IE工序动作分析案例
IE工业工程经典案例分析

IE工业工程经典案例分析IE工业工程(Industrial Engineering)是一门涵盖工程、管理和人文社会科学等多学科的学科,其主要研究内容包括工业系统的设计、改进和优化。
在实际应用中,IE工业工程经常被用于分析和解决现实问题,提高工作效率和生产效益。
下面将介绍一些IE工业工程经典案例的分析。
一、汽车生产线优化汽车生产线是典型的工业系统,工业工程可以通过优化生产线,提高生产效率和质量。
例如,一家汽车制造公司发现生产线上存在许多不必要的工序和物料的运输,在IE工业工程师的帮助下,对整个生产线进行了分析和改进。
首先,IE工业工程师对生产线进行了布局分析,优化了工序之间的距离和物料传递的路径,降低了物流成本和生产周期。
其次,IE工业工程师使用工程技术手段,如自动化设备和机器人,取代了一些繁琐和重复的工序,提高了生产效率。
最后,IE工业工程师还设计了一个智能化的生产调度系统,通过实时监控,优化了生产计划和资源分配,实现了生产线的高效运行。
通过以上优化措施,该汽车制造公司成功提高了生产效率和质量,降低了生产成本,增强了市场竞争力。
二、物流配送优化IE工业工程师通过数据收集和分析,对物流网络进行了建模和优化。
他们利用运筹学方法,设计了一个最优的配送路线和调度策略,使得快递员的送货路线最短,减少了送货时间和成本。
此外,IE工业工程师还设计了一个智能化的仓储和分拣系统,通过自动化设备和信息技术,快速准确地将包裹分拣和装车,提高了工作效率和准确率。
通过上述优化措施,该快递公司成功提高了物流配送的效率和准确率,降低了成本,增加了客户满意度。
三、医疗服务流程改进IE工业工程在改善医疗服务流程方面也有着重要应用。
例如,一家医院发现其就诊流程存在许多瓶颈和低效的环节,患者等待时间长,医生工作效率低下。
IE工业工程师通过对整个就诊流程进行了分析和改进,提出了一系列优化方案。
首先,IE工业工程师通过调查和模拟实验,找出了就诊流程中的瓶颈环节和低效操作。
IE七大手法及案例

防呆法之 自动原理
3.自动原理 以各种光学、电学、力学、机构学、化学等原理来限制某些动作的执行或不 执行,以避免错误之发生。目前这些自动开关非常普遍,也是非常简易的 “自动化”之应用。 (1)以“浮力”的方式来控制 例:抽水马桶之水箱内设有浮球,水升至某一高度时,浮球推动拉杆,切断
水源。 (2)以“重量”控制的方式来完成 例:电梯超载时,门关不上,电梯不能上下,警告钟也鸣起。 (3)以“光线”控制的方式来完成 例:自动照相机,光线若不足时,则快门按不下去。 (4)以“时间”控制的方式来完成 例:洗手间内的“烘手机”,按一次只有“一分钟”,时间一到自动停止。
防呆法之 自动原理
(5)以“方向”控制的方式来完成 例:超级市场内进口及出口之单向栏栅,只能进不能出。或只能出不能进。 (6)以“电流”用量的方式来完成 例:家庭的电源开关皆装置保险丝,用电过量时,保险丝就熔断,造成断电。 (7)以“温度”控制的方式来完成 例:家庭内冷气机之温度控制,冷度够时,自动停止,温度上升时,自动开启
双手法 动改法
IE七大手法简介
授人以鱼,不如授人以渔!
名称 动改法 防呆法 五五法 双手法
人机法
流程法 抽查法
目的 改善人体动作的方式,减少疲劳使工作更为舒适、更有效率. 如何避免做错事情,使工作第一次就做好的. 借着质问的技巧来发掘出改善的构想. 研究人体双手在工作时的过程,借以发掘出可改善之地方.
判断以下防呆用的是什么原理?
治具上面贴有 不一样的颜色
相符原理
机器工作时需手同时下 压绿色按扭方可
保险原理
AB C
AB C
相符原理
断根原理
相符原理
断根原理
手机壳生产混穴的防呆改善
IE动作分析资料案例

IE动作分析资料案例IE是指工业工程(Industrial Engineering),是一门涉及到工业系统设计、改进和优化的学科。
IE动作分析是IE领域的一项重要工具,用于分析和优化工人在工作中的动作和姿势,以改善工作效率和工作条件。
下面将通过一个实际案例来说明IE动作分析的应用。
案例背景:工厂的一个装配线上,工人负责将零件组装成最终产品。
该装配线的生产效率较低,工人在组装过程中常常需要屈膝、弯腰等操作,导致工人疲劳度较高,工作效率受到影响。
因此,工厂决定使用IE动作分析方法来改善工人的工作动作和姿势,以提高装配线的生产效率。
1.观察和记录工人的动作和姿势:在装配线上观察工人的操作过程,记录工人的各个动作和姿势,包括屈膝、弯腰、伸腿等动作。
2.量化工作动作和姿势:使用IE工具进行工作动作和姿势的量化。
例如,使用动作时间研究方法测量每个动作的时间,使用人体测量仪测量工人在不同姿势下的肌肉活动度和疲劳度。
3.分析工作动作和姿势的问题:根据量化结果,分析工作动作和姿势存在的问题。
例如,可能发现工人在一些动作中花费了过多的时间,或者一些姿势对工人的肌肉活动度造成了负面影响。
4.设计改进措施:根据分析结果,设计改进措施来优化工作动作和姿势。
例如,通过重新安排工作站和工作布局,减少工人弯腰和屈膝的操作。
另外,可考虑引入辅助工具或设备来减轻工人的负担,提高工作效率。
5.实施改进措施并测量效果:将设计的改进措施应用到装配线上,并进行测量和评估。
比较改进前后的工作效率、工人疲劳度等指标,评估改进的效果。
6.持续改进:根据实施效果,反馈给工人和管理层,并进行持续改进。
持续监测和评估工人的工作动作和姿势,寻找改进的机会,并进行相应的优化。
案例结果:通过IE动作分析与改进的方法,该工厂成功优化了装配线上工人的工作动作和姿势。
改进后,工人的弯腰和屈膝操作减少,节省了大量时间。
工人的疲劳度也明显降低,工作效率得到显著提高。
IE现场改善讲义《动作分析》

空手
抓
搬运
动作要素改善检查表
(1) 可否使用导轨或挡块进行定位? 修正位置 (2) 物品的角度、形状能否配合定位进行改变? (3) 可否通过设计使定位不会出错? (1) 是否可以使用固定装置或诱导装置方便组合? 组合 (2) 能否依次装配很多件? (1) 能否使用工具进行分解? 分解 (2) 可否一次分解很多件? (1) 工具的大小、形状、重量能否改变? 使用 (2) 工具的拿法拿的位置能否简单化? (3) 工具、仪器、设备的使用能否简单化?
拆卸(DA):将一物分解为两个以上目的物的动素。 它包括从物体被控制(握取),处于可拆卸状态的 一瞬间到完全拆开的瞬间。拆卸常在“握取”之 后以及“移动”或“放开”之前发生。
第一类动素说明
放开(RL):放下目的物的动素。它包括从手指开 始离开目的物的瞬间直至手指完全离开目的物的 瞬间。“开放”是与“握取”“抓”“持住”等 相反的动素,是所有动素中时间消耗最少的。当 用身体某一部份对物体控制的状态解除的一瞬间 也视为“放开。 检查(I):将目的物与规定标准相比较的动素。它 包括从眼睛开始寻找的一瞬间到目的物被发现的 瞬间。
基本动作要素分析
基本动作要素分析的基本思想是吉尔布雷斯奠定的, 他认为人所进行的作业是由某些基动作要素(简称动 素)按不同方式、不同顺序组合而成的。 为了探求从事某项作业的最合理的动作系列,必须 把整个作业过程中人的动作,按动作要素加以分解, 然后对每一项动素进行分析研究,淘汰其中多余的 动作,改善那些不合理的动作。
案例说明-1
案例说明-2
案例说明-3
案例说明-4
动作分析
沙布利克分析基本步骤 仔细观察作业过程,大体把握作业重点,最好 能在脑海中描绘出整个动作过程。 把整个动作过程分解成几个较大阶段性动作 (作业要素)。 按左右手、眼睛对阶段性动作进行动作要素分 解,把动作描述、相应的记号记入沙布利克分 析表。 将分析结果与实际动作进行对照,找出遗漏或 错误的地方进行修改。 应记得在表中填写单位名称、产品名、作业名 称、分析人、分析时间等使分析表完整。
IE与作业分析教学案例

3.其他方法: 1)无法测试环境要素
2.)可以进行微细的分析
(四)WS法的步骤
1.确定目的 2.取得相关人员的协助 3.决定观测的范围 4.观测对象参别化 5.决定观测的项目 6.决定观测的数量 7.决定观测的时间 8.决定观测的路径与地点 9.准备观测的表格 10.预备观测 11.正式观测
五.IE的重点目标—设计,设定,改善
设计制作新系统 设定使设计,改善后的系统能稳定发挥应
有的功能 改善强化原有的系统
六.IE手法涵盖的领域
Work study 处理processing Decision making 行动科学最适化 其他生产管理手法
七.IE追求的目标
提高生产现场的综合生产力 1.综合生产生产力公式=稼动率*标准化率*努 力程度*平衡率 80%*75%*70%*80%=33.6% 2.综合生产力的责任部门: 稼动率;业务部门及厂长 标准化率:经营层,管理者 平衡率:IE及管理者 努力程度:作业员,管理者
(五)案例演练—作业分析
请提出目前的一个作业,制作作业分析, 并提出改善案 。
四. 时 间 研 究
(一)标准工时的意义 (二)标准工时的目的 (三)标准工时的构成
(一)标准工时的意义
1利用决定好的设备 2.依照规定的作业条件 3.针对要求的工作有一定的熟练度及适性的
作业员 4.所定的工作时间内,没有对身体有不良影
WORK STUDY
努力程度
平衡率
生产现场的综合生产力 标准化率
稼动率
八.管理的循环—P—D—C--A
改善
设计
管理的循环
查检
实施
参,IE的7大手法
Line balancing 工程分析 稼动研究 动作研究 时间分析 Material handling layout
IE工业工程动作分析报告
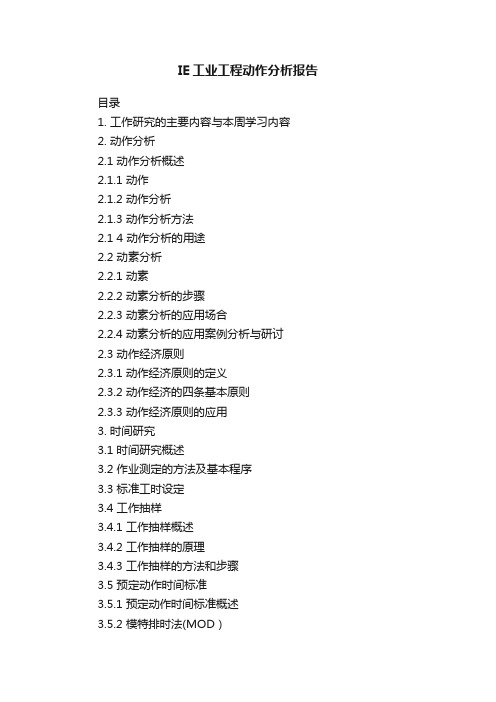
IE工业工程动作分析报告目录1. 工作研究的主要内容与本周学习内容2. 动作分析2.1 动作分析概述2.1.1 动作2.1.2 动作分析2.1.3 动作分析方法2.1 4 动作分析的用途2.2 动素分析2.2.1 动素2.2.2 动素分析的步骤2.2.3 动素分析的应用场合2.2.4 动素分析的应用案例分析与研讨2.3 动作经济原则2.3.1 动作经济原则的定义2.3.2 动作经济的四条基本原则2.3.3 动作经济原则的应用3. 时间研究3.1 时间研究概述3.2 作业测定的方法及基本程序3.3 标准工时设定3.4 工作抽样3.4.1 工作抽样概述3.4.2 工作抽样的原理3.4.3 工作抽样的方法和步骤3.5 预定动作时间标准3.5.1 预定动作时间标准概述3.5.2 模特排时法(MOD)3.5.2.1 MOD法的特点3.5.2.2 模特排时法的动作分类3.5.2.3 模特法的动作分析3.5.2.4 动作的改进3.6 生产线平衡分析1. 工作研究的主要内容与本周学习内容:基础IE的全过程是:利用程序分析、作业分析和动作分析获得最佳程序和方法,然后再利用时间研究将所有作业制定出标准时间。
2. 动作分析2.1 动作分析概述程序分析是从大处着眼,根据程序图分析生产过程的种种浪费,从合理安排程序中去寻求提高工作效率的方法。
而动作研究则是在程序决定后,研究人体各种操作动作之浪费,以寻求省力、省时、安全的最经济的方法。
动作分析的实质是研究分析人在进行各种工作操作时之细微动作,删除无效动作,使操作简便有效,以提高工作效率。
其内容为:发现操作人员的无效动作或浪费现象,简化操作方法,减少工人疲劳,在此基础上制定出标准的操作方法,为制定动作时间标准作技术准备。
它包括:动素分析、影象分析、动作经济原则等内容。
2.1.1 动作工艺流程和作业的具体实施方法,如为寻找、握取、移动、装配必要的目的物,操作者身体各个部位的每一个活动。
IE七大手法应用案例

精选PPT
13
6.五五法案例(2)
▪ 严格分析所记录的全部事实。采用提问技术对所记录的全部事实逐项提问。 ▪ 对步骤3的“操作”进行提问
❖ 问:完成了什么?是否必要?(What) ❖ 答:选取比需要稍长的橡皮管。该操作为保证需要所必须。 ❖ 问:为什么? ❖ 答:怕在柜台上量时不够长,故必须选择稍长的橡皮管。 ❖ 问:有无其它更好的办法? ❖ 答:可能有,假如能够储存各种不同长度的管子。 ❖ 问:何处做?(即在什么地方锯)(Where) ❖ 答:在柜台上。
精选PPT
4
装配螺栓与垫圈的动素程序图(原方法)
操作者左手的动作
伸向4号箱中的螺栓 从4号箱中选出并握取一个螺栓 带螺栓到桌子的中心部位 持住螺栓
带已完成的装配件到5号箱 放开装配件
操作者右手的动作
伸向3号箱中的锁紧垫圈 从3号箱中选出并握取一个锁紧垫圈 带锁紧垫圈到桌子的中心部位 定好锁紧垫圈装上螺栓的位置并装配在螺栓上
上锯。
❖ 问:有无其它更合适的时间锯? ❖ 答:似可在最初于铁架处取管子时锯,或事先锯好最常用的各种尺
寸的管子。
精选PPT
15
6.五五法案例(4)
❖ 问:由谁做?(由什么人来锯)(Who)
❖ 答:由发料员锯。
❖ 问:为何要发料员锯?
❖ 答:仓库没有其他人。
❖ 问:有无其他更合适的人锯?
❖ 答:如果由具有锯切经验的专人来锯可能更好。
改善后换模流程
加工 找新模板
完工处理
卸模板
清理机台
完工处理
加工
装刀具
寻边
装模板
在上一个工件加工完成之前把新的待加工模板找好﹐清理机台后直接装新模板﹐ 可缩短换模作业时间。
IE教材操作分析和动作分析

•空闲时间 •工作时间 •整个周期 •利用率
•抬起钻头,取出铸件放在一边, 清除钻模的铁屑,时间0.75
•2.5 •1.25
•3.75
•1.25/3.75=33%
•空闲 •1.25 •2.5
•2.5/3.75=67%
PPT文档演模板
IE教材操作分析和动作分析
人机操作图 实例分析
PPT文档演模板
项目
的质量和产量
操作分析的类型: 根据不同的调查目的,操作分析可分为:
1.人机操作分析(含闲余能量分析) 2.联合操作分析 3.双手操作分析
PPT文档演模板
IE教材操作分析和动作分析
•IE七大手法之三
•人机法
•1.理论知识 •2.实际案例 •3.实践练习
• 1.手法名称:
•
人机配合法(Man-Machine Chart);简称为“人机法”.
周程时间(min)
利用率
人
机
•人 •移开铣成件
•用压缩空气清洁机器, 装铸 •件, 开动机器精铣
•锉锐边, 用压缩空气清洁
•在面板上用模板量深度, 成品 •放入箱内, 取新铸件置机旁
•空闲
•时间(min)
•0.2 •0.4 •0.6 •0.8 •1.0 •1.2 •1.4
现行方法 1.2 0.8 0.8 1.2 2.0 60% 40%
•
在机器的工作过程中, 调查、了解在操作周期内机器操作与工人操作
的相互关系, 以充分利用机器与工人的能量及平衡操作。
•
(加工完一个零件的整个过程称为一个操作周期或周程)
• 2.目的:
•
学习如何记录人与机器配合工作时之过程.
• 1>. 发掘空闲与等待时间
IE七大手法改善案例

五. 防錯法 案例3:SMT空焊降低改善1/3
改善前 1.1 新機種Raptor量產初期,SMT BSide目檢工站發現SD Conn空焊(浮高)與掉件不良,達0.78%,占總不良比重:22%, 居不良首位.
五. 防錯法 案例3:SMT空焊降低改善2/3
改善后 在BSide Reflow前增加一個夾具(如圖),能彈性的支撑SD
改善前
改善后
設計制作測試自動拔插治具,減少誤操作,減少劃傷
五. 防錯法 案例2:SMT上料防混料改善1/3
上料防混料---防錯料台車支架的使用
改善前
改善後
HITACHI台車
軌道 號條
碼
自製防錯料 台車支架
物料
料帶易重疊交叉,且不易發現 掃描軌道號太遠,不易判斷對應軌道
以上缺陷使上料員不能及時發現
上料
2
2
5 爐前目檢
1
1
6
AOI
1
1
7 爐后比對
1
1
8 爐后目檢
2
1
合計
10人 8人
精簡 1
1 2
B side
改善前 改善后
NO 工站
人數
1
線長
1
1
2 全技員
1
0
3
印刷
1
1
4
上料
2
2
5 爐前目檢 1
1
6
AOI
1
1
7 爐后比對 1
1
8 爐后目檢 3
1
合計
11人 9人
精簡 1
2 2
五. 防錯法 案例1:L10測試治具改善1/1
Conn,防止焊點重熔時受重力等影響產生不良.
IE与动作分析详解

业 25
时 间
20
改善后
作
业
时 间
20
1234567
123456
生产线平衡观点
41
时间分析实例:
1、前轴总成装配线20道、30道时间差异较 大,其中20道需时比30道多约20秒; 怎样才能达到工序平衡?
42
1.对20道 30道的 工序内容 作相应调 整:
将打码动 作划入下 一工序
使工序间 能力更趋 平衡。
• 必需決定作業者一周期所推出的製品單位大小。分析 之際,一旦忽略了這一點,就無法獲知每一單位的所 需時間,亦無法與其他工程展開比較。
• 接下來在一般的平面流動圖,記入作業者的動作。
50
平面流程图(改善前)
穿衣間 ○○
盥廁 洗所 室3 ○○
5 2
4
書房
○ 76 1
○ 食堂
○
○ 寢室
前門
1、从寝室到更衣间;2、从更衣间到厕所;3、从厕所到卫生 间;4、从卫生间去厨房;5、从厨房去更衣间;6、从更衣间 到书房;7、从书房到大门。
43
2、前轴总成装配油制动器调整制动间隙涨 紧时,需拨40齿左右,少数大于40齿,导 致此道工序比上道工序多耗时约10秒,成 为生产瓶颈。 此工序内容已无法分解,怎么办?
44
2.联系 厂家对 油制动 间隙进 行预调, 使该道 工序调 整时间 减少 30%!!
45
3、快速换模
此台加工中心加工M1和M10两种前轮毂,经常需要切换
配置。为高效率地进行生产、需高效系统的布置
必须的机械设备、综合配列原材料、零件仓库、
检验场所、货物的出入口等,以达到人和物流顺
畅的目的。搬运管理良好与否,对生产效率和生
IE实践基础课程(动作分析5)

第2步:分析现在的方法
1.有效利用IE的分析手法 2.用动作分析表对现在的作业方法进行分
析. 3.为了正确把握事实真相,要符合5W1H的
原则.
第3步:获取改善的方案
1.发挥丰富的创造力. 2.要运用动作经济原则和所有改善原则. 3.听取他人意见.
第4步:作出具体方案并提交
2.分析现在的方法
要素作业名:仔细观察作业,把其粗略分割 成若干个要素作业,在要素作业名栏内填 写作业的发生顺序.
时间测定:要素作业的时间一般要使用秒 表进行测试.至少要测试5次,取其平均值.
3.从要素作业中获得想法
此要素可以省略吗?可以改善想法.
1.检讨想法的实现性,经济性,有效性. 2.把可能实现的想法具体化,订立改
善具体方案. 3.预测新方法的效果. 4.决定改善方案. 5.准备把新改善方法进行提交.
第5步:实施新方案
1.针对新方法实施必要的训练. 2.实施新方法并确认其结果. 3.改订作业标准并进行跟踪. 4.寻找更好的方案.
第1步:发现改善的重点
1.如何改善和明确改善的目的.
2.改善的第一步要对现在的工作抱怀疑态 度.如果认为目前的工作方法是最理想的, 那么便会认为没有改善的必要.
3.要充分了解现在的作业方法,材料,设备, 治工具,作业区域配置.品质等各项目.从中 选取效果最明显的改善项目,即发现改善 重点.
4.动作分析的展开
这是用要素作业单位对想法进行检讨的 阶段.可以省略的要素作业不用分析.主要 针对不可以省略的要素作业进行再深层 的分析,浮现目前未出现的改善想法. (动作分析的真正意义)
5.动作分析的实施
使用动作分析表,对不可以省略的要素作 业进行分析.
IE工程动作分析之MOD法在装配流水线平衡中的应用

MOD法在装配流水线平衡中的应用在日益激烈的巿场竞争下,每个汽车及零部件制造企业都致力于生产效率的不断提高。
如何优化流水线的生产能力,是我们工业工程人员研究的主要课题,而流水线的平衡便是达到这一目标的方法之一。
本文结合公司生产实际,应用IE(工业工程)工具——MOD法,对公司装配流水线的平衡问题进行了改进。
平衡流水线的工作流程1、系统的瓶颈一条流水线的生产能力取决于其生产能力最薄弱的环节,这个环节我们称之为瓶颈。
平衡流水线的目的就是通过提高瓶颈环节的生产能力来优化整条流水线的生产能力,从而降低成本,提高利润。
2、寻找瓶颈环节主要采用时间测定中的秒表法来寻找瓶颈环节。
通过使用秒表对各工序环节多次计时,剔除异常值,求得算术平均值。
将每个环节的时间与生产能力要求相比较,达不到要求的即是瓶颈环节,也便是改进点。
对瓶颈环节进行分析改进,主要采用了MOD法(模特法)。
图1 工作流程图3、MOD法MOD法是预订时间标准(PTS)法的一种,它不是通过直接观察和测定,而是利用预先为各种动作制定的标准时间来确定操作所需时间。
传统的PTS法的优点在于不受作业熟练度和评比者主观性的影响,相对客观公正,但是也较耗时。
MOD法则更为简练、易于掌握,适合实际生产操作。
基于人体工程学实验总结出来的MOD法其基本原理如下:(1)通过大量的试验研究,MOD法将生产实际中操作的动作归纳为21种。
(2)相同条件下,不同的人做同一动作所需时间值基本相等。
(3)使用身体不同部位动作时,其动作所用的时间值互成比例(如:手的动作是手指动作的2倍,小臂的动作是手指动作的3倍等)。
因此,根据手指一次动作时间单位的量值,可直接计算其他身体部位动作的时间值。
MOD法时间单位的设定,根据人的动作级次来确定。
以一个正常人的级次最低、速度最快、能量消耗最少的一次手指动作的时间消耗值,作为时间单位,即1 MOD=0.129 s。
同时,还可在运用中根据企业的实际情况,决定MOD的单位时间值大小。
IE工业工程方法技术之动作分析改善实例
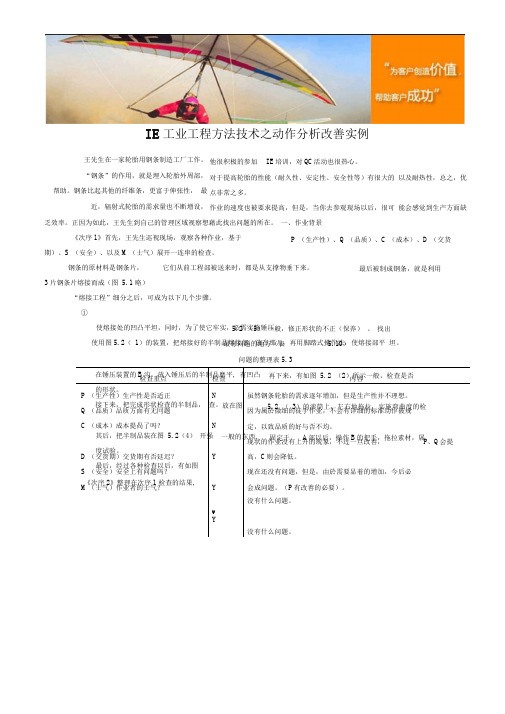
IE 工业工程方法技术之动作分析改善实例他很积极的参加 IE 培训,对QC 活动也很热心。
对于提高轮胎的性能(耐久性、安定性、安全性等)有很大的 以及耐热性,总之,优点非常之多。
作业的速度也被要求提高,但是,当你去参观现场以后,很可 能会感觉到生产方面缺乏效率。
正因为如此,王先生到自己的管理区域视察想藉此找出问题的所在。
一、作业背景《次序1》首先,王先生巡视现场,观察各种作业,基于期)、S (安全)、以及M (士气)展开一连串的检查。
钢条的原材料是钢条片,它们从前工程部被送来时,都是从支撑物垂下来。
3片钢条片熔接而成(图 5.1略)“熔接工程”细分之后,可成为以下几个步骤。
①检查重点 检查内容P (生产性)生产性是否适正 N 虽然钢条轮胎的需求逐年增加,但是生产性并不理想。
Q (品质)品质方面有无冋题因为属於微细的徒手作业,不会有详细的标准动作被规C (成本)成本提咼了吗?N定,以致品质的好与否不均。
现状的作业没有上升的现象,不过一旦改善, P 、Q 会提D (交货期)交货期有否廷迟?Y高,C 则会降低。
S (安全)安全上有问题吗?现在还没有问题,但是,由於需要显着的增加,今后必M (士气)作业者的士气?Y会成问题。
(P 有改善的必要)。
V没有什么问题。
Y没有什么问题。
5.2 (5) 一般,修正形状的不正(保养) 。
找出最有问题的地方(表 5.10)问题的整理表5.3王先生在一家轮胎用钢条制造工厂工作。
“钢条”的作用,就是埋入轮胎外周部, 帮助。
钢条比起其他的纤维条,更富于伸张性, 最近,辐射式轮胎的需求量也不断增设, 使熔接处的凹凸平坦,同时,为了使它牢实,必需实施锤压。
使用图5.2( 1)的装置,把熔接好的半制品熔接部,放在那儿,再用脚踏式操作法,使熔接部平 坦。
在锤压装置的B 沟,放入锤压后的半制品磨平, 有凹凸的形状。
接下来,把完成形状检查的半制品, 查。
再下来,有如图 5.2 (2)所示一般,检查是否 放在图 5.2 ( 3)的滚筒上,左右地拖拉,实施弯曲度的检 P (生产性)、Q (品质)、C (成本)、D (交货最后被制成钢条,就是利用其后,把半制品装在图 5.2(4) 开强度试验。
IE流程分析改善案例

√
浪费动作-若"4"改进可 取消
√
半成品测试与装配 人员同线
3
产品交接
3 ○→
▽□◇√
√
浪费动作-若"4"改进可 取消
√
半成品测试与装配 人员同线
4
半成品测试
4 ○→
▽□◇√√
距离太远-跟装配人员同 线
√
半成品测试与装配 人员同线
5 不良品搬运到维修组 25
3 ○→
▽□◇√
√
浪费动作-若"7"改进可 取消
9
产品交接
3 ○→
▽□◇√
√
浪费动作-若"7"改进可 取消
√
半成品维修与测试 人员同线
工作站 成品组装
作业名称
10
维修品测试
11 合格品搬运到装配组 15
12
产品交接
13
组装2
以下从略
成品组装与测试
产品型号 产品名称
4 ○→
▽□◇
2 ○→
▽□◇√
3 ○→
▽□◇√
4 ○→
▽□◇
工作地点 文件页码
第2页 共3页 文件编号 制作日期
半成品维修与测试 人员同线
6
产品交接
3 ○→
▽□◇√
√
浪费动作-若"7"改进可 取消
半成品维修与测试 人员同线
7
不良半成品维修
8 ○→
▽□◇√√
距离太远-跟测试人员同 线
半成品维修与测试 人员同线
8 维修品搬运到测试组 25
3 ○→
▽□◇√
√
浪费动作-若"7"改进可 取消
- 1、下载文档前请自行甄别文档内容的完整性,平台不提供额外的编辑、内容补充、找答案等附加服务。
- 2、"仅部分预览"的文档,不可在线预览部分如存在完整性等问题,可反馈申请退款(可完整预览的文档不适用该条件!)。
- 3、如文档侵犯您的权益,请联系客服反馈,我们会尽快为您处理(人工客服工作时间:9:00-18:30)。
3000
created by (创建):
张东海
工序级别: STCH(针数/cm): machine time 设备时间(TMU): manual time(TMU) 手工时间(TMU): Total time 合计时间 total +allowance: 1.3053 2372 4.5 MST : 2.5000 HSF : Std time: 标准时间: Std time: 标准时间:
SEAM DIAGRAM AND PART DRAWING(拼缝部件图)
CODE (代码)
GP1H MAP1 GPAG AJPT FOOT MBTB TCUT GPAG AJPT FOOT MBTB TCUT
Get part with 1 hand
DESCRIPTION(描述) 单手取裁片 单手取附件配对 调整抓的动作 将裁片移至压脚位 手动开始回针
TIMES M/C TMU 1 20 1 1 1 1 1 1 11 11 11 11 11 56 10 43 38 34 50 110 473 418 374 550 0 0 0 0 0 0 0 0 0 0 0 0 0 0 2176
MA TMU 0 0 0 0 0 0 0 0 0 0 0 0 0 0 0 0 0 0 0 0 0 0 0 0 0 0 0
GSD工序动作分析表
operation code(工序代号):64 operation title(工序名称): 定裤耳上下*6,穿装饰金属标。 operation Type(操作类型): Sew 车间
Operation Description(工序描述): Machine(机器):
SN
R.P.M(转速):
剪线:剪刀剪(第一次) 调整抓的动作 将裁片移至压脚位 手动开始回针
将单块裁片对准或调整位置
Match parts to FOOT(without obtain) Machine backTack at beginning(lever) Trim-cut with scissors(1st)
剪线:剪刀剪(第一次)
Match & add part with 1 hand Get part by adjusting grasp Adjust 1 part(top)
将单块裁片对准或调整位置
Match parts to FOOT(without obtain) Machine backTack at beginning(lever) Trim-cut with scissors(1st) Get part by adjusting grasp Adjust 1 part(top)Biblioteka Amended by(修改):
1.0400 ROF : 667 Smv bandle 绑扎时间: Smv bandle 绑扎件数: 1
0
Allowance: 宽放: 12.5% Allowance: 宽放: 9.0%
0
0%
0
2176
2372
100%
15
Total Smv/unit :
1.4228 WORKPLACE LAYOUT(工作场所图片)