车外圆端面和台阶
端面、外圆 台阶轴
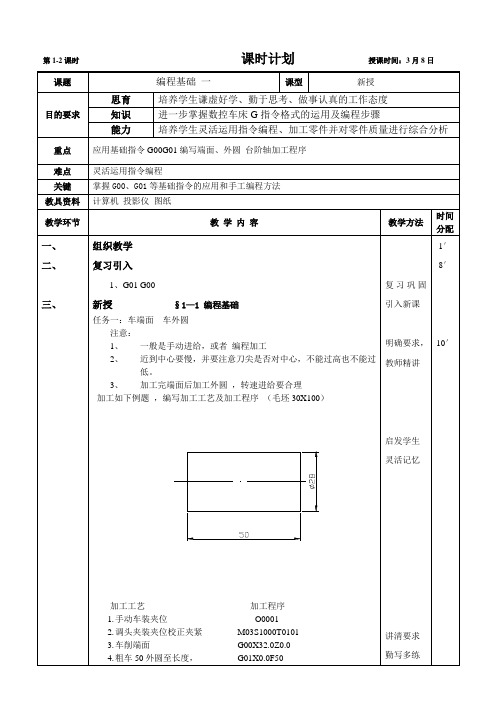
第1-2课时课时计划授课时间:3月8日课题编程基础一课型新授目的要求思育培养学生谦虚好学、勤于思考、做事认真的工作态度知识进一步掌握数控车床G指令格式的运用及编程步骤能力培养学生灵活运用指令编程、加工零件并对零件质量进行综合分析重点应用基础指令G00G01编写端面、外圆台阶轴加工程序难点灵活运用指令编程关键掌握G00、G01等基础指令的应用和手工编程方法教具资料计算机投影仪图纸教学环节教学内容教学方法时间分配一、二、三、组织教学复习引入1、G01 G00新授§1—1 编程基础任务一:车端面车外圆注意:1、一般是手动进给,或者编程加工2、近到中心要慢,并要注意刀尖是否对中心,不能过高也不能过低。
3、加工完端面后加工外圆,转速进给要合理加工如下例题,编写加工工艺及加工程序(毛坯30X100)加工工艺加工程序1.手动车装夹位O00012.调头夹装夹位校正夹紧M03S1000T01013.车削端面G00X32.0Z0.0复习巩固引入新课明确要求,教师精讲启发学生灵活记忆讲清要求1′8′10′留0.5mm精车余量G00X28.50Z2.05.精车50的外圆至最终尺寸G01Z-55.0F1006.测量误差分析补刀G00X32.0Z2.07.取50长换刀切断G00X28.08.拆下工件G01Z-55.0F80G00X100Z100T0202S600G00X32.0Z-54.0G01X0.0F30.0G00X100.0Z100.0M30任务二:车台阶轴注意:1、左偏刀两把粗车刀和精车刀主切削刃偏角要稍大于90度2、粗车进给量、背吃刀量要较大。
3、刀具切削角参数都偏小,以保证刀具的强度。
加工工艺1.手动车装夹位2.调头夹装夹位校正夹紧3.车削端面4.分刀粗车ø50ø40外圆,至长度留0.5mm精车余量5.精车ø40 ø50的外圆至最终尺寸并倒角6.测量误差分析补刀加工7.取总长50长换刀切断8.拆下工件工程程序O0002M03S1000T0101 ; G01Z-20;G00X52.0Z0.0; X46. 0 结合实际图样,初步领会具体应用教师提出要求,学生10′5′四、五六、G01X-1F0.1; X50.0Z-22;Z2.0 Z-45G00X50.5; G00X100Z100G01Z-45.0F0.2; T0202G00X52.0Z2.0; G00X53.0Z-45.0;G00X46.0; G01X2F0.05;G01Z-20.0; X52.0;G00X52 G00X100.0Z100.0G00Z2.0; M30;X42.0;G01Z-20.0;X52.0;G00Z2.0;X40.5;G01Z-20.0;G00X52.0;G0Z2.0;G01X36.0F0.1;G01Z0.0;X40.0Z-2.0;课堂练习课堂小结通过本节课掌握车端面、车外圆、车台阶的加工工艺及编程方法课后作业整理上图程序课后反思领会学生反复练习师生共同回顾,突出51′七通过上课所讲的编程实例,使学生进一步了解一般的编程流程:包括工艺分析、基点坐标数值计算、加工程序的编写。
外圆台阶端面加工6
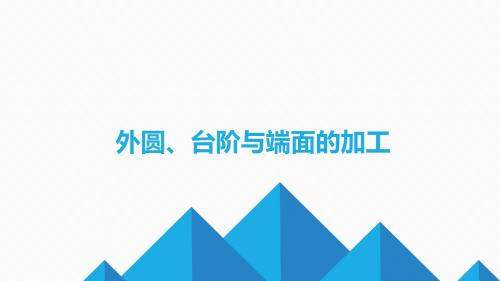
(3)进给量的确定 可查阅切削用量手册选取每转进给量f,由公式计 算进给速度:v=fn 粗车一般选取为0.3~0.8mm/r;精车常取 0.1~0.3mm/r
2、轴加工相关编程指令格式
1)快速点定位 G00格式:G00x-z-; 注意:G00不能设置在工件上,一般应离开工件2-5mm 的安全距离,移动过程中不能和机床、夹具干涉。如图 3-1-9所示
外圆、台阶与端面的加工
主要内容
零件图工艺分 轴加工相关编
析
1
程指令格式
2
常见外圆的检 测及使用方法
3
课堂训练
4
1、零件图工艺分析
1)零件结构和尺寸分析 2)加工工序的划分 3)加工顺序的确定 4)确定刀具的进给路线 5) 数控车切削用量的选择
1)零件结构和尺寸分析
图1
图 2
如图1所示的零件,需用三把不同的切槽刀来 切槽,在没有特殊需要的情况下,显然是不合理 的;如果改成如图2所示的结构,只需要一把刀具 就可以切出三个槽。这样即减少刀具数量又节省 了换刀时间,还少占用刀架刀位。
图3
图4
再如图3所示加工过渡比较大的轴台阶时, 不能直接加工成直角台阶,这样容易造成台阶处 应力集中,零件在使用过程中容易断裂;正确的 应加工成如图4所示的结构,端面过渡处应有比 较大的圆弧半径,结构允许时可设计成过渡圆锥。
除此以外,我们还要对零件图的精度及技术 要求的分析,主要分析图纸上的尺寸偏差,粗糙度, 同心度,位置度等精度要求,只有在此基础上才能 对加工方法、装夹方式、刀具和切削用量做出正确 合理的选择。
4)确定刀具的进给路线
(2)巧设换到点,如图3-1-8a所示,A点离工件较 远,换刀时空运行较长,如果改设3-1-8b所示那样, 大大缩短了换刀时空距离。 (3)最短的切削进给路线,提高生产效率,降低刀 具刀量的确定 在工艺系统刚性和机床功率允许的条件下,尽可能选取较大 的背吃刀量,以减少进给次数,当零件的精度要求较高时, 其所留精车余量一般为0.1-0.5mm。 (2)主轴转速的确定 n a、根据实践经验来确定 b、查表计算 特别是交流变频调速数控车床,切削速度确定后,利用公式 v=πdn/1000计算主轴转速 c、车螺纹时主轴转速:n≤1200/p -k 其中p为螺纹的螺距或者导程,k为保险系数,一般取80.
车外圆、端面和台阶
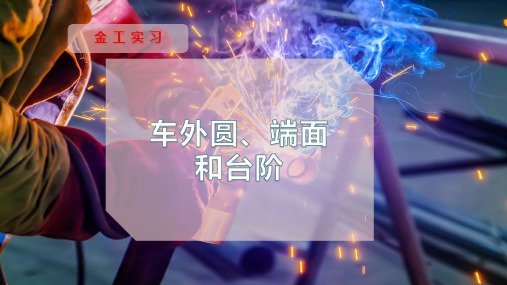
车外圆、端面和台阶
精车是为了保证工件的尺寸精度和表面质量,因 此要适当减小副偏角,刀尖处应磨成有小圆弧的过渡刃, 适当加大前角,并用油石仔细地打磨车刀前后面。在选 取切削用量时优先选取较高的切削速度,再取较小的进 给量,最后根据工件尺寸确定背吃刀量。
粗车和精车开始前都必须进行试切,试切方法及 其步骤如图1-28所示。
车外圆、端面和台阶
图1-30 车台阶
车外圆、端面和台阶
台阶长度的测量如图1-31所示。对于未注长度公差的台阶长 度可用钢直尺测量;对于尺寸公差要求高的台阶长度,需用深度 游标卡尺测量;对大批生产的台阶长度,可用样板测量。
图1-31 台阶长度的测量
金工实习
车外圆、端面和台阶
图1-28 试切方法及其步骤
车外圆、端面和台阶
车外圆、端面和台阶
车外圆、端面和台阶
1Байду номын сангаас2 车端面
车端面时,常用弯头车刀进行,如图1-29所示。 车刀安装时,刀尖必须准确地对准工件的旋转中心, 否则将在端面中心处留有凸台,且易崩坏刀尖。车削 端面时,切削速度由外向中心会逐渐减小,将影响端 面的表面粗糙度,因此工件切削速度要选高些。接近 中心时可停止自动进给,改用手动缓慢进给至中心, 可保护刀尖。
车外圆、端面和台阶
1.3 车台阶
阶梯轴上不同直径的相邻两轴段组成台阶,可采用 90°外圆车刀或45°端面弯头车刀车出台阶外圆,如图130所示;再用主偏角大于90°的外圆车刀横向进给车出 环形端面,也可用切断刀横向进给车出环形端面。用外 圆刀或切断刀车台阶端面时,端面与台阶外圆处应接刀 平整,不能产生内凹外凸。粗车台阶时,长度余量应放 在大直径轴段。多阶梯台阶车削时,应先车最小直径台 阶,从两端向中间逐个进行。
数控车床加工工艺编程-外圆、端面、台阶轴加工
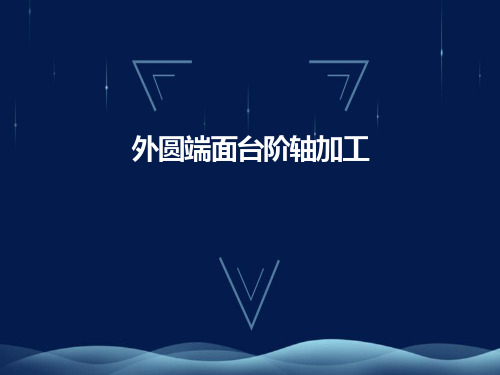
用,因此它的技术要求一般有:
各挡外圆之间的同轴度、外圆
和台阶平面的垂直度、台阶平
面的平面度以及外圆和台阶平
面相交处的清角。
车削台阶时,通常使用90°外圆偏刀。 车刀的装夹应根据粗、精车的特点进行安 装。如粗车时余量多,为了增加切削深度, 减少刀尖压力,车刀装夹可取主偏角小于 90°为宜(一般为85°~90°)。精车时为了 保证台阶平面和轴心线垂直,应取主偏角 大于90°(一般为93°左右)。
fr —每转进给量,(mm/r)
3、切削速度V
主运动的线速度叫切削速度,单位为m/min。 车削外圆时的切削速度计算公式为:
V=πdn/1000
其中: d—工件待加工表面的直径,(mm);
n—工件的转速,(r/min); V—切削速度,( m/min)。
车削台阶轴 在同一工件上,有几个直径大小不同的圆 柱体连接在一起像台阶一样,就叫它为台 阶工件。俗称台阶为“肩胛”。台阶工件 的车削,实际上就是外圆和平面车削的组 合。故在车削时必须兼顾外圆的尺寸精度 和 (1台)台阶阶长工度件的的技要术求要求。
车削台阶工件的方法
车削台阶工件,一般分粗、精车进行。车削前根据 台阶长度先用刀尖在工件表面刻线痕,然后按线痕进 行粗车。粗车时的台阶每档均略短些,留精车余量。 精车台阶工件时,通常在机动进给精车外圆至近台阶 处时,以手动进给代替机动进给。当车至平面时,然 后变纵向进给为横向进给,移动中滑板由里向外慢慢 精车台阶平面,以确保台阶平面垂直轴心线。
车削台阶轴时的注意事项
1)台阶平面和外圆相交处要清角,防止产生凹坑和出 现小台阶。 2)车刀没有从里向外横向切削或车刀装夹主偏角小于 90°,以及刀架、车刀、滑板等发生移位会造成台阶平 面出现凹凸。 3)台阶工件的长度测量,应从一个基准面量起,以防 累积误差。 4)刀尖圆弧较大或刀尖磨损会使平面与外圆相交处出 现较大圆弧。 5)主轴没有停妥,不能使用量具进行测量。 6)使用游标卡尺进行测量时,卡脚应和测量面贴平, 以防卡脚歪斜产生测量误差。松紧程度要适当,以防过 紧或过松造成测量误差;取下时,应把紧固螺钉拎紧, 以防副尺移动,影响读数的正确。
外圆、端面、台阶的车削

刀具磨损 部位 前刀面
刀具磨损产生 以较高的切削速度和较大 切削厚度(ac>0.5㎜)切 削塑性材料时 较低的切削速度和较小切 削厚度(ac<0.1㎜)切削 塑性材料时或切削脆性材 料时
表示方法 用月牙洼深度KT 表示 用棱面高度VB表 示
后刀面
前、后刀 面同时磨 损
同时出现 中等切削速度和中等进给 在前、后 量切削塑性材料时 刀面上
3.切削力、切削热与切削温度 切削力、 切削力 (1)切削力 切削加工时,工件材料抵抗刀具切削所产生的阻力成为称为切削力。切削力 来源于工件的弹性变形和塑性变形抗力以及切屑对前刀面和后刀面的摩擦力(图a) a)主切削力Fz 主运动速度方向的分力。是最大的一个分力,消耗功率最多, 是计算机床功率、车刀强度、设计夹具和选择切削用量的依据。Fz力会使刀杆产 生弯曲(图b),因此,装车刀时尽量使刀杆伸出短些。 b)进给抗力Fx 进给方向的分力,纵向车削外圆时又称为轴向力。 c)切深抗力Fy 切深方向的分力,纵向车削外圆时又称为径向力。Fy力会使 工件在水平面内弯曲(图c),主要影响工件的形状精度,也是产生车削振动的主 要因素。
4.刀具的磨损与刀具的寿命 刀具的磨损与刀具的寿命 刀具的磨损是指在车削过程中,车刀的前刀面和后刀面处于剧烈的摩擦和切削 热作用下,使车刀变钝而失去了正常的切削能力。 刀具的磨损是由摩擦和切削热 两个方面的因素造成的。
a) 后刀面磨损
b)前刀面磨损 c)前、后刀面同时磨损
刀具磨损 的形式 前刀面磨 损 后刀面磨 损
剧烈磨损
5. 切屑的形状及控制 切屑的形状 车削金属时,被切削层金属经受了较大的塑性变形变成切屑。切屑在流动和 卷曲过程中碰到障碍物,切屑将附加变形。因工件材料、车刀几何角度及切削用 量的不同,切屑附加变形的程度也不同,车削塑性材料时,常会出现“C”字形切 屑、螺旋状切屑和带状切屑等
3(车外圆及车端面)

项目三车削外圆及端面一、教学目的1.掌握手动、机动进给车削外圆、端面和台阶的方法。
2.掌握调整机动进给手柄位置的方法。
3.会用划线盘找正工件。
4.掌握游标卡尺的使用方法,会用游标卡尺测量工件的外圆、用钢直尺测量长度并检查平面凹凸,达到图样的精度要求。
5.掌握试切削,试测量的方法车削外圆。
6.遵守操作规程,养成文明生产,安全生产的良好习惯。
二、教学重点及难点1.教学重点掌握车削外圆、端面和台阶的方法2.教学难点刻度盘的计算及应用三、实训内容四、准备工作设备:切割机、车床工具:45°和90°硬质合金外圆车刀、通用装夹工具一套量具:钢直尺、游标卡尺、千分尺。
五、工艺分析由于该零件较短,没有特殊的同轴度要求,加工时采用三爪自定心卡盘直接装夹进行加工。
考虑到倒角和去毛刺的需要,先加工大端直径再调头加工另一端。
其机械加工过程卡片和机械加工工序卡见附表。
六、操作过程1.检查毛坯尺寸,装夹一端外圆,伸出长度大于60mm,用划针盘找正夹紧;2.车平端面,粗精车D1、长45mm,倒角2×45°;3.调头垫铜皮,装夹外圆,伸出长度大于70mm,找正夹紧,粗精车端面至总长L1;4.用钢直尺刻线长L2mm,粗车D2,留精车余量1~2mm;5.用钢直尺刻线长L1mm,粗车D3,留精车余量1~2mm;6.精车D2和L2、D3和L3至图形要求,倒角2×45°和1×45°。
七、质量检查内容及评分标准八、安全及注意事项1.车削时防止车刀碰着卡盘。
2.转动刀架时,防止车刀与工件、卡盘发生碰撞。
3.测量或清除铁屑时,要先停车,工件转动时不准用手触摸工件。
4.车削过程中戴好防护眼镜。
九、容易产生的问题和注意事项1、工件端面中心留有凸头,原因是刀尖没有对准工件中心,偏高或偏低。
2、端面不平有凹凸,产生原因是进刀量过深、车刀磨损,滑板移动、刀架和车刀紧固力不足,产生扎刀或让刀。
车床加工评估参考

车床加工评估参考车床是利用工件的旋转运动和刀具的相对切削运动来实现加工的,可进行外圆、端面、倒角、台阶、清槽、切断、锥面、孔、螺纹、滚花、成形面等…十余种加工方式。
依车床的功能形能和使用刀具的不同又可分为多种类型。
以下内容结合工模课实际情况,对普通卧式车床加工S45材质(单件)时的工时评估作说明:一、外圆加工:⒈1加工刀具选用硬质合金车床,工件直径设定大于50mm,自动走刀速度设定为每分钟100mm,每次进刀深度(即去除材料余量)依次设定为单边…1mm、1mm、0.5mm。
⒈2加工工时包括:a.识读图纸、材料(或工件)装夹、刀具准备;(5分钟)b.加工外圆依公式:T=(长度÷100)×(进刀次数+1)+1计算时间,进刀次数依加工余量和每次进刀量判断,两个“1”分别表示修正尺寸时加工的一刀和变更加工参数时设定的1分钟;c.测量时间;(1分钟)d.当长径比(长度兴直径的比值)较大,采用顶尖支撑加工时,另增加顶针孔加工时间。
(3分钟)⒈3加工工时评估范列:a.长度50mm,余量5mm,加工工时为9分钟;b.长度100mm,余量5mm,加工工时为11分钟。
⒈⒋细长轴加工不适合以上方式计算工时。
二、端面加工:2.1加工刀具选用硬合金车刀,走刀速度设定为每分钟100mm,进刀次数设定为3次。
2.2加工工时包括:a.刀具调整;(0.5分钟)b.端面依公式:T=(半径÷100)×3+0.5计算时间。
三、倒角加工:3.1加工刀具选用硬质合金车刀,采用手动进刀。
3.2加工工时包括:a.刀具调整;(0.5分钟)b.加工倒角。
(0.5分钟)3.3加工工时评估范列:一次装夹情况下倒0.5mm角,1分钟加工2个倒角1.5mm以上角1分钟加工1个。
四、台阶加工:4.1加工内容包括外圆加工和端面加工两部分。
4.2加工工时包括:a.识读图纸、刀具调整;(2分钟)b.加工外圆依公式:T=(长度÷100)×(进刀次数+1)+1计算时间;c.加工端面依公式:T2=(深度÷100)×3+1计算时间;d.测量时间。
项目三外圆、端面、台阶的车削资料要点

机械工程系实习讲义首页教学过程及教学内容[课前组织]1.检查学生出勤情况,填写教学日志。
2.检查学生装束是否整齐3.讲述要求:纪律、卫生、学习方法、如何作笔记4.宣布本项目的学习任务与目的要求:[设备工量具准备]任务一车削基础知识(1)了解车削加工时切削用量的选择原则。
(2)了解金属车削的过程。
(3)基本掌握车削过程中表面质量的控制方法。
(4)了解车刀切削时磨损的原因与刀具寿命的含义。
任务二外圆、端面、台阶的车削(1)掌握试切法与试测法控制外圆尺寸的方法。
(2)熟练掌握工件找正和安装方法。
(3)掌握零件尺寸的测量方法和对质量进行简单分析。
任务三切外沟槽、切断(1)了解切断刀和车槽刀的种类和用途。
(2)了解切断刀和车槽刀的组成部分和角度要求。
(3)掌握掌握切断刀和车槽刀的刃磨方法。
(4)掌握外沟槽的车削方法和测量方法。
(5)了解车沟槽时产生的问题和防止方法。
(6)掌握直进法和左右车削法切断工件。
[入门指导]任务一车削的基础知识导语:在车削加工时,合理选择切削用量对提高劳动生产率,延长刀具的使用寿命,保证加工质量,降低生产成本有着重要的意义。
一、车削加工时切削用量的选择1.合理选择切削用量的含义衡量切削用量是否合理的标准:①能否保证加工零件的质量要求(主要是加工精度和表面质量)②在加工系统刚性许可的条件下,是否充分利用了车床功率。
③在保证加工质量和刀具寿命的条件下,是否充分发挥了刀具的切削性能。
2.选择切削用量的原则(1)切削深度的选择(2)进给量的选择(3)切削速度的选择•选择切削速度的一般原则如下1)车刀材料使用硬质合金车刀可比高速工具钢车刀的切削速度快。
2)工件材料切削强度和硬度较高的工件时,因为产生的热量和切削力都比较大,车刀容易磨损,所以切削速度应选得低些。
脆性材料如铸铁工件,虽然强度不高,但车削时形成崩碎切屑,热量集中在切削刃附近,不易传散。
因此,切削速度也应取得低一些。
3)表面粗糙度要求表面粗糙度值小的工件,如用硬质合金车刀车削,切削速度应取得高些;如用高速工具钢车刀车削,切削速度应取得低些。
3 外圆、端面、台阶
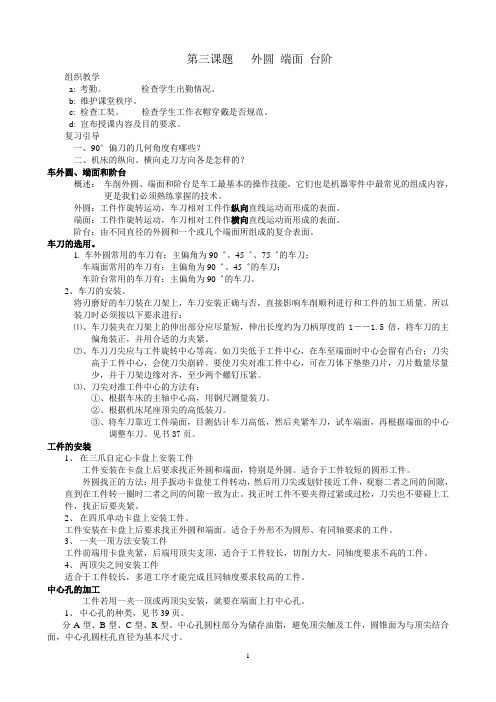
第三课题外圆端面台阶组织教学a: 考勤。
检查学生出勤情况。
b: 维护课堂秩序。
c: 检查工奘。
检查学生工作衣帽穿戴是否规范。
d: 宣布授课内容及目的要求。
复习引导一、90°偏刀的几何角度有哪些?二、机床的纵向、横向走刀方向各是怎样的?车外圆、端面和阶台概述:车削外圆、端面和阶台是车工最基本的操作技能,它们也是机器零件中最常见的组成内容,更是我们必须熟练掌握的技术。
外圆:工件作旋转运动,车刀相对工件作纵向直线运动而形成的表面。
端面:工件作旋转运动,车刀相对工件作横向直线运动而形成的表面。
阶台:由不同直径的外圆和一个或几个端面所组成的复合表面。
车刀的选用。
1. 车外圆常用的车刀有:主偏角为90゜、45゜、75゜的车刀;车端面常用的车刀有:主偏角为90゜、45゜的车刀;车阶台常用的车刀有:主偏角为90゜的车刀。
2、车刀的安装。
将刃磨好的车刀装在刀架上,车刀安装正确与否,直接影响车削顺利进行和工件的加工质量。
所以装刀时必须按以下要求进行:⑴、车刀装夹在刀架上的伸出部分应尽量短,伸出长度约为刀柄厚度的1――1.5倍,将车刀的主偏角装正,并用合适的力夹紧。
⑵、车刀刀尖应与工件旋转中心等高。
如刀尖低于工件中心,在车至端面时中心会留有凸台;刀尖高于工件中心,会使刀尖崩碎。
要使刀尖对准工件中心,可在刀体下垫垫刀片,刀片数量尽量少,并于刀架边缘对齐,至少两个螺钉压紧。
⑶、刀尖对准工件中心的方法有:①、根据车床的主轴中心高,用钢尺测量装刀。
②、根据机床尾座顶尖的高低装刀。
③、将车刀靠近工件端面,目测估计车刀高低,然后夹紧车刀,试车端面,再根据端面的中心调整车刀。
见书37页。
工件的安装1、在三爪自定心卡盘上安装工件工件安装在卡盘上后要求找正外圆和端面,特别是外圆。
适合于工件较短的圆形工件。
外圆找正的方法:用手扳动卡盘使工件转动,然后用刀尖或划针接近工件,观察二者之间的间隙,直到在工件转一圈时二者之间的间隙一致为止。
项目三外圆、端面、台阶的车削
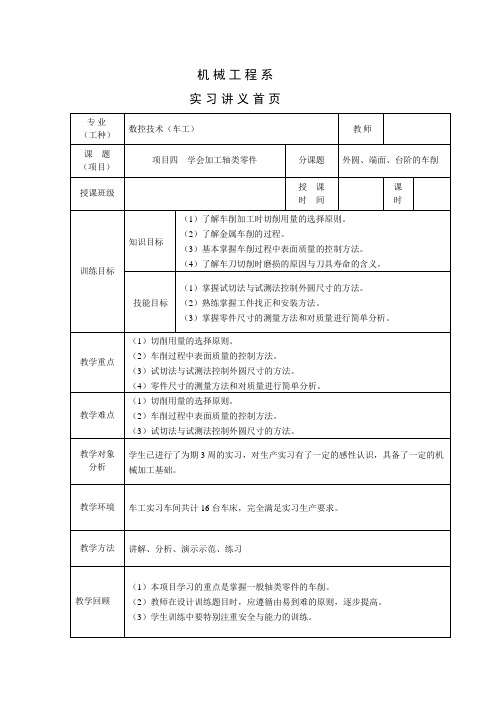
机械工程系实习讲义首页教学过程及教学内容[课前组织]1.检查学生出勤情况,填写教学日志。
2.检查学生装束是否整齐3.讲述要求:纪律、卫生、学习方法、如何作笔记4.宣布本项目的学习任务与目的要求:[设备工量具准备]任务一车削基础知识(1)了解车削加工时切削用量的选择原则。
(2)了解金属车削的过程。
(3)基本掌握车削过程中表面质量的控制方法。
(4)了解车刀切削时磨损的原因与刀具寿命的含义。
任务二外圆、端面、台阶的车削(1)掌握试切法与试测法控制外圆尺寸的方法。
(2)熟练掌握工件找正和安装方法。
(3)掌握零件尺寸的测量方法和对质量进行简单分析。
任务三切外沟槽、切断(1)了解切断刀和车槽刀的种类和用途。
(2)了解切断刀和车槽刀的组成部分和角度要求。
(3)掌握掌握切断刀和车槽刀的刃磨方法。
(4)掌握外沟槽的车削方法和测量方法。
(5)了解车沟槽时产生的问题和防止方法。
(6)掌握直进法和左右车削法切断工件。
[入门指导]任务一车削的基础知识导语:在车削加工时,合理选择切削用量对提高劳动生产率,延长刀具的使用寿命,保证加工质量,降低生产成本有着重要的意义。
一、车削加工时切削用量的选择1.合理选择切削用量的含义衡量切削用量是否合理的标准:①能否保证加工零件的质量要求(主要是加工精度和表面质量)②在加工系统刚性许可的条件下,是否充分利用了车床功率。
③在保证加工质量和刀具寿命的条件下,是否充分发挥了刀具的切削性能。
2.选择切削用量的原则(1)切削深度的选择(2)进给量的选择(3)切削速度的选择•选择切削速度的一般原则如下1)车刀材料使用硬质合金车刀可比高速工具钢车刀的切削速度快。
2)工件材料切削强度和硬度较高的工件时,因为产生的热量和切削力都比较大,车刀容易磨损,所以切削速度应选得低些。
脆性材料如铸铁工件,虽然强度不高,但车削时形成崩碎切屑,热量集中在切削刃附近,不易传散。
因此,切削速度也应取得低一些。
3)表面粗糙度要求表面粗糙度值小的工件,如用硬质合金车刀车削,切削速度应取得高些;如用高速工具钢车刀车削,切削速度应取得低些。
车工工艺学与技能训练ppt课件

车刀刀尖与工件回转中心应等高 a)刀尖对正中心 b)刀尖过高 c)刀尖过低
d)留有凸头 e)刀尖崩碎
20
2. 车刀对中心的方法
车刀对中心的方法
21
3. 车刀的夹紧
22
ห้องสมุดไป่ตู้
三、刻度盘的原理及应用
车削工件时,为了准确和迅速地掌握背吃刀量,通常利用 中滑板或小滑板上的刻度盘作为进刀的参考依据。
中滑板的刻度盘装在横向进给丝杠端头上,若横向进给丝 杠的螺距为5 mm,刻度盘一周等分100格,当摇动中滑板手柄 一周时,中滑板移动5 mm ,则刻度盘每转过一格时,中滑板 的移动量为:
33
Ⅰ型游标卡尺
Ⅲ型游标卡尺
34
2. 游标卡尺的读数方法 读数方法以0.02 mm精度为例,读数时先读出游标零线左
边在尺身上的整数毫米值,接着加上游标尺上与尺身刻线对齐 的刻线左侧的数字× 0.1,再加上该数字右侧刻线数×0.02, 即为被测表面的实际尺寸。
读数方法
35
3. 游标卡尺的使用方法
4
5)为了增加刀尖强度,改善散热条件,使车刀耐用, 刀尖处应磨有修圆刀尖或倒角刀尖。
6)粗车塑性金属(如中碳钢)时,为使切屑能自行折 断,应在车刀前面上磨有断屑槽。常用的断屑槽有直线形和 圆弧形两种,断屑槽的尺寸主要取决于背吃刀量和进给量。
倒棱
倒角刀尖
5
(2)精车刀 工件精车后需要达到图样要求的尺寸精度和较小的表面
在切削过程中,刀具推挤工件,首先使工件上的一层金 属产生弹性变形,刀具继续进给时,在切削力的作用下,金 属产生不能恢复原状的滑移(即塑性变形)。当塑性变形超 过金属的强度极限时,金属就从工件上断裂下来成为切屑
切屑形状的分类
四、车削加工方法之车外圆
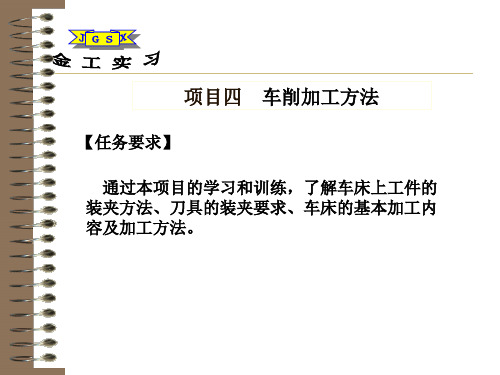
(5)直径的测量
(6)中、小滑板刻度盘的正确使用
由于螺纹配合间隙的影响,会有手柄逆时针小幅 转动时,刀具静止不动而影响尺寸精度及台阶 任务要求:能正确选用切削用量;正确选择和使用车外 圆的常用刀具;正确选择和使用外圆量具;加工工艺正 确;控制外圆柱面的直径、长度尺寸的精度及表面粗糙 度精度的方法正确。加工工件如图所示。
但支顶精度低于固定顶尖。
固定顶尖
回转顶尖
前顶尖及其安装
鸡心夹头
自制鸡心夹头(拨叉)
a)鸡心夹头; b)自制鸡心夹头; c)对开夹板
二、刀具的装夹
对常用车刀的装夹有下面的要求: 1.刀尖的高度应与机床主轴轴线等高。 2.刀具的伸出长度应为刀杆厚度的1~1.5倍。 3.刀垫应与刀架端面对齐、数量应尽量少,一般不超过3
中心孔与中心钻: 有A、B、C及R型四种结构形状,用中心钻钻出,其中A
型结构简单,应用广泛;B型中心孔是在A型的基础上多了 120°护锥面,保护60°的定位圆锥面。
顶尖:
有固定顶尖(死顶尖)和回转顶尖(活顶尖)两种,固 定顶尖的装夹刚度大,支撑精度高,但顶尖的支顶锥面与 中心孔的锥面之间有相对转动,会由于摩擦而产生热量, 需控制支顶力的大小,也可在中心孔中加润滑脂减小摩擦, 避免因过热烧毁顶尖及中心孔;回转顶尖适合较高的转速,
个。 4.刀杆的对称线应垂直于工件轴线。 5.每个车刀至少应用2个螺钉压紧。
三.车床的基本加工
1.车削外圆、台阶和端面
粗车和精车
工件的加工一般应分成粗加工和精加工两个加工阶段。在 粗加工阶段,应将毛坯的加工余量基本去除,只留出少量 的精加工余量即可。在机床动力、刀具强度等条件允许的 情况下,应使刀具在一次走刀的切削中尽量多的切去多余 的余量,进给量尽量大些,以减少切削时间,提高生产率, 所以,要求粗车刀具有较高的强度;在精加工阶段,要去 除粗加工剩余的精加工余量,保证工件的加工精度,所以, 要求精车刀锋利,耐磨,车削质量好。
实训课题一 车端面、外圆、台阶的车削
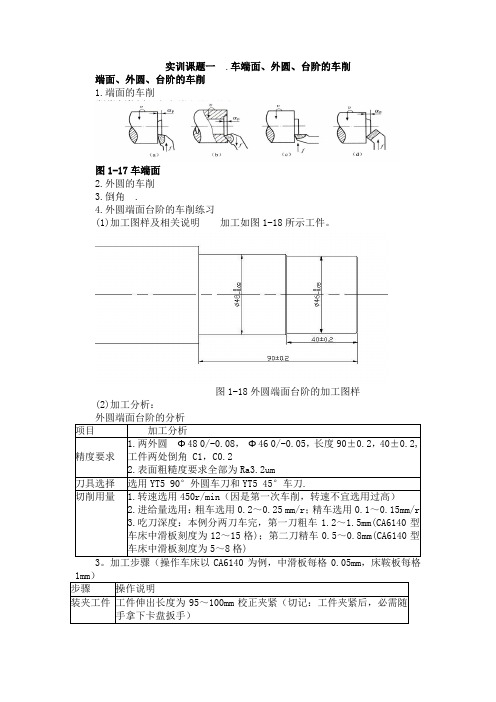
实训课题一.车端面、外圆、台阶的车削端面、外圆、台阶的车削
1.端面的车削
图1-17车端面
2.外圆的车削
3.倒角 .
4.外圆端面台阶的车削练习
(1)加工图样及相关说明加工如图1-18所示工件。
图1-18外圆端面台阶的加工图样(2)加工分析:
1.工件夹紧后,必须随手拿下卡盘扳手,不允许去摸旋转的工件和铁屑。
2.安装刀具时,一定要擦净各接合表面。
车端面时,刀尖要严格对准工件的旋转中心,以免车出的端面留下小凸台。
3.启动主轴前,应注意刀具是否与工件相撞;应启动主轴对刀;
4..进给途中严禁接触和测量工件;
5.操作时必须先停车,后变速,不允许用量具测量旋转中的工件和清理铁屑,也不准用手清除铁屑,以防割破手指,要用专用的铁屑钩。
6.不允许用工具敲击床身导轨及其他部位,装夹校正工件时,外圆和端面两者兼顾, 加工时,不允许擅自离开车床。
7.夹紧力是否恰当,加工深度的正确选取。
五、思考题
1.车削加工必须具备哪些运动?
2.工件和车刀的安装应注意是什么?
3.粗、精车的概念试切的方法与步骤如何选择粗、精车的切削用量?
4.试切的方法与步骤是什么?
5.车削加工必须具备哪些运动?
6.在车床上车一直径为60mm的轴,现要一次进给车至直径为52mm。
如果选用切削速度Vc=80m/min,求切削深度和车床主轴转速各是多少?
6.实训总结、填写实训报告
11.剖析出现问题的原因。
2. 就本课题学习效果进行作记录并总结,以利于今后教学改革。
3。
填写实训报告和填写好教学日志。
车外圆、端面与台阶
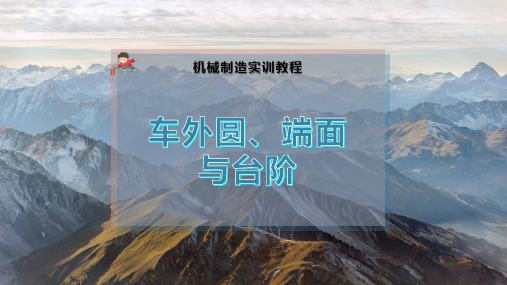
• 然后再粗、精车外圆和端面。以粗车后的铸铁棒为坯料,按图所示工 件的尺寸和粗糙度要求,进行粗、精车外圆和端面。
• ①装夹工件。用三爪卡盘夹紧工件,其夹紧长度为50mm左右。 • ②安装车刀。选用主偏角 Kr=45°和 Kr≥90°的偏刀两把,按要
求装在小刀架上。
• ③切削用量。精车铸件的切削用量为 αp=0.3~0.5mm、f=0.05~ 0.2mm/r、v=60~100m/min(n=285~476r/min)。精车时按此用量 调整车床。
• ④粗、精车端面和外圆。先用45 °外圆端面车刀车端面,车平即可。 再用90 °外圆偏刀粗、精车外圆及台阶端面,先粗车犗67×29尺寸, 最后用试切法精车犗66×(30±0.5)尺寸。车好后用45 °车刀倒角。
• 最后车台阶和钻中心孔。工件车好后,以它为坯料,按图所 示工件的尺寸、形位公差要求进行车削台阶和钻中心孔。加 工步骤如下:
1. 三爪卡盘装夹工件:
当用卡盘扳手转动小锥齿轮时,大锥齿轮随之转动,在 大锥齿轮背面平面螺纹的作用下,使3个爪同时向中心移动或 退出,以夹紧或松开工件。
小锥齿轮
大锥齿轮
(背面)
卡爪
三爪卡盘对中性好,装夹直径较小的外圆表面时用正爪 进行装夹。装夹较大直径的外圆表面时可用3个反爪进行装夹, 如图所示。
试切的方法和步骤:
车端面:
对工件端面进行车削的方法称为车端面。车端面应用 端面车刀,开动车床使工件旋转,移动大拖板(或小拖板)控 制切深,中拖板横向走刀进行车削。图示为端面车削时的几 种情形。
车端面时应注意:
1.刀尖要对准工件中心,以免车出的端面留下小凸台。
2.车削时被切部分直径不断变化,从而引起切削速度 的变化,所以车大端面时要适当调整转速,使车刀靠 近工件中心处的转速高些,靠近工件外圆处的转速低 些。
车工实训课题四车外圆端面和台阶
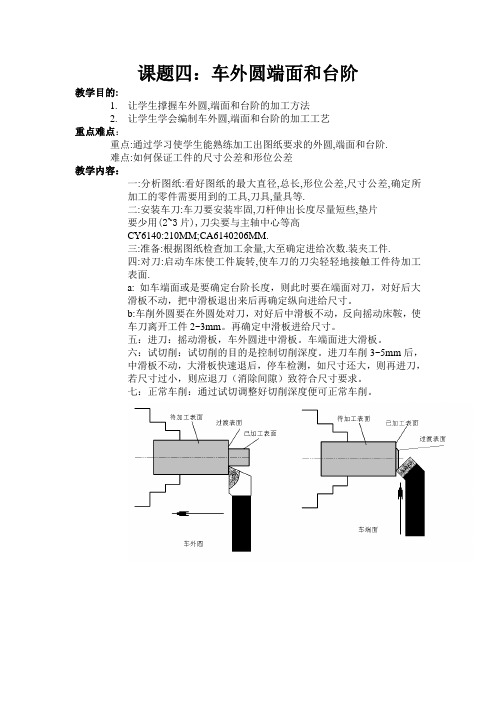
课题四:车外圆端面和台阶教学目的:1.让学生撑握车外圆,端面和台阶的加工方法2.让学生学会编制车外圆,端面和台阶的加工工艺重点难点:重点:通过学习使学生能熟练加工出图纸要求的外圆,端面和台阶.难点:如何保证工件的尺寸公差和形位公差教学内容:一:分析图纸:看好图纸的最大直径,总长,形位公差,尺寸公差,确定所加工的零件需要用到的工具,刀具,量具等.二:安装车刀:车刀要安装牢固,刀杆伸出长度尽量短些,垫片要少用(2~3片),刀尖要与主轴中心等高CY6140:210MM;CA6140206MM.三:准备:根据图纸检查加工余量,大至确定进给次数.装夹工件.四:对刀:启动车床使工件旋转,使车刀的刀尖轻轻地接触工件待加工表面.a: 如车端面或是要确定台阶长度,则此时要在端面对刀,对好后大滑板不动,把中滑板退出来后再确定纵向进给尺寸。
b:车削外圆要在外圆处对刀,对好后中滑板不动,反向摇动床鞍,使车刀离开工件2~3mm。
再确定中滑板进给尺寸。
五:进刀:摇动滑板,车外圆进中滑板。
车端面进大滑板。
六:试切削:试切削的目的是控制切削深度。
进刀车削3~5mm后,中滑板不动,大滑板快速退后,停车检测,如尺寸还大,则再进刀,若尺寸过小,则应退刀(消除间隙)致符合尺寸要求。
七:正常车削:通过试切调整好切削深度便可正常车削。
台阶轴的加工加工工艺(注:切削用量不能写入加工工艺、但学生第一次加工零件、为安全考虑本工艺附有切削用量)1.夹持毛坯,伸长约为50mm。
车平端面(45°车刀),钻中心孔。
(n=1000r/min),车装夹基准¢42X38mm(n=500r/min)2.调头夹持毛坯,车平端面,控制总长143mm,夹持夹位钻中心孔(n=1000r/min)3.一夹一顶粗车¢42X39mm;¢40X19mm.4.调头一夹一顶粗车¢41X38mm;¢39X18mm.车¢44。
n=500r/min t 8 B5.精车¢43-0.05mm;¢40-0.05X39mm; ¢38-0.05X19mm倒角。
车削加工基本工艺【车削加工基础篇 】

车削加工在机械生产中具有良好的适应性,其切削过程较为平稳,而且是连续进行,而且切削力的变化较小。
对被加工零件个表面位置精度有一定的保证,适合对有色金属零件进行精加工。
本文就来具体介绍一下车削加工的基本工艺。
一、车轴类工件轴类工件时机器中经常遇到典型零件之一,车床车削也是比较常用、比较普遍的加工方法。
轴类工件是旋转体零件,长度大于直径,由外圆柱面、断面和台阶组成。
1、外圆车刀:常用的外圆车刀有直头外圆车刀、90°偏刀和45°偏刀。
2、车外圆:直头外圆车刀强度较好;常用于粗车外圆,90°偏刀主偏角大,适合车外圆、断面和台阶;45°弯头车刀适用于车削不带台阶的光滑轴。
二、车端面和台阶圆柱体两端的平面叫做端面。
由直径不同的两个圆柱体相连的部分叫做台阶。
1、车端面的方法:右偏刀车端面,是由外向里进刀,容易扎入工件而形成凹面;用右偏刀由中心向外车削端面,车削顺利,不容易产生凹面。
用左偏刀由外向中心车端面,利用主切削刃切削,切削条件有所改善。
弯头车刀车削端面以主切削刃进行,很顺利。
它不仅可用于车端面,还可以车外圆和倒角。
2、车台阶方法:车削低于5mm台阶工件,可以让偏刀在车外圆一次完成。
车削高于5mm 台阶的工件,因为肩部过款,车削会引起震动。
因此,高台阶工件可先用外圆车刀把台阶车程大致形状,然后由偏刀分层切削完成。
三、车槽与切断1、车槽:在工件表面上车沟槽的方法叫做切槽,槽的形状有外槽、内槽和端面槽。
(1)切槽刀:常选用高速钢切槽刀。
(2)切槽方法·对于精度不高和宽度较窄的矩形沟槽,可以用刀宽等于槽宽的切槽刀,采用直进法一次车出。
·车削宽槽,可以多次直进法切削,并在槽两侧留一定精车余量。
·车削较小圆弧形槽,可以用成形车刀车削。
·较大圆弧槽,可以使用双手联动车削,用样板检查修整。
2、切断:切断刀的形状与切槽刀相似,常用切断方法有直进法和左右借刀法,直进法用于铸铁等脆性材料;左右借刀法用于钢等塑性材料。
- 1、下载文档前请自行甄别文档内容的完整性,平台不提供额外的编辑、内容补充、找答案等附加服务。
- 2、"仅部分预览"的文档,不可在线预览部分如存在完整性等问题,可反馈申请退款(可完整预览的文档不适用该条件!)。
- 3、如文档侵犯您的权益,请联系客服反馈,我们会尽快为您处理(人工客服工作时间:9:00-18:30)。
精车)Ra10--3.2㎛,(精车)Ra0.8--1.6㎛。
•5)、表面热处理要求:根据工件材料和实际需求,轴类工件常进行退
火或正火、调质、淬火、渗氮等热处理,以获得一定的强度、硬度、
韧性和耐磨性。
三、安装工件及其校正
1.用三爪自定心卡盘安装工件
图3-1 三爪自定心卡盘结构和工件安装
a)结构 b)夹持棒料 c)反爪夹持大棒料
三爪自定心卡盘的结构如图3-1a)所示,当用卡盘扳手转动小锥齿轮时,大锥齿轮也随之转动,在大锥齿轮背面平面螺纹的作用下,使三个爪同时向心移动或退出,以夹紧或松开工件。
它的特点是对中性好,自动定心精度可达到0.05--0.15㎜。
可以装夹直径较小的工件.
如图3-1b所示。
当装夹直径较大的外圆工件时可用三个反爪进行.
如图3-1c所示。
但三爪自定心卡盘由于夹紧力不大,所以一般只适宜于重量较轻的工件,当重量较重的工件进行装夹时,宜用四爪单动卡盘或其它专用夹具。
2.用一夹一顶安装工件
对于一般较短的回转体类工件,较适用于用三爪自定心卡盘装夹.但对于较长的回转体类工件,用此方法则刚性较差。
对一般较长的工件,尤其是较重要的工件,不能直接用三爪自定心卡盘装夹,而要用一端夹住,另一端用后顶尖顶住的装夹方法。
吃刀量较小,约0.1~0.2毫米,切削速度则可用较高或较低速。
初学者可用较低速。
为了提高工件表面粗糙度,用于精车的车刀的前、后刀面应采用油石加机油磨光,有时刀尖磨成一个小圆弧。
为了保证加工的尺寸精度,应采用试切法车削。
试切法的步骤如图3-2所示。
差图
a)开车对刀,使车刀和工件表面轻微接触 b) 向右退出车刀
c)按要求横向进给ap1 d) 试切1~3毫米
e) 向右退出,停车,测量 f)调整切深至ap2后,自动进给车外圆
5.刻度盘的原理和应用
刻度盘的原理:车削工件时,为了正确迅速地控制背吃刀量,可以利用中拖板上的刻度盘。
中拖板刻度盘安装在中拖板丝杠上。
当摇动中拖板手柄带动刻度盘转一周时,中拖板丝杠也转了一周。
这时,固定在中拖板上与丝杠配合的螺母沿丝杠轴线方向移动了一个螺距。
因此,安装在中拖板上的刀架也移动了一个螺距。
如果中拖板丝杠螺距为4mm,当手柄转一周时,刀架就横向移动4mm。
若刻度盘圆周上等分200格,则当刻度盘转过一格时,刀架就移动了0.02mm。
使用中拖板刻度盘控制背吃刀量时应注意的事项:
(1)由于丝杠和螺母之间有间隙存在,因此会产生空行程(即刻度盘转动,而刀架并未移动)。
使用时必须慢慢地把刻度盘转到所需要的位置(图3-3a)。
若不慎多转过几格,不能简单地退回几格(图3-3b),必须向相反方向退回全部空行程,再转到所需位置(图3-3C)。
图3-3 手柄摇过头后的纠正方法
a)要求手柄转至30,但转过头成40
b) 错误:直接退至30
c)正确:反转约一周后,再转至所需位置30
(2)由于工件是旋转的,使用中拖板刻度盘时,车刀横向进给后的切除量刚好是背吃刀量的两倍,因此要注意,当工件外圆余量测得后,中拖板刻度盘控制的背吃刀量是外圆余量的二分之一,而小拖板的刻度值,则直接表示工件长度方向的切除量。
6.纵向进给
纵向进给到所需长度时,关停自动进给手柄,退出车刀,然后停车,检验。
7.车外圆时的质量分析
七、车端面
对工件的端面进行车削的方法叫车端面。
端面的车削方法:车端面时,刀具的主刀刃要与端面有一定的夹角。
工件伸出卡盘外部分应尽可能短些,车削时用中拖板横向走刀,走刀次数根据加工余量而定,可采用自外向中心走刀,也可以采用自圆中心向外走刀的方法。
常用端面车削时的几种情况如图3-4所示。
图3-4 车端面的常用车刀
车端面时应注意以下几点:
1)车刀的刀尖应对准工件中心,以免车出的端面中心留有凸台。
2)偏刀车端面,当背吃刀量较大时,容易扎刀。
背吃刀量a
p
的选择:粗车时
a p =0.2mm~1mm,精车时a
p
=0.05 mm~0.2mm。
3)端面的直径从外到中心是变化的,切削速度也在改变,在计算切削速度时必须按端面的最大直径计算。
4)车直径较大的端面,若出现凹心或凸肚时,应检查车刀和方刀架,以及大拖板是否锁紧。
车端面的质量分析:
1)端面不平,产生凸凹现象或端面中心留“小头”;原因时车刀刃磨或安装不正确,刀尖没有对准工件中心,迟到深度过大,车床有间隙拖板移动造成。
2)表面粗糙度差。
原因是车刀不锋利,手动走刀摇动不均匀或太快,自动走刀切削用量选择不当
八、车台阶
车削方法:车削台阶的方法与车削外圆基本相同,但在车削时应兼顾外圆直径和台阶长度两个方向的尺寸要求,还必须保证台阶平面与工件轴线的垂直度要求。
车高度在5mm以下的台阶时,可用主偏角为90°的偏刀在车外圆时同时车出;车高度在5 mm以上的台阶时,应分层进行切削,如图3-5所示。
图 3-5 台阶的车削
台阶长度尺寸的控制方法:
1)台阶长度尺寸要求较低时可直接用大拖板刻度盘控制。
2)台阶长度可用钢直尺或样板确定位置,如图3-6a、3-6b所示。
车削时先用刀尖车出比台阶长度略短的刻痕作为加工界限,台阶的准确长度可用游标卡尺或深度游标卡尺测量。
图3-6 台阶长度尺寸的控制方法
3)台阶长度尺寸要求较高且长度较短时,可用小滑板刻度盘控制其长度。
车台阶的质量分析:
1)台阶长度不正确,不垂直,不清晰。
原因是操作粗心,测量失误,自动走刀控制不当,刀尖不锋利,车刀刃磨或安装不正确。
2)表面粗糙度差。
原因是车刀不锋利,手动走刀不均匀或太快,自动走刀切削用量选择不当。
实训图样1
一、样图如上:
二、装夹方法:用一夹一顶装夹或两顶装夹。
三、刀具、量具选择,
刀具:450 车刀、900车刀、中心钻等。
量具、游标卡尺,千分尺。
车削工艺:
1、用三爪自定心卡盘夹持坯料,车端面,钻B型Φ3中心孔,粗车外圆至卡
盘处,外圆留1㎜的精车余量。
2、调头找正夹牢,车端面,截总长至尺寸,钻Φ3中心孔,粗车剩余坯料外
圆。
3、用两顶尖装夹,精车Φ34±0.045外圆。
实训图样2
一、样图如上:
二、装夹方法:用一夹一顶装夹或两顶尖装夹。
三、刀具、量具选择,
刀具:450 车刀、900车刀,中心钻等。
量具、游标卡尺,千分尺
车削工艺:
1、用三爪自定心卡盘夹持坯料,车端面,钻B型Φ3中心孔,粗车外圆至卡
盘处,外圆留1㎜的精车余量。
2、调头找正夹牢,车端面,截总长至尺寸,钻Φ3中心孔,粗车剩余坯料外
圆。
3、用两顶尖装夹,精车Φ30±0.05外圆。
实训图样3
一、
样图如上:
二、装夹方法:用一夹一顶装夹或两顶装夹。
三、刀具、量具选择,
刀具:450 车刀、900车刀、切断刀\中心钻等。
量具:游标卡尺,千分尺。
车削工艺:
1、用三爪自定心卡盘夹持坯料外圆(露出部分长度不少于100㎜),用450
车刀手动横进给车端面。
2、用900车刀手动纵进给粗车Φ28、Φ24两级外圆,留2㎜精车余量,并保
证阶台长度,钻中心孔。
3、用切断刀手动进给车槽至尺寸。
4、调头夹住Φ28外圆,用手动车端面截总长至尺寸,钻中心孔。
5、用后顶尖顶住,用手动进给粗车Φ34,Φ25两级外圆,留下2㎜余量。
6、采用两顶尖装夹,精车Φ25、Φ34、Φ28、Φ24至尺寸,倒角符合要求。
实训图样4
样图如上:
一、装夹方法:用一夹一顶装夹或两顶装夹。
二、刀具、量具选择,
刀具:450 车刀、900车刀、切断刀、中心钻等。
量具:游标卡尺,千分尺。
车削工艺:
1、用三爪自定心卡盘夹持坯料外圆,用450车刀手动横进给车端面,钻中心
孔。
粗车Φ30外圆至卡盘处。