超重型精密数控轧辊磨床创新机加工艺论文
论述与分析轧辊磨床工艺改进

239学术论丛论述与分析轧辊磨床工艺改进齐洪震唐山瑞丰钢铁(集团)有限公司摘要:本文在轧辊磨床的基础设备、工作原理进行简单阐述,并针对目前轧辊磨床工艺存在的问题:(1)磨损问题;(2)精度不高;(3)数控系统落后;(4)曲线磨制落后,提出相应改进方案:(1)对机床进行保养;(2)提高磨床精度;(3)发展数控系统在轧辊磨床方面的应用;(4)增加多样磨制,以此提高轧辊磨床工艺技术。
关键词:轧辊磨床工艺;改进方案引言随着科技及工业发展,轧辊磨床工艺逐渐进入我们的视野,轧辊磨床工艺是对工件进行精密加工的生产流水线,具有结构稳定、精准的优势,在工业生产中带来一定便捷性,给工厂带来效益。
轧辊磨床工艺技术的高低直接影响加工效率、钢板产品的质量,最终影响组合产品品质,所以对轧辊磨床工艺技术进行改进是十分有必要的。
轧辊磨床基础设备较为复杂,影响产品品质的因素也较多,所以在对轧辊磨床工艺进行改进时,要系统分析,明确问题因素,实施相应对策,解决问题。
1.轧辊磨穿工艺的运作性质1.1设备结构轧辊磨床设备由机械设备由(1)床身,保证磨床工艺过程中的精度;(2)头架,保证磨床过程中驱动的稳定进行;(3)尾架,在轧辊过程中进行轴向定位,避免发生窜动脱离;(4)托架,用来支撑轧辊;(5)砂轮架,由成型机构、主轴等影响辊型成型的重要部分组成,是轧辊磨床的核心;(6)中凹成型机构,具有靠模式、凸轮式、数控成型式几种类型;(7)冷却过滤系统,增大使用寿命及精度,具有冷却、清洁、润滑、防锈等功能;(8)电控设备,对机床进行控制及错误检查;(9)轴定义,在数控磨床工艺中给各个装置分配标准值和实际值。
1.2工作原理轧辊磨床设备各部件相互配合,磨削时砂轮高速旋转,磨削量小而精准,磨床控制系统接收在线测量系统测量的实时轧辊数据,根据相关数据进行相应磨削调整。
2.目前轧辊磨床工艺存在的问题2.1精度不高目前轧辊磨床工艺存在精度不高的原因主要是安装及磨损问题。
浅谈轧辊磨床磨削轧辊
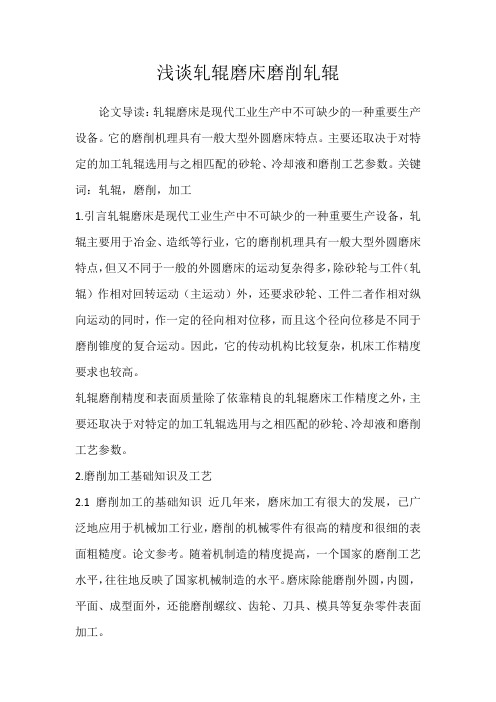
浅谈轧辊磨床磨削轧辊论文导读:轧辊磨床是现代工业生产中不可缺少的一种重要生产设备。
它的磨削机理具有一般大型外圆磨床特点。
主要还取决于对特定的加工轧辊选用与之相匹配的砂轮、冷却液和磨削工艺参数。
关键词:轧辊,磨削,加工1.引言轧辊磨床是现代工业生产中不可缺少的一种重要生产设备,轧辊主要用于冶金、造纸等行业,它的磨削机理具有一般大型外圆磨床特点,但又不同于一般的外圆磨床的运动复杂得多,除砂轮与工件(轧辊)作相对回转运动(主运动)外,还要求砂轮、工件二者作相对纵向运动的同时,作一定的径向相对位移,而且这个径向位移是不同于磨削锥度的复合运动。
因此,它的传动机构比较复杂,机床工作精度要求也较高。
轧辊磨削精度和表面质量除了依靠精良的轧辊磨床工作精度之外,主要还取决于对特定的加工轧辊选用与之相匹配的砂轮、冷却液和磨削工艺参数。
2.磨削加工基础知识及工艺2.1 磨削加工的基础知识近几年来,磨床加工有很大的发展,已广泛地应用于机械加工行业,磨削的机械零件有很高的精度和很细的表面粗糙度。
论文参考。
随着机制造的精度提高,一个国家的磨削工艺水平,往往地反映了国家机械制造的水平。
磨床除能磨削外圆,内圆,平面、成型面外,还能磨削螺纹、齿轮、刀具、模具等复杂零件表面加工。
磨床—磨床在磨削工件时,按加工要求不同,工作台纵向运动的速度必须可以调整,能实现无极变速,并在换向时有一定的精度要求,磨床要具备这些条件,磨床的纵向往复运动采用了液压传动,液压传动在磨床的工作台驱动及横向快速进退等方面已广泛应用。
液压传动工作原理—在机床上为改善液压传动的性能,以满足生产加工中的各种要求,磨床工作的液压传动系统是由以下四部分组成:执行部分—液压机(液压缸、液压马达)在压力油的推动下,作直线运动或回转运动,即将液体的压力能转换为机械能。
控制部分—压力控制阀,流量控制阀,方向控制阀等,用以控制液压传动系统所需要的力速度方向和工作性能的要求。
辅助部分—油箱滤油器,油管和油管接头等。
机械制造及自动化专业毕业论文--一种先进的超精密磨床
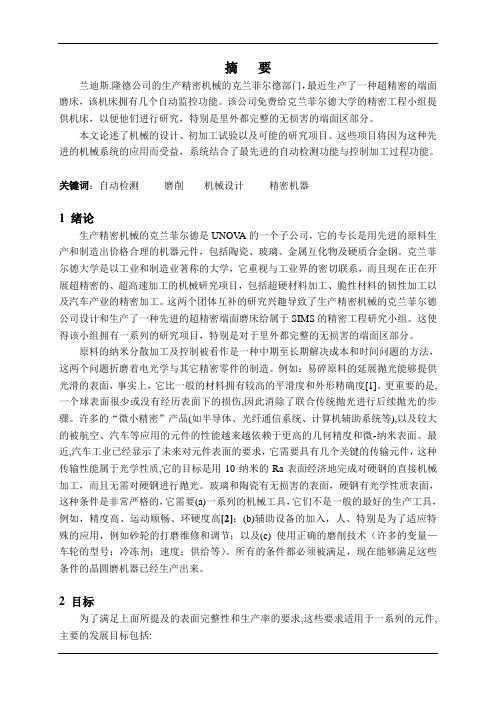
摘要兰迪斯.隆德公司的生产精密机械的克兰菲尔德部门,最近生产了一种超精密的端面磨床,该机床拥有几个自动监控功能。
该公司免费给克兰菲尔德大学的精密工程小组提供机床,以便他们进行研究,特别是里外都完整的无损害的端面区部分。
本文论述了机械的设计、初加工试验以及可能的研究项目。
这些项目将因为这种先进的机械系统的应用而受益,系统结合了最先进的自动检测功能与控制加工过程功能。
关键词:自动检测磨削机械设计精密机器1 绪论生产精密机械的克兰菲尔德是UNOV A的一个子公司,它的专长是用先进的原料生产和制造出价格合理的机器元件,包括陶瓷、玻璃、金属互化物及硬质合金钢。
克兰菲尔德大学是以工业和制造业著称的大学,它重视与工业界的密切联系,而且现在正在开展超精密的、超高速加工的机械研究项目,包括超硬材料加工、脆性材料的韧性加工以及汽车产业的精密加工。
这两个团体互补的研究兴趣导致了生产精密机械的克兰菲尔德公司设计和生产了一种先进的超精密端面磨床给属于SIMS的精密工程研究小组。
这使得该小组拥有一系列的研究项目,特别是对于里外都完整的无损害的端面区部分。
原料的纳米分散加工及控制被看作是一种中期至长期解决成本和时间问题的方法,这两个问题折磨着电光学与其它精密零件的制造。
例如:易碎原料的延展抛光能够提供光滑的表面,事实上,它比一般的材料拥有较高的平滑度和外形精确度[1]。
更重要的是,一个球表面很少或没有经历表面下的损伤,因此消除了联合传统抛光进行后续抛光的步骤。
许多的“微小精密”产品(如半导体、光纤通信系统、计算机辅助系统等),以及较大的被航空、汽车等应用的元件的性能越来越依赖于更高的几何精度和微-纳米表面。
最近,汽车工业已经显示了未来对元件表面的要求,它需要具有几个关键的传输元件,这种传输性能属于光学性质,它的目标是用10纳米的Ra表面经济地完成对硬钢的直接机械加工,而且无需对硬钢进行抛光。
玻璃和陶瓷有无损害的表面,硬钢有光学性质表面,这种条件是非常严格的,它需要(a)一系列的机械工具,它们不是一般的最好的生产工具,例如,精度高、运动顺畅、环硬度高[2];(b)辅助设备的加入,人、特别是为了适应特殊的应用,例如砂轮的打磨维修和调节;以及(c) 使用正确的磨削技术(许多的变量—车轮的型号;冷冻剂;速度;供给等)。
数控车床论文(精选5篇)

数控车床论文(精选5篇)第一篇:数控车床论文[摘要]:数控系统经过一段时间的使用,电子原器件性能下降,甚至损坏,有些机械部件如导轮及导轮轴承等也是如此。
【关键词】:润滑、定期润滑、定期调整浅析机床数控系统的技术维护数控系统经过一段时间的使用,电子原器件性能下降,甚至损坏,有些机械部件如导轮及导轮轴承等也是如此。
为了保持机床能正常可靠地工作,延长其使用寿命,就必须对数控系统进行日常的维护。
数控系统经过一段时间的使用,电子原器件性能下降,甚至损坏,有些机械部件如导轮及导轮轴承等也是如此。
为了保持机床能正常可靠地工作,延长其使用寿命,就必须对数控系统进行日常的维护。
概括地说主要注意以下几个方面:一、制定数控系统的日常维护的规章制度要根据各部件的特点,确定各自保养规则。
如明确规定哪些部件需要经常清洁、校验(如CNC系统的光电输人机或电报机头的清洁)哪些部件需要定期润滑调整(如轴承、丝杠、传动齿轮的定期润滑支流伺服电动机电刷和换向器应每半月检查一次等)。
二、定期润滑数控机床上需要定期润滑的部位均有说明,主要有机床导轨,丝杠,螺母、传动齿轮等处,一般用油枪注人,轴承和滚珠丝杠如有保护套式的可以经半年后拆开来注油。
三、尽a少开数控柜和强电柜的门因为在加工车间的空气中大都含有油污,灰尘甚至金属颗粒,一旦它们落在数控系统内的印制线路或原器件上,极易导致器件绝缘性下降,甚至导致原器件上,极易导致器件绝缘性下降,甚至导致元器件及线路的损坏。
有的操作者在夏天为了使数控系统超负荷工作,而打开数控柜的门来散热,这样会导致数控系统的加速损坏。
正确的方法应是设法降低设备外部环境温度,除非进行必要的维护,不能随便打开柜门,更不允许在使用时敞开柜门。
四、定期调整丝杠螺母、导轨及电极丝挡块,进电块等,根据使用时间,间隙大小或沟槽深浅进行调整,部分数控线切割机床采用锥形开槽式的调节螺母,则需要适当地拧紧一些,凭经验和手感确定间隙,保持转动灵活,滚动导轨的调整方法为松开工作台一边的导轨固定螺钉,拧调节螺钉看百分表的反映使其紧靠另一边,挡丝块和进电块如使用日久,摩擦出沟痕,须转动或移动一下,以改变接触位置即可。
超重型精密数控轧辊磨床的创新机加工艺
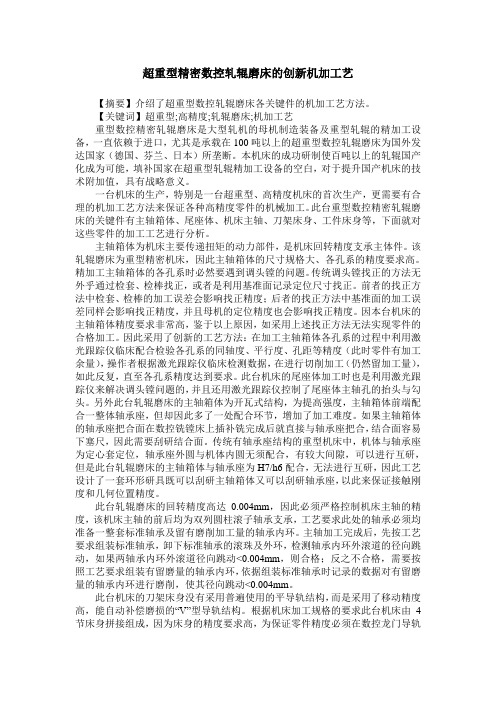
超重型精密数控轧辊磨床的创新机加工艺【摘要】介绍了超重型数控轧辊磨床各关键件的机加工艺方法。
【关键词】超重型;高精度;轧辊磨床;机加工艺重型数控精密轧辊磨床是大型轧机的母机制造装备及重型轧辊的精加工设备,一直依赖于进口,尤其是承载在100吨以上的超重型数控轧辊磨床为国外发达国家(德国、芬兰、日本)所垄断。
本机床的成功研制使百吨以上的轧辊国产化成为可能,填补国家在超重型轧辊精加工设备的空白,对于提升国产机床的技术附加值,具有战略意义。
一台机床的生产,特别是一台超重型、高精度机床的首次生产,更需要有合理的机加工艺方法来保证各种高精度零件的机械加工。
此台重型数控精密轧辊磨床的关键件有主轴箱体、尾座体、机床主轴、刀架床身、工件床身等,下面就对这些零件的加工工艺进行分析。
主轴箱体为机床主要传递扭矩的动力部件,是机床回转精度支承主体件。
该轧辊磨床为重型精密机床,因此主轴箱体的尺寸规格大、各孔系的精度要求高。
精加工主轴箱体的各孔系时必然要遇到调头镗的问题。
传统调头镗找正的方法无外乎通过检套、检棒找正,或者是利用基准面记录定位尺寸找正。
前者的找正方法中检套、检棒的加工误差会影响找正精度;后者的找正方法中基准面的加工误差同样会影响找正精度,并且母机的定位精度也会影响找正精度。
因本台机床的主轴箱体精度要求非常高,鉴于以上原因,如采用上述找正方法无法实现零件的合格加工。
因此采用了创新的工艺方法:在加工主轴箱体各孔系的过程中利用激光跟踪仪临床配合检验各孔系的同轴度、平行度、孔距等精度(此时零件有加工余量),操作者根据激光跟踪仪临床检测数据,在进行切削加工(仍然留加工量),如此反复,直至各孔系精度达到要求。
此台机床的尾座体加工时也是利用激光跟踪仪来解决调头镗问题的,并且还用激光跟踪仪控制了尾座体主轴孔的抬头与勾头。
另外此台轧辊磨床的主轴箱体为开瓦式结构,为提高强度,主轴箱体前端配合一整体轴承座,但却因此多了一处配合环节,增加了加工难度。
全自动重型数控轧辊磨床研制
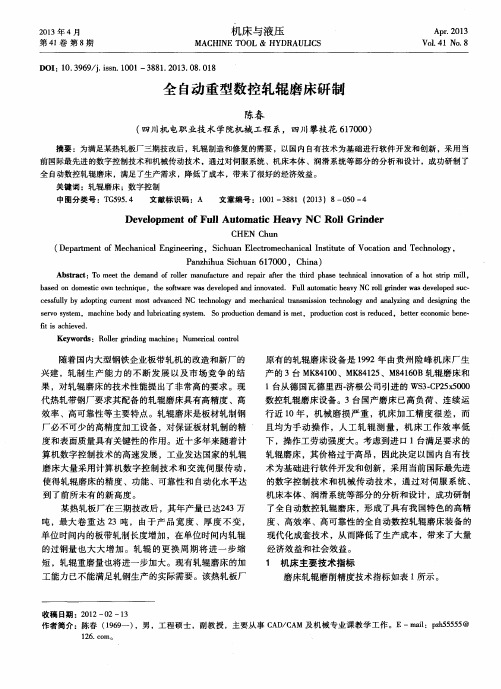
中图分类 号 :T G 5 9 5 . 4 文献标识码 :A 文章编号 :1 0 0 1 —3 8 8 1( 2 0 1 3 )8— 0 5 0— 4
De v e l o p me nt o f Fu l l Aut o ma t i c He av y N C Ro l l Gr i n de r
2 0 1 3年 4月
机床与液压
MACHI NE T OOL & HYDRAUL I CS
Ap r . 2 01 3 V0 】 . 41 No . 8
第4 l卷 第 8 期
DOI : 1 0 . 3 9 6 9 / j . i s s n . 1 0 0 1—3 8 8 1 . 2 0 1 3 . 0 8 . 0 1 8
CHEN Ch u n
( D e p a r t m e n t o f Me c h a n i c a l E n g i n e e r i n g ,S i c h u a n E l e e t r o me c h a n i c a l I n s t i t u t e o f V o c a t i o n a n d T e c h n o l o g y , P a n z h i h u a S i c h u a n 6 1 7 0 0 0 ,C h i n a )
使得轧辊磨床 的精度 、功能 、可靠性和 自动化水平达 到 了前所未有 的新高度 。 某热 轧板 厂在三期技改后 ,其年产量 已达2 4 3万 吨 ,最 大卷 重 达 2 3吨 ,由于产 品宽 度 、厚 度 不变 ,
超重型精密数控轧辊磨床设计

响。
国家 高档数控机床 与基础制造装备重大专项资助项 目
( 号 : 2 0 Z 4 0 .7 ) 编 0 9 X0 0 20 1
MK 4 5/5 0 超 重 型 精 密 数 控 轧 辊 磨 A8 2 010 0H
床 , 为五 轴 三 联 动 数 控 轧 辊 磨 床 。它 采 用 西 门 予
拖板 带着 砂轮 架在 后床 身上 作纵 向移动 ,砂 轮架 采
用静 压 闭式导 轨在拖 板上 作横 向移 动 。砂轮 主轴 由
静压轴 承 支承旋 转 ,通 过 计算机 控制 ,实现 微量 进 给及 曲面 磨削 。工件装 夹在 前床 身上 的头 、尾 架顶 尖之 问 , 由头架 驱动 旋转 ,并可 实现 无级 调速 。机 床 配备 有 可调整 的工 件托 架 ,用 于托 持细 长型 的工 件 。尾架可沿前床身 自动移 动及 夹紧 ,尾架项尖可机 动伸缩 10 mm,并配有 工件 顶 紧力检 测装 置 。同 5 时 ,尾架上装有砂轮 修整器 ,砂轮 自动测径装置 、自 动修 整控 制装 置等 ,以备 自动磨 削 , 自动修 整用 。
精密 制造 与 自动化
2 1年 第 3 01 期
超重 型精密数控轧辊磨床设计木
段 斌 华
( 上海机 床厂 有 限公 司 上 海 2 0 9 ) 0 0 3
摘 要 以超重型精 密数控 轧辊 磨床设计 为对象 ,阐述 了机床的结构特 征、设计难 点及创新 内容 。利用有 限元分
析方法和仿真技术,对机床各主要部件进行 了静力学 、动力学的分析研 究。针对 国家 “ 高档数控机床 与基础 制造 装 备科 技重大专项课题 ” “ MK 4 5 /5 0 一 超重 型精密数控 轧辊磨床 ” 项 目,介绍 了在设计开发过程 中 A8 2 010 0H 所运用 的新技术 、新机构和新工艺 ,通过 了国家机床质量监督检验 中心 的检验及专家的技术鉴定,为企业提供 了 超 大型重型轧辊 的表 面磨 削基础制造装备 ,为超重型精密磨床设计提供 了新思路 。 关键 词 超 重 精密 数控 轧辊 磨床 关键技术 先进水平
浅谈如何提高数控轧辊磨床的磨削质量
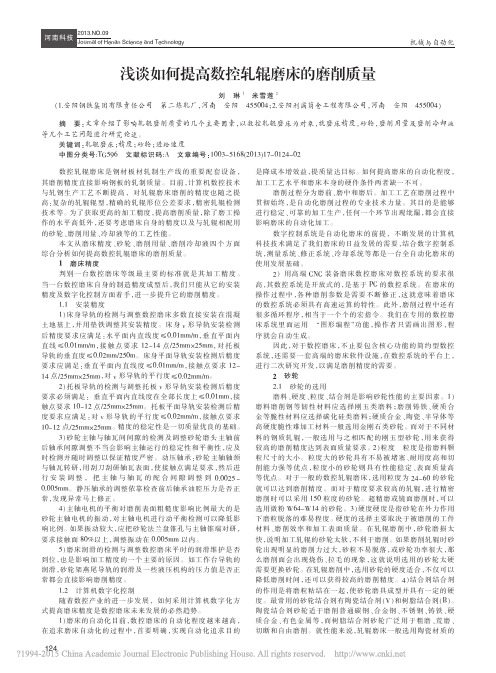
数控轧辊磨床是钢材板材轧制生产线的重要配套设备,其磨削精度直接影响钢板的轧制质量。
目前,计算机数控技术与轧钢生产工艺不断提高,对轧辊磨床磨削的精度也随之提高:复杂的轧辊辊型,精确的轧辊形位公差要求,精密轧辊检测技术等。
为了获取更高的加工精度,提高磨削质量,除了磨工操作的水平高低外,还要考虑磨床自身的精度以及与轧辊相配用的砂轮、磨削用量、冷却液等的工艺性能。
本文从磨床精度、砂轮、磨削用量、磨削冷却液四个方面综合分析如何提高数控轧辊磨床的磨削质量。
1磨床精度判别一台数控磨床等级最主要的标准就是其加工精度。
当一台数控磨床自身的制造精度成型后,我们只能从它的安装精度及数字化控制方面着手,进一步提升它的磨削精度。
1.1安装精度1)床身导轨的检测与调整数控磨床多数直接安装在混凝土地基上,并用垫铁调整其安装精度。
床身v 形导轨安装检测后精度要求应满足:水平面内直线度≤0.01mm/m ,垂直平面内直线≤0.01mm/m ,接触点要求12~14点/25mm ×25mm ,对托板导轨的垂直度≤0.02mm/250m 。
床身平面导轨安装检测后精度要求应满足:垂直平面内直线度≤0.01mm/m ,接触点要求12~14点/25mm ×25mm ,对v 形导轨的平行度≤0.02mm/m 。
2)托板导轨的检测与调整托板v 形导轨安装检测后精度要求必须满足:垂直平面内直线度在全部长度上≤0.01mm ,接触点要求10~12点/25mm ×25mm 。
托板平面导轨安装检测后精度要求应满足:对v 形导轨的平行度≤0.02mm/m ,接触点要求10~12点/25mm ×25mm 。
精度的稳定性是一切质量优良的基础。
3)砂轮主轴与轴瓦间间隙的检测及调整砂轮磨头主轴前后轴承间隙调整不当会影响主轴运行的稳定性和平衡性,应及时检测并随时调整以保证精度严密。
动压轴承:砂轮主轴轴颈与轴瓦转研,用刮刀刮研轴瓦表面,使接触点满足要求,然后进行安装调整,把主轴与轴瓦的配合间隙调整到0.0025~0.005mm 。
大型重载多功能数控轧辊磨床的研制

砂轮 架横 向进 给运 动 ( 轴 ) 测量 装置 进给 运动 ( 轴 、X 姗 2轴 )
中凸 ( )磨 削运 动 ( 凹 U轴 )
头 架 驱 动 交 流 电动 机 砂 轮 架 驱 动 交 流 电动 机 圆柱 面 磨 削 精 度
圆度 纵 截 面 上 直 径 一致 性 表 面 粗糙 度 R a 中 凸 ( 面 磨 削精度 凹) 圆度
辊 、橡 胶 辊 等 的 粗 磨 、精 磨 加 工 ,能够 完 成 中 凸
( ) 曲线辊面 以及 圆锥 形辊 面等 部位 的磨 削 。 凹
1 1 机床主要技术规格参数 .
最大 磨 削直 径
可扩 展 至
20 0mm 0
22 0mm 0
最 小 烘 缸 磨 削 直 径
最 小 轧 辊 磨 削 直 径
砂 轮 线速 ( 线速 ) 恒 数 控 最 小分 辨 率 砂轮 架移 动速 度 拖 板移 动速 度 ( 轴) 测量 直 径 范 围 托架 支 承 直径 范 围 软着 陆装 置 托直 径 托 持范 围 冷却泵 流量
4 s 5 m/ 00 01 .0 mm 1 ~ 1 2 mi O 0mm/ n 0 4 ~40 0mm mi 0 0 / n 8 ~ 22 0mm 0 0 10 5 0  ̄8 0mm 80 0 n 0  ̄2 0t i 0 o 4 0Lmi 0 / n
需 要 ,上海机 床 多年来 一 直从事 大 型、重 载 、高精
度 数控 轧辊 的研 发 , 最近 研制 的 MK8 2 010 0 H 4 o /5 0-
成 各 种 型 面 的数 控 磨 削及 型面 修 整 。砂 轮 架通 过 直线导轨可在拖板上作横 向移动 ,实现进给磨 削。工 件 装 夹 在 位 于 前 床 身 的 头 架 及 尾 架 之 间 , 由头 架带 动工件 旋转 ,可 实现 无级 调速 。装卸 工件 采用 软着 陆装 置 ,方便工 件 的装卸 。尾架 顶尖 套筒机 动 伸 缩 ,并配 有 工件顶 紧力 检测 装置 ,保证 工件 安全
轧辊磨床的数控化应用技术
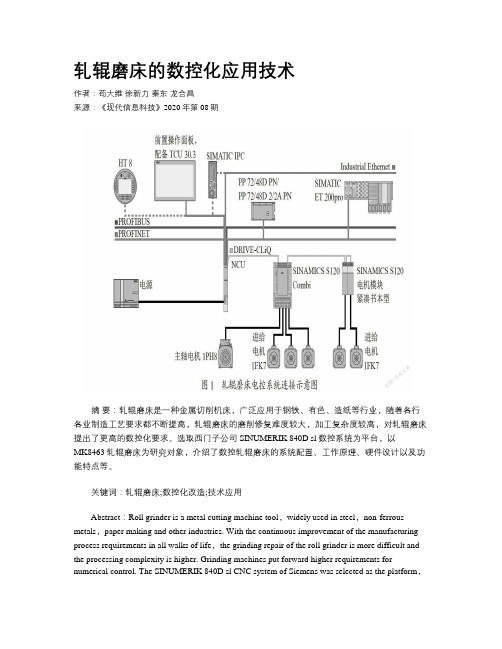
轧辊磨床的数控化应用技术作者:苟大维徐新力秦东龙合昌来源:《现代信息科技》2020年第08期摘要:轧辊磨床是一种金属切削机床,广泛应用于钢铁、有色、造纸等行业,随着各行各业制造工艺要求都不断提高,轧辊磨床的磨削修复难度较大,加工复杂度较高,对轧辊磨床提出了更高的数控化要求。
选取西门子公司SINUMERIK 840D sl数控系统为平台,以MK8463轧辊磨床为研究对象,介绍了数控轧辊磨床的系统配置、工作原理、硬件设计以及功能特点等。
关键词:轧辊磨床;数控化改造;技术应用Abstract:Roll grinder is a metal cutting machine tool,widely used in steel,non-ferrous metals,paper making and other industries. With the continuous improvement of the manufacturing process requirements in all walks of life,the grinding repair of the roll grinder is more difficult and the processing complexity is higher. Grinding machines put forward higher requirements for numerical control. The SINUMERIK 840D sl CNC system of Siemens was selected as the platform,and the MK8463 roll grinder was taken as the research object. The system configuration,working principle,hardware design and functional characteristics of the CNC roll grinder were introduced.Keywords:roller grinder;numerical control transformation;technical application0 引言随着我国经济社会的快速发展和科技水平的不断提升,工业化进程不断加快,轧辊磨床作为满足特殊工艺要求的重要工业生产设备,广泛应用于钢铁产业、有色金属冶炼产业、造纸印刷产业等诸多工业的生产过程。
轧辊磨床数控技术应用

浅议轧辊磨床数控技术的应用【摘要】热轧2050轧辊磨床是用于轧辊表面精加工的设备,其主要功用是磨削热轧厂的工作辊和支承辊,其数控系统为ibso公司专为德国waldrich轧辊制造厂开发的第一代产品,型号为ilc-500。
随着用户对钢板表面质量要求的不断提高,轧辊磨床的磨削精度成为制约钢板质量和板形精度的瓶颈,同时磨辊间减少操作人员数量并提高劳动生产率的要求也越来越强烈,故决定对热轧2050轧辊磨床进行改造。
本章重点介绍具体改造方案。
【关键词】数控技术;轧辊磨床1.热轧轧辊磨床的结构和工作特点在钢铁企业中,轧辊主要用于热、冷轧钢板轧制,由于其在高温、高负载等恶劣条件下工作,故很快就发生磨损,当轧辊磨损到一定程度,为保证轧件表面质量和尺寸精度,需要及时换辊。
而更换下来的轧辊也需要迅速放到轧辊磨床上进行磨削,磨削到一定精度要求后再送回轧机使用。
1.1轧辊磨床的结构磨床主要有以下三部分独立的部件机械地组成:1.1.1后床身,包括:转动砂轮的砂轮主轴沿轧辊长度方向往复纵向运动的砂轮刀架砂轮趋近和退回磨床/轧辊中心横向运动的砂轮头1.1.2前床身,用来转动、支撑和调整轧辊的,包括:转动轧辊的床头箱主轴,床头箱装有固定从动轴心的一个顶尖,这个轴心通常用来与缓冲器一起协作工作,这个缓冲器用来防止从动轴心由于接触转动轧辊产生的磨损,这个缓冲器有两个主要部件构成,一个部件(安装在从动轴心上)是通过滚柱轴承连接到它的转动部件上,另一个部件与轧辊的终端连接。
1.1.3测量臂,用来测量轧辊几何尺寸的。
1.2现代轧辊磨床的特点现代轧辊磨床主要特点:cnc控制、高度自动化和集成化、磨削效率和精度高。
轧辊磨床的主要运动如砂轮、轧辊的旋转运动均采用了全数字化直流传动,控制精度高并可实现在一定范围内无级调速。
砂轮主轴采用了毛细管节流的静压支承,床身导轨采用了静压导轨,具有足够的刚度及耐磨性。
砂轮能完成微量进给,连续和端头自动进给和砂轮磨损补偿进给,能磨削出最大凸度或凹度为3毫米的任何形状的曲线。
210978900_数控技术在轧辊磨床上的应用与分析

管理及其他M anagement and other数控技术在轧辊磨床上的应用与分析于晓明摘要:轧辊磨床本身就是轧制钢板生产线的核心配置,高精度磨削的精密高效磨削可以保证钢板制造业的生产效率和质量。
本文首先介绍了轧辊磨床的概述,同时阐述了数控技术的基本概念,最后阐述了轧辊磨床的数控化,旨在为钢材轧制行业更好的发展提供参考。
关键词:数控技术;轧辊磨床;应用;概念在经济全球化的背景下,对轧辊加工提出了新的要求,以技术要求为主,加速提高轧钢技术,促进轧钢行业的发展。
将数控技术应用于轧辊磨床,实现自动化控制,进而调整控制轴的速度和位置,通过下达管理指令、执行操作指令来改进操作,保证稳定运行。
本文主要对数控技术在轧辊磨床中的应用进行探讨和阐述,旨在为轧辊磨床技术的改进提供一个方向。
1 轧辊磨床概述轧辊磨床是支撑钢板工业生产的重要设备。
磨削精度和磨削效率对气缸的质量和钢铁生产过程的实际性能有很大影响。
在实际厚板轧制过程中,由于氧化温度高、机械磨损等原因,气缸类型发生变化,轧制精度降低。
因此,钢铁制造商定期研磨和维修钢瓶。
在气缸磨削过程中,数控气缸磨削系统有一个计算气缸表面夹板的数学模型。
由于在各种连接机构的传动条件下,砂轮对气缸金属表面的磨削效率和精度有很大影响,因此可以对气缸表面进行科学的分析,以达到理论计算的理想气缸形状。
自动辊磨机系统主要为磨辊控制系统提供实时测量数据反馈,控制系统将相关闭环控制指令引导至辊磨机进行精确控制。
一般来说,磨削气缸的结构分为两类:工件机架的移动结构和磨床机架的移动结构。
如果砂光机辊的直径和重量较小,则可以将其作为可移动的框架结构放置。
此外,如果加工气缸的实际直径和重量较高,则必须将辊磨机放置在砂轮架的移动结构中。
目前,圆柱曲线的磨削是通过内磨机构进行的,滚子磨床有不同的结构形式,其中凸轮杆的结构最为广泛。
中高磨削结构可以有效满足气缸精度的要求,但真正的中高机床结构复杂,传动链长,调整过程复杂,降低了实际刚度,对磨削精度有一定影响。
刍议HERKULES轧辊磨床磨削工艺优化
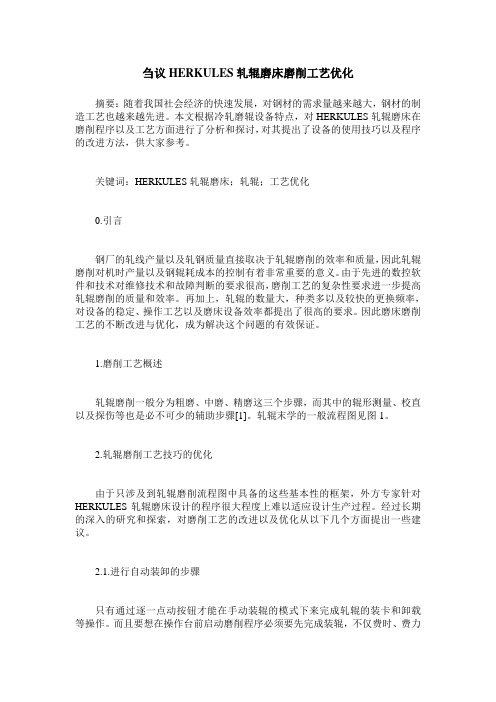
刍议HERKULES轧辊磨床磨削工艺优化摘要:随着我国社会经济的快速发展,对钢材的需求量越来越大,钢材的制造工艺也越来越先进。
本文根据冷轧磨辊设备特点,对HERKULES轧辊磨床在磨削程序以及工艺方面进行了分析和探讨,对其提出了设备的使用技巧以及程序的改进方法,供大家参考。
关键词:HERKULES轧辊磨床;轧辊;工艺优化0.引言钢厂的轧线产量以及轧钢质量直接取决于轧辊磨削的效率和质量,因此轧辊磨削对机时产量以及钢辊耗成本的控制有着非常重要的意义。
由于先进的数控软件和技术对维修技术和故障判断的要求很高,磨削工艺的复杂性要求进一步提高轧辊磨削的质量和效率。
再加上,轧辊的数量大,种类多以及较快的更换频率,对设备的稳定、操作工艺以及磨床设备效率都提出了很高的要求。
因此磨床磨削工艺的不断改进与优化,成为解决这个问题的有效保证。
1.磨削工艺概述轧辊磨削一般分为粗磨、中磨、精磨这三个步骤,而其中的辊形测量、校直以及探伤等也是必不可少的辅助步骤[1]。
轧辊末学的一般流程图见图1。
2.轧辊磨削工艺技巧的优化由于只涉及到轧辊磨削流程图中具备的这些基本性的框架,外方专家针对HERKULES轧辊磨床设计的程序很大程度上难以适应设计生产过程。
经过长期的深入的研究和探索,对磨削工艺的改进以及优化从以下几个方面提出一些建议。
2.1.进行自动装卸的步骤只有通过逐一点动按钮才能在手动装辊的模式下来完成轧辊的装卡和卸载等操作。
而且要想在操作台前启动磨削程序必须要先完成装辊,不仅费时、费力而且效率不高。
自动装卸程序对轧辊所处的状态能够自动识别,轧辊装卡与卸载的动作也按照程序指令自动完成,而且机床可以同时进行许多工作,在这个过程中,有以下几点需要注意:①只有先增加暂停步骤才能进行自动装辊步骤,避免出现磨床上没有轧辊的情况下程序误启动的现象,造成尾架自行前进到尾架侧托架,致使导轨的损坏[2]。
②磨床上的轧辊应尽量精确其摆放位置,才能启动自动装辊。
数控技术在轧辊磨床上的应用

环 控 制 。
(下转 87页 )
C 科学技术
J CieliCe and ted )noloc]u
—
要 。尤其 是近 年来 广西 某新材 料 有限公 司积 极进 行技 术研发 创 对最终 的产品质量造成 不利影响 。除此之外 ,由于该尾矿处理流
用 于磨 削轧 机工 作辊 和平 整机 工作辊 。每 台磨床 的 电气控 制系
收稿 日期 :2018-01 作者 简介 :刘金芝 ,女,生于 1981年 ,汉族,吉林通 化人,本科 ,中级工程 师 研 究方向 :电气 自动化。
图 2 闭 环 控 制 图
3.2.2 主 轴 驱 动 头架及 砂轮采用西 门子 1PH7型交流电机驱动 ,内装西 门子
以上 两方面 的要求 决定 了磨床 必须 做相应 的技 术改 进才能 跟 上轧钢技领 域不断快 速发展的步伐 。
1 轧 辊磨床概述
’
磨 床 是钢 材板 材轧 制生 产线 的重 要配 套设 备 ,其磨 削精度
和 磨 削效率 直接 影响 钢板 的轧 制质量 与 生产效 率 。轧辊 在钢板
轧 制过程 中 因高温 氧化和 机械 磨损等 原因会 导致 辊面几 何精度
的 精 密 加 工 。
交流伺服 单元采用 光 电编码器实现 位置检 测反馈 ,2500个脉 冲
/r。系统 最 小分 辨率 为 0.001mm/0.001。 ,保证 了系 统 的可 靠
2 CNC数控的基本概念
运 行。伺服驱动三个 控制回路如 图 2所示 。
CNC(计 算机数 字控制 )用于 的磨床 自动控 制 ,主要 功能是
辊筒模具超精密机床系统设计与工艺
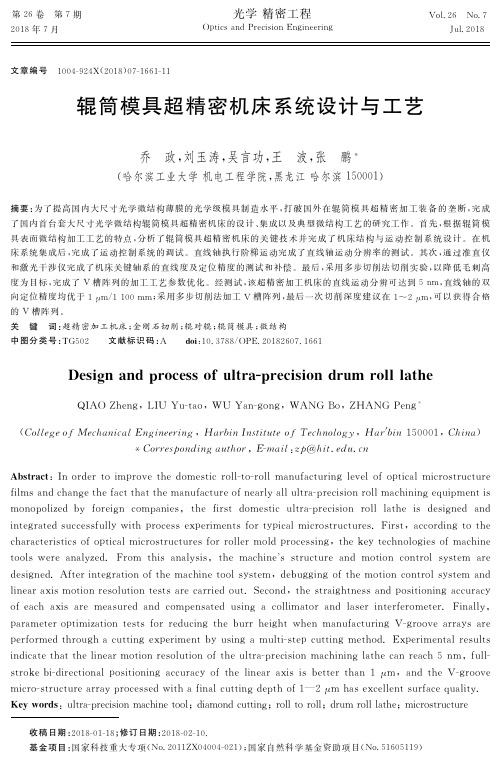
光学 精密工程
OpticsandPrecisionEngineering
Vol.26 No.7
Jul.2018
文 章 编 号 1004924X(2018)07166111
辊筒模具超精密机床系统设计与工艺
收 稿 日 期 :20180118;修 订 日 期 :20180210. 基 金 项 目 :国 家 科 技 重 大 专 项 (No.2011ZX04004021);国 家 自 然 科 学 基 金 资 助 项 目 (No.51605119)
1662
光学 精密工程
犃犫狊狋狉犪犮狋:Inordertoimprovethedomesticrolltorollmanufacturinglevelofopticalmicrostructure filmsandchangethefactthatthemanufactureofnearlyallultraprecisionrollmachiningequipmentis monopolized by foreign companies,thefirst domestic ultraprecision rolllatheis designed and integratedsuccessfullywithprocessexperimentsfortypicalmicrostructures.First,accordingtothe characteristicsofopticalmicrostructuresforrollermoldprocessing,thekeytechnologiesofmachine toolswereanalyzed.From thisanalysis,the machinesstructureand motioncontrolsystem are designed.Afterintegrationofthe machinetoolsystem,debuggingofthe motioncontrolsystem and linearaxismotionresolutiontestsarecarriedout.Second,thestraightnessandpositioningaccuracy ofeach axisare measuredandcompensated usingacollimatorandlaserinterferometer.Finally, parameteroptimizationtestsforreducingtheburrheightwhen manufacturing Vgroovearraysare performedthroughacuttingexperimentbyusinga multistepcutting method.Experimentalresults indicatethatthelinearmotionresolutionoftheultraprecision machininglathecanreach5nm,full strokebidirectionalpositioningaccuracyofthelinearaxisisbetterthan1μm,andthe Vgroove microstructurearrayprocessed withafinalcuttingdepthof1—2μm hasexcellentsurfacequality. 犓犲狔狑狅狉犱狊:ultraprecisionmachinetool;diamondcutting;rolltoroll;drumrolllathe;microstructure
浅谈如何提高数控轧辊磨床的磨削质量

浅谈如何提高数控轧辊磨床的磨削质量摘要:文章介绍了影响轧辊磨削质量的几个主要因素。
以数控轧辊磨床为对象,就磨床精度,砂轮,磨削用量及磨削冷却液等几个工艺问题进行研究论述。
关键词:轧辊磨床;精度;砂轮;进给速度数控轧辊磨床是钢材板材轧制生产线的重要配套设备,其磨削精度直接影响钢板的轧制质量。
目前,计算机数控技术与轧钢生产工艺不断提高,对轧辊磨床磨削的精度也随之提高:复杂的轧辊辊型,精确的轧辊形位公差要求,精密轧辊检测技术等。
为了获取更高的加工精度,提高磨削质量,除了磨工操作的水平高低外,还要考虑磨床自身的精度以及与轧辊相配用的砂轮、磨削用量、冷却液等的工艺性能。
本文从磨床精度、砂轮、磨削用量、磨削冷却液四个方面综合分析如何提高数控轧辊磨床的磨削质量。
1.磨床精度判别一台数控磨床等级最主要的标准就是其加工精度。
当一台数控磨床自身的制造精度成型后,我们只能从它的安装精度及数字化控制方面着手,进一步提升它的磨削精度。
1.1安装精度1.1.1.床身导轨的检测与调整数控磨床多数直接安装在混凝土地基上,并用垫铁调整其安装精度。
床身v形导轨安装检测后精度要求应满足:水平面内直线度≤0.01mm/m,垂直平面内直线≤0.01mm/m,接触点要求12~14点/25mm×25mm,对托板导轨的垂直度≤0.02mm/250m。
床身平面导轨安装检测后精度要求应满足:垂直平面内直线度≤0.01mm/m,接触点要求12~14点/25mm×25mm,对v形导轨的平行度≤0.02mm/m。
1.1.2.托板导轨的检测与调整托板v形导轨安装检测后精度要求必须满足:垂直平面内直线度在全部长度上≤0.01mm,接触点要求10~12点/25mm×25mm。
托板平面导轨安装检测后精度要求应满足:对v形导轨的平行度≤0.02mm/m,接触点要求10~12点/25mm×25mm。
精度的稳定性是一切质量优良的基础。
超精密加工技术论文

超精密加工技术论文超精密加工技术简介论文学校:XXXXX学院:XXXX班级:XXXXX专业:XXXXX姓名:XXXX学号:XXXX指导教师:XXX超精密加工技术一、概述超精密机械加工技术是现代机械制造业最主要的发展方向之一, 已成为在国际竞争中取得成功的关键技术。
这一方面是因为,尖端技术和国防工业的发展离不开精密和超精密加工技术, 当代精密工程、微细工程和纳米技术是现代制造技术的基础, 也是明天技术的基础。
另一方面很多新技术机电产品要提高加工精度, 这促使精密和超精密加工技术得到发展和推广, 提高了整个机械制造业的加工精度和技术水平,使机械产品的质量、性能和可靠性得到普遍的提高, 大大提高了产品的竞争力。
1、超精密加工的内涵超精密加工是一个十分广泛的领域,它包括了所有能使零件的形状、位置和尺寸精度达到微米和亚微米范围的机械加工方法。
精密和超精密加工只是一个相对的概念,其界限随时间的推移而不断变化。
在当今技术条件下,普通加工、精密加工、超精密加工的加工精度可以作如下的划分:1)、普通加工加工精度在1µm、表面粗糙度Ra 0.1µm以上的加工方法。
2)、精密加工加工精度在0.1-1µm、表面粗糙度Ra0.01-0.1µm之间的加工方法。
3)、超精密加工加工精度高于0.1µm、表面粗糙度小于Ra0.01µm的加工方法。
2、发展超精密加工技术的重要性现代机械制造业之所以要致力于提高加工精度,其主要原因在于:可提高产品的性能和质量,提高其稳定性和可靠性;促进产品的小型化;增强零件的互换性,提高装配生产率。
精密和超精密加工技术的发展,直接影响到一个国家尖端技术和国防工业的发展,因此世界各国对此都极为重视,投入很大力量进行研究开发,同时实行技术保密,控制关键加工技术及设备出口。
随着航空航天、高精密仪器仪表、惯导平台、光学和激光等技术的迅速发展和多领域的广泛应用,对各种高精度复杂零件、光学零件、高精度平面、曲面和复杂形状的加工需求日益迫切。
- 1、下载文档前请自行甄别文档内容的完整性,平台不提供额外的编辑、内容补充、找答案等附加服务。
- 2、"仅部分预览"的文档,不可在线预览部分如存在完整性等问题,可反馈申请退款(可完整预览的文档不适用该条件!)。
- 3、如文档侵犯您的权益,请联系客服反馈,我们会尽快为您处理(人工客服工作时间:9:00-18:30)。
超重型精密数控轧辊磨床的创新机加工艺【摘要】介绍了超重型数控轧辊磨床各关键件的机加工艺方法。
【关键词】超重型;高精度;轧辊磨床;机加工艺
重型数控精密轧辊磨床是大型轧机的母机制造装备及重型轧辊的精加工设备,一直依赖于进口,尤其是承载在100吨以上的超重型数控轧辊磨床为国外发达国家(德国、芬兰、日本)所垄断。
本机床的成功研制使百吨以上的轧辊国产化成为可能,填补国家在超重型轧辊精加工设备的空白,对于提升国产机床的技术附加值,具有战略意义。
一台机床的生产,特别是一台超重型、高精度机床的首次生产,更需要有合理的机加工艺方法来保证各种高精度零件的机械加工。
此台重型数控精密轧辊磨床的关键件有主轴箱体、尾座体、机床主轴、刀架床身、工件床身等,下面就对这些零件的加工工艺进行分析。
主轴箱体为机床主要传递扭矩的动力部件,是机床回转精度支承主体件。
该轧辊磨床为重型精密机床,因此主轴箱体的尺寸规格大、各孔系的精度要求高。
精加工主轴箱体的各孔系时必然要遇到调头镗的问题。
传统调头镗找正的方法无外乎通过检套、检棒找正,或者是利用基准面记录定位尺寸找正。
前者的找正方法中检套、检棒的加工误差会影响找正精度;后者的找正方法中基准面的加工误差同样会影响找正精度,并且母机的定位精度也会影响找正精度。
因本台机床的主轴箱体精度要求非常高,鉴于以上原因,如采用上
述找正方法无法实现零件的合格加工。
因此采用了创新的工艺方法:在加工主轴箱体各孔系的过程中利用激光跟踪仪临床配合检验各孔系的同轴度、平行度、孔距等精度(此时零件有加工余量),操作者根据激光跟踪仪临床检测数据,在进行切削加工(仍然留加工量),如此反复,直至各孔系精度达到要求。
此台机床的尾座体加工时也是利用激光跟踪仪来解决调头镗问题的,并且还用激光跟踪仪控制了尾座体主轴孔的抬头与勾头。
另外此台轧辊磨床的主轴箱体为开瓦式结构,为提高强度,主轴箱体前端配合一整体轴承座,但却因此多了一处配合环节,增加了加工难度。
如果主轴箱体的轴承座把合面在数控铣镗床上插补铣完成后就直接与轴承座把合,结合面容易下塞尺,因此需要刮研结合面。
传统有轴承座结构的重型机床中,机体与轴承座为定心套定位,轴承座外圆与机体内圆无须配合,有较大间隙,可以进行互研,但是此台轧辊磨床的主轴箱体与轴承座为h7/h6配合,无法进行互研,因此工艺设计了一套环形研具既可以刮研主轴箱体又可以刮研轴承座,以此来保证接触刚度和几何位置精度。
此台轧辊磨床的回转精度高达0.004mm,因此必须严格控制机床主轴的精度,该机床主轴的前后均为双列圆柱滚子轴承支承,工艺要求此处的轴承必须均准备一整套标准轴承及留有磨削加工量的
轴承内环。
主轴加工完成后,先按工艺要求组装标准轴承,卸下标准轴承的滚珠及外环,检测轴承内环外滚道的径向跳动,如果两轴承内环外滚道径向跳动<0.004mm,则合格;反之不合格,需要按照
工艺要求组装有留磨量的轴承内环,依据组装标准轴承时记录的数据对有留磨量的轴承内环进行磨削,使其径向跳动<0.004mm。
此台机床的刀架床身没有采用普遍使用的平导轨结构,而是采用了移动精度高,能自动补偿磨损的“v”型导轨结构。
根据机床加工规格的要求此台机床由4节床身拼接组成,因为床身的精度要求高,为保证零件精度必须在数控龙门导轨磨床上进行最后的磨削精加工,但由于受母机数控龙门导轨磨床加工零件规格的限制,一次只能磨削2节床身,由于床身采用的是“v”型导轨结构,那么怎样保证相拼接床身之间的尺寸一致性是机加的难点,最后通过增加一节工艺用短床身解决了这一问题。
工艺增加了一节与零件床身主体结构一致只是长度只有1米的短床身,在数控龙门导轨磨床上进行磨削加工时,先按照第一节床身、第二节床身、工艺用短床身的连接顺序一同磨削床身,然后按照工艺用短床身、第三节床身、第四节床身的顺序连接,按照已加工完的工艺用短床身进行控制相拼接床身之间的尺寸一致性。
此台机床的工件床身也没有采用普遍使用的平导轨结构,采用的是“山”型导轨,其加工方法同刀架床身的加工方法类似。
通过以上例子可以看出,合理的机加工艺方法对于零件的合格加工至关重要,也正因为采用了创新的机加工艺方法才使得我厂的超重型数控轧辊磨床得以成功研制。
[科]
【参考文献】
[1]于骏一,邹青.机械制造技术基础.机械工业出版社,
2003.
[2]张耀宸.机械加工工艺设计实用手册.航空工业出版社,1993.。