分段造船工艺
现代造船用分段法

,现代造船用分段法,即把船体按场地条件,分成若干个模块,先造好模块然后移到船台上合拢,以下都假定是按分段造船处理大流程:钢材下料是第一个环节(一般造船合约付定金后的第一个付款阶段)进行小组装:把加工好的单独的钢材部件装配成大部件,主要是强化平板分段组装:把大部件和切割好的及加工成型的钢材并装成分段模块,这是船体模组开始成形,一般从底部开始造,船的艏艉比较复杂,也会先开工分段焊接的同时也进行预舾装,一些跟结构有紧密关系的部件会先安装在分段里,主要是各种管子,通海阀组,部分楼梯,大型基座等,因为分段合并后不好施工分段装焊完成通过报验后进行涂装,主要是密闭舱室的内部油漆,如双层底,边舱等,需要打沙除锈,在分段时做效率高效果好造好若干个分段后开始上船台,这个英文叫 keel laying 是传统放龙骨的意思,现代造船没有真正放龙骨的概念,所以最初一批分段放到船台上定位就等于是放龙骨。
这是很重要的环节,一般船舱收取第二期的付款在船台上进行分段合拢,即把独立的分段模组结合起来,其中包括准确定位,割除结构余量,合龙缝施焊。
如此车间继续生产分段,陆续移到船台上合拢,船体开始成形主机是最大的机器,和其他比较大型的设备一样,在机舱部份的分段完全合拢前会先会先放到机舱底分段上,因为需要大型吊机吊装,所以同时定位摆放在基座上船艉部分装配完成后,进行艉轴镗孔,加工出与主机轴准确对中的轴套。
这工序要求很高的精准度,不能出现结构变形,所以一般在晚上进行,因为不平均的日照会令船体缘中轴线弯曲。
而且镗孔后不能够再有大型焊接施工,因为烧焊会引致钢结构变形,所以一般会等到船体差不多完成时才做。
当船体完全合拢后,基本上形成完整水密结构,船体就会下水。
有几个理由船要在没有造完前就下水:1.船台的承重力有限,不能承担整条造好的船的重量,特别是对从斜轨道滑下水的船台.2.如果船是滑下水的,船体进水时产生的应力限制了最大下水重量3.即便船台有足够能力,又比如在干船坞里造船,基本上下水重量没有限制,但船台是重要的生产资产,其利用率直接影响船厂的营利,所以当在建船只一旦能自浮便得马上腾空船台造另外一条船,尽量利用生产资源下水前会做第一度船底外板涂装船体下水时第三个付款点,船体结构大致完成船体下水后移舶到舾装码头,进行内部装配包括所有的机械设备,管路连接,电工装配,舱室内装等工程,就好像毛房装修一样,同时甲板机械也进行安装。
船舶分段建造
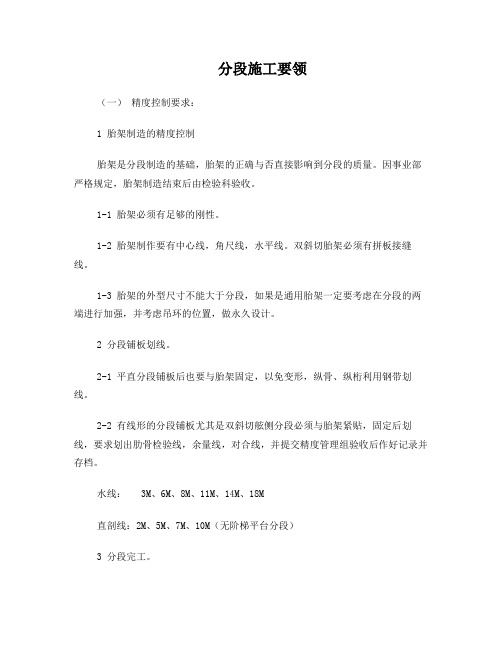
分段施工要领(一)精度控制要求:1 胎架制造的精度控制胎架是分段制造的基础,胎架的正确与否直接影响到分段的质量。
因事业部严格规定,胎架制造结束后由检验科验收。
1-1 胎架必须有足够的刚性。
1-2 胎架制作要有中心线,角尺线,水平线。
双斜切胎架必须有拼板接缝线。
1-3 胎架的外型尺寸不能大于分段,如果是通用胎架一定要考虑在分段的两端进行加强,并考虑吊环的位置,做永久设计。
2 分段铺板划线。
2-1 平直分段铺板后也要与胎架固定,以免变形,纵骨、纵桁利用钢带划线。
2-2 有线形的分段铺板尤其是双斜切舷侧分段必须与胎架紧贴,固定后划线,要求划出肋骨检验线,余量线,对合线,并提交精度管理组验收后作好记录并存档。
水线: 3M、6M、8M、11M、14M、18M直剖线:2M、5M、7M、10M(无阶梯平台分段)3 分段完工。
3-1 分段完工后必须按图纸要求划出肋骨检验线,水线,中心线,直剖线以及分段对合线。
3-2 精度管理组在完工测量时必须认真检查分段的外形尺寸(以立体图作为测量草图)、焊接变形数据,型值必须控制在允许误差范围内,超差一律返工修正,不给后道工序造成隐患,并将数据存档,必要情况下应传达给船台或船坞。
3-3 检验工具必须经常校对,修正。
3-4 严格执行自由边火工工艺。
4 分段制造过程中焊接变形控制。
分段制造过程中的焊接变形一般可以分为两个过程。
4-1 在胎架上的变形,分段在胎架上制造时,由于构件间的焊接而产生变形。
此时,由于受胎架的刚性强制固定而显得不很突出,一旦脱离胎架,处于自由状态时就发现了明显的变形。
这种变形是很难控制的。
它是受装配构件时自强与强制情况及间隙大小而影响。
但是,这种变形是局部的,不是大面积的。
4-2 分段在胎架上随制造进度而产生变形。
例如,带有转圆的底部分段,(反造)在转圆外板焊接时就产生变形,这种变形是大面积的,而且造成的影响较大,在胎架制造时加放变形是防范措施之一。
4-3 分段脱离胎架后的焊接变形。
船体分段装配工艺
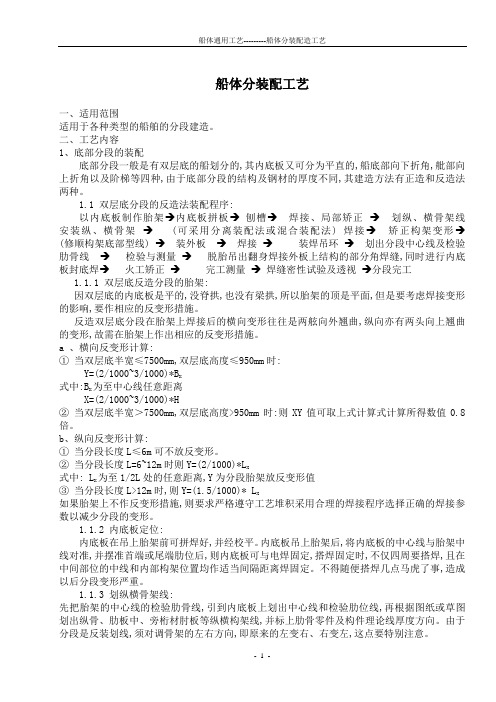
船体分装配工艺一、适用范围适用于各种类型的船舶的分段建造。
二、工艺内容1、底部分段的装配底部分段一般是有双层底的船划分的,其内底板又可分为平直的,船底部向下折角,舭部向上折角以及阶梯等四种,由于底部分段的结构及钢材的厚度不同,其建造方法有正造和反造法两种。
1.1 双层底分段的反造法装配程序:以内底板制作胎架→内底板拼板→刨槽→焊接、局部矫正→划纵、横骨架线安装纵、横骨架→ (可采用分离装配法或混合装配法) 焊接→矫正构架变形→(修顺构架底部型线) →装外板→焊接→装焊吊环→划出分段中心线及检验肋骨线→检验与测量→脱胎吊出翻身焊接外板上结构的部分角焊缝,同时进行内底板封底焊→火工矫正→完工测量→焊缝密性试验及透视→分段完工1.1.1 双层底反造分段的胎架:因双层底的内底板是平的,没脊拱,也没有梁拱,所以胎架的顶是平面,但是要考虑焊接变形的影响,要作相应的反变形措施。
反造双层底分段在胎架上焊接后的横向变形往往是两舷向外翘曲,纵向亦有两头向上翘曲的变形,故需在胎架上作出相应的反变形措施。
a 、横向反变形计算:①当双层底半宽≤7500mm,双层底高度≤950mm时:Y=(2/1000~3/1000)*BX为至中心线任意距离式中:BXX=(2/1000~3/1000)*H②当双层底半宽>7500mm,双层底高度>950mm时:则XY值可取上式计算式计算所得数值0.8倍。
b、纵向反变形计算:①当分段长度L≤6m可不放反变形。
②当分段长度L=6~12m时则Y=(2/1000)*LX式中: L为至1/2L处的任意距离,Y为分段胎架放反变形值X③当分段长度L>12m时,则Y=(1.5/1000)* LX如果胎架上不作反变形措施,则要求严格遵守工艺堆积采用合理的焊接程序选择正确的焊接参数以减少分段的变形。
1.1.2 内底板定位:内底板在吊上胎架前可拼焊好,并经校平。
内底板吊上胎架后,将内底板的中心线与胎架中线对准,并摆准首端或尾端肋位后,则内底板可与电焊固定,搭焊固定时,不仅四周要搭焊,且在中间部位的中线和内部构架位置均作适当间隔距离焊固定。
船舶分段生产工艺
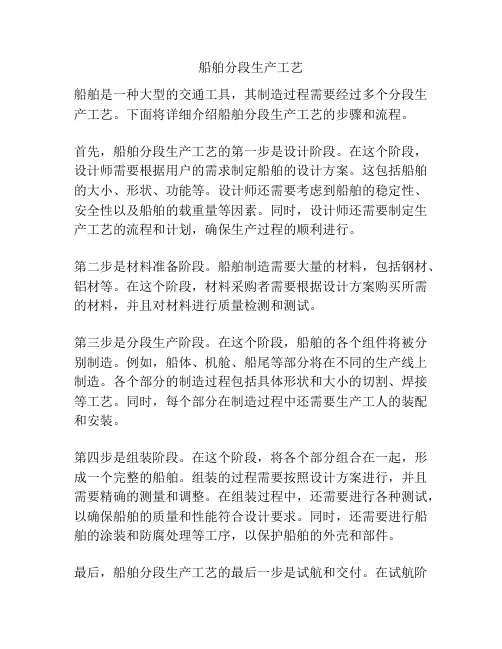
船舶分段生产工艺船舶是一种大型的交通工具,其制造过程需要经过多个分段生产工艺。
下面将详细介绍船舶分段生产工艺的步骤和流程。
首先,船舶分段生产工艺的第一步是设计阶段。
在这个阶段,设计师需要根据用户的需求制定船舶的设计方案。
这包括船舶的大小、形状、功能等。
设计师还需要考虑到船舶的稳定性、安全性以及船舶的载重量等因素。
同时,设计师还需要制定生产工艺的流程和计划,确保生产过程的顺利进行。
第二步是材料准备阶段。
船舶制造需要大量的材料,包括钢材、铝材等。
在这个阶段,材料采购者需要根据设计方案购买所需的材料,并且对材料进行质量检测和测试。
第三步是分段生产阶段。
在这个阶段,船舶的各个组件将被分别制造。
例如,船体、机舱、船尾等部分将在不同的生产线上制造。
各个部分的制造过程包括具体形状和大小的切割、焊接等工艺。
同时,每个部分在制造过程中还需要生产工人的装配和安装。
第四步是组装阶段。
在这个阶段,将各个部分组合在一起,形成一个完整的船舶。
组装的过程需要按照设计方案进行,并且需要精确的测量和调整。
在组装过程中,还需要进行各种测试,以确保船舶的质量和性能符合设计要求。
同时,还需要进行船舶的涂装和防腐处理等工序,以保护船舶的外壳和部件。
最后,船舶分段生产工艺的最后一步是试航和交付。
在试航阶段,船舶将进行各种测试和调整,以确保船舶的稳定性和性能。
一旦测试通过,船舶将交付给用户,准备投入使用。
总而言之,船舶分段生产工艺是一个复杂而精细的过程,需要多个环节的配合和协调。
从设计、材料准备、分段生产、组装到试航和交付,每个阶段都需要严格按照工艺流程进行。
只有这样,才能保证船舶的质量和性能符合设计要求。
船舶分段制作及焊接工艺

船舶分段制作及焊接工艺1目的本工艺阐述了分段建造程序、分段精度的控制方法以及分段焊接工艺,旨在保证船舶分段质量满足船东及船级社的要求。
2适用范围适用于本公司船舶分段建造及焊接全过程。
3职责3.1技术部负责提供分段施工图、施工要领、建造规范、负责分段建造细则工艺的编制,并及时对图纸上存在的错误、遗漏等问题进行修正。
焊接规格表和焊接原则工艺等有关资料。
3.2公司结构部负责分段建造详细计划的编制,负责总体生产计划的下达。
3.3生产管理部负责分段作业计划的安排、产品质量的控制以及生产过程中的调度和协调。
3.4结构部管理人员同时负责对施工人员提出技术要求,并现场进行指导。
3.5安环部负责对生产过程中的安全进行监控。
3.6质量部负责对分段制造过程中的精度、制造质量进行检查控制;负责对新材料(包括进口钢材)牵头进行工艺评定,对船体结构焊接质量进行控制和检验。
3.7船厂各相关部门负责做好本工序的自检、互检工作,确保焊接质量。
4分段制作工艺4.1结构部在产品开工之前应先组织施工人员进行分段建造规范及有关节点图册的学习。
4.2施工人员在接收到分段图纸后应先熟悉图纸,掌握施工要领以及施工工艺,以确保在施工过程中对图纸不存在模糊感觉。
4.3结构部根据分段作业计划要求于分段开工前填写送料申请单交内业,结构部材料接收人在内业送料结束核对齐全后,在送料通知单存根联上签字,交内业留存备查。
4.4部件预制4.4.1施工过程中应按照图纸核对零件号安装,并且检查此代号是否符合图纸上规定的尺寸要求。
4.4.2施工过程中应检查零部件的材质是否符合图纸要求。
4.4.3施工过程中要按照装配节点图册及焊接规格表进行施工。
4.4.4板列预装及“T”型材预装a、板列预装前应先检查零件上的数控粉线是否准确或重新划出结构安装线,标出理论线位置及折边方向,然后再安装其上面的结构。
b、“T”型直梁采用倒装法,要先在面板上划出腹板安装线再安装腹板,“T”型弯梁采用侧装法安装,装配完工后在腹板上划出辅助检验线,以检验“T”型材经焊接后的型线是否准确,并作为火工矫正线型的依据。
船舶分段制造方法

船舶分段制造方法
船舶分段制造方法是指将一艘船舶按照设计图纸分成若干个部
分进行制造的方法。
这种方法可以提高船舶制造工艺的效率和质量,降低制造成本,同时也方便了船舶的维护和维修。
船舶分段制造一般分为以下几个步骤:
1. 设计分段方案:根据船舶设计图纸,确定船舶分段的位置、数量和大小,制定分段方案。
2. 制作模板:按照设计图纸制作模板,用于制作船舶分段的模型。
3. 切割分段:根据模板进行切割,将船舶分段进行切割和加工,制作成符合要求的零件。
4. 焊接分段:根据设计要求,将分段进行钢结构焊接,形成船舶分段的零件。
5. 组装分段:将焊接好的分段进行组装,形成完整的船舶结构。
6. 检验和验收:对船舶分段进行质量检验和验收,确保船舶分段的质量符合要求。
船舶分段制造方法可以有效提高船舶制造工艺的效率和质量,降低制造成本,也方便了船舶的维护和维修。
因此,船舶制造企业普遍采用船舶分段制造技术,以提高船舶制造的效率和质量。
- 1 -。
大型船舶艉柱分段制作工艺

大型船舶艉柱分段制作工艺艉柱分段主要由轴毂、尾管和前轴承座三部分组合而成。
在现阶段大型船舶建造过程中始终存在着轴毂、尾管和前轴承座安装精度难以控制,焊接质量无法保证的问题,使得分段返工量大,制作周期较长。
随着造船行业对坞期不断缩短,分段制作的精度和质量更加显得重要。
不断优化、改进分段制作工艺,从分段制作的各个环节控制精度和质量势在必行。
2分段制作基面及流程分段以左侧为制作基面,在模板胎架上侧造,制作流程如下:胎架制作及地面划线f轴毂部件上胎定位f安装散件―吊装尾管部件f吊装前轴承座部件f首尾端面划“十字”标记线f拉线测量、标记、调整f结构装配f结构焊接。
3分段胎架制作工艺制作胎架是分段制作的第一步,一个良好的胎架不仅可以保证分段的顺利建造,而且在降低劳动强度、改善施工环境、控制分段精度和质量方面起到重要的作用。
本分段胎架采用专用模板胎架形式,选用槽钢和数控切割模板制作。
胎架制作前在平整的地面上划出胎架中心线、胎架模板安装地样线,并做好标记;制作时在每道模板安装地样线处设置一档槽钢支柱,支柱间用角钢连接加强固定;胎架支柱完工后根据数控模板上的水平线、中垂线及模板安装地样线定位安装胎架模板(各检验线偏差W 2mm,并做适当的加强固定,形成一个整体的模板胎架;同时在首尾两端立标杆(垂直度偏差W 20mm,并开拉线孔;最后对胎架做精度检验,完成胎架制作。
见图1。
4结构装配及精度控制工艺艉柱分段的装配难点是控制轴毂、尾管和前轴承座这三个部件的装配精度,即此三个部件的轴中心线重合和分段总长。
4.1三轴中心线重合工艺(1)三个部件吊装后,在轴毂尾端面和前轴承座首端面以拉粉线测量的方式标记出水平方向和垂直方向的“十字”标记线,检查确认后打好洋冲标记。
见图2。
(2)从轴毂经尾管、前轴承座拉一条钢丝线(见图3),以钢丝线为基准,测量各个部件首尾端面,即A点、B点、C点、D点、E点、F点端面内壁至钢丝线的距离L1、L2、L3、L4 (见图3),使用拉码、千斤顶调整轴毂、尾管和前轴承座的相对位置,使L仁L2=L3=L4 (L1、L2、L3、L4最大相差W 2mm,即可判断轴毂、尾管和前轴承座轴中心线重合,同时与钢丝线重合。
船体分段制作工艺流程

船体分段制作工艺流程船体分段现场制造工艺流程生产范围大组立是船舶制造的一种生产管理模式,是船体分段装配的一个生产阶段。
就是将零件和部件组成分段的生产过程。
人员搭配大组立生产以班为单位,一个班一般分为三到四个班组,一个班组的成员有一个组长、三个师傅、六个徒弟、两个电焊工、一个打磨工。
图纸资料大组立相关图纸有零件明细表、产品完工图、制作工艺、焊接工艺等。
工具割枪、米尺、线垂、千斤顶、水平尺、水平管、花兰螺丝、铁锤、铁楔、角尺、电焊机、自动二氧化碳焊接、打磨机机舱双层底大组立机舱双层底工艺流程胎架或平台准备——铺内底板——构件安装位置划线——构件安装——焊接——管铁舾装安装焊接——外板安装——焊前检查——构件与外板焊接——打磨——密性实验——交验装配作业标准分段长:L <±4mm分段宽: B <±4mm分段高:H <±4mm分段方正度:(内底板四角水平)<±8mm(加测机座内底板水平)货舱双层底大组立工艺流程胎架或平台准备——内底板拼装——自动二氧化碳焊接——构件安装位置划线——内底纵骨安装焊接——构件小组(肋板)安装焊接——舾装——补漆¬外底板拼装——焊接——构件安装位置划线——外底纵骨装焊——组装完成——焊接——打磨——舾装——完工检查——报验装配作业标准分段长:L <±4mm分段宽:B <±4mm分段高:H <±3mm分段方正度:<4mm (内、外底板对角线差值)分段扭曲度:<±8mm (内底板四角水平)纵骨端平面度:<±4mm内、外底板中心线偏差<±3mm内、外底板肋位线偏差<±3mm货舱顶边水舱大组立货舱顶边水舱分段工艺流程胎架或平台准备——斜板拼装——焊接——构件安装位置划线——斜板纵骨安装焊接——构件(肋板)安装焊接——舾装——补漆¬甲板拼装——焊接——纵骨装焊——组装完成——焊接——打磨——舾装——完工检查——报验装配作业标准分段长: L <±4mm分段宽: B <±4mm分段高: H <±4mm分段方正度:(测上甲板)<4mm分段扭曲度:(上甲班)<±8mm纵骨端平面:<±4mm货舱舭部大组立工艺流程胎架或平台准备——斜底板拼装——焊接——构件安装位置划线——斜底纵骨安装焊接——构件小组(肋板)安装焊接——舾装——补漆¬外底板拼装——焊接——构件安装位置划线——外底纵骨装焊——组装完成——焊接——打磨——舾装——完工检查——报验装配作业标准分段长: L <±4mm分段宽: B <±4mm内底高:H1±3mm舭部尖顶高:H2±4mm分段方正度:(测斜板)<4mm分段扭曲度:(测斜板)<±8mm。
造船分段焊接原则工艺
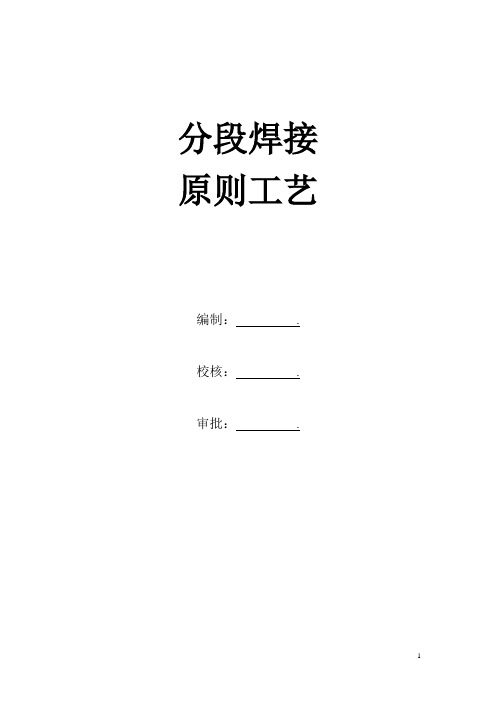
分段焊接原则工艺编制:.校核:.审批:.本原则工艺对船体分段、上层建筑装焊各个环节的质量控制、建造要求等作原则阐述,以确保工程质量满足设计要求。
一. 生产前期准备1.1 生产设计生产前,分段、上层建筑图纸必须经过生产设计细化,配备:制作胎架图、样板表、零件图(板材、型材;并对是否冷加工加以区分)、平面板架图、拼版成型图、曲面板架图、框架图、元件成型图、分段制造工作图、分段总装图、各类套料图、零件清单、材料清单等配备齐全。
1.2 技术交流开工前,车间应与有关设计人员协调,落实解决生产施工中的图纸以及施工中可能预见的各种装焊工艺上的技术问题、质量控制点的控制办法,以保证产品的质量和生产的连续。
1.3 材料准备工程材料清单配备材料,并对材料的材质、数量、平整度等进行核对检查,避免偏差。
二. 制作要领2.1 预处理及制作加工准备2.1.1 钢板在下料切割前,应进行矫平等预加工处理,钢板矫平后不得出现折皱、翘曲等影响质量的现象,表面不应有明显的凸痕和其它损伤,必要时应进行局部整修或打磨、整平。
2.1.2 号料前应清除钢材表面油污、氧化皮等污物,并进行车间底漆预处理(板材预处理方由合同规定)。
2.1.3号料前应检查钢板的牌号、规格、质量,确认无误合格后,方可号料。
2.1.4号料所划的切割线必须正确清晰,号料尺寸偏差满足规范。
2.1.5各类钢结构部件的零件,应采用气割切割,并优先考虑数控切割和自动、半自动气割。
手工气割只能用于次要零件或切割后仍需边缘加工的零件。
2.1.6气割前应将料面上的浮锈及脏物清除干净,钢料应放平、垫稳,割缝下面应留有空隙。
2.1.7气割零件尺寸允许偏差应符合下列规定:2.1.7.1不同厚度板材拼接削斜要求根据船规的要求,不同厚度钢板进行焊接时,其厚度差大于3mm,则应将厚板的边缘削斜,使其均匀过渡(见图)。
如厚度差小于等于3mm,则不削斜。
A:无坡口要求(薄板)d ﹥3mm 时,则L ≧3d ,且Lmin =20mm 图1 无坡口B :有坡口要求.d ﹥3mm 时,则 L ≧3d ,且Lmin =图2 坡口开在板厚差一侧d ﹥3mm 时,则 L ≧3d ,且Lmin =图3 坡口开在板厚差一侧 C: FCB 法接头参见图3d ﹥2mm 时,则L ≧6d ,且Lmin =30mm ,Lmax =Max (3d,45mm )D: 垂直气电焊(CV )对坡口削斜要求:与采用垂直气电焊焊接接头相交的对接接缝,如其拼接接头存在板厚差而削 斜,则应在现场对靠近垂直气电焊对接接缝坡口边缘100mm 范围内区域进行打 磨,使此局部削斜过渡的斜坡满足L ≧5d 。
0106船体分装配造工艺
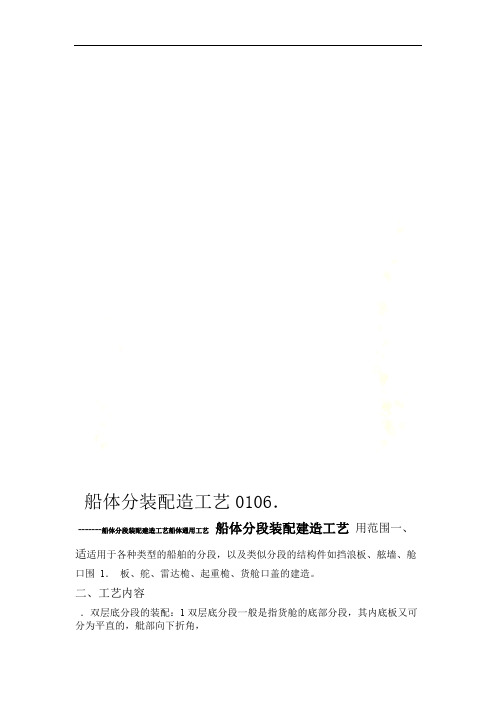
船体分装配造工艺0106.-------船体分段装配建造工艺船体通用工艺船体分段装配建造工艺用范围一、适适用于各种类型的船舶的分段,以及类似分段的结构件如挡浪板、舷墙、舱口围1.板、舵、雷达桅、起重桅、货舱口盖的建造。
二、工艺内容.双层底分段的装配:1双层底分段一般是指货舱的底部分段,其内底板又可分为平直的,舭部向下折角,舭部向上折角,以及阶梯等四种,由于双层底分段的结构形式,通常建造方法有正身建造及反身建造。
1双层底分段的反身建造1. 装配程序:2.以内底板为基准,制作胎架→内底板拼板→刨槽→焊接、局部矫正→划纵、横骨架线→安装纵、横骨架→(可采用分离装配法或混合装配法)→焊接→矫正构架变形→(修顺构架底部型线)→装外板→焊接→装焊吊环→划出分段中心线及检验肋位线→检验与测量→脱胎吊出翻身→焊接外板上结构的部分角焊缝,同时进行内底板封底焊→火工矫正→完工测量→焊缝密性试验及透视→分段完工双层底分段反身建造的胎架:因双层底的内底板是平面,但在制造上建分段胎架则 1.1.1 要考虑甲板梁拱。
通常胎架的基准面是平面或带梁拱,若考虑焊接变形的影响,要作相应的反变形措施:双层底分段反身建造,在胎架上焊接后的横向变形往往是两舷向外翘曲,纵向亦有两头向上翘曲的变形,故需在胎架上作出相应的反变形措施。
a、横向反变形Y计算:①当双层底半宽B≤7500mm,双层底高度H≤950mm时:Y=(2/1000~3/1000)×Bx式中:Bx为至中心线任意距离X=(2/1000~3/1000)×H②当双层底半宽B>7500mm,双层底高度>950mm,则X、Y值可取上式计算所得数值0.8倍。
-- 1 --船体通用工艺-------船体分段装配建造工艺b、纵向反变形计算:6m可不放反变形。
①当分段长度L≤Lx)×时,则Y=(2/100012m ②当分段长度L=6~为分段胎架放反变形值1/2L处的任意距离,YLx 式中:为至Lx(1.5/1000)×时,则③当分段长度L>12mY=把内底的周如果胎架上不作反变形措施,则要求在分段制造中采用加强固定措施,围和中部搭焊牢固。
吨船舶分段制造工艺设计

34000DWT船舶分段的制造工艺The Segmented manufacturing process of a 34000DWTBulk Cargo Carrier摘要在当今世界上,造船业竞争越来越激烈,造船业的发展也越来越迅速。
各种船舶也应运而生,散货船便是其中之一。
散货船是散装货船简称,是专门用来运输不加包扎的货物,如煤炭、矿石、木材、牲畜、谷物等。
因为散货船在运送货物上相对于其他渠道而言有运量大,运费低的优势,所以很多厂商在选择运输方式时,选择了用散货船运输。
这便成了散货船需求量大的原因。
而造船业是一个工程繁琐,劳动力付出大,建造周期长的产业。
如何才能在现有的有限的设备和有限的劳动力的情况下,更好的去适应时代的发展要求?本毕业设计,主要就是从船舶分段的制造工艺方面来介绍船舶制造企业在现阶段,如何做到降本增效,提高产品质量,适应现阶段的发展要求,使之更好的生存下去。
关键词:船舶制造工艺;降本增效;分段;建造周期引言由于经济危机的影响,虽然经济已经慢慢的复苏了,可是航运业仍然处于低谷,没有复苏的起色。
航运业的不景气给造船业带来了巨大的影响。
由于订单量不断减少,部分企业甚至已经接不到订单。
这使船舶制造企业面临了巨大的考验。
而在这时,船东不仅没有放宽对船舶的要求,反而对船舶质量的要求更加苛刻,使得部分小型企业已经面临倒闭的风险。
在此时,船厂想要继续生存下去,只有想方设法提高产品质量,同时还要努力做到降低成本,从而在度过这一艰难时期。
船舶分段在制造过程中,只有严格控制生产工艺,才能在提高质量的同时做到降本增效。
1船舶分段的划分现代船厂建造船舶时大多采用分段制造、船台合拢的方法。
即根据船体结构的情况和船厂生产工艺、起重设备能力等条件,将船体划分为若干分段,分别制造,最后在船台上依次合拢成完整的船体。
一艘大、中型船舶的船体,往往被分成几十个到近百个分段,因此分段制造的工作量在船体建造过程中占有很大的比例。
船体分段制作工艺规范

方圆船舶船体分段制作工艺规范编制:张松华方圆造船有限公司2011年9月28日船体分段制造工艺规范1.目的:为缩短造船周期,提高生产效率,加强产品施工制作过程中的质量自主控制和管理,上道工序为下道工序提供合格、优良的零部件和产品,确保船体分段施工准确无误和管、电、铁舾件在分段制作期间一次完成。
特制订本工艺规范。
2.适用范围:适用于产品的设计、下料、加工及分段制造,总组全过程的质量、精度控制。
3.部门职能:3.1、设计部从设计的角度研究如何缩短分段建造周期及船台合拢周期,为提高分段的建造精度而优化设计图纸。
3.2、项目部船体科负责工艺文件的消化及技术指导,实施过程中的监控和检查,同时对外包施工队、施工小组工艺文件执行,进行教育及监控。
3.3、质检科负责精度控制自零部件加工至分段制造、中组合拢的约束过程的精度检查,记录考核信息反馈,对各重要环节实施现场测控和数据确认,并建立各产品数据库,同时还要对现场制造进行过程跟踪监控。
3.4、建立船体建造精度质量管理与控制组织机构(设立二名专职精度管理员),各部门科长、主管负责对精度、质量管理与精度控制组织机构的领导,并对其工作组织检查。
3.5、各科主管、外包队队长负责按图纸和工艺要求,工艺纪律进行施工对建造精度质量进行自主控制为主原则,同时配合质检科、精控人员进行检测和控制。
4.实施:4.1、精度管理员工作要求4.1.1、根据项目部下发生产任务分布情况,将工作范围从准备下料开始到船舶合拢结束,覆盖于整个施工全过程。
在零部件控制工序,分段建造控制工序,分段总组工序过程。
要在主管支持、领导下,精控人员进行认真制作过程监控工作,要多到现场进行指导。
发现不符合工艺规范、工艺纪律施工情况,要立即进行指正,并且指导他们用什么方法整改为最佳,必要时发出整改意见书。
同时也要求相关施工队中的人员积极配合,及时整改,确保把质量事故隐患消灭在萌芽状态。
使制造的分段成为合格产品后才能流到下道工序。
船体分段吊装工艺探索分析

船体分段吊装工艺探索分析船体分段吊装工艺是指在船舶建造过程中,将船体分为多个段落进行建造,然后通过吊装工艺将这些段落组装在一起,最终完成整艘船舶的建造。
这种工艺方式被广泛应用于大型船舶的建造中,可以提高建造效率、降低成本、减少建造周期,因此对于船舶建造行业具有重要意义。
本文将对船体分段吊装工艺进行探索分析,探讨其有关技术特点、优势和挑战。
一、技术特点1. 多分段建造:与传统的整体建造方式不同,船体分段吊装工艺将船体分为多个段落进行建造。
这样可以使得各个段落的建造工作能够同时进行,提高了建造效率。
2. 模块化设计:吊装工艺需要对船体各个段落进行模块化设计,以适应吊装和组装的需要。
模块化设计可以使得各个段落的尺寸、重量等参数相对统一,方便吊装和组装。
3. 精确计算:吊装工艺需要对吊装过程中的重心、受力、平衡等参数进行精确计算,以确保吊装过程的安全和稳定。
二、优势2. 降低成本:相比传统的整体建造方式,船体分段吊装工艺可以降低建造成本。
可以采用现代化生产设备和工艺,提高生产效率和降低生产成本;可以通过模块化设计和吊装工艺,减少了人力和物力资源的浪费。
3. 灵活性强:船体分段吊装工艺可以使得船舶建造过程更加灵活。
在建造过程中,可以灵活调整各个段落的建造顺序和进度,以适应生产进度的需要。
三、挑战1. 吊装精度要求高:船体分段吊装工艺需要保证吊装过程中的精度和稳定性,否则容易发生意外。
特别是在大型船舶建造中,吊装精度要求更加严格。
2. 吊装设备要求高:船体分段吊装工艺需要使用先进的吊装和运输设备,以适应各个段落的吊装和组装。
这需要投入大量的资金和技术支持。
3. 安全隐患增多:船体分段吊装工艺增加了船舶建造过程中的吊装和组装环节,容易导致安全隐患。
因此需要严格控制各个环节的安全风险。
船体分段吊装工艺在船舶建造行业具有广泛的应用前景。
通过对吊装工艺的探索分析,可以发现其在提高建造效率、降低成本等方面具有明显的优势。
船舶分段建造工艺过程
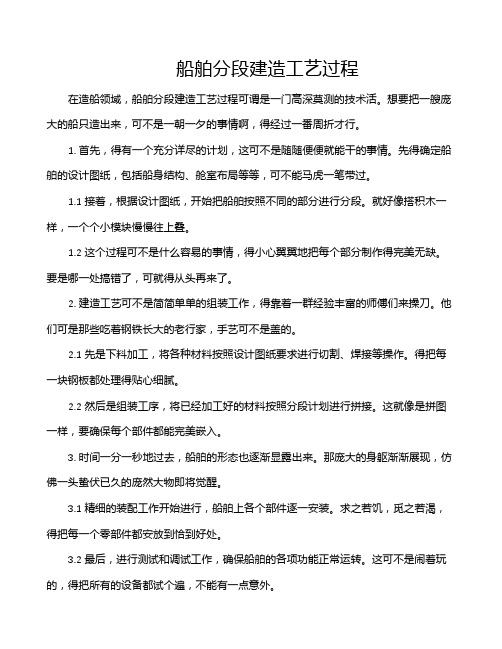
船舶分段建造工艺过程在造船领域,船舶分段建造工艺过程可谓是一门高深莫测的技术活。
想要把一艘庞大的船只造出来,可不是一朝一夕的事情啊,得经过一番周折才行。
1. 首先,得有一个充分详尽的计划,这可不是随随便便就能干的事情。
先得确定船舶的设计图纸,包括船身结构、舱室布局等等,可不能马虎一笔带过。
1.1 接着,根据设计图纸,开始把船舶按照不同的部分进行分段。
就好像搭积木一样,一个个小模块慢慢往上叠。
1.2 这个过程可不是什么容易的事情,得小心翼翼地把每个部分制作得完美无缺。
要是哪一处搞错了,可就得从头再来了。
2. 建造工艺可不是简简单单的组装工作,得靠着一群经验丰富的师傅们来操刀。
他们可是那些吃着钢铁长大的老行家,手艺可不是盖的。
2.1 先是下料加工,将各种材料按照设计图纸要求进行切割、焊接等操作。
得把每一块钢板都处理得贴心细腻。
2.2 然后是组装工序,将已经加工好的材料按照分段计划进行拼接。
这就像是拼图一样,要确保每个部件都能完美嵌入。
3. 时间一分一秒地过去,船舶的形态也逐渐显露出来。
那庞大的身躯渐渐展现,仿佛一头蛰伏已久的庞然大物即将觉醒。
3.1 精细的装配工作开始进行,船舶上各个部件逐一安装。
求之若饥,觅之若渴,得把每一个零部件都安放到恰到好处。
3.2 最后,进行测试和调试工作,确保船舶的各项功能正常运转。
这可不是闹着玩的,得把所有的设备都试个遍,不能有一点意外。
终于,在种种辛苦努力之后,一艘完整的船舶终于呈现在我们面前。
那感觉就像是看到了一个美丽的作品,每一个分段都是师傅们心血的结晶。
船舶分段建造工艺过程,看似繁复,实则工匠之心,化繁为简。
每一个细节都蕴含着匠人的智慧和汗水,每一个部件都承载着他们的梦想和信念。
所以,当我们看到那艘完整的船舶漂浮在大海上,我相信,每一个参与其中的师傅都会由衷地感到骄傲和自豪。
他们用双手打造了一个奇迹,一个让人心驰神往的航行之梦。
愿他们的努力被铭记,愿这艘船舶带着无数的梦想驶向更远的天际。
厦船重工分段建造流程
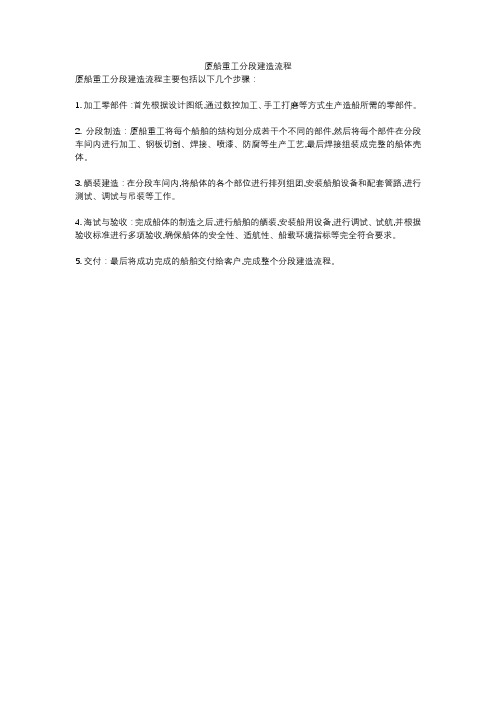
厦船重工分段建造流程
厦船重工分段建造流程主要包括以下几个步骤:
1. 加工零部件:首先根据设计图纸,通过数控加工、手工打磨等方式生产造船所需的零部件。
2. 分段制造:厦船重工将每个船舶的结构划分成若干个不同的部件,然后将每个部件在分段车间内进行加工、钢板切割、焊接、喷漆、防腐等生产工艺,最后焊接组装成完整的船体壳体。
3. 舾装建造:在分段车间内,将船体的各个部位进行排列组团,安装船舶设备和配套管路,进行测试、调试与吊装等工作。
4. 海试与验收:完成船体的制造之后,进行船舶的舾装,安装船用设备,进行调试、试航,并根据验收标准进行多项验收,确保船体的安全性、适航性、船载环境指标等完全符合要求。
5. 交付:最后将成功完成的船舶交付给客户,完成整个分段建造流程。
- 1、下载文档前请自行甄别文档内容的完整性,平台不提供额外的编辑、内容补充、找答案等附加服务。
- 2、"仅部分预览"的文档,不可在线预览部分如存在完整性等问题,可反馈申请退款(可完整预览的文档不适用该条件!)。
- 3、如文档侵犯您的权益,请联系客服反馈,我们会尽快为您处理(人工客服工作时间:9:00-18:30)。
分段造船工艺
船舶建造是一个复杂的过程,其中分段造船工艺是关键步骤之一。
分段造船工艺是指将船体分成若干个独立的模块,然后分别进行制造和装配的工艺流程。
这种工艺使船舶建造更加高效、灵活和可控。
下面将详细介绍分段造船工艺的步骤和特点。
一、分段制造步骤
1. 设计方案确定:在分段造船工艺开始之前,首先需要确定船体的设计方案。
设计方案包括船舶的结构设计、管道系统设计、电气系统设计等。
这些设计方案将作为分段制造的依据。
2. 分段制造计划编制:根据设计方案,制定分段制造计划。
计划包括分段的数量、尺寸、制造工艺和装配顺序等。
分段制造计划的编制需要考虑到船体的结构强度、制造工艺的可行性以及工期的安排等因素。
3. 材料准备:在分段制造之前,需要准备好所需的材料。
这些材料包括钢板、型钢、焊材、涂料等。
材料的选择需要根据设计要求和船舶的使用环境来确定。
4. 分段制造:根据分段制造计划,将船体分成若干个独立的模块进行制造。
制造过程包括钢板切割、型钢加工、焊接、校直和涂装等。
每个模块的制造过程需要严格按照设计要求和工艺规范进行。
5. 分段装配:分段制造完成后,将各个模块进行装配。
装配过程包括模块之间的焊接、螺栓连接、管道安装、设备安装等。
装配的顺序需要根据设计要求和工艺规范来确定,以确保各个模块能够准确无误地连接在一起。
6. 分段试验:在分段装配完成后,需要进行分段试验。
试验内容包括结构强度试验、水密性试验、设备功能试验等。
试验的目的是验证分段制造和装配的质量,以确保船体的安全性和可靠性。
二、分段造船工艺的特点
1. 提高生产效率:分段造船工艺将船体分成若干个模块,不同模块可以同时制造和装配,大大提高了生产效率。
同时,分段制造可以将船体制造的风险和难度分散到各个模块中,降低了制造过程中的错误和损失。
2. 灵活性和可控性强:分段造船工艺使船舶建造过程更加灵活和可控。
每个模块都是独立制造和装配的,可以根据需要进行调整和优化。
同时,分段制造可以根据工期和资源的限制来安排制造计划,确保项目的顺利进行。
3. 质量控制精确:分段造船工艺可以对每个模块进行独立的质量控制。
制造和装配过程中,可以随时检查和修正问题,确保每个模块的质量符合设计要求和工艺规范。
这样可以避免船体整体制造完成
后才发现质量问题,减少修复和改造的成本和风险。
4. 节约成本和资源:分段造船工艺可以充分利用现有的生产设备和人力资源。
每个模块的制造和装配可以在不同的生产线上进行,不会造成生产资源的浪费。
同时,分段造船工艺可以提前制造和装配某些模块,减少了项目周期和资金的压力。
分段造船工艺是船舶建造过程中的重要环节。
通过合理的分段制造和装配,可以提高生产效率、灵活性和质量控制精确度,同时节约成本和资源。
分段造船工艺的应用已经成为现代船舶建造的主流,对于提高船舶建造的效率和质量具有重要意义。