物控管理程序-生产退料作业流程-正文X2
物控工作流程

物控工作流程第一篇:物控工作流程物控工作流程一、接单接到订单后,PMC需进行确认是否为新客户或者是新产品,如果为新客户或者是新产品,需再确认订单的注意事项(包括样品单与量试单),依订单注意事项追踪相关资料,确保订单建立与生产,计划时无异常情况。
二、物料请购物控员接到审核后的订单,首先应核对物料清单,然后进行物料的需求状况分析,计算出物料的用量〔标准用量=标准单位用量×计划生产量×(1+设定标准不良率)〕和材料的请购天数,并且根据库存良品及实物的确认确定物料的请购量及物料的到料时间,做到不断料,不呆料,不囤料。
三、物料异常供应商来料不良进料品管应发来料不合格品处理通知单,物控员根据实际情况作出特采,分选,重工,返修,批退处理,并且及时与采购确认来料的交期。
当处理紧急物料时,物控员应提前一天通知进料品管并要求物料来料时品管需在2H内作出检验结果,物控员跟踪入库及上线直到订单出货。
四、设计变更物料接到变更通知后,物控员需确认是否有订单需求并且立即对库存进查核。
若为报废则立即通知仓管进行全部报废处理。
有正式订单需求的要在第一时间下采购订单,注明为设计变更物料要求采购8H内确认供应商的交期。
若为重工返修之物料,物控员需立即通知生产单位重工返修后入庫。
若为限定使用,物控员需根据限定要求通知仓库作标识进行隔离区分,当库存物料用后之余量不足一张订单则申请报废处理。
若为继续使用,物控员需掌握库存的使用状况,当余量不足一张订单则申请报废处理。
五、紧急物料当订单交期较短时且物料异常较大时物料会存在供应商交期困难,物控员在下PR单时需注明原因,同时要求采购4小时内回复,物控员将最终交期知会相关部门。
若为物控员漏单,则需注明情况并且作紧急物料处理确保订单正常出货。
物控员每周需将紧急物料列出明细,在周例会说明并跟踪异常情况。
六、订单变更接到变更订单的通知后,物控员需立即做交期调整一览表,对需要交期或数量要调整的部分知会采购速通知供应商进行变更。
物控管理流程

物控管理流程第一篇:物控管理流程物控管理流程目的:有效控制各车间收料,领料,退料规范化,确保生产能够顺利进行,提高生产效率,降低库存资金,降低营运费用。
(一)原材料入库流程1仓库管理员收到供应商送货通知单,采购订单,入库单,三单齐全后逐一核实,原材料数量,规格,型号,颜色,包装完整无损,外检验收合格后,办理入库手续。
外检判定不合格直接退回供应商,填报公司不合格产品退货单,外检,采购审核后方可放行,保安室接到物品放行单要核实物品种类是否相符。
(二)原材料出库流程1仓库管理员收到车间原材料领料单必须车间主任或者生产经理审核后备料,并逐一核实生产指令单要求,数量,型号,规格,颜色备料。
(三)外购零部件入库流程1仓库管理员收到供应商送货通知单,采购订单,入库单,三单齐全后逐一核实,生产指令单数量,规格,型号,颜色,包装完整无损,外检验收合格后办理入库手续。
外检判断不合格放入不合格品区等待退货,填报公司不合格产品退货单,外检,采购审核后方可放行,保安室接到物品放行单要核实物品种类是否相符。
(四)外购零部件出库流程1仓库管理员收到车间审核后生产领料单,逐一核实生产指令单数量,型号,规格,颜色提前备料,按照线别放入备料区,等待领料员签收。
(五)自制物料入库流程1仓库管理员收到自制物料入库单,逐一核实指令单数量,名称,颜色,型号,检验员签字后产品合格标识(√),然后办理入库登记及产品归位。
(六)自制物料出库流程1仓库管理员收到车间审核后生产领料单,逐一核实生产指令单数量,型号,规格,颜色提前备料,按照线别放入备料区,等待领料员签收。
(七)生产辅料(办公用品)入库流程1仓库管理员收到供应商送货通知单,零星采购单,入库单,三单齐全后,逐一核实数量,规格,型号,名称,包装完整无损,外检验收合格后办理入库手续。
外检判断不合格放入不合格品区等待退货,填报公司不合格产品退货单,外检,采购审核后方可放行,保安室接到物品放行单要核实物品种类是否相符。
退料流程管理规范

退料流程管理规范一、背景介绍在生产过程中,由于各种原因,可能会出现需要退回供应商的物料情况。
为了规范退料流程,确保退料操作的准确性和及时性,提高退料处理的效率,制定本《退料流程管理规范》。
二、适用范围本规范适用于公司所有部门和员工,包括生产、采购、质量等相关人员。
三、退料流程1. 退料申请1.1 退料申请人填写《退料申请单》,包括退料物料名称、数量、退货原因等信息。
1.2 退料申请单需经主管审核后方可提交给采购部门。
2. 采购部门处理2.1 采购部门收到退料申请单后,核对退料物料的准确性和完整性。
2.2 采购部门根据退料申请单中的信息,与供应商联系并协商退货事宜。
2.3 采购部门将退货协商结果反馈给退料申请人,并通知其进行下一步操作。
3. 退料操作3.1 退料申请人根据采购部门的通知,按照指定的退货方式进行退料操作。
3.2 退料操作包括将退货物料进行包装、标识,并填写退货单据。
3.3 退料申请人将退货物料和退货单据交给仓库管理员进行入库操作。
4. 仓库管理4.1 仓库管理员收到退货物料和退货单据后,核对物料的准确性和完整性。
4.2 仓库管理员将退货物料进行入库操作,并记录入库信息。
4.3 仓库管理员将退货单据归档,并将入库信息反馈给退料申请人。
5. 财务处理5.1 财务部门根据仓库管理员提供的入库信息,进行退货物料的财务处理。
5.2 财务部门将退货物料的相关财务凭证进行登记和记录。
6. 结案审批6.1 退料申请人根据财务部门提供的财务凭证,填写《退料结案审批单》。
6.2 退料结案审批单需经主管审核后方可提交给财务部门。
6.3 财务部门收到退料结案审批单后,核对相关信息,并进行结案审批。
四、责任与义务1. 退料申请人应准确填写退料申请单,并按照规定的流程进行操作。
2. 采购部门应及时处理退料申请,并与供应商协商退货事宜。
3. 仓库管理员应核对退货物料的准确性和完整性,并进行入库操作。
4. 财务部门应根据入库信息进行财务处理,并及时提供相关财务凭证。
生产领退料流程及要求
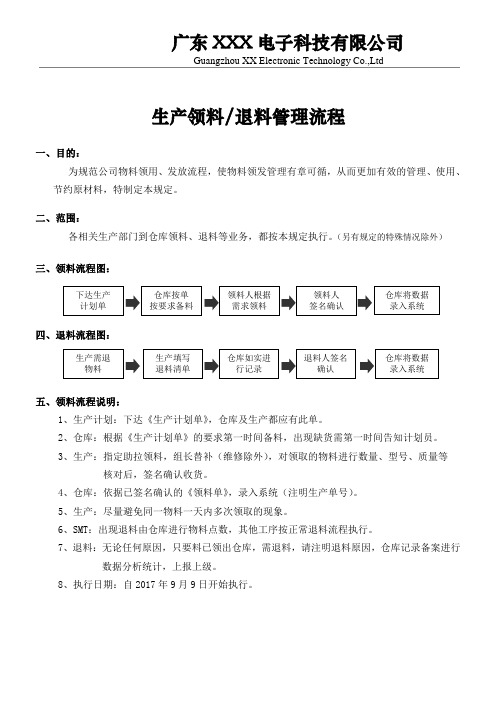
广东XXX 电子科技有限公司
Guangzhou XX Electronic Technology Co.,Ltd
生产领料/退料管理流程
一、目的:
为规范公司物料领用、发放流程,使物料领发管理有章可循,从而更加有效的管理、使用、节约原材料,特制定本规定。
二、范围:
各相关生产部门到仓库领料、退料等业务,都按本规定执行。
(另有规定的特殊情况除外)
三、领料流程图:
四、退料流程图:
五、领料流程说明:
1、生产计划:下达《生产计划单》,仓库及生产都应有此单。
2、仓库:根据《生产计划单》的要求第一时间备料,出现缺货需第一时间告知计划员。
3、生产:指定助拉领料,组长替补(维修除外),对领取的物料进行数量、型号、质量等
核对后,签名确认收货。
4、仓库:依据已签名确认的《领料单》,录入系统(注明生产单号)。
5、生产:尽量避免同一物料一天内多次领取的现象。
6、SMT :出现退料由仓库进行物料点数,其他工序按正常退料流程执行。
7、退料:无论任何原因,只要料已领出仓库,需退料,请注明退料原因,仓库记录备案进行
数据分析统计,上报上级。
8、执行日期:自2017年9月9日开始执行。
退料作业流程(生产退料)

生产
品管
仓库
会计
备注
1.材料退库需求原因:
厂内工单套料领出,制造过程中可能发生制程不良和来料不良或取消订单批量退库等
2.材料退料单输入:
由生产单位于工单管理子系统『录入退料单』按工单批次对应相关料号、数量等信息录入单据
3.打印录入退料单凭证:
由生产单位打印录入退料凭证
4.核准否Y/N:
由生产部主管审查是否核准此退料单(如不核准需重新修正材料录入退料数据或作废此单据)
6.账务处理:
退料完成后由仓库单位于生产管理子系统『录入库存交易单』确认后审核过账
7.退料单凭证存查:
领料单凭证共五联:白联公司留底/红色财务/黄联仓管员/绿联品管/蓝联退料部门
Y
生产退料必须有品质判定,贴上有效标识,仓库接收时严格按照仓库作业标准执行
仓管单位可打印『库存明细表』供材料退库后存量帐的明细查询
5.检验良品或不良品:
此材料录入退料数据应由品管单位审查材料是否为良品或者不良品,贴上相应标识再由生产物料员退库(如果没有品质判定仓库有权拒收)
5-1.良品退库:
此退料单判定为良品退良品仓库,仓管核对确认签收
5-2.不良品退库:
此退料单判定属于来料不良或者制程不良两种
仓管核对确认签收பைடு நூலகம்制程不良后面持续处理
仓库物料管理流程仓库收料、发料、退料、盘点工作流程

仓库物料管理流程一、范围 (1)二、目的 (1)三、管理流程 (1)3.1收料 (1)3.2.发料 (2)3.3.成品 (3)3.4.管理 (3)3.5.退料 (4)3.6仓库单据管理 (4)3.7盘点 (5)3.8仓库对特殊物品的管理 (5)3.9仓库的六防工作 (5)四、最低库存量与安全库存量管理 (5)一、范围适用于全公司全体员工。
二、目的为了使仓库管理更完善规范化,为了能使成本核算更准确,物料能得到更好的控制与管理,特作出此管理流程。
三、管理流程3.1收料供应商送货到仓库,仓管员必须拿供应商的送货单与货物相对照清点是否单物相符。
同时通知验货人员到场第一时间验货,验货及清点完毕后,看对方送货单是否签名齐全后办理进仓手续(开具四联收料单,由检验人员、供应商复合以及仓管员签字为准,开单要求清晰明了)。
办完进仓手续后仓管员将进仓单附于送货单后面送由财务或结现金或月结同时交送一联成本核算。
如图:3.2.发料发料原则“先进先出”;生产车间用料领料按物料清单开具生产单生产所需物料的三联领料单,领料单开具必须注明生产单号。
领料单由所需物料所属组别的组长开具(开单要求清晰明了不得乱涂乱画否则仓管员有权拒发),给车间主管核准一式三联。
拿至仓库,仓管员凭领料单(按先进先出的原则)对照生产单物料清单给予首次发放。
物料发完后仓管员必须在发料人上签字双方确认各自拿回所属联领料单。
发完物料按单入台帐以及分好单据红色联及时上交财务,本程序也适用于打印备料单的领料发料。
如图:3.3.成品生产车间完成成品生产,由包装组组长开具四联成品进仓单,交由质检检验合格后进仓,仓管员清点清楚。
发货由业务发出发货通知单,仓管开具成品出仓单以及经手人签字后装车发货。
最后入台帐。
如图:3.4.管理3.4.1仓库现场管理以5S为标准(整理、整顿、清扫、清除、素养)。
仓库可分为五金仓库(原材料、辅料、以及工具的管理);半成品仓(自造、外购以及外发加工的半成品)。
退料流程管理规范
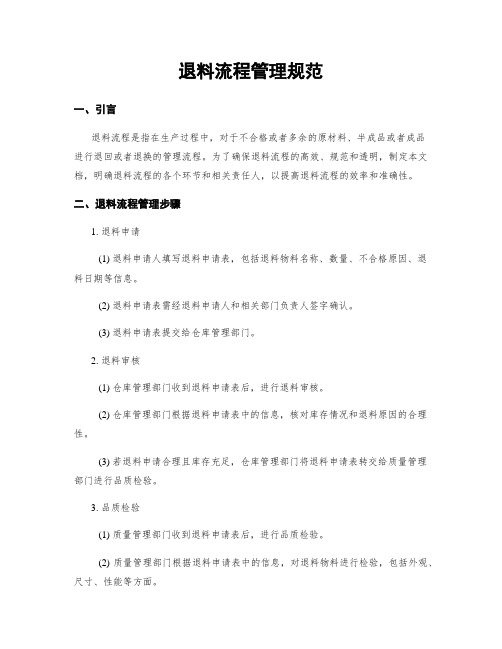
退料流程管理规范一、引言退料流程是指在生产过程中,对于不合格或者多余的原材料、半成品或者成品进行退回或者退换的管理流程。
为了确保退料流程的高效、规范和透明,制定本文档,明确退料流程的各个环节和相关责任人,以提高退料流程的效率和准确性。
二、退料流程管理步骤1. 退料申请(1) 退料申请人填写退料申请表,包括退料物料名称、数量、不合格原因、退料日期等信息。
(2) 退料申请表需经退料申请人和相关部门负责人签字确认。
(3) 退料申请表提交给仓库管理部门。
2. 退料审核(1) 仓库管理部门收到退料申请表后,进行退料审核。
(2) 仓库管理部门根据退料申请表中的信息,核对库存情况和退料原因的合理性。
(3) 若退料申请合理且库存充足,仓库管理部门将退料申请表转交给质量管理部门进行品质检验。
3. 品质检验(1) 质量管理部门收到退料申请表后,进行品质检验。
(2) 质量管理部门根据退料申请表中的信息,对退料物料进行检验,包括外观、尺寸、性能等方面。
(3) 若退料物料符合质量要求,质量管理部门将退料申请表转交给采购部门进行退货手续。
4. 退货手续(1) 采购部门收到退料申请表后,进行退货手续。
(2) 采购部门根据退料申请表中的信息,核对退货物料的数量和质量,与供应商进行退货商议。
(3) 采购部门与供应商达成一致后,进行退货手续,包括填写退货单、退款等。
(4) 采购部门将退货单和相关文件归档,并通知财务部门进行退款操作。
5. 财务处理(1) 财务部门收到退货单后,进行财务处理。
(2) 财务部门核对退货单和相关文件的准确性,进行退款操作。
(3) 财务部门将退货单和相关文件归档,并将退款信息通知相关部门。
6. 退料报废(1) 若退料物料不符合质量要求,质量管理部门将退料物料进行报废处理。
(2) 报废处理包括填写报废单、销毁或者返工等操作。
(3) 报废单和相关文件归档,并通知仓库管理部门进行相应的库存调整。
7. 监督与评估(1) 相关部门定期对退料流程进行监督和评估,以确保流程的有效性和合规性。
生产车间物料管理规定,生产领料流程,生产退料流程

生产车间物料管理规定,生产领料流程,生产退料流程生产车间物料管理规定,生产领料流程,生产退料流程只看楼主•楼主谭龙•收藏2012-11-15 08:16:40一、生产领料1. 生产部根据工单和生产计划组织生产,生产所需原材料,严格按照工单信息填写《领料单》,领料单上必须填写工单号、领用部门、物料名称、必要的物料规格描述、计量单位、请领数等信息。
2. 原则上领料单中原材料规格必须和生产工单一致,但若因其他原因需要用其他规格的原材料替换工单中原材料规格的,必须在领料单中备注栏标注“材料替换”等类似字样。
3.仓库部根据生产部的领料需求发货,并在领料单中填写实发数量。
仓库部必须见领料单方可发货,生产部门不得私自从原材料库领出原材料。
4.领料单一式三联,财务部、仓库部、生产部各一联,财务联由仓库部转交。
二、生产退料1.对于需要退回仓库的原材料,生产部填制《退料单》,退料单中必须填写订单号、物料名称、数量。
2.仓库部根据生产部的退料需求收货,并在退料单中填列实收数量,生产部不得私自将未办理退料手续的材料转入原材料仓库。
3.退料单一式三联,财务部、仓库部、生产部各一联,财务联由仓库部转交。
三、辅料领用辅料领用及单据传递程序可参照生产领料、生产退料流程执行。
四、不良品管理1.生产部必须加强对生产过程中的不良品现场管理,生产过程中挑选出的不良品统一放置于规定区域,已报废不良品、待处理不良品必须严格分区域、分产品规格存放,防止混乱。
2.生产部清理出需要报废的不良品,交品质部确认,品质部确认后出具《报废单》。
报废单上必须填写生产工单号、物料代码(成品)、物料名称(成品)、报废数量、报废原因等信息。
3.已开具报废单的报废品根据实际情况转入废料仓库,未开具报废单的废品不得随意转入废料仓库。
4.报废单一式三联,财务部、品质部、生产部各一联。
财务联由品质部转交。
•沙发谭龙•回复此层2012-11-15 08:17:26五、成品入库1.生产部生产的完工产品应先办理成品入库手续,转入仓库成品仓库,不得直接从车间销售出货。
生产退料管理制度
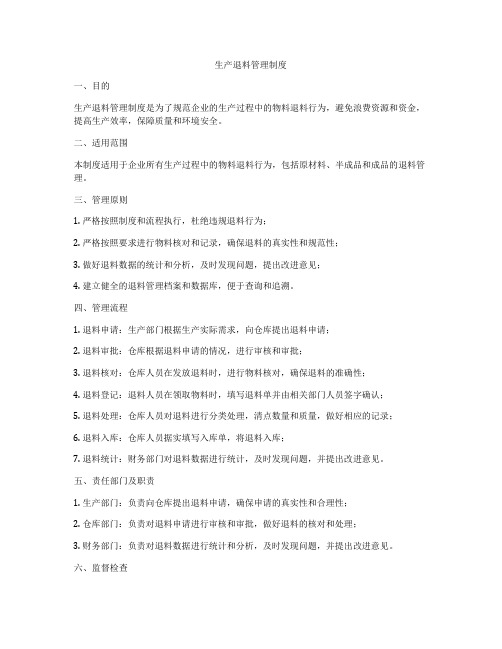
生产退料管理制度一、目的生产退料管理制度是为了规范企业的生产过程中的物料退料行为,避免浪费资源和资金,提高生产效率,保障质量和环境安全。
二、适用范围本制度适用于企业所有生产过程中的物料退料行为,包括原材料、半成品和成品的退料管理。
三、管理原则1. 严格按照制度和流程执行,杜绝违规退料行为;2. 严格按照要求进行物料核对和记录,确保退料的真实性和规范性;3. 做好退料数据的统计和分析,及时发现问题,提出改进意见;4. 建立健全的退料管理档案和数据库,便于查询和追溯。
四、管理流程1. 退料申请:生产部门根据生产实际需求,向仓库提出退料申请;2. 退料审批:仓库根据退料申请的情况,进行审核和审批;3. 退料核对:仓库人员在发放退料时,进行物料核对,确保退料的准确性;4. 退料登记:退料人员在领取物料时,填写退料单并由相关部门人员签字确认;5. 退料处理:仓库人员对退料进行分类处理,清点数量和质量,做好相应的记录;6. 退料入库:仓库人员据实填写入库单,将退料入库;7. 退料统计:财务部门对退料数据进行统计,及时发现问题,并提出改进意见。
五、责任部门及职责1. 生产部门:负责向仓库提出退料申请,确保申请的真实性和合理性;2. 仓库部门:负责对退料申请进行审核和审批,做好退料的核对和处理;3. 财务部门:负责对退料数据进行统计和分析,及时发现问题,并提出改进意见。
六、监督检查1. 仓库主管对退料流程进行监督和检查,确保执行到位;2. 质量部门定期对退料数据进行抽查,发现问题及时处理;3. 稽查部门对退料制度和流程进行全面检查,发现问题及时纠正。
七、附则1. 对于违反退料管理制度的行为,将根据情节轻重给予相应的处罚;2. 本制度自颁布之日起执行。
以上即为生产退料管理制度,希望各部门严格遵守执行,确保生产过程中的物料退料行为符合规范和要求。
仓库退料管理流程

仓库退料管理流程仓库退料的流程是什么,办理退料有哪些相关的手续。
小编给大家整理了关于仓库退料流程,希望你们喜欢!产线退货流程1. 找到要退料的原限额领料单,点击领料;2. 在本次出库数量那一栏对应的子件(原材料)填上要退回仓库的数量(由于是退料,这里一定要填负数);3. 然后点击保存4.点击分单,就会生成一张红字的材料出库单温馨提示:红字的材料出库单相当于一张入库单5.参照订单生成一张红字到货单,然后保存6. 参照红字到货单生成红字采购入库单,保存,审核7.查询采购订单执行统计表,可查看对应的数量8.做采购发票时,要参照蓝字采购入库单和红字采购入库单生成同一张发票仓库退料管理规定1、目的为规范公司物品的退料工作,有效的对物料进行控管,降低不必要的损耗节约成本,特编制本规定2、适用范围本规定适用于公司指令性、号令性、技术、质量、生产、工程、销售、采购、综合等仓库领用物品的退库3、职责3.1《物料退库单》是物资退库的唯一凭证3.2 仓库保管根据审批后《物料退库单》内容做物料的退库3.3 无《物料退库单》,仓库保管拒绝物资退回仓库。
3.4退库工作由各职能部门配合仓库完成3.5企管部对退库过程进行管控4、过程4.1对于领用的物料在使用时遇有物料异常、用料变更、节余或因其它情况需要退回仓库时,相关部门安排人员进行退库。
4.2退库时退库单位填写《物料退库单》,物料退库凭单的填写要字迹清晰、页面整洁、项目齐全。
4.3退库方式4.3.1公司指令性退库公司指令性退库是指由公司层面发起的物料召回退库活动。
4.3.2技术性退库技术性退库是指因设计变更或设计错误来不及修正导致的领用物料退库。
4.3.3告知错误退库告知错误退库是指由销售、服务、生产任务、工程任务、研发认购指令下达错误导致的领用物料退库。
4.3.4质量问题退库质量问题退库是指由销售、生产、研发、工程过程中所用物料发现自身存在的外观、性能等质量问题而提出的物料退库。
退料流程管理规范

退料流程管理规范一、引言退料流程管理是指在生产过程中,对于不合格或多余的原材料、半成品或成品进行退回、处理和管理的一系列操作。
合理的退料流程管理可以提高生产效率,降低成本,确保产品质量,保障企业的经济效益和声誉。
本文将详细介绍退料流程管理的标准格式和要求。
二、退料流程管理步骤1. 退料申请生产人员在发现不合格或多余的原材料、半成品或成品时,应填写退料申请表。
申请表中应包含以下信息:- 退料类型:原材料、半成品或成品;- 退料数量:具体退回的数量;- 退料原因:不合格、过期、多余等;- 退料日期:填写退料申请的日期;- 申请人:填写申请退料的人员姓名。
2. 退料审批退料申请表需提交给相关主管进行审批。
主管应仔细核对申请表中的信息,并根据实际情况决定是否批准退料。
审批结果需在申请表上签字确认,并将申请表交给仓库管理人员进行后续操作。
3. 退料处理仓库管理人员根据退料申请表上的信息,对退料进行处理。
具体处理方式包括:- 核对退料数量:核对实际退回的数量是否与申请表上的数量一致;- 检查退料质量:对退回的原材料、半成品或成品进行质量检查,确保符合退料标准;- 记录退料信息:将退料的品名、规格、数量等信息记录在退料记录表中;- 退料处理方式:根据退料的性质,选择合适的处理方式,如销毁、重新加工、二次利用等。
4. 退料归档退料处理完成后,相关退料记录和申请表需进行归档。
归档内容包括:- 退料记录表:记录退料的品名、规格、数量、退料日期等信息;- 退料申请表:包括退料类型、退料数量、退料原因、申请人等信息;- 退料审批表:记录退料审批的结果和主管签字确认。
5. 退料追溯退料追溯是指对退料流程进行全程追踪和记录,以便于后期的质量追溯和问题分析。
在退料追溯中,应包括以下内容:- 退料流程记录:记录退料的每个环节和操作人员;- 退料质量检查记录:记录对退料进行的质量检查结果;- 退料处理方式记录:记录对退料的具体处理方式;- 退料归档记录:记录退料的归档情况。
物控管理程序-生产退料作业流程-正文X2
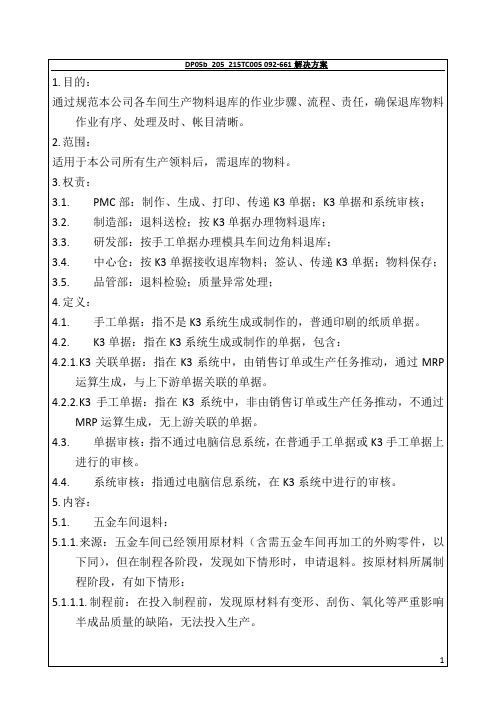
3.5.品管部:退料检验;质量异常处理;
4.定义:
4.1.手工单据:指不是K3系统生成或制作的,普通印刷的纸质单据。
4.2.K3单据:指在K3系统生成或制作的单据,包含:
4.2.1.K3关联单据:指在K3系统中,由销售订单或生产任务推动,通过MRP运算生成,与上下游单据关联的单据。
C.传递:五金MC当即将该<K3红字领料单>和<K3领料单>“PMC部联”传递给审单员,将<退料检验单>、<K3红字领料单>和<K3领料单>其余各联传递给五金车间车间物料员。
5.1.5.退料:
5.1.5.1.库别:参照<生产入库作业流程>5.1.4.1章节,五金车间车间物料员持<退料检验单>、<K3红字领料单>和拟退料不良物料,退原材料库或相应外购库的“不良品储位”。
E.如需补料:参照《生产领料作业流程》第5.1.4章节执行领料,但必须提前或同时办理退料作业。
5.2.5.2.混料情形:
A.库别:参照<生产入库作业流程>5.1.4.1章节,总装车间班组物料员持<退料检验单>、<K3红字领料单>、<K3其他出库单>、<K3其他入库单>和拟退物料,退相应的总装库区。
B.核单与点收:参照<生产入库作业流程>5.1.4.2章节,总装车间班组物料员和相应仓库责任仓管员,核对<K3红字领料单>、<K3其他出库单>、<K3其他入库单>和<退料检验单>,点收退料实物,并将混料物料按<退料检验单>的判定做仓位和储位的调整。
生产物料管理流程,仓库货物领料、退料、借料与盘点流程
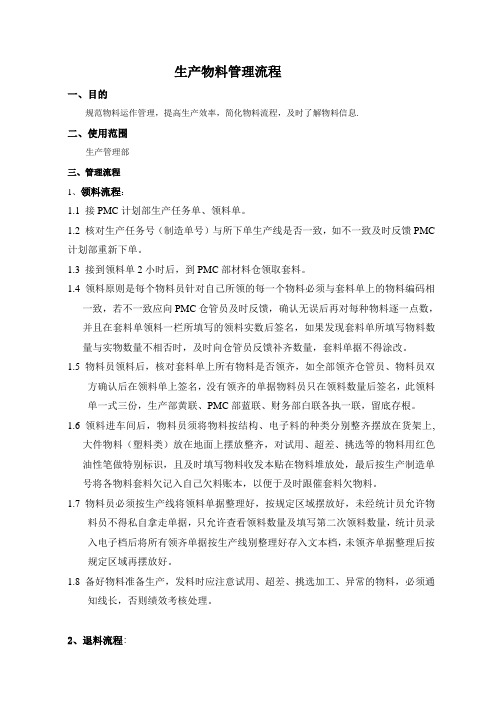
生产物料管理流程一、目的规范物料运作管理,提高生产效率,简化物料流程,及时了解物料信息.二、使用范围生产管理部三、管理流程1、领料流程:1.1 接PMC计划部生产任务单、领料单。
1.2 核对生产任务号(制造单号)与所下单生产线是否一致,如不一致及时反馈PMC 计划部重新下单。
1.3 接到领料单2小时后,到PMC部材料仓领取套料。
1.4 领料原则是每个物料员针对自己所领的每一个物料必须与套料单上的物料编码相一致,若不一致应向PMC仓管员及时反馈,确认无误后再对每种物料逐一点数,并且在套料单领料一栏所填写的领料实数后签名,如果发现套料单所填写物料数量与实物数量不相否时,及时向仓管员反馈补齐数量,套料单据不得涂改。
1.5 物料员领料后,核对套料单上所有物料是否领齐,如全部领齐仓管员、物料员双方确认后在领料单上签名,没有领齐的单据物料员只在领料数量后签名,此领料单一式三份,生产部黄联、PMC部蓝联、财务部白联各执一联,留底存根。
1.6 领料进车间后,物料员须将物料按结构、电子料的种类分别整齐摆放在货架上,大件物料(塑料类)放在地面上摆放整齐,对试用、超差、挑选等的物料用红色油性笔做特别标识,且及时填写物料收发本贴在物料堆放处,最后按生产制造单号将各物料套料欠记入自己欠料账本,以便于及时跟催套料欠物料。
1.7 物料员必须按生产线将领料单据整理好,按规定区域摆放好,未经统计员允许物料员不得私自拿走单据,只允许查看领料数量及填写第二次领料数量,统计员录入电子档后将所有领齐单据按生产线别整理好存入文本档,未领齐单据整理后按规定区域再摆放好。
1.8 备好物料准备生产,发料时应注意试用、超差、挑选加工、异常的物料,必须通知线长,否则绩效考核处理。
2、退料流程:2.1 生产过程中,将不良品物料挑选出,做上标识放在不良品区。
2.2 将不良品给质管部巡线技术员确认是否可以接受,若能接受则在不良标识上写上“OK”表示已确认;若不能接受,放回不良品区做好标识,下班后统一交给生产线退料员,退料员确认数量且记录退料数后退到物料房相应生产线。
退料流程管理规范
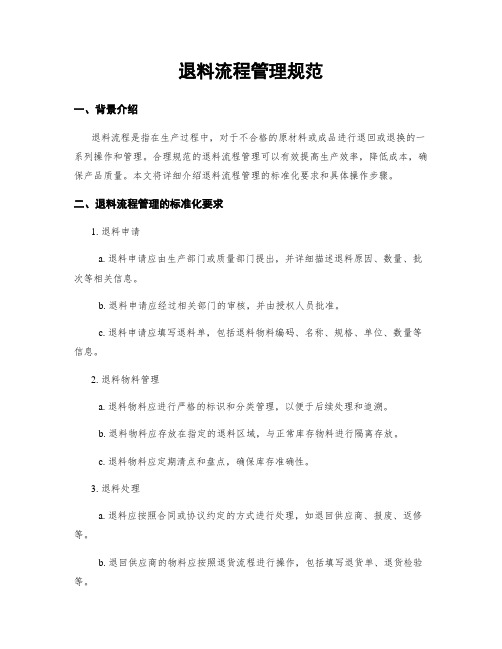
退料流程管理规范一、背景介绍退料流程是指在生产过程中,对于不合格的原材料或成品进行退回或退换的一系列操作和管理。
合理规范的退料流程管理可以有效提高生产效率,降低成本,确保产品质量。
本文将详细介绍退料流程管理的标准化要求和具体操作步骤。
二、退料流程管理的标准化要求1. 退料申请a. 退料申请应由生产部门或质量部门提出,并详细描述退料原因、数量、批次等相关信息。
b. 退料申请应经过相关部门的审核,并由授权人员批准。
c. 退料申请应填写退料单,包括退料物料编码、名称、规格、单位、数量等信息。
2. 退料物料管理a. 退料物料应进行严格的标识和分类管理,以便于后续处理和追溯。
b. 退料物料应存放在指定的退料区域,与正常库存物料进行隔离存放。
c. 退料物料应定期清点和盘点,确保库存准确性。
3. 退料处理a. 退料应按照合同或协议约定的方式进行处理,如退回供应商、报废、返修等。
b. 退回供应商的物料应按照退货流程进行操作,包括填写退货单、退货检验等。
c. 报废物料应按照公司的废品管理制度进行处理,包括填写废品报告、废品处置等。
d. 需要返修的物料应按照返修流程进行操作,包括填写返修单、返修检验等。
4. 退料记录和报表a. 对于每一次退料,应及时记录相关信息,包括退料原因、数量、批次、退料人员等。
b. 退料记录应按照一定的格式进行归档和保存,以便于后续的查询和分析。
c. 定期生成退料报表,包括退料数量、金额、原因分析等,以便于管理层进行决策和改进。
5. 退料流程的监控和改进a. 对退料流程进行定期的内部审核和外部评审,发现问题及时进行纠正和改进。
b. 建立退料流程的关键绩效指标,如退料率、退料处理周期等,并进行监控和分析。
c. 根据退料流程的实际情况,不断优化和改进流程,提高退料处理的效率和准确性。
三、退料流程管理的具体操作步骤1. 退料申请a. 生产部门或质量部门提出退料申请,包括退料原因、数量、批次等信息。
退料流程管理规范

退料流程管理规范一、引言退料流程是指在生产过程中,将不合格或多余的原材料、半成品或成品退回供应商或仓库的管理流程。
退料流程的规范化管理对于提高生产效率、降低成本、保证产品质量具有重要意义。
本文旨在制定一套退料流程管理规范,以确保退料流程的顺利进行。
二、退料申请1. 退料申请人员应填写退料申请表,包括以下信息:- 退料物料名称、规格型号、数量等详细信息;- 退料原因,如质量问题、生产过剩等;- 退料日期及要求退料的截止日期;- 退料人员的姓名、部门等基本信息。
2. 退料申请表应经申请人员本人签字确认,并提交给相关部门经理审核。
三、退料审核1. 相关部门经理应及时对退料申请进行审核,包括以下内容:- 退料原因是否合理;- 退料物料是否符合退料标准;- 退料数量是否准确。
2. 审核结果应在退料申请表上注明,并签字确认。
四、退料处理1. 经审核通过的退料申请,应由相关部门负责人通知仓库管理员进行退料处理。
2. 仓库管理员应按照以下步骤进行退料处理:- 核对退料物料的名称、规格型号、数量等信息;- 对退料物料进行验收,确保退料物料符合退料标准;- 在退料记录中登记退料物料的详细信息,包括退料日期、退料数量等;- 将退料物料妥善存放在指定区域,并进行标识。
3. 退料记录应包括以下内容:- 退料物料的名称、规格型号、批次等信息;- 退料日期、退料数量等信息;- 退料人员的姓名、部门等基本信息;- 退料原因。
五、退料追溯1. 为了保证产品质量追溯的需要,退料流程应具备退料追溯功能,包括以下要求:- 退料记录应按照时间顺序进行编号,并妥善保存;- 退料记录应包括退料物料的详细信息,以便于追溯退料物料的来源和去向;- 退料记录应与生产记录、质量记录等相关信息进行关联,以便于全面了解退料物料的使用情况。
2. 在退料记录中,应注明退料物料的去向,如退回供应商、报废等。
六、退料报废1. 对于不合格的退料物料,应按照相关规定进行报废处理。
生产物料退料控制程序
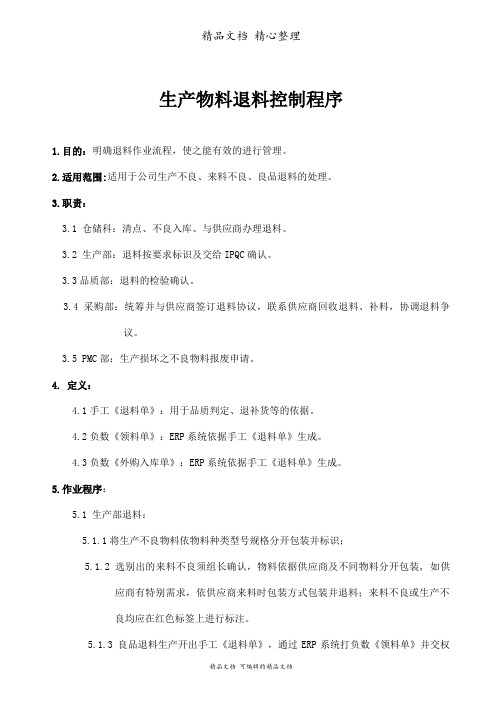
生产物料退料控制程序1.目的:明确退料作业流程,使之能有效的进行管理。
2.适用范围:适用于公司生产不良、来料不良、良品退料的处理。
3.职责:3.1 仓储科:清点、不良入库、与供应商办理退料。
3.2 生产部:退料按要求标识及交给IPQC确认。
3.3品质部:退料的检验确认。
3.4 采购部:统筹并与供应商签订退料协议,联系供应商回收退料、补料,协调退料争议。
3.5 PMC部:生产损坏之不良物料报废申请。
4. 定义:4.1手工《退料单》:用于品质判定、退补货等的依据。
4.2负数《领料单》:ERP系统依据手工《退料单》生成。
4.3负数《外购入库单》:ERP系统依据手工《退料单》生成。
5.作业程序:5.1 生产部退料:5.1.1将生产不良物料依物料种类型号规格分开包装并标识;5.1.2 选别出的来料不良须组长确认,物料依据供应商及不同物料分开包装, 如供应商有特别需求,依供应商来料时包装方式包装并退料;来料不良或生产不良均应在红色标签上进行标注。
5.1.3 良品退料生产开出手工《退料单》,通过ERP系统打负数《领料单》并交权责人员签名确认后交于相关IPQC或IQC确认。
5.1.4 生产不良、来料不良生产开出《不良品处理报告》交于相关IPQC或IQC确认。
5.2 品管部、PE确认退料:5.2.1退料确认采用单次抽样/正常检验Ⅱ,AQL4.0检验与判断;并应出具书面检验报告。
5.2.2 来料不良之电子料退料由IQC确认,非电子料之退料由相关IPQC确认;生产不良、良品退仓由IPQC确认。
5.2.3 所有不良品进行报废或退货处理必须非IQC确认的必须由IQC最终确认。
5.2.5 客供料退料由IPQC确认,必要时由QE协助;5.2.6 退料时应确认物料的标识状况、品质状况、包装方式;5.2.7电子料退料在200PCS以内的由检验员确认,200PCS以上的须品管领班/组长复核确认;5.2.8贵重物料如IC/模块、火牛、电池退料在50PCS以上的须由跟线PIE确认后交IPQC组长初步确认、IQC工程师或组长再次确认;5.2.9 非电子料退料在500PCS以内的由检验员确认,500PCS以上的由领班/组长再次确认。
仓库物料管理流程仓库收料、发料、退料、盘点工作流程

仓库物料管理流程一、范围 (1)二、目的 (1)三、管理流程 (1)3.1收料 (1)3.2.发料 (2)3.3.成品 (3)3.4.管理 (3)3.5.退料 (4)3.6仓库单据管理 (4)3.7盘点 (5)3.8仓库对特殊物品的管理 (5)3.9仓库的六防工作 (5)四、最低库存量与安全库存量管理 (5)一、范围适用于全公司全体员工。
二、目的为了使仓库管理更完善规范化,为了能使成本核算更准确,物料能得到更好的控制与管理,特作出此管理流程。
三、管理流程3.1收料供应商送货到仓库,仓管员必须拿供应商的送货单与货物相对照清点是否单物相符。
同时通知验货人员到场第一时间验货,验货及清点完毕后,看对方送货单是否签名齐全后办理进仓手续(开具四联收料单,由检验人员、供应商复合以及仓管员签字为准,开单要求清晰明了)。
办完进仓手续后仓管员将进仓单附于送货单后面送由财务或结现金或月结同时交送一联成本核算。
如图:3.2.发料发料原则“先进先出”;生产车间用料领料按物料清单开具生产单生产所需物料的三联领料单,领料单开具必须注明生产单号。
领料单由所需物料所属组别的组长开具(开单要求清晰明了不得乱涂乱画否则仓管员有权拒发),给车间主管核准一式三联。
拿至仓库,仓管员凭领料单(按先进先出的原则)对照生产单物料清单给予首次发放。
物料发完后仓管员必须在发料人上签字双方确认各自拿回所属联领料单。
发完物料按单入台帐以及分好单据红色联及时上交财务,本程序也适用于打印备料单的领料发料。
如图:3.3.成品生产车间完成成品生产,由包装组组长开具四联成品进仓单,交由质检检验合格后进仓,仓管员清点清楚。
发货由业务发出发货通知单,仓管开具成品出仓单以及经手人签字后装车发货。
最后入台帐。
如图:3.4.管理3.4.1仓库现场管理以5S为标准(整理、整顿、清扫、清除、素养)。
仓库可分为五金仓库(原材料、辅料、以及工具的管理);半成品仓(自造、外购以及外发加工的半成品)。
退补料管理控制程序与步骤,生产退补料业务操作指引说明
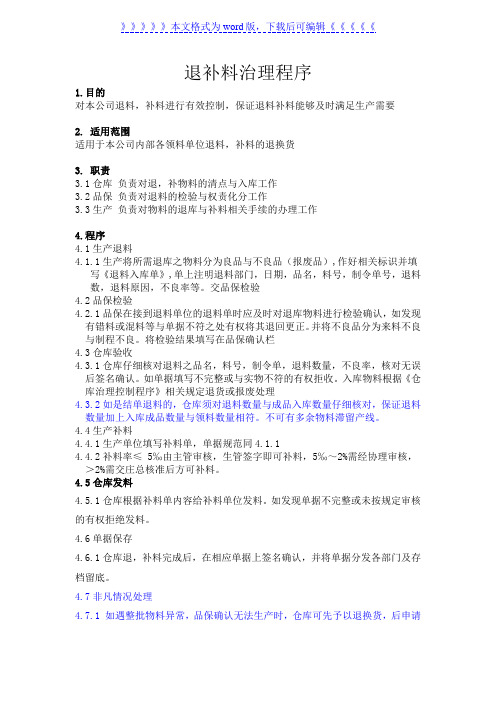
退补料治理程序1.目的对本公司退料,补料进行有效控制,保证退料补料能够及时满足生产需要2.适用范围适用于本公司内部各领料单位退料,补料的退换货3.职责3.1仓库负责对退,补物料的清点与入库工作3.2品保负责对退料的检验与权责化分工作3.3生产负责对物料的退库与补料相关手续的办理工作4.程序4.1生产退料4.1.1生产将所需退库之物料分为良品与不良品(报废品),作好相关标识并填写《退料入库单》,单上注明退料部门,日期,品名,料号,制令单号,退料数,退料原因,不良率等。
交品保检验4.2品保检验4.2.1品保在接到退料单位的退料单时应及时对退库物料进行检验确认,如发现有错料或混料等与单据不符之处有权将其退回更正。
并将不良品分为来料不良与制程不良。
将检验结果填写在品保确认栏4.3仓库验收4.3.1仓库仔细核对退料之品名,料号,制令单,退料数量,不良率,核对无误后签名确认。
如单据填写不完整或与实物不符的有权拒收。
入库物料根据《仓库治理控制程序》相关规定退货或报废处理4.3.2如是结单退料的,仓库须对退料数量与成品入库数量仔细核对,保证退料数量加上入库成品数量与领料数量相符。
不可有多余物料滞留产线。
4.4生产补料4.4.1生产单位填写补料单,单据规范同4.1.14.4.2补料率≤ 5‰由主管审核,生管签字即可补料,5‰~2%需经协理审核,>2%需交庄总核准后方可补料。
4.5仓库发料4.5.1仓库根据补料单内容给补料单位发料。
如发现单据不完整或未按规定审核的有权拒绝发料。
4.6单据保存4.6.1仓库退,补料完成后,在相应单据上签名确认,并将单据分发各部门及存档留底。
4.7非凡情况处理4.7.1如遇整批物料异常,品保确认无法生产时,仓库可先予以退换货,后申请品保复检。
4.7.2如生产急出货物料,退料单需注明急出货,仓库可先行补料给产线,再将退料送品保检验,品保出结果后,仓库依4.3.1流程操作4.8流程图:。
- 1、下载文档前请自行甄别文档内容的完整性,平台不提供额外的编辑、内容补充、找答案等附加服务。
- 2、"仅部分预览"的文档,不可在线预览部分如存在完整性等问题,可反馈申请退款(可完整预览的文档不适用该条件!)。
- 3、如文档侵犯您的权益,请联系客服反馈,我们会尽快为您处理(人工客服工作时间:9:00-18:30)。
A.非原材料原因导致物料或半成品报废,但可以改制成其他工件时,该物料或半成品做退料处理。
B.多料、混料。
5.1.2.送检:五金车间各班组出现上述情形,需要退料时,班组物料员清点退料数量,开具<退料检验单>送检项,交给五金车间IPQC。
5.1.3.检验与报告:
5.1.3.1.检验:五金车间IPQC根据《产品检验管理程序》和对应产品的《进料检验作业指导书》要求,进行检验、判定,填报<退料检验单>。IPQC组长确认后,送品管部经理(或经理助理,以下同)审核。检验应在60分钟内完成。
b)将<K3其他出库单>、<K3其他入库单>、<K3红字领料单>和<退料检验单>“中心仓联”自行归档,传递<K3其他出库单>“领料部门联”和<K3其他入库单>“入库部门联”给中心仓文员。
c)传递<K3红字领料单>、<K3其他出库单>、<K3其他入库单>“财务部联”和<退料检验单>“PMC部联”给PMC部审单员。
C.签认:参照<生产入库作业流程>5.1.4.3章节,总装车间班组物料员和相应仓库责任仓管员在<K3红字领料单>相应栏位签认。
D.传递:参照<生产入库作业流程>5.1.4.4章节,各责任仓管员完成传递<K3红字领料单>和<退料检验单>“制造部联”给物料员;“中心仓联”自行归档;<K3红字领料单>“财务部联”和<退料检验单>“PMC部联”给PMC部审单员。
E.如需补料:参照《生产领料作业流程》第5.1.4章节执行领料,但必须提前或同时办理退料作业。
5.2.6.审核:
5.2.6.1.审单:参照《生产领料作业流程》第5.1.2.2章节,审单员完成<K3红字领料单>(或有<K3领料单>、<K3其他出库单>、<K3其他入库单>,以下同)的审核。
a)质量不良物料,退“不良品库”。
b)多料的合格物料,退“良品库”。
B.制<K3领料单>:
a)无需补料:无此步骤。
b)需补料:参照本程序5.1.4.2章节,总装MC以总装PC允可的补料数量,制做并打印<K3领料单>,须备注“补退料”字样。
C.传递:参照本程序5.1.4.2章节,总装MC当即传递该<K3红字领料单>(或有<K3领料单>)各联和<退料检验单>分别传递给审单员和总装车间物料员。
5.2.4.2.混料情形:
A.制<K3红字领料单>:参照本程序5.1.4.1章节,总装MC以原领料料号,以<退料检验单>判定的混料数,入原领料料号对应的“不良品库”,制作并打印<K3红字领料单>。
B.制<K3其他出库单>:总装MC以原领料料号,以<K3红字领料单>数量,制作手工<K3其他出库单>,出库库别为原领料料号对应的“不良品库”,领料部门为“中心仓”,并备注<K3红字领料单>单号及“混料调整出库”字样。
5.2.3.检验与报告:
5.2.3.1.检验:参照本流程5.1.3.1章节,总装车间IPQC、IPQC组长、品管部经理(或副经理,以下同)进行检验、判定,出具并审核总装车间<退料检验报告>。
退料检验判定报废的,则由中心仓责任仓管员按照《报废作业流程》作业。
5.2.3.2.补料会签:参照本流程5.1.3.2章节,PMC部总装PC在已审核<退料检验单>上会签补料意见。
5.1.5.4.传递:参照<生产入库作业流程>5.1.4.4章节,各责任仓管员完成传递<K3红字领料单>和<退料检验单>“制造部联”给车间物料员;“中心仓联”自行归档;<K3红字领料单>“财务部联”和<退料检验单>“PMC部联”给PMC部审单员。
5.1.5.5.如需补料:参照《生产领料作业流程》第5.1.4章节执行领料,但必须提前或同时办理退料作业。
A.PMC部报告:参照《生产领料作业流程》5.1.2.2章节,审单员报告五金车间未送达<K3红字领料单>,审核后分发中心仓、制造部、财务部、总经办各部负责人。
B.财务部报告:参照《生产领料作业流程》5.1.2.2章节,信息管理主管报告五金车间未审核<K3红字退料单>,审核后分发中心仓、制造部、PMC部、总经办各部负责人。
C.传递:五金MC当即将该<K3红字领料单>和<K3领料单>“PMC部联”传递给审单员,将<退料检验单>、<K3红字领料单>和<K3领料单>其余各联传递给五金车间车间物料员。
5.1.5.退料:
5.1.5.1.库别:参照<生产入库作业流程>5.1.4.1章节,五金车间车间物料员持<退料检验单>、<K3红字领料单>和拟退料不良物料,退原材料库或相应外购库的“不良品储位”。
C.报告反馈::参照《外购入库作业流程》第5.14.3.3章节执行。
5.2.总装车间退料:
5.2.1.来源:总装车间已经领用各总装物料,但在制程各阶段,发现如下情形时,申请退料:
5.2.1.1.自制(含委外,以下同)物料:发生混料、多料、来料质量不良或总装作业导致来料质量不良但可返修(或改制、改用途)的。
5.2.5.退料:
5.2.5.1.非混料情形:
A.库别:参照<生产入库作业流程>5.1.4.1章节,总装车间班组物料员持<退料检验单>、<K3红字领料单>和拟退物料,退相应的总装库区。
B.核单与点收:参照<生产入库作业流程>5.1.4.2章节,总装车间班组物料员和相应仓库责任仓管员,核对<K3红字领料单>和<退料检验单>,点收退料实物。
E.如需补料:参照《生产领料作业流程》第5.1.4章节执行领料,但必须提前或同时办理退料作业。
5.2.5.2.混料情形:
A.库别:参照<生产入库作业流程>5.1.4.1章节,总装车间班组物料员持<退料检验单>、<K3红字领料单>、<K3其他出库单>、<K3其他入库单>和拟退物料,退相应的总装库区。
B.核单与点收:参照<生产入库作业流程>5.1.4.2章节,总装车间班组物料员和相应仓库责任仓管员,核对<K3红字领料单>、t;和<退料检验单>,点收退料实物,并将混料物料按<退料检验单>的判定做仓位和储位的调整。
5.1.1.1.制程前:在投入制程前,发现原材料有变形、刮伤、氧化等严重影响半成品质量的缺陷,无法投入生产。
5.1.1.2.制程中:在制造过程中,发现原材料严重不良,直接影响半成品质量或导致制程不良率过高,无法继续生产。
5.1.1.3.制程后:生产已经完成,但半成品尚未入库,由于原材料自身的原因,导致半成品不良,无法入库。
1.目的:
通过规范本公司各车间生产物料退库的作业步骤、流程、责任,确保退库物料作业有序、处理及时、帐目清晰。
2.范围:
适用于本公司所有生产领料后,需退库的物料。
3.权责:
3.1.PMC部:制作、生成、打印、传递K3单据;K3单据和系统审核;
3.2.制造部:退料送检;按K3单据办理物料退库;
3.3.研发部:按手工单据办理模具车间边角料退库;
5.2.1.2.外购物料:发生混料、多料、来料质量不良或总装作业导致来料质量不良且有不良实物的。
5.2.1.3.验货不良物料:根据其产品检验要求,客人或总部QC在验货时产生不良物料,必须更换合格为物料方可出货的。
5.2.2.送检:总装车间各班组出现上述情形,需要退料时,班组物料员清点退料数量,开具<退料检验单>送检项,交给总装车间IPQC。
4.2.2.K3手工单据:指在K3系统中,非由销售订单或生产任务推动,不通过MRP运算生成,无上游关联的单据。
4.3.单据审核:指不通过电脑信息系统,在普通手工单据或K3手工单据上进行的审核。
4.4.系统审核:指通过电脑信息系统,在K3系统中进行的审核。
5.内容:
5.1.五金车间退料:
5.1.1.来源:五金车间已经领用原材料(含需五金车间再加工的外购零件,以下同),但在制程各阶段,发现如下情形时,申请退料。按原材料所属制程阶段,有如下情形:
C.制<K3其他入库单>:总装MC以混料物料本身料号,
a)如混料物料本身为合格品,则以<退料检验单>判定的混料合格品数量,制作手工<K3其他入库单>,入混料物料本身料号对应的“良品库”,入库部门为“中心仓”,并备注<K3红字领料单>单号及“混料调整入库”字样。
b)如混料物料本身为不合格品,则以<退料检验单>判定的混料不合格品数量,制作手工<K3其他入库单>,入混料物料本身料号对应的“不良品库”,入库部门为“中心仓”,并备注<K3红字领料单>单号及“混料调整入库”字样。
D.制<K3领料单>:
a)无需补料,无此步骤。
b)需补料,总装MC以原领料料号,以总装PC允可的补料数量,选择原关联生产任务单,制做并打印<K3领料单>,须备注“补退料”字样。
E.传递:总装MC当即传递该<K3红字领料单>(或有<K3领料单>,以下同)、<K3其他出库单>、<K3其他入库单>“PMC部联”传递给审单员,传递<K3红字领料单>(或有<K3领料单>,以下同)、<K3其他出库单>、<K3其他入库单>其余各联和<退料检验单>给总装车间班组物料员。