物质含量处于受控状态,保证重工产品的顺利流通,特制定本作业办法。
2.0适用范围公司所有原材料、半成品、成品重工均属之。
3.0定义重工:对不良项目作修正、换补等使之成为良品之作业方式。
4.0职责4.1品控部:负责重工过程的监督、重工产品的检验、记录,产品生产的失败分析。
4.2制造部门:负责半成品、成品重工的申请和重工环境的安排、重工工时的登记及实施重工作业。
4.3采购:负责与供应商沟通要求其进行重工,如供应商申请本公司进行重工,由采购提出材料重工申请,重工费用供应商支付。
5.0作业内容:5.1原材料重工进料检验发现来料之不符合项目属于次要缺点,并可以通过修正、换补等方式减小或去除缺点时,立即粘贴不合格标识标示隔离,开出品质异常单,并通知采购与供应商进行沟通,如生产急用或供应商需要到我司重工者,由采购与生管协调安排重工。
5.1.1供应商重工供应商派人到我司进行产品重工,由生管安排重工地点、工治具、设备等并通知品控部门进行重工监督及检验。
5.1.2我司自行重工5.1.2.1如供应商来料异常请求我司协助重工时,由采购提出材料重工申请,生管开出重工《生产订单》安排重工地点,人员,工治具、设备等,并通知品控部门进行重工监督及检验。
5.1.2.2重工所消耗的工时及费用由采购与供应商商定,具体扣款项目由采购提供财务科进行扣除。
5.2IPQC及FQC判退之不良半成品、成品重工。
5.2.1制程检验发现产品品质异常,并可以通过修正、换补等方式减小或去除缺点时,品控立即粘贴不合格标识标示隔离,开出品质异常单。
5.2.2由品控提出重工申请,生管开出重工《生产订单》安排重工地点、工治具、设备等并通知品控部门进行重工监督及检验。
5.3库存品重检不合格品、OQC退货产品、客户退货品重工5.3.1库存品重检、OQC出货检验发现产品及客户退货品之不符合项目属于次要缺点,并可以通过修正、换补等方式减小或去除缺点时,品控立即粘贴不合格标识标示隔离,开出品质异常单。
重工作业流程

1. PE director approve 2. Data Center release
Production rework
FQA Inspection
5
重工作业流程
表格:
重工作业说明书
重工作业说明书填写检核表
6
重工作业流程
实例:
以F01L018.00产品无法开机Sorting为例来说明重工作 业流程.
3
权责:
重工作业流程
制造处产品工程单位(PE):负责确认重工步骤及提供重工样品并 负责制作所有重工之作业流程建立重工作业指导书.
品保工程单位(PQE):负责重工样品之确认并负责确认重工后是 否需加特别之测试并与客户需求一致.
品保检验单位(IPQC/OBA):负责确认产品外观/电性检验. 数据中心(DCC)﹕确认该文件可以生效﹐并给予文件编号与发行
生产管理单位(PC):负责安排协调重工之排程.
制造单位(PD):负责执行重工作业,准确提供需重工数量,重工 注意事项,开出重工费用Charge单.
制工部(IE):提供重工SOP,评估重工工时及重工费用. 4
作业流程:
重工作业流程
RD
ECN MEMO
MFG
异常停 线通知
QA
Hold Notice CQCN
重工作业流程
重工作业流程
目的:
建立重工作业程序及标准,作为管理重工产品之依据,确 保重工作业申请与执行过程需求之质量管理以期确保重 工质量,避免不合格品流出.
2
重工作业流程
定义:
适用于ECN/ECR导入,制程异常,测试线异常,OBA退货(外观 及电性),RMA判定重工,BC8M修护良品,Hold Notice,会议记 录,客户端需求变更等需重工之产品.
制程中不良品管制流程
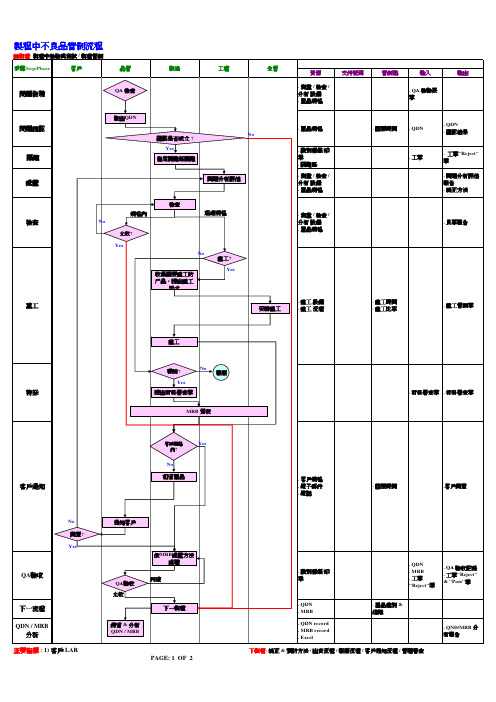
下一製程
. QDN . MRB . QDN record . MRB record . Excel
. 產品鑑別 & 追蹤 . QND/MRB 分 析報告
下製程: 矯正 & 預防方法 / 出貨流程 / 報廢流程 / 客戶通知流程 / 管理審查
PAGE: 1 OF 2
客戶通知
. 回覆時間
.客戶同意
No
No 同意?
通知客戶
Yes 依MRB處置方法 處理 . QDN . MRB . 工單 "Reject"章
QA驗收
QA驗收 允收
判退
. 識別標籤/印 章
. QA 驗收記錄 . 工單"Reject" & "Pass"章
下一流程 QDN / MRB 分析 主要指標 : 1) 客戶 LAR
. 良率報告
Yes No 重工? Yes
收集需要重工的 产品,提出重工 需求
重工
安排重工
. 重工 設備 . 重工 流程
. 重工時間 . 重工比率
. 重工管制單
重工
特採? Yes
No
報廢
特採
提出材料審查單
. 材料審查單 . 材料審查單
MRB 簽核
客戶規格 內?
Yes
No 扣留產品 . 客戶規格 . 電子郵件 . 電話
. 回覆時間
. QDN
. QDN . 確認結果
隔離
指定隔離區隔離
. 識別標籤/印 章 . 隔離區 問題分析評估 . 測量 / 檢查 / 分析 設備 . 產品規格
. 工單
. 工單"Reject" 章 . 問題分析評估 報告 . 矯正方法
制程品质异常处理程序(含表格)
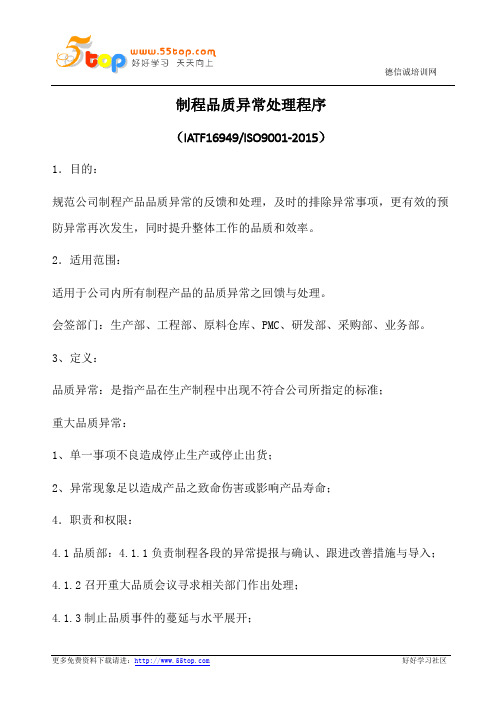
制程品质异常处理程序(IATF16949/ISO9001-2015)1.目的:规范公司制程产品品质异常的反馈和处理,及时的排除异常事项,更有效的预防异常再次发生,同时提升整体工作的品质和效率。
2.适用范围:适用于公司内所有制程产品的品质异常之回馈与处理。
会签部门:生产部、工程部、原料仓库、PMC、研发部、采购部、业务部。
3、定义:品质异常:是指产品在生产制程中出现不符合公司所指定的标准;重大品质异常:1、单一事项不良造成停止生产或停止出货;2、异常现象足以造成产品之致命伤害或影响产品寿命;4.职责和权限:4.1品质部:4.1.1负责制程各段的异常提报与确认、跟进改善措施与导入;4.1.2召开重大品质会议寻求相关部门作出处理;4.1.3制止品质事件的蔓延与水平展开;4.1.4对实施的对策做复核,发出最终的改善结果;4.2生产部:负责品质异常提出及初步的原因排除,执行技术部门给出的对策;4.3工程部:对制程的异常进行原因分析,给出有效的改善措施;4.4研发部:因设计不符合对制程产生的品质异常做出调整,并给出有效的改善对策;当出现重大品质事件协助查找不良原因;4.5PMC:根据品质异常处理状况对订单评估与调整;4.6采购部:掌握品质异常之材料影响程度,跟进进料品质状况和协助制程中出现异常处理;4.7业务部:因品质造成影响出货暂停出货或让步出货,以及修改出货计划;4.8仓库:根据因品质不良产品做出区分和标示;5、参考数据<成品检验规范><SOP作业指导书>6.作业程序:6.1制程品质异常确定6.1.1当在生产过程中,生产各段发现或经工程PE分析确认同一材料和工站出现不良数出现5PCS,一批总不良率超出3%时由品质IPQC提报异常单进行处理;6.1.2当生产各工段出现不良率达到100%或在接线、测试段直接烧机事件,跟线品质IPQC并立即要求生产源头停止下拉和不良标示以及发出停线报告,签核到品质中心主管后并以OA通知到相应部门,同时做生产的调整;6.1.3出货检验中出现不良率超出BJH-QU-ETS-007、BJH-QU-ETS-160标准值,由OQC提报异常由部门主管签核后转至生产包装负责人确认并通知工程PE到现场进行分析,按6.2执行;如急需出货并上升到中心主管审核通过或业务员与客户确认OK方可做让步接收出货;品质做单据保存以其客户使用状况的跟进;6.2正常制程品质异常处理6.2.1当产线出现异常达到6.1.1规定值时由跟线IPQC现场确认现场可改善或者由部门主管以上级确认可生产,将有效改善对策以及确认信息给到跟线的拉长执行,跟据生产对策实施IPQC再次确认改善效果,OK后按正常生产流程作业,NG时再返回对策实施;6.2.2当产线出现异常达到6.1.1规定值时由跟线IPQC现场确认现场不能改善时,及时开始品质异常处理单并填写发生异常工序、生产数量、不良现象、标准值、不良值、不良率等状况,由制程品质组长和主管签核后附带不良品转至跟线PE工程师并要求跟线人员以其IPQC到现场做进一步分析;6.2.3工程PE工程师接到品质开出的异常处理单并到异常发生工段做进一步分析确认,同时在30分钟内给出可执行的临时对策给到生产执行和现场指导,生产可恢复正常生产,若临时对策因设计、材料所至需生产挑选、加工使用由生产进行统计无效工时由责任归属承担,需要做实验验证分析结果跟进实验时间给出临时对策但总体时间不能超出8小时以外;6.2.4PE工程师在完成异常分析将分析状况填写至品质异常处理单上,同时给出临时对策、责任归属部门返回跟线IPQC转至到制程品质QE确认原因分析及责任归属,当责任归属对工程所分析的结果有异议时,品质QE主导对异常分析结果异议部门到现场进行确认,品质QE做最终判定。
产品质量异常处理流程

产品质量异常处理流程一、目的:标准质量异常处置作业,使质量异常发作时处置过程有据可依有规可循,使质量异常能在规则的时间内有效改善,并采取相应的预防措施,避免相同问题反复发作。
降低处置质量异常的本钱,满足客户质量请求。
二、范围:质量异常、制程异常、出货前异常、客户埋怨三、定义:1、质量异常(1)产品质量异常:1)不契合相关检验规范请求,且不良率超越质量目的时。
2)有经过改善且有效果确认,但又反复发作质量异常时。
3)客户埋怨及退货时。
4)其它情形,影响到产品质量时。
2、制程异常(1)不恪守操作规范操作。
(2)固然照操作规范操作,但因各种规范不完善,致使无法控制变异缘由。
(3)运用不合格的原料或资料。
(4)机械发作毛病或磨损。
(5)其它情形,可能存在质量隐患时。
四、职责1、质控部:(1)担任各消费部门质量异常不良的提出(2)担任不良现象及不良比例确实认和断定,暂时对策效果确实认及不良物料的处置。
(3)担任质量外观不良类的最终断定与判决。
2、技术部:担任构造类和功用类质量异常的剖析与暂时对策的提出。
3、消费部门:担任按质控部/技术部暂时对策的执行,并配合处置相关不良品处置。
4、业务部:担任接纳客户投诉并反应信息至技术、质控,投诉剖析完成后把处置结果反应至客户。
5、其它部门:在问题触及时担任问题的剖析、措施的提出及执行。
五、工作程序:1、进料质量异常:(1) IQC依相关检验规范断定不合格,针对不合格物料标示“不合格”,并通知仓库立刻移至不良品区域。
(2)异常成立1小时内开立《质量异常处置单》通知采购/消费管理部门。
(3)采购接《质量异常处置单》后1小时内转义务供给商。
(4)供给商需于4小时内针对异常物料提出暂时对策,如对异常内容有疑问,需在4小时内与相关人员确认分明,必要时到现场确认。
(5)供给商必需在《质量异常处置单》请求的期限前回复完好的改善计划。
(6) SQE针对供给商回复内容停止确认,针对改善措施不合格局部予以退件,请求供给商重新回复。
质量异常反馈流程

編號:2014-1028-01
製造 品管
2011-3-2 **
異常情形描述: 2011/3/1時品管**在檢驗3#生產321616-A時發現有毛邊不良,批號為:1030105323,檢驗確認毛
邊過大NG,經對上下批追蹤確認,發現上兩個時間段都有此不良,批號分別 為:1030100323,1022808323.連續三批都有毛邊不良,而我們量測員未發現,也未做標識隔離,不良可 能會流出,造成客戶投訴,故請A班顀分析,並於3日內回覆有效的改裝對策.
排列图、直方图、控制图 制定或修改工作规程、检查规程 及其它有关规章制度
3. 戴明循环的优点: • 适用于日常管理,且同时适用于个体管理与团队管
理; • 戴明循环的过程就是发现问题、解决问题的过程; • 适用于项目管理; • 有助于持续改进提高; • 有助于供应商管理; • 有助于人力资源管理; • 有助于新产品开发管理; • 有助于流程测试管理。
异常
品 报废
挑选
特采
3.异常品标签:
三. 责任判定原则
1 用事实说话 在描述中尽量不要出现:“我认为…….”、
“我觉得……”等带有主观性色彩的词语,多 采用客观的方法来进行描述,如“拍图片” 、“保留样品”等等。
2 用数据说话
在分析过程中,多采用数据来说明问题, 以避免文字性描述带来分歧。
3 提供完整分析过程
五. 问题讨论
Q1:产品验证如何操作? Q2:碰到有争议的问题如何处理?
核心价值观
客户第一、阳光沟通、团队协作 拥抱变化、学习成长
行为准则 团尊勇队重气、、行简反为单馈准、、重认则用真、、检责查任、并行
尊重、简单、重用、检查、并行 勇气、反馈、认真、责任
不良品维修管理规定
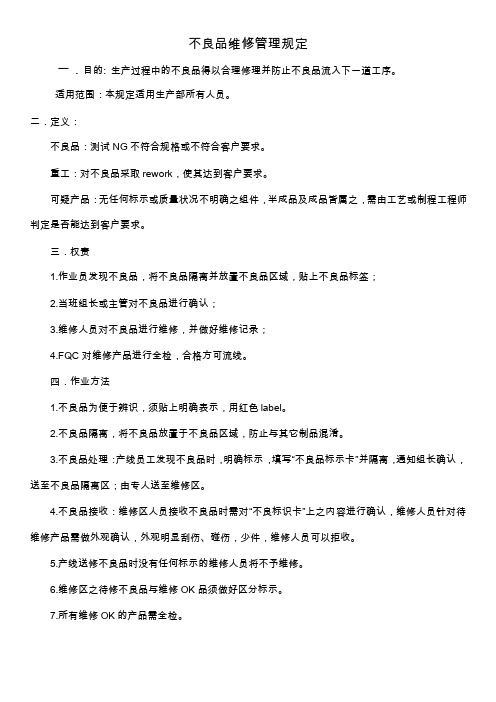
不良品维修管理规定
一.目的: 生产过程中的不良品得以合理修理并防止不良品流入下一道工序。
适用范围:本规定适用生产部所有人员。
二.定义:
不良品:测试NG不符合规格或不符合客户要求。
重工:对不良品采取rework,使其达到客户要求。
可疑产品:无任何标示或质量状况不明确之组件,半成品及成品皆属之,需由工艺或制程工程师判定是否能达到客户要求。
三.权责
1.作业员发现不良品,将不良品隔离并放置不良品区域,贴上不良品标签;
2.当班组长或主管对不良品进行确认;
3.维修人员对不良品进行维修,并做好维修记录;
4.FQC对维修产品进行全检,合格方可流线。
四.作业方法
1.不良品为便于辨识,须贴上明确表示,用红色label。
2.不良品隔离,将不良品放置于不良品区域,防止与其它制品混淆。
3.不良品处理:产线员工发现不良品时,明确标示,填写“不良品标示卡”并隔离,通知组长确认,送至不良品隔离区;由专人送至维修区。
4.不良品接收:维修区人员接收不良品时需对“不良标识卡”上之内容进行确认,维修人员针对待维修产品需做外观确认,外观明显刮伤、碰伤,少件,维修人员可以拒收。
5.产线送修不良品时没有任何标示的维修人员将不予维修。
6.维修区之待修不良品与维修OK品须做好区分标示。
7.所有维修OK的产品需全检。
退回、返工、重工产品处理规定

1.目的为确保客户退回品、制程不合格品的返工和重工后产品符合本公司质量、食品安全、BRC 要求和客户要求。
特制定本规定。
2.适用范围经判定为需返工或重工的不合格品。
3.职责3.1生产:负责厂内品管判定的重工品及客户退回的不良品需重工的之生产安排。
3.2品管:负责提供重工品的相关信息,特别是客户要求,并负责提供不良限度样品以利生产进行重工作业, 同时对此问题协同生产等有关部门做原因分析调查,提出矫正预防措施。
3.3业务:对需重工的不合格品按客户要求及品管提供的不良限度样品样品实施重工,并对此问题协同品管做原因分析调查,负责实施矫正预防措施并进行效果追踪。
4.定义无5.作业内容5.1制程检验的重工品:1)检验员在抽检时,品质判定NG时,应填写《重工通知单》经品质组长确认后,交现场组长签字确认(附不良样品),有异议时生产与品管协商解决,若双方确认OK后生产班组长安排作业员按重工方法要求对重工品进行矫正和修复。
必要时应对重工之不良品作特殊标识,以便追溯。
2)对已确认需重工品,生产设立专门重工区,与产线产品隔离、区分并标示,在《不良品处理记录表》上对不良状况进行记录。
3)生产应对重工合格品作标记区分,不良品按《不合格品质制程序》处理,并记录于《不良品处理记录表》中。
4)品管对重工品应按《产品检验规范》进行检验处理。
5.2出货检验及客户判定退货的重工品:1)品检在出货检验及客户退货品检验的不良率超过允收水平时,开立《品质异常处理单》经品质(组)长确认,交计划、业务等各相关部门负责人会签(附不良样品)后,由品质部经理裁决确定为重工时,品管将《品质异常处理单》复印件贴在重工品上。
2)计划按《品质异常处理单》开出《车间生产工艺制造作业单》通知业务部门进行重工处理。
3)生产单位接到计划的制造作业单后,依计划排程,按重工方法要求安排作业员对产品进行重工,必要时应对合格品作特殊标记,不良品按《不合格品控制程序》处理,并记录于《不良品处理记录表》中。
MRB流程
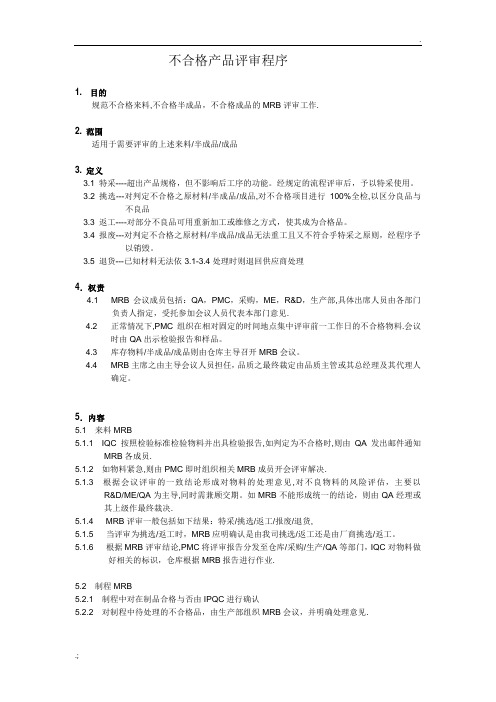
不合格产品评审程序1. 目的规范不合格来料,不合格半成品,不合格成品的MRB评审工作.2. 范围适用于需要评审的上述来料/半成品/成品3. 定义3.1 特采----超出产品规格,但不影响后工序的功能。
经规定的流程评审后,予以特采使用。
3.2 挑选---对判定不合格之原材料/半成品/成品,对不合格项目进行100%全检,以区分良品与不良品3.3 返工----对部分不良品可用重新加工或维修之方式,使其成为合格品。
3.4 报废---对判定不合格之原材料/半成品/成品无法重工且又不符合乎特采之原则,经程序予以销毁。
3.5 退货---已知材料无法依3.1-3.4处理时则退回供应商处理4.权责4.1 MRB会议成员包括:QA,PMC,采购,ME,R&D,生产部,具体出席人员由各部门负责人指定,受托参加会议人员代表本部门意见.4.2 正常情况下,PMC组织在相对固定的时间地点集中评审前一工作日的不合格物料.会议时由QA出示检验报告和样品。
4.3 库存物料/半成品/成品则由仓库主导召开MRB会议。
4.4 MRB主席之由主导会议人员担任,品质之最终裁定由品质主管或其总经理及其代理人确定。
5.内容5.1 来料MRB5.1.1 IQC按照检验标准检验物料并出具检验报告,如判定为不合格时,则由QA发出邮件通知MRB各成员.5.1.2 如物料紧急,则由PMC即时组织相关MRB成员开会评审解决.5.1.3 根据会议评审的一致结论形成对物料的处理意见,对不良物料的风险评估,主要以R&D/ME/QA为主导,同时需兼顾交期。
如MRB不能形成统一的结论,则由QA经理或其上级作最终裁决.5.1.4 MRB评审一般包括如下结果:特采/挑选/返工/报废/退货,5.1.5 当评审为挑选/返工时,MRB应明确认是由我司挑选/返工还是由厂商挑选/返工。
5.1.6 根据MRB评审结论,PMC将评审报告分发至仓库/采购/生产/QA等部门,IQC对物料做好相关的标识,仓库根据MRB报告进行作业.5.2 制程MRB5.2.1 制程中对在制品合格与否由IPQC进行确认5.2.2 对制程中待处理的不合格品,由生产部组织MRB会议,并明确处理意见.5.3 库存品MRB5.3.1 仓库定期对库存品进行清点并送检,由QA部依据相关检验标准进行检验,如检验不合格,由出具不合格检验报告。
停线异常处理作业流程

2. IPQC通知QE 5分钟内到现场确认,QE并于10分钟内初步分析或判定不
良状况为材料、电子或机构问题
3. 制造准备不良机台.1.提案单位5分钟内开立停线通知单,由品管主导
召开停线会议.
4.ENG提出短期对策﹑责任单位及短期对策导入时间于2H内完成。如ENG 2H内不能提供短期对策,而在处理方式上各部门有争议,需由最高层主管 2小时
异常修正联络单-CAR
异常修正联络单-CAR 异常修正联络单-CAR
1.在以下状况下由生产/品保提出停线:
1.1同种不良连续5台,同一小时同一不良达5%; 1.2同一小时内累计不良现象之不良率T1≧5%,T2≧15%;
10分钟
1.3制程中出现安规异常时;
1.4同一小时单件材料不良率≧3%时开异常单换料.
13.2产线检验人员﹑IPQC﹑产线组长须对导入后的对策进行确认.
14.短期对策有效则继续生产﹔无效则重新检讨.
15.长期对策导入须有QE人员跟踪﹔长期对策有效则可结案并于效果确
认内如实填写,对策无效,则重新检讨.
16.重工品必须按重工WI或ME现场指导进行作业﹐重工品须经品管人员
重新进行检验﹔重工内容详细记录报表内.
继续生产 Yes
核准﹕
审核﹕
制表﹕
决议是否开线.
5.有短期对策时由品保召开检讨会议.
6.ME/PE/PTE/IQC/PMC责任单位须提出长期对策﹐及长期对策导入时间
导入方式于48H完成.
.
10分钟
8.质量问题发质量异常修正联络单给分析单位ME/PE/PTE.
9.不良内容要详细描述清楚,要求写明不良项﹑不良数﹑不良率﹑检验
MFG
IPQC/QE