车身设计流程及方法
车身设计流程

车身设计流程车身设计是汽车制造中非常重要的一个环节,它直接关系到汽车外观的美观性和空气动力学性能。
车身设计流程是一个系统工程,需要设计师们在整个设计过程中进行严谨的规划和精细的操作。
下面将详细介绍车身设计的整个流程。
首先,车身设计的第一步是需求分析和概念设计。
在这一阶段,设计师们需要充分了解市场需求和用户喜好,通过市场调研和用户反馈来确定设计方向。
同时,设计师们还需要进行概念设计,通过手绘草图或数字模型来勾勒出初步的设计构思。
接下来是设计方案的确定和细化。
在这一阶段,设计师们需要根据概念设计的初步构思,进行多轮的设计讨论和修改,最终确定最佳的设计方案。
同时,还需要对设计方案进行细化,包括车身结构、线条设计、尺寸比例等方面的具体规划。
然后是CAD建模和数字仿真。
在这一阶段,设计师们需要利用CAD软件进行车身的三维建模,通过数字仿真技术对车身结构和空气动力学性能进行模拟分析,以验证设计方案的可行性和优化设计。
随后是样车制作和试制。
在这一阶段,设计师们需要制作样车进行实物验证,通过试制来检验设计方案的可行性和实用性,同时也需要对试制样车进行实际测试和调整,以确保设计方案的完善性。
最后是成品车身的生产和改进。
在这一阶段,设计师们需要与工程师和生产部门密切合作,对成品车身进行生产工艺的优化和改进,以确保车身的质量和工艺达到最佳状态。
总的来说,车身设计流程是一个复杂而又精细的过程,需要设计师们在整个设计过程中进行严谨的规划和精细的操作。
只有通过严谨的流程和精湛的技术,才能设计出符合市场需求和用户喜好的优秀车身设计。
《车身总布置》课件
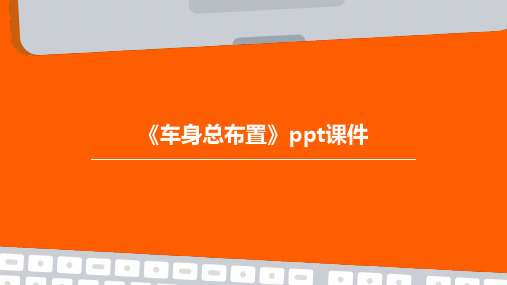
通过智能化布置,可以大大提高 设计效率,减少人工干预,降低 设计成本,同时还可以优化车身
结构,提高车身性能。
智能化布置的实现需要借助先进 的计算机辅助设计软件和人工智 能算法,如CAD、CAE、机器学
习等。
绿色环保理念
绿色环保理念是指在车身总布置中注重环保和可持续发展,尽可能减少对环境的负 面影响。
Hale Waihona Puke SUV车身总布置SUV车身总布置与轿车车身总 布置有所不同,因为SUV车型 通常具有更高的离地间隙和更
加强调越野性能的特点。
在SUV车身总布置中,需要特 别考虑到车辆的通过性和越野 性能,以确保车辆在复杂路况
下的稳定性和安全性。
SUV车身总布置还需要考虑到 车辆的外观和内部空间,以满 足消费者对于空间和舒适性的 需求。
布置其他附件
空调和通风系统
根据车内空间和人机工程学要求,合 理布置空调和通风系统的管道和出风 口位置。
安全装置
根据车型的定位和安全法规要求,合 理布置安全气囊、安全带等安全装置 的位置和数量。
03
车身总布置的优化方法
基于尺寸的优化方法
尺寸优化
通过调整车身结构尺寸参数,以实现性能优化 和结构减重。
在车身总布置中,应充分考虑人机工 程学原理,合理布置车内空间,优化 座椅、方向盘、仪表盘等部件的位置 和尺寸。
在车身材料选择上,应优先选择可再生、可回收、低污染的材料,同时还要注重减 少车身重量,降低能耗。
在设计过程中,应充分考虑空气动力学和热力学性能,优化车身造型和结构,以降 低风阻和热负荷。
人性化设计
人性化设计是指将人的需求和感受放 在首位,注重提高车身使用者的舒适 性和便利性。
同时还要注重提高车内的空气质量和 音响效果,以及提供智能化的人机交 互界面,以提升使用者的驾驶体验和 舒适感。
车身主断面设计总体流程与要点

玻璃厚度及涂胶厚度:
1. 玻璃厚度: 《QC/T 9656-1999 汽车用安全玻璃》标准规定汽车用 安全玻璃分为夹层玻璃、钢化玻璃、区域钢化玻璃等几种, 乘人用汽车前风窗玻璃必须为夹层玻璃,其余可采用钢化 玻璃或区域钢化玻璃,其厚度规定如下:
车身主断面设计总体流程和要点
车身主断面设计总体流程和要点
车身主断面设计总体流程和要点
车身主断面设计总体流程和要点
车身主断面设计总体流程和要点
车身主断面设计总体流程和要点
车身主断面设计总体流程和要点
车身主断面设计总体流程和要点
车身主断面设计总体流程和要点
车身主断面设计总体流程和要点
车身主断面设计总体流程和要点
车身主断面设计总体流程和要点
车身主断面设计总体流程和要点
车身主断面设计总体流程和要点
车身主断面设计总体流程和要点
车身主断面设计—逆向求解
车身主断面主要参数的确立(举例)
主要参数包括如下内容:
1.玻璃厚度及涂胶厚度 2.车门框密封间隙 3.车门、顶盖及前舱盖内外板间涂胶层厚度 4.焊接边宽度 5. 前门、后背门一、二级开度,前舱盖开度
车身主断面图的标注
1、 车身主断面位置和主断面代号在整车三视图的相应位置上的标注见图 A.1-1和图A.1-2,主断面位置和主断面代号的对应表见表A.1。
2、 每个主断面都应绘制图片文件。钣金件应按正确的方向生成料厚线。
3、 标注内容
a) 未倒角前的焊接接合边宽度(设计时数值应圆整)。 b) 安装密封条的配合间隙。 c) 造型面到前风窗玻璃、前车门玻璃、后车门玻璃、后背门玻璃或后挡
车身主断面设计总体流程和要点
车身主断面设计流程
车身主断面设计流程与要点详述

车身主断面设计流程与要点详述引言车身设计是汽车设计过程中至关重要的一环,而车身主断面的设计对整个车身的结构和外观具有重要的影响。
本文将详细阐述车身主断面设计的流程和要点,以帮助读者更好地理解和实践相关内容。
流程车身主断面设计的过程可以分为以下几个阶段:1.概念设计阶段:在此阶段,设计师需要通过市场调研、需求分析等方法确定车辆的定位和目标群体,并获取相关的设计要求和约束条件。
在此基础上,进行创意构思,形成初始的设计概念。
2.形状设计阶段:在此阶段,设计师需要将概念设计转化为具体的车身形状。
这需要考虑到车身的动力学特性、气动学特性、空间利用率等因素,并结合美学和品牌形象的要求进行设计。
设计师可以利用CAD软件进行形状设计,并对设计方案进行评估和优化。
3.结构设计阶段:在此阶段,设计师需要对车身的结构进行详细设计。
这涉及到材料选择、各部件的连接方式、承载能力等方面的考虑。
设计师需要充分了解车身结构的力学特性,以确保车身能够满足强度和刚度的要求。
此外,还需要考虑到制造和维修的可行性,并进行相应的优化。
4.评估和优化阶段:在此阶段,设计师需要对设计方案进行评估和优化。
通过使用CAE软件进行结构分析和仿真,设计师可以评估车身在不同工况下的性能表现,并进行相应的调整和改进。
此外,还需要进行原型制作和测试,以验证设计方案的可行性。
要点详述在车身主断面设计过程中,以下几个要点需要特别注意:1.功能性:车身主断面的设计首先要满足车辆的功能要求,如空间利用率、行李箱容量、进出车辆的便捷性等。
此外,还需要考虑到车身的安全性,如碰撞安全性、防护能力等。
2.美学性:车身主断面的设计也是展示车辆品牌形象和设计理念的重要元素。
设计师需要考虑到车身线条的流畅性和比例的协调性,以及与整个车身的一致性和和谐性。
此外,还需要考虑到不同市场和消费群体的审美偏好。
3.科技感:随着技术的不断进步,车身主断面的设计也需要具备一定的科技感。
设计师可以使用一些创新的设计元素和材料,如智能化的车身面板、LED灯光等,来提升车辆的科技感和现代感。
轿车车身的设计与开发流程说明书
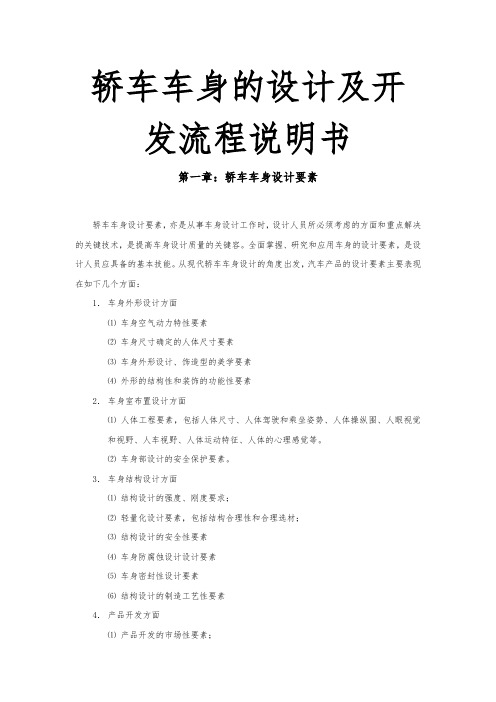
轿车车身的设计及开发流程说明书第一章:轿车车身设计要素轿车车身设计要素,亦是从事车身设计工作时,设计人员所必须考虑的方面和重点解决的关键技术,是提高车身设计质量的关键容。
全面掌握、研究和应用车身的设计要素,是设计人员应具备的基本技能。
从现代轿车车身设计的角度出发,汽车产品的设计要素主要表现在如下几个方面:1.车身外形设计方面⑴车身空气动力特性要素⑵车身尺寸确定的人体尺寸要素⑶车身外形设计、饰造型的美学要素⑷外形的结构性和装饰的功能性要素2.车身室布置设计方面⑴人体工程要素,包括人体尺寸、人体驾驶和乘坐姿势、人体操纵围、人眼视觉和视野、人车视野、人体运动特征、人体的心理感觉等。
⑵车身部设计的安全保护要素。
3.车身结构设计方面⑴结构设计的强度、刚度要求;⑵轻量化设计要素,包括结构合理性和合理选材;⑶结构设计的安全性要素⑷车身防腐蚀设计设计要素⑸车身密封性设计要素⑹结构设计的制造工艺性要素4.产品开发方面⑴产品开发的市场性要素;⑵系列化产品发展要素;⑶生产、工艺继承性要素。
第二章:整车开发流程随着汽车设计技术及手段的发展特别是现代工程技术方法的飞速进步,日益成熟的CAD/CAE/CAM一体化产品开发技术在轿车车身设计领域的应用,轿车设计方逐步由传统的设计方法向着以大大缩短产品开发周期和提高产品设计精度方面转变。
一般来说,整车开发时间为三年,由于市场竞争的日趋激烈,为抢夺有限的市场资源,整车开发时间逐渐缩短,更新换代非常平凡,稍微大一点的公司每年基本上要推出1款新车,有些汽车生产公司一年还有好几辆,以前的开发流程已经不能满足现代社会汽车设计的要求,根据最新的时间概念,设计一款全新的轿车,从项目成立到小批量生产,最快的大概只需18个月的时间了。
一、第一项目开发流程图:从时间的需求角度来说,大致时间安排如下(从立项日开始):天天30天75天120天140天190天240天310天360天480天500天540天600天二、第二项目开发流程图:从主要节点出发注:此处Test/试验包括一下部分(当然,这些试验不可能在较短的时间完成):1.安全气囊的匹配试验2.电喷系统、ABS、匹配试验3.排气系统、悬挂系统、转向、制动等系统匹配试验4.整车碰撞试验,国家强检及3C认证试验5.相关零部件的性能、寿命试验第三章:项目开发流程1、项目策划阶段1.1在项目概念批准之前,项目经理应协助销售公司市场部做好市场调研,提交《新产品市场调研报告》。
汽车车身研发设计流程

汽车车身研发设计流程一、需求分析在汽车车身研发设计的最初阶段,首先要进行需求分析。
这一步骤主要确定新车型的定位、目标市场、消费者需求和竞争对手情况等。
通过对这些信息的综合分析,为后续的设计工作提供明确的方向和目标。
二、概念设计基于需求分析的结果,进行概念设计。
这一阶段主要关注整体造型、风格和车型定位等方面的设计。
通过初步的三维建模和效果图制作,展现新车型的外观和内饰设计理念。
三、详细设计在概念设计得到认可后,进入详细设计阶段。
这一阶段涉及对新车型各个部件的详细设计,如车身结构、零部件尺寸和装配关系等。
同时,还需进行初步的工艺分析和可行性评估。
四、结构设计在详细设计的基础上,进行结构设计。
这一步骤主要关注车身结构和各个零部件的精确建模与设计。
确保结构设计满足性能要求、工艺性和装配需求。
五、性能模拟在结构设计完成后,通过使用专业的仿真软件进行性能模拟,以评估新车型的性能表现。
这包括碰撞安全、动力学性能、空气动力学等方面的模拟。
六、工艺性审查在性能模拟得到满意结果后,进行工艺性审查。
这一步骤主要评估新车型的可制造性和生产效率。
确保新车型的制造工艺可行,设备需求合理,并满足生产节拍要求。
七、供应商选择根据新车型的零部件需求,选择合适的供应商进行合作。
这一过程需综合考虑供应商的技术能力、产品质量、成本和交货期等因素。
与供应商建立良好的合作关系,确保零部件供应的可靠性和经济性。
八、样品制作与测试在确定了零部件供应商后,开始制作新车型的样品并进行一系列的测试。
这些测试包括但不限于装配测试、性能测试、环境适应性测试和碰撞安全性测试等。
确保新车型在实际生产中表现良好,符合设计要求和安全标准。
九、设计验证在样品测试完成后,进行设计验证阶段。
这一步骤主要是对新车型的设计进行全面评估和审核,确保设计满足所有要求,并进行必要的优化和改进。
通过第三方审核或专家评估来进一步确认设计的可靠性和有效性。
十、投产准备在设计验证得到批准后,开始投产准备阶段。
车身设计流程

车身设计流程车身设计是汽车设计中非常重要的一个环节,它直接关系到汽车外观的美观性和空气动力学性能。
因此,车身设计流程显得尤为重要。
下面将从概念设计、初步设计、详细设计和验证测试四个方面来介绍车身设计的流程。
首先是概念设计阶段。
在这个阶段,设计师需要对汽车的整体风格和造型进行初步构思和定位。
他们需要根据市场需求、品牌定位和竞争对手的分析,确定汽车的整体设计风格,包括车身线条、外观比例和设计元素等。
在这个阶段,设计师需要进行大量的市场调研和用户需求分析,以确定设计方向和风格。
接下来是初步设计阶段。
在这个阶段,设计师需要将概念设计转化为具体的三维模型和设计草图。
他们需要考虑到汽车的结构、空间布局和制造工艺等因素,以确保设计的可行性和实用性。
同时,他们还需要与工程师和制造工艺师密切合作,以确保设计的可制造性和成本控制。
然后是详细设计阶段。
在这个阶段,设计师需要对初步设计进行深入的细化和完善。
他们需要考虑到每一个细节,包括车身线条、进气格栅、车灯设计、轮毂造型等,以确保整体的和谐和统一。
同时,他们还需要进行多次的设计评审和修改,以确保设计的完美和优化。
最后是验证测试阶段。
在这个阶段,设计师需要将设计的样车进行实车制作和测试。
他们需要对汽车的空气动力学性能、安全性能和稳定性能进行全面的测试和评估,以确保设计的合理和可靠。
同时,他们还需要进行用户体验测试和市场反馈调研,以了解用户的需求和反馈,以便进行最后的修改和优化。
总的来说,车身设计流程是一个复杂而又严谨的过程。
设计师需要在每一个阶段都进行充分的思考和深入的研究,以确保设计的完美和优化。
只有这样,才能设计出符合市场需求和用户喜好的优秀汽车车身。
3.1 汽车车身设计开发流程与方法

第三章汽车车身设计开发技术与方法3.1汽车车身设计开发流程与方法学3.1.1车身设计开发主要工作内容及流程(程序)1)车身总布置设计及安全法规计算校核(或三维数字虚拟样机Archetype)2)造型设计3)三维曲面和造型面设计4)1:5或1:4 模型及1:1外模型制作或数控加工(或三维数字模型)5)1:1内模型(或三维数字模型)6)发动机舱三维数字模型7)地板三维数字模型8)测量与曲面光顺9)白车身结构详细设计(BIW)(9.1)1:1外模型光顺后数据分块(9.2) 车身设计断面的定义与尺寸确定(9.3) 密封结构确定与密封件选择(9.4) 确定分块线(9.5) 与车身有关的设计硬点的确定(9.6) 左右侧围设计(A, B, C, D柱设计, 前后翼子板设计)(9.7) 顶盖设计(外板, 横梁与纵边梁设计) (9.8) 发动机前围板设计(9.9) A柱下段设计(9.10) 发动机舱与前轮包设计(9.11) 前后灯具设计(9.12) 格栅设计(9.13) 前围板设计(9.14) 前保险杠设计(9.15) 地板总成设计(前中后)(9.16) 后门总成设计(9.17) 前门总成设计(9.18) 尾门总成设计(9.19) 前发动机罩设计(9.20)前风当总成设计10)内饰、外饰设计11)先行车, 螺钉车或概念车的(Prototype)试制,第二轮试验样车(定型车)试制12)碰撞与结构分析及结构优化设计13)成型过程仿真14) 模具与工艺工装设计如图3.1.1为车身详细设计阶段面向对象的产品模型(OPM)并行设计流程图OM2 OM2 OM2 OM2 OM2 OM2T21: CAD T22: DF A可装配设计T23: CAE T24: 评审T25: DFM 可制造设计T26: CS 碰撞仿真IM21: 输入产品模型,请求详细设计OM21: 向下游预发布零部件信息OM22: 输出DF A结果OM23: 输出CAE结果OM24: 输出同意或修改概要设计建议OM25: 输出DFM结果输出OM26: CS结果图3.1.1 汽车车身并行详细设计OPM模型31 32 3334 35T 31: CAPP T 32: CAFD 机算机辅助工装卡具设计(CA FIT DE SIGN)T 33: CAM T 34: MPS(制造过程仿真) T 35: 评审 IM 31: 请求加工过程设计 OM 31: 输出CAPP 结果 OM 33: 输出 CAFD 结果OM 33: 输出CAM 结果 OM 34: 输出MPS结果OM 35: 输出同意或修改详细设计建议图3.1.2 汽车产品开发试制与加工过程设计OPM 模型 g 1: 请求详细设计(结构) g 2: 预发布零部件消息,请求试制或加工过程设计 g 3: 请求修改概念设计(造型设计) g 4: 请求修改详细设计(结构设计)图3.1.3 汽车车身并行开发过程OPM 模型图3.1.4 车型数字化设计过程3.1.2 车身结构设计方法学1 1995年后的先进的车身设计技术与方法1995年后车身设计技术发展与市场需求体现在如下几个方面:图3.1.5 虚拟产品开发描述图3.1.6 白车身设计过程描述图3.1.7 并行设计与开发周期降低图3.1.8 全数字化设计方法图3.1.9 确定设计结构方案图3.1.10 产品设计及工艺设计集成计方法图3.1.12 参数化结构断面设计图3.1.13 全相关参数化的车身开发全过程2 数字化车身结构设计方法学(1)设计硬点设计区的设计方法复杂的结构实际上是众多简单的设计的叠加组合(复杂设计简单化)任何复杂的车身结构设计与设计结果都是由如下两个方面决定: (a) 满足诸多设计硬点的特征结构设计(HARDPOINT DESIGN AREA), 例如, 造型面硬点, 与车身有关的零部件装配孔面及结构等设计硬点, 选定的设计断面结构, 造型分界线硬点, 造型形状形成的设计断面引导线硬点, 车身零件间的焊接装配面, 零件的分块线硬点. (b) 自由设计区设计(FREE DESIGN AREA), 即在满足设计硬点基础上, 进行的自由设计区, 一般非设计硬点的设计区域都属于自由设计区, 自由设计区不同的设计人员会得到不同的设计结果, 这也是自由设计区自由的特点, 但这不等于自由设计区可以胡乱设计, 应遵循如下一些设计原则, 以便才能使设计结构更合理, 水平更高.因此车身设计过程与方法应满足如下公式:车身结构设计特征(BSDF)=自由设计区自由设计特征(FDF)+断面设计硬点决定的设计特征(SDHF)+造型设计硬点决定的特征(IDHF)+造型决定的断面引导主轴线(一个零件多个断面几何中心连线)特征(ISSF)+其他附件或COPY件等确定的设计硬点特征(CDHF)+零件分块线与焊接边界线等的设计硬点特征(BDHF)即为:BSDF=FDF+SDHF+IDHF+ISSF+CDHF+BDHF车身零件结构的设计过程或设计建模(BSDP or BSDM)=用三维CAD软件完成车身结构设计特征的过程或结果(BSDFP or BSDFM)即为:BSDP=BSDFPBSDM=BSDFM车身设计建模(BDM)=完成所有车身零件的设计建模与装配设计建模的总称(TOL_BSDM) 即为:BDM=TOL_BSDM全数字化车身设计开发(BDD)=采用三维CAD 软件完成全部车身设计建模, 并采用CAD/CAE/CAM一体化技术完成车身设计,结构优化及制造(或制造模具)的全过程(3D_CAD/CAE/CAM_BDM).即为:BDD=3D_CAD/CAE/CAM_BDM(2) 自由设计区的设计方法与设计原则a 自由设计区的设计方法(a) 先用三维CAD软件将设计硬点确定的结构与特征连接成一体, 成为一个粗的异型大面, 中间可以用一些平面与设计硬点面的相交获得连接线或倒角线.(b) 对设计硬点之间形成的设计区域-自由设计区每一个进行分析, 强度和刚度一般性要求的部位一般小于50*50mm的面积区域, 可以不加特征结构(加强筋, 加强沉孔(如果没有密封要求), 折边, 卷边等特征结构建模), 但要在边界上导角. 大于50*50的区域一般要加特征以便加强结构并导角,较大的区域不留任何空地, 以便使刚度最大, 材料最省.a 自由设计区的设计准则(a) 最大刚度原则- 自由设计区必须尽力获得最大刚度的设计原则, 因此, 要加加强筋和加强沉孔, 以便获得高水平的设计结构.(b) 最轻量化原则- 设计结构要确保满足刚度要求的基础上使材料最省的原则, 尽可能使结构设计可以使料厚簿一些, 没有密封要求的结构可以用沉孔以便轻量化与刚度最大化的双嬴, 等要充分考虑结构形式和结构方案.(c) 最大园角原则-自由设计区, 一般都是内部结构区域, 不在外观缝隙线条区域. 因此, 为了提高冲压工艺性, 减少制造成本, 应尽可能设计较大的设计过渡园角. 但不能影响设计硬点结构. 在在外观区域应尽可能最小园角原则,最小值为料厚(d) 特征结构最大斜度原则- 筋槽设计的立面尽可能采用较大的斜度. 以便获得较好的制造工艺性, 防止冲压裂纹和褶皱.(e) 最符合工艺性原则-从设计结构上和面的光顺程度上尽可能获得好的制造工艺性, 如材料流动均匀性与制造可能性.(f) 创新与多样化设计原则-自由自由就意味着允许多样化, 也就是创新原则.(g) 最复杂化原则, 因为模具加工不会增加制造成本, 只会降低成本(如材料轻, 成本低了).(h) 满足CAE/OPTIMIZATION结构优化分析设计要求.。
- 1、下载文档前请自行甄别文档内容的完整性,平台不提供额外的编辑、内容补充、找答案等附加服务。
- 2、"仅部分预览"的文档,不可在线预览部分如存在完整性等问题,可反馈申请退款(可完整预览的文档不适用该条件!)。
- 3、如文档侵犯您的权益,请联系客服反馈,我们会尽快为您处理(人工客服工作时间:9:00-18:30)。
汽车车身CAE分析
汽车碰撞仿真模拟
通过模拟汽车碰撞过程中的速度、加速度、 变形和各部件的能量吸收,从而有效指导设计师对
汽车车身进行合理的结构设计,为提高汽车的安全 性能、顺利通过汽车碰撞试验起者决定性的作
车身设计流程及方法
车身设计流程及方法
车身设计方法及一般工作流程介绍
车身设计是整车设计重要组成部分
在国外,有将汽车 开发定义为: 1、底盘设计 2、车身设计 3、内饰设计
汽车车身设计流程
汽车车身开发设计流程过程描述: 1、车身造型及初步外表面 2、车身总布置设计及工程分析 3、车身竞争性车型结构分析及主 断面设 计 4、车身结构设计 5、车身CAE分析 6、车身结构工艺性分析 7、车身工艺数据 8、车身样车试制 9、车身样车试验 10、车身数据修改、NC数据 11、模具样车试制及小批量生产 12、样车的性能试验 13、批量生产
a 最大刚度原则- 自由设计区必须尽力获得最大刚度的设计原则, 因此, 要加加强筋和加强沉孔, 以便获得高水平的设计结构. b 最轻量化原则- 设计结构要确保满足刚度要求的基础上使材料最省的 原则 c 最大园角原则-自由设计区, 一般都是内部结构区域, 不在外观缝隙线 条区域(最小园角原则,最小值为料厚). 因此, 为了提高冲压工艺性, 减 少制造成本, 应尽可能设计较大的设计过渡园角. 但不能影响设计硬 点结构. d 特征结构最大斜度原则- 筋槽设计的立面尽可能采用较大的斜度. 以便 获得较好的制造工艺性, 防止冲压裂纹和褶皱. e 最符合工艺性原则-从设计结构上和面的光顺程度上尽可能获得好的 制造工艺性, 如材料流动均匀性与制造可能性. f 创新与多样化设计原则-自由自由就意味着允许多样化, 也就是创新原 则. g 最复杂化原则, 因为模具加工不会增加制造成本, 只会降低成本(如材 料轻, 成本低了).。
车身造型及初步外表面
车身总布置设计
造型工程可ቤተ መጻሕፍቲ ባይዱ性分析
车身主断面设计
定义车身 设计断面
车身主断面
如何进行主断面设计
支掌曲线 参考轴线
造型面 支掌线
支掌
造型
参考轴线
基本断面
支掌曲线 支承
支掌
绘制成精细设计断面图以便管理复杂设计结构
汽车车身三维结构设计
汽车车身钣金设计自由设计区基本原则: