3.2 型材弯曲成形
铝合金型材 弯曲
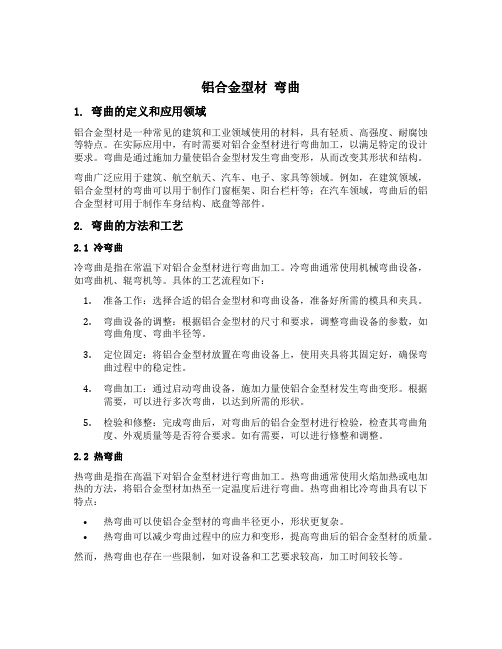
铝合金型材弯曲1. 弯曲的定义和应用领域铝合金型材是一种常见的建筑和工业领域使用的材料,具有轻质、高强度、耐腐蚀等特点。
在实际应用中,有时需要对铝合金型材进行弯曲加工,以满足特定的设计要求。
弯曲是通过施加力量使铝合金型材发生弯曲变形,从而改变其形状和结构。
弯曲广泛应用于建筑、航空航天、汽车、电子、家具等领域。
例如,在建筑领域,铝合金型材的弯曲可以用于制作门窗框架、阳台栏杆等;在汽车领域,弯曲后的铝合金型材可用于制作车身结构、底盘等部件。
2. 弯曲的方法和工艺2.1 冷弯曲冷弯曲是指在常温下对铝合金型材进行弯曲加工。
冷弯曲通常使用机械弯曲设备,如弯曲机、辊弯机等。
具体的工艺流程如下:1.准备工作:选择合适的铝合金型材和弯曲设备,准备好所需的模具和夹具。
2.弯曲设备的调整:根据铝合金型材的尺寸和要求,调整弯曲设备的参数,如弯曲角度、弯曲半径等。
3.定位固定:将铝合金型材放置在弯曲设备上,使用夹具将其固定好,确保弯曲过程中的稳定性。
4.弯曲加工:通过启动弯曲设备,施加力量使铝合金型材发生弯曲变形。
根据需要,可以进行多次弯曲,以达到所需的形状。
5.检验和修整:完成弯曲后,对弯曲后的铝合金型材进行检验,检查其弯曲角度、外观质量等是否符合要求。
如有需要,可以进行修整和调整。
2.2 热弯曲热弯曲是指在高温下对铝合金型材进行弯曲加工。
热弯曲通常使用火焰加热或电加热的方法,将铝合金型材加热至一定温度后进行弯曲。
热弯曲相比冷弯曲具有以下特点:•热弯曲可以使铝合金型材的弯曲半径更小,形状更复杂。
•热弯曲可以减少弯曲过程中的应力和变形,提高弯曲后的铝合金型材的质量。
然而,热弯曲也存在一些限制,如对设备和工艺要求较高,加工时间较长等。
3. 弯曲后的铝合金型材质量控制在铝合金型材弯曲过程中,为了保证弯曲后的铝合金型材的质量,需要进行质量控制。
常用的质量控制方法包括以下几个方面:3.1 原材料选择选择优质的铝合金型材作为原材料,确保其材质和性能符合要求。
典型型材弯曲零件的工艺方法

典型型材弯曲零件的工艺方法摘要:本文就某工程典型型材弯曲零件的加工工艺技术要求出发,对这几类零件的成形难点进行了分析和研究,提出了在成形这二类零件的工艺改进方法,总结了零件的成形规律。
关键词:“收边”“放边”新技术一、前言本文主要介绍防火壁板是如何通过工艺改进实现零件质量提升。
飞机钣金型材零件加工工艺又分为:压下陷型材,压弯型材,滚绕弯型材,拉弯型材,复杂形型材。
型材零件的种类很多,但是从材料的变形性质来看,最终无非就是“收”和“放”两种。
“收”的主要问题是起皱,在型材零件加工过程中比较容易控制,但在一些弯曲半径小的“收边”零件的起皱变形量较大,如不及时平皱还是会造成零件报废。
而“放”的主要问题是拉裂,拉裂在加工过程中由于受到材料塑性极限、受力均匀程度、变形方式、变形条件等因素影响,在加工过程中则不易控制。
二、“收”边类典型零件机翼前缘缘条加工2.1前缘缘条零件特点机翼前缘缘条类型材零件是安装在飞机中外翼最前端的骨架零件,外面连接单曲度的蒙皮,型材缘条类零件安装在蒙皮的内表面。
所以该类零件要根据单曲度的蒙皮的外形变化而变化。
由于前缘蒙皮零件的曲度、角度变化比较大,所以缘条类型材零件的曲度、角度变化也比较大。
2.2前缘缘条零件成形工艺难点在成形零件顶部单曲度弯曲半径中,由于零件弯曲半径R太小,材料截面尺寸比较大,操作空间小,无法用较大的榔头从而大大增加了操作人员的加工难度,所以只能用小榔头和在工艺准备过程中申请的工装在液压机上逐步地校正并配合压高机成形零件的理论外形,直到校正出合格的零件。
2.3前缘缘条零件传统的工艺方法存在问题以前传统的工艺方法是将毛料中间部分的腹板(成形后在零件的顶部)全部铣切掉,只剩下缘条面的材料厚度,打磨完成后再进行拉弯成形,由于拉弯时材料顶部无腹板支撑,且毛料截面尺寸及其角度变化剧烈,因此拉弯成形后零件顶部出现不同深度的凹坑,且在零件顶部有腹板处和无腹板处的交接处因为材料内部应力集中等原因,极其容易产生裂纹,致使零件报废。
管材三维自由弯曲成形技术及装备

三维自由弯曲成形技术是塑性成形领域近年来的一项重要的技术创新,可实现管材、型材、线材精确无模连续弯曲成形,特别适用于复杂空间形状弯曲构件或者弯曲半径连续变化的复杂弯曲构件。
在国内,南航团队率先开展了系统的研发工作,在基础理论、关键技术、数字化装备及重大工程应用上取得了全面进展,实现了对国外同类技术的赶超。
管材三维自由弯曲成形基础理论研究三维自由弯曲成形材料变形规律建立了考虑轴向推力的自由弯曲力学模型,分析了应变中性层移动规律和对管材内外侧壁厚分布的影响,见图1、图2。
结论:轴向推力导致应力应变中性层外移,降低了弯曲外侧的壁厚减薄率,提高了管材成形质量。
图1 管材应变中性层向外弧移动图2 管材内外侧壁厚沿弯曲角度分布三维自由弯曲成形缺陷形成机理针对管材截面畸变及失稳起皱缺陷的形成机理及分布规律进行研究,建立了基于壳体能量的缺陷预测模型。
管材自由弯曲横截面椭化畸变及分布规律见图3、图4,管材开始弯曲部分的横截面畸变率呈现较高的峰值;在弯曲过程的中段和结束部分,弯管横截面畸变率较低,即明显的截面畸变现象出现在过渡段。
图3 管材自由弯曲横截面椭化畸变图4 管材自由弯曲横截面椭化分布规律基于壳体能量原理的起皱预测模型见图5,波纹起皱现象集中出现在圆弧段成形部分。
图5 基于壳体能量原理的起皱预测模型型材弯扭机理建立了方形截面型材自由弯扭理论解析模型,阐明了方形截面型材不同面上的应力应变分布规律。
结论:弯曲内表面受到的应力整体处于下降趋势;弯曲外表面、扭转内表面和扭转外表面的等效应力均呈整体上升趋势;按逆时针方向,扭转外表面、弯曲外表面及扭转内表面上的等效应变分布均呈先下降再增高的趋势。
扭转对弯曲作用机理建立了平椭截面型材自由弯扭过程中截面扭转角与弯曲回弹后半径关系的理论分析模型,揭示了沿平椭型材长轴和短轴弯扭时截面扭转对弯曲变形的影响规律。
三维自由弯曲成形关键技术管材轴线精确解析建立了自由弯曲模具三维运动轨迹模型,将弯曲弧段进行划分(图6):将单弯分为过渡段1、中间圆弧段和过渡段2,代表偏心、停留和回程。
3.2 型材弯曲成形
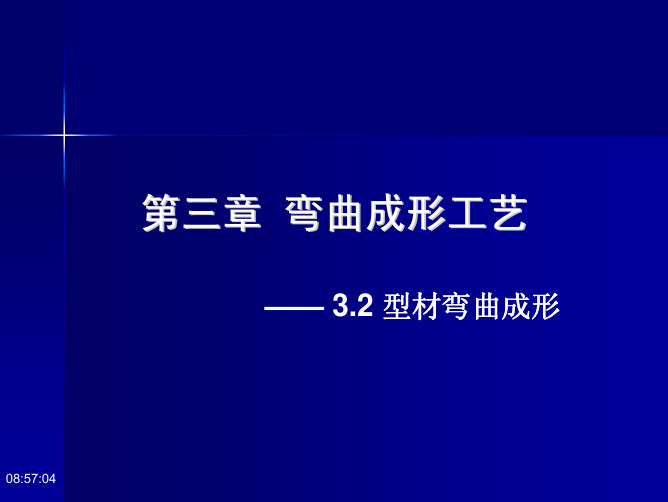
加热温度495〜503°C,在水中冷却,通常采 用; • 不完全退火状态: 加热温度350〜370°C,空气冷却,用于中间 工序; • 完全退火状态: 加热温度390〜430°C,然后以每小时30的冷 却速度降低至250〜270°C,最后在空气中冷 却,用于形状比较复杂的型材零件;
08:57:04
型材滚弯机
滚弯等曲率 型材滚弯机
滚弯变曲率 型材滚弯机
立式的
卧式的
四轮滚弯机
08:57:04
六轮滚弯机
三、型材滚弯基本原理
1、滚弯过程 2、滚轮中心距的确定
基本假设(——为简化工程计算提出的假设) : *在弯曲滚轮之间的变形区域内,近似地认为型材是等曲
率的圆弧 *忽略滚轮与型材之间的摩擦力对弯曲变形的影响 *应力沿腹板高度的分布采用线性近似实际应力曲线
08:57:04
• 下料与校正 下料与
冶金工厂供应的挤压型材,技术条 件较宽,例如允许非直线度2 mm/m,角 度偏差±2 〜 3º等,所以在成形为飞机 的长桁、框缘之前必须加以校正。 校正的主要内容有校直、校扭、校 角。
08:57:04
• 拉弯成形
拉弯前必须正确选择材料的供应状态 。对于硬铝(LY12)最好是新淬火状 态或退火状态。淬火及时效状态只能 用于弯曲半径较大的情况。
08:57:04
滚弯型材
挤压类
板弯类
等曲率
变曲率
角材
丁字型材
收边角材
08:57:04
放边角材
收边型材
放边型材
板弯型材零件 Π 形 型 材 圆 弧 形 型 材
角 形 型 材
半 圆 形 型 材
复 杂 形 型 材
08:57:04
型材拉弯成形及回弹分析

This work in the dissertation may provide a rational and useful method for
improving the quality of stretch bending forming of extrusions and a useful tool for
两华大学硕十学位论文
数。该方法可通过拉弯件轮廓曲线上布点的密度来控制模具轮廓曲线上曲率分 段的多少和误差大小。本文还通过有限元分析方法计算了拉弯型材的回弹量, 用于评估拉弯模轮廓面的回弹修正量,以及拉弯件的校形余量的减少情况。本 .文的工作为提高汽车和飞机拉弯件的质量和促进工装的数字化设计提供了一合 理有效的方法。
两华大学硕十学位论文
assumptions.In bending stages friction unit model and stress·strain analysis and bending moment was detailed.The analysis of stretch bending spring-back was introduced and the formula for calculating sheet and extrusions spring—back radius
★能成形空间结构复杂的型材零件 ★能成形屈强比大的型材弯曲零件 ★具有不同工艺方法相结合的综合成形特点 ★弯曲精度高,回弹小 因此型材拉弯在飞机、汽车型材弯曲件的生产中得到了非常广泛的应用。 在飞机生产中,飞机框肋上的缘条、机身前后段、发动机短仓的长桁等尺 寸大的型材弯曲件是组成飞机骨架的关键零件,并直接影响到飞机的气动力外 形,形状精度要求很高。’在汽车生产中,拉弯主要用于加工车身结构和保险杠 的中空铝型材弯曲件,在保持与钢铁制件同样的抗冲击强度条件下,能减轻车 体重量,降低使用成本。拉弯工艺可实现铝型材的高精度弯曲,但由于拉弯成 形中可能会出现壁厚减薄破裂、起皱、截面畸变等成形缺陷,而这些成形缺陷 与型材的材料性能、截面形状及工艺参数这些因素密切相关,非常复杂。 目前拉弯成形性的研究迫切需要解决以下两个关键技术问题【l】:1.合理确 定拉弯成形过程中的工艺参数;2.准确预测拉弯零件的回弹量。实际生产中拉 弯模修正量及工艺参数的确定主要以实际经验或通过试错法来解决,即根据经 验反复调整修模量,改变主拉力、补拉力等工艺参数。有时还需要多次预拉弯 及热处理,最终成形后还要进行人工校形。这种方法成本高,时间长,形状精 度难以保证。随着产品加工精度要求的日益提高,近/净成形的要求逐步增加, 数字化设计制造也对拉弯成形工艺提出了新的要求,传统的拉弯成形工艺已不 能满足现代生产的需要。随着科技的进步,技术的不断的革新,特别是CAD/CAE 技术的不断发展,大型的CAD通用软件为拉弯模具的设计提供了强大的技术支 持。在CAD软件环境下,可以得到零件的一些有效的几何信息,例如通过几何分 析功能,可以得到整条曲线的曲率分布及其大小,可以检查曲面的质量。为模
板材弯曲成型的实施步骤

板材弯曲成型的实施步骤介绍板材弯曲成型是一种常见的加工方法,可以用于制作各种具有曲线形状的零件,如灯具、家具、艺术品等。
本文将介绍板材弯曲成型的实施步骤,包括准备工作、材料选择、工具和设备、操作方法等。
准备工作在进行板材弯曲成型之前,需要做好一些准备工作,确保顺利进行。
以下是准备工作的步骤:1.清洁工作区:将工作区域清洁干净,清除任何杂物和尘土。
2.准备工具和材料:准备好所需的工具和材料,如切割工具、夹具、胶水等。
3.安全措施:确保有足够的通风和光线,佩戴适当的安全装备,如手套和护目镜。
材料选择选择合适的材料对于板材弯曲成型至关重要。
以下是一些常用的材料选择:•木材:木材是一种常用的材料,适用于制作家具和艺术品。
常见的木材类型有橡木、胡桃木等。
•金属:某些金属材料也可以进行弯曲成型,如铝合金、不锈钢等。
•塑料:塑料材料具有较好的韧性和成型性,适用于制作各种曲线形状的零件。
工具和设备在进行板材弯曲成型之前,需要使用一些工具和设备来帮助完成任务。
以下是一些常见的工具和设备:1.切割工具:用于将板材切割成适当的大小和形状。
常见的切割工具有锯子和电锯。
2.加热设备:用于加热板材,使其变得柔软和易于弯曲。
常见的加热设备有热风枪和热板。
3.夹具:用于固定板材,保持其在加热和冷却过程中的形状。
常见的夹具有木夹和金属夹。
4.胶水:用于固定板材的曲线形状,使其保持弯曲状态。
选择适合材料的胶水,并确保完全干燥后才移除夹具。
操作方法进行板材弯曲成型时,需要按照一定的操作方法进行。
以下是一些常用的操作方法:1.切割板材:根据设计要求,使用切割工具将板材切割成所需的大小和形状。
2.加热板材:使用加热设备加热板材,使其变得柔软。
根据材料的不同,加热温度和时间也会有所不同。
3.弯曲板材:在加热后的板材上施加适当的弯曲力量,使其弯曲成所需的形状。
此时,需要使用夹具将板材固定,并保持一段时间使其冷却。
4.固化胶水:使用适合材料的胶水,在板材弯曲部位涂抹一层胶水,然后将板材夹紧。
型材在生产中弯曲变形原因与处理方法
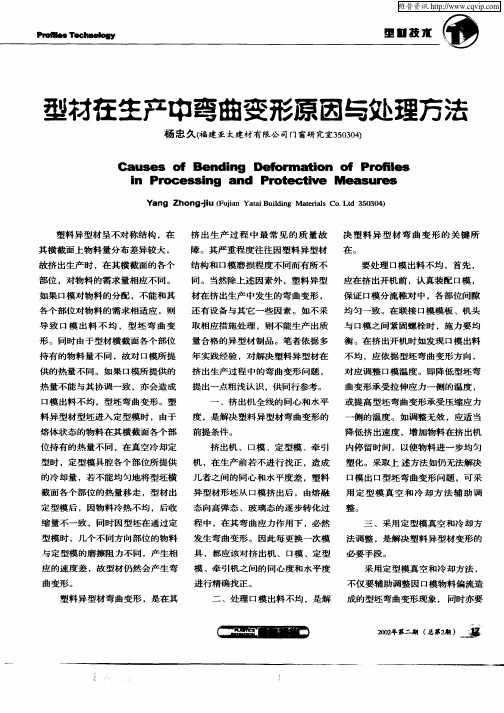
要处 理 口模 出料 不 均 ,首 先 , 应在 挤 出开 机 前 ,认真 装 配 口模 ,
保 证 口模 分 流稚 对 中 ,各部 位 间 隙
如 果 口模 对 物料 的分 配 ,不 能 和 其 材 在挤 出生 产 中发 生 的 弯 曲变 形 ,
各 个 部位 对 物料 的需 求 相适 应 ,则 还 有设 备 与 其它 一些 因素 。如 不 采 均 匀 一致 。在联 接 口模 模板 、机头 导 致 口模 出料 不 均 ,型 坯 弯 曲 变 取 相 应 措施 处 理 ,则不 能 生 产 出质
一
供 的热 量 不 同 。如 果 口模 所 提供 的 挤 出生 产 过程 中 的弯 曲变 形 问题 , 热 量 不能 与其 协调 一 致 ,亦 会 造成 提 出一 点粗 浅认 识 ,供 同行 参考 。 口模 出料 不均 ,型坯 弯 曲 变形 。塑 料 异型 材 型坯 进 入 定型 模 时 ,由于
均 形 成 的 弯 曲应 力 。有 可 能 收 到一 并 不 是 一 成不 变 的 。作 为 塑料 异 型 材 生 产 与管理 人 员 ,在 日常 生产 过 程 中 ,应 了解 、熟 悉 模 具 的 工 作 、 磨 损 特 性 ,密 切 关 注 模 具 工 作 质
量 ,并 做 好 监 测 记 录 。视 情 况 随 时
轴 向位 置 的 冷 却水 量 。 当定 型模 内
型模 时 ,相 对而 言 由于 未 充满 定 型
型 模 螺栓 上紧 。但 该方 法 处 理 塑 料
模 ,磨 擦 阻 力 较小 。如 减 少该 侧 定 异 型 材 弯 曲变 形 ,易 导 致 型材 内应 型 模冷 却 ,则 使该 侧 型 坯 温 度 高 , 磨 擦 阻 力增 加 ,移 动速 度 减慢 。 由 于两 者 的 综 合作 用 ,型 材 的弯 曲变 形不 但 得 不 到有 效 控 制 ,反而 会 加
型材弯曲的原因及解决方法
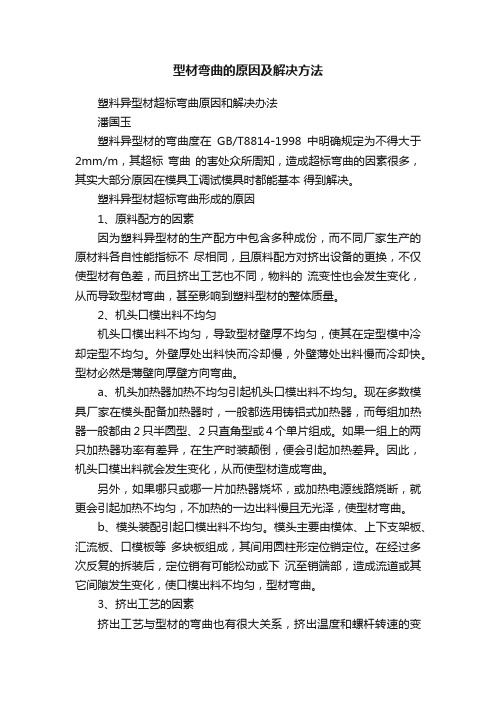
型材弯曲的原因及解决方法塑料异型材超标弯曲原因和解决办法潘国玉塑料异型材的弯曲度在GB/T8814-1998中明确规定为不得大于2mm/m,其超标弯曲的害处众所周知,造成超标弯曲的因素很多,其实大部分原因在模具工调试模具时都能基本得到解决。
塑料异型材超标弯曲形成的原因1、原料配方的因素因为塑料异型材的生产配方中包含多种成份,而不同厂家生产的原材料各自性能指标不尽相同,且原料配方对挤出设备的更换,不仅使型材有色差,而且挤出工艺也不同,物料的流变性也会发生变化,从而导致型材弯曲,甚至影响到塑料型材的整体质量。
2、机头口模出料不均匀机头口模出料不均匀,导致型材壁厚不均匀,使其在定型模中冷却定型不均匀。
外壁厚处出料快而冷却慢,外壁薄处出料慢而冷却快。
型材必然是薄壁向厚壁方向弯曲。
a、机头加热器加热不均匀引起机头口模出料不均匀。
现在多数模具厂家在模头配备加热器时,一般都选用铸铝式加热器,而每组加热器一般都由2只半圆型、2只直角型或4个单片组成。
如果一组上的两只加热器功率有差异,在生产时装颠倒,便会引起加热差异。
因此,机头口模出料就会发生变化,从而使型材造成弯曲。
另外,如果哪只或哪一片加热器烧坏,或加热电源线路烧断,就更会引起加热不均匀,不加热的一边出料慢且无光泽,使型材弯曲。
b、模头装配引起口模出料不均匀。
模头主要由模体、上下支架板、汇流板、口模板等多块板组成,其间用圆柱形定位销定位。
在经过多次反复的拆装后,定位销有可能松动或下沉至销端部,造成流道或其它间隙发生变化,使口模出料不均匀,型材弯曲。
3、挤出工艺的因素挤出工艺与型材的弯曲也有很大关系,挤出温度和螺杆转速的变化,同样会引起型材弯曲,有时还会引起牵引抖动及型材的局部有波浪产生。
4、定型模的冷却和装配的因素。
定型模长期使用会使冷却水路或多或少的结垢,水流量相应减少,引起型材定型冷却不均匀不充分而发生弯曲。
同样,长时间生产对真空气路不清理或清理不彻底,真空吸附力也大大减小(相反,真空表反映的数据增大),使型材不能紧贴定型模,热交换和冷却不充分或不均匀而变形弯曲。
小弯曲半径薄壁不锈钢管推弯成形工艺研究

小弯曲半径薄壁不锈钢管推弯成形工艺研究
王彦岐;徐雪峰;范玉斌;肖洁;曾祥;危立明;谢君
【期刊名称】《材料科学》
【年(卷),期】2024(14)4
【摘要】相对弯曲半径越小,壁厚越薄,管材弯曲成形的成形难度越大。
本文针对外径D = 86 mm,壁厚t = 0.8 mm,弯曲半径1 D的小弯曲半径不锈钢管开展了推弯成形工艺研究。
基于有限元与实验相结合的方法,探究了管坯几何结构、反推力以
及润滑方式对弯管成形质量的影响,结果表明:推弯成形管坯应采用补偿端头减少弯
曲内侧材料堆积,避免起皱,对于90˚的目标弯管零件,45˚的补偿端头最为合适;反推
力过小时,支撑力不足易起皱,反推力过大会导致摩擦增加阻碍弯曲内侧材料流动,增加起皱风险;通过分区域润滑,针对性调节材料流动,能够减少弯曲内侧增厚起皱风险。
【总页数】12页(P415-426)
【作者】王彦岐;徐雪峰;范玉斌;肖洁;曾祥;危立明;谢君
【作者单位】南昌航空大学航空制造工程学院南昌;南昌航空大学工程训练中心南昌
【正文语种】中文
【中图分类】TG3
【相关文献】
1.薄壁小弯曲半径管弯管模及工艺设计
2.薄壁小弯曲半径的弯管工艺
3.6A02铝合金异形截面小弯曲半径薄壁管液压成形工艺研究
4.小弯曲半径钛管差温推弯成形工艺研究
5.小弯曲半径厚壁热揻弯管成形工艺数值模拟
因版权原因,仅展示原文概要,查看原文内容请购买。
双曲面不锈钢型材零件的弯曲成形工艺-精选文档

双曲面不锈钢型材零件的弯曲成形工艺.、八、一前言双曲面不锈钢型材零件的弯曲成形工艺项目中有两项不锈钢零件,形状虽简单,但尺寸较大,且材料厚度较厚,成形、敲修都困难。
文章通过对零件和材料进行充分工艺性分析,比较各种可行的加工方案,形成最优加工方案,并最终生产出合格零件,满足了生产的要求。
1零件的材料和工艺性分析1.1 零件的材料分析这两项不锈钢型材零件的材料为“ 17-7PH,料厚为5 2.03mm 17-7PH材料是典型的半奥氏体沉淀硬化型不锈钢。
其退伙供应状态的主要机械性能为:抗拉强度6、=1034MPa屈服强度6 s= 724Mpa延伸率5 =10%可以看出这种材料在常温下成形有一定难度,需较大的成形力,零件易回弹等。
1.2零件的工艺性分析此类零件的形状和典型剖面尺寸见图1。
图1从图1 中可以看出这是较典型的型材类零件,实现该零件的断面形状,方法很多,也不困难,但零件的弧面及其下陷通常需在以下两种受力情况下才可以实现:(1)若b 面不受力,而a 面受轴向的压应力和横向拉应力,则a 面的材料聚积、增厚,在工装中形成弧面。
下陷受上、下工装的挤压而产生。
(2)若a、b 面均受均匀拉应力,则a 面的材料变薄、弯曲;b 面的材料聚积、增厚,在工装中形成弧面。
而下陷只能单独成形。
因此,从以上零件的材料和工艺性分析可以看出:该零件的材料成形性能非常不好,而且其零件的形状特点,使零件的工艺性不稳定,给零件的成形增加了很大的难度,选择恰当的加工方案,成为解决问题的关键。
2确定加工成形方案2.1加工成形方案的分析、论证加工成形方案的确定主要考虑三个因素:质量、成本、周期(成本和周期包括工装),这两个加工方案也主要是从这三方面进行综合分析、论证。
2.1.1拉弯成形。
拉弯成形是将轧压成形后的直型材在拉弯模上进行弯曲,弯曲的同时在零件的a、b 两面施加均匀的轴向拉力,使材料截面内的应力分布都变为拉应力,夹钳与拉弯模的相对移动迫使零件贴胎虽然经验分析告诉我们“拉弯成形”卸载后零件的回弹较大(如图2),必须对拉弯模进行反复修正回弹量,反复试验拉弯,直至加工出合格零件。
一种型材拉弯成形方法

一种型材拉弯成形方法引言型材是广泛应用于建筑、机械制造和装饰等行业的一种重要材料。
在使用型材时,我们经常需要对其进行弯曲,以满足特定需求。
传统的型材拉弯成形方法存在一些问题,例如成形效率低、成形质量难以保证等。
本文介绍了一种基于数控技术的型材拉弯成形方法,可以提高成形效率和质量,并减少人力投入。
方法概述该型材拉弯成形方法主要包括以下几个步骤:1. 型材预处理在进行拉弯成形前,需要对型材进行预处理,以确保成形过程的顺利进行。
预处理包括清洗型材表面、去毛刺、除锈等。
2. 软件编程在型材拉弯成形之前,需要进行数控编程。
通过使用专门设计的软件,根据设计要求绘制型材的弯曲轨迹。
软件可以实现对型材拉弯成形过程的控制和监测。
3. 机床设备调试在进行型材拉弯成形之前,需要对机床设备进行调试。
通过调节机床设备的参数和检查硬件设备,确保机床设备的正常运行。
4. 型材拉弯成形按照编好的数控程序,将型材固定在机床上,并由数控设备控制机床进行型材拉弯成形。
数控设备会根据预设的弯曲轨迹,通过控制下料架的运动和力度,使型材在预定的位置和角度上进行弯曲。
整个过程由计算机实时控制和监测,因此可以实现精确控制和监测。
5. 成形检测与调整在型材拉弯成形完成后,需要对成品进行检测和调整。
可以通过比对成品和设计要求的差异来进行调整,使成品达到设计要求。
优势与应用相比传统的型材拉弯成形方法,本文介绍的基于数控技术的型材拉弯成形方法具有以下优势:1. 高效性:采用数控技术,可以实现自动化生产,提高了成形效率。
同时,数控设备可以快速调整成形角度和位置,减少了调整时间。
2. 精度高:数控设备可以精确控制和监测型材的成形过程,保证了成品的质量和精度。
3. 灵活性强:通过软件编程,可以根据不同的型材和设计要求,制定不同的弯曲轨迹。
因此,适用于不同尺寸和形状的型材。
4. 节约人力:采用数控技术,减少了人力投入,提高了生产效率。
该型材拉弯成形方法适用于各种建筑、机械制造和装饰等行业。
质量管理三级文件工艺部分
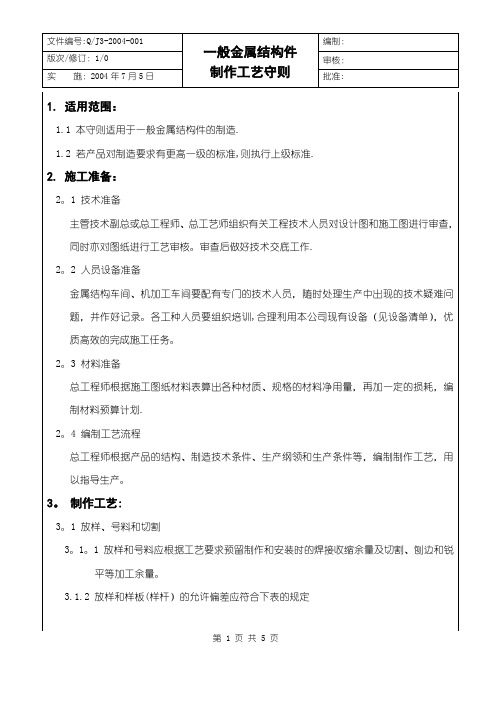
第 2 页共 5 页项目允许偏差零件宽度、长度±3.0mm边缘缺棱 1.0mm型钢端部垂直度 2.0mm3.2 矫正和成型3。
2.1 碳素结构钢在环境温度低于-16℃,低合金结构钢在环境温度低于-12℃时,不得进行冷矫正和冷弯曲。
3。
2。
2 当零件采用热加工成形时,加热温度宜控制在900~1000℃;碳素结构钢在温度下降到700℃之前、低合金结构钢在温度下降到800℃之前,应结束加工;低合金结构钢应缓慢冷却。
3。
2.3 矫正后的钢材表面,不应有明显的凹面或损伤,划痕深度不得大于0.5mm。
钢材矫正后的允许偏差应符合下表的规定。
项目允许偏差图例钢板的局部平面度t≤14 1.5 t >14 1。
0型钢弯曲矢高l/1000且不大于5。
0角钢肢的垂直度b/100 双肢栓接角钢的角度不得大于90°槽钢翼缘对腹板的垂直度b/80工字钢、H型钢翼缘对腹板的垂直度b/100且不大于2.0第 3 页共 5 页第 4 页共 5 页第 5 页共 5 页如图一:图一图二2。
5。
7 封头由瓣片和顶圆板对接制成时,焊缝只允许是径向和环向的。
径向焊缝之间的最小距离应大于3S(封头板厚)且不小于100毫米,中心顶圆板直径应小于1/2Dg(一般取1/2Dg—100毫米),如图二,顶园板一般不采用拼接.2.6 号料样板应符合图形,其公差要求如下:2。
6。
1 样板长宽方向偏差为0~1毫米。
2.6.2 样板上相邻孔中心距偏差及孔中心位移为≤0.5毫米。
2。
6。
3 规则的号料样板对角线之差为≤1毫米。
2。
7 检验用样板应有足够刚性,且符合如下要求:2.7。
1检验面应连续、光滑,尺寸应准确。
2.7.2筒体、封头、锥体、弯管(曲率)、支承圈等圆弧检验样板的弧长,一般按中心角不小于60°制作.2。
8 筒体的展开下料尺寸一般按下列公式计算:L =π(D+△φ)+H中其中:L—筒体下料展开长度,毫米图三3。
1.3筒节划线公差3.1。
铝合金板材弯曲成型性能
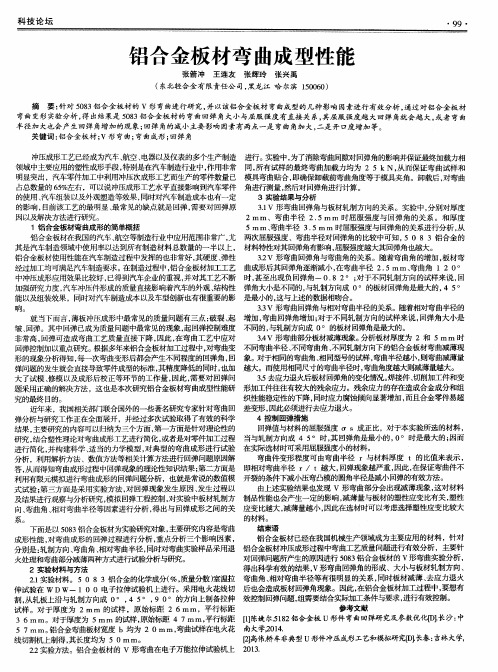
冲压成形工艺已经成为汽车 、 航空 、 电器以及仪表 的多个生产制造 进行。 实验中, 为了消除弯曲间隙对回弹角的影响并保证最终加载力相 领域中主要应用的塑性成形手段 , 特别是在汽车制造行业 中, 作用非常 同, 所有试样的最终弯曲加载力均为 2 5 k N, 从而保证弯曲试样 和 明显突出,汽车零件加工 中利用冲压次成形工艺而生产的零件数量已 模具弯 曲贴合 , 即确保卸载前弯曲角度等于模具夹角。卸载后 , 对弯曲 占总数量的 6 5 %左右,可以说 冲压成形工艺水平直接影响到汽车零件 角进行测量 , 然后对 回弹角进行计算。 的使用 、 汽车组装 以及外观塑造等效果 , 同时对汽车制造成本也有一定 3 实验 结果与 分析 的影 响 , 目前 该工 艺 的最 明 显 、 最 常 见 的缺 点 就 是 回 弹 , 需 要 对 回 弹原 3 . 1 V 形弯曲回弹角与板材轧制方 向的关系。实验中, 分别对厚度 因以及解决方法进行研究。 2 mm 、弯 曲半径 2 . 5 I l l m 时屈服强度 与回弹角 的关 系。和厚度 1铝 合金 板材 弯 曲成 形 的简 单概括 5 mm 、 弯 曲半径 3. 5 mm 时屈服强度与回弹角 的关 系进行分析 , 从 铝合金板材在我国的汽车、 航空等制造行业中应用范围非常广 , 尤 两次屈服强度 、弯曲半径对回弹角的比较中可知 , 5 0 8 3铝合金的 其是汽车制造领域 中使用率以达到所有制造材料总数量的一半以上 , 材料特性对其回弹角有影响, 屈服强度越大其回弹角也越大。 铝合金板材使用性能在汽车制造过程 中发挥的也非常好, 其硬度 、 性 3 . 2 V形弯曲回弹角与弯曲角的关 系。随着弯曲角 的增加 , 板材弯 经过加工均可满足汽车制造要求。 在制造过程中, 铝合金板材加工工艺 曲成形后其回弹角逐渐减小 , 在弯曲半径 2. 5 mm、 弯曲角 1 2 0。 甚至出现负 回弹角一 0. 8 2。 ; 对于不同轧制方向的试样来说 , 回 中冲压成形应用效果 比较好 , 已得到汽车企业的重视 , 并对其工艺不断 时, 加强研究力度 , 汽车冲压件形成的质量直接影响着汽车的外观 、 结构性 弹角大小是不同的, 与轧制方 向成 0。的板材回弹角是最大的, 4 5。 能以及组装效果 ,同时对汽车制造成本以及车型创新也有很重要的影 是最小的, 这与上述的数据相吻合 。 3 . 3 V形弯曲回弹角与相对弯 曲半径的关系。随着相对弯曲半径的 响。 就当下而言 , 薄板 冲压成形 中最常见的质量问题有三点 : 破裂 、 起 增加 , 弯曲回弹角增加; 对于不同轧制方向的试样来说 , 回弹角大小是 皱、 回弹。其中回弹已成为质量问题 中最常见 的现象 , 起回弹控制难度 不同的, 与轧制方向成 0 。的板材回弹角是最大的。 3 4v形弯曲部分板材减薄现象。 分析板材厚度为 2和 5 mm 时 非常高, 回弹可造成弯曲工艺质量直接下降 , 因此 , 在弯曲工艺中应对 回弹控制加以重点研究 。 根据多年来铝合金板材加工过程中, 对弯 曲变 不同弯 曲半径 、 不同弯曲角 、 不 同轧制方向下的铝合金板材弯曲减薄现 相同型号的试样, 弯曲半径越小 , 则弯曲减薄量 形的现象分析得知 , 每一次弯曲变形后都会产生不 同程度的回弹角, 回 象。对于相同的弯曲角 、 弯曲角度越大则减薄量越大。 弹问题的发生就会直接导致零件成型的标准 , 其精度降低的同时 , 也加 越大。而使 用相同尺寸的弯曲半径时 , 3 . 5 去应力退火后板材 回弹角的变化情况。 焊接件、 切削加工件和变 大了试模 、 修模以及成形后校正等环节 的工作量 , 因此 , 需要对回弹问 题采用正确的解决方法 , 这也是本次研究铝合金板材弯曲成型性能研 形加工件往往有较大的残余应力。残余应力的存在造成合金成分和组 织性能稳定性的下降, 同时应力腐蚀倾 向显著增加 , 而且合金零件易超 究的最终 目的。 近年来 ,我国相关部门联合国外的一些著名研究专家针对弯曲回 差变形 , 因此必须进行去应力退火。 弹分析与研究工作正在全面展开 ,并经过多次试验取得了有效的科学 4控制回弹措施 回弹值与材料的屈服强度 盯 s成正比,对于本实验所选的材料 , 结果 , 主要研究的内容可以归纳为三个方面, 第一方面是针对理论 f 生 的 5 o时, 其 回弹角是最小的 , 0 。时是最大的; 因而 研究 , 结合塑性理论对弯 曲成形工艺进行简化 , 或者是对零件加工过程 当与轧制方向成 4 进行简化 , 并构建科学 、 适 当的力学模型 , 对典型的弯曲成形进行试验 在实际选材时可采用屈服强度小的材料 。 弯曲件变形程度可 由弯曲半径 r与材料厚度 t的比值来表示 , 分析 ,利用解析方法 、数值方法等相关计算方法进行回弹问题原因解 回弹现象越严重 , 因此, 在保证弯曲件不 答, 从而得知弯曲成形过程中回弹现象的理论性知识结果 ; 第- - -W面是 即相对弯曲半径 r/ t越大, 利用有限元模拟进行弯曲成形的回弹问题分析 ,也就是常说的数值模 开裂的条件下减小压弯凸模的圆角半径是减小回弹的有效方法。 由上述实验结果也发现 v形弯曲部分会 出现减薄现象 , 这对材料 式试验 ; 第三方面是采用实验方法 , 对回弹现象发生原因 、 发生过程以 减薄量与板材的塑性应变比有关 , 塑性 及结果进行观察与分析研究 , 模拟 回弹工程控制, 对实验 中板材轧制方 制品性能也会产生一定的影响, 减薄量越小 , 因此在选材时可以考虑选择塑 陛应变 比较大 向、 弯曲角 、 相对弯 曲半径等因素进行分析 , 得 出与回弹成形之间的关 应变 比越大 ,
弯曲成形工艺 PPT课件

总结提高 学生归纳
1
弯曲变形过程 弯曲变形特点
?
2
影响回弹的因素 减小回弹的措施
?
3
最小弯曲半径 影响因素 弯曲毛坯尺寸的 确定
?
《汽车结构及制造技术》
作业题
1、简述弯曲变形过程及弯曲变形特点 2、简述影响弯曲件回弹的主要因素 3、简述影响最小相对弯曲半径rmin/t的因素
《汽车结构及制造技术》
将不对称形状的弯曲件组合成对称弯曲件弯曲,然后 再切开,使坯料弯曲时受力均匀,不容易产生偏移
《汽车结构及制造技术》
6.3 弯曲工艺计算
6.3.1 弯曲力的计算
拟定弯曲工艺和选择设备的重要依据。
由变形过程的自由弯曲阶段和校正弯曲阶段对应有自由 弯曲力和校正弯曲力。
⑴ 自由弯曲力
图3-26 软凹模弯曲《源自车结构及制造技术》6.2.2 弯裂分析及工艺设计
1.最小相对弯曲半径的概念 最小相对弯曲半径是指:在保证毛坯弯曲时外表面不发
生开裂的条件下,弯曲件内表面能够弯成的最小圆角半径与 坯料厚度的比值,用rmin/t来表示。该值越小,板料弯曲的性
能也越好。
2. 影响最小弯曲半径的因素 (1)材料的力学性能 (2)工件的弯曲中心角(图6-13)
曲最好使用同一基准定位。
•
(2)结构中要能防止毛坯在变形过程中发生位移,毛坯的安放和
制件的取出要方便、安全和操作简单。
•
(3)模具结构尽量简单,并且便于调整修理。对于回弹性大的材
料弯曲,应考虑凸模、凹模制造加工及试模修模的可能性以及刚度和
强度的要求。
《汽车结构及制造技术》
6.4.1典型弯曲模具的结构
(3)板材的纤维方向(图6-14) (4)板料的冲裁断面质量和表面质量
铝合金型材弯曲成形制造技术
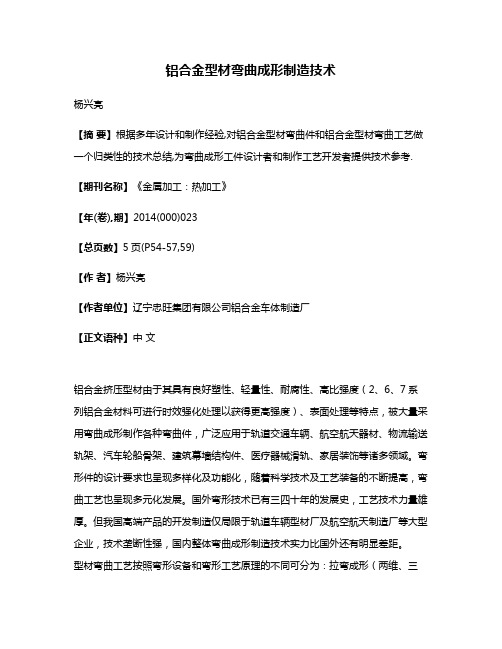
铝合金型材弯曲成形制造技术杨兴亮【摘要】根据多年设计和制作经验,对铝合金型材弯曲件和铝合金型材弯曲工艺做一个归类性的技术总结,为弯曲成形工件设计者和制作工艺开发者提供技术参考.【期刊名称】《金属加工:热加工》【年(卷),期】2014(000)023【总页数】5页(P54-57,59)【作者】杨兴亮【作者单位】辽宁忠旺集团有限公司铝合金车体制造厂【正文语种】中文铝合金挤压型材由于其具有良好塑性、轻量性、耐腐性、高比强度(2、6、7系列铝合金材料可进行时效强化处理以获得更高强度)、表面处理等特点,被大量采用弯曲成形制作各种弯曲件,广泛应用于轨道交通车辆、航空航天器材、物流输送轨架、汽车轮船骨架、建筑幕墙结构件、医疗器械滑轨、家居装饰等诸多领域。
弯形件的设计要求也呈现多样化及功能化,随着科学技术及工艺装备的不断提高,弯曲工艺也呈现多元化发展。
国外弯形技术已有三四十年的发展史,工艺技术力量雄厚。
但我国高端产品的开发制造仅局限于轨道车辆型材厂及航空航天制造厂等大型企业,技术垄断性强,国内整体弯曲成形制造技术实力比国外还有明显差距。
型材弯曲工艺按照弯形设备和弯形工艺原理的不同可分为:拉弯成形(两维、三维)、辊弯成形、压弯成形、绕弯成形。
按照工件形状的不同又可分为:二维弯形工件(见图1)、空间三维弯形工件(见图2)。
下面,按照弯形设备和弯形工艺原理对弯形工艺进行归类总结。
1.拉弯成形工艺(1)拉弯成形工作原理(二维)拉弯过程基本分为3个步骤:第一步,设备拉伸缸钳口夹住材料并给型材施加预拉伸力,达到材料屈服强度。
第二步,拉弯机回转缸加载弯曲回转,拉伸缸按照程序设定轴向拉力,使型材围绕拉弯模具做贴合运动而使材料成形。
第三步,根据材料变形回弹情况增加补拉伸(拉弯设备结构示意见图3)。
拉弯成形过程中,工件在弯曲的同时,拉伸缸始终给工件施加轴向拉力,材料长度伸长部分始终被拉伸缸牵引补偿,这就避免了材料的起皱趋向,能够得到良好的弧度效果。
- 1、下载文档前请自行甄别文档内容的完整性,平台不提供额外的编辑、内容补充、找答案等附加服务。
- 2、"仅部分预览"的文档,不可在线预览部分如存在完整性等问题,可反馈申请退款(可完整预览的文档不适用该条件!)。
- 3、如文档侵犯您的权益,请联系客服反馈,我们会尽快为您处理(人工客服工作时间:9:00-18:30)。
• 夹头设计:
08:57:04
五、工艺规程设计
1、型材零件制造工艺性分析 对型材的一般性工艺要求: * 型材种类的选择 * 截面形状的选择 * 材料种类的选择 * 型材的形状 * 内部元件 2.工艺规程与工艺装备
08:57:04
工艺规程
1、下毛料 2、检验 3、拉弯成形 4、淬火 5、拉弯校形 6、检验 7、按外形样板划线压下陷 8、铣缺口与端头 9、按切钻样板划线钻导孔 10、检验 11、阳极化 12、涂底漆
08:57:04
收边角材滚弯时的斜弯现象
角材滚弯时的扭转变形
08:57:04
限制收边滚弯角材斜-扭变形方法之一
08:57:04
08:57:04
限制收边滚弯角材斜-扭变形方法之二
2、剖面角度的改变
原因:在导轮以外的变形区缘条上表面
没有受任何约束。弯曲滚轮对型材作用 力的合力P′不通过弯曲中心(如图) 而引起扭转变形。 处理该问题的方法之一是采用六轮滚弯 机进行滚弯,斜扭问题解决了,剖面的 角度也就保持不变。
第三章 弯曲成形工艺
—— 3.2 型材弯曲成形
08:57:04
3.2 型材弯曲成形
• 3.2.1 型材滚弯成形 • 3.2.2 型材拉弯成形 • 3.2.3 型材绕弯成形
08:57:04
3.2.1 型材滚弯成形
一、型材滚弯零件分类 二、型材滚弯机 三、型材滚弯基本原理 四、型材滚弯的一般性问题 五、滚轮的构造与设计 六、控制型材滚弯回弹量的方法
08:57:04
滚弯型材
挤压类
板弯类
等曲率
变曲率
角材
丁字型材
收边角材
08:57:04
放边角材
收边型材
放边型材
板弯型材零件 Π 形 型 材 圆 弧 形 型 材
角 形 型 材
半 圆 形 型 材
复 杂 形 型 材
08:57:04
挤压型材零件 滚 ( 绕 ) 弯 型 材
压 下 陷 型 材
压 弯 型 材
型材拉弯过程中的主要问题是:
• 加载方式的选择 • 回弹半径的计算与模具合理外形 的确定 • 轴向预拉力与轴向总拉力的确定
08:57:04
二、型材拉弯机
1.转台式拉弯机 此类机床构造简单,制造方便,但是对 于长度很大的型材零件,由于拉伸作动筒的 行程较大,给机床设计带来一定的困难。 2.转臂式拉弯机 此类拉弯机的基本原理是拉弯模与台面 固定不动,支臂与拉伸作动筒绕拉弯模转 动,使零件产生弯曲变形,并保持轴向拉力 始终与拉弯模相切。
M max P = ( x − R 2sinα )cosα
'
上导轮对型材施加的弯曲力 P 为 1
2M max P1 = 2P cosα = x − R 2sinα
'
08:57:04
四、型材滚弯的一般性问题
1、斜弯曲-扭转变形 2、剖面角度的改变 3、腹板与缘条错动 4、收边腹板失稳起皱
5、型材的两端保留直线段问题
通用拉弯模的基本原理是利用各种 小尺寸的标准元件——模块,按需 要的模具合理外形组合排列。拉弯 一批零件后可以迅速改作它用。模 块设计时应注意:工作半径不宜过 小,以免引起皱纹;宽度不能过 大,通用性可大些;固定可靠且迅 速。
08:57:04
08:57:04
• 夹头设计:
夹头内的夹块必须按型材的剖面更换。 由于型材在拉弯过程中受到很大的轴向 拉力,夹块的齿面应保持可靠地咬住型 材毛料,均匀传递拉力。为了防止将整 个拉力集中于型材的某一剖面,齿面前 端应带有平缓的过渡区,所有夹块应与 型材表面均匀接触,并使拉力的合力近 似地通过型材剖面的形心。
4、定位孔的位置
定位孔的位置应满足两个要求: 模具的外形应与在两旁钳口内准 备拉弯的型材相切; 模具的中心线与机床轴线重合。
08:57:04
5、安全装置
型材拉弯时可能因为偶然因素 而突然断裂,向外弹开而伤及 人员,在操作台前考虑加防护 罩或挡板。
08:57:04
安全装置
08:57:04
通用拉弯模
08:57:04
1.转台式拉弯机
08:57:04
2.转臂式拉弯机
08:57:04
转臂式拉弯机
08:57:04
08:57:04
三、型材拉弯基本原理
1、回弹现象的分析 2、回弹半径的计算方法 基本假设(——为简化工程计算提出的假设) : * 平截面假设 * 型材拉弯属于纯弯曲,亦即不考虑剪力的影 响 * 采用折线型近似实际应力曲线,并认为拉伸 曲线与压缩曲线相同 3、轴向预拉力与总拉力的确定
08:57:04
1、拉弯模的剖面形状
模具的剖面形状应符合于材型剖面的特点, 间隙δ一般取0.2~0.5mm。
A=B+△B+(2~10)
08:57:04
拉弯模的剖面形状
08:57:04
2、拉弯模的长度
模具的有效长度应较零件切割长度 每边增加10mm;两端圆角半径R不 宜小于20mm;工作中机床的夹头应 能自由进入模具的后方,以便保证 正确的轴向拉力作用方向,并减少 毛料两端的工艺余量。因此在必要 时模具两端开出缺口形状。
08:57:04
收边型材腹板失稳起皱
5、型材的两端保留直线段问题
• 原因: -- 与板料滚弯类似。弯曲滚轮与导轮之 间有一定的水平中心距 • 减小两端余量的方法有: -- 调整机床,缩短弯曲滚轮的中心距; -- 几个零件合并起来滚弯而后分开。
08:57:04
五、滚轮的构造与设计
型材滚弯机所用的工艺装备是上、下导 轮与弯曲滚轮。 对于斜角为零或斜角很小的角材或丁字 型材,可采用通用滚轮进行滚弯。 对于斜角较大与剖面形状复杂的型材, 可采用专用滚轮进行滚弯。
拉 弯 型 材
复 杂 形 型 材
08:57:04
存在问题:
• 回弹半径的计算与滚轮中心距的确定 • 斜弯曲-扭转变形 • 剖面角度的改变 • 腹板与缘条的错动 • 腹板失稳起皱 • 两端保留直线段 • 滚轮的设计
08:57:04
二、型材滚弯机
08:57:04
数控四轴型材滚弯机(VPR-SPEC-CNC))
08:57:04
• 下料与校正 下料与
冶金工厂供应的挤压型材,技术条 件较宽,例如允许非直线度2 mm/m,角 度偏差±2 〜 3º等,所以在成形为飞机 的长桁、框缘之前必须加以校正。 校正的主要内容有校直、校扭、校 角。
08:57:04
• 拉弯成形
拉弯前必须正确选择材料的供应状态 。对于硬铝(LY12)最好是新淬火状 态或退火状态。淬火及时效状态只能 用于弯曲半径较大的情况。
• 新淬火状态:
加热温度495〜503°C,在水中冷却,通常采 用; • 不完全退火状态: 加热温度350〜370°C,空气冷却,用于中间 工序; • 完全退火状态: 加热温度390〜430°C,然后以每小时30的冷 却速度降低至250〜270°C,最后在空气中冷 却,用于形状比较复杂的型材零件;
08:57:04
08:57:04
滚轮的设计
• 型材内边缘与滚轮之间的合理间隙值选取 范围为0.1~0.2毫米。 • 滚轮的截面形状必须符合型材截面。 • 滚轮的直径按如下原则确定:
—— 应适当增大上下导轮的直径,以使型材和 导轮间具有较大的接触面积,改善型材在 导轮间的支持状况。 —— 应尽量减少弯曲轮和导轮之间的中心距, 以便缩短型材在其间的悬空段长度。
原因:相对弯曲半径较小的收边角材,如果滚轮间
的间隙过大,就可能产生腹板失稳起皱的现象。
解决问题的原则是:从腹板的两侧加以足够的约
束,防止失稳时腹板朝厚度方向起皱的可能性;或 者减少“压缩曲杆”的细长比 。
方法之一是:滚轮间的垫圈厚度的尺寸应加以控
08:57:04
制,一般应比腹板厚度的实际尺寸约大0.1~0.2毫 米。其次是调整机床、缩短弯曲滚轮间距。
08:57:04
08:57:04
(a)
08:57:04
型材滚弯过程的受力分析
导轮对型材施加外力就像一承受集中载荷 P1 的简支梁, 如图6-3(b)所示,其最大弯矩为
M max = ( P' α )( x − R 2sinα ) cos
式中
x α = arcsin Rnq + H + R2
故得弯曲滚轮对型材施加的弯曲力 P'为
08:57:04
曲率中心异侧的型材三种拉弯成形方法
* 新淬火状态的毛料先拉伸、后弯曲,随后 按辅助凸模弯曲,最后拉校; * 新淬火状态的毛料先拉伸、后按辅助凸模 弯曲,随后在按凸模弯曲,最后拉校; * 新淬火状态的毛料先拉伸、后弯曲,拉校 及利用辅助凸模压紧毛料,然后按辅助凸模 弯曲,最后进行拉校;
08:57:04
板料压弯与型材拉弯应力分布的比较
08:57:04
卸载时应力与回弹应变的关系
08:57:04
四、拉弯模设计
根据产量分为两类: 专用拉弯模 —— 用于批生产 通用拉弯模 —— 用于试制生产
08:57:04
专用拉弯模设计要点如下:
1、拉弯模的剖面形状 2、拉弯模的长度 3、典型结构模具与强度 4、定位孔的位置 5、安全装置
08:57:04
一、型材滚弯零件分类
飞机上的型材主要用于做骨架(机身、 机翼以及进气道的隔框、加强缘条等),分 为挤压型材和板弯型材两大类。 滚弯的挤压型材可分为等曲率的与变曲 率的两种。常用的型材剖面有角材与丁字形 型材。
08:57:04
与外蒙皮连接的一般是收边的,如图(a)、 (b)所示,与内蒙皮连接的一般是放边的,如 图(c),(d)所示。
08:57:04
曲率中心异侧的型材三种拉弯成形方法
08:57:04
• 压下陷