害事件发生后结果的严重性S判别标准
风险后果的严重性判断标准

严重性分值 5 4 3 2 1
财产损失
停工时间
(或超支) (或延误时间)
对产品/顾客的影响
≥50万元 ≥10万元 ≥1万元 <1万元
无
≥10天
潜在失效后果影响产品安全和/或 不符合政府法规
≥5天 ≥1天 半天
基本功能丧失或降低
次要功能丧失或降低(产品可以使 用,但舒适性/便利性方面性能丧
失或降低)
外观或噪声不符合要求,一定或可 能引起顾客注意Βιβλιοθήκη 没有误时顾客没有反应
准
对过程的影响
可能危及操作者
可能产生废品,生产线停止 或速度降低
产品须离线返工后再被接受 产品在后工序加工前需要在 线返工,或给工作过程带来
轻微不便 对工作过程没有影响
事件后果严重性S判别准则

>10
1套装置停工或设备
地区影响
4
不符合公司的安全操作程序、规定
轻微受伤、间歇不舒服
<10
受影响不大,几乎不停工
公司及周边范围
5
完全符合
无伤亡
无损失
没有停工
形象没有受损
表:3-2事件后果严重性S判别准则
等级
法律、法规及其他要求
人员
财产损失/万元
停工
公司形象
1
违反法律、法规和标准
死停工
重大国际
国内影响
2
潜在违反法规和标准
丧失劳动能力
>25
2套装置停工、设备停工
行业内、
省内影响
3
不符合上级公司或行业的安全方针、制度、规定等
截肢、骨折、听力丧失、
风险等级的确定及划分标准
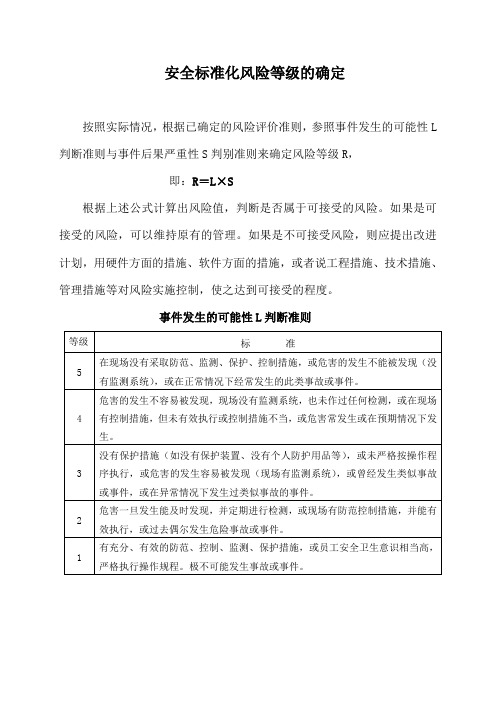
安全标准化风险等级的确定
按照实际情况,根据已确定的风险评价准则,参照事件发生的可能性L 判断准则与事件后果严重性S判别准则来确定风险等级R,
即:R=L×S
根据上述公式计算出风险值,判断是否属于可接受的风险。
如果是可接受的风险,可以维持原有的管理。
如果是不可接受风险,则应提出改进计划,用硬件方面的措施、软件方面的措施,或者说工程措施、技术措施、管理措施等对风险实施控制,使之达到可接受的程度。
事件发生的可能性L判断准则
事件后果严重性S判别准则
风险等级R判定准则及控制措施
重大风险的记录
根据风险评价结果,车间要对判定的重大风险进行严格控制和管理,记录重大风险,并定期更新。
车间应对每一个重大风险制定出一套严格的安全管理措施。
(1)技术措施:包括设施设计、建造、运转、维修,以及有计划的检查。
(2)组织措施:包括对人员的培训与指导、提供保证其安全的设备,工作人员水平、工作时间、职责的确定,以及对外来合同工和现场临时工的管理。
(3)管理措施:建立重大风险领导分工负责制。
(4)教育措施:包括对从业人员的操作技能培训和安全生产知识的教育培训。
制定应急救援计划
根据风险评价的结果,经评估作为重大风险的应制订现场应急救援方案,并定期检验和评估现场应急救援的有效程度,每年进行一次修订。
制定应急救援预案的目的是抑制突发事件,减少事故对员工、居民和环境的危害。
因此,应急救援预案应提出详尽、实用、明确和有效的安全技术与组织措施。
LS法安全风险评价准则

危害的发生不容易被发现,现场没有检测系统,也未发生过任何监测,或在现场有控制措施,但未有效执行或控制措施不当,或危害发生或预期情况下发生
3
没有保护措施(如没有保护装置、没有个人防护用品等),或未严格按操作程序执行,或危害的发生容易被发现(现场有监测系统),或曾经作过监测,或过去曾经发生类似事故或事件。
高度危险
采取紧急措施降低风险,建立运行控制程序,定期检查、测量及评估
立即或近期整改
9-12
C/3级
显著危险
可考虑建立目标、建立操作规程,加强培训及沟通
2年内治理
4-8
D/4级
轻度危险
可考虑建立操作规程、作业指导书但需定期检查
有条件、有经费时治理
1-3
E/5级
稍有危险
无需采用控制措施
需保存记录
表C.1-4 风险矩阵表
后
果
等
级
5
轻度危险
ห้องสมุดไป่ตู้显著危险
高度危险
极其危险
极其危险
4
轻度危险
轻度危险
显著危险
高度危险
极其危险
3
轻度危险
轻度危险
显著危险
显著危险
高度危险
2
稍有危险
轻度危险
轻度危险
轻度危险
显著危险
1
稍有危险
稍有危险
轻度危险
轻度危险
轻度危险
1
2
3
4
5
风
险
评
价
准
则
风险矩阵分析法(LS)
风险矩阵分析法(简称LS),R=L×S,其中R是风险值,事故发生的可能性与事件后果的结合,L是事故发生的可能性;S是事故后果严重性;R值越大,说明该系统危险性大、风险大。
风险矩阵法(LSR)和LEC危险性评价法

风险矩阵法(LSR)和LEC危险性评价法
风险矩阵法,是一种能够把危险发生的可能性和伤害的严重程度综合评估风险大小的定性的风险评估分析方法。
风险度R=可能性(L)×后果严重性(S)
R值越大,说明危险性大、风险大。
危害事件发生的可能性(L):
事件后果严重性(S):
风险等级(R):
LEC危险性评价法
一种评价具有潜在危险性环境中作业时的半定量评价法,适用于生产作业岗位风险分级评价。
数学模型:
危险性分值D=发生概率L×暴露频率E×严重度C
式中:
D———危险性分值(风险值);
L———发生事故/事件的可能性(概率);
E———暴露于危险环境的频繁程度(频率);
C———事故/事件后果可能的严重程度(严重度)。
事故/事件发生的可能性L值
事故发生的可能性L值事故发生的可能性L值完全可以预料10 很不可能,可以设想0.5
相当可能 6 极不可能0.2 可能,但不经常 3 实际不可能0.1
可能性小,完全意外 1
暴露于危险环境的频繁程度值
暴露的频繁程度E值暴露的频繁程度E值
事故/事件可能后果C值
LEC评价危险性D值及分级步骤如下:
(1)参照表1、表2、表3,分别查出被评岗位的事故发生概率L、作业人员暴露频率E、事故严重度C的对应数值。
(2)根据公式D=L×E×C计算该岗位危险性分值D。
LEC评价法D值与风险等级。
风险评价方法(SCL、JHA、LEC)解释与举例

风险管理——评价方法说明一、选定的方法二、方法介绍1、工作危害分析法(JHA)(1)定义:从作业活动清单中选定一项作业活动,将作业活动分解为若干个相连的工作步骤,识别每个工作步骤的潜在危害因素,然后通过风险评价判定风险等级,制定控制措施。
(2)特点:①.是一种半定量评价方法。
②简单易行,操作性强。
③分解作业步骤,比较清晰。
④有别于掌握每一步骤的危险情况,不仅能分析作业人员不规范的危害,而且能分析作业现场存在的潜在危害(客观条件)。
2、作业条件危险性分析法(LEC)(1)定义:作业条件危险性评价法是一种简便易行的衡量人们在某种具有潜在危险的环境中作业的危险性的半定量评价方法。
该方法以与系统风险有关的三种因素指标值之积来评价系统风险的大小,并将所得作业条件危险性数值与规定的作业条件危险性等级相比较,从而确定作业条件的危险程度。
作业条件危险性评价法(LEC法)是以所评价的环境与某些作为参考环境的对比为基础,将作业条件的危险性作因变量(D),事故或危险事件发生的可能性(L)、暴露于危险环境的频率(E)及危险严重程度(C)为自变量,确定了它们之间的函数式,根据实际经验,给出了3个自变量的各种不同情况的分数值,采取对所评价的对象根据情况进行“打分”的办法,然后根据公式计算出其危险性分数值,再在按经验将危险性分数值划分的危险程度等级表查出其危险程度的一种评价方法。
(2)特点:①是一种半定量评价方法。
②简单易行,操作性强,危险程度的级别划分比较清楚、醒目。
③有利于掌握企业内部危险点的危险情况,有利于促进改措施的实施。
④缺点:由于它主要是根据经验来确定3个因素的分数值及划定危险程度等级,因此具有一定的局限性,只能作为作业的局部评价,不能普遍适用。
3、安全检查表方法(SCL)(1)定义:安全检查表分析法是利用检查条款按照相关的标准规范等对已知的危险类别、设计缺陷和与一般工艺设备、操作、管理相关的潜在危险性和有害性进行判别检查。
JHA及SCL风险评价方法讲解(参考)

JHA及SCL风险评价方法讲解一、作业危害分析(JHA)介绍作业危害分析(Job Hazard Analysis,JHA)又称作业安全分析(Job Safety Analysis,JSA)、作业危害分解(Job Hazard Breakdown, JHB),是一种定性风险分析方法。
实施作业危害分析,能够识别作业中潜在的危害,确定相应的工程措施,提供适当的个体防护装置,以防止事故发生,防止人员受到伤害。
此方法适用于工艺操作,设备设施检修等。
作业危害分析将对作业活动的每一步骤进行分析,从而辨识潜在的危害并制定安全措施作业危害分析的主要步骤是:1、确定(或选择)待分析的作业;2、将作业划分为一系列的步骤;3、辨识每一步骤的潜在危害;4、确定相应的预防措施。
划分的作业活动步骤不能太笼统, 步骤划分也不宜太细,以致出现许多的步骤。
根据经验,一项作业活动的步骤一般不超过10项,要保持各个步骤正确的顺序。
为了辨识危害,需要对作业活动作进一步的观察和分析。
辨识危害应该思考的问题是:可能发生的故障或错误是什么?其后果如何?事故是怎样发生的?其他的影响因素有哪些?发生的可能性?以下是危害辨识的部分内容:·是否穿着个体防护服或配戴个体防护器具?·操作环境、设备、地槽、坑及危险的操作是否有有效的防护?·维修设备时,是否对相互连通的设备采取了隔离?·是否有能引起伤害的固定物体,如锋利的设备边缘?·操作者能否触及机器部件或机器部件之间操作?·操作者能否受到运动的机器部件或移动物料的伤害?·操作者是否会处于失去平衡的状态?·操作者是否管理着带有潜在危险的装置?·操作者是否需要从事可能使头、脚受伤或被扭伤的活动(往复运动的危害)?·操作者是否会被物体冲撞(或撞击)到机器或物体?·操作者是否会跌倒?·操作者是否会由于提升、拖拉物体或运送笨重物品而受到伤害?·作业时是否有环境因素的危害——粉尘、化学物质、放射线、电焊弧光、热、高噪音?工作危害分析(JHA)记录表单位:二车间日期:3月18日风险度R :a) 轻微的(L×S=1~3);b) 可承受的(L×S=4~8);c) 中等的(L×S=9~12);d) 重大的(L×S=15~16);e) 不可承受的(L×S=20~25)建议的改进措施:A—表示轻微的,不必采取措施;B—表示可承受的,应维持现状、保持记录,但要保持检查或测量;C—表示中等的,应制定管理制度、规定、规程进行控制;D—表示重大的,应制定目标、指标、管理方案,限期治理;E—表示不可承受的,应立即采取隐患治理措施;二、安全检查表分析(SCL)所谓安全检查表,就是为系统地辨识和诊断某一系统的安全状况而事先拟好的问题清单。
风险评价方法

风险评价方法A.1风险矩阵(LS)法风险矩阵法(简称LS),R=L×S ,其中R是危险性(也称风险度),是事故发生的可能性与事件后果的结合,L是事故发生的可能性;S是事故后果严重性;R值越大,说明被评价对象危险性大、风险大。
表A.1-1 事故发生的可能性(L)判断准则表A.1-2 事件后果严重性(S)判别准则表A.1-3 安全风险等级判定准则(R值)及控制措施A.1-4 风险矩阵表后果等级543211 2 3 4 5事故发生的可能性等级A.2作业条件危险性分析(LEC)评价法作业条件危险性分析评价法(简称LEC)。
L(likelihood,事故发生的可能性)、E(exposure,人员暴露于危险环境中的频繁程度)和C(consequence,一旦发生事故可能造成的后果)。
给三种因素的不同等级分别确定不同的分值,再以三个分值的乘积D(danger,危险性)来评价作业条件危险性的大小,即:D=L×E×C。
D值越大,说明该作业活动危险性大、风险大。
表A.2-1 事故事件发生的可能性(L)判断准则表A.2-2 暴露于危险环境的频繁程度(E)判断准则表A.2-3 发生事故事件偏差产生的后果严重性(C)判别准则A.2-4 风险等级判定准则及控制措施(D)A.3作业条件风险程度评价——MES法作业条件风险程度评价法(简称MES法),R= M×E×S ,其中R 是危险性(也称风险度),是事故发生的可能性与事件后果的结合,M是控制措施的状态;E是人体暴露于危险状态的频繁程度或危险状态出现的频次;S是事故的可能后果;R值越大,说明危险性大、风险大。
A.3.1控制措施的状态M对于特定危害引起特定事故(这里“特定事故”一词既包含“类型”的含义,如碰伤、灼伤、轧入、高处坠落、触电、火灾、爆炸等;也包含“程度”的含义,如死亡、永久性部分丧失劳动能力、暂时性全部丧失劳动能力、仅需急救、轻微设备损失等)而言,无控制措施时发生的可能性较大,有减轻后果的应急措施时发生的可能性较小,有预防措施时发生的可能性最小。
故障严重度(S)评分标准

故障严产生的影响操作人员和机器设备安全 或违反有关法律法规的极其严重的故障模式。 在有故障预兆的情况下,产生的影响操作人员和机器设备安全或 违反有关法律法规的极其严重的故障模式。 对生产线造成较大的破坏,产品可能必须100%报废,使产品或 系统丧失主要功能的故障模式,顾客非常不满。 对生产线造成较大的破坏,产品须分选,部分产品报废,导致 产品或系统丧失主要功能的故障模式,顾客不满。 对 生 产 线 造 成 较 大 的 破 坏 , 部 分 产 品报 废( 但产 品 不 需 分 选),一些部件失效,影响产品的舒适性和方便性,使顾客感 觉有些不满。 对生产线造成较小的破坏,产品可能必须100%的返工,一些部 件失效,影响产品的舒适性和方便性,顾客感觉有些不满。 对生产线造成较小的破坏,产品须分选,部分产品须返工,顾 客不满,加工精细、外观、噪音等方面不符合要求,大部分顾 客能发现有缺陷。 对生产线造成很小的破坏,部分产品站外在线须返工,加工精 细、外观、噪音等方面不符合要求,有一半顾客能发现有缺陷 。 对生产线造成很小的破坏,部分产品站内外在线须返工,加工 精细、外观、噪音等方面不符合要求,但很少有顾客能发现有 缺陷。 无影响
严重度(S)
10 9 8 7 6 5 4 3 2 1
事件后果严重性S判别准则

等级
法律、法规及其他要求
人
财产损失/万元
停工
公司形象
5
违反法律、法规和标准
造成1人死亡或2~3人重伤
>10
部分装置(≥2套)或设备停工
市内影响
4
潜在违反法规和标准
造成1人重伤或4~5人轻伤
>5
2套装置停工,或设备停工
县域影响
3
不符合公司和行业的安全方针、Leabharlann 度、规定等造成2—3人轻伤
>2
1套装置停工或设备
公司影响
2
不符合公司的安全操作程序、规定
造成一人轻伤
<2
受影响不大,几乎不停工
本部门影响
1
完全符合
无伤亡
无损失
没有停工
形象没有受损
评估危害及影响后果的严重性

有否 制度
制度 名称
执行 情况
日期:二〇〇七年三月 日
严重性 可能性 风险度 (S) (L) (R=S*L)
建议改正/控制措施
微职业中毒或岗位 职工职业病可能发
<100 万元
生
持续排放大量无毒污染 物,临近居民受到影响
收到多数外部人员投 诉,给处造成一定社会影 响
5
可造成 10 人及以 可造成职工严重职
上重伤或死亡 3 业中毒或职业病发 >100 到比较严重污染
收到多数外部人员投 诉和地方政府干预,给处 造成严重社会影响
可能性 严重性 风险度
L
S
R
潜在后果/影响
风险控制与削减措施
责任人 完成时间
备注:登记中等及以上危害因素(风险度≥9),按风险高低顺序排列,描述精简、准确,易于理解,措施要有针对性、可操作性。
领导审核:
工
登记人:
年月
序 号
工作步骤
工作危害分析(JHA)记录表
岗分析人员:
危害或潜在事件
主要后果
现有安全措施
<5 万元以下
临时/偶尔排放有毒污 染物,处内职工多数受 受到内部个别员工投诉 到一定影响
3
造成 5-10 人轻伤 或 1-2 人重伤
有少数职工造成轻 微职业中毒
<10 万元
临时/偶尔排放中等污 染物,临近居民受到轻 微影响
收到多数员工投诉,本 处形象受到影响
4
可造成多数职工轻
轻伤或 3-9 人重 伤或 1-2 人死亡
评估危害及影响后果的严重性(S)判别标准
等级 项目 人员受伤情况
职业健康影响 直接经济损失
环境污染
风险矩阵评价法RLS

风险矩阵评价法R L S
TPMK standardization office【 TPMK5AB- TPMK08- TPMK2C- TPMK18】
风险矩阵评价法基本原理是根据危险源辨识确定的危害及影响程度与危害及影响事件发生的可能性乘积确定风险的大小。
1、确定危害事件发生的严重程度(S)
对照表1从人员伤亡情况、财产损失、法律法规符合性、环境破坏和对企业声誉损坏五个方面对后果的严重程度进行评价取值,取五项得分最高的分值作为其最终的S 值。
表1-危害事件发生的严重程度(S)
2、确定危害事件发生的可能性(L)
对照表2从偏差发生频率、安全检查、操作规程、员工胜任程度、控制措施五个方面对危害事件发生的可能性进行评价取值,取五项得分的最高的分值作为其最终的L 值。
表2-危害事件发生的可能性(L)
3、确定了S和L值后,根据R=L×S计算出风险度R的值,依据表3的风险矩阵进行风险评价分级。
(注:风险度R值的界限值,以及L和S定义不是一成不变的,可依据具体情况加以修订。
)
表3-风险矩阵(R)
根据R的值的大小将风险级别分为以下五级:
R=L×S=17~25:关键风险(Ⅰ级),需要立即停止作业;R=L×S=13~16:重要风险(Ⅱ级),需要消减的风险;
R=L×S=8~12:中度风险(Ⅲ级),需要特别控制的风险;R=L×S=4~7:低度风险(Ⅳ级),需要关注的风险;
R=L×S=1~3:轻微风险(Ⅴ级),可接受或可容许风险。
表4风险分级控制模型表。
伤害严重程度的判定标准

伤害严重程度的判定标准
伤害严重程度的判定标准通常由法律、医学和社会公认的标准
共同确定。
在法律上,不同国家和地区可能有不同的判定标准,但
通常会考虑伤害的类型、程度和影响。
一般来说,严重伤害可能指
导致长期残疾、重大器官损伤或危及生命的伤害。
医学上,伤害严
重程度的判定可能涉及到损伤的部位、深度、范围和对身体功能的
影响。
社会公认的标准可能包括对受害者生活质量的影响、康复所
需的时间和成本等因素。
综合考虑法律、医学和社会公认的标准,
可以对伤害严重程度进行综合评估和判定。
在司法实践中,通常会
由专业人士如法医、法官和律师来进行具体的判定工作,以确保公
正和合理。
值得注意的是,伤害严重程度的判定标准可能会因国家、地区、具体案件和法律条文的不同而有所差异,需要具体问题具体
分析。
双预防体系建设--风险矩阵法(LS)
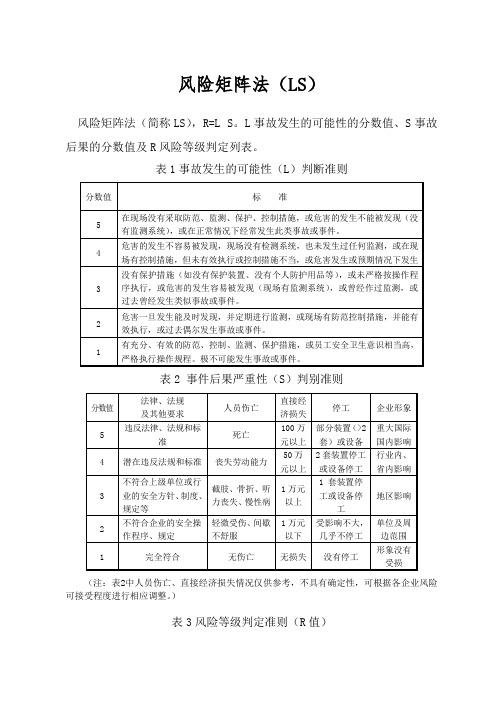
风险矩阵法(简称LS),R=L×S。L事故发生的可能性的分数值、S事故后果的分数值及R风险等级判定列表。
表1事故发生的可能性(L)判断准则
分数值
标准
5
在现场没有采取防范、监测、保护、控制措施,或危害的发生不能被发现(没有监测系统),或在正常情况下经常发生此类事故或事件。
4
危害的发生不容易被发现,现场没有检测系统,也未发生过任何监测,或在现场有控制措施,但未有效执行或控制措施不当,或危害发生或预期情况下发生
高度危险
4
轻度危险
轻度危险
显著危险
高度危险
及其危险
5
轻度危险
显著危险
高度危险
及其危险
及其危险
图例:低风险一般风险较大风险重大风险
1万元以上
1套装置停工或设备停工
地区影响
2
不符合企业的安全操作程序、规定
轻微受伤、间歇不舒服
1万元以下
受影响不大,几乎不停工
单位及周边范围
1
完全符合
无伤亡
无损失
没有停工
形象没有受损
(注:表2中人员伤亡、直接经济损失情况仅供参考,不具有确定性,可根据各企业风险可接受程度进行相应调整。)
表3风险等级判定准则(R值)
风险值
风险度
风险等级
颜色
20—25
高度危险
较大风险
橙
9—12
显著危险
一般风险
黄
4—8
轻度危险
低风险
蓝
﹤4
稍有危险
表4风险矩阵表
风险等级
后果严重性
1
2
3
4
5
可能性
1
LSR评价法

公司形象
5
违反法律、法规和标准
死亡
>50
部分装置(>2套)或设备停工
重大国际国内影响
4
潜在违反法规和标准
丧失劳动能力
>25
2套装置停工、或设备停工
行业内、省内影响
3
不符合上级公司或行业的安全方针、制度、规定等
截肢、骨折、听力丧失、慢性病
>10
1套装置停工或设备
地区影响
2
不符合公司的安全操作程序、规定
2
危险、有害因素一旦发生能及时发现,并定期进行监测,或现场有防范控制措施,并能有效执行,或过去偶尔发生危险事故或事件。
1
有充分、有效地防范、控制、监测、保护措施,或员工安全卫生意识相当高,严格执行操作规程。极不可能发生事故或事件。
表2事件后果严重性(S)判别准则
等级
法律、法规
及其他要求
人
财产损失/万元
轻微受伤、间歇不舒服
<10
受影响不大,几乎不停工
公司及周边范围
1
完全符合
无伤亡
无损失
没有停工
形象没有受损
表3风险等级判定准则及控制措施
风险度
等级
应采取的行动/控制措施
实施期限
20—25
巨大风险
在采取措施降低危害前,不能继续作业,对改进措施进行评估
立刻
15—16
重大风险
采取紧急措施降低风险,建立运行控制措施,定期检查、测量及评估
附件3
LSR评价法
LSR评价法:﹙风险等级评价﹚风险是发生特定危害事件的可能性及后果的结合。
风险值R=可能性L×后果严重性S
L—可能性;
- 1、下载文档前请自行甄别文档内容的完整性,平台不提供额外的编辑、内容补充、找答案等附加服务。
- 2、"仅部分预览"的文档,不可在线预览部分如存在完整性等问题,可反馈申请退款(可完整预览的文档不适用该条件!)。
- 3、如文档侵犯您的权益,请联系客服反馈,我们会尽快为您处理(人工客服工作时间:9:00-18:30)。
>10
套装置停工或设备
公司范围内中等污染
地区影响
2
不符合公司的安全操作程序、规定
轻微受伤、间歇不舒适
<10
受影响不大,几不停工
装置范围污染
公司及周边范围
1
完全符合
无伤亡
无损失
没有停工
没有污染
形象没有受损
危害事件发生后结果的严重性S与法规的符合性、人员伤亡、财产损失、停工、环境污染资源消耗、公司形象等有关,从上表可以看出等级越大,后果的严重性就越大。
害事件发生后结果的严重性S判别标准
等级
法律、法规及其他要求
人
财产
(万元)
停工
环境污染、资源消耗
公司形象
5
违反法律、法规和标准
发生死亡
>50
部分装置(>2套)或设备停工
大规模、公司外
重大国际国内影响
4
潜在违反法规和标准
丧失劳动能力
>
行业内、省内影响
3
不符合上级公司或行业的方针、制度、规定等
(3)风险度R。风险度可以通过下表的风险矩阵得到:
风险评估矩阵
1
2
3
4
5
1
1
2
3
4
5
2
2
4
6
8
10
3
3
6
9
12
15
4
4
8
12
16
20
5
5
10
15
20
25
(4)风险等级判定准则。风险等级判定准则及控制措施可以参考下表: