SMT典型工艺流程
SMT工艺流程及各工位操作规范

SMT工艺流程及各工位操作规范概述表面贴装技术(Surface Mount Technology,简称SMT)是一种电子组装技术,广泛应用于电子产品的制造过程中。
本文将介绍SMT工艺流程的各个环节,以及各个工位的操作规范。
SMT工艺流程SMT工艺流程可以分为以下几个步骤:1.元件和PCB准备:在工艺开始之前,需要准备好元件和PCB板。
元件应进行分类、清洁和盘装。
PCB板应进行清洁和定位。
2.印刷:将焊膏粘贴到PCB板上。
3.安装:将元件粘贴到PCB板的焊膏上,这一步骤也称为贴片。
4.回流焊接:使焊膏熔化,并固定元件到PCB板上。
5.检查:检查焊接质量,包括元件是否安装正确,焊点是否合格。
6.清洗:清洗PCB板和元件以去除焊膏残留物。
7.测试:对已焊接的PCB板进行功能和性能测试。
8.包装:将已测试合格的PCB板进行包装,以备下一步骤的使用。
工位操作规范1. 元件和PCB准备工位•元件分类:根据元件相关规格和封装形式,进行分类并放置在对应位置,以便后续使用。
•元件清洁:使用适当的清洁剂和工具对元件进行清洁,以去除表面的污垢和油渍。
•元件盘装:根据所需数量,将清洁的元件装入元件盘,确保装盘过程中元件之间的间隔适当。
•PCB清洁:使用清洁剂和无尘布对PCB板进行清洁,确保表面干净无污垢。
•PCB定位:使用适当的夹具或模板,确保PCB板在后续工艺过程中位置准确。
2. 印刷工位•选择合适的印刷机:根据PCB板的尺寸和要求,选择适合的印刷机进行操作。
•调整印刷机参数:根据焊膏的特性和PCB板的要求,调整印刷机的速度、压力和刮刀角度等参数。
•焊膏印刷:将焊膏均匀地印刷到PCB板上,确保覆盖面积和厚度均匀一致。
3. 安装工位•选择合适的贴片机:根据PCB板的尺寸和元件的要求,选择适合的贴片机进行操作。
•调整贴片机参数:根据元件封装形式和PCB板的要求,调整贴片机的速度、压力和放料方式等参数。
•元件安装:将元件粘贴到已上焊膏的PCB板上,确保位置准确。
smt车间生产工艺 流程
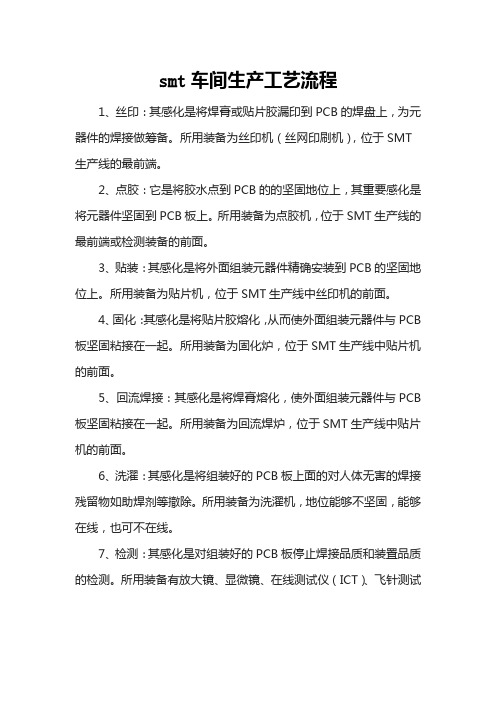
smt车间生产工艺流程
1、丝印:其感化是将焊膏或贴片胶漏印到PCB的焊盘上,为元器件的焊接做筹备。
所用装备为丝印机(丝网印刷机),位于SMT 生产线的最前端。
2、点胶:它是将胶水点到PCB的的坚固地位上,其重要感化是将元器件坚固到PCB板上。
所用装备为点胶机,位于SMT生产线的最前端或检测装备的前面。
3、贴装:其感化是将外面组装元器件精确安装到PCB的坚固地位上。
所用装备为贴片机,位于SMT生产线中丝印机的前面。
4、固化:其感化是将贴片胶熔化,从而使外面组装元器件与PCB 板坚固粘接在一起。
所用装备为固化炉,位于SMT生产线中贴片机的前面。
5、回流焊接:其感化是将焊膏熔化,使外面组装元器件与PCB 板坚固粘接在一起。
所用装备为回流焊炉,位于SMT生产线中贴片机的前面。
6、洗濯:其感化是将组装好的PCB板上面的对人体无害的焊接残留物如助焊剂等撤除。
所用装备为洗濯机,地位能够不坚固,能够在线,也可不在线。
7、检测:其感化是对组装好的PCB板停止焊接品质和装置品质的检测。
所用装备有放大镜、显微镜、在线测试仪(ICT)、飞针测试
仪、主动光学检测(AOI)、X-RAY检测系统、功效测试仪等。
地位依据检测的必要,能够配置在生产线适合的处所。
8、返修:其感化是对检测呈现毛病的PCB板停止返工。
所用对象为烙铁、返修工作站等。
配置在生产线中随意率性地位。
SMT工艺流程及各工位操作规范

SMT工艺流程及各工位操作规范SMT(表面贴装技术)是一种电子组装技术,广泛应用于电子产品的制造中。
在SMT工艺流程中,需要经过一系列的工位操作,以确保电子产品的质量和稳定性。
以下是SMT工艺流程及各工位操作规范的简要介绍。
1. 印刷工艺:在印刷工艺中,操作员需要将油墨印刷到PCB(印刷电路板)上。
操作规范包括:确保油墨的质量和稠度,精准地将油墨印刷到指定的区域,以及及时清洁印刷设备。
2. 贴片工艺:在贴片工艺中,操作员需要将SMT元件精准地贴片到PCB上。
操作规范包括:确保元件的质量和定位精度,避免元件的错位和损坏,以及及时清洁贴片设备。
3. 焊接工艺:在焊接工艺中,操作员需要使用热风和焊膏将SMT元件与PCB焊接在一起。
操作规范包括:确保焊接的温度和时间控制在合适范围内,避免产生焊接质量问题,以及及时清洁焊接设备。
4. 检测工艺:在检测工艺中,操作员需要使用X射线检测或其他检测设备对焊接后的PCB进行质量检测。
操作规范包括:确保检测设备的准确性和稳定性,及时发现和修复焊接质量问题。
5. 清洗工艺:在清洗工艺中,操作员需要使用清洗设备将PCB上的残渣和污垢清洗干净。
操作规范包括:确保清洗设备的清洁度和能效性,避免清洗剂残留,以及及时清洁清洗设备。
以上是SMT工艺流程及各工位操作规范的简要介绍。
在实际生产过程中,操作员需要严格按照规范操作,以确保产品质量和生产效率。
同时,定期维护和保养设备,做好生产记录和质量追溯,也是确保SMT工艺质量的重要保证。
SMT(表面贴装技术)是一种广泛应用于电子产品制造中的先进电子组装技术。
它相对于传统的插件装配技术具有更高的生产效率、更高的集成度和更好的可靠性。
SMT工艺需要通过一系列的工位操作来完成产品的生产,每个工位都有其独特的操作规范和技术要求。
以下将介绍SMT工艺中常见的工位和操作规范。
6. 烘烤工艺:在烘烤工艺中,操作员需要将已经焊接好的PCB放入烘烤设备中进行固化和干燥。
SMT典型工艺流程
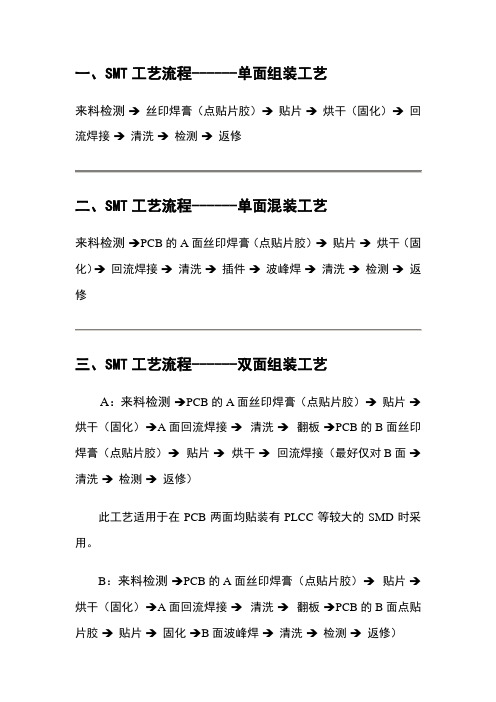
一、SMT工艺流程------单面组装工艺
来料检测→丝印焊膏(点贴片胶)→贴片→烘干(固化)→回流焊接→清洗→检测→返修
二、SMT工艺流程------单面混装工艺
来料检测→PCB的A面丝印焊膏(点贴片胶)→贴片→烘干(固化)→回流焊接→清洗→插件→波峰焊→清洗→检测→返修
三、SMT工艺流程------双面组装工艺
A:来料检测→PCB的A面丝印焊膏(点贴片胶)→贴片→烘干(固化)→A面回流焊接→清洗→翻板→PCB的B面丝印焊膏(点贴片胶)→贴片→烘干→回流焊接(最好仅对B面→清洗→检测→返修)
此工艺适用于在PCB两面均贴装有PLCC等较大的SMD时采用。
B:来料检测→PCB的A面丝印焊膏(点贴片胶)→贴片→烘干(固化)→A面回流焊接→清洗→翻板→PCB的B面点贴片胶→贴片→固化→B面波峰焊→清洗→检测→返修)
此工艺适用于在PCB的A面回流焊,B面波峰焊。
在PCB的B 面组装的SMD中,只有SOT或SOIC(28)引脚以下时,宜采用此工艺。
四、SMT工艺流程------双面混装工艺
A:来料检测→PCB的B面点贴片胶→贴片→固化→翻板→PCB的A面插件→波峰焊→清洗→检测→返修先贴后插,适用于SMD元件多于分离元件的情况
B:来料检测→PCB的A面插件(引脚打弯)→翻板→PC B的B面点贴片胶→贴片→固化→翻板→波峰焊→清洗→检测→返修
先插后贴,适用于分离元件多于SMD元件的情况
C:来料检测→PCB的A面丝印焊膏→贴片。
smt工艺流程步骤

smt工艺流程步骤SMT(表面贴装技术)工艺流程是一种用于电子组装的重要技术。
下面将详细介绍SMT工艺流程的步骤。
第一步:基板准备在开始SMT工艺流程之前,首先需要准备好电子产品的基板。
一般来说,基板是通过化学方法去除表面污垢,然后经过打磨和去毛刺处理,以确保基板表面光滑和精确尺寸。
第二步:印刷贴装在印刷贴装步骤中,一层名为“贴装胶浆”的胶水被平均地印在基板的表面上。
然后,贴装设备会将元件逐个精确地放置在胶水上。
这些元件包括电阻器、电容器、晶体管、集成电路等。
贴装设备通常使用计算机控制,以确保元件的准确位置。
第三步:回流焊接在回流焊接步骤中,贴装好的元件将被送入一个特殊的炉子中,称为回流炉。
在回流炉中,基板通过一系列的加热区域,以达到焊接的温度。
当基板达到回流焊接的温度时,焊料会熔化并封固在基板上,连接元件和基板。
第四步:清洗在焊接完成后,基板上可能会残留一些焊接过程中产生的污垢和残留物。
因此,清洗是SMT工艺流程中一个非常重要的步骤。
清洗通常使用化学溶液或超声波清洗机进行。
这将确保基板表面干净,且不会对电路功能产生负面影响。
第五步:检验在检验步骤中,基板将经过一系列的测试和检查,以确保电路的正常功能。
常见的测试方法包括可视检查、自动光学检查、X射线检查和各种电气测试。
这些测试可以帮助检测到任何电路连接问题或组件缺陷,并进行修复或更换。
第六步:封装和包装在完成检验后,基板将被封装和包装。
封装是将基板放置在具有特定尺寸和形状的外壳中的过程。
封装可以提供保护和机械支撑。
之后,封装好的产品将被包装成最终的电子产品,以便运输和销售。
总结:SMT工艺流程是一种现代化的电子组装技术,提供了高效、精确、快速的方式来组装电子产品。
这种工艺可以大大提高生产效率,减少成本,并提高电路质量。
通过以下步骤:基板准备、印刷贴装、回流焊接、清洗、检验、封装和包装,我们可以完成整个SMT工艺流程,生产出高质量的电子产品。
SMT工艺流程及各工位操作规范

SMT工艺流程及各工位操作规范一、前言SMT(Surface Mount Technology)是一种基于表面贴装技术的电子元件贴装工艺。
本文将介绍SMT工艺的整体流程以及各工位操作的规范。
二、SMT工艺流程概述SMT工艺流程包括PCB板表面处理、贴片、回流焊等多个环节。
下面将详细介绍各个流程的操作规范。
1. PCB板表面处理在SMT工艺中,PCB板表面处理是非常重要的一环。
正确的表面处理可以确保元件的粘贴牢固,焊接质量良好。
•清洗:在表面处理之前,一定要对PCB板进行清洗,去除表面的污垢和氧化层。
•化学处理:可以通过化学方法对PCB板进行表面处理,增加元件与PCB板之间的黏附力。
2. 贴片在SMT工艺中,贴片是将各种电子元件粘贴到PCB板上的过程。
•手动贴片:对于一些小批量生产,可以采用手动贴片的方式,但需要保证操作人员的技术熟练度。
•自动贴片:对于大批量生产,通常会采用自动贴片机进行操作,提高生产效率。
3. 回流焊回流焊是SMT工艺中的最后一道工序,通过高温将电子元件焊接到PCB板上。
•控温控时间:在回流焊过程中,要严格控制温度和时间,确保焊接的质量。
三、各工位操作规范1. 贴片操作规范•在进行贴片操作时,要保证工作环境的清洁,避免灰尘和杂物影响粘贴效果。
•操作人员应熟练掌握贴片机的操作技巧,保证元件的精准贴合。
•贴片机的清洁和维护也是非常重要的,定期清洁贴片机,保持其良好运行状态。
2. 回流焊操作规范•操作人员要保证在回流焊过程中的安全,避免高温烫伤等意外发生。
•严格遵守回流焊的温度和时间要求,确保焊接的质量。
•在回流焊过程中,要及时检查焊接部位是否均匀,确保焊点完全熔合。
四、结论SMT工艺在电子生产制造中扮演着重要的角色,正确的操作规范可以提高生产效率,确保产品质量。
制定良好的工艺流程和操作规范对于SMT工艺的成功应用至关重要。
smt的工艺流程
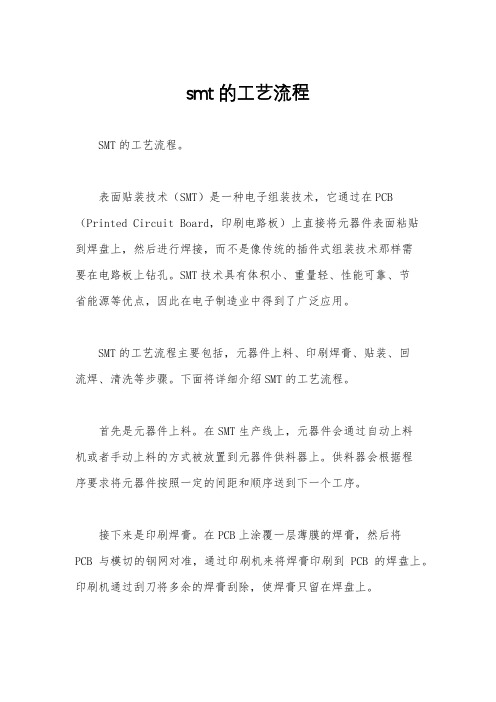
smt的工艺流程SMT的工艺流程。
表面贴装技术(SMT)是一种电子组装技术,它通过在PCB (Printed Circuit Board,印刷电路板)上直接将元器件表面粘贴到焊盘上,然后进行焊接,而不是像传统的插件式组装技术那样需要在电路板上钻孔。
SMT技术具有体积小、重量轻、性能可靠、节省能源等优点,因此在电子制造业中得到了广泛应用。
SMT的工艺流程主要包括,元器件上料、印刷焊膏、贴装、回流焊、清洗等步骤。
下面将详细介绍SMT的工艺流程。
首先是元器件上料。
在SMT生产线上,元器件会通过自动上料机或者手动上料的方式被放置到元器件供料器上。
供料器会根据程序要求将元器件按照一定的间距和顺序送到下一个工序。
接下来是印刷焊膏。
在PCB上涂覆一层薄膜的焊膏,然后将PCB与模切的钢网对准,通过印刷机来将焊膏印刷到PCB的焊盘上。
印刷机通过刮刀将多余的焊膏刮除,使焊膏只留在焊盘上。
然后是贴装。
在SMT贴装机的作用下,元器件从供料器上被吸取到贴装头上,然后根据程序要求精准地贴装到PCB的焊盘上。
SMT贴装机具有高速、高精度的特点,能够满足不同元器件的贴装要求。
接着是回流焊。
在回流焊炉中,通过加热将焊膏熔化,使得元器件与PCB焊盘之间形成可靠的焊接连接。
回流焊炉具有多个加热区域,可以根据焊接工艺要求进行温度曲线的控制,以确保焊接质量。
最后是清洗。
在SMT生产过程中,焊接过程中可能会产生焊渣或者残留的焊膏,因此需要进行清洗。
清洗机通过喷淋、刷洗等方式将PCB表面的污垢清洗干净,以确保电路板的质量。
总结一下,SMT的工艺流程包括元器件上料、印刷焊膏、贴装、回流焊、清洗等步骤。
这些步骤相互配合,共同完成了电子组装的工艺流程,为电子产品的生产提供了高效、精准的制造技术支持。
通过不断的工艺改进和技术创新,SMT技术将会在未来的电子制造领域发挥越来越重要的作用。
SMT整个工艺流程细则
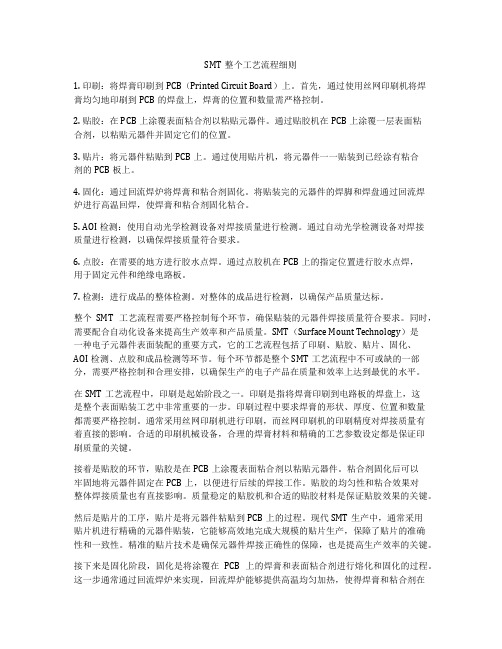
SMT整个工艺流程细则1. 印刷:将焊膏印刷到PCB(Printed Circuit Board)上。
首先,通过使用丝网印刷机将焊膏均匀地印刷到PCB的焊盘上,焊膏的位置和数量需严格控制。
2. 贴胶:在PCB上涂覆表面粘合剂以粘贴元器件。
通过贴胶机在PCB上涂覆一层表面粘合剂,以粘贴元器件并固定它们的位置。
3. 贴片:将元器件粘贴到PCB上。
通过使用贴片机,将元器件一一贴装到已经涂有粘合剂的PCB板上。
4. 固化:通过回流焊炉将焊膏和粘合剂固化。
将贴装完的元器件的焊脚和焊盘通过回流焊炉进行高温回焊,使焊膏和粘合剂固化粘合。
5. AOI检测:使用自动光学检测设备对焊接质量进行检测。
通过自动光学检测设备对焊接质量进行检测,以确保焊接质量符合要求。
6. 点胶:在需要的地方进行胶水点焊。
通过点胶机在PCB上的指定位置进行胶水点焊,用于固定元件和绝缘电路板。
7. 检测:进行成品的整体检测。
对整体的成品进行检测,以确保产品质量达标。
整个SMT工艺流程需要严格控制每个环节,确保贴装的元器件焊接质量符合要求。
同时,需要配合自动化设备来提高生产效率和产品质量。
SMT(Surface Mount Technology)是一种电子元器件表面装配的重要方式,它的工艺流程包括了印刷、贴胶、贴片、固化、AOI检测、点胶和成品检测等环节。
每个环节都是整个SMT工艺流程中不可或缺的一部分,需要严格控制和合理安排,以确保生产的电子产品在质量和效率上达到最优的水平。
在SMT工艺流程中,印刷是起始阶段之一。
印刷是指将焊膏印刷到电路板的焊盘上,这是整个表面贴装工艺中非常重要的一步。
印刷过程中要求焊膏的形状、厚度、位置和数量都需要严格控制。
通常采用丝网印刷机进行印刷,而丝网印刷机的印刷精度对焊接质量有着直接的影响。
合适的印刷机械设备,合理的焊膏材料和精确的工艺参数设定都是保证印刷质量的关键。
接着是贴胶的环节,贴胶是在PCB上涂覆表面粘合剂以粘贴元器件。
SMT工艺流程范文

SMT工艺流程范文SMT(Surface Mount Technology)是一种表面贴装技术,是目前电子制造中最常见的一种组装技术。
SMT工艺流程指的是在使用SMT技术进行电子产品组装的过程中所涉及的各个环节和步骤。
下面将详细介绍SMT工艺流程。
一、PCB(Printed Circuit Board)制造在SMT工艺流程中的第一步是制造PCB,即将电路图案通过化学蚀刻、酸洗等方式在铜层上制作出来。
然后通过钻孔、埋线、喷锡等工艺步骤,将PCB制作得更加完整。
二、基板上涂敷焊膏在完成PCB制造之后,下一步是将焊膏涂敷到PCB上。
焊膏是一种半固态的合金,可以在高温下熔化并粘附到PCB上,用于连接元件和PCB。
三、自动贴装在涂敷完焊膏之后,下一步是将元件自动贴装到PCB上。
这一步骤主要是通过自动贴装机来完成的。
自动贴装机会将元件从元件库中取出,并定位到正确的位置,然后利用真空吸盘将元件粘附到PCB上。
四、回流焊接在自动贴装完成后,下一步是进行回流焊接。
回流焊接是利用热空气或者热波对焊膏进行加热,使其熔化并与PCB和元件相互粘结在一起。
这样,PCB上的元件就能够实现良好的电气连接。
五、清洗在焊接完成后,需要对PCB进行清洗。
清洗的目的是去除焊接过程中留下的焊剂残留物、污染物等,以保证产品的质量和性能。
六、检测清洗完成后,需要对已焊接的PCB进行检测以确保其质量。
检测的方式包括视觉检测、电气测试等,主要是为了验证焊接是否正确、是否存在短路、虚焊等问题。
七、组装在完成检测后,下一步是对PCB进行组装。
这一步骤包括将已焊接的PCB装入外壳、安装按键、显示屏、电池等。
组装的过程通常需要进行多个步骤,具体根据产品的要求而定。
八、测试组装完成后,需要对整个产品进行测试以确保其能正常运行。
测试的方式包括功能测试、性能测试、可靠性测试等,以验证产品的质量和可靠性。
九、包装以上就是SMT工艺流程的基本步骤。
SMT工艺流程的每个环节都非常重要,只有每个环节都完成得非常精细和严谨,才能确保最后的产品质量和性能。
SMT工艺流程PPT课件
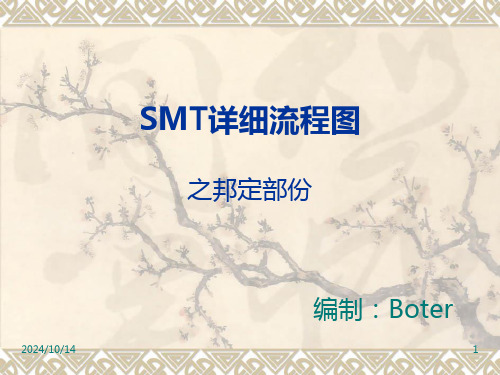
之邦定部份
2024/10/14
编制:Boter
1
准备夹具、测试架 技术资料核对
机器配置准备
设备参数调试 N
设备故障修理 Y
交生产线继续使用
邦定工艺流程图
邦定
生产线安排生产
物料上机 N
核对物料 Y
点胶、贴芯片
PMC
下达生产计划
领料员发放物料
邦定测试过镜修理 封胶
烤箱固化
炉后检查
产品装箱
2024/10/14
邦定技术服务商
配件、维修和技 术支持
2
研发中心
拟发工程更改单 拟发新工程料单
2024/10/14
邦定工艺控制流程图
邦定
ME按料单制 作生产程序和上料卡
ME工艺组更改工程料 单、生产程序及上料卡
备份保存
按工艺要求制作邦定工艺指 导卡
相关部门
拟发工程更改单
品管 审核
Y
贴 胶 纸 工 艺 卡
Y
线长 N
是否停拉 Y 停拉
品管
N
Y 是否停拉
N
抽检机 芯品质 是否良
好Y
入库、出货
•ME有责任
对生产线提 出的工艺问 题进行调试、 确认。
•对模组进行检 查,发现不良 现象及时调试。 •调试不了的请 ME调试。
2024/10/14
•对机芯进行全 检,对不良机 芯进行纠正, 并及时反映给 操作工。保证 机芯100%合格。
邦定转机流程图
接上级生产安排 按工艺指导卡领PCB及IC
N
IPQC核对物料
Y
邦机程序调试
各生产环节生产参数确认 首件生产及确认
正常生产
SMT生产工艺流程

SMT生产工艺流程一、SMT生产工艺流程表面贴装工艺:单面组装工艺流程:(全部表面贴装元器件在PCB的一面)来料检测->丝印焊膏->贴片->回流焊接->(清洗)->检验->返修。
双面组装; (表面贴装元器件分别在PCB的A、B两面)来料检测-> PCB的A面丝印焊膏->贴片-> A面回流焊接->翻板-> PCB的B面丝印焊膏->贴片-> B面回流焊接->(清洗)->检验->返修混装工艺:单面混装工艺: (插件和表面贴装元器件都在PCB的A面)来料检测-> PCB的A面丝印焊膏->贴片-> A面回流焊接-> PCB的A面插件->波峰焊或浸焊(少量插件可采用手工焊接)-> (清洗) ->检验->返修(先贴后插)双面混装工艺:(外表贴装元器件在PCB的A面,插件在PCB的B面) A.来料检测-> PCB的A面丝印焊膏->贴片->回流焊接-> PCB的B面插件->波峰焊(少量插件可采用手工焊接) ->(清洗)->检验->返修。
B.来料检测-> PCB的A面丝印焊膏->贴片->手工对PCB 的A面的插件的焊盘点锡膏-> PCB的B面插件->回流焊接->(清洗) ->检验->返修(外表贴装元器件在PCB的A、B面,插件在PCB的任意一面或两面)先按双面组装的方法举行双面PCB的A、B两面的外表贴装元器件的回流焊接,然后进行两面的插件的手工焊接即可二、SMT工艺设备介绍1.模板:首先根据所设计的PCB肯定是不是加工模板。
假如PCB 上的贴片元件只是电阻、电容且封装为1206以上的则可不用制造模板,用针筒或自动点胶设备举行锡膏涂敷;当在PCB中含有SOT、SOP、PQFP、PLCC和BGA封装的芯片和电阻、电容的封装为0805以下的必需制造模板。
SMT工艺经典十大步骤

SMT工艺经典十大步骤第一步骤:製程设计表面黏著组装製程,特别是针对微小间距元件,需要不断的监视製程,及有系统的检视。
举例说明,在美国,焊锡接点品质标準是依据IPC-A-620及国家焊锡标準ANSI / J-STD-001。
了解这些準则及规范后,设计者才能研发出符合工业标準需求的產品。
量產设计量產设计包含了所有大量生產的製程、组装、可测性及可*性,而且是以书面文件需求為起点。
一份完整且清晰的组装文件,对从设计到製造一系列转换而言,是绝对必要的也是成功的保证。
其相关文件及CAD资料清单包括材料清单(BOM)、合格厂商名单、组装细节、特殊组装指引、PC板製造细节及磁片内含Gerber资料或是IPC-D-350程式。
在磁片上的CAD资料对开发测试及製程冶具,及编写自动化组装设备程式等有极大的帮助。
其中包含了X-Y轴座标位置、测试需求、概要图形、线路图及测试点的X-Y座标。
PC板品质从每一批货中或某特定的批号中,抽取一样品来测试其焊锡性。
这PC板将先与製造厂所提供的產品资料及IPC上标定的品质规范相比对。
接下来就是将锡膏印到焊垫上迴焊,如果是使用有机的助焊剂,则需要再加以清洗以去除残留物。
在评估焊点的品质的同时,也要一起评估PC板在经歷迴焊后外观及尺寸的反应。
同样的检验方式也可应用在波峰焊锡的製程上。
组装製程发展这一步骤包含了对每一机械动作,以肉眼及自动化视觉装置进行不间断的监控。
举例说明,建议使用雷射来扫描每一PC板面上所印的锡膏体积。
在将样本放上表面黏著元件(SMD) 并经过迴焊后,品管及工程人员需一一检视每元件接脚上的吃锡状况,每一成员都需要详细纪录被动元件及多脚数元件的对位状况。
在经过波峰焊锡製程后,也需要在仔细检视焊锡的均匀性及判断出由於脚距或元件相距太近而有可能会使焊点產生缺陷的潜在位置。
细微脚距技术细微脚距组装是一先进的构装及製造概念。
元件密度及复杂度都远大於目前市场主流產品,若是要进入量產阶段,必须再修正一些参数后方可投入生產线。
smt工艺流程

smt工艺流程SMT (Surface Mount Technology) 是一种电子组装工艺,它将电子元器件直接安装在印刷电路板(PCB)的表面上,与传统的TH (Through Hole) 技术相比,SMT可以提高电路板的密度,减小尺寸,提高生产效率。
下面是SMT工艺流程的简要介绍:1. 贴片:首先,从供应商那里购买电子元器件,然后将元器件放置在贴片机上。
贴片机使用自动化机械手臂将元器件精确地放置在PCB表面上的预定位置。
2. 点胶:对于需要固定的元器件,使用点胶机将胶水点在元器件的底部,以确保元器件在焊接过程中不松动。
3. 固化:将点胶的PCB送入固化炉中,通过加热使胶水固化,从而使元器件固定在PCB上。
4. 热风炉:将PCB放入热风炉中,通过加热使焊膏熔化,从而实现焊接。
焊膏起到导电和固定元器件的作用。
5. 高度检测:使用高度检测设备检测贴片后的元器件的高度是否符合要求,以确保元器件的稳定性和正确性。
6. AOI (Automated Optical Inspection):使用光学检测设备对焊接好的PCB进行检测。
AOI可以检测焊接是否良好,有无虚焊、错位等问题。
7. 测试:对已焊接的PCB进行功能测试,确保其符合设计要求,没有故障。
8. 清洗:使用清洗剂对PCB进行清洗,去除焊膏残留物和其他污垢。
9. 包装:将已经完成测试和清洗的PCB进行包装,以便运输和存储。
需要注意的是,SMT工艺流程可以根据实际情况进行调整和修改,上述的流程只是一个基本的参考。
此外,SMT工艺流程还需要考虑静电防护、温度控制、湿度控制等因素,以确保成品品质和稳定性。
SMT主要流程(精选5篇)

SMT主要流程(精选5篇)第一篇:SMT主要流程SMT主要流程:备料---印刷---贴片---中段(炉前目检)---后段(炉后测试)---焊接一.白夜班交接1.设备交接当天下班前,要不机器擦干净,飞达摆放整齐,接班人确认。
2.工作交接工作范围内的5S,如:废料袋,空胶管,空料盘等,送到指定位置前要检查是否有物料夹在一起。
工作台面如:剪刀,酒精瓶,接料袋,计算器等摆放整齐。
3.物料交接白夜班下班前要把重要材料交接清楚,特别是做了一半的订单一定要点好数量,填好转接记录并签名确认。
二.工作内容1.把当天的保养记录表填好。
如:防潮柜,温湿度记录表,贴片机保养记录表,冰箱记录表等。
2.确认上线的物料,如材料少数或材料已超过除湿期的必须第一时间通知领班,由领班协调处理。
3.飞达上的物料确认,按照机台的排料表用量,把用量多的接好,并填好上料记录表,自己确认OK后在通知IPQC查料。
4.有方向的物料一定要确认好方向和丝印,在给QC确认,并写好记录。
5.机器在正常生产的情况下,要在线上来回巡查。
如:抛料是否超标,重要材料是否正确,用量多的材料是否同步,生产是否平衡。
如有异常及时向技术员或领班反映,要求调整。
6.机器所抛物料要及时拿出来,用袋子装好,在换档次前把材料手贴上去。
订单生产结束后多余物料随订单转到后站。
7.处理机器异常时要把安全盖打开,看清显示器上面报警提示,在做处理。
如不会处理时通知技术员处理。
8.如果一台机器报警频繁,要及时通知技术员。
9.下班前要把当天的产能报表,抛料记录表填好交给领班。
10.做好锡膏的使用记录,搅拌记录及回温记录表。
并上交领班确认并签字。
11.关心集体,节约公司成本,节约从自己做起,严格按照‘三按两遵守’的标准要求自己。
(三按:按文件,按指导书,按流程。
两遵守:遵守公司的规章制度,遵守工艺路线)三.印刷要诀:锡膏没解冻,印也印不动。
锡膏瓶不盖,能印好才怪。
钢网没调平,印了也是零。
台上乱摆放,安全没保障。
SMT工艺流程

SMT工艺流程1. 引言表面贴装技术(Surface Mount Technology,SMT)是一种电子组件的安装方式,它将表面电阻、电容、集成电路等元件直接焊接在印刷电路板(Printed Circuit Board,PCB)的表面上,而不是通过插针插入孔内。
SMT工艺流程是将电子元器件安装到PCB上的一系列步骤,它的高效性和可靠性使得SMT成为现代电子制造中最主要的组装技术之一。
本文将介绍SMT工艺流程的基本步骤和关键要点。
2. SMT工艺流程概述SMT工艺流程主要包括以下几个步骤:•印刷贴胶(Stencil Printing):将SMT贴装胶(Solder Paste)通过印刷方法均匀地涂刷到PCB的焊盘位置上。
印刷贴胶的质量直接影响后续的焊接质量。
•贴装(Component Placement):将SMT元件按照布局图的要求,利用高精度的贴装机器将元件放置在印刷好贴装胶的焊盘上。
贴装机器通常使用视觉系统来确保准确的位置。
•回流焊接(Reflow Soldering):通过回流炉将焊盘上的贴装胶加热到熔点,使得焊盘与元件之间的接合面液化,然后冷却固化,完成焊接过程。
回流焊接可以使用气体或者电炉来加热。
•清洗(Cleaning):清洗是一个可选的步骤,它的目的是去除焊接过程中可能残留的贴装胶、焊接剂或者其他污染物。
清洗可以使用溶剂、超声波或者水等方法。
•检查(Inspection):通过视觉检查或者自动检测设备来检查焊接的质量。
不合格的焊接可以进行修复或者重新制造。
3. SMT工艺流程详细步骤3.1 印刷贴胶印刷贴胶是SMT工艺流程中的第一步。
通常使用金属制成的Stencil来进行印刷,Stencil上有小孔,孔的位置和数量与PCB焊盘的位置和数量相对应。
印刷贴胶的质量对后续的焊接质量有很大影响。
3.2 贴装贴装是将SMT元件放置到已印刷好贴装胶的焊盘上。
贴装机器通常是自动化的,并具有高精度的定位能力。
SMT工艺流程简述
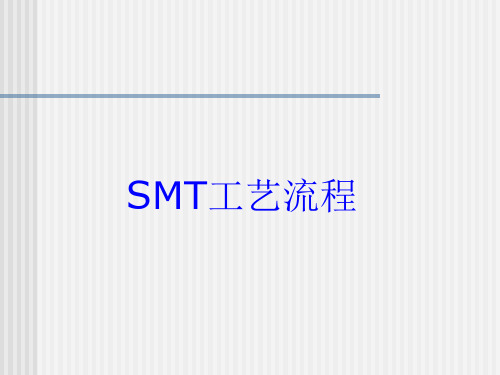
典型的表面贴装工艺分为三步:施加焊锡膏(印刷 Printing)---贴装元器件(贴装Pick and place)---回
流焊接(回流焊Reflow)。源自2、SMT生产线工艺流程图:
PCB投入 SMT 产线:
锡膏印刷
印刷检查
印刷机
貼片机
回流焊
贴片
• 由于采用的接触式印刷,刮刀、模板、基 板之间都是接触的,所以这三者的平整度也 将直接影响到印刷品质。
• 综上所述,为了达到良好的印刷结果,必 须有正确的锡膏材料(黏度、金属含量、最 大 粉末尺寸和尽可能最低的助焊剂活性)、 正确的工具(印刷机、模板和刮刀)和正确的 工艺过程(良好的定位、清洁拭擦)的结合。 根据不同的产品,在印刷程序中设置相应的 印刷工艺参数,如刮刀压力、印刷速度、模 板自动清洁周期等。
4、SMT设备工艺流程
4.2投入的PCB在设备之间传输
PCB在各个设备之间的传输按设备间距定制传送台,使用轨道传输板子
4、SMT设备工艺流程
4.3 印刷机介绍(Printer )
型号:SPG/NM-EJP6A(松下)
*印刷机的主要功能是将搅拌均匀的 锡膏通过刮刀在钢网上做往复式动 作,通过钢网上的开孔把锡膏印刷到 PCB板上而实现。
4、SMT设备工艺流程
4.7 AOI检查机
• AOI即自动光学检测, AOI检查机的功能即用光学手段获取被测物图形, 一般通过传感器(摄像机)获得检测物的照明图像并数字化,然后以某种方 法进行比较、分析、检验和判断,相当于将人工目视检测自动化、智能化。
• 运用高速高精度视觉处理技术自动检测PCB板上各种不同帖装错误及焊 接缺陷。PCB板的范围可从细间距高密度板到低密度大尺寸板,并可提供在 线检测方案以提高生产效率及焊接质量 。
SMT工艺流程

SMT工艺流程简介:表面贴装技术(SMT)是一种在PCB(印刷电路板)上表面组装电子元器件的技术。
SMT技术的发展对电子行业的生产效率和产品性能提升起到了重要作用。
本文将介绍SMT工艺流程的基本步骤和关键环节。
SMT工艺流程步骤:1. PCB 设计在SMT工艺流程开始之前,首先需要进行PCB设计。
PCB设计包括电路板布线,器件布局等,直接影响着后续的SMT工艺。
2. 贴片加工1.预处理:PCB表面清洁处理,去除油污和杂质,以确保焊接质量。
2.接收贴片:将各种SMT零件从供应商处接收并进行检验。
3.丝网印刷:通过丝网印刷的方式在PCB上涂覆焊膏。
4.贴片:使用贴片机将SMT元器件精确定位并贴合在PCB上。
3. 焊接1.传送至炉子:贴片完成后的PCB被传送至回流焊炉,进行焊接过程。
2.回流焊接:在高温环境下,焊膏熔化,将SMT元器件与PCB焊接固定。
焊接完成后冷却固化。
4. 检验和调试1.目视检查:工作人员对焊接质量、元器件位置进行目视检查。
2.AOI检测:自动光学检测系统对PCB表面进行检查,发现异常情况。
3.功能测试:通过功能测试设备对PCB进行整体性能测试,确保SMT组装的电路板符合要求。
5. 包装和出厂1.清洁:清洁已经通过测试的PCB,确保表面干净。
2.包装:采用适当的包装方式,将成品PCB包装好,准备出厂。
总结:SMT工艺流程是PCB表面组装中的关键步骤,通过以上步骤的精细操作和检验,可以保证SMT组装的PCB具有优良的电气性能和可靠性。
随着电子行业的不断发展,SMT技术也在不断进步,带动了整个电子制造行业的快速发展。
以上是关于SMT工艺流程的基本介绍,希望对读者有所帮助。
SMT工艺流程及各工位操作规范
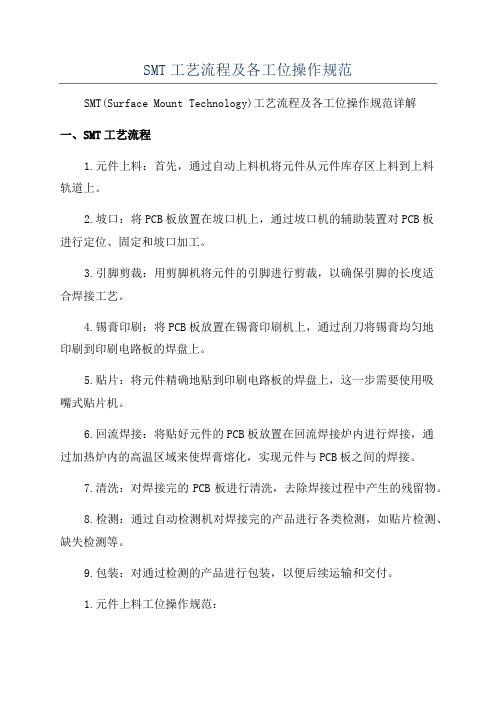
SMT工艺流程及各工位操作规范SMT(Surface Mount Technology)工艺流程及各工位操作规范详解一、SMT工艺流程1.元件上料:首先,通过自动上料机将元件从元件库存区上料到上料轨道上。
2.坡口:将PCB板放置在坡口机上,通过坡口机的辅助装置对PCB板进行定位、固定和坡口加工。
3.引脚剪裁:用剪脚机将元件的引脚进行剪裁,以确保引脚的长度适合焊接工艺。
4.锡膏印刷:将PCB板放置在锡膏印刷机上,通过刮刀将锡膏均匀地印刷到印刷电路板的焊盘上。
5.贴片:将元件精确地贴到印刷电路板的焊盘上,这一步需要使用吸嘴式贴片机。
6.回流焊接:将贴好元件的PCB板放置在回流焊接炉内进行焊接,通过加热炉内的高温区域来使焊膏熔化,实现元件与PCB板之间的焊接。
7.清洗:对焊接完的PCB板进行清洗,去除焊接过程中产生的残留物。
8.检测:通过自动检测机对焊接完的产品进行各类检测,如贴片检测、缺失检测等。
9.包装:对通过检测的产品进行包装,以便后续运输和交付。
1.元件上料工位操作规范:-定期检查上料机的状态,确保其正常运转。
-按照指定的元件上料顺序进行操作,避免元件之间的混淆。
-检查元件的品质,确保上料的元件符合要求。
2.坡口工位操作规范:-检查坡口机的状态,确保其正常工作。
-确保PCB板的定位和固定是准确的。
-在坡口加工前,检查PCB板是否合格,确保其质量。
3.引脚剪裁工位操作规范:-确认所使用的剪脚机具备安全保护装置。
-严格按照元件的引脚长度要求进行剪裁。
-注意操作时的手部安全,避免受伤。
4.锡膏印刷工位操作规范:-检查锡膏印刷机的状态,确保其正常工作。
-根据印刷要求,选择适当的刮刀,并确保其清洁。
-确保印刷膜的厚度和印刷速度符合要求。
5.贴片工位操作规范:-确认贴片机的状态,确保其正常工作。
-检查吸嘴的状况,确保吸嘴的吸附力和准确度。
-在贴片时,确保元件的定位准确,避免偏差。
6.回流焊接工位操作规范:-确认回流焊接炉的状态,确保其正常工作。
smt贴片工艺流程介绍

smt贴片工艺流程介绍
SMT贴片工艺流程是指表面贴装技术(Surface Mount Technology)的工艺流程,用于电子元器件的贴片装配过程。
以下是一般的SMT贴片工艺流程介绍:
1. 钻孔:在电路板上打孔,用于通过孔技术的元件安装。
2. 原板处理:对电路板进行清洁和涂覆表面粗糙度,以提
高焊接和贴附性。
3. 贴附:将胶料或用于贴附元器件的胶水涂在电路板表面。
4. 精确定位:使用自动定位设备将元器件准确地放置在电
路板上的预定位置,通常采用精确自动点胶机或贴片机完成。
5. 固定焊接:将已定位的元器件通过回焊炉中的热熔焊料进行焊接,使元件与基板永久连接。
6. 清洗:清洗电路板以去除生产过程中的残留物,通常使用溶剂或超声波清洗机。
7. 检测:进行必要的自动或手动检测,以确保贴片工艺的质量和精度。
8. 二次焊接:在需要的情况下,对电路板的焊点进行二次焊接或再流焊,以确保全部焊点质量和可靠性。
9. 高度检测:使用高度检测设备,如光学或激光测高仪,检查元器件的高度是否符合要求。
10. 成品检验:对完成的电路板进行全面的检查,以确保符合设计要求和品质标准。
以上是一般的SMT贴片工艺流程介绍,具体的工艺流程可能会根据不同的产品要求和制造商的特定流程进行适当调整。
SMT生产工艺流程

SMT生产工艺流程一、SMT特点①、组装密度高、电子产品体积小、重量轻,贴片元件的体积和重量只有传统插装元件的1/10左右,一般采用SMT之后,电子产品体积缩小40%〜60%,重量减轻60%~80%。
②、可靠性高、抗震能力强。
焊点缺陷率低。
③、高频特性好。
减少了电磁和射频干扰。
④、易于实现自动化,提高生产效率。
⑤、降低成本达30%~50%o⑥、节省材料、能源、设备、人力、时间等。
二、工艺组成印刷(红胶/锡膏)——>检测(可选SPI全自动或人工检测)一>贴装(先贴小器件后贴大器件)——>检测(可选AOI 光学/目视检测)一一>焊接(采用热风回流焊进行焊接)一一>检测(选用AOI光学检测外观及功能性测试检测)一›维修(使用工具;焊台及热风拆焊台等)一一>分板(手工或者分板机进行切板)三、工艺流程可简分为:锡膏印刷一一>元件贴片一>回流焊接一一>产品检修(每道工艺中均可加入检测环节以控制质量)锡膏印刷:其作用是将锡膏呈45度角用刮刀漏印到PCB的焊盘上,为元器件的焊接做准备。
所用设备为印刷机锡膏印刷机),位于SMT生产线的最前端。
元件贴装:其作用是将表面组装元器件准确安装到PCB的固定位置上。
所用设备为(贴片机),位于SMT生产线中印刷机的后面,一般为高速机和泛用机按照生产需求搭配使用。
回流焊接:其作用是将焊膏融化,使表面组装元器件与PCB牢固焊接在一起。
所用设备为(回流焊炉),位于SMT生产线中贴片机的后面,对于温度要求相当严格,需要实时进行温度量测,所量测的温度以Profi1e的形式体现。
AOI光学检测:其作用是对焊接好的PCB进行焊接质量的检测。
所使用到的设备为全自动光学检测机(AOI),位置根据检测的需要,可以配置在生产线合适的地方。
有些在回流焊接前,有的在回流焊接后。
产品检修:其作用是对检测出现故障的PCB进行返修。
所用工具为烙铁、返修工作站等。
配置在AO1光学检测后。
切板/分板:其作用对多连板PCBA进行切分,使之分开成单独个体,一般采用V-cut与机器切割方式。
- 1、下载文档前请自行甄别文档内容的完整性,平台不提供额外的编辑、内容补充、找答案等附加服务。
- 2、"仅部分预览"的文档,不可在线预览部分如存在完整性等问题,可反馈申请退款(可完整预览的文档不适用该条件!)。
- 3、如文档侵犯您的权益,请联系客服反馈,我们会尽快为您处理(人工客服工作时间:9:00-18:30)。
一、SMT工艺流程------单面组装工艺
来料检测→丝印焊膏(点贴片胶)→贴片→烘干(固化)→回流焊接→清洗→检测→返修
二、SMT工艺流程------单面混装工艺
来料检测→PCB的A面丝印焊膏(点贴片胶)→贴片→烘干(固化)→回流焊接→清洗→插件→波峰焊→清洗→检测→返修
三、SMT工艺流程------双面组装工艺
A:来料检测→PCB的A面丝印焊膏(点贴片胶)→贴片→烘干(固化)→A面回流焊接→清洗→翻板→PCB的B面丝印焊膏(点贴片胶)→贴片→烘干→回流焊接(最好仅对B面→清洗→检测→返修)
此工艺适用于在PCB两面均贴装有PLCC等较大的SMD时采用。
B:来料检测→PCB的A面丝印焊膏(点贴片胶)→贴片→烘干(固化)→A面回流焊接→清洗→翻板→PCB的B面点贴片胶→贴片→固化→B面波峰焊→清洗→检测→返修)
此工艺适用于在PCB的A面回流焊,B面波峰焊。
在PCB的B 面组装的SMD中,只有SOT或SOIC(28)引脚以下时,宜采用此工艺。
四、SMT工艺流程------双面混装工艺
A:来料检测→PCB的B面点贴片胶→贴片→固化→翻板→PCB的A面插件→波峰焊→清洗→检测→返修先贴后插,适用于SMD元件多于分离元件的情况
B:来料检测→PCB的A面插件(引脚打弯)→翻板→PC B的B面点贴片胶→贴片→固化→翻板→波峰焊→清洗→检测→返修
先插后贴,适用于分离元件多于SMD元件的情况
C:来料检测→PCB的A面丝印焊膏→贴片。