轮胎硫化时间的优化
硫化工艺对成品轮胎性能的影响

硫化工艺对成品轮胎性能的影响发布时间:2021-08-09T15:05:02.750Z 来源:《探索科学》2021年7月13期作者:贾肖阳邓龙齐林连刚邓龙[导读] 目前,我国的综合国力的发展迅速,硫化是轮胎生产中的重要环节之一,需要消耗大量的能量,约占轮胎生产总能耗的60%。
为了提高轮胎生产效率,加大产出,需要对硫化工艺进行优化。
全钢载重子午线轮胎的胎圈、胎肩等部件容易出现硫化程度不均匀,这些关键部件出现欠硫或过硫,将严重影响轮胎的使用性能,同时各部件的不同硫化程度也将在一定程度上影响轮胎的使用性能。
八亿橡胶有限责任公司贾肖阳邓龙齐林连刚邓龙山东枣庄 277000摘要:目前,我国的综合国力的发展迅速,硫化是轮胎生产中的重要环节之一,需要消耗大量的能量,约占轮胎生产总能耗的60%。
为了提高轮胎生产效率,加大产出,需要对硫化工艺进行优化。
全钢载重子午线轮胎的胎圈、胎肩等部件容易出现硫化程度不均匀,这些关键部件出现欠硫或过硫,将严重影响轮胎的使用性能,同时各部件的不同硫化程度也将在一定程度上影响轮胎的使用性能。
关键词:硫化工艺;成品轮胎性能;影响引言随着工业的发展,能源的消耗越来越快,这是地球难以承受的负担。
在政策的积极响应下,更多的工厂创新技术,生产低耗能产品,以降低能源的使用,保障自然环境的可持续性。
在汽车领域中,由于汽车长时间的行驶,对轮胎的损坏更高,所以轮胎的质量需要达到更高的水平,如耐磨损性、高耐热性、稳定性等。
其中轮胎硫化过程是轮胎生产中最重要的一步,轮胎的质量取决于硫化程度的高低。
但硫化耗能也是最高,并存在严重的过硫问题,所以怎样优化配方、改善工业硫化是一项重要的研究课题,亟待解决。
1硫化温度分布为对比两种硫化工艺下轮胎硫化升温情况,选取具有代表性的测温点数据作温度曲线。
胎圈及肩部测温点中分别选取升温速度较慢的测温点,缓冲部位测温点选取通入内冷水后降温最快的测温点。
内冷却硫化工艺测温后期胎冠表面中心及胎侧表面温度开始下降;通入冷却水后气密层中心、缓冲层中心、下模胎圈部位温度下降明显。
轮胎硫化工艺条件的优化
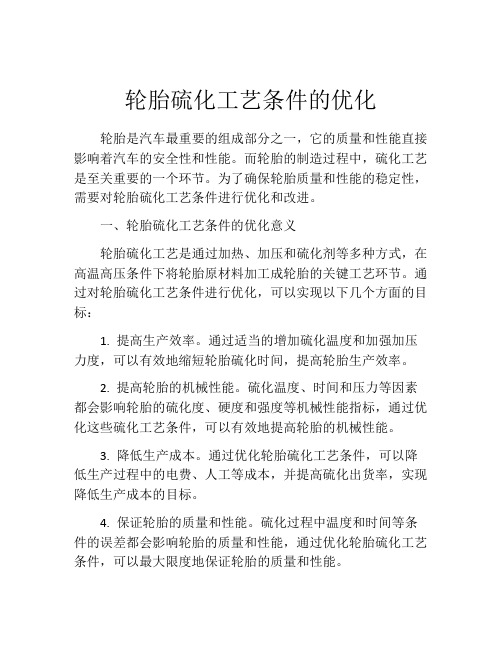
轮胎硫化工艺条件的优化轮胎是汽车最重要的组成部分之一,它的质量和性能直接影响着汽车的安全性和性能。
而轮胎的制造过程中,硫化工艺是至关重要的一个环节。
为了确保轮胎质量和性能的稳定性,需要对轮胎硫化工艺条件进行优化和改进。
一、轮胎硫化工艺条件的优化意义轮胎硫化工艺是通过加热、加压和硫化剂等多种方式,在高温高压条件下将轮胎原材料加工成轮胎的关键工艺环节。
通过对轮胎硫化工艺条件进行优化,可以实现以下几个方面的目标:1. 提高生产效率。
通过适当的增加硫化温度和加强加压力度,可以有效地缩短轮胎硫化时间,提高轮胎生产效率。
2. 提高轮胎的机械性能。
硫化温度、时间和压力等因素都会影响轮胎的硫化度、硬度和强度等机械性能指标,通过优化这些硫化工艺条件,可以有效地提高轮胎的机械性能。
3. 降低生产成本。
通过优化轮胎硫化工艺条件,可以降低生产过程中的电费、人工等成本,并提高硫化出货率,实现降低生产成本的目标。
4. 保证轮胎的质量和性能。
硫化过程中温度和时间等条件的误差都会影响轮胎的质量和性能,通过优化轮胎硫化工艺条件,可以最大限度地保证轮胎的质量和性能。
二、轮胎硫化工艺条件的优化方法1. 优化硫化温度和时间。
随着硫化温度的升高,硫化速度和硫化度也会随之增加。
但是当温度过高的时候,不仅会增加硫化丝的断裂可能性,还会导致轮胎变形和硫化不均匀等问题。
因此,在硫化温度和硫化时间之间需要进行平衡,找到二者之间的最佳组合。
2. 加强加压力度。
加压力度是影响硫化度和轮胎硬度的重要因素。
通过加强加压力度,可以有效地提高轮胎硫化质量和机械性能,并缩短硫化时间。
3. 采用新型硫化剂。
目前市场上流行的硫化剂主要有硫、硫代硫酸酯、过氧化物等。
通过选择合适的硫化剂,可以对轮胎硫化工艺条件进行优化,并有效提高轮胎的硬度和强度,以及耐久性和耐磨性等性能指标。
4. 采用自动化控制系统。
通过采用现代化的自动化控制系统,可以有效地控制轮胎硫化过程中的温度和时间等条件,提高硫化质量和生产效率,并减少操作人员的劳动强度和误操作可能性。
确定和优化轮胎硫化时间的方法
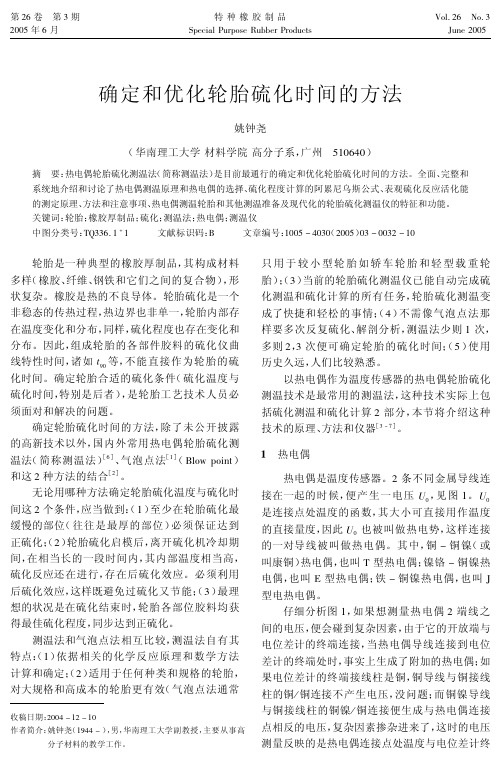
只用于较小型轮胎如轿车轮胎和轻型载重轮 胎);(3)当前的轮胎硫化测温仪已能自动完成硫 化测温和硫化计算的所有任务,轮胎硫化测温变 成了快捷和 轻 松 的 事 情;( 4 )不 需 像 气 泡 点 法 那 样要多次反复硫化、解剖分析,测温法少则 1 次, 多则 2,3 次便可确定轮胎的硫化时间;(5)使用 历史久远,人们比较熟悉。
2005 年
姚钟尧 确定和优化轮胎硫化时间的方法
33
不是等于 0,借助冰点的附加电压测量的电压是 涉及冰点连接点处温度为 0℃ 的温度,“ 冰点连 接”叫做参比端温度为 0℃ 。
图 1 热电偶测温原理电路图
端接线柱处温度之间的温差,并非单纯是热电偶 连接点处的温度。克服这个问题的一种方法是将 铜镍 / 铜电位差计连接置为已知温度 0℃( 冰点), 见图 2,之所以选择 0℃ 是因为可用冰浴精密产生 和控制它。应当理解,在冰浴中的连接点的电压
热电势值查出温度值。这类表的优点是,可以直
接从现场测得的热电势按表格迅速查出温度值;
第 3 种形式为 E( t),S( t)分度表。由这种表可以
从温度 t 查出热电势 E 和塞贝克系数( 即热电势
率 dE / dt),这对测量准确度要求较高的计量传递
工作、热物理的研究工作以及有关热工程的设计
等,在计算温度—热电势关系时十分有用。
表 1 铜 - 铜镍热电偶 E( t)分度表
2
0. 078 0. 470 0. 870 1. 279 1. 696 2. 122 2. 556 2. 998 3. 448 3. 907 4. 372 4. 845 5. 325 5. 812 6. 305 6. 805 7. 310 7. 823 8. 341 8. 865 9. 395 9. 930 10. 471 11. 017 11. 569
7.50R16 CST27全钢轻型载重子午线轮胎硫化工艺的改进

第 9 期王俊霞等.7.50R16 CST27全钢轻型载重子午线轮胎硫化工艺的改进5597.50R16 CST27全钢轻型载重子午线轮胎硫化工艺的改进王俊霞,慕振兴,许建欣[浦林成山(山东)轮胎有限公司,山东威海 264300]摘要:采取提高硫化温度、缩短硫化时间的方法对7.50R16CST27全钢轻型载重子午线轮胎的硫化工艺进行改进。
改进后硫化条件为外部蒸汽温度 (150±3)℃,内部蒸汽温度 (210±5)℃,氮气压力 (2.7±0.3) MPa,总硫化时间 37 min。
硫化工艺改进后,硫化效率提高了10%,轮胎的外缘尺寸、胎面胶物理性能、胎体钢丝帘线渗胶性能和耐久性能基本相当,高速性能提高。
关键词:全钢轻型载重子午线轮胎;硫化发泡点试验;硫化工艺;高速性能;耐久性能中图分类号:U463.341+.6;TQ330.6+7 文章编号:1006-8171(2019)09-0559-03文献标志码:B DOI:10.12135/j.issn.1006-8171.2019.09.0559随着轮胎行业的发展,对全钢子午线轮胎的耐磨性能、高速性能和使用寿命提出了更高的要求。
同时,轮胎市场竞争日益激烈,生产高性能、低成本的轮胎成为众多轮胎企业的研究重点。
硫化是轮胎生产的重要步骤之一,通过改进硫化工艺可以有效提高硫化效率,降低生产成本[1-2]。
硫化温度和硫化时间成反比关系,传统的硫化工艺一般采用低温硫化以保证轮胎质量,但这种硫化方式硫化时间长,阻碍了产能的提升,造成能源浪费、生产成本增加等问题。
为提高硫化生产效率,我公司采取提高硫化温度、缩短硫化时间的方法对7.50R16 CST27全钢轻型载重子午线轮胎的硫化工艺进行改进,取得了良好效果。
1 改进前硫化工艺改进前硫化工艺为:外部蒸汽温度 (143±3)℃,内部蒸汽温度 (198±5)℃,氮气压力 (2.7±0.3) MPa。
工程机械轮胎胶囊罐式硫化的改进
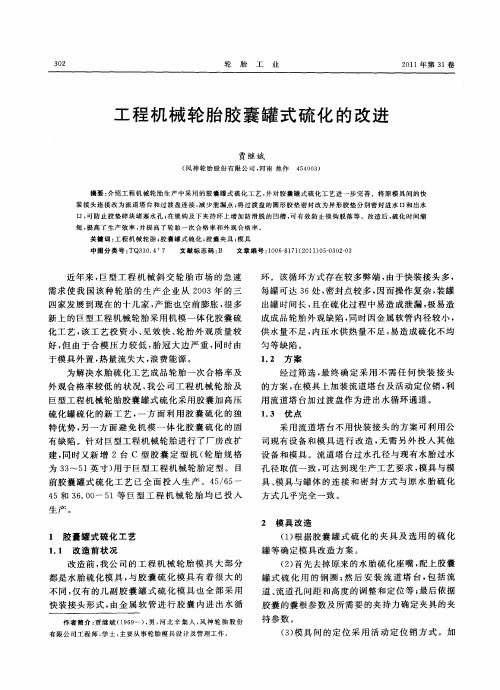
原过 渡盘 的密 封采用 一个 大 的圆形胶 垫共 同 封住 进水 口和 出水 口。胶 垫 压 缩 量 为 5mm, 在
硫化 过 程 中 , 由于过 热 水 的温 度 高 、 压力 大 , 垫 胶 在使 用几 次后 受过热 水 冲击部 分会 脱落并 被挤 人
流道塔 台的进 水孔 内 , 数 多 了会堵 塞 流道 塔 台 次
硫 化罐 硫化 的新 工 艺 , 方 面利 用 胶囊 硫 化 的 独 一
用流道 塔 台加 过渡 盘作 为进 出水循 环通道 。
1 3 优 点 .
特优 势 , 一方 面避 免 机 模一 体 化 胶囊 硫 化 的 固 另
有缺 陷 。针 对 巨型工程 机械 轮胎进行 了厂房改 扩 建, 同时又新 增 2台 C型 胶 囊 定 型机 ( 胎 规 格 轮 为 3 ̄ 5 3 1英寸 ) 用于 巨型工 程机 械轮胎 定型 。 目
不 重合 的 问题 , 其 是夹 具 在 带 着 胎坯 向模 具 里 尤
安 放 时 , 具 很 容 易 装 偏 , 将 钢 圈甚 至 夹具 压 夹 会
坏 。为 此 , 用 了 流 道 塔 台 上 增 加 4个 导 向 滑 块 采
( ) 造前 a改
结构 ( 图 2 。在 夹 具 下落 过 程 中 , 用 锁 钩 盘 见 ) 利 上 的 中心孔 自动找正 , 流道塔 台改造 后 , 按原 对 再
改造 前 , 我公 司 的工 程 机械 轮 胎 模 具 大部 分
都 是水胎 硫化 模具 , 与胶 囊 硫 化模 具有 着 很 大 的
不 同 , 有 的几副 胶 囊 罐 式硫 化 模 具也 全 部 采 用 仅
道 、 道孔 间距和 高度 的调整 和定位 等 ; 后依 据 流 最 胶囊 的囊根 参数及 所需要 的夹持力 确定 夹具 的夹
轮胎硫化工艺条件的优化
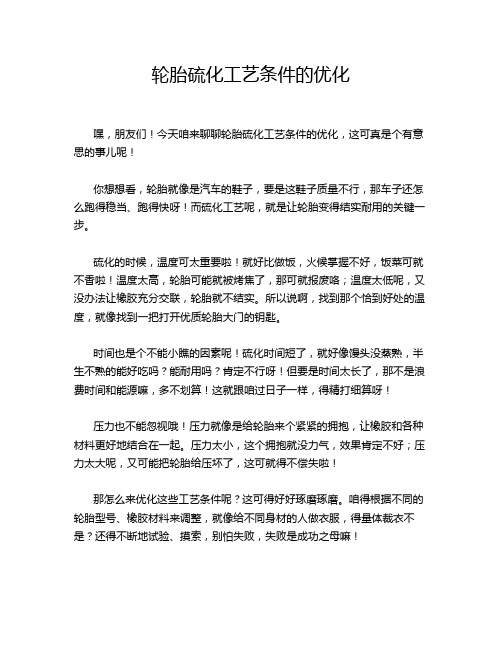
轮胎硫化工艺条件的优化嘿,朋友们!今天咱来聊聊轮胎硫化工艺条件的优化,这可真是个有意思的事儿呢!你想想看,轮胎就像是汽车的鞋子,要是这鞋子质量不行,那车子还怎么跑得稳当、跑得快呀!而硫化工艺呢,就是让轮胎变得结实耐用的关键一步。
硫化的时候,温度可太重要啦!就好比做饭,火候掌握不好,饭菜可就不香啦!温度太高,轮胎可能就被烤焦了,那可就报废咯;温度太低呢,又没办法让橡胶充分交联,轮胎就不结实。
所以说啊,找到那个恰到好处的温度,就像找到一把打开优质轮胎大门的钥匙。
时间也是个不能小瞧的因素呢!硫化时间短了,就好像馒头没蒸熟,半生不熟的能好吃吗?能耐用吗?肯定不行呀!但要是时间太长了,那不是浪费时间和能源嘛,多不划算!这就跟咱过日子一样,得精打细算呀!压力也不能忽视哦!压力就像是给轮胎来个紧紧的拥抱,让橡胶和各种材料更好地结合在一起。
压力太小,这个拥抱就没力气,效果肯定不好;压力太大呢,又可能把轮胎给压坏了,这可就得不偿失啦!那怎么来优化这些工艺条件呢?这可得好好琢磨琢磨。
咱得根据不同的轮胎型号、橡胶材料来调整,就像给不同身材的人做衣服,得量体裁衣不是?还得不断地试验、摸索,别怕失败,失败是成功之母嘛!咱可以一点一点地调整温度,看看哪个温度下出来的轮胎质量最好。
时间也是,多试几次不同的时长,找到那个最合适的点。
压力也一样,慢慢尝试,总能找到最佳的压力值。
这过程可能有点麻烦,但是你想想,一旦咱把工艺条件优化好了,那生产出来的轮胎得多棒呀!质量杠杠的,用起来放心,卖出去也有底气呀!这不是一举多得嘛!咱可不能嫌麻烦,要知道,好东西都是要下功夫的呀!就像那好酒,得经过长时间的酿造才能香醇可口。
咱这轮胎硫化工艺条件的优化也是一样,得用心去钻研,去尝试。
总之,轮胎硫化工艺条件的优化可不是一件简单的事儿,但只要咱肯下功夫,肯用心,就一定能做出高质量的轮胎来。
让我们一起加油,让我们的轮胎在马路上欢快地奔跑吧!。
提升半钢轮胎硫化效率的设备工艺优化

提升半钢轮胎硫化效率的设备工艺优化张森森,李 浩,加 凡,郑求义(中策橡胶集团股份有限公司,浙江杭州310018)摘要:基于半钢轮胎硫化过程中不必要的等待时间和动作浪费,对硫化周期进行分解并进行设备工艺优化。
通过优化步序转换的跳转程序和采取“降等待”“趋重叠”及“减行程”等措施实现对合模硫化时间和开合模节拍时间的优化,缩短生产等待时间,提高硫化生产效率。
关键词:半钢轮胎;硫化;液压硫化机;生产效率;设备工艺优化中图分类号:TQ336.1;TQ330.4+7 文章编号:1006-8171(2023)04-0242-04文献标志码:B DOI:10.12135/j.issn.1006-8171.2023.04.0242目前半钢轮胎生产所使用的液压硫化机普遍采用B型油压式中心机构、上下硫化室结构(下硫化室固定,上硫化室通过油缸升降开合模具)、单加压缸加压的框架式双模液压硫化机,其电气控制系统采用三菱Q系列可编程逻辑控制器(PLC),以三菱工业触摸屏作为人机操作界面。
若要提升硫化设备的生产效率,首先要清楚地了解整个硫化机的结构和运作流程,并利用其机械结构及电气系统的控制特点进行针对性改造,缩短硫化各步骤时间或动作影响时间,从而提高硫化生产效率[1-4]。
半钢轮胎液压硫化机的正常运行状态主要分为合模硫化状态和开模非硫化状态。
合模硫化时间分为正硫化时间和非正硫化时间,开模非硫化时间主要指硫化结束后开模卸胎时间和装胎进缸合模时间(简称开合模节拍时间)。
本工作对硫化过程中的各分解时间进行分析,以期缩短硫化周期,提高设备的生产效率。
1 合模硫化时间的优化1.1 正硫化时间正硫化时间受轮胎硫化工艺条件限制和轮胎品质约束,除非工艺人员切割轮胎气泡点并反复试验验证,否则不允许随意更改。
因此只能着眼于步序转换的跳步时间优化。
原PLC控制系统采用分制计时法,6 s计为0.1 min。
在实际程序编写过程中,为确保步序工艺时间,增加了0.1 s的每6 s计数时间延迟(见图1),即如果单缸轮胎硫化时间需12 min,总跳转时间就增加了12 s(0.1×12/0.1)。
一种改善轮胎硫化时上下侧温差的方法

缩小胶囊上下侧温差,提升轮胎硫化均匀性。
氮气硫化;缸盖;高度;角度;冷凝水;温差硫化时间,提高轮胎硫化效率而被轮胎行业广泛使用。
在氮气硫化过程中,胶囊内的介质状态之间转变复杂,介质分布的高度、方向存在着温差,其中上下侧温差最大可达℃。
同时,橡胶又是热的不良导体,表层与内层温差随着断面厚度而增大,形成温度滞后损失,造成上下侧胎肩部位在中国橡胶应用技术APPLIED TECHNOLOGY41中国橡胶应用技术APPLIED TECHNOLOGY一、试验部分1.试验设备和材料2.试验方案(1) 试验原理氮气硫化过程中,胶囊内的介质包括下侧的冷凝水和上侧的蒸汽、氮气混合气体,因冷凝水位于胶囊最低处,受到胶囊夹缘的阻挡。
同时,传统的缸盖高压气体喷出时无法有效地打到冷凝水聚集的地方(图1),故冷凝水无法形成环流通过回口排出,一直存在于胶囊下侧,造成下侧温度偏低,上下侧表1 试验设备和材料序号名称厂家型号1硫化机益阳益神橡胶机械有限公司65寸机械机2测温仪华南理工大学——3热电偶美国WATLOW GORDON T 型4轮胎合肥万力轮胎有限公司12.00R20 SAP06+5胶囊永一(上海)轮胎胶囊科技有限公司RB12001图2 模拟缸盖喷出口示意图图1 胶囊内集聚的冷凝水图3 冷凝水环流示意图温差偏大。
本试验将硫化机中心机构缸盖重新加工改造,设计合适的喷出口高度、角度,将喷出的高压气体打在胶囊下侧冷凝水聚集的地方(图2),激起冷凝水形成环流,将上下侧介质混合均匀(图3)。
同时,在程序排凝时可以通过回口排出一部分冷凝水,从而间接减少了轮胎硫化时胶囊上下侧温差。
(2)试验方法①正常缸盖试验。
使用正常缸盖硫化,在12.00R20 SAP06+胎胚上按照既定位置进行热电偶埋线(图4),使用测温仪及其组图4 埋线点注:1/2/3/4/5/6为带束层端点;7/8/9/10/11/12/13/14为胎侧内衬层表面(90°分布);15/16为胎侧;17为胎冠42应用技术APPLIED TECHNOLOGY图5 正常缸盖与改造缸盖在硫化过程中胶囊表面温差/时间推移图图6 正常缸盖与改造缸盖在硫化过程中胎肩温差与时间推移图图7 正常缸盖与改造缸盖在硫化过程中胎肩硫化当量与时间推移图件测量整个硫化周期埋线部位的温度,计算各埋线部位的硫化当量。
轮胎胶料抗硫化返原性的优化
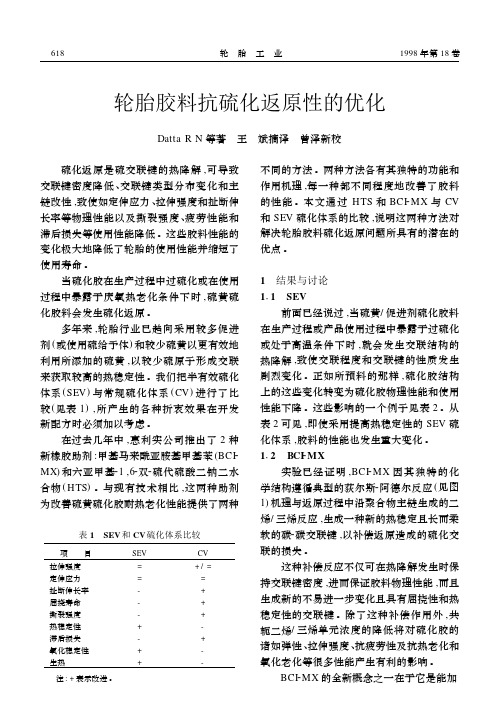
6
15. 2 14. 6
160 150
30 26
12 42
5. 20 5. 12
注 : 配方 : SMR CV 100 , 炭黑 N330 50 , 氧化锌 510 ,硬脂酸 210 ,芳烃油 310 ,防老剂 6PPD 210 ,促进 剂 CBS 0. 6 ,硫黄 2. 5 ,加工助剂 Perkalink 900 110 。
原性能见表 8 。从表 8 数据清楚地看出 ,配
方 中加入BCI2MX可获得良好的抗爆破性
2 BCI2MX/ HTS 并用 显然 ,上述讨论中 BCI2MX 和 H TS 尽管
作用机理不同 ,但都能改善胶料的抗硫化返 原性 ,并且都能不同程度地提高使用性能 。
前面已经指出 ,H TS 在硫化过程中参与
硫化体系 BCI2MX/ 份
100 %NR 或 IR ,或与 50 % 以上 NR 或 IR 的并用胶
SBR/ BR 其它如 NBR 等不饱和橡胶
EV~SEV SEV~CV
高硫 SEV~CV SEV~CV
0. 25~0. 40 0. 50~0. 75 0. 50~0. 75 0. 25~0. 40 0. 25~0. 50
配方编号
1
2
3
4
33 10 20 5 31 10 19 5
15. 4 12. 4 11. 7
15. 3 14. 5 14. 6
15. 4 13. 7 11. 4
15. 4 16. 1 16. 2
100 125 130 110 90 90 110 110 90 80 95 105
BO 33 52 26 BO 30 60 27 BO 26 66 25
图 3 示出了 150 ℃下胶料的硫化特性 。 正如所预料的 ,BCI2MX 对工艺特性只有很 小甚至几乎没有什么影响 ,而 H TS 对硫化确
轮胎硫化机节能改进
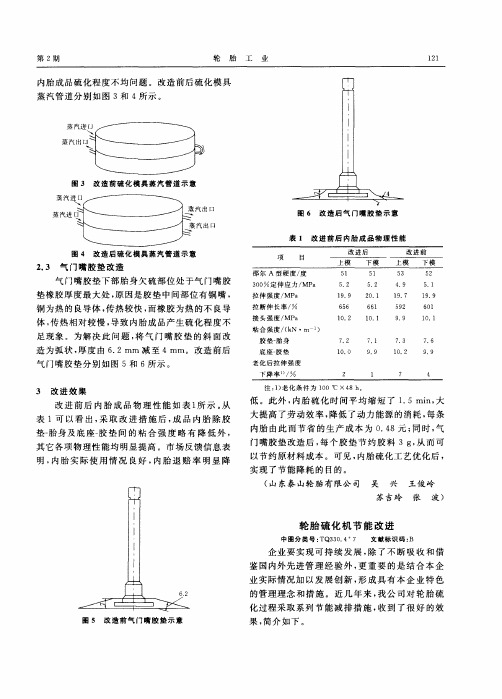
() 1 存在 问题 通 常 B型 硫 化 机 胶 囊使 用 0 8 0 9MP , . ~ . a 2 0℃ 过 热蒸 汽 喷 射 抽 真空 , 台硫 化机 抽 真 空 0 每 蒸汽 消耗量 约 为 0 0 h 。3 . 3t・ _ , 6台 硫 化 机 年抽
浪费 。 ( ) 进 2改
3 ~4 , 能效 回 收
( ) 在 问题 1存 我公 司 载 重 斜 交 轮 胎 生 产 采 用 1 6 3 mm 1 ( 3 5英 寸 ) 型硫 化 机 , 硫 化 过 程 中胶 囊 放 6. 定 在
第 2期
轮
胎
工
业
内胎成 品硫化程 度不均 问题 。改 造前后 硫化模具
蒸汽管 道分别如 图 3 4所示 。 和
图 3 改 造 前 硫化 模 具 蒸 汽 管 道 示 意
汽 出 口 汽 出 口
图 6 改造 后 气 门嘴 胶 垫 示意
表 l 改进 前 后 内胎成 品物 理 性 能 图 4 改 造 后 硫化 模 具 蒸 汽 管 道 示 意
真空耗 汽量超 过 90 0t浪费 大量蒸 汽 。 0 ,
( ) 进 2改
冷凝 水产生量 不 同 , 冷凝 水 排放 与关 闭设 定 值 可 方便 地通过 上位 机进 行 调 整 , 既保 证 满 足工 艺 要
求, 又可节约蒸 汽消 耗 。
为节 约蒸 汽 , 在热 水 除氧 站 增设 1套 由 2台
苏 吉玲 张 波)
垫一 胎身及 底 座一 垫 间 的粘 合 强 度 略 有 降 低 外 , 胶
其 它各项物理 性能均 明显提 高 。市场 反馈信 息表 明, 内胎 实 际使 用 情 况 良好 , 内胎 退 赔 率 明显 降
基于人工智能技术的轮胎硫化优化

基于人工智能技术的轮胎硫化优化王国林;施斌;姬新生;王晨;梁晨【摘要】以提高轮胎硫化程度均匀性为目标,运用ABAQUS软件对11.00R22.5载重子午线轮胎建立了硫化仿真有限元模型,结合轮胎硫化实际过程进行了温度场仿真分析.在温度场分析基础上,利用阿累尼乌斯方程计算轮胎硫化程度.利用正交试验设计、神经网络和遗传算法等优化技术,建立了轮胎硫化数值优化设计方法.对轮胎硫化过程中以外温蒸汽边界条件为设计变量对轮胎硫化程度均匀性进行优化,使轮胎硫化程度均匀性和硫化时间均得到改善.通过对优化前、后结果进行对比分析表明:采用优化后的外温蒸汽边界可以使轮胎硫化程度均匀性得到提高,性能得以提升,同时在不降低轮胎硫化性能情况下减少了硫化时间,缩短了生产周期,节约能源的同时提高了生产效率.%In order to optimize the tire curing degree of uniformity, the curing FE models of radial tire 11.00R22. 5 were built by ABAQUS and the temperature fields were analyzed. Based on this, the curing degrees of tire were calculated by Arrhenius Equation. With the help of orthogonal experimental design,neural network and genetic algorithm, a new optimization approach for determination of external steam temperature during tire vulcanization process was proposed. It was expected that the refined optimization technique would lead to good curing degree of uniformity and curing time. From the comparison between the initial results and optimized results, it finds that more uniform level of the optimized tire vulcanization has been reached and the performance of tire has been upgraded. At the same time, the production cycle decreases and the productivity increases due to the reduced tire vulcanization.【期刊名称】《江苏大学学报(自然科学版)》【年(卷),期】2011(032)002【总页数】4页(P144-147)【关键词】子午线轮胎;硫化;有限元分析;优化;仿真【作者】王国林;施斌;姬新生;王晨;梁晨【作者单位】江苏大学,汽车与交通工程学院,江苏,镇江,212013;江苏大学,汽车与交通工程学院,江苏,镇江,212013;风神轮胎股份有限公司,河南,焦作,454003;江苏大学,汽车与交通工程学院,江苏,镇江,212013;江苏大学,汽车与交通工程学院,江苏,镇江,212013【正文语种】中文【中图分类】U463.341+.3轮胎作为汽车的重要组成部件,其好的性能对汽车安全性、舒适性等极其重要.轮胎生产中,硫化过程对轮胎的质量起重要的作用.目前国内的研究主要集中在轮胎硫化性能的分析方法和试验方法,以及相关的评价指标[1]上,而国外的轮胎优化问题已经开展了大量的相关研究[2-3],但是基于有限元对轮胎硫化性能进行优化分析的研究还较少.为此,本研究以提高轮胎硫化程度均匀性为优化目标,以轮胎硫化过程中外温蒸汽为设计变量,结合有限元分析与人工智能技术建立一套数值优化设计方法.该方法采用正交试验设计原理安排试验方案,应用有限元分析完成虚拟试验过程,以提取的试验数据为训练样本,建立设计变量与优化目标之间的非线性映射关系的神经网络模型,运用进化算法可以搜索出轮胎硫化时外温蒸汽的最优历程[4-6].1 硫化程度分析1.1 硫化温度场问题描述硫化过程以瞬态传热来处理,其热传导方程为式中k为材料热传导系数;T为温度;Q为内热源;ρ为材料密度;c为材料比热容;t为时间.考虑到轮胎的硫化条件和环境,忽略辐射的影响和钢模与蒸汽之间的热阻.内热源对硫化温度场的影响较小,故忽略内热源.由于橡胶的导热系数很小,胶囊和过热水传热的主要热阻是橡胶的导热热阻,故将钢模与蒸汽以及胶囊与过热水之间的传热简化成第一类热边界,即式中f(t)为已知边界的温度函数.1.2 硫化程度计算橡胶在一定硫化温度下有一个最佳硫化时间,即正硫化时间.橡胶的硫化程度可以表示为胶料的实际等效硫化时间与在某一基准温度下的工艺正硫化时间的比值.轮胎硫化是瞬态传热过程,硫化期间由于胎内各部位存在温度梯度,所以各部位的硫化程度也不一样.硫化强度是胶料在一定的温度下,单位时间所能达到的硫化程度,通常用阿累尼乌斯方程式来计算,即式中v为不同时刻相对于温度T0的相对硫化速度,s-1;T0为参比热力学温度;E为硫化反应活化能,kJ/mol;R为气体常数,值为8.314 3×10-3kJ/ (mol·K).对于轮胎这种厚制品,不同时刻各部位温度不相等,在选定基准温度和已知某点温度时间历程,可以计算其硫化程度:式中te为硫化结束时的时间.根据数值积分的梯形公式,式(4)可离散化为式中vm为第m个时间间隔的相对硫化速度.若取基准温度T0,由式(3)可知,基准温度下的相对硫化速度v0为1 s-1,则到达正硫化时的硫化程度Ev90数值上等于胶料的正硫化时间(t90),这里引入硫化程度:来衡量胶料经过某一硫化历程后所获得的相对硫化程度,用以比较不同胶料的硫化程度.2 优化问题的描述2.1 有限元分析模型的建立以11.00R22.5型全钢载重子午线轮胎为研究对象[7],图1为利用ABAQUS 软件建立的三维轮胎硫化温度场分析模型,升温模型包含钢模和胶囊,降温模型为空气中的冷却过程.轮胎橡胶的热物性参数、硫化模具以及胶囊的材料参数均由风神轮胎股份有限公司提供.图1 轮胎硫化有限元模型Fig.1 Finite element model of tire curing2.2 优化模型的建立2.2.1 设计变量的选取轮胎硫化后的性能与硫化程度有着直接的关系,硫化程度受外温蒸汽的影响较大.选取外温蒸汽变化历程作为设计变量.2.2.2 目标函数的选取根据硫化的实际情况,可以从胶料硫化程度的均匀性来评估,硫化程度均匀性可以用硫化程度的偏度值来表征[8-9],即式中si为第i个节点的硫化结束时的硫化程度(由三维有限元分析得出);n为轮胎断面节点个数;¯s为断面所有节点的硫化程度的平均值.目前,轮胎企业为节约能源减少成本,提高生产效率,在硫化均匀性较好的情况下尽量减少硫化时间.故选取断面硫化均匀程度作为优化的目标函数,尽可能缩短硫化时间.2.3 优化数学模型图2为硫化模具外部蒸汽的温度历程[10],T1,T2为蒸汽温度,t1,t2为时间. 图2 外温蒸汽历程Fig.2 Outer temperature steam process轮胎硫化优化的数学模型为式中f(x)为硫化程度的偏度值;T1H,T1L是T1的上下边界值;T2H,T2L是T2的上下边界值;t1的上下边界值为t1H,t1L;t2的上下边界值为t2H,t2L.3 优化过程3.1 正交试验设计利用正交试验设计方法[11]选用正交表L9(34)安排试验方案.T1在408.15~418.15 K之间选取,T2在424.15~434.15 K之间选取,t1在960~1 160 s之间选取,t2在2 480~2 680 s之间选取.将各因素的水平数取为3,将选定的范围分为3等份,即可得到各因素的水平取值.3.2 数值拟合径向基函数(RBF)网络是以函数逼近理论为基础而构造的一类前向网络,这类网络的学习等价于在多维空间中寻找训练数据的最佳拟合平面.径向基函数网络的每个隐含层神经元传递函数都构成了拟合平面的一个基函数.径向基函数网络与BP网络相比规模通常较大,但学习速度较快,并且网络的函数逼近能力优于后者.故采用RBF网络来拟合外温蒸汽历程和硫化程度的偏度值之间的映射关系.为了提高神经网络的泛化能力,将样本数据分为训练集和测试集.训练集用于训练网络,使网络按照学习算法调节结构参数,以达到学习的目的;测试集则是用于评价已训练好的网络性能.提取9组样本点中的任意8组样本点作为训练样本,剩下的1组样本点作为测试样本.3.3 优化搜索遗传算法是一种借鉴生物界自然选择和自然遗传机制的随机搜索算法.它与传统的算法不同,大多数古典的优化算法是基于一个单一的度量函数(评估函数)的梯度或较高次统计,以产生一个确定性的试验解序列;遗传算法不依赖于梯度信息,而是通过模拟自然进化过程来搜索最优解.遗传算法通过有组织、随机的信息交换来重新组合适应性好的串,生成新的串的群体.根据建立的优化模型,采用遗传算法进行优化求解.取搜索精度为1×10-6,种群大小为50,交叉概率为0.25,变异概率为0.09,遗传代数为50.搜索过程如图3所示,经过50代进化之后,可以确定轮胎硫化偏度值较小时对应的1组设计变量为[408.79,1 136.10,431.91,2 506.70]T.图3 遗传算法搜索过程Fig.3 Genetic algorithm search process4 结果分析与讨论采用搜寻出的最优解对外温蒸汽边界条件进行修改并进行了有限元重分析,图4为原始的蒸汽边界和优化了的蒸汽边界对比.图4 蒸汽边界对比Fig.4 Comparison of boundary conditions of steam图5为重分析后的有限元仿真以及Matlab计算断面硫化程度示意图.图5 重分析结果云图Fig.5 Re-analysis of contours结果表明:原始外温蒸汽条件下轮胎断面硫化程度偏度值为0.699 4,优化后的偏度值为0.421 6,可见优化后的硫化程度更加均匀,轮胎性能有所提高;优化后的轮胎没有欠硫和严重过硫,同时外温蒸汽时间比原始的缩短了3.2 min,单条轮胎的生产周期减少,显著提高了生产效率,并且可以节约能源.5 结论(1)针对轮胎硫化的工艺过程[12]结合有限元分析、正交试验设计、神经网络和遗传算法[13]对外温蒸汽历程进行了分析和优化.结果表明:优化后的轮胎硫化程度更加均匀,对轮胎性能等方面有很大提高.同时,生产周期缩短了3.2 min,提高了轮胎的生产效率.(2)该优化方法具有广泛的应用范围,利用神经网络的数值拟合,不需要针对具体优化要求构建数学模型.利用有限元分析代替样机试验,大大减少了现场的实际试验次数.参考文献(References)Yan Xiangqiao.Finite element analysis system of the tire curing process [J].China Synthetic Rubber Industry,2005,52(9):550-557.(in Chinese)【相关文献】[2] Cho J R,Jeong H S,Yoo W S.Multi-objective optimization of tire carcass contours using a systematic aspiration-level adjustment procedure[J].Computational Mechanics,2002,29:498-509.[3] Cho J R,Shin S W,Yoo W S.Crown shape optimization for enhancing tire wear performance by ANN[J].Computers and Structures,2005,83:920-933.[4] Ghoreishy M H R,Naderi G.Three dimensional finite element modelling of trucktyre curing process in mould[J].Iranian Polymer Journal,2005,14(8):735-743.[5] Samadi M.Simulation of post-cure inflation process of tires(part I)study of tire cord thermoelastic characteristics[J].Iranian Journal of Polymer Science and Technology,1994,3(1):60-71.[6] Gent A N,Walter J D.The Pneumatic Tire[M].Washington DC:NHTSA,2005. [7]林波.基于灵敏度分析的子午线轮胎疲劳性能优化[D].镇江:江苏大学汽车与交通工程学院,2008.[8]葛金虎.基于有限元的轮胎磨损性能优化[D].镇江:江苏大学汽车与交通工程学院,2008. [9]王伟,邓涛,张萍,等.轮胎硫化程度的计算分析[J].合成橡胶工业,2005,28(3):191-194.Wang Wei,Deng Tao,Zhang Ping,et al.Calculation analysis for degree of cure of tire [J].China Synthetic Rubber Industry,2005,28(3):191-194.(in Chinese)[10] Prentice G A,Williams M C.Numerical evalution of the sate of cure in a vulcanizing rubber article[J].Rubber Chemistry and Technology,1980,53(5):1023-1031.[11] Montgomery D C.实验设计与分析[M].北京:人民邮电出版社,2009.[12]张岩梅,邹一明.橡胶制品工艺[M].北京:化学工业出版社,2005.[13]郑金华.多目标进化算法及其应用[M].北京:科学出版社,2007.。
轮胎硫化工艺条件的优化
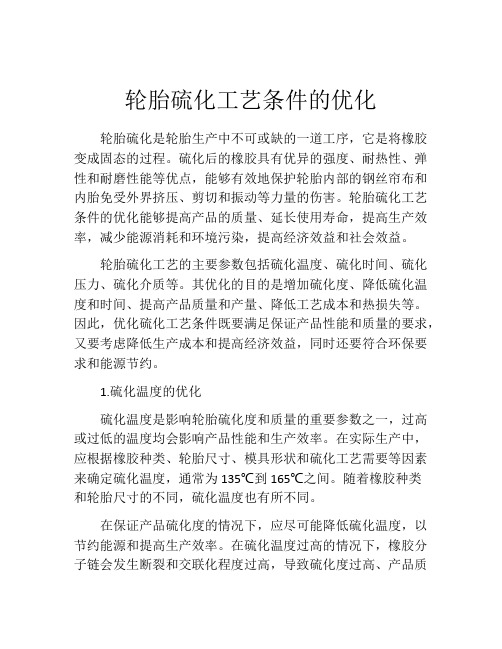
轮胎硫化工艺条件的优化轮胎硫化是轮胎生产中不可或缺的一道工序,它是将橡胶变成固态的过程。
硫化后的橡胶具有优异的强度、耐热性、弹性和耐磨性能等优点,能够有效地保护轮胎内部的钢丝帘布和内胎免受外界挤压、剪切和振动等力量的伤害。
轮胎硫化工艺条件的优化能够提高产品的质量、延长使用寿命,提高生产效率,减少能源消耗和环境污染,提高经济效益和社会效益。
轮胎硫化工艺的主要参数包括硫化温度、硫化时间、硫化压力、硫化介质等。
其优化的目的是增加硫化度、降低硫化温度和时间、提高产品质量和产量、降低工艺成本和热损失等。
因此,优化硫化工艺条件既要满足保证产品性能和质量的要求,又要考虑降低生产成本和提高经济效益,同时还要符合环保要求和能源节约。
1.硫化温度的优化硫化温度是影响轮胎硫化度和质量的重要参数之一,过高或过低的温度均会影响产品性能和生产效率。
在实际生产中,应根据橡胶种类、轮胎尺寸、模具形状和硫化工艺需要等因素来确定硫化温度,通常为135℃到165℃之间。
随着橡胶种类和轮胎尺寸的不同,硫化温度也有所不同。
在保证产品硫化度的情况下,应尽可能降低硫化温度,以节约能源和提高生产效率。
在硫化温度过高的情况下,橡胶分子链会发生断裂和交联化程度过高,导致硫化度过高、产品质量下降、能源浪费和环境污染等问题;而在硫化温度过低的情况下,硫化度不足、产品质量差、生产效率低等问题也会出现。
因此,在优化硫化温度时,需要综合考虑橡胶种类、轮胎尺寸、模具形状、硫化时间和压力等多种因素,根据实际情况来确定最佳硫化温度,以平衡硫化度、产品性能和生产效率三者之间的关系。
2.硫化压力的优化硫化压力是影响轮胎硫化度和质量的另一个重要参数,它直接影响轮胎的形状和几何尺寸。
在实际生产中,硫化压力与硫化温度、时间和介质等参数一起控制,以保证产品硫化度和合格率。
在优化硫化压力时,需要考虑橡胶种类、轮胎尺寸、模具形状、压力区域等因素。
一般来说,硫化压力应该高于橡胶的流动点压力,以避免橡胶在硫化过程中发生形变和变形。
轮胎硫化胶囊寿命提升措施
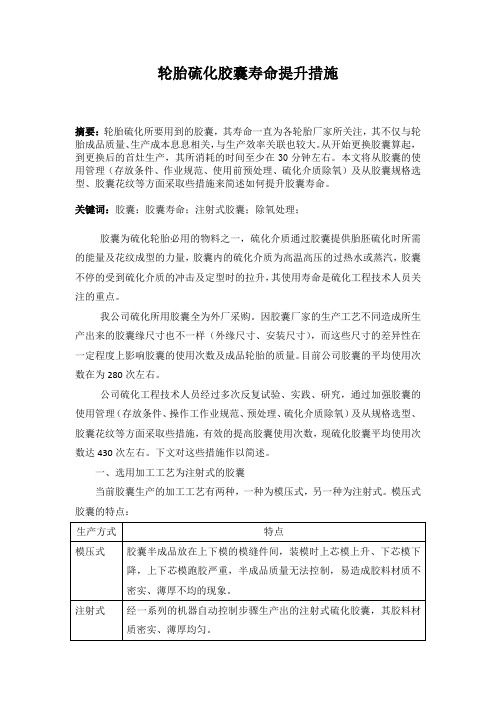
轮胎硫化胶囊寿命提升措施摘要:轮胎硫化所要用到的胶囊,其寿命一直为各轮胎厂家所关注,其不仅与轮胎成品质量、生产成本息息相关,与生产效率关联也较大。
从开始更换胶囊算起,到更换后的首灶生产,其所消耗的时间至少在30分钟左右。
本文将从胶囊的使用管理(存放条件、作业规范、使用前预处理、硫化介质除氧)及从胶囊规格选型、胶囊花纹等方面采取些措施来简述如何提升胶囊寿命。
关键词:胶囊;胶囊寿命;注射式胶囊;除氧处理;胶囊为硫化轮胎必用的物料之一,硫化介质通过胶囊提供胎胚硫化时所需的能量及花纹成型的力量,胶囊内的硫化介质为高温高压的过热水或蒸汽,胶囊不停的受到硫化介质的冲击及定型时的拉升,其使用寿命是硫化工程技术人员关注的重点。
我公司硫化所用胶囊全为外厂采购。
因胶囊厂家的生产工艺不同造成所生产出来的胶囊缘尺寸也不一样(外缘尺寸、安装尺寸),而这些尺寸的差异性在一定程度上影响胶囊的使用次数及成品轮胎的质量。
目前公司胶囊的平均使用次数在为280次左右。
公司硫化工程技术人员经过多次反复试验、实践、研究,通过加强胶囊的使用管理(存放条件、操作工作业规范、预处理、硫化介质除氧)及从规格选型、胶囊花纹等方面采取些措施,有效的提高胶囊使用次数,现硫化胶囊平均使用次数达430次左右。
下文对这些措施作以简述。
一、选用加工工艺为注射式的胶囊当前胶囊生产的加工工艺有两种,一种为模压式,另一种为注射式。
模压式胶囊的特点:选定一台双模硫化机其一边安装注射式胶囊、另一边安装模压式胶囊,硫化胶囊为同一厂家生产,其胶囊配方相同,经过工程技术人员硫化测温试验、胶囊使用次数记录对比,可得出:1、注射式胶囊较模压式胶囊传热要快,可缩短轮胎生产的硫化时间,从而提高产能、降低能耗,相关数据见表1。
表1 A13#硫化机注射式胶囊与模压式胶囊测温试验数据2、同时胶囊耐老化性能更优越,使用寿命长,比模压式硫化胶囊使用次数增加160次左右,相关数据见表2。
表2 A13#硫化机注射式硫化胶囊与模压式硫化胶囊使用次数数据二、选用合适规格的硫化胶囊胶囊厂家的不同,其胶囊规格尺寸(胶囊断面周长、外直径、夹缘高度等)存在一定差异,如何让胶囊外缘尺寸与成品轮胎规格尺寸、设备工装尺寸的吻合性最优,在胶囊选型时需考虑相关伸张值及胶囊尺寸。
轮胎硫化至终检的物流优化

第 5 期杨小林等.轮胎硫化至终检的物流优化301轮胎硫化至终检的物流优化杨小林,孙华东[双钱集团(江苏)轮胎有限公司,江苏如皋 226500]摘要:分析轮胎厂硫化车间至终检车间的X光检测段物流存在的问题,在原有布局的基础上,提出自动输送、自动扫描、自动修边、建立外观检查平台、自动扫描称量再送至X光机进行X光检测的优化方案。
改造后,自动化程度提升,用工人员减少,效益明显。
关键词:轮胎;物流;缓存;硫化;自动修边;X光检测中图分类号:TQ336.1+1;TQ330.4+93 文章编号:1006-8171(2019)05-0301-05文献标志码:B DOI:10.12135/j.issn.1006-8171.2019.05.0301我公司以前最终检验处轮胎检测设备分散于现场各点,且是手工修边,各检测设备相互独立,靠人工进行传送、分拣、检测、入库,人员劳动强度大,效率低。
按日产10 000条全钢子午线轮胎计,轮胎硫化完成后手工修边、外观检查、校核质量后再进行X光检测,用工总人数达68,且无任何信息化、自动化,因此对最终检验实施物流优化改造很有必要。
本工作对轮胎硫化后从地沟传送带出来至完成轮胎修边、外观检查、轮胎称量、X光机检测段进行物流优化。
1 现场工况1.1 基础数据日产量 10 000条全钢子午线轮胎;硫化机生产频率 50 min(每模);硫化机数量 195台(1#~4#地沟共104台,5#~8#地沟共91台);输送形式 输送流水线;工作时间 24 h·d-1;最大轮胎外直径 1 260 mm;最大轮胎质量 126 kg;最大轮胎断面宽度 450 mm;生产轮胎规格 381~622 mm(15~24.5英寸);修边、外观检查、称量、X光检测抽检比例 100%(特殊规格可不修边)。
1.2 现场布局物流优化前轮胎终检车间现场布局如图1所示。
硫化车间1#和2#地沟出来的轮胎经1#上下层传送带送至1#双工位手工修边机,3#和4#地沟出来的轮胎经2#上下层传送带送至2#双工位手工修边机,5#(8#)地沟出来的轮胎经3#(5#)传送带送至3#双工位手工修边机,6#和7#地沟出来的轮胎经4#上下层传送带送至4#双工位手工修边机。
轮胎硫化工艺条件的优化
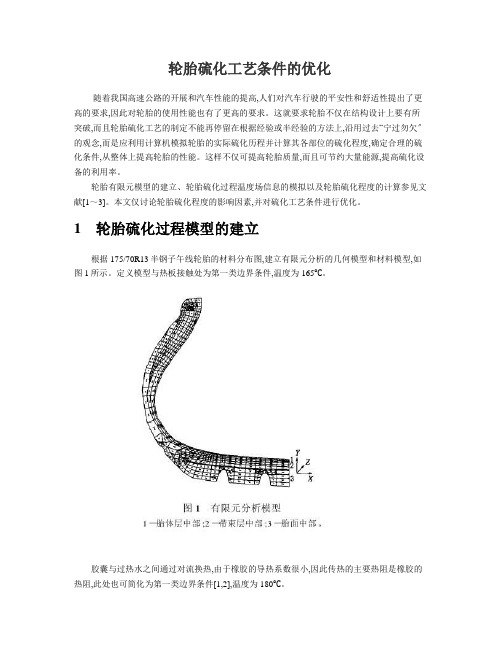
轮胎硫化工艺条件的优化随着我国高速公路的开展和汽车性能的提高,人们对汽车行驶的平安性和舒适性提出了更高的要求,因此对轮胎的使用性能也有了更高的要求。
这就要求轮胎不仅在结构设计上要有所突破,而且轮胎硫化工艺的制定不能再停留在根据经验或半经验的方法上,沿用过去“宁过勿欠〞的观念,而是应利用计算机模拟轮胎的实际硫化历程并计算其各部位的硫化程度,确定合理的硫化条件,从整体上提高轮胎的性能。
这样不仅可提高轮胎质量,而且可节约大量能源,提高硫化设备的利用率。
轮胎有限元模型的建立、轮胎硫化过程温度场信息的模拟以及轮胎硫化程度的计算参见文献[1~3]。
本文仅讨论轮胎硫化程度的影响因素,并对硫化工艺条件进行优化。
1轮胎硫化过程模型的建立根据175/70R13半钢子午线轮胎的材料分布图,建立有限元分析的几何模型和材料模型,如图1所示。
定义模型与热板接触处为第一类边界条件,温度为165℃。
胶囊与过热水之间通过对流换热,由于橡胶的导热系数很小,因此传热的主要热阻是橡胶的热阻,此处也可简化为第一类边界条件[1,2],温度为180℃。
模型与外界空气之间有对流换热,由于模型外外表覆盖绝热保温材料,因此换热可忽略不计,此边界可作为绝热边界处理。
轮胎出模后与空气之间有自然对流换热和辐射换热[2]。
模具初始温度取80℃,轮胎初始温度为25℃,胶囊初始温度为100℃。
2硫化程度的影响因素2.1硫化时间应用轮胎硫化过程模拟有限元模型在边界条件不变的情况下(热板温度165℃,胶囊内过热水温度180℃,分别求出图1所示3点过热水循环)时间为10,12,14和16min时的温度2时间关系,将结果代入计算硫化程度的程序中,求出各点在不同过热水循环时间下的硫化程度,如图2所示。
由图2可见,在所研究的时间范围内,过热水循环时间与3个节点位置处的硫化程度均呈线性关系,但对各部位的影响程度不同,过热水循环时间对胎体层和带束层硫化程度的影响比对胎面胶硫化程度的影响大得多,这是因为在硫化过程中胎体层和带束层更靠近胶囊的缘故。
优化内胎硫化工艺实现节能降耗

叠。
操作工开工前应取样检查缝合器的间隙,同时加强复检工作。
定期检查零度带束层导开装置,发现问题应停机进行维修。
更换轮胎规格时,应检查零度带束层导开装置、限位开关以及贴合鼓转速与零度带束层导开速度的匹配,测量并确保导开前后零度带束层宽度一致。
根据材料分布图和零度带束层伸张率,合理设定贴合鼓周长。
(3)精确计算轮胎内轮廓,选择合适的硫化胶囊。
严格控制硫化胶囊的使用寿命,定期更换硫化胶囊。
定期检查水缸压力,一旦水缸压力不足则不能进行硫化。
定期检查活络块的伸缩性,并详细记录清楚。
3 改进效果 通过采取上述措施,全钢载重子午线轮胎胎里拱发生率由0.4%减小到0.1%,轮胎均匀性合格率由96%提高到98%。
(杭州朝阳橡胶有限公司 毛建清王海燕 卢 青)优化内胎硫化工艺实现节能降耗中图分类号:TQ33611+2;TQ330.6+7 文献标识码:B 内胎物理性能的好坏直接影响车辆的安全性能。
随着子午线轮胎的发展,无内胎轮胎的比例逐渐增大,内胎用量逐渐减小。
为在激烈的市场竞争中立于不败之地,轮胎生产企业更加重视在提高内胎质量的同时降低生产成本。
本工作主要通过优化内胎硫化工艺,在提高内胎物理性能的同时,实现节能降耗的目的。
1 硫化工艺优化 对车间大料进行硫化特性抽检试验,抽检试验分别于2008年12月2,4,6,8,10和12日分6次进行。
试验结果表明,胶料t90的平均值为3.54 min,而原内胎硫化施工标准中t90均高于5.50 min,因此进行减时硫化试验,对硫化工艺进行优化,即t90采用4min。
硫化时间缩短后,内胎出现了气门嘴胶垫下部胎身硫化程度不足现象。
为此,采取以下改进措施。
2 改进措施2.1 硫化模具嘴子座改造 将硫化模具原实心嘴子座改造为中空蒸汽加热嘴子座,并使蒸汽在中空室内循环,以提高传热效率,加快气门嘴胶垫下胎身的硫化速度,改进硫化胶性能,使内胎物理性能的均匀性得到改善。
改造前后硫化模具嘴子座分别如图1和2所示。
发泡点法验证轮辋护胶对判定轮胎硫化时间的影响
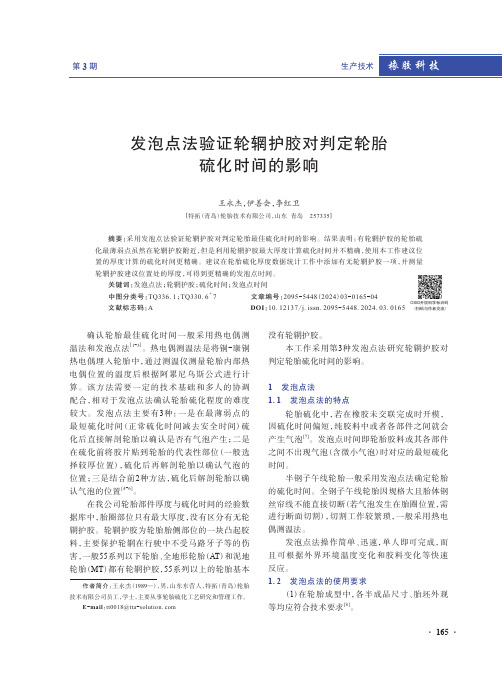
165发泡点法验证轮辋护胶对判定轮胎硫化时间的影响王永杰,伊善会,李红卫[特拓(青岛)轮胎技术有限公司,山东 青岛 257335]摘要:采用发泡点法验证轮辋护胶对判定轮胎最佳硫化时间的影响。
结果表明:有轮辋护胶的轮胎硫化最薄弱点虽然在轮辋护胶附近,但是利用轮辋护胶最大厚度计算硫化时间并不精确,使用本工作建议位置的厚度计算的硫化时间更精确。
建议在轮胎硫化厚度数据统计工作中添加有无轮辋护胶一项,并测量轮辋护胶建议位置处的厚度,可得到更精确的发泡点时间。
关键词:发泡点法;轮辋护胶;硫化时间;发泡点时间中图分类号:TQ336.1;TQ330.6+7 文章编号:2095-5448(2024)03-0165-04文献标志码:A DOI :10.12137/j.issn.2095-5448.2024.03.0165确认轮胎最佳硫化时间一般采用热电偶测温法和发泡点法[1-3]。
热电偶测温法是将铜-康铜热电偶埋入轮胎中,通过测温仪测量轮胎内部热电偶位置的温度后根据阿累尼乌斯公式进行计算。
该方法需要一定的技术基础和多人的协调配合,相对于发泡点法确认轮胎硫化程度的难度较大。
发泡点法主要有3种:一是在最薄弱点的最短硫化时间(正常硫化时间减去安全时间)硫化后直接解剖轮胎以确认是否有气泡产生;二是在硫化前将胶片贴到轮胎的代表性部位(一般选择较厚位置),硫化后再解剖轮胎以确认气泡的位置;三是结合前2种方法,硫化后解剖轮胎以确认气泡的位置[4-6]。
在我公司轮胎部件厚度与硫化时间的经验数据库中,胎圈部位只有最大厚度,没有区分有无轮辋护胶。
轮辋护胶为轮胎胎侧部位的一块凸起胶料,主要保护轮辋在行驶中不受马路牙子等的伤害,一般55系列以下轮胎、全地形轮胎(AT )和泥地轮胎(MT )都有轮辋护胶,55系列以上的轮胎基本没有轮辋护胶。
本工作采用第3种发泡点法研究轮辋护胶对判定轮胎硫化时间的影响。
1 发泡点法1.1 发泡点法的特点轮胎硫化中,若在橡胶未交联完成时开模,因硫化时间偏短,纯胶料中或者各部件之间就会产生气泡[7]。
- 1、下载文档前请自行甄别文档内容的完整性,平台不提供额外的编辑、内容补充、找答案等附加服务。
- 2、"仅部分预览"的文档,不可在线预览部分如存在完整性等问题,可反馈申请退款(可完整预览的文档不适用该条件!)。
- 3、如文档侵犯您的权益,请联系客服反馈,我们会尽快为您处理(人工客服工作时间:9:00-18:30)。
cure
degree.The results of the curing tempera—
ture-measuring and the durability experiments of cured tire showed that the tire 9.00R2016PRS811 was overcured
cure to a
certain extent,and the properties of cured tire did
to
not
attain
as
to
the optimum.The
ቤተ መጻሕፍቲ ባይዱ
time of the tire 9.00R2016PRS81 1 was shortened from 54 min
48 min
第32卷第3期
2011年6月
特种橡胶制品
Special Purpose Rubber Products
V01.32
NO.3
2011
June
轮胎硫化时间的优化
赵菲,夏荣芝,毕雪玲 (青岛科技大学橡塑材料与工程教育部重点实验室,青岛
266042)
摘要:主要通过气泡点的检测和硫化程度的计算等方法优化了轮胎硫化时间。硫化测温及减时耐久性测试 结果表明,9.00R2016PRS811型轮胎存在一定程度的过硫,轮胎性能未达到最佳状态。在保证轮胎性能的前 提下,将硫化时间由原来的54rain缩短至48min,减少了能耗,提高了生产效益。
其硬三角与肩部混炼胶,青岛赛轮股份有限公司。
1.2主要设备与仪器
双模轮胎定型硫化机,LL—B1525×4220× 2,中国环球集团橡胶机械有限公司;轮胎高速耐 久性试验机,QNS4--1324型,青岛高校测控技术 有限公司;硫化仪,MDR2000型,上海埃迩法仪 器科技有限公司;硫化测温仪,TNX—F型,上海 埃迩法仪器科技有限公司;橡胶加工分析仪, RPA2000型,上海埃迩法仪器科技有限公司。 1.3选择测温部位 根据硫化测温资料和测温经验,重点选择那 些重要而又具有代表性的部位,如,轮胎使用过程 中易出现质量问题的子口、胎肩和胎冠等部位。 硫化测温时间间隔为10s。轮胎出模后,常 温条件下自然冷却,待轮胎内最高温度点降至 110℃以下时,停止测温。
从表3可看出,减时硫化轮胎的耐久性能明 显优于原始轮胎,耐久时数比原始轮胎提高了
53%。
2.2硫化测温实验
2.2.1实测温度一时间曲线
胎肩和三角部位的实测硫化温度随时间的变
化见图1。
圈1各部位胶料实测温度一时间曲线
万方数据
赵菲等轮胎硫化时间的优化
从图I可看出,三角胶的温度较肩部胶的高, 但后硫化阶段的降温速率也较快。 2.2.2等效硫化速率和等效硫化程度的计算 等效硫化速率用下列公式计算:
[J].檬塑技术与装备,2005,31(1):17—21. [6]谭德征.轮胎硫化工艺的优选[J].轮胎工业,2005,25(2):
万方数据
特种橡胶制品
109—111. 748.
第32卷第3期
[7]于泳,等.硫化测温技术的应用[J].轮胎工业,2000,20
(11):678—681.
E93王象民.用DSC优化轮胎硫化周期的新方法l-J].橡胶参考 资料,2007,37(3)148—52.
ensuring the proper—
ties of cured tire,and the energy consumption was reduced,and the productivity was increased. Key words:tire;curing time;blow point;curing temperature-measuring
(1)从硫化测温和常规耐久实验中可看出,目 前国内生产的轮胎硫化时间过长,存在一定程度 的过硫,轮胎性能未达到最佳状态。 (2)从活化能计算、硫化测温及硫化程度的计 算结果可看出,三角胶对温度敏感性较大,过硫程 度较大。 (3)从硫化程度计算结果可看出,后硫化效应 在整个硫化过程中占有很大比重,在计算硫化程 度时应考虑后硫化效应。 (4)通过合理缩短硫化时间,可以提高9.00 R2016PRS811型轮胎的生产效率,节省能耗,提 高轮胎性能。
口0
(2)
将参比温度To的硫化速率Do赋值为1.0, 上式可进一步简化为:
口=eelR(1/%一1/D (3)
本实验中取To为151℃,由式(3)可计算任 意温度相对151℃下的等效硫化速率,等效硫化
程度为E=∑口t。等效硫化速率和等效硫化
程度的计算结果分别见表4和表5。
表4肩部胶等效硫化程度的计算结果
时间,步骤如下:
累计行驶时间,h:rain 累计行驶里程,km 气压增加率,%
97:40 5288.9 5.9 150:3 8153.3 12.2 0.9 1.2
外径增加率,%0.7 断面宽增加率。%0.8
(1)裁3片宽10cm,厚分别为lmm,2mm和 3mm,长约为轮胎断面轮廓长的胶片。 (2)取一实验胎坯,将准备好的胶片沿横断 面方向依次贴于轮胎内侧,胶片间隔约为10~ 15mm,压实贴紧,尽量排除气泡,贴好后做出标 记,注明胶片厚度及位置。 (3)将贴好的胎坯先按表2中2#方案的硫 化条件放入硫化机中硫化。 (4)将硫化好的轮胎按常规检测后,在标记 部位沿横断面剖开,取出带有标记的几段断面。检 测气孔,其中未贴胶片及贴有胶片的断面根据胶 片厚度由小到大依次记为oP,1P,2P和3P。用 放大镜仔细观察断面,特别是轮胎肩部和胎圈三 角最厚部位。若各断面均观察不到气泡,则按表 2中3#方案条件再做一次气泡实验,若3#方案 条件下有气泡,则按4#方案实验;若各断面均有
v_A2=eE/R(1/T1—1/r2)
铆1
=u£=10.93×1—10.93。三角胶在参比温度下 (151℃)的恒温硫化程度为15.18。 从表4和表5中可以看出,变温硫化条件下 肩部胶与三角胶的部位硫化程度分别为12.74和 28.40。因此,肩部胶与三角胶的部位过硫程度分 别为16.56%和87.1%,说明肩部胶与三角胶的 部位均存在一定程度的过硫。实际生产中,一般 要求轮胎硫化程度最低的部位过硫程度达到 20%左右。为了安全,将总硫化时间定为48 较为合理。 从表4和表5还可看出,后硫化效应在整个 硫化过程中占有很大比重,在计算硫化程度时应 考虑后硫化效应,可适当缩短硫化时间。因此,国 外有人认为硫化锦纶载重轮胎时,启模时硫化程 度应达到70%以上,较为适宜;对于子午线轮胎, 则提出用气泡点时间作为硫化时间。笔者将气泡 实验与硫化测温实验和性能分析结果相结合,最 终确定了最佳硫化时间。
1.4测温前的准备
测试各部位胶料的硫化曲线。 众所周知,活化能随胶料组分的改变而变化。 因此,应使用各部位胶料的活化能计算各自的硫 化程度。选取轮胎肩部与硬三角部位的混炼胶,
万方数据
50
特种橡胶制品
第32卷第3期
按标准ASTMD一2084,用MDR2000型硫化仪 分别做141℃,151℃与161℃三个温度下的硫化 曲线,求出不同特性时间t40,t50,t60,t70,t80,t90和 £。。下的活化能,得出各个胶料的平均活化能及硫 化平坦期范围。结果表明,肩部胶和三角胶的活 化能分别为98.8 kJ/tool和110.9 14/mol。 1.5耐久性测试 耐久性按GB/T 4501--2008测试。
1.6原始硫化条件
气泡,则按1#方案实验。逐轮改变硫化时间,直 至找出气泡点。各个方案的实验结果见表2。 从表2可看出,1#方案下断面OP~3P均未 发现气泡,各项常规测试均合格,说明1#方案下 轮胎各部位均已达到完全硫化。2#方案下各层 均出现气泡,且气泡较大,因此,总硫化时间为 33min时轮胎欠硫,2#方案不可行。3#方案下 OP---3P均观测不到气泡,各项常规测试也合格, 说明总硫化时间为39min时,轮胎各部位也已达 到正硫化,判断气泡点约在39min左右。为安全 考虑,增加硫化安全因子,最终确定的硫化时间为 气泡点时间加上安全时间,企业内部安全时间为 气泡点时间的15%。最终硫化时间的确定还要 结合硫化测温和高速耐久性试验。耐久性试验结
品,2005,26(3):33—41.
[43王顺利,邵文波.9.00--20/16PR外胎硫化测温[J].轮胎工 业,2001,21(2):115—117. [5]王其营,等.浅谈硫化设备的性能与操作对外胎质量的影响
肩部胶在151℃下的正硫化时间为10.93 rain,在参比温度(151’C)下的恒温硫化程度为:E
3结论
min
(1)
式中:E一胶料硫化反应活化能;R一气体常数; T1,T2一绝对温度;口。,口。一分别是L和丁2下的 硫化速率。 定义Do是在已知温度L下计算的已知速率 (取自在To条件下运行的硫化仪曲线),在任意 温度T条件下的速率D可参照在温度T。下的 DO,从而To变为参比温度。因此上式变为: 旦一eE/R(1/TO一1/D
果见表3。 表2气泡点检测实验结果
9.00R2016PRS811全钢载重子午线轮胎的 原始硫化条件见表1。
表1原始硫化工艺条件 热板温度147"C士2"C模套温度162℃±2℃内压2.6MPa士0.1MPa 内温170"(2-I-2’C 压力,MPa
时间
2结果与讨论 2.1气泡点检测试验 气泡点法是测试轮胎硫化程度的最古老方 法。本实验采用贴胶片找气泡点的方法优化硫化
表5三角胶等效硫化程度的计算结果
参考文献: [1]王登祥.美国轮胎公司确定轮胎硫化时间的方法[J].轮胎 工业,1999,19(5):290—295. [2]傅彦杰.橡胶厚制品硫化温度与等效硫化时间的测定[J]. 橡胶工业.1997,44(9):552—557. [3] 姚钟尧.确定和优化轮胎硫化时问的方法[J].特种橡胶制
关键词:轮胎;硫化时间;气泡点;硫化测温 中图分类号:TQ336.1+1 文献标识码:A 文章编号:1005—4030(2011)03一0049一03