车架铆接工艺准则
浅谈现代化重型汽车车架铆接质量控制

浅谈现代化重型汽车车架铆接质量控制摘要车架的铆接工艺是车架制造过程中的关键技术之一,约占汽车车架总成及分总成加工工作的80%以上,在汽车载荷和使用性能方面,车架要求有足够的强度和刚度方可满足车辆的各种运行路况,而铆接质量的控制就显得至关重要。
关键词铆接工艺;铆接质量我公司铆接车间采用2条自动流水作业和1条简易轨道流水线,各工序转运采用自动板链式输送和轨道小车推动式输送,目前可以满足牵引车、自卸车、载货车、专用特种车以及军用越野车等各种车型铆接任务。
1 铆钉材料选用原则铆接的钢结构中,铆钉材料必须具有较高的塑性和不可淬性。
常用钢制的铆钉。
一般钢制铆钉的材料采用以下几种材料制作:普通碳素钢:如Q235、Q215A、BL2、BL3;普通碳素铆接用钢:如ML2、ML3、ML10、ML15、ML20;优质碳素钢:如10、15;我公司车架所用钢制铆钉一般选用普通碳素铆接用钢中的ML10和ML15。
2 铆钉直径选用原则铆钉直径的确定选择是根据结构件的受力情况,考虑铆接件的强度要求,通过力学分析和计算得到的。
铆钉直径的正确选择,主要是根据板料的厚度来确定。
板料厚度又必须依以下三个原则确定:①板料与板料搭接按较厚板料的厚度确定;②厚度相差较大时以较薄板料的厚度确定;③钢板与型材铆接时,以两者的平均厚度确定。
多层板料的总厚度,不应超过铆钉直径的4倍[1]。
铆钉直径也可按下列公式计算:d=式中d—铆钉直径mm;t—板料厚度mm。
3 鉚钉长度的选用原则铆钉钉杆的长度一般是根据被铆接件的总厚度、铆钉直径和铆接工艺等因素来确定的。
对于车架铆钉长度选用原则:铆钉钉杆的体积等于铆接孔的体积加上成形铆头体积[2]。
常用半圆头铆钉的钉杆长度计算公式如下:半圆头铆钉L=(1.65~1.75)d+1.1t式中L—铆钉长度mm;d—铆钉直径mm;t—被铆接件的总厚度mm。
4 铆钉孔径的选用原则铆钉孔直径一般比铆钉直径稍大。
在铆接时,如孔径过大,钉杆容易弯曲,影响铆接质量和铆接强度;如孔径与铆钉直径相等或过小,铆接时铆钉难以插入孔内,或者引起板料凸起和凹入,造成表面不平整,甚至因铆钉膨胀挤坏板料。
载重车架生产工艺课件-铆接

4
T48自卸车
81.41016.6373
车架前宽后窄,变 截面,和 T48牵引 车前段相同
10、工艺文件中的符号、代号及含义
例:AC300N.m 扭力扳手 适用范围:300N.m B16 气扳机 适用范围:最大拧紧螺栓直径M16 S18 套筒 适用于六方为18的螺栓 S-087-171 专用工装代号
DZ9112510140 DZ9100510170 2 S29 DZ9114512710
DZ9114512910 DZ9114515700
9.2德御车系列 为了加宽横梁上、下连接板距离,采用新横梁结构,为了降重心, 横梁位置降低,横梁连接板加高、加宽。横梁连接板上翻,部分 弯梁采用MAN结构形式。
12、铆接工艺知识及铆接标准:
12.1、铆接 车架总成铆接分为冷铆和热铆。 12.1.1、冷铆:铆钉在常温状态下的铆接称为冷铆。 铆接时,所用的铆钉由低碳钢制成,而且要经过退火处理。冷铆时,铆 钉杆不易镦粗,为保证连接强度,钉孔直径和钉杆直径应尽量接近,使钉和 孔严密,防止板料之间有滑动现象,产生冲击应力。一般铆钉孔比铆钉直径 大0.5mm,冷铆铆接力F=20d2(吨),即Φ12铆钉冷铆压力为30吨,Φ14 铆钉冷铆压力为40吨。 冷铆优点:操作过程简化迅速,铆钉孔比热铆填充得紧密。 12.1.2、热铆:铆钉加热后的铆接称为热铆。 铆钉加热温度为1000度以上,铆接力F=10A(A为铆钉截面积cm2), 即Φ16铆钉热铆压力为20吨,Φ18铆钉热铆压力为25吨。 热铆优点:铆钉冷却后,在长度方面的收缩受到板料厚度的限制,钉杆 产生的内应力,作用在板料上,使板料压紧。当铆接件受力时,铆接件和板 料之间产生很大的摩擦阻力,因而提高了铆接件的联接强度。
外六角或内六角 8.8 / 8 Nm 45 45 50 75 75 80 115 125 180 190 260 270 290 10.9 / 10 Nm 65 65 70 105 110 115 170 185 260 280 370 390 410 12.9 / 12 Nm 75 75 85 125 130 135 200 215 310 330 430 450 480
车架铆接通用技术要求

精品资料车架铆接通用技术要求发布精品资料前言车架铆接通用技术要求1 范围本标准规定了我公司客车车架总成及其零部件的铆接技术要求。
本标准适用于公司产品设计、工艺设计、操作与质量检验。
2 引用标准QJ/DD04.3.01-2010 切削加工件通用技术条件3 一般要求3.1 铆钉对应的铆钉孔直径及偏差按表1执行。
表1 单位为毫米3.2 铆钉孔间距偏差按QJ/DD04.3.01-2010执行。
3.3 铆钉、铆接零件表面应清洁,不得有锈层、油垢,铆钉孔不得有毛刺。
3.4 铆接零件装配应相互紧贴,可采用螺栓、定位销或夹子紧固被铆接零件,不允许采用焊接(点焊)的方法紧固。
3.5 铆接操作时,上、下铆头和铆钉应同心,以保证铆钉成形准确。
3.6 车架及其零部件采用冷铆铆接。
当技术文件有明确要求时,可采用热铆铆接。
3.7 热铆铆钉加热温度为800℃~900℃,并在500℃以上完成铆接过程。
3.8 热铆铆钉在装入铆钉孔前,必须清除氧化皮,对烧损、烧细、烧坏的铆钉不允许使用。
3.9 根据设备要求,合理选择铆接压力,保证铆钉成形质量。
3.10 铆接后,不符合要求的铆钉应铲去重铆;铲去铆钉时,不应损坏母体金属及相邻铆钉,其铲入深度不得超过0.5 mm。
3.11 铆接质量技术要求3.11.1 铆接后被铆零件应在铆钉四周3倍铆钉杆直径范围内紧密贴合,其间隙不得超过0.05 mm。
3.11.2 成形铆钉头按附录A《铆接缺陷产生原因分析及缺陷检查表》及铆钉预制头要求执行。
3.11.3 其余铆接质量技术要求按附录A《铆接缺陷产生原因分析及缺陷检查表》执行。
附录A 铆接缺陷产生原因分析及缺陷检查表单位为毫米铆接缺陷简图允许偏差缺陷原因检查方法铆钉头与母材贴合不紧密不允许1、铆钉头与铆钉杆连接处有凸起地方2、铆接时,顶具未顶紧1、外部检查2、用锤敲击3、用0.05 mm塞尺检查铆钉头歪斜不允许1、铆接时粗心大意2、顶具放置偏斜1、外部检查2、用0.05 mm 塞尺检查铆钉头有裂纹不允许1、铆钉材质低劣2、铆钉加热过度外部检查铆钉杆在铆钉孔内弯曲不允许铆钉孔大且铆钉杆长敲击钉头铆钉在铆合件内断开不允许1、零件间有间隙2、装配不正确3、压的不紧敲击铆缝用手锤敲打时,铆钉头振荡或活头不允许1、铆接件压的不紧2、铆钉杆在孔内不严密用手锤敲打两面铆钉头铆钉头有凹痕b≤2但在重要地方不允许顶具松动或疏忽而形成外部检查铆钉头周围有帽缘b≤1.51、铆钉杆长2、铆钉模小外部检查铆钉头中心与铆钉杆中心偏移b≤1.51、铆接时粗心大意2、顶具放置偏斜外部检查铆钉头边缘缺肉b+d≤2c≤1.51、铆钉杆短2、铆钉模大外部检查和用样板检查铆钉头过小b≤0.1d1、铆钉杆短2、铆钉模小外部检查和用样板检查铆钉头周围有硬伤(母材上)h≤11、铆钉模大2、铆钉模安放不正外部检查埋头铆钉的钉头突出h≤0.5时允准许用砂轮磨去1、铆钉杆长2、埋头锥边小外部检查埋头铆钉的钉头凹进h≤0.5铆钉杆长度不够埋头锥边大外部检查_________________________________。
汽车车架的铆接和焊修技术
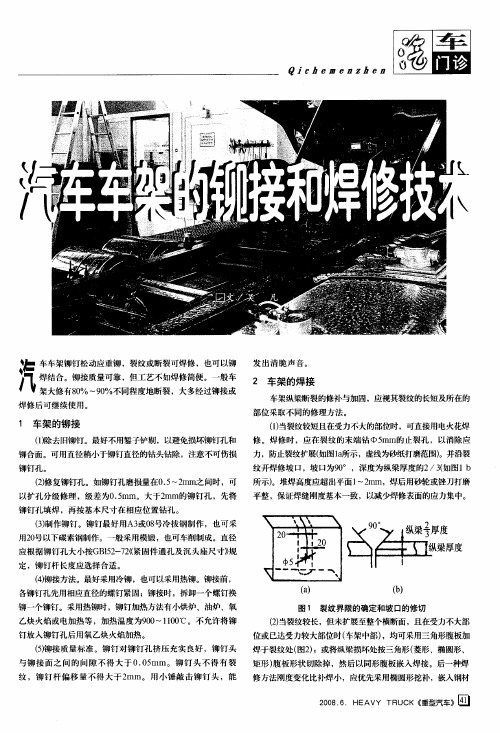
大多经过铆接或
车架纵梁断裂的修补与加固,应视其裂纹的长短及所在的 部位采取不同的修理方法。 () 1当裂纹较短且在受力不大的部位时,可直接用电火花焊
修 。焊修时 ,应在裂纹的末端钻 ①5 mm的止裂孔 ,以消除应
1 车架 的铆 接
() 1 除去旧铆钉。最好不用錾子铲剔,以避免损坏铆钉孔和 铆合面。可 用直径稍小于铆钉直径的钻头钻除 ,注意不可伤损
修方法刚度变化比补焊小 ,应优先采用椭圆形挖补,嵌入钢材
1 71 " 1 7
(铆接质量标 准。铆钉对铆钉 孔挤压充实 良好 ,铆钉头 5 )
与铆接 面 之 间的 间隙 不得 大于 0. 5 m。铆 钉头 不 得 有裂 0r a
纹 ,铆钉 杆偏 移量 不得 大于 2 m。用 小锤敲 击铆 钉头 ,能 a r
() 1 若在受力大的部位焊加强腹板,要注意焊接应力对纵梁 的影响,可采用 图5 的方法。加强板比纵梁边缘宽 出25( .t 为车 t 架纵梁厚度) ,并把焊缝焊成 凹形。
() 2车架上焊缝长度大时 ,应采用断续分段焊法(n 所 I 图6
示) 。每段焊缝长度和间距请参阅下表 。
图2 三角形加强腹板 的厚度 、材质应与纵梁材质相 同。
() 6寒冷季节,应将焊接部位预热至2 ~5  ̄ 0 0 C,以防炸裂; 图 3 角钢切角 图 4 弯角圆弧半径 焊后缓慢冷却,清除焊渣 ,用砂轮、锉刀等工具修整焊缝 。
黼 ■ 鬻 ■ 一 黧 ■ 麓 一 麓 ● 麓 一 麓 ■ 臻 ■ 鞠 ■ ■ 一 ■ 瓣 一 鬃 一 辫 一 鞭 一 一 ■ ■ 一 一 一 一 ■ 一 ■ 一 曩 一 一 ■
为了减小应力集中,加强板的端部应做成逐渐减小的斜角 形( ) 图3。加强板的形状如 图4 所示 ,其弯角圆弧半径应不大于
车架铆接通用技术要求

QJ/DD 03.3.05-2001 车架铆接通用技术要求发布QJ/DD 03.3.05-2001 前言1 范围本标准规定了我公司客车车架总成及其零部件的铆接技术要求。
本标准适用于公司产品设计、工艺设计、操作与质量检验。
2 引用标准QJ/DD04.3.01-2010 切削加工件 通用技术条件 3 一般要求3.1 铆钉对应的铆钉孔直径及偏差按表1执行。
表1 单位为毫米3.2 铆钉孔间距偏差按QJ/DD04.3.01-2010执行。
3.3 铆钉、铆接零件表面应清洁,不得有锈层、油垢,铆钉孔不得有毛刺。
3.4 铆接零件装配应相互紧贴,可采用螺栓、定位销或夹子紧固被铆接零件,不允许采用焊接(点焊)的方法紧固。
3.5 铆接操作时,上、下铆头和铆钉应同心,以保证铆钉成形准确。
3.6 车架及其零部件采用冷铆铆接。
当技术文件有明确要求时,可采用热铆铆接。
3.7 热铆铆钉加热温度为800℃~900℃,并在500℃以上完成铆接过程。
3.8 热铆铆钉在装入铆钉孔前,必须清除氧化皮,对烧损、烧细、烧坏的铆钉不允许使用。
3.9 根据设备要求,合理选择铆接压力,保证铆钉成形质量。
3.10 铆接后,不符合要求的铆钉应铲去重铆;铲去铆钉时,不应损坏母体金属及相邻铆钉,其铲入深度不得超过0.5 mm 。
3.11 铆接质量技术要求3.11.1 铆接后被铆零件应在铆钉四周3倍铆钉杆直径范围内紧密贴合,其间隙不得超过0.05 mm 。
3.11.2 成形铆钉头按附录A 《铆接缺陷产生原因分析及缺陷检查表》及铆钉预制头要求执行。
3.11.3 其余铆接质量技术要求按附录A 《铆接缺陷产生原因分析及缺陷检查表》执行。
附录A 铆接缺陷产生原因分析及缺陷检查表 单位为毫米 车架铆接通用技术要求_________________________________。
铆接工艺守则

SQB42018——2009
我公司车架常用铆钉为精制半圆头铆钉,其编号方法遵循 GB/T 867—1986
中的编号规则。例如:直径 12mm、长 50mm,钢制、氧化的半圆头铆钉编号(图
号)为 Q4501250。我公司车架常用铆钉规格:直径分别为 12、14、16、18mm,
长在 30~55mm 之间。例如:直径 12mm、长 50mm,钢制、氧化的半圆头铆钉
标牌铆 钉
GB/T827—1986① 1.6~5 3~20 用于铆标牌
抽芯铆 钉
GB/T12615~ 12618—1990
3~6
铆接容易,用于汽车车 6~40 身覆盖体、支架等部
位,单面铆接
击芯铆 钉
GB/T1585—1995
① 为商品紧固件产品,应优先选用。
2~5
3~20
用于各种车辆,船舶、 航空、机械制造、电讯 器材和钢木家具等的 单面铆接
将型钢或压型制件与板件用 铆钉连接在一起
3
SQB42018——2009
3.3.3 按照铆钉所受剪切力的情况可分为单剪切、双剪切和多剪切三种连接 形式。 3.3.4 按照每一主板上铆钉的行列可分为单排、双排、三排等连接形式。 3.3.5 按照连接板上铆钉的排列形式可分为平行排列和交错排列两种连接 形式。 3.4 铆钉
7
SQB42018——2009
3.4.3.1 钢结构连接铆钉 常见的钢结构连接铆钉形式有半圆头铆钉、平锥头铆钉、沉头铆钉、半
沉头铆钉、平头铆钉、扁圆头铆钉和扁平头铆钉等(见表 2)。
在各种铆接缝中,半圆头铆钉应用最广泛。特别是强固结合用半圆头铆
钉和密固结合用半圆头铆钉两种铆钉应用更为广泛。常用粗制半圆头铆钉的
车架通用技术条件
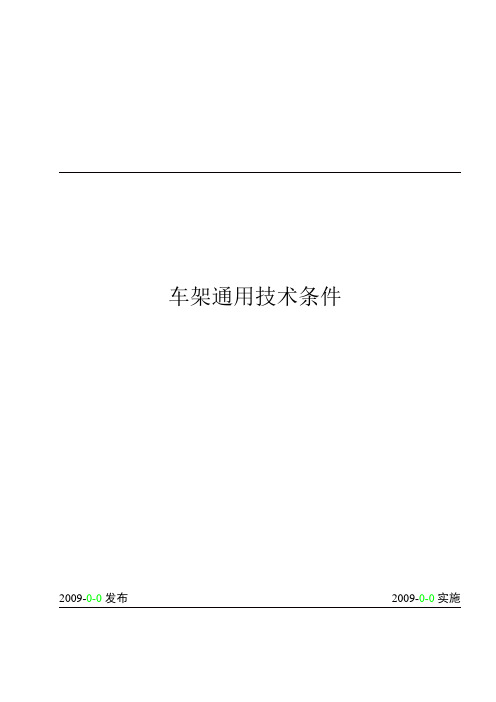
车架通用技术条件前言车架通用技术条件1前言本技术条件是公司车架通用的基本要求,适用于公司车架设计及检验。
2引用标准QJ/DD04.3.23-87 铆接工艺通用技术条件QJ/DD04.3.50-2010 焊接件通用技术条件QJ/DD04.16-2009 客车油漆涂层QJ/DD09.8.10-2009 装配通用技术条件3技术要求3.1车架铆接要求3.1.1铆接要求按QJ/DD04.3.23-87铆接工艺通用技术条件执行。
3.1.2不同心的铆钉孔,允许采用同径铰刀铰孔后铆接。
3.1.3铆接后,不合要求但又在允许偏差范围内的铆钉数,不超过总数的10%,单件上不超过1个。
3.1.4纵梁铆接完成后,对纵梁上下翼面及腹面出现的孔不同心现象,按原孔尺寸引钻。
3.2车架定位焊要求3.2.1槽型梁腹面前后面、上下翼面各焊一段,异型管梁前后腹面各焊一~二段,其余小件每件焊至少两段,每段焊缝长约10 mm,焊角高低于板厚,该焊缝在后续焊接中应被覆盖上。
3.3车架焊接要求3.3.1焊接标准按QJ/DD04.3.50-2010焊接件通用技术条件执行。
3.3.2焊接采用CO2气体保护焊,焊角高度与所焊零件板厚相同。
3.3.3焊接顺序:先焊纵梁联接处→横梁→立柱→其余各支撑梁、小件;焊接中要求由内向外,由中间向前后逐步、对称、交错进行。
3.3.4纵梁搭接、联接处及关键联接件在焊夹具上完成焊接。
3.3.5联接板的塞焊孔≤30mm时,塞焊孔焊平;塞焊孔>30mm时,塞焊孔焊一周;板周边在两孔间断续焊,焊缝长同孔径,焊角高均同板厚。
3.3.6焊接过程中,车架应处于平整状态。
3.4车架检查、修正要求3.4.1车架平面度技术要求3.4.1.1专用焊夹具上生产的老车型车架,平面度≤8mm。
3.4.1.2其余车架平面度≤6mm,每2米≤2mm;带落差车架平面度要求相同,公差按各落差面积分布。
3.4.1.3带行李仓车架在X方向直线度:纵梁≤6mm,每2米≤2mm;支撑梁端头处≤3mm。
车架铆接通用工艺守则(A4)

校对(日期)
审核(日期)
标准化(日期)
会签(日期)
批准(日期)
标记
处数
更改文件号
签字(日期)
长沙仙达实业有限公司
车架铆接通用工艺守则
第4页
共6页
7.5每班每铆第一个铆钉前,应点动操作铆钳,观察动、静铆模是否对中,若不对中,先查明原因,调整或更换铆模使其对中后,再进行铆接。
7.6铆钉头部与尾部应同动、静铆模的端部铆坑对中,若铆钉歪斜,调整后再铆。
6.1铆钉材料为10号或15号优质碳素钢(亦可用ML10、ML15),冷墩加工成型,退火处理,表面氧化(发兰),化学成分、机械性能符合GB6478-86。
6.2严格按照图纸规定选用铆钉规格,铆钉长度理论计算公式:L=1.12∑δ+1.4d其中L为铆钉长度,∑δ为被铆零件厚度之和,d为铆钉直径。
6.3铆钉表面不允许有影响使用的裂缝。
8.2.4铆钉头成形直径不小于1.5倍的钉杆的直径。
8.2.5被铆接零部件结合面要贴合紧密,在小于铆钉直径3倍区域内最大间隙不大于0.2mm。
编制(日期)
校对(日期)
审核(日期)
标准化(日期)
会签(日期)
批准(日期)
标记
处数
更改文件号
签字(日期)
长沙仙达实业有限公司
车架铆接通用工艺守则
第5页
共6页
8.2.6铆钉头与被铆接零部件要贴合紧密,沿铆钉头周围至少有120°范围间隙不大于0.05mm,其余部位间隙不大于0.2mm。
4.6.4铆钉成型后,动铆模不回或回程太短;
4.6.5动铆模下行无力;
4.6.6噪音大,活塞爬行。
4.7设备要定期保养,且有维保记录。
- 1、下载文档前请自行甄别文档内容的完整性,平台不提供额外的编辑、内容补充、找答案等附加服务。
- 2、"仅部分预览"的文档,不可在线预览部分如存在完整性等问题,可反馈申请退款(可完整预览的文档不适用该条件!)。
- 3、如文档侵犯您的权益,请联系客服反馈,我们会尽快为您处理(人工客服工作时间:9:00-18:30)。
车架铆接工艺准则
1 目的
为加强公司的工艺管理,完善车架铆接工艺,保证车架铆接质量,提高产品竞争力,特制定本准则。
2 范围
本规范适用于本公司中重型卡车的车架总成及其零部件。
3 铆钉
3.1 铆钉材料、化学成分、机械性能应符合Q450-1995;
3.2 铆钉表面一般进行氧化处理。
4 铆钉孔
4.1 铆钉孔中心到弯曲边的最小距离(见图1)应符合表1规定。
表1 (单位:mm)
4.2 测量点
铆钉孔孔边距“X”应从图2所示测量点计起。
4.3 角度偏差
纵梁上、下翼面对腹板的角度偏差为±1°或±1.5mm (当翼板宽度为90mm时),见图3.
4.4 铆钉孔的直径,见表2.
表2 (单位:mm)
4.5 去毛刺
4.5.1 无论产品图样上是否注明去毛刺,实际加工过程中都必须对孔的两端打磨或倒角,以去除毛刺。
去毛刺后,手指肚划过孔端边沿应感觉平滑、无明显凸兀感,孔内必须无残留铁屑或飞边。
4.5.2 零件装配时铆钉孔允许的最大位移量(错位量)为 1.6mm,为消除位移可采用与孔径对应的铰刀绞孔,以保证铆钉能顺利插入。
4.5.3 铆钉孔位移量不大于1.0mm时,允许使用导正销或其它方法来使铆钉顺利插入铆钉孔, 否则应绞孔至铆钉能顺利插入。
4.5.4 绞孔时铰刀的最大倾斜角为5°,铆钉插入前铆钉孔两端应按4.4.1的要求去毛刺。
5 铆接
5.1 铆钉墩头成型应为球冠形(或近似球冠形),其直径dk应不小于铆钉杆直径的
1.5倍,其高度K应不小于铆钉预制头高度,见图4。
5.2 铆钉、铆接零件表面应清洁,不得有锈层、油垢,铆钉孔不得有毛刺。
5.3 铆接后,铆钉头与钢板间及各铆接零件间的贴合面必须紧密贴合。
5.3.1 铆钉头(包括成型头及预制头)与被铆钢板间必须紧密贴合,其间隙不得大于0.05mm,见图5。
5.3.2 被铆零件间的贴合面在铆钉沿周3d(3倍铆钉杆直径)范围内必须紧密贴合,其间隙不得大于0.05mm ,见图5。
5.3.3 铆钉孔到弯边距离小于3d时,圆角部分不做上述要求。
5.4 铆接操作时,上、下铆头和铆钉应同心,以保证铆钉成形准确。
5.5 车架及其零部件采用冷铆铆接。
当技术文件有明确要求时,可采用热铆铆接。
5.6 热铆铆钉加热温度为800℃~900℃,并在500℃以上完成铆接过程。
5.7 热铆铆钉在装入铆钉孔前,必须清除氧化皮,对烧损、烧细、烧坏的铆钉不允许使用。
5.8 铆接后,不符合要求的铆钉应铲去重铆;铲去铆钉时,不应损坏母体金属及相邻铆钉,其铲入深度不得超过0.5 mm。
6 铆接压力
铆接压力见表3。
表3 铆接压力
铆钉直径d 10 12 14 16
铆接压力p(吨) 冷铆26 28 35 48 热铆10 15 20 26
注:铆接压力p的误差为±1吨.
7 其余铆接技术要求按附录A《铆接缺陷产生原因分析及缺陷检查表》执行。
附录A 铆接缺陷产生原因分析及缺陷检查表
铆接缺陷示意图允许偏差缺陷原因分析检查方法铆钉头与母
材贴合不紧密不允许
1、铆钉头与铆钉杆
连接处有凸起地方
2、铆接时,顶具未
顶紧
1、目测
2、用0.05 mm塞
尺检查
铆钉头歪斜不允许1、铆接时粗心大意
2、顶具放置偏斜
1、目测
2、用0.05 mm塞
尺检查
铆钉头有裂纹不允许
1、铆钉材质低劣
2、铆钉加热过度
目测
铆钉杆在铆钉孔内弯曲不允许
铆钉孔大且铆钉杆
过长
用手锤轻轻敲击
钉头
铆钉在铆合件内断开不允许
1、零件间有间隙
2、装配不正确
3、压的不紧
用手锤敲击铆缝
用手锤敲打
时,铆钉头振荡或活头不允许
1、铆接件压的不紧
2、铆钉杆在孔内不
严密
用手锤敲打两面
铆钉头
铆钉头有凹痕b≤2但在
重要地方
不允许
顶具松动或疏忽而
形成
外表查看,并测量
铆钉头周围有帽缘b≤1.5
1、铆钉杆过长
2、铆钉模小
目测
铆钉头中心
与铆钉杆中心偏移b≤1.5
1、铆接时粗心大意
2、顶具放置偏斜
目测
铆钉头边缘残缺或外形不完整b+d≤2
c≤1.5
1、铆钉杆短
2、铆钉模大
目测
铆钉头过小b≤0.1d 1、铆钉杆短
2、铆钉模小
外表查看,并测量
铆钉头周围
有硬伤(母材上)h≤1
1、铆钉模大
2、铆钉模安放不正
目测
埋头铆钉的钉头突出h≤0.5时
允许用砂
轮磨去
1、铆钉杆长
2、埋头锥边小
目测
埋头铆钉的钉头凹进h≤0.5
铆钉杆长度不够
埋头锥边大
目测。