汽车发动机缸体铸造技术
汽车缸体铸造工艺

汽车缸体铸造工艺一、缸体材料车用发动机缸体缸盖的材质主要有灰铸铁,铝合金,蠕墨铸铁等。
传统的发动机无论是缸体还是缸盖都是采用铸铁的,但是铸铁有着许多先天的不足,例如重量大、散热性差、摩擦系数高等等。
所以,许多发动机厂商都在寻找更适合的材料制造发动机的构成部件,比如密度小的铝。
铝的比重轻,单位体积的铝结构强度要小于铸铁,所以铝缸体通常体积反而大些。
但铝容易和燃烧时产生的水发生化学作用,耐腐蚀性不及铸铁缸体,尤其对温度压强都更高的增压引擎更是如此。
铸铁缸体和铝缸体各有其优缺点,所以所以高增压的引擎很多都采用铸铁缸体,小型车的缸体则更多向铝缸体发展。
金属中的元素组成会对金属材料的性能产生较大的影响,就钢铁而言,钢中含碳量增加,屈服点和抗拉强度升高,但塑性和冲击性降低,当碳量0.23%超过时,钢的焊接性能变坏,因此用于焊接的低合金结构钢,含碳量一般不超过0.20%。
碳量高还会降低钢的耐大气腐蚀能力,在露天料场的高碳钢就易锈蚀;此外,碳能增加钢的冷脆性和时效敏感性。
不同的缸体元素配比也是有差别的。
合肥江淮铸造有限责任公司缸体化学成分要求化学成分(%)C Si Mn P S Cr Cu Ti Sn Pb下限 3.25 1.95 0.60 0.00 0.06 0.25 0.30 0.00 0.06 0.00 0上限 3.40 2.10 0.90 0.06 0.10 0.35 0.50 0.03 0.09 0.00 4二、原材料熔炼熔炼设备选用:中频感应保温电炉:生产效率10t/h,外水冷长炉龄大排距冲天炉:生产效率7t/h。
1、原材料原材料一般为回炉料,废钢和生铁。
回炉料是厂家的常备材料,在使用时必须注意其本身的干净程度。
回炉料的加入量必须严格按一定比例,否则会导致铁水的Si、S含量不易控制。
江淮生产的缸体铸件回炉料使用量一般不超过20%。
在江淮的缸体生产中,废钢的使用量超过50%。
这是由于生铁本身含有粗大石墨,而石墨熔点较高,在2000℃以上,在熔炼中不能熔尽,使得结晶过程中石墨变得粗大。
汽车发动机缸体的铸造工艺

的产 品质量 提 出了更高 的要 求。 我公 司为某 主机厂 新开 发一 种 1 汽 车发动 机缸 .L 5 体 ,产 品内腔形状复杂 ,铸件最大轮廓尺 寸为4 0I 0 I T mX
30 2 mmx 5 I,重 量3 g 23n l l/ 8k ,材质 为H 5 。加 工后 T2 0 缸筒壁厚 5 mm,最 小壁厚3m m,并 要进行水 压 、气压
随着现在 社会 对环 境越来 越重 视 ,对 汽 车尾气 的
排放标 准 提 出了更高要 求 。为 了满足这 种要 求 ,各 主
机 厂加大 了对发 动机 的研ຫໍສະໝຸດ 发力度 ,现在 大多 数厂 家都
2 工艺 设 计
2 1 制芯工 艺 .
采用 了多气 门 电喷发 动机 。缸体是 发 动机 的重要部 件 之一 ,随着 汽车 发动机 技术 的发 展 ,对 发动机 缸体 的
所有 砂 芯均采 用覆膜 砂制 芯 ,除水套 芯 、油道 芯
为高 强度覆 膜砂 外 ,其 余为低 强度 覆膜砂 ,具 体覆膜
砂性能见表 1 。
表1 覆膜砂性能
Tabl o r isofp e oa e a e 1Pr pe te r c t d s nd
尺寸精 度 和力学 性能要 求越 来越 高 ,因此对 缸体铸 件
东风汽车铸造三厂缸体铸造工艺流程(一)

东风汽车铸造三厂缸体铸造工艺流程(一)
东风汽车铸造三厂缸体铸造工艺流程
工艺概述
•工艺名称:东风汽车铸造三厂缸体铸造工艺流程
•目标:生产高质量的汽车发动机缸体
流程步骤
1.原料准备
–选择高品质的铸造材料,如铸铁等
–对原料进行质检,检测其化学成分和力学性能2.模具制备
–设计并制作合适的缸体模具
–确保模具材料和工艺能满足生产要求
3.模具预处理
–清洗和除锈模具,确保表面光洁
–进行模具涂覆,保护模具表面,方便后续操作4.浇注过程
–熔炼铸造材料,保证熔体的均匀性和温度
–使用浇注设备,将熔体倒入模具中
–控制浇注速度和压力,避免产生缺陷
5.硬化
–等待熔体冷却和凝固
–使用冷却介质或冷却水辅助加速凝固过程
6.模具拆卸
–小心地拆卸模具,不损坏缸体
–仔细检查缸体表面是否有破损或缺陷
7.后处理
–进行缺陷修复和表面处理,如打磨、喷涂等
–进行最终的质量检测,并记录检测结果
8.包装和出厂
–对合格的缸体进行包装,以防损坏
–准备出厂文件和运输安排,确保产品安全送达工艺优势
•高质量:严格质检和控制确保缸体的质量稳定性
•高效率:流程的合理设计和设备的优化提高了生产效率
•环保可持续:对原料和能源的合理利用,降低环境影响
结论
这份文章详细介绍了东风汽车铸造三厂缸体铸造工艺流程的各个步骤。
该工艺以高质量、高效率和环保可持续为目标,通过严格质检和控制,以及流程的合理设计和设备的优化,确保生产出高质量的汽车发动机缸体。
五种常见的铸造工艺及其在铸造行业中的应用案例
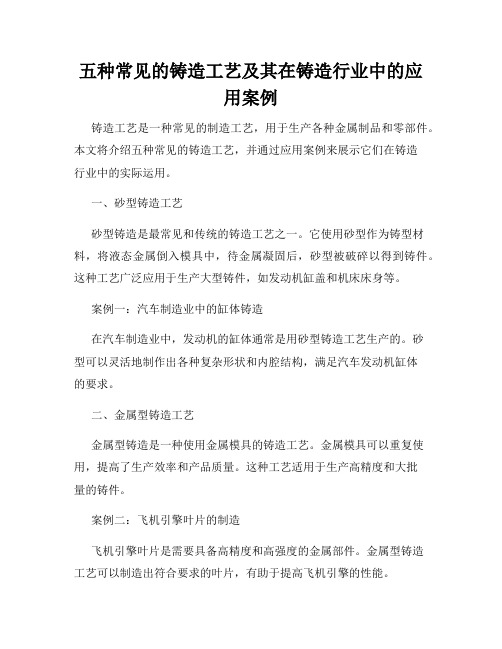
五种常见的铸造工艺及其在铸造行业中的应用案例铸造工艺是一种常见的制造工艺,用于生产各种金属制品和零部件。
本文将介绍五种常见的铸造工艺,并通过应用案例来展示它们在铸造行业中的实际运用。
一、砂型铸造工艺砂型铸造是最常见和传统的铸造工艺之一。
它使用砂型作为铸型材料,将液态金属倒入模具中,待金属凝固后,砂型被破碎以得到铸件。
这种工艺广泛应用于生产大型铸件,如发动机缸盖和机床床身等。
案例一:汽车制造业中的缸体铸造在汽车制造业中,发动机的缸体通常是用砂型铸造工艺生产的。
砂型可以灵活地制作出各种复杂形状和内腔结构,满足汽车发动机缸体的要求。
二、金属型铸造工艺金属型铸造是一种使用金属模具的铸造工艺。
金属模具可以重复使用,提高了生产效率和产品质量。
这种工艺适用于生产高精度和大批量的铸件。
案例二:飞机引擎叶片的制造飞机引擎叶片是需要具备高精度和高强度的金属部件。
金属型铸造工艺可以制造出符合要求的叶片,有助于提高飞机引擎的性能。
三、压铸工艺压铸是一种将液态金属注入高压模具中,通过施加压力使金属充填模腔的铸造工艺。
压铸可用于生产精密度高、尺寸复杂的铸件。
案例三:手机外壳的生产手机外壳通常由铝合金或镁合金制成,具有精密的尺寸和复杂的结构。
压铸工艺能够满足手机外壳的质量和生产效率要求。
四、连续铸造工艺连续铸造是一种将液态金属连续倒入模具中,通过连续冷却和切割得到连续条状铸坯的工艺。
它适用于生产长条状铸件,如铁路轨道和钢板等。
案例四:钢铁工业中的连铸连铸广泛应用于钢铁工业,以生产各种规格和长度的钢坯。
通过连续铸造工艺,可以提高钢坯的质量和生产效率。
五、精密铸造工艺精密铸造是一种生产高精度和复杂形状铸件的工艺。
它通常结合了其他铸造工艺,如石膏型铸造和失蜡铸造等。
案例五:航空航天领域中的精密铸造在航空航天领域,精密铸造被广泛应用于生产航空发动机的复杂部件,如叶轮、涡轮等。
精密铸造工艺的使用可以确保零部件的高精度和性能要求。
总结:通过对五种常见铸造工艺的介绍和应用案例的展示,可以看出在铸造行业中这些工艺的重要性和广泛运用。
汽车发动机铝合金缸体压铸工艺的改进

汽车发动机铝合金缸体压铸工艺的改进发布时间:2023-02-07T02:42:26.222Z 来源:《福光技术》2023年1期作者:张义琪[导读] 这种工艺能够降低机械制造的成本,提升机械制造的生产率,缩短汽车发动机铝合金缸体制造的时间。
广东鸿图南通压铸有限公司江苏省南通市 226300摘要:对某汽车发动机压铸铝合金缸体原有工艺及试漏过程中油路渗漏,导致废品率增加的问题进行分析,找出产生问题的主要因素,并对其进行合理优化改进。
改进后的工艺有效地降低了油路渗漏导致缸体废品率增加的几率,工艺改进取得满意成效。
关键词:压铸缸体;气孔缺陷;工艺改进;品质提升1缸体压铸工艺的优点1.1效率高在进行汽车制造时经常会采用压铸工艺,这种工艺在进行压铸加工时,采用的是迅速压铸成型的工艺,这种工艺能够降低机械制造的成本,提升机械制造的生产率,缩短汽车发动机铝合金缸体制造的时间。
1.2工艺流程简化传统铸造工艺的制造流程相对来讲较为复杂,与之相比较而言,压铸工艺的优势非常明显,压铸加工时不需要经过非常繁琐的加工流程,在进行加工时毛刺、飞边出现较少,加工人员只需要将模具加工完成之后产品取出即可。
1.3其他优点精度高。
缸体压铸的精度进一步提升。
铸件的韧性和表面硬度较高。
减低材料成本。
2某汽车发动机压铸铝合金缸体简介图1某汽车发动机压铸铝合金缸体示意图其材料为ADC12,轮廓尺寸为367mm×190mm×263mm,最小壁厚为3mm,铸件净重13.2kg,硬度90~110HB(Z105),铝合金缸体结构包括缸筒、水套、高压油道、曲轴箱、主轴承座等,油路要求在0.3MPa下打压26s内允许泄漏量为≤2mL/min。
生产工艺路线:合金熔炼→压铸→清理→粗加工→浸润处理→一次打压试漏→精加工→二次打压试漏→检验。
该发动机缸体在打压试漏过程中出现不同程度的油路渗漏现象,此类油路渗漏现象的产生严重影响了发动机缸体的品质,使发动机缸体的废品率增加。
铸造工艺设计(flash)
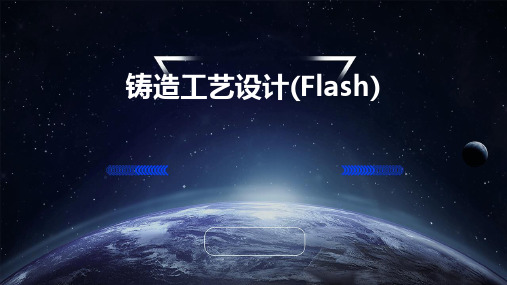
Flash铸造工艺可以根据客户需求定制不同 形状、大小和材料的零件,具有很强的灵 活性。
Flash铸造工艺的应用场景
航空航天
Flash铸造工艺可以制造出高精度、高性能的航空航天零件,满足了 航空航天领域对高性能材料和高精度制造的需求。
汽车制造
Flash铸造工艺可以快速制造出汽车零部件,提高了汽车制造的效率 和灵活性。
铸造工艺设计(Flash)
• 引言 • 铸造工艺设计基础 • Flash铸造工艺设计 • 铸造工艺设计实例 • 铸造工艺设计的未来发展
01
引言
主题简介
铸造工艺设计(Flash)
01
本课程主要介绍铸造工艺的基本原理、设计方法和技术,以及
在生产中的应用。
铸造工艺
02
铸造是一种通过将液态金属倒入模具中,冷却凝固后形成所需
详细描述
精密零件的铸造工艺设计要求精度高、技术难度大。在设计中,需要充分考虑同时,还需要采用先进的铸造技术,如消失模铸造、精密铸造等,以提高产品精度和质 量。
05
铸造工艺设计的未来发展
铸造工艺设计的新技术
01
02
03
3D打印技术
利用3D打印技术直接制造 出铸造模具,减少传统模 具制造的繁琐流程,提高 生产效率。
THANKS
感谢观看
虚拟现实技术
通过虚拟现实技术进行铸 造工艺模拟,实现铸造过 程的可视化,便于提前发 现和解决潜在问题。
增材制造技术
利用增材制造技术制造出 具有复杂结构的金属零件, 突破传统铸造工艺的限制。
铸造工艺设计的环保趋势
绿色铸造
采用环保材料和工艺,减 少铸造过程中对环境的污 染,实现绿色生产。
循环经济
汽车发动机缸体模具设计及低压铸造工艺

汽车发动机缸体模具设计及低压铸造工艺摘要:目前,对于汽车铝合金发动机缸体采用压力铸造的方法较为广泛。
因此,压铸造工艺在汽车发动机缸体铸造中的应用过程,通过缸体模型合理的设计,调整与优化相关工艺参数,可以达到提高合格率的目的。
关键词:汽车发动机;模具设计;低压铸造工艺引言下缸体是汽车发动机上的重要零件,其上部与气缸体、下部与油底壳相连;气缸体与下缸体之间安装有曲轴。
下缸体在发动机工作过程中的特点是:处于高温状态下工作,承受较大的热冲击作用和承受较大的力,工作条件较为恶劣。
下缸体对气密性要求较高。
另外,此铸件在缸体的螺栓孔处及水泵孔凸台处较为厚大,极易产生铸造缺陷。
选择低压铸造工艺方法,采用合理的工艺参数、模具结构及局部快冷生产此铸件,不仅能解决铸件上厚大部位铸造缺陷的问题,同时也能满足此铸件组织致密性的要求。
1汽车发动机缸体结构本次研究以GM-L850发动机下缸体为例,铸件重为10.3 kg,轮廓尺寸为471 mm,371 mm和91mm,壁厚平均为4.0 mm。
材质是铝合金,这种材料具有力学性能好以及铸造工艺性能好的特点,因此,在汽车发动机铸造中应用比较广泛。
为了满足具体的工艺条件,在结构设计中进行的主要措施有两个:①在曲轴孔半圆处对工艺余量增加,以能够在下部形成一个厚大部位;②为了能够对模具结构简化,可以不铸出产品机械加工斜孔。
发动机铸件结构如图1。
2发动机缸体铸造模具设计铸造模具设计中所采用的是UG软件CAD模块,依照具体的工艺和产品毛坯三维模型,实施分型拆模,从而得到模具型芯、型腔、滑块以及镶块等,之后将这些模具分型与标准或者是非标准零件结合实施装配,经过一系列干涉检查、成型分析等流程之后,也就能够获取模具。
在进行模具三维设计中,重点是要表而形成分模成型特征,其他特征则较易实现。
汽车发动机缸体模具工作流程如图2.3模具设计3.1模具结构形式为了顺利开模,模具分型要采用多分型面,模具有6个方向开模,分别是:底模、顶模、右模、左模、前模及后模(具体模具结构见图3)。
汽车发动机铸铁缸盖的铸造技术

!"&
废品多 汽车用铸铁件,缸盖的废品率一般都是最高的,
常见废品有:
+
中国铸造装备与技术 ! " #$$%
专题综述
缸盖内外形多由砂芯组成, 砂芯粘结剂 ! 气孔: 多为发气物质, 出气量大。缸盖铸件又不允许有任何 气孔存在, 所以缸盖气孔成了常见缺陷。 缸盖中有油、 有水、 有气, 且都有压力, 故 "渗漏: 对缸盖密封要求严格,东风公司一般是用 !"#$%& 气 压、 稳压 ’()* 检查不得有漏气现象。 缸盖壁厚相差很 大, 保证薄的不白口厚的不疏松也有难度, 故渗漏缺 陷时有发生。 由于结构复杂, 较难使凝固时各部位互 # 变形: 不干扰。缸盖的结合面 (有燃烧室面) 又厚又大, 很容 易造成铸件弯曲, 为保证各燃烧室尺寸准确, ( 用 +、 , 缸燃烧室底面及侧面定位加工) 还必须保证铸件在长 度方向弯曲度-.((, 一般是将模具做成反挠度形式, 当然也有其他一些妙着,否则在防变形上也是困难 的。 任何一个工厂的铸件成分总在变化中, 常与原材 料、 质量、 成本联系在一起。 究其什么成分好是没有标 准 的 , 一 般 产 品 要 求 是 : 缸 盖 本 体 强 度 A+!7$%& ,
汽车用材料的特点是要求重量轻强度高,随着 发动机功率的日益提高,产品的技术要求也随之不 断增加。发动机气缸盖当前正由铸铁材料向铝镁合 金转变,特别是轿车生产许多厂已采用低压铸造或 金属型铸造生产 ! 缸发动机铝缸盖,但灰铸铁作为 传统材料依然由于成本低、 工艺性好, 有良好的尺寸 稳定性和热疲劳性能, 当前仍有一定市场, 特别在高 功率发动机上还占有半壁江山,但对结构要求不断 提高。 东风公司商用车气缸盖都用铸铁材料生产, 采用 ’(&))*+&&))*%%&)) 外形的 "#$%&& 发动机, 双缸盖, 单重 +,-,./ ; 康明斯 0 系列发动机用整体缸 盖, 外形为 (,+))*+1,))*%&,)), 重 $1./。平均壁 厚都在 !-,)) 左右, 因为壁厚增加 %)), 重量就增加 这 %%2 。汽车自重若减少 %&23 燃油可节省 $2452 , 是一个很大的竞争节能数值。铸件重量偏差不允许 超过 6,2 , 缸盖历来是典型的灰铁薄壁铸件。 在缸盖上除有特殊形状的配气燃烧室外, 有进气 道、 排气道, 还有冷却水套、 润滑油道等, 内腔形状复 杂多变。一般水套壁厚仅 !)) 左右, 气道壁厚 ’)) 左右, 而气阀座位置一般在 !!&)) 以上, 近几年又采 用多气阀顶置结构, 使缸盖内部的复杂性更有提高。
发动机箱体铸造工艺设计

封面摘要本文综合分析了采用铸造工艺生产汽车发动机箱体的方法,从铸造设备、铸造模具设计、生产工艺、铸造生产中常见的问题及对策等多个角度,对铸造工艺的技术动向以及今后的研究课题提出了自己的见解。
对国内外发动机箱体铸造生产进行了总结,其材质主要以C(质量分数,下同):3.15%~3.3%,CE:3.95%~4.05%,Si/C:0.6%~0.7%的灰铸铁为主。
一般选择冲天炉-有芯工频电炉进行熔炼,孕育剂仍普遍采用75SiFe,立浇底注式浇注系统和保温冒口有利于获得优质箱体,冷芯制芯工艺已逐渐取代热芯工艺。
通过提高浇注温度、型砂紧实率等措施可减少箱体常见缺陷渗漏的出现。
铸造过程中合金配比工艺研究当箱体中含Cr量从0.308%上升到0.343%并不能明显增加珠光体数量和片间距的等级,但是可使铸件各部位的硬度总体呈上升趋势。
铸件抗拉强度值上升幅度很大。
一般可上升20~30MPa.在箱体中加入Sn可以明显提高铸件的布氏硬度和组织中的珠光体含量,但对于提高珠光体的片间距等级和减少渗碳体量则效果不明显。
关键词:铸造工艺;灰铸铁;模具设计ABSTRACTThis paper analyzes the use of the casting process to produce automobile engine box approach from many angles common foundry equipment, casting mold design, manufacturing process, casting production problems and countermeasures on the casting process technology trends and future research put forward their own views.For domestic and engine block, cylinder head casting a summary, the material mainly C (mass fraction): 3.15% ~ 3.3%, CE: 3.95% ~ 4.05%, Si / C: 0.6% ~ 0.7 % of gray cast iron main. Generally choose cupola - a core-frequency electric furnace smelting, inoculant is still widely used 75SiFe, Li pouring bottom gating and riser system is conducive to quality block, cylinder heads, cold-core making process has been gradually replaced by heat core processes. By increasing the pouring temperature, sand compaction rate and other measures to reduce the block, cylinder heads common defect leakage occurs.Alloy Casting process, when the ratio of the cylinder Cr content increased from 0.308% to 0.343% did not significantly increase the number and spacing of pearlite grade, but can cast various parts of hardness overall upward trend. Casting a great tensile strength values rise. Generally rise 20 ~ 30MPa. Adding Sn in the cylinder can significantly improve the casting Brinell hardness of pearlite content and organization, but for improving the pearlite spacing levels and reduce the amount of cementite is ineffective.Keywords: casting; gray iron; mold design摘要 (2)ABSTRACT (3)1 前言 (6)1.1课题背景 (6)1.2箱体铸件国内外研究现状和发展趋势 (6)1.2.1国外发动机箱体铸造技术生产状况 (7)1.2.2我国发动机箱体铸件的生产状况 (7)1.3灰铸铁箱体材料的发展 (8)1.3.1箱体材料要求 (8)1.3.2灰铸铁箱体材料 (8)1.3.3灰铸铁的组织和几种合金元素的影响 (9)1.3.4国内外箱体生产中灰铸铁材质的选择 (13)1.4本课题研究的内容 (18)2 低合金灰铸铁箱体工艺简介 (19)2.1生产设备及原材料 (19)2.1.1生产设备 (19)2.2结构简介 (19)2.3材质要求 (20)2.4造型及浇注系统设计 (21)2.4.1造型工艺 (21)2.4.2浇注系统 (22)2.5制芯及组芯工艺方案设计 (23)2.5.1制芯 (23)2.5.2组芯 (23)2.6孕育剂的加八方法 (25)2.6.1孕育机理及目的 (25)2.6.2生产孕育铸铁铸件的条件 (25)2.7.1原材料 (26)3 合金元素对发动机箱体性能的影响 (27)3.1引言 (27)3.2试验装置及试验方法 (28)3.2.1试验装置 (28)3.2.2原材料 (28)3.2.3制样 (28)3.3铬对箱体力学性能和金相组织的影响 (29)3.3.1试验目的及内容 (29)3.3.2试验结果 (29)3.4锡对箱体力学性能和金相组织的影响 (22)3.4.1试验目的及内容 (33)3.4.2实验结果 (33)4 结论 (42)致谢 (43)参考文献 (44)1 前言1.1课题背景发动机箱体的铸件是发动机生产中难度最大、最重要的一环,其质量对发动机的功率、油耗等性能起着决定性的作用。
汽车发动机缸体缸盖消失模铸造技术的研究与应用(一)

()消失模铸件 机械 加工余量 小 ( 3 25.35 .mm) 、
札拨I 热 I 加
20
— —
0 垩 翌 塑 ■j 1 兰
口
w w 日d l 时 c抑
维普资讯
譬
艺 分 面 I 处 片 至 l 不 理 方 油 括 ● 均 案 底 钐 方 不 上 壳 阳 式 尽 多 面 直 图 相 采 水 列 所 同 用 平 式 一 在 合 l 、如
维普资讯
栏 目主持
日文华
汽车发动机缸体缸盖 消失模铸造技术的研究与应用 ( 一)
安徽 全 柴集 团 有 限公 司 ( 椒 全 2 9 0 ) 王新 节 35 0
【 摘饕】 为了胯低发尉 机单位功率曲重量指标、油耗指标及尾气排数指标,我f研究并开发了消失模 } :
实现 自补缩 。从而减小铸件所需的 冒口尺寸:另一方面 由于泡沫模型簇的组装 自由度大 ,易于实现一 型多件浇
注成形 .提高了工艺出品率
铁 高;而铸铁产品的防振能 力 自润册能 力和高温力学 性能远 大于铝合金 ~因此可 预见 ,普通 灰铸铁 、高牌 号孕育铸铁 、台金铸铁 、蠕墨铸铁和球墨铸铁 等材馥的
铸铁件 ,作为一种发动机新 材料.蠕墨铸铁与普通 灰铸 铁相 比,抗 拉强 度 提 高了 约 7% .弹 性 模量 增 加 近 5
4 %.疲劳强度几 乎是灰铸 铁的 2倍 ,用蠕墨铸铁 取代 0 献铸铁生 产的发动机缸体至少可减轻重量 1 %,同时太 0
发动机缸体 、缸盖的制造水平 足衡量一个 国家制造 业水平的重要标志之一.在很大 程度上代表 r 个国家
本文重点介 绍 直列 四缸 二 气 门下 置凸 轮柴 油机 缸
体、 缸盖消失模铸造工艺的关键技术与应用状况。
汽车动力系统铸件的浸渗技术

汽车动力系统铸件的浸渗技术作者:隋枚在汽车动力系统铸件和粉末冶金件中,微孔的存在将导致渗漏,影响汽车的动力性能,本文介绍的浸渗技术对各类承压铸件可起到致密化和无渗漏的作用,对提高企业经济效益起着重要的作用。
铸件的微孔与浸渗微孔的产生和影响气孔是出现在材料中的一种现象,特别是金属零件在铸造过程中常出现:由液态向固态变化过程中时体积变化而产生的收缩气孔;不充分的压力状态导致表面或内部产生的液流孔;由模具中出现的各种各样气体截留而造成的气孔等。
其中一些难以被肉眼发现的微细孔隙或缺陷若被气体或者液体渗透,会造成铸件壁渗漏或表面缺陷,使零件在使用过程中丧失应有的功能,影响产品的性能;机加工时会产生噪音,加速刀具的磨损;缩短铸件使用寿命。
另外,废品率的提高又影响了成本节约。
微孔现象也普遍存在于粉末冶金制造过程中。
铸件浸渗铸件浸渗,就是将稳定且柔韧的密封材料填充铸件所有的微孔及互联气隙(浸渗可以覆盖万分之一mm至0.5mm大小的微孔),使被浸渗后的部分对热、油、化学物品或其它外部影响(如振动)有抵抗力,获得高质量的表面处理。
浸渗过程不会导致已经过表面处理及其它加工工序部件的外形尺寸的改变,或对其有任何的污染,并可缩短生产时间,提高产品质量,减少浪费,是针对微孔的一种永久性解决且节约成本的最佳方案。
目前,浸渗技术已被广泛应用,成为汽车零件铸造过程中不可或缺的工艺流程。
汽车动力系统的典型浸渗铸件如发动机缸体、缸盖、曲轴箱、进气歧管、油泵、油嘴、水泵、阀盖、变速箱壳体、压缩机等。
浸渗处理能够覆盖直径在万分之一毫米至0.5毫米的范围的微孔,处理后的铸件承压能力能够达到铸件的破裂强度。
浸渗技术浸渗技术主要包括三大要素:密封剂、设备、工艺流程。
密封剂浸渗密封剂的性能直接影响浸渗的效果。
传统的浸渗密封剂,如硅酸钠(又称水玻璃)价格便宜,但性能不好――温度变化时,容易脆裂,且因粘度高,附着在部件表面,浪费严重,另外,生产周期过长;聚酯,有较好的密封效果和良好的耐化学腐蚀性,但含有毒素及有害溶剂,不易生产。
汽车发动机气缸盖低压铸造工艺研究

汽车发动机气缸盖低压铸造工艺研究东安汽车动力股份有限公司铸造公司朱昱摘要本文综合分析了采用低压铸造工艺生产汽车发动机气缸盖的独特优点,从低压铸造设备、低压铸造模具设计、生产工艺、低压铸造生产中常见的问题及对策等多个角度,对低压铸造工艺的技术动向以及今后的研究课题提出了自己的见解。
关键词低压铸造气缸盖模具设计浇注系统排气系统缩松微量元素浇冒口1 绪论随着汽车工业的飞速发展和现代汽车制造业轻量化、节能环保要求的不断提高,铝合金铸件在汽车发动机锻铸件中所占比重日益增大,铝合金特种成形工艺获得了较快发展,其中尤以低压铸造工艺的应用得到了迅速的普及应用与推广。
与其它传统的铝合金铸造工艺相比,低压铸造工艺有着十分明显的优势。
采用设计合理的带有冷却系统的模具可实现铸件的顺序凝固,铸件从底部得到浇注和补缩,因此可以不用冒口,铸件的工艺出品率高(一般在90%以上),由于在压力下充型,铸件组织致密,尺寸精度和表面光洁度很好且可以采用砂芯制造出复杂的缸体、缸盖类铸件。
低压铸造工艺在资源匮乏的日本应用十分广泛,近年来随着中国汽车工业的发展和国际间技术合作与交流的增强,我国如广汽本田、东风日产、一汽丰田、重庆长安等厂家纷纷引进低压铸造工艺用于生产气缸盖铸件,产品质量良好,目前均已形成了较大规模。
低压铸造是液态金属在干燥的空气压力作用下,沿着升液管由下而上地充填型腔,以形成铸件的一种方法。
由于在整个铸造过程中采用的压力较低,所以称之为低压铸造。
金属液是在外力作用下结晶凝固,进行补缩,它的充型过程不同于重力铸造及高压高速充型铸造(压铸),具有以下独特的优点:(1)液体金属充型比较平稳,速度易控制;(2)铸件成形性好。
在压力下充型,流动性增加,有利于获得轮廓清晰的铸件;(3)铸件组织致密,综合力学性能高。
对要求耐压、防漏的铸件其效果更好;(4)工艺出品率高。
浇注过程中,压力卸掉后浇口中未凝固的金属液回流到保温炉里再次用于铸造。
汽车发动机缸体缸盖消失模铸造技术的研究与应用

20 0 7年第 1 期
20 0 7年 2月
铸 造
设 备
研
究
F b2 0 N e .07 o l
R S A C T D E N F U D Y E U P N E E R H S U ISO O N R Q IME T
・
frea d al a x a sigtmp rtr 9 ℃ :s k ere0 2 F N i h o dt n o e raep we. oc i g e u t e aue 1 n s h n e mo ed ge , S ntec n io fd mac t o r i Ke wo d :uo bl ,n ie,yid rbo k & c l d rh a ls fa c sig c ti n mae a y r s a tmo i e gn c l e l e n c yi e e d,ot o m a t , a r trl n n s o i
sm t nidxct o no . / w ・ , ig xa sn m rtr 9℃ ads o e ere . S ecn io fwsn u pi e u dw n15g k h a a ehut gt p a e o n ls i ee u n m k ge 1 N i t odt no iig d 0 F nh i t t
应用 研 究 ・
汽 车发 பைடு நூலகம் 机 缸体 缸 盖 消 失 模 铸 造 技术 的 研 究 与 应 用
王新 节
( 安徽 全柴集团有限公 司, 安徽 全椒 2 90 ) 350
摘 要 : 了降低发 动机 单位功率的重量指标 、 为 油耗指标及尾 气排放 指标 , 们研 究并开发 了直列四缸二 我
轿车发动机铝合金缸体和缸盖的铸造技术

/ 《铸造技术》 ) ’ " " ’
吴浚郊: 轿车发动机铝合金缸体和缸盖的铸造技术
・’ B )・
! ! ! ! ! ! ! ! ! ! ! ! ! ! ! ! ! ! ! ! ! ! ! ! ! ! ! ! ! ! ! ! ! ! ! ! ! ! ! ! ! ! ! ! ! ! ! ! ! ! ! ! ! ! ! ! ! ! ! ! ! ! ! ! ! ! 注机 (配!台电磁泵) , 每小时生产率达! " "型。 ! 精确砂型铸造 常温下在芯盒内通气快速硬化砂芯的 “冷芯盒” 制 芯技术的应用, 使制芯生产率和砂芯尺寸的可预见性 得以提高, 精确砂芯组芯造型 (即精确砂型) 一定程度 上取代常用于生产铸铁及铸铝汽车件的粘土砂型及金 属型。以下简述几种具有代表性的使用精确砂型的铸 造方法。 ( )英国 # 重力 ! $ % &法采用冷芯盒砂芯组芯造型, 浇注。由于所用的工艺装备 (芯盒) 制造得十分精确, 可获得尺寸十分精确的铝铸件, 该方法可生产壁厚仅 缸盖。 ’ ( )* * 的复杂铝合金发动机缸体、 ( )德国 + ’ , % . & /铸造厂采用 ! 种独特的方法来 进行冷芯盒砂芯的组装。先制好的!底盘砂芯滞留在 第!套芯盒的下芯盒内。该底盘砂芯的下芯盒就作为 输送 “夹具” 逐次通过生产线上的每 ! 台射芯机, 利用 芯盒上精确的定位销、 套系统进行自动砂芯装配 (图 ) 。每台射芯机生产相应的 ! 层砂芯, 除第 ! 台射芯 0 机外, 其余的射芯机皆将制造的砂芯滞留在上芯盒中, 以便进行由上而下的组装。 产! 种 E ( <F@ A汽车柴油机的铝缸盖。在! G 0 A年将 迄今已生产了 ) 其用于生产’ ( ’F 四缸铝缸盖, " "万 件。 ! G 0 A年通用公司在其所属的土星汽车厂用实型 铸造生产铝缸体和缸盖以及球铁曲轴和凸轮轴。 G " 年 代 末, >? 公 司 铸 造 开 发 和 验 证 中 心 (= ) 开发用实型铸造生产出铝缸体 (质量 E ) H @ = "I 3 及缸盖 (质量’ ) 的技术。在’ ’I " " !年 >? 公司萨金 3 诺铸造厂 (J 用此法生产了 ’ ? = K) 0 0" " " 件铝缸体和 ’ 0 0" " "件铝缸盖。预计到’ " " ’年! "月, J ? = K 可达 到日产’! 件铝缸体和 件铝缸盖的目标。 " " ’! " " 德国 L ?M 汽 车 公 司 在 几 年 前 已 建 立 成 年 产 件铝缸盖的实型铸造厂。 < < "" " " # 湿型铸造 美国 >? 汽车公司萨基诺金属铸造厂数年前将 生产铸铝件的高压造型线改建为生产铝缸盖, ’ " " !年 用粘土砂湿型生产了!G ’ )" " "铝缸盖。 丹麦 H N J + 公司一直致力于开发垂直分型无箱射 压造型机及低压浇注来生产铝铸件, 特别是铝缸体。 这种工艺采用低压体铝液从砂型侧面由下而上地充填 型腔。在充填完毕后, 将砂型底侧的浇口切断, 并将 ! 通气小管从上向下插入砂型的冒口内, 引入气压体冒 口进行补缩。如果这种工艺能成功地用于大量生产铝 缸体, 则由于上述造型机的高生产率 ( / 小时 ! ’ " "型 / 小时) , 它将带来很大的经济效益。 < " "型 $ 结束语 世界著名汽车厂铝合金缸体、 缸盖所用的铸造工
缸体相关知识点总结
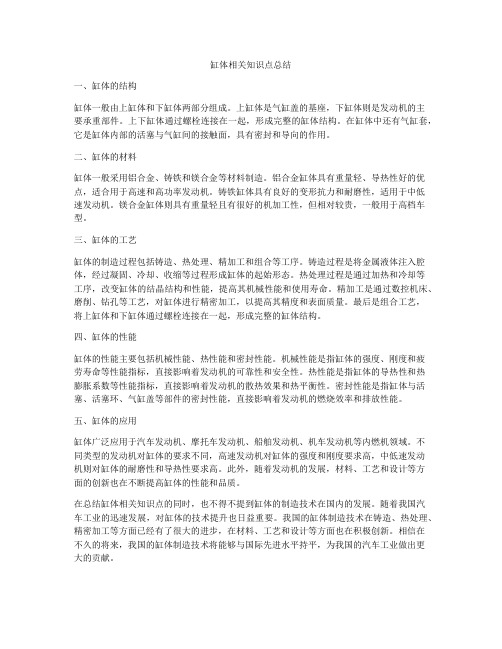
缸体相关知识点总结一、缸体的结构缸体一般由上缸体和下缸体两部分组成。
上缸体是气缸盖的基座,下缸体则是发动机的主要承重部件。
上下缸体通过螺栓连接在一起,形成完整的缸体结构。
在缸体中还有气缸套,它是缸体内部的活塞与气缸间的接触面,具有密封和导向的作用。
二、缸体的材料缸体一般采用铝合金、铸铁和镁合金等材料制造。
铝合金缸体具有重量轻、导热性好的优点,适合用于高速和高功率发动机。
铸铁缸体具有良好的变形抗力和耐磨性,适用于中低速发动机。
镁合金缸体则具有重量轻且有很好的机加工性,但相对较贵,一般用于高档车型。
三、缸体的工艺缸体的制造过程包括铸造、热处理、精加工和组合等工序。
铸造过程是将金属液体注入腔体,经过凝固、冷却、收缩等过程形成缸体的起始形态。
热处理过程是通过加热和冷却等工序,改变缸体的结晶结构和性能,提高其机械性能和使用寿命。
精加工是通过数控机床、磨削、钻孔等工艺,对缸体进行精密加工,以提高其精度和表面质量。
最后是组合工艺,将上缸体和下缸体通过螺栓连接在一起,形成完整的缸体结构。
四、缸体的性能缸体的性能主要包括机械性能、热性能和密封性能。
机械性能是指缸体的强度、刚度和疲劳寿命等性能指标,直接影响着发动机的可靠性和安全性。
热性能是指缸体的导热性和热膨胀系数等性能指标,直接影响着发动机的散热效果和热平衡性。
密封性能是指缸体与活塞、活塞环、气缸盖等部件的密封性能,直接影响着发动机的燃烧效率和排放性能。
五、缸体的应用缸体广泛应用于汽车发动机、摩托车发动机、船舶发动机、机车发动机等内燃机领域。
不同类型的发动机对缸体的要求不同,高速发动机对缸体的强度和刚度要求高,中低速发动机则对缸体的耐磨性和导热性要求高。
此外,随着发动机的发展,材料、工艺和设计等方面的创新也在不断提高缸体的性能和品质。
在总结缸体相关知识点的同时,也不得不提到缸体的制造技术在国内的发展。
随着我国汽车工业的迅速发展,对缸体的技术提升也日益重要。
我国的缸体制造技术在铸造、热处理、精密加工等方面已经有了很大的进步,在材料、工艺和设计等方面也在积极创新。
5汽车发动机气缸盖低压铸造工艺研究

汽车发动机气缸盖低压铸造工艺研究东安汽车动力股份有限公司铸造公司朱昱摘要本文综合分析了采用低压铸造工艺生产汽车发动机气缸盖的独特优点,从低压铸造设备、低压铸造模具设计、生产工艺、低压铸造生产中常见的问题及对策等多个角度,对低压铸造工艺的技术动向以及今后的研究课题提出了自己的见解.关键词低压铸造气缸盖模具设计浇注系统排气系统缩松微量元素浇冒口1 绪论随着汽车工业的飞速发展和现代汽车制造业轻量化、节能环保要求的不断提高,铝合金铸件在汽车发动机锻铸件中所占比重日益增大,铝合金特种成形工艺获得了较快发展,其中尤以低压铸造工艺的应用得到了迅速的普及应用与推广。
与其它传统的铝合金铸造工艺相比,低压铸造工艺有着十分明显的优势。
采用设计合理的带有冷却系统的模具可实现铸件的顺序凝固,铸件从底部得到浇注和补缩,因此可以不用冒口,铸件的工艺出品率高(一般在90%以上),由于在压力下充型,铸件组织致密,尺寸精度和表面光洁度很好且可以采用砂芯制造出复杂的缸体、缸盖类铸件。
低压铸造工艺在资源匮乏的日本应用十分广泛,近年来随着中国汽车工业的发展和国际间技术合作与交流的增强,我国如广汽本田、东风日产、一汽丰田、重庆长安等厂家纷纷引进低压铸造工艺用于生产气缸盖铸件,产品质量良好,目前均已形成了较大规模。
低压铸造是液态金属在干燥的空气压力作用下,沿着升液管由下而上地充填型腔,以形成铸件的一种方法。
由于在整个铸造过程中采用的压力较低,所以称之为低压铸造。
金属液是在外力作用下结晶凝固,进行补缩,它的充型过程不同于重力铸造及高压高速充型铸造(压铸),具有以下独特的优点:(1)液体金属充型比较平稳,速度易控制;(2)铸件成形性好.在压力下充型,流动性增加,有利于获得轮廓清晰的铸件;(3)铸件组织致密,综合力学性能高。
对要求耐压、防漏的铸件其效果更好;(4)工艺出品率高。
浇注过程中,压力卸掉后浇口中未凝固的金属液回流到保温炉里再次用于铸造。
论汽车铝合金缸体缸盖铸造工艺研究现状
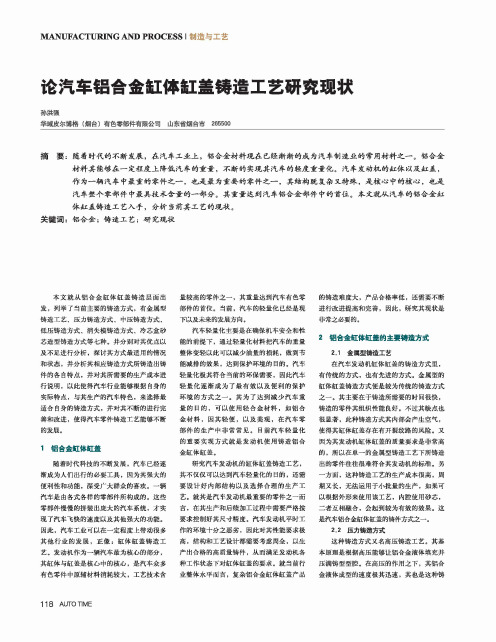
MANUFACTURING AND PROCESS I卸造与工艺论汽车铝合金缸体缸盖铸造工艺研究现状孙洪强华域皮尔博格(烟台)有色零部件有限公司山东省烟台市2655〇〇摘要:随着时代的不断发展,在汽车工业上,铝合金村料现在已经渐渐的成为汽车制造业的常用材料之一。
铝合金材料其能够在一定程度上降低汽车的重量,不断的实现其汽车的轻度重量化。
汽车发动机的缸体以及缸盖,作为一辆汽车中最重的零件之一,也是最为重要的零件之一,其结构既复杂又特殊,是核心中的核心,也是汽车整个零部件中最具技术含量的一部分。
其重量达到汽车铝合金部件中的首位。
本文就从汽车的铝合金缸体缸盖铸造工艺入手,分析当前其工艺的现状。
关键词:铝合金;铸造工艺;研究现状本文就从铝合金缸体缸盖铸造层面出发,列举了当前主要的铸造方式,有金属型 铸造工艺、压力铸造方式、中压铸造方式、低压铸造方式、消失模铸造方式、冷芯盒砂 芯造型铸造方式等七种。
并分别对其优点以 及不足进行分析,探讨其方式最适用的情况 和状态,并分析其相应铸造方式所铸造出铸 件的各自特点,并对其所需要的生产成本进 行说明,以此使得汽车行业能够根据自身的 实际特点,与其生产的汽车特色,来选择最 适合自身的铸造方式,并对其不断的进行完 善和改进,使得汽车零件铸造工艺能够不断 的发展。
1铝合金缸体缸盖随着时代科技的不断发展,汽车已经逐 渐成为人们出行的必要工具,因为其强大的 便利性和功能,深受广大群众的喜欢。
一辆 汽车是由各式各样的零部件所构成的。
这些 零部件慢慢的拼装出庞大的汽车系统,才实 现了汽车飞快的速度以及其他强大的功能。
因此,汽车工业可以在一定程度上带动很多 其他行业的发展,正像:缸体缸盖铸造工艺。
发动机作为一辆汽车最为核心的部分,其缸体与缸盖是核心中的核心,是汽车众多 有色零件中原辅材料消耗较大,工艺技术含量较高的零件之一,其重量达到汽车有色零部件的首位。
当前,汽车的轻量化已经是现下以及未来的发展方向。
铝合金汽车发动机缸体的压铸生产

铝合金汽车发动机缸体的压铸生产本文著作:布勒中国邹智厚卢宏远徐仲杰长安汽车研究院乐虎万伯谦布勒瑞士压铸有限公司FfitSche Bemhard摘要:本文阐述了高压铸造生产缸体的特点,并简单介绍了压铸岛的一些必须设各及v型缸体的生产要点。
1.缸体压铸特点众所周知,压铸产品中有很多产品用于汽车的零部件。
随着对环保,轻量化的要求日益提高,汽车中的许多关键部件,如发动机缸体等,逐渐转向压铸生产。
多年来,欧美和日本的大多数汽车公司已经采用压铸方法生产铝合金发动机缸体。
在国内,用压铸方法生产铝合金发动机缸体目前也成为一种趋势。
相比传统的铸造,压铸缸体有以下优点:(1)效率高。
在所有的铸造方法中,压铸是一种生产率最高的方法。
这主要是由压铸过程的特点决定的,且随着生产工艺过程机械化、自动化程度进一步发展而提高。
生产一个缸体的时间一般为3分钟左右,相对传统的低压或者砂型铸造省时省力:(2)精度高a只需个别部位加工即可使用:(3)铸件的强度和表面硬度较高;(4)节能省耗。
一般每台设备每年可生产7万件左右:(5)占地面积少。
(6)工艺路线短。
传统的铸造工艺,缸体生产需要经过造型、制芯、浇注、冷却、落砂、清理、机加,热处理等诸多工序。
而压铸则只需提前加工模具,浇注后很快将缸体毛坯铸件从压铸岛中取出,或者由人工去除飞边毛刺,之后进行检验、加工等便可。
压铸也有一定的缺点:(1)铸造缺陷较多。
由于液体合金充型速度极快,型腔中的气体很难完全排除,常以气孔形式存留在铸件中。
另外,压铸填充过程中的氧化夹杂等,如果集渣包等设计不合理,容易残留在产品内部:(2)压铸初次投资较高。
有统计,如果生产的缸体数量低于10万个的话,低压铸造或砂型铸造的成本低于压铸。
2.缸体图片及压铸岛布局排量在2.0以下的汽车缸体一般为直列3缸或四缸,而大于2.0排量的缸体则可能为直列六缸或V型六缸。
目前来讲,一般的压铸岛(压铸机和各周边设备一起统称为压铸岛)布局比较复杂,而且没有标准的布局格式。
- 1、下载文档前请自行甄别文档内容的完整性,平台不提供额外的编辑、内容补充、找答案等附加服务。
- 2、"仅部分预览"的文档,不可在线预览部分如存在完整性等问题,可反馈申请退款(可完整预览的文档不适用该条件!)。
- 3、如文档侵犯您的权益,请联系客服反馈,我们会尽快为您处理(人工客服工作时间:9:00-18:30)。
●用擦洗砂代替水洗砂; ●为减少发气量降低了低 氮树脂用量,由过去2.5%一2.8% 降为2.2%~2.5%,加入硅烷作偶 联剂提高强度; ●使用树脂存放期不超过 三个月,时间长了砂芯膨胀大, 芯子易变形开裂; ●芯盒中固化温度不变,固 化时间由60s延长到80s; ●采用四开盒制芯; ●芯砂及涂料中加入氧化 铁粉; ●非常注意芯子防潮。 3.4芯子的出气和清整 3.4.1芯子排气:砂芯除严格控 制原材料的发气量外,芯子本身 也要做得排气通畅,特别是芯头 部位,要设计足够大的芯头,便 于开出足够大的通气道和加大 砂芯间的接触防止金属钻入。水 套芯可在芯子内部钻孔,形成内 部通气网络,打穿处用修补料抹 死。缸筒芯应做成中空。 3.4.2芯子的清整:要清除芯子 的飞边毛刺,不然浇出的铸件出 现凹痕,会严重削弱该处的强 度,往往成为缸体开裂的源头。 东风公司曾一度发生缸底面开 裂,有的在落砂震动时就开裂, 造成重大经济损失。 芯子的射嘴在去除时常发 生打缺芯子本体的现象,过去都 用修补料抹平,但修补料受热变 形不一致,浇注时容易脱落造成 铸件夹砂等废品,现都将射嘴根 部做出lmm高的小台阶,打掉射 嘴后用砂条磨平。 3.5缸体芯子的安装方法 对直列六缸缸体常用下列 方法安装砂芯。 3.5.1独立组合式:即先将芯子 在专用组芯工作台上有序地排 列组合,然后用专用夹具提起放 入砂型中。这种下芯方法本公司 沿用多年,工序少、生产率高。缺
在精度上常用加工后缸孔 壁厚的偏差来衡量,上世纪偏差 要求±(O.5-1)ram,现在要求± (0.2~0.5)ram。主要靠水套芯和圆 棒芯(缸筒芯)的制造精度与控 制二者的相对位置来保证,也涉 及各种材料的热变形。康明斯B 系列缸体,外型856x360x460 (mm)、重190kg,缸径a114mm、 自由式径中心距137mm,两缸之 间的空隙C即水套芯厚仅4ram, 由于铸件废品多,进口毛坯要 400美元一件,很不合算,造成加 工单位经常停产待料。
汽车铸件的全球化采购不
收稿日期:2005—03—21 文章编号:2005—041
万方数据
容忽视,铸造水平体现在质量和 成本上。为提高缸体类复杂铸件 的铸造技术,厂际问相互交流生 产经验和体会很有必要,此文意 在抛砖引玉。
1提高缸体铸件精度分析 1.1基准选择
铸造和机加工都需要工艺 基准面。缸体上有上千个尺寸, 每个尺寸在生产中都会有偏差, 构成的尺寸链有时很大,这在设 计上是不被允许的。基准的选择 就是从哪点量起,通过它可严格 控制外模尺寸,芯子尺寸、下芯 位置以及毛坯几何形状精度。加 工基准则用来确定毛坯加工的 定位点。基准的选择要合理而且 前后应当一致。
性(即以缸筒外壁加工内孔),一 般偏差小于lmm。
上下方向靠基准芯(缸顶芯 又称枕头芯)定位,即在水套芯上 做出与缸盖通水孔小芯头,严格 控制芯头高度(康明斯B系列为 33.7+0.1mm、水套芯与缸顶面距 离为19.2+0.1mm,将水套芯与缸 顶面芯胶合或螺栓固定,水套芯 两端头也做出大的工艺孔,’(距缸 顶面40.2±0.1mm)该孔不仅出砂 出气,还作为高度和宽度方向的 加工基准。该工艺孔的芯头分别 固定在缸体前后端面芯的窝座 上,最后锁合成联体,这样所有砂 芯构成部位都能保证尺寸精度。
粘合工艺可提前进行,组合 好后整体浸涂料,上悬链进行烘 干,彻底干后缓冷,再稍作清整 (外芯头不上涂料,出气孔不能 堵塞),然后和造型线同步。当前 轿车缸体生产多用此法(巴西生 产康明斯C系列也用此法)。多 数厂反应,该工无返修品,铸件 内废1%左右,外废0.2%~0.4%。
下芯时多采用两次定位方 式,一是框架先与砂箱定位,芯 子夹具再沿框架内滑道下移至 型内。这样消除了擦砂磕碰现 象。
铸件精度是一个综合指标, 公司过去仅能达到9~10级,现 在大多要求是7~8级,因此在各 个工艺环节都要建立新的起点。
2造型工艺的改进 2.1高压造型
虽然各种造型方法都能生 产出缸体铸件,但如今缸体技术 条件要求之高,应首推高压造 型。公司原用中低压造型生产球 铁曲轴十年多,改为高压造型 后,仍用原来的模板,但铸件轻 了1.5kg,工艺改进后冒口也减少 了6kg,校正工作量也由2%~3% 降为零。
①旧砂温度应控制在35~ 40℃内;
②型砂水分控制在3.1%~ 3.6%,下型应该更低一些;
⑧有效膨润土量7%~8.5%; ④煤粉4%~5.5%。 使其湿压强度稳定在0.13~ 0.16MPa,通气度在1 10—150。 2.2.2改进砂斗:保持型砂性能 稳定,混制与造型的距离越近越 好。为使每班结束时贮砂斗中不 存砂,下一班开始时能用到新制 备的型砂,现已将造型机上方砂 斗由40t容量改为lOt(国外为生 产5:--10箱用量),在砂斗下方每 半小时测试一次型砂性能,不合 格时由回砂皮带立即返回重混, 此举措对减少型废成效显著。 2.2.3提高表面成型及抗粘砂 能力:不少铸造厂在砂型表面喷 耐热涂料(水基用煤气喷干,醇 基点燃干燥),有更多的厂采用 面砂(或用树脂自硬砂),虽然在 型砂表面增加了工序,但对减少 冲砂和表面缺陷、提高表面粗糙 度、减少型废、减少清理工作量 等大有好处。多数厂反应铸件返 修品大量减少,铸件成本降低。
7
后再予修正。 1.4提高工装制造精度
过去用普通加工机床,用样 板手动加工模具,精度仅为± 0.2mm,现在用数控铣床加工,精 度在±0.03ram。过去铸件壁厚是 5.5±1.5mm,现在已要求3.5± 0.5mm,大量或成批生产铸件精 度要靠精密的工装。以水套砂芯 为例,原来热芯盒制造精度为-I- 0.5mm,现在是±0.35mm。起模斜 度也大大减小,有的根本不允许 留斜度,故必须使用四开模或六 开模制芯机生产。
4缸体材质 缸体材料发展的方向是铸
铁一铝合金一蠕铁。现在仅轿车 有部分铝合金缸体、赛车已有用 蠕铁缸体,大部分还是灰铁材质, 一般牌号Hrl250,以康明斯B系 列要求为例:本本试样orb> 210MPa,缸顶面硬度HBl97±7、 A型石墨>80%、B型<10%,石墨 长度3-6级,基体为细片状珠光 体,铁素体<10%,碳化物+磷化 物<5%。 4.1铸铁成分的控制
3型芯制作 生产缸体铸件,要由十多个
砂芯组合而成,每个砂芯尺寸精 确和定位准确有非常重要意义。 3.1热芯盒与冷芯盒
砂芯在芯盒中硬化,用芯盒 尺寸保证芯子精度,取出后又能 保持尺寸稳定,是生产高精度砂 芯的重要手段。
热芯盒和冷芯盒工艺都是用 树脂砂吹制砂芯,为获得棱角清 晰的砂芯,满意的紧实性是必要 的,因为再修芯的可能性受到限 制,所以芯盒的设计必须力求使 气体在芯盒排出的速度大于进气 速度,不然就降低了压实性,故应 允分利用排气塞,在分盒面及顶 出孔周围要加工出0.25mm的排 气槽和间隙加强排气,并应经常 清理芯盒表面脂垢,以避免芯子 表面粘砂、粗糙、结疤。 3.2覆膜砂的使用
覆膜砂可直接购买,且存放 方便,在使用中砂的流动性好,可 省去上涂料,存在优点较多,故应 用较多。
使用中的问题是覆膜砂不能 存放太久,时间长了会产生砂粒 分离现象,更不能使用结块的,不 然生产出的芯子又硬又脆、容易 产生龟裂或破损。
‘。
3.3水套芯 在缸体芯子中水套芯属重要
砂芯,因为在长冲程发动机向短 冲程发展中,缸体外型尺寸变小, 意味着水套容积减小,水套芯必 将做得更加单薄精巧,这给该芯 的强度、通气和防止变形增加了 难度。
③劳动强度大,一条造型线 (班产600~700型)需要两套组 芯工作台,若用一组工作人员非 常劳累;
④芯子数量大又都是临时 急忙组合,芯子的出气孔来不及 串通,铁液钻芯子的现象时有发 生。 3.5.2粘合式下芯:即用快干型 粘合剂(或用螺栓联结、或用二 次射砂联结),将所有芯子结合 为一体,然后用下芯夹具(或吊 钩)提起放入型腔。这种工艺组 芯夹具简单,下芯夹具也简单, 芯子放置位置精度高,砂芯间的 配合精度也高(相当一个大芯 子)。
影响铸件精度的还有错边 的问题,要定期检查模板和砂箱 的定位销和衬套尺寸,新销子是 名义尺寸岩o,新衬套名义尺寸与 嘶,磨损极限销子最小允许 一0.25mm、衬套最大+0.25mm,这 也是国外常用标准。东风公司已 将砂箱编号,每周轮流取下10 副砂箱按标准检查合格后再上 线使用。
影响铸件精度还有工艺的 稳定性,如型砂、芯砂、铁液成分 等都是不能轻易改变的。
万方数据
点是: ①组芯工作台必须定位准
确、芯子之间定位、下芯夹具的 定位也均须准确。但实际生产中 很难做到准确定位,此外,工作 台上有散落砂将芯子垫起影响 定位,芯子位置精度不高有间隙 就有位移,就会有散砂,不仅返 修品多,清理工作量也大,也影 响铸件尺寸精度。
②下芯夹具的刚性要好,夹 起时芯子ห้องสมุดไป่ตู้不变形不位移;
缸体主要是照顾几个缸筒 尺寸,涉及芯子的精度。水套芯 形成缸筒外壁,圆棒芯形成缸筒 内壁,选用基准就是要使前后几 个缸筒尺寸变化最小。 1.2水套芯做工艺基准
我公司取缸体水套中间工 艺孔(出砂孔)中心(即3~4缸中 间楔形块定位)作缸体前后方向 基准,这样的基准可将尺寸链减 为最小,保证了缸筒壁厚的均匀
高压造型优点很多,我公司 把压力控制在0.9~1.1MPa,型腔 表面硬度C型80以上。
万方数据
8
2.2提高型砂性能 2.2.1’控制型砂组成:型砂性能 受组成和混碾影响,型砂性能差 不仅会产生废品,还会影响造型 本身。
型砂性能测试如紧实率和 破碎指数很重要,基本上能反映 型砂使用的综合性能,一般紧实 率控制在45%~50%,破碎指数 80%左右,高破碎指数虽然型砂 韧性好但难压实。配砂的经验 是:
汽车发动机缸体铸造技术
赵书城 (东风汽车公司,湖北十堰市442001)
摘要:主要从缸体铸件工艺基准的选择、型芯砂性能的控制、提高铸件精度的措施、型芯制作、铁液成份 控制等方面介绍了东风汽车公司汽车发动机缸体铸件的生产技术。
关键词:发动机缸体;铸铁生产 中图分类号:TG25;文献标识码:A;文章编号:1006—9658(2005)03—04