高频感应炉燃烧后红外吸收法测定
硫的分析方法综述

硫的分析方法综述硫是自然界分布很广的一种元素,它主要以自然硫、硫化物和硫酸盐等状态存在于自然界中,有色金属矿石中的硫主要以硫化物、硫酸盐存在,某些矿石中还存在自然硫。
硫的测定方法主要有硫酸钡重量法、燃烧-中和滴定法、燃烧-碘量法、高频感应炉燃烧-红外吸收光谱法、燃烧库仑滴定法、X荧光光谱法、比浊法、ICP-AES法、氧化铝色层分离-硫酸钡重量法、还原蒸馏-次甲基蓝光度法、直读光谱法、离子色谱法、气相色谱法等等。
在硫的分析检测中,较常采用硫酸钡重量法、燃烧-中和滴定法、燃烧-碘量法、高频感应炉燃烧-红外吸收光谱法。
重量法因为分析周期长,手续烦杂等原因,在日常的实际样品分析中很少采用,一般只在仲裁分析中采用。
以下主要就硫酸钡重量法、燃烧-中和滴定法、燃烧-碘量法、高频感应炉燃烧-红外吸收光谱法这四种方法分别作综述。
一、硫酸钡重量法方法原理在含有硫酸根的溶液中用盐酸调节0.06~0.12mol/L HC1酸度,加入BaC12,BaC12+Na2SO4→BaSO4+2NaC1,对含硫量在0.3%以上都适用,但对含有大量K+、Na+碱金属离子不是非常准确的方法,会使结果增高或偏低。
‘(1)当溶液中没有任何盐类存在时,沉淀BaSO4产生两种相反误差:①由于BaSO4的溶解度。
②由于BaSO4对BaC12的吸附。
(2)在有碱金属盐类存在下沉淀BaSO4时也会产生两种误差:①中性的碱金属硫酸盐(Na2S04)共沉淀:②碱金属的酸式硫酸盐(NaHSO4)共沉淀。
第一种情况:因Na2SO4分子量比BaSO4小,所以产生负误差,结果偏低。
第二种情况:OHSOSONaNaHSO2342℃35042+↑+−−→−所以偏低更厉害。
如果事先用NH 4OH 分离Fe 则存在(NH 4)2SO 4,2232℃2354243643SO O H NH N SO NH +++−−→−)(会使结果更偏低。
为了避免以上离子影响,速加BaC12会增加BaSO 4 对BaC12的吸附,慢加BaC12可使BaSO 4对BaC12吸附减至为0,煮沸是为了获得比较大颗粒沉淀,便于过滤洗涤。
镍钴锰三元素氢氧化物化学分析方法
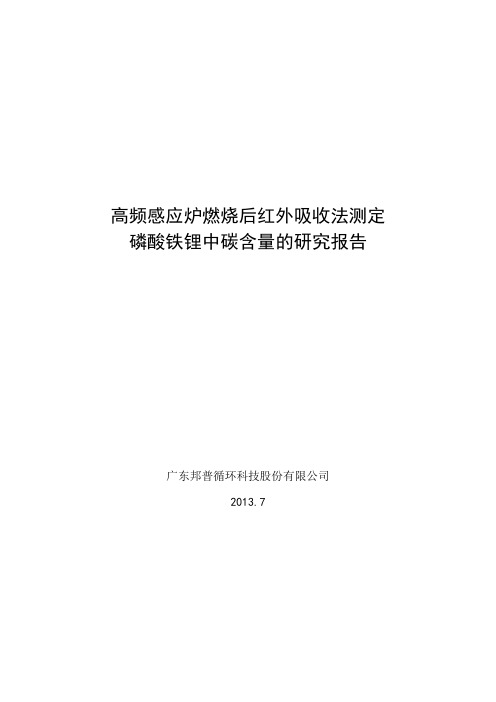
高频感应炉燃烧后红外吸收法测定磷酸铁锂中碳含量的研究报告广东邦普循环科技股份有限公司2013.7高频感应炉燃烧后红外吸收法测定磷酸铁锂中碳含量谢英豪,黎俊茂,袁杰摘要:试样中的碳经过富氧条件下的高温加热,氧化为二氧化碳气体。
该气体经处理后进入相应的吸收池,对相应的红外辐射进行吸收,由探测器转化为信号,经计算机处理输出结果。
结果表明:该方法测定磷酸铁锂中碳的精密度为小于1.0%,此方法准确、快速、灵敏度高,适用于实际样品的分析。
关键词:高频红外吸收法法;磷酸铁锂;测定;碳前言:现代仪器测定碳的方法主要有高频感应炉燃烧后红外吸收法[1]、X射线荧光光谱法[2-4]、离子色谱法[5]等。
高频感应炉燃烧后红外吸收法因结果准确、精密度高、操作简便、分析速度快等优点被广泛应用于分析钢铁材料中的碳元素。
本文在高频感应炉燃烧后红外吸收法[6]的基础上,研究了磷酸铁锂正极材料中碳含量的测定,实验结果良好,该方法能满足科研及产业化生产的需要。
1 实验部分1.1 主要试剂1.1.1 氧气:纯度不低于99.5 %。
1.1.2 干燥剂:无水高氯酸镁,粒度0.7 mm~1.2 mm。
1.1.3 净化剂:烧碱石棉,粒度0.7 mm~1.2 mm。
1.1.4 纯铁:纯度大于99.8 %,碳含量小于0.002 %。
1.1.5 钨粒:碳含量小于0.002 %。
1.1.6 瓷坩埚:瓷坩埚大小应精确,能够用于在高频感应炉中燃烧;用前将瓷坩埚置于马弗炉中,于1200 ℃灼烧不少于2 h,取出稍冷后储存在干燥器中。
1.2 仪器除非另有说明,分析中仅使用普通实验室设备。
高频感应燃烧炉和红外吸收定碳仪可以从厂家购买。
仪器的操作按照制造厂商的说明书。
根据制造厂技术规范,需要一个调压器来控制进炉氧气的压力(通常为28 kN/m2)。
市售商品仪器的特性参见GB/T 21631.1—2008中的附录B。
1.3 分析步骤1.3.1试料试样用前应置于110℃的烘箱中干燥1 h,取出后储存在干燥器中。
高频燃烧-红外吸收法测定高纯净度GH4169高温合金中碳
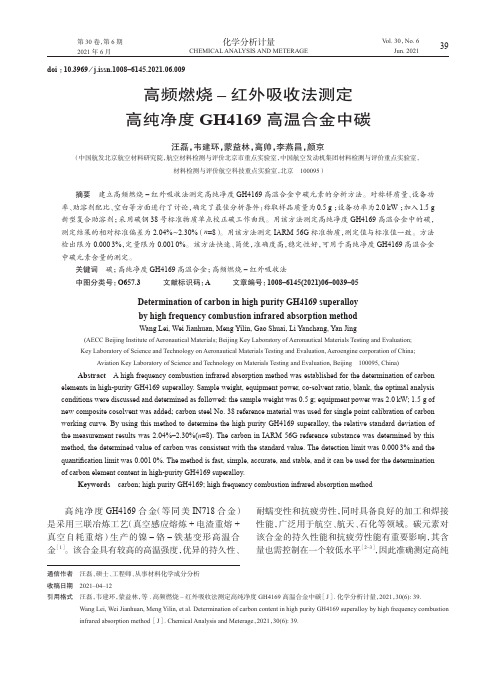
化学分析计量CHEMICAL ANALYSIS AND METERAGE第30卷,第6期2021年6月V ol. 30,No. 6Jun. 202139doi :10.3969/j.issn.1008–6145.2021.06.009高频燃烧–红外吸收法测定高纯净度G H 4169高温合金中碳汪磊,韦建环,蒙益林,高帅,李燕昌,颜京(中国航发北京航空材料研究院,航空材料检测与评价北京市重点实验室,中国航空发动机集团材料检测与评价重点实验室,材料检测与评价航空科技重点实验室,北京 100095)摘要 建立高频燃烧–红外吸收法测定高纯净度GH4169高温合金中碳元素的分析方法。
对称样质量、设备功率、助溶剂配比、空白等方面进行了讨论,确定了最佳分析条件:称取样品质量为0.5 g ;设备功率为2.0 kW ;加入1.5 g 新型复合助溶剂;采用碳钢38号标准物质单点校正碳工作曲线。
用该方法测定高纯净度GH4169高温合金中的碳,测定结果的相对标准偏差为2.04%~2.30% (n =8)。
用该方法测定IARM 56G 标准物质,测定值与标准值一致。
方法检出限为0.000 3%,定量限为0.001 0%。
该方法快速、简便,准确度高,稳定性好,可用于高纯净度GH4169高温合金中碳元素含量的测定。
关键词 碳;高纯净度GH4169高温合金;高频燃烧–红外吸收法中图分类号:O657.3 文献标识码:A 文章编号:1008–6145(2021)06–0039–05Determination of carbon in high purity GH4169 superalloyby high frequency combustion infrared absorption methodWang Lei, Wei Jianhuan, Meng Yilin, Gao Shuai, Li Yanchang, Yan Jing(AECC Beijing Institute of Aeronautical Materials; Beijing Key Laboratory of Aeronautical Materials Testing and Evaluation; Key Laboratory of Science and Technology on Aeronautical Materials Testing and Evaluation, Aeroengine corporation of China;Aviation Key Laboratory of Science and Technology on Materials Testing and Evaluation, Beijing 100095, China)Abstract A high frequency combustion infrared absorption method was established for the determination of carbon elements in high-purity GH4169 superalloy. Sample weight, equipment power, co-solvent ratio, blank, the optimal analysis conditions were discussed and determined as followed: the sample weight was 0.5 g; equipment power was 2.0 kW; 1.5 g of new composite cosolvent was added; carbon steel No. 38 reference material was used for single point calibration of carbon working curve. By using this method to determine the high purity GH4169 superalloy, the relative standard deviation of the measurement results was 2.04%–2.30%(n =8). The carbon in IARM 56G reference substance was determined by this method, the determined value of carbon was consistent with the standard value. The detection limit was 0.000 3% and the quanti fication limit was 0.001 0%. The method is fast, simple, accurate, and stable, and it can be used for the determination of carbon element content in high-purity GH4169 superalloy.Keywords carbon; high purity GH4169; high frequency combustion infrared absorption method高纯净度GH4169合金(等同美IN718合金)是采用三联冶炼工艺(真空感应熔炼+电渣重熔+真空自耗重熔)生产的镍–铬–铁基变形高温合 金[1]。
燃烧-高频红外碳硫分析法测定土壤中全碳量

2018年第37卷第2期243~246页云南地质C N53-1041/P I S S N1004-1885燃烧-高频红外碳硫分析法测定土壤中全碳量赵星,宋江伟,史旭峰(云南有色地质局308队测试中心,云南个旧661000)摘要:将测试样品导人高频炉中,在燃烧炉高温下经过氧气氧化燃烧,在助瑢剂存在下,将碳转化为 二氧化碳气体,以氧气为载气注人红外检测仪器,测定二氧化碳。
用标准物质绘制校准曲线,计算试样中的碳量。
该方法经过对仪器参数优化后,结果稳定,仪器检出限D?= 0.0015%,测定下限0.0059%,测定范围满足生产需求。
关键词:高频炉;燃烧;土壤;碳含量;红外检测仪中图分类号#0657. 33 文献标识码:A文章编号#1004-1885 (2018) 2-243-4碳是一种很常见的元素,它以多种形式广泛存在于大气和地壳和生物之中。
碳单质很早就被人认识和 利用,碳的一系列化合物一有机物更是生命的根本。
碳在地壳中的质量分数为0.027%,在自然界中分布 很广。
土壤中重金属污染与土壤中极强吸附性的物质碳元素富含程度有很大关系,在环境污染研究中,科 学家着重研究的是重金属污染的研究,而碳的含量高低也就成了污染的根源性问题[1(2]。
20世纪70年代以来,科学家采用各种方法对碳进行定量分析。
目前分析碳的分析方法有红外光度 法、容量法、重量法等。
基本原理都是将样品在通氧情况下高温燃烧生成C〇2,利用各种方法吸收后进行 测定。
高频红外碳硫分析仪能将样品在高频炉中燃烧时,生成的C〇2以氧气为载体,导人红外检测器,检测后的信号经前置放大后送计算机进行数据处理,其分析快速、准确、可靠。
且高频炉对于管式炉难于 燃烧的特种样品,如金属、石墨、炉渣及非金属氧化物等,均有较好的燃烧效果,同时也免除了管式炉长 时间高温辐射之苦,是一种相当实用的检测方法。
1实验部分1.1仪器(1)高频红外碳硫分析仪(型号HCS878A)(2) CPA124S电子天平(万分之一天平)1.2标准物质、试剂、材料(1)标准物质:土壤及水系沉积物标准物质(国家一级)(2)试剂:纯铁助溶剂(1C<0. 001%,粒度小于1.25mm)钨粒(1C<0. 001%)(3)材料:高频红外碳硫分析仪坩埚1.3仪器工作条件样品的燃烧是分析中首要结局的重要问题。
高频燃烧—红外吸收法测定金属铬中硫含量
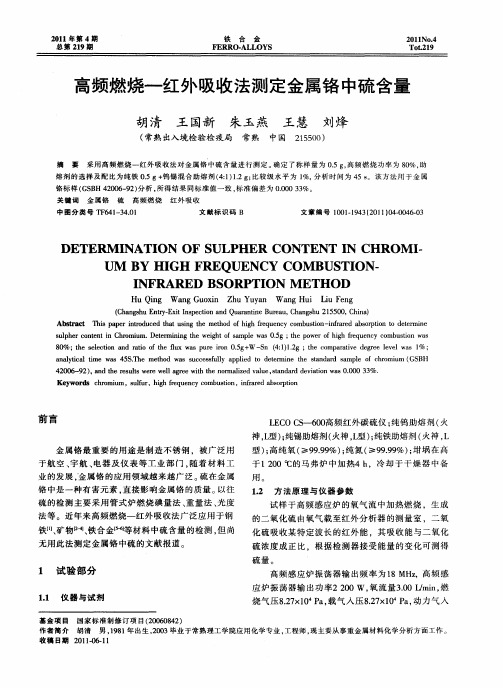
用。 1 方 法原理 与 仪器参 数 . 2
金 属铬 最重 要 的用 途 是制 造不 锈钢 ,被 广 泛用
试样 于 高频 感应 炉 的氧 气流 中加 热燃 烧 ,生成 的 二氧 化硫 由氧 气 载至 红外 分析 器 的测 量室 ,二氧 化硫 吸收某 特定 波 长 的红外 能 ,其 吸 收能 与二 氧化 硫 浓度 成正 比 .根 据检 测器 接 受能 量 的变化 可 测得
硫量 。
法 等 。近年来 高 频燃烧 一 红外 吸收 法广 泛应 用于钢
Ke wo d c r mi m 。s l r ih fe u n y c mb s o y rs h o u u f ,h g r q e c o u t n,ifa e b o t n u i n rr d a s r i p o
前 言
L C S 60 E O C 一 0 高频红 外碳硫 仪 ; 钨助熔 剂 ( 纯 火 神 ,型 )纯锡助熔剂 ( L ; 火神 ,型)纯铁助熔 剂 ( L ; 火神 , L
UM Y GH RE B HI F QUE NCY COMBUS I T ON.
I RARED oRP oN ETH oD NF BS TI M
H ig uQ n Wa gG oi Z uY yn Wa gH i LuF n n u xn h u a n u i e g
(hn suE t — x set nadQ aat eB ra, h nsu2 5o , hn) C agh n yE iI p c o n u rni ueu C agh 15o C ia r tn i n
高频燃烧—红外吸收法测定大气粉尘中碳硫
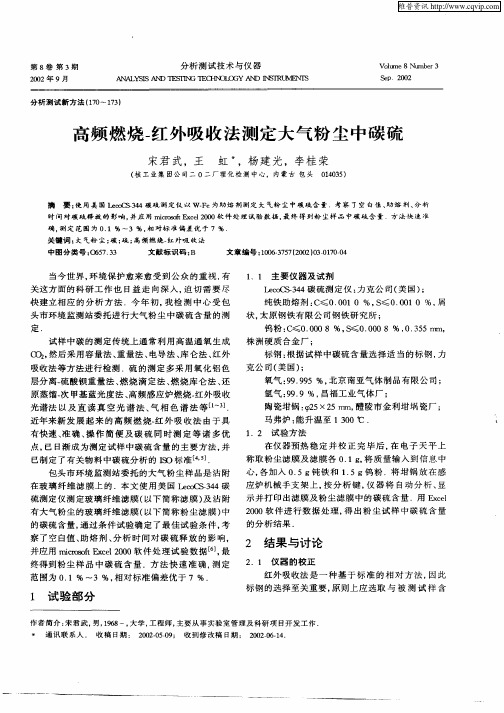
氧 气 :9 9 5%, 9 .9 北京 南 亚气 体 制 品有 限 公 司 ; 氩 气 :9 9%, 9. 昌福 工 业气 体 厂 ;
陶瓷坩 锅 : 5x2 , 陵市 金 利坩 埚 瓷 厂 ; 5m 醴 马 弗炉 : 升 温至 13 0℃ . 能 0
1 2 试 验方 法 .
1 试 验 部 分
标 钢 的选 择 至关 重 要 。 原则 上 应 选 取 与 被 测 试 样 含
作 者 简 介 : 君 武 , ,9 8 大 学 , 程 师 , 要 从 事 实 验 室 管 理 及 科 研 项 目开 发 工 作 宋 男 16 一, 工 主 * 通 讯 联 系 人 . 收 稿 E期 : 20 —50 ; 收 到 修 改 稿 E期 : 20 ,61 . t 020 ,9 t 020—4
1 、1 主 要 仪 器及 试剂
L c  ̄-4 ec S3 4碳硫 测 定 仪 : 克公 司 ( 国 ) l 力 美 ; 纯铁 助 熔 剂 : ≤ 0 0 10 %。 ≤ 0 0 10 %, C 0 S 0 屑
关 这方 面 的 科 研 工 作 也 日益 走 向 深 入 , 切 需 要 尽 迫 快 建立 相 应 的 分 析 方 法 .今 年 初 , 检 测 中 心 受 包 我
维普资讯
第 8卷 第 3期
20 02年 9月
分 析 测试 技 术与 仪 器
AN AL I YS S AND 1] 汀 】 1ECH 1 GY G 0 AND N RUMENP I NI S
Vll e 8 Nt b r3 0 in mae l S p.2 0 e 02
头 市环 境 监 测站 委托 进 行 大气 粉 尘 中碳 硫 含 量 的 测
定.
高频燃烧炉红外吸收法测定铁矿石中的硫含量

( 广东省韶关钢铁集 团有 限公 司, 广东 韶关 52 2 ) 11 3 摘 要: 介绍利用高频燃烧炉红外光谱法对铁矿石 中不 同含量 的硫 进行测 定 , 过对 助熔剂及 用量 、 品称 量、 通 样 样
品与助熔剂加入顺序 的选择 , 分析时间与 比较水平 的选择 等试验 , 确定 了方法 的最佳分 析参数 . 该法 方便快捷 , 分 析结果令人满意 , 测定范围在 0 0 8 ~ 0 精密度 06 % ~ .2 视样 品硫含量 ) 该方法符合铁矿石 国家标准 .0 % 2 %, .4 3 1 %( . ( B6 3 . 6 G 7 0 1 》 G 7 0 1 、 B63 . 7 的测试要求 .
总第 10期 8
2 1 年 6月 01
南
方
金Байду номын сангаас
属
S m. 1 0 u 8
S OUTHERN METAI 5
J n 2 1 ue 0 1
文 章 编 号 : 09— 7 0 2 1 )3— 0 1一 4 10 90 (0 1 o 0 2 o
高 频 燃 烧 炉 红 外 吸 收 法 测 定 铁 矿 石 中 的硫 含 量
范 围.
1 实验部分
1 1 仪 器 .
不易完全 ; 当硫含量高时 , 燃烧法热分解 产生大量
S :滴 定 不易掌 握 . 用 高频 燃 烧 炉 红 外 吸 收法 测 O, 利
LC E O公 司 C S一60红 外 碳 硫 分 析 仪 , 次 分 0 每 析样 品前 必须 预热 1h以上.
表 2可见 : 铁量 一 定 , +S w n比例 由 9 1向 55 : : 变化 时 , 品熔融 状 态 很 好 , 较 平 滑 , 观 察 到 燃 样 且 但 烧粉 尘 随 S n量减 少 而 减少 , W +S 当 n比到 8 2时 : 坩 埚边 缘 较 干 净 , 粉 尘 , 过 8 2 试 样 燃烧 释 放 无 超 :, 峰 形不好 , 因此 , 本实 验选 W +S n比例 为 82 :.
红外吸收法测定碳含量的测量不确定度评定

EVALUATIoN oF UNCERTAINTY oF MEASUREMENT oF CARBoN
CoNTENT BY INFRA.RED ABSoRPTIoN
He Lunying,Xu Lihui
METHoD
(Chongqing Instmment M砒erials Research Institute,The National En舀neering and Technology Research Center
掣=筹’-o.ooo
……。 88
3.3标准物质引入的标准不确定度 证书给出标准物质的标准偏差如表1所示,其 中不锈钢(材字239a)的碳含量测量结果的相对标 准偏差最大为O.036%,其平均值标准偏差为
收稿日期:2006一03也6
万方数据
14
化学分析计量
2006年,第15卷,第4期
0.002%(n=2),标准值由8个实验室共同完成的, 因此由标准物质引起的标准不确定度为:
万方数据
何伦英,等:红外吸收法测定碳含量的测量不确定度评定
13
红外吸收法测定碳含量的测量不确定度评定
何伦英徐丽辉
(重庆仪表材料研究所,国家仪表功能材料工程技术研究中心,重庆400700) 摘要对CCS一140型高频感应炉燃烧红外吸收法测定碳含量的不确定度进行了评定,分析了测量不确定度的 主要来源,包括仪器的精密度引入的不确定度,标准物质标准值的不确定度,试样称量的不确定度,以及坩埚、助熔 剂等引起的空白不确定度。当碳含量为0.366%时,测量结果的扩展不确定度为O.叭O%。 关键词测量不确定度红外吸收法碳评定
1.2环境条件
3.2试样称量引入的标准不确定度 对于数字显示式电子天平怛J,其分辨率6,为
- 1、下载文档前请自行甄别文档内容的完整性,平台不提供额外的编辑、内容补充、找答案等附加服务。
- 2、"仅部分预览"的文档,不可在线预览部分如存在完整性等问题,可反馈申请退款(可完整预览的文档不适用该条件!)。
- 3、如文档侵犯您的权益,请联系客服反馈,我们会尽快为您处理(人工客服工作时间:9:00-18:30)。
高频感应炉燃烧后红外吸收法测定磷酸铁锂中碳含量的研究报告广东邦普循环科技股份有限公司2013.7高频感应炉燃烧后红外吸收法测定磷酸铁锂中碳含量谢英豪,黎俊茂,袁杰摘要:试样中的碳经过富氧条件下的高温加热,氧化为二氧化碳气体。
该气体经处理后进入相应的吸收池,对相应的红外辐射进行吸收,由探测器转化为信号,经计算机处理输出结果。
结果表明:该方法测定磷酸铁锂中碳的精密度为小于1.0%,此方法准确、快速、灵敏度高,适用于实际样品的分析。
关键词:高频红外吸收法法;磷酸铁锂;测定;碳前言:现代仪器测定碳的方法主要有高频感应炉燃烧后红外吸收法[1]、X射线荧光光谱法[2-4]、离子色谱法[5]等。
高频感应炉燃烧后红外吸收法因结果准确、精密度高、操作简便、分析速度快等优点被广泛应用于分析钢铁材料中的碳元素。
本文在高频感应炉燃烧后红外吸收法[6]的基础上,研究了磷酸铁锂正极材料中碳含量的测定,实验结果良好,该方法能满足科研及产业化生产的需要。
1 实验部分1.1 主要试剂1.1.1 氧气:纯度不低于99.5 %。
1.1.2 干燥剂:无水高氯酸镁,粒度0.7 mm~1.2 mm。
1.1.3 净化剂:烧碱石棉,粒度0.7 mm~1.2 mm。
1.1.4 纯铁:纯度大于99.8 %,碳含量小于0.002 %。
1.1.5 钨粒:碳含量小于0.002 %。
1.1.6 瓷坩埚:瓷坩埚大小应精确,能够用于在高频感应炉中燃烧;用前将瓷坩埚置于马弗炉中,于1200 ℃灼烧不少于2 h,取出稍冷后储存在干燥器中。
1.2 仪器除非另有说明,分析中仅使用普通实验室设备。
高频感应燃烧炉和红外吸收定碳仪可以从厂家购买。
仪器的操作按照制造厂商的说明书。
根据制造厂技术规范,需要一个调压器来控制进炉氧气的压力(通常为28 kN/m2)。
市售商品仪器的特性参见GB/T 21631.1—2008中的附录B。
1.3 分析步骤1.3.1试料试样用前应置于110℃的烘箱中干燥1 h,取出后储存在干燥器中。
称取0.200 0 g试样,精确至0.000 1 g。
(粒度应不大于0.10 mm)1.3.2 分析前准备仪器启动前用氧气(1.1.1)检查气路的气密性,燃烧室、过滤器应经常清理。
按仪器要求定期更换干燥剂(1.1.2)、净化剂(1.1.3)。
确认正常后,启动仪器,按说明书要求进行预热和仪器的检查调试,保证仪器处于正常稳定的工作状态。
1.3.3 空白试验称取0.35 g纯铁(1.1.4)和2.0 g钨粒(1.1.5)置于瓷坩埚(1.1.6)中,于同一量程或通道,按1.3.5进行测定。
重复测定直到读数比较稳定为止。
记录最小的、比较稳定一致的三次读数,计算平均值并输入到仪器中,在测定试料时仪器会自动扣除空白值。
1.3.4 校正实验选择碳含量大于待测试料的有证标准物质来校正仪器。
在选定的通道上进行3~5 次分析,对系统进行线性调节,得出校正系数。
再用与试料含量相近的标准物质进行验证,在其允许差范围内方可进行试样分析。
1.3.5测定加入0.35 g纯铁(1.1.4)于瓷坩埚(1.1.6)中、将坩埚置于电子天平上,称量,去皮。
再向瓷坩埚中加入试料(1.3.1),并称量、输入试料质量,取下。
加入约2.0 g钨粒(1.1.5)覆盖在试料上,将瓷坩埚移至坩埚基座上。
按仪器说明进行操作,仪器自动进行分析,分析结束后记录碳的百分含量。
2 实验结果2.1 称样量按照试验处理步骤,进行高频红外碳硫仪吸收法对磷酸铁锂碳含量的测定,结果如表1所示:表1 试样量对分析结果的影响序号称样量/g 测量值/% 序号称样量/g 测量值/%1 0.0971 1.535 9 0.2062 1.5682 0.1134 1.531 10 0.3973 1.5603 0.0969 1.533 11 0.3985 1.5584 0.0972 1.537 12 0.6008 1.5465 0.1028 1.533 13 0.5999 1.5426 0.2003 1.562 14 0.5986 1.5387 0.2037 1.566 15 0.7976 1.5248 0.2000 1.562 16 0.8002 1.527从上表1可以看出,此方法测出磷酸铁锂的碳含量为1.565%,实验数据比较稳定,仪器在此碳含量范围的允许误差为0.03%。
当称样量为0.1g时,测量结果偏低;当称样量为0.2~0.4g时,测量结果较稳定且比0.1g时要高;当称量大于0.4g时,测量数据又显示不稳定,这是因为称样量较大,试样在坩埚内燃烧时出现飞溅现象,导致测量数据不稳定,而且从分析时吸收波形图上看到有二次燃烧的迹象,可能有部分试样燃烧不完全。
这表明样品称样量对测量结果有很大的影响。
因此确定称样量为0.2g。
2.4 样品、助溶剂对碳硫含量分析的成败关键,在于燃烧环节。
为了提高回收率并使数据趋于稳定,助熔剂不可或缺。
钨粒及其合金,是燃烧常用助熔剂。
实验经验表明,助熔剂的加入次序,也对碳硫释放有影响。
助熔剂不仅具有增加样品中导磁物质,从而提高燃烧温度。
还具有增加样品流动性、稀释样品的作用。
分析过程中,样品、助熔剂的叠放次序。
直接影响燃烧结果和分析稳定性。
例如铁基样品直接在氧气下经高频感应而燃烧,反应剧烈,飞溅严重,容易造成燃烧室石英管的破损和陶瓷保护套的污染。
换成以钨粒打底,样品置于上层,发现燃烧室中石英管也很快被污染,陶瓷保护套上粘了一层厚厚的铁屑,很难清理,不仅影响了燃烧管的使用寿命,还阻碍了氧气的供应,从而影响分析结果的稳定性。
将样品置于底层,钨粒置于上层。
分析结束后燃烧室内石英管非常干净,陶瓷热保护套上无金属飞溅,分析结果稳定。
所以分析试样时,要让助熔剂均匀置于上层。
因此本实验样品、助溶剂的加入次序为纯铁、试料、钨粒。
2.2助溶剂配比样品燃烧是否完全是影响分析结果稳定性的关键,W粒能提供较高的热值,透气性好,能降低碳硫释放速度,是高频炉常用的助熔剂;高纯Fe也是很好的助熔剂,将两者混合使用,可以得到很好的碳硫释放曲线。
两者不同的配比的分析结果见表2。
由表2可见,当W粒加入量约为2.0g、纯Fe加入量约为0.35g时,C的释放曲线均为平滑的单峰曲线,C的分析结果接近标准值;当W粒加入量<2.0g时,C释放曲线有双峰出现,且分析结果偏低;当纯Fe加入量>0.3g时,坩埚内有不同程度的喷溅,使C的释放曲线不平滑,分析结果不稳定。
因此,当试样量约为0.20g时,选择W粒加入量约为2.0g、纯Fe加入量0.35 g作为助熔剂。
表2 熔剂配比对分析结果的影响序号W粒加入量/g 纯Fe加入量/g C测定值/%1 1.50020.2003 1.5522 1.50150.2509 1.5433 1.50080.3004 1.5334 2.00120.3011 1.5525 2.00060.3513 1.5656 2.00010.4008 1.5627 2.50070.4006 1.5588 2.50110.4501 1.5549 2.50030.5013 1.5472.3 精密度按照本实验方法测定磷酸铁锂中碳含量,平行进行5组试验,其平均相对标准偏差RSD不大于1.0%,有很高的的精密度。
结果见表3。
表3 精密度实验结果厂家碳含量/% 平均值/% RSD/%天齐 2.829 2.844 2.839 2.824 2.837 2.835 0.28海门 2.147 2.166 2.139 2.153 2.132 2.147 0.61卓能 1.549 1.571 1.562 1.577 1.565 1.565 0.672.4 加标回收实验选择称样量为0.2g,根据1.3分析步骤,以高纯石墨粉(纯度>99.95%)作为标准样品,利用高频红外碳硫仪吸收法进行加标回收法实验。
实验数据如表4所示:表4 加标回收率测定结果序号原称量值/g 原测量值/%加标量/g加标称量值/g加标测量值/%回收率/%1 0.2003 1.565 0.003 0.2033 3.023 100.182 0.2015 1.565 0.003 0.2045 3.015 100.203 0.2021 1.565 0.003 0.2051 3.001 99.874 0.2008 1.565 0.003 0.2038 3.002 99.605 0.3515 1.565 0.007 0.3585 3.502 100.436 0.3507 1.565 0.007 0.3577 3.482 99.737 0.3502 1.565 0.007 0.3572 3.479 99.578 0.3511 1.565 0.007 0.3581 3.512 100.65从表4可以看出,采用加标回收法,得到加标回收率为99.57~100.65%,说明高频红外碳硫仪吸收法的分析结果准确度高。
2.5 方法准确度样品中主要成分磷酸铁锂可以溶于酸溶液,而样品中的C不可溶于酸,因此通过酸溶的方法,不溶物的重量即为碳的重量。
称取0.20g样品,加入15mL盐酸(1+1),盖上表面皿,加热至微沸15min,加入20mL水继续保持微沸10min,用中速滤纸过滤,滤纸过滤前置于烘箱中105℃干燥2h,在干燥器中冷却至室温,称重。
过滤后滤纸置于烘箱中105℃干燥2h,在干燥器中冷却至室温后称重,通过前后重量差计算碳含量。
结果如表5所示。
表5 准确度实验结果序号磷酸铁锂质量/g 前滤纸质量/g 后滤纸质量/g 碳质量分数/%1 10.0001 1.4815 1.6372 1.5572 10.0000 1.4903 1.6473 1.5703 9.9998 1.4872 1.6433 1.5614 10.0005 1.4856 1.6427 1.5715 10.0012 1.4833 1.6394 1.561平均值 1.564碳元素质量分数取5次平均值,得到磷酸铁锂的碳质量分数为1.564%,结果与高频红外碳硫仪吸收法的结果相符。
说明使用高频红外碳硫仪测定磷酸铁锂的碳含量具有很高的准确度。
3 结论本实验采用高频感应炉燃烧后红外吸收法测定磷酸铁锂中碳的含量,试样中的碳经过富氧条件下的高温加热,氧化为二氧化碳气体。
该气体经处理后进入相应的吸收池,对相应的红外辐射进行吸收,由探测器转化为信号,经计算机处理输出结果。
结果表明:该方法测定磷酸铁锂中碳的精密度小于1.0%,此方法准确、快速、灵敏度高,适用于实际样品的分析。
参考文献[1]史世云,温宏利,李冰.高频燃烧-红外碳硫仪测定地质样品中的碳和硫[J].岩矿测试,2001,20(4):267-271[2]袁家义,白雪冰,王卿,等.X 射线荧光光谱法测定地质样品中的氯和硫[J].岩矿测试,2004,33(3):225-227[3]詹秀春,陈永君,郑妙子.地质样品中痕量氯溴和硫的X 射线荧光光谱法测定[J].岩矿测试,2002,21(1):12-18[4]Pasitschniak A. Determination of sulfur content by X-Ray fluorescence in sample containing a single sulfide phase[J].XRS,1986,15(3):97-99.[5]李蕾.氧弹燃烧-离子色谱法测定机油中的氯、硫、磷含量[J].武汉工程大学学报,2009,31(7):38-40[6] GB/T 14265-1993, 金属材料中氢、氧、氮、碳和硫分析方法通则.。