洁净钢的成分控制
第二篇洁净钢发展及钢中夹杂物控制

Institute of Ferrous Metallurgy
脱氧产物总结
• 单个脱氧产物的直径一般小于10μm,由于尺寸较小,除非最终产品要求极高, 一般不会危害钢材的使用性能; • 若脱氧产物与炉渣、耐材反应形成大颗粒夹杂,则会对钢材性能产生严重影响。
表 不同钢中发现的典型脱氧产物 钢种 Al镇静钢 Si镇静钢 Ca处理镇静钢 Al镇静钢,有残余Mg 钛处理镇静钢 脱氧产物类型 Al2O3 SiO2 、MnO-SiO2 CaO-Al2O3 MgAl2O4 Al2O3、 TiOx、 TiN 备注 脱氧后在钢液中形成,固态 脱氧或凝固过程中形成,固态或液态夹杂物 与氧化铝反应形成,固态或液态 与氧化铝反应形成,固态 TiOx形成于二次氧化过程, TiN形成于凝固 过程,均为固态夹杂物
2.3 钢种对夹杂物特征的要求
钢种 IF钢 汽车深冲钢板 易拉罐钢 压力容器钢 抗HIC钢(油气管) 管线钢 滚珠轴承 帘线钢 重轨钢 最高纯净度,×10-6 [C]≤30, [N] ≤40, T.O ≤40 [C]≤10, [N] ≤50 [C]≤10, [N] ≤30 [C]≤30, [N] ≤30, T.O ≤20 [P] ≤70 [P]≤50, [S] ≤10 [S]≤30, [N] ≤35, T.O ≤30 T.O ≤10 [H]≤30, [N] ≤40, T.O ≤15 [H]≤2, [N] ≤40, T.O ≤20 最小夹杂物尺寸,μm
图 FeO-MnO-SiO2 三元相图
Institute of Ferrous Metallurgy
钢中夹杂物来源Ⅰ---脱氧产物
• Si+Mn+Al脱氧
• 脱氧产物:
MnO·SiO2
℃ 1150
洁净钢与纯净钢
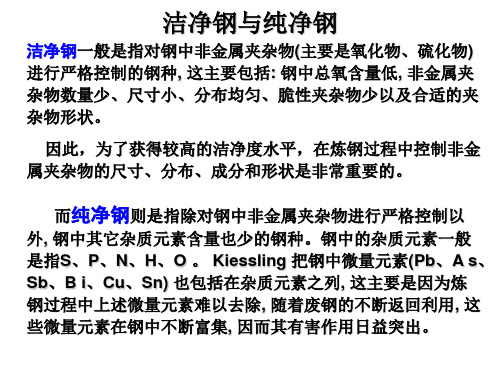
洁净关钢于一纯般净是钢指(对pu钢ri中ty非st金ee属l)夹或杂洁物净(钢主(要c是lea氧n化st物ee、l) 硫的化概物念), 进目行前严国格内控外制尚的无钢统种一, 这的主定要义包。括: 钢中总氧含量低, 非金属夹 杂物数量少、尺寸小、分布均匀、脆性夹杂物少以及合适的夹 杂物形状。
纯净钢除了要考虑[S]+[P]+[N]+[O]+[H]五大元素外,随废钢
量的增加,还要关注Cu、Zr、Sn、Bi、Pb等伴生元素。
研究发现,即Байду номын сангаас将钢中总氧降到10ppm以下,钢液中仍 然存在15微米尺度的夹杂物,因此洁净钢的研究目前沿 着两种发展方向进行: 一种是控制钢中总氧量来降低夹杂物含量; 另一种是控制夹杂物成分以减小其对钢性能的影响。
洁净钢是一个相对概念
当1.2某钢0世中一纪的杂杂6质0质年含元代量素:降或[S]非低+[金P到]属+什[N夹么]杂+[水O物]平直+[H接决]或<定9间0于0接p钢p影m种响;和产产品的品生用产途; 性金么不程能属这同度或夹种的决使杂钢年定用物就78代 于性的可00年年, 装能数以代代对 备时量认::,、为洁 和[[SS该尺是净工]]++钢寸洁[[钢艺PP就或净]]++有现不分钢[[NN不代是布。]]++同化洁对可[[OO净产见的水]]++钢品,[[平要HH;的“]]。求<<而性洁8600;如能净00pp有果都钢ppmm害杂没”;;质有不元元影同素素响于降或,“低非那纯 净念地<22钢不生.0高p”是产p附的为出m加概了可;9值念一以0年夹,味稳产代杂“追定品:物洁求地对[S净纯满数]洁+钢净足量[P净”用,]而要+度并户[是N少不加的]为+;指工[要了O夹越和]能求+纯使杂[够H是越用物]高<:好要1效尺0。求0T率寸p[所的p、O要m以优]低;要小质,成洁低商<本净5品0、钢μ钢成的m材批概;。 这夹2样杂1世的物纪“形洁态净要钢合”概适[S念。]+不[P仅]+具[N有]+质[O量]+含[H义]<,5而0p且pm具。有经济含义。
洁净钢生产技术的发展与耐火材料的相互关系

总之,洁净煤技术作为一项重要的能源技术,在缓解全球能源危机和保护环 境方面具有重要意义。今后,我们应进一步加大洁净煤技术的研究与推广力度, 促进其在全球能源转型中发挥更大的作用。
在当今时代,空气洁净技术已经成为我们日常生活中不可或缺的一部分。尤 其在最近几年,随着全球气候变化的加剧和新冠疫情的爆发,空气洁净技术的度 越来越高。本次演示将介绍空气洁净技术的新发展,包括其应用领域、技术原理、 创新实践等方面,并探讨未来的发展方向。
近年来,空气洁净技术取得了许多突破性进展。其中,一种新型的空气净化 技术——光触媒净化技术备受。光触媒净化技术主要利用紫外线的照射,激活光 触媒反应,产生具有氧化能力的自由基,从而分解和去除空气中的有害物质。与 传统的空气净化技术相比,光触媒净化技术具有更高效、更环保、更持久等优点, 因此被广泛应用于室内空气净化、工业废气处理等多个领域。
洁净钢生产技术的未来发展
随着科技的不断发展,洁净钢生产技术也在不断创新和进步。未来洁净钢生 产技术的发展将朝着高效、节能、环保的方向发展。同时,新材料的研发和应用 也将推动洁净钢生产技术的进步。例如,以纳米技术为基础的纳米耐火材料、纳 米金属陶瓷等新型材料的出现和应用,将为洁净钢生产技术的发展带来新的机遇 和挑战。
1、建筑领域:洁净钢在建筑领域被广泛应用于桥梁、高层建筑、厂房等结 构件的制作。
2、汽车领域:洁净钢在汽车制造业中具有重要作用,用于生产高性能汽车 零部件,提高汽车的安全性和舒适性。
3、家电领域:洁净钢在家电行业主要用于生产高档次、高性能的家电产品, 如高档冰箱、洗衣机等。
四、洁净钢的优势
相比其他钢种,洁净钢具有以下优势:
五、结论
综上所述,洁净钢因其优良的性能和广泛的应用领域,具有极大的重要性和 价值。随着科技的不断发展,相信洁净钢在未来还将发挥更大的作用,推动工业 领域的进步。我们期待着洁净钢在未来的发展趋势和更多创新应用。
钢洁净度的评定和控制二

A C D钢公司 " # $ 7 2 / : &’ $ 0 2 K" # $ 0 2 K : &’ $ 8 2 / 0 / / 7 克利夫兰厂 美国 . / / 7 " # $ 6 1 2 / : &’ $ 6 2 /" # $ @ 2 6 : &’ $ 6 2 8 0 内陆钢公司 # $ ( 2 0 : &’ $ 1 2 6" # $ 6 2 @ : &’ $ 0 2 @ 0 / / 8 美国 . " @号 ; $ " -
? @ & BA> &含量对中间包内钢水总氧含量 # $ % & ’ 的影响 ) ! 1 " 策+ 为了减少 ? 采取了如下对 @ &和 A> &的污染 *
& B( % A> ’ ( A> & B1 % 7 8 ’ C7 8 1 (
钢洁净度的评定和控制 二.
OQ P O
从根本上降低补吹频率 4 ; $ "采用副枪 : 采用高效的机械挡渣设备 : 如挡渣球 浮在钢 水和炉渣界面之间 . 有助于减少出钢带入钢包的 : 渣 量约7 钢. 也 可 采 用 一 些 传 感 器9 出 钢 < = > ? : 后: 钢包厚渣层引起了大量渣携带问题 9 例如 : 美 国内陆钢公司第 @ ; $ "车间标准钢种通过机械扒 渣 使钢包炉 渣层厚度低于 @ A &" . 8 B B90 / / 7年 A C D钢 公 司 克 力 夫 兰 厂 最 后 钢 包 渣 平 均 厚 度 为 厂低碳铝镇 ! 1 B B: A C D钢 公 司 印 第 安 那 E F G H I G 静钢钢包渣层厚 / 高强度低合金钢钢包渣 ! B B: 层厚 0 要求增碳条件的钢种渣层厚 7 1 B B:
为什么通过控制渣成分能提高钢的洁净度

为什么通过控制渣成分能提高钢的洁净度?由于轴承部件处于机械设备的连接轴位置,故受到反复应力,因此在使用一定时同之后,可能产生疲劳裂纹。
所以为了保证再与机械设备的使用寿命同步,必须提高轴承钢的品质。
一般来讲.大部分产品所用的轴承钢主要具有较高的Cr-C系成分。
影响轴承钢寿命的因素是非金属夹杂和确偏析等。
在这些因素中,已经用各种方籣对非金属夹杂的影响进行了研究。
根据这些研究可知,非金属天杂起到了应力集中点的作用,并且最终导致了疲劳裂纹的产生和扩大微信公众号:hcsteel。
主要结论是:①当碱度高于4时,由于Si02是稳定的且不作为氢源.所以对于成分[%(质量分数)]为0.99C-O,3Mn-l. 3Cr的轴承钢的去除夹杂来讲,顶渣的碱度并不影响钢的洁净度。
②对于轴承钢去除夹杂来讲,控制CaO/Al2 03比是最为有效的方法(控制其值在1. 7---1.8最有效)。
通过采用这种方法,可以使全氧T[OJ从(10~12) Xl0-6降低到(5-8)Xl0-6。
③随着出钢时氧含量的降低,轴承钢的T[0]降低,但当CaO/AI2 03; >2,O时,由于在炼钢时间内要达到平衡状态的Ti0太高,所以对出钢时的氧含量没有实质性影响。
在原有工艺的基础上,可增加A1量对降低氧化物、硫化物、夹杂物起到积极的作用。
主要原因在蓋跞初期钢中的氧主要是以Al2 03夹杂物形式存在,这有利于在喷吹过程中去除。
在喷吹过程中,Ca0与Alz。
S结合,提供了很好的去除条件,优化后的工艺使轴承钢的质量有明显的改善,这是降低钢中氧化物夹杂的重要技术思路。
这是因为喷人钢液中的Ca具有相当强的脱硫能力。
喷吹Si-Ca粉的过程,应主要是Ca的脱硫,但覆盖渣对脱硫的影响不可忽略。
具有强的脱氧能力的覆盖渣,在出钢及喷吹过程中在渣钢界面进行脱硫反应,还通过钙脱硫产物间的相互作用,促进钙脱硫反应的进行,保证了深脱硫效果的实现。
喷粉精炼工艺之所以取得比电炉工艺成倍的提高材质的使用寿命,关键在于喷粉工艺通过喷吹装置吹入粉状物质,大大加速反应的动力学,有利于夹杂物细化和上浮,提高了材质的纯洁度。
洁净钢的生产实践

洁净钢的生产实践
洁净钢是一种高质量、低含杂质的钢,它的生产实践主要有以下几个方面。
一、原料准备
使用洁净钢前,必须对原料进行良好的准备,包括对原料的分析、检测和加工。
首先,应检查原料的成分,如少量元素的含量、碳含量和其它元素的含量,以确保原料的质量。
其次,通过进行化学分析,确保原料不含有杂质,以及原料中应该有的元素含量。
最后,应将原料进行冶炼或热处理,以达到所需的物理性能。
二、清洗
为了确保洁净钢的质量,必须在生产过程中进行清洗。
清洗的目的是去除原料上的污垢和油污,以便更好地精炼钢,使其达到洁净钢的要求。
清洗的方法有化学法和物理法。
常用的物理法清洗方法有振动清洗、气动清洗、风力清洗、旋流清洗、喷射清洗等。
三、精炼
精炼是洁净钢生产实践中最重要的环节,因为它是洁净钢质量的决定因素。
精炼的目的是去除杂质,使钢中的各种元素达到所需的含量。
精炼的方法有电弧炉精炼法、渣浆精炼法和熔渣精炼法。
四、冷却
冷却是洁净钢生产实践的重要一步,它主要是为了确保洁净钢的结构稳定,同时也是为了改善洁净钢的耐腐蚀性和焊接性能。
冷却的方法有水冷却、空气冷却等。
五、检测
检测是洁净钢生产实践的最后一步,目的是确定洁净钢的质量。
检测主要有机械性能检测、表面质量检测、化学成分检测、热处理检测等。
以上是洁净钢生产实践中的主要步骤,其中每一步都必须精确控制,才能保证洁净钢的质量。
只有通过严格的检测,才能保证洁净钢的质量,从而满足客户的要求。
如何冶炼洁净钢

冶炼洁净钢应根据品种和用途要求,铁水预处理-炼钢-精炼-连铸的操作都应处于严格的控制之下,主要控制技术对策如下:(1)铁水预处理。
对铁水脱硫或三脱工艺(脱Si、脱P、脱S),入炉铁水硫含量应小于0.005%甚至小于0.002%。
(2)转炉复合吹炼和炼钢终点控制。
改善脱磷条件,提高终点成分和温度一次命中率,降低钢中溶解氧含量,减少钢中非金属夹杂物数量。
(3)挡渣出钢。
采用挡渣锥或气动挡渣器,钢包内渣层厚度控制在50mm以下,转炉内流出的氧化性炉渣会增加氧化物夹杂。
防止出钢下渣可避免回磷和提高合金吸收率。
为保证钢包渣百分之百合格,在钢水接收跨设置钢渣扒渣机是有利的。
(4)钢包渣改质。
出钢过程向钢流加入炉渣改质剂,还原FeO并调整钢包渣成分。
(5)炉外精炼。
根据钢种质量要求选择一种或多种精炼组合方式完成钢水精炼任务,达到脱氢、极低C化、极低S化、脱氮、减少夹杂物和夹杂物形态控制等。
1)LF炉。
包盖密封,造还原渣,可扩散脱氧、脱硫、防止渣中FeO和MnO对钢水再氧化。
调整和精确控制钢水成分、温度,排除夹杂物并进行夹杂物形态控制。
2)真空处理。
冶炼超低碳钢的脱碳和脱氧、脱氢、脱氮,排除脱氧产物。
(6)保护浇注。
在浇注过程中采用保护浇注技术对生产洁净钢尤为重要。
1)钢包→中间包注流用长水口+吹氩保护,控制钢水吸氮量小于1.5ppm(1.5×10-4%),甚至为零。
2)中间包→结晶器用浸入式水口+保护渣的保护浇注,钢水吸氮小于2.5ppm(2.5×10-4%)。
3)浇注小方坯时,中间包→结晶器采用氩气保护浇注,气氛中Φ02<1%。
4)在第一炉开浇前中间包内充满空气,为防止钢水中生成大量的Al203和吸氮,在中间包内充入氩气,并用耐火纤维密封中间包体与包盖间的缝隙。
(7)中间包冶金。
在中间包内组织钢水的合理流动,延长钢水停留时间,促进夹杂物上浮。
1)采用碱性包衬的大容量深熔池中间包;2)中间包加砌挡墙+坝、多孔挡墙、过滤器,采用吹氩搅拌、阻流器;3)中间包覆盖剂可保温、隔绝空气,吸附夹杂物;生产洁净钢中间包采用碱性覆盖剂为宜;4)滑动水口高的自开率,自开率应大于95%;5)开浇、换包、浇注即将结束时防止卷渣;6)应用中间包热态循环使用技术;7)应用中间包真空浇注技术。
钢中夹杂物控制原理

钢中夹杂物控制原理钢中氧的存在形式T[O]=[O]溶+[O]夹(1)转炉吹炼终点:[O]夹=>0,T[O]→[O]溶=200~1000ppm[O]溶决定于:l 钢中[C],转炉吹炼终点钢中[C]与a[O] 关系如图l 渣中(FeO);l 钢水温度。
1 顶底复吹转炉炉龄C–Fe的选择性氧化平衡点根据式[C] + [O] = {CO} (1) lg (Pco/ac* [%O])= 1149/T–2.002以及反应[Fe] + [O] = (FeO)(2) lg aFeo/[%O] = 6317/T – 2.739得到反应(FeO)+ [C] = [Fe] + {CO} (3) lg (Pco/ac* aFeo)= –5170/T+4.736 结论钢液中C-Fe的选择性氧化平衡点为[C]=0.035%,也就是说终点[C] < 0.035%时,钢水的过氧化比较严重。
图1-1的统计数据也说明了这点。
同时由式(1)可以求出此时熔池中的平衡氧含量为740ppm。
理论分析1)终点[C]-[O]关系1) 当终点[C]<0.04%时钢水的终点氧含量较高2) 当终点[C]在0.02~0.04%范围时,有些炉次钢水氧波动在平衡曲线附近(区域Ⅰ)有些炉次钢水氧含量则远离平衡曲线(区域Ⅱ),说明在该区域钢水过氧化严重。
2)温度对氧含量的影响在终点[C] = 0.025~0.04%时,终点氧含量虽然较分散,但总的趋势是随着终点温度的升高,终点氧基本呈上升趋势。
1620℃~1680℃之间,氧含量总体水平较低,平均为702ppm ,该范围的炉次共占总炉次的30%左右;出钢温度大于1680℃时,终点钢水氧含量有明显的升高趋势,平均为972ppm ,占总炉次的70%左右。
3)终渣氧化性对终点氧的影响20040060080010001200140016001800160016201640166016801700172017401760终点温度(℃)终点氧含量(p p m )渣中(FeO+MnO)增加,终点[O]有增加趋势;终点[C]<0.04%,渣中(FeO+MnO)增加且波动较大,说明此时吹氧脱碳是比较困难的,而铁则被大量氧化。
洁净钢氧含量的控制
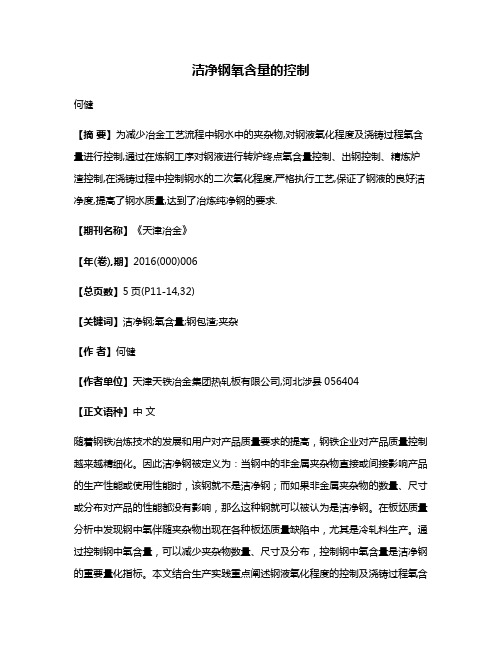
洁净钢氧含量的控制何健【摘要】为减少冶金工艺流程中钢水中的夹杂物,对钢液氧化程度及浇铸过程氧含量进行控制,通过在炼钢工序对钢液进行转炉终点氧含量控制、出钢控制、精炼炉渣控制,在浇铸过程中控制钢水的二次氧化程度,严格执行工艺,保证了钢液的良好洁净度,提高了钢水质量,达到了冶炼纯净钢的要求.【期刊名称】《天津冶金》【年(卷),期】2016(000)006【总页数】5页(P11-14,32)【关键词】洁净钢;氧含量;钢包渣;夹杂【作者】何健【作者单位】天津天铁冶金集团热轧板有限公司,河北涉县056404【正文语种】中文随着钢铁冶炼技术的发展和用户对产品质量要求的提高,钢铁企业对产品质量控制越来越精细化。
因此洁净钢被定义为:当钢中的非金属夹杂物直接或间接影响产品的生产性能或使用性能时,该钢就不是洁净钢;而如果非金属夹杂物的数量、尺寸或分布对产品的性能都没有影响,那么这种钢就可以被认为是洁净钢。
在板坯质量分析中发现钢中氧伴随夹杂物出现在各种板坯质量缺陷中,尤其是冷轧料生产。
通过控制钢中氧含量,可以减少夹杂物数量、尺寸及分布,控制钢中氧含量是洁净钢的重要量化指标。
本文结合生产实践重点阐述钢液氧化程度的控制及浇铸过程氧含量控制。
当转炉吹炼到终点时,钢水中溶解了过多的氧,我们称之为溶解氧[O]溶。
我们将钢水中总氧含量表示为T[O],钢水中T[O]含量能够反映出钢水纯净度,也就是钢中夹杂物的水平,一般表示T[O]为:T[O]=[O]溶+[O]夹,因此想要降低钢中T[O]含量,只能从[O]溶和[O]夹两方面入手,。
分析造成冷轧料表面线状缺陷和表面起皮缺陷原因,主要在于连铸坯下含有Al2O3等类型夹杂物。
因此想要降低冷轧料表面的缺陷,就要降低钢中的脱氧夹杂物,而要降低钢中夹杂物,首先就要降低转炉终点钢水氧含量([O]溶),这是产生夹杂物的源头;其次,充分发挥精炼能力促使脱氧产物([O]夹)的上浮排除;避免钢水在连铸浇铸过程中的二次氧化。
钢的纯净度评测及其控制

钢的纯净度估测及其控制<The Evaluation Methods and Control of Steel Cleanliness>1.引言随着社会发展和科技进步, 对钢质量, 尤其对它的纯净度(cleanliness)要求越来越高. 除了要降低钢中非金属氧化物夹杂物(non-metallic oxide inclusions)的含量, 控制其尺寸、形貌和成分外, 就洁净钢(clean steel)而言, 还要求控制其硫(S)、磷(P)、氢(H)、氮(N), 甚至碳(C), 并且要尽可能减少钢中金属杂质元素(metallic impurity elements), 诸如: 砷(AS)、锡(Sn) 、锑(Sb)、硒(Se)、铜(Cu)、锌(Zn)、铅(Pb)、镉(Cd)、碲(Te)、铋(Bi)等.不同钢种因其不同的应用场合和条件,对上述要求也各不相同。
例下表所示:表1 对不同钢种典型的纯净度要求(Typical steel cleanliness requirements for various steel grades)钢中的金属杂质元素(metallic impurity elements)通常被视为残余元素(trace elements).由于它们在炼钢和精炼过程很难去除,所以在钢中不断累积,成为废钢供应的一大问题。
鉴于钢中如存在超量的残余金属元素,会造成晶间偏析(intergranular segregation)、有害析出物和其它一些问题。
目前,在钢的生产过程中为了克服钢中残余元素造成的危害,尤其是电炉炼钢,通常采用严格控制废钢的种类和用量。
近年来世界各国普遍采用高炉铁水、直接还原铁、海绵铁、碳化铁或其它相对纯的铁来替代废钢,旨在降低钢中残余元素含量。
从钢中残余元素角度讨论钢纯净度问题近年来已有不少相关研究的报道和论文发表。
我们今天主要讨论钢厂普遍存在,大家又十分关注并想得到解决的问题:〈低碳铝镇静钢氧化物夹杂对其纯净度的影响〉。
钢洁净度的评定和控制一

钢洁净度的评定和控制!一"关键词钢洁净度夹杂物尺寸分布形态#$%&’吸氮(前言市场对洁净钢的需求逐年增加)除了要求降低钢中非金属氧化物夹杂含量和控制其形态*化学成分及尺寸分布外)还要求降低钢中杂质元素!如+,*-*.*/*甚至0"和痕量元素!如+12*,3*,4*,5*06*-4及78"含量9表(为普通用钢内杂质元素对其机械性能的影响9表(钢中杂质元素对其机械性能的影响元素存在形式对机械性能的影响, #$&硫化物和氧化物夹杂延性)冲击值)各向异性可成型性!延伸率)断面收缩率和弯曲性能"深冲和冷拔性能低温韧性疲劳强度0 /固溶体沉积位移珠光体和渗碳体碳化物和氮化物析出固溶度!增加")淬透性变形老化!增加")延性和韧性!降低"位移!增加")延性和韧性!降低"沉淀)晶粒细化!增加")韧性!增加"碳化物和氮化物在晶间析出致脆裂-固溶体固溶度!增加")淬透性!增加"回火脆性析出)二次加工脆化钢材中的夹杂物可引起许多缺陷)例如)美国国家钢公司:8;<52=厂低碳铝镇静钢发生边部裂纹)经鉴定)该裂纹是由脱氧和二次氧化产物1>?&@夹杂*来自中间包覆盖剂的铝酸钙和夹带的结晶器保护渣而引起9纵向裂纹发生在带钢表面平行于轧制方向)裂纹可导致低碳铝镇静钢汽车板表面缺陷和可成型性问题)正如美国内陆钢公司A号7&B车间和国家钢公司大湖厂多项研究论文所述)钢中的铝酸盐夹杂物来自裹入结晶器的脱氧产物和复合非金属夹杂物9钢的洁净度取决于钢中非金属夹杂物的数量*形态和尺寸分布)因钢种及其用途不同而定义不同)如表?所示9表?各类钢种对钢洁净度的要求钢种夹杂物含量C D(E F A G夹杂物最大尺寸C H I J B钢汽车板和深冲钢%0’K@E)%/’KA E)#$%&’KA E%0’K(E)%/’KL E%0’K@E)%/’K@E(E EM J罐%0’K@E)%/’K@E)#$%&’K?E?E压力容器用合金钢%-’KN E合金钢棒材%.’K?)%/’K(E O?E)#$%&’K(E抗.J0钢!酸性介质油气管"%-’KL E)%,’K(E管线钢%,’K@E)%/’K@L)#$%&’K@E)%/’KL E(E E 连续退火薄板%/’K?E焊接厚板%.’K($L轴承钢#$%&’K(E(L轮胎钢芯线%.’K?)%/’KA E)#$%&’K(L(E晶粒未取向电磁钢板%/’K@E厚板%.’K?)%/’K@E OA E)#$%&’K?E单个夹杂+(@)夹杂物簇+?E E 线材%/’KP E)#$%&’K@E?E由于大型宏观夹杂对钢的机械性能危害最大)其尺寸分布非常重要9据报道)(Q R典型的低碳铝镇静钢含(E N O(E S个夹杂物!其中)仅含T E O(@E H I夹杂物A E E个)(@E O?E E H I夹杂物(E 个)?E E O?N E H I夹杂物少于(个"9显然)检测少量大型夹杂物是非常困难的9尽管大型夹杂物在数量上比小型夹杂物少得多)但其总体积分数可能较大)有时一个大型夹杂物能引起整个一炉钢的灾难性缺陷9因此)洁净钢不仅要控制钢中夹杂物平均含量)而且还要避免夹杂物尺寸超过对产品有害的临界尺寸9由此)表?中列出了许多钢材对夹杂物最大尺寸的限定值9夹杂物尺寸分布的UVWU?E E A年第(期鞍钢技术1/X1/X#Y0./&Z&X[重要性在图!中得到了进一步解释"测试结果表明#大于$%&’的夹杂物由钢包内的!()!*!%+,-降到中间包的%(./*!%+,-"因此#尽管钢包内钢水总氧含量稍高且夹杂物总量较多#中间包内的钢水还是较洁净的"图!钢包和中间包内0123$夹杂物尺寸分布非金属夹杂物来源很多#包括45!6脱氧产物"例如低碳铝镇静钢内的主要夹杂物是0123$#该夹杂物因钢中溶解氧与加入的脱氧剂5如016化学反应而产生#0123$夹杂在富氧环境下生成#形状呈树枝状#其中可能也包括一些较小的0123$颗粒碰撞聚集物"526二次氧化产物"例如钢水中残留的7018被渣中9:3氧化或暴露在大气中氧化生成0123$"5$6出钢时带入的冶金炉渣"通常为球形液态夹杂"5,6其它来源的外来夹杂物"如飞灰;剥落的耐火砖衬和陶瓷炉衬颗粒"这类夹杂物通常尺寸大且形状不规则"它们常常作为0123$非均质形核的晶核并夹带某些颗粒"5.6化学反应产物"如用<=改质处理夹杂物时#反应进行不正常时出现的产物"控制钢的洁净度贯穿炼钢工艺的各项操作#内容包括4脱氧和合金化的时间及地点;炉外精炼的程度和顺序;搅拌和倒包操作;保护浇铸装置;中间包几何形状及操作;各种冶金熔剂的吸收能力以及浇铸操作"钢的洁净度问题在各类相关文献中都是备受关注的"!>/%年?@:A A 1@B C首次全面综述了关于钢锭内夹杂物和痕量元素的控制及评价方法"最近#这一学术领域由D E ;F G 1=H H =和<I =’J提出最新论述#内容增加了热力学条件"本文介绍了钢洁净度技术的最新进展#首先回顾了钢的洁净度的评价方法#接着概述了世界许多钢厂对低碳铝镇静钢的洁净度;总氧含量K (738和吸氮的间接测量"最后叙述了钢包;中间包和连铸操作中#提高钢的洁净度的操作实践"本文收集了许多关于钢的洁净度的数据#目的是为洁净钢生产提供有用的信息#焦点是控制0123$夹杂"2钢洁净度的评价方法研究和控制钢的洁净度的关键是其精确的评价方法#在炼钢生产的各个阶段测定夹杂物的数量;尺寸分布;形状和化学成分"尽管测定技术有多种5有精确而昂贵的直接测定法#还有快速而廉价的间接测定法6#只有可靠性是相对的选择依据"2(!直接测定法钢的洁净度的一些直接测定法概述如下45!6金相显微镜观测5D D 36"这是一种传统的方法#用光学显微镜检测二维钢样薄片#并且用肉眼定量"整理整个试样复合型夹杂物检验结果时#提出问题"例如#由于较小的一簇夹杂物在整理试验结果时可被忽略"但是#用这种方法数小夹杂物太浪费时间#而大型夹杂物又太少"尽管有些方法二维结果与三维实际情况相关#问题还是很多"526图像扫描5L 06法"该法采用高速计算机计算显微镜视频扫描图像"根据灰度的断续分辨明暗区#比肉眼观测的D D 3法大有改进#很容易测定较大面积和较多数量的夹杂物"但是#有时容易将非金属夹杂物引起的划痕;麻点和凹坑弄错"5$6硫印法"这种方法通用而廉价"通过对富硫区进行腐蚀#区分宏观夹杂和裂纹"该法的问题与其他二维方法相同"5,6电解5蚀6法"这种方法精确度高但费时"较大的钢样52%%C M 2N C 6完全被酸5F <16溶解#然后收集残留的非金属夹杂物#以便计算和进一步分析"另外#为了保留非金属夹杂物9:3#将浸入9:<12或9:O 3,溶液的钢样通电溶解"这种方法适合观测单个且完整的夹杂物"5.6电子束熔炼5P Q 6法"在真空条件下#用电子束熔化钢样#夹杂物上浮到钢水表面"通常电子RS T R U 鞍钢技术V 2%%,年第!期束熔炼查找的是上浮夹杂物特定区域!目前已开发出了电子束熔炼的升级法"#$%#&’(用来评估夹杂物尺寸分布!此法靠测定几个区域的上浮夹杂物尺寸(推断所有夹杂物的上浮结果(从而计算夹杂物尺寸分布指数!")’水冷坩埚熔炼法"**’!在电子束熔炼的条件下(先将熔融钢样表面的夹杂物浓缩(再冷却后(样品被分解(夹杂物被分离出来!这种方法靠减少溶解金属的体积分离夹杂物!"+’扫描电子显微术",#-’!这种方法可清晰地观测到每种夹杂物的三维组织结构和化学成分(用电子探针分析仪"#.-/’检测化学成分!"0’脉冲鉴别分析光谱测量法"1#,%.2/’!光学发射光谱测量法是分析钢中溶解元素的传统方法!13456钢公司采用这一技术在取样789:;之内分析出总氧含量<微小夹杂物尺寸分布和化学成分!为了检测固态夹杂物(作发射火花的闪光记录!为了优化铁元素的基础发光信号和夹杂物的干扰发光信号比值(定义了电信号的特征曲线!高强度=/>?火花峰值就是脉冲鉴别分析指数!"@’曼内斯曼夹杂物检测法"-A2/,’!先使钢样波动(以排除气泡(然后超声扫描检测固态夹杂物和固<气复合夹杂物(这一方法最近被重新发现(命名为B,C.法!"78’激光衍射颗粒尺寸分析法"B2.,/’!采用这项激光技术检测其他方法"如淀泥法’检测出的夹杂物的尺寸分布!"77’常规的超声波法"*D,’!该法可以确定固态钢样内大于E8F9的夹杂物尺寸分布!"7E’锥形样品扫描法!此法用螺旋运动检测仪"如超声系统’自动扫描连铸产品的圆锥形样品表面每个位置的夹杂物!"7G’分级热分解法"H I2’!不同氧化物夹杂在不同温度还原(如氧化铝基氧化物还原温度为7J88K或7)88K(耐火材料夹杂物还原温度为7@88K(总氧含量为每个加热步骤测出的氧含量之和!"7J’激光显微探针质谱分析法"B/--,’!用脉冲激光束照射每个颗粒(选择电离临界值之上最低激光强度值作为其化学状态特征光谱图!通过与标样比较(激光显微探针质谱分析的强度峰值与每个化学元素对应!"7L’M N射线光电子光谱法"M.,’!此法采用M N射线检测尺寸大于78F9的夹杂物化学状态!"7)’俄歇电子光谱法"/#,’!采用电子束检测夹杂物化学状态!"7+’光电扫描法!分析用其他方法分离出来的夹杂物的光电扫描信号(以监测其尺寸分布!"70’库尔特计数分析法!这种方法与B A-*/法相似(可检测电蚀法分离出的夹杂物尺寸分布!"7@’液态金属洁净度分析法"B A-*/’!这种方法用传感器在线直接检测钢液中的夹杂物!由于穿过空隙进入传感器的夹杂物颗粒能改变空隙断面的电导率(检测电导率的变化便可检测夹杂物!"E8’钢水超声技术!此法吸收超声脉冲反射信号(在线检测钢中夹杂物!E O E间接方法根据成本<时间要求和取样的难度(钢铁工业通常采用检测钢中总氧<吸氮和其他的间接方法测量钢的洁净度!E O E O7定氧钢的总氧含量是溶解氧和非金属氧化物夹杂结合的氧之和!用定氧传感器很容易测定溶解氧=1?(用脱氧元素"如铝’化学反应平衡热力学控制钢中的总氧!铝和氧反应平衡条件如下P>6Q R S>6Q"=/>?E=1?G’S%)E+08T U"R’VE8O L J"7’例如P70+G W"7)88K’时(RS7O8L X78%7G(如果=/>?S8O8G YZ8O8)Y(溶解氧=1?为"8[888G YZ8O888L Y’!由于溶解氧含量不是很多(可间接地测定钢中氧化物夹杂的氧含量(以其代替总氧含量!钢中大夹杂物占少数(且定氧用钢样尺寸太小"约E8Q’(样品内几乎无大的夹杂物(既使一个样品内有一个大夹杂物(由于读数异常地高(数据很可能大打折扣!因此(总氧含量实际上代表小型氧化物夹杂中的氧含量(而不是大型氧化物夹杂含量!然而(总氧含量低会降低大型氧化物夹杂存在的可能性(如图E所示!可见(总氧含量指标仍非常重要(且通常标志着钢的洁净度!如图G所示(检测到的钢水样内的总氧含量与产品的裂纹发生率明显有关!尤其是中间包取样成分标志着处理板坯的洁净度!如日本川崎钢公司要求中间包钢水样I O=1?低于8O88G Y的条\]^\钢洁净度的评定和控制"一’件下!可保证冷轧薄板供货免检"#$##%&’#$##((&为要求检验的临界值"#$##((&以上的炉次要改判)一些钢厂生产低碳铝镇静钢各工序钢中*+,-.控制水平如表%所示/表%空格部分意味着参考文献中无合适的数据0)图1钢中总氧含量和宏观夹杂之间的关系图%中间包内总氧含量与产品裂纹指数间的关系从表%可以得出下述结论2/30随着新技术的实现!低碳铝镇静钢中*+ ,-.含量逐年降低)例如!新日铁钢中*+,-.从345#年的#+##6&’#+##(&降低到344#年的#+##1&)/1078处理的钢水*+,-./#$##3&’#$##%&0比钢包气体搅拌*+,-./#$##%(&’#$##6(&0含量低)/%0随着工序的进行!*+,-.逐步降低!依次为2钢包#$##6&9中间包#$##1(&9结晶器#$##1&及板坯内#$##3(&)1+1+1吸氮检测表%国内外先进钢铁厂生产纯净钢各工序钢中全氧量:;3#<6&钢厂精炼方法钢水包中间包结晶器板坯时间美洲内陆钢公司6号=->?@>%#16133(344#阿姆克@A B B C D E F G H厂78I#’3#(3(’6#/1(03I+4’1%+J3443 K+L钢公司?F M N A H厂=-O真空脱气3%’353443北美某厂1#’%(1#’%#3#’3(3443 *A P Q D H公司8N M M A R F H厂1#’%#3443加拿大多法斯科厂?>S78343%3%+134413446 ?*T钢公司克力夫兰厂13’15344(阿特莱斯不锈钢厂气体搅拌%I’6(%#’%J344(美国UD A M E F H炼钢车间V M N W F<781%X3#11X31344(巴西K R A P A H N R厂3%344%欧洲芬兰劳塔鲁基拉赫钢厂6J X31%1%J35344%芬兰Y F D M Z N M厂/高碳钢0气体搅拌%11%1###德国V A C C A H[D M厂3#’3(3#\3(3446荷兰霍戈文艾莫伊登厂真空脱气]^]Y3(’%1_>钢1#’%#34463446法国索拉克V‘H Q A M Q厂78<V=1#’(#3445英钢联78a3#3446奥钢联林茨厂3I3446亚洲川崎制铁千叶厂786#1#34J4川崎制铁水岛厂Y*=/b c^N-:]C1-%0a1(/3+J0a%(/3+10a6#/#+J0a((344Id Y Y!传统787835344% d Y Y!78加喷粉78喷粉5344% d Y Y!传统T-V T-V%%+J344% d Y Y!T-V加喷粉T-V喷粉1(+3344% d Y Y京滨厂3号炉a1#3443新日铁8Ne Z A P N H厂1I34J4韩国浦项钢公司781(’%3a15a3#344%34433443台湾中钢公司?>S78a%#313446中国宝钢集团公司^]L<-=78351+(5#4%(513’1(6J+J3%+J’35+(3441344(中国武钢集团公司78S?>53’5%36+51##1注2/0内数据为平均值)fghf i鞍钢技术j1##6年第3期不同炼钢容器内!尤其是钢包和中间包"#钢中含氮量不同说明倒包过程吸氮$例如#%&’()*钢厂洁净钢生产要求从钢包到中间包吸氮上限为+,++-.$脱氧后#钢中溶解的氧含量低使其迅速吸氮#因此#通过检测吸氮#可以间接粗略检测吸氧$二次氧化导致的钢的洁净度和产品质量问题如图/01所示$值得注意的是#硫是减少吸氮和氧化的表面活性元素$图1吸氮和总氧含量与钢的质量指数的关系表1总结了几个钢厂生产低碳铝镇静钢时每道工序的吸氮情况#由表/01可以得出如下结论2 !-"通过采用新技术和改进操作#吸氮逐年降低$如法国索拉克钢公司敦刻尔克厂#中间包到结晶器钢水吸氮从-344年的+,+++3.降低到-335年的+,+++-.$!5"一般而言#钢包到结晶器钢水吸氮可控制在+6+++-.7+6+++/.#通过优化倒包操作可减少浇铸期间吸入的空气#将吸入空气控制在+6+++-.以下#保护浇铸对吸氮的作用将在下文讨论$!/"多数钢厂将低碳铝镇静钢的氮含量控制在+6++/.7+6++1.#主要靠炼钢转炉或电炉操作加以控制#但也受炉外精炼和保护浇铸操作的影响$表1国内外先进钢铁厂各工序钢中吸氮情况!89:;<=-+>1."钢厂工艺89:;时间多法斯科钢公司钢包?中间包中间包?结晶器中间包?结晶器中间包?结晶器@--,4+,/+,A5-335-33A 威尔顿钢公司钢包?结晶器中间包?结晶器17-+@A-33/前-33/后阿姆克钢公司阿什兰厂中间包?结晶器5-33/内陆钢公司1号B C D钢包?中间包/-33+美钢联费尔菲尔德厂钢包?中间包1E,A-33A-33A前法国索拉克钢公司敦刻尔克厂钢包?中间包中间包?结晶器钢包?中间包中间包?结晶器+,A7-,/-/3-33A-335-33A前-344墨西哥钢公司钢包?结晶器A-33F 德国迪林根厂钢包?中间包钢包?结晶器AA-33/-33/中国宝钢钢包?中间包-7A-33A中国武钢钢包?结晶器/,473,/-33A5,5,/溶解铝减少值的检测对低碳铝镇静钢而言#钢中溶解铝的减少意味着发生了二次氧化$然而#由于铝也能被炉渣二次氧化#所以检测溶解铝的降低值比检测吸氮精度低$5,5,1炉渣成分检测分析每项操作前后炉渣成分的变化#可检测出夹杂物被炉渣吸收的情况$另外#通过观测渣中痕量元素变化和夹杂物成分#可检测出每炉钢炉渣中夹杂物$5,5,A检测浸入式水口结瘤因结瘤引起的浸入式水口寿命缩短#一般说明钢水的洁净度低$众所周知#低碳铝镇静钢内少量G H5C/夹杂就能引起水口堵塞$连铸低碳铝镇静钢结瘤物典型成分为2G H5C/A-,E.#D&11.# I*C5,/.#J’C5-,1.#K L C+,F.$!待续"潘秀兰编译!编辑许平静"收稿日期25++/>+E>-5MNOM钢洁净度的评定和控制!一"。
纯净钢简介及使用

•
4 行业对纯净钢的要求
• • • • 目前齿轮行业标准已将汽车用齿轮钢的氧含量规定为≤20ppm,而很多采用 LF+VD或LF+RH精炼处理的特殊钢厂家,已可以将齿轮钢的氧含量控制在 15ppm以下(国外一般水平)。 非金属夹杂物中B、D类夹杂对齿轮的疲劳寿命影响非常大,这两类夹杂物也 与氧含量有关,同时与非金属夹杂物的尺寸及分布有很大关系。 目前要求B类夹杂不大于2级,D类夹杂不大于l级。 A类夹杂对齿轮钢的疲劳寿命影响不大,并且随着易切削齿轮的发展,钢中对 硫含量的上、下限都提出了要求,因此齿轮钢今后对A类夹杂的数量、形态及 分布提出要求。 c类夹杂为硅酸盐类夹杂,由于冶炼装备的变化,目前国内大多数特钢厂都可 以达到1级以下的水平。
4 行业对纯净钢的要求
铃木加普腾 OTEVA70SC:在中等高温环境下具有高的抗扑来性能和抗松弛性能
4 行业对纯净钢的要求
4.2 轴承钢
•
轴承钢质量的优劣主要从三个方面来衡量:一是纯净度,即钢中夹杂物的含 量,主要是氧化物的含量;二是轴承钢的均匀性,一般指夹杂物的形态和分布; 三是钢材的表面质量,包括尺寸精度和表面裂纹等。
4 行业对纯净钢的要求
• • 日本大同特钢减少钛系夹杂减轻“疲劳度” 大同特钢生产采用MRAC-SSS工艺生产的高质量轴承钢,其钢中氧含量≤5ppm, 可以低到3.4ppm;钛含量≤5ppm;氮含量≤30ppm,并且可以得到极细小的氧化物 夹杂和钛系夹杂物。采用MARC工艺后,钢中未发现≥7.5μm的Al2O3氧化物夹 杂,并且钢中几乎不存在CaO-Al2O3系夹杂物。钢中钛的夹杂物含量少,尺寸 细小。 采用MRAC-SSS工艺生产的超纯净轴承钢的接触疲劳寿命得到延长,较传统精 炼工艺生产的轴承钢长25%以上!
洁净炼钢的夹杂物特征和质量控制

清 洁炼 钢 工具 和 质量 控 制 同等 重 要 , 因为在 工 艺过 程 中 , 通过 钢水 洁净度 的测 量设定 它 们 的标 准 。
过去 经 常采用 多重过 程 中和离 线工具 确定 钢种 的 洁 净度 。先 前 出 版 的 文 献 列 出 了 在 安 塞 乐 米 塔 尔 R & D 以及 北美 钢 厂 平 时采 用 的 一 些 技 术 。这 些 技 术包 括采 用 自动扫 描 电子 显 微镜 ( S E M) 、 阴极 电子 激发 光显 微镜 ( C L M) 、 脉 冲鉴 别分 析 ( P D A) 对钢 水 和炉 渣化 学成 分测量 、 夹 杂物分 析 , 并 且测 量产 品特
或者 对产 品性 能 的不 利影 响降 至最小 。
采 用 发 射光 谱 仪分 析 棒 状钢 样 化学 组 成 , 采用 力 可燃 烧分 析仪 分 析 中 间包 或 结 晶器 试 样 中的硫 。 试 样首 先经 发射 光谱 仪 P D A分析 夹 杂物 , 然后 采 用 相 同的光谱 仪分 析 钢水 化 学 组 成 , 仅 有钙 处 理 钢 种
2 0 1 6年第 4期
现
代
冶
金
2 1
洁净 炼 钢 的夹 杂物 特 征 和质 量 控 制
( 美国) P . K a u s h i k等
摘
要: 为 了适应内外部顾客的需求 , 提高炼钢 和浇铸过程 , 包括监测和评价现有和新 开发的钢水精炼 工艺。半成
品的内部质量控制需要一种工具 , 其与工艺过程反常导致 产 品缺 陷相关 。本 文重点关 注 了采 用的技术 , 像成 品钢
生 产 过 程 控制 条 件 的必 要 性 所 带 来 的优 点 , 同时可提高钢材质量。
钢洁净度的评定和控制

钢洁净度的评定和控制1前言市场对洁净钢的需求逐年增加,除了要求降低钢中非金属氧化物夹杂含量和控制其形态、化学成分及尺寸分布外,还要求降低钢中杂质元素(如:S、P、H、N、甚至C)和痕量元素(如:As、Sn、Sb、Se、Cu、Pb及Bi)含量。
表1为普通用钢内杂质元素对其机械性能的影响。
钢材中的夹杂物可引起许多缺陷,例如,美国国家钢公司Midwest厂低碳铝镇静钢发生边部裂纹,经鉴定,该裂纹是由脱氧和二次氧化产物Al2O3夹杂、来自中间包覆盖剂的铝酸钙和夹带的结晶器保护渣而引起。
纵向裂纹发生在带钢表面平行于轧制方向,裂纹可导致低碳铝镇静钢汽车板表面缺陷和可成型性问题,正如美国内陆钢公司4号BOF车间和国家钢公司大湖厂多项研究论文所述,钢中的铝酸盐夹杂物来自裹入结晶器的脱氧产物和复合非金属夹杂物。
钢的洁净度取决于钢中非金属夹杂物的数量、形态和尺寸分布,因钢种及其用途不同而定义不同,如表2所示。
由于大型宏观夹杂对钢的机械性能危害最大,其尺寸分布非常重要。
据报道,1kg典型的低碳铝镇静钢含107~109个夹杂物(其中,仅含80~130Lm夹杂物400个,130~200Lm夹杂物10个,200~270Lm 夹杂物少于1个)。
显然,检测少量大型夹杂物是非常困难的。
尽管大型夹杂物在数量上比小型夹杂物少得多,但其总体积分数可能较大,有时一个大型夹杂物能引起整个一炉钢的灾难性缺陷。
因此,洁净钢不仅要控制钢中夹杂物平均含量,而且还要避免夹杂物尺寸超过对产品有害的临界尺寸。
由此,表2中列出了许多钢材对夹杂物最大尺寸的限定值。
夹杂物尺寸分布的重要性在图1中得到了进一步解释。
测试结果表明,大于30Lm的夹杂物由钢包内的1.61×10-4%降到中间包的0.58×10-4%。
因此,尽管钢包内钢水总氧含量稍高且夹杂物总量较多,中间包内的钢水还是较洁净的。
图1钢包和中间包内Al2O3夹杂物尺寸分布非金属夹杂物来源很多,包括:(1)脱氧产物。
洁净钢冶炼及质量控制

• 脱氧与夹杂物
• 复吹
炉外精炼
• 含义:把炼钢炉炼出的成品钢或半成品钢,
在炉外设备中进行脱硫、脱氧、脱碳、去气、 去夹杂、调整化学成分和温度等处理,进一 步提高钢的质量和品质的工艺方法。 • 功能 • 手段 • 方法
连铸
• 连铸过程
• 二次氧化与保护浇注
• 中间包冶金
• 保护渣
夹杂物控制
• 非金属夹杂物:在冶炼和浇注过程中产生或混入钢中,
经加工或热处理后仍不能消除而且与钢基体无任何联系而 独立存在的氧化物、硫化物、氮化物等非金属相,统称为 非金属夹杂物,简称夹杂物。 • 非金属夹杂物是指其存在状态不受一般热处
理的显著影响的非金属化合物。
补充:夹杂物分类
• 按化学成分分类
• 按夹杂物的来源分类
钢中微量元素(Pb 、As 、Sb 、Bi 、Cu 、Sn) 的含量
也很低
纯净钢与洁净钢概念
• 洁净钢( clean steel) :指对钢中非金属夹杂物(主要是
氧化物、硫化物) 进行严格控制的钢种,要求夹杂物对钢 的性能无害。 这主要包括:钢中总氧含量低,非金属夹杂物 • 数量少 ;尺寸小
• 分布均匀;形状合适
• 钢材的断裂过程是裂纹的不断发生和发展的过程,而夹 杂物往往作为显微裂纹的起点而起重要的作用。因此,
夹杂物对金属材料与断裂过程有关的性能指标如延伸率
﹑断面收缩率等影响很大。当夹杂物的数量增加时,钢 的塑性下降。
• 夹杂物对钢的疲劳寿命有不利的影响,按降低疲劳寿命
的程度从强到弱排列:刚玉﹑球状不变性夹杂﹑半塑性
• 按夹杂物的颗粒大小分类
• 按加工时夹杂物的变形性能来分类
夹杂物控制
洁净钢精炼渣控制工艺研究

3. 28
1. 41
RH 出站 43. 09 6. 34 34. 66
9. 14
1. 85
0. 27
2
出钢
40. 97 8. 89
1. 77
5. 81 21. 99
5. 33
RH 进站 49. 83 7. 56 31. 00
6. 84
0. 45
0. 27
RH 破空 42. 86 6. 94 33. 30
表 2 铸坯总氧和大型夹杂物含量
炉次 w( T. O) /10 - 6
1
29
2
27
3
28
10 kg 铸坯中大型夹杂物量 / mg 3. 72 4. 09 2. 32
由表 2 可知,铸坯总氧含量都在 30 × 10 - 6 以 下,10 kg 铸坯中大型夹杂物平均含量3. 38 mg 左 右,大型夹杂物控制水平较高。中薄板坯连铸机 可连浇 6 炉以上,解决了 Ti-IF 钢难浇性问题。
SiO2 对脱氧钢液的二 次 氧 化。从 表 1 中 可 以 看 出,精炼渣的二元碱度很高,w( CaO) / w( SiO2 ) = 5 ~ 11。钢包渣吸收 Al2 O3 夹杂的能力保持在较 高的水平,同时防止了由 SiO2 引起的二次氧化, 抑制了回硅、回硫。
除精炼渣碱度以外,渣中 w ( CaO) / w( SiO2 ) 对脱氧有着不可忽视的作用。日本川崎水岛厂生 产 超 低 碳 钢 的 试 验 表 明[2], 当 顶 渣
第2 期
袁晓峰,等:洁净钢精炼渣控制工艺研究
·47·
的相对溶解速率较高。
图 3 Al2 O3 在 CaO-Al2 O3 -SiO2 渣系的相对溶解速率
精炼渣碱度对钢水脱氧有较大影响。研究表 明[6],随着碱度提高和渣中 SiO2 含量的降低,精 炼渣的脱氧能力提高,这是由于渣中 SiO2 含量的
H08A冶炼操作

洁净钢的成分控制(8)洁净钢的成分控制---钢中氢含量当压力为1毫巴时,氢气在钢中溶解度为0.91×10-4%。
实际上,通常要求钢中[H]<2×10-4%。
为了达到此目标,保持钢液处于非常低的压力是非常重要的。
脱[H]主要靠转炉炼钢初期通过CO的激烈沸腾脱氢和RH处理过程中脱氢。
其余各阶段均是增氢的,所以脱[H]的重点在于防止脱气处理后连铸过程各阶段的增氢,应该严格控制渣成分和状态。
由于造渣剂,合金料的潮湿以及新砌中间包未干,大气吸入所引起的增氢等等。
氢的去除以前主要在炼钢初期通过CO激烈沸腾得到,自真空处理技术出现以后钢中氢已可稳定控制在2×10-6以下。
严格杜绝各工序造渣剂、合金料、覆盖剂以及耐材的潮湿,避免碳氢化合物、空气与钢水接触,都有助于降低钢中氢的含量。
在真空度<66.7Pa,且吹Ar量>50L/min条件下,保持10min以上,在真空处理过程中,以弱电磁搅拌为主。
搅拌方向向上,搅拌电流为400~600A,离站前,净化弱搅拌时间不小于5min。
整个真空处理时间约25~35min。
可使钢中氢含量<2×10-6,最低达0.92×10-6。
2008-11-22 21:55:29 作者:zhaoluo 来源:制钢参考网浏览次数:324 文字大小:【大】【中】【小】洁净钢的成分控制---钢中氧及夹杂物的控制硬线钢丝、钢轨、轴承钢、弹簧钢等中高碳合金钢或优质碳钢,对钢中夹杂物有严格的要求。
为保证钢材质量,必须采用低氧钢精炼工艺技术。
对低氧钢精炼工艺的基本要求是:(1)严格控制钢中总氧含量,一般要求钢中[T.O]≤25×10-6。
对于轴承钢,为提高钢材的疲劳寿命,则要求钢中[T.O]≤10×10-6。
(2)严格控制钢中夹杂物的形态,避免出现脆性Al2O3夹杂物。
如硬线钢精炼,要求严格控制钢中夹杂物成分中w(Al2O3)≤25%。
洁净钢生产工艺及技术

洁净钢生产工艺及技术1. 引言洁净钢是一种具有高纯净度和低杂质含量的钢材,它在现代工业中具有广泛的应用。
洁净钢的生产工艺和技术对于提高钢材的质量和性能具有重要意义。
本文将介绍洁净钢的生产工艺及技术,包括材料准备、熔炼工艺、净化工艺和热处理工艺等方面。
2. 材料准备洁净钢的生产首先需要准备高质量的原材料。
一般而言,使用优质的铁矿石和石墨粉为原材料。
在材料准备过程中,需要对铁矿石进行破碎、筛分和磁选等处理,以去除其中的杂质。
同时,还需要对石墨粉进行筛分和干燥处理,以确保其纯净度和质量。
3. 熔炼工艺洁净钢的熔炼工艺是保证钢材质量的关键步骤。
在熔炼过程中,采用电弧炉作为主要设备,并在炉内加入适量的石墨粉,以促进石墨的溶解和扩散。
此外,还需要在熔炼过程中控制熔炼温度、保持炉内气氛的稳定,并通过合理调整熔炼时间和翻炉工艺等措施,以确保熔炼的钢液质量达到洁净钢的要求。
4. 净化工艺净化工艺是提高钢材纯净度的重要措施。
常用的净化工艺包括真空脱气、氧化脱硫和氢脱氮等。
在真空脱气过程中,通过将熔炼好的钢液置于真空环境下,利用钢液中的氢、氮等气体的挥发性,将其去除。
氧化脱硫是指在钢液中加入氧化剂,使之与硫反应生成气体,从而将硫从钢液中去除。
氢脱氮是指通过在钢液中通入氢气,使之与钢液中的氮气反应生成气体,从而将氮从钢液中去除。
5. 热处理工艺热处理工艺是洁净钢生产的最后一道工序,它能够通过改变钢材的组织结构,进一步提高钢材的性能。
常见的热处理工艺包括淬火、回火和正火等。
淬火是指将热处理后的钢材迅速冷却,以使其获得较高的硬度和强度。
回火是指将淬火后的钢材加热到适当的温度,然后冷却,以使其获得合适的韧性和延展性。
正火是指将热处理后的钢材加热到适当的温度,保温一段时间后,进行缓慢冷却,以改变钢材的组织结构。
6. 结论洁净钢的生产工艺及技术对于提高钢材的质量和性能具有重要意义。
在生产过程中,需要注意材料准备、熔炼工艺、净化工艺和热处理工艺等方面的要求,以确保生产出符合洁净钢标准的优质钢材。
- 1、下载文档前请自行甄别文档内容的完整性,平台不提供额外的编辑、内容补充、找答案等附加服务。
- 2、"仅部分预览"的文档,不可在线预览部分如存在完整性等问题,可反馈申请退款(可完整预览的文档不适用该条件!)。
- 3、如文档侵犯您的权益,请联系客服反馈,我们会尽快为您处理(人工客服工作时间:9:00-18:30)。
洁净钢的成分控制在钢铁冶炼过程中,一部分杂质元素可以去除,但仍有一部分将残留在钢中,这些残余元素的存在是钢材质量产生不稳定的主要因素之一。
在这些元素中,某些残余元素由于易于偏析,即使其含量很低,也对钢材性能产生很强的有害影响。
因此正确认识钢铁产品中残余元素问题,建立洁净钢的概念及其工艺控制是保证现代钢铁工业生产优质钢材的重要前提。
提高钢的洁净度,可以明显改善钢材的机械性能和加工性能。
主要表现在:(1) 洁净度对钢材机械性能的影响降低钢中的S、P、N等的杂质含量,可以明显提高钢材的强度和韧性,如当钢中的[S]≤0.004%时,NiCrMo钢的冲击韧性明显提高;对于AIST4340钢,[P]从0.03%下降到0.003%,室温C型缺口冲击能约提高20%,而对于含B钢,控制[N]≤20ppm,可以获得很高的强度和低温韧性。
对于轴承钢,降低钢中的全氧含量,可以明显提高轴承的寿命。
因此,高质量的轴承钢,要求钢中T[O]≤10×10-4%。
同时,钢中夹杂物的尺寸、分布与性质对钢材的疲劳极限也有很大的影响。
降低钢中夹杂物,有利于提高钢材的疲劳强度。
对于硅钢(Si=3%),降低钢中的S和T[O]的含量([S] ≤20ppm,T[O] ≤15ppm),可以使无取向硅钢片的铁芯损失降低到2.3w/kg以下。
而降低钢中的[C]和[N]含量,可以提高硅钢片的最大导磁率,降低矫顽力。
(2) 洁净度对钢材加工性能的影响焊接性能是钢材最重要的使用性能之一,降低钢中的含C量或降低钢的碳当量,有利于改善钢的焊接性能。
汽车板、家用电器和DI罐用钢等钢材,不仅要求一定的强度,还要求要有良好的深冲性能,降低钢中C含量,可以明显改善钢的深冲性能。
汽车用高质量IF钢,要求钢中C+N≤50ppm。
此外,生产热轧薄板,必须严格控制钢中大型Al2O 3夹杂物的数量,才能避免轧制过程中产生裂纹,获得良好的表面质量。
如生产0.3mmDI罐用钢板的关键技术是彻底杜绝30~40mm的大型脆性夹杂的出现。
钢中夹杂物的数量与类型对切削刀具寿命有明显的影响,这是由于钢种的脆性夹杂增大了工件与刀具间的摩擦阻力,不利于钢材的切削性能。
因此,尽量降低钢中的脆性夹杂物的含量,有利于改善钢材的切削性能。
钢中的脆性夹杂物对耐磨性有着极坏的影响,对于钢轨钢和轴承钢,钢中Al2O3等脆性夹杂往往造成钢材表面剥落、腐蚀。
因此,严格控制钢中Al2O3近似等于零,可以解决表面磨损的问题,提高钢材的耐磨性能。
N和C一样,是间隙型杂质。
低温时,容易在Fe原子晶格内扩散,引起时效,使钢材低温锻造性能下降。
对于0.35%的碳钢,如果控制钢中的固溶N含量≤50ppm,可以明显降低钢材冷锻时裂纹的产生率。
钢中含有硅及锰元素时,将大大促进残余元素引起的第二类回火脆性。
这可能是由于硅、锰促进残余元素在钢中的扩散及偏析能力。
相反,钢中如果添加适量的钼,一般为0.2~0.5,则可有效地抑制第二类回火脆性。
理论研究和生产实践都证明钢材的纯净度越高,其性能越好,使用寿命也越长。
钢中杂质含量降低到一定水平,钢材的性能将发生质变。
如钢中碳含量从40×10-6降低到20×10-6,深冲钢的伸长率可增加7%。
提高钢的纯净度还可以赋予钢新的性能(如提高耐磨腐蚀性等),因此纯净钢已成为生产各种用于苛刻条件下高附加值产品的基础,其生产具有巨大的社会经济效益。
需要指出的是对不同钢种其中的杂质元素的种类是不同的,如硫在一般钢中都视为杂质元素,但在易切削钢中其为有益元素;IF钢中氮是杂质元素,但在不锈钢中氮可以代替一部分镍和其它贵重合金元素,其固溶强化和弥散强化作用可提高钢的强度。
钢中[H]含量过多,易于产生氢发裂和白点,导致钢的严重缺陷。
硫是钢中的有害元素之一,是表面活性元素,常以MnS的形式在钢材晶界上或异相界面上偏析聚集。
硫对钢材最大的危害是引起钢的热脆,显著降低了钢的热加工性能。
而对于铁素体不锈钢,要求钢中S≤20ppm,保证钢材的热加工性能。
碳钢的S ≤ppm,热加工时可避免产生热裂纹现象。
此外,硫降低钢材的韧性,恶化钢的Z向性能,并对氢致裂纹有较大影响。
因此,要求管线钢具有较高的抗氢致裂纹(HIC)和抗硫应力裂纹(SSCC)的能力,要求控制钢中S≤10×10-6。
近20年来,随着宇航、航空、石油、汽车、国防及微电子工业的蓬勃发展,对钢铁杂质含量的要求越来越苛刻,因为人们发现钢的纯净度愈高,性能愈好。
例如轴承钢:当含氧量[O%]由30×10-4%降为15×10-4%时接触疲劳寿命提高5倍:降到10×10-4%时接触疲劳寿命提高15倍:降到5×10-4%时接触疲劳寿命提高30倍;又如为满足汽车工业对深冲压成型薄板的需求而推出的IF钢(无间隙相元素钢)对碳含量的要求更降至[%C]<30×10-4%已属于超低碳钢。
生产工艺:纯净钢的生产主要集中在两方面:(1)尽量减少钢中杂质元素的含量;(2)严格控制钢中的夹杂物,包括夹杂物的数量、尺寸、分布、形状、类型。
减少钢中溶质元素的含量主要在各种铁水预处理以及二次精炼设备中营造最佳去除的热力学和动力学条件来实现,钢中夹杂物的控制主要是减少其生成、对其进行改性、促其上浮。
通常纯净钢生产工艺包括以下几部分:铁水预处理,转炉复吹,出钢挡渣、扒渣、对炉渣改性,二次精炼(真空、吹气、加热、造渣)、全程保护浇铸、中间包冶金、结晶器冶金及采取各种促使夹杂物去除的措施等。
根据对脱磷采取的不同工艺,洁净钢生产工艺大致可以分为以下两种工艺流程[12]:(1)铁水“三脱”洁净钢生产工艺:以日本为代表,主要的工艺特点是采用铁水预处理脱磷工艺,生产洁净钢。
技术特点是:采用铁水三脱预处理工艺,脱Si、脱S和脱P。
目前,多采用转炉作为铁水“三脱”的反应器,不再需要铁水预脱硅。
复合吹炼转炉采用少渣冶炼工艺,脱碳升温并进行脱磷;通常采用多功能的RH 进行钢水精炼,深脱磷、深脱硫和脱气;转炉弱脱氧“沸腾”出钢,避免钢水吸氮,适宜冶炼超低氮钢;连铸采用保护浇注、夹杂物过滤等一系列技术措施,保证钢水质量。
(2) 钢水精炼洁净钢生产工艺;以欧美为代表,主要依靠转炉脱磷,并采用钢包喷粉深脱磷。
其技术特点是:采用转炉冶炼低碳钢脱磷,脱碳、脱硅、脱磷和升温精炼;转炉弱脱氧出钢,钢包喷粉深脱磷,然后扒渣;LF升温脱硫精炼;RH脱氧和深脱硫,连铸保护浇注;不适宜生产超低N和低P钢种。
(3) 两种精炼工艺的技术比较采用铁水“三脱”工艺,脱P的热力学、动力学条件优于铁水精炼工艺;铁水“三脱”工艺流程短,工艺简单,更适宜冶炼超纯净钢;铁水“三脱”工艺生产纯净钢,生产成本明显低于钢水精炼工艺洁净钢的成分控制--钢液碳的控制钢中碳对钢的性能影响最大,碳含量高能增加钢的强度,但使塑性下降、冲压性能变坏。
因此一般优质深冲型铝镇静钢要求[C]≤0.05%、IF钢要求[C]≤0.007%。
钢中碳的控制主要集中于两点:炉外精炼使钢中碳达到极低水平、防止连铸过程增碳。
RH处理脱碳主要受制约有以下两个因素:一是钢液环流量(是浸渍管直径的函数);二是钢液向气泡[C]传递速率(是真空室横截面积及搅拌能的函数)。
因此可以通过增加钢液循环流量和净化气体流量来提高反应速度。
其主要手段是增大浸渍管直径和吹Ar流量。
目前,国外RH处理,吹Ar流量有500NL/min的记录,浸渍管直径有达1m的记录,国外一些厂家RH处理后钢中[C]最好的降到9~12×10-4%。
防止增碳,首先是防止RH处理从真空罐渣壳中吸碳。
特别是钢包用炭化稻壳保温,这一现象就显得尤为突出。
其次是防止连铸过程中增碳。
中钢公司研究了中间包不同覆盖剂对增碳的影响,发现:使用炭化稻壳,增[C]11.7×10-4%;使用某种粒状保护渣,增[C]7.3×10-4%;使用Mg基粒状覆盖剂,增[C]3.5×10-4%。
法国Sollac Dumkirk厂研究发现,开浇和换钢包期间,增[C]严重,可达10~20×10-4%。
因此,为防止增碳应注重以下几点:一是进一步降低耐火材料中的[C]量,使钢水与含碳材料接触面最小;二是中间包使用含碳少的保温材料;三是减少结晶器保护渣中的[C]含量。
采用RH可以实现超低碳钢精炼。
但当钢中w([C])≤0.002%时,由于钢水静压力的影响,RH脱碳速度减弱,趋于停止。
为了进一步降低钢中含碳量,日本近几年开发出以下新工艺:(1)提高钢水循环流量Q,促进脱碳反应——REDA法。
新日铁八幡钢厂对350tDH 炉进行改造:取消真空室下部槽和吸嘴,将真空室直接插入钢水中,利用钢包底吹Ar搅拌能,大幅度提高RH钢水的循环流量。
使熔池混匀时间从80s降低到40~60s,脱碳速度明显提高。
处理20min,可保证钢水w([C])≤10×10-6;处理30min,钢水[C]可达到3×10-6。
(2)提高容量传质系数αk,促进脱碳反应。
日本川崎钢铁公司为实现超低碳钢冶炼,采用H2作为搅拌气体,吹入RH真空室。
利用RH真空脱气的功能,使H2气从钢液中逸出时增加了反应界面,提高RH的容量传质系数αk。
处理20min,可使钢中[C]达到3×10-6。
众所周知脱硫的热力学条件是高温、高碱度、低的氧化性,因此脱硫应注意以下三点:金属液和渣中氧含量要低、使用高硫容量的碱性渣、钢渣要混合均匀。
铁水预处理可以深度脱硫,也可以部分脱磷。
目前广泛采用在铁水包或鱼雷罐中喂线、喷粉的铁水预处理方法,,喷粉可以造就良好的动力学条件,极大扩展反应界面。
二次精炼是生产超低硫钢所必不可少的手段,所用方法主要为喷粉、真空、加热造渣、喂线、吹气搅拌,实践中常常是几种手段综合采用。
钢中的长条形(尤其是沿晶界分布的)硫化物是产生氢致裂纹的必然条件,对钢水进行钙处理可将其改变为球形,降低其危害,一般钙硫比(Ca/S)接近2为佳。
炉渣的脱硫能力决定于炉渣碱度和渣中FeO含量;对于高碱度炉渣,脱硫反应速度的限制性环节是金属侧硫的传质速度,增强熔池搅拌,有利于提高脱硫速度。
采用低碱度精炼渣可有效地消除钢中点状夹杂物。
实践证明,碱度控制在2.0~2.5范围内,渣量为2%时,脱硫率可达70%。
在EBT电炉出钢过程中投入的脱硫剂,若添加适量的萤石(<10%),可显著提高脱硫效果,且不会对钢包的使用寿命构成危害。
通过含BaO和不含BaO渣系的脱硫动力学对比实验表明:含BaO脱硫渣系具有比不含BaO的脱硫渣系有更快的脱硫速率。
含BaO精炼渣系具有较好的深脱硫作用,在实验室条件下,可将钢中硫稳定的脱除至5×10-6以下,完全适用于极低硫钢的精炼。