250 t转炉生产用氧实践
转炉工艺操作规程
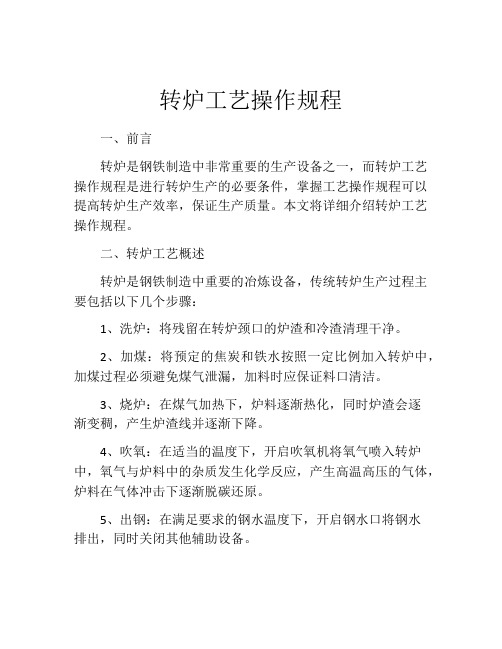
转炉工艺操作规程一、前言转炉是钢铁制造中非常重要的生产设备之一,而转炉工艺操作规程是进行转炉生产的必要条件,掌握工艺操作规程可以提高转炉生产效率,保证生产质量。
本文将详细介绍转炉工艺操作规程。
二、转炉工艺概述转炉是钢铁制造中重要的冶炼设备,传统转炉生产过程主要包括以下几个步骤:1、洗炉:将残留在转炉颈口的炉渣和冷渣清理干净。
2、加煤:将预定的焦炭和铁水按照一定比例加入转炉中,加煤过程必须避免煤气泄漏,加料时应保证料口清洁。
3、烧炉:在煤气加热下,炉料逐渐热化,同时炉渣会逐渐变稠,产生炉渣线并逐渐下降。
4、吹氧:在适当的温度下,开启吹氧机将氧气喷入转炉中,氧气与炉料中的杂质发生化学反应,产生高温高压的气体,炉料在气体冲击下逐渐脱碳还原。
5、出钢:在满足要求的钢水温度下,开启钢水口将钢水排出,同时关闭其他辅助设备。
6、停炉:在出钢完成后,将转炉进行清理,消除隐患,准备下一次生产。
三、转炉工艺操作规程1、洗炉操作人员进入转炉周围进行检查,确认转炉颈口、台阶等部位无异物。
在高温状态下,使用聚乙烯皮扫、黑铁皮扫等清洁品,进行全面的清洗。
清洗完毕后反复检查,确保转炉内外部干净无异物。
2、加煤在加煤过程中,操作人员需要在上料前先确认料口无异物,且料口周围没有明火等安全隐患。
根据生产计划,按照一定的比例开足橱门,平均分配炉料。
在加料过程中,需要注意煤气泄漏,并及时清理料口,保证料口干净,加料完毕后及时关闭料门,防止煤气泄漏。
3、烧炉加煤后,操作人员需要监控转炉内部温度,确认炉体温度达到烧炉条件,才能进行下一步操作,同时应注意炉内温度和氧气流量的平衡,保证热量分布均匀。
在炉渣变稠时,要注意炉门、倾炉口等设备的密封,防止炉渣外溢。
4、吹氧吹氧是冶炼中重要的步骤,操作人员要掌握合理的吹氧时间和氧气流量,以保证化学反应的完全性和热量的平衡性。
在吹氧后,需要确认炉料的C、Si等指标已经达到要求,同时也需要注意控制炉内的压力和氧气流量。
转炉吹氧自动控制在转炉炼钢中的研究和应用
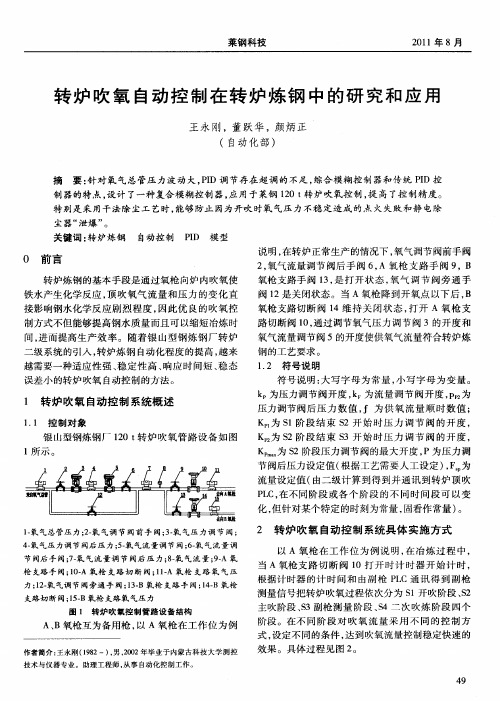
4氧 气 压 力 调 节 阀后 压 力 ;一 气 流 量 调 节 阀 ;一 气 流 量 调 一 5氧 6氧
2 转 炉 吹 氧 自动 控 制 系统 具 体 实 施 方 式
以 A氧 枪 在 工 作 位 为 例 说 明 , 冶 炼 过 程 中 , 在 当 A氧枪支 路 切 断 阀 l 开 时 计 时 器 开 始 计 时 , 0打
2 氧气 流量 调节 阀后 手 阀 6 A氧 枪 支路 手 阀 9, , , B 氧 枪支 路手 阀 1 , 打 开状 态 , 3是 氧气 调 节 阀旁 通 手
阀1 2是关 闭 状态 。 当 A氧枪 降 到开 氧点 以下后 , B
Байду номын сангаас
氧 枪支 路切 断 阀 l 持 关 闭状 态 , 4维 打开 A 氧枪 支 路 切断 阀 1 , 过调节 氧气 压 力 调节 阀 3的开 度 和 0通 氧 气流量 调节 阀 5的开 度使供 氧气 流量 符合转 炉炼
钢 的工 艺要求 。
1 2 符 号说 明 .
制方 式不但 能 够提 高钢水 质量 而且 可 以缩短 冶炼 时 间 , 而提 高生 产 效 率 。 随着 银 山 型钢 炼 钢 厂 转 炉 进
二级 系统 的引 入 , 炉炼 钢 自动化 程度 的提 高 , 来 转 越 越需 要一种 适应 性 强 、 定 性 高 、 应 时 间 短 、 态 稳 响 稳
制 器的特 点 , 计 了一种 复合模 糊控 制 器 , 用 于 莱钢 10 t 炉吹 氧控 制 , 高 了控 制 精度 。 设 应 2 转 提
特 别是 采 用干 法除 尘工 艺时 , 能够 防止 因为 开吹 时氧 气 压 力不 稳 定造 成 的 点 火失 败 和静 电除
转炉富氧吹炼设计及生产实践

每 24 h转炉生产按 5炉次计 : 1 周期至少多处
理热料为 : 15 ×3 + 17 ×2 = 79 t,每包按 18 t计 ,多处
理 4~5包冰铜 。
3 控制部分
转炉富氧吹炼过程中 ,氧浓度控制十分关键 ,氧 浓度过低达不到预期的目的 ,氧浓度过大 ,造成单位 时间内转炉反应热提高过快 ,影响炉衬寿命 ;同时氧 气浓度过高 ,容易造成炉内铜过吹 ,泡沫渣形成过 多 ,容易冒炉 ,严重时会发生危险 ;另外如果管道积 存氧气浓度过高 ,开炉时若碰到火花容易发生爆炸 。 因此 ,转炉通氧控制中 ,安全控制风量 、氧流量配比 调节 ,以及风 、氧阀门联锁等十分关键 。 3. 1 转炉富氧接入方式 本设计由供氧总管引出一支管 G0给转炉供氧 , 再由管道 G1 、G2分别连接 1#、2# 920风机主风道供给 单台转炉 ,接入点设在 920 风机放空阀的后面 。示 意图见图 1所示 。 3. 2 氧气管线上控制配置
2#风机 - 3#转炉 :时间 3. 2 h /炉次 , 32 m in /包
转炉吹炼富氧浓度 24%时 , 2 台转炉的作业时
间 ,以单台风机所对的转炉计算 :
转炉炼钢供氧制度
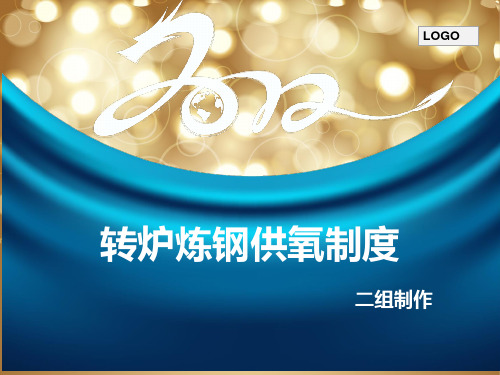
转炉炼钢供氧制度
二组制作
供氧制度的主要内容
LOGO
喷头结构 供氧强度 供氧压力 枪位控制
一、氧枪的结构 喷头
导热性能好的止痛锻造。 导热性能好的止痛锻造。 有单孔拉瓦尔型、 有单孔拉瓦尔型、多孔 拉 瓦尔型(以 瓦尔型( 三孔居多)。 三孔居多)。
LOGO
枪身
无缝钢管制作的三层套 管组合而成。 管组合而成。
3
每吨金属所消耗标准状态的氧气量为48m3 每吨金属所消耗标准状态的氧气量为48m3 每吨金属的实际需氧量为64.0~56.5m3 每吨金属的实际需氧量为64.0~56.5m3
2012-4-21
三、供氧压力
LOGO
氧气的压力是转炉炼钢中供氧操作的一个重要参 数. 转炉中涉及的氧气压力主要是喷头前的绝对压力 和使用压力P P0和使用压力P用. 通常所说的供氧压力是指转炉车间内氧气压力测 定点的表压值,又称使用压力,常以P 来表示. 定点的表压值,又称使用压力,常以P用来表示. 使用压力P 与喷头前压力P 间的关系为: 使用压力P用与喷头前压力P0间的关系为: P用=P0-0.1+(0.15~0.25) 实际供氧压力允许有约45%的正偏差, 45%的正偏差 实际供氧压力允许有约45%的正偏差,特别是在采 用分阶段定量装入法时,随着装入量的递增, 用分阶段定量装入法时,随着装入量的递增,要相 应提高供氧压力,以增大供氧量. 应提高供氧压力,以增大供氧量.
2012-4-21
吹氧类型与枪位控制
LOGO LOGO
转炉吹氧类型的三类操作: 转炉吹氧类型的三类操作
1.衡氧压变枪位操作 衡氧压变枪位操作 2.衡枪位变氧压操作 衡枪位变氧压操作 3.变枪位变氧压操作 变枪位变氧压操作 枪位控制 转炉炼钢中枪位控制的基本原则是:根据吹炼中 转炉炼钢中枪位控制的基本原则是 根据吹炼中 出现的具体情况及时进行相应的调整,力争做到既不 出现的具体情况及时进行相应的调整 力争做到既不 出现喷溅,又不产生反干 使冶炼过程顺利到达终点.实 又不产生反干,使冶炼过程顺利到达终点 出现喷溅 又不产生反干 使冶炼过程顺利到达终点 实 际生产中,生产条件千变万化 枪位也不能一成不变,而 际生产中 生产条件千变万化,枪位也不能一成不变 而 生产条件千变万化 枪位也不能一成不变 应根据具体情况进行相应的调整.影响枪位的因素主 应根据具体情况进行相应的调整 影响枪位的因素主 要是熔池深度、铁水的温度和成分、 要是熔池深度、铁水的温度和成分、石灰的质量和用 供氧压力等. 量、供氧压力等.
转炉煤气回收量的分析与实践

转炉煤气回收量的分析与实践摘要:本文通过物料平衡的方法,计算出转炉煤气回收的极限量,并结合实际生产操作,放宽转炉煤气回收条件,将转炉实际最大回收量与极限量进行对比,并从电能利用方面分析提高转炉煤气回收量的经济性。
关键词:转炉煤气极限回收经济性1 概述随着国家能源政策的进一步加强,钢铁市场竞争的越发剧烈,各钢铁企业在追求钢材品质的同时,更在力争如何降低吨钢能耗,而在整个冶炼工序中,唯一能实现负能冶炼的就是转炉炼钢环节。
转炉煤气回收占整个转炉工序能源回收的80%-90%,是降低炼钢能耗,实现负能炼钢的关键环节,因此,各企业都十分重视转炉煤气回收,尽可能的多回收转炉煤气。
目前,对如何提高转炉煤气回收的研究较多,但对于煤气回收量的潜力有多大的研究较少,从而导致一些企业对吨钢回收量预估不足,后续煤气柜和加压系统配置能力偏低,一旦想提高吨钢煤气回收量则困难重重,设备能力受限,造成能源的浪费;同时也有些企业为了追求吨钢回收量,过大的配置煤气柜容量,以及加压机风量的配置,提高了工程一次投资成本和运行成本,设备能力上也是大马拉小车,造成一定程度的浪费。
本文基于碳平衡原理,建立转炉煤气回收量计算模型,计算了转炉煤气回收量的极限值,同时放宽回收条件,从实际生产中最大限度的提高吨钢回收量,得到生产数据,进而根据实际回收量与极限回收量对比确定转炉煤气回收的潜力,为后续回收设施的选型提供可靠依据。
2 转炉煤气极限回收量计算模型根据冶金反应原理,转炉烟气主要是由原料中碳氧化产生的,含碳原料主要有铁水和炭质发热剂。
原料中的碳以一定的比例氧化成CO、CO,以炉气形式排2出,经炉口处吸入一定的空气形成烟气。
转炉烟气根据回收设备条件和回收技术水平,回收成可利用的能源介质即转炉煤气。
按物料平衡和热平衡建立转炉煤气回收量计算模型,如下:式中:折算为标准热值后的转炉煤气量,m3/t;3018——CO热值,Kcal/m32000——标准热值,Kcal/m3碳氧化生成的炉气量,m3/t;炭质发热剂生成的炉气量,m3/t;空气吸入系数,即实际空气吸入量与转炉气完全燃烧所需的理论空气量的比值;转炉煤气回收比,即煤气回收量与转炉煤气发生量的比值,%;的分配比。
转炉炼钢车间设计
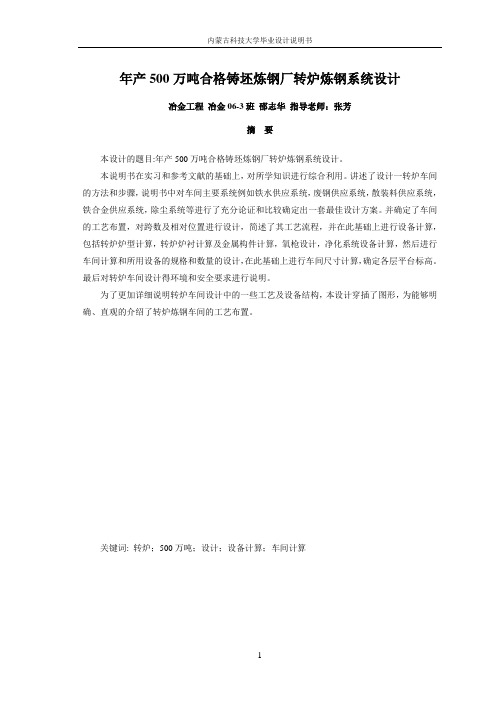
年产500万吨合格铸坯炼钢厂转炉炼钢系统设计冶金工程冶金06-3班邵志华指导老师:张芳摘要本设计的题目:年产500万吨合格铸坯炼钢厂转炉炼钢系统设计。
本说明书在实习和参考文献的基础上,对所学知识进行综合利用。
讲述了设计一转炉车间的方法和步骤,说明书中对车间主要系统例如铁水供应系统,废钢供应系统,散装料供应系统,铁合金供应系统,除尘系统等进行了充分论证和比较确定出一套最佳设计方案。
并确定了车间的工艺布置,对跨数及相对位置进行设计,简述了其工艺流程,并在此基础上进行设备计算,包括转炉炉型计算,转炉炉衬计算及金属构件计算,氧枪设计,净化系统设备计算,然后进行车间计算和所用设备的规格和数量的设计,在此基础上进行车间尺寸计算,确定各层平台标高。
最后对转炉车间设计得环境和安全要求进行说明。
为了更加详细说明转炉车间设计中的一些工艺及设备结构,本设计穿插了图形,为能够明确、直观的介绍了转炉炼钢车间的工艺布置。
关键词: 转炉;500万吨;设计;设备计算;车间计算第一章 文献综述 第二章 生产规模及产品方案2.1 金属平衡计算87%铁水 510.78万吨入炉金属料 587.1万吨13%废钢 76.32万吨 93%转炉钢水 546万吨97%钢包 529.62万吨 LF 精炼 529.62万吨3%损失 16.38万吨2%损耗 10.59万吨98%RH 精炼 519.03万吨0.7%损失 3.63万吨99.3%中间包 515.40万吨0.03%氧化铁皮 0.15万吨97.5%钢坯 502.51万吨1.2%连铸切头 6.18万吨1%中间罐结壳 5.15万吨0.5%连铸废品 2.51万吨99.5%合格坯500万吨图2.1 金属平衡表2.2 生产规模的确定该转炉车间的生产规模是年产合格铸坯500万吨。
2.2.1 转炉座数和大小的确定设计年产500万吨合格铸坯的转炉炼钢系统。
由金属平衡表计算可知,所需的转炉钢水年产量为546万吨。
炼钢生产中转炉炼钢脱氧工艺

炼钢生产中转炉炼钢脱氧工艺摘要:近些年来,随着炼钢企业的快速发展,很多先进的炼钢技术和设备被的应用和推广。
在具体的炼钢生产过程中,广泛的应用转炉炼钢脱氧方法,有利于提高钢产品的质量,相关技术人员需要对转炉中的氧气含量进行有效的控制,对提高岗产品质量具有重要的作用,也是整个炼钢生产过程中的重要环节。
由于炼钢生产过程中会产生一些氧气成分,作为生产管理人员应该明确炼钢生产过程中所产生的氧气对钢产品的质量有着重要的危害和影响,所以应该加强脱氧方法和技术的研究与创新,善于运用先进的脱氧工艺和脱氧技术不断提高脱氧效果,因此,文章对炼钢生产中转炉炼钢脱氧工艺的相关内容进行分析,为炼钢企业提高钢产品质量提出一些合理化建议。
关键词:炼钢;转炉炼钢;脱氧工艺前言:近些年来,炼钢企业竞争日趋激烈,所以企业管理者应该加强产品质量的重视,同时做到有效的成本控制,不断提高市场竞争力。
通过改善炼钢生产核心技术的方式,实现企业的长远发展[1-2]。
在具体的炼钢过程中,转炉炼钢是重要的生产环节,在转炉炼钢运行过程中会产生一定量的氧气,通过技术人员的分析和研究表明,转炉炼钢生产所产生的氧气对钢铁产品质量具有一定的影响[5],所以在生产过程中要求技术人员采用有效的脱氧方法,提升脱氧效果[3-4]。
在基础生产工艺的前提和基础上,对脱氧工作进行优化和完善,对提高钢铁产品质量具有重要的作用。
1转炉炼钢的含义转炉生产过程中,通过高温和高炉的作用下,对钢进行氧化处理,目的是降低生钢的碳元素含量,有利于保障产品的质量。
由于所冶炼的钢与铁材质上存在很大的差异,其中所富含的碳总量也存在不同,钢的碳含量一般在2%以下,比生铁熔点更高。
转炉炼钢生产过程中都广泛的运用低碳钢,这种钢材的材质和硬度相对不高,所以这类钢材在使用过程中具有一定的可塑性,在不同的生产与制造领域中得到了广泛的应用。
2炼钢过程中的影响因素分析在具体的炼钢工作中,相关人员应该注重炼钢设备与炼钢质量的有效控制,在不同的炼钢环节,科学合理的使用原材料,满足炼钢工作的质量要求,生产出符合要求的产品。
转炉少渣炼钢工艺操作(转炉造渣方式)

2)留渣量较大时,采用精炼返回渣实现炉渣固化;
留渣量较大的情况下,留渣量随循环炉次增加而增加,脱磷期结束倒 渣量在4吨(100吨转炉)左右计算,循环第2炉留渣量在8~9吨左右。留渣
量较大情况下溅渣护炉时间延长至6分钟左右,采用精炼返回渣可以起到
迅速固化炉渣的作用。
• 3)适量加入精炼返回渣
为改善大渣量条件下的炉渣固化效果,缩短溅渣护炉时间,同
少渣炼钢工艺简介
姓名:柴先义
部门:炼钢作业部
日期:2014-5-20
目 录
第1章 少渣炼钢工艺简介
第2章 少渣炼钢工艺操作
第3章 少渣炼钢工艺难点控制
第4章 国内外少渣炼钢效果
炼钢作业部
第1章 少渣炼钢工艺简介
1.1 少渣炼钢工艺简析
铁水“三脱”使传统炼钢工艺发生了显著变化,在铁水预处
理阶段进行脱硅、脱磷和脱硫,使炼钢转炉的主要功能转变为
少钢工艺路线中,后三种炼钢工艺 铁水经过“三脱”预处理后再脱碳炼钢,能够做到少渣 操作 。四种转炉炼钢工艺路线的渣量比较见图1。从图l 可以看出,后三种炼钢工艺的吨钢渣量低于70 kg/t。
1.3 氧气转炉常用的造渣方法
1、单渣法: 在吹炼过程中只造1次渣,中途不倒渣、不扒渣,直到吹炼终点 出钢。单渣操作工艺比较简单,吹炼时间短,劳动条件好,易于实现 自动控制。正常情况下脱磷效率在80%左右,脱硫效率为30%~40%; 第一批渣料是在开吹的同时加入,第二批渣料的加入时间是在硅锰氧 化基本结束,第一批渣料基本化好,碳焰初起时加入。 2、双渣法: 在吹炼中期倒出或扒除1/2~2/3炉渣,然后加入渣料重新造渣的 方法为双渣操作。根据铁水成分和所炼钢种的要求,也可以多次倒炉 倒渣造新渣。在铁水含硅较高,含磷大于0.5%,吹炼优质钢,吹炼中、 高碳钢种时,都可以采用双渣操作。采用双渣操作可以在转炉内保持 最小的渣量,同时又能达到最高的脱磷硫效率。双渣操作脱磷效率在 90%以上,脱硫效率约45%。双渣操作会延长吹炼时间,增加热量损 失,降低金属收得率,不利于自动控制,恶化劳动条件。
双渣法冶炼实践

_
/ 淫
双渣法 > 台炼 实践
石 磊 唐 文 明 王 玉 生 刘 国 庆
摘要 : 本 文叙 述 了邯 铜 邯 宝 炼钢 厂 2 5 0 t 转 炉 双 渣 法 炼 钢 工 业 性 试 验 。邯 宝 炼钢 厂 转 炉 通过 采 用 双 渣 法 工 艺 进 行 冶 炼 , 转
度/ ℃ 耗 氧
合 适的炉渣成分 . 在 造 第 ~ 次 渣 的过 程 中 . 前期熔池 较低 的
温 度情 况下 能快 速 成 渣 . 具 备 脱 磷 能 力 转 炉 脱 磷 的反 应 方 程式如下 :
/ m i n
S , % S / %
【 % [ P v %
氧/ p p m 碳 , % 量 / N M3
( 1 )
l o g K = l o g ( a P 2 ( 幽2 1 P l a [ o 1 ) = 4 3 4 4 3 / T 一 3 3 . 0 2
根据上式可知 . 随 着 温 度 的降 低 . 反应常数急剧升高 . 磷
的 脱 除 能 力 大 大 提升 所 留 的 炉 渣 . 有 比较 高 的 温度 和合 适 的碱度 . 在 前 期 较 低 的熔 池 温 度 下 能 快 速 成 渣 . 有 利 于 脱 磷
文 献 标识 码 : B
作者 单位 : 河 北 钢铁 集 团邯 郸 钢 铁 集 团有 限 责 任 公 司邯 宝 炼钢 厂
刖 禹
一
、
高 了 合金 收得 率 氧 含 量 的 降低 , 降 低 了钢 液 中能 引 入 的氧
化物夹杂 , 从 而 为 洁 净 钢 的 生 产 创 造 了有 利 条 件 。而 且 通 过
耗 、 石 灰 和 轻 烧 白云 石 消耗 的 目的 。 通 过 前 期 采 用 留渣 作 业 . 所 留炉 渣 . 具 备 一 定 的 温 度 和
氧气顶吹转炉设计

3.1 转炉炉型设计3.1.1 转炉炉型设计概述(1)公称容量及其表示方法公称容量(T),对转炉容量大小的称谓,即平时所说的转炉的吨位。
它是转炉生产能力的主要标志和炉型设计的重要依据。
目前国内外对公称容量的含义的解释还很不统一,归纳起来,大体上有以下三种表示方法:1)以平均金属装入量(t)表示;2)以平均出钢量(t)表示;3)以平均炉产良坯量(t)表示。
在一个炉役期内,炉役前期和后期的装入量或出钢量不同,随着吹炼的进行,炉衬不断地受到侵蚀,熔池不断扩大,装入量增大,所以三种表示方法都是以其平均容量来表示。
这三种表示方法各有其优缺点,以平均金属装入量表示公称容量,便于进行物料平衡和热平衡计算,换算成新炉装入量时也比较方便。
以平均炉产良坯量表示公称容量,便于车间生产规模和技术经济指标的比较,但是在进行炉型设计时需做较复杂的换算。
以平均出钢量表示公称容量则介于两者之间,其产量不受操作方法和浇铸方法的影响,便于炼钢后步工序的设计,也比教容易换算成平均金属装入量和平均炉产良坯量。
设计的公称容量与实际生产的炉产量基本一致。
所以在进行炉型设计时采用以平均出钢量表示公称容量比较合理。
(2)炉型的定义:转炉炉型是指转炉炉膛的几何形状,亦即指由耐火材料砌成的炉衬内形。
(3)炉型设计的意义转炉是转炉炼钢车间的核心设备,炉型及其主要参数对转炉炼钢的生产率、金属收得率、炉龄等技术经济指标都有着直接的影响,炉型设计的是否合理关系到冶炼工艺能否顺利进行的问题,如喷溅问题,除与操作因素有关外,炉型设计是否合理也是个重要因素,并且车间的主厂房高度以及主要设备,像除尘设备,倾动机构设备等都与炉型尺寸密切相关。
而且转炉一旦投产使用,炉型尺寸就很难再作改动,因为不论变动直径还是高度都牵涉到耳轴位置,它是与转炉基础联系在一起的,一般不能随意变动。
所以说,设计一座炉型结构合理,满足工艺要求的转炉是保证车间正常生产的前提。
而炉型设计又是整个转炉设计的关键。
转炉底吹工艺优化的研究与实践

转炉底吹工艺优化的研究与实践尚 游(山东钢铁股份有限公司莱芜分公司炼钢厂 济南 271104)摘 要:目前,莱钢型钢炼钢厂转炉底吹工艺比较落后,底吹工艺对转炉冶金效果的促进作用不够明显。
为了充分改善底吹工艺、吹炼参数,莱钢型钢炼钢厂根据生产实际情况,调整了底吹枪分布,研究了最佳底吹流量参数,通过稳定炉底,加强对底吹“炉渣-金属蘑菇头”的维护,使转炉碳氧积在炉龄增长的情况下得到良好控制,促进了低成本、高效化冶炼。
关键词:底吹分布;供气强度优化;碳氧积RESEARCH AND PRACTICE ON OPTIMIZATION OF CONVERTER BOTTOM BLOWING PROCESSShang You(The Steelmaking Plant, Laiwu Branch of Shandong Iron and Steel Co., Ltd., Jinan 271104, China)Abstract: At present, the bottom blowing process of the converter in the steel section mill of Lai Steel is relatively backward, and the bottom blowing process has not promoted the metallurgical effect of the converter obviously. In order to fully improve the bottom blowing process and blowing parameters, the section steel mill of Lai Steel adjusted the distribution of bottom blowing gun according to the actual production situation, studied the optimum parameters of the bottom blowing flow, and strengthened the maintenance of the bottom blowing “furnace slag-metal mushroom head” by stabilizing the furnace bottom. The maintenance of the “head” ensures the good control of the carbon and oxygen product of the converter under the condition of growing furnace age, and promotes low-cost and high-efficiency smelting. Key words: bottom blowing distribution; optimization of gas supply intensity; carbon and oxygen product作者:尚游,男,38岁,工程师收稿日期:2020-07-24莱钢银山型钢炼钢厂自2004年7月份开始,逐步投产了4座120 t顶底复吹转炉,通过不断摸索操作工艺,采用更加科学合理的操作技术,复吹技术有了很大的进步,底吹透气砖寿命实现了与转炉炉龄同步,已突破万炉大关。
04-武钢250t转炉“负能炼钢”节能实践(PPT)

偏差
-
控制单元
被控对 象
介质消耗折 算标准煤值
输出量
反馈量 图5 构建工序能耗闭环控制系统
五、提高转炉工序“负能炼钢”水平主要做 法及技术
以原先最佳的转炉工序能耗值(作参考)作为其系统的给 定量,以对工序能耗影响大的电耗、氧气消耗、煤气消耗 及转炉煤气回收、蒸汽回收作为该系统的被控对象,以制 定的相关管理方法、采取的相应措施及科技攻关项目作为 控制单元,并以每天从计控公司发出的E-mail上取出的各 能源介质消耗的数据为准,输入计算机计算出的每天或每 月的工序能耗作为系统的反馈量,与给定量进行比较作为 控制系统的偏差,其扰动因素主要有因生产节奏和工艺要 求等造成的回炉,使得该炉钢水吹氧量过大、吨钢回收的 转炉煤气下降、钢水温度不足造成钢包炉电极加热用电量 增加;有因生产节奏不稳定、环境温度的高低、气候潮湿 的不同、空气和煤气的配比的不同以及烘烤对象的冷热不 同,造成铁水罐、钢水罐烘烤时间长短不一,影响了煤气 的消耗量;还有因公司内部回收的转炉煤气和蒸汽用户不 足,多余的回收转炉煤气和蒸汽只得放散等等。
四、转炉工序能耗分析
氩气 6.4% 其它 15.69% 氧气 34.89%
蒸汽回 收 21.92% 煤气回 收 78.08% 图4 转炉能源回收组成比例图
氮气 5.91% 煤气 16.17%
电 20.94%
图3 能源消耗组成比例图
转炉工序能耗的构成转炉工序能耗组成比例由图3内诸工序能源消耗和图4 能源回收两部分组成,消耗的能源介质为氧气、电、煤气、氮气、氩气、压缩 空气、蒸汽和水等,回收部分为转炉煤气和蒸汽,是实现转炉“负能炼钢”的 关键要素。 由图3可见氧气消耗占34.89%,但它与吹炼过程有关,降低氧气消耗的潜力 较大,氩气的消耗随着高附加值、高难度产品比例的增加而增加,而电力和煤气 消耗尽管所占比例低于氧气,但随着科学的管理和技术改造、生产的进一步合理 组织将有较大幅度下降,降低工序能源单位消耗量的关键是减少氧气、电力和煤 气的消耗量。而转炉出口烟气总热量属于二次能源范围, 折合标准煤32.71公斤 /吨钢,显然回收转炉煤气、蒸汽已经成为三炼钢厂实现“负能炼钢”的关键要 素,它是属于二次能源范围,如果将它随意放散不仅白白浪费了大量能源,还会 由于CO有毒造成公害,通过回收煤气和蒸汽可回收二次能源,对全厂节能减排、 降低生产成本具有非常重要的意义。
250T氧气顶吹转炉主体设备设计及支撑机构设计详解

本科毕业设计(论文)250T氧气顶吹转炉主体设备设计及支撑机构设计xx燕山大学里仁学院2015年6月燕山大学里仁学院本科毕业设计(论文)课题名称:250T氧气顶吹转炉主体设备设计及支撑机构设计系别:机械工程系年级专业:冶炼11-3班学生姓名: xx指导教师:许xx完成日期: 2015年6月燕山大学里仁学院毕业设计(论文)任务书摘要氧气顶吹转炉主体设备是实现炼钢工艺操作的主体设备,它由炉体、炉体支撑系统、炉体倾动机构以及炉体与托圈联接装置等组成。
本次设计针对250T氧气顶吹转炉主体设备和支撑机构进行。
炉体采用A型炉(即锥球型),活炉帽死炉底结构;托圈采用整体式托圈结构,其断面形状选择矩形断面;炉体倾动力矩的计算利用Solidworks 软件绘制实体从而得到炉体、炉液的重心和重量,结合计算公式进行计算;为保证转炉在倾动过程中的安全性,最佳耳轴位置的确定利用全正力矩原则进行;炉体支撑系统选用耳轴与耳轴轴承座的支承方式;倾动机构选用带有扭力杆式缓冲装置的四点才啮合全悬挂式倾动机构;炉体与托圈联接装置采用活节螺栓与止动托座配合的连接结构。
同时对250T氧气顶吹转炉的主体设备和支撑装置中的各个部分进行工作原理的分析和结构设计。
并且针对其工作状况和受力情况等进行理论分析和校核。
关键字氧气顶吹转炉主体设备;倾动机构;支撑装置AbstractThe main equipment in oxygen top-blown converter Is the realization of the main equipment in bof steelmaking process the body of the equipment operation, and it is supported by furnace, furnace system, furnace tilting mechanism, as well as linkage and coil, furnace lining, etc. The design for the main equipment in 250 t oxygen top-blown converter and tilting mechanism.Furnace adopt type A furnace (namely cone ball type), live hat die hearth furnace structure; Supporting ring with the ring structure, the cross section shape select rectangle cross section; Furnace tilting torque calculation using Solidworks software rendering entities to get the center of gravity and weight of the furnace, furnace, combined with the formula to calculate; In order to ensure the safety in the process of converter in tilting, best trunnion position using the principle of positive moment; Furnace body support system selects the trunnion and trunnion bearing supporting way; Tilting mechanism with torsion bar used buffer device only four meshing full suspension type tilting mechanism; Furnace body and supporting ring connection device adopts eyelet bolt and retaining bracket with the connection of the structure.At the same time for 250 t oxygen top-blown converter of the individual parts of the body of the equipment and the connecting device for the analysis of the working principle and structure design. And for its working condition and stress distribution of the theory analysis and checking.Keyword The main equipment in oxygen top-blown converter ;Tilting mechanism ;support device目录摘要 .................................................................................................. 错误!未定义书签。
邯钢新区二期250t转炉氧气管道施工方案
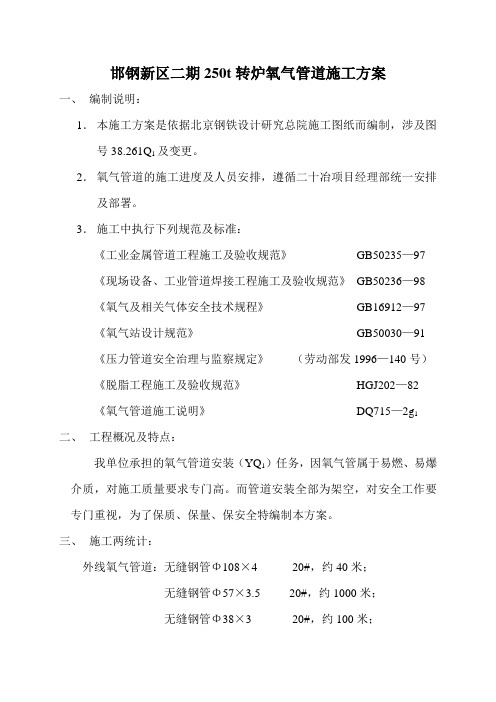
邯钢新区二期250t转炉氧气管道施工方案一、编制说明:1.本施工方案是依据北京钢铁设计研究总院施工图纸而编制,涉及图号38.261Q1及变更。
2.氧气管道的施工进度及人员安排,遵循二十冶项目经理部统一安排及部署。
3.施工中执行下列规范及标准:《工业金属管道工程施工及验收规范》GB50235—97《现场设备、工业管道焊接工程施工及验收规范》GB50236—98《氧气及相关气体安全技术规程》GB16912—97《氧气站设计规范》GB50030—91《压力管道安全治理与监察规定》(劳动部发1996—140号)《脱脂工程施工及验收规范》HGJ202—82《氧气管道施工说明》DQ715—2g1二、工程概况及特点:我单位承担的氧气管道安装(YQ1)任务,因氧气管属于易燃、易爆介质,对施工质量要求专门高。
而管道安装全部为架空,对安全工作要专门重视,为了保质、保量、保安全特编制本方案。
三、施工两统计:外线氧气管道:无缝钢管Φ108×4 20#,约40米;无缝钢管Φ57×3.5 20#,约1000米;无缝钢管Φ38×3 20#,约100米;四、氧气管道安装施工:1.道施工应按设计图纸要求进行,如现场变更及材料代用,须征得设计部门的同意认可。
2.管材、管件、阀门进场必须具有制造厂的合格证明书,并应进行外观检查,要求其表面无裂纹、缩孔、夹渣、折叠、重皮等缺陷。
接触氧气的表面必须完全去除毛刺、焊瘤、粘砂、铁锈和其它可燃物等,保持内壁光滑洁净。
管道的除锈应进行到显现本色为止。
3.氧气阀门必须为氧气专用阀门(已脱脂),并出具出厂试压记录,进场后用四氯化碳浸泡阀门(开、闭三次)进行脱脂。
4.法兰、法兰盖的密封面应平坦、光洁,不得有毛刺或径向沟槽,凹凸面法兰应能自然嵌合,凸面的高度不得低于凹槽的深度。
5.氧气用垫片采纳紫铜、铝、聚四氟乙烯、石墨缠绕垫片等。
垫片应质地柔韧,表面应无折损、皱纹等缺陷。
转炉氧枪及供氧技术知识

转炉氧枪及供氧技术知识1.喷头设计需考虑哪些因素?要紧依照炼钢车间生产能力大小、原料条件、供氧能力、水冷条件和炉气净化设备的能力来决定。
同时考虑到转炉的炉膛高度、直径大小、熔池深度等参数确定其孔数、喷孔出口马赫数和氧流股直径。
关于原料中废钢比高、高磷铁水冶炼或需二次燃烧提温等情形,则其氧枪喷头的设计就需专门考虑。
依照以上因素确定氧气流量(Nm3/h)、喷头马赫数、操作氧压(MPa)、喷头孔数、喉口直径(mm)、喷孔出口直径(mm),喷孔夹角等。
2.转炉炉容比(V/T)的概念,及它对吹炼过程有何阻碍?转炉炉容比(V/T)是指转炉炉腔内的自由空间的容积V(m3)与金属装入量(铁水+废钢+生铁块单位t)之比。
装入量过大,则炉容比相对就小,在吹炼过程中可能导致喷溅增加、金属损耗增加、易烧枪粘钢;装入量过小,则熔池变浅,炉底会因氧气射流对金属液的强烈冲击而过早损坏,甚至造成漏钢。
大型转炉的炉容比一样在0.9-1.05m3/t之间,而小型转炉的炉容比在0.8m3/t左右。
通常在转炉容量小、铁水含磷高、供氧强度大、喷孔数少,或用铁矿石或氧化铁皮做冷却剂等情形下,则炉容比应选取上限。
反之则选取下限。
3.如何选取熔池深度?通常最大冲击深度L与熔池深度h之比选取L/h=0.4 —0.7。
当L/h〈0.3时,即冲击深度过浅,则脱碳速度和氧的利用率会大为降低,还会导致显现终点成分及温度不平均的现象;当L/h〉0.7时,即冲击深度过深,有可能损坏炉底和喷溅严峻;在适合的炉容比情形下,假如熔池装入量过浅,可考虑将熔池砌成台阶形。
4.如何运算冲击反应区深度?运算公式为:h/d=(ρ出/ρ钢)1/2·(β / H)1/2·V出/g1/2 (4.1)出式中h —冲击反应区深度mρ—出口气体密度kg/m3;出ρ钢液密度kg/m3;钢——β—常数,决定于射流的马赫数M,当M=0.5—3.0 时,距出口15×d,β=6—9,M大,取上限;出H —枪位m;V—射流出口速度m/s;出g——重力加速度m2/s。
阳极炉
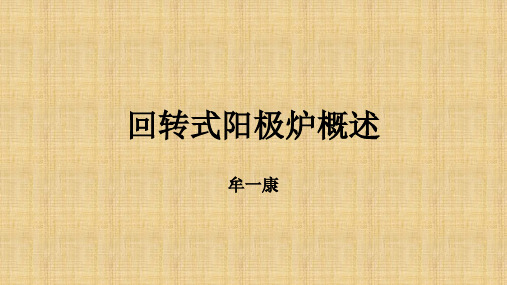
四、回转式阳极炉倾动方式
• 回转式阳极炉传动装置主要由主电机、副电机、气动电机、主变 速箱、副变速箱、电磁离合器和大小齿圈组成。回转炉的倾转是 依靠电动机和气动电机、电磁离合器变速箱以及控制装置来实现 的。 • 回转式阳极炉的倾动方式设有快速倾动、慢速倾动和气动以及事 故(气动电机)倾转。一般情况下氧化、还原浇铸刚开始阶段使 用快速倾转。而放渣、浇铸、修炉使用慢速倾动。气动一般是指 炉体已过顶部位置,而炉选开关又处在炉前控制,此时则使用气 动控制倾转炉体,事故倾转是指炉体正在加料、氧化、还原、浇 铸时突然停电,此时气动电机会自动气动,将炉体从不同方向转 到顶部位置。快速倾转的速度为0.6r/min,慢速倾转和事故倾转 的速度为0.06r/min。
三、回转式阳极炉供热
• 回转式阳极炉供热目前主要采用重油或液化石油气作为燃料进行加热和保温, 我公司采用天然气作为燃料属于最新实践。 • 燃烧效果的好坏直接关系到熔融铜温度的高低。一般情况,操作人员只需从 炉口或装设在燃烧器上的观察孔观察或从燃烧室与炉体的接头处目测火焰呈 绿色,炉内呈白光色,燃烧效果就比较好。若呈暗红色则表示燃烧效果较差。 回转炉直接热利用率为8%-15%,60%以上的热量由烟气带出。 • 影响燃烧效果的因素有一下几种:
右侧为豫光金铅Φ 4000mm×12000mm 阳极炉; 下侧为铜陵Ф 4900mm×14380mm阳极 炉。
二、回转式阳极炉结构
• 回转式阳极炉炉型与圆筒形相似,由以下部分组成:炉体、燃烧 器、燃烧室、传动机构、炉体支撑结构、炉体驱动系统。
• 1-排烟口;2-炉体;3-砌砖体;4-炉盖;5-氧化还原口;6-燃烧器; 7-炉口;8-托辊;9-传动装置;10-出铜口
2采用透气砖技术通过透气砖装置向炉内通入氮气使熔体一直处于轻微的搅拌状态温度场均匀大大缩短氧化还原时间同时提高阳极铜的质稀氧燃烧技术是最近几年来兴起的节能的燃烧技术氧气燃烧炉温高且均匀烟气量大大减少大幅度提高了燃烧热效率因而可以显著降低燃料消耗
钢厂转炉心得
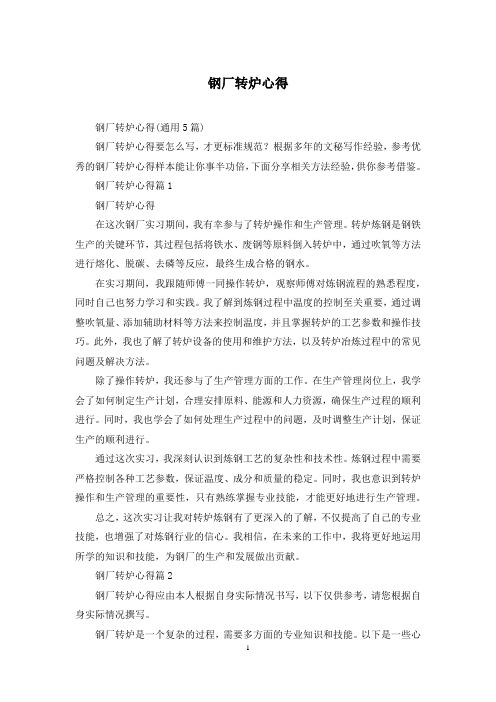
钢厂转炉心得钢厂转炉心得(通用5篇)钢厂转炉心得要怎么写,才更标准规范?根据多年的文秘写作经验,参考优秀的钢厂转炉心得样本能让你事半功倍,下面分享相关方法经验,供你参考借鉴。
钢厂转炉心得篇1钢厂转炉心得在这次钢厂实习期间,我有幸参与了转炉操作和生产管理。
转炉炼钢是钢铁生产的关键环节,其过程包括将铁水、废钢等原料倒入转炉中,通过吹氧等方法进行熔化、脱碳、去磷等反应,最终生成合格的钢水。
在实习期间,我跟随师傅一同操作转炉,观察师傅对炼钢流程的熟悉程度,同时自己也努力学习和实践。
我了解到炼钢过程中温度的控制至关重要,通过调整吹氧量、添加辅助材料等方法来控制温度,并且掌握转炉的工艺参数和操作技巧。
此外,我也了解了转炉设备的使用和维护方法,以及转炉冶炼过程中的常见问题及解决方法。
除了操作转炉,我还参与了生产管理方面的工作。
在生产管理岗位上,我学会了如何制定生产计划,合理安排原料、能源和人力资源,确保生产过程的顺利进行。
同时,我也学会了如何处理生产过程中的问题,及时调整生产计划,保证生产的顺利进行。
通过这次实习,我深刻认识到炼钢工艺的复杂性和技术性。
炼钢过程中需要严格控制各种工艺参数,保证温度、成分和质量的稳定。
同时,我也意识到转炉操作和生产管理的重要性,只有熟练掌握专业技能,才能更好地进行生产管理。
总之,这次实习让我对转炉炼钢有了更深入的了解,不仅提高了自己的专业技能,也增强了对炼钢行业的信心。
我相信,在未来的工作中,我将更好地运用所学的知识和技能,为钢厂的生产和发展做出贡献。
钢厂转炉心得篇2钢厂转炉心得应由本人根据自身实际情况书写,以下仅供参考,请您根据自身实际情况撰写。
钢厂转炉是一个复杂的过程,需要多方面的专业知识和技能。
以下是一些心得体会,供您参考:1.转炉操作需要严格遵守操作规程,不能随意更改参数或操作。
2.转炉操作需要不断调整和优化,要根据实际情况进行调整,不能一味地追求产量或质量。
3.转炉操作需要与炉前、炉后等各个岗位紧密配合,不能出现脱节或延误的情况。
北京科技大学钢铁生产全流程虚拟仿真平台实习报告
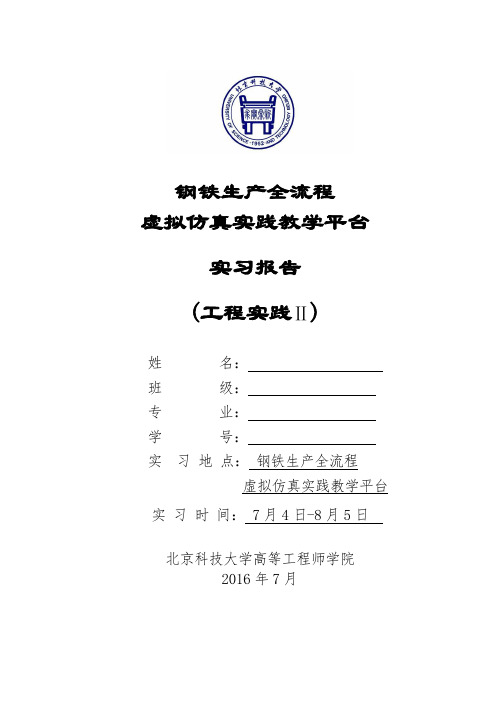
钢铁生产全流程虚拟仿真实践教学平台实习报告(工程实践Ⅱ)姓名:班级:专业:学号:实习地点:钢铁生产全流程虚拟仿真实践教学平台实习时间: 7月4日-8月5日北京科技大学高等工程师学院2016年7月目录目录 (I)1前言 (1)2实习背景描述 (1)2.1实习性质 (1)2.2实习目的 (1)2.3实习要求 (2)2.4实习单位的基本情况 (2)2.5实习安排情况 (3)3实习内容 (4)3.1 邯郸钢铁生产 (4)3.2钢铁生产全流程虚拟平台 (10)3.2.1烧结 (10)3.2.2高炉炼铁 (11)3.2.3炼钢 (13)3.2.4连铸 (26)4总结 (27)4.1收获与感受 (27)4.2建议 (28)参考文献 (28)致谢 (29)1前言我北京科技大学是“211工程”院校,“985优势学科创新平台”,求实鼎新,崇尚实践。
按照北京科技大学卓越工程师培养计划的总体要求,依托冶金工程国家一级重点学科,按照“夯实学科基础、注重专业交叉、强化工程实践、培养创新能力”的总体思路,以实际工程为背景,以工程技术研究为主线,着力提高学生的工程意识、工程素质和工程实践能力。
高等工程师学院院长刘立从项目概况、应用现状、应用愿景及发展规划等方面介绍了虚拟平台建设情况,展示了虚拟平台钢铁生产全流程实践教学资源。
技术人员现场演示了转炉炼钢虚拟仿真教学系统的认知学习、实践操作和创新实践等功能。
教务处处长宋波对虚拟平台的启用表示祝贺并指出虚拟仿真教学方式具有较强实践性与趣味性,希望各学院在实习实践及课堂教学等环节中积极引入虚拟仿真教学资源,提升实践教学效果。
虚拟平台展示了现代钢铁生产流程特点,采用了创新性教学方法与手段,不仅能为工程实践教学提供支撑,还可为学生创新创业提供平台。
钢铁生产全流程虚拟仿真实践教学平台于2013年开始筹建,2015年10月完成项目验收,2016年1月获批教育部“国家级虚拟仿真实验教学中心”。
现有实验室2个,实验教学面积400平米,虚拟仿真实践教学系统10套,形成了由软件、硬件和网络系统组成的虚拟仿真实践教学环境,具有认知学习、实践操作、考核鉴定、设计教学、创新实践、教学资源管理等功能,能够支撑专业课程、认识实习、生产实习、工程设计、毕业设计等教学环节。
- 1、下载文档前请自行甄别文档内容的完整性,平台不提供额外的编辑、内容补充、找答案等附加服务。
- 2、"仅部分预览"的文档,不可在线预览部分如存在完整性等问题,可反馈申请退款(可完整预览的文档不适用该条件!)。
- 3、如文档侵犯您的权益,请联系客服反馈,我们会尽快为您处理(人工客服工作时间:9:00-18:30)。
2008年10月第24卷第5期炼钢SteelmakingOct.2008VoL24No.5・1・250t转炉生产用氧实践卢凯,陈念铀(武汉钢铁(集团)公司炼钢总厂,湖北武汉430083)摘要:介绍了武钢炼钢总厂三分厂转炉合理用氧的相关情况,通过采用合适的氧枪喷头和转炉用氧工艺参数,不断优化转炉过程枪位控制和造渣制度,使转炉终点控制以及各项技术经济指标均有显著改善。
关键词:转炉;用氧;氧枪喷头中图分类号:TF724.5文献标识码:B文章编号:1002-1043(2008)05420014)4Practiceofoxygenblowin250tconverterrefiningLUKai。
CHENNian-you(CentralSteel-makingPlantofWISCO,Wuhan430083,China)Abstract:ThepresentpaperintroducestheinformationaboutappropriateuseofoxygenintheconverterofNo.3Steel—makingPlantofWISCO.Byselectionofsuitablenozzleoftheoxygenlanceandreasonableprocessingparametersoftheoxygenblowforthecon-verterandbyoptimizationpersistentlyofthepositioncontroloftheoxygenlanceaswellastheslaggingscheduleintheprocessoftheconverterrefiningtheendpointcontroloftheconverterandallthetechnicalandeconomicalindicatorshavebeenprominentlyim—proved.Keywords:converter;oxygenusage;nozzleofoxygenlance转炉用氧是氧气顶吹转炉炼钢最重要的操作,是控制整个吹炼过程的主导因素,并且直接影响转炉的冶炼效果和钢的质量。
本文介绍武汉钢铁(集团)公司炼钢总厂三分厂(以下简称炼钢三分厂)250t氧气转炉生产用氧的实践,通过不断优化转炉过程枪位控制和造渣制度,提高转炉计算机控制炼钢水平所取得的显著效果。
1转炉主要技术特点炼钢三分厂有3座250t氧气顶吹转炉,其主要技术特点如下:转炉类型顶底复合吹炼吹炼控制方式静态模型与副枪动态模型相结合氧枪5孔,供氧压力1.0~1.2MPa底吹模式LBE型,N2/Ar自动切换底吹供气强度0.02--0.12m3/(min・t)2供氧情况据资料报导,氧枪喷嘴马赫数Ma=2.0~2.3,既可节省能量又容易获得稳定的操作,但必须采用合理的管道设计,具备足够的压力能。
炼钢三分厂的氧气由两根①500mm的干管输送,到达厂区后改为∞00ITffn的干管进人氧气减压阀站。
进入吹炼减压阀站的干管在站内形成环状布置,每座转炉均配有一套减压阀组。
为保证氧气供应,另在厂区内布置有7个650m3贮氧球罐,与主干管形成并联布置。
合理的管道设计保证了氧气输送所需的压力能,从而达到最佳操作效果。
炼钢三分厂设计的总管氧压为1.8~3.0MPa,实际总管压力约在2.3~3.0MPa。
3转炉用氧情况供氧是氧气顶吹转炉炼钢最重要的操作,是控制整个吹炼过程的主导因素,并且直接影响冶作者简介:卢凯(1970一),男(汉族),湖北武汉人,武汉钢铁(集团)公司炼钢总厂。
工程师.万方数据・2・炼钢第24卷炼效果和钢的质量。
它是保证杂质去除速度、熔池升温速度、造渣速度、控制喷溅和去除钢中气体与夹杂的关键操作。
此外,它还影响终点碳和温度的控制,影响炉龄,对转炉强化冶炼,扩大钢的品种和提高质量都有重要影响。
供氧制度的主要内容包括确定合理的氧枪喷头结构、供氧强度、供氧压力、枪位控制[1]。
3.1氧枪喷头炼钢三分厂的氧枪本体由3根钢管相套而成,其端部为氧枪喷头。
为了加快冷却水流经喷头时的流动速度、提高喷头的冷却强度以及减少枪体积渣,氧枪本体在喷头以上6m长度内,其外管与中管均设计为锥形管,下直径收缩量约102mm,使氧枪本体插入炉内的部分呈倒锥形。
炼钢三分厂原有氧枪喷头有铸造和锻压组合式喷头两种。
在更换2支锻压组合式氧枪喷头(即转炉吹炼1086炉)的隋况下,与采用铸造氧枪喷头吹炼同样炉数的数据进行对比,使用不同氧枪喷头的转炉终渣及氧枪喷头寿命等操作数据如表1所示。
表1不同氧枪喷头的操作数据与铸造喷头相比,锻压组合喷头具有如下优点。
(1)喷头端部采用纯铜锻压制造,致密度高,导热系数大,内壁光滑且薄,冷却水流设计合理,喷头冷却条件较好。
(2)采用锻压组合喷头,转炉吹炼过程平稳,喷溅小,喷头冶金效果良好,由表1可见,转炉终渣伽(T.Fe)低约1%,提高了金属收得率。
(3)具有较高的耐蚀性和抗变形能力,不易粘渣,喷头使用寿命延长,提高了转炉作业率。
由于锻造氧枪喷头具有上述优点,因此,从2007年起炼钢三分厂开始全部采用锻造氧枪喷头,其结构如图1所示。
3.2供氧强度供氧强度的大小应根据转炉的设计吨位、炉容比来确定。
供氧强度过大,容易造成严重的喷溅,供氧强度过小,则将延长转炉吹炼时间。
因此,通常在不产生喷溅的情况下,尽可能采用较大的供氧强度[2l。
1一喷头底部f2一定位块,3一分水盘f4一喉管f5一喷头上部;6一中管,7一外管,8一O型密封圈图1氧枪喷头结构图3.3供氧压力供氧压力应保证使射流出口速度达到超音速,并使喷头出口处氧压稍高于炉膛内炉气压力,这样才能获得有效动量最大和最佳性能的射流。
炼钢三分厂氧枪喷头入口处设计滞止压力为1.0MPa,吹炼时氧气工作压力为1.0"--1.2MPa。
3.4氧枪枪位控制氧枪枪位是供氧制度的一个重要参数。
确定合适的枪位主要考虑两个因素:一是要有一定的冲击面积;二是在保证炉底不被损坏的条件下,有一定的冲击深度。
氧气射流的穿透深度按下述公式确定:L=Lkexp(一0.78^/Lhn)(1)Lho=63.0(K・F&/rid)213(2)式(1~2)中,L为穿透深度,mm;k为h=0的L,mm;h为氧枪与熔池液面距离(氧枪枪位),rtllTl;R为供氧流量,rn3/h;d为氧枪孔径,mm;行为孔数;K为取决于孔倾斜角的系数(见图2)。
喷孔倾角,(。
)图2系数K与喷孔倾斜角的关系氧气射流的穿透深度与熔池深度(Lo)应有合适的比值(L/Lo)。
在吹炼过程中,为防止炉底熔损和喷孔损坏,保持转炉吹炼的稳定性,L/厶万方数据第5期卢凯,等:250t转炉生产用氧实践・3・必须不大于0.8,炼钢三分厂实际控制在L/Lo=0.60--一0.75。
炼钢三分厂氧枪操作采用恒压变枪位操作,通过变动枪位来控制转炉的化渣速度和渣中的T-Fe含量。
氧枪枪位采取高一低一低的控制方式,见图3;造渣采用单渣法操作,这样有利于实现计算机控制炼钢。
在动态控制阶段,根据副枪的测量结果对转炉吹炼过程不断进行修正,以达到合适的转炉终点控制目标。
造渣方式由原来一批料方式调整为二批料方式,从而保证前期尽快成渣并化透,提高转炉的去磷效果。
同时,根据钢种要求的不同,分别采用不同的计算机吹炼模式,以达到转炉吹炼过程枪位控制的最优化。
饕譬篓饕耋0102030405060708090100供氧量/%图3造渣方式改进前后的转炉吹炼模式4冶金效果4.1钢中碳和氧的控制近年来,炼钢三分厂通过应用计算机炼钢控制技术和复吹转炉溅渣护炉技术,不断提高转炉终点控制水平,计算机炼钢控制率和转炉终点C-t双命中率(△叫(C)为±0.015%;&为±12℃)稳定保持在90%以上。
因2005年4月份炼钢三分厂3号转炉才投产,转炉设备状况需要不断完善,岗位人员对设备的掌握程度以及操作水平还有待于提高,导致2005—2006年的实际控制水平有所降低,如表2所示。
取改进前2005年3月份的340炉和改进后2006年3月份的730炉操作数据进行对比,改进后的转炉终点平均[%C]・[%03=较改进前降低3.6%。
4.2渣中总铁量炉渣的氧化性,通常用渣中全铁的含量来衡量。
氧化性是转炉渣的重要性质之一,其重要性表2转炉计算机炼钢控制情况在于对化渣速度、炉渣粘度、喷溅程度、去除钢液中硫和磷的能力、铁耗大小和对转炉终点钢液中含氧量等有着很大的影响。
转炉吹炼过程中,在保证转炉去除磷、硫的条件下,应将渣中T.Fe质量分数控制在适当的范围内,实际生产中按12%~18%控制,如图4所示。
常用的方法是:(1)尽可能控制终点碳在出钢要求的中上限;(2)接近终点前适当降低枪位;(3)吹炼结束时,加入少量石灰稠化炉渣,使氧从炉渣向金属中的传递减慢;(4)采用大气量底吹后搅拌降低终渣T.Fe含量。
4.3脱磷在转炉造渣方式由一批料改为二批料后,通过对转炉吹炼模式的不断优化,转炉吹炼过程喷溅现象得到有效改善,转炉终渣平均T.Fe与改进前基本相同;同时,转炉吹炼终点钢中磷较改进前降低7.5%,分布情况如图4~5所示。
ll1213141516171819202l22渣中以T.Fe)/%图4转炉终渣中T.Fe的控制转炉终点钢中w(e)no。
图5转炉终点钢中磷的控制万方数据・4・炼钢第24卷4.4品种质量炼钢三分厂应用自主开发的转炉计算机炼钢控制技术和复吹转炉溅渣护炉技术,使转炉吹炼的冶金效果得到了保证,从而确保了钢的质量和新品种的开发。
近3年来,炼钢三分厂生产的重点钢种包括深冲用IF钢、管线钢、桥梁钢、耐候钢、汽车大梁钢、石油储备罐用钢等500多个钢种,以汽车用钢为代表的高附加值产品产量大幅提高,如图6所示。
铸坯综合质量合格率稳定保持在99.90%以上。
5转炉用氧情况展望国内外的实践表明,科学地提高转炉供氧强度,能够缩短转炉的冶炼时间,提高炼钢厂生产效率和钢产量,使生产成本相对降低,能为钢铁厂带来明显的经济效益。
因此,结合炼钢三分厂现有的工艺设备条件,开展大型转炉高效用氧技术的研究十分必要。
炼钢三分厂与钢铁研究总院合作,共同开发的大型转炉高效吹氧技术,可以适应大型转炉炼钢工艺特点,合理调整转炉吹炼过程的枪位控制、氧气流量等参数,改善化渣情况,降低转炉终点钢水磷含量,同时,对今后采用“三脱”铁水吹炼提供有力的依据。
目前,新的氧枪喷头正处于现场工业性试验中,已取得了阶段性的试验数据。
6结语(1)氧枪喷嘴马赫数Ma=2.0~2.3,既可节省能量又容易获得稳定的操作,从而达到转炉的最佳操作效果。
(2)与铸造氧枪喷头比较,锻造氧枪喷头具有冷却条件好,转炉终渣硼(T.Fe)低约1%,喷头使用寿命高,冶金效果良好等特点。