制程不良现象分析
制程不良TOP6分析

不良现象主要不良原因直接导致不良原因调整光模块失败无光BOSA NG/匹配U7性不好ESD静电击伤/来料
BOSA光纤折损拿取产品
BOSA管脚连锡焊接手法
光纤端面脏点纤
U7 NG ESD静电击伤/来料
U2000 NG ESD静电击伤/来料
误测操作手法
C3079与C944连锡仅针对R16小板焊接手法
语音测试失败Q2N损件拿取产品
Q2N NG ESD静电击伤/来料
Q1N 损件拿取产品
Q1N NG ESD静电击伤/来料电源灯不亮D14损件(灯体)拿取产品
C208连锡焊接手法
U2000 NG ESD静电击伤/来料
U2000空焊SMT来料
U2003 NG ESD静电击伤/来料LOS灯不亮D11损件(灯体)拿取产品
U2 NG ESD静电击伤/来料
U3 NG ESD静电击伤/来料调整光模块失败 ER BOSA NG来料
U7 NG ESD静电击伤/来料
误测操作手法
内纤压断光纤折损拿取产品
改善措施
宣导员工遵守ESD防静电规则,加强生产区域ESD防静电管理
宣导员工轻拿轻放产品,防止产品与任何物体碰撞、摩擦
加强焊接工序陪训,优化改善焊接夹具
宣导员工按要求点纤,品质部门加强监督
请SQE联系供应商提出改善对策,和防范对策,给出具体的改善方案。
并持跟踪后续质量表现情况。
加强测试工序员工培训,定期维护测试设备,优化改善测试流程加强焊接工序陪训,优化改善焊接夹具。
组装制程不良训练

•不到位 •灯不亮 •无波 •高翘 • 漏件、少件 •缝隙 • 错没将线材卡入槽内,嚴重時於線材会产生
產生断裂。 允收標準
将线材卡入槽内為允收,若發現即需重新组装。 影響性
线材容易断裂,会造成外壳组装有缝隙,并因此 会導致功能失效。
灯不亮
特點 按下按键后LED灯不亮。
制程控制要点(三)
•4.工艺文件,必须保证足够的适宜的工作文件可 以供生产和检验使用,且在相應的機種文件上標明 R控制要点。
•5.对于客户退回的产品的处理,应该保证其处理 的及时性,并且分析真因找出彻底解决办法。
•6.对于参与生产的相关人员,包括仓库,检验, 维修,重工,物料员等等人员,都必须进行生产 制程的相关培训,以保证都有足够的相关知识和 足够的认识。以保证对于制程的执行力度。培训 合格后必须进行相关的资格考核,考核合格者方 可上岗。
2.原材料来料不良、组装不当造成 補救處置 1.改善搬运、运输过程,增加防护措施(如: 加防震泡棉)。 2.严格按SOP操作,不产生错误动作。 3.来料不良则统计比率,并将数据报告给相关 部门要求改善。
制程控制要点(一)
•1.制程生产前进行全范围的检查,利 用一个制程检查清单保证每个制程涉 及点均已进行了清洁,隔离,标识等 动作,人员进行了相关培训。
THE END!
補救處置 1.立即将错误的零件更换为正确的。 2.培训教育员工增加自检正确率,按照“三不” 原则进行生产。 。 3.混料现象则统计比率,并将数据报告给相关 部门要求改善。
损件
特點 零件产生了破裂、断开等不良现象。
允收標準 产品零件无损坏现象为允收。
影響性 严重影响产品功能、性能、外观。
造成原因
1.搬运、运输过程造成碰撞。
制程不良的分析报告
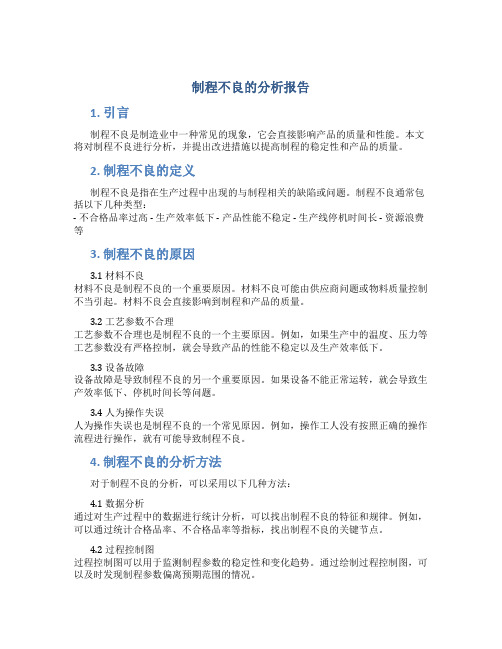
制程不良的分析报告1. 引言制程不良是制造业中一种常见的现象,它会直接影响产品的质量和性能。
本文将对制程不良进行分析,并提出改进措施以提高制程的稳定性和产品的质量。
2. 制程不良的定义制程不良是指在生产过程中出现的与制程相关的缺陷或问题。
制程不良通常包括以下几种类型:- 不合格品率过高 - 生产效率低下 - 产品性能不稳定 - 生产线停机时间长 - 资源浪费等3. 制程不良的原因3.1 材料不良材料不良是制程不良的一个重要原因。
材料不良可能由供应商问题或物料质量控制不当引起。
材料不良会直接影响到制程和产品的质量。
3.2 工艺参数不合理工艺参数不合理也是制程不良的一个主要原因。
例如,如果生产中的温度、压力等工艺参数没有严格控制,就会导致产品的性能不稳定以及生产效率低下。
3.3 设备故障设备故障是导致制程不良的另一个重要原因。
如果设备不能正常运转,就会导致生产效率低下、停机时间长等问题。
3.4 人为操作失误人为操作失误也是制程不良的一个常见原因。
例如,操作工人没有按照正确的操作流程进行操作,就有可能导致制程不良。
4. 制程不良的分析方法对于制程不良的分析,可以采用以下几种方法:4.1 数据分析通过对生产过程中的数据进行统计分析,可以找出制程不良的特征和规律。
例如,可以通过统计合格品率、不合格品率等指标,找出制程不良的关键节点。
4.2 过程控制图过程控制图可以用于监测制程参数的稳定性和变化趋势。
通过绘制过程控制图,可以及时发现制程参数偏离预期范围的情况。
4.3 原因分析对制程不良的原因进行分析,可以帮助我们找出问题的根源。
常见的原因分析方法包括5W1H法、鱼骨图、因果关系图等。
5. 制程不良的改进措施为了提高制程的稳定性和产品的质量,可以采取以下改进措施:5.1 加强材料质量控制合理选择供应商,并建立供应商质量管理体系,加强对采购材料的质量控制。
5.2 优化工艺参数通过对工艺参数的优化调整,确保制程参数在合理范围内,并加强对工艺参数的监控。
常见制程不良原因分1

常见制程不良原因分析任何一个变压器在生产过程中,难免有或多或少的问题,发生的原因可能牵涉到设计,材料,工法,作业人员的疏忽…….等等,致制程出一些不良品,仅就我们本厂生产进的产品做一简单的探讨分析.1.直流电阻(DCR)的问题A.DCR过低此种情形很少发生,造成可能的原因为:1.线径用大了2.规格订得不理想3.圈数不足4.用错骨架或DR CORE中径虽然大部份的SPEC在DCR部份订MAX,当然也有SPEC是±?%,对于MAX的规格,往往会疏忽注意,因此我们在寻拉过程中就要留意我们的电阻,尤其是多根线并绕时的电阻,实测值是不是与指示卡定的规格相差很远.例如:SC5726-001A型号N3(2.3-1)=0.35*3根﹐DCR SPEC=20 MAX 正常值=12.8断线1根后﹐DCR=19 .当遇到这样的情形的时候我们就要主动提出来要求工程收缩电阻范围.B.DCR过高发生的原因:1.线径用错2.拉力过大,把线拉细3.圈数太多4.以mm(日规)线径取代了A WG(美规)线5.铜皮引线焊点冷焊(包焊)6.温度过高.铜线的温度系数是0.0039/℃,一奥姆的电阻,温度每上升一度其电阻增加0.0039Ω.(一般大家可以接受的是25℃)2.电感(INDUCTANCE)的问题A.电感过高可能的原因1.圈数是否多了2.磁芯的选择是否错误3.GAP是否磨太浅4.磁芯来料本身的AL值过高5.客户订的规格是否合理6.没有GAP的磁芯组装含浸后电感一般不成线性略有上升7.高μi值的磁芯,如滤波器类受烘干凡立水的温度影响,一般均会降低.所以我们通常采用80-90℃烘干式或用自然阴干式.8.对于有GAP磁芯若电感高一点点,可用砂纸磨磁芯中柱一下,以调整电感值符合规格.B.电感低的原因1.圈数是否少了2.磁芯的选择是否错误3.GAP是否磨得太深4.磁芯来料本身的AL值是否太低5.客户订的规格是否合理7.仪器误差(我们厂一般以HP4284为准)8.磁芯接合处有异物9.层间短路或连锡10.另外一提的是同一对磁芯同一个线包,在夏天测试电感值比在冬天高,这是正常现象,因为磁芯的导磁系数随温度变化(省略图)11.有GAP磁芯电感低可以用细砂纸轻磨磁芯两边柱,以达到规定的电感值3.漏电感(LEAKAGE INDUCTANCE)1.未均匀疏绕2.排线重迭交叉3.铜皮未包紧,焊点大初级与次级绕组间,能量无法交连而减漏掉的能量,漏电感对电路上晶体(三极管)的伤害很大一般变压器都希望漏电感越小越好.为了降低漏电感,许多变压器都采用三明治绕法,即把初级圈分成二半:一半绕最里层,一半绕最外层,中间夹着次级圈,如此可使初次级更为接近,而降低漏电感.漏电感与绕组铜线的DCR值有关,短路时尽量用小电阻的短路导线.4. 圈数不良的问题A.真正的圈数不良在绕组中的某一组或以上圈数多或少,在测试中可以显示出来B.假性的圈数不良这是制程中很困扰的问题,其实它的圈数是正确的,但订定的规格的范围却超出了.TE输数据的范围是为了确保质量,变压器输出电压的稳定性.一般都有收缩范围.影响到圈数比测试超出百分比的原因:1.布线太乱2.同一层中有的布满幅宽,有的未布满3.GAP太深,感应不准确,影响到测试读值4.主绕组圈数太多时测试圈比值不稳定5.校正圈比是否为不良时,用没有GAP的磁芯较准确5. 短路的问题变压器在测量电感时发现非常低,接近漏电感值时,应检查是否短路,其中一个绕组短路(内部短路,或引出线PIN间连锡短路)或是让人最为头痛的铜皮短路.6 耐压不良的问题HI-POT测试是变压器必须100%全测的要求造成HI-POT不良的原因:1.二绕组之间引出线碰触或太近2.PIN与PIN间锡渣造成3.挡墙太窄或绕在线挡墙4.绝缘胶布未完全覆盖或层数太少5.绕组间的空间距离不足6.PIN间助焊剂残留造成绝缘不足以承受HI-POT高压7.四侧端引出线与磁芯间距离不足8.距离不足电弧(ARCING)引发HI-POT10.漆包线来料有针孔11.三层绝缘线在制程中破皮12.铜皮反包胶纸破损HI-POT测试目前大家习惯于规格上的一分钟电压值*1.2倍变成一秒钟.例如:3000V 1mA 1MIN变成3600V 1mA 1SEC漏电流越小,测试规格越严格,当规格上要求电流为3mA时不要用2mA或1mA去测试,2mA比3mA要严格,不要弄错7. 层间不良一般一个绕组有几层,但没有包层间绝缘胶纸的情况下.或者有绕组铜皮的情况下才会测试层间绝缘.1.铜皮反包胶纸破损.导致短路2.铜线破皮(0210)《古代散文》复习思考题一、填空题1.甲骨卜辞、和《易经》中的卦、爻辞是我国古代散文的萌芽。
最新smt制程不良原因及改善措施分析ppt课件
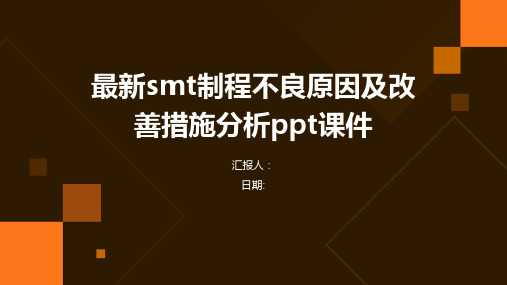
汇报人: 日期:
目录
• SMT制程概述 • SMT制程不良原因分析 • SMT制程改善措施分析 • 案例分析与实施效果评估
01
SMT制程概述
SMT制程简介
表面组装技术
SMT是表面组装技术(Surface Mounted Technology)的缩写,是一种将电 子元件直接安装在印刷电路板(PCB)表面的技术。
降低成本
SMT技术提高了生产效率 ,降低了生产成本,使得 电子产品更加普及和个性 化。
SMT制程常见问题
锡膏印刷问题:锡膏印刷是SMT制程中的关键步 骤之一,常见问题包括锡膏量不足、偏移、桥接 等,影响焊接质量。
焊接问题:焊接过程中可能出现虚焊、冷焊、焊 接不良等问题,主要原因包括温度设置不当、焊 接时间不足、PCB污染等。
元件贴装问题:元件贴装过程中可能出现元件偏 移、翻转、损坏等问题,主要原因包括设备参数 设置不当、元件供料器故障等。
针对以上问题,我们将详细介绍不良原因分析及 改善措施,以提高SMT制程的良率和生产效率。
01
SMT制程不良原因分析
设备故障导致的不良
设备老化
长时间运行的设备可能出 现磨损和老化,导致定位 不准、传输错误等不良现 象。
维护不足
设备缺乏定期维护和保养 ,可能导致精度下降、故 障率增加。
操作不当
操作人员对设备不熟悉或 操作不规范,可能引发误 操作,造成产品不良。
材料问题导致的不良
原材料缺陷
原材料本身存在缺陷,如PCB 板翘曲、元器件引脚氧化等,
影响制程质量。
储存条件不当
材料储存环境湿度过高、温度过高 或过低可能导致材料性能发生变化 。
smt制程不良原因及改善措施

03 员工技能水平参差不齐,操作不规范,导致不良 品率上升。
展望未来发展趋势并提出应对策略建议
未来SMT制程将朝着高 精度、高效率、高自动
化方向发展。
01
加强原材料质量管控, 确保产品品质稳定。
03
建立完善的品质管理体 系,加强品质监控和数 据分析,及时发现并解
决问题。
05
建议企业加大设备投入 ,引进先进技术和设备
,提高制程效率。
02
定期对员工进行技能培 训和操作规范教育,提
高员工技能水平。
04
THANKS
谢谢您的观看
案例背景介绍
01
某SMT生产线在生产过程中出现 多种制程不良,如焊点不良、元 件偏移等,导致产品良品率下降 。
02
生产线面临生产压力大、交期紧 张等挑战,急需解决制程不良问 题。
原因分析及定位关键问题
对生产线上的各个环节进行详细分析 ,找出可能造成制程不良的原因,如 设备老化、操作不规范、物料问题等 。
建立原材料库存管理制度
对原材料进行分类管理,建立合理的库存管理制度,避免原材料积 压和浪费。
加强设备维护与保养
制定设备维护计划
01
根据设备的使用情况和生产需求,制定合理的设备维护计划,
包括定期检查、保养、维修等。
提高设备维护水平
02
加强设备维护人员的培训和管理,提高设备维护水平,确保设
备的正常运行。
smt制程不良原因及改善措施
汇报人: 2023-12-19
目录
• SMT制程简介 • SMT制程不良原因分析 • SMT制程改善措施探讨 • 案例分享:成功改善SMT制
程不良的实践经验 • 总结与展望:未来SMT制程
SMT制程不良原因及改善对策

SMT制程不良原因及改善对策SMT制程(Surface Mount Technology)是一种常用的电子组装技术,广泛应用于电子产品的制造过程中。
然而,由于各种原因所引起的不良现象在SMT制程中时有发生。
本文将讨论SMT制程不良原因以及改善对策。
1.焊接不良:焊接不良可以导致焊点虚焊、焊接断裂等问题。
常见的原因包括焊接温度不够、焊接时间不足、焊接设备不稳定等。
改善对策包括提高焊接设备的质量和稳定性、增加焊接温度和时间的控制精度等。
2.贴装不良:贴装不良可以导致元件偏移、元件漏贴等问题。
常见的原因包括贴装位置错误、贴装头磨损、胶垫损坏等。
改善对策包括提高贴装机的精度和稳定性、定期更换贴装头和胶垫等。
3.元件损坏:元件在SMT制程中容易受到机械损伤、电静电等因素的影响而受损。
改善对策包括提供合适的防护措施,如使用防静电设备、增加元件存储和运输的保护等。
4.焊盘不良:焊盘不良可以导致焊点接触不良、导致电路连通性问题。
常见的原因包括锡膏质量不佳、焊盘形状不准确等。
改善对策包括使用高质量的锡膏、提高焊盘生产过程的精度等。
5.引脚弯曲:引脚弯曲会导致元件无法正确插入或连接。
常见的原因包括元件存储和运输过程中引脚受到碰撞、搬运过程中的不当操作等。
改善对策包括提供合适的存储和运输保护措施、培训操作人员正确操作等。
改善SMT制程不良有很多对策,下面列举了其中一些常见的:1.提高设备的质量和稳定性:定期对设备进行维护和保养,确保其正常运行和精度稳定。
采用高质量的设备和工具,可大大降低不良率。
2.优化工艺参数:根据产品要求和设备特性,合理的调整焊接温度、焊接时间等工艺参数,以确保焊接效果和质量。
3.加强员工培训:提供必要的培训和指导,使操作人员熟悉SMT制程的原理和操作技巧,减少人为失误和操作不当导致的不良。
4.严格品质管理:建立完善的品质管理体系,包括设备校验、材料检测、过程控制等环节,确保产品质量稳定。
5.提供合适的存储和运输保护:对元件进行正确的存储和运输保护,避免机械损伤、静电损伤等因素导致的元件损坏。
制程不良原因分析及改善08.01.31
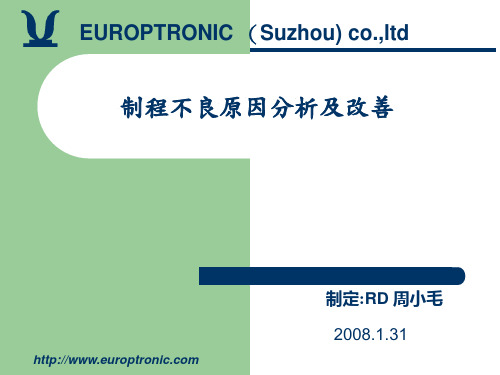
Page16
Thank you!
Page17
Page4
有感产品生产流程
卷取 排板 压型 LQC 滴油
外检
打印
分选
烘烤
包封
T/P
FQC
包装/PQC
Page5
金属化/无感产品生产流程
卷取 压型 包纸 喷金 清除 LQC
外检
打印
烘烤
包封
滴油
焊接
电检
加工成形
FQC
包装/PQC
Page10
4)内涂素子垂漆 原因:a)不素子下降速度快 b)内漆配比异常 c)环氧树脂过期(主剂、固化剂、稀释剂) 5)产品露白 原因: a)素子滴油位调整不当 b)素子高低不平
Page11
有感产品电性不良 1)产品容量不良(CAP) 原因:a)电极相对位置蛇形变化 b)参数给定异常(容量升值差异) c)不同原材料批号相混 d)不同机台产品相混 2)产品耐压不良(TV) 原因: a)点焊电流,毛刺 b)外封受损 c)点焊导线倒勾 d)电极与介质间相对位置安全距离不足
Page2
一、制程不良类别定义
制程不良从产品型式上分两大类: 1)产品制造过程外观不良。(超出管理标准) 2)产品制造过程电容不良。(超出管理标准) 制程不良从发生型式分为: 1)人为因素造成的不良 2)材料因素造成的不良 3)机器因素造成的不良 4)操作方法造成的不良 5)环境因素造成的不良
Page15
六、改善措施的成效追踪评估
QC根据相关部门提出的原因分析及改善对策进行效果追 踪确认。 追踪效果确认方法: 1)改善前攺善后数据比较(数据统计) 2)问题点结案 3)更改作业文件及作业方法
SMT制程不良原因及改善对策

PAD 离轨道边小 于3mm.
PAD氧化
未及时收板,PCB在回焊 炉中碰撞
零件过大过重
零件脚弯
人为手抹锡膏
零件厚度不均
备料时料带过紧
零件氧化
手放散料
异形零件
空气流通速度过快
手推撞板
焊盘上有异物
室温过高 锡膏印刷后硬化
PCB印刷后露置 空气中过久
人为手拨 缺锡
手摆料
PAD间距与组 件长度不符
零件与PAD不符
PCB
通风不畅
室内过于潮湿
温度高
手推撞板
零件
手碰零件
旧
超过
手放散料 缺乏教育训练
新工上线 缺乏责任感
反 破过 向 损周
期
锡 不 搅 使用 锡粉径 膏 均 拌 时间 粒过大
锡 膏
将锡膏加到钢网开口处
锡膏厚 短路
手印锡膏
有异 含 松 物 量香
锡 有锡 膏 水膏
手抹锡膏
印 手印台
零件间距离太近
稀 份内
钢网贴纸未贴好 手拨零件
(3) WHERE——何处?在哪里做?从 哪里入手?
(4) WHEN——何时?什么时间完成? 什么时机最适宜?
(5) WHO——谁?由谁来承担?谁来 完成?谁负责?
(6) HOW ——怎么做?如何提高效率? 如何实施?方法怎样?
(7) HOW MUCH——多少?做到什么 程度?数量如何?质量水平如何?费用产 出如何?
发明者用五个以w开头的英语单词和两 个以H开头的英语单词进行设问,发现解 决问题的线索,寻找发明 5W2H分析法思 路,进行设计构思,从而搞出新的发明项 目,这就叫做5W2H法。
(1) WHY——为什么?为什么要这么做? 理由何在?原因是什么?造成这样的结果 为什么?
pcb制程常见不良及分析技术
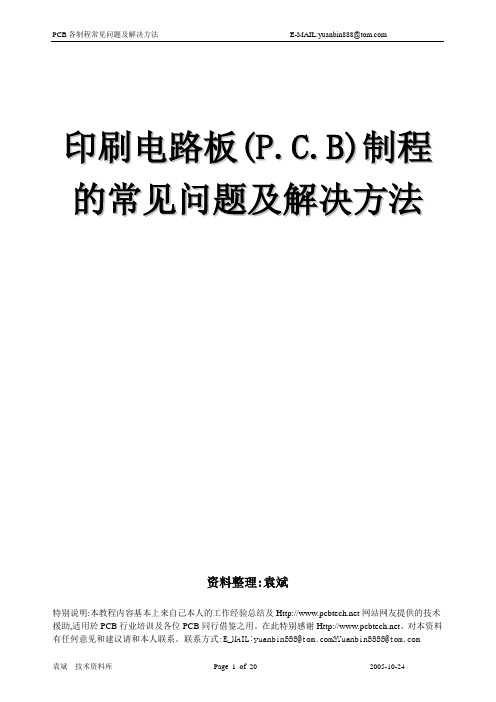
印刷电路板(P.C.B)制程的常见问题及解决方法
资料整理:袁斌
特别说明:本教程内容基本上来自己本人的工作经验总结及网站网友提供的技术援助,适用於PCB行业培训及各位PCB同行借鉴之用。
在此特别感谢。
对本资料有任何意见和建议请和本人联系。
联系方式:E_MAIL:******************&*******************
目录:
(一)图形转移工艺 (2)
(二)线路油墨工艺 (4)
(三)感光绿油工艺 (5)
(四)碳膜工艺 (7)
(五)银浆贯孔工艺 (8)
(六)沉铜(PTH)工艺 (9)
(七)电铜工艺 (11)
(八)电镍工艺 (12)
(九)电金工艺 (13)
(十)电锡工艺 (14)
(十一)蚀刻工艺 (15)
(十二)有机保焊膜工艺 (15)
(十三)喷锡(热风整平)艺 (16)
(十四)压合工艺 (17)
(十五)图形转移工艺流程及原理 (20)
(十六)图形转移过程的控制 (24)
(十七)破孔问题的探讨 (28)
(十八)软性电路板基础 (33)
(十九)渗镀问题的解决方法 (38)。
制程不良现象分析

21)层压机未及时抽空(加压过程挤不出);2)真空泵问题,或硅胶板破、硅胶条不严密导致;真空度或压力不够;3)来料不良,例如EVA含有水分子;空气被密封在EVA胶膜内;4)EVA裁剪后,放置时间过长,它已吸潮;5)层压时间过长或温度过高,使有机过氧化物分解,产出氧气;1)层压人员随时检查真空表显示值,要有预防措施;2)维护真空泵的同时,对硅胶板的使用寿命要严格控制;3)注意EVA放置的周围环境和使用时间;4)延长真空时间 检查层压机的密封圈检查真空度和抽气速率;5)检查抽气速度 加快硅胶板下压速度 降低层压温度 ,使用表面压花的EVA膜 检查加热板温度 ;人员、反光检验及层压员也可能造成);2)来料不良,或过程中掉至,(由于EVA、背板、小车子有静电的存在,把飘在空气中的头发,灰尘及一些小垃圾吸到表面);的材料有质检意识;2)反光检验员提高质检意识,仔细,负责任的检验,重中之重;3)做好6S管理,保持周边工作环境的整太阳能组件生产过程主要不良现象造成的原因及纠正措施(以下图片仅仅是一种不良现象代表)1不良图片不良原因纠正措施1)提高来料质检的力度和方法;2)对串焊台及时清理。
包括单焊人员的质量意识(同时控制焊接手势);3)对层压机的维护,提高加压阶段的稳定性;4)对新员工的培训,包括盖层压布的手势并对现场指导为主;1)电池片本身质量,隐裂所致(暗伤)加上EVA的流动性;2)焊珠顶破或者焊锡堆积过厚;3)层压机加压阶段压力大导致;4)EVA不平整(鼓包现象严重);5)层压人员盖层压布布手势不正确;6)单串焊手势过重致使造成;未按工艺要求(离起焊点绝缘边3-4mm);裂片气泡1)单焊人员焊接速度过快,及辅焊带手势不对;2)焊带规格与电池片主栅线不匹配,容易露白;虚焊导致(层压后);3)新员工不知,更加容易造成;1)通过培训加强新老员工的焊接手势及质量意识,对其问题引起重视;焊问题的产生;31)主要原因帽子佩戴不严密(主要集中排版人员、反光检验及层压员也可能造成);2)来料不良,或过程中掉至,(由于EVA、背板、小车子有静电的存在,把飘在空气中的头发,灰尘及一些小垃圾吸到表面);1)确保佩戴帽子严密,同时要对所用到的材料有质检意识;2)反光检验员提高质检意识,仔细,负责任的检验,重中之重;3)做好6S管理,保持周边工作环境的整洁,并勤洗衣裤做好个人卫生;41)排版人员不经意将残留焊条溅进,(往往是手套毛丝钩进导致,剪的过程飞入);2)剪多余焊带时未一刀剪下,多次剪所致;3)拿第一张EVA碰到排版桌边的PET,其粘在EVA上;非排版人员帮贴PET过程碰到桌上的PET致其渐入组件内;1)对剪下的残留焊带要一一放入盒子,统一回收,切忌,养成习惯性动作!!!保持排版台的干净整齐;2)反光检验员得仔细,做到心中有数!3)改善焊带长度;4)排版人员拿EVA要养成良好的手势,勿使EVA接触PET;51)单焊时,重复焊接导致焊锡堆积(焊锡丝过量),串焊过程致使焊锡溅出;单焊造成焊锡黏在单片上;2)串焊盒未清理干净,有焊锡,致排版过程掉入;1)保重焊接手势正确,勿重复焊接,确保一次性拉到位;多其过程出现的焊锡及时清理,保证焊接台面的整洁;2)时刻擦洗串焊磨具台和串焊盒,预防焊锡、焊渣等调入;3)反光检验要认真检查,尤其是头尾焊锡,易造成短路;露白发焊条/焊屑/PET焊锡1)排版人员漏剪导致,尤其是上下班时更易造成(其容易导致短路);1)要对剪焊带有个习惯,一定的顺序,并把一一剪下的放置回收盒中,对每次剪完后要自检一次;2)反光检验更要认真负责,有条理的检查;101)EVA含有杂质,未融化小颗粒;2)层压前有杂物掉进EVA上(小虫子等);3)单串焊手套脏(含有助焊剂的残留物);1)裁剪员,排版人员要提高质检意识,对过程中不良的及时予以拿出(蚊子等);2)当天的板子尽早层压完,加强车间的防虫管理,及密封性,保持车间整洁;111)EVA收缩导致;2)排版人员未测量间距致使不足;1)加强EVA收缩的实验,同时提高准确性,即时去供应商取得联系;2)要用2mm对其使用,不能目测了事;9杂物气泡互连条未剪串间距不足12131)排版人员漏剪导致,尤其是上下班更易出错;1)要对剪焊带有个习惯,一定的顺序(从左往右),对每次剪完后要自觉检查一次 ;2)反光检验要认真负责,有条理的检查;3)更改汇流条设计尺寸,最合理化;141)排版人员未控制汇间距(PET贴的过紧);2)EVA收缩导致间距不足;1)利用黄蜡板的间距,一一焊接;2)汇流条间更改PET贴法的工艺;3)移上下距离时重新检验一遍;4)反光检验要认真负责,有条理的检查;151)分选人员存在颜色误区(应区分单片的浅、中、深);2)更换一道中的不良单片导致其中一片存在色差;3)单焊人员色差意识低导致;4)修复人员更换单片容易造成色差;1)分选人员严格把控色差,统一分类;2)对更换不良单片要说明色差情况;3)单串焊人员要有自检意识,杜绝色差流入下道工序;4)反光检验人员要仔细检查,对色差及时反馈与改组;5)修复人员返修前要查看其色差问题;剪汇流条未剪色差汇流条间距16171)反光检验处汇流条划痕;2)割边过程拿刀手势不正确导致;3)装框过程角码掉落;4)清理背面胶过程刀片划至;5)裁剪过程刀片划伤及排版过程刀片划至;1)反光检验台上有随工单遮住汇流条引出端;2)对新员工的培训及组长的指导;3)清理过程要求品质意识,注意拿刀片的手势;4)裁剪背板时要时刻注意拿刀方向;181)EVA与玻璃间脱层,原因①EVA问题(粘结剂不足)②玻璃含有油污,灰尘等1)首先品质过程巡检及工艺员要有敏感有必要对层压后抽检;2)强化对EVA实验,尽量细化,及时反馈与供应商;1)条形码受潮;2)层压机加热板温度过高;1)保证条形码储存在干燥的环境,或提前几天打印;2)层压后有层压员负责对其擦洗(橡皮、酒精);背板剥离强度不合格条码糊211)焊接手势过重导致缺角;或焊接工艺不达标(起收点间距未控制好);2)排版人员剪汇流条过急碰到单片,易造成缺角;1)通过培训提高焊接工艺要求;2)在排版过程时拿电池串要稳拿稳放;剪汇流条时要细心,力道不要太大;1)焊带、电池片及助焊剂不匹配;1)对每批次电池片工艺员要确认焊带、电池片及助焊剂的匹配性;3)控制标准的焊接环境温湿度;19201)焊台电烙铁温度设置偏高;2)焊接时间过长;3)黄蜡板孔未对住;1)定时对其焊台温度的抽检;2)对黄蜡板的工艺技术改善;3)通过培训指导,注重焊斑的严重性;4)层压后检验员及时与改组反馈问题;1)绝缘层开口裁斜;2)排版人员未对其拉到位;1)保证开口完好的情况下,排版人员要对其拉到位,同时自检;2)检验员对其监督反馈;焊斑绝缘层未放到位缺角虚焊1)来料存在问题;2)过程中撞击所致或划到装框机进刀口;3)清理过程刀片划至;1)操作人员要对使用材料有自检的能力;2)装框过程要注意手势,时常查看装框后的效果;242)焊接手势及焊接速度过快;3)环境温度过高,容易造成虚焊;2)通过培训提高焊接手势及焊接时间要求;3)控制标准的焊接环境温湿度;1)长短边来料存在尺寸上的误差;2)装框机气源不足;1)来料不良导致;2)修边或装框过程与桌面硬物接触划至;3)清理正面过程刀片使用不当(过重);1)对其半成品接触的桌面采取保护措施(垫上橡胶布);2)通过培训提高清理人员的质量意识;22231)来料要加强的同时,操作人员要对使用材料有自检的能力;2)装框要有一个准备的工作,确保装框机正常运行;间距过大铝边框碰焊玻璃划伤253)清理过程刀片划至;3)抬组件时要拿稳,勿大手大脚 ;4)清理时用刀片要仔细;1)装线盒时,未对残留胶带清理干净;1)撕胶带时,容易抠起汇条至折弯;2)盖上层压布不小心导致扭曲;1)层压人员盖上层压布过程要边盖边检查(尤其是新员工) ;2)装线盒时要认真对待,巧取;271)背板上有未固化的硅胶,装线盒过程于其接触导致;1)尽量保证背板上不留多余硅胶;2)清理过程要一一检查线盒及引出线上的硅胶,确保不流入客户手中;1)对其胶带的更改(美纹纸),容易撕起;2)通过培训提高操作人员要品质意识;2826框碰伤引出线内打折引出线有硅胶引出线有残留焊带1)贴标签的手势不对,导致空气进入,引起气泡;1)贴的方向一定要顺手;确保平整,并用手抚平;291)电池片整体移位,导致条形码背铝边框遮住;2)电池片移位(背板)导致铝边框上下间距不足;1)层压前要控制其电池片上下的距离,认真对待每次层压前的距离测量,减少后道不必要的麻烦;2)盖上层压布要确保一次盖到位;1)线盒硅胶打的不均匀;2)安装线盒不够用力,未均匀的挤出,容易导致线盒脱落现象;1)打胶要符合线盒胶的工艺要求,保证均匀溢出 ;2)安装线盒时要有自检意识,不足之处及时补胶;3)成品检验要一一检查;3130背板/电池移位接线盒一角无硅胶标签内有气泡暗341)单焊过程要控制焊接工艺,尤其焊接温度,焊接手势;1)通过培训提高员工的质量意识,并现场监督焊接要求是否符合工艺要求;1)电池片本身质量,隐裂所致(暗伤)加上EVA的流动性;2)焊珠顶破或者焊锡堆积过厚;3)层压机加压阶段压力大导致;4)EVA不平整(鼓包现象严重);(离起焊点绝缘边3-4mm);1)提高来料质检的力度和方法;2)对串焊台及时清理。
PCB各制程不良分析手册
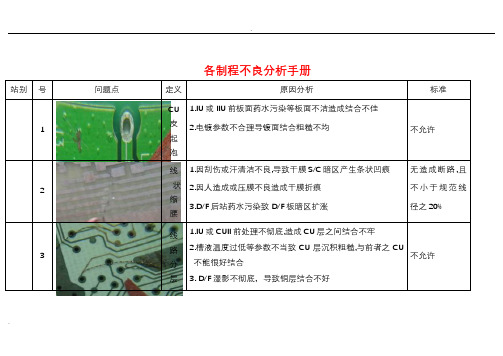
各制程不良分析手册站别号问题点定义原因分析标准1 CU皮起泡1.IU或IIU前板面药水污染等板面不洁造成结合不佳2.电镀参数不合理导镀面结合粗糙不均不允许2 线状缩腰1.因刮伤或汗清洁不良,导致干膜S/C暗区产生条状凹痕2.因人造成或压膜不良造成干膜折痕3.D/F后站药水污染致D/F板暗区扩涨无造成断路,且不小于规范线径之20%3 线路分层1.IU或CUII前处理不彻底,造成CU层之间结合不牢2.槽液温度过低等参数不当致CU层沉积粗糙,与前者之CU不能很好结合3. D/F湿影不彻底,导致铜层结合不好不允许.4 蚀刻不尽1.蚀刻参数未管控好2.流锡或剥膜不尽3.IU或IIU前干膜掉落(刮落或与板面结合不牢)4.干膜前板面沾胶线路间不超过规范线径之20%,且未造成短路电镀5线路分层1.IU或CUII前处理不彻底,造成CU面结合不牢2.槽液温度过低等参数不当致CU层沉积粗糙,与前者之CU不能很好结合3.D/F湿影不彻底,导致铜层结合不好不允许6脏点短路1.干膜底片未清洁净,导致其明区沾污部分未被曝光固化,即此线距部分会被镀上CU及sn/pb而造成短路不允许.7 CU面凹陷1.基材本身有针点凹陷不良(检查基板表面)2.压合时CU皮表面沾尘或PP质量不良造成压合后此瑕玼3.电镀铜时因槽液特别是光泽剂不正常导致CU积不良。
(2.3.可通过做切片观查,以作为参考)A手指不允许,板面每点不大于20mil,不超过板厚的1/58 CU面残缺1.D/F沾膜,撕膜不净,导致蚀刻时被蚀掉2.板面沾胶或沾药水导致CU面无锡层保护层3.电镀部分喷嘴坏损造成局部过蚀4.板面镀锡层被刮伤大铜面每点不大于20mil,每面只允许1点,其它地方不允许电镀9 短路1.干膜S/C未清洁净,致其明区沾污部分未被曝光固化,即此线距部分会被镀上CU及sn/pb而造成短路2.外层干膜刮伤,导致镀上锡层而造成短路不允许.加工10孔内塞SN1.喷锡时风刀塞SN,浸锡时间不够等参作业参数不合理2.孔内有毛刺其它杂物造成孔塞3.L/Q塞墨孔内积墨或塞墨不良喷锡板导通孔塞锡不高出板面可允收;零件孔塞锡不允收;A手指附近15mm内导通孔塞锡不允收11孔边锡高1.喷锡前孔边CU面不洁,造成CU/SN结合力小于SN/PB内聚力2.前后风刀间距过大,,造成一面之锡被回吹3.风刀距轨道间距过大,风量扫锡整平力不够4.浸锡时间不足等参数不良锡厚40U″-1000 U″,且锡面上无毛尖状颗粒状突加12 锡面凹坑1.喷锡前CU不洁或CU面不平整2.锡铅不纯或空气内含有杂物3.风刀不良1.不影响焊锡性和锡厚(40U″-1000 U″).工13 板面树脂1.L/Q显影时绿油未彻底去除干净,致化A时药液沉积不上不允许14 A面花斑1.化A前CU面不洁2.NI槽NI含量不足等参数不合理;NI槽污染3.摇摆动作不到位不允许15 架锡桥1.喷锡前板面有不洁2.锡铅内或空气中含有杂质3.风刀不良不允许16 板面沾锡1.喷锡前因防焊漏印或CU面防焊被刮掉,致露出CU面,在此HAL时露CU部分被喷上锡线路上不允并列存在;大铜面每面不超过3个点,每点不大于10mil.加工17A手指针孔1.前站CU面有凹坑2.镀A时电流密度过大,致NI/A沉积时粗糙不平整3.镀A地槽液含量不当或受污染每点不超过10mil,每排不超过3个点,18A面手印1.化A前CU面不洁2.NI槽NI含量不足等参数不合理;NI槽污染3.摇摆动作不到位(此现象一般为手印所致)不允许19锡面锡高1.喷锡前板面有不洁2.锡铅内或空气中含有杂质3.风刀不良(此板有造成锡面粗糙)锡厚40U″-1000 U″,锡面不允许有颗粒状或毛尖20锡高不良1.喷锡前板面有不洁2.锡铅内或空气中含有杂质3.风刀不良锡厚40U″-1000 U″,锡面不允许有颗粒状或毛尖.加工21PAD锡高1.喷锡前板面有不洁2.喷锡时风压小/风刀间距不对等制作参数不佳锡厚40U″-1000 U″,锡面不允许有颗粒状或毛尖湿膜2防焊露CU1.棕片不良2.挡点偏移或过大3.印刷后碰及板面未干之油墨4.网版不洁致漏墨不良每点≤10mil,每面不超过3点23防焊异物1.印刷前板面有脏物2.板面沾干油墨每点≤10mil,每面不超过3点,且无明显色差.24 刮伤露铜1.印刷防焊后因人为操作不当造成板面之防焊被刮掉而露CU 每点≤10mil,每面不超过3点湿膜25织纹显露1.L/Q退洗时间长2.基板质量问题3.压合不良基材上无明显白点白斑,经热冲击试验不会造成分层起泡26板面积墨1.该处电镀镀铜较厚,致印刷时下墨不良2.刮刀不平整3.网版高度等参数不合理4.网版漏墨不均不会造成色为准27防焊侧蚀1.油墨质量不行2.显影槽液对CU漆界面处之油墨攻击过度3.防焊重工次数过多1.线路上不允许2.PAD边缘不超过10mil.湿膜28防焊侧蚀1.油墨质量不行2.显影槽液对CU漆界面处之油墨攻击过度3.防焊重工次数过多1.线路上不允许2.PAD边缘不超过10mil29孔边起泡1.有污染或前处理刷磨时水气未烤干2.孔边积墨致油墨较厚,致不能均一固化3.L/Q烘烤条件不当,热固化不均每点不超过3点,每点不超过10mil,3M撕胶防焊不脱落30板面漏印1. 印刷时因网版未清洁尽或网版脏点或干油墨致印一下2.刮刀不平整3.电镀镀铜不均4.设PIN不平致不能规范作业每点不超过3点,每点不超过10mil.31 板面脏污1.印防焊后因人为操作不当使防焊表面沾上油脂或其它物质不破坏防焊且不影响客户防焊颜色之要求湿膜32对偏阴影1.因棕片对偏致使沾在CU面上之防焊被曝光而不能被显影掉(PAD阴影)2.因印刷后静置时间过长或烘烤时间过长或烤箱未保养好造成(主要为孔边阴影)PAD阴影部分不超过本身宽度1/8,SMT允许1mil,光学点允许2mil33孔边露CU1.网版挡点偏移或过大或作业过程中有变形不良≤2mil34防焊阴影1.因棕片对偏致使沾在CU面上之防焊被曝光而不能被显影掉(PAD阴影)2.因印刷后静置时间过长或烘烤时间过长或烤箱未保养好造成(主要为孔边阴影)PAD阴影部分不超过本身宽度1/8,SMT允许1mil,光学点允许2mil.35 孔边起泡1.有污染或前处理刷磨时水气未烤干2.孔边积墨致油墨较厚,致不能均一固化3.L/Q烘烤条件不当,热固化不均每点不超过3点,每点不超过10mil,3M撕胶防焊不脱落湿膜36孔边起泡1.一般为印板过程中有滴到防白水等外物造成防焊色差每点不超过3点,每点不超过10mil,3M撕胶防焊不脱落37防焊起泡1.有污染或前处理刷磨时水气未烤干2.孔边积墨致油墨较厚,致不能均一固化3.L/Q烘烤条件不当,热固化不均每点不超过3点,每点不超过10mil,3M撕胶防焊不脱落.38 板面脏污1.一般为印板过程中有滴到防白水等外物造成防焊色差不允收39 孔内积墨1.印刷时刮刀压力过大,致下墨过大,挤入孔内2.如孔过小在作业中也易产生此不良3.以上为空网印刷时产生零件孔不允收;导通孔每面不超过3个孔;卡板A手指15mm内不允许;其它无明确定义文字40沾文字漆1.网版未调正导致印偏沾漆2.A/W文字划线条太靠近CU PAD3.网片破损不允许41文字印偏1.网版未调正2.PIN针套错或没套好3.定位PIN孔钻偏PAD部分不超过本身宽度1/8,SMT允许1mil.42 文字漏印1.制作中覆墨不良2.刮刀未研磨好不锋利3.印刷时用力不够不允许43 文字印反印刷时人为误操作导致套PIN套反不允许文字44文字印反印刷时人为误操作导致套PIN套反不允许45文字漏印1.制作中覆墨不良2.刮刀未研磨好不锋利3.印刷时用力不不允许.46 沾文字漆1.机台上有油墨沾在板面2.印刷手手上沾有油墨并反沾于板面3.网版有破洞造成感光膜脱落不允许47 文字积墨1.油墨粘度过小,下墨不均2.覆墨时间太长3.印刷架网高度过低以清晰可认为准文字48文字沾漆1.网版未调正导致印偏沾漆2.A/W文字划线条太靠近CU PAD3.网片破损不允许49文字漏印1.网版显影不尽或油墨太干致下墨不良2.覆墨不良或印板时用力不均3.刮刀不锋利不允许.50 文字阴影1.多次印刷或吸纸不当2.网版未抬起覆墨或网版反面有残墨3.板弯板翘PAD部分不超过本身宽度1/8,SMT允许1mil51 文字印倒1.套PIN套错误不允许5253文字52文字脱落1.油墨质量差,结合力不强2.烘烤时间或温度不当,致文字固化不够3.板面油烟等不洁物造成文字与板面结合力不强不允许.53 文字重影1.印刷时有多次重印2.网版未调正或上PIN不牢3.重印时上PIN偏移未与网版对正不允许54 文字印偏1.网版未调正2. PIN未套正3.PIN孔偏移PAD部分不超过本身宽度1/8,SMT允许1mil55 沾文字漆1.机台上沾有油漆或手上沾漆2.脏点沾漆或刮伤沾漆3.网板破损不允许.干膜56条状短路1.棕片上沾有条状杂物或贴膜前板面沾条状油污(此现象多为底片保护膜破损)2.贴膜或曝光后因人为操作不当将铜面干膜刮不允许57干膜脱落1.贴膜前板面沾油污/沾胶或其它杂物2.贴膜时压力/温度过小等不当致干膜与铜面结合不牢3. 贴膜或曝光后因人为操作不当将铜面干膜刮4.干膜自身附著力不好不允许58条状短路1.棕片上沾有条状杂物或贴膜前板面沾条状油污2.贴膜或曝光后因人为操作不当将铜面干膜刮伤不允许59点状短路1.棕片上沾有点状杂物或贴膜前板面沾点状油污2.贴膜或曝光后因人为操作不当将铜面干膜刮伤不允许.干膜站60干膜膜破1.干膜韧性不足,较脆2.CU板板面杂物或巴厘过高3.贴膜后静置时间过长,曝光能量太低4.显影、水洗喷压过大或显影速度过慢不允许61板面沾污1.板面沾胶/沾油垢等不良物不允许62干膜脱落1.干膜挈性不足,较脆2.CU板板面杂物或巴厘过高3.贴膜后静置时间过长或显影速度过慢不允许.63 干膜沾膜1.棕片之暗区被刮伤2.显影不尽或显影时残膜反沾大铜每面不超过2个点,每点小于10mil,其它部位不允收干膜站64线路突出1.贴膜后沾有脏点或底片上沾有脏点2.操作刮伤干膜不超过原稿线径的20%65干膜断路1.底片之暗区被刮伤2.显影不尽或显影时残膜反沾不允许.66 干膜短路1.棕片上沾有点状杂物或贴膜前板面沾点状油污2.贴膜或曝光后因人为操作不当将铜面干膜刮伤不允许67 干膜对偏1.干膜站对底片时未保证孔环之ring各方向宽度相等(前提为孔正),2.板子或底片有涨缩零件孔余环≥2mil,导通孔孔偏不超过孔环的1/4,且与线路相连处不小于2mil干膜站68撕膜不尽1.割膜不良致撕膜时未能整块撕起2.撕膜时起膜位置不对成型线以内不允许.69 NPTH孔膜破1.钻孔后巴厘处理不彻底,即巴厘高2.干膜封孔能力不够3.跨孔过大4.干膜静置时间过长或显影时冲压过大不允收70 干膜脱落1.贴膜前板面沾油污/沾胶或其它杂物2.贴膜时压力/温度过小等不当致干膜与铜面结合不牢3.贴膜或曝光后因人为操作不当将铜面干膜刮4.干膜附著力不好不允许71 板面油污1.贴膜以前,因设备漏油或人为操作不当,致使油污直接或间接沾污板面不允许.成型站72模具冲偏1.板弯板曲或吹气过大或人为操作不当致板子未套好PIN孔时模冲造成不允许73槽孔捞偏1.定位PIN栽斜2.程式有错误超客户公差不允许74模冲伤孔1.套PIN套偏2.模具弹力胶不平衡3.板材涨缩或PIN针偏大不允许75斜边金丝1.铣刀不利或下刀点过于靠刀边2.因设备或人为调试不当致铣刀抖动较大3.斜板行进时用力不平衡不允许.成型站76V-CUT过穿1.调刀过深或铣刀不水平2.过板时叠板所致3.板弯板曲或V-CUT刀具运转不稳不允许77V-CUT过反1.未按进料方向放板过V-CUT2.程式错误不允许78V-CUT伤铜1. V-CUT两边挡板不平行2.板子外型有偏差3. V-CUT间距过小4. V-CUT刀角度偏大或刀片磨损过重不允收.79 V-CUT过穿1.调刀过深或铣刀不水平2.过板时叠板所致3.板弯板曲或V-CUT刀具运转不稳不允许成型站80V-CUT冲反1.未按磨具进料方向入板2.S/C面设计相似,识别有误3.模具未设防呆PIN不允收81V-CUT毛屑1. V-CUT在要求范围内调试2.客户外形公差小,且槽口偏小3.刀片角度过大或刀口不锋利按客户要求有不同.82 V-CUT伤铜1. V-CUT两边挡板不平行2.板子外型有偏差3. V-CUT间距过小4. V-CUT刀角度偏大或刀片磨损过重不允收83 模具冲偏1.板弯板曲或吹气过大或人为操作不当致板子未套好PIN孔时模冲造成不允许成型站84斜边不齐1.板弯板曲/斜边台面不平2.斜边行进时用力平均3.斜边不锋利/铣刀运转时稳定性不佳不允收.85 断导线1.铣刀不锋利或下刀点太靠刀边不允收86 织纹显露1.PP之玻璃布间距过大/TG点不稳定等PP品质不良2.压合时参数不当致流胶过大3.L/Q重工时退洗时间过长,导致药水对树脂攻击严重,显露出玻织布基材上无明显白点白斑,经热冲击试验不会造成分层起泡87 靶孔偏1.D/F对S/C时对偏2.钻靶时钻偏无线路土3mil,有线路土2.5mil.钻孔站88钻孔孔偏1.钻孔资料有误2.钻机精度不够(超出土3mil)或机台有故障3.叠板数超规范或钻头质太差土3mil 89多钻孔1.程式有误不允收90孔烧焦1.钻孔速度过快2.钻头排屑不良或钻针设定过深3.断半针作业或spindle掉刀不允许91光学点残1.干膜沾膜2.电镀过蚀3.人为刮伤不允收.品检站91A手指氧化1.镀A时A槽药水浓度不当或有槽液污染,或水洗不尽2.转运和生产作业时手接触污染3.不以收92锡面凹坑1.喷锡前CU不洁或CU面不平整2.锡铅不纯或空气内含有杂物3.风刀不良1.不影响焊性及锡厚为为准93线路断路1.D/F棕片刮伤,即暗区部分线路被固化,蚀刻时被蚀掉2.操作中锡铅被刮全伤,CU线路无保护层3.镀锡铅前CU线路处有油污或沾胶不允许.94 线路断路1.D/F棕片刮伤,即暗区部分线路被固化,蚀刻时被蚀掉2.操作中锡铅被刮全伤,CU线路无保护层3.镀锡铅前CU线路处有油污或沾胶不允许品检站95A面发白1.化A前处理微蚀过度2.因化NI后水洗不洁或A槽槽液非正常导致A厚不足无明色差且A厚在管控范围96A手指刮伤1.因人为操作不当造成镀A前或镀A后A手指上之刮痕不造成露NI,不超过3根,无明显刮痕.97 刮伤露铜1.防焊印刷后,人为操作不当将板面之防焊刮掉每点不超过3点,每点不超过10mil98 条状针点1.此为较有规律的直条状,应与机器设备之规律性运转有关2.D/F磨刷时板面被沾有油脂或点状胶类物3.D/F显影影时有去膜不尽或有不浴物附于板面每PCS不超过3点,每点不超过10mil,厚度不超过1/5板厚品检站99CU面凹陷1.基材本身有针点凹陷不良(检查基板表面)2.压合时CU皮表面沾尘或PP质量不良造成压合后此瑕玼3.电镀铜时因槽液特别是光泽剂不正常导致CU积不良A手指不允许,每面少于3点,每点不大于20mil,不超过板厚的1/5100板面沾锡1.喷锡前因防焊漏印或CU面防焊被刮掉,致露出CU面,在HAL时露CU部分被喷上锡线路上不允并列存在;大铜面每面不超过3个点,每点不大于10mil.101 CU面花班1.此为防焊之后之花班2.防焊之前CU有沾胶或油脂等物污染3.因防焊本身品质不良造成显影溶解时局部不尽4.因退洗不尽重工或显影时未冲洗净致有药水水痕不允许102 SN手指刮伤1.此锡手指刮伤处有喷上锡,另此为明显人为造成2.为喷锡前因人为操作不当导致锡手指被刮掉部分不允收品检站103电镀针点1.此仅指电镀本站造成之此不良2.镀铜时槽液有机污染或金属污染致CU2+沉积不均3.光泽剂中之carrier不足或过量4.电镀前处理CU面未处理净A手指不允许;大铜面每面少于3点,每点不大于20mil,不超过板厚的1/5.104 线细1.干膜曝光时赶气不到位或吸真空不足或曝光能量不足不均导致S/C线复制线在干膜板时比原稿小且小于标准2.显影过度或走蚀刻时因速度过慢或槽液管控不当导蚀刻出之线路小于原稿之20%不于原稿之20%105 板面沾锡1.喷锡前因防焊漏印或CU面防焊被刮掉,致露出CU面,在HAL时露CU部分被喷上锡线路上不允并列存在;大铜面每面不超过3个点,每点不大于10mil106 板损1.在生产过程中或板料转运中因人员操作不当导致板子有碰到机器或地面,造成板子局部破损不允收.品检站107板面CU瘤1.D/P活化/去脂平整或微蚀槽液受有机或金属污染2.电镀铜槽添加剂不当或阳极有破损导致金属污染不允收108电镀铜残1.因撕膜不尽或板面油脂/沾胶等造成D/F后该处未镀上CU与锡铅保护层,蚀刻时被蚀掉2.镀锡铅后因锡铅氧化或锡铅刮伤致蚀刻时被掉大铜面每点不大于20mil,每面只允许1点,其它地方不允许109线路断路1.D/F棕片刮伤,即暗区部分线路被固化,蚀刻时被蚀掉2.操作中锡铅被刮全伤,CU线路无保护层3.镀锡铅前CU线路处有油污或沾胶时每刻不允许110防焊刮伤1.印刷防焊后因人为操作不当造成板面之防焊被刮伤不允收.品检站111A手指刮伤1.因人为操作不当造成镀A前或镀A后A手指上之刮痕不造成露NI,不超过3根,无明显刮痕112A面花斑1.化A前CU面不洁2.NI槽NI含量不足等参数不合理;NI槽污染3.摇摆动作不到位不允收113板面上金1.因前站防焊脱落,导致后续走化A时化上A/NI2.走A线前处理磨刷过重致防焊有被刷掉不允收.114 A氧化1.化A时A槽药水浓度不当或有槽液污染,或水洗不尽2.转运和生产作业时手接触污染不允收.。
10月制程不良分析总结报告
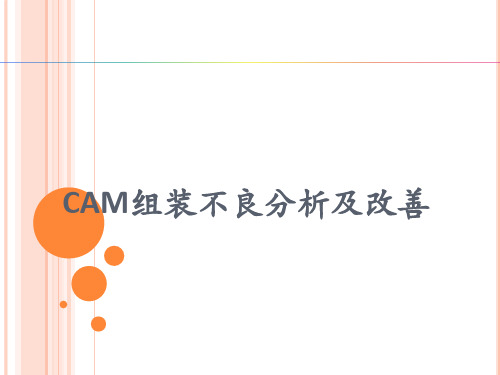
法
使用激光分板、超声波清洗 COB
公司高层
11月10日
棉签擦拭次数,废弃棉签误用 棉签蘸取酒精量多 振动后才能测试,终检前跌落工 序 百级工作台封装—测试洁净度 环
梁江(技术) 梁江(技术) 刘新昌(CAM) 马宏伟(品质)
10月30日 10月30 11月3日 11月1日 透明赃物 IPQC巡查 外校 避免硬板打磨 粉尘
CAM组装不良分析及改善
一.制程不良报表 二.TOP3不良原因分析 三.改善措施及验证计划
一.制程不良前三项
1.脏污 2.功能不良 3.模糊
从10月报表统计出前三大不良项目为:
二.TOP3不良原因分析
1.脏污原因分析:
人
漏检 自身作业水平 人员作业没有休息 棉签蘸取酒精太多
脏 污
测
没有调焦最清晰
说明:OQC退检数据下降,说明产线发现问题的能力提高,流出问题减少
使用的棉签是正牌,
棉签公司网站为 http://www.sa-nyo.co.jp/
脏污棉签防止误用装置 (丢进去后无法从顶部取出)
试验1 使用1280*1024显示屏检测前、后,OQC检出不良数据对比 使用前 10月27日 10月28日 10月29日 10月30日 11月3日 OQC检出不良批数 4 1 5 9 11 使用后 11月6日 11月7日 11月8日 11月9日 11月10日 OQC检出不良批数 6 2 6 3 2
11月5日
11月3日 11月3日
委外做镀层分析
川田 符合使用规定要求
功能不良改善措施
改善对象
措施要点
上料前目视检查FPC洁净度
责任人员
张光水(SMT)
实施时间
11月1日
SMT制程不良原因及改善报告
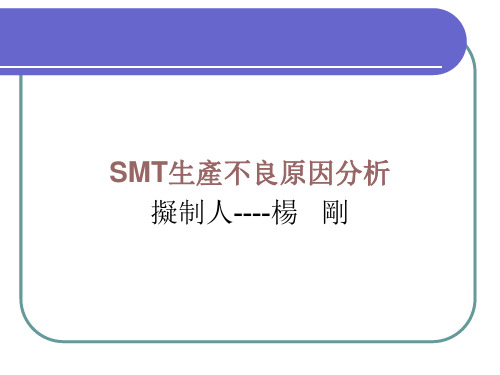
新旧锡膏混用
手放零件方法不当 载板系统不良 元件数据 轨道速度过快 设定不当 吸嘴 规格 吸嘴 弯曲 置件 不稳 坐标 偏移
方法
机器
人
人为跳掉 mark 作业
材料
零件有一边焊盘 吃锡不良 零件过大过重 未及时收板,PCB在回焊 炉中碰撞 人为手抹锡膏 备料时料带过紧 零件厚度不均 零件氧化 异形零件 手推撞板 人为手拨 缺锡 PAD间距与组 件长度不符 零件与PAD不符 手摆料 缺乏质量意识 PAD宽度与组件 宽度不符 零件脚歪 焊盘上有异物 零件脚弯 PAD 离轨道边小 于3mm. PAD氧化
(3) WHERE——何處?在哪裡做?從 哪裡入手? (4) WHEN——何時?什麼時間完成? 什麼時機最適宜? (5) WHO——誰?由誰來承擔?誰來 完成?誰負責?
(6) HOW ——怎麼做?如何提高效率? 如何實施?方法怎樣? (7) HOW MUCH——多少?做到什麼 程度?數量如何?品質水準如何?費用產 出如何?
环境
人
材料
露铜 无尘布毛絮堵 塞钢网开口 氧化 沾锡性
焊盘 有杂物 距板边不足3mm 沾油漆 不平整
缺乏质量意识 人为设定E-pass模式 手放散料遗漏/错误 收板不及时炉内撞板 人为设定跳过
PCB
设计 有异物 变形 黏 性 低
印刷后PCB板停留时间过长 手推撞板 手抹锡膏 通风不畅 生产模式被改动 (pass,idle) 未上锡 不正确操机 温度高锡膏变硬 未认真检查 真空不畅 程序缺件 擦钢网方法不正确 元件高度设定太薄 作业标准书不完善 流程错误 新旧锡膏混用 清线时关 闭料站 更改贴片顺序 紧急停止 锡膏印刷缺锡 电磁阀不良 钢网材质 传感器失灵 机器故障 轨道不洁 Z轴不平 机器振动 开口堵塞 MTS振动太大 轨道卡板 气压 Mark点设置 钢网设计不良 钢网未开口 运转速度 开口不正确 贴片 速度 过快 吸嘴 尺寸 不符 吸 嘴 弯 曲 坐 标 误 差 吸 嘴 磨 损 吸嘴 堵塞 跳掉次序数据 收板 零 件 氧 化 外形 尺寸 变形 厚度 不规 损 大小 抛件 差异 则 件 料带过紧 或过松 沾 锡 料带粘性 物质多 性 包裝不良
制程异常分析改善汇总

防焊前五项制程问题分析:一、防焊空泡:造成原因:1、前处理不良。
(H2SO4浓度、水质、吹干段角度及风量,吸水海棉清洁度、烘干温度)。
2、磨刷后放置时间过长,室内湿度偏低。
3、印刷台面沾有油墨及其它有机溶剂,反沾板面,油墨搅拌不均。
4、预烤不足。
5、曝光能量太低或太高。
6、显影侧蚀太多。
7、HAL浸助焊剂时间太长,锡槽温度太高,浸锡时间太长。
预防措施:1、前处理作业必须按SOP要求生产。
2、磨刷后放置时间不得超过2H ,室内湿度控制在50-60%之间。
3、印刷台面保持清洁,印第一面时台面上垫一张白纸,以保证板面清洁度。
4、预烤温度保持70±2℃,烤后之板保证不粘棕片。
5、曝光能量保持在9-13格。
6、显影点控制在50-60%,避免过多侧蚀。
7、后烤通风保持良好,塞孔板必须分段烘烤。
8、HAL作业须完全按照SOP操作,不可有违规作为。
二、L/Q内圈阴影:原因分析:1、油墨过期。
2、预烤时间过长,温度过高。
3、挡点印刷时,孔环处积墨过多,印刷房湿度不够。
4、曝光前,静置时间过长。
5、显影速度过快,压力过小。
6、棕片遮光度不够。
7、曝光时吸真空压力未能达到要求。
改善对策:1、油墨按照先进先出的方式使用,保证在油墨保质期内使用。
2、预烤时间和温度按SOP要求作业,且烤好后及时取出防止冷烤。
3、印刷房湿度保持在50-60%之间,挡点印刷保持连贯,且印一PNL刮一次网版。
4、预烤后板静置时间不能眼过12H,最连贯4H以内对位完。
5、显影点保持在50-60%之间。
6、选用遮光度及质量较好之棕片生产。
7、吸真空不得低于600㎜Hg,且须保持导气良好。
三、卡锡珠:原因分析:1、印刷塞孔不满(量产板)。
2、退洗板导通孔内油墨未剥除干净。
3、油墨本身质量问题。
4、HAL贴胶未贴好,某些孔呈半覆盖状态。
5、HAL浸助焊剂及浸锡时间过短。
改善对策:1、从印刷各条件去改善塞孔程度。
(刮刀压力、角度、确度、速度、网目T数量)2、选用适合的退洗液,尽可能洗净导通孔内油墨,保证塞孔效果。
制程异常分析(典型案例)报告
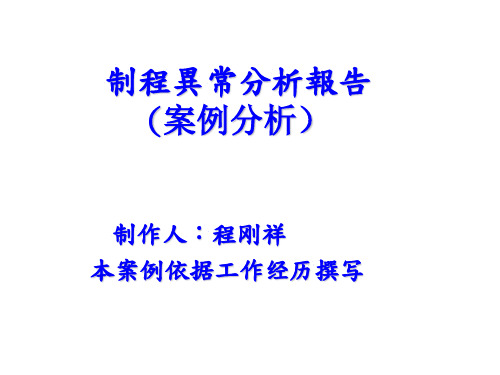
制作人:程刚祥 本案例依据工作经历撰写
一、不良现象描述
a.日期: 2019/12/25
工位: 孔规
b.機型:XXXXX-0X USB 3.1 TYPE-3 沉板母座
c.不良現象及不良率:
USB 3.1 TYPE-3 沉板母座上在做孔规测量,放入孔规不顺畅(不平贴,严
重者可能导致SMT装板不良) 。
剪除毛刺或剪短
孔规检测
五、长期对策
a.图面,作业指导书标准化: 1、修订SIP,补充内容:料带预断点检验毛刺环节并加以组装实配5PCS; 2、来料通过CCD和二次元量测把握冲压件上毛刺的缺陷等级,不得大于 0.01mm。 b.JIG/TOOL工治具修复合理化: 1、通知冲压工序,对该模具进行确认并修复; c.防呆(POKA YOKE)措施(颜色形状方向,声音左右,夹治具布局设变): 1、首件重点检验此异常,重点抽查并以实配检测是否平贴,是否顺畅。
不良圖片說明
12月12日、量化数据求出: 1、抽查料带库存品发现: 其中12月21日2500*7(外强);3500*4; 3500*6外发、 共
计420.9KPCS,经检查铁壳预断面宽度为:0.147-0.125mm,切断后有毛刺(高度超出 0.02mm)现象;
b.现场,现物,现状调查: 1、抽查来料7托盘/ 420.9KPCS ;成品2280PCS各5PCS; c. 调查制程,物料,设备5M1E因子: 1、可能因子:法/机/料。(人/机/物/环/法)
三、验证可能因子(分析)
a. 预计验证时间表: 1、12月26日现场检讨并确认SOP(作业指导); 2、12月26日已抽查来料库存/成品; b. 验证可能因子: 装配不到位;胶芯来料不良,铁壳来料异常; c.验证报告分析提出说明: 1、USB 3.1 TYPE-3 沉板母座上的铁壳预断位点应力异常,手工掰 断有毛刺,高出胶芯界面0.02mm;
SMT制程不良原因及改善措施分析

改善对策
1、印刷前清洗干净; 2、调整印刷机或点胶机; 3、更换新红胶; 4、印刷过程避免异物掉过去; 5、调整炉温或用纸皮垫着过炉; 6、调整贴装高度。
产生原因
1、机器贴装时无吹气抛料无吹气,抛料 盒毛刷不良; 2、贴装高度设置过高元件未贴装到位; 3、头部气阀不良; 4、人为擦板造成; 5、程序修改错误; 6、材料上错; 7、机器异常导致元件打飞造成错件。
1、锡膏活性较弱; 2、钢网开孔不佳; 3、铜铂间距过大或大铜贴小元件; 4、刮刀压力太大; 5、元件脚平整度不佳(翘脚、变形) 6、回焊炉预热区升温太快; 7、PCB铜铂太脏或者氧化; 8、PCB板含有水份; 9、机器贴装偏移; 10、锡膏印刷偏移; 11、机器夹板轨道松动造成贴装偏移; 12、MARK点误照造成元件打偏,导致空焊; 13、PCB铜铂上有穿孔;
产生原因
1、原材料不良; 2、规正器不顺导致元件夹坏; 3、吸着高度或贴装高度过低导致; 4、回焊炉温度设置过高; 5、料架顶针过长导致; 6、炉后撞件。
改善对策
1、检查原材料并反馈IQC处理; 2、维修调整规正座; 3、调整机器贴装高度; 4、调整回焊炉温度; 5、调整料架顶针; 6、人员作业时注意撞件。
产生原因
改善对策
1、调整回流焊温度(降低升温速度); 2、锡膏在使用前必须回温4H以上; 3、将室内温度控制到30%-60%); 4、将PCB板进烘烤; 5、避免在锡膏内加稀释剂; 6、重新开设密钢网; 7、更换适用的锡膏,按照规定的时间对锡膏 进行搅拌:回温4H搅拌4M。
SMT制程不良原因及改善对策

调整印刷机平台的水平度平行度;
6
基板表面异物造成周边元件锡膏印刷 过厚;
基板使用前进行除尘作业;
7
一次面基板背面残留锡膏过炉形成锡 珠,二次面锡膏印刷时垫起钢网形成 多锡;
避免一次面基板粘附锡膏,避免洗 板作业;
8 修理员回锡过多;
指导修理员按标准作业。
11
立起
产生原因
1 铜铂两边大小不一产生拉力不均; 2 预热升温速率太快; 3 机器贴装偏移; 4 锡膏印刷厚度不均; 5 回流焊内温度分布不均; 6 锡膏印刷偏移; 7 机器轨道夹板不紧导致贴装偏移; 8 机器头部晃动贴装偏移; 9 焊盘两端的散热程度不一致融化速度差异; 10 炉温设置不当; 11 铜铂间距过大; 12 MARK点误照造成元件打偏; 13 料架不良,元件吸着不稳打偏; 14 原材料不良; 15 钢网开孔不良;
发形成干锡膏,混入印刷产生钢网堵孔。
改善对策
10
多锡
产生原因
改善对策
1 钢网开孔过大或厚度过厚;
按标准制作钢网;
2 锡膏印刷厚度过厚;
调整印刷参数(压力、脱模等) ;
3 钢网底部粘锡;
清洗钢网;
4 IC元件底部接地焊盘锡膏溢出形成多 接地焊盘开孔适当减小,贴装高度适
锡;
当调高;
5
印刷平台不平行或高于基板导致印刷 多锡;
19 原材料设计不良;
反馈IQC联络供应商;
20 料架中心偏移;
校正料架中心;
21 机器吹气过大将锡膏吹跑;
将贴片吹气调整为0.2mm/cm² ;
22 元件氧化;
更换OK之材料;
23 PCB贴装后长时间没过炉,导致活性剂挥发; 及时将PCB-A过炉,生产过程中避免堆积;
smt制程不良原因及改善措施
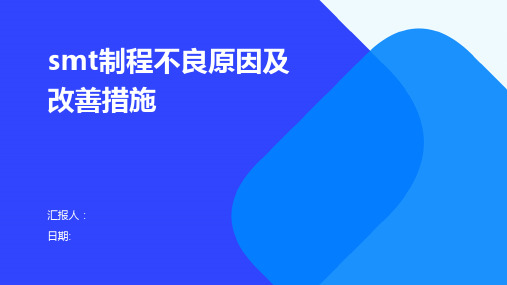
3
检测不良
PCB板翘曲变形、尺寸偏差等
环境因素(温度、湿度)影响检测结果
检测不良
01
改善措施
02
提高检测设备精度,定期校准和维护保养
03
优化检测程序,提高检测灵敏度和准确性
检测不良
01
加强PCB板的质量控制,防止翘 曲变形和尺寸偏差等问题
02
控制环境因素,确保检测环境稳 定和适宜的温度、湿度等条件
03
SMT制程改善措施
原材料控制
确保供应商的原材料质量稳定可 靠,进行严格的进料检验和测试 ,防止不良原材料进入生产环节
。
与供应商建立长期稳定的合作关 系,定期对供应商进行评估和审 计,确保供应商遵循质量标准和
要求。
对原材料存储和保管进行严格控 制,避免潮湿、污染和氧化等问
题的发生。
设备维护与保养
产成本,增强市场竞争力。
质量管理体系的运行与维护
质量管理体系的运行
企业需要建立专门的质量管理部门或质量管理团队来负责质 量管理体系的运行和维护,确保质量管理体系的有效性和持 续性。
质量管理体系的维护
企业需要定期对质量管理体系进行审查和更新,以确保其适 应市场和客户需求的变化,同时及时发现和解决潜在问题。
检查和返工
检查焊接质量和零件放置位置 ,对不良品进行返工。
SMT制程重要性
01
02
03
提高生产效率
SMT制程可以实现自动化 和批量生产,从而提高生 产效率。
提高产品质量
SMT制程可以提供高精度 的零件放置和稳定的焊接 质量,从而提高产品质量 。
降低成本
SMT制程可以减少零件的 包装和运输成本,同时也 可以降低人力成本。
- 1、下载文档前请自行甄别文档内容的完整性,平台不提供额外的编辑、内容补充、找答案等附加服务。
- 2、"仅部分预览"的文档,不可在线预览部分如存在完整性等问题,可反馈申请退款(可完整预览的文档不适用该条件!)。
- 3、如文档侵犯您的权益,请联系客服反馈,我们会尽快为您处理(人工客服工作时间:9:00-18:30)。
21)层压机未及时抽空(加压过程挤不出);2)真空泵问题,或硅胶板破、硅胶条不严密导致;真空度或压力不够;3)来料不良,例如EVA含有水分子;空气被密封在EVA胶膜内;4)EVA裁剪后,放置时间过长,它已吸潮;5)层压时间过长或温度过高,使有机过氧化物分解,产出氧气;1)层压人员随时检查真空表显示值,要有预防措施;2)维护真空泵的同时,对硅胶板的使用寿命要严格控制;3)注意EVA放置的周围环境和使用时间;4)延长真空时间 检查层压机的密封圈检查真空度和抽气速率;5)检查抽气速度 加快硅胶板下压速度降低层压温度 ,使用表面压花的EVA膜检查加热板温度 ;人员、反光检验及层压员也可能造成);2)来料不良,或过程中掉至,(由于EVA、背板、小车子有静电的存在,把飘在空气中的头发,灰尘及一些小垃圾吸到表面);的材料有质检意识;2)反光检验员提高质检意识,仔细,负责任的检验,重中之重;3)做好6S管理,保持周边工作环境的整太阳能组件生产过程主要不良现象造成的原因及纠正措施(以下图片仅仅是一种不良现象代表)1不良图片不良原因纠正措施1)提高来料质检的力度和方法;2)对串焊台及时清理。
包括单焊人员的质量意识(同时控制焊接手势);3)对层压机的维护,提高加压阶段的稳定性;4)对新员工的培训,包括盖层压布的手势并对现场指导为主;1)电池片本身质量,隐裂所致(暗伤)加上EVA的流动性;2)焊珠顶破或者焊锡堆积过厚;3)层压机加压阶段压力大导致;4)EVA不平整(鼓包现象严重);5)层压人员盖层压布布手势不正确;6)单串焊手势过重致使造成;未按工艺要求(离起焊点绝缘边3-4mm);裂片气泡1)单焊人员焊接速度过快,及辅焊带手势不对;2)焊带规格与电池片主栅线不匹配,容易露白;虚焊导致(层压后);3)新员工不知,更加容易造成;1)通过培训加强新老员工的焊接手势及质量意识,对其问题引起重视;焊问题的产生;31)主要原因帽子佩戴不严密(主要集中排版人员、反光检验及层压员也可能造成);2)来料不良,或过程中掉至,(由于EVA、背板、小车子有静电的存在,把飘在空气中的头发,灰尘及一些小垃圾吸到表面);1)确保佩戴帽子严密,同时要对所用到的材料有质检意识;2)反光检验员提高质检意识,仔细,负责任的检验,重中之重;3)做好6S管理,保持周边工作环境的整洁,并勤洗衣裤做好个人卫生;41)排版人员不经意将残留焊条溅进,(往往是手套毛丝钩进导致,剪的过程飞入);2)剪多余焊带时未一刀剪下,多次剪所致;3)拿第一张EVA碰到排版桌边的PET,其粘在EVA上;非排版人员帮贴PET过程碰到桌上的PET致其渐入组件内;1)对剪下的残留焊带要一一放入盒子,统一回收,切忌,养成习惯性动作!!!保持排版台的干净整齐;2)反光检验员得仔细,做到心中有数!3)改善焊带长度;4)排版人员拿EVA要养成良好的手势,勿使EVA接触PET;51)单焊时,重复焊接导致焊锡堆积(焊锡丝过量),串焊过程致使焊锡溅出;单焊造成焊锡黏在单片上;2)串焊盒未清理干净,有焊锡,致排版过程掉入;1)保重焊接手势正确,勿重复焊接,确保一次性拉到位;多其过程出现的焊锡及时清理,保证焊接台面的整洁;2)时刻擦洗串焊磨具台和串焊盒,预防焊锡、焊渣等调入;3)反光检验要认真检查,尤其是头尾焊锡,易造成短路;露白发焊条/焊屑/PET焊锡1)排版人员漏剪导致,尤其是上下班时更易造成(其容易导致短路);1)要对剪焊带有个习惯,一定的顺序,并把一一剪下的放置回收盒中,对每次剪完后要自检一次;2)反光检验更要认真负责,有条理的检查;101)EVA含有杂质,未融化小颗粒;2)层压前有杂物掉进EVA上(小虫子等);3)单串焊手套脏(含有助焊剂的残留物);1)裁剪员,排版人员要提高质检意识,对过程中不良的及时予以拿出(蚊子等);2)当天的板子尽早层压完,加强车间的防虫管理,及密封性,保持车间整洁;111)EVA收缩导致;2)排版人员未测量间距致使不足;1)加强EVA收缩的实验,同时提高准确性,即时去供应商取得联系;2)要用2mm对其使用,不能目测了事;9杂物气泡互连条未剪串间距不足12131)排版人员漏剪导致,尤其是上下班更易出错;1)要对剪焊带有个习惯,一定的顺序(从左往右),对每次剪完后要自觉检查一次 ;2)反光检验要认真负责,有条理的检查;3)更改汇流条设计尺寸,最合理化;141)排版人员未控制汇间距(PET贴的过紧);2)EVA收缩导致间距不足;1)利用黄蜡板的间距,一一焊接;2)汇流条间更改PET贴法的工艺;3)移上下距离时重新检验一遍;4)反光检验要认真负责,有条理的检查;151)分选人员存在颜色误区(应区分单片的浅、中、深);2)更换一道中的不良单片导致其中一片存在色差;3)单焊人员色差意识低导致;4)修复人员更换单片容易造成色差;1)分选人员严格把控色差,统一分类;2)对更换不良单片要说明色差情况;3)单串焊人员要有自检意识,杜绝色差流入下道工序;4)反光检验人员要仔细检查,对色差及时反馈与改组;5)修复人员返修前要查看其色差问题;剪汇流条未剪色差汇流条间距16171)反光检验处汇流条划痕;2)割边过程拿刀手势不正确导致;3)装框过程角码掉落;4)清理背面胶过程刀片划至;5)裁剪过程刀片划伤及排版过程刀片划至;1)反光检验台上有随工单遮住汇流条引出端;2)对新员工的培训及组长的指导;3)清理过程要求品质意识,注意拿刀片的手势;4)裁剪背板时要时刻注意拿刀方向;181)EVA与玻璃间脱层,原因①EVA问题(粘结剂不足)②玻璃含有油污,灰尘等1)首先品质过程巡检及工艺员要有敏感有必要对层压后抽检;2)强化对EVA实验,尽量细化,及时反馈与供应商;1)条形码受潮;2)层压机加热板温度过高;1)保证条形码储存在干燥的环境,或提前几天打印;2)层压后有层压员负责对其擦洗(橡皮、酒精);背板剥离强度不合格条码糊211)焊接手势过重导致缺角;或焊接工艺不达标(起收点间距未控制好);2)排版人员剪汇流条过急碰到单片,易造成缺角;1)通过培训提高焊接工艺要求;2)在排版过程时拿电池串要稳拿稳放;剪汇流条时要细心,力道不要太大;1)焊带、电池片及助焊剂不匹配;1)对每批次电池片工艺员要确认焊带、电池片及助焊剂的匹配性;3)控制标准的焊接环境温湿度;19201)焊台电烙铁温度设置偏高;2)焊接时间过长;3)黄蜡板孔未对住;1)定时对其焊台温度的抽检;2)对黄蜡板的工艺技术改善;3)通过培训指导,注重焊斑的严重性;4)层压后检验员及时与改组反馈问题;1)绝缘层开口裁斜;2)排版人员未对其拉到位;1)保证开口完好的情况下,排版人员要对其拉到位,同时自检;2)检验员对其监督反馈;焊斑绝缘层未放到位缺角虚焊1)来料存在问题;2)过程中撞击所致或划到装框机进刀口;3)清理过程刀片划至;1)操作人员要对使用材料有自检的能力;2)装框过程要注意手势,时常查看装框后的效果;242)焊接手势及焊接速度过快;3)环境温度过高,容易造成虚焊;2)通过培训提高焊接手势及焊接时间要求;3)控制标准的焊接环境温湿度;1)长短边来料存在尺寸上的误差;2)装框机气源不足;1)来料不良导致;2)修边或装框过程与桌面硬物接触划至;3)清理正面过程刀片使用不当(过重);1)对其半成品接触的桌面采取保护措施(垫上橡胶布);2)通过培训提高清理人员的质量意识;22231)来料要加强的同时,操作人员要对使用材料有自检的能力;2)装框要有一个准备的工作,确保装框机正常运行;间距过大铝边框碰焊玻璃划伤253)清理过程刀片划至;3)抬组件时要拿稳,勿大手大脚 ;4)清理时用刀片要仔细;1)装线盒时,未对残留胶带清理干净;1)撕胶带时,容易抠起汇条至折弯;2)盖上层压布不小心导致扭曲;1)层压人员盖上层压布过程要边盖边检查(尤其是新员工) ;2)装线盒时要认真对待,巧取;271)背板上有未固化的硅胶,装线盒过程于其接触导致;1)尽量保证背板上不留多余硅胶;2)清理过程要一一检查线盒及引出线上的硅胶,确保不流入客户手中;1)对其胶带的更改(美纹纸),容易撕起;2)通过培训提高操作人员要品质意识;2826框碰伤引出线内打折引出线有硅胶引出线有残留焊带1)贴标签的手势不对,导致空气进入,引起气泡;1)贴的方向一定要顺手;确保平整,并用手抚平;291)电池片整体移位,导致条形码背铝边框遮住;2)电池片移位(背板)导致铝边框上下间距不足;1)层压前要控制其电池片上下的距离,认真对待每次层压前的距离测量,减少后道不必要的麻烦;2)盖上层压布要确保一次盖到位;1)线盒硅胶打的不均匀;2)安装线盒不够用力,未均匀的挤出,容易导致线盒脱落现象;1)打胶要符合线盒胶的工艺要求,保证均匀溢出 ;2)安装线盒时要有自检意识,不足之处及时补胶;3)成品检验要一一检查;3130背板/电池移位接线盒一角无硅胶标签内有气泡暗341)单焊过程要控制焊接工艺,尤其焊接温度,焊接手势;1)通过培训提高员工的质量意识,并现场监督焊接要求是否符合工艺要求;1)电池片本身质量,隐裂所致(暗伤)加上EVA的流动性;2)焊珠顶破或者焊锡堆积过厚;3)层压机加压阶段压力大导致;4)EVA不平整(鼓包现象严重);(离起焊点绝缘边3-4mm);1)提高来料质检的力度和方法;2)对串焊台及时清理。
包括单焊人员的质量意识(同时控制焊接手势);3)对层压机的维护,提高加压阶段的稳定性;1)原材料所致;2)功率档混淆;1)加强来料的检验力度;提高抽检比例,及时反馈与供应商; 2)过程中要控制功率档混淆现象(尤其更换单片的过程);331)原材料所致;1)加强来料的检验力度;提高抽检比例,及时反馈与供应商;32焊接黑斑裂片暗片断栅1)加强来料的检验力度;提高抽检比例,及时反馈与供应商;354)EVA不平整(鼓包现象严重);5)层压人员盖层压布布手势不正确;6)单串焊手势过重致使造成;未按工艺要求(离起焊点绝缘边3-4mm);定性;4)对新员工的培训,包括盖层压布的手势并对现场指导为主;1)原材料所致;1)加强来料的检验力度;提高抽检比例,及时反馈与供应商;3836371)原材料污染;1)加强来料的检验力度;提高抽检比例,及时反馈与供应商;1)原材料所致;网纹污染片黑心片。