制程异常分析报告书
质量管理:制程异常处理规定

质量管理:制程异常处理规定1.目的为确保在生产过程中出现不符合产品要求的产品得到识别和控制,以防止其非预期使用或交付,特制定本规范,提供客户良好的质量保证,提高客户满意度。
2.范围适用本公司生产的所有产品,制程生产、制程检验、出货前检验等岗位发现的不满足标准要求之产品。
3.定义3.1严重缺点(CRI):严重影响产品功能以致无法使用,或违反法律法规,或造成使用之人身安全之缺点3.2主要缺点(MAJ):其结果或许会导致故障,或实质上减低产品之使用性能,以致不能达成期望之目标3.3次要缺点(MIN):产品之使用性能也许实质上不致减低其期望目的或虽然与设定之目标有差异,但在产品使用与操作上,并无多大影响。
3.4重要原材料定义为:液晶屏、触摸屏+控制卡、AD板、恒流板、适配器、主板、高压板、OPS、扬声器、内存、硬盘、WIFI+4G+天线类、摄像头+MIC类、风扇、液晶+TP全贴合类。
其余为一般材料。
3.5制程异常划分如下两类:A.同一生产订单材料上线率超过规定;①同一订单同材料料号相同问题点:≥50套产品,一般材料不良率≥10%,重要原材料≥5%;<50套产品,一般材料不良数≥5,重要原材料不良数≥3;②同订单同材料料号累计问题点:≥50套产品,一般材料不良率≥20%,重要原材料≥10%;<50套产品,一般材料不良数≥10,重要原材料不良数≥6;B.同一生产订单在对半成品、成品检验过程中所发现的不良率超过规定;①同一订单相同问题点:≥50套产品,性能不良率≥5%,外观不良≥10%;<50套产品,性能不良数≥3,外观不良数≥5;4.职责4.1品质部:4.1.1负责执行生产首件、制程巡检、成品的检验作业,以确保产品质量能满足品质检验标准的要求;4.1.2对制造部所发现的不良进行判定,符合以上3.5项A、B类的异常应开立《制程品质异常报告单》;4.1.3对异常批次不良品做标识、隔离;4.1.4制造部、品质部所确认的不良情况应完整记录在表单上并通过正式邮件和临时微信等形式通报相关部门;4.1.5对返工、返修后的产品品质复检确认,并填写相应的检验记录;4.1.6在收到技术或工程部返工方案验证OK通知信息后组织相关人员发起返工会议;4.1.7对改善对策实施的有效性进行追踪确认,并将结案《异常处理报告单》归档编号管理,以便追溯,统一归档为电子档;4.2制造部:4.2.1负责材料上线前检验、半成品、成品的初检作业,以确保产品质量能满足品质检验标准的要求;4.2.2负责材料上线不良、半成品、成品初检等所发现的不良反馈当班线长/品质IPQC/FQC确认;4.2.3配合相关部门给出的临时处理决策(如停线、换料、返工、返修、验证等作业);4.2.4经品质确认标识的来料不良品安排退料、换料等作业;4.3工程部(主导负责量产、小批量阶段):4.3.1主导小批量、量产(除样机)等阶段不良原因分析,判定责任部门,并与相关责任单位进行异常确认与讨论,制定纠正预防措施;4.3.2主导该批次不良品的临时处理方案,包括但不限于批量返工前返工方案验证、指导返工作业等;如30分钟内讨论无果的工程应及时向生产部发出停线、换料、切线等通知。
制程能力分析报告
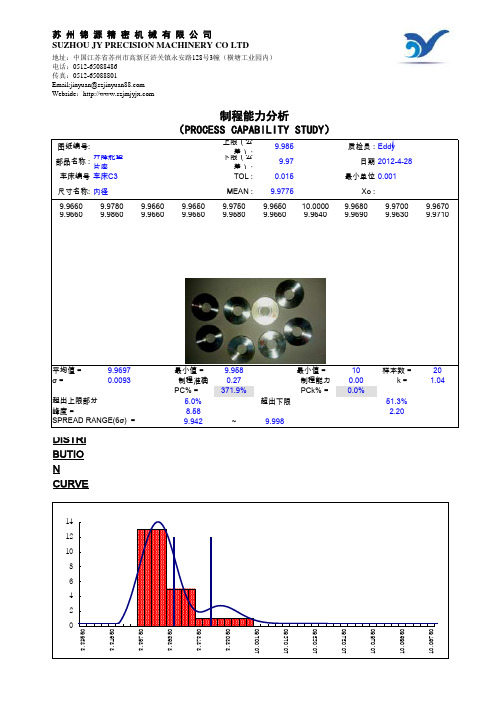
0பைடு நூலகம்
制程能力分析报告制程能力分析cpk制程能力分析制程能力分析表制程能力制程能力指数制程改善报告pcb制程能力制程检验报告初期制程能力
苏 州 锦 源 精 密 机 械 有 限 公 司 SUZHOU JY PRECISION MACHINERY CO LTD
地址:中国江苏省苏州市高新区浒关镇永安路128号3幢(横塘工业园内) 电话:0512-65088486 传真:0512-65088801 Email:jinyuan@ Webside:
制程能力分析 STUDY) (PROCESS CAPABILITY STUDY)
图纸编号: 部品名称 : 升降舵垫片座 车床编号 车床C3 尺寸名称: 内径 9.9660 9.9660 9.9780 9.9860 9.9660 9.9660 9.9650 9.9650 上限(公差) : 下限(公差) : TOL : MEAN : 9.9750 9.9580 9.985 9.97 0.015 9.9775 9.9650 9.9660 10.0000 9.9640 质检员 : Eddy 日期 2012-4-28 最小单位 0.001 Xo : 9.9680 9.9690 9.9700 9.9630 9.9670 9.9710
平均值 = σ=
9.9697 0.0093
超出上限部分 峰度 = SPREAD RANGE(6σ) =
最小值 = 9.958 最小值 = 制程准确度 = 0.27 制程能力指数 PC% = 371.9% PCk% = 5.0% 超出下限部分 = 8.58 SKEWNESS = 9.942 ~ 9.998
10 0.00 0.0%
样本数 = k= 51.3% 2.20
20 1.04
IPQC作业规范及常见制程异常改善分析报告

IPQC作业规范及常见制程异常改善分析报告IPQC作业规范及常见制程异常改善分析报告IPQC 作業規範及常見制程異常改善分析報告一.作業規範:1. 首件作業中必須依據客戶簽樣、產品圖、制程作業標準書、生產工令單作業,其中有任何一樣料號不同不得作業.並應立即呈報上級,到有結果反饋回來才可生產.2. 首件作業應全方位檢查,所有重點與非重點尺寸均需檢測,所檢測的部位需用正確的量測工具或制具.任何尺寸需依圖面尺寸公差或客戶簽樣尺寸生產,不得超越极限(有班長或班長級以上干部簽樣及實配合格不在此例) ,有客戶承認的可生產.3. 首件檢測人員需要認真看清楚制造部架模技工所開首件認可書的料號,提防有工程變更或張冠李戴現象發生.4. 首件認可只是表示模具的一種穩定狀態,IPQC 巡檢人員不得以首件作為生產參考依據,必須參照成品圖、作業標準書、客戶簽樣生產(外觀、尺寸相同) .在開機生產時IPQC 巡查人員所檢測產品尺寸與客樣或圖面公差不符時不得自做主張,需立即通知首檢人員或班長確認,首檢人員或班長認為該尺寸可產需在巡檢記錄表上簽名確認,否則IPQC 巡檢人員有權拒絕生產並立即上報課長級以上干部處理,則首檢人員或班長記過處罰.相反IPQC 巡檢人員沒有上報,若產生制程不良則由該巡檢人員全權承擔.5.IPQC 班長每隔1.5~2小時對所有機臺生產品質狀況進行確認,並在IPQC 巡檢記錄上簽名,若無照此方式作業,則制程不良由該IPQC 巡檢人員與班長共同承擔.6.QC 課長與班長對IPQC 所有人員的作業規範不定時進行稽核並登記在冊.有查核到沒有照上述規定作業的人員初次口頭警告,第二次記過處罰,累犯不改人員降職降薪論處.7. 品質記錄的填寫要真實準確並按時記錄,不得有弄虛做假行為.8.IPQC 人員在制程檢測作業中有治具檢測的一定要用治具檢測,不得有不檢行為.9.IPQC 作業人員在處置制程不良品時凡屬尺寸超差但經實配合格的需征得班長同意或知悉,不得隱滿不報或自做主張.10.IPQC 檢驗人員在制程作業中發現制程生產呈現不穩定狀態時,需立即開出策書>進行改善,並負有追蹤改善結果確認之義務.11.IPQC 首檢與巡檢人員在檢測工作中需對所檢測產品的上、下工程進行了解,提防有制造人員拿錯料生產,造成漏工序(如漏衝孔、漏鉚釘、漏壓毛刺等) 情況存在.二.制程常見異常分析:改善措施: C . 原材料表面來料有壓傷壓傷產品表面有髒污、粒子, B . 產品衝制后的廢料,未及時清衝制,造成壓傷A . 工件表面太髒的用風槍、布條清理后再進行衝制.B . 要求作業員每衝制1pcs 產品,用風槍把模具內的廢料、鈇屑吹干凈,並每衝制10~20pcs產品自檢一次.C . 加大IQC 進料檢驗的隨機性取樣,來料不良需通知供商處理或選別生產.A . 作業員拿、取料方式不正確,B . 擺料方式不正確,產品與產品 PE 片,直接疊放,劃傷 C . 隔板太髒,表面有粒子,作業員拿取產品時沒有直起直落,而是在隔板上拖動造成劃傷A . 班、組長、巡檢員去監督與教導作業員的拿取方式,輕拿輕放,避免產品與模具碰撞造成劃傷. B . 產品與產品之間不準疊放,中間用隔板或PE 片隔開.C . 教導作業員的拿取料方式,不準在隔板上拖動,需直取直落,隔板有髒污或粒子的用風槍把隔板吹干凈,太髒的隔板不準使用.A . 教導作業員拿取料方式,拿取料薄的工件時使產品受力均勻.B . 教導作業員按規定擺放產品,且產品擺放高度不得超過七層. C . 修正模具,使產品脫料順暢. C . 模具不脫料或脫料不順暢,作業員把產品從模具內取出時掰變形變形 . 作業員拿、取料方式不 B . 產品擺放方式不正確,擺放高度。
品质异常报告范例

2、机器运转无任何非常,各参数无非常无变化;
3、材料材质无非常,无变化;
4、各制程操作方法无非常,无变化;
5、全部制程环境无非常,无变化;
确认: 日期:202X/5/4
纠正和预防计策:(针对上面哪一项产生的非常写,尽量不要写是什么变化,触及到变化变更特别是参数的,那是4M变更,4M变更很多公司特别强调了变更要申报备案记录,如果你在非常里描写了你们私自变更什么,你们就会扯不清,所以。。。)
ZZZZ有限公司
品质非常报告单
日期:202X/5/6
管理NO:GX-QP-13-004
客户
品名
XX
材料
XX
工艺
XXX
订单数量
一批
ቤተ መጻሕፍቲ ባይዱ交货
一批
检验
☑全检
良品数
良品率
方式
□抽检
次品数
一批
次品率
80%
质量非常现象描写:XX显现严重缺点批量性非常不良。
确认: 日期:202X/5/3
原因分析:(分析手法人机料法环俗称8D报告,一样公司够用了,有问题的是哪一项就针对哪一项进行改进)
1、针对我司制程检验上的漏洞,第一更新标准检验指导书(已更新于19/5/3完成),其次要求供应商立刻验证并改进严重缺点,对供应商改进后的三到五个批次加严全检,实时沟通改进情形(即日起实行)。
2、针对产品较难控制的XXX,在改进严重缺点的条件下,尽量控制其他XX,每批做测试追踪改进状态。并要求供应商严格依照作业指导生产,我司已于5/4组织主管人员到供应商进行监督,于现场验证了改进情形后无其他非常产生。(客户需要知道的是你做了什么,而不是以后要注意什么,针对根本性的问题做了哪些动作,比如工厂内部开会记录,会议记录表,都可以提供给客户看,一样客户品质管控人员,SQE很爱好这样的记录,然后他们跟上级交代也有理有据)
制程不良的分析报告
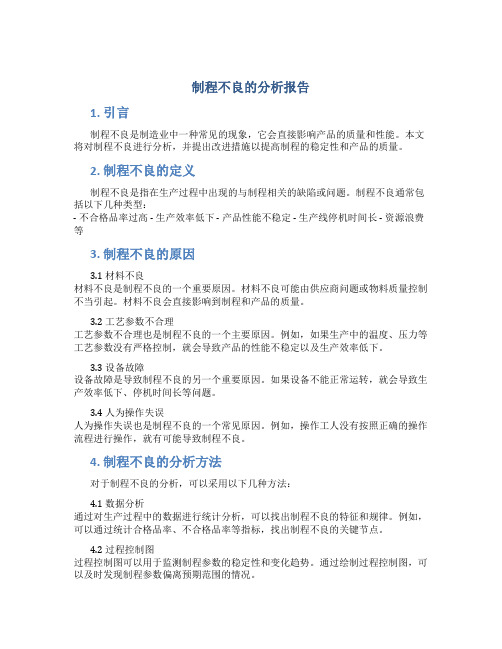
制程不良的分析报告1. 引言制程不良是制造业中一种常见的现象,它会直接影响产品的质量和性能。
本文将对制程不良进行分析,并提出改进措施以提高制程的稳定性和产品的质量。
2. 制程不良的定义制程不良是指在生产过程中出现的与制程相关的缺陷或问题。
制程不良通常包括以下几种类型:- 不合格品率过高 - 生产效率低下 - 产品性能不稳定 - 生产线停机时间长 - 资源浪费等3. 制程不良的原因3.1 材料不良材料不良是制程不良的一个重要原因。
材料不良可能由供应商问题或物料质量控制不当引起。
材料不良会直接影响到制程和产品的质量。
3.2 工艺参数不合理工艺参数不合理也是制程不良的一个主要原因。
例如,如果生产中的温度、压力等工艺参数没有严格控制,就会导致产品的性能不稳定以及生产效率低下。
3.3 设备故障设备故障是导致制程不良的另一个重要原因。
如果设备不能正常运转,就会导致生产效率低下、停机时间长等问题。
3.4 人为操作失误人为操作失误也是制程不良的一个常见原因。
例如,操作工人没有按照正确的操作流程进行操作,就有可能导致制程不良。
4. 制程不良的分析方法对于制程不良的分析,可以采用以下几种方法:4.1 数据分析通过对生产过程中的数据进行统计分析,可以找出制程不良的特征和规律。
例如,可以通过统计合格品率、不合格品率等指标,找出制程不良的关键节点。
4.2 过程控制图过程控制图可以用于监测制程参数的稳定性和变化趋势。
通过绘制过程控制图,可以及时发现制程参数偏离预期范围的情况。
4.3 原因分析对制程不良的原因进行分析,可以帮助我们找出问题的根源。
常见的原因分析方法包括5W1H法、鱼骨图、因果关系图等。
5. 制程不良的改进措施为了提高制程的稳定性和产品的质量,可以采取以下改进措施:5.1 加强材料质量控制合理选择供应商,并建立供应商质量管理体系,加强对采购材料的质量控制。
5.2 优化工艺参数通过对工艺参数的优化调整,确保制程参数在合理范围内,并加强对工艺参数的监控。
品质检讨报告
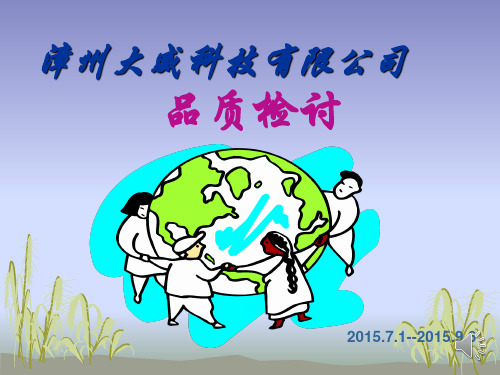
8月5日 单人站训练器 8月5日 8月6日 8月7日 倒立机 倒立机 倒立机
少锁双杠结构的小 包装员工不细心导致漏锁 手垫螺丝 塑料盖子破损 漏放零备件 堵头破损 包装纸箱防护不到位,材质差 1.抽检不到位;2.包装员工不细心导致漏放 配件 物流运输损坏,材质差纸箱包装后涨箱导致 破损
8月7日 单人站训练器 钢丝绳及滑轮破损 客户组装督导导致破损 8月10 靠垫、管塞脚垫破 倒立机 螺栓氧化,物流运输损坏 日 损,螺栓氧化生锈 8月10 单人站训练器 漏泡棉管 漏放及过磅不彻底 日 8月10 大飞鸟 导轨管氧化生锈 导轨管电镀效果差 日 8月10 三人站双杠 漏双杠下支撑管 漏放、全检过磅不彻底 日 8月12 1.物流运输损坏,2.包装纸箱设计紧凑、涨 老款倒立机 背垫破损 日 箱 8月14 单人站综合训 少螺丝 1.漏放,2.过称全检不彻底 日 练器 1.焊接U型座装夹不到位,2.夹具未以孔定 8月15 右扶手孔位无法组 倒立机 位,3.U型座孔位底部存在设计尺寸过小缺 日 装 陷 8月15 上支撑架滑轮孔方 1.焊接装夹方向装反导致焊反,2.治具无防 大飞鸟 日 向焊反 呆
异常描述 异常简图 原因分析 改善措施 责任部门责任主管
新款架子护罩-电 镀不良率30%
电镀不良 电镀不良
1、本批次挑选出货,联 络厂商改善电镀工艺; 2、IQC针对委外电镀件外 供应商创业电镀件, 采购 观进行10%比例的抽检, 表面氧化、生锈、电 品管 发现不良立即要求厂商挑 镀不良 选返镀; 3、IQC对每批次抽1pcs作 盐雾测试,并对测试记录,
4.出韩国bike保护罩丝印大威logo客诉1台
• 原因分析: • 员工对产品品牌意识 不强造成混用 • 改善措施: • 生产主管加强宣导培 训 • 专人专岗加工,并自 检、互检
smt制程能力分析报告

smt制程能力分析报告:分析报告制程能力s mt smt制程怎么样smt制程怎么学好smt论坛篇一:SMT制程管理的重要性我对国外SMT厂家的多年,发现在SMT应用上,他们有多项工作做得不足够,其中一项是制造过程的管理工作。
早前,[电子工业]的主编和我谈到我以往系列文间提及的制程管理应用概念,相信国内厂家也会用得着。
因而我特写本篇来谈谈这方面的概念。
制程管理,译自英文中的Process Management一词。
由于我们把焦点放在SMT的制造技术上所以我把Process译成(即制造过程)。
其实Process Manage-ment所涵盖的范围更广。
本广只就SMT 制造有关的范围加以探讨。
从THT到SMT的管理需求变化制程管理,并不是专为SMT而同设的。
但要较成功的应用SMT 这门技术,正确的推行有必要的。
制程管理虽不是门新的管理技术,但它得人们认识、重视、有效应用并比SMT这门技术来早。
也正为这原因,许多由THT(插件技术)提升SMT的厂家并没有意识到在管理上需要做改革的工作。
在THT制造环境下,忽略制程管理并不会为制造商带来太大的问题;但对於SMT制造工作而言,尤其是进入微间距和采用现今BGA和倒装片(Flip-Chip)之类技术的情况下,制程管理是不可或缺的管理工具。
制程管理为何对SMT应用那么重要?回答这问题,们得了解THT和SMT之间存在许多不同的地方,尤以下下旬几项最为显著:1、微型化-SMT发展的动力,主要是突破旧有组装技术对产品微型化的限制。
由于THT本身的技术局限,不断提升微型化的程度。
2、质量因素-THT和SMT两者的组装技术不大相同,影响质量的因素也大分别。
虽然在许多方面,SMT组装质量已证实比THT 更及更可靠,但SMT保证中工作比THT较为复杂。
3、自动化-SMT的发明变带来了高度的自动化,此亦是SMT 生产效率比THT更高的原因。
以上三点所带出的信息是:SMT成品检查不易进行;成品寿命或可靠性的变化幅度大;制程工艺对成品的质量影响日益深刻;返修成本和代价高;即时诊断和改正生产误差的重要性提高等等。
10月制程不良分析总结报告
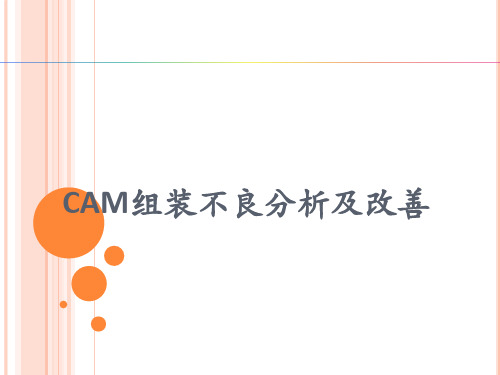
法
使用激光分板、超声波清洗 COB
公司高层
11月10日
棉签擦拭次数,废弃棉签误用 棉签蘸取酒精量多 振动后才能测试,终检前跌落工 序 百级工作台封装—测试洁净度 环
梁江(技术) 梁江(技术) 刘新昌(CAM) 马宏伟(品质)
10月30日 10月30 11月3日 11月1日 透明赃物 IPQC巡查 外校 避免硬板打磨 粉尘
CAM组装不良分析及改善
一.制程不良报表 二.TOP3不良原因分析 三.改善措施及验证计划
一.制程不良前三项
1.脏污 2.功能不良 3.模糊
从10月报表统计出前三大不良项目为:
二.TOP3不良原因分析
1.脏污原因分析:
人
漏检 自身作业水平 人员作业没有休息 棉签蘸取酒精太多
脏 污
测
没有调焦最清晰
说明:OQC退检数据下降,说明产线发现问题的能力提高,流出问题减少
使用的棉签是正牌,
棉签公司网站为 http://www.sa-nyo.co.jp/
脏污棉签防止误用装置 (丢进去后无法从顶部取出)
试验1 使用1280*1024显示屏检测前、后,OQC检出不良数据对比 使用前 10月27日 10月28日 10月29日 10月30日 11月3日 OQC检出不良批数 4 1 5 9 11 使用后 11月6日 11月7日 11月8日 11月9日 11月10日 OQC检出不良批数 6 2 6 3 2
11月5日
11月3日 11月3日
委外做镀层分析
川田 符合使用规定要求
功能不良改善措施
改善对象
措施要点
上料前目视检查FPC洁净度
责任人员
张光水(SMT)
实施时间
11月1日
制造业车间管理异常分析(精)
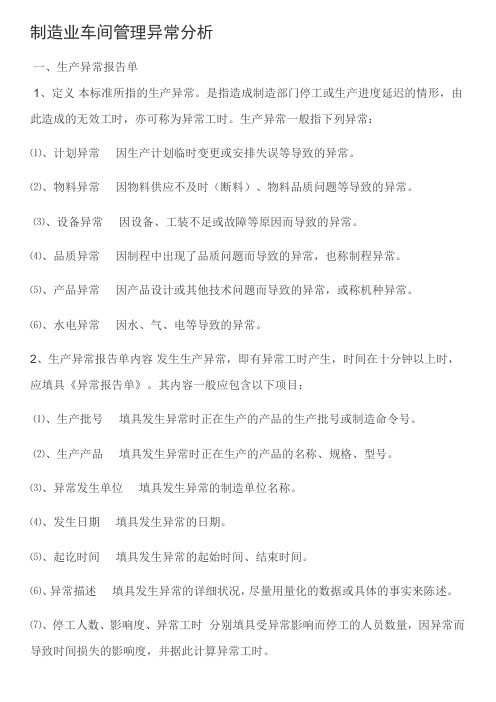
制造业车间管理异常分析一、生产异常报告单1、定义本标准所指的生产异常。
是指造成制造部门停工或生产进度延迟的情形,由此造成的无效工时,亦可称为异常工时。
生产异常一般指下列异常:⑴、计划异常因生产计划临时变更或安排失误等导致的异常。
⑵、物料异常因物料供应不及时(断料)、物料品质问题等导致的异常。
⑶、设备异常因设备、工装不足或故障等原因而导致的异常。
⑷、品质异常因制程中出现了品质问题而导致的异常,也称制程异常。
⑸、产品异常因产品设计或其他技术问题而导致的异常,或称机种异常。
⑹、水电异常因水、气、电等导致的异常。
2、生产异常报告单内容发生生产异常,即有异常工时产生,时间在十分钟以上时,应填具《异常报告单》。
其内容一般应包含以下项目:⑴、生产批号填具发生异常时正在生产的产品的生产批号或制造命令号。
⑵、生产产品填具发生异常时正在生产的产品的名称、规格、型号。
⑶、异常发生单位填具发生异常的制造单位名称。
⑷、发生日期填具发生异常的日期。
⑸、起讫时间填具发生异常的起始时间、结束时间。
⑹、异常描述填具发生异常的详细状况,尽量用量化的数据或具体的事实来陈述。
⑺、停工人数、影响度、异常工时分别填具受异常影响而停工的人员数量,因异常而导致时间损失的影响度,并据此计算异常工时。
⑻、临时对策由异常发生的部门填具应对异常的临时应急措施。
⑼、填表单位由异常发生的部门经办人员及主管签核。
⑽、责任单位对策(根本对策)3、使用流程⑴、异常发生时,发生部门的第一级主管应立即通知技术部门或相关责任单位,前来研究对策,加以处理,并报告直属上级。
⑵、制造部门会同技术部门、责任单位采取异常的临时应急对策并加以执行,以降低异常的影响。
⑶、异常排除后,由制造部门填具《异常报告单》一式四联,并转责任单位。
⑷、责任单位填具异常处理的根本对策,以防止异常重复发生,并将《异常报告单》的第四联自存,其余三联退生产部门。
⑸、制造部门接责任单位的异常报告单后,将第三联自存,并将第一联转财务部门,第二联转生产部门。
PCB各制程不良分析报告手册簿
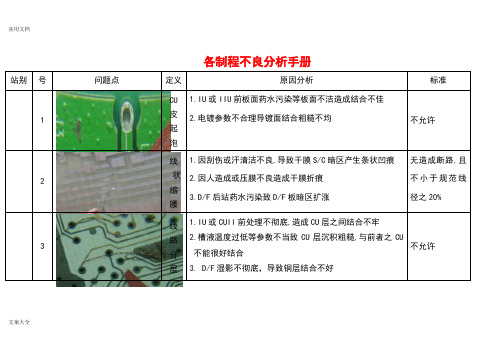
各制程不良分析手册站别号问题点定义原因分析标准1 CU皮起泡1.IU或IIU前板面药水污染等板面不洁造成结合不佳2.电镀参数不合理导镀面结合粗糙不均不允许2 线状缩腰1.因刮伤或汗清洁不良,导致干膜S/C暗区产生条状凹痕2.因人造成或压膜不良造成干膜折痕3.D/F后站药水污染致D/F板暗区扩涨无造成断路,且不小于规范线径之20%3 线路分层1.IU或CUII前处理不彻底,造成CU层之间结合不牢2.槽液温度过低等参数不当致CU层沉积粗糙,与前者之CU不能很好结合3. D/F湿影不彻底,导致铜层结合不好不允许文案大全4 蚀刻不尽1.蚀刻参数未管控好2.流锡或剥膜不尽3.IU或IIU前干膜掉落(刮落或与板面结合不牢)4.干膜前板面沾胶线路间不超过规范线径之20%,且未造成短路电镀5线路分层1.IU或CUII前处理不彻底,造成CU面结合不牢2.槽液温度过低等参数不当致CU层沉积粗糙,与前者之CU不能很好结合3.D/F湿影不彻底,导致铜层结合不好不允许6脏点短路1.干膜底片未清洁净,导致其明区沾污部分未被曝光固化,即此线距部分会被镀上CU及sn/pb而造成短路不允许文案大全7 CU面凹陷1.基材本身有针点凹陷不良(检查基板表面)2.压合时CU皮表面沾尘或PP质量不良造成压合后此瑕玼3.电镀铜时因槽液特别是光泽剂不正常导致CU积不良。
(2.3.可通过做切片观查,以作为参考)A手指不允许,板面每点不大于20mil,不超过板厚的1/58 CU面残缺1.D/F沾膜,撕膜不净,导致蚀刻时被蚀掉2.板面沾胶或沾药水导致CU面无锡层保护层3.电镀部分喷嘴坏损造成局部过蚀4.板面镀锡层被刮伤大铜面每点不大于20mil,每面只允许1点,其它地方不允许电镀9 短路1.干膜S/C未清洁净,致其明区沾污部分未被曝光固化,即此线距部分会被镀上CU及sn/pb而造成短路2.外层干膜刮伤,导致镀上锡层而造成短路不允许文案大全加工10孔内塞SN1.喷锡时风刀塞SN,浸锡时间不够等参作业参数不合理2.孔内有毛刺其它杂物造成孔塞3.L/Q塞墨孔内积墨或塞墨不良喷锡板导通孔塞锡不高出板面可允收;零件孔塞锡不允收;A手指附近15mm内导通孔塞锡不允收11孔边锡高1.喷锡前孔边CU面不洁,造成CU/SN结合力小于SN/PB内聚力2.前后风刀间距过大,,造成一面之锡被回吹3.风刀距轨道间距过大,风量扫锡整平力不够4.浸锡时间不足等参数不良锡厚40U″-1000 U″,且锡面上无毛尖状颗粒状突起加12 锡面凹坑1.喷锡前CU不洁或CU面不平整2.锡铅不纯或空气内含有杂物3.风刀不良1.不影响焊锡性和锡厚(40U″-1000 U″)文案大全工13 板面树脂1.L/Q显影时绿油未彻底去除干净,致化A时药液沉积不上不允许14A面花斑1.化A前CU面不洁2.NI槽NI含量不足等参数不合理;NI槽污染3.摇摆动作不到位不允许15 架锡桥1.喷锡前板面有不洁2.锡铅内或空气中含有杂质3.风刀不良不允许16 板面沾锡1.喷锡前因防焊漏印或CU面防焊被刮掉,致露出CU面,在此HAL时露CU部分被喷上锡线路上不允并列存在;大铜面每面不超过3个点,每点不大于10mil文案大全加工17A手指针孔1.前站CU面有凹坑2.镀A时电流密度过大,致NI/A沉积时粗糙不平整3.镀A地槽液含量不当或受污染每点不超过10mil,每排不超过3个点, 18A面手印1.化A前CU面不洁2.NI槽NI含量不足等参数不合理;NI槽污染3.摇摆动作不到位(此现象一般为手印所致)不允许19锡面锡高1.喷锡前板面有不洁2.锡铅内或空气中含有杂质3.风刀不良(此板有造成锡面粗糙)锡厚40U″-1000 U″, 锡面不允许有颗粒状或毛尖20锡高不良1.喷锡前板面有不洁2.锡铅内或空气中含有杂质3.风刀不良锡厚40U″-1000 U″, 锡面不允许有颗粒状或毛尖文案大全加工21PAD锡高1.喷锡前板面有不洁2.喷锡时风压小/风刀间距不对等制作参数不佳锡厚40U″-1000 U″, 锡面不允许有颗粒状或毛尖湿膜2防焊露CU1.棕片不良2.挡点偏移或过大3.印刷后碰及板面未干之油墨4.网版不洁致漏墨不良每点≤10mil,每面不超过3点23防焊异物1.印刷前板面有脏物2.板面沾干油墨每点≤10mil,每面不超过3点,且无明显色差文案大全24 刮伤露铜1.印刷防焊后因人为操作不当造成板面之防焊被刮掉而露CU 每点≤10mil,每面不超过3点湿膜25织纹显露1.L/Q退洗时间长2.基板质量问题3.压合不良基材上无明显白点白斑,经热冲击试验不会造成分层起泡26板面积墨1.该处电镀镀铜较厚,致印刷时下墨不良2.刮刀不平整3.网版高度等参数不合理4.网版漏墨不均不会造成色为准27防焊侧蚀1.油墨质量不行2.显影槽液对CU漆界面处之油墨攻击过度3.防焊重工次数过多1.线路上不允许2.PAD边缘不超过10mil文案大全湿膜28防焊侧蚀1.油墨质量不行2.显影槽液对CU漆界面处之油墨攻击过度3.防焊重工次数过多1.线路上不允许2.PAD边缘不超过10mil29孔边起泡1.有污染或前处理刷磨时水气未烤干2.孔边积墨致油墨较厚,致不能均一固化3.L/Q烘烤条件不当,热固化不均每点不超过3点,每点不超过10mil,3M撕胶防焊不脱落30板面漏印1. 印刷时因网版未清洁尽或网版脏点或干油墨致印一下2.刮刀不平整3.电镀镀铜不均4.设PIN不平致不能规范作业每点不超过3点,每点不超过10mil文案大全31 板面脏污1.印防焊后因人为操作不当使防焊表面沾上油脂或其它物质不破坏防焊且不影响客户防焊颜色之要求湿膜32对偏阴影1.因棕片对偏致使沾在CU面上之防焊被曝光而不能被显影掉(PAD阴影)2.因印刷后静置时间过长或烘烤时间过长或烤箱未保养好造成(主要为孔边阴影)PAD阴影部分不超过本身宽度1/8,SMT允许1mil,光学点允许2mil33孔边露CU1.网版挡点偏移或过大或作业过程中有变形不良≤2mil34防焊阴影1.因棕片对偏致使沾在CU面上之防焊被曝光而不能被显影掉(PAD阴影)2.因印刷后静置时间过长或烘烤时间过长或烤箱未保养好造成(主要为孔边阴影)PAD阴影部分不超过本身宽度1/8,SMT允许1mil,光学点允许2mil文案大全35 孔边起泡1.有污染或前处理刷磨时水气未烤干2.孔边积墨致油墨较厚,致不能均一固化3.L/Q烘烤条件不当,热固化不均每点不超过3点,每点不超过10mil,3M撕胶防焊不脱落湿膜36孔边起泡1.一般为印板过程中有滴到防白水等外物造成防焊色差每点不超过3点,每点不超过10mil,3M撕胶防焊不脱落37防焊起泡1.有污染或前处理刷磨时水气未烤干2.孔边积墨致油墨较厚,致不能均一固化3.L/Q烘烤条件不当,热固化不均每点不超过3点,每点不超过10mil,3M撕胶防焊不脱落文案大全38 板面脏污1.一般为印板过程中有滴到防白水等外物造成防焊色差不允收39 孔内积墨1.印刷时刮刀压力过大,致下墨过大,挤入孔内2.如孔过小在作业中也易产生此不良3.以上为空网印刷时产生零件孔不允收;导通孔每面不超过3个孔;卡板A手指15mm内不允许;其它无明确定义文字40沾文字漆1.网版未调正导致印偏沾漆2.A/W文字划线条太靠近CU PAD3.网片破损不允许41文字印偏1.网版未调正2.PIN针套错或没套好3.定位PIN孔钻偏PAD部分不超过本身宽度1/8,SMT允许1mil文案大全42 文字漏印1.制作中覆墨不良2.刮刀未研磨好不锋利3.印刷时用力不够不允许43 文字印反印刷时人为误操作导致套PIN套反不允许文字44文字印反印刷时人为误操作导致套PIN套反不允许45文字漏印1.制作中覆墨不良2.刮刀未研磨好不锋利3.印刷时用力不不允许文案大全46 沾文字漆1.机台上有油墨沾在板面2.印刷手手上沾有油墨并反沾于板面3.网版有破洞造成感光膜脱落不允许47 文字积墨1.油墨粘度过小,下墨不均2.覆墨时间太长3.印刷架网高度过低以清晰可认为准文字48文字沾漆1.网版未调正导致印偏沾漆2.A/W文字划线条太靠近CU PAD3.网片破损不允许49文字漏印1.网版显影不尽或油墨太干致下墨不良2.覆墨不良或印板时用力不均3.刮刀不锋利不允许文案大全50 文字阴影1.多次印刷或吸纸不当2.网版未抬起覆墨或网版反面有残墨3.板弯板翘PAD部分不超过本身宽度1/8,SMT允许1mil51 文字印倒1.套PIN套错误不允许5253文字52文字脱落1.油墨质量差,结合力不强2.烘烤时间或温度不当,致文字固化不够3.板面油烟等不洁物造成文字与板面结合力不强不允许文案大全53 文字重影1.印刷时有多次重印2.网版未调正或上PIN不牢3.重印时上PIN偏移未与网版对正不允许54 文字印偏1.网版未调正2. PIN未套正3.PIN孔偏移PAD部分不超过本身宽度1/8,SMT允许1mil55 沾文字漆1.机台上沾有油漆或手上沾漆2.脏点沾漆或刮伤沾漆3.网板破损不允许文案大全干膜56条状短路1.棕片上沾有条状杂物或贴膜前板面沾条状油污(此现象多为底片保护膜破损)2.贴膜或曝光后因人为操作不当将铜面干膜刮不允许57干膜脱落1.贴膜前板面沾油污/沾胶或其它杂物2.贴膜时压力/温度过小等不当致干膜与铜面结合不牢3. 贴膜或曝光后因人为操作不当将铜面干膜刮4.干膜自身附著力不好不允许58条状短路1.棕片上沾有条状杂物或贴膜前板面沾条状油污2.贴膜或曝光后因人为操作不当将铜面干膜刮伤不允许59点状短路1.棕片上沾有点状杂物或贴膜前板面沾点状油污2.贴膜或曝光后因人为操作不当将铜面干膜刮伤不允许文案大全干膜站60干膜膜破1.干膜韧性不足,较脆2.CU板板面杂物或巴厘过高3.贴膜后静置时间过长,曝光能量太低4.显影、水洗喷压过大或显影速度过慢不允许61板面沾污1.板面沾胶/沾油垢等不良物不允许62干膜脱落1.干膜挈性不足,较脆2.CU板板面杂物或巴厘过高3.贴膜后静置时间过长或显影速度过慢不允许文案大全63 干膜沾膜1.棕片之暗区被刮伤2.显影不尽或显影时残膜反沾大铜每面不超过2个点,每点小于10mil,其它部位不允收干膜站64线路突出1.贴膜后沾有脏点或底片上沾有脏点2.操作刮伤干膜不超过原稿线径的20%65干膜断路1.底片之暗区被刮伤2.显影不尽或显影时残膜反沾不允许文案大全66 干膜短路1.棕片上沾有点状杂物或贴膜前板面沾点状油污2.贴膜或曝光后因人为操作不当将铜面干膜刮伤不允许67 干膜对偏1.干膜站对底片时未保证孔环之ring各方向宽度相等(前提为孔正),2.板子或底片有涨缩零件孔余环≥2mil,导通孔孔偏不超过孔环的1/4,且与线路相连处不小于2mil干膜站68撕膜不尽1.割膜不良致撕膜时未能整块撕起2.撕膜时起膜位置不对成型线以内不允许文案大全69 NPTH孔膜破1.钻孔后巴厘处理不彻底,即巴厘高2.干膜封孔能力不够3.跨孔过大4.干膜静置时间过长或显影时冲压过大不允收70 干膜脱落1.贴膜前板面沾油污/沾胶或其它杂物2.贴膜时压力/温度过小等不当致干膜与铜面结合不牢3.贴膜或曝光后因人为操作不当将铜面干膜刮不允许71 板面油污1.贴膜以前,因设备漏油或人为操作不当,致使油污直接或间接沾污板面不允许文案大全成型站72模具冲偏1.板弯板曲或吹气过大或人为操作不当致板子未套好PIN孔时模冲造成不允许73槽孔捞偏1.定位PIN栽斜2.程式有错误超客户公差不允许74模冲伤孔1.套PIN套偏2.模具弹力胶不平衡3.板材涨缩或PIN针偏大不允许75斜边金丝1.铣刀不利或下刀点过于靠刀边2.因设备或人为调试不当致铣刀抖动较大3.斜板行进时用力不平衡不允许文案大全成型站76V-CUT过穿1.调刀过深或铣刀不水平2.过板时叠板所致3.板弯板曲或V-CUT刀具运转不稳不允许77V-CUT过反1.未按进料方向放板过V-CUT2.程式错误不允许78V-CUT伤铜1. V-CUT两边挡板不平行2.板子外型有偏差3. V-CUT间距过小4. V-CUT刀角度偏大或刀片磨损过重不允收文案大全79 V-CUT过穿1.调刀过深或铣刀不水平2.过板时叠板所致3.板弯板曲或V-CUT刀具运转不稳不允许成型站80V-CUT冲反1.未按磨具进料方向入板2.S/C面设计相似,识别有误3.模具未设防呆PIN不允收81V-CUT毛屑1. V-CUT在要求范围内调试2.客户外形公差小,且槽口偏小3.刀片角度过大或刀口不锋利按客户要求有不同文案大全82V-CUT伤铜1. V-CUT两边挡板不平行2.板子外型有偏差3. V-CUT间距过小4. V-CUT刀角度偏大或刀片磨损过重不允收83 模具冲偏1.板弯板曲或吹气过大或人为操作不当致板子未套好PIN孔时模冲造成不允许成型站84斜边不齐1.板弯板曲/斜边台面不平2.斜边行进时用力平均3.斜边不锋利/铣刀运转时稳定性不佳不允收文案大全85 断导线1.铣刀不锋利或下刀点太靠刀边不允收86 织纹显露1.PP之玻璃布间距过大/TG点不稳定等PP品质不良2.压合时参数不当致流胶过大3.L/Q重工时退洗时间过长,导致药水对树脂攻击严重,显露出玻织布基材上无明显白点白斑,经热冲击试验不会造成分层起泡87 靶孔偏1.D/F对S/C时对偏2.钻靶时钻偏无线路土3mil,有线路土2.5mil文案大全钻孔站88钻孔孔偏1.钻孔资料有误2.钻机精度不够(超出土3mil)或机台有故障3.叠板数超规范或钻头质太差土3mil 89多钻孔1.程式有误不允收90孔烧焦1.钻孔速度过快2.钻头排屑不良或钻针设定过深3.断半针作业或spindle掉刀不允许91光学点残1.干膜沾膜2.电镀过蚀3.人为刮伤不允收文案大全品检站91A手指氧化1.镀A时A槽药水浓度不当或有槽液污染,或水洗不尽2.转运和生产作业时手接触污染3.不以收92锡面凹坑1.喷锡前CU不洁或CU面不平整2.锡铅不纯或空气内含有杂物3.风刀不良1.不影响焊性及锡厚为为准93线路断路1.D/F棕片刮伤,即暗区部分线路被固化,蚀刻时被蚀掉2.操作中锡铅被刮全伤,CU线路无保护层3.镀锡铅前CU线路处有油污或沾胶不允许文案大全94 线路断路1.D/F棕片刮伤,即暗区部分线路被固化,蚀刻时被蚀掉2.操作中锡铅被刮全伤,CU线路无保护层3.镀锡铅前CU线路处有油污或沾胶不允许品检站95A面发白1.化A前处理微蚀过度2.因化NI后水洗不洁或A槽槽液非正常导致A厚不足无明色差且A厚在管控范围96A手指刮伤1.因人为操作不当造成镀A前或镀A后A手指上之刮痕不造成露NI,不超过3根,无明显刮痕文案大全97 刮伤露铜1.防焊印刷后,人为操作不当将板面之防焊刮掉每点不超过3点,每点不超过10mil98 条状针点1.此为较有规律的直条状,应与机器设备之规律性运转有关2.D/F磨刷时板面被沾有油脂或点状胶类物3.D/F显影影时有去膜不尽或有不浴物附于板面每PCS不超过3点,每点不超过10mil,厚度不超过1/5板厚品检站99CU面凹陷1.基材本身有针点凹陷不良(检查基板表面)2.压合时CU皮表面沾尘或PP质量不良造成压合后此瑕玼3.电镀铜时因槽液特别是光泽剂不正常导致CU积不良A手指不允许,每面少于3点,每点不大于20mil,不超过板厚的1/5 100板面沾锡1.喷锡前因防焊漏印或CU面防焊被刮掉,致露出CU面,在HAL时露CU部分被喷上锡线路上不允并列存在;大铜面每面不超过3个点,每点不大于10mil文案大全101 CU面花班1.此为防焊之后之花班2.防焊之前CU有沾胶或油脂等物污染3.因防焊本身品质不良造成显影溶解时局部不尽4.因退洗不尽重工或显影时未冲洗净致有药水水痕不允许102 SN手指刮伤1.此锡手指刮伤处有喷上锡,另此为明显人为造成2.为喷锡前因人为操作不当导致锡手指被刮掉部分不允收品检站103电镀针点1.此仅指电镀本站造成之此不良2.镀铜时槽液有机污染或金属污染致CU2+沉积不均3.光泽剂中之carrier不足或过量4.电镀前处理CU面未处理净A手指不允许;大铜面每面少于3点,每点不大于20mil,不超过板厚的1/5文案大全104 线细1.干膜曝光时赶气不到位或吸真空不足或曝光能量不足不均导致S/C线复制线在干膜板时比原稿小且小于标准2.显影过度或走蚀刻时因速度过慢或槽液管控不当导蚀刻出之线路小于原稿之20%不于原稿之20%105 板面沾锡1.喷锡前因防焊漏印或CU面防焊被刮掉,致露出CU面,在HAL时露CU部分被喷上锡线路上不允并列存在;大铜面每面不超过3个点,每点不大于10mil106 板损1.在生产过程中或板料转运中因人员操作不当导致板子有碰到机器或地面,造成板子局部破损不允收文案大全品检站107板面CU瘤1.D/P活化/去脂平整或微蚀槽液受有机或金属污染2.电镀铜槽添加剂不当或阳极有破损导致金属污染不允收108电镀铜残1.因撕膜不尽或板面油脂/沾胶等造成D/F后该处未镀上CU与锡铅保护层,蚀刻时被蚀掉2.镀锡铅后因锡铅氧化或锡铅刮伤致蚀刻时被掉大铜面每点不大于20mil,每面只允许1点,其它地方不允许109线路断路1.D/F棕片刮伤,即暗区部分线路被固化,蚀刻时被蚀掉2.操作中锡铅被刮全伤,CU线路无保护层3.镀锡铅前CU线路处有油污或沾胶时每刻不允许110防焊刮伤1.印刷防焊后因人为操作不当造成板面之防焊被刮伤不允收文案大全品检站111A手指刮伤1.因人为操作不当造成镀A前或镀A后A手指上之刮痕不造成露NI,不超过3根,无明显刮痕112A面花斑1.化A前CU面不洁2.NI槽NI含量不足等参数不合理;NI槽污染3.摇摆动作不到位不允收113板面上金1.因前站防焊脱落,导致后续走化A时化上A/NI2.走A线前处理磨刷过重致防焊有被刷掉不允收文案大全114A氧化1.化A时A槽药水浓度不当或有槽液污染,或水洗不尽2.转运和生产作业时手接触污染不允收文案大全。
制程优化数据分析报告(3篇)
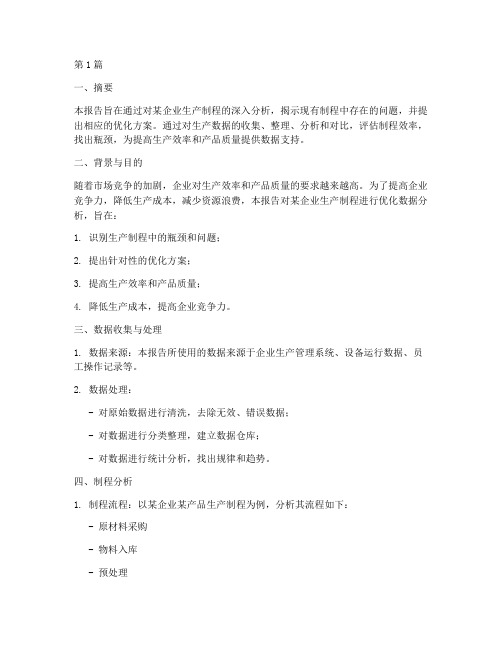
第1篇一、摘要本报告旨在通过对某企业生产制程的深入分析,揭示现有制程中存在的问题,并提出相应的优化方案。
通过对生产数据的收集、整理、分析和对比,评估制程效率,找出瓶颈,为提高生产效率和产品质量提供数据支持。
二、背景与目的随着市场竞争的加剧,企业对生产效率和产品质量的要求越来越高。
为了提高企业竞争力,降低生产成本,减少资源浪费,本报告对某企业生产制程进行优化数据分析,旨在:1. 识别生产制程中的瓶颈和问题;2. 提出针对性的优化方案;3. 提高生产效率和产品质量;4. 降低生产成本,提高企业竞争力。
三、数据收集与处理1. 数据来源:本报告所使用的数据来源于企业生产管理系统、设备运行数据、员工操作记录等。
2. 数据处理:- 对原始数据进行清洗,去除无效、错误数据;- 对数据进行分类整理,建立数据仓库;- 对数据进行统计分析,找出规律和趋势。
四、制程分析1. 制程流程:以某企业某产品生产制程为例,分析其流程如下:- 原材料采购- 物料入库- 预处理- 成形- 检验- 包装- 出库2. 制程瓶颈分析:- 原材料采购:原材料采购周期长,供应商不稳定,导致生产计划难以执行;- 物料入库:物料入库速度慢,库存积压严重;- 预处理:预处理设备老化,效率低,导致生产进度延误;- 成形:成形设备故障率高,维修时间长;- 检验:检验流程繁琐,效率低;- 包装:包装效率低,产品破损率高;- 出库:出库速度慢,物流成本高。
3. 数据分析:- 原材料采购:通过分析采购周期、供应商稳定性等指标,发现采购周期过长,供应商稳定性不足;- 物料入库:通过分析入库速度、库存积压等指标,发现入库速度慢,库存积压严重;- 预处理:通过分析预处理设备运行时间、故障率等指标,发现设备老化,效率低;- 成形:通过分析成形设备故障率、维修时间等指标,发现故障率高,维修时间长;- 检验:通过分析检验流程、检验效率等指标,发现流程繁琐,效率低;- 包装:通过分析包装效率、产品破损率等指标,发现效率低,破损率高;- 出库:通过分析出库速度、物流成本等指标,发现出库速度慢,物流成本高。
产品制程FMEA分析总结报告
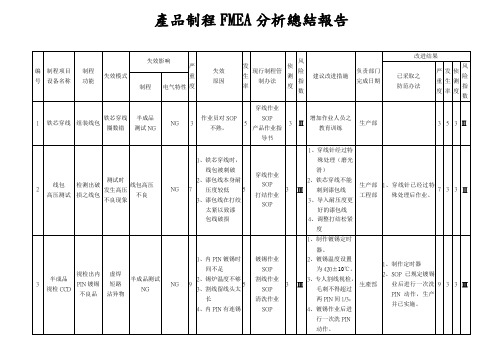
分析总结﹕
结论:
1.线包高压管控重点在于穿线针作业前需打磨处理;
2.内PIN虚焊因浸锡时间不够,导入定时器可有效管制时间;
3.内PIN短路为毛刺过长浸锡后造成相邻端子连锡,组立后导入CCD视检可有效检验毛刺;
4.外PIN端子歪斜因浸锡后产品直接放置清洗篮,超声波振动造成端子碰撞,将清洗篮更为
平放清洗治具可有效改善此问题;
5.外PIN镀锡不良为作业员镀锡手法不当所致,纠正作业员镀锡手法可有效改善此问题;
6.成品高壓因外PIN浸锡与锡面高度未管控导致漆包线被烫伤,导入限位治具、锡面管控可有效改善此问题.
產品制程FMEA 分析總結報告
風險優先係數:RPN (Risk Priority Number)名詞定義:(在客戶收到產品前,目前流程檢測出失效的能力) →(影響的)嚴重度:對客戶需求所造成之影響的重重要性[1=不嚴重~ 10=非常嚴重] →(原因的)發生度:特定原因發生並產生失效模式的頻率[1=不常發生~10=時常發生] →(現行管制能力)偵測度:現行管制計劃的偵測力[1=可偵測出來~10=不能偵測出來] ※等級尺度應由小組決定
※ 風險優先係數評點法:
→排列RPN 的優先順序,對最優先問題採取適當的措施. →RPN=(嚴重度*發生率*偵測度)1/3
C 1 : 影響機能故障的嚴重程度(嚴重度) C 2 : 故障發生的頻度(發生率)
C 3 : 故障發生檢測的難易度(偵測度) Cs : 故障評點
Cs = ( C 1˙C 2˙C 3 )1/3
表1. C 1的評價點 表2. C 2的評價點 表3. C 3的評價點 表4. C S 與故障等級之關
校准: 审核: 制定: 时间:。
制程异常分析改善汇总

防焊前五项制程问题分析:一、防焊空泡:造成原因:1、前处理不良。
(H2SO4浓度、水质、吹干段角度及风量,吸水海棉清洁度、烘干温度)。
2、磨刷后放置时间过长,室内湿度偏低。
3、印刷台面沾有油墨及其它有机溶剂,反沾板面,油墨搅拌不均。
4、预烤不足。
5、曝光能量太低或太高。
6、显影侧蚀太多。
7、HAL浸助焊剂时间太长,锡槽温度太高,浸锡时间太长。
预防措施:1、前处理作业必须按SOP要求生产。
2、磨刷后放置时间不得超过2H ,室内湿度控制在50-60%之间。
3、印刷台面保持清洁,印第一面时台面上垫一张白纸,以保证板面清洁度。
4、预烤温度保持70±2℃,烤后之板保证不粘棕片。
5、曝光能量保持在9-13格。
6、显影点控制在50-60%,避免过多侧蚀。
7、后烤通风保持良好,塞孔板必须分段烘烤。
8、HAL作业须完全按照SOP操作,不可有违规作为。
二、L/Q内圈阴影:原因分析:1、油墨过期。
2、预烤时间过长,温度过高。
3、挡点印刷时,孔环处积墨过多,印刷房湿度不够。
4、曝光前,静置时间过长。
5、显影速度过快,压力过小。
6、棕片遮光度不够。
7、曝光时吸真空压力未能达到要求。
改善对策:1、油墨按照先进先出的方式使用,保证在油墨保质期内使用。
2、预烤时间和温度按SOP要求作业,且烤好后及时取出防止冷烤。
3、印刷房湿度保持在50-60%之间,挡点印刷保持连贯,且印一PNL刮一次网版。
4、预烤后板静置时间不能眼过12H,最连贯4H以内对位完。
5、显影点保持在50-60%之间。
6、选用遮光度及质量较好之棕片生产。
7、吸真空不得低于600㎜Hg,且须保持导气良好。
三、卡锡珠:原因分析:1、印刷塞孔不满(量产板)。
2、退洗板导通孔内油墨未剥除干净。
3、油墨本身质量问题。
4、HAL贴胶未贴好,某些孔呈半覆盖状态。
5、HAL浸助焊剂及浸锡时间过短。
改善对策:1、从印刷各条件去改善塞孔程度。
(刮刀压力、角度、确度、速度、网目T数量)2、选用适合的退洗液,尽可能洗净导通孔内油墨,保证塞孔效果。
8D报告

V A s-i F oV-ASIAINFO TECHNOLOGY CO.,LTD.广亚讯科技有限公司8-D 分析报告客户名称 阜康达发文部门 品质部 品名规格 F10诺基亚接口L=6.8MM品名料号 批量 3K AQL 值 抽样数量100PCS不合格数量19PCS要求回复日期2011-10-11异常类别:□进料异常 □制程异常 □最终检验异常 客户报怨 □库存异常 异常处理裁决: 裁决人: Discipline 1:问题分析团队(Team Member ):业务:蒿红义 品质:师春梅 侯桂花 工程:章金涛 生产:杨和雄 仓管:冉瑞雪 Discipline 2: 问题描述(Problem Description ):发文者: 业务部 部门负责人: 蒿红义 贵司反应此批物料弹片端子歪斜日期:2011-10-10Discipline 3: 原因分析(Root Cause Analysis) :分析者: 品质部 工程部 生产部 部门负责人: 师春梅 章金涛 杨和雄 物料端子角度是模具打料时本身成形的形状,组装成品后没有偏出胶芯的槽位,在此基础上不会影响端子的通电性日期:2011-10-10Discipline 4: 立即改善对策(Containment Action ): 责任者: 预计完成实际完成1. 查询仓库无此物料库存2. 产线上待生产的物料隔离严检3. 与贵司及时沟通了解不良情况,以作相应的改善措施4. 不良品可退回我司,补换货冉瑞雪 杨和雄 侯桂花2011-10-10 2011-10-11Discipline5: 永久改善对策(Corrective Action ):责任者: 预计完成实际完成1. 先重新组装新的物料,严格检验端子的歪斜性,给贵司补换货2. 重新修改模具杨和雄 章金涛2011-10-11 2011-10-11Discipline6: 对策效果验证(Corrective Action Confirmation ): 责任者: 预计完成 实际完成待追踪师春梅2011-10-10 2011-10-11Discipline 7: 预防再发生对策(Preventive Action ): 责任者 预计完成实际完成制作SOP 标准作业指导书师春梅2011-10-10 2011-10-11Discipline 8: 效果确认与标准化(Confirmation and Standardization )::确认人:□ 对策有效 □ 对策无效 新SCAR#: □ 可结案 □ 尚须对策 结案日期: 核准表单编号:GYX-QA-F029 A0。
芯片封装异常报告
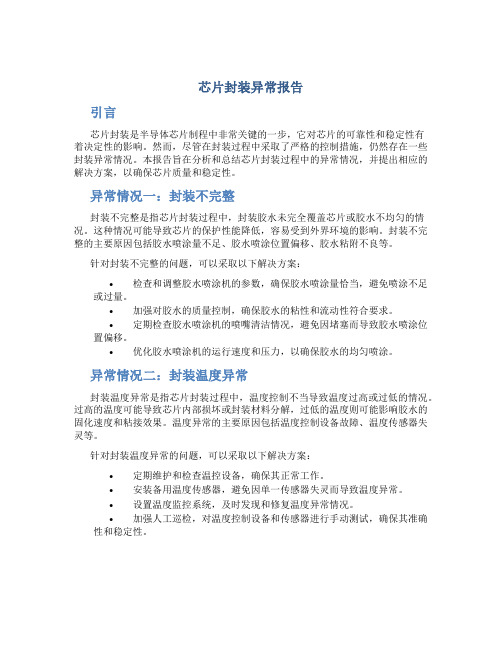
芯片封装异常报告引言芯片封装是半导体芯片制程中非常关键的一步,它对芯片的可靠性和稳定性有着决定性的影响。
然而,尽管在封装过程中采取了严格的控制措施,仍然存在一些封装异常情况。
本报告旨在分析和总结芯片封装过程中的异常情况,并提出相应的解决方案,以确保芯片质量和稳定性。
异常情况一:封装不完整封装不完整是指芯片封装过程中,封装胶水未完全覆盖芯片或胶水不均匀的情况。
这种情况可能导致芯片的保护性能降低,容易受到外界环境的影响。
封装不完整的主要原因包括胶水喷涂量不足、胶水喷涂位置偏移、胶水粘附不良等。
针对封装不完整的问题,可以采取以下解决方案:•检查和调整胶水喷涂机的参数,确保胶水喷涂量恰当,避免喷涂不足或过量。
•加强对胶水的质量控制,确保胶水的粘性和流动性符合要求。
•定期检查胶水喷涂机的喷嘴清洁情况,避免因堵塞而导致胶水喷涂位置偏移。
•优化胶水喷涂机的运行速度和压力,以确保胶水的均匀喷涂。
异常情况二:封装温度异常封装温度异常是指芯片封装过程中,温度控制不当导致温度过高或过低的情况。
过高的温度可能导致芯片内部损坏或封装材料分解,过低的温度则可能影响胶水的固化速度和粘接效果。
温度异常的主要原因包括温度控制设备故障、温度传感器失灵等。
针对封装温度异常的问题,可以采取以下解决方案:•定期维护和检查温控设备,确保其正常工作。
•安装备用温度传感器,避免因单一传感器失灵而导致温度异常。
•设置温度监控系统,及时发现和修复温度异常情况。
•加强人工巡检,对温度控制设备和传感器进行手动测试,确保其准确性和稳定性。
异常情况三:封装粘接不良封装粘接不良是指芯片封装过程中,胶水与芯片或封装基板之间的粘接效果不好,导致它们无法牢固地粘合在一起。
这种情况可能导致芯片脱落、封装裂纹等严重问题。
封装粘接不良的主要原因包括胶水质量不佳、粘接面清洁不彻底、胶水与芯片表面不兼容等。
针对封装粘接不良的问题,可以采取以下解决方案:•优化胶水的配方和质量控制,确保其粘接效果和可靠性。
制程异常分析(典型案例)报告
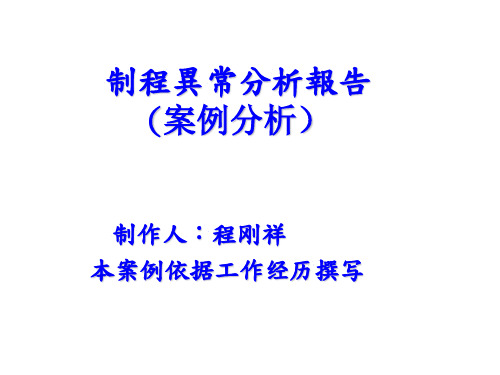
制作人:程刚祥 本案例依据工作经历撰写
一、不良现象描述
a.日期: 2019/12/25
工位: 孔规
b.機型:XXXXX-0X USB 3.1 TYPE-3 沉板母座
c.不良現象及不良率:
USB 3.1 TYPE-3 沉板母座上在做孔规测量,放入孔规不顺畅(不平贴,严
重者可能导致SMT装板不良) 。
剪除毛刺或剪短
孔规检测
五、长期对策
a.图面,作业指导书标准化: 1、修订SIP,补充内容:料带预断点检验毛刺环节并加以组装实配5PCS; 2、来料通过CCD和二次元量测把握冲压件上毛刺的缺陷等级,不得大于 0.01mm。 b.JIG/TOOL工治具修复合理化: 1、通知冲压工序,对该模具进行确认并修复; c.防呆(POKA YOKE)措施(颜色形状方向,声音左右,夹治具布局设变): 1、首件重点检验此异常,重点抽查并以实配检测是否平贴,是否顺畅。
不良圖片說明
12月12日、量化数据求出: 1、抽查料带库存品发现: 其中12月21日2500*7(外强);3500*4; 3500*6外发、 共
计420.9KPCS,经检查铁壳预断面宽度为:0.147-0.125mm,切断后有毛刺(高度超出 0.02mm)现象;
b.现场,现物,现状调查: 1、抽查来料7托盘/ 420.9KPCS ;成品2280PCS各5PCS; c. 调查制程,物料,设备5M1E因子: 1、可能因子:法/机/料。(人/机/物/环/法)
三、验证可能因子(分析)
a. 预计验证时间表: 1、12月26日现场检讨并确认SOP(作业指导); 2、12月26日已抽查来料库存/成品; b. 验证可能因子: 装配不到位;胶芯来料不良,铁壳来料异常; c.验证报告分析提出说明: 1、USB 3.1 TYPE-3 沉板母座上的铁壳预断位点应力异常,手工掰 断有毛刺,高出胶芯界面0.02mm;
35制程品质异常报告

35制程品质异常报告一、引言品质异常对于制程来说是一个非常重要且需要及时解决的问题。
本报告将对35制程中出现的品质异常进行分析,并提出解决措施,以确保产品的品质符合客户的要求。
二、品质异常概述在35制程中,我们发现了以下几个品质异常问题:1.厚度偏差:产品的厚度在设定范围内有较大的偏差,导致产品的功能受到影响。
2.制程偏差:制程过程中的一些步骤存在偏差,导致产品的质量无法得到有效的控制。
3.缺陷率过高:产品中出现的缺陷率较高,无法满足客户的要求。
4.设备故障:制程中使用的设备存在故障问题,导致制程不稳定,品质无法得到保证。
三、实际分析经过对品质异常问题的实际分析,我们得出以下结论:1.厚度偏差问题主要是由于制程中的参数控制不准确导致的。
需要对制程参数进行进一步的调整和优化,以减小厚度偏差。
2.制程偏差问题主要是由于工艺流程中的一些环节存在异常,导致制程步骤无法按照规定的要求进行。
需要对制程流程进行重新审核和改进,确保每个步骤的执行准确无误。
3.缺陷率过高问题主要是由于原材料的质量问题、设备的操作不当等原因导致的。
需要对原材料的选择进行筛选和检测,同时加强设备操作培训和质量控制。
4.设备故障问题主要是由于设备的老化和维护不当导致的。
需要对设备进行定期的维护保养,同时考虑更换老化严重的设备,以确保制程的稳定性和品质的可靠性。
四、解决措施为了解决上述品质异常问题,我们提出以下解决措施:1.厚度偏差问题的解决:通过对制程参数的调整和优化,确保每个生产批次的厚度控制在合理的范围内。
2.制程偏差问题的解决:重新审核制程流程,对每个环节进行详细的操作指导,并加强对操作人员的培训和管理,确保制程步骤的准确执行。
3.缺陷率过高问题的解决:加强对原材料的质量检测和选择,同时对设备操作人员进行培训和素质提升,严格控制每个生产批次的质量。
4.设备故障问题的解决:定期对设备进行维护保养,及时替换老化严重的设备,确保设备的正常运行和制程的稳定性。
制程品质异常报告(精)
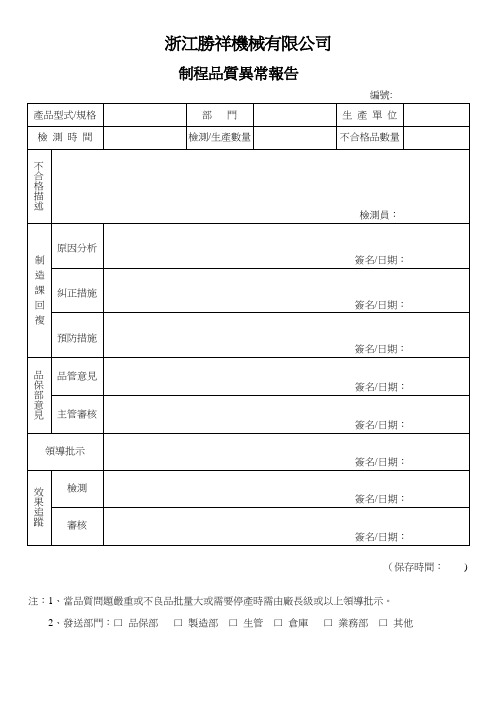
浙江勝祥機械有限公司制程品質異常報告編號:(保存時間:) 注:1、當品質問題嚴重或不良品批量大或需要停產時需由廠長級或以上領導批示。
2、發送部門:口品保部口製造部口生管口倉庫口業務部口其他________品质管理制度公司为了保证产品的品质制定,品质管理制度的推行,能提前发现异常、迅速处理改善,借以确保及提高产品品质符合管理及市场需要。
目录展开编辑本段1、总则第一条:目的为保证本公司品质管理制度的推行,并能提前发现异常、迅速处理改善,借以确保及提高产品品质符合管理及市场需要,特制定本细则。
第二条:范围本细则包括:(一)组织机能与工作职责;(二)各项品质标准及检验规范;(三)仪器管理;(四)品质检验的执行;(五)品质异常反应及处理;(六)客诉处理;(七)样品确认;(八)品质检查与改善。
第三条:组织机能与工作职责本公司品质管理组织机能与工作职责。
各项品质标准及检验规范的设订第四条:品质标准及检验规范的范围规范包括:(一)原物料品质标准及检验规范;(二)在制品品质标准及检验规范;(三)成品品质标准及检验规范的设订;第五条:品质标准及检验规范的设订(一)各项品质标准总经理室生产管理组会同品质管理部、制造部、营业部、研发部及有关人员依据"操作规范",并参考①国家标准②同业水准③国外水准④客户需求⑤本身制造能力⑥ 原物料供应商水准,分原物料、在制品、成品填制"品质标准及检验规范设(修)订表"一式二份,呈总经理批准后品质管理部一份,并交有关单位凭此执行。
(二)品质检验规范总经理室生产管理组召集品质管理部、制造部、营业部、研发部及有关人员分原物料、在制品、成品将①检查项目②料号(规格)③品质标准④检验频率(取样规定)⑤检验方法及使用仪器设备⑥允收规定等填注于"品质标准及检验规范设(修)订表"内,交有关部门主管核签且经总经理核准后分发有关部门凭此执行。
第六条:品质标准及检验规范的修订(一)各项品质标准、检验规范若因①机械设备更新②技术改进③制程改善④市场需要⑤加工条件变更等因素变化,可以予以修订。
制程、材料异常不良分析报告模板 PPT

异常不良分析
流程
<4> 临 时 对 策
说明
制定的方案可以在最短时间内临时解决问题的有效对策.
例1:当产线材料出现异常时,确认其它D/C是否可用,如果试做 OK可换良品D/C材料进行生产.针对材料来料尺寸不良,如需 加工原材料才可以生产,需由PE/PQE召开会议检讨,决定临时 改善方案,最后临时对策需经PQE验证,合格后并通知IE制作 临时SOP,再导入产线生产.
异常不良分析
流程
<3> 不 良 分 析
说明
2.分析问题时应注意每个环节都要仔细分析,利用相关实验 或对比方法找出相关原因.
例:当产品出现组装问题时,PE首先确认是物料来料尺寸是 否在图面管控内,量测时我们要注意量测准确性,这样有利于 减少PE分析误差, 量测完后如尺寸NG,需对样品进行编号储 存,便于相关单位进行核查,分析完后再对两个零件做公差配 合分析以及实物配合分析.
异常不良分析
流程
<2> 不 良 确 认
说明
1.根据产线组长及IPQC反馈的异常问题,由PE进行现厂确 认,确认其问题是否与反映问题相符合,确认完成后属于材
料来产问题(例如:外观不良、严重变形)的需填写“制程材料
异常信息反馈表”,见附件:
并通知PQE处理。
例:xx BASE来料RS-MMC PIN孔多胶,导致PIN无法组装,首先 要确认不良材料生产厂商和生产日期及BASE模穴号.来料不 良率,现产线生产状况.确认不良信息后向上级进行会报.
例2:当确认为机台异常时,应立即通知产线机修进行调机,调 机后需由PE工程师进行确认,无问题后方可生产.
异常不良分析
流程
<5> 长 期 对 策